DOI:
10.1039/C5RA01569C
(Paper)
RSC Adv., 2015,
5, 34803-34811
High performance N-doped porous activated carbon based on chicken feather for supercapacitors and CO2 capture†
Received
26th January 2015
, Accepted 7th April 2015
First published on 8th April 2015
Abstract
A low cost carbon precursor to produce carbon with large specific surface area and abundant heteroatoms is essential for CO2 uptake and supercapacitors to realize economic viability. We report a facile synthesis method and superior performance of a kind of porous activated carbon based on chicken feather. Herein, different activated temperatures and alkali/carbon ratios (KOH vs. carbon in g/g) are used to tailor the pore structure and the surface chemistry, so the samples show a wide range of specific surface area and nitrogen content. The sample activated at 600 °C with the alkali/carbon ratio of 4 is rich in nitrogen and micropores (<1 nm), exhibiting the highest CO2 uptake of 6.5 mmol g−1 and the largest specific capacitance of 351 F g−1 at 0.1 A g−1. Moreover, the sample activated at 800 °C with the alkali/carbon ratio of 5.5 retained 260 F g−1 at 30 A g−1 with a retention rate of 98% after 10
000 cycles (1 A g−1), indicating the excellent retention capability under high current densities and long cycle life.
Introduction
In general, porous activated carbon is prepared by carbonization of carbon precursors and sequential physical activation (CO2, H2O, air or microwave) or chemical activation (KOH, NaOH, K2CO3, ZnCl2 or H3PO4).1,2 Due to its large specific surface area, high porosity, outstanding electrical conductivity, high stability and favourable corrosion resistance,3 activated carbon can be widely applied in many fields, such as pollutant sorbents,4 supercapacitors,5–8 lithium ion anodes9 and CO2 capture.10,11 Among many kinds of carbon from different precursors, the bio-based activated carbon is a kind of economical and promising material because of the simple preparation process, low cost, environmentally friendly and high performance.12 Recently, many animal byproducts have been utilized in preparation of N-doped porous carbon and showed great potential as electrode materials for supercapacitors or as solid-state adsorbents in CO2 capture.13–18
According to the method of energy storage, the supercapacitors can be divided into two types, one is electrical double layer capacitor (EDLC) based on quickly ion adsorption–desorption, and the other one is pseudocapacitor originated from reversible faradaic reactions.19–21 Because of its high specific surface area, large porosity and the abundant surface functional groups, the porous activated carbon can make the electrode material store more counter-ions electrostatically in the diffuse layer formed next to the surface and lead to a higher electrical double layer capacitance.22 Besides, the surface N-contain functional groups of porous activated carbon can react with the aqueous electrolyte reversibly and induce an additional pseudo-capacitance. With different atom size and electronegativity, the doped nitrogen can result in electronic structural distortion and enhance the conductivity.23,24 Thus, the N-doped porous carbon is promising for the high performance supercapacitors. For example, the human hair-derived carbon exhibited high specific capacitance of 340 F g−1 and good stability over 20
000 cycles.15 Pigskin-derived porous carbon flakes can be prepared by KOH activation at low temperature and displayed initial capacitance of 547 F g−1.25 Gizzard pepsin-derived hierarchical N-doped porous carbon showed the specific capacitance of 198 F g−1.17 The chicken eggshell membranes and egg white protein can be used to prepare N-doped porous carbons, which show extraordinary high specific capacitance at 297 F g−1 and 390 F g−1, respectively.13,18 And the high-capacity carbon has been obtained from chicken feather with the capacitance of 253 F g−1 in 1 M H2SO4 at 1 A g−1.14 It shows that the chicken feather composed of keratin is a promising candidate for porous carbon. However, the synergetic influences of carbonization temperature, activation temperature and alkali/carbon ratio on heteroatom doping, pore structure, and pore size distribution have not been investigated, which is critical to the improvement of electrochemical performance. Hence, it is meaningful to do more work to further discuss the chicken feather-derived carbon.
Moreover, the N-doped porous carbon materials have been considered superior for CO2 capture due to their high specific surface area and ample N-doping. Modification of carbon surface with the electron-donating element N can increase surface polarity, hence enhance the interactions between CO2 and the carbon surface besides the weak van der Waals forces.26 For instance, a facile one-pot evaporation induced self-assembly method fabricated N-doped porous carbon shows a high CO2 uptake of 4.30 mmol g−1 at 298 K and 1 atm.11 The wide pore size distribution, large specific area and N-doped activated porous carbon need to be further studied about the influence of material structure and heteroatom doping on the CO2 capture.
In this work, we firstly investigated the pyrolysis process and heteroatom doping of chicken feather at varying heat-treated temperature in detail, and the chicken feather-based porous carbon with higher nitrogen content, larger specific area has been prepared. Different activation temperatures and alkali/carbon ratios were applied to tailor the pore structure and surface chemistry. Then the porous carbon was characterized by elemental analysis, X-ray diffraction, X-ray photoelectron spectroscopy and gas adsorption analyser. And the influences on the electrochemical performance and CO2 capture of pore structure and N-doping are also analysed.
Experimental
Preparation of chicken feather-derived activated carbon
The chicken feather was collected from the Dahongmen market in Beijing. Firstly, the chicken feather was washed by distilled water for several times, and then dried at 80 °C for 12 h. Secondly, the clean chicken feather was placed into a tube furnace for carbonization at different temperatures (250, 300, 400, 500 and 600 °C) for 2 h under N2 atmosphere (300 ml min−1) at a heating rate of 5 °C min−1. After smashed in mortar and sieved by the griddle (20 mesh), the resultants were obtained and denoted as CFC-T, respectively, where T indicates carbonization temperature. Thirdly, the sample carbonized at 500 °C (CFC-500) and KOH (Beijing Chemical Co., Ltd China) were mixed uniformly at a alkali/carbon ratio of 4 by distilled water, then the sludge was dried at 80 °C for 20 h, and then placed into the tube furnace for activation at 600, 650, 700, 750 and 800 °C for 3.5 h, respectively. These chicken feather-derived activated samples were denoted with CFAC-T-4K, where T indicates activation temperature. Different alkali/carbon ratios of 3 and 5.5 are also applied for activation at 800 °C for 3.5 h, respectively, which were denoted by CFAC-800-nK, where n indicates the alkali/carbon ratio. Finally, the products were washed by 1 M HCl (Beijing Chemical Co., Ltd China) and distilled water to remove the residual KOH, K2CO3 and inorganic ashes, and dried up at 80 °C for 12 h. The schematic diagram is shown in Fig. 1.
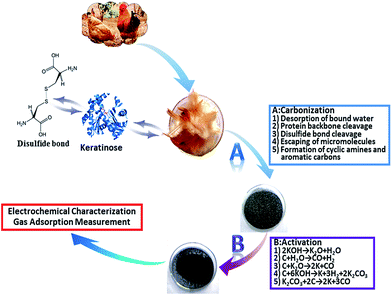 |
| Fig. 1 The schematic diagram of preparation of the chicken feather-derived activated carbon. | |
Characterization
A Hitachi S-4700 scanning electron microscope (SEM) at 5–20 kV and a JEOL JEM-3010 transmission electron microscope (TEM) at 200 kV were applied to examine the morphology of the samples. A Thermogravimetric Analyzer (Beijing Hengjiu Scientific Instrument Co. China) was applied to analyse the pyrolysis progress of chicken feather. X-ray diffraction patterns (XRD) were obtained by a Rigaku D/MAX-2500 equipped with Cu Kα radiation to characterize the crystal structure. Raman spectra (Renishaw inVia Micro-Raman Spectroscopy System at 514 nm) were obtained to verify the degree of graphitization. An Elementar vario EL CUBE (Elemental Analyse system GmbH, Germany) was used to analysis the samples' elementary composition. X-ray photoelectron spectra (XPS) were obtained on a Thermo VG ESCALAB 250 spectrometer equipped with a monochromatic Mg Kα X-ray source (1253.6 eV), which can be used to examine the surface atomic composition. A Micromeritics ASAP 2020 surface area and porosity analyser was employed in N2 adsorption–desorption (77 K) and CO2 adsorption (273 K) analysis to obtain the N2/CO2 adsorption isotherms of the samples. Samples were degassed at 300 °C under vacuum for 12 h prior to measurement. Brunauer–Emmett–Teller (BET) and density functional theory (DFT) were used to calculate the specific surface area and the pore size distribution, respectively.
Electrochemical characterization
Cyclic voltammetry curve (CV) and electrochemical impedance spectroscopy (EIS) were obtained by a CHI 760E electrochemical work station (Shanghai Chenhua Instrument Co., China). The galvanostatic charge–discharge tests were carried out on a LAND CT2001A tester. The working electrode material was the mixture of the activated sample, acetylene black and poly-tetrafluoroethylene (PTFE) at a mass ratio of 8
:
1
:
1, and then pressed onto a piece of nickel foam which works as current collector to form a working electrode. The platinum gauze electrode and Hg/HgO electrode were used as the counter and the reference electrode, respectively, constituting a three-electrode system with the working electrode. And all experiments were performed in N2-saturated 6 M KOH electrolyte. In this work, the specific capacitance (C) was calculated according to the eqn (1): |
 | (1) |
where I is the discharge current (A), Δt is the discharge time (s), m is the mass of active material in the working electrode (g) and ΔV is the potential window (V). The energy density (E, J g−1) was calculated according to the eqn (2): |
 | (2) |
where C is the specific capacitance (F g−1), ΔV is 0.8 V in this work.
Results and discussion
Morphology
On the microscale, Fig. 2a exhibits the fibrous structure of chicken feather. After samples were treated at a high temperature, the shape was totally changed, which showed various types, such as flakes and blokes with smooth or wavelike surface. It is because that chicken feather melted completely and charred into charcoal mainly containing heterocyclic amines and aromatic carbon (Fig. 2b).27–29 The skeleton structure with rough surface was generated by KOH etching (Fig. 2c). These interconnected pores within carbon materials provided a favourable path for transportation of electrolyte ions. Fig. 2d–f display the HRTEM images of the typical activated samples. The amorphous structure and well-distributed micropores can be clearly observed. Thus, KOH activation is conducive to the formation of porous texture which could be benefit for supercapacitors.30,31
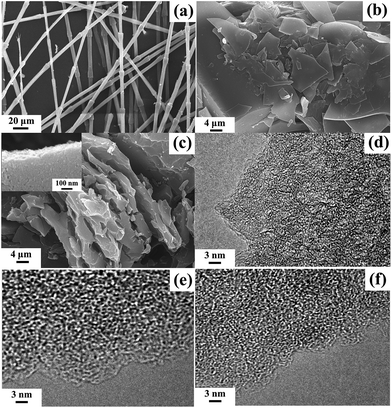 |
| Fig. 2 SEM images: chicken feather (a); CFC-500 (b); CFAC-750-4K (c) (the insert image shows the magnified part). HRTEM images: CFAC-750-4K (d); CFAC-800-5.5K (e); CFAC-650-4K (f). | |
Pyrolysis process of chicken feather
Chicken feather mainly contains keratin, a protein containing multiple amino acids linked by disulphide cross-linking bridge bond between the cysteine.32,33 In Fig. 3, the thermogravimetry (TG) and the derivative thermogravimetry (DTG) curves were used to analyse the pyrolysis process of chicken feather in N2 atmosphere. And the first mass loss of 10 wt% appears at about 100 °C due to the evaporation of water. The second mass loss at 200–375 °C is a major loss of 56 wt%, corresponding to the volatilization of NH3, CO2, H2O and sulphur-containing compounds.28 In the DTG curve, the successive and overlapped stages can be observed from the major decomposition section with maximum degradation rates at 215 °C (inflexion), 265 °C (inflexion) and 300 °C (peak), indicating the complexity of the chicken feather pyrolysis and validated by Senoz's work.27 The detailed conversion reactions are exhibited in Fig. 1. Above 500 °C, the mass drops slightly and the char coal is formed. Thus, highly carbonized CFC-500 can be used as a suitable activating precursor, and excessive heat is not benefit for retention of heteroatoms. In conclusion, the carbonization extent has great influence on tailoring the structure and chemical composition of the as-prepared carbon.
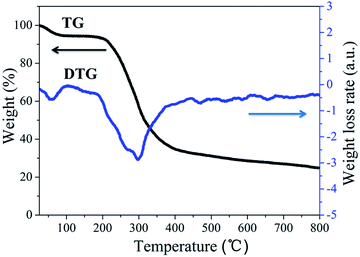 |
| Fig. 3 TG and DTG curves of the chicken feather. | |
Physical structure
The XRD patterns of the CFC-500 and the relevant activated samples are shown in Fig. 4a, reflecting the degree of structural disorder after activation. Two broad diffraction peaks can be observed at 2θ = 25° and 43°, related to the (002) plane and the overlapped peak of (100) and (101) planes of hexagonal carbon, respectively.34 From the image it can be observed that the intensities of peaks at 25° decrease sharply after activation, and fade out along with the rise of the activated temperature or the alkali/carbon ratio, suggesting the increasing extent of disorder as the activation enhancing. It also can be observed that there is an increasing intensity in low-angle diffraction after the sample is activated, corresponding to the presence of abundant micropores, confirmed by the HRTEM images (Fig. 2d–f).
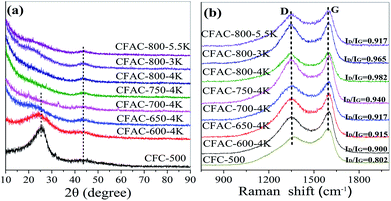 |
| Fig. 4 XRD patterns (a) and Raman spectra (b) of the CFC-500 and the corresponding activated samples. | |
To further identify the chemical structure of the chicken feather-derived porous carbon, the Raman spectra measurement was conducted and shown in Fig. 4b. Two broad bands are located at ∼1348 and ∼1595 cm−1, corresponding to the D band and the G band, respectively.35 The D/G ratio of band intensities (ID/IG) indicates the degree of structural disorder.15 The ID/IG of the activated precursor CFC-500 was calculated to be 0.802, it increases after activation and grows along with temperature rising (0.900, 0.915, 0.917, 0.940 and 0.982 follows a rising temperature order). Even though the heteroatom content decreases as temperature rising, which can decline the number of defects in carbon skeleton, the intensive KOH activation introduces more defects, so the degree of disorder increases. Compared with CFAC-800-4K (0.982), the ID/IG of CFAC-800-5.5K (0.917) is much lower due to the decrease of random micropores caused by excess activation. According to the Raman and XRD analysis, a high activation temperature and alkali/carbon ratio can enhance the degree of structural disorder, which can further influence electric conductivity.
Chemical composition
To further investigate the changes of elemental composition of chicken feather during pyrolysis and activation process, the elemental analysis is conducted (Fig. 5 and Table S1†). After high temperature carbonization and sequential activation, the carbon content increases continuously from 48.6 to 91.5 wt%, while the heteroatoms decrease obviously (N: 15.4–1.0 wt%, H: 7.1–0.4 wt% and S: 2.2–0.2 wt%). During the carbonization, the sulphur content decreases to only a small amount of 0.66 wt% at 250 °C, indicating that disulfide bond cleavage occur at the temperature lower than 250 °C.28 On the other hand, the nitrogen content decreases slightly from 15.44 wt% to 12.83 wt% (600 °C). During the activation, the nitrogen content decreases sharply to 7.1 wt% (600 °C), and 1.7 wt% (700 °C). Thus, samples activated at lower than 700 °C can contain rich-N at alkali/carbon ratio of 4. But in term of at a low alkali/carbon ratio of 3, the sample activated at 800 °C also possesses a relatively high nitrogen content of 2.08 wt%. Besides, CFAC-750-4K and CFAC-800-4K show similar elemental composition, suggesting the sufficient cyclization and aromatization reactions and escaping of heteroatoms at the temperature above 750 °C. In all, the results indicate that the activated temperature and use level of alkali play important roles in elemental composition of the samples.
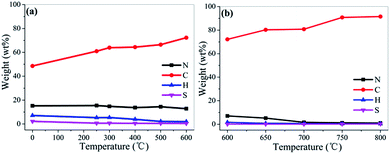 |
| Fig. 5 Elemental composition: chicken feather and carbonized samples (a); activated samples from CFC-500 (b). | |
XPS spectra analysis of the charcoal precursor carbonized at 500 °C and the relevant activated carbons is conducted to investigate the surface chemical characteristic. The spectra are shown in Fig. S1,† and the surface chemical compositions are shown in Table 1. As to the activated samples, the surface content of N is accord with the bulk content, but CFC-500 shows a much lower surface one than the bulk one, suggesting the surface of carbon precursor (CFC-500) is effectively activated by KOH. What's more, the surface of the as-prepared activated carbon is also rich in oxygen. Herein, the N atoms can be classified into four types of chemical states: pyridinic N (N-6, 398.7 ± 0.3 eV), pyrrolic and pyridone N (N-5, 400.3 ± 0.3 eV), quaternary N (N-Q, 401.4 ± 0.5 eV) and pyridine-N-oxide (N-X, 402–405 eV).36,37 The deconvoluted peaks of N1s are shown in Fig. 6, displaying dramatic changes of contents of N-6 and N-5. The activated precursor CFC-500 possesses high contents of N-6 and N-5. The sharp decrease of N-6 and N-5 occur at activated temperature of 600 °C and 650 °C, respectively. N-6/N-5/O-containing surface functional groups can trigger various redox effects and lead to addition of the pseudo-capacitance.38 The O1s spectra are deconvoluted into three peaks at 531.5, 532.9 and 534.5 eV (Fig. 7), which correspond to carbonyl oxygen in quinones (O-I), carbonyl oxygen in esters and anhydrides or oxygen atoms in phenolic hydroxyl (O-II), and non-carbonyl oxygen in esters and anhydrides (O-III), respectively.39 And O-I species are considered to cause pseudo-capacitance effects.40 In addition, the abundant O-containing groups can increase the wettability of carbon material and heighten the electrochemical performance.
Table 1 Surface elementary composition and contents of different kinds of N, O of the sample carbonized at 500 °C and the corresponding different temperature activated samples
Samples |
N (at%) |
C (at%) |
O (at%) |
N-6 (at%) |
N-5 (at%) |
N-Q (at%) |
N-X (at%) |
O-I (at%) |
O-II (at%) |
O-III (at%) |
CFC-500 |
4.48 |
78.04 |
17.15 |
1.87 |
1.13 |
0.48 |
0.99 |
3.20 |
11.21 |
2.73 |
CFAC-600-4K |
3.82 |
79.33 |
16.55 |
1.42 |
1.10 |
0.47 |
0.83 |
3.45 |
9.59 |
3.51 |
CFAC-650-4K |
2.46 |
81.20 |
15.99 |
0.66 |
0.76 |
0.39 |
0.64 |
0.87 |
10.06 |
5.05 |
CFAC-700-4K |
1.62 |
82.97 |
17.13 |
0.47 |
0.34 |
0.26 |
0.55 |
1.84 |
11.45 |
3.84 |
CFAC-750-4K |
1.35 |
83.31 |
15.03 |
0.49 |
0.22 |
0.22 |
0.41 |
2.46 |
10.52 |
2.05 |
CFAC-800-4K |
0.90 |
83.77 |
15.32 |
0.29 |
0.13 |
0.18 |
0.30 |
2.71 |
10.42 |
2.19 |
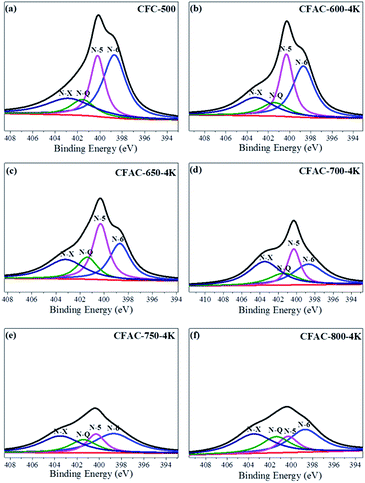 |
| Fig. 6 N1s core level spectra of CFC-500 and the corresponding activated samples. | |
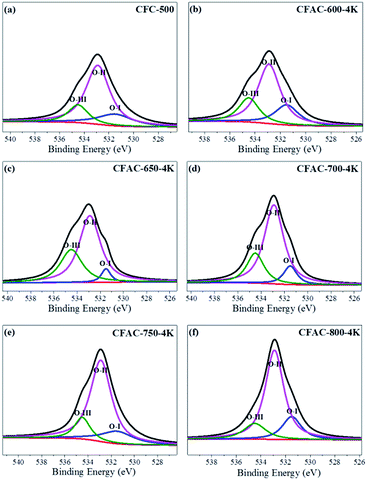 |
| Fig. 7 O1s core level spectra of CFC-500 and the corresponding activated samples. | |
Porous texture and CO2 capture
Fig. 8 shows the N2/CO2 sorption isotherms and the corresponding pore size distributions of chicken feather-derived activated carbons. According to the IUPAC classification,41,42 the N2 adsorption–desorption isotherms of the activated carbons transformed gradually from type I at 600 °C to type IV at 800 °C (Fig. 8a). The sample activated at 600 °C is microporous material, and were changed to micro–mesoporous material when treated at temperatures above 650 °C. The isotherms with broad knees and hysteresis loops of type H2 at 0.4 < P/P0 < 0.6 can be clearly observed at activation temperature above 750 °C, illustrating the material with the micro–mesoporous network. Fig. 8b and c displays the corresponding pore size distributions. The high activated temperatures and alkali/carbon ratio could produce a highly activated process, which can increases the proportion of mesopores, and the activated temperature plays a more significant role in tailoring pore structure. The pore texture parameters changing with activated temperature are shown in Fig. 9 and Table 2. The BET specific surface areas and the single point adsorption total pore volumes of the varying activated temperature group samples increase dramatically from 1610 m2 g−1 to 3430 m2 g−1 and from 0.86 to 2.27 cm3 g−1 when the activated temperature rises from 600 °C to 800 °C, respectively. These of the mesopores (>2 nm) change according to the BET specific surface area, while trends of the micropores (<1 nm) are opposite. Comparing samples activated at 800 °C, the BET specific surface area and total pore volume increase sharply when the ratio increases from 3 to 4, and CFAC-800-5.5K possesses the largest total pore volume, resulting from the highly intensive activation. Hence, the pore structure properties changing with varying activated temperature and alkali/carbon ratio is attributed to the changing capability of KOH in producing neo-pores and enlarging the pores at different reaction conditions.
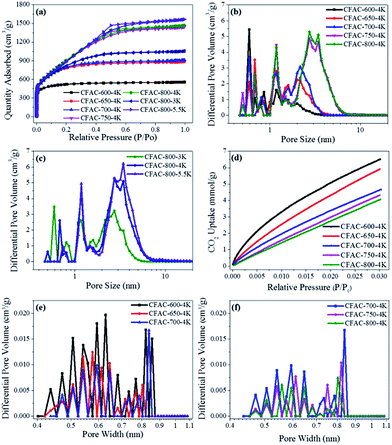 |
| Fig. 8 (a) N2 (77 K) adsorption–desorption isotherms, (b and c) the N2 adsorption related pore size distributions of the activated samples; (d) CO2 (273 K) adsorption isotherms, (e and f) the CO2 adsorption related pore size distributions of the samples activated at different temperatures. | |
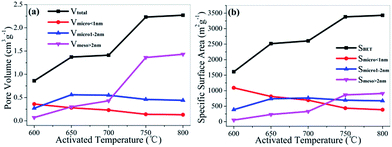 |
| Fig. 9 The porous texture of the as-prepared samples changing with the rising activated temperature, (a) the pore volume, (b) the specific surface area (Vtotal is the total pore volume, SBET is the BET specific surface area and the others are the parameters calculated by DFT method). | |
Table 2 Pore structure parameters of the activated samples tested by N2 adsorption and CO2 adsorption isotherms
Samples |
aSBET m2 g−1 |
bDave nm |
cVt cm3 g−1 |
DFT method |
CO2 adsorption |
eSmicro<1 nm m2 g−1 |
eS1 nm<micro<2 nm m2 g−1 |
eSmeso>2 nm m2 g−1 |
eVmicro<1 nm cm3 g−1 |
eV1 nm<micro<2 nm cm3 g−1 |
eVmeso>2 nm cm3 g−1 |
dCO2 uptake mmol g−1 |
The specific surface areas (SSA) calculated by BET method from the N2 adsorption isotherms. The average pore diameters obtained by Horvath–Kawazoe (HK) method from the N2 adsorption isotherms. The single point adsorption total pore volumes from the N2 adsorption isotherms. The CO2 uptake from the CO2 adsorption isotherms. The pore size distributions by DFT method from the N2 adsorption isotherms. |
CFAC-600-4K |
1610 |
0.64 |
0.86 |
1092 |
388 |
52 |
0.36 |
0.27 |
0.07 |
6.5 |
CFAC-650-4K |
2515 |
0.81 |
1.37 |
814 |
739 |
232 |
0.28 |
0.56 |
0.30 |
5.9 |
CFAC-700-4K |
2605 |
0.92 |
1.41 |
694 |
766 |
331 |
0.23 |
0.55 |
0.43 |
4.7 |
CFAC-750-4K |
3381 |
1.61 |
2.23 |
436 |
692 |
864 |
0.14 |
0.46 |
1.36 |
4.3 |
CFAC-800-4K |
3430 |
1.66 |
2.27 |
386 |
673 |
909 |
0.13 |
0.44 |
1.43 |
4.1 |
CFAC-800-3K |
2861 |
1.09 |
1.63 |
704 |
668 |
499 |
0.23 |
0.47 |
0.70 |
— |
CFAC-800-5.5K |
3373 |
1.88 |
2.42 |
129 |
640 |
987 |
0.05 |
0.41 |
1.64 |
— |
To analyse the CO2 uptake performance of the as-prepared samples, CO2 adsorption isotherms and the related pore size distributions from 0.4 to 0.8 nm are measured and shown in Fig. 8d–f. It is easy to observe that CFAC-600-4K occupies the abundant ultra-micropores, which is more suitable for CO2 capture. The CO2 uptake of the sample activated at 600 °C is the highest in the all samples (6.5 mmol g−1), and it declines with the rising activated temperature to 4.1 mmol g−1 (Table 2). It is well known that the amble micropores smaller than 1 nm are responsible for high CO2 uptake at 1 bar,10,43 and porous carbon doped with the electron-donating N can produce basic sites and increase surface polarity to enhance the interaction between CO2 and the porous carbon.11 Thus, combined with the above element analysis and XPS results, it is confirmed that N-doped and micropores (<1 nm) are benefit to CO2 uptake, and the declining N-content and micropore (<1 nm) volume along with the rising activated temperature lead to the CO2 uptake declination. Also, the as-prepared samples with tailored pore structures can obtain prior performance of CO2 capture.
Electrochemical properties
To examine the electrochemical performance of the activated samples, CV tests have been conducted in 6 M KOH solution from −0.8 V to 0.2 V at varying scan rates, and the cathodic currents are defined positive in this work. The rectangular curves should be detected when the energy is stored by the electrical double layer mechanism.44 Fig. 10a and b show the anomalous rectangular curves with redox humps induced by nitrogen at −0.8 to −0.35 V, indicating the combination of the EDLC and pseudocapacitance. The redox humps of samples with high N-6 content (Fig. 10a) are more obvious than that with low N-6 content (Fig. 10b), because N-6 can induce redox reactions and increase pseudocapacitance in alkaline electrolyte. The mechanism of redox reaction involves N/O-containing groups reacting with ions in electrolyte along with reversibly electronic migration. Importantly, N-5/N-6 can react with ions in electrolyte that can improve the pseudocapacitance (Fig. 11).13,45 In Fig. 10a, it can be observed that the large pore volume will result in the improvement of capacitance at −0.35–0.2 V. In Fig. 10b, the curves of samples with low N content differentiate in size instead of shape due to influence of pore structures, and higher pore volume is in favour of larger specific capacitance. CV curves of CFAC-650-4K and CFAC-800-5.5K are shown in Fig. 10c & d, respectively. CFAC-650-4K shows superior rate performance at −0.8 to −0.35 V, indicating the rapidly reversible redox reaction. And the poor rate performance at −0.35–0.2 V is caused by the low porosity impeding ion rapid diffusion. However, CFAC-800-5.5K displays good rate performance in all range, since the highly developed porous passages facilitate the ion rapid diffusion and the large mesopore proportion provide space for electrolyte penetration.
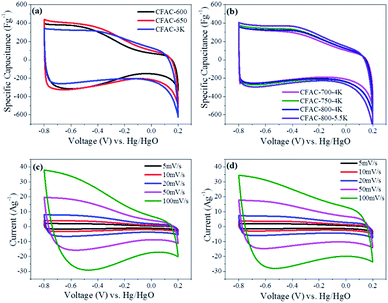 |
| Fig. 10 Cyclic voltammetry curves of the activated samples with high N-6 content (a) and low N-6 content (b) at a scan rate of 5 mV s−1. Cyclic voltammetry curves of CFAC-650-4K (c) and CFAC-800-5.5K (d) at varying scan rates. | |
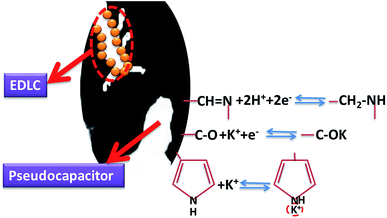 |
| Fig. 11 The mechanism of redox reactions for pseudocapacitance. | |
Impedance analysis is shown in Fig. 12. In Fig. 12a, the nearly vertical slope in low frequency section indicates the electric double layer energy storage. In high frequency section, the intercept of the semicircle with the real axis represents the equivalent series resistance (ESR).46 The differences of the ESRs are attributed to the pseudo-capacitive resistance. In Fig. 12b, the most of ESRs are less than 0.4 Ω, and the ESR decreases as the activated temperature rises, suggesting the low heteroatoms will reduce the additional resistance. The middle frequency section, the slope of 45° part, corresponds to the ion diffusion resistance.47 It is obvious that this section is shortened due to sufficient activation creating unblocked passages to facilitate the diffusion of ions.
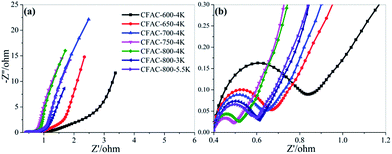 |
| Fig. 12 Nyquist plots of the activated samples (a) and its magnified image (b). | |
Galvanostatic charge–discharge tests have been conducted in a three-electrode system in different current densities from 0.1 to 30 A g−1 in 6 M KOH solution. Galvanostatic charge–discharge curves of CFAC-650-4K and CFAC-800-5.5K at different current densities are shown in Fig. 13a and b, respectively. The symmetrical isosceles triangle-like images suggest the electrical double layer characteristic. Compared with CFAC-650-4K, CFAC-800-5.5K with large pore volume displays less voltage drop, indicating the better cycling stability in high current densities. The specific capacitances of the activated samples in different current densities are shown in Fig. 13c & d. As exhibited in Table 3, the as-prepared carbons have superb electrochemical property compared with other literatures. CFAC-650-4K has higher specific surface areas than CFAC-600-4K (2515 m2 g−1 vs. 1610 m2 g−1), but they obtained similar initial specific capacitance in 0.1 A g−1 (351 F g−1 vs. 342 F g−1), since high N-6 content of CFAC-600-4K can compensate its relative poor porous structure (1.42 wt% vs. 0.66 wt%). CFAC-650-4K displays high specific capacitance of 342 F g−1 in 0.1 A g−1 and 225 F g−1 in 30 A g−1, and the large energy density of 30.4 W h kg−1 at 0.1 A g−1 and 20.0 W h kg−1 at 30 A g−1. By contrary, CFAC-600-4K shows poor performance in rapidly charge–discharge condition due to the blocked passage inhibiting the fast diffusion of ions (Table 4). On the other hand, the sample activated at high degree, like CFAC-800-5.5K, with the largest pore volume and mesopore proportion, performs perfect in capacitance retention, it shows a high specific capacitance of 288 F g−1 in 0.1 A g−1, 258 F g−1 in 10 A g−1 and still 260 F g−1 in 30 A g−1. The energy density of CFAC-800-5.5K acquired 25.6 W h kg−1 at 0.1 A g−1 and 23.1 W h kg−1 at 30 A g−1. In addition, the long cycle life for supercapacitor is an important goal for practical application, CFAC-800-5.5K shows a superb specific capacitance of 260 F g−1 and a higher retention rate of 98.48% after 10
000 cycles at 1 A g−1. In all, the rich-N sample (CFAC-650-4K) shows good charge–discharge performance, while the highly porous sample (CFAC-800-5.5K) is much suitable for large current application.
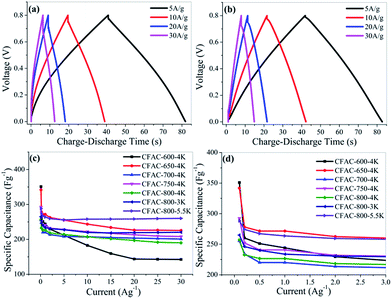 |
| Fig. 13 Charge–discharge curves of CFAC-650-4K (a) and CFAC-800-5.5K (b) at different current densities; specific capacitances (c) and its magnified image (d) of the activated samples at different current densities. | |
Table 3 Supercapacitor performance of biomass based N-doped activated carbons present in the literatures
Raw materials |
Electrolyte |
SBET (m2 g−1) |
N (at%) |
O (at%) |
Specific capacitance (F g−1) |
Current density (A g−1) |
Energy density (W h kg−1) |
Power density (kW kg−1) |
Reference |
The specific capacitance was obtained by CV curve at a scan rate of 5 mV s−1. The sample was tested in 30 A g−1. |
Human hair and glucose |
KOH |
849 |
3.1 |
10.7 |
264 |
0.25 |
7 |
0.045 |
16 |
Chicken feather |
H2SO4 |
1839 |
— |
— |
278 |
1 |
4.77 |
8.35 |
14 |
Human hair |
KOH |
451 |
2.82 |
13.32 |
192 |
0.3 |
— |
— |
5 |
Gizzard pepsin |
KOH |
2150 |
3.21 |
7.95 |
198 |
1 |
— |
— |
17 |
Fermented rice |
KOH |
2106 |
— |
— |
219 |
15 |
— |
— |
6 |
Fungi |
TEABF4 |
2264 |
2.27 |
8.53 |
158 |
0.1 |
— |
— |
7 |
Watermelon and PPy |
KOH |
158 |
2.12 |
15.45 |
281 |
5a (mV s−1) |
— |
— |
8 |
Chicken feather |
KOH |
2515 |
2.46 |
15.99 |
351 |
0.1 |
23.1 |
11.2b |
Our work |
Table 4 Specific capacitance (C) and energy density (E) at varying currents of the as-prepared samplesa
Samples |
0.1 A g−1 |
1 A g−1 |
5 A g−1 |
10 A g−1 |
20 A g−1 |
30 A g−1 |
C (F g−1) |
E (W h kg−1) |
C (F g−1) |
E (W h kg−1) |
C (F g−1) |
E (W h kg−1) |
C (F g−1) |
E (W h kg−1) |
C (F g−1) |
E (W h kg−1) |
C (F g−1) |
E (W h kg−1) |
The standard deviations of C are less than 10 F g−1. |
CFAC-600-4K |
351 |
31.2 |
244 |
21.7 |
212 |
18.8 |
183 |
16.3 |
144 |
12.8 |
142 |
12.6 |
CFAC-650-4K |
342 |
30.4 |
272 |
24.2 |
255 |
22.7 |
244 |
21.7 |
226 |
20.1 |
225 |
20.0 |
CFAC-700-4K |
256 |
22.8 |
220 |
19.6 |
208 |
18.5 |
208 |
18.5 |
204 |
18.1 |
201 |
17.9 |
CFAC-750-4K |
292 |
26.0 |
241 |
21.4 |
228 |
20.3 |
222 |
19.7 |
213 |
18.9 |
208 |
18.5 |
CFAC-800-4K |
257 |
22.8 |
227 |
20.2 |
214 |
19.0 |
207 |
18.4 |
197 |
17.5 |
190 |
16.9 |
CFAC-800-3K |
265 |
23.6 |
234 |
20.8 |
228 |
20.3 |
220 |
19.6 |
219 |
19.5 |
220 |
19.6 |
CFAC-800-5.5K |
288 |
25.6 |
264 |
23.5 |
256 |
22.8 |
258 |
22.9 |
258 |
22.9 |
260 |
23.1 |
Conclusions
In this paper, an N-doped porous carbon with large surface area is successfully prepared from chicken feather via carbonization and KOH activation. The various pore structure and surface elements of the activated samples can be achieved by changing parameter settings according to demands. The higher activated temperature or alkali/carbon ratio can result in a larger specific surface area and mesopore proportion, while a lower micropore proportion and heteroatom content. N-doped sites are the active sites to improve the affinities with CO2 and carrier ions, thus increasing the CO2 uptake and the pseudocapacitance; and the hygrophilous oxygen-containing groups could decrease the charge transport resistance to improve the electrochemical performance. Thus, the highest capacitance (351 F g−1) and CO2 uptake (6.5 mmol g−1) are obtained from CFAC-600-4K, and CFAC-800-5.5K exhibits the excellent retention rate (98% after 10
000 cycles at 1 A g−1), the method presented in this work could prepare the low cost material with highly promising application in energy storage and CO2 uptake.
Acknowledgements
We greatly acknowledge the financial support by the National Natural Science Foundation of China (51372012).
Notes and references
- R. J. White, V. Budarin and R. Luque, Chem. Soc. Rev., 2009, 38, 3401 RSC
. - L. Borchardt, M. Oschatz and S. Kaskel, Mater. Horiz., 2014, 1, 157 RSC
. - L. Hao, X. L. Li and L. J. Zhi, Adv. Mater., 2013, 25, 3899 CrossRef PubMed
. - W. C. Peng, S. Z. Liu, H. Q. Sun, Y. J. Yao, L. J. Zhic and S. B. Wang, J. Mater. Chem. A, 2013, 1, 5854 Search PubMed
. - Z. H. Guo, Q. W. Zhou, Z. J. Wu, Z. G. Zhang, W. Zhang, Y. Zhang, L. J. Li, Z. Z. Cao, H. Wang and Y. F. Gao, Electrochim. Acta, 2013, 113, 620 CrossRef PubMed
. - S. Y. Gao, Y. L. Chen, H. Fan, X. J. Wei, C. G. Hu, H. X. Luo and L. T. Qu, J. Mater. Chem. A, 2014, 2, 3317 Search PubMed
. - J. C. Wang and Q. Liu, RSC Adv., 2015, 5, 4396 RSC
. - Y. M. Ren, J. M. Zhang, Q. Xu, Z. M. Chen, D. Y. Yang, B. Wang and Z. Jiang, RSC Adv., 2014, 4, 23412 RSC
. - X. Y. Zhou, J. J. Tang, J. Yang, J. Xie and B. Huang, J. Mater. Chem. A, 2013, 1, 5037 Search PubMed
. - N. P. Wickramaratne and M. Jaroniec, J. Mater. Chem. A, 2013, 1, 112 Search PubMed
. - X. Y. Ma, M. H. Cao and C. W. Hu, J. Mater. Chem. A, 2013, 1, 913 Search PubMed
. - P. Kalyani and A. Anitha, Int. J. Hydrogen Energy, 2013, 38, 4034 CrossRef CAS PubMed
. - Z. Li, L. Zhang and B. S. Amirkhiz, Adv. Energy Mater., 2012, 2, 431 CrossRef CAS PubMed
. - Q. Wang, Q. Cao and X. Y. Wang, J. Power Sources, 2013, 225, 101 CrossRef CAS PubMed
. - W. J. Qian, F. X. Sun and Y. H. Xu, Energy Environ. Sci., 2014, 7, 379 Search PubMed
. - W. J. Si, J. Zhou and S. M. Zhang, Electrochim. Acta, 2013, 107, 397 CrossRef PubMed
. - X. T. Hong, H. Z. Zeng and L. J. Hui, Electrochim. Acta, 2014, 130, 464 CrossRef PubMed
. - Z. Li, Z. W. Xu and X. H. Tan, Energy Environ. Sci., 2013, 6, 871 Search PubMed
. - M. A. Sakkaa, H. Gualous, J. V. Mierlo and H. Culcu, J. Power Sources, 2009, 194, 581 CrossRef PubMed
. - A. Eddahech, O. Briat and M. Ayadi, Electr. Power Syst. Res., 2014, 106, 134 CrossRef PubMed
. - K. Y. Xie and B. Q. Wei, Adv. Mater., 2014, 26, 3592 CrossRef PubMed
. - R. Kötz and M. Carlen, Electrochim. Acta, 2000, 45, 2483 CrossRef
. - E. Raymundo-Pinero, K. Kierzek and J. Machnikowski, Carbon, 2006, 44, 2498 CrossRef PubMed
. - A. Stein, Z. Y. Wang and M. A. Fierke, Adv. Mater., 2009, 21, 265 CrossRef CAS PubMed
. - Y. Wang, R. Yang, Y. Wei, Z. J. Zhao and M. Li, RSC Adv., 2014, 4, 45318 RSC
. - E. Yoo, J. J. Nakamura and H. S. Zhou, Energy Environ. Sci., 2012, 5, 6928 Search PubMed
. - E. Senoz, R. P. Wool, C. W. J. McChalicher and C. K. Hong, Polym. Degrad. Stab., 2012, 97, 297 CrossRef CAS PubMed
. - M. Brebu and I. Spiridon, J. Anal. Appl. Pyrolysis, 2011, 91, 288 CrossRef PubMed
. - F. J. Wortmann, G. Wortmann, J. Marsh and K. Meinert, J. Struct. Biol., 2012, 177, 553 CrossRef CAS PubMed
. - J. X. Jiang, F. Su, A. Trewin, C. D. Wood, N. L. Campbell, H. Niu, C. Dickinson, A. Y. Ganin, M. J. Rosseinsky, Y. Z. Khimyak and A. I. Cooper, Angew. Chem., Int. Ed., 2007, 46, 8574 CrossRef PubMed
. - F. Su, C. K. Poh, J. S. Chen, G. Xu, D. Wang, Q. Li, J. Lin and X. W. Lou, Energy Environ. Sci., 2011, 4, 717 CAS
. - M. Zoccola, A. Aluigi and C. Tonin, J. Mol. Struct., 2009, 938, 35 CrossRef PubMed
. - E. Deydier, R. Guilet, S. Sarda and P. Sharrock, J. Hazard. Mater., 2005, 121, 14 CrossRef PubMed
. - J. P. Paraknowitsch, J. Zhang and D. Su, Adv. Mater., 2010, 22, 87 CrossRef PubMed
. - E. Yoo, J. J. Nakamura and H. S. Zhou, Energy Environ. Sci., 2012, 5, 6928 Search PubMed
. - C. O. Ania, V. Khomenko, E. R. Pinero, J. B. Parra and F. Béguin, Adv. Funct. Mater., 2007, 17, 1828 CrossRef PubMed
. - R. J. J. Jansen and H. V. Bekkum, Carbon, 1995, 33, 1021 CrossRef CAS
. - X. Hong, K. S. Hui, Z. Zeng, K. N. Hui, L. Zhang, M. Mo and M. Li, Electrochim. Acta, 2014, 130, 464 CrossRef CAS PubMed
. - S. Biniak, G. Szymanski, J. Siedlewsk and A. Swiatkowski, Carbon, 1997, 35, 1799 CrossRef CAS
. - D. H. Jurcakova, M. Seredych, G. Q. Lu and T. J. Bandosz, Adv. Funct. Mater., 2009, 19, 438 CrossRef PubMed
. - R. Yang, G. Q. Liu, M. Li, J. C. Zhang and X. M. Hao, Microporous Mesoporous Mater., 2012, 158, 108 CrossRef CAS PubMed
. - A. M. Puziy, O. I. Poddubnaya, A. M. Alonso, F. Suarez-Garcıa and J. M. D. Tascon, Carbon, 2002, 40, 1507 CrossRef CAS
. - M. Sevilla, C. Falco, M. M. Titiricic and A. B. Fuertesa, RSC Adv., 2012, 2, 12792 RSC
. - A. Elmouwahidi, Z. Z. Benabithe, F. A. Marín and C. M. Castilla, Bioresour. Technol., 2012, 111, 185 CrossRef CAS PubMed
. - U. B. Nasini, V. G. Bairi, S. K. Ramasahayam, S. E. Bourdo, T. Viswanathan and A. U. Shaikh, J. Power Sources, 2014, 250, 257 CrossRef CAS PubMed
. - L. Wei, M. Sevilla, A. B. Fuertes, R. Mokaya and G. Yushin, Adv. Funct. Mater., 2012, 22, 827 CrossRef CAS PubMed
. - H. L. Wang, Z. W. Xu, A. Kohandehghan, Z. Li, K. Cui, X. H. Tan, T. J. Stephenson, C. K. King'ondu, C. M. B. Holt, B. C. Olsen, J. K. Tak, D. Harfield, A. O. Anyia and D. Mitlin, ACS Nano, 2013, 7, 5131 CrossRef CAS PubMed
.
Footnote |
† Electronic supplementary information (ESI) available: XPS spectra of the CFC-500 and the activated samples at varying temperatures; table of bulk elementary composition of chicken feather and the as-prepared carbonized and activated samples. See DOI: 10.1039/c5ra01569c |
|
This journal is © The Royal Society of Chemistry 2015 |
Click here to see how this site uses Cookies. View our privacy policy here.