DOI:
10.1039/C5RA04682C
(Paper)
RSC Adv., 2015,
5, 34109-34116
Flame retardancy of clay–sodium silicate composite coatings on wood for construction purposes
Received
17th March 2015
, Accepted 7th April 2015
First published on 7th April 2015
Abstract
Composites of clay minerals mixed with sodium silicate as new inorganic flame retardants for wood have been investigated. Vermiculite beads were exfoliated by an ultra-sonication method and characterized by scanning electron microscopy, Fourier transform infrared absorption spectroscopy and thermogravimetry. The fire properties of wood samples coated with vermiculite and various vermiculite–sodium silicate composites were tested by a cone calorimeter. When the samples were exposed to the heat flux during the test, formation of a solid foamy layer was observed and composite coatings were effective in delaying of ignition coupled with decreasing the heat release rate and the total heat release. Synergy between the low thermal conductivity of the foamy layer and the release of water molecules from the composites improved the flame retardancy of these composite coatings. Among the coatings, multiple layers of sodium silicate and vermiculite exhibited the best flame retardancy in terms of maximum ignition time and minimum heat release rate.
1 Introduction
Wood is a natural resource and one of the most important structural and aesthetic building materials being widely used over the world for construction purpose. Protection of wood from fire is an important and challenging issue for the construction industry to increase the escape time and minimize losses. The fire behaviour of wood can be chemically modified with the incorporation of Flame Retardants (FR). FR are the chemicals added to the substrate to enhance the fire resistivity of the substrate. Generally, intumescent and non-intumescent are the known FR for coating purpose. Intumescent Flame Retardants (IFR) are of great interest due to their volume expansion, low smoke evolution, higher efficiency and low toxicity during combustion.1
For the past decades, variety of FR have been extensively studied by many researchers.2–5 At present, organic–inorganic polymer nanocomposites are attracting much attention because of their improved mechanical properties and flame retardancy.4,6 For instance, clay mixed with polymer,7 expandable graphite with cyanate ester resin and triazine/ammonium polyphosphate based flame retardant8,9 and layered double hydroxide10 have been reported.
Similarly polymer based FR for wood substrate were reported by several authors.11–17 Hassan et al. developed a new fire intumescent system which includes pentaerythritol, polyammonium phosphate, melamine and montmorillonite clay and polyurethane for wood coating.12 Composites of wood-plastic, urea-formaldehyde resin with mineral fillers and nitrogen phosphorous flame retardants have been reported.13–15 Interestingly, a recent report by Sun et al. showed significant reduction in the amount of heat release and delayed ignition time for the nano zinc oxide and titanium dioxide coated wood.16,17 In order to further improve the fire resistance of wood and to replace the existing flammable polymers, in the present work inorganic–inorganic hybrid composite material is investigated as new FR by a simple coating method. To develop such composites vermiculite (clay mineral) and sodium silicate have been chosen as coating materials.
Vermiculite is a natural hydrated magnesium aluminium silicate clay mineral18 and is known for its excellent properties such as low density, low cost, abundant availability, high thermal stability, chemical stability and adsorption capability.19,20 In this work, vermiculite has been chosen to develop a thermally stable and environment friendly inorganic composite flame retardant for wood. Similarly, sodium silicate is a popular inorganic adhesive and intumescent inorganic material, which forms a solid foamy layer against flame, and can delay the flame spread effectively.21 The water solubility and atmospheric instability are the major concern about sodium silicate. However, it is suggested that the degradation of sodium silicate with the interaction of atmospheric gases can be prevented by an oxide layer deposition on sodium silicate.22 Although patents related to sodium silicate coating for wood flame retardancy and antifungal activity are available,22,23 quantitative studies to improve the flame retardancy of wood with sodium silicate by using a cone calorimeter have not been reported.
Therefore, the current investigation aims to develop coating based on composites of vermiculite and sodium silicate to increase the ignition resistance of wood and to reduce the rate of flame spread. The fire parameters obtained by a cone calorimetric test are presented and discussed.
2 Experimental
2.1 Materials
Red pine wood (10 cm × 10 cm × 1.9 cm, Tsukuba-Flat Co. Ltd, Japan; imported from the USA), Na2SiO3·xH2O (38% SiO2 and 19% Na2O, Nissei Sangyo Co. Inc., Japan), NaCl (99.5% Kanto Chemical Co. Inc., Japan), Vermiculite beads (Showa KDE Co. Ltd., Japan) and ethanol (99.5% Koso Chemical Co. Ltd, Japan) were used as the starting materials.
2.2 Preparation of exfoliated vermiculite
Exfoliated vermiculite flakes were prepared by ultrasonication method. Initially, 2 g of vermiculite beads were mixed with 10 ml of 1 M sodium chloride solution and kept undisturbed for 24 h. The mixture was washed with distilled water thrice and aged for 24 h at 80 °C. The resultant mixture was then sonicated in an ultrasonic bath (as one single frequency ultrasonic cleaner, US-4R, China) for 10 min and transferred into a separating funnel. The colloidal solution was then kept undisturbed for 12 h. After aging, the unexfoliated vermiculites were settled at the bottom of separating funnel. Finally, the exfoliated vermiculites (top portion) were separated by removing the unexfoliated vermiculites (bottom portion) slowly from the separating funnel and dried at 60 °C for 6 h in hot air oven. The yield of exfoliated vermiculite was found to be 30 wt%.
2.3 Characterization
Exfoliated vermiculite flakes were observed by a scanning electron microscope (SEM
:
JEOL-JSM-6010LA). The size of exfoliated flakes from SEM image was measured by an ImageJ software (NIH, USA). Fourier transformed infrared spectra (FTIR) were recorded by a FTIR spectrometer (Thermoscientific Nicolet 4700) using a KBr disc in the frequency range of 400–4000 cm−1. Thermal analysis was performed by Bruker AXS TG-DTA 2000S between 25 °C and 1000 °C at 10 °C min−1 in air. The internal structure of expanded sodium silicate and vermiculite–sodium silicate composite after furnace test was observed by X-ray computed tomography (CT X-ray: SMZ0160 CT).
2.4 Preparation of coating compositions
Three types of coating compositions were prepared as follows: (i) vermiculite coating material was prepared by mixing 1 g of exfoliated vermiculites with 10 ml of ethanol, (ii) commercially available sodium silicate (38% SiO2 and 19% Na2O, Nissei Sangyo Co. Inc., Japan) was used without any further treatment and (iii) 3.1 wt% of vermiculite–sodium silicate composite was prepared by mixing of 0.5 g of exfoliated vermiculite in 10 ml of sodium silicate. The mixed viscous liquid was stirred in a centrifugal mixer (rotator) for 1 min at 2000 rpm and used for coating.
2.5 Preparation of samples for cone calorimetric test
The prepared coating materials were applied on the surface of the wood by brush. The coating thickness was measured from the cross sectional SEM images of duplicate samples. The average thickness of sodium silicate and vermiculite–sodium silicate composite coatings was found to be 90 μm and 350 μm respectively. Before the cone calorimetric test, the coated wood samples were maintained at 23 °C and 50% humidity in a constant humidity chamber for one week. Single, double, triple and quadruple layers of coatings were applied to make different set of samples. Coating descriptions and the weight difference of wood samples are listed in are listed in Tables 1 and 2 respectively.
Table 1 Sample codes and coating description
Sample code |
Coating description |
N |
No coating |
V |
One layer of vermiculite |
SS |
One layer of sodium silicate |
VSS |
One layer of vermiculite + one layer of sodium silicate |
VSS2 |
(One layer of vermiculite + one layer of sodium silicate) × 2 |
5VSS |
One layer of 5% vermiculite–sodium silicate composite |
Table 2 Weight difference of the samples and coating materials
Sample code |
Wta of wood (g) |
Wt after I layer (g) |
Wt after II layer (g) |
Wt after III layer (g) |
Wt after IV layer (g) |
Coating wt (g) |
Coating wt (g m−2) |
Weight. |
N |
81.757 |
— |
— |
— |
— |
— |
— |
V |
79.711 |
79.797 |
— |
— |
— |
0.086 |
8.56 |
SS |
80.100 |
81.534 |
— |
— |
— |
1.434 |
143.40 |
VSS |
83.013 |
83.180 |
84.528 |
— |
— |
1.515 |
151.50 |
VSS2 |
79.853 |
80.007 |
81.342 |
81.365 |
82.759 |
2.905 |
290.46 |
5VSS |
87.098 |
88.334 |
— |
— |
— |
1.236 |
123.62 |
2.6 Cone calorimetric (cone) test
Fire properties of the specimens were evaluated by a cone calorimeter (Toyoseiki, C4) according to ISO 5660. The specimens were held in a metal frame and exposed only the surface (10 cm × 10 cm) that protected the specimen edges, sides and the back surface during testing. The specimens were placed horizontally in the metal sample holder and ignited by a spark igniter in air at a heat flux of 50 kW m−2. The following parameters were determined with the computer-aided analysis; time to ignition (TTI, sec), heat release rate (HRR, kW m−2), peak HRR (PHRR, kW m−2), total heat release (THR, MJ m−2), mass loss rate (MLR, g m−2 s−1), total mass loss (g m−2), specific extinction area (SEA, m2 kg−1), total smoke production (TSP, m2 m−2), heat of combustion (HOC, MJ kg−1), yield of carbon monoxide (CO, kg kg−1) and carbon dioxide (CO2, kg kg−1).
3 Results
3.1 Spectral analysis of vermiculite
A secondary electron image of vermiculite flakes is shown in Fig. 1a. Formation of exfoliated vermiculites was observed from the SEM image. By image analysis, it was identified that the thickness of each layer is in the range of 0.8 to 1.2 μm. The average size of the flakes was observed as around 50 μm. An FTIR spectrum of exfoliated vermiculite is shown in Fig. 1b. The spectrum indicates the stretching and bending frequencies of Si–O/Al–O, interlayer water and OH stretching. The bands at 3427 cm−1 and 1635 cm−1 correspond to stretching and bending frequency of interlayer water respectively. The stretching frequency of OH was observed at 3720 cm−1.24 Vibrational modes of Si–O/Al–O were observed between 500 and 1050 cm−1. Fig. 1c shows thermogravimetric and differential thermal analysis (TG-DTA) curves of vermiculite. The TGA curve indicates that weight loss occurs in three stages. First stage in the region of 30–100 °C is due to the release of adsorbed water, the second loss between 100 °C and 200 °C is attributed to the release of interlayer water. The third loss occurring gradually in the region 200 °C to 1000 °C is due to the release of structurally bonded water. The different stage of thermal effect was further confirmed by the three endothermic peaks from the DTA curve in the same region. Similar spectral observations of vermiculite were noticed by Huo et al.24
 |
| Fig. 1 (a) SEM image (b) FTIR spectrum and (c) TG-DTA of exfoliated vermiculite. | |
3.2 Cone calorimetric results
3.2.1 Observation of samples during and after test. Interesting visible observations were noticed during the cone test. The uncoated (N) and vermiculite (V) coated samples generated fume before ignition. However, in the case of sodium silicate (SS) and composites coated samples, evolution of fume was absent due to the formation of an intumescent layer on the surface of wood. Fig. 2a and b show the photographs of pristine wood and VSS2 sample taken from the video after 30 seconds of cone test. The intumescency of VSS2 coating was observed as the expansion of coating during the test (Fig. 2b). Photographs of all the samples surface and side view after cone test are shown in Fig. 3 and 4 respectively. Fig. 3 shows notable difference on the surface of the samples. For vermiculite coated sample (V), formation of a thin layer of vermiculite on the surface was observed whereas thick porous layers were formed on the substrate for sodium silicate (SS) and composite coated samples (VSS, VSS2, 5VSS). The intumescent behaviour of sodium silicate coated samples is due to the release of water molecules from sodium silicate.21 The intumescency of sample VSS2 (Fig. 4) was the greatest as noticed by the height reaching up to 2.4 cm above the surface of the wood during the test.
 |
| Fig. 2 Photographs of (a) wood and (b) VSS2 coated samples after 30 seconds of cone test. | |
 |
| Fig. 3 Photographs of the samples surface after cone test. | |
 |
| Fig. 4 Photographs of the samples side view after cone test. | |
The important parameters obtained by the cone calorimeter, i.e., time to ignition (TTI), peak heat release rate (PHRR), average heat release rate (AHRR) and total heat release (THR) are given in Table 3.
Table 3 Cone calorimetric analysis data
Sample code |
Ignition time (Sec) |
PHRR (kW m−2) |
Maximum HRR in 5 min (kW m−2) |
AHRR(kW m−2) |
THR (MJ m−2) |
N |
17 |
179 |
179 |
83 |
98 |
V |
20 |
166 |
166 |
78 |
93 |
SS |
54 |
134 |
94 |
68 |
78 |
VSS |
66 |
120 |
75 |
57 |
64 |
VSS2 |
101 |
106 |
49 |
46 |
50 |
5VSS |
60 |
144 |
59 |
55 |
63 |
3.2.2 Time to ignition (TTI). TTI values of the samples were given in Table 3. The minimum and maximum TTI was recorded as 17 and 101 seconds for the samples N and VSS2 respectively. The results indicate that the sodium silicate coated samples significantly delayed ignition. This is due to the intumescent behaviour of sodium silicate by releasing water molecules from its structure and the water cools the underlying substrate.21 In addition to the release of H2O, formation of a low thermal conducting foamy layer on the substrate could have slowed the temperature rise of the wood and reduced the supply of oxygen to the burning surface and suppressed the flame spread.
3.2.3 Heat release rate (HRR). HRR is considered as an important parameter to examine the fire behaviour of a material.25 The evolution of HRR with time for all the samples is shown in Fig. 5. Heat release rate of the samples generally exhibited two peaks in two regions with respect to time. The first peaks appeared in the period between 7 and 277 seconds correspond to the surface ignition of the samples and the second peaks to the combined effect of cracking and ignition of back surface of the samples between 745 and 1200 seconds. Though the peak heat release rate (PHRR) is defined as the maximum heat release rate measured during the whole test period, in the present study, first peaks which appeared due to surface ignition are taken into consideration in order to find the effect of our coatings. The peak heat release rates (PHRR) and the maximum heat release rates in 5 minutes were compared in Table 3 accordingly.
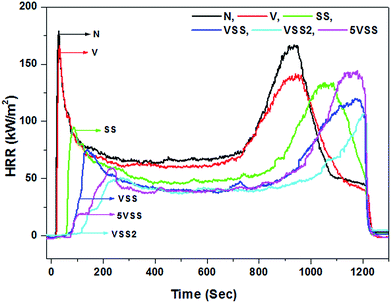 |
| Fig. 5 Heat release rate curves as a function of time. | |
During the first 5 minutes of cone test, the highest heat release rate was obtained for the sample N (179 kW m−2) and the lowest for VSS2 (49 kW m−2). Vermiculite coated sample (V) shows a decrease in HRR value to 166 kW m−2. This is 7% less than the uncoated wood sample (N). The decreased HRR could be due to the release of water molecules present in the vermiculite but is rather minor. From the TGA curve of vermiculite (Fig. 1c), it is identified that up to 5 wt% loss occurs due to the adsorbed and interlayer water molecules of vermiculite between the room temperature and 200 °C. This indicates that the presence of 5 wt% of adsorbed and interlayer water molecules of vermiculite structure is responsible for the 7% reduction of HRR value. However, sodium silicate coated sample SS shows 47% decrease of HRR in comparison with the uncoated wood sample. The large decrease of PHRR in sodium silicate coated samples could be attributed to the release of ∼30 wt% water molecules from sodium silicate in the temperature range of 30–200 °C.26 Vermiculite and sodium silicate coated sample VSS showed a HRR of 75 kW m−2. This is 58% lower than the uncoated wood. For the sample 5VSS, 67% and 37% reduction in HRR was noticed when compared to the sample N and sample SS respectively. The lowest HRR was registered as 49 kW m−2 for the multilayer coated sample VSS2 which is 73% lower than the uncoated sample.
3.2.4 Total heat release (THR). THR is an important parameter for the fire behaviour of wood because, according to the fire safety standards of Japan, if a material releases less than 8 MJ m−2 of heat in 5, 10 and 20 minutes it is classified as flame resisting material, quasi-non-combustible material and non-combustible material respectively.27 The difference in THR of all samples with respect to time is presented in Fig. 6. THR curves show a gradual increase for the samples N and V whereas in the case of sodium silicate coated samples SS, VSS, VSS2 and 5VSS, the increasing rate of THR is comparatively less than those of N and V samples. The minimum THR (50 MJ m−2) was observed for the sample VSS2, which is 49% lower than the uncoated wood (N). The THR of SS and 5VSS samples were 78 MJ m−2 and 63 MJ m−2 respectively. The effect of incorporation of 3.1 wt. % vermiculite powder into sodium silicate is reflected in the THR as observed in HRR. Composite of vermiculite–sodium silicate (5VSS) shows ∼20% lower THR than sodium silicate. The decrease in THR of a composite is related with the structures of SS and 5VSS. Since the foamy layer of SS (Fig. 10) is comparatively lighter than the composite layer, it easily creates holes at higher temperature and becomes a permeated foam. This leads to increase the thermal conductivity of SS layer at high temperature than the composite layer and allows the flammable gases to escape easily to increase the THR. Fig. 7 shows the bar diagram of THR of sodium silicate coated samples in 5 minutes. It is interesting to note that sample 5VSS composite released 8 MJ m−2 of heat after 5 minutes and the sample VSS2 released 6.6 MJ m−2 due to the double layer coating of sodium silicate. Hence, 5VSS composite and double layer vermiculite–sodium silicate coated sample VSS2 can be good flame resisting materials for wood.
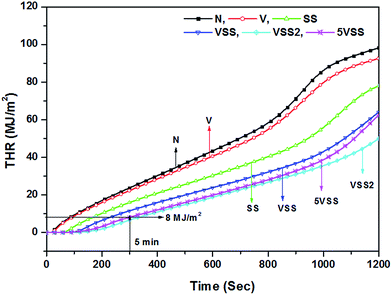 |
| Fig. 6 Total heat release curves as a function of time. | |
 |
| Fig. 7 Total heat release of samples in 5 minutes. | |
3.2.5 Mass loss. The mass loss of samples till ignition is found to be dependant with the amount of water content present in the coatings and the moisture content from wood substrate. The mass loss versus total heat release of the samples was plotted to explain this behaviour and it is shown in the inset of Fig. 8. The mass loss of pristine wood till ignition was identified as 47 g m−2 whereas it was 105 g m−2 for the sodium silicate coated sample. This indicates that the difference in mass loss between sample N and sample SS (58 g m−2) is due to the release of ∼40 wt% of water molecules from sodium silicate. When two layers of sodium silicate was applied, the mass loss was found to be 214 g m−2, which is almost double compared to the single layer sodium silicate coated sample. This large mass loss indicates that the amount of water content present in the coatings is highly responsible for the mass loss before the sample ignite. Total mass loss curves of all samples are shown in Fig. 8. The mass loss of samples N and V is higher than the SS coated samples due to the rapid ignition. In the period 0 to 800 seconds the mass loss of N and V is observed as gradual and it suddenly decreased between 800 to 900 seconds due to the back surface ignition. This effect is comparatively less for the SS coated samples.
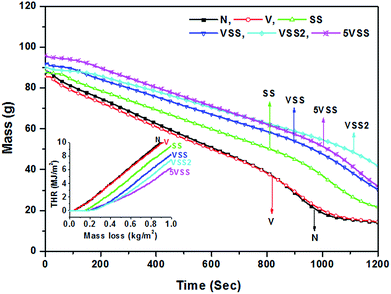 |
| Fig. 8 Total mass loss curves as a function of time. Inset shows total heat release curves as a function of mass loss. | |
3.2.6 ASEA and SPR. The average specific extinction area (ASEA) is the amount of smoke produced per unit mass of specimen burnt. The least ASEA (5.1 m2 kg−1) was observed for the double layer coated sample VSS2. The Smoke Production Rate (SPR) against time is shown in Fig. 9. The curves of SPR are closely related with the HRR curves of the samples. This proves that the amount of smoke release during combustion follows the rate of heat release.
 |
| Fig. 9 Smoke production rate curves as a function of time. | |
However, the SPR curves show that the smoke production rate of samples after surface ignition is maintained as zero till the beginning of second peak. This indicates that the higher amount of smoke produced immediately after ignition. After surface ignition, oxygen travels through the cracks to the entire portion of wood samples (maintained the SPR as zero) and started burning effectively to produce higher amount of smoke again.28 Sodium silicate coated samples show significant reduction of SPR. Samples VSS2 and 5VSS composite registered minimum smoke production rate and delayed smoke release. Amounts of carbon monoxide (CO) and carbon dioxide (CO2) produced from the unit mass of burnt sample (yield of CO and CO2) were determined. Release of CO was absent for the vermiculite-sodium silicate composite and it was negligible for other samples including sample N. Table 4 shows the cone data of avg. SEA, TSP, avg. yield of CO and CO2. The minimum CO2 release 0.57 kg kg−1 was obtained for the sample VSS2 and the maximum found for the sample N (0.86 kg kg−1). The minimum SPR, absence of CO release and minimum CO2 release of VSS2 sample could be due to the formation of dense foamy layer, which can act as a physical barrier on the substrate and reduce the release of gases.
Table 4 Cone calorimetric data of ASEA, TSP, yield of CO and CO2
Sample code |
ASEA (m2 kg−1) |
TSP (m2 m−2) |
Avg. CO yield (kg kg−1) |
Avg.CO2 yield (kg kg−1) |
N |
28.4 |
2.14 |
0.3 × 10−4 |
0.86 |
V |
30.8 |
2.91 |
0.4 × 10−4 |
0.86 |
SS |
30.1 |
0.17 |
0.2 × 10−4 |
0.80 |
VSS |
16.8 |
0.51 |
0.1 × 10−4 |
0.66 |
VSS2 |
5.1 |
0.27 |
0.4 × 10−4 |
0.57 |
5VSS |
18.8 |
0.23 |
0 |
0.70 |
4 Discussion
In order to understand the effect of vermiculite addition into sodium silicate, a furnace test on 45 mm × 45 mm × 15 mm sized wood samples was carried out. Sodium silicate was applied only on the surface of one of the wood samples and maintained at 30 °C and 60% humidity in a constant temperature humidity chamber for one week. After a week, the sides and back surface of the SS coated sample were covered with aluminium foil and placed on the metal sample holder. The inner part of metal sample holder was covered by thermally insulated fibres. The sample holder was introduced into the 500 °C preheated furnace for 5 min and taken out. Similar procedure was followed to test a vermiculite composite (5VSS) coated sample.
Fig. 10a and c show the photographs of SS and 5VSS after the furnace test. They display different surface appearance, i.e., SS coating shows an expanded layer with larger pores than the 5VSS coating expanded layer. A remarkable change of internal structure was also observed from the cross sectional CT X-ray images of SS and 5VSS (Fig. 10e and f). The addition of vermiculite into sodium silicate changed the internal structure from thick and foamy into thinner and denser with a large internal space beneath. It is presumed that the porosity of SS expanded layer allows oxygen to interact with the ignited surface to enhance the fire and heat release rate. However, in the case of vermiculite composites, the fine particles of exfoliated vermiculites acts as a filler between the pores and makes the surface denser than the SS coated sample. This dense expanded layer acted as a physical barrier on the substrate and restricted the interaction of oxygen with ignited surface to suppress the flame and heat release rate. This observation is closely related with the images obtained during the cone calorimetric test by means of flame intensity. Photographs of SS and 5VSS during cone test after 60 seconds are shown in Fig. 10b and d respectively. From the images, it is noted that the flame intensity of SS is higher than the composite. The higher flame intensity of SS coated sample could be attributed to the highly porous nature of the expanded layer. This behaviour is also reflected in the HRR curves shown in Fig. 5; while HRR increased sharply to a value close to 100 kW m−2 after ignition whereas it gradually increased to 19 kW m−2 and plateaued for 47 seconds and then reached a peak value of 20 kW m−2 for the composite due to the dense layer on the surface. Thus, vermiculite addition into sodium silicate resulted in higher ignition resistance and lower HRR values than sodium silicate coated sample.
 |
| Fig. 10 Photographs of (a) SS after furnace test, (b) SS after 60 seconds of cone test, (c) 5VSS after furnace test, (d) 5VSS after 60 seconds of cone test, (e) cross sectional CT X-ray image of SS after furnace test and (f) cross sectional CT X-ray image of 5VSS after furnace test. | |
The reproducibility of duplicate samples were triplicated by a furnace test. The coating weight and ignition time were considered to check the reproducibility of the results. Ignition of the samples was noted through the transparent glass in the furnace and taken out immediately after ignition. The ignition time was noted by a stop watch. From the results, the precision of ignition time for VSS2 coatings (average weight 350 g m−2) was found to be in the range of ±20 seconds for an average of 7 min.
Furthermore, the TTI is found to be dependent on the coating weight. Coating weights of samples SS and VSS2 are 143 g m−2 and 290 g m−2 (Table 2) respectively. It is worth noting that 143 g m−2 of SS coating has delayed the ignition up to 54 seconds (34 seconds longer than the uncoated sample) and maintained the HRR as zero. When the coating weight increased to 152 g m−2 with the addition of vermiculite layer along with SS layer, the zero value of HRR was further retained up to 66 seconds. For the highest coating weight (VSS2: 290 g m−2), the HRR was registered as zero up to 101 seconds, which is almost double compared to the sample SS.
5 Conclusions
A new inorganic flame retardant based on vermiculite-sodium silicate composite for wood has been developed. The incorporation of vermiculite clay mineral into the commercial sodium silicate improved fire properties as measured by the cone calorimeter. Vermiculite and sodium silicate mixed composite material deliver lower PHRR, AHRR, THR, AHOC, AMLR, ASEA, CO and CO2 yield than the monolithic vermiculite or sodium silicate coated samples. Particularly the total heat release of 8 MJ m−2 in 5 minutes indicates that the composite is classified as a flame resistant material. The intumescent behaviour of sodium silicate forms a solid layer with vermiculite and protects the wood from rapid ignition. When sodium silicate and vermiculite applied twice, the double layers showed less than 8 MJ m−2 heat release in 5 minutes. Though composites of vermiculite and sodium silicate showed best flame retardancy with higher ignition time and lower heat release rate and total heat release, stability of composites against atmospheric gases needs to be investigated for construction applications.
Acknowledgements
Dr K. Sakuraya and Dr H. Murakami are greatly acknowledged for instrumental analysis support. Mr H. Nagamori from Takenaka Corporation is indebted for the cone calorimetric analysis. Dr Makoto Watanabe and Ms Akiko Takenouchi are acknowledged for CT X-ray images.
Notes and references
- G. Camino, L. Costa and G. Martinasso, Polym. Degrad. Stab., 1989, 23, 359–376 CrossRef CAS.
- E. D. Weil, in Encyclopedia of Polymer Science and Technology, John Wiley & Sons, 2004, vol. 10, DOI:10.1002/0471440264.pst513.
- A. Innes and J. Innes, in Handbook of Environmental Degradation of Materials, ed. M. Kutz, Elsevier, 2nd edn, 2012, ch. 10, pp. 309–335 Search PubMed.
- S. Bourbigot and S. Duquesne, J. Mater. Chem., 2007, 17, 2283–2300 RSC.
- N. Ayrilmis, T. Akbulut, T. Dundar, R. H. White, F. Mengeloglu, U. Buyuksari, Z. Candan and E. Avci, Constr. Build. Mater., 2012, 33, 63–69 CrossRef PubMed.
- S. Liang, N. M. Neisius and S. Gaan, Prog. Org. Coat., 2013, 76, 1642–1665 CrossRef CAS PubMed.
- M. Liu, X. Zhang, M. Zammarano, J. W. Gilman, R. D. Davis and T. Kashiwagi, Polymer, 2011, 52, 3092–3103 CrossRef CAS PubMed.
- J. Han, G. Liang, A. Gu, J. Ye, Z. Zhang and L. Yuan, J. Mater. Chem., 2013, 1, 2169–2182 RSC.
- G. Bai, C. Guo and L. Li, Constr. Build. Mater., 2014, 50, 148–153 CrossRef PubMed.
- D. Y. Wang, A. Das, A. Leuteritz, R. N. Mahaling, D. Jehnichen, U. Wagenknecht and G. Heinrichb, RSC Adv., 2012, 2, 3927–3933 RSC.
- J. Stejskal, M. Trchova, J. Brodinova and I. Sapurina, J. Appl. Polym. Sci., 2007, 103, 24–30 CrossRef CAS PubMed.
- M. A. Hassan, R. Kozlowski and B. Obidzinski, J. Appl. Polym. Sci., 2008, 110, 83–90 CrossRef CAS PubMed.
- H. Seefeldt and U. Braun, Macromol. Mater. Eng., 2012, 297, 814–820 CrossRef CAS PubMed.
- G. V. Plotnikova, A. N. Egorov and A. K. Khaliullin, Macromol. Chem. Polym. Mater., 2003, 76, 310–313 CAS.
- J. Jiang, J. Li, J. Hu and D. Fan, Constr. Build. Mater., 2010, 24, 2633–2637 CrossRef PubMed.
- Q. F. Sun, Y. Lu, H. M. Zhang, D. J. Yang, J. S. Xu, J. Li, Y. X. Liu and J. T. Shi, Mater. Res. Innovations, 2012, 16, 326–331 CrossRef CAS PubMed.
- Q. F. Sun, H. Yu, Y. Liu, J. Li, Y. Cui and Y. Lu, J. Mater. Sci., 2010, 45, 6661–6667 CrossRef CAS.
- M. Valaskova and G. S. Martynkova, in Clay Minerals in Nature – Their Characterization, Modification and Application, Intech, Croatia, 1st edn, 2012, ch. 11, pp. 209–238 Search PubMed.
- J. Addison, Regul. Toxicol. Pharmacol., 1995, 21, 397–405 CrossRef CAS PubMed.
- Y. Liang, J. Yu, Z. Feng and P. Ai, Constr. Build. Mater., 2013, 48, 1114–1119 CrossRef PubMed.
- E. M. Bulewicz, A. Pelc, R. Kozjowski and A. Miciukiewicz, Fire Mater., 1985, 9, 171–175 CrossRef CAS PubMed.
- K. M. Slimak and R. A. Slimak, US pat., 7297411 B2, 2007.
- M. Hellberg and A. Ohrn, US pat. pub. no., US2013/0244049 A1, 2013.
- X. Huo, L. Wu, L. Liao, Z. Xia and L. Wang, Powder Technol., 2012, 224, 241–246 CrossRef CAS PubMed.
- M. M. Hirschler, in Heat release in fires, ed. V. Babrauskas and S. J. Grayson, Chapman & Hall, 1992, ch. 12, pp. 375–422 Search PubMed.
- J. Lindholm, A. Brink, C. E. Wilen and M. Hupa, J. Appl. Polym. Sci., 2012, 123, 1793–1800 CrossRef CAS PubMed.
- T. Hakkarainen and Y. Hayashi, Fire Sci. Technol., 2001, 21, 19–42 CrossRef.
- J. Lindholm, A. Brink and M. Hupa,http://www.ffrc.fi/FlameDays_2009/4B/LindholmPaper.pdf.
|
This journal is © The Royal Society of Chemistry 2015 |
Click here to see how this site uses Cookies. View our privacy policy here.