DOI:
10.1039/C5RA12369K
(Paper)
RSC Adv., 2015,
5, 68551-68557
Electrochemical reduction of CO2 to HCOOH on a synthesized Sn electrocatalyst using a Co3O4 anode
Received
26th June 2015
, Accepted 31st July 2015
First published on 31st July 2015
Abstract
The present work investigates the electrocatalytic effect of tin (Sn) and cobalt oxide (Co3O4) on the reduction of CO2 to products electrochemically (RCPE). Electrocatalytic (Sn) powder was synthesized by an electrodeposition method from a SnCl2·2H2O solution. Experiments were conducted using Co3O4 and Sn electrodes as the anode and cathode, respectively, in 0.5 M potassium and sodium carbonate and bicarbonate solutions. The electrodes were prepared by coating the electrocatalysts onto a graphite plate surface. The experiments were conducted with different applied voltages (1.5 to 3.5 V) and time intervals (5, 10, 15, 20 and 25 min) in the various electrolyte solutions. It was observed that HCOOH acid was the only product formed for all the applied conditions. At 1.5 V and 2 V, maximum Faradaic efficiencies of 74.04% and 92.6% for HCOOH production were obtained from 20 and 5 min reactions in a KHCO3 electrolyte solution. The ability of Co3O4 to perform water oxidation and the Sn electrocatalyst to reduce CO2 to HCOOH was established from the obtained results. The optimized reaction conditions to achieve high Faradaic efficiencies are explained in detail.
1. Introduction
Fossil fuels are used as the world’s primary energy source. Since the energy produced from fossil fuels is cheap, most of the energy generated in present technology is from fossil fuels. The process of energy generation deals with combustion of fossil fuels like coal, natural gas and petroleum. CO2 as well as some other gases like nitrous oxide, methane and halocarbons, are released into the atmosphere as greenhouse gases during this combustion. Utilization of fossil fuel energy is drastically increasing due to the rapid rise in population. The emissions of greenhouse gases, mainly CO2, are proportional to the energy generation and are the main cause of global warming.1–3 In all countries, most of the environmentally challenging issues arise due to CO2. Hence, it is highly recommended to control this greenhouse gas before its release into the environment. Many methods exist for the reduction of CO2 into various products, and the reduction of CO2 to products electrochemically (RCPE) is a particularly promising method due to several advantages. Firstly, RCPE in aqueous systems has yielded high selectivity at a low cost by using a heterogeneous catalyst.4–7 Secondly, the entire reaction process can be done at ambient temperature and pressures.8 Thirdly, it can be done using solar energy as an energy source.9–11 Fourthly, energy generated for the RCPE can be stored in the form of fuels.12,13 Fifthly, generation of the proton source from wastewater decreases the overall chemical consumption. Finally, RCPE systems have a compact design and are easy to scale up for industrial applications.
It is envisaged from the above literature that RCPE is going to be a promising technology for the reduction of CO2 to produce several products. Reduction of CO2 mainly depends on the electrocatalyst used in the reaction and the applied potentials. However, work is ongoing to improve the reduction rates by improving the stability and efficiency of electrocatalysts. The majority of attention is focused on studying the extent of catalyst deactivation in order to find a developed electrocatalyst of high stability.14 Electrolytes,15 pH16 and catalyst structure17–19 play major roles for product selectivity in RCPE. Copper is a well known electrocatalyst in RCPE as various products like methane, ethylene and other hydrocarbons are formed with significant efficiencies. However, due to the formation of multiple products, the process becomes more complex.20 In order to reduce this complexity, CO2 has to be reduced to a single product with a high Faradaic efficiency. If a liquid product is formed from RCPE with a high Faradaic efficiency, this could be a sustainable approach for future liquid fuel production. Some studies were done for RCPE with Pb and Sn electrocatalysts to form HCOOH.21–25 In most RCPE processes platinum (Pt) was used as an anode for the oxidation of water.26,27 However, few authors have investigated the effect of water oxidation using Co3O4 electrocatalyst for hydrogen evolution reactions.28–31
From the extensive literature survey, it was observed that Pt was used as an anode electrocatalyst for the oxidation reaction in most of the cases. The use of Co3O4 as an electrocatalyst in place of Pt for RCPE is scant and might be a better alternative. The present work explores the use of Co3O4 as an anode and tin (Sn) as a cathode material in RCPE for the reduction of CO2 to HCOOH as a single liquid product. The role of the electrocatalyst anode (Co3O4) and cathode (Sn) towards RCPE is explained with respect to the rate of reaction for all applied voltages using a 2-electrode glass cell. To the best of our knowledge, no studies have been reported using Co3O4 as an anode for RCPE with a Sn electrocatalyst. Therefore, the data generated in this investigation might be useful in the field of RCPE during the selection of low cost and appropriate electrocatalysts.
2. Experimental
2.1. Materials, characterization and product analysis
Materials. Graphite plates (1.5 × 2.5) cm2 were purchased from Sunrise enterprises, Mumbai. Sodium bicarbonate (NaHCO3), potassium bicarbonate (KHCO3), sodium carbonate (Na2CO3), potassium carbonate (K2CO3), tin chloride dihydrate (SnCl2·2H2O), acetone (CH3COCH3) and isopropyl alcohol ((CH3)2CHOH) were procured from Merck, India. Nafion (5 wt%) solution was obtained from DuPont, USA and a direct current (DC) source was purchased from Crown, India. All the chemicals were used without any further purification and deionized water was used in all experiments.
Characterization. The Sn electrocatalyst was characterized using a Fourier Transform Infrared Spectrophotometer (FTIR) (make: Shimadzu; model: IR Affinity-1). Peaks were recorded in the range of 500–4000 cm−1 by crushing the sample with KBr (IR grade). X-ray diffraction (XRD) analysis was done using a X-ray diffractometer (make: Bruker; model: D8 advance) between 10° to 80° 2θ. Particle size analysis of the synthesized electrocatalyst was done using a Delsa nano (make: Beckman coulter; model: Delsa nano C) particle size analyzer.
Product analysis. The product from the CO2 reduction was analyzed by ultra-fast liquid chromatography (UFLC, Shimadzu LC-20AD, UV-detector: deuterium lamp SPD-20A). The product was detected at a 205 nm wavelength by injecting 20 μl of the reacting sample into the C-18 Column (10 × 4 mm). Tetrabutyl ammonium hydrogen sulfate (5 mM) was used as the mobile phase at a flow rate of 1 ml min−1.
2.2. Electrochemical synthesis of the Sn powder
The tin (Sn) powder was synthesized by an electrodeposition method.32 A schematic for the synthesis of the Sn powder is shown in Fig. 1. Metal powder was extracted from the solution of 0.1 M SnCl2·2H2O by supplying energy between the metallic copper plate and graphite plate in an electrolytic cell. A constant current of 0.2 A was applied for 3 min during which the Sn deposition took place on the graphite plate. The deposited Sn powder was removed with acetone. Furthermore, this catalyst solution was heated at 100 °C for 1 h to obtain Sn powder.
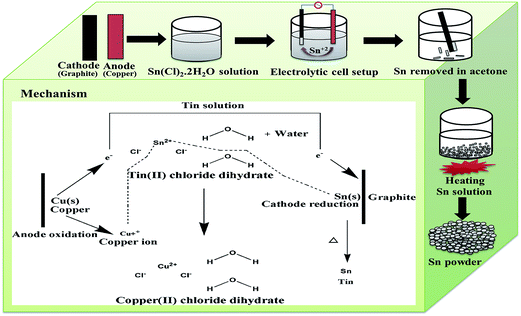 |
| Fig. 1 Schematic representation and mechanism for the synthesis of Sn powder. | |
2.3. Preparation of the electrodes
The electrodes were prepared in a 200 μl solution of nafion + isopropyl alcohol (IPA) in a ratio 1
:
5 which acts as a binder. 7.5 mg of the electrocatalyst (Co3O4 or Sn) was added to the binder solution, and sonicated for 30 min. These solutions were coated onto graphite plate surfaces at 80 °C to produce electrodes with active areas of 2 mg cm−2. Thereafter, the electrodes were dried for 2 h in an oven at 100 °C.
2.4. Electrochemical studies of the CO2 reduction
The prepared electrodes were used in RCPE in a 2-electrode homemade glass cell in order to study their effect on CO2 reduction. Fig. 2 shows a schematic of the experimental setup used for RCPE using a 2-electrode cell. The glass cell was filled with 80 ml of a prepared 0.5 M electrolyte solution which was saturated with CO2 by continuous bubbling for 50 min. RCPE experiments were conducted in the CO2 saturated solutions by connecting the electrodes to the DC source. Experiments were conducted at potentials of 1.5, 2, 2.5, 3 and 3.5 V with reaction times of 5, 10, 15, 20 and 25 min for every applied voltage.
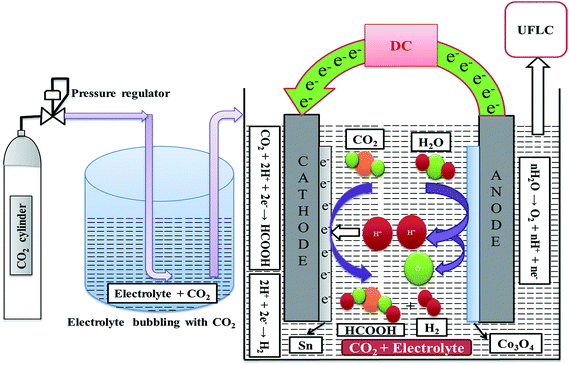 |
| Fig. 2 Experimental setup for the reduction of CO2 to HCOOH on a Sn electrocatalyst. | |
3. Results and discussion
3.1. Characterization and mechanism of formation of the Sn electrocatalyst
A FTIR spectrum of the synthesized Sn electrocatalyst is presented in Fig. 3a. The broad bands around 3000–3600 cm−1 and 1642 cm−1 correspond to O–H stretching vibrations and O–H bending vibrations respectively, and are attributed to adsorbed water. The band at 1000–1250 cm−1 confirms the presence of Sn.32 An XRD pattern of the synthesized Sn electrocatalyst is shown in Fig. 3b. Peak positions at 30.7°, 32.08°, 43.97°, 45.0°, 55.46°, 62.67°, 63.93°, 64.73°, 72.59°, 73.34° and 79.7° are matched closely to the Sn structure.33 The particle size analysis was performed using a Delsa nano (make: Beckman coulter; model: Delsa nano C) particle size analyzer and the particle size distribution data for synthesized catalyst is shown in Fig. 3c. The particle size of Sn powder was found to be in the range of 156.7–278.9 nm. The distribution median size (Dv50) of the Sn electrocatalyst particles was found to be 192.5 nm. A mechanism for the formation of the Sn electrocatalyst is shown in Fig. 1. Oxidation of copper (Cu(s) → Cu2+ + 2e− (0.34 V)) and reduction of tin (Sn2+ + 2e− → Sn (0.14 V)) take place at the anode and cathode, respectively. Sn ions from the electrolyte solution are deposited on the cathode surface by accepting electrons generated at the anode (oxidation). Copper ions formed at the anode are the driving force for the deposition of Sn ions on the surface of the graphite plate. The deposition rate was proportional to the formation of new copper chloride molecules in solution. Further, upon heating, the deposited Sn powder on graphite gives the Sn electrocatalyst.
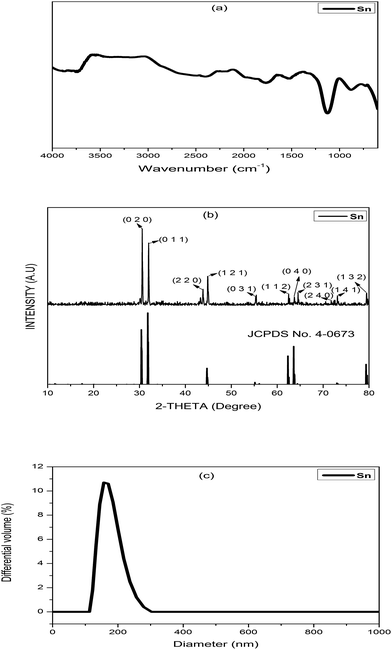 |
| Fig. 3 Characterization of the Sn electrocatalyst: (a) FTIR, (b) XRD, and (c) particle size analysis. | |
3.2. RCPE studies of the Sn electrocatalyst in different electrolyte solutions
3.2.1. Variation of the current density with applied voltage during CO2 reduction on the Sn electrocatalyst. Experimental results for the variation of the current density with applied voltages are shown in Fig. 4 for all the electrolytes. It was observed that the current density increased with increase in applied voltages in all cases. Reduction of CO2 signifies the increase of current density. Increase in current density indicates a high reaction rate for CO2 reduction or hydrogen generation. Fig. 4 shows that the potassium and sodium carbonate electrolytes give a high current density compared to the bicarbonate electrolytes. This confirms that the rate of reaction is higher for the carbonates of potassium and sodium. It is also found that the potassium electrolytes show higher current densities than the sodium electrolytes. In summary, the increase in the current density signifies the increase in the rate of reaction of CO2 reduction that occurs at the surface of the cathode in all the conditions applied.
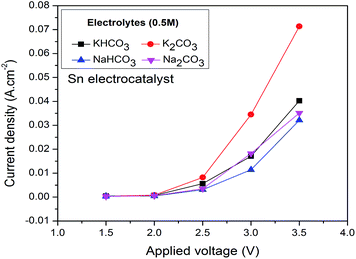 |
| Fig. 4 Variation of the current density with applied voltage during CO2 reduction with the Sn electrocatalyst. | |
3.2.2. Reduction of CO2 to HCOOH in KHCO3 solution (time vs. Faradaic efficiency). In order to find the applied energy utilized for CO2 reduction, the Faradaic efficiency was calculated over time for the applied voltages in 0.5 M KHCO3 electrolyte solution and shown in Fig. 5a. It was observed that the only product formed was HCOOH for the applied conditions. This signifies that the synthesized electrocatalyst was able to reduce CO2 to a single product. The higher maximum Faradaic efficiencies were obtained at the lower applied voltages of 1.5 V and 2 V compared with the others considered here. The Faradaic efficiencies for the reduction of CO2 to HCOOH at 1.5 V with reaction times of 5, 10, 15, 20 and 25 min were observed to be 8.28, 13.54, 52.2, 74.04 and 40.61%, respectively. Overall, the highest efficiencies (74%) were observed for this applied voltage after 20 min of reaction. Similar results were shown when Pt was used as the anode (Table 1) after a reaction time of 30 min.22 High Faradaic efficiencies (92.6, 67.36, 10.17, 0.91 and 14.51%) were obtained (Fig. 5a) at 2 V. RCPE at 2 V shows significant results for HCOOH with a high Faradaic efficiency of 92.6% for the 5 min reaction. However, at this applied voltage maximum energy was utilized in reducing CO2 to HCOOH. With Sn/Pt electrodes in 0.1 M KHCO3 solution at 2 V, a Faradaic efficiency of 47% was reported22 and a maximum Faradaic efficiency of 92.3% was observed.34 Faradaic efficiencies at 2.5 V decreased over time, with efficiencies of 16, 5.33, 3.45, 7.77 and 1.09%, of which a maximum efficiency of 16% was observed at reaction time of 5 min. Low Faradaic efficiencies of 0.10, 0.83, 2.87, 1.22 and 0.23% at 3 V and 0.43, 0.22, 0.21, 0.73 and 0.69 at 3.5 V, respectively, were found (Fig. 5a). Considering the above results it may be envisaged that low efficiencies were obtained at 3 V and 3.5 V due to other side reactions, especially hydrogen evolution due to a high proton generation at the Co3O4 anode. The synthesized electrocatalyst was able to reduce CO2 to HCOOH in all applied conditions. However, higher efficiencies were obtained at low potentials compared with high potentials. The optimized conditions for RCPE for HCOOH formation were observed to be 1.5 V (20 min) and 2 V (5 min).
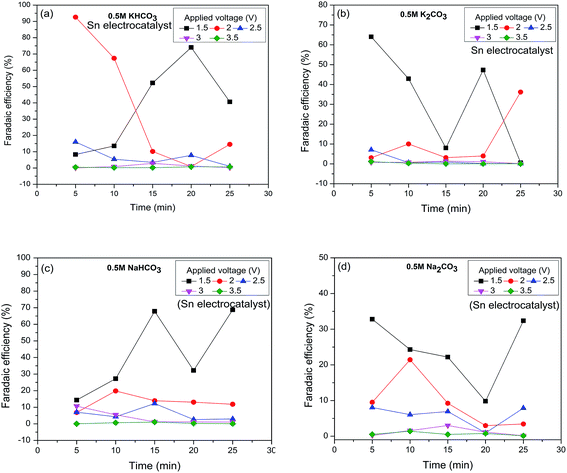 |
| Fig. 5 Variation of Faradaic efficiency over time during the reduction of CO2 to HCOOH using (a) KHCO3, (b) K2CO3, (c) NaHCO3, and (d) Na2CO3 electrolyte solutions. | |
Table 1 Comparison of HCOOH Faradaic efficiencies with different experimental conditions and with the literature
Electrode |
Electrolyte |
Applied voltage (V) |
Reaction time (min) |
Faradaic efficiency (HCOOH) (%) |
References |
Anode |
Cathode |
Pt |
Sn |
0.5 M KHCO3 |
1.5 |
30 |
74 |
22 |
2 |
30 |
47 |
1.5 |
120 |
20 |
2 |
120 |
20 |
Pt |
Sn |
0.1 M K2CO3 |
1.5 |
30 |
— |
2 |
30 |
14.2 |
1.5 |
120 |
— |
2 |
120 |
13 |
Pt |
Sn |
0.1 M KHCO3 |
1.39 |
— |
92.3 |
34 |
Pt |
Sn |
0.1 M KHCO3 |
1.8 |
60 |
91 |
25 |
Co3O4 |
Sn |
0.5 M KHCO3 |
1.5 |
20 |
74.08 |
Present work |
2 |
5 |
92.6 |
0.5 M K2CO3 |
1.5 |
5 |
64.03 |
2 |
25 |
36.18 |
0.5 M NaHCO3 |
1.5 |
25 |
68.72 |
2 |
10 |
19.83 |
0.5 M Na2CO3 |
1.5 |
10 |
32.82 |
2 |
10 |
21.44 |
3.2.3. Reduction of CO2 to HCOOH in K2CO3 solution. The reduction of CO2 to HCOOH using Sn and Pt as the cathode and anode materials in 0.1 M K2CO3 solution was investigated and reasonable Faradaic efficiencies were obtained for the different applied voltages.22 The Faradaic efficiencies of HCOOH formation from RCPE using Co3O4 as the anode at different applied voltages in presence of a 0.5 M K2CO3 electrolyte solution were investigated in this work and are shown in Fig. 5b. Significant results were obtained for RCPE at low applied voltages, particularly at 2 V and 1.5 V. However, on comparing with KHCO3 solution (Table 1), the efficiencies obtained were lower. This may be due to a high hydrogen formation.23 For RCPE at 1.5 V, the Faradaic efficiencies for HCOOH with reaction times of 5, 10, 15, 20 and 25 min were 64, 43, 8, 47.3 and 0.60%, respectively. A Faradaic efficiency of 39% was reported at 1.5 V.22 Overall, the applied voltage is able to reduce CO2 to HCOOH with good efficiency and the optimized reaction condition at this potential is a 5 min reaction giving an efficiency of 64%. It was observed that for RCPE at 2 V the efficiency increases with time and the obtained Faradaic efficiencies were 3, 10, 3, 4 and 36%. A Faradaic efficiency of 36% for a 25 min reaction was observed as the optimized reaction at this particular applied voltage. The RCPE at 2.5 V shows low Faradaic efficiencies of 7.1, 0.62, 0.90, 0.15 and 0.12%. Low efficiencies were observed with high current density, which may be due to other side reactions (Fig. 5b). At 3 V and 3.5 V, very low Faradaic efficiencies were obtained (for 5, 10, 15, 20 and 25 min reactions) as 0.73, 0.75, 1.36, 1.08 and 0.1% and 1.14, 0.31, 0.02, 0.02 and 0.03%, respectively. The RCPE results were also confirmed by the formation of HCOOH in all the experimental conditions considered here. However, lower efficiencies were obtained for carbonate solutions compared with the bicarbonate solutions. The higher current densities, so obtained, may be due to competition in the hydrogen evolution reactions. The use of the synthesized Sn catalyst and Co3O4 as an anode in the reduction of CO2 to HCOOH is proven to be an efficient method.
3.2.4. Reduction of CO2 to HCOOH in NaHCO3 solution. The experimental results of the reduction of CO2 to HCOOH in a 0.5 M NaHCO3 electrolyte solution are shown in Fig. 5c. High Faradaic efficiencies were observed at 1.5 V, and low efficiencies for the remaining applied voltages (Fig. 5c). However, the only product formed in all the applied conditions was HCOOH. At 1.5 V, the Faradaic efficiencies of 14.3, 27.2, 67.8, 32.2 and 68.7%, respectively, were obtained after 5, 10, 15, 20 and 25 min reactions. A decrease in efficiency in the 40 min reaction may be due to the oxidation of HCOOH at the Co3O4 anode.25 However, maximum Faradaic efficiencies of 68.7% (25 min) and 67.8% (15 min) were observed as optimum conditions. A 19% Faradaic efficiency was reported for a Sn/SnOx catalyst in a 0.5 M NaHCO3 solution at 0.7 V.23 Faradaic efficiencies of 6.8, 19.8, 13.9, 13 and 11.8% were obtained for RCPE at 2 V. This shows a lower Faradaic efficiency of the reduction of CO2 compared to that observed with the applied voltage of 1.5 V in these experimental conditions. For reaction at 2.5 V, low efficiencies of 7.02, 4.3, 12.26, 2.60 and 2.97% were observed (Fig. 5c). Lower efficiencies were observed as the reaction favors hydrogen generation (Fig. 5). The Faradaic efficiencies observed for the reduction of CO2 to HCOOH at 3 V and 3.5 V were 10.6, 5.4, 1.2, 1.1 and 1.05% and 0.03, 0.67, 1.07, 0.26 and 0.06%, respectively. It may be concluded from this section that RCPE is favored at all applied voltages and a maximum efficiency is observed at 1.5 V which is the optimum potential for HCOOH formation.
3.2.5. Reduction of CO2 to HCOOH in Na2CO3 solution. An RCPE study using Sn as an electrocatalyst in a 0.5 M Na2CO3 solution for HCOOH formation is shown in Fig. 5d. Formation of HCOOH in all applied conditions showed that low applied voltages are more favorable for high Faradaic efficiencies. Faradaic efficiencies of 32.8, 24.3, 22.2, 9.8 and 32.3% were obtained at 1.5 V. A sudden decrease in efficiency after a 15 min reaction was due to HCOOH oxidation at the anode.25 However, this voltage was more favorable for the reduction of CO2 to HCOOH with an efficiency of 32.3% after 25 min. For the reaction at 2 V, Faradaic efficiencies of 9.5, 21.4, 9.2, 2.9 and 3.4% were observed (Fig. 5d). It may be noted that the efficiencies were lower than those obtained from RCPE in the NaHCO3 electrolyte solution. In a Na based electrolyte solution RCPE took place effectively with a Sn/SnOx electrode.23 The Faradaic efficiencies of 8, 6, 6.9, 0.91 and 7.8% obtained at 2.5 V were observed to be lower in comparison with the above applied voltages. Low efficiencies were obtained at 3 V (0.20, 1.55, 2.98, 1.14 and 0.1%) and 3.5 V (0.49, 1.40, 0.49, 0.76 and 0.10%). This may be due to a high proton generation at Co3O4 which leads to increased hydrogen formation at the cathode surface. RCPE using this electrolyte was able to form HCOOH from CO2 at all applied voltages. Optimum conditions for maximum efficiencies were found at low applied voltages for RCPE.Finally, the application of Co3O4 as an anode for the reduction of CO2 to HCOOH was proven. Comparison of the HCOOH Faradaic efficiencies in different experimental conditions with the literature is shown in Table 1. From the table it may be concluded that the use of Co3O4 as an alternative to Pt as the anode for RCPE is economically favorable. The experimental conditions for high HCOOH Faradaic efficiencies of RCPE over time are also shown with respect to the applied voltages. It is concluded that bicarbonate electrolyte solutions were able to reduce more CO2 than carbonate solutions.
4. Conclusion
A study on RCPE was done by synthesizing Sn electrocatalysts via an electrodeposition method. The results showed that Co3O4 was able to oxidize H2O efficiently for CO2 reduction. Higher Faradaic efficiencies were obtained with bicarbonate based electrolyte solutions than with carbonate solutions at low applied voltages. The synthesized electrocatalyst was able to reduce CO2 to HCOOH effectively at all applied voltages. A maximum Faradaic efficiency of 92.6% was observed at 2 V with a reaction time of 5 min and 74.06% at 1.5 V after 20 min in KHCO3 solution. With a NaHCO3 solution, high Faradaic efficiencies of 68.72% were observed at 1.5 V with a reaction time of 25 min, which is the most optimum condition for RCPE. This preliminary study will be helpful towards finding cheap and effective electrocatalysts for RCPE (as alternatives to expensive Pt).
References
- L. Li, N. Zhao, W. Wei and Y. Sun, Fuel, 2013, 108, 112–130 CrossRef CAS.
- R. Bredesen, K. Jordal and O. Bolland, Chem. Eng. Process., 2004, 43, 1129–1158 CrossRef CAS.
- S. Shafiei and R. A. Salim, Energy Policy, 2014, 66, 547–556 CrossRef CAS.
- M. Alvarez-Guerra, S. Quintanilla and A. Irabien, Chem. Eng. J., 2012, 207–208, 278–284 CrossRef CAS.
- M. R. Goncalves, A. Gomes, J. Condeco, R. Fernandes, T. Pardal, C. A. C. Sequeira and J. B. Branco, Energy Convers. Manage., 2010, 51, 30–32 CrossRef CAS.
- I. Ganesh, Renewable Sustainable Energy Rev., 2014, 31, 221–257 CrossRef CAS.
- R. J. Lim, M. Xie, M. A. Sk, J.-M. Lee, A. Fisher, X. Wang and K. H. Lim, Catal. Today, 2014, 233, 169–180 CrossRef CAS.
- S. Kaneco, K. Iiba, K. Ohta, T. Mizuno and A. Saji, J. Electroanal. Chem., 1998, 441, 215–220 CrossRef CAS.
- J. L. White, J. T. Herb, J. J. Kaczur, P. W. Majsztrik and A. B. Bocarsly, J. CO2 Util., 2014, 7, 1–5 CrossRef CAS.
- S. Kaneco, H. Katsumata, T. Suzuki and K. Ohta, Appl. Catal., B, 2006, 64, 139–145 CrossRef CAS.
- Y. Ping, Y. Ta, P. Yen and C. P. Huang, Sep. Purif. Technol., 2013, 117, 3–11 CrossRef.
- M. Gattrell, N. Gupta and A. Co, Energy Convers. Manage., 2007, 48, 1255–1265 CrossRef CAS.
- D. T. Whipple and P. J. A. Kenis, J. Phys. Chem. Lett., 2010, 1, 3451–3458 CrossRef CAS.
- Y. Hori, H. Konishi, T. Futamura, A. Murata, O. Koga, H. Sakurai and K. Oguma, Electrochim. Acta, 2005, 50, 5354–5369 CrossRef CAS.
- Q. Wang, H. Dong and H. Yu, J. Power Sources, 2014, 271, 278–284 CrossRef CAS.
- N. Sreekanth and K. L. Phani, Chem. Commun., 2014, 50, 11143–11146 RSC.
- W. J. Durand, A. A. Peterson, F. Studt, F. Abild-Pedersen and J. K. Norskov, Surf. Sci., 2011, 605, 1354–1359 CrossRef CAS.
- F. Jia, X. Yu and L. Zhang, J. Power Sources, 2014, 252, 85–89 CrossRef CAS.
- G. Keerthiga, B. Viswanathan and R. Chetty, Catal. Today, 2014, 8–13 Search PubMed.
- P. Bumroongsakulsawat and G. H. Kelsall, Electrochim. Acta, 2014, 141, 216–225 CrossRef CAS.
- V. S. K. Yadav and M. K. Purkait, RSC Adv., 2015, 5, 40414–40421 RSC.
- F. Koleli, T. Atilan, N. Palamut, A. M. Gizir, R. Aydin and C. H. Hamann, J. Appl. Electrochem., 2003, 33, 447–450 CrossRef.
- Y. Chen and M. W. Kanan, J. Am. Chem. Soc., 2012, 5–8 Search PubMed.
- B. Innocent, D. Liaigre, D. Pasquier, F. Ropital, J.-M. Leger and K. B. Kokoh, J. Appl. Electrochem., 2008, 39, 227–232 CrossRef.
- W. Lv, R. Zhang, P. Gao and L. Lei, J. Power Sources, 2014, 253, 276–281 CrossRef CAS.
- J. D. Watkins and A. B. Bocarsly, ChemSusChem, 2014, 7, 284–290 CrossRef CAS PubMed.
- D. W. Dewulf and A. J. Bard, Catal. Lett., 1988, 1, 73–79 CrossRef CAS.
- A. Han, H. Wu, Z. Sun, H. Jia and P. Du, Phys. Chem. Chem. Phys., 2013, 15, 12534–12538 RSC.
- S. Dey, B. Mondal and A. Dey, Phys. Chem. Chem. Phys., 2014, 16, 12221–12227 RSC.
- M. Bajdich, A. Vojvodic, J. K. Norskov and A. T. Bell, J. Am. Chem. Soc., 2013, 135, 13521–13530 CrossRef CAS PubMed.
- J. Yang, K. Walczak, E. Anzenberg, F. M. Toma, G. Yuan, A. Schwartzberg, Y. Lin, M. Hettick, A. Javey, J. W. Ager, J. Yano, H. Frei and I. D. Sharp, J. Am. Chem. Soc., 2014, 136, 6191–6194 CrossRef CAS PubMed.
- M. A. M. Ibrahim, F. Kooli and S. N. Alamri, Int. J. Electrochem. Sci., 2013, 8, 12308–12320 CAS.
- P. Wu, N. Du, H. Zhang, J. Yu, Y. Qi and D. Yang, Nanoscale, 2011, 3, 746–750 RSC.
- K. Hara, A. Kudo and T. Sakata, J. Electroanal. Chem., 1995, 391, 141–147 CrossRef.
|
This journal is © The Royal Society of Chemistry 2015 |