DOI:
10.1039/C5RA03256C
(Paper)
RSC Adv., 2015,
5, 38382-38390
Smart cleaning cotton fabrics cross-linked with thermo-responsive and flexible poly(2-(2-methoxyethoxy)ethoxyethyl methacrylate-co-ethylene glycol methacrylate)
Received
21st February 2015
, Accepted 20th April 2015
First published on 20th April 2015
Abstract
The smart cleaning ability of cotton fabrics is realized by cross-linking thermo-responsive random copolymer to the cotton. Poly(2-(2-methoxyethoxy)ethoxyethyl methacrylate-co-ethylene glycol methacrylate), denoted as P(MEO2MA-co-EGMA), is synthesized from 2-(2-methoxyethoxy)ethoxyethyl methacrylate (MEO2MA) and ethylene glycol methacrylate (EGMA) with a molar ratio of 17
:
3. Its dilute aqueous solution (1 mg mL−1) presents a lower critical solution temperature (LCST) of 38 °C. Furthering increase the solution concentration, the LCST shifts towards lower temperature. By applying citric acid as a cross-linker, P(MEO2MA-co-EGMA) is successfully immobilized onto cotton fabrics. The obtained cotton fabrics also possess thermo-responsive property with a LCST at 37 °C. The smart cleaning ability is confirmed by single fiber cleaning experiments using a confocal microscope. It is observed that the cleaning ability of the cotton with cross-linked P(MEO2MA-co-EGMA) can be prominently enhanced at low temperature (below LCST). In addition, due to the low glass transition temperature of P(MEO2MA-co-EGMA) (−26 °C), the polymer is in a gel state at room temperature and will not negatively impact fabric softness. P(MEO2MA-co-EGMA) is a promising candidate for preparing textiles with smart cleaning ability and great fabric hand.
Introduction
In recent decades, thermo-responsive polymers have attracted more and more attention due to their unique properties: they can respond to an external thermal stimulus by changing their chemical and physical properties, which can be either a variation of hydrophobicity,1 a change of volume,2,3 or an alternation of surface properties.1 The reason for this abrupt change is the variation of hydrogen bonds with temperature.4 At low temperatures, intermolecular hydrogen bonds can be formed between the thermo-responsive polymers and water, which results in dissolution of these polymers in water. The obtained aqueous polymer solutions are transparent. However, when the temperature is increased above a critical value, the thermo-responsive polymers prefer to form intramolecular hydrogen bonds instead of intermolecular bonds with water. Therefore, the formerly dissolved polymer will separate out from water, and the solution will become turbid.3 The corresponding critical temperature is denoted as lower critical solution temperature (LCST). Among various thermo-responsive polymers with LCST behavior, poly(N-isopropylacrylamide) (PNIPAM) is mostly investigated because PNIPAM possesses not only a sharp transition at LCST, but also a LCST close to the human body temperature (32 °C).1,5 PNIPAM is widely studied in the field of biology and medicine,6–11 with a focus on drug delivery, diagnostics, chemical separation and surface modification. PNIPAM can be also introduced into textiles, which directly contact the human body to realize special functions to the traditional fabrics,12–19 such as body temperature or air permeability control, water storage, water proof and aroma/vitamin release. However, PNIPAM possesses two remarkable disadvantages when applied in textiles. The first disadvantage is the high glass transition temperature (Tg) of PNIPAM (140 °C).20 Thus, PNIPAM is in the glassy state at ambient conditions. If PNIPAM is introduced into the textiles to produce smart textiles, for example in case of textiles used for wound healing, the obtained fabrics have a high stiffness, which may cause hurt in contact with the tender wound. The second disadvantage is its difficulty to adjust the LCST of PNIPAM according to its applications. For example, smart textiles designed for fire fighters require much higher LCST than that used for athletes, making PNIPAM not feasible for fire fighter applications. Therefore, thermo-responsive polymers with lower Tg and adjustable LCST are favored in the textile industry. Recently, a new series of thermo-responsive polymers with poly(ethylene oxide) (PEO) as side chains were successfully synthesized.21,22 Comparing to the well investigated PNIPAM, this class of thermo-responsive polymers has several advantages. First, most of the methacrylates have a Tg lower than 0 °C. For instance, the Tg of poly[(2-(2-methoxyethoxy)ethylmethacrylate)] (PMEO2MA) is −40 °C. Further increasing the number of PEO units in the side chain to 3 units (poly(2-[2-(2-methoxyethoxy)ethoxy]ethylmethacrylate), PMEO3MA), Tg is even further decreased (−50 °C).21 Due to their low Tg, these thermo-responsive polymers are in gel states at room temperature. If they are introduced into textiles, the obtained smart textiles will feel soft and comfortable. Secondly, the LCST of this class of thermo-responsive polymers is related to the number of PEO units in the side chains. The more PEO units in the side chain, the higher is the LCST of the polymer. For instance, PMEO2MA has a LCST at around 28 °C. Increasing the number of PEO units to 3 units, the LCST is shifted to 50 °C. Further prolonging the PEO part to 8–9 units, the LCST can be increased to even 90 °C.21 Hence, by varying the ratio of monomers with different PEO units in the copolymer, the LCST can be easily and precisely adjusted according to different application requirements.
As mentioned above, thermo-responsive polymers can switch from hydrophilicity to hydrophobicity when the temperature is raised above LCST.3 It is well known that the fabric cleaning performance can be improved when fabrics are more hydrophilic. In a simple case this can be achieved with a hydrophilic copolymer coating of the fabric. However, with a thermo-responsive polymer, a switching between a hydrophobic and a hydrophilic state can be achieved. If a thermo-responsive polymer with a LCST around body temperature is introduced into textiles, the clothes will be in the hydrophobic state and the dirt cannot sustain on the textile surface when they are worn above the LCST. However, when the washing temperature is lower than the LCST, the thermo-responsive polymers will switch to the hydrophilic state in the washing process and soils on the textiles can be easily removed. Therefore, textiles with thermo-responsive polymers can be used to enhance the cleaning ability during laundry. Such textiles will be superior to those coated with simple hydrophilic copolymers.
In order to realize the enhancement of the cleaning ability as mentioned above, thermo-responsive polymers need to be immobilized onto the textiles. General approaches for the immobilization include grafting23 and cross-linking.24,25 Comparing to grafting, the cross-linking can be viewed as more user friendly and effective for fabric treatments. For this reason, citric acid is used as a cross-linker in our investigation. The monomers 2-(2-methoxyethoxy)ethoxyethyl methacrylate (MEO2MA) and ethylene glycol methacrylate (EGMA) are used to synthesize the thermo-responsive random copolymer P(MEO2MA-co-EGMA). Since EGMA can introduce reactive end group –OH into the copolymer, the cross-linker can react with the copolymer and –OH groups of the cotton. Thus, P(MEO2MA-co-EGMA) can be immobilized onto the cotton surface.
Experimental
Materials
The thermo-responsive random copolymer poly(2-(2-methoxyethoxy)ethoxyethyl methacrylate-co-ethylene glycol methacrylate), denoted as P(MEO2MA-co-EGMA), was synthesized by 2-(2-methoxyethoxy)ethoxyethyl methacrylate (MEO2MA) and ethylene glycol methacrylate (EGMA) with a molar ratio of 17
:
3. The monomer MEO2MA (purity 95%) and EGMA (purity 95%) was purchased from Sigma Aldrich. n-Hexane and citric acid were obtained from Gaojing fine chemical. Ethyl-2-bromoisobutyrate (EBiB, purity 98%), N,N,N′,N′′,N′′-pentamethyldiethylenetriamine (PMDETA, purity 99%), anisole and sodium hypophosphite were received from Aladdin. Tetrahydrofuran (THF) was from Yongda Chemicals. CuBr (purity 98.5%) was bought from Qiangshun Chemicals.
Synthesis of random copolymer P(MEO2MA-co-EGMA)
For polymerization, monomer MEO2MA (3.14 mL; 17 mmol), EGMA (0.94 mL; 3 mmol), PMDETA (45 μL; 0.21 mmol), catalyzer CuBr (20 mg; 0.14 mmol), 10 mL anisole, initiator EBiB (21 μL; 0.14 mmol) were added into a clean tube in the glove box. Afterwards, the tube was sealed and immersed into an oil bath preheated to 90 °C. After 2 h, the reaction was quenched by placing the reaction tube into the ice water. The mixture was first diluted by THF, and then eluted in the aluminum oxide column by THF to remove residual CuBr. Finally it was precipitated thrice into hexane. The obtained random copolymer P(MEO2MA-co-EGMA) was a transparent and viscous gel.
ATR-FTIR spectroscopy
With ATR-FTIR spectroscopy (Bruker Vertex 70 spectrometer), the functional groups and the intermolecular hydrogen bonds formed between polymers and water were investigated. The scanned wavelength covered a range from 600 cm−1 to 4000 cm−1 with a resolution of 4 cm−1. During the measurements, the initially prepared cotton fabrics with cross-linked P(MEO2MA-co-EGMA) were first probed. Afterwards, they were placed in a sealed plastic cell with pre-installed saturated water vapor atmosphere. The swollen cotton fabrics were measured again after swelling reached an equilibrium state. Then, by increasing the temperature of the sample cell above LCST, the variation of the hydrogen bonds in the fabrics was accessed.
UV-Vis spectroscopy
By UV-Vis spectroscopy (Perkin Elmer UV/Vis Lambda 35 spectrometer), the transition behavior of P(MEO2MA-co-EGMA) in aqueous solution was investigated. The LCST of P(MEO2MA-co-EGMA) was determined by the alternation of transparency, when the temperature increased from 32 °C to 42 °C with an increase rate of 0.2 °C min−1. The concentration was fixed as 1 mg mL−1. The wavelength applied was 500 nm.
Preparation of cotton fabrics with cross-linked P(MEO2MA-co-EGMA)
The cotton fabrics with cross-linked P(MEO2MA-co-EGMA) were prepared as following: first, the original cotton fabrics were immersed in a solution containing 4% (wt%) P(MEO2MA-co-EGMA), 2% citric acid, 3% sodium hypophosphite, 91% H2O for 4 h. Afterwards, the fabrics were moved out from the solution and rolled. The immersion and roll process were repeated twice to ensure a sufficient amount of copolymer and cross-linker on the cotton surface. For the thermal treatment, first the fabrics were placed in an oven with a temperature of 60 °C for 8 min. Then, the temperature was raised to 130 °C and thermo-stated for 2 min. After thermal treatment, the fabrics were flushed with water to remove all unreacted copolymer and cross-linker. Finally, the cotton fabrics with cross-linked P(MEO2MA-co-EGMA) were mounted in the oven at 60 °C for 10 min to remove the residue water. In order to compare the influence of different amounts of cross-linked P(MEO2MA-co-EGMA) to the softness of the cotton fabrics, the polymer concentrations were selected as 1%, 2%, 4% and 8%.
Confocal microscopy
The smart cleaning ability of cotton fabrics with cross-linked P(MEO2MA-co-EGMA) was measured by confocal microscopy (Nikon C2), abbreviated as CM. Cooking oil was used to mimic the dirt on the fabrics and Nile red was selected as the fluorescent dye. During the measurements, both cotton fabrics, with or without cross-linked P(MEO2MA-co-EGMA), were first dipped into the cooking oil for 60 s and then immersed into the Nile red for 60 s. After drying in the oven for 24 hours, the dyed fabrics were probed by CM at 15 °C. Afterwards, the dyed fabrics were rinsed by the distilled water with different temperatures to simulate the washing process of the fabrics below and above the LCST. Both fabrics were rinsed with water at a temperature of 45 °C (above the LCST) for 10 times and the rinsed fabrics were measured by CM again. Then, the fabrics were further rinsed with water at a temperature of 25 °C (below the LCST) for another 10 times, and remeasured by CM. The cleaning performance was distinguished by the fluorescence intensities of the fabrics before and after rinsing. The fluorescence intensities of the fibers were analyzed by the software Image-Pro Plus.
Scanning electron microscopy (SEM)
Scanning electron microscopy (SEM, JEOL JSM-5610LV) was used to probe the surface morphology of the cotton fabrics, with and without cross-linked P(MEO2MA-co-EGMA). The magnitude selected was 2000×. The working distance and the voltage applied in the measurements were 6 mm and 30 kV, respectively.
X-ray photoelectron spectroscopy (XPS)
The surface compositions of the cotton fabric and the cotton fabric with cross-linked P(MEO2MA-co-EGMA) were analysed by X-ray photoelectron spectrometer (XPS, Axis Ultra from Kratos Analytical, UK). A monochromatized Al-Kα X-ray was selected as the excitation source (1486.7 eV). The survey scans were obtained at 100 eV pass energy and 1 eV steps.
Washing fastness measurements
The washing fastness measurements were performed to test the durability of the cross-linked P(MEO2MA-co-EGMA) on the cotton fabric. During the measurements, the detergent concentration was fixed at 1 mg mL−1. First, the cotton fabric was placed in a beaker containing distilled water. The ratio of cotton to distilled water was 1
:
50. After washing for 30 min, the cotton fabric was moved out from the beaker and flushed with distilled water to remove the residue detergent. After drying in the oven for 12 hours, the cotton was weighed. The washing process was repeated 5 time to test the fastness of the cross-linked P(MEO2MA-co-EGMA) on the cotton fabric.
Contact angle measurements
The contact angle and wetting time of the cotton fabrics with cross-linked P(MEO2MA-co-EGMA) at different temperatures were probed by the drop shape analyzer (Krüss DSA20). During the measurements, 2 μL distilled water was dropped onto the cotton surface. For the contact angle measurements, the contact angles of the water droplets after approaching the cotton surface were monitored. For the wetting time measurements, the time of the water droplet immerses into the cotton was counted. For each sample, the measurements were repeated four times to minimize the experimental error.
Softness measurements
Fabric softness was measured by Phabrometer. Before the measurements, the cotton fabrics were cut into circular shape with a diameter of 12 cm. The precut fabrics were stored in an atmosphere with a temperature of 20 ± 2 °C and a relative humidity of 65 ± 3% for 24 h. Four samples were probed during the measurements. Among them, one was the original cotton fabric. Three of them were the cotton fabrics with cross-linked P(MEO2MA-co-EGMA) prepared from solution concentrations of 1%, 2%, and 4%.
Results and discussion
Characterization of P(MEO2MA-co-EGMA)
The schematic presentation for the synthesis of P(MEO2MA-co-EGMA) is shown in Fig. 1. In our present investigation, the ratio of MEO2MA to EGMA (m
:
n) is fixed as 17
:
3.
 |
| Fig. 1 Schematic presentation for the synthesis of P(MEO2MA-co-EGMA). | |
The obtained copolymer was characterized by 1H-NMR in deuterated chloroform and by size exclusion chromatography (SEC) in THF. Fig. 2 shows the characteristic 1H-NMR spectrum of P(MEO2MA-co-EGMA). The signal (10) from the methoxy group –CH2–O–CH3 in the MEO2MA side chain is resolved. Simultaneously, the signal (9) from the hydroxyl group –CH2–OH in the EGMA side chain is also visible in the spectra. Thus, it confirms the presence of both, MEO2MA and EGMA in the copolymers. SEC reveals a moderate polydispersity of 2.23. The obtained number average molar mass is Mn = 34
100 g mol−1.
 |
| Fig. 2 Characteristic 1H-NMR spectrum of P(MEO2MA-co-EGMA). | |
The glass transition temperature (Tg) is determined by DSC with a heat rate of 10 °C min−1. From the curve obtained (Fig. 3), Tg of P(MEO2MA-co-EGMA) is determined as −26 °C, which is well below 0 °C.
 |
| Fig. 3 DSC curve of P(MEO2MA-co-EGMA). | |
In order to investigate the transition behavior of the thermo-responsive random copolymer P(MEO2MA-co-EGMA) in aqueous solutions, measurements with UV-Vis spectroscopy are performed.
Fig. 4 shows the transmission of the P(MEO2MA-co-EGMA) aqueous solutions as a function of temperature. The solution concentrations are varied from 1 mg mL−1 (black) to 5 mg mL−1 (red) and 10 mg mL−1 (blue). From Fig. 4b, it is obvious that the P(MEO2MA-co-EGMA) aqueous solution is thermo-responsive. It switches from a transparent state (transmission 100%) to a turbid state (transmission 0), when the temperature is raised above the LCST. By plotting the first derivative of the transmission to the temperature as a function of temperature (Fig. 3a), the LCST can be determined as the temperature showing the minimum value in the first derivative. Thus, the LCST of P(MEO2MA-co-EGMA) is 38 °C when the concentration is 1 mg mL−1. In comparison with the homopolymer PMEO2MA, which possesses a LCST of 28 °C, the LCST of P(MEO2MA-co-EGMA) is 10 °C higher. The possible reason for the raise of the LCST is the introduction of EGMA. As the PEO side chains are longer and there are additional –OH groups in EGMA, the hydrophilicity of the obtained random copolymer is enhanced, inducing the transition behavior to occur at a higher temperature. Moreover, unlike the well investigated PNIPAM, which possesses a very sharp and abrupt transition, P(MEO2MA-co-EGMA) shows a broader transition region (around 2 °C). The reason might be related to the missing of strongly polarized H-atoms in P(MEO2MA-co-EGMA). In PNIPAM, both, the C
O and N–H groups can form intermolecular hydrogen bonds between water molecules and polymers at low temperatures. PNIPAM can act in hydrogen bonds both as an acceptor (C
O) and as a donor (N–H). When the temperature is increased above the LCST, both hydrogen bonds will be broken in a collective way,26 causing the transition behavior to be abrupt. In contrast, there is only C
O groups in P(MEO2MA-co-EGMA) which can form hydrogen bonds. As a consequence, P(MEO2MA-co-EGMA) can only act as an acceptor and not as a donor. No collective bond breaking will be stimulated. Thus, the transition behavior observed in case of P(MEO2MA-co-EGMA) is not as abrupt as that of PNIPAM, but smeared over several degrees.
 |
| Fig. 4 (a) The first derivative of the transmission to the temperature as a function of temperature. The concentrations are 1 mg mL−1 (black), 5 mg mL−1 (red) and 10 mg mL−1 (blue). (b) The transmission of P(MEO2MA-co-EGMA) aqueous solutions as a function of temperature investigated by UV-Vis spectroscopy. | |
When the concentration is increased from 1 to 5 mg mL−1, a similar transition behavior is observed. However, the LCST shifts towards lower temperature (from 38 °C to 36 °C, see Fig. 4a). Further increasing the concentration to 10 mg mL−1 results in no further decrease of the LCST as the transition behavior is almost identical to that of the solution with a concentration of 5 mg mL−1. A concentration dependence of the thermo-responsive behavior, e.g. of the cloud point was reported before in case of low polymer concentrations.27
Characterization of cotton fabrics with cross-linked P(MEO2MA-co-EGMA)
After characterizing the transition behavior of P(MEO2MA-co-EGMA) in aqueous solutions, which confirms the thermo-responsive capability of the random copolymer, it is introduced into cotton fabrics by cross-linking. Fig. 5 presents the cross-linking phenomenon during the preparation. The COOH– functional groups in citric acid can react with OH– groups in P(MEO2MA-co-EGMA) and cotton fabrics. Therefore, P(MEO2MA-co-EGMA) is not only immobilized on cotton surface, but also forms a hydrogel with a cross-linked network structure.
 |
| Fig. 5 Schematic presentation for the cross-linking phenomenon of the copolymer with the cotton fabrics during the preparation. | |
XPS is applied to analyze the surface before and after cross-linking. The obtained spectrum for the original cotton (black) and the cotton with cross-linked P(MEO2MA-co-EGMA) (red) are shown in Fig. 6. The solution concentration used for the preparation is 8%. The amount of O significantly decreases after the cotton fabric is cross-linked with P(MEO2MA-co-EGMA). Simultaneously the amount of C increases after cross-linking. From the spectrum, the ratios of C/O in the original cotton and cotton with cross-linked P(MEO2MA-co-EGMA) can be calculated as 1.92 and 3.1, respectively. According to literature, the fractions of C and O in cotton are 44.44% and 49.39%, respectively. For P(MEO2MA-co-EGMA) these values are changed to 57.89% and 35.17%, respectively. Comparing these values, more C will be on the surface if the cross-linking process succeeds. Thus, the increase of C/O ratio from XPS demonstrates the surface coverage with the copolymer.
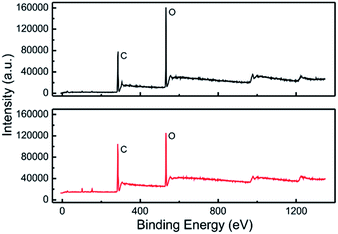 |
| Fig. 6 XPS spectrum of the original cotton (black) and cotton with cross-linked P(MEO2MA-co-EGMA) (red). The solution concentration used for the preparation is 8%. | |
Fig. 7 shows the FESEM images of the original cotton fabric and the cotton fabrics with cross-linked P(MEO2MA-co-EGMA) (solution concentration of 2%, 4% and 8%). From Fig. 7a, it is obvious that the original cotton fabric shows a smooth surface. There is no dust or polymer observed. After cross-linking the cotton fabric with P(MEO2MA-co-EGMA) (solution concentration of 2%), there is no prominent change observable on the surface (Fig. 7b). There are only very thin lines connecting the cotton fibers in the image. It might be the copolymer used in the preparation. Furthering increasing the concentration to 4%, the surface of fiber becomes rough (Fig. 7c). There is a thin copolymer layer observed on the surface. However this thin layer is not homogenous. The possible reason might be the insufficient amount of copolymer used for the preparation, which cannot cover the whole surface. When the solution concentration is increased to 8%, the thin copolymer layer on the surface is more homogenous (Fig. 7d). Even a thin layer connecting two neighboring fibers is visible in the image (marked by red ellipse in Fig. 7d).
 |
| Fig. 7 FESEM images of (a) an original cotton fiber, (b–d) a cotton fiber with cross-linked P(MEO2MA-co-EGMA). The solution concentrations are 2% (b), 4% (c) and 8% (d), respectively. | |
In order to confirm that P(MEO2MA-co-EGMA) is immobilized onto the cotton by cross-linking, washing fastness measurements are performed on the cotton fabrics with and without cross-linked P(MEO2MA-co-EGMA). For comparison, cotton fabrics coated with the same amount of P(MEO2MA-co-EGMA) but without using the cross-linker citric acid are investigated as well. It should be noted that the preparation for these two series of cotton fabrics is else identical and the only difference is the use of citric acid. Fig. 8a compares the weight loss of the cotton fabrics coated with P(MEO2MA-co-EGMA) with citric acid (circles) and without citric acid (squares). The solution concentrations are varied with 2% (red), 4% (blue) and 8% (green). Pure cotton (black squares) shows only a minor decrease with increasing washing time, which can be attributed to the loss of cotton fibers during washing. In case of cotton fabric with cross-linked P(MEO2MA-co-EGMA) the weight also decreases. However, even the maximum value of the weight loss (green circles) is less than 2%. A possible reason for such weight loss of the cotton fabrics with cross-linked P(MEO2MA-co-EGMA) can be a small amount of copolymers used in the preparation are not cross-linked with cotton. Non cross-linked polymers are only entangled with each other and such physically attached copolymers will be removed during washing. In contrast, cotton coated with P(MEO2MA-co-EGMA) but without cross-linking via citric acid shows an intense weight loss after washing. Because all P(MEO2MA-co-EGMA) is only physically attached to the cotton, the polymers will be easily removed by washing. For example, the weight loss of cotton prepared with a P(MEO2MA-co-EGMA) solution with a concentration of 8% (green squares) is 7.4% after washing two times. Afterwards it stays constant. It should be noted that the weight increase of this cotton fabric has been around 7.5% after coating, which means that most of the copolymer has been already washed away after washing twice. As indicated by the bar, there is a huge difference of weight loss between cotton fabrics with and without using cross-linker citric acid. It can be attributed to the cross-linking of P(MEO2MA-co-EGMA) to the cotton fabrics.
 |
| Fig. 8 (a) Weight loss of the original cotton fabric (black squares), cotton fabrics coated with P(MEO2MA-co-EGMA) with (open circles) and without citric acid (open squares) as function of washing times. The solution concentration varies is 2% (red), 4% (blue) or 8% (green). (b) Wetting time of the original cotton fabric (filled squares), cotton fabrics coated with P(MEO2MA-co-EGMA) with (open circles) and without citric acid (open squares) as a function of temperature after washing 5 times. The solution concentration for both cotton fabrics are fixed at 8%. | |
In addition, to confirm that the part left on the cotton after washing is still cross-linked P(MEO2MA-co-EGMA), wetting time measurements are performed on the original cotton (filled squares), cotton coated with P(MEO2MA-co-EGMA) with (open circles) and without citric acid (open squares) after washing (Fig. 8b). The P(MEO2MA-co-EGMA) solution concentrations for both cotton fabrics are fixed at 8%. The wetting time of the original cotton does not change with temperature, indicating that it is not thermo-responsive. In case of the cotton fabric with cross-linked P(MEO2MA-co-EGMA), the wetting time dramatically increases from 12.8 s to 28.6 s when the temperature is above LCST. As the wetting time is related to the surface hydrophobicity, the longer is the wetting time, the more hydrophobic is the surface. Thus, from the change of the wetting time, it can be ensured that the cotton fabrics with cross-linked P(MEO2MA-co-EGMA) are still thermo-responsive after washing five times. On the contrary, the wetting time of the cotton coated P(MEO2MA-co-EGMA) but without citric acid remains constant when the temperature increases above LCST. It shows no more thermo-responsive capability. Therefore, it can be concluded that most of the copolymer coated on the cotton has been washed away and only pure cotton fabric is left.
In order to ensure that the layer observed on the surface is P(MEO2MA-co-EGMA), ATR-FTIR measurement are performed (Fig. 9). Curve 1 in Fig. 9 displays the spectra of the original cotton fabric. As the main component in the cotton is cellulose, O–H (3300–3600 cm−1) and C–H bands (2800–3000 cm−1), as well as the characteristic peak of C–O (1104 cm−1), are observed in curve 1. After the cotton fabric is cross-linked with P(MEO2MA-co-EGMA) (solution concentration of 4%), the spectra obtained (curve 2) is similar as the original cotton fabric. However, there is one difference between curve 1 and curve 2. The characteristic peak assigned to C
O emerges at 1728 cm−1, which can be attributed to the C
O in the side chain of MEO2MA and EGMA moieties. Thus, the presence of P(MEO2MA-co-EGMA) is successfully shown in the spectra. The C
O peak is not very prominent, which might be caused by the FTIR mode used in the measurements. In the applied ATR-FTIR mode, the penetration depth is only several μm. Because the cross-linked P(MEO2MA-co-EGMA) layer on the surface is very thin (around 1 μm) and not homogeneous, the spectrum obtained is mainly from cellulose. Therefore the amplitude of the C
O peak from MEO2MA and EGMA is largely diluted.
 |
| Fig. 9 (a) ATR-FTIR spectra ranging from 600 cm−1 to 4000 cm−1 and (b) zoom-in from 600 cm−1 to 2400 cm−1. From top to bottom, (1) original cotton fabric, (2) cotton fabric with cross-linked P(MEO2MA-co-EGMA) at 25 °C, (3) cotton fabric with cross-linked P(MEO2MA-co-EGMA) swelling in the water vapor atmosphere at 25 °C for 2 h and (4) cotton fabric with cross-linked P(MEO2MA-co-EGMA) swelling in the water vapor atmosphere at 25 °C for 2 h, then thermo-stated at 45 °C. The solution concentration for the preparation is 8%. The curves are shifted vertically for clarity. | |
When the cotton fabrics with cross-linked P(MEO2MA-co-EGMA) have been exposed to a water vapor atmosphere for 2 h at 25 °C, similar as the PMDEGA based thermo-responsive polymers previously investigated,4,28 a characteristic peak in the FTIR spectra, related to the intermolecular hydrogen bonds (1640 cm−1) is observed (see curve 3 in Fig. 9b). Therefore, it can be concluded that water is absorbed by P(MEO2MA-co-EGMA) and intermolecular hydrogen bonds are formed between C
O and O–H. Further increasing the temperature to 45 °C, this characteristic peak at 1640 cm−1 shrinks as the temperature is above the LCST. Hence, it is again confirmed that P(MEO2MA-co-EGMA) is successfully immobilized on the cotton fabrics and the obtained fabrics possess the thermo-responsive capability.
When the temperature is above the LCST, the state of thermo-responsive polymer will switch from hydrophilicity to hydrophobicity. Thus, the time needed for a water droplet to wet the surface and the contact angle between the water droplet/surface will be influenced. For this reason, the wetting time and contact angle of the cotton fabrics with cross-linked P(MEO2MA-co-EGMA) are measured to further investigate the transition behavior. Fig. 10a represents the evolution of the wetting time as a function of temperature. As expected, in case there is no cross-linked P(MEO2MA-co-EGMA) on the cotton fabrics, the wetting time of the original cotton fabric (black circles) does not depend on temperature because the original cotton fabric is not thermo-responsive. When the cotton fabric is cross-linked with P(MEO2MA-co-EGMA) (blue circles, solution concentration of 8%), a prominent raise of wetting time (15.1 s) is observed, when the temperature is above its LCST (around 38 °C). This abrupt change can be attributed to the switching of the surface from hydrophilicity to hydrophobicity.
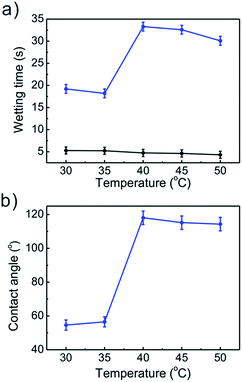 |
| Fig. 10 (a) Wetting time of the original cotton (black circles) and the cotton fabrics with cross-linked P(MEO2MA-co-EGMA) (blue circles, solution concentration of 8%) as a function of temperature. (b) Contact angle of the cotton fabrics with cross-linked P(MEO2MA-co-EGMA) (solution concentration of 8%) as a function of temperature. | |
The evolution of contact angle is similar as the wetting time when the temperature passes the LCST. Fig. 10b shows the contact angle of the cotton fabrics with cross-linked P(MEO2MA-co-EGMA) (solution concentration of 8%) as a function of temperature. When the temperatures are 30 °C and 35 °C, the contact angles are only 55° and 56°, respectively. Small values indicate that the P(MEO2MA-co-EGMA) cross-linked on the cotton fabric is still hydrophilic, as the LCST is not passed. When the temperature is raised to 40 °C (above the LCST), the contact angle dramatically increases to 118°, illustrating the switching from hydrophilicity to hydrophobicity and the cotton surface is no longer hydrophilic. Further increasing the temperature to 45 °C and 50 °C, the contact angle almost stays as a constant, showing that the surface remains hydrophobic.
From the results of XPS and washing fastness measurements, it is confirmed that P(MEO2MA-co-EGMA) is cross-linked onto the cotton fabrics. By ATR-FTIR, wetting time and contact angle measurements, it is ensured that the cotton fabrics with cross-linked P(MEO2MA-co-EGMA) are thermo-responsive. By varying the temperature, the surface can switch from hydrophilicity (below the LCST) to hydrophobicity (above the LCST), which will be further demonstrated in the smart cleaning performance.
Smart cleaning measurements
In our investigation, cooking oil is used to mimic the dirt on the clothes. Because the cooking oil has a good affinity with Nile red, the fluorescence intensity of Nile red can be used to distinguish the amount of cooking oil left on the fabrics after washing. Consequently, the cleaning ability of the fabrics can be evaluated by the fluorescence intensity from the fabric surface. The less intensity is observed after washing, the better cleaning ability of the fabrics is demonstrated. Fig. 11a and b show the CM images of the fibers from the cotton fabrics, without and with cross-linked P(MEO2MA-co-EGMA) (solution concentration of 8%) at 20 °C. The fluorescence intensities of the fibers are obtained by making a cut along the fiber and averaging the intensity by the software Image pro plus. The intensities are presented in Fig. 12. It is clear that the intensities from the fibers without and with cross-linked P(MEO2MA-co-EGMA) before rinsing are 249 and 254, respectively. Comparing these two values, it is obvious that after dipped into the cooking oil and dyed with Nile red, both fibers possess similar fluorescence intensities, indicating the amount of Nile red on these two fibers are very close to each other.
 |
| Fig. 11 Confocal microscopy images of (a) an original cotton fibre and (b) the cotton fibre with cross-linked P(MEO2MA-co-EGMA) at 20 °C, (c) original and (d) coated cotton fibers rinsed with water at a temperature of 45 °C (above the LCST) for 10 times, and (e) original and (f) coated cotton fibers rinsed with water at a temperature of 25 °C (below the LCST) for another 10 times. | |
 |
| Fig. 12 The fluorescence intensities of the original cotton fibre (black) and cotton fibre with cross-linked P(MEO2MA-co-EGMA) (red). | |
Fig. 11c and d show the CM images of these two fibers after rinsing with distilled water at a temperature of 45 °C (above the LCST) for 10 times. To the fiber without cross-linked P(MEO2MA-co-EGMA), the intensity almost stays as a constant (249 to 238), indicating the rinsing itself will not significantly influence the fluorescence intensity of the fibers. In case of the fiber with cross-linked P(MEO2MA-co-EGMA), as the water temperature is higher than the LCST, P(MEO2MA-co-EGMA) is assumed to be hydrophobic and has a good contact with the cooking oil. As a consequence, the cooking oil cannot be easily removed from the fiber by washing. As mentioned above, Nile red has a good affinity with cooking oil, causing the Nile red is also not removed from the fiber and the fluorescence intensity remains mostly unchanged. However, from the intensity values obtained from the cutting, it decreases from 254 to 192, which is a significant decrease in intensity as compared to the original cotton fiber. This decrease in intensity can be explained by the state of P(MEO2MA-co-EGMA). Although ideally the copolymer is assumed in the hydrophobic state at 45 °C, in reality it is only in a more hydrophobic state as compared with the state at 25 °C. Thus, a certain amount of cooking oil is still removed even at 45 °C.
Afterwards, both fibers are further rinsed with distilled water at a temperature of 25 °C (below the LCST) for another 10 times. From the obtained CM images (Fig. 11e and f), it is clear that the fluorescence intensity of the fiber with cross-linked P(MEO2MA-co-EGMA) is much weaker, illustrating more Nile red together with cooking oil are removed from this fiber. The fluorescence intensity values show the same tendency as well. For the original cotton fiber, the value decreases from 238 to 179, indicating that only 25% Nile red has been removed. However, for the fiber with cross-linked P(MEO2MA-co-EGMA), the value dramatically decreases from 192 to 92, meaning that more than 50% Nile red has been washed away from the fiber when the temperature of water is 25 °C. Therefore, it can be concluded that the cleaning ability of the cotton fabrics with cross-linked P(MEO2MA-co-EGMA) is much better than that of the original cotton when the temperature is lower than the LCST. The reason for the better cleaning performance can be attributed to the variation of the surface state. P(MEO2MA-co-EGMA), which is located on the cotton surface, will switch to be more hydrophilic when the temperature is lower than the LCST. As expected, when the cotton surface turns to hydrophilic, the affinity between the cotton surface and the cooking oil will be reduced and water penetration between the cotton fiber and the cooking oil is greatly increased, leading to a much better cleaning performance on the cotton fiber with the thermo-responsive polymer.
Fabric softness
As mentioned in the introduction, P(MEO2MA-co-EGMA) is in a gel state at room temperature. Therefore, it is assumed that P(MEO2MA-co-EGMA) will not influence the softness of the cotton fabrics after cross-linking. Table 1 shows the softness of the obtained fabrics in the investigation. The original cotton fabric presents a softness of 10.69. When the P(MEO2MA-co-EGMA) solutions applied are dilute (1% and 2%), the softness only slightly increases to 10.72 and 10.83, respectively. Further increasing the concentration to 4%, the softness raises to 10.96. It is only 2.5% larger than the original cotton fabrics. As the increase of the softness is so small, it can be concluded that, P(MEO2MA-co-EGMA) applied in the investigation will not influence the softness of the cotton fabrics.
Table 1 Softness of the original cotton fabrics and the cotton fabrics with cross-linked P(MEO2MA-co-EGMA) (solution concentration varies with 1%, 2% and 4%)
|
Original cotton |
P(MEO2MA-co-EGMA) |
Solution concentration |
0 |
1% |
2% |
4% |
Softness |
10.69 |
10.72 |
10.83 |
10.96 |
Conclusions
Cotton fabrics with smart cleaning ability are realized by cross-linking of the thermo-responsive random copolymer P(MEO2MA-co-EGMA) on the cotton surface. P(MEO2MA-co-EGMA) is successfully synthesized from MEO2MA and EGMA with a ratio of 17
:
3. Due to the incorporation of EGMA monomers, which possess additional –OH groups, the LCST of P(MEO2MA-co-EGMA) is about 38 °C in the dilute aqueous solution (1 mg mL−1), which is higher than that of the homopolymer PMEO2MA. The immobilization of P(MEO2MA-co-EGMA) onto the cotton fabrics is achieved by cross-linking with citric acid. After swelling in water vapor atmosphere at room temperature, an extra characteristic peak related to the hydrogen bonds between C
O and water is observed in the ATR-FTIR measurements. Moreover, this peak shrinks when the temperature passes the LCST, illustrating the previously formed intermolecular hydrogen bonds are broken and water is repelled. Thus, it is confirmed that the obtained cotton fabrics is thermo-responsive as well. In addition, both the wetting time and contact angle of the cotton fabrics significantly rise, when the temperature is above the LCST, indicating the cotton surface switches from hydrophilicity to hydrophobicity. Because the cleaning performance can be enhanced when the surface is more hydrophilic, the cotton fabrics with cross-linked P(MEO2MA-co-EGMA) can be used to prepare the fabrics with smart cleaning ability. Such fabrics can be cleaned at much lower temperatures as compared with common cotton fabrics, which would allow for saving significant amount of energy in textile cleaning. With the confocal microscopy measurements, the smart cleaning ability is indeed observed. Unlike the well investigated PNIPAM, the softness of the cotton fabrics cross-linked with P(MEO2MA-co-EGMA) remains very soft after the cross-linking. Hence, it can be concluded that P(MEO2MA-co-EGMA) is a good candidate to prepare smart textiles with smart cleaning performance and soft hand.
Acknowledgements
This work was supported by the National Natural Science Foundation of China (Grant no. 51403186) and Zhejiang Provincial Natural Science Foundation of China (Grant no. LQ14E030009). PMB thanks for support by the DFG priority program “Intelligente Hydrogele” (Mu1487/8).
Notes and references
- F. M. Winnik, Macromolecules, 1990, 23(1), 233–242 CrossRef CAS.
- M. Zeiser, I. Freudensprung and T. Hellweg, Polymer, 2012, 53, 6096–6101 CrossRef CAS PubMed.
- S. Meyer and W. Richtering, Macromolecules, 2005, 38, 1517–1519 CrossRef CAS.
- Q. Zhong, E. Metwalli, G. Kaune, M. Rawolle, A. M. Bivigou-Koumba, A. Laschewsky, C. M. Papadakis, R. Cubitt and P. Müller-Buschbaum, Soft Matter, 2012, 8, 5241–5249 RSC.
- J. Adelsberger, A. Kulkarni, A. Jain, W. N. Wang, A. M. Bivigou-Koumba, P. Busch, V. Pipich, O. Holderer, T. Hellweg, A. Laschewsky, P. Müller-Buschbaum and C. M. Papadakis, Macromolecules, 2010, 43, 2490–2501 CrossRef CAS.
- B. Jeong and A. Gutowska, Trends Biotechnol., 2002, 20, 360 CrossRef CAS.
- W. X. Song, Q. He, H. Mohwald, Y. Yang and J. B. Li, J. Controlled Release, 2009, 139, 160–166 CrossRef CAS PubMed.
- D. C. Coughlan, F. P. Quilty and O. I. J. Corrigan, J. Controlled Release, 2004, 98, 97–114 CrossRef CAS PubMed.
- L. E. Bromberg and E. S. Ron, Adv. Drug Delivery Rev., 1998, 31, 197–221 CrossRef CAS.
- C. de las Heras Alarcon, S. Pennadam and C. Alexander, Chem. Soc. Rev., 2005, 34, 276–285 RSC.
- Y. Guan and Y. J. Zhang, Soft Matter, 2011, 7, 6375–6384 RSC.
- W. Choi, A. Tuteja, S. Chhatre, J. M. Mabry, R. E. Cohen and G. H. Mckinley, Adv. Mater., 2009, 21, 2190–2195 CrossRef CAS PubMed.
- K. S. Chen, J. C. Tsai, C. W. Chou, M. R. Yang and J. M. Yang, Mater. Sci. Eng., C, 2002, 20, 203–208 CrossRef.
- K. L. Pavla, M. C. G. W. Marijin and J. Dragan, Cellulose, 2012, 19, 257–271 CrossRef.
- P. Glampedaki, Surface Modification Systems for Creating Stimuli Responsiveness of Textiles, University of Twente, Enschede, 2010, pp. 61–76 Search PubMed.
- H. Yang, H. Zhu, M. M. Hendrix, N. J. H. G. M. Lousberg, G. de With, A. C. C. Esteves and J. H. Xin, Adv. Mater., 2013, 25, 1150–1154 CrossRef CAS PubMed.
- J. B. Xie and Y. L. Hsieh, J. Appl. Polym. Sci., 2003, 89, 999–1006 CrossRef CAS PubMed.
- A. Kulkarni, A. Tourrette, M. M. C. G. Warmoeskerken and D. Jocic, Carbohydr. Polym., 2010, 82, 1306–1314 CrossRef CAS PubMed.
- M. Ishida, H. Sakai, S. Sugihara, S. Aoshima, S. Yokoyama and M. Abe, Chem. Pharm. Bull., 2003, 51, 1348–1349 CrossRef CAS.
- K. Van Durme, G. Van Assche and B. Van Mele, Macromolecules, 2004, 37, 9596–9605 CrossRef CAS.
- J. F. Lutz and A. Hoth, Macromolecules, 2006, 39, 893–896 CrossRef CAS.
- J. F. Lutz, O. Akdemir and A. Hoth, J. Am. Chem. Soc., 2006, 128, 13046–13047 CrossRef CAS PubMed.
- V. Audonnet, L. Malaquin and J. L. Viovy, Bioanalytical Reviews, 2011, 3, 41–46 CrossRef.
- S. F. Liu and Z. Y. Gu, J. Donghua Univ., 2010, 27, 469–476 CAS.
- S. F. Liu, Z. Y. Gu and J. R. Niu, J. Text. Res., 2009, 30, 101–106 Search PubMed.
- Y. Okada and F. Tanaka, Macromolecules, 2005, 38, 4465–4471 CrossRef CAS.
- T. M. Eggenhuisen, C. R. Becer, M. W. M. Fijten, R. Eckardt, R. Hoogenboom and U. S. Schubert, Macromolecules, 2008, 41, 5132–5140 CrossRef CAS.
- Q. Zhong, E. Metwalli, M. Rawolle, G. Kaune, A. M. Bivigou-Koumba, A. Laschewsky, C. M. Papadakis, R. Cubitt and P. Müller-Buschbaum, Macromolecules, 2013, 46, 4069–4080 CrossRef CAS.
|
This journal is © The Royal Society of Chemistry 2015 |
Click here to see how this site uses Cookies. View our privacy policy here.