DOI:
10.1039/C5RA07952G
(Paper)
RSC Adv., 2015,
5, 52710-52717
Modification with boehmite-derived alumina nanoparticles enhances mechanical properties of resin
Received
30th April 2015
, Accepted 8th June 2015
First published on 8th June 2015
Abstract
Nanostructured γ-Al2O3 with an average particle size of 90 nm was synthesized by coated silica in solution. As a type of hard template, the coated silica shell layer could decrease the sinter of alumina particles during the phase transition process at 550 °C. The average particle size of γ-Al2O3 is significantly affected by boehmite concentration, amount of sodium silicate, and layers of silica. The mechanical properties of waterborne acrylic resin were enhanced significantly after the addition of γ-Al2O3 nanoparticles with dispersant (SK-5040). For solvent-based polyurethane resin, the surface of γ-Al2O3 nanoparticles needed to be modified by stearic acid to achieve proper dispersion and stability. For comparison, the effect of different fillers (including ZnO, TiO2 and SiO2) was also tested under the same conditions.
1. Introduction
Paint is widely used in our daily life, and can protect and decorate metal and wood etc. Scratch-resistance is a major indicator in the paint industry, especially for automotive paint. To improve the performance of the paint, various metals and oxide nanoparticles were added into paints that are known as nanocomposite coatings. Nanocomposite coatings have received much attention because of the considerable improvement in abrasion, scratch, UV resistance, thermal stability and flame retardancy, as well as other mechanical properties.1–7
Nanostructured oxides were widely used as additives in the coating industry, such as alumina (Al2O3), silica (SiO2), titania (TiO2), zinc oxide (ZnO) and calcium carbonate (CaCO3).8,9 Alumina were selected as nanoparticle additives as they are known not only for their hardness on Mohs' scale (9 and 7, respectively), but also for their excellent scratch and abrasion properties imparted to coatings upon their addition.10 P. Kardar et al. studied the effect of nanoalumina particles on mechanical properties, including scratch resistance, hardness and gloss, of UV-cured epoxy acrylate.11 K. D. Shailesh et al. presented the effect of addition of nanoalumina as pigment on the performance of alkyd-based waterborne coating.12
However, it is very difficult to synthesize γ-Al2O3 lower than 100 nm, because nanoparticles of alumina is very prone to sintering during the phase transformation from AlOOH to γ-Al2O3. To prepare nanostructured γ-Al2O3 particles (typically < 100 nm), preventing the reaction of the M–OH groups on the surface of boehmite (AlOOH) powder during the heating process appears critically important to avoid excessive grain growth and aggregation.13–15 C. Graf et al. presented a method to coat colloids with silica, such as metals (gold, silver and iron), metal oxides (kaolinite, TiO2, iron oxide and alumina), polystyrene, silica, graphite and cellulose.16 L.-T. Cheng et al. prepared α-Al2O3 nanoparticles by coating boehmite on the surface of θ-Al2O3.13 M. P. B. van Bruggen reported that nanostructured γ-Al2O3 particles could be synthesized by coating a thin layer of silica.17
In addition, because of their extremely large surface/particle size ratio, nanoparticles tend to agglomerate strongly. Hence, it is necessary to disperse nanoparticles without aggregation in organic resin and to yield a better compatibility between the nanoparticles and the polymeric materials. One approach is adding the dispersant by a physical method, such as polymer dispersant or inorganic polymers.18,19 The other approach is surface modification on nanoparticles with different silica coupling agents and fatty acid by chemical methods.9,20–22 Surface treatment could guarantee a durable chemical junction between two incompatible phases by formation of chemical physical interactions with polymer resin. Therefore, in the acrylate resin SK-5040 (poly(carboxylic acid) salt) was chosen as dispersant and in the polyurethane resin the surface of γ-Al2O3 nanoparticles was modified by stearic acid.
This paper mainly focus on the synthesis of nanostructured γ-Al2O3 by coated silica in solution and its effect on the properties of acrylic resin and polyurethane resin. As shown in Fig. 1, nanostructured γ-Al2O3 was prepared by a two-step coating procedure with sodium silicate and tetraethoxysilane, especially. The silica layer, as a physical barrier, weakened hardness agglomeration of particles caused by sintering during the heating process. Then, the effects of γ-Al2O3 nanoparticles as filler on scratch resistance, hardness and gloss of polyurethane resin and acrylate resin were studied. For comparison, the properties of the nanocomposite coating with the addition of other metal oxides (silica, titania and zinc oxide) were evaluated.
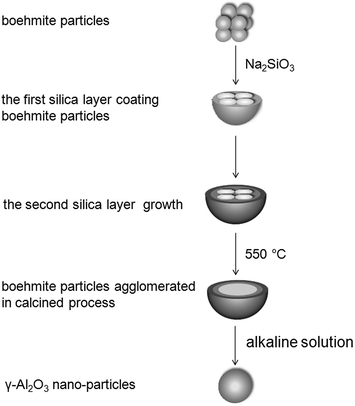 |
| Fig. 1 Scheme of the general procedure for the coating of boehmite with silica. | |
2. Experimental methods
Boehmite (AlOOH) with an average size of 25 nm were purchased from Hangzhou Wan Jing New Material Company. Zinc oxide, titanium(IV) oxide and silica (200 nm diameter) were also obtained from Hangzhou Wan Jing New Material Company. Sodium silicate and tetraethoxysilane (TEOS, ≥ 98%) were obtained from Tianjin Guangfu Fine Chemical Research Institute. SK-5040 was purchased from Beijing Shouchuang Nano Technology Company.
2.1. Preparation of nanostructured γ-Al2O3 and nanocomposite coating
2.1.1. Preparation of nanostructured γ-Al2O3. The synthesis of nanostructured γ-Al2O3 involves two main steps: (1) boehmite particles are coated with silica; (2) silica layer is removed. First, boehmite was dispersed in deionized water to obtain the desired concentration solution. Then, hydrochloric acid was added to adjust the pH value of the solution to 5–6. Second, 3 wt% sodium silicate solution was added to a solution of boehmite with a peristaltic pump under vigorous stirring until the pH value of the solution to 10.0–10.5. Then, the above mixed solution was stirred at room temperature for 2 h. Third, the second silica coating was achieved by direct addition of TEOS solution, in which the volume ratio of TEOS to anhydrous ethanol was 1/9, and then the TEOS solution was injected rapidly into the mixture under vigorous stirring at 50 °C. Fourth, after stirring for 2 h, the sample was centrifuged at 8000 r min−1. Subsequently, the resulting product was washed three times with anhydrous ethanol, then dried at 80 °C, and calcined at 550 °C for 2 h in air atmosphere. Finally, the calcined powders were added to 0.5 mol L−1 NaOH solution stirred for 5 h, and then the slurry was filtered and washed several times with deionized water until the pH value of the solution to 7, after which the wet material was dried at 80 °C for 5 h.
2.1.2. Surface modification of γ-Al2O3 nanoparticles. 5.0 g of γ-Al2O3 nanoparticles were dried under vacuum for 12 h at 100 °C and then dispersed in 40 mL anhydrous ethanol with the aid of ultrasonication for 60 min. In addition, 2 g of stearic acid were added to 10 mL anhydrous ethanol under stirring until the stearic acid was completely dissolved. Subsequently, the stearic acid solution was added dropwise to the nanostructured γ-Al2O3 slurry. The reaction mixture was then refluxed at 120 °C for 5 h. The sample was centrifuged and then the residual sediment was stirred in anhydrous ethanol for 10 min, and the whole process was repeated three times. The purpose was to remove stearic acid on the modified surface of nanoparticles by physical adsorption. The nanoparticles were finally dried in a low-pressure oven at 80 °C for 12 h.
2.1.3. Preparation of nanocomposite coating. Two types of paint system were investigated in this paper. Paint A was a waterborne system, in which the weight ratio of waterborne acrylic resin to deionized water was 2
:
1. Unmodified γ-Al2O3 nanoparticles were added to deionized water in various concentrations, namely 0 wt%, 1.0 wt%, 2.0 wt%, 3.0 wt%, 4.0 wt% and 5.0 wt%, with aid of ultrasonication for 60 min. The obtained slurry was introduced to the acrylic resin slowly. To achieve proper dispersion and compatibility, SK-5040 (1.0 wt% of γ-Al2O3) was added to the clear resin solution. The dispersion was performed mechanically using a stirrer for 5 h at room temperature.Paint B was a solvent-based system, in which the weight ratio of the solvent-based polyurethane resin to the solvent mixture was 2
:
1. The solvent mixture consisted of 1-butanol (65 wt%), butyl acetate (20 wt%), and cyclohexanone (15 wt%). Modified γ-Al2O3 nanoparticles (0 wt%, 1.0 wt%, 2.0 wt%, 3.0 wt%, 4.0 wt% and 5.0 wt% of polyurethane resin) were added to the solvent mixture under ultrasonication. The obtained slurry was mixed with polyurethane resin and then was stirred for 5 h at room temperature.
2.2. Characterization and test
Powder X-ray diffraction (XRD) was performed on a Bruker D8 focus diffractometer, with Cu Kα radiation at 40 kV and 40 mA. The transmission electron microscope (TEM) images were acquired using a Philips Tecnai G2 F-20 field emission gun TEM. Scanning electron microscope (SEM) images were acquired using a TESCAN VEGA3 SBH. Fourier transform infrared analysis (FTIR) was performed on a Bruker Tensor 37. The compositions of the sample were measured by inductively coupled plasma-atomic emission spectrometry (ICP-AES). The particle sizes of γ-Al2O3 nanoparticles were determined using Malvern Zetasizer Nano-ZS90 laser particle analyzers. The obtained γ-Al2O3 nanoparticles were mixed with deionized water to form slurries with a dilute concentration (0.05 wt%) of solids for the determination of particle size. Nanocomposite films were painted on glass and stainless steel plates using a pneumatic spray gun and then dried at 140 °C for 4 h. The thickness of the film was about 40–60 μm. The scratch resistance of the films was measured using a QHZ scratch tester equipped with a tip of 1 mm diameter. The applied load was varied in the range of 50–2000 g. The hardness was measured using a QBY hardness tester and was determined from eqn (1):where t is the time required for the pendulum to move from 5° to 2° on the cured film and t1 is the damping time (440 s).
The influence of nanoparticles on the optical properties of dried nanocomposite coatings was determined in terms of 60° gloss by means of a glossmeter (GLOSSMETER, KGZ-60).
3. Results and discussion
3.1. Synthesis of nanostructured γ-Al2O3
Fig. 1 shows the general procedure for the coating of boehmite with silica. The synthesis of nanostructured γ-Al2O3 involves coating and removal of silica. Fig. 2 shows the SEM and TEM images of different samples. As shown in Fig. 2a, the γ-Al2O3 particles obtained by directly calcined boehmite particles at 550 °C are sintered irregular bulk solids (5–20 μm). The phase transition to γ-alumina is accompanied by severe agglomeration because of sintering. Therefore, it is important to preserve morphology of boehmite during the phase transformation process is essential to obtain nanostructured γ-Al2O3 particles. The silica layer, as a physical barrier, covered on the surface of boehmite and effectively weakened hard agglomeration of particles caused by sintering. This procedure include coating step of sodium silicate and further coating step of tetraethoxysilane (TEOS). Fig. 2b shows that the SEM image of γ-Al2O3 particles coated by silica layers. The amorphous silica deposited on the surface of γ-Al2O3 particles and impeded the aggregation of γ-Al2O3 particles into substantially large grain size during the phase transformation process. After washing in the NaOH solution, γ-Al2O3 nanoparticles was about 90 nm in size, as shown in Fig. 2c. Obviously, compared with uncoated γ-Al2O3 particles, the size of γ-Al2O3 particles coated by silica decreased significantly. Fig. 2d shows the TEM image of boehmite precursor, which has an average size of 25 nm. Comparison of the results in Fig. 2d and e, we can see that γ-Al2O3 particles were synthesized from several boehmite particles. To study the composition of the obtained γ-Al2O3 particles, ICP-AES was used to detect the content of the impurity ions (sodium and silicon). The amounts of sodium and silicon ions in the products are 0.02 wt%, and 0.07 wt%, respectively. The ICP-AES result indicates that washing with deionized water can remove most of the sodium and silicon ions.
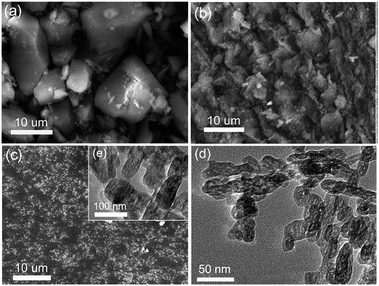 |
| Fig. 2 SEM and TEM images of different samples, (a) SEM image of uncoated γ-Al2O3 particles, (b) SEM image of silica-coated γ-Al2O3 particles without washing, (c) SEM image of silica-coated γ-Al2O3 particles with washing, (d) TEM image of boehmite precursor, (e) TEM image of silica-coated γ-Al2O3 particles with washing. | |
As shown in Fig. 3, XRD patterns also indicated that the silica-coated γ-Al2O3 consisted of γ-Al2O3 particles and silica layer. The silica layer, as a physical barrier, prevents interaction among the M–OH groups of the γ-Al2O3 surface by hydrogen ion adsorption and/or formation of hydrogen bonding at the interface.
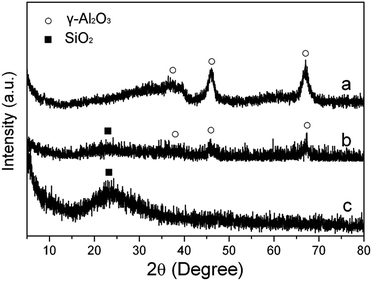 |
| Fig. 3 XRD patterns of (a) the silica-coated γ-Al2O3 particles with washing, (b) the silica-coated γ-Al2O3 particles without washing, (c) the amorphous SiO2 calcined at 550 °C. | |
Fig. 4 shows the particle sizes distribution of different samples dispersed in water. The γ-Al2O3 particles obtained by directly calcined boehmite particles at 550 °C are sintered irregular bulk solids, which have an average size of 4874 nm (Fig. 4a). The γ-Al2O3 particles obtained by two-step silica coated procedure have smaller size than that of obtained by one-step silica coated procedure (Fig. 4b and c). More than 80% of the synthesized particles were within the size range from 30 nm to 110 nm. The nanostructured γ-Al2O3 nanoparticles have good dispersion and stability in deionized water. M. P. B. van Bruggen has done detailed studies that addition of extra sodium silicate to already coated rods did not result in growth of the silica layer. It appeared that once a layer of silica has formed, no more silica, at any pH value ranging from 5 to 9, deposits on the particles.23 Therefore, in the second step of the coating we use TEOS as silicon source to produce a second layer.
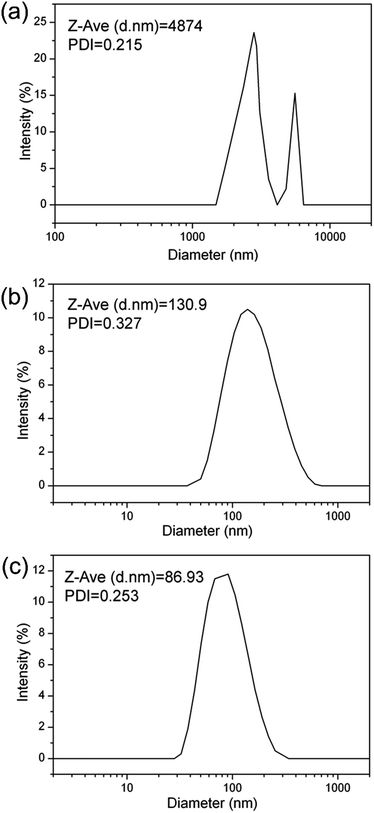 |
| Fig. 4 Particle-size distribution of (a) uncoated γ-Al2O3 particles in water, (b) obtained by one-step procedure coated γ-Al2O3 particles, (c) obtained by two-step procedure γ-Al2O3 particles. | |
In order to investigate the impact of various concentrations of boehmite solution, a series of γ-Al2O3 were prepared using coated silica at different boehmite concentrations (6, 12, 18, 24, 30, and 50 g L−1). As shown in Fig. 5, average particle size of γ-Al2O3 gradually increased with increasing concentration of boehmite. Number of boehmite particles in the same volume is increased with increasing concentration of boehmite. Because of Brownian motion, collide with each other becomes more easily between the particles. Thus, they are more prone to form aggregates larger size secondary aggregates, which led to the increase in γ-Al2O3 particle size, and particle size distribution becomes wider.
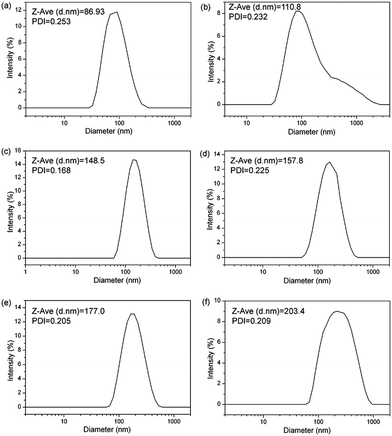 |
| Fig. 5 Particle-size distribution of γ-Al2O3 prepared using coated silica at different boehmite concentrations: (a) 6 g L−1, (b) 12 g L−1, (c) 18 g L−1, (d) 24 g L−1, (e) 30 g L−1, (f) 50 g L−1. | |
To further study the influence of the amount of sodium silicate to theγ-Al2O3 particle size, a series of γ-Al2O3 were prepared at different sodium silicate content in water (30, 40, 50, 60, and 70 g 3.0 wt% sodium silicate solution). As shown in Fig. 6, average particle size of γ-Al2O3 gradually decreased with amount of sodium silicate increasing, and the particle size distribution becomes concentrated (20–200 nm). Average particle size of γ-Al2O3 almost has no change when the amount of sodium silicate solution more than 60 g (Fig. 6d). The results prove that boehmite particles have been completely encapsulated by silica layer at this time.
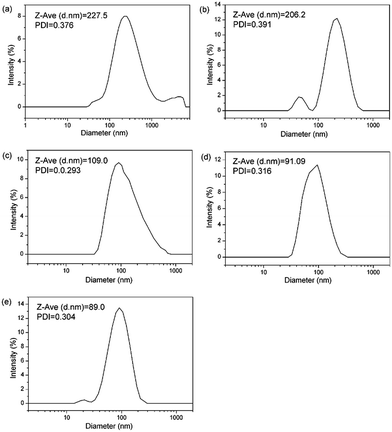 |
| Fig. 6 Particle-size distribution of γ-Al2O3 at different amount of 3.0 wt% sodium silicate solution: (a) 30 g, (b) 40 g, (c) 50 g, (d) 60 g, (e) 70 g. | |
3.2. Dispersion and stability test in paint A and paint B
It was easy to cause soft aggregation of nanoalumina particles in waterborne acrylic resin because of the extremely large surface/particle size ratio. Therefore, SK-5040, which was consisted of poly (carboxylic acid) salt, as a polymer dispersant was introduced to paint A. The effect of SK-5040 was that its anchor groups could form multipoint adsorption on the surface of nanostructured γ-Al2O3 by ionic bonds, covalent bonds and hydrogen bonds. Then, a single-molecule layer or multimolecule layer was generated as a protective film.24 Therefore, the tendency of aggregation among the particles greatly weakened. As can be seen from Fig. 7a, nanostructured γ-Al2O3 particles can uniformly disperse in relatively high-viscosity acrylic resin (2.0 wt% γ-Al2O3 and 1.0 wt% SK-5040). In addition, Fig. 7b shows that paint A remained stable after 10 days and produced only a little clear supernatant appeared on the top of the sample after 20 days.
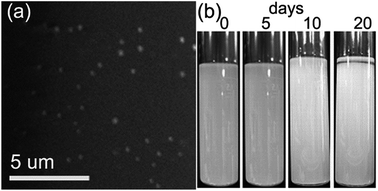 |
| Fig. 7 (a) SEM image of unmodified γ-Al2O3 particles in paint A (2.0 wt% γ-Al2O3 and 1.0 wt% SK-5040), (b) photos of unmodified γ-Al2O3 particles in paint A after various days. | |
In the paint B system, the superhydrophobic alumina surface was fabricated using stearic acid. Therefore, the modified γ-Al2O3 nanoparticles can yield a better dispersion and stability in solvent-based polyurethane resin, as can be seen from Fig. 8a and b. Paint B remained stable for 20 days. Fig. 8c shows the FTIR spectra of unmodified γ-Al2O3 nanoparticles, stearic acid-modified γ-Al2O3 nanoparticles and pure stearic acid. In the spectrum of stearic acid-modified nanostructured γ-Al2O3, new peaks appeared in the regions 1457.5 and 1558 cm−1, which are caused by vibration of COO–Al.25 This spectrum confirmed the condensation reaction between the carboxyl groups of stearic acid and the γ-Al2O3 surface hydroxyl groups.
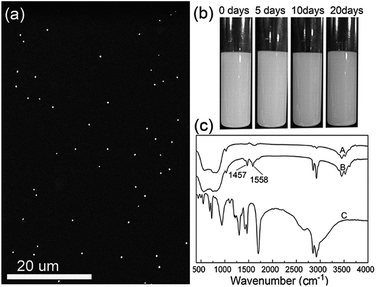 |
| Fig. 8 SEM image of γ-Al2O3 particles in paint A (b) stability of 3 wt% (solid particles of the resin) nanocomposite coating γ-Al2O3 particles in paint A (c) FTIR spectra of (A) unmodified nano γ-Al2O3 (B) stearic acid-modified nano γ-Al2O3 (C) pure stearic acid. | |
3.3. Effect of nanostructured γ-Al2O3 on mechanical and optical properties measurements
3.3.1. Scratch resistance. The scratch resistance of the nanocomposite was evaluated by incorporating nanoparticles (alumina, silica, zinc oxide and titanium(IV) oxide) at different concentrations, including 0 wt%, 1.0 wt%, 2.0 wt%, 3.0 wt%, 4.0 wt% and 5.0 wt% of the resin. As can be seen from Fig. 9, the presence of nanoparticles had a considerable effect on scratch resistance of paint A and paint B. Obviously, nanostructured γ-Al2O3 is a preferred oxide in coatings to improve scratch resistance compared with silica, zinc oxide and titanium(IV) oxide at the same content. It is known that the Mohs value of alumina is higher than that of the other three metal oxides. The embedded nanostructured Al2O3 particles have better interaction with the base matrix forming a hard coating, which does not allow them to be released from the matrix during the abrasive action, thereby improving the scratch and abrasion resistance of the coatings.12
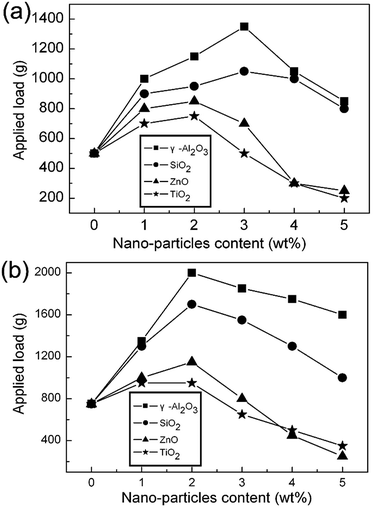 |
| Fig. 9 Effect of various nanostructured particles on scratch resistance of (a) the paint A coating, (b) the paint B coating. | |
The microscopic morphology of paint B/nanoalumina coating interacting with the resin is shown in Fig. 10. In addition, as its active surface has intensely adsorbed molecular chains, the hard particles have an effect on bearing parts of the load when it fractures, as can be seen from Fig. 10.7,26–28
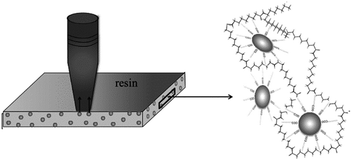 |
| Fig. 10 Modified nanostructured alumina dispersion in the paint B. | |
It was also found that there was a noticeable transition point at a certain content. From the study shown in Fig. 9a, for low concentrations of γ-Al2O3 nanoparticles in the paint A coating, the extent of abrasion of the coating is reduced. The scratch resistance at the γ-Al2O3 nanoparticles concentration of 3.0 wt% reached the optimum and then began to decrease with further increase in the filler concentration. Fig. 9b shows that in the paint B coating, a turning point appeared at a concentration of 2.0 wt%. It was consistent with what we expected. Excess γ-Al2O3 nanoparticles in turn might cause a greater roughness on the surface of the films. The binding force between nanoalumina and the paint weakened. Therefore, nanoalumina easily fell off in the wear process and then the effect of antiscratch was lost.
3.3.2. Hardness. Similarly, the effect of nanoparticles on the hardness of the paint A coating and the paint B coating, including alumina, silica, zinc oxide and titania, are presented in Fig. 11 It can be seen that the formulation with nanoparticles showed higher hardness. Nanostructured γ-Al2O3 was the preferred oxide in coatings to increase hardness compared with silica, zinc oxide and titanium(IV) oxide at the same content. This can be attributed to the surface roughness and also to the elastic–plastic deformation of the films. In addition, nanostructured γ-Al2O3 has a high surface concentration of active sites and is strongly combined with the resin. It is this feature that increases the cross-link density of the cured films.28,29 As discussed earlier, the Mohs value of alumina is higher than those of the other three types of metal oxide. Therefore, the hardness of the cured film with nanostructured γ-Al2O3 is also higher than those with zinc oxide, titanium(IV) oxide and silica.
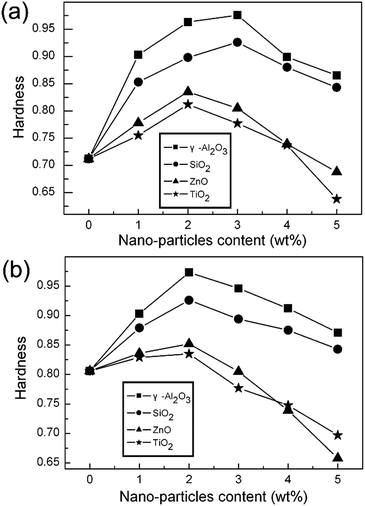 |
| Fig. 11 Effect of various nanostructured particles on hardness of (a) the paint A coating, (b) the paint B coating. | |
Fig. 11 also shows that the hardness was evaluated for the various γ-Al2O3 particle concentrations: 0 wt%, 1.0 wt%, 2.0 wt%, 3.0 wt%, 4.0 wt% and 5.0 wt%. As can be seen, there was a similar trend in the paint A coating and in the paint B coating in comparison with the scratch resistance. There was a noticeable transition point at a certain concentration. The hardness reached the optimum when the concentration of nanostructured γ-Al2O3 was 3.0 wt% in the paint A coating and 2.0 wt% in the paint B coating. However, the hardness of the film began to decrease with a further increase in the nanostructured γ-Al2O3 content. With the increase of nanostructured γ-Al2O3 particles in the paint, on the one hand, the binding force between nanostructured γ-Al2O3 and the paint was destroyed. On the other hand, the presence of excess nanoparticles can affect the rheology of the wet films, and therefore the surface of the films having nanoparticles might have a greater roughness.
3.3.3. Hardness. The gloss of the cured films without and with nanostructured γ-Al2O3 was also determined to evaluate the effect of the nanoparticles on the appearance of the films. As can be seen in Fig. 12, the gloss of films with the nanoparticles remains high except that it decreases to some extent for the samples with the zinc oxide and the titanium(IV) oxide.
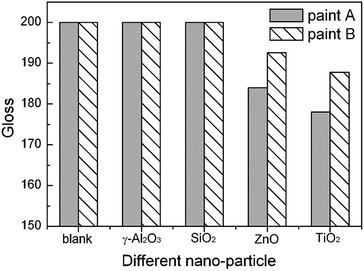 |
| Fig. 12 Effect of various nanostructured particles to gloss of the paint A coating and the paint B coating. | |
Fig. 13 shows that the 60° gloss of dried nanocomposite coatings decreased with an increase of nanoparticle content. In the paint A coating, the gloss began to reduce when 5.0 wt% of γ-Al2O3 nanoparticles was introduced, and in the paint B coating, the phenomenon was even more obvious. The reduction of gloss is attributed to an increase of surface roughness because of the presence of the particles and aggregates. Such surface roughness decreases the diffuse reflection of visible light.30
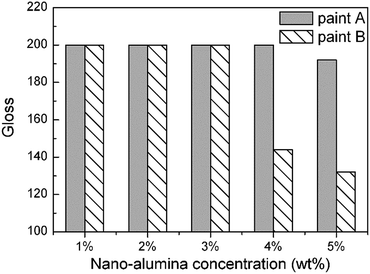 |
| Fig. 13 Effect of nanostructured alumina concentrations to gloss of the paint A coating and the paint B coating. | |
4. Conclusions
Nanostructured γ-Al2O3 was prepared by coating boehmite needles with a thin layer of silica. Starting with a colloid-on-colloid adsorption process in the first coating step, the coating process was gradually changed to molecular growth, finally yielding the second layer silica using TEOS. The silica layer decreases the sinter of alumina nanoparticles during the phase transformation. A good dispersion was expected to be the key to achieving suitable properties. SEM demonstrated that the dispersion of γ-Al2O3 nanoparticles in paint A and paint B was efficient. The effect of alumina nanoparticles on the mechanical and optical properties of the acrylic resin and the polyurethane was investigated and compared with other nanometer materials. The results indicate that the scratch resistance of the film is improved in the presence of nanostructured γ-Al2O3. The scratch resistance respectively reaches optimum when the concentration of nanostructured γ-Al2O3 is 3.0 wt% of the resin in the paint A system and is 2.0 wt% of the resin in the paint B system. In addition, the film hardness is also increased when γ-Al2O3 nanoparticles are included in the formulation. Similarly, the hardness reaches optimum when the concentration of nanostructured γ-Al2O3 is 3.0 wt% of the resin in the paint A system and is 2.0 wt% of the resin in the paint B system. Finally, it was observed that films having γ-Al2O3 nanoparticles still had a very high gloss before the concentration of the particles reached 4.0 wt%.
Acknowledgements
This work was financially supported by the NSFC (21376123, U1403293), MOE (IRT-13R30 and 113016A), NSFT (15JCQNJC05500), and the Research Fund for 111 Project (B12015).
References
- M. Natali, G. Carta, V. Rigato, G. Rossetto, G. Salmaso and P. Zanella, Electrochim. Acta, 2005, 50, 4615–4620 CrossRef CAS PubMed
. - I. Corni, N. Neumann, S. Novak, K. König, P. Veronesi, Q. Chen, M. P. Ryan and A. R. Boccaccini, Surf. Coat. Technol., 2009, 203, 1349–1359 CrossRef CAS PubMed
. - Z. Z. Wang, P. Gu and Z. Zhang, Wear, 2010, 269, 21–25 CrossRef CAS PubMed
. - L. Sung, J. Comer, A. Forster, H. Hu, B. Floryancic, L. Brickweg and R. Fernando, J. Coat. Technol. Res., 2008, 5, 419–430 CrossRef CAS
. - C. Y. H. Lim, D. K. Leo, J. J. S. Ang and M. Gupta, Wear, 2005, 259, 620–625 CrossRef CAS PubMed
. - M. L. Nobel, S. J. Picken and E. Mendes, Prog. Org. Coat., 2007, 58, 96–104 CrossRef CAS PubMed
. - S. K. Dhoke, R. Bhandari and A. S. Khanna, Prog. Org. Coat., 2009, 64, 39–46 CrossRef CAS PubMed
. - C. Sow, B. Riedl and P. Blanchet, J. Coat. Technol. Res., 2011, 8, 211–221 CrossRef CAS
. - M. Sabzi, S. M. Mirabedini, J. Zohuriaan-Mehr and M. Atai, Prog. Org. Coat., 2009, 65, 222–228 CrossRef CAS PubMed
. - J. Hajas, P. Lenz and K. Schulte, Proc. RadTech Europe Conference and Exhibition, B. GmbH, Germany, Barcelona, SP, October, 2005 Search PubMed
. - P. Kardar, M. Ebrahimi and S. Bastani, Prog. Org. Coat., 2008, 62, 321–325 CrossRef CAS PubMed
. - S. Dhoke, T. Mangal Sinha and A. Khanna, J. Coat. Technol. Res., 2009, 6, 353–368 CrossRef CAS PubMed
. - L. Cheng, M. Tsai, W. J. Tseng, H. Hsiang and F. Yen, Ceram. Int., 2008, 34, 337–343 CrossRef CAS PubMed
. - S. Ananthakumar, V. Raja and K. G. K. Warrier, Mater. Lett., 2000, 43, 174–179 CrossRef CAS
. - A. P. Philipse, A. Nechifor and C. Patmamanoharan, Langmuir, 1994, 10, 4451–4458 CrossRef CAS
. - C. Graf, D. L. J. Vossen, A. Imhof and A. van Blaaderen, Langmuir, 2003, 19, 6693–6700 CrossRef CAS
. - M. P. B. van Bruggen, M. Donker, H. N. W. Lekkerkerker and T. L. Hughes, Colloids Surf., A, 1999, 150, 115–128 CrossRef CAS
. - L. Wu, Y. Huang, Z. Wang and L. Liu, J. Eur. Ceram. Soc., 2010, 30, 1327–1333 CrossRef CAS PubMed
. - H. Li, Y. Yan, B. Liu, W. Chen and S. Chen, Powder Technol., 2007, 178, 203–207 CrossRef CAS PubMed
. - L. Feng, H. Zhang, P. Mao, Y. Wang and Y. Ge, Appl. Surf. Sci., 2011, 257, 3959–3963 CrossRef CAS PubMed
. - K. G. Gatos, J. G. M. Alcázar, G. C. Psarras, R. Thomann and J. Karger-Kocsis, Compos. Sci. Technol., 2007, 67, 157–167 CrossRef CAS PubMed
. - M. Z. Rong, M. Q. Zhang, G. Shi, Q. L. Ji, B. Wetzel and K. Friedrich, Tribol. Int., 2003, 36, 697–707 CrossRef CAS
. - M. P. B. van Bruggen, Langmuir, 1998, 14, 2245–2255 CrossRef CAS
. - Y. Fan, X. Bao, H. Wang, C. Chen and G. Shi, J. Catal., 2007, 245, 477–481 CrossRef CAS PubMed
. - N. Sarier, E. Onder and S. Ersoy, Colloids Surf., A, 2010, 371, 40–49 CrossRef CAS PubMed
. - S. K. Dhoke and A. S. Khanna, Corros. Sci., 2009, 51, 6–20 CrossRef CAS PubMed
. - H. Hsiang, Y. Chang, C. Chen and F. Yen, Appl. Surf. Sci., 2011, 257, 3451–3454 CrossRef CAS PubMed
. - P. Kardar, M. Ebrahimi and S. Bastani, Prog. Org. Coat., 2008, 62, 321–325 CrossRef CAS PubMed
. - A. Shafiei-Zarghani, S. F. Kashani-Bozorg and A. Z. Hanzaki, Wear, 2011, 270, 403–412 CrossRef CAS PubMed
. - S. Chen, B. You, S. Zhou and L. Wu, J. Appl. Polym. Sci., 2009, 112, 3634–3639 CrossRef CAS PubMed
.
|
This journal is © The Royal Society of Chemistry 2015 |
Click here to see how this site uses Cookies. View our privacy policy here.