DOI:
10.1039/C5RA08493H
(Paper)
RSC Adv., 2015,
5, 58655-58662
Study of the effect of a novel high-performance gel polymer electrolyte based on thermoplastic polyurethane/poly(vinylidene fluoride)/polystyrene and formed using an electrospinning technique
Received
7th May 2015
, Accepted 22nd June 2015
First published on 22nd June 2015
Abstract
In this paper, nanofibrous membranes based on poly(vinylidene fluoride) (PVDF) doped with thermoplastic polyurethane (TPU) and polystyrene (PS) are prepared using an electrospinning technique and the corresponding composite gel polymer electrolytes (GPEs) are obtained after activation in liquid electrolyte. Their morphology characteristics and electrochemical performance are systematically investigated using scanning electron microscopy (SEM), a universal testing machine (UTM), thermal analysis (TGA), galvanostatic charge–discharge and electrochemical impedance spectroscopy. The GPE based on TPU/PVDF/PS shows a high ionic conductivity of 5.46 mS cm−1, an electrochemical stability window of 6.3 V, and a first discharge capacity of 169.5 mA h g−1 which is about 99.9% of the theoretical capacity of LiFePO4. The TPU/PVDF/PS films show a high tensile strength (12.8 ± 0.3 MPa) and elongation (99.4 ± 0.2%). With the help of excellent polyelectrolyte complexes, the prepared nanofibrous membranes present superior electrochemical and mechanical performances, which are very promising for application in polymer lithium ion batteries.
1. Introduction
Lithium ion batteries have been investigated widely and deeply during the time of energy source rapid growth, due to their high energy density, high working voltage, non-memory effect, etc. Gel polymer electrolytes (GPEs) play an important part in the comprehensive performance of lithium-ion batteries by determining the interfacial structure, bulk resistance and so on, and have received considerable attention in recent years for application in polymer lithium-ion batteries.1–5
As for the matrix for GPEs, the preparation and the composition of the polymer membrane have significant impact on the performance of the final obtained products.6 Several methods for producing GPEs have been tried to improve the ionic conductivity, such as a phase inversion method, γ-ray irradiation method, solvent casting technique, TIPS technique, and electrospinning technique.7–9 Among these methods, the electrospinning technique which converts the solution of polymer into lots of uniform and slender nanofibers using high voltage is a simple, controllable and efficient approach.10 Furthermore choosing appropriate original materials is also extremely significant for the properties of GPEs.
Poly(vinylidene fluoride) (PVDF) is a semi-crystalline polymer, with anti-oxidation properties, superior thermal porosities, mechanical properties and interfacial stability with lithium metal.11–13 Thermoplastic polyurethane (TPU) belongs to an elastomer class possessing high tensile strength, elasticity as well as low crystallinity. TPU has a two-phase microstructure of soft segments and hard segments. The hard and soft phases are thermodynamically incompatible, which promotes hydrogen bonding within the hard domain involving urethane C
O and N–H moieties on adjacent polymer chain segments. The whole system benefits from these two phases since the hard parts afford spatial stability and the soft phases are conducive to good ionic conductivity owing to that the soft segments didn’t form an ionic cluster after being dissolved in alkali metal.14 Previous studies based on coaggregant like thermoplastic polyurethane (TPU)/linear poly(ethylene oxide) (PEO) (TPU–PEO), thermoplastic polyurethane (TPU)/polyacrylonitrile (PAN) (TPU–PAN) and polyurethane/poly(vinylidene fluoride) (TPU–PVDF) as GPEs for rechargeable lithium batteries have been reported.15–17 In addition, it was found that polystyrene (PS) polymers exhibit the merits of low price, low water absorption, good optic transparency, easy processing, high glass transition temperature, low dielectric loss and high dielectric breakdown field (about 500 mV m−1), which makes these polymers attractive candidates as the polymer matrix for the development of polymer-based dielectric composites.18 Therefore, the GPEs based on PVDF, TPU and PS possess high ionic conductivity and preeminent mechanical stability at ambient temperature.10
In this work, we explore for the first time a novel electrospun membrane prepared from a TPU–PVDF–PS mixture solution. In addition, we make TPU/PS, PVDF/PS and TPU/PVDF/PS mixture solutions into three different membranes. Then the nonwoven films are immersed into 1 M LiClO4–EC/PC liquid electrolyte solution to be activated at room temperature in a glove box. We investigate the ionic conductivity, electrochemical properties, cycle performances and rate capabilities of these electrospun fibrous polymer electrolytes for lithium ion batteries. The results of these experiments demonstrate that the GPE of TPU/PVDF/PS shows a high ionic conductivity of 5.46 × 10−3 S cm−1, with an electrochemical stability up to 6.3 V versus Li+/Li and a first charge capacity of 169.9 mA h g−1, with LiFePO4 as the cathode material. The TPU/PVDF/PS film has the longest elongation of 99.4%, with a maximum breaking tensile strength of 12.8 MPa. Both the tensile strength and elongation at break are excellent.
2. Experimental
2.1 Materials
Thermoplastic polyurethane (TPU, Yantaiwanhua, 1190A), polystyrene (PS, Yangzishihua) and poly(vinylidene fluoride) (PVDF, Alfa Aesar) were dried under vacuum at 80 °C for 24 h. LiClO4·3H2O (AR, Sinopharm Chemical Reagent Co., Ltd.) was dehydrated in a vacuum oven at 120 °C for 72 h. The 1.0 M liquid electrolyte was made by dissolving a certain quality of LiClO4 in ethylene carbonate (EC, Shenzhen Capchem Technology Co., Ltd.)/propylene carbonate (PC, Shenzhen Capchem Technology Co. Ltd.) (1/1, v/v). N,N-Dimethylformamide (DMF) and acetone were of analytical purity and used as received without further treatment.
2.2 Preparation of the TPU/PS, PVDF/PS and TPU/PVDF/PS fibrous membranes
Firstly a certain amount of TPU, PVDF and PS powder (6/6/1, w/w/w) were homogeneously dissolved in a mixture of acetone/N,N-dimethylacetamide (3
:
1, w/w) forming a 10 wt% solution. Then, a 10 wt% PVDF/PS solution and 10 wt% TPU/PS solution were made in the same way, several times. The solutions were electrospun under a high voltage of 24.5 kV and tip-to-collector distance of 15 cm at room temperature, respectively. Porous fibrous films were obtained on the collector plate. The electrospun porous fibrous films were finally dried under vacuum at 80 °C for 12 h.
2.3 Preparation of the gel polymer electrolytes
The thickness of the TPU/PVDF/PS nonwoven films used was ∼100 μm. At room temperature, the dried TPU/PVDF/PS nonwoven films were activated by dipping in 1 M LiClO4–EC/PC liquid electrolyte solutions for 1 h in a glove box filled with argon. The surface of swelled membranes were wiped using filter paper and then gel polymer electrolytes were obtained.
2.4 Membrane characterization
Scanning electron microscopy (SEM, Hitachi S-3500 N, Japan) was used to examine the morphology of the films. The thermal stability of the films was monitored using thermogravimetric analysis (model TQAQ 50, TA Company, USA). The TGA measurements were carried out under a dry nitrogen atmosphere at a heating rate of 20 °C min−1 from 30 to 900 °C.
The mechanical strength of the polymer gel electrolyte films was measured using a universal testing machine (UTM, Instron Instruments). There were some difficulties in surveying the “wet” films (with electrolyte), therefore the tests measured the mechanical properties of the “dry” membrane (without electrolyte). The extension rate was kept at ∼5 mm min−1. The dimensions of the sheet used were 2 cm × 5 cm × 150–250 μm (width × length × thickness). The porosity was investigated by immersing the membranes into n-butanol for 1 h and then calculated using the following relation:
|
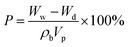 | (A) |
where
Ww and
Wd are the mass of the wet and dry membrane, respectively,
ρb is the density of
n-butanol, and
Vp the volume of the dry membrane.
The electrolyte uptake was determined by measuring the weight increase and calculated according to eqn (B):
|
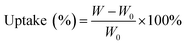 | (B) |
where
W0 is the weight of the dried film and
W is the weight of the swelled film.
The ionic conductivity of the composite film was measured with a SS/PE/SS blocking cell by AC impedance measurements using a Zahner Zennium electrochemical analyzer with a frequency range of 0.1–1 MHz. The thin films were prepared about 100 mm in thickness and 1.96 cm2 in area for the impedance measurements. Thus, the ionic conductivity could be calculated from the following equation:
|
 | (C) |
In
eqn (C),
σ is the ionic conductivity,
Rb is the bulk resistance, and
h and
S are the thickness and area of the film, respectively.
2.5 Cell assembly and performance characteristics
The electrochemical stability was measured using a linear sweep voltammetry (LSV) of a Li/PE/SS cell using a Zahner Zennium electrochemical analyzer at a scan rate of 5 mV s−1, with a voltage from 2.5 V to 7 V. For charge–discharge cycling tests, a Li/PE/LiFePO4 cell was assembled. The LiFePO4 cathode was prepared as a blend with acetylene black and PVDF binder at a ratio of 80
:
10
:
10 by weight. The cell was subjected to electrochemical performance tests using an automatic charge–discharge unit, a Neware battery testing system (model BTS-51, ShenZhen, China), between 2.5 and 4.2 V at 25 °C, at different current densities.
3. Results and discussion
3.1 Morphology and structure
Fig. 1 shows the SEM images of the membranes prepared by electrospinning of the polymer solutions (TPU/PS, PVDF/PS, and TPU/PVDF/PS). It is clear that the membranes are made up of a network of interlaid and nearly straight tubular structure fibers. The fibers of TPU/PS (Fig. 1(a)) are cross linked very stickily and unevenly, with diameter distribution values ranging between 1 μm and 20 μm, and an average fiber diameter of ∼12 μm. As shown in Fig. 1(b), the PVDF/PS nonwoven films (Fig. 1(b)) have many slim and oval beads, with the diameter distribution values ranging between 1 μm and 10 μm, and an average fiber diameter of ∼8 μm, while the fibers of the mix of TPU, PVDF and PS (Fig. 1(c)) are relatively uniform and slender, with diameter distribution values of about 1.5 μm.
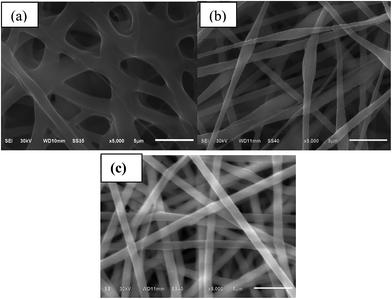 |
| Fig. 1 SEM images of the electrospun membranes (a) TPU/PS, (b) PVDF/PS and (c) TPU/PVDF/PS. | |
Due to rapid evaporation of the solvent during electrospinning, all the membranes present a network structure composed of full interconnection with nanosized fibers. The parameters influencing the morphology of the electrospun fiber membranes include the distance between the nozzle of the syringe and the collector, the applied voltage, the dielectric constant of the solution and the concentration of the polymer solution. However, the only difference made is the component of the electrolyte. The diameter distribution values of the TPU/PVDF/PS membranes are the smallest. We envisage the following reasons. The increased content of PVDF/PS has been attributed to the increasing dielectric constant of the medium for electrospinning. Electrospun jets are easily formed at the nozzle of the syringe for the TPU/PVDF/PS composite solution and cause formation of fibers with the lowest diameter.
3.2 Thermal analysis
Thermograms of the membranes with different compositions are shown in Fig. 2. The TPU/PS membrane and the TPU/PVDF/PS film both start to lose weight at about 300 °C, and the TPU/PS membrane has 6% weight left at 530 °C while the TPU/PVDF/PS film had lost 80% of its mass at 500 °C. The PVDF/PS diaphragm loses weight from 470 °C to 530 °C with a 75% mass reduction. As is shown, the TPU/PVDF/PS films are more stable. This may due to the strong interactions among the three polymer matrixes (TPU, PVDF and PS). The addition of PVDF/PS causes interaction between its fluorine groups and the carbonyls (C
O) and amino-groups (–NH) in TPU. Thus the interactions of the three polymer chains would be stronger and the PVDF/PS chains would restrict the movement of the TPU chains during the glass transition. This enhances the compatibility of TPU/PVDF/PS.
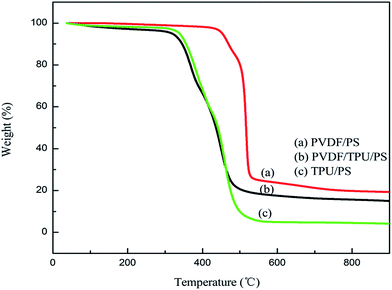 |
| Fig. 2 Thermograms of the (a) TPU/PS, (b) PVDF/PS and (c) TPU/PVDF/PS films. | |
3.3 Porosity, electrolyte uptake and ionic conductivity
The porosity and wettability of the nanofibrous membrane are the important factors for the performance of polymer lithium-ion batteries (Table 1). The results of porosity determination using an n-butanol uptake method are presented in Table 1. The porosity of the TPU/PS membrane was about 48%, and the porosity of the PVDF/PS membrane was 80%. Among all these membranes, TPU/PVDF/PS showed the highest porosity (87%).
Table 1 Surface area, height and porosity of the fibrous membranes
Samples |
Surface area (cm−2) |
Height (cm) |
Porosity (%) |
TPU/PS |
1.988 |
0.014 |
48 |
PVDF/PS |
1.962 |
0.012 |
80 |
TPU/PVDF/PS |
1.861 |
0.012 |
87 |
Fig. 3 shows the uptake behavior of the electrospun fibrous membranes. The percentage of electrolyte uptake can be calculated according to eqn (B). The TPU/PS fibrous film showed an electrolyte uptake of about 120% within 2 min, while for the PVDF/PS membrane this was 275% and for the TPU/PVDF/PS film this was 330%. The uptake of the electrolyte solution reached up to 124% [TPU/PS], 341% [TPU/PVDF/PS] and 280% [PVDF/PS], respectively. After 15 min, it was found that the electrolyte uptake of these three curves become stable. The membrane with TPU/PVDF/PS always has the highest electrolyte uptake percentage.
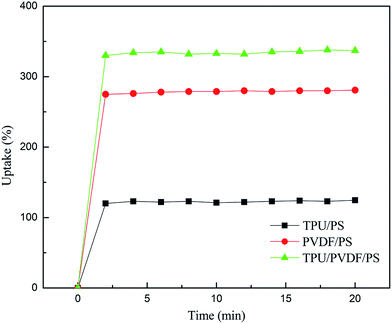 |
| Fig. 3 The uptake behavior of the electrospun fibrous films. | |
Fig. 4 shows the impedance spectrum of the TPU/PVDF/PS based fibrous polymer electrolyte. It is a typical AC impedance for a gel polymer electrolyte. From the morphology of the prepared porous electrospun TPU/PVDF/PS membrane in Fig. 1, it is known that there are many interconnected pores in the porous membrane, so enough liquid electrolyte was absorbed by the polymer membrane to form a gelled polymer electrolyte. Being of improved ionic conductivity, there are three phases in the prepared GPEs, such as the PVDF solid state, the gel state and the absorbed liquid electrolyte state. Due to the high crystalline character of the PVDF polymer chains, the diffusion of lithium ions in the electric field is prevented, and ion conduction mainly occurs through the entrapped liquid electrolyte and the swelling gel layer.19 In addition, the pores are also interconnected by sub-micron windows, which offer channels for the migration of ions and are small enough to well retain the electrolyte solution in the membrane. Obviously, the higher the electrolyte-solution uptake is, the more Li+ ions are in the gelled polymer electrolyte. It is known that ions are current carriers. This may be the reason for the high frequency semicircle disappearing in the impedance spectra. This leads to a further conclusion that the conductivity is mainly the result of ion conduction.20 It can be observed clearly from Fig. 4 that the bulk resistance (Rb) of the TPU/PS fibrous polymer electrolyte is 11.7 Ω. In Fig. 4 the PVDF/PS has a bulk resistance of 3.01 Ω. However, in Fig. 4 the bulk resistance (Rb) of the TPU/PVDF/PS fibrous polymer electrolyte is only 1.18 Ω. The decrease in the average fiber diameter leads to an increase in the absorption ratio of the electrolyte solution, and a higher uptake of the liquid electrolyte, which means more Li+ in the same volume, which leads to a lower bulk resistance (Rb). Through the data in Table 1, the ionic conductivity could be calculated with eqn (C). The ionic conductivity of the TPU/PS and PVDF/PS fibrous polymer electrolytes is 4.78 × 10−4 S cm−1 and 2.03 × 10−3 S cm−1, respectively. However the TPU/PVDF/PS fibrous polymer electrolyte film has an ionic conductivity of 5.46 × 10−3 S cm−1. TPU is a linear polymer material. Its molecular structure is complicated, containing ether groups, ester groups and duplicated carbamate-chains (–R–O–CO–NH–R–NH–CO–O–). The duplicated carbamate-chain (–R–O–CO–NH–R–NH–CO–O–), which is in the hard segments of TPU, offers amino-groups (–NH). So the strong electron-withdrawing functional group (–C–F) which is in the backbone structure of PVDF can form hydrogen bonds with the amino-groups (–NH). The formability and rigidity of PS are excellent. Its molecular structure contains conjugates of benzene, while it avails the migration of lithium-ions. Therefore, the ionic conductivity of the TPU/PVDF/PS fibrous polymer electrolyte film is the most superior.
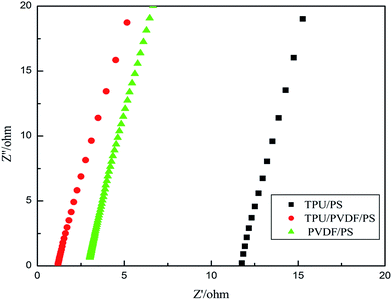 |
| Fig. 4 Impedance spectra of the gel polymer electrolytes. | |
In addition, the main parameters that influence the porosity, electrolyte uptake and ionic conductivity of electrospun fiber membranes are the average fiber diameters and ions carriers. Kim et al. had reported that decreasing the average fiber diameters can result in a decrease in leakage rate.21 This particular structure may result in high electrolyte uptake, porosity and ionic conductivity. The presence of fully interconnected pores in the structure makes it appropriate as a host matrix for the preparation of gel polymer electrolytes.
3.4 Evaluation in a Li/LiFePO4 cell
Fig. 5(a) shows the first charge–discharge capacity curves of the cells with GPEs of different combinations of TPU/PVDF/PS. The charge–discharge curves are similar to what is observed for lithium ion batteries in general, which signifies a good contact between the electrodes and the TPU/PVDF/PS based GPEs. The GPE with TPU/PS delivers a charge capacity of 136.5 mA h g−1 and a discharge capacity of 135.6 mA h g−1, only 80% of the theoretical capacity of LiFePO4. The PVDF/PS gel polymer electrolyte delivers a charge capacity of 155.6 mA h g−1 and a discharge capacity of 153.6 mA h g−1. The TPU/PVDF composite polymer electrolyte shows a charge capacity of 169.9 mA h g−1 and a discharge capacity of 169.5 mA h g−1, which is about 99.9% of the theoretical capacity. The charge–discharge capacities of lithium-ion batteries always depend on the electrode material, electrolyte, and separator. In this work, the only difference is in the polymer electrolytes. From the results, we can find that the TPU/PVDF/PS based GPE delivers a discharge capacity of 169.5 mA h g−1. The increased lithium-ion diffusion ability from the ion-complex may be the reason why the initial capacity of the lithium battery can be improved. As for detailed reasons, a further study is under way.
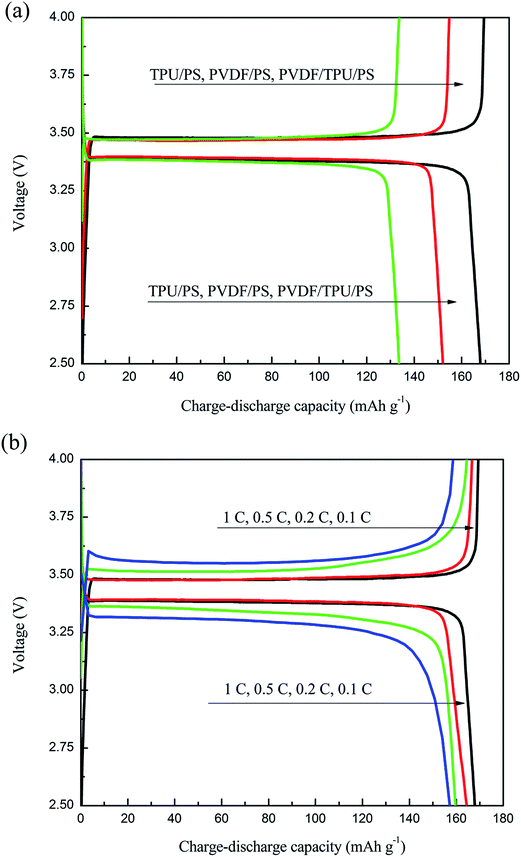 |
| Fig. 5 (a) First charge–discharge capacities of the GPEs based on electrospun TPU/PS, PVDF/PS and TPU/PVDF/PS membranes. (b) First charge–discharge capacities of the GPEs based on an electrospun TPU/PVDF/PS membrane at different capacity rates (1C = 170 mA h g−1). | |
Furthermore, we studied the charge–discharge capacity of the cell with a GPE of TPU/PVDF/PS at different current rates, and the results can be seen from Fig. 5(b). It is noted that the charge and discharge capacities of LiFePO4 are 169.9 and 169.5 mA h g−1 at 0.1C. Although the discharge capacities decrease with the increasing current rates due to the higher polarization at higher current densities, the anode material still exhibits high discharge capacities of 166.8, 161.9 and 160.1 mA h g−1 at relatively smaller current rates of 0.2, 0.5 and 1C. The Li cell with the GPEs has been evaluated for its cycle ability properties under the 0.1C rate at 25 °C and the cycling performances of batteries with the three kinds of GPEs are shown in Fig. 6(a). The batteries using the different kinds of GPEs show a relatively stable performance with little capacity fading. Compared to the cells with GPEs containing TPU/PS and PVDF/PS in Fig. 6(a), the cell with the TPU/PVDF/PS based GPE in Fig. 6(a) has the highest discharge capacity in the whole 50 cycles and exhibits a significantly improved cycle performance. After 50 cycles, the battery with the GPE based on TPU/PVDF/PS retains 97% of the initial discharge capacity, while the batteries with GPEs based on the TPU/PS and PVDF/PS nanofibrous membranes deliver 85% and 90% of the initial discharge capacity. There is no evident capacity fading of the cell with the TPU/PVDF/PS based GPE after a few cycles. This suggests that the cell exhibits a better reversibility. Maybe this results from a better stabilization of the system as a whole. This study shows that electrospun TPU/PVDF/PS based GPEs are very suitable for Li/LiFePO4 cells under low current densities (0.1C) at room temperature.
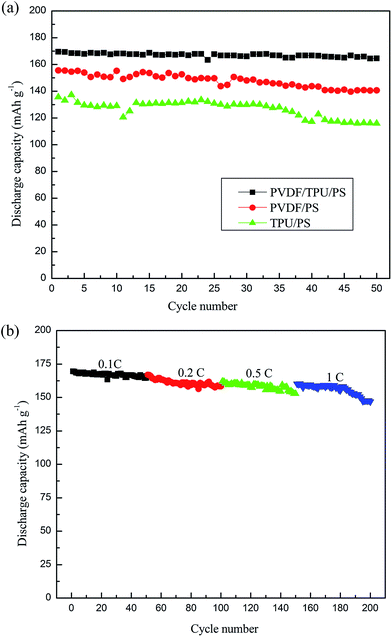 |
| Fig. 6 (a) The cycle performance (discharge capacities) of the GPEs based on electrospun TPU/PS, PVDF/PS and TPU/PVDF/PS membranes. (b) The cycle performance (discharge capacities) of the GPE based on an electrospun TPU/PVDF/PS membrane at different capacity rates. | |
At the same time, the cycle performance of the cells with GPEs of TPU/PVDF/PS at different current rates from 0.1 to 1C was investigated and the results are illustrated in Fig. 6(b). At lower current rates (0.2C), the capacity retentions are close to 96% after 50 cycles. Even at a high rate of 1C, the capacity retention is as high as 93% and the cell still maintains a discharge capacity of 146 mA h g−1 after 50 cycles. The outstanding electrochemical performance of the GPEs is attributed to the particular morphology and structure of TPU/PVDF/PS of nanofibers, high porosity and no microphase separation of the mingling among TPU, PVDF and PS.
The results of the evaluation in Li/LiFePO4 cells indicate that the electrochemical performance of the composite gel polymer electrolytes is further enhanced with the interacting of TPU/PVDF/PS. This may be due to the strong interactions among the polymer matrixes (TPU, PVDF and PS). The molecular structure of PS contains olefin-chains (R–C
C) and benzene (p–π) chains. Thus the interaction of the polymer chains would be stronger. Perhaps for two reasons: first, the PVDF chains would restrict the movement of the TPU chains during the glass transition, and second, the interactions between the PS chains and the hard segments of TPU make the whole system better and better.
3.5 Electrochemical stability
The results of electrochemical stability tests of the gel polymer electrolytes using LSV are shown in Fig. 7. The electrochemical stability of the TPU/PS and PVDF/PS fibrous polymer electrolytes is at 4.7 V and 5.6 V. While the stability of the TPU/PVDF/PS gel polymer electrolyte is further enhanced. Their electrochemical stability follows the order: membrane of TPU/PS (4.7 V) < PVDF/PS (5.6 V) < TPU/PVDF/PS (6.3 V). From Fig. 7, we can obviously see that the gel polymer electrolyte of TPU/PVDF/PS shows the best electrochemical stability. The decomposition process, which is associated with the electrode/electrolyte, results in the onset of current flow in the high voltage range. This onset voltage is the upper limit of the electrolyte stability range. There is almost no electrochemical reaction in the potential range from 2.5 V to 6.3 V for the TPU/PVDF/PS gel polymer electrolyte. The better electrochemical stability may be due to a better compatibility between the liquid electrolyte and nanofirbrous membranes with less leakage of the liquid electrolyte. Therefore, the swollen phase of the membrane probably includes complex compounds such as associated VdF-Li+ groups. This complex formation with lithium ions and VdF groups of PVDF enhances the electrochemical stability of the GPEs. The electrochemical stability was also influenced by the large and fully interconnected pores, high porosity, higher specific surface area, uniform morphology of the membranes and average fiber diameters. The oxidation stability of the GPE increased with the decreasing of the average fiber diameters. So the gel polymer electrolyte of TPU/PVDF/PS shows the best electrochemical stability. These polymer electrolytes should render very suitable for applications in lithium-ion batteries because of the high anodic stability.14,22
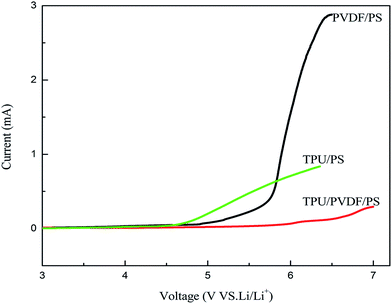 |
| Fig. 7 Linear sweep voltammograms of the gel polymer electrolytes. | |
3.6 Mechanical properties
Fig. 8 shows the stress–strain curves of the polymer membranes. The results of the mechanical strength tests show that the hybrid fillers improved the mechanical performance of the membranes. The PVDF/PS membrane extended only 68.8% with a maximum breaking tensile strength of 6.44 MPa. Referring to the TPU/PS film, the membrane had 86.8% elongation and was broken under a 9.83 MPa tensile strength. While the mixed film has the longest elongation of 99.4%, it can bear tensile strength below 12.8 MPa. Both the tensile strength and elongation of the mixed films at break were enhanced. The reasons are as below. The copolymers fabricated with TPU, PVDF and PS are homogeneous and symphysic. There is no microphase separation of the intermixing TPU, PVDF and PS in the electrospun film and in consequence it has a great contact area with the polymeric matrix. When the material is struck, the greater microcracking will absorb more impact energy. So further expansion of the cracks is blocked.
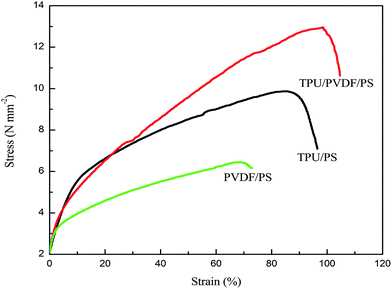 |
| Fig. 8 Stress–strain curves of the electrospun PVDF/PS, TPU/PS and TPU/PVDF/PS membranes. | |
As we all know, elongation at break often reflects the impact performance of a material and the impact resistance is shown by the material toughness. A higher toughness in the mechanical properties will reduce the risk of collapse of the membrane, which suggests that the membrane prepared through polymers TPU, PVDF and PS is more suitable for application in polymer lithium ion batteries.
4. Conclusions
GPEs based on fibrous TPU/PVDF/PS composite membranes were prepared by electrospinning the 10 wt% polymer solution in DMF/acetone (3
:
1, w/w) at room temperature. The optimum blend composition was observed for the electrolyte TPU/PVDF/PS. PS is a kind of outstanding polymer which is beneficial for the migration of ions. With the addition of PS, the performances of the polymer electrolyte membranes have been improved obviously. The GPEs based on TPU/PVDF/PS have a high ionic conductivity of 5.46 × 10−3 S cm−1, with an electrochemical stability up to 6.3 V versus Li+/Li at room temperature. The first discharge capacity of the TPU/PVDF/PS based gel polymer electrolyte lithium battery is about 169.5 mA h g−1, which is relatively close to the theoretical capacity of LiFePO4. This is a remarkable enhancement in performance since the GPEs are able to serve for lithium ion polymer batteries. After 50 cycles the cell shows a very stable charge–discharge behavior and little capacity loss under constant current voltage conditions, at the 0.1C rate at 25 °C. The TPU/PVDF/PS mixed film has the longest elongation of 99.4%, and it can bear tensile strength below 12.8 MPa. As is shown above, the cell with the TPU/PVDF/PS based gel polymer electrolyte displays superior potential and is very suitable for rechargeable lithium batteries.
Acknowledgements
The authors gratefully appreciate the financial support from the Youth Project of National Nature Science Foundation of China (no. 51203131).
References
- J. Y. Song, Y. Y. Wang and C. C. Wan, J. Power Sources, 1999, 77, 183–197 CrossRef CAS
. - H. P. Zhang, P. Zhang, Z. H. Li, M. Sun, Y. P. Wu and H. Q. Wu, Electrochem. Commun., 2007, 9, 1700–1703 CrossRef CAS PubMed
. - X. J. Wang, J. J. Kang, Y. P. Wu and S. B. Fang, Electrochem. Commun., 2003, 5, 1025–1029 CrossRef CAS PubMed
. - L. Z. Fan and J. Maier, Electrochem. Commun., 2006, 8, 1753–1756 CrossRef CAS PubMed
. - F. Croce, L. Settimin and B. Scrosati, Electrochem. Commun., 2006, 8, 364–368 CrossRef CAS PubMed
. - W. L. Li, Y. J. Xing, Y. H. Wu, J. W. Wang, L. Z. Chen, G. Yang and B. Z. Tang, Electrochim. Acta, 2015, 151, 289–296 CrossRef CAS PubMed
. - C. R. Yang, Z. D. Jia, Z. C. Guan and L. M. Wang, J. Power Sources, 2009, 189, 716–720 CrossRef CAS PubMed
. - P. Raghavan, J. W. Choi, J. H. Ahn, G. Cheruvally, G. S. Chauhana, H. J. Ahn and C. Nah, J. Power Sources, 2008, 184, 437–443 CrossRef CAS PubMed
. - R. Prasanth, N. Shubha, H. H. Hng and M. Srinivasan, J. Power Sources, 2014, 245, 283–291 CrossRef CAS PubMed
. - N. Wu, Q. Cao, X. Y. Wang, X. Y. Li and H. Y. Deng, J. Power Sources, 2011, 196, 8638–8643 CrossRef CAS PubMed
. - W. W. Cui, D. Y. Tang and Z. L. Gong, J. Power Sources, 2013, 223, 206–213 CrossRef CAS PubMed
. - Y. S. Zhu, S. Y. Xiao, Y. Shi, Y. Q. Yang and Y. P. Wu, J. Mater. Chem. A, 2013, 1, 7790–7797 CAS
. - L. Zhou, N. Wu, Q. Cao, B. Jing, X. Y. Wang, Q. Wang and H. Kuang, Solid State Ionics, 2013, 249–250, 93–97 CrossRef CAS PubMed
. - L. Zhou, Q. Cao, B. Jing, X. Y. Wang, X. L. Tang and N. Wu, J. Power Sources, 2014, 263, 118–124 CrossRef CAS PubMed
. - H. H. Kuo, W. C. Chen, T. C. Wen and A. Gopalan, J. Power Sources, 2002, 110, 27–33 CrossRef CAS
. - Y. L. Du and T. C. Wen, Mater. Chem. Phys., 2001, 71, 62–69 CrossRef CAS
. - P. Santhosh, T. Vasudevan, A. Gopalan and K.-P. Lee, Mater. Sci. Eng., B, 2006, 135, 65–73 CrossRef CAS PubMed
. - C. Yang, Y. H. Lin and C. W. Nan, Carbon, 2009, 47, 1096–1101 CrossRef CAS PubMed
. - W. Wieczorek, J. R. Stevens and Z. Florjahczyk, Solid State Ionics, 1996, 85, 67–72 CrossRef CAS
. - M. Jacob, S. Prabaharan and S. Radhakrishna, Solid State Ionics, 1997, 104, 267–276 CrossRef CAS
. - J. R. Kim, S. W. Choi, S. M. Jo, W. S. Lee and B. C. Kim, Electrochim. Acta, 2004, 50, 69–75 CrossRef CAS PubMed
. - N. Wu, Q. Cao, X. Y. Wang, S. Li, X. Li and H. Deng, J. Power Sources, 2011, 196, 9751–9756 CrossRef CAS PubMed
.
|
This journal is © The Royal Society of Chemistry 2015 |
Click here to see how this site uses Cookies. View our privacy policy here.