DOI:
10.1039/C5RA11847F
(Paper)
RSC Adv., 2015,
5, 68476-68484
Intumescent flame retardancy of a DGEBA epoxy resin based on 5,10-dihydro-phenophosphazine-10-oxide
Received
19th June 2015
, Accepted 30th July 2015
First published on 30th July 2015
Abstract
5,10-Dihydro-phenophosphazine-10-oxide (DPPA) served as a co-curing agent for 4,4′-diaminodiphenylmethane in the curing reaction of bisphenol A diglycidyl ether (DGEBA) epoxy resin (EP). 1H NMR tracking the reaction of DPPA with DGEBA revealed that the P–H bond in DPPA had a higher reactivity with the epoxy group than the N–H bond. DPPA could promote the curing reaction of DDM with DGEBA. DPPA endowed the epoxy resin with a high flame-retardant efficiency due to the unique combination of phosphorus and nitrogen in the phenophosphazine ring. The cured epoxy resin could achieve a V-0 rating in the UL-94 test with a limiting oxygen index (LOI) of 33.6% at only 2.5 wt% DPPA. The reduced peak heat release rate and total heat release, and increased char yield further verified the excellent flame retardancy of EP. The flame-retardant mechanism of the epoxy resin was investigated by thermogravimetry-Fourier transform infrared spectrometry (TG-FTIR), scanning electron microscopy, elemental analysis and FTIR spectrometry. The results indicated that DPPA catalyzed the formation of the rigid intumescent char and the generation of the blowing-out effect in the epoxy resin matrix.
1. Introduction
Epoxy resins have been widely used in many fields such as coatings, adhesives, aerospace structure materials, electronic laminate materials, and insulation materials due to their excellent adhesion, solvent and chemical resistance, mechanical properties and insulation characteristics. The high flammability, however, limits broader applications of epoxy resins.1–3 It is necessary to prepare high-performance epoxy resins with non-flammability to meet the quality requirements of today’s society for epoxy resins. Because of the possible health and environmental hazards associated with the use of halogenated flame retardants, the worldwide interest in halogen-free flame retardants has increased in recent years.4–6
As halogen-free flame retardants, reactive compounds containing organo-phosphorus are known to be the most promising, and have been proved to endow epoxy resins with flame retardancy and release less toxic gas and smoke during combustion.7–10 9,10-Dihydro-9-oxa-10-phosphaphenanthrene-10-oxide (DOPO) and its derivatives have recently attracted a lot of attention in the flame retardant modification of epoxy resins. However, their incorporation was also found to decrease the glass transition temperature (Tg), initial degradation temperature and mechanical properties of epoxy resins because of a large additive amount of flame retardant.11–14 Therefore, overcoming these bottlenecks is a very critical issue for obtaining halogen-free flame retardant epoxy materials with high performance.
It has been found that flame retardant compounds containing both phosphorus and nitrogen elements exhibit enhanced flame-retardant efficiency due to a synergistic effect between phosphorus and nitrogen.15–18 The P-containing group can act both in the gas phase and in the condensed phase (via char formation) at the same time, and the N-containing group can release inert gases to dilute oxygen and facilitate the expansion of the char layer during the combustion.19–21 Therefore, it is desirable to use this synergistic approach to reduce the amount of flame retardants in order to obtain excellent flame retarding epoxy materials.
5,10-Dihydro-phenophosphazine-10-oxide (DPPA) (Scheme 1) is a compound containing phosphorus and nitrogen elements in its phenophosphazine ring. Compared with the flame retardant DOPO, containing only phosphorus, the unique combination of phosphorus and nitrogen elements in the phenophosphazine ring may endow DPPA with special flame retardation. In addition, a DPPA molecule including two reaction centres of P–H and N–H can be used for curing epoxy resins. Schaefer et al.22 explored its flame retardant ability in epoxy resins. However its curing capability and flame retardant mechanism have never been reported.
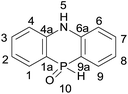 |
| Scheme 1 Molecular structure of DPPA. | |
DPPA served as both a co-curing agent of 4,4′-diaminodiphenylmethane and a flame retardant for DGEBA epoxy resin in this paper. The curing behaviour, flame-retardant properties and mechanism of the cured epoxy resin were investigated.
2. Experimental
2.1 Materials
Diphenylamine and 4,4′-diaminodiphenylmethane (DDM) were purchased from Aladdin Reagents (Shanghai) Co., Ltd. Epoxy resin (DGEBA, trade name: CYD128, epoxy value: 0.51) was supplied by SINOPEC Assets Management Corporation Baling Petrochemical Branch. Phosphorus trichloride was provided by Sinopharm Chemical Reagent Co., Ltd. Ethanol, glacial acetic acid, and dichloromethane were obtained from Guangzhou Chemical Reagent Factory.
2.2 Synthesis and characterization of DPPA
The synthesis of DPPA was carried out according to the reported procedure.23,24 A mixture of 0.30 mol diphenylamine and 0.32 mol PCl3 was stirred at room temperature for 30 min. The reaction mixture was then slowly heated to 210 °C and kept for another 7 h. The reaction vessel was cooled to room temperature and flushed with N2 to remove HCl and residual PCl3. The obtained brown solid was powdered and then cautiously added to about 100 ml boiling water. After stirring for 2 h, the resultant brown solid was dissolved in hot ethanol and filtered to remove the insoluble components. The filtrate was treated with 10% aqueous NaOH to precipitate a yellow substance and then the ethanol was evaporated to get a crude product. After being washed three times with water, the product DPPA was recrystallized from glacial acetic acid and vacuum-dried at 70 °C for 24 h.
1H NMR (400 MHz, DMSO-d6) δ (ppm): 10.42 (s, 1H, N–H), 9.18 and 8.83 (d, 1H, split P–H), 7.84–7.12 (m, 8H, Ar-H).
13C NMR (400 MHz, DMSO-d6) δ (ppm): 142.55 (C4a), 142.51 (C6a), 133.74 (C1, C9), 132.56 (C3), 132.49 (C7), 120.96 (C1a), 120.85 (C9a), 117.04 (C4), 116.98 (C6), 111.39 (C2), 110.41 (C8).
31P NMR (400 MHz, DMSO-d6) δ (ppm): −9.48.
HRESI-MS: m/z = 216.0573 (M + 1)+, C12H11NOP (anal. calcd for C12H10NOP: 215.05).
2.3 Preparation of the cured epoxy resins
Taking the active proton number in DPPA and DDM into consideration, the curing agents and DGEBA were mixed in a 1
:
1 equivalent ratio. The cured epoxy resin was obtained via the following thermal curing process. At first, DPPA was added to DGEBA by mechanical stirring under N2. The reaction mixture was stirred for 1 h at 160 °C to form a homogenous liquid. After cooling to 80 °C, DDM was added and stirred until dissolved completely. Then, the resin was vacuum-degassed in a mold and sequentially cured at 80 °C for 2 h, 110 °C for 1 h, 150 °C for 2 h, 180 °C for 2 h and 200 °C for 2 h. Finally, the sample was allowed to cool slowly to room temperature. A series of flame-retarding epoxy resins with 0.5 wt%, 1.0 wt%, 1.5 wt%, 2.0 wt%, 2.5 wt% and 3.0 wt% was prepared. The detailed formulation is listed in Table 1.
Table 1 Detailed formulation of the flame-retarding epoxy resins
Samples |
DPPA (wt%) |
DGEBA (wt%) |
DDM (wt%) |
P (wt%) |
N (wt%) |
EP-0 |
0 |
79.82 |
20.18 |
0 |
2.85 |
EP-0.5 |
0.5 |
79.61 |
19.89 |
0.07 |
2.84 |
EP-1.0 |
1.0 |
79.39 |
19.61 |
0.14 |
2.84 |
EP-1.5 |
1.5 |
79.18 |
19.32 |
0.22 |
2.83 |
EP-2.0 |
2.0 |
78.96 |
19.04 |
0.29 |
2.82 |
EP-2.5 |
2.5 |
78.75 |
18.75 |
0.36 |
2.81 |
EP-3.0 |
3.0 |
78.53 |
18.47 |
0.43 |
2.81 |
2.4 Characterization and measurement
1H, 13C and 31P NMR spectra were obtained using a Bruker DRX 400 spectrometer, and samples were prepared in deuterated dimethyl sulfoxide solution with tetramethylsilane as an internal standard. High resolution electrospray ionization mass spectrometry (HRESI-MS) was measured using a Bruker micro TOF-Q II mass spectrometer.
The non-isothermal curing kinetics and glass transition temperature (Tg) were measured using differential scanning calorimeter (DSC) analysis with a Netzsch DSC 200F3A01 under nitrogen. The mid-point between onset and offset of the inflectional tangent on the measured curve was defined as Tg.
Dynamic mechanical analysis (DMA) was performed using a Netzsch DMA 242C with a heating rate of 3 °C min−1 and a frequency of 1 Hz under air. The sample size was 40 mm × 10 mm × 4 mm. The test was performed in the bending mode with an amplitude of 30 μm.
Thermogravimetric analysis (TGA) was carried out using a Netzsch 2209F1 thermogravimetric analyzer with a temperature range of 25–700 °C and a heating rate of 10 °C min−1 under nitrogen and air. To detect gas species from the thermo-degradation of the cured epoxy resins, TGA-FTIR was performed using a Bruker STA449C/3MFC/G thermogravimetry-Fourier transform infrared spectrometer. FT-IR spectra were recorded using a Netzsch 870 FTIR Spectra-photometer with the samples in KBr pellet form.
The LOI test was conducted using an oxygen index instrument (Fire Testing Technology Co. Ltd, UK) with sheet dimensions of 150 × 6.5 × 3.2 mm3 according to ASTM D2863-97. A vertical burning test was carried out on a UL 94 flammability meter (Fire Testing Technology Co. Ltd, UK) with sheet dimensions of 130 × 13 × 3.2 mm3 according to ANSL UL 94-1985.
The forced combustion behaviour was measured using a FTT, UK cone calorimeter according to ISO5660 under an external heat flux of 35 kW m−2. The sample for the cone calorimetric analysis was 100 × 100 × 4 mm3.
Scanning electron microscopy (SEM) experiments were performed using a NOVA NANOSEM 430. The sample for SEM was made electrically conductive by being sputter-coated with a thin layer of gold–palladium alloy. Element analysis of the char residue was investigated using a Shimadzu electron probe microanalysis (EPMA) 1600 with an EDAX Genesis energy-dispersive X-ray spectroscopy analyzer (EDS).
3. Results and discussion
3.1 Reactivity of DPPA
The DPPA molecule has two reaction centres: P–H and N–H. The big p–π conjugation from the nitrogen atom and two benzene rings may increase the stability of the N–H bond and reduce its reaction activity to some degree. In order to determine the reaction activity order of P–H and N–H with the epoxy group, a mixture of 1 mol DPPA and 2 mol DGEBA was stirred at 160 °C for an hour, then at 185 °C for 4 hours under N2. The reaction mixture was sampled at different times for 1H NMR measurement and the results are shown in Fig. 1. After reaction for 10 min at 160 °C, both signals of P–H (8.83 and 9.18 ppm) and N–H (10.42 ppm) can be seen. After reaction for 60 min at 160 °C, the signal corresponding to P–H disappears and the signal of N–H at 10.42 ppm moves to 10.13 ppm. At last, the signal of N–H disappears after reaction for an additional 240 min at 185 °C. The results indicate that both P–H and N–H in the DPPA molecule can react with the epoxy group while the reactivity of P–H is higher than that of N–H.
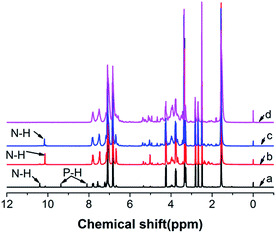 |
| Fig. 1 1H NMR spectra of the reaction mixture as the reaction proceeds (a: 160 °C, 10 min; b: 160 °C, 60 min; c: 185 °C, 60 min; d: 185 °C, 240 min). | |
3.2 Curing behaviour
Fig. 2 presents DSC thermograms of EP-0 and EP-3.0 at different heating rates. Both systems show a single exothermic peak corresponding to the ring-opening reaction of DGEBA. The onset curing temperature (To), end curing temperature (Tf), exothermic peak temperature (Tp), curing heat (ΔH) and activation energy (Ea) calculated by Kissinger’s method25 are listed in Table 2. It is found that EP-3.0 has a lower To and Tp than EP-0 under the same curing conditions. Compared with EP-0, To and Tp of EP-3.0 decrease by 10.6 and 8.8 °C, respectively, under a heating rate of 10 °C min−1. In addition, a smaller ΔH value for EP-3.0 can be observed, indicating that less heat is released during the curing reaction for EP-3.0. But the Ea values for EP-3.0 and EP-0 are quite close. The results indicate that the incorporation of DPPA can decrease the curing reaction temperature and accelerate the curing reaction of DDM with DGEBA to some degree.
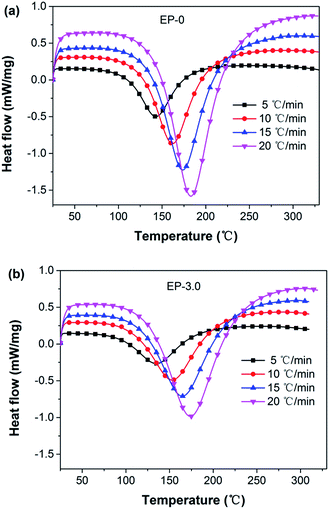 |
| Fig. 2 DSC thermograms of EP-0 (a) and EP-3.0 (b) at different heating rates. | |
Table 2 Curing parameters from the DSC thermograms of EP-0 and EP-3.0
Samples |
β (°C min−1) |
To (°C) |
Tp (°C) |
Tf (°C) |
ΔH (J g−1) |
Ea (kJ mol−1) |
EP-3.0 |
5 |
44.3 |
134.8 |
245.6 |
−326.1 |
46.8 |
10 |
54.9 |
153.1 |
270.6 |
−328.9 |
15 |
67.4 |
164.6 |
296.0 |
−319.3 |
20 |
73.3 |
174.0 |
301.7 |
−332.9 |
EP-0 |
5 |
52.0 |
142.9 |
231.4 |
−398.7 |
47.5 |
10 |
65.5 |
161.9 |
264.9 |
−385.2 |
15 |
74.1 |
173.7 |
285.3 |
−396.9 |
20 |
87.8 |
183.0 |
300.1 |
−406.0 |
3.3 Flammability of cured epoxy resins
3.3.1 LOI and UL-94 analysis. The improvement due to DPPA on the LOI value and UL-94 rating of the epoxy resins is presented in Table 3. EP-0 is highly flammable with a low LOI value (24.1%) and receives no rating in the UL-94 test. The LOI values increase significantly from 24.1% to 34.2% with increasing DPPA content from 0 to 3 wt%. It is notable that only 2.5 wt% DPPA makes the epoxy resin achieve a UL-94 V-0 rating, where the content of phosphorus element is as low as 0.36%. The results indicate that DPPA imparts excellent flame retardancy to DGEBA epoxy resin.
Table 3 LOI and UL-94 results of epoxy resins with different contents of DPPA
Samples |
LOI (vol%) |
UL-94 |
t1 + t2 (s) |
Drips |
Rating |
EP-0 |
24.1 |
Lasting burning |
Yes |
No rating |
EP-0.5 |
28.3 |
53.2 ± 4.2 |
No |
No rating |
EP-1.0 |
29.4 |
44.4 ± 3.7 |
No |
No rating |
EP-1.5 |
31.4 |
24.4 ± 2.9 |
No |
V-1 |
EP-2.0 |
31.9 |
14.7 ± 3.6 |
No |
V-1 |
EP-2.5 |
33.6 |
2.7 ± 2.0 |
No |
V-0 |
EP-3.0 |
34.2 |
2.6 ± 1.9 |
No |
V-0 |
The blowing-out effect26,27 is observed for all cured epoxy resins containing DPPA during the UL-94 test, while no blowing-out effect is observed for EP-0. After the first ignition, EP-0 burns rapidly, and the fire spreads quickly from the ignited end. In addition, flaming drips during burning occur. However, for EP-3.0 samples, strong airflows are emitted in the initial several seconds after ignition, leading to the flame being blown away from the ignited end. When the igniter is removed, the flame is rapidly blown out by the airflows from the ignited end. This is the so-called blowing-out effect. The airflows are caused by the jet of pyrolytic gases from the char layer. Video screenshots of EP-0 and EP-3.0 during the UL-94 test are shown in Fig. 3 and 4, respectively. Although the blowing-out effect for the epoxy resin with 5 wt% DOPO was also observed, it took a longer time to occur. In addition, 5 wt% DOPO did not help the epoxy resin to achieve the V-0 rating.28 Therefore the flame retardant efficiency of DPPA on epoxy resins is much higher than that of DOPO. It may be deduced that the unique combination of phosphorus and nitrogen atoms in the phenophosphazine ring indeed plays a key role in upgrading the flame-retarding efficiency of DPPA.
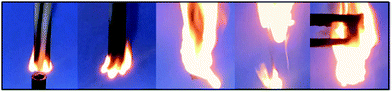 |
| Fig. 3 Video screenshots of the flame application in the first 10 s of the UL-94 test for EP-0. | |
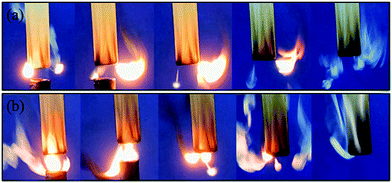 |
| Fig. 4 Video screenshots of the flame application in the first 10 s (a) and second 10 s (b) of the UL-94 test for EP-3.0. | |
3.3.2 Cone calorimeter analysis. Cone calorimeter analysis is a useful method to practically analyze the combustion behaviour of materials due to the continuity of thermal irradiance and a steady ignition source on a moving or dripping sample. HRR and THR curves of EP-0, EP-0.5, EP-1.5 and EP-2.5 are presented in Fig. 5. Key combustion parameters, including the peak of heat release rate (PHRR), mean HRR, total heat release (THR) and mean mass loss rate (MMLR) are summarized in Table 4. The PHRR value decreases from 877 to 568 kW m−2 as the DPPA content increases from 0 to 2.5 wt%. The THR value is greatly reduced from 181 to 129 MJ m−2 as the DPPA content increases, and the THR value of EP-2.5 is reduced by 29% compared to that of EP-0. Furthermore, the residual weight dramatically increases as the content of DPPA increases and that of EP-2.5 is a 75% increase over that of EP-0. Additionally, MHRR and MMLR values of the epoxy resins containing DPPA are lower than those of EP-0. All results suggest that the incorporation of DPPA can effectively suppress the combustion of epoxy resins.
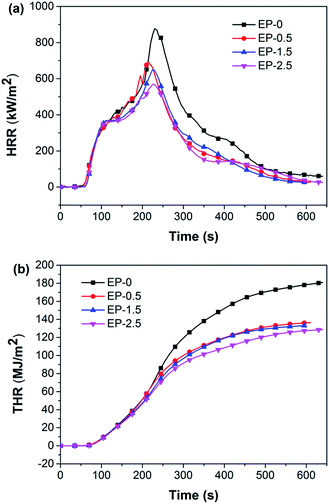 |
| Fig. 5 HRR (a) and THR (b) curves of the epoxy resins with different DPPA contents. | |
Table 4 Cone calorimeter data for the epoxy resins with different contents of DPPA
Samples |
EP-0 |
EP-0.5 |
EP-1.5 |
EP-2.5 |
PHRR (kW m−2) |
877 |
692 |
652 |
568 |
MHRR (kW m−2) |
306 |
244 |
246 |
220 |
THR (MJ m−2) |
181 |
136 |
133 |
129 |
MMLR (g s−1) |
0.0964 |
0.0920 |
0.0933 |
0.0840 |
Residual weight (%) |
12.1 |
16.4 |
18.7 |
21.2 |
3.4 Thermal analysis
The glass transition temperatures (Tg) of EP-0 and EP-2.5 were evaluated from DSC and DMA thermograms (Fig. 6). The Tg of EP-2.5 is 159.4 °C (from DSC) and 160.0 °C (from DMA), and only 3.8 °C and 6.3 °C lower than 163.2 °C (from DSC) and 166.3 °C (from DMA) of EP-0. It is well-known that Tg is ascribed to the segmental motion of polymeric networks. Large volume phenophosphazine rings give a great steric hindrance to the segmental motion of polymeric networks, which benefits the escalation of Tg.29 According to the rubber theory of elasticity and the calculation method described in the literature,30 the calculated crosslinking degree is 4780 mol m−3 for EP-2.5, slightly lower than 4875 mol m−3 for EP-0. It suggests that a small decrease in Tg may be attributed to the decline in the crosslinking degree accompanied by the incorporation of DPPA.
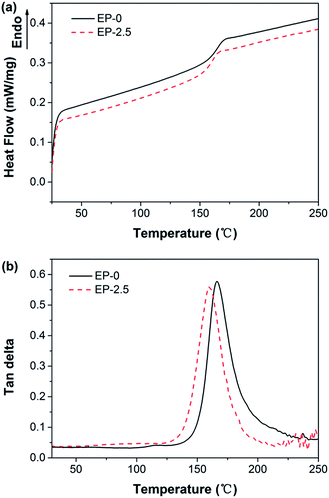 |
| Fig. 6 DSC (a) and DMA (b) thermograms of EP-0 and EP-2.5. | |
Fig. 7 and 8 show the TGA thermograms of EP-0 and EP-2.5 under both N2 and air, respectively. The onset degradation temperatures (T5%), 10% and 50% weight loss temperatures (T10%, T50%), char yields at 650 °C (Yc) and maximum weight loss rates (Rmax) are summarized in Table 5. It is found that both EP-0 and EP-2.5 exhibit one-stage thermal degradation under N2. The T5% and Yc of EP-0 are 367.4 °C and 15.8%, respectively. The incorporation of DPPA makes the epoxy resin quickly degrade at the early stage. EP-2.5 has a lower T5%, T10% and T50%. However, its degradation rate decreases above 378 °C and its maximum weight loss rate is lower than that of EP-0. As a result, Yc of EP-2.5 goes up to 22.3%.
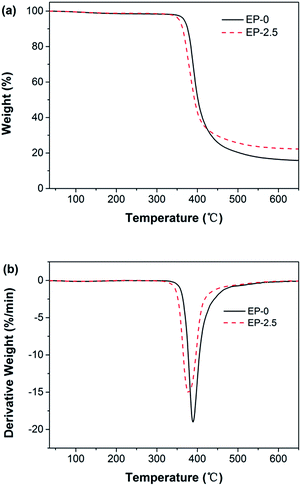 |
| Fig. 7 TGA (a) and DTG (b) curves of EP-0 and EP-2.5 under N2. | |
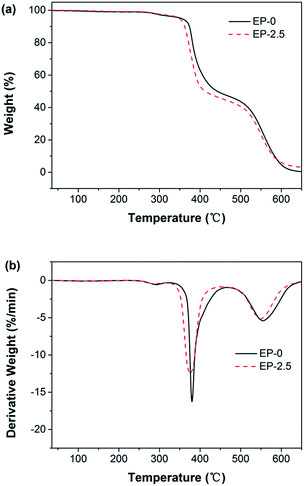 |
| Fig. 8 TGA (a) and DTG (b) curves of EP-0 and EP-2.5 under air. | |
Table 5 TGA and DTG parameters of epoxy resins with different contents of DPPA under N2 and air
Samples |
N2 |
Air |
EP-0 |
EP-2.5 |
EP-0 |
EP-2.5 |
T5% (°C) |
367.4 |
355.4 |
353.6 |
349.3 |
T10% (°C) |
375.9 |
363.7 |
373.8 |
362.2 |
T50% (°C) |
401.6 |
393.0 |
442.6 |
412.9 |
Rmax (% min−1) |
19.0 |
15.1 |
16.3, 5.4 |
12.5, 5.2 |
Yc (%) |
15.8 |
22.3 |
0.46 |
3.1 |
The thermal degradation processes of both EP-0 and EP-2.5 under air clearly exhibit two stages, different from those under N2. Compared with EP-0, the degradation of EP-2.5 occurs earlier, meanwhile there exists a lower T5%, T10% and T50%. Yc of EP-2.5 is 3.1 wt%, higher than 0.46 wt% of EP-0. EP-2.5 degrades more quickly than EP-0 below 376 °C, and its first maximum weight loss rate is 23% lower than that of EP-0. A similar phenomenon is observed under N2. The earlier degradation of EP-2.5 under both N2 and air indicates that DPPA can promote the degradation of the epoxy resin matrix. At the same time, a slower degradation in the late stage and a higher char yield of EP-2.5 demonstrate that early degradation is advantageous for the formation of a stable char barrier at a higher temperature, which is in accordance with the mechanism of improving flame retardancy in the reported studies.11–14
3.5 TGA-FTIR analysis
The pyrolytic gas species from EP-0 and EP-2.5 under air were investigated using TGA-FTIR in order to understand the flame inhibition mechanism. FTIR spectra of volatile gases evolved from EP-0 and EP-2.5 at 380 °C, 400 °C and 450 °C are shown in Fig. 9. The major gases detected from the decomposition of EP are phenol derivatives or water (3650 cm−1), compounds containing aromatic rings (3046, 1605, 1507, and 1341 cm−1), compounds containing alkane (2970, 2932, 2880, and 2869 cm−1), ester or ether components (1766, 1256, and 1178 cm−1), CO2 (2383 and 2302 cm−1), and CO (2180 and 2108 cm−1).31 Although the major gases from EP-2.5 are similar to those from EP-0, some changes can be observed with the addition of DPPA. The new broad peak around 1032 cm−1 and a much higher peak at 889 cm−1 from EP-2.5 at 380 °C suggest the release of compounds containing phosphorus,32 which may act in gas-phase flame inhibition.33,34 In addition, the peak intensity of the pyrolytic products from EP-2.5 is much larger than that from EP-0 at 380 °C, especially for hydrocarbons and aromatic compounds. However, the intensity of the peaks of C
O (1766 cm−1), CO2 (2383 and 2302 cm−1) and CO (2180 and 2108 cm−1) from EP-2.5 is smaller than those from EP-0 at 380 and 400 °C, indicating that the degradation process of the epoxy resin matrix is changed by the incorporation of DPPA. Along with the rise of temperature, the difference in the FTIR spectra between EP-2.5 and EP-0 reduces. The results indicate that DPPA obviously promotes the thermo-oxidative degradation of the epoxy resin at the early stage and the flame inhibition action of phosphorus-containing products in the gas phase happens to some extent.
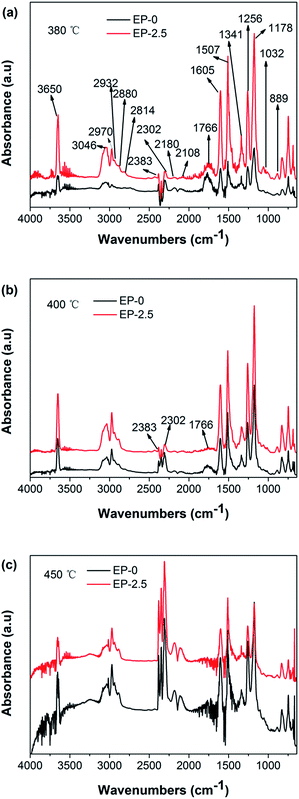 |
| Fig. 9 FTIR spectra of pyrolytic gas products for EP-0 and EP-2.5 at (a) 380 °C, (b) 400 °C, (c) 450 °C. | |
3.6 Char layer analysis
3.6.1 Digital images. Usually, the residue formed during combustion can give some important information regarding the inherent flammability characteristics of a polymeric material, which can reflect the flame-retarding mechanism in the condensed phase to some degree. Digital photos of residues for EP-0 and EP-2.5 after the cone calorimeter test are presented in Fig. 10. There is a little residue left for EP-0 and its char layer is very loose and fragile. However, a distinctly intumescent charring occurs and the char layer is compact and rigid for EP-2.5. These phenomena suggest that DPPA can catalyze the formation of an intumescent char layer in the epoxy resin matrix .
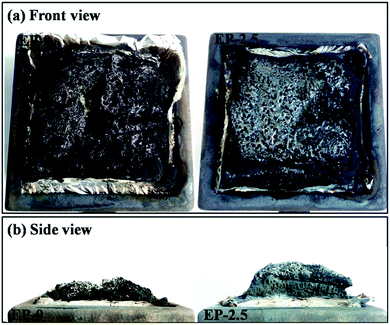 |
| Fig. 10 Digital photos of the residues for EP-0 and EP-2.5. | |
3.6.2 Elemental composition. In order to further understand why epoxy resins with DPPA give rise to the unique char structure, elemental composition of the residues left after the cone calorimeter test is investigated using EPMA-EDS. The content of C, O, P, and N in the exterior and interior char layers for EP-0, EP-0.5, EP-1.5 and EP-2.5 are listed in Table 6. It is found that for epoxy resins containing DPPA, the content of P element in the exterior char layer is much higher than that in the interior char layer, which indicates an accumulation of phosphorus on the surface of the char layer. P element in the phenophosphazine ring is converted to phosphoric acid during burning, which may esterify and dehydrate the pyrolyzing epoxy resin and form simultaneously a phosphorus-rich carbonaceous layer.
Table 6 Elemental composition (%) of the residues after the cone calorimeter test
Samples |
EP-0 |
EP-0.5 |
EP-1.5 |
EP-2.5 |
Exterior |
C |
93.49 |
92.32 |
93.02 |
89.17 |
O |
4.31 |
5.04 |
4.84 |
6.27 |
N |
2.19 |
2.30 |
1.24 |
1.73 |
P |
0 |
0.34 |
0.90 |
2.83 |
Interior |
C |
91.12 |
90.76 |
92.00 |
93.49 |
O |
5.96 |
6.76 |
5.96 |
4.07 |
N |
2.93 |
2.26 |
1.63 |
1.79 |
P |
0 |
0.22 |
0.40 |
0.64 |
3.6.3 SEM photographs. The marked difference between EP-2.5 and EP-0 in both the exterior and interior structure of the char layers can be seen in Fig. 11 and 12, SEM images of the char layer after the cone calorimeter test. For EP-0, both the exterior and interior char layers are very loose, fragile, and there are lots of large porous holes distributed on the surface. EP-2.5 presents a glassy exterior char layer without any bubbles broken along the surface while some integrated closed honeycomb pores and closed bubbles can be seen in the interior char layer. In addition, the SEM image of the cross-section char layer for EP-2.5 is shown in Fig. 13 and a typical honeycomb-like intumescent structure can be observed. This microstructure of the char layers indicates the occurrence of intumescent flame retardation for EP-2.5.
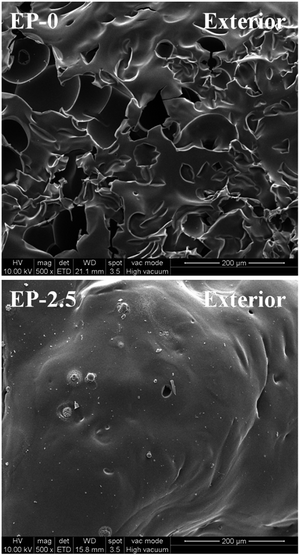 |
| Fig. 11 SEM images of the exterior char layers for EP-0 and EP-2.5. | |
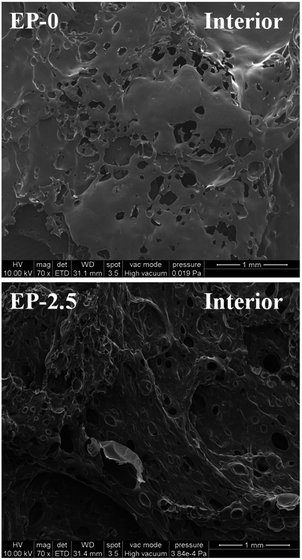 |
| Fig. 12 SEM images of the interior char layers for EP-0 and EP-2.5. | |
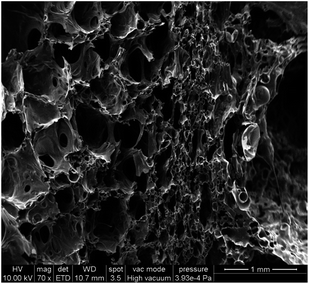 |
| Fig. 13 SEM image of the cross-section char layer for EP-2.5. | |
In order to further understand the relationship between the flame retardant mechanism and the microstructure of the residue char, the end of the EP-2.5 sample ignited via the vertical burning test was also subjected to SEM observation (Fig. 14). A rigid plate-like surface char layer with convex stomates marked by the yellow circle can be observed. Moreover, an inner cavity and a bottom char layer are observed from the fracture. It is speculated that the phosphoric acid transformed from the phenophosphazine ring induces the degradation of the epoxy resin matrix to quickly form a rigid char layer after ignition. Meanwhile, large amounts of pyrolytic gases are produced during the combustion, which cause the char layer to gradually expand. Furthermore, the flame is blown out when the pyrolytic gases penetrate through the surface char layer with increasing inner gas pressure. As a result, the convex stomate is left on the surface of char layer. The blowing-out effect plays an important role in the high flame retardancy of EP-2.5.
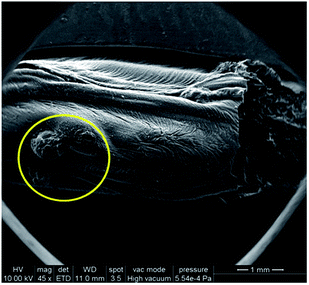 |
| Fig. 14 SEM image of the end of EP-2.5 ignited via the vertical burning test. | |
3.6.4 FTIR spectra. Fig. 15 shows the FTIR spectra of the exterior and interior chars for EP-0 and EP-2.5 after the cone calorimeter test. It is obvious that the spectra of the two exterior chars are very different from each other. The intensified sharp peak at 1577 cm−1 and the appearance of new peaks at 1513, 1445, 1279 cm−1 for EP-2.5 indicate that some new aromatics and polyaromatics35 are formed during combustion. The differences also exist in the FTIR spectra of the two interior chars as shown in Fig. 15b. The stronger and sharper peak at 1575 cm−1 indicates greater amounts of aromatic compounds in EP-2.5 char, compared with EP-0 char. The peaks at 1012 and 869 cm−1 can be discerned in the EP-2.5 residue, suggesting the presence of P–O–P, P–O–Ph and P–O–C. It is speculated that the decomposition products from the phenophosphazine ring and the epoxy resins react with each other to form cross-linked phosphorocarbonaceous and phosphorooxidative char with highly carbonized aromatic networks. A high flame retardancy for EP-2.5 is consequently believed to correlate with the retention and structure of phosphorus in the char from the phenophosphazine ring.
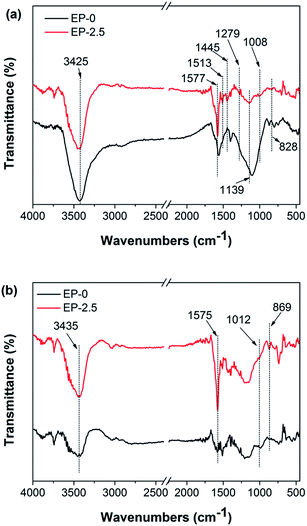 |
| Fig. 15 FTIR spectra of the exterior char (a) and the interior char (b) for EP-0 and EP-2.5. | |
4. Conclusions
DPPA is an effective intumescent flame retardant for DGEBA epoxy resin because of its unique phenophosphazine ring. The epoxy resin could achieve a V-0 rating in the UL-94 test with a LOI of 33.6% at only 2.5 wt% DPPA. The PHRR decreases from 877 kW m−2 in EP-0 to 568 kW m−2 in EP-2.5. DPPA can promote the degradation of the epoxy resin matrix to form a stable char barrier at a higher temperature. The flame-retardant strategy of DPPA combines the intumescent charring and blowing-out effect, which are evaluated by an in-depth characterization of the charred residue and evolved gas, and is different from the flame retardant mechanism of traditional DOPO. DPPA provides the potential ability to upgrade the flame retardancy of epoxy resins at low loading.
Acknowledgements
We gratefully acknowledge support from the Joint Fund of NSFC with Guangdong Provincial Government (U1201243) and the project for scientific research conditions of Guangzhou (No. 2012224-7).
Notes and references
- L. Xiao, D. Sun, T. Niu and Y. Yao, High Perform. Polym., 2014, 26, 52–59 CrossRef PubMed.
- S. X. Cai and C. H. Lin, J. Polym. Sci., Part A: Polym. Chem., 2005, 43, 2862–2873 CrossRef CAS PubMed.
- G. R. Xu, M. J. Xu and B. Li, Polym. Degrad. Stab., 2014, 109, 240–248 CrossRef CAS PubMed.
- X. Qian, L. Song, B. Yuan, B. Yu, Y. Shi, Y. Hu and R. K. K. Yuen, Mater. Chem. Phys., 2014, 143, 1243–1252 CrossRef CAS PubMed.
- Y. Lin, J. Sun, Q. Zhao and Q. Zhou, Polym.-Plast. Technol. Eng., 2012, 51, 896–903 CrossRef CAS PubMed.
- G. H. Hsiue, Y. L. Liu and J. Tsiao, J. Appl. Polym. Sci., 2000, 78, 1–7 CrossRef CAS.
- J. Y. Shieh and C. S. Wang, J. Appl. Polym. Sci., 2000, 78, 1636–1644 CrossRef CAS.
- U. Braun, A. I. Balabanovich, B. Schartel, U. Knoll, J. Artner, M. Ciesielski, M. Doering, R. Perez, J. K. W. Sandler, V. Altstaedt, T. Hoffmann and D. Pospiech, Polymer, 2006, 47, 8495–8508 CrossRef CAS PubMed.
- Y. Q. Xiong, X. Y. Zhang, J. Liu, M. M. Li, F. Guo, X. N. Xia and W. J. Xu, J. Appl. Polym. Sci., 2012, 125, 1219–1225 CrossRef CAS PubMed.
- C. H. Lin, C. K. Hsu, M. W. Wang, S. A. Dai and T. Y. Juang, J. Polym. Sci., Part A: Polym. Chem., 2014, 52, 390–400 CrossRef CAS PubMed.
- G. Ribera, L. A. Mercado, M. Galia and V. Cadiz, J. Appl. Polym. Sci., 2006, 99, 1367–1373 CrossRef CAS PubMed.
- H. Liu, K. Xu, H. Ai, L. Zhang and M. Chen, Polym. Adv. Technol., 2009, 20, 753–758 CrossRef CAS PubMed.
- T. Mariappan, Z. You, J. Hao and C. A. Wilkie, Eur. Polym. J., 2013, 49, 3171–3180 CrossRef CAS PubMed.
- B. Liang, J. Cao, X. Hong and C. Wang, J. Appl. Polym. Sci., 2013, 128, 2759–2765 CrossRef CAS PubMed.
- G. You, Z. Cheng, H. Peng and H. He, J. Appl. Polym. Sci., 2015, 132, 41859 CrossRef PubMed.
- M. J. Chen, Z. B. Shao, X. L. Wang, L. Chen and Y. Z. Wang, Ind. Eng. Chem. Res., 2012, 51, 9769–9776 CrossRef CAS.
- Z. Bai, L. Song, Y. Hu, X. Gong and R. K. K. Yuen, J. Anal. Appl. Pyrolysis, 2014, 105, 317–326 CrossRef CAS PubMed.
- Q. Tai, Y. Hu, R. K. K. Yuen, L. Song and H. Lu, J. Mater. Chem., 2011, 21, 6621–6627 RSC.
- Q. Lv, J. Q. Huang, M. J. Chen, J. Zhao, Y. Tan, L. Chen and Y. Z. Wang, Ind. Eng. Chem. Res., 2013, 52, 9397–9404 CrossRef CAS.
- Y. Xiong, Z. Jiang, Y. Xie, X. Zhang and W. Xu, J. Appl. Polym. Sci., 2013, 127, 4352–4358 CrossRef CAS PubMed.
- W. Y. Chen, Y. Z. Wang and F. C. Chang, J. Polym. Res., 2004, 11, 109–117 CrossRef CAS.
- A. Schaefer, S. Seibold, O. Walter and M. Doering, Polym. Degrad. Stab., 2008, 93, 557–560 CrossRef CAS PubMed.
- K. A. Bello, K. Shen, D. Zhao, M. Esancy and H. Freeman, Dyes Pigm., 2000, 46, 121–128 CrossRef CAS.
- Z. G. Yin, K. Jin, D. F. Zhao, Q. J. Peng and H. S. Freeman, Chem. J. Chin. Univ., 2003, 24, 1210–1215 CAS.
- C. S. Wang and C. H. Lin, Polymer, 2000, 41, 8579–8586 CrossRef CAS.
- W. Zhang, X. Li and R. Yang, Polym. Degrad. Stab., 2014, 99, 118–126 CrossRef CAS PubMed.
- W. Zhang, X. Li and R. Yang, Polym. Adv. Technol., 2013, 24, 951–961 CrossRef CAS PubMed.
- W. Zhang, X. Li, L. Li and R. Yang, Polym. Degrad. Stab., 2012, 97, 1041–1048 CrossRef CAS PubMed.
- J. Sun, X. Wang and D. Wu, ACS Appl. Mater. Interfaces, 2012, 4, 4047–4061 CAS.
- P. H. Henna and R. C. Larock, Macromol. Mater. Eng., 2007, 292, 1201–1209 CrossRef CAS PubMed.
- W. Zhang, X. Li and R. Yang, J. Appl. Polym. Sci., 2013, 130, 4119–4128 CAS.
- A. Toldy, B. Szolnoki, I. Csontos and G. Marosi, J. Appl. Polym. Sci., 2014, 131, 40105 CrossRef PubMed.
- N. M. Neisius, M. Lutz, D. Rentsch, P. Hemberger and S. Gaan, Ind. Eng. Chem. Res., 2014, 53, 2889–2896 CrossRef CAS.
- M. Xu, W. Zhao and B. Li, J. Appl. Polym. Sci., 2014, 131, 41159 Search PubMed.
- H. Liu, X. Wang and D. Wu, Polym. Degrad. Stab., 2014, 103, 96–112 CrossRef CAS PubMed.
|
This journal is © The Royal Society of Chemistry 2015 |
Click here to see how this site uses Cookies. View our privacy policy here.