DOI:
10.1039/C5RA03762J
(Paper)
RSC Adv., 2015,
5, 30234-30238
Extractive desulfurization of fuel using N-butylpyridinium-based ionic liquids†
Received
3rd March 2015
, Accepted 20th March 2015
First published on 23rd March 2015
Abstract
Sulfur compounds in fuels have become one of the sources of serious environmental problems. The extractive desulfurization using ionic liquids (ILs) has attracted great attention in recent years. In this work, the pyridinium-based ionic liquids (ILs) N-butylpyridinium thiocyanate ([C4Py][SCN]), N-butylpyridinium bis(trifluoromethylsulfonyl)imide ([C4Py][NTf2]), and N-butylpyridinium dicyanamide ([C4Py][N(CN)2]) were used as extractants for desulfurization of model fuels. The results demonstrate that the structure of the anion influences the extractive performance of ILs, following the order of [NTf2] < [SCN] < [N(CN)2], which was proved by the electrostatic interaction between ions and DBT through molecular dynamics simulations (MD). In addition, the selectivity of sulfur compounds by the extraction process followed the order of dibenzothiophene (DBT) > benzothiophene (BT) > 4,6-dimethyldibenzothiophene (4,6-DMDBT). Moreover, the [C4Py][N(CN)2] can be recycled at least 4 times with little decrease in the desulfurization activity.
1. Introduction
Air pollution, caused by the emission of SOx which is mainly from the combustion of sulfur compounds in gasoline and diesel fuel, is one of the most serious environmental problems in the world. So, many countries have established stringent regulations to limit the sulfur content of transportation fuels. The hydrodesulfurization (HDS) technique must be operated at high temperature and pressure and consumes large amounts of hydrogen to achieve the low level of sulfur (<50 ppmw), which means that it needs high investment and operating costs.1,2 To address the challenges of HDS, some desulfurization technologies including extractive desulfurization,3,4 oxidative desulfurization,5–7 adsorptive desulfurization8,9 and biodesulfurization10,11 have been investigated extensively. Among these technologies, extractive desulfurization attracted great attention due to its application at ambient conditions without special equipment requirements. Although some organic solvents, such as DMF and DMSO were used as extractants to remove aromatic sulfur compounds from the fuel, the results were not satisfactory. In addition, these extractants are usually flammable and volatile organic compounds, which will lead to safety and environmental problems.4
Recently, the extractive desulfurization using ionic liquids (ILs) from fuels has been investigated12–26 due to their special properties, such as negligible vapour pressure, the broad liquid temperature range, the tailorability.27 The extractive desulfurization of fuels using ILs was firstly reported by Wasserscheid et al.,4,12 and they found that the size of the ions played a key role in influencing the extractive performance. Zhang et al.13,14 also proved that the structural effect of ILs on the adsorption capability for thiophene by multinuclear NMR spectroscopy. In our previous work,28–30 we further confirmed that the size and structure of cations played an important role in affecting the extractive performance of ILs. In order to have a better insight into the structure–property relationship of this series of ILs with respect to the extractive desulfurization, the anion of pyridinium-based ILs was altered from [BF4] to [SCN], [N(CN)2] and [NTf2]. The extractive mechanism was proposed by the radial distribution functions (RDFs) and intermolecular energies electrostatic interaction between ions and DBT through molecular dynamics simulations (MD).
2. Experimental section
2.1. Materials
Benzothiophene (BT), dibenzothiophene (DBT), and 4,6-dimethyldibenzothiophene (4,6-DMDBT) were purchased from Acros Organics (USA). Their chemical structures were shown in Fig. 1. All other reagents were purchased from Beijing Chemical Company and were of analytical grade. Methanol was purchased from Fisher Scientific and was of HPLC grade.
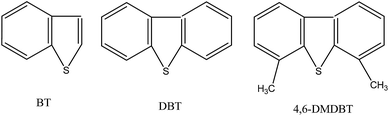 |
| Fig. 1 Chemical structures of the sulfur compounds. | |
2.2. Preparation of ionic liquids
[C4Py][SCN], [C4Py][N(CN)2] and [C4Py][NTf2] were prepared according to the published procedure.28,31,32 The structure of these ILs has been identified by 1H NMR and 13C NMR spectra with a Bruker 600 MHz spectrometer, and the 1H NMR and 13C NMR data being available from ESI† agree with IL structures (Fig. 2). The water content in the ILs was determined by Karl Fischer titration and are below 0.08 wt%. The residual halide content was measured by PXSJ-226 Series Ion meter and are less than 0.10 wt%.
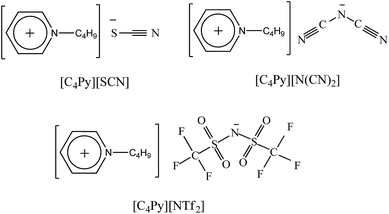 |
| Fig. 2 The structures of the N-butylpyridinium-based ionic liquids. | |
2.3. Extractive desulfurization process
Model fuel was prepared by dissolving BT, DBT, and 4,6-DMDBT in n-octane, respectively, giving a corresponding sulfur content 300 ppmw. All of the extractive desulfurization experiments were conducted in a 25 mL flask. The mass ratios of ILs to model fuel were 1
:
1, 1
:
3, 1
:
5. The ILs were added to the model fuel, mechanically stirred with running speed 600 rpm for 15 min at 25 °C to reach thermodynamic equilibrium. The n-octane phase was then separated from the ionic liquid phase for analysis.
Sulfur partition coefficient on mass basis (KN), which is defined as the ratio of sulfur concentration in IL to the sulfur concentration in the model fuel. In this work, the mass of ILs and model fuel are equal.
KN = [sulfur concentration]IL/[sulfur concentration]model fuel |
2.4. Analytical methods
High-performance liquid chromatography (HPLC) was used for the quantitative assay of BT, DBT, and 4,6-DMDBT in the n-octane phase. HPLC was performed using the Agilent 1100 (HP1100, Agilent, Santa Clara, CA) liquid chromatograph equipped with an autosampler, a reversed-phase Zorbax SB-C18 column (4.6 × 150 mm; 3.6 μm), and an ultraviolet detector. The mobile phase was 90% of methanol in water (v/v, %), with a flow rate of 1.0 mL min−1. For the quantification of BT, DBT and 4,6-DMDBT, the external standard method was used at 280 nm.
The method to analyze the ILs-saturated model fuel sample is according to the published procedure.17,29
3. Results and discussion
3.1. Mutual-solubility of the ILs and model fuel
The mutual solubility of the ILs and model fuel is a key index for assessing the application of an extractant. In this work, the solubility of N-butylpyridinium-based ILs in the model fuel was investigated by HPLC. The results indicated that no obvious N-butylpyridinium-based IL peak was found, which meant that the N-butylpyridinium-based ILs has negligible solubility in model fuel. However, the model fuel has a certain solubility in the N-butylpyridinium-based ILs (Table 1), which was detected using a gravimetric method by weighing the mass difference of a given amount of N-butylpyridinium-based ILs and the corresponding N-butylpyridinium-based ILs saturated with model fuel. As shown in Table 1, the solubility of model fuel in N-butylpyridinium-based ILs follows the order of [C4Py][SCN] < [C4Py][N(CN)2] < [C4Py][NTf2], with the maximum solubility being 0.81 wt% for [C4Py][NTf2], which is smaller than that reported in our previous work.29,30 When the anion of N-butylpyridinium-based ILs varied from [SCN] to [NTf2], the size of the anions of N-butylpyridinium-based ILs became larger and the hydrophobic of the ILs became stronger. So the solubility of model fuel in N-butylpyridinium-based ILs increases accordingly.
Table 1 Solubility of model fuel in N-butylpyridinium-based ILs at 25 °C in mass percentage
ILs |
[C4Py][SCN] |
[C4Py][N(CN)2] |
[C4Py][NTf2] |
Oil solubility in IL, wt% |
0.24 |
0.39 |
0.81 |
3.2. Influence of different ILs on sulfur removal
Three N-butylpyridinium-based ILs were investigated for extraction desulfurization at the following conditions: the model oil was 300 ppmw S in n-octane, the mass ratios of ILs to model fuel were set at 1
:
1, 1
:
3, 1
:
5 at 25 °C. The extractive desulfurization performances of N-butylpyridinium-based ILs were displayed in Fig. 3. As seen from Fig. 3, the mass ratios of ILs to model fuel played a key role in affecting the desulfurization performance of N-butylpyridinium-based ILs. For example, when the mass ratios of [C4Py][N(CN)2] to model fuel (BT as sulfur compound) varied from 1
:
5 to 1
:
1, the sulfur removal increased from 26.2% to 63.5%. Fig. 3 also indicated that the kinds of N-butylpyridinium-based ILs influenced the sulfur removal. For a certain mass ratios of ILs to model fuel, the extractive performance of studied N-butylpyridinium-based ILs followed the order of [C4Py][NTf2] < [C4Py][SCN] < [C4Py][N(CN)2] for a given sulfur compound. The ILs studied in this work have the same cations and different anions, leading to the different desulfurization performance, which is in accordance with the results reported by Su et al. that the sizes of cation and anion greatly affected the interaction of absorbed thiophene and methylimidazole based-ILs.33
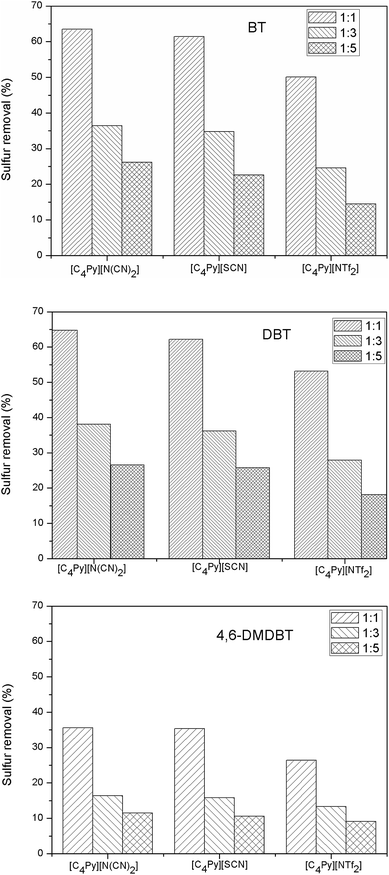 |
| Fig. 3 Sulfur removal for extraction of sulfur compounds with different ILs at different mass ratio of IL to model fuel. | |
Molecular dynamics simulations were performed using MDynamix 5.0 package34 to elucidate why [C4Py][N(CN)2] exhibits a better extractive performance than [C4Py][NTf2] and [C4Py][SCN], and DBT was used as model compounds in this work. The equilibrated time lasted for more than 1.0 ns, and each production phase lasted for 5.0 ns. In order to clarify difference of the interaction between anions and DBT, RDFs between anion of ILs and DBT were investigated. As seen from Fig. 4, it is clear that the interaction between DBT and [NTf2] anion is stronger than that of [SCN] and [N(CN)2], characterized by a sharp, intense peak (2.0) at around 4.5 Å for [NTf2] and a wide peak (0.75, 0.55) at around 4.5 Å for [N(CN)2], [SCN], respectively. However, extractive desulfurization by ILs is the synergy between cation and anion of ILs. Thus, the interaction between ions and DBT are calculated and displayed in Table 2. It can be seen that the total interactions energies between [C4Py][SCN], [C4Py][N(CN)2], [C4Py][NTf2] and DBT are −157.25 kJ mol−1, −164.04 kJ mol−1, −146.51 kJ mol−1, respectively, and follow the order of [C4Py][NTf2] < [C4Py][SCN] < [C4Py][N(CN)2], which is in good agreement with the order of extractive performance of N-butylpyridinium-based ILs. In other words, the intermolecular interactions energies between N-butylpyridinium-based ILs and DBT cause the difference in desulfurization performance for DBT.
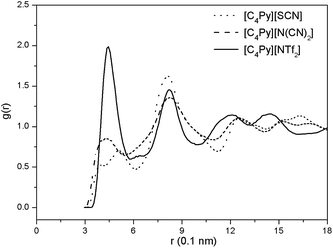 |
| Fig. 4 Radial Distribution Function (RDF) between anion and DBT. | |
Table 2 Interaction energy between ions of N-butylpyridinium-based ILs and DBT
IL |
Electrostatic interaction (kJ mol−1) |
[C4Py][SCN] |
Cation–DBT |
−63.93 |
Anion–DBT |
−93.32 |
IL–DBT |
−157.25 |
[C4Py][N(CN)2] |
Cation–DBT |
−67.34 |
Anion–DBT |
−96.70 |
IL–DBT |
−164.04 |
[C4Py][NTf2] |
Cation–DBT |
−43.40 |
Anion–DBT |
−103.11 |
IL–DBT |
−146.51 |
The sulfur partition coefficient on mass basis (KN) was listed in Table 3 based on the data in Fig. 3. As shown in Table 3, BT and DBT sulfur compounds can be extracted with higher efficiency using these three ILs. In addition, the KN values for DBT in other ILs were listed in Table 4. It can be seen from Table 4 that the sulfur removal performance of these three ILs was superior to most reported ILs in the literatures. Table 4 also indicated that these three ILs studied in this work are more competitive and feasible for extractive desulfurization from fuel.
Table 3 Sulfur partition coefficients (KN) for extraction of sulfur compounds with N-butylpyridinium-based ILsa
IL |
KN in mg(S) kg(IL)−1/mg(S) kg(oil)−1 |
BT |
DBT |
4,6-DMDBT |
Model oil: 300 ppmw S as sulfur compound in n-octane; mass ratio 1 : 1, mixing time 15 min, 25 °C. |
[C4Py][SCN] |
1.59 |
1.64 |
0.54 |
[C4Py][N(CN)2] |
1.74 |
1.84 |
0.55 |
[C4Py][NTf2] |
1.00 |
1.13 |
0.36 |
Table 4 Sulfur partition coefficients for extraction of DBT with different ILs
IL |
KN in mg(S) kg(IL)−1/mg(S) kg(oil)−1 |
IL |
KN in mg(S) kg(IL)−1/mg(S) kg(oil)−1 |
Model oil,4 500 ppmw S as DBT in n-dodecane; mass ratio 1 : 1, mixing time 15 min, room temperature. 60 °C. Real gasoline,17 sulfur as DBT, 298.15 K. Model oil,28 160 ppmw S as DBT in n-dodecane, mass ratio 1 : 1, mixing time 15 min, room temperature. 300 ppmw S as DBT in n-octane, mass ratio 1 : 1, mixing time 15 min, 25 °C. |
[C4mim][Cl/AlCl3]a |
4.0 |
[C2mim][DEP]c |
1.27 |
[C4mim][BF4]a |
0.7 |
[Cmim][DMP]c |
0.46 |
[C4mim][PF6]b |
0.9 |
[C4Py][BF4]d |
0.77 |
[C4mim][OcSO4]a |
1.9 |
[C4Py][SCN]e |
1.64 |
[C2mim][EtSO4]a |
0.8 |
[C4Py][N(CN)2]e |
1.84 |
[Cmim][Me2PO4]a |
0.7 |
[C4Py][NTf2]e |
1.13 |
[C4mim][DBP]c |
1.59 |
|
|
3.3. Influence of sulfur species on sulfur removal
To study the extractive performance of [C4Py][N(CN)2] on different sulfur compounds, BT, DBT, and 4,6-DMDBT were selected as the representative in this study (the chemical structures of BT, DBT, and 4,6-DMDBT were shown in Fig. 1). The results in Fig. 5 indicated that the sulfur removal through extraction process decreased in the order of DBT > BT > 4,6-DMDBT for [C4Py][N(CN)2]. For the three sulfur compounds, the different sulfur removal may be influenced mainly by aromatic π-electron density of sulfur compounds and the steric hindrance, which is in accord with the results reported by Zhang et al. that sulfur compounds with higher density of aromatic π-electron are favorably absorbed by ionic liquids and the steric effects of the sulfur compounds also influence the absorption capacity of ILs.13,14 In addition, the difference of the electron density on the sulfur atoms may further result in the different sulfur removal. As calculated by Otsuki et al.,5 the electron density on the sulfur atoms of BT, DBT, 4,6-DMDBT is 5.739, 5.758, 5.760, respectively. The electron density on the sulfur atom of DBT is as much as 4,6-DMDBT. So, the low extractive performance of [C4Py][N(CN)2] on 4,6-DMDBT was mainly affected by the methyl substitution at the 4 and 6 positions of DBT, which remarkably hinders the approach of 4,6-DMDBT to IL. Therefore, the sulfur removal selectivity of sulfur compounds followed the order of 4,6-DMDBT < BT < DBT for the mentioned IL.
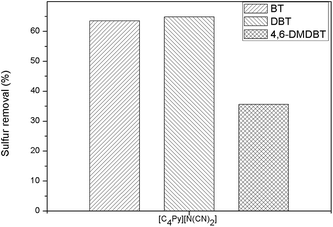 |
| Fig. 5 The extractive performance of [C4Py][N(CN)2] for BT, DBT, 4,6-DMDBT from model fuel. Experimental conditions: IL: model fuel (w/w): 1 : 1, extraction time: 15 min, 25 °C. | |
3.4. Recycling of the ionic liquids
The regeneration and subsequent recycling of ILs are greatly important in industrial application. In this work, the regeneration of [C4Py][N(CN)2] was investigated by the water dilution process, which is similar to published procedures.17,28 The 1H NMR analyses of the [C4Py][N(CN)2] after regeneration was studied. The result showed that there was no change in the structure of the [C4Py][N(CN)2]. In addition, the data shown in Table 5 indicated that the [C4Py][N(CN)2] could be recycled four times without a significant decrease in extractive performance. Nevertheless, due to the high energy cost for water evaporation, this method is only suitable for laboratory scale not in industry. Some low energy cost techniques for separating IL form water should be investigated in the further.
Table 5 Sulfur removal from model fuel by recycling of [C4Py][N(CN)2]
IL |
Cyclesa |
Sulfur removal, (%) |
Experimental conditions: IL: model fuel (w/w): 1 : 1, sulfur content 300 ppmw (DBT), 25 °C. |
[C4Py][N(CN)2] |
1 |
64.6 |
2 |
63.5 |
3 |
63.1 |
4 |
62.9 |
4. Conclusions
Three N-butylpyridinium-based ILs were found to be effective for removal of aromatic sulfur compounds from model fuel. The results indicated that the extractive performance of these ILs followed the order of [C4Py][NTf2] < [C4Py][SCN] < [C4Py][N(CN)2], and for a given IL, the selectivity of sulfur compounds by extraction process followed the order of DBT > BT > 4,6-DMDBT under the same conditions. These ILs would not contaminate the model fuel due to their insolubility. On the other hand, model fuel has a certain solubility in these ILs, varying from 0.24 wt% for [C4Py][SCN] to 0.81 wt% for [C4Py][NTf2]. Radial distribution function (RDF) between anion of ILs and DBT and interaction energy analysis indicated that synergying between anion and cation greatly affected the desulfurization performance of ILs. Moreover, molecular dynamics simulations (MD) results further proved that the better desulfurization performance of [C4Py][N(CN)2] is mostly attributed to the stronger interaction between the ions and DBT. The IL [C4Py][N(CN)2] could be regenerated through a water dilution process. According to these results, [C4Py][N(CN)2] might be used as promising solvents for the extractive desulfurization of fuel.
Acknowledgements
We are grateful to the National Natural Science Foundation of China (no. 21206169, 21436010, 21076113), and the National High Technology Research and Development Program of China (no. 2013AA06540201) for their partial financial support of this research.
References
- A. J. Hernández-Maldonado and R. T. Yang, J. Am. Chem. Soc., 2004, 126, 992–993 CrossRef PubMed.
- C. S. Song, Catal. Today, 2003, 86, 211–263 CrossRef CAS.
- Y. Shiraishi, Y. Hirai and I. Komasawa, Ind. Eng. Chem. Res., 2001, 40, 293–303 CrossRef CAS.
- J. Eßer, P. Wasserscheid and A. Jess, Green Chem., 2004, 6, 316–322 RSC.
- S. Otsuki, T. Nonaka, N. Taksshima, W. Qian, A. Ishihara, T. Imai and T. Kabe, Energy Fuels, 2000, 14, 1232–1239 CrossRef CAS.
- R. Sundararaman and C. S. Song, Energy Fuels, 2013, 27, 6372–6376 CrossRef CAS.
- W. S. Zhu, B. L. Dai, P. W. Wu, Y. H. Chao, J. Xiong, S. H. Xun, H. P. Li and H. M. Li, ACS Sustainable Chem. Eng., 2015, 3, 186–194 CrossRef CAS.
- R. T. Yang, A. J. Hernández-Maldonado and F. H. Yang, Science, 2003, 301, 79–81 CrossRef CAS PubMed.
- J. Xiao, X. X. Wang, M. Fujii, Q. J. Yang and C. S. Song, AIChE J., 2013, 59, 1441–1445 CrossRef CAS.
- Y. G. Li, H. S. Gao, W. L. Li, J. M. Xing and H. Z. Liu, Bioresour. Technol., 2009, 100, 5092–5096 CrossRef CAS PubMed.
- N. K. Bordoloi, S. K. Rai, M. K. Chaudhuri and A. K. Mukherjee, Fuel Process. Technol., 2014, 119, 236–244 CrossRef CAS PubMed.
- A. Bösmann, L. Datsevich, A. Jess, A. Lauter, C. Schmitz and P. Wasserscheid, Chem. Commun., 2001, 2494–2495 RSC.
- S. G. Zhang and Z. C. Zhang, Green Chem., 2002, 4, 376–379 RSC.
- S. G. Zhang, Q. L. Zhang and Z. C. Zhang, Ind. Eng. Chem. Res., 2004, 43, 614–622 CrossRef CAS.
- N. H. Ko, J. S. Lee, E. S. Huh, H. Lee, K. D. Jung, H. S. Kim and M. Cheong, Energy Fuels, 2008, 22, 1687–1690 CrossRef CAS.
- J. D. Holbrey, I. López-Martin, G. Rothenberg, K. R. Seddon, G. Silvero and X. Zhang, Green Chem., 2008, 10, 87–92 RSC.
- Y. Nie, C. X. Li, H. Meng and Z. H. Wang, Fuel Process. Technol., 2008, 89, 978–983 CrossRef CAS PubMed.
- P. S. Kulkarni and C. A. M. Afonso, Green Chem., 2010, 12, 1139–1149 RSC.
- C. Asumana, G. R. Yu, X. Li, J. J. Zhao, G. Liu and X. C. Chen, Green Chem., 2010, 12, 2030–2037 RSC.
- H. Y. Lu, Y. N. Zhang, Z. X. Jiang and C. Li, Green Chem., 2010, 12, 1954–1958 RSC.
- A. R. Hansmeier, G. W. Meindersma and A. B. de Haan, Green Chem., 2011, 13, 1907–1913 RSC.
- B. Rodriguez-Cabo, A. Arce and A. Soto, Fluid Phase Equilib., 2013, 356, 126–135 CrossRef CAS PubMed.
- H. Y. Lu, W. Z. Ren, H. Y. Wang, Y. Wang, W. Chen and Z. H. Suo, Appl. Catal., A, 2013, 453, 376–382 CrossRef CAS PubMed.
- J. J. Gao, H. Meng, Y. Z. Lu, H. X. Zhang and C. X. Li, AIChE J., 2013, 59, 948–958 CrossRef CAS.
- J. Zhang, J. Li, T. Ren, Y. Hu, J. Ge and D. Zhao, RSC Adv., 2014, 4, 3206–3210 RSC.
- H. S. Gao, S. J. Zeng, H. Y. He, H. F. Dong, Y. Nie, X. P. Zhang and S. J. Zhang, Sep. Sci. Technol., 2014, 49, 1208–1214 CrossRef CAS.
- N. V. Plechkova and K. R. Seddon, Chem. Soc. Rev., 2008, 37, 123–150 RSC.
- H. S. Gao, M. F. Luo, J. M. Xing, Y. Wu, Y. G. Li, W. L. Li, Q. F. Liu and H. Z. Liu, Ind. Eng. Chem. Res., 2008, 47, 8384–8388 CrossRef CAS.
- H. S. Gao, Y. G. Li, Y. Wu, M. F. Luo, Q. Li, J. M. Xing and H. Z. Liu, Energy Fuels, 2009, 23, 2690–2694 CrossRef CAS.
- H. S. Gao, C. Guo, J. M. Xing and H. Z. Liu, Sep. Sci. Technol., 2012, 47, 325–330 CrossRef.
- N. M. Yunus, M. I. A. Mutalib, Z. Man, M. A. Bustam and T. Murugesan, Chem. Eng. J., 2012, 189–190, 94–100 CrossRef CAS PubMed.
- S. J. Zeng, H. S. Gao, X. C. Zhang, H. F. Dong, X. P. Zhang and S. J. Zhang, Chem. Eng. J., 2014, 251, 248–256 CrossRef CAS PubMed.
- B. M. Su, S. G. Zhang and Z. C. Zhang, J. Phys. Chem. B, 2004, 108, 19510–19517 CrossRef CAS.
- A. P. Lyubartsev and A. Laaksonen, Comput. Phys. Commun., 2000, 128, 565–589 CrossRef CAS.
Footnote |
† Electronic supplementary information (ESI) available: NMR data of the investigated ILs. See DOI: 10.1039/c5ra03762j |
|
This journal is © The Royal Society of Chemistry 2015 |
Click here to see how this site uses Cookies. View our privacy policy here.