DOI:
10.1039/C5RA10952C
(Paper)
RSC Adv., 2015,
5, 69573-69582
Polymer nanocomposites using click chemistry: novel materials for hydrogen peroxide vapor sensors†
Received
9th June 2015
, Accepted 30th July 2015
First published on 30th July 2015
Abstract
Herein, we report the synthesis of nanocomposites (NCs) prepared by azide-functionalized polystyrene (Az-f-PS) coupled with alkyne-functionalized nanographite platelets (Alk-f-NGPs) by using copper(I) catalyzed azide–alkyne click chemistry. Linear polystyrene (PS) was functionalized with an azide moiety after bromine-termination of PS through atom transfer radical polymerization (ATRP) using CuBr/2,2′-bipyridyl as a catalyst. The nanographite platelets (NGPs) were formed from graphite flakes through intercalation followed by functionalization with an alkyne moiety. The structure and micromorphology of the prepared NCs were confirmed by NMR, FTIR, Raman, XRD, TGA, SEM, TEM and AFM techniques. The electrical properties of the click nanocomposites (C-NCs) were investigated and the C-NCs were found to posses the resistance of 1.08 × 108 Ω at 1 wt% NGPs loading. The C-NCs with fast response (∼3 s), rapid recovery (∼60 s) and excellent repeatability at room temperature provide novel materials for chemiresistive sensors for detection of H2O2 vapors.
1 Introduction
Polymer materials are widely used in industry due to their ease of production, lightweight and often ductile nature.1 However, the disadvantages such as low modulus and strength compared to metals and ceramics limit their applications in various fields. In this context, a very effective approach to improve electrical and mechanical properties is to add fibres, whiskers, platelets or particles as reinforcements to the polymer matrix.2 A variety of fillers have been considered over the years which include metals, silica, clay, and carbon-based fillers as reinforcements.3 Among these, a range of carbon-based fillers such as carbon black, fullerene, carbon nanotubes (CNTs), and graphene have gained prominence.4–6
In recent years, there has been increasing interest in the field of polymer nanocomposites (NCs) which have been extensively studied since the 1990s and reported to be the materials of 21st century. NCs are a special class of materials having unique properties and wide application in diverse areas.7–9 NCs possess nano dimension, unique designs and property combinations that are not found in conventional composites. Innumerable applications of these polymer NCs in nanoelectronic devices, optoelectrical devices, molecular electronics, sensor, field emission devices and many others have been extensively reported.2,4,10 At present, NCs employing carbon-based reinforcement materials are dominated by carbon nanotubes but the intrinsic bundling of carbon nanotubes, their intrinsic impurities from catalysts and their high cost have been hampering their application. Hence, graphene and NGPs provide low-cost alternative to CNTs due to their excellent properties similar to CNTs and natural abundance of their precursor graphite.11,12 Compared to carbon nanotubes, less work has been done on NGPs although they have in-plane electrical, thermal and mechanical properties.13
The main challenge in the fabrication of these NCs lies in the establishment of homogeneous dispersion of NGPs in polymer matrix because the NGPs have a strong tendency to aggregate.14 NGPs usually form stabilized bundles due to van der Waals interactions and therefore are extremely difficult to disperse and align in a polymer matrix.15 Many methods have been developed so far to assist dispersion of filler within the polymer matrix such as high-power ultrasonic mixers, surfactants,16 melt mixing,17 solution mixing,18 in situ polymerization,19,20 grafting to nanofillers21 and grafting to polymer.22 However, these methods for covalent immobilization suffer from certain drawbacks like low efficiency, less control on molecular weight of polymer and reaction condition.23
Recently, click chemistry, using Cu(I)-catalyzed (3 + 2) Huisgen dipolar cycloaddition has received enormous attention in polymer and material science. In particular the functionalization of polymer matrix and fillers using click chemistry is the recent and potential technique to achieve excellent filler dispersion.12 It was postulated that the use of click chemistry has been successfully employed in the fabrication of NCs having high reactivity (in presence of all functional groups), reliability (not affected by O2, H2O, etc.) and selectivity (affording 1,4-regioselective 1,2,3-triazoles) by Shengtong Sun et al.24 ‘Click’ chemistry25–27 is predominately based around the Huisgen cycloaddition of azide moiety with alkyne moiety to the surface of matrix as well as filler.28–30 In contrast to previously reported methods, click chemistry offers high yielding formations at low temperatures, more control on reaction conditions, possible choice of dipoles/dipolarophiles with desired side groups and the characterization of reaction intermediates. Click reaction has been extensively studied in recent decades with steadily increasing application in the areas of medicinal, polymer, supramolecular, coordinational chemistry, chemical biology and material sciences.31,32
In the present work, polystyrene (PS) was functionalized using ATRP technique and NCs were prepared by click reaction. The combination of surface-initiated ATRP and click reaction provides a novel, well controlled and efficient process of the synthesis of a wide variety of new materials with potential uses.33 To our best knowledge this is the first time click reaction between azide-functionalized polystyrene (Az-f-PS) and alkyne-functionalized NGP (Alk-f-NGPs) was used to prepare NCs to find its application in chemiresistive sensor for detecting H2O2 vapor.
Chemiresistive sensor for detection of target gases has gained great deal of attention in research due to its increasing demand for monitoring of environmental pollution.34,35 Standard methods of gas detection are limited to solid and liquid samples. However, the issues related to available conventional gas sensors are their bulky architectures, high price, high power consumption, non-portability and breakdown voltage which is inefficient and risky in operation. Therefore, there is an urgent need for rapid vapor phase detection with a simple electronic sensor.36 Herein, we report the synthesis of the C-NCs through click chemistry which can be used as chemiresistive sensors for the detection of H2O2 vapors with fast response and rapid recovery at room temperature. So far there has been no report on the use of NCs prepared by the click reaction for chemiresistive sensing and the work reported may open a promising area of exploration among gas sensors.
2 Experimental
2.1 Materials and characterization
Styrene (chemically pure) was purified by 5% sodium hydroxide aqueous solution followed by washing with deionized water and dried with anhydrous sodium sulphate and finally distilled under vaccum. The natural graphite flakes (from Asbury carbons Inc.) were used for preparing nano graphite. Chemically pure concentrated sulfuric and nitric acids were used as chemical oxidizers to prepare expanded graphite. Propargyl bromide, tin(II) chloride dihydrate, isoamyl nitrite, 2,2′-bipyridyl, copper(I) bromide, sodium azide and bromotris(triphenylphosphine)copper(I) were purchased from Sigma-Aldrich, Inc. (UK) and used as received. All reagents and solvents of analytical grade were used as received. All experiments for polymerization reaction were conducted under purified nitrogen by use of standard Schlenk flask.
A 500 MHz Nuclear Magnetic Resonance (NMR) Bruker Avance III spectrometer was used for 1H NMR analysis. Spectra were recorded at 28 °C in deuterated chloroform. The gel permeation chromatography (GPC), Perkin-Elmer, Turbo matrix-40 was utilized to determine the molecular weight and poly-dispersity index (PDI). THF was used as the eluent at a flow rate of 1.0 ml min−1, and the calibration was carried out using low polydispersity polystyrene standards. Raman spectra were collected in the range from 3000 to 800 cm−1 using a Renishaw inVia Reflex spectrometer (UK) with an excitation source of 514 nm. The laser beam was focused on the sample using an optical microscope. FTIR spectra were recorded on a Nicolet 5700 instrument in the transmission mode in the wave number range of 400–4000 cm−1 at room temperature. Spectroscopic-grade KBr pellets were used for collecting the spectra with a resolution of 4 cm−1, performing 32 scans. The nature of polymer nanocomposites was confirmed by X-ray diffraction (XRD) studies carried out on a D8 Advance XRD instrument (Bruker) using Cu Kα-radiation (λ = 1.54 Å) in the scattering range (2θ) of 10–70° with a scan rate of 0.02° s−1 and a slit width of 0.1 mm. A thermogravimetric analyzer (Mettler Toledo TGA/SDTA 851e) was used to measure the thermal stability of the material under an inert atmosphere (flowing N2 gas) in the temperature range of 25–700 °C. The cell pathlength was kept constant during all the experiments. The morphology of C-NCs and NGPs were examined using scanning electron microscopy (SEM, Zeiss (MA EVO-18 Special Edition)). The SEM samples were prepared by dispersing the powder in ethanol using ultra-sonication and placing small drops of the suspension on silicon wafers and sputter-coating with gold before analysis. High-resolution transmission electron microscopy (HRTEM) was performed using a JEOL 2100F instrument. The surface topography of the functionalized polymer NC surfaces was investigated by atomic force microscopy (AFM). A multimode scanning probe microscope equipped with a Nanoscope IIIa SPM was used to capture the AFM images with a scan size 2 μm × 2 μm. Nanoscope software was used to determine the root-mean-square (RMS) roughness. The resistance and the sensor properties of the C-NCs were measured by a standard two-probe technique using a Keithley programmable current source (model 6517 B) at room temperature. For the electrical measurements, rectangular films of (2 cm × 2 cm) were prepared and ohmic contacts were made on the film using silver paste.
2.2 Functionalization of NGPs
Synthesis of functionalized nanographite platelets. NGPs were prepared according to the modified Hummer's methods reported earlier by our group.37 The natural flake graphite was first dried in a vacuum oven for 24 h at 80 °C and a mixture of concentrated sulfuric acid and fuming acid (4
:
1, v/v) was slowly added, under appropriate cooling and stirring, to the graphite flakes. After 16 h of reaction, the acid-treated natural graphite was filtered and washed thoroughly with deionized water until the pH level of the solution reached 6. After being dried at 100 °C overnight, the resulting graphite intercalation compound (GIC) was subjected to a thermal shock at 1050 °C for 15 s in a muffle furnace to form exfoliated graphite (EG). 1 g EG was mixed and saturated with 400 ml alcohol solution consisting of alcohol and distilled water with a ratio of 65
:
35 for 12 h. The mixture was subjected to ultrasonic irradiation for various times and after hours of sonication, EG particles were effectively fragmented into foliated graphite (FG). The FG dispersion was then filtered and dried at 80 °C to remove residue solvents. The as-prepared FG powder, called functionalized NGPs, was then kept in a dry dessicator for testing and further use Scheme 1.
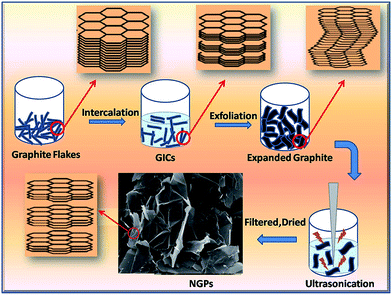 |
| Scheme 1 Schematic representation of formation of NGPs from natural graphite flakes through acid intercalation and thermal shock exposure at 1050 °C. | |
Synthesis of p-nitrophenyl propargyl ether. The solution of p-nitrophenol (55.65 g, 400 mmol) and tetrabutylammonium bromide (12.89 g, 40 mmol) was heated at 60 °C in 0.8 N sodium hydroxide solution. The propargyl bromide was added dropwise in the mixture with stirring for 24 h. By cooling the mixture to room temperature a yellow white precipitate was formed which was further washed with distilled water (3 × 100 ml). This forms crude pale yellow crystals which were dissolved in dioxane (ca. 300 ml) and were precipitated in distilled water (1000 ml) until a white powder is formed.
Synthesis of p-aminophenyl propargyl ether. At 10 °C, the solution of p-nitrophenyl propargyl ether (31.90 g, 180 mmol) in dioxane (500 ml) was added dropwise to the solution of stannous chloride dihydrate (203.00 g, 900 mmol) in concentrated HCl. After complete addition the mixture was stirred for 48 h at room temperature, until it became yellow in color. The reaction mixture is neutralized with aqueous sodium hydroxide and then by using dichloromethane (400 ml) the solution was extracted. The separated organic layer was dried over anhydrous sodium sulphate and then the solvent was evaporated in vaccum. This yields brown viscous oil which was purified under pressure to form highly viscous oil, which was then crystallized.
Synthesis of alkyne-functionalized nanographite platelets (Alk-f-NGPs). The prepared NGPs were used for alkyne functionalization without any further treatment. p-Nitrophenyl propargyl ether by reduction to aniline derivative forms p-aminophenyl propargyl ether. To the crystals of p-aminophenyl propargyl ether in a Schlenk flask under nitrogen environment isoamyl nitrite (7.81 g, 66.65 mmol, 5 equiv. mol−1 of carbon) was added slowly via syringe. After stirring for 5 h at 60 °C the paste was diluted with dimethylformamide (DMF) and filtered through PTFE (450 mm pore size) membrane. The solid was dispersed and washed with DMF by sonication followed by filtration to remove the DMF. The product was dried in a vaccum oven (55 °C) for 72 h.
2.3 Functionalization of polymer
Atom transfer radical polymerization of styrene. Atom transfer radical polymerization (ATRP) method was performed to get high yield and reactive functional groups in PS which will act as highly active binding sites for biomolecules.33 In this method a dry Schlenk flask equipped with a magnetic bar was evacuated and refilled with nitrogen three times. Then the mixture of deoxygenated styrene (10.40 g, 0.10 mol, 75 equiv.), solvent DMF, ligand 2,2′-bipyridyl (416 mg, 2.66 mmol), catalyst (CuBr, 191 mg) and initiator (ethyl 2-bromoisobutyrate, 260 mg) was degassed by freeze–pump–thaw cycles. After the reaction of 4 to 6 h the mixture was diluted with THF and then passed through a column of neutral alumina and precipitated in methanol to give bromo-terminated PS.
Synthesis of azide-functionalized polystyrene (Az-f-PS). The prepared bromo-terminated PS by ATRP was dissolved in DMF. The substitution of bromine-end with azide-end was installed on polymer with NaN3 (676 mg, 10.40 mmol, 10.00 equiv.). The complete transformation takes overnight stirring and washing with distilled water and methanol to remove NaBr and NaN3. Then the azide-modified PS was dried under vaccum at room temperature, yielding a white amorphous solid.
2.4 Click reaction: coupling of alkyne-f-NGPs to azide-f-PS by Huisgen cycloaddition
The alkyne-functionalized NGPs (5 mg) with DMF (15 ml) were dispersed through sonication. After the dispersion, azide-functionalized polystyrene (500 mg) with catalyst (PPh3)3CuBr (65 mg, 0.070 mmol) were mixed. The mixture was evacuated and refilled with nitrogen three times followed by stirring for 24 to 65 h at 100 °C. The mixture after cooling to room temperature was diluted with THF and dispersed by sonication and filtered through PTFE membrane. The product was washed with THF, methanol, aqueous ammonium hydroxide solution (28%) and CH2Cl2 and dried under vaccum for 24 h.
2.5 Preparation of sensor device and sampling system
The conductivity of the film was measured for the films prepared by the click chemistry method (C-NCs) and solution blending method38 (S-NCs) at room temperature within the potential window of −10 V to 10 V. The two point probe Keithley 6517B electrometer was used for calibration. The principle operation of the chemiresistive sensors is based on the measurement of resistance change associated with the adsorption of analyte by the NCs material.39 The sensing measurements were conducted under a static condition in a sealed chamber with a total volume of 5 l. The temperature inside the chamber remained constant at 25 °C, monitored by a mercury thermometer. The films of C-NCs were prepared from the powder sample using hydraulic press at a compression pressure of 5 tons. Two ohmic contacts were made on each end of the film using silver paste with 0.1 mm spacing between the two contacts. The prepared film was placed in a closed chamber and exposed to the vapors of hydrogen peroxide. When the electrical resistance of the composite approached its equilibrium value, the vapors of H2O2 were removed from the closed vessel with a flow of air in order to clean the sensor environment.
3 Results and discussion
The ATRP of styrene was performed resulting in bromo-functionalized-PS depicting monomodal and symmetric peak with Mn and PDI (Mw/Mn) of 2360 and 1.07 respectively as shown in figure ES1.† After the nucleophilic substitution, the GPC curve of the azide-functionalized-PS shifted to higher molecular weight with Mn and PDI of 2770 and 1.06 respectively. The Az-f-PS and Alk-f-NGPs were coupled via [3 + 2] Huisgen cycloaddition between the alkyne and azide end groups using either CuI or the organosoluble Cu(I) species, [(PPh3)3CuBr] as catalyst, as depicted in Scheme 2. The successful click coupling results in the formation of triazole links as shown in Scheme 3. Here, all reactions were performed in DMF, yielding polymer functionalized NCs by click reaction. In this study, excess PS was used in an attempt to drive the click reactions for high conversion, and this excess polymer was easily removed after each reaction by ultra-filtration and prolonged washing with THF. In addition, trace amounts of copper salts in the products were removed by washing with an aqueous ammonium hydroxide solution.
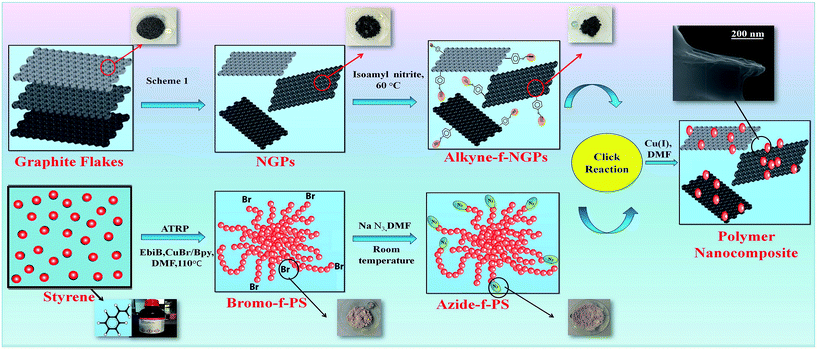 |
| Scheme 2 Schematic representation of the functionalization of NGPs with PS by click reaction. | |
 |
| Scheme 3 Scheme representing the nanocomposite (triazole conjugate) formation by click chemistry. | |
Fig. 1 represents dispersion images of NGPs, Alk-f-NGPs and C-NCs in THF. All three materials look different because of their respective structural and physicochemical properties. The samples were dispersed by sonication for 60 min in THF at 1 mg ml−1 loading and allowed to stand for 24 h. Clearly NGPs and Alk-f-NGPs are completely insoluble in THF and (all other organic solvents). Alkyne functionalization has tuned the material to exhibit higher density then its precursor (NGPs). However C-NCs exhibited high solubility forming a clear yellow colored solution without any discernible particulate materials and can remain stable for three weeks due to the functionalization through hydrophobic polymeric chain.40
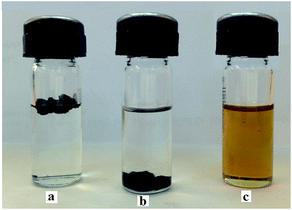 |
| Fig. 1 Dispersion of three separate samples in THF (a) NGPs (b) Alk-f-NGPs (c) C-NCs. | |
1H NMR was used to detect and quantify the polystyrene samples. A bromo-terminated PS sample was prepared using ATRP in the presence of the catalyst (CuBr) and initiator (ethyl 2-bromoisobutyrate). The quartet at 3.4–3.8 ppm, (2Ha) is representative of the methylene-oxy protons from the initiator ethyl 2-bromoisobutyrate moiety (R functionality) which is partially overlapped with the solvent peak (THF). The complex asymmetric shape of these signals is due to polymer tacticity, the restricted motion of the end groups, and conformation effects. To perform azide-alkyne click reaction, the bromo-terminated PS (Hb) was transformed in an azide-terminated PS (Hc) by nucleophilic substitution. This reaction was quantitative as verified by 1H NMR. In Fig. 2 signal at 4.35–4.65 ppm showing triplet is due to the methine proton neighboring the bromine chain end (Hb). After twenty four hours of reaction with NaN3, it was completely shifted to upfield (3.85–4.0) (Hc) due to the quantitative substitution of bromine into azide moiety.41–43 The Integration of the new signal in Fig. 3 confirms the chain end transformation was quantitative. Hence, the transformation of ATRP bromide chain end into azide moiety was found to be quantitative.
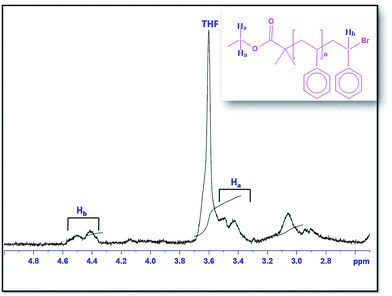 |
| Fig. 2 1H NMR spectrum (zoom of the region 4.8–2.6 ppm) of bromo-terminated polystyrene. Spectra was recorded at room temperature in CDCl3. | |
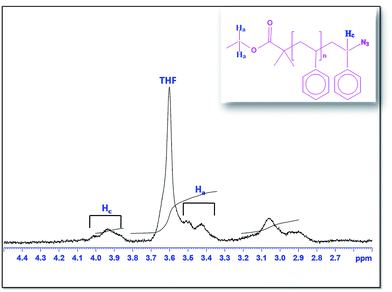 |
| Fig. 3 1H NMR spectrum (zoom of the region 3.85–4.0 ppm) of azide-terminated polystyrene. Spectra was recorded at room temperature in CDCL3. | |
Fig. 4(a) depicts the IR spectra of unmodified NGPs, the Az-f-PS and the C-NCs. The NGPs and C-NCs shows a broad peak at 3450 cm−1 due to the presence of O–H stretching vibration. A small but clearly discernible signal at 2100 cm−1 is present in the spectrum of Az-f-PS which represents the characteristic signal of azide functionality, indicating that the PS has been grafted. The azide signal at 2100 cm−1 is weak and magnification of the three spectra in the region between 2000 and 2200 cm−1 is depicted in Fig. 4(b). After the Huisgen cycloaddition click reaction, the disappearance of the azide stretch in C-NCs indicates that most of the azides must have consumed during the reaction.44 The triazole bands in the C-NCs spectrum at 1457 cm−1 and 1636 cm−1 confirms the successful “click” reaction.45 The characteristic bands of polystyrene for C–H stretching and bending vibrations of methylene groups at 2920 cm−1, 2850 cm−1 and 1650 cm−1 apparently arises in the C-NCs spectrum after click reaction.46
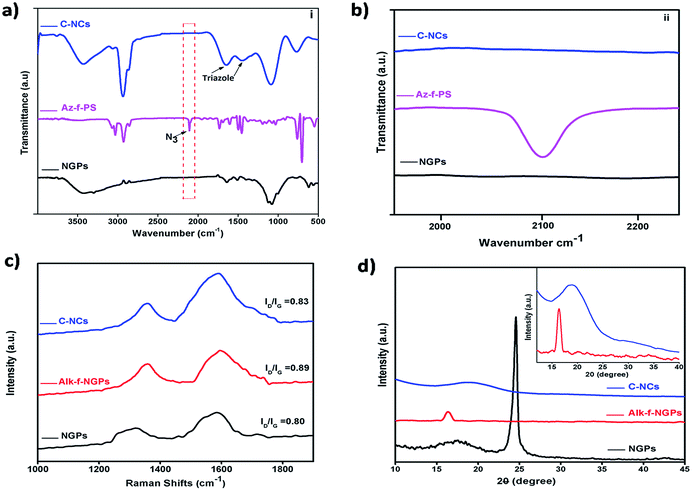 |
| Fig. 4 (a) IR spectra of NGPs, Az-f-PS and C-NCs (b) expanded region between 2000 and 2200 cm−1 of the three samples, highlighting the appearance and disappearance of the azide stretch at 2100 cm−1. (c) Raman spectra of NGPs, Alk-f-NGPs and C-NCs. (d) XRD spectra of NGPs, Alk-f-NGPs and C-NCs. | |
Raman scattering is strongly sensitive to the electronic structure and proves to be an essential tool to characterize graphite and graphene materials. The Raman spectrum of graphene is characterized by two main features, the G mode arising from the first order scattering of the E2g phonon of sp2 C atoms and the D mode arising from a breathing mode of k-point photons of A1g symmetry.47 It is observed from Fig. 4(c) that the peak of NGPs around 1321 cm−1 (D-band) is related to the defects and disorder in the hexagonal lattice, while the 1587 cm−1 (G-band) is due to the vibration of sp2-bonded carbon atoms in the 2D hexagonal lattice.48,49 The calculated ID/IG ratio for pristine NGPs is 0.80, which represents the atomic ratio of sp2/sp3 carbons and express the extent of disordered NGPs. Upon reaction of NGPs with alkyne moiety the intensity of D band increases relative to G band, which indicates the conversion of sp2 hybridized carbon to sp3 hybridized carbon along with blue shift of G position. This was due to the presence of unrepaired defects that remain after functionalization with alkyne moiety. In contrast to Alk-f-NGPs the ID/IG ratio of C-NCs seem to decrease to 0.83 after click reaction. This decrease in ID/IG ratio attributed to the defect healing effect along with the restoration of sp2 network during click reaction as depicted in Fig. 4(c).28,45,50
Fig. 4(d) exhibited XRD patterns of NGPs, Alk-f-NGPs and C-NCs. The interlayer distance can be easily calculated from the diffraction angle of the corresponding material according to Bragg's equation: nλ = 2d
sin
θ. NGPs shows a typical sharp diffraction peak at 24.1° with the corresponding d-spacing of ∼0.37 nm. In addition, after alkyne functionalization of NGPs, the Alky-f-NGPs exhibit an diffraction peak at 16.4° with d-spacing ∼0.54 nm suggesting the successful grafting of alkyne moiety onto NGPs and partial reduction of NGPs during the functionalization process. The increase in the interlayer distance depicts the exertion of the alkyne moiety on the platelets.51 For the C-NCs a broad peak at 19.8° with d-spacing ∼0.44 nm was observed. The d-spacing of C-NCs is larger than that of pristine NGPs, illustrating that the PS chains attached on the NGPs by click reaction disrupts the van der Waals interactions and enlarges the interlayer distance of the platelets.52,53 Moreover it confirms the expected coexisting structures of both NGPs and PS demonstrating that the NGPs are exfoliated and dispersed uniquely in the polystyrene matrix.54
We further investigated the thermal stability using thermogravimetric analysis (TGA) under N2 atmosphere. Fig. 5 shows that the NGPs are not thermally stable, a slight weight loss started below 100 °C, then it begins to decompose and degrades completely at 450 °C which is presumably due to the gradual removal of labile oxygen containing functional groups. Pristine PS begins to decompose at 320 °C and degrades at 440 °C, which is attributed to main-chain pyrolysis. But after click reaction, the C-NCs exhibits good thermal stability with no weight loss below 340 °C and the pyrolysis shifts towards a higher temperature range compared to that of neat PS. The shift in the temperature is due to the interfacial strong interaction existing between the PS and NGPs which can restrict the mobilization of polymer chains and effectively protect against thermal degradation.55 However, to a certain extent the presence of PS in the composites slightly affects the reduction degree.56 The C-NCs exhibit higher thermal stability due to the phenyl-triazole groups formed in the click product.57 Additionally, a higher residue (20%) of C-NCs at higher temperature can be attributed to the presence of NGPs covalently linked to PS which are sufficient to block the premature evaporation of the decomposed molecular fragments of the polymer and increase the residence time.54,58
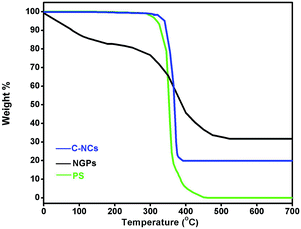 |
| Fig. 5 TGA spectra of C-NCs, NGPs and PS. | |
Scanning electron microscopy (SEM) analysis of pristine NGPs and C-NCs by click reaction was performed by placing the sample on the slide. Fig. 6 shows micrographs of NGPs obtained after ultrasonication in water/ethanol solution. A droplet of the dispersed NGPs in water/ethanol was poured into the specific support and allowed to evaporate to obtain the micrographs. The micrographs revealed that the stacked graphite flakes are separated into thinner petal-like structure, after ultrasonication in Fig. 6(a). Bare and flat surface of NGPs without any curvature is clearly observed in Fig. 6(b). The azide–alkyne click reaction results in uniform dispersion of NGPs in PS matrix as seen in Fig. 6(c). This is attributed to the enhanced compatibility between polystyrene and NGPs through click reaction, leading to strong interaction between the filler and the polymer matrix. The Fig. 6(d) feature individual platelets of nanographite well dispersed throughout the polymer matrix at 200 nm. The dispersion is further observed using TEM images.
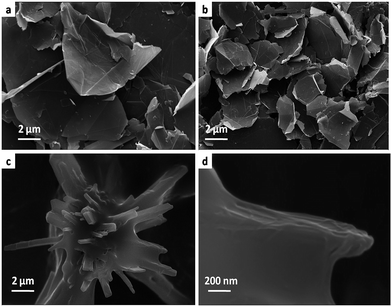 |
| Fig. 6 SEM image of (a) petal-like structure of NGPs at 2 μm (b) bare and flat surface NGPs at 2 μm (c) SEM image of C-NCs at 2 μm (d) at 200 nm. | |
High-resolution transmission electron microscopy (TEM) analysis of the C-NCs was performed by placing a single drop of chloroform solution onto holey carbon-coated copper grid. The Fig. 7 represents interconnected structure established by the homogeneous dispersion of NGPs and polystyrene. The inset shows a particular well-resolved feature in which polymer is well dispersed on platelets of nanographite. To complement the TEM data, atomic force microscopy (AFM) was also performed.
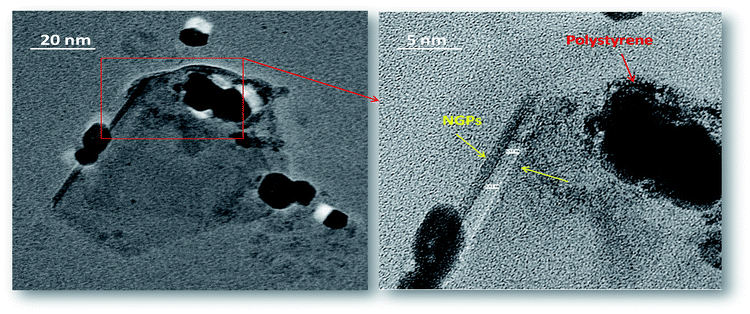 |
| Fig. 7 Surface topography of C-NCs by TEM at (a) 20 nm (b) 5 nm. | |
The C-NCs were analyzed on the basis of surface morphology using current AFM images. AFM provides a measure of the thickness of the interface layers of polystyrene on NGPs. Upon click reaction, the soluble material of Az-f-PS and Alk-f-NGPs exhibits relative uniform dispersion. The PS coated on NGPs, shows a minimum height profile of approximately 20 nm as depicted in Fig. 8. The effect of incorporating NGPs in the organization of PS matrix could be correlated with the increase in the density of pleats with the percentage of NGPs, which could be verified by the increase in surface roughness of 1.207 nm. The C-NCs show an obvious increase in the root mean square (rms) surface roughness of 2.069 nm.
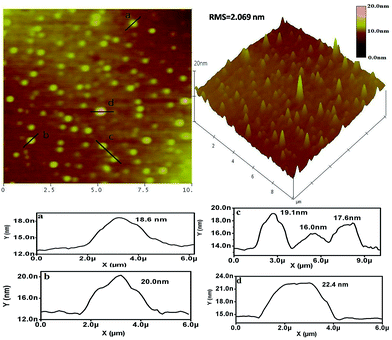 |
| Fig. 8 Surface topography determined by AFM images of the C-NCs. Total scales of images vary from (16–22 nm) a, b, c and d. | |
3.1 Electrical conductivity of polymer NCs
Measurement of electrical conductivity is an important step to evaluate the polymer NCs. Significant difference of resistance was observed for NCs prepared by the click method and solution blending method.38 Fig. 9(a) shows that the electrical resistance for C-NCs is 1.08 × 108 Ω with 1 wt% NGPs, which is three order lower than that for polymer-functionalized nanocomposite prepared by solution blending method (S-NCs) having 9.1 × 1011 Ω. The interconnected network and uniform dispersion of NGPs in the PS matrix is responsible for the increase in the properties at filler loading. This results in an increase in the electrical conductive pathway within the nanocomposite system.48,59
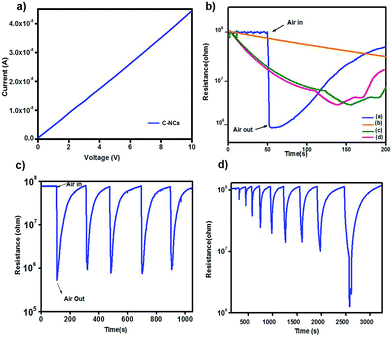 |
| Fig. 9 (a) Resistance of C-NCs (b) response of C-NCs to H2O2 (blue), xylene (orange), toluene (green), benzene (pink), (c) repeatability of C-NCs to H2O2 at every 5 seconds (d) response and recovery of the C-NCs to H2O2 with time (s). | |
3.2 Response of C-NCs to H2O2 vapors
The response of C-NCs films for H2O2 vapor60 was measured using conventional resistance measurement methods by placing the sensor inside the gas chamber and exposing to the vapor as shown in Scheme 4. Here, the response time is the time taken for the sensor to reach the saturation value after the sensor was exposed to H2O2 vapor and the recovery time is the time in which the resistance of the sensor returns to 90% of the initial value after removal of the vapor. As seen in Fig. 9(b), the response of sensing film C-NCs to H2O2 vapor is considerably high. The initial resistance of C-NCs before exposure to H2O2 vapor was measured as 1.08 × 108 Ω and the resistance decreases to 1.29 × 106 Ω on exposure and this indicates the immediate response of C-NCs. To certain the specificity of C-NCs films to H2O2 vapor it was tested against the vapors of other solvents of PS. The responses of the C-NCs films to solvents like benzene, toluene and xylene does not give detectable response as shown in Fig. 9(b). Moreover, other solvents of PS like dichloromethane, acetone and chloroform were also unable to illustrate any detectable response for C-NCs films. As compared to conventional gas sensors, C-NCs shows rapid response within 3 seconds of exposure to H2O2 vapor. In addition, the C-NCs demonstrates excellent reproducibility and repeatability at every 5 seconds (Fig. 9(c)). In Fig. 9(d), the minimum response time of C-NCs is 3 seconds and the recovery time is not more than 60 seconds for H2O2 vapors. Here, the resistance of the C-NCs films goes on decreasing with increase in the exposure time with (3, 5, 10, 20, 30, 40, 50, 60, 100, 120) seconds of H2O2 vapor but after 120 seconds of exposure, the resistance becomes stable. This confirms the stability, reproducibility and repeatability of the C-NCs film to H2O2 vapor.
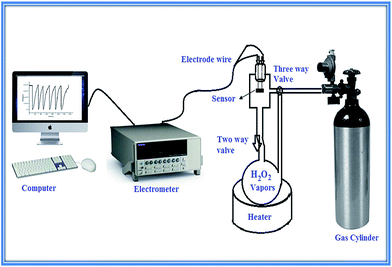 |
| Scheme 4 Schematic diagram of experimental set-up for sensing chemical vapors (H2O2) using C-NCs film. | |
The sensitivity of H2O2 vapor was calculated by using:
here,
R0 and
R are the original resistance and the maximum resistance of the films upon exposure to H
2O
2 vapours respectively. The sensitivity to H
2O
2 vapors at 120 seconds was found to be 91.1%.
3.3 Sensing mechanism of the chemiresistor
NGPs provides an additional surface area for adsorption sites and reaction with target gases, which may lead to high sensor response and response speed since the surface of NGPs is known to be active to various reducing and oxidizing gases. The decrease in resistance on exposure to H2O2 vapors was because of the formation of densely conductive network which leads to a large increase in the electrical conductivity of the film. The conducting paths are formed inside the C-NCs material is due to the quantum mechanical tunneling effects. Here, the distance between the conducting elements is such that electron hopping can occur. It seems that vapors of H2O2 is adsorbed due to the interaction of some polar functional groups of NGPs hydroxyl groups which can influence the charge transfer between NGPs61 and the adsorbed H2O2 vapors.62–64
3.4 The effect of polymer type on sensor stability
Although the methods of polymer blend into graphitic material had considerable effect on the response of the sensor towards vapors. This means even the selection of methods and the polymer can improve the fabrication of sensor for desired vapor. Moreover, the polymeric material also acts as an adhesive substance which provides physical stability and durability to the sensing film. The stability of the C-NCs was examined by testing the sensor response after storing the films for about three months in air and at room temperature. The stored films exhibited similar response to H2O2 vapors as before.
4 Conclusions
The present work shows that the NGPs are very promising nanofiller for polymeric materials. In time NGPs could replace CNT due to their parallel properties with cheaper cost. The main challenge of the homogeneous dispersion of nanofiller in polymer matrix was successfully overcome by Cu(I)-catalyzed [3 + 2] Huisgen cycloaddition click reaction. The click reaction is proceeded after the functionalization of both the azide and alkyne moiety. The PS functionalization with azide moiety, after bromine-termination of PS through ATRP, was confirmed by the complete upfield shifting of NMR signals from (4.35–4.65) ppm to (3.85–4.0) ppm. FT-IR confirms the attachment of strong azide moiety at 2100 cm−1, which is covalently bound to PS chains as a part of the polymer which has increased the flexibility and segmental mobility of PS. The reduction degree of C-NCs in Raman spectroscopy indicates that the conjugated sp2-hybridized carbon networks are restored in the composite. SEM, TEM and AFM analysis clearly shows the homogeneous dispersion of NGPs in PS matrix. The resistance of the pure PS is about 1 × 1014 Ω, much higher than that of the C-NCs 1.08 × 108 Ω obtained in our work, revealing that the conductivity has been improved greatly with addition of only a 1% of NGPs. The C-NCs is a promising sensor material which gives a spontaneous response within 3 seconds of exposure to H2O2 vapors with complete recovery at room temperature by just exposing the sensor to air. The prepared C-NCs gas sensor has the potential to be used in fabrication of efficient, potable hand-held device for H2O2 sensing at low cost.
Acknowledgements
One of the authors is grateful to the Amity University Uttar Pradesh for providing financial support in the form of JRF. We thank Dr John E. Moses, University of Nottingham for providing technical support.
Notes and references
- P. H. C. Camargo, K. G. Satyanarayana and F. Wypych, Mater. Res., 2009, 12, 1 CrossRef CAS.
- I. Y. Jeon and J. B. Baek, Materials, 2010, 3, 3654 CrossRef CAS PubMed.
- L. Bokobza, Polymer, 2007, 48, 4907 CrossRef CAS PubMed.
- P. C. Ma, N. A. Siddiqui, G. Marom and J. K. Kim, Composites, Part A, 2010, 41, 1345 CrossRef PubMed.
- A. S. Patole, et al., Eur. Polym. J., 2012, 48, 252 CrossRef CAS PubMed.
- D. A. Dikin, et al., Nature, 2007, 448, 457 CrossRef CAS PubMed.
- T. K. Das and S. Prusty, Polym.-Plast. Technol. Eng., 2013, 52, 319 CrossRef CAS PubMed.
- L. Chen, D. Rende, L. S. Schadler and R. Ozisik, J. Mater. Chem. A, 2013, 1, 3837 CAS.
- M. C. Weisenberger, E. A. Grulke, D. Jacques, T. Ramtell and R. Andrews, J. Nanosci. Nanotechnol., 2003, 6, 535 CrossRef PubMed.
- H. Quan, B. Zhang, Q. Zhao, R. K. K. Yuen and R. K. Y. Li, Composites, Part A, 2009, 40, 1506 CrossRef PubMed.
- S. Kim and L. T. Drzal, J. Adhes. Sci. Technol., 2009, 23, 1623 CrossRef CAS PubMed.
- T. Ramanathan, A. A. Abdala, S. Stankovich, D. A. Dikin, M. Herrera-Alonso, R. D. Piner, D. H. Adamson, H. C. Schniepp, X. Chen, R. S. Ruoff, S. T. Nguyen, I. A. Aksay, R. K. Prud'Homme and L. C. Brinson, Nat. Nanotechnol., 2008, 3, 327 CrossRef CAS PubMed.
- M. Fang, K. Wang, H. Lu, Y. Yang and S. Nutt, J. Mater. Chem., 2009, 19, 7098 RSC.
- J. Liang, Y. Huang, L. Zhang, Y. Wang, Y. Ma, T. Guo and Y. Chen, Adv. Funct. Mater., 2009, 19, 2297 CrossRef CAS PubMed.
- N. G. Sahoo, S. Rana, J. W. Cho, L. Li, S. H. Chan and N. G. Sahoo, et al., Prog. Polym. Sci., 2010, 35, 837 CrossRef CAS PubMed.
- H. K. F. Cheng, Y. Pan, N. G. Sahoo, K. Chong, L. Li, S. H. Chan and J. Zhao, J. Appl. Polym. Sci., 2012, 124, 1117 CrossRef CAS PubMed.
- R. E. Gorga and R. E. Cohen, J. Polym. Sci., Part B: Polym. Phys., 2004, 42, 2690 CrossRef CAS PubMed.
- H. F. Yang, C. S. Shan, F. H. Li, Q. X. Zang, D. X. Han and L. Niu, J. Mater. Chem., 2009, 19, 8856 RSC.
- H. M. Etmimi and P. E. Mallon, Polymer, 2013, 54, 6078 CrossRef CAS PubMed.
- J. Kim, S. M. Hong, S. Kwak and Y. Seo, Phys. Chem. Chem. Phys., 2009, 11, 10851 RSC.
- L. Cui, J. Liu, R. Wang, Z. Liu and W. Yang, J. Polym. Sci., Part A: Polym. Chem., 2012, 50, 4423 CrossRef CAS PubMed.
- T. Sehgal and S. Rattan, J. Radioanal. Nucl. Chem., 2010, 286, 71 CrossRef CAS.
- S. H. Lee, D. R. Dreyer, J. An, A. Velamakanni, R. D. Piner, S. Park, Y. Zhu, S. O. Kim, C. W. Bielawski and R. S. Ruoff, Macromol. Rapid Commun., 2010, 31, 281 CrossRef CAS PubMed.
- S. Sun and P. Wu, J. Phys. Chem. A, 2010, 114, 8331 CrossRef CAS PubMed.
- X. Feng, S. Zhu, K. Yue, H. Su, K. Guo, C. Wesdemiotis, W. B. Zhang, S. Z. D. Cheng and Y. Li, ACS Macro Lett., 2014, 3, 900 CrossRef CAS.
- H. Su, J. Zheng, Z. Wang, F. Lin, X. Feng, X. H. Dong, M. L. Becker, S. Z. D. Cheng, W. B. Zhang and Y. Li, ACS Macro Lett., 2013, 2, 645 CrossRef CAS.
- R. K. Iha, K. L. Wooley, A. M. Nyström, D. J. Burke, M. J. Kade and C. J. Hawker, Chem. Rev., 2009, 109, 5620 CrossRef CAS PubMed.
- H. M. Li, F. O. Cheng, A. M. Duft and A. Adronov, J. Am. Chem. Soc., 2005, 127, 14518 CrossRef CAS PubMed.
- Z. Guo, L. Liang, J. J. Liang, Y. F. Ma, X. Y. Yang, D. M. Ren, Y. S. Chen and J. Y. Zheng, J. Nanopart. Res., 2008, 10, 1077 CrossRef CAS.
- S. Campidelli, B. Ballesteros, A. Filoramo, D. D Diaaz, G. Torre, T. Torres, G. M. A. Rahman, C. Ehli, D. Kiessling, F. Werner, V. S. gobba, D. M. Guldi, C. Cioffi, M. Prato and J. P. Bourgoin, J. Am. Chem. Soc., 2008, 130, 11503 CrossRef CAS PubMed.
- T. Heinrich, C. H.-H. Traulsen, E. Darlatt, S. Richter, J. Poppenberg, N. L. Traulsen, I. Linder, A. Lippitz, P. M. Dietrich, B. Dib, W. E. S. Unger and C. A. Schalley, RSC Adv., 2014, 4, 17694 RSC.
- G. Molteni, C. L. Bianchi, G. Marinoni, N. Santod and A. Ponti, New J. Chem., 2006, 30, 1137 RSC.
- L. Bai, L. Zhang, Z. Cheng and X. Zhu, Polym. Chem., 2012, 3, 2685 RSC.
- O. S. Kwon, S. J. Park, H. Yoon and J. Jang, Chem. Commun., 2012, 48, 10526 RSC.
- L. Guan, S. Wang, W. Gu, J. Zhuang, H. Jin, W. Zhang, T. Zhang and J. Wang, Sens. Actuators, B, 2014, 196, 321 CrossRef CAS PubMed.
- R. Schulte-Ladbeck, A. Edelmann, G. Quintas, B. Lendl and U. Karst, Anal. Chem., 2006, 78, 8150 CrossRef CAS PubMed.
- S. Rattan, P. Singhal and A. L. Verma, Polym. Eng. Sci., 2013, 53, 2045 CAS.
- S. Stankovich, D. A. Dikin, G. H. B. Dommett, K. M. Kohlhaas, E. J. Zimney, E. A. Stach, R. D. Piner, S. T. Nguyen and R. S. Ruoff, Nature, 2006, 442, 282 CrossRef CAS PubMed.
- F. J. Ibanez, U. Gowrishetty, M. M. Crain, K. M. Walsh and F. P. Zamborini, J. Anal. Chem., 2006, 78, 753 CAS.
- R. K. Layek and A. K. Nandi, Polymer, 2013, 54, 5087 CrossRef CAS PubMed.
- J. F. Lutz, H. G. Börner and K. Weichenhan, Macromol. Rapid Commun., 2005, 26, 514 CrossRef CAS PubMed.
- J. F. Lutz and K. Matyjaszewski, Macromol. Chem. Phys., 2002, 203, 1385 CrossRef CAS.
- J. F. Lutz and K. Matyjaszewski, Polym. Chem., 2005, 43, 897 CrossRef CAS PubMed.
- M. Ergin, B. Kiskan, B. Gacal and Y. Yagci, Macromolecules, 2007, 40, 4724 CrossRef CAS.
- H. Li, Q. Zheng and C. Han, Analyst, 2010, 135, 1360 RSC.
- S. Sun, Y. Cao, J. Feng and P. Wu, J. Mater. Chem., 2010, 20, 5605 RSC.
- Z. J. Fan, W. Kai, J. Yan, T. Wei, L. J. Zhi, J. Feng, Y. M. Ren, L. P. Song and F. Wei, ACS Nano, 2011, 5, 191 CrossRef CAS PubMed.
- S. Ramakrishnan, M. Dhakshnamoorthy, E. J. Jelmy, R. Vasanthakumari and N. K. Kothurkar, RSC Adv., 2014, 4, 9743 RSC.
- A. Tiberj, N. Camara, P. Godignon and J. Camassel, Nanoscale Res. Lett., 2011, 6, 478 CrossRef PubMed.
- K. N. Kudin, B. Ozbas, H. C. Schniepp, R. K. Prud'homme, I. A. Aksay and R. Car, Nano Lett., 2008, 8, 36 CrossRef CAS PubMed.
- H. R. Mamaqani, V. H. Asl, K. Khezric and M. S. Kalajahia, RSC Adv., 2014, 4, 24439 RSC.
- C. Chen, R. Li, L. Xu and D. Yan, RSC Adv., 2014, 4, 17393 RSC.
- N. Wu, X. She, D. Yang, X. Wu, F. Su and Y. Chen, J. Mater. Chem., 2012, 22, 17254 RSC.
- F. Meng, H. Ishida and X. Liu, RSC Adv., 2014, 4, 9471 RSC.
- Y. Wu, R. Cao, L. Ji, W. Huang, X. Yang and Y. Tu, RSC Adv., 2015, 5, 28085 RSC.
- P. G. Song, Z. H. Cao, Y. Z. Cai, L. P. Zhao, Z. P. Fang and S. Y. Fu, Polymer, 2011, 52, 4001 CrossRef CAS PubMed.
- X. Qiang, F. Chen, X. Y. Ma and X. B. Hou, J. Appl. Polym. Sci., 2014, 131, 40652 Search PubMed.
- Q. Ma, J. Luo, Y. Chen, W. Wei, R. Liu and X. Liu, J. Polym. Sci., Part A: Polym. Chem., 2015 DOI:10.1002/pola.27751.
- K. Inyawilert, A. Wisitsoraat, C. Sriprachaubwong, A. Tuantranont, S. Phanichphant and C. Liewhiran, Sens. Actuators, B, 2015, 209, 40 CrossRef CAS PubMed.
- Z. Liu, Y. Liu, L. Zhang, S. Poyraz, N. Lu, M. Kim, J. Smith, X. Wang, Y. Yu and X. Zhang, Nanotechnology, 2012, 23, 335603 CrossRef PubMed.
- G. Lu, L. E. Ocola and J. Chen, Nanotechnology, 2009, 20, 445502 CrossRef PubMed.
- T. Someya, J. Small, P. Kim, C. Nuckolls and J. T. Yardley, Nano Lett., 2003, 7, 877 CrossRef.
- T. Alizadeh and L. H. Soltani, J. Hazard. Mater., 2013, 248–249, 401 CrossRef CAS PubMed.
- G. R. Hutchison, M. A. Ratner and T. J. Marks, J. Phys. Chem. B, 2001, 105, 2881 CrossRef CAS.
Footnote |
† Electronic supplementary information (ESI) available: ES 1: GPC curves of PS–Br and PS–N3, ES 2: tabular representation of GPC data for PS–Br and PS–N3. See DOI: 10.1039/c5ra10952c |
|
This journal is © The Royal Society of Chemistry 2015 |
Click here to see how this site uses Cookies. View our privacy policy here.