DOI:
10.1039/C5RA08714G
(Paper)
RSC Adv., 2015,
5, 55579-55587
Characterization and comparison of uniform hydrophilic/hydrophobic transparent silica aerogel beads: skeleton strength and surface modification†
Received
11th May 2015
, Accepted 15th June 2015
First published on 16th June 2015
Abstract
Silica aerogel is a good adsorbent due to the large surface area and chemical stability. However, its inherent poor mechanical properties and hydrophobicity limit applications in water treatment. To improve the adsorption performance of silica aerogel, uniform transparent hydrophilic mesoporous silica aerogel beads with highly degree of sphericity were synthesized through a facile aging immersion and ambient pressure drying route. The designed hydrophilic silica aerogel beads possessed the mesopores, mean diameter of approximately with the average pore size of 12.51 nm, the specific surface area of 582.52 m2 g−1, and the pore volume of 1.46 cm3 g−1. For comparison, hydrophilic silica aerogel beads without skeleton improvement and hydrophobic silica aerogel beads were also obtained, respectively. The synthesized novel hydrophilic silica aerogel beads displayed a significantly improved adsorption performance with a favorable dye absorption capacity, superior to that of previously synthesised silica-based aerogel beads materials. This study demonstrates a facile and low-cost route toward transparent silica aerogel beads with macroscopic beads structures, which can be used as adsorbents, catalytic supports or the template to synthesize novel functional materials requiring high transmittance, high surface area and effective mass transport.
1. Introduction
Aerogels are the most highly porous nanostructured materials currently available, have a large surface area, high porosity, low bulk density, and extremely low thermal conductivity which have attracted great interest in a broad range of both commercial and fundamental scientific applications during recent decades.1–7
As well known, aerogels are normally prepared by the supercritical drying using an expensive estersil. High cost and long production cycle limit industrial-scale production of aerogels. Besides, the practical application of aerogels has been constrained because of their fragility and irregularity. To solve these problems, silica aerogel beads are recommend to replace the monolithic silica aerogels. Due to this silica aerogel beads are the small spheroid, solvent exchange process is much faster and the beads are regularity and more convenient for application; this can considerably improve the product quality and reduce the production time and cost. Silica aerogel beads have recently been synthesized at ambient pressure, many researchers had made a great contribution.8–11 Although these methods are much easier, the key step to obtain the silica beads is tedious and unmanageable, and the solution is complex and difficult to recycle. In addition, both the hydrophobic and hydrophilic aerogel beads have obvious crack because of surface modification and heat-treated. One of the challenges in the area of silica aerogel beads is to develop a facile approach that possessed better accuracy and repetition.
In this study, we have successfully synthesised of hydrophilic/hydrophobic transparent silica aerogel beads with highly degree of sphericity at an ambient pressure via the ball dropping method (BDM). Different from the previous reports,8 a kind of high viscosity oil phase (dimethyl silicon oil) was used to replace the complex solution phases aimed to make the reaction easy to control and keep the wet gel with highly degree of sphericity. In order to improve skeleton strength of the gel, wet silica beads were aging by immersing in large volume of tetraethoxysilane (TEOS)–ethanol–water solution to reduce shrinkage during drying. However, this skeleton strength approach pursued in this study significantly shortens the synthesis aerogel beads process, which represents a novel skeleton strength mechanism. Meanwhile, we compared the properties of obtained strengthened silica aerogel beads with other silica beads which were surface-modified or untreated. The hydrophilic silica aerogel beads synthesized after skeleton strength approach were used as solid adsorbent for dye removing, which showed excellent physicochemical properties as well as remarkable adsorption performance effect.
2. Materials and methods
2.1 Preparation of silica hydrogel beads using sodium silicate (water-glass)
Silica hydrogel beads were prepared through hydrolysis and polycondensation of sodium silicate as a silica precursor (molar ratio SiO2
:
Na2O = 3.02). Sodium silicate was purchased from Shanghai Qingfeng Chem. Inc. Acetic acid, which was used as an acid catalyst, was purchased from Sinopharm Chemical Reagent Co. Ltd., China. Tetraethoxysilane (TEOS) was purchased from Shanghai Lingfeng chemical regent. Co., Ltd.
Fig. 1 shows the experimental procedures used for the preparation of mesoporous silica aerogel beads at ambient pressure via a simultaneous solvent exchange and skeleton improvement process. In order to prepare the silica sols, aqueous silicate solution was mixed with acetic acid-catalyzed water under continuous stirring. Acetic acid solution was added to the aqueous solution of sodium silicate until the pH of the solution became ∼5.8. This procedure was executed rapidly to avoid sol gelation. Then, the sols were droped into a container with 70 °C dimethyl silicon oil. As the droplets came into contact with the hot dimethyl silicon oil, the temperature increased, resulting in polymerization of the silica (polymerization speed improved rapidly) and gel bead formed. After gelation, the silica beads were transferred into the beaker, and washed with distilled water at 65 °C for 2 h for 3 times to remove the sodium ions trapped inside the wet beads. In order to further treatment, the silica beads were immersed in ethanol at 60 °C for 2 h for 3 times to exchange the water in the aerogel pores with ethanol. After washing, the beads were divided into three.
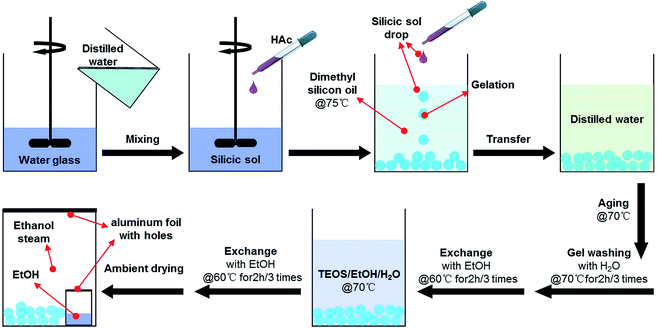 |
| Fig. 1 Schematic illustration of the preparation process of SiO2 aerogels beads. | |
2.2 Preparation of hydrophobic silica aerogel beads via solvent exchanging/skeleton improvement
The skeleton improvement was carried out by immersing the prepared hydrogel beads in ethanol/tetraethoxysilane/water solution at 70 °C for 24–48 h. After skeleton improvement, the beads were washed with ethanol to remove the unreacted tetraethoxysilane. The wet beads were dried at room temperature (∼25 °C) for 24 h and then 60 °C for 6 h to reduce shrinkage during drying. In order to ensure completely evaporation of the pore liquid, the beads were dried at 180 °C for 1 h. The sample was named as Sil-S.
2.3 Preparation of silica xerogel beads
For comparison, a part of the wet beads were dried at room temperature (∼25 °C) for 24 h and then 60 °C for 6 h to reduce shrinkage during drying. In order to ensure compete evaporation of the pore liquid, the beads were dried at 180 °C for 1 h. The sample was named as Sil-U.
2.4 Preparation of hydrophilic silica aerogel beads via simultaneous solvent exchange/surface modification
The rest of wet beads were modified by Trimethylchlorosilane (TMCS) via simultaneous solvent exchange/surface modification which has been reported previously.8 The sample was named as Sil-M.
2.5 Characterization methods
The phase of beads were characterized by X-ray diffraction (XRD) (D8 Advance Diffractometer, Bruker, Germany) with a Cu-Kα radiation (λ = 1.5406 Å) at a scanning rate of 10° min−1; The small angle diffraction patterns (SXRD) were collected at room temperature. The powder SXRD patterns were carried out using a Bruker-AXS D8 Advance diffractometer equipped with Cu-Kα incident radiation (50 kV, 60 mA). The small angle diffraction patterns were collected at room temperature over the range of 0.5–10°. The pore size distributions (PSDs) of aerogel beads were analyzed by the BJH nitrogen gas adsorption and desorption method (ASAP 2000, Micromeritics, USA). The Brunauer–Emmett–Teller (BET) method was used to determine the surface area of the final products. Surface area was measured based on the amount of N2 gas adsorbed at various partial pressures, and a single condensation point (p/p0 = 0.99) was used to determine the pore size and cumulative pore volume. Before N2 adsorption, the sample was degassed at 200 °C. Pore size distributions were calculated from the desorption isotherms.12 The microstructure of the aerogel beads was probed by field emission scanning electron microscope (SEM, Model Philips XL-30SEM analyzer) and transmission electron microscopy (TEM, JEOL-JEM-2010, Japan). Fourier transform infrared spectroscopy (FTIR) (Thermo Nicolet, USA) was used to study the chemical states of the silica aerogel beads. The hydrophilcity of the sample was tested by measuring the percentage of water absorbed after placing the mesoporous silica aerogel beads directly on the surface of water. The contact angle (θ) was measured by a contact angle meter (OCA20 contact angle analyzer, Data Physics, San Jose, CA). The change in weight of the samples over time was then assessed using an electronic microbalance (Model OHAUS EPG214C USA) with an accuracy of 10−5 g. The oil absorption capacity of the silica aerogel beads was also investigated as follows. The silica aerogel beads were crushed to a powder, and then 10 g of powder was placed on a polyethylene plate, which does not absorb oil. Dioctyl-phthalate (DOP) was added drop-by-drop to the center of the sample from a burette, and the mixture was thoroughly kneaded with a spatula after each drop was added. The operation of dropping and kneading was repeated until the entire sample became a solid putty lump. The amount of DOP used was recorded and the oil absorption amount was expressed in terms of ml g−1 (that is, the volume of oil absorbed/weight of the sample).
The tapping densities of the obtained silica aerogel beads were calculated based on their mass to volume ratios. The volume was calculated by filling a measuring cylinder with the silica aerogel beads. An electronic microbalance (Model OHAUS EPG214C USA) was used to measure the mass of the aerogel beads. The percentage volume shrinkage and the porosity of the prepared aerogels were determined as follows:
%Porosity = (1 − ρb/ρs) × 100% |
where
ρs and
ρb are the skeletal and bulk densities of the silica aerogel, respectively.
3. Results and discussion
3.1 Mechanism of sol–gel polymerization and skeleton improvement of silica wet beads
The preparation of silica beads involves the sol-to-gel transition which is referred as gelation. In the transition, the sol become highly viscous and ceases to move.13 The gelation time depends strongly on the amount of catalyst added to the sol. These observations can be explained by the general theory of silica polymerization. As the pH of the sol increased from 1 to 5, the gelation time decreased from 450 min to ∼5 min.14 Interestingly, the siloxane gel showed rheological property. It was noticed that when mechanical force was applied, siloxane gel transforms to a flowable sol. When the force was removed, the static property of the gel was retained with uniform distribution of the component to form transparent homogenous gel. More specifically, when the silicic sol drop came into the dimethyl silicon oil, the drop keeps round due to the surface tension of the high viscosity dimethyl silicon oil. And with the increasing of temperature, the reaction speed improves rapidly during the process of falling. This is because an increase in the temperature of the sol increased the rate of the condensation reactions and caused silica clusters to aggregate at a relatively faster rate to form a three-dimensional porous silica network. The silica particles aggregated into the gel network, and the wet beads were obtained.
Generally, the silica network formed by the polymerization of colloidal silica is weak. In order to reduce irreversible shrinkage of hydrogel beads during drying, an aging process is applied to strengthen the as-formed SiO2 framework, rendering it strong enough to resist the surface tension originating from the solvent extraction. This was done via a skeleton improvement process using the ethanol/tetraethoxysilane/water solution. The expected chemical reactions for the skeleton improvement are as follows:
|
 | (1) |
|
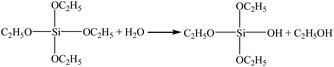 | (2) |
Thus, TEOS reacts with water (eqn (2)), and OH groups present on the silica surface (eqn (1)), to form O–Si–O bonding; consequently, the as-formed SiO2 framework is strengthened. During the skeleton improvement process, the reaction between H2O and TEOS can help to speed up the reaction rate of TEOS with the OH groups on the silica surface. The skeleton improvement of the beads by TEOS is essential before APD, because it prevents the formation of new siloxane bonds between the adjacent silica cluster and therefore irreversible shrinkage of the bead-based gels; besides, the process strengths the framework of the silica beads, rendering it strong enough to resist the surface tension originating from the solvent extraction.15 In the present study, we strengthened the silica beads using TEOS by a skeleton improvement process.
The wet silica beads without surface modification and skeleton improvement and the wet silica beads modified with trimethylchlorosilane were also prepared for comparison.
3.2 Physical properties and XRD studies
The synthesis conditions and the experimental results on the packing bed density, shape and the appearance of the aerogel beads synthesized by the ball dropping method (BDM) are given in Table 1. Significant change has been observed in the packing bed density of the aerogel beads and had the values in the range of 0.163–0.268 g cm−3. All the samples had a spherical shape (Fig. 2(a–c)) since the homogeneous sols could be obtained for the BDM. However, the sample Sil-U showed smaller shape because of shrinkage during the ambient pressure drying; the sample Sil-M showed obvious cracks due to a “spring-back effect” which limited the applications.2 The sample Sil-S showed a spherical shape without obvious creaks because that the beads had been successfully strengthened by the TEOS though the silica beads is hydrophilic. All the aerogel beads prepared by BDM were transparent indicated that the pores and particles present in the aerogel beads are regular. This is because that the wet gels keep a prefect sphericity due to the high surface tension and viscosity of dimethyl silicon oil during the BDM, which made the wet beads can bear more pressure during the dry process.
Table 1 Physical properties of silica aerogel beads by BDM
Physical property |
Sil-U |
Sil-S |
Sil-M |
Gelation time (minutes) |
|
∼10 |
|
Packing bes density (g cm−3) |
0.268 |
0.175 |
0.163 |
Porosity (%) |
68.67 |
84.67 |
86.44 |
Oil absorption (ml g−1) |
2.61 |
2.81 |
3.35 |
Water absorn (ml g−1) |
2.53 |
2.78 |
0.19 |
Shape and appearance |
Spheroid/semitransparent |
Spheroid/transparent |
Spheroid/transparent |
 |
| Fig. 2 Silica aerogel or xerogel prepared by different drying method. ((a) Sil-U, (b) Sil-M, (c) Sil-S). | |
The XRD diffractograms of three kinds of silica beads in the region 5–80° are provided in Fig. 3(a). The broad, weak peak centered at 15–30° is single crystal diffraction peak indicated that all the silica beads are amorphous. At the same time, small angle XRD was employed to confirm the mesoporous silica. As can be seen from Fig. 3(b), all the silica beads have a diffraction peak at 2θ value of ca. 1–2° consistent with the characteristic diffraction pattern of mesoporous silica.16 The Sil-U show the highest peak, indicating that the Sil-U possess the best mesoporous distributed structure. This is because the structure of Sil-M and Sil-S were changed during the modified and strengthen process.
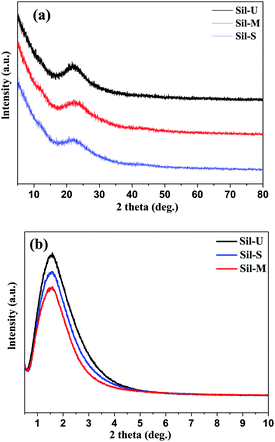 |
| Fig. 3 XRD pattern of the SiO2 aerogels beads. | |
3.3 FTIR and contact angle studies
To promote the actual application of these SiO2 aerogel beads, we further investigated their hydrophilic/hydrophobic properties. The chemical state of the silica aerogel beads was confirmed using Fourier transform infrared spectroscopy (FTIR). The FTIR spectra of the three kinds of silica beads in the region 4000–400 cm−1 are provided in Fig. 4. The strong and weak peaks centered at 1070 and 495 cm−1, respectively, correspond to Si–O–Si bonding of the silica beads, and provide the most information concerning the structure of the silica network.17,18 In the silica beads Sil-U and Sil-S, a strong –OH peak at 3450 cm−1 indicates that a significant fraction of the Si atoms exist on the surface of a silica beads as the hydroxylated species, and the weak absorption at 1640 cm−1 corresponds to deformation vibrations of the adsorbed water molecules; and the two weak peaks observed at 976 cm−1 and 960 cm−1 for both the Sil-U and the Sil-S are due to Si–OH stretching vibrations, indicating the presence of unmodified material. Though the FTIR spectra of the Sil-U and Sil-S are similar, there are some differences. In the silica beads Sil-S, the peak at 2975 cm−1 and 882 cm−1 is due to Si–C bonding, and the –OH peak intensities were relatively reduced compared to Sil-U; Si–OH, Si–H2O and C–H peaks are present, indicating that the silica beads are strengthened with TEOS successfully and hydrophilic. In contrast, in the silica beads Sil-M, the –OH peak intensities were significantly reduced,19 the strong absorption peak at 1360 cm−1 corresponds to the terminal –CH3 group, and the peak at 840 cm−1 is due to Si–C bonding, which is attributed to the surface modification of silica beads by TMCS.20,21
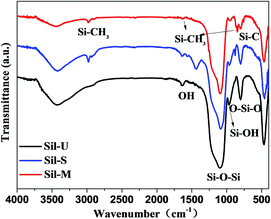 |
| Fig. 4 FTIR spectra of the silica aerogel beads. | |
The digital photos of silica aerogel beads are shown in Fig. 5. The water contact angle of Sil-M was 138°(Fig. 5(b)), illustrating that the sample showed hydrophobicity.22 In contrast, the water contact angle of Sil-U and Sil-S was much lower (Fig. 5(a) and (c)), indicating that Sil-U and Sil-S were hydrophilic. The test of contact angle is corresponding to the FTIR spectra analysis.
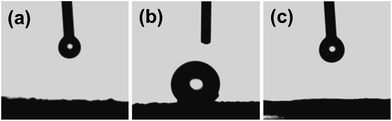 |
| Fig. 5 Optical images of a water droplet on the surface of silica beads.((a) Sil-U, (b) Sil-M, (c) Sil-S). | |
3.4 FE-SEM and TEM studies
The mesoporous structure of silica beads was confirmed by field-emission scanning electron microscopy (FE-SEM) and transmission electron microscopy (TEM). Fig. 6(a–c) shows the pore characteristics and structure morphology of mesoporous silica beads based on FE-SEM micrographs of (a) Sil-U, (b) Sil-M, (c) Sil-S. In general, the silica beads Sil-U formed dense aggregates of spheres while silica beads Sil-M and Sil-S had highly porous structures. This is because the untreated silica beads shrank more during APD, resulting in dense aggregates of dried silica beads and the loss of mesopores.23 The modified silica beads shrank little during APD, indicating that the surface of SiO2 hydrogel beads had been successfully modified by TMCS. And the strengthened silica beads also shrank little during APD, indicating that the SiO2 framework of the hydrogel beads had been successfully strengthened by the hydrolysis of TEOS. Fig. 6(e and f) shows representative TEM images of (d) Sil-U, (e) Sil-M and (f) Sil-S. The untreated silica beads appeared as dense, aggregated silica particles. In contrast, the beads modified with TMCS and the beads strengthed with TEOS were characterized by a highly porous silica network with uniform pore size. The phenomenon is corresponding to the SEM analysis.
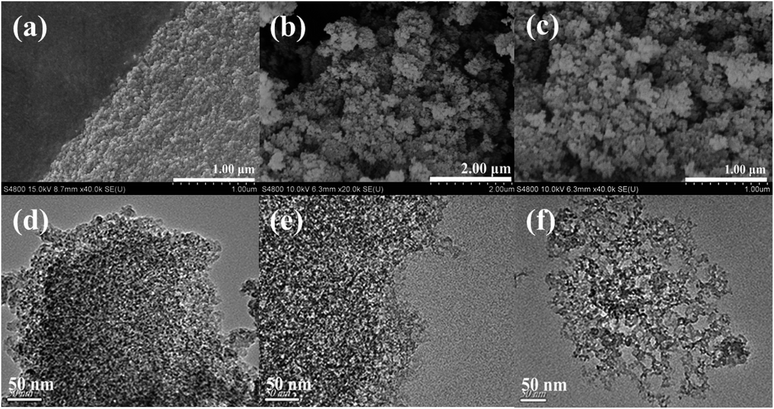 |
| Fig. 6 FE-SEM micrograph of mesoporous silica beads.((a) Sil-U, (b) Sil-M, (c) Sil-S); TEM micrograph of mesoporous silica beads.((d) Sil-U, (e) Sil-M, (f) Sil-S). | |
3.5 Nitrogen physisorption studies
The porosity properties of the mesoporous silica beads obtained at different conditions were further compared by examining their nitrogen adsorption–desorption isotherms and pore size distributions. Fig. 7(a) shows the N2 adsorption/desorption isotherms of Sil-U, Sil-M and Sil-S. The maximum amount of the N2 gas adsorbed by a porous solid obviously depends on the volume of the pores present in that material. It is seen that the samples adsorbed maximum amount of the gas which saturated at similar date with the corresponding relative pressure of 0.99.This is because the sample Sil-U, Sil-M and Sil-S showed similar pore volume (1.464–1.579 cc g−1) of the pores. The amounts of N2 gas adsorbed by the aerogel beads are quite consistent with the pore volumes of the respective samples listed in Table 2.
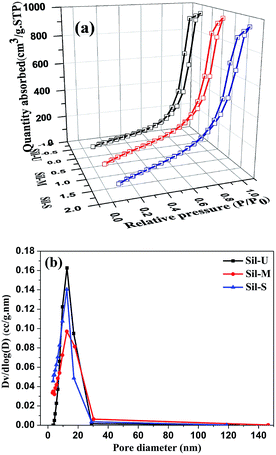 |
| Fig. 7 (a) N2 adsorption/desorption isotherms and (b) pore size distributions of silica beads. | |
Table 2 Textural properties of silica aerogel beads by APD
Physical property |
Sil-U |
Sil-S |
Sil-M |
BET surface area (m2 g−1) |
351.27 |
582.52 |
515.38 |
Cumulative pore volume (cm3 g−1) |
1.60 |
1.47 |
1.48 |
Average pore diameter (nm) |
12.6 |
12.5 |
12.5 |
The physisorption isotherms obtained for the aerogel beads are Type IV which is the characteristic feature of the mesoporous materials.24–26 The desorption cycles of the isotherms showed a hysteresis loop for all the samples which is generally attributed to the capillary condensation occurring in the mesopores. The shape of the hysteresis loop depends on the shape of the pores present in the respective material. Therefore, in the present studies, the adsorption branch of the isotherm has been employed for the PSD analysis. Fig. 7(b) shows the pore size distribution (PSDs) curves of the silica beads. All the silica beads have a broad pore size distribution with a peak pore diameter of 12 nm. As per the IUPAC classification of pores, all the silica beads showed a peak in the mesopore region (2–120 nm) indicating that the mesopores in the silica beads have remained intact, even after the drying process.
3.6 Mechanism discussion
Based on the aerogels of different treatments, the mechanism of water glass based SiO2 hydrogel in the solution was proposed (Fig. 8).
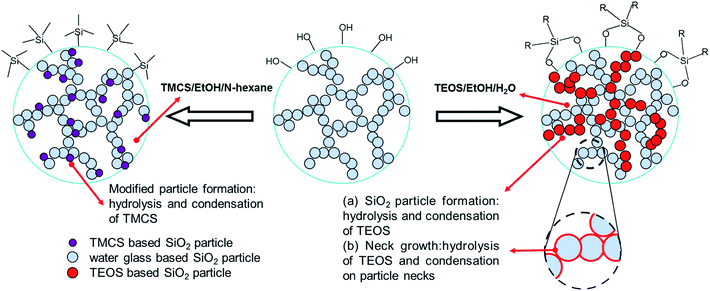 |
| Fig. 8 Schematic illustration of the modification and aging mechanism of SiO2 beads. | |
To obtain hydrophobic silica aerogel beads at an ambient pressure, the as-prepared silica wet gel beads were modified using an ethanol/TMCS/n-hexane solution via simultaneous solvent exchange and surface modification process. Descriptions of the formation of silica wet gel beads, simultaneous solvent exchange, and surface modification procedure were reported previously.8 Compared to the wet silica beads Sil-U, the modified silica beads have less silicanol groups (Si–OH) on the silica surface and more non-polar alkyl groups which reduce irreversible shrinkage and even cause spring back during the drying. But, just because of the “spring-back effect”, the surface of the aerogel beads cracked which limits application.
In order to strengthen the as-formed SiO2 skeleton, rending it strong enough to resist the surface tension originating from the solvent extraction, an aging process is applied. In previous studies, the wet alcogel beads originated from TEOS/alcohol precursor was usually strengthened in the alcohol atmosphere27–29 or in the alcohol solution.30
In these alcogel beads, the water quantity was very small, which rendered the reaction between TEOS and H2O (or the hydrolysis of TEOS) was rather mild. In current aging strategy using water glass as the precursor, some water were added in the ethanol solution of silicon alkoxide, and the TEOS molecule diffusing from the external solution could hydrolyze at a higher rate, thus enhancing silica framework in the hydrogel beads to a better extend. Therefore, this aging procedure can significantly reduce the beads shrinkage during drying and obtain the aerogel beads. Based on the microstructure evolution of aerogels with the aging time, the aging mechanism of water glass based SiO2 hydrogel in TEOS/ethanol/H2O aging solution was proposed (Fig. 8). This aging process is intrinsically different from those of alcogel based powders, films or monolith, because the coexistence of considerable amount of water and TEOS in the pores allows more active hydrolysis and condensation. There were mainly two processes occurring in the gel network during the aging process. The first one (process a) was the neck growth, which had been widely considered as a source of microstructure enhancement.31
This process dominated the early stage of the aging, because the diffusion of TEOS into pore network, was time-demanding and the low concentration of silicon hydroxyl groups (Si(OH)4) was not favorable for the condensation among different Si(OH)4 molecules. Particle necks with concave surfaces could provide preferable condensing spots from the point of energy, and fresh monomers in the pore network preferably attached to the particle necks by direct surface condense, which lead to the growth of necks and the enhancement of the structural strength. With the aging prolonging, more monomers diffused into pores and the condensation among different Si(OH)4 molecules prevailed gradually. As a consequence, the pore structure was enhanced because more skeletons were formed and served as supports that resist shrinkage.
3.7 The test for absorb ability of silica aerogel beads
Fig. 9 is the test for absorb ability of silica aerogel beads. The sample Sil-S (Fig. 9(e)) with a spherical shape was bluish and transparent before adsorption. That silica aerogel beads Sil-S strongly absorbed the dyestuffs RhB and MB (Fig. 9(c) and (d)), which indicates the aerogel has a highly porous structure. The Sil-M beads absorbed dyestuffs is unsaturated while the dark beads is saturated. Besides, the samples had a spherical shape and had no crack on the surface of the beads no matter before or after adsorption. For comparison, the samples Sil-U and Sil-M were also used to absorb the dyestuff (RhB). Fig. 9(a) showed that the sample Sil-M was hard to be saturated by the dyestuff due to the hydrophobicity which cause the infiltration performance with liquid is reduced. Fig. 9(b) showed that the sample Sil-U was cracked after absorbed the dyestuff because of poor mechanical properties. Therefore, neither of the samples Sil-U and Sil-M were suitable for water treatment application. And during the same time, the RhB removal (%) of the sample Sil-S is the highest of the three samples, which indicates the sample Sil-S has broad applying area and well application prospect in water treatment.
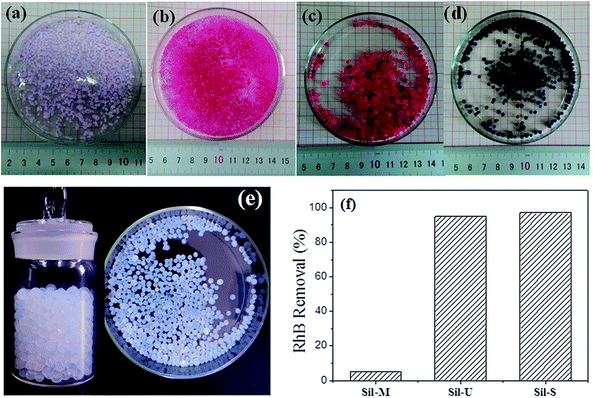 |
| Fig. 9 The test for absorb ability of silica aerogel beads.((a) Sil-M absorbed RhB, (b) Sil-U absorbed RhB, (c) Sil-S absorbed RhB, (d) Sil-S absorbed MB, (e) Sil-S, (f) absorb ability of different silica aerogel of dye RhB). | |
The recyclability of sorbents is key criteria for the adsorption applications. There are two common methods (calcination and solvent decoration) for recycling. For example, for those flammable and useless pollutants, high-temperature calcination is a good choice. The picture of the silica aerogel beads (Sil-S) adsorbed the dye after the calcination is provided (Fig. S1†). After 550 °C calcination, most aerogel beads remained its shape, size, and inherent 3D porous structure. On the other hand, for precious pollutants, solvent decoration is an attractive alternative method.
Furthermore, repeated recycle tests were performed for silica aerogel beads (Sil-S) through solvent decoration (Fig. S2†). In order to demonstrate the cyclic test, the dye (RhB) was adsorbed by using the silica aerogel beads (Sil-S). After that the material was washed by ethanol to release the dye. This sorption–evaporation process was repeated for 8 times. As shown in Fig. S2,† less than 2 wt% of residual dye remained in the silica aerogel after each cycle, and no obvious change of sorption capacity was observed after 8 cycles, indicating a stable sorption and recycling performance of the silica aerogel beads.
3.8 The test for the compressive strength of silica aerogel beads
Aerogels are usually brittle, and therefore owing to the complexity involved during machining and gripping, it is difficult to prepare specimens and conduct testing under tension, torsion, or under multiaxial stresses.1 Usually, aerogels with thickness about 1 cm should be prepared for compression due to the requirement of the superconducting quantum interference device. However, the silica aerogel beads cannot meet the requirements of the device due to the actual shape. In order to test the compressive strength of the aerogel beads (Sil-S), the video (Movie S1†) showed that silica aerogels after three shells of high temperature high pressure autoclave with weight of 5.5 kg was placed on the top of four silica aerogel beads (Sil-S) were provided. It proved that the silica aerogel beads exhibited good mechanical property which is beneficial to practical applications.
4. Conclusions
Hydrophilic mesoporous sodium silicate-based silica aerogel beads were produced by skeleton improvement of wet silica beads by ambient pressure drying. High sphericity silica beads were obtained by rapid gelation of colloidal silica sol in hot dimethyl silicon oil. To minimize shrinkage during drying, wet silica beads were aging by immersing in large volume of tetraethoxysilane(TEOS)–ethanol–water solution. For comparison, wet silica beads without surface modification and skeleton improvement and the wet silica beads modified with trimethylchlorosilane were also dried. We investigated the surface area, pore volume, pore diameter, hydrophobicity, and morphology of the silica beads. Obtained aerogel beads possessed the mesopores pores, with the average pore size of 12.51 nm, the specific surface area of 582.52 m2 g−1, and the pore volume of 1.46 cm3 g−1. This product has better morphology than untreated silica beads and the modified silica beads. This synthesis route that exploits a low-cost silica source (sodium silicate) and skeleton improvement process, is suitable for economic and large-scale industrial production of silica aerogel beads.
Acknowledgements
The authors gratefully acknowledged the National Natural Science Foundation (21306067, 51402130), the Industry High Technology Foundation of Jiangsu Province (BE2013090), the Scientific Innovation Research of College Graduate in Jangsu Province (SJLX_0480, KYLX_1065 and KYXX_0025), the Science & Technology Foundation of Zhenjiang (GY2013046 and GY2014004).
Notes and references
- L. L. Ren, S. M. Cui, F. C. Cao and Q. H. Guo, An easy way to prepare monolithic inorganic oxide aerogels, Angew. Chem., Int. Ed., 2014, 53, 10147–10149 CrossRef CAS PubMed.
- M. A. Aegerter, N. Leventis and M. M. Koebel, Aerogels Handbook, Springer, New York, 2011 Search PubMed.
- J. P. Randall, M. A. B. Measor and S. C. Jana, Tailoring mechanical properties of aerogels for aerospace applications, ACS Appl. Mater. Interfaces, 2011, 3, 613–626 CAS.
- S. M. Jung, H. Y. Jung, M. S. Dresselhaus, Y. J. Jung and J. Kong, A facile route for 3D aerogels from nanostructured 1D and 2D materials, Sci. Rep., 2012, 2, 2849 Search PubMed.
- B. P. Sarawade, J. K. Kim, A. Hilonga and H. T. Kim, Production of low-density sodium silicate-based hydrophobic silica aerogel beads by a novel fast process and ambient pressure drying process, Solid State Sci., 2010, 12, 911–918 CrossRef PubMed.
- R. Xiong, C. H. Lu, Y. R. Wang, Z. H. Zhou and X. X. Zhang, Nanofi brillated cellulose as the support and reductant for the facile synthesis of Fe3O4/Ag nanocomposites with catalytic and antibacterial activity, J. Mater. Chem. A, 2013, 1, 14910–14918 CAS.
- Z. H. Zhou, C. H. Lu, X. D. Wu and X. X. Zhang, Cellulose nanocrystals as a novel support for CuO nanoparticles catalysts: facile synthesis and their application to 4-nitrophenol reduction, RSC Adv., 2013, 3, 26066–26073 RSC.
- P. He, X. D. Gao, X. M. Li, Z. W. Jiang, Z. H. Yang, C. L. Wang and Z. Y. Gu, Highly transparent silica aerogel thickfilms with hierarchical porosity from water glass via ambient pressure drying, Mater. Chem. Phys., 2014, 147, 65–74 CrossRef CAS PubMed.
- D. S. Bhagat, Y. H. Kim, Y. S. Ahn and J. G. Yeo, Textural properties of ambient pressure dried water-glass based silica aerogel beads: one day synthesis, Microporous Mesoporous Mater., 2006, 96, 237–244 CrossRef PubMed.
- B. P. Sarawade, J. K. Kim, A. Hilonga, D. V. Quang, S. J. Jeon and H. T. Kim, Synthesis of sodium silicate-based hydrophilic silica aerogel beads with superior properties: Effect of heat-treatment, J. Non-Cryst. Solids, 2011, 357, 2156–2162 CrossRef PubMed.
- S. Yun, H. J. Luo and Y. F. Gao, Superhydrophobic silica aerogel microspheres from methyltrimethoxysilane: rapid synthesis via ambient pressure drying and excellent absorption properties, RSC Adv., 2014, 4, 4535–4542 RSC.
- P. B. Sarawade, D. V. Quang, A. Hilonga, S. J. Jeon and H. T. Kim, Synthesis and characterization of micrometer-sized silica aerogel nanoporous beads, Mater. Lett., 2012, 81, 37–40 CrossRef CAS PubMed.
- J. Wang, Y. Wei, W. N. He and X. T. Zhang, A versatile ambient pressure drying approach to synthesize silica-based composite aerogels, RSC Adv., 2014, 4, 51146–51155 RSC.
- J. Estella, J. C. Echeverria, M. Laguna and J. J. Garrido, Effects of aging and drying conditions on the structural and textural properties of silica gels, Microporous Mesoporous Mater., 2007, 102, 274–282 CrossRef CAS PubMed.
- Z. F. Jiang, J. M. Xie, D. L. Jiang, Z. X. Yan, J. J. Jing and D. Liu, Enhanced adsorption of hydroxyl contained/anionic dyes on non functionalized Ni@SiO2 core-shell nanoparticles: Kinetic and thermodynamic profile, Appl. Surf. Sci., 2014, 292, 301–310 CrossRef CAS PubMed.
- R. A. Oweini and H. E. Rassy, Synthesis and characterization by FTIR spectroscopy of silica aerogels prepared using several Si(OR)4 and R′′Si(OR′)3 precursors, J. Mol. Struct., 2009, 919, 140–145 CrossRef PubMed.
- W. Wei, X. M. Lü, D. L. Jiang, Z. X. Yan, M. Chen and J. M. Xie, A novel route for synthesis of UV-resistant hydrophobic titania-containing silica aerogels by using potassium titanate as precursor, Dalton Trans., 2014, 43, 9456–9467 RSC.
- F. Zhou, H. Z. Gu and C. F. Wang, Preparation and microstructure of in-situ gel modified expanded vermiculite, Ceram. Int., 2013, 39, 4075–4079 CrossRef CAS PubMed.
- L. J. Wang, S. Y. Zhao and M. Yang, Structural characteristics and thermal conductivity of ambient pressure dried silica aerogels with one-step solvent exchange/surface modification, Mater. Chem. Phys., 2009, 113, 485–490 CrossRef CAS PubMed.
- L. S. White, M. F. Bertino, G. Kitchen, J. Young, C. Newton, R. Al-Soubaihi, S. Saeedcd and K. Saoud, Shortened aerogel fabrication times using an ethanol–water azeotrope as a gelation and drying solvent, J. Mater. Chem. A, 2015, 3, 762–772 CAS.
- A. Li, H. X. Sun, D. Z. Tan, W. J. Fan, S. H. Wen, X. J. Qing, G. X. Li, S. Y. Li and W. Q. Deng, Superhydrophobic conjugated microporous polymers for separation and adsorption, Energy Environ. Sci., 2011, 4, 2062–2065 CAS.
- J. L. Gurav, A. V. Rao, A. P. Rao, D. Y. Nadargi and S. D. Bhagat, Physical properties of sodium silicate based silica aerogels prepared by single step sol–gel process dried at ambient, J. Alloys Compd., 2009, 476, 397–402 CrossRef CAS PubMed.
- W. C. Li, A. H. Lu and S. C. Guo, Control of Mesoporous Structure of Aerogels Derived from Cresol–Formaldehyde, J. Colloid Interface Sci., 2002, 254, 153–157 CrossRef CAS.
- Y. Kong, X. D. Shen, S. Cui and M. H. Fan, Facile synthesis of an amine hybrid aerogel with high adsorption efficiency and regenerability for air capture via a solvothermal-assisted sol–gel process and supercritical drying, Green Chem., 2015, 17, 3436–3445 RSC.
- Y. Zhao and G. H. Tang, Monte carlo study on carbon-gradient-doped silica aerogel insulation, J. Nanosci. Nanotechnol., 2015, 15, 3259–3264 CrossRef CAS PubMed.
- J. L. Mohanan and S. L. Brock, Influence of synthetic and processing parameters on the surface area, speciation, and particle formation in copper oxide/silica aerogel composites, Langmuir, 2003, 15, 2567–2576 CAS.
- S. H. Hyun, J. J. Kim and H. H. Park, Synthesis and characterization of low-dielectric silica aerogel films, J. Am. Ceram. Soc., 2000, 83, 533–540 CrossRef CAS PubMed.
- S. H. Hyun and G. S. Kim, Synthesis and characterization of silica aerogel films for inter-metal dielectrics via ambient drying, Thin Solid Films, 2004, 460, 190–195 CrossRef PubMed.
- P.-J. Yu, M.-H. Lee, H.-M. Hsu, H.-M. Tsai and Y. W. Chen-Yang, Silica aerogel-supported cobalt nanocomposites as efficient catalysts toward hydrogen generation from aqueous ammonia borane, RSC Adv., 2015, 5, 13985–13992 RSC.
- G. S. Kim and S. H. Hyun, Synthesis of window glazing coated with silica aerogel films via ambient drying, J. Non-Cryst. Solids, 2003, 320, 125–132 CrossRef CAS.
- A. S. Dorcheh and M. H. Abbasi, Silica aerogel; synthesis, properties and characterization, J. Mater. Process. Technol., 2008, 199, 10–26 CrossRef PubMed.
Footnotes |
† Electronic supplementary information (ESI) available. See DOI: 10.1039/c5ra08714g |
‡ The first two authors contributed equally to this work. |
|
This journal is © The Royal Society of Chemistry 2015 |
Click here to see how this site uses Cookies. View our privacy policy here.