DOI:
10.1039/C5RA07096A
(Paper)
RSC Adv., 2015,
5, 56171-56180
A novel biobased plasticizer of epoxidized cardanol glycidyl ether: synthesis and application in soft poly(vinyl chloride) films†
Received
20th April 2015
, Accepted 18th June 2015
First published on 19th June 2015
Abstract
A novel plasticizer derived from cardanol, and epoxied cardanol glycidyl ether (ECGE), was synthesized and characterized by 1H-NMR and 13C-NMR. The effects of ECGE combined with the commercial plasticizer dioctyl phthalate (DOP), in soft poly(vinyl chloride) (PVC) films, were studied. The mechanical properties of PVC films showed both tensile strength and percent elongation increases with increasing ECGE content. Thermogravimetric analysis (TGA) was performed to characterize the thermal stabilities of the plasticized samples and showed the stability of films increased on increasing the content of ECGE. The properties of volatility, extraction, and exudation resistance of plasticizers were tested and analysis by means of solubility parameters as reported in the literature suggests the ECGE has similar or higher stability for these properties than DOP. FTIR analysis of the films also revealed that ECGE interacted with PVC. Due to its inherent chemical backbone and the modified epoxy groups, ECGE properly balanced the properties and improved the performance of PVC films compared with the neat DOP plasticizer.
1. Introduction
Poly(vinyl chloride) (PVC) is one of the most important synthetic resins in terms of consumption. It has been widely used in various applications from rigid to soft products because of its high versatility, excellent durability and contamination resistance.1,2 Since PVC is rigid, brittle, and has low thermal stability, it has to be compounded with plasticizers in order to possess the mechanical properties, process ability, and thermal stability required for product quality specifications. Consequently, plasticizers have become the most consumable additives in PVC. During the last decade, the worldwide production of plasticizers was around 5 million tons per year,3 among which phthalates play an important role and account for more than 80% due to their good performance and low cost.4 However, in recent years, phthalates have been criticized for their potentially toxic effects on human health and environmental impact.5–10 For this reason, some countries have implemented restrictive regulations regarding the use of phthalates in flexible PVC products, especially the products used by children.11 The use of phthalates is incontrovertibly becoming more limited. Hence, there is a trend to replace phthalates by alternative plasticizers and mixtures.12–16 Currently, there is growing interest in the research and use of natural-based plasticizers which are characterized by low toxicity and low migration levels. They mainly include modified and epoxidized triglyceride oils from soybean oil, linseed oil, sunflower oil, glycerol monoester, and fatty acid esters.17–20 As the plastics industry and environmental awareness continues to grow, there is an urgent and unmet need to develop new natural plasticizers with improved properties and cost competitiveness.
Due in part to its versatile chemical structure and low cost, cardanol can be considered to be a very promising raw-material to develop new derived materials to be used in environmentally friendly processes.11,21 Cardanol is an extracted product from cashew nut shell liquid, which is one of the most commonly used renewable agricultural resource materials.22 Cardanol and its derivatives usually have major applications in bio-composites,23 synthetic resins,24,25 epoxy curing agents,26 and coatings.27–30 Recently, cardanol has been used as a plasticizer in the polymer and rubber industries, with or without modification, and has shown significant plasticizing effects.31,32 Furthermore, cardanol-based plasticizers have been reported to be a kind of efficient plasticizer for PVC. Greco et al.11,33 have prepared cardanol acetate and epoxidated cardanol acetate plasticizers through esterification and epoxidation modification. The results indicated that the epoxidated cardanol acetate showed a complete miscibility with PVC, and the cardanol acetate can be used as secondary plasticizer of PVC and partially replace DEHP.
In this study, a novel cardanol derived plasticizer, epoxidized cardanol glycidyl ether (ECGE), was synthesized through the substitution of a hydroxyl group and double bonds in cardanol with a glycidyl ether group and an epoxy group. The rationale behind designing ECGE lies in the fact that cardanol provides the main chemical structure of a rigid aromatic core and flexible alkyl chains, which is similar to phthalate. It can be modified by addition of epoxy groups to improve its compatible properties with PVC (Scheme 1). The ECGE was expected to improve the plasticizing effect, thermal stability and exudation resistance on PVC compounds in a similar manner to commercial phthalate and epoxy plasticizers. Another consideration is that epoxy plasticizers are used as secondary plasticizers in soft PVC34 because they contain unreacted double bonds. Hydroxyl groups formed via epoxidation hydrolysis might increase the migration of the plasticizer from PVC products when used in large amounts. Therefore, we focused on the effects of the partial substitution of ECGE for dioctyl phthalate (DOP) in soft PVC films. Moreover, the mechanical properties, thermal behaviors, and exudation resistance properties of plasticized PVC films were investigated.
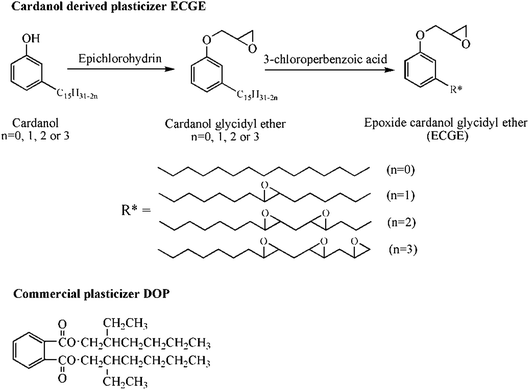 |
| Scheme 1 The compounds used in this study and the conversion of cardanol into ECGE. | |
2. Experimental
2.1 Materials
Cardanol was procured from Shanghai Meidong Biological Materials Co., Ltd. (Shanghai, China) and was purified by distillation using a Pascal 2105 SD vacuum pump (Asslar, Germany) at 220–230 °C under 3–5 Torr. The product obtained was pale yellow in color, which contained 3.6% triene, 62.1% diene, 25.7% monoene, and 3.1% saturated compounds. Epichlorohydrin (99%), sodium hydroxide (97+%), calcium oxide (98%), benzyltriethylammonium chloride (97%), dichloromethane (99%), and DOP (99%) were purchased from Sigma-Aldrich Co. (St Louis, MO). 3-Chloroperbenzoic acid was obtained from Anhui Wotu Chemical Co., Ltd., (Hefei, Anhui, China). PVC (DG-1000K) was purchased from the Tianjin Dagu Chemical Co., Ltd., (Tianjin, China) with average degree of polymerization of 1010–1050, apparent density of 0.57 g mL−1, volatile of 0.16%, whiteness of 80% (160 °C, 10 min), residue VCM content of 0.2 μg g−1. Calcium stearate and zinc stearate were supplied by Changzhou Huaren Chemical Co., Ltd., (Jiangsu, China).
2.2 Preparation
2.2.1 Preparation of ECGE. To a 250 mL flask equipped with a magnetic stirrer, reflux condenser and thermometer were charged: 5.00 g (17 mmol) of CD, 12.25 g (132 mmol) of epichlorohydrin, and 0.09 g (0.485 mmol) benzyltriethylammonium chloride. The final mixture was slowly heated to 95 °C and remained at that temperature for 2.5 h. After the mixture was cooled to 60 °C, 0.66 g (0.017 mmol) sodium hydroxide and 1.23 g (0.017 mmol) calcium oxide were added. The reaction was allowed to continue at 60 °C for 3 h. The excess and unreacted epichlorohydrin, which is moderately toxic, could be recycled and reused by distillation from the crude product. Therefore even if scale-up the process the toxicity of product and environmental pollution could be reduced. After the solids were filtered, 5.22 g cardanol glycidyl ether (CGE) was obtained. Next, 3.57 g (10 mmol) CGE was added in a 100 mL three-necked round bottom flask equipped with a magnetic stirrer, thermometer sensor and reflux condenser. A mixture of 15 g (176 mmol) dichloromethane and 2.59 g (15 mmol) 3-chloroperbenzoic acid was added slowly into the flask. The resultant solution was allowed to react at 30 °C for 3 h. After the reaction was complete, the crude product was filtered and washed with a saturated solution of sodium sulfite, sodium bicarbonate, and sodium chloride solution, respectively. Finally, the organic phase was dried with anhydrous magnesium sulfate and then filtered. The filtrate was distilled under vacuum to recycle the dichloromethane and 3.29 g yellowish liquid was obtained (yield: 78% relative to cardanol). The ECGE has a density of 1.03 g cm−3, epoxy value of 5.87% and acid value of 0.72 mg g−1. The main byproduct of the epoxidation process was chlorobenzoic acid which is an organic intermediate with moderately toxic. The dichloromethane is low toxicity and can be recycled. Although the epoxidation using the 3-chloroperbenzoic acid as oxygen source is efficient and relatively green, more attention should be paid to the safety issue of the 3-chloroperbenzoic acid when scale-up.
2.2.2 Preparation of plasticized PVC test specimens. A series of plasticized PVC specimens with different plasticizers at different concentrations were prepared. The compositions are shown in Table 1. First, PVC powder (100 g), plasticizers (40 g), and thermal stabilizers (2.0 g, Ca soap/Zn soap = 3/1) were mixed using a mechanical mixer at room temperature (RT) for 5 min. Second, the mixture was compounded into a homogeneous mixture at 160 °C for 5 min by a Plasti-Corder Lab-Station (South Hackensack, NJ). Finally, the films were made using a Carver 3969 mini hot press (Wabash, IN) at 170 °C for 5 min.
Table 1 Formulation of the soft PVC films
Component |
Formulations |
S0 |
S1 |
S2 |
S3 |
PVC (g) |
100.00 |
100.00 |
100.00 |
100.00 |
ECGE (g) |
0.00 |
4.00 |
8.00 |
12.00 |
DOP (g) |
40.00 |
36.00 |
32.00 |
28.00 |
Calcium stearate (g) |
1.50 |
1.50 |
1.50 |
1.50 |
Zinc stearate (g) |
0.50 |
0.50 |
0.50 |
0.50 |
2.3 Characterizations
1H and 13C NMR spectra of the compounds in deuterated chloroform (CDCl3) were recorded with a Bruker 400 MHz spectrometer (Bruker, Rheinstetten, Germany) at RT.
Fourier transform infrared (FTIR) analysis was conducted using a Thermo Nicolet Nexus 470 spectrometer (Thermo Scientific, Madison, WI). The samples were scanned from 4000 to 500 cm−1.
Tensile test was measured according to ASTM standard D638, type V, using an Instron 4201 equipped with a 1 kN electronic load cell. The cross-head speed was set at 10 mm min−1. All samples were conditioned at 23 °C and 50% humidity for 1 day prior to tensile testing. Five sample pieces were prepared from each group to obtain an average value.
Hardness of specimens was measured using Rex Gauge H-1000-SP Shore A Durometer (Buffalo Grove, IL). Five measures were performed to obtain an average value.
Volatility property was evaluated by placing a PVC sample (20 mm × 20 mm × 1 mm) were placed in a convection oven (Waltham, MA) at 70 °C for 24 h and cooled to RT in a desiccator for 2 h. The weight changes were measured before and after the heating.
The extraction resistance to water, hexane, NaOH, and acetic acid were measured. The samples (20 mm × 20 mm × 1 mm) were soaked in water, hexane, 5% (w/w) NaOH, and 4% (w/w) acetic acid at 23 °C for 24 h. After being rinsed with flowing water, the samples were dried in a convection oven (Waltham, MA) at 30 °C for 24 h. The weight losses before and after the dipping were measured.
Exudation of the plasticizer was evaluated by placing a sample (20 mm × 20 mm × 1 mm) between two pieces of filter paper. These systems were then placed in a convection oven (Waltham, MA) at 40 °C for 72 h. The weights of the films were measured after washing the surfaces of the films with acetone and drying at RT. The weight changes before and after washing were calculated.
Thermogravimetric analysis (TGA) was carried out on a Q500 TGA (TA Instruments, New Castle, DE). Each sample was scanned from ambient temperature to 400 or 600 °C at a heating rate of 5, 10, 15, 20, and 25 °C min−1, respectively. The TGA experiment was performed under a 60 mL min−1 nitrogen flow. The kinetic parameters such as activation energy (Ea, kJ mol−1) and pre-exponential factor (A) were evaluated by the Kissinger equation:
|
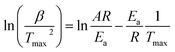 | (1) |
where
R = gas constant (8.314 J mol
−1 K).
Eqn (1) indicates that ln(
β/
Tmax2) and 1/
Tmax are in a linear correlation.
E and
A can be calculated from the slope (
a) and intercept (
d) on the curves of ln(
β/
Tmax2) change
versus 1/
Tmax.
|
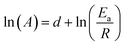 | (3) |
3. Results and discussion
3.1 Characterization
Fig. 1 and 2 display the 1NMR and 13C NMR of cardanol and ECGE, respectively. The characteristic peaks at 6.7–7.3 ppm correspond to the proton on the benzene ring. Compared to the spectrum of cardanol (Fig. 1(a)) and ECGE (Fig. 1(b)), the peaks at 5.2–5.5 ppm, corresponding to the proton of –CH
CH– and –OH, have almost disappeared. This indicates that the phenolic hydroxyl group and unsaturated double bonds on the side chain have been converted. Additionally, the new peaks at 2.76, 3.38, 4.00, and 4.20 ppm indicate the existence of a glycidyl ester in ECGE.35 Furthermore, the peaks at 2.9–3.1 ppm corresponding to the proton of the –CH–O–CH group have appeared on the 1H NMR spectrum of ECGE, also indicating the occurrence of epoxidation. The changed chemical shift of the peaks at 1.2–1.8 ppm also supports the production of epoxidized groups after the epoxidation reaction. The 13C NMR chemical shift peaks at 126.44–137.11 ppm are present in Fig. 2(a) but have disappeared in the spectrum shown in Fig. 2(b). Likewise, the glycidyl ester group and the –CH–O–CH group are distinct between cardanol and ECGE. The chemical shifts of the three carbons in the glycidyl ester group occurred at 44.90, 50.24, and 68.60 ppm, respectively.36 The new peaks at 56.91 ppm correspond to the carbons in the –CH–O–CH group.
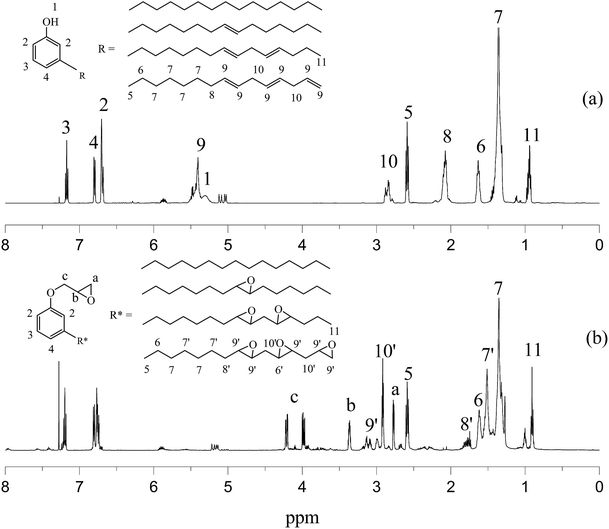 |
| Fig. 1 1H NMR spectra of (a) cardanol and (b) ECGE. | |
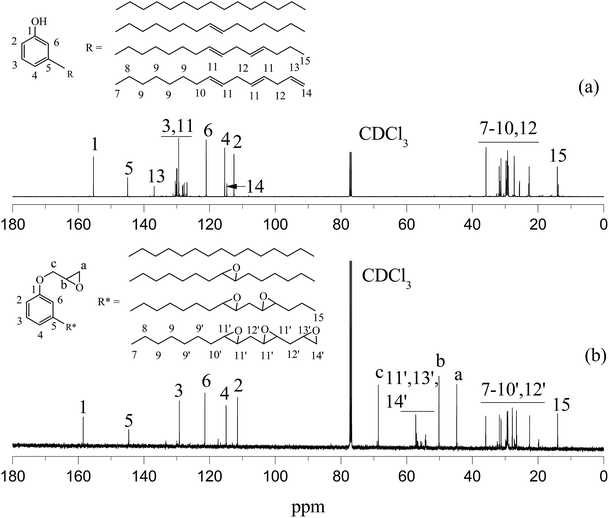 |
| Fig. 2 13C NMR spectra of (a) cardanol and (b) ECGE. | |
3.2 Mechanical properties
The changes in tensile strength, percent elongation, Young's modulus and Shore hardness of the obtained plasticized PVC samples are shown in Table 2. It is observed that almost all the properties of films S1–S3 increased with the increasing of ECGE content. Moreover, compared with film S0, films S1–S3 have better tensile strength, percent elongation, and toughness properties, but poor Young's modulus properties. These results might be attributed to the molecular features of the plasticizers.11,37 By having a higher ECGE content, more polar groups (e.g., epoxy, aromatic ring, terminal glycidyl ether) and longer alkyl chains are incorporated into the PVC matrix. The polar groups of the plasticizers interact with the polar parts of the PVC molecule, reducing the PVC–PVC interactions at sites where polymer chains could associate37 (as shown in Fig. 3), and increasing the space between polymer molecules. Furthermore, the motion of long alkyl chains of ECGE will also create more free volume in the polymer. Compared with pure DOP, added ECGE will increase the random motion of the PVC chains in the non-associated regions of the polymer, as well as the volume of the amorphous part of the plasticized flexible PVC. After adding 10% ECGE, the percent elongation of film S1 is greatly improved to 969.19%, showing 16.48% more flexibility when compared to pure DOP and PVC. However, continued increasing of the ECGE concentration slightly decreases the percent elongation. This may be due to a measurement error,38 but still implies that the influence of flexible alkyl chains might be balanced with that of the rigidity group when 30% ECGE was added. Hence, it can be concluded that the ECGE showed higher plasticization efficiency than DOP, and film S2 showed the highest percent elongation value of 981.58%. In other words, much less plasticizer of this formulation is needed in order to get the same elongation value as film S0.
Table 2 Results obtained from tensile measurements and shore hardness
Sample |
Tensile strength (N mm−2) |
Percent elongation (%) |
Young's modulus (MPa) |
Shore hardness (HA) |
S0 |
22.90 ± 1.51 |
832.05 ± 46.29 |
5.98 ± 0.23 |
91.4 ± 0.29 |
S1 |
22.87 ± 0.46 |
969.19 ± 21.52 |
4.99 ± 0.092 |
91.0 ± 0.51 |
S2 |
24.25 ± 0.45 |
981.58 ± 48.63 |
5.11 ± 0.125 |
91.0 ± 0.22 |
S3 |
24.38 ± 0.68 |
981.53 ± 36.32 |
5.17 ± 0.10 |
91.1 ± 0.20 |
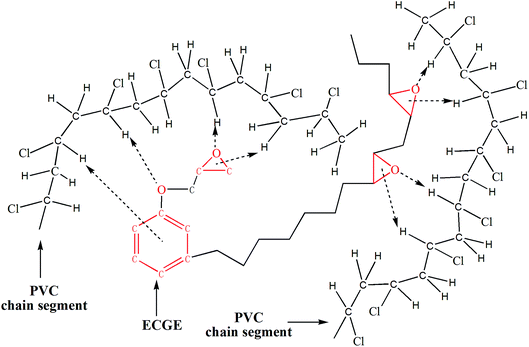 |
| Fig. 3 Possible interaction between ECGE and PVC molecular in the plasticized system. | |
Young's modulus dropped in films S1–S3 compared with that of film S0, indicating the rigidity decreased with the introduction of ECGE. It attributed to the higher efficiency of ECGE on enhancing the free volume of the amorphous part in the flexible product. On the other hand, with the increase of ECGE content, more rigid groups were present and the Young's modulus relatively increased within films S1–S3, indicating the high content ECGE can bestow upon the plasticized PVC with a relative high level of rigidity.
Table 2 also shows the tensile strength increased with the increase of ECGE concentration, indicating the enhancement of the strength of the PVC matrix. Film S3 has the highest tensile strength of 24.383 MPa, which is 6.46% higher than film S0. This result corresponded to Bargellini's report that the tensile strength is related to the magnitude of the plasticizers polarity,2,37 which also changed with the plasticizers proportions. It can be concluded that the addition of ECGE provides not only a significant improvement in flexibility and toughness, but also an improvement in the strength of PVC compounds. Furthermore, Table 2 indicates that the films contain ECGE show slightly lower hardness than that of S0, which means they still have relatively good wettability and long life. All the mechanical research results suggest that ECGE can endow PVC resin with well-balanced properties of flexibility, toughness, strength and hardness, and can improve the applicability of the finished flexible product.
3.3 Material characterization by FTIR
FTIR spectra of the PVC film samples were obtained and are shown in Fig. 4. The FTIR spectra shifted according to chemical compound and can indicate the interaction between the plasticizers and PVC.39 In the spectrum of film S0, there are some characteristic peaks: C
O stretching at 1721, C
C aromatic stretching at 1599 and 1578 cm−1, CH2–Cl angular deformation at 1427 cm−1, CH3 and CH2 groups deformation at 1379 and 1331 cm−1, CH–Cl out of plane angular deformation at 1257 cm−1, C–H aromatic deformation at 1270 and 1118 cm−1, C–O stretching at 1122 and 1073 cm−1, C–H out of plane trans deformation at 960 cm−1, and C–Cl bond stretching at 833, 694, and 615 cm−1. These bonds are in accordance with data found in the literature for PVC.40 After the incorporation of ECGE into the formulations, two obvious variations have been found in the spectrum of films S1–S3. First, the characteristic features of the CH–Cl gradually shifted lower (maximum 3 cm−1 lower) with the increase of ECGE content. This result can be explained by eqn (4) derived from Hooke's law:41 |
 | (4) |
where v is the vibration frequency, k is the force constant, and m is the mass. Eqn (4) shows the relationship of force constant to the wave number (vibration frequency). As the wave number decreases, the force constant decreased, indicating the intermolecular bonding force of PVC–PVC was weakened when the polar functional groups in ECGE interacted with the PVC. Second, the absorption frequencies of the glycidyl ether group and epoxide groups in ECGE shifted from 910–855 cm−1 to 858 cm−1. This phenomenon can be mainly attributed to the formation of the hydrogen bonds between the polar parts of ECGE (benzene ring, glycidyl ether group and epoxy groups) and the PVC (carbon–chloride bond). This is consistent with Fig. 3, therefore, it can be concluded that the mixed plasticizers of ECGE and DOP can interact with PVC as expected.
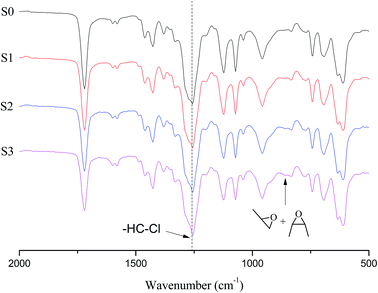 |
| Fig. 4 FTIR spectra of PVC films with different plasticizers. | |
3.4 Thermal stability and degradation kinetics
Fig. 5 shows the TGA curves of the S0, S1, S2, and S3 films heated in nitrogen at the rate of 10 °C min−1. It was observed from the TGA curves that all the samples are thermally stable in nitrogen gas below 190 °C and mainly displayed three-stage thermal degradation above this temperature. The first stage degradation (about 220–340 °C) is the fastest and corresponded to dechlorination of PVC, with formation and stoichiometric elimination of HCl and a few chlorinated hydrocarbons.36 In the second stage of degradation (about 340–420 °C), the weight was almost stable, which may be associated with the formation of aromatic compounds by the cyclization of conjugated polyene sequences.42,43 In the last stage (>420 °C), the third degradation was shown. It is mainly contributed to the degradation of the complex structures resulting from aromatization, escaping olefins and a few HCl.43,44 Furthermore, the TGA characteristic temperatures of PVC films are illustrated in Table 3, including the onset, 10% and 50%, weight loss temperatures (T10 and T50) for the degradation. Clearly, ECGE improves the thermal stability of PVC films, and an increase in ECGE content generally results in a higher increase in thermal stability. Compared with sample film S0, the films modified by ECGE had a maximum increase of 27.77 °C and 16.87 °C in T10 and T50 respectively. This may be mainly due to the multi epoxy groups of ECGE which can scavenge for HCl and delay the degradation events.45–47
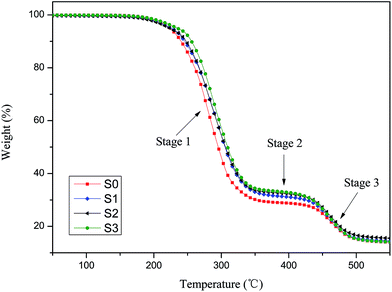 |
| Fig. 5 TGA curves of PVC films at a heating rate of 10 °C min−1. | |
Table 3 The thermal degradation parameters and kinetic parameters for the PVC samples
Sample |
Tia (°C) |
T10a (°C) |
T50a (°C) |
Equations |
Ea (kJ mol−1) |
ln A |
R2 |
Values of 10 °C min−1. Ti: onset temperature of TGA. |
S0 |
194.01 |
242.57 |
291.28 |
y = 10.22475 − 11.36278x |
94.47 |
12.66 |
0.98348 |
S1 |
198.68 |
251.63 |
303.03 |
y = 12.02394 − 12.66175x |
105.27 |
14.56 |
0.98037 |
S2 |
199.86 |
256.24 |
305.10 |
y = 14.08981 − 13.60553x |
113.12 |
16.70 |
0.98985 |
S3 |
200.03 |
263.46 |
308.15 |
y = 14.84261 − 14.18513x |
117.94 |
17.49 |
0.98040 |
Fig. 6 shows the TGA and DTG thermograms of the samples heated in nitrogen at several heating rates from 5 °C min−1 to 25 °C min−1. It can be clearly seen that the thermal degradation curves of the samples shifted to higher temperatures with increasing the heating rates. The kinetic parameters calculated from the Kissinger method48 for the samples are summarized in Table 3. It was found that the Ea values of different formulations followed the order of the samples S3 > S2 > S1 > S0. Generally, a higher Ea suggests a higher thermal degradation resistance. The increase in the Ea could be explained by the enhancement of the intermolecular distance and chain mobility.49 Hence, ECGE in small amounts could increase the thermal stability of the PVC matrix effectively.
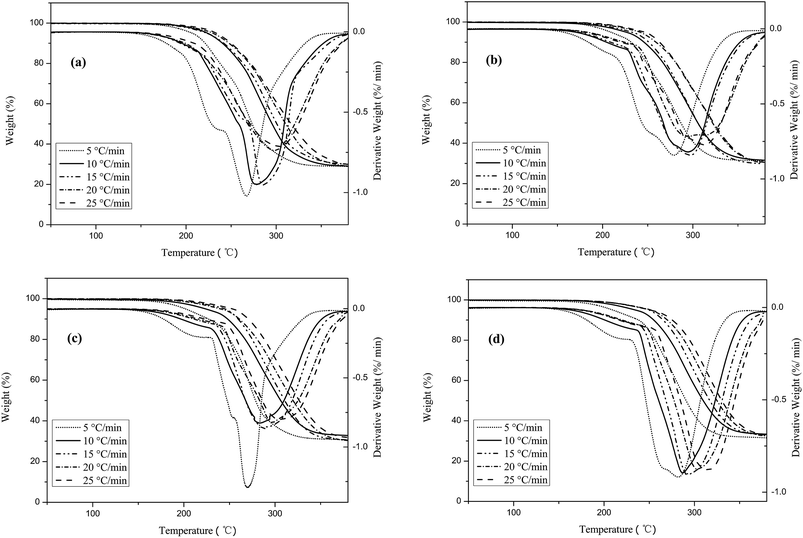 |
| Fig. 6 TGA and DTG curves of the PVC films at different heating rates: (a) S0, (b) S1, (c) S2, (d) S3. | |
3.5 Volatility, extraction, and exudation resistance
The weight losses of the PVC films by volatilization, exudation and extraction in water, hexanes, 5% (w/w) NaOH, and 4% (w/w) acetic acid are shown in Fig. 7. These properties of the plasticizers from the polymer were strongly dependent on the molecular weight, solubility, compatibility, and chemical structure of the plasticizers.29
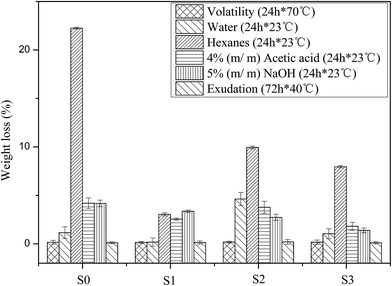 |
| Fig. 7 Weight losses of PVC films after volatilization, extraction and exudation testing. | |
The volatilization loss decreased in the samples in the following order: S0, S1, S2, and S3. Since the mixed plasticizers have a similar molecular weight as the pure DOP, the volatilization was mainly effected by the chemical structure of the plasticizers.50 ECGE has stronger interactions with PVC than DOP because of the polar functional groups of the glycidyl ether group and epoxy group on the side chain; therefore, it can be concluded that the volatilization resistance of PVC films can be improved significantly by substituting ECGE for DOP.
Furthermore, with the substitution of a small amount of ECGE into DOP, the resistance of extraction by hexanes, 5% (w/w) NaOH, and 4% (w/w) acetic acid was better than that of samples using pure DOP, but water resistance was the opposite. Films S1–S3 exhibited similar exudation resistance to film S0. These results can be attributed to the intermolecular interaction and compatibility between mixed plasticizers and PVC, which can be inferred according to the solubility parameter theory. The solubility parameter of PVC and plasticizer can be determined using the Small eqn (5), which is more accurate for plasticizers in low molecular weight.51
|
 | (5) |
In addition, the solubility parameters of mixed plasticizers can be calculated according to the additivity rule:52
|
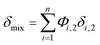 | (6) |
|
 | (7) |
where
δ is the solubility parameter, Δ
E is energy of vaporization,
Vi is molar volume, and
Fi is the molar attraction constant.
ρ and
M are the density and molecular weight of the plasticizer or chain unit of the polymer, respectively.
Φi,2 and
δi,2 are the volume fraction and solubility parameter of the component
i, respectively.
Furthermore, according to van Krevelen,52 good solubility between polymer and plasticizers occurs when the difference in value of the solubility parameter (eqn (8)) is as small as possible:
|
DS = δPVC − δPlasticizer
| (8) |
where
δPVC and
δPlasticizer denotes the solubility parameter of the polymer and plasticizer, respectively.
The value of different terms calculated according to eqn (5), (6) and (8) are reported in Table 4. It can be seen that the DS of ECGE is lower than that of pure DOP and mixed plasticizers, indicating a good miscibility between ECGE and PVC due to the high polar group content for ECGE. The substitution of DOP with ECGE leads to a decrease of the polar group contribution. Consequently, the solubility parameters of mixed plasticizers are lower than that of ECGE, although higher than that of DOP. This explains why the weight loss of extraction by organic solvent and acid–base solvent, as well as the volatilization of plasticized PVC, were improved with the substitution of a small amount of ECGE into DOP. Furthermore, since the DS values of films S1–S3 and pure DOP did not vary significantly, the exudation resistances of all the samples were at similar levels.
Table 4 Solubility parameters for PVC and plasticizers
Items |
δ (J cm−3)1/2 |
DS (J cm−3)1/2 |
PVC |
9.66 (ref. 51) |
— |
DOP |
8.89 |
0.77 |
ECGE |
9.11 |
0.55 |
Mixed plasticizer of S1 |
8.91 |
0.75 |
Mixed plasticizer of S2 |
8.93 |
0.73 |
Mixed plasticizer of S3 |
8.95 |
0.71 |
4. Conclusions
In the present study, a novel natural plasticizer, epoxidized cardanol glycidyl ether (ECGE), was synthesized from cardanol and incorporated into soft PVC films to evaluate its effects on partially replacing the commercial plasticizer DOP. The plasticizing performance of ECGE modified PVC films was mainly evaluated by the analysis of flexibility, toughness, strength, thermal stability, and compatibility compared with those of DOP. The mechanical properties revealed that the incorporation of ECGE could significantly increase the flexibility and toughen the PVC films. The results of TGA showed the thermal stability of PVC films increased with increasing the content of ECGE. The volatility, extraction and exudation resistance tests suggested the ECGE has similar or higher stability on those properties than that of DOP. Thus, it can be concluded that the ECGE can partially replace DOP in soft PVC film formulations, and could allow the production of highly effective, lower cost, and more eco-friendly products.
Acknowledgements
The authors are grateful for the financial support from basic research funding earmarked for the National Commonwealth Research Institute, Chinese Academy of Forestry (Grant number: CAFINT2014C12), and the National “Twelfth Five-Year” Plan for Science and Technology Support (Grant number: 2014BAD02B02). The authors also gratefully acknowledge Mr Daniel Knetzer for help in DMA and TGA analysis and Mrs Kathy Hornback for help in preparing PVC test specimens.
References
- Y. Zhou, N. Yang and S. Hu, Resour., Conserv. Recycl., 2013, 73, 33–40 CrossRef PubMed.
- S. Vadukumpully, J. Paul, N. Mahanta and S. Valiyaveettil, Carbon, 2011, 49, 198–205 CrossRef CAS PubMed.
- M. G. A. Vieira, M. A. da Silva, L. O. dos Santos and M. M. Beppu, Eur. Polym. J., 2011, 47, 254–263 CrossRef CAS PubMed.
- J. S. Choi and W. H. Park, Polym. Test., 2004, 23, 455–460 CrossRef CAS PubMed.
- F. Chiellini, M. Ferri and G. Latini, Int. J. Pharm., 2011, 409, 57–61 CrossRef CAS PubMed.
- F. Chiellini, M. Ferri, A. Morelli, L. Dipaola and G. Latini, Prog. Polym. Sci., 2013, 38, 1067–1088 CrossRef CAS PubMed.
- C. J. Hines, N. B. Hopf, J. A. Deddens, M. J. Silva and A. M. Calafat, Int. Arch. Occup. Environ. Health, 2012, 85, 317–325 CrossRef CAS PubMed.
- D. Lithner, Å. Larsson and G. Dave, Sci. Total Environ., 2011, 409, 3309–3324 CrossRef CAS PubMed.
- J. Sampson and D. De Korte, Transfus. Med., 2011, 21, 73–83 CrossRef CAS PubMed.
- S. S. Hill, B. R. Shaw and A. H. Wu, Clin. Chim. Acta, 2001, 304, 1–8 CrossRef CAS.
- A. Greco, D. Brunetti, G. Renna, G. Mele and A. Maffezzoli, Polym. Degrad. Stab., 2010, 95, 2169–2174 CrossRef CAS PubMed.
- Z. Li, N. Liu, Y. Yao, S. Chen, H. Wang and H. Wang, RSC Adv., 2015, 5, 901–907 RSC.
- M. Li, J. Yuan, M. Pan, H. Song and L. Tang, Polym. Mater.: Sci. Eng., 2012, 1, 013 Search PubMed.
- Z. Qiu and P. Zhou, RSC Adv., 2014, 4, 51411–51417 RSC.
- D. Wu, P. R. Chang and X. Ma, Carbohydr. Polym., 2011, 86, 877–882 CrossRef CAS PubMed.
- B. Garg, T. Bisht and Y. Ling, RSC Adv., 2014, 100, 57297–57307 RSC.
- P. G. Nihul, S. T. Mhaske and V. V. Shertukde, Iran. Polym. J., 2014, 23, 599–608 CrossRef CAS PubMed.
- D. Yang, X. Peng, L. Zhong, X. Cao, W. Chen, X. Zhang, S. Liu and R. Sun, Carbohydr. Polym., 2014, 103, 198–206 CrossRef CAS PubMed.
- O. Fenollar, D. García, L. Sánchez, J. López and R. Balart, Eur. Polym. J., 2009, 45, 2674–2684 CrossRef CAS PubMed.
- B. Garg, T. Bisht and Y.-C. Ling, RSC Adv., 2014, 4, 57297–57307 RSC.
- C. Voirin, S. Caillol, N. V. Sadavarte, B. V. Tawade, B. Boutevin and P. P. Wadgaonkar, Polym. Chem., 2014, 5, 3142–3162 RSC.
- B. Rao and A. Palanisamy, Eur. Polym. J., 2013, 49, 2365–2376 CrossRef CAS PubMed.
- A. Barreto, D. Rosa, P. Fechine and S. Mazzetto, Composites, Part A, 2011, 42, 492–500 CrossRef PubMed.
- R. Yadav and D. Srivastava, Eur. Polym. J., 2009, 45, 946–952 CrossRef CAS PubMed.
- F. Jaillet, E. Darroman, A. Ratsimihety, R. Auvergne, B. Boutevin and S. Caillo, Eur. J. Lipid Sci. Technol., 2014, 116, 63–73 CrossRef CAS PubMed.
- M. Sultania, J. Rai and D. Srivastava, Mater. Chem. Phys., 2012, 132, 180–186 CrossRef CAS PubMed.
- B. Sandrino, C. D. S. Clemente, T. M. B. F. Oliveira, F. W. P. Ribeiro, F. J. Pavinatto, S. E. Mazzetto, P. de Lima-Neto, A. N. Correia, C. A. Pessoa and K. Wohnrath, Colloids Surf., A, 2013, 425, 68–75 CrossRef CAS PubMed.
- M. Kathalewar and A. Sabnis, J. Coat. Technol. Res., 2014, 11, 601–618 CrossRef CAS PubMed.
- S. Kanehashi, K. Yokoyama, R. Masuda, T. Kidesaki, K. Nagai and T. Miyakosh, J. Appl. Polym. Sci., 2013, 130, 2468–2478 CrossRef CAS PubMed.
- M. Kathalewar, A. Sabnis and D. D’Mello, Eur. Polym. J., 2014, 57, 99–108 CrossRef CAS PubMed.
- S. Mohapatra and G. B. Nando, Ind. Eng. Chem. Res., 2013, 52, 5951–5957 CrossRef CAS.
- M. Alexander and E. T. Thachil, J. Appl. Polym. Sci., 2006, 102, 4835–4841 CrossRef CAS PubMed.
- E. Calò, A. Greco and A. Maffezzoli, Polym. Degrad. Stab., 2011, 96, 784–789 CrossRef PubMed.
- S. W. Kim, J. G. Kim, J. I. Choi, I. R. Jeon and K. H. Seo, J. Appl. Polym. Sci., 2005, 96, 1347–1356 CrossRef CAS PubMed.
- J. Dorsey, G. Dorsey, A. Rutenberg and L. Green, Anal. Chem., 1977, 49, 1144–1145 CrossRef CAS.
- M. Semsarzadeh, M. Mehrabzadeh and S. Arabshahi, Eur. Polym. J., 2002, 38, 351–358 CrossRef CAS.
- P. H. Daniels, J. Vinyl Addit. Technol., 2009, 15, 219–223 CrossRef CAS PubMed.
- S. Wang, J. Wang, Q. Ji, A. Shultz, T. Ward and J. McGrath, J. Polym. Sci., Part B: Polym. Phys., 2000, 38, 2409–2421 CrossRef CAS.
- L. Coltro, J. B. Pitta and E. Madaleno, Polym. Test., 2013, 32, 272–278 CrossRef CAS PubMed.
- M. Altenhofen da Silva, M. G. Adeodato Vieira, A. C. Gomes Maçumoto and M. M. Beppu, Polym. Test., 2011, 30, 478–484 CrossRef CAS PubMed.
- R. J. Anderson, Organic spectroscopic analysis, Royal Society of Chemistry, 2004 Search PubMed.
- Y. Soudais, L. Moga, J. Blazek and F. Lemort, J. Anal. Appl. Pyrolysis, 2007, 78, 46–57 CrossRef CAS PubMed.
- Q. Yao and C. A. Wilkie, J. Vinyl Addit. Technol., 2001, 7, 26–36 CrossRef CAS PubMed.
- G. Pitchaimari, K. Sarma, L. Varshney and C. Vijayakumar, Thermochim. Acta, 2014, 597, 8–18 CrossRef CAS PubMed.
- G. Ayrey, B. Head and R. Poller, J. Polym. Sci., Macromol. Rev., 1974, 8, 1–49 CrossRef CAS PubMed.
- I. Lerke and W. Szymański, J. Appl. Polym. Sci., 1977, 21, 2067–2075 CrossRef CAS PubMed.
- R. F. Grossman, Journal of Vinyl Technology, 1993, 15, 25–28 CrossRef CAS PubMed.
- M. Li, J. Zhang, K. Huang, S. Li, J. Jiang and J. Xia, RSC Adv., 2014, 108, 63576–63585 RSC.
- L. Dai, L.-Y. Wang, T.-Q. Yuan and J. He, Polym.
Degrad. Stab., 2014, 99, 233–239 CrossRef CAS PubMed.
- G. Wypych, Handbook of plasticizers, ChemTec Publishing, 2004 Search PubMed.
- P. Small, J. Appl. Chem., 1953, 3, 71–80 CrossRef CAS PubMed.
- D. W. van Krevelen and K. Te Nijenhuis, Properties of polymers: their correlation with chemical structure; their numerical estimation and prediction from additive group contributions, Elsevier, 2009 Search PubMed.
Footnotes |
† Mention of trade names or commercial products in this publication is solely for the purpose of providing specific information and does not imply recommendation or endorsement by the U.S. Department of Agriculture. USDA is an equal opportunity provider and employer. |
‡ Jie Chen is a visiting student at U.S. Department of Agriculture. |
|
This journal is © The Royal Society of Chemistry 2015 |
Click here to see how this site uses Cookies. View our privacy policy here.