DOI:
10.1039/C5RA00718F
(Paper)
RSC Adv., 2015,
5, 19315-19320
Flexible and enhanced thermal conductivity of a Al2O3@polyimide hybrid film via coaxial electrospinning†
Received
13th January 2015
, Accepted 10th February 2015
First published on 10th February 2015
Abstract
A novel core–shell structure of Al2O3 nanoparticles (NPs) attached on poly(amic acid) (PAA) fiber has been successfully developed by facile coaxial electrospinning technology for the first time. The as-prepared PAA fiber went through imidization to prepare the Al2O3@polyimide (Al2O3@PI) film. The resultant films with different Al2O3 contents are characterized by scanning electron microscopy, Fourier transform infrared spectroscopy, thermal gravimetric analysis, and dynamical mechanical analysis. The results indicated that the Al2O3 NPs could uniformly decorate the surface of fibers with a diameter of about 1 μm, which enhanced the thermal and mechanical properties of the fiber-based films. In particular, the flexible film with a high content of Al2O3 of 59.3 wt% presents a high storage modulus (2.11 GPa) and excellent thermal stability (474 °C at 5% mass loss) as well as superior in plane thermal conductivity of 9.66 W m−1 K−1. Finally, compared with pure PI film, the Al2O3@PI fiber-based film exhibits excellent thermal transfer ability in light emitting diode packaging. Therefore, the novel Al2O3@PI fiber-based film with integrated properties of insulation, thermal conductivity and flexibility can be used for wearable electronics and power devices.
Introduction
With the progress in size and performance of electronic devices which have rapidly become denser and more powerful, the continued miniaturization of electronic device components requires higher heat dissipation. There is no doubt that the operating temperature of the junction has exponentially affected the reliability of an electronic device.1 Thus, developing high thermal conductivity materials to dissipate unwanted heat quickly and effectively is desirable.2 Compared with low-melting-point solder alloys, polymer based composites with good adhesion to various substrates, economic and excellent processing performance have attracted a great deal of interest in the field of electronic packaging.3,4 However, the thermal conductivity of the polymers is usually in the order of 0.2 W m−1 K−1. To overcome this problem, various conductive materials, such as Ag,5 graphene,6 carbon nanotube,7 graphite8 are used as thermal transfer medium to fill the polymer matrix. Though these fillers can increase thermal conductivity to a certain extent, they simultaneously cause the target composites to be electrically conductive.9 On the other hand, high thermal conductive materials with electrically insulation are much more significant and meet the special demand of electronic packaging. Thus, some ceramic fillers including boron nitride,10,11 aluminum nitride,12 silicon carbide,13 and alumina (Al2O3),14 etc., are used as high thermal conductive fillers to blend with polymer substrate. It is well known that a high volume fraction of thermally conductive fillers, generally >60 vol%,1 is necessary to obtain high thermal conductivity for the composite. However, such high contents of inorganic fillers would consequentially disserve the mechanical property and flexibility of polymer composite to limit its practical application. Furthermore, the thermal conductivity of composite is lower than expected because of high thermal resistance at the interface between the filler and the resin.15 Therefore, developing novel composites with high thermal conductivity and mechanical property are still a challenge.
Among the polymer fiber fabrication methods, electrospinning has emerged as an attractive technique for the preparation of an array of merits of the ultrafine fibers in micro/nano-scale fineness.16 The as-prepared materials with functional architecture have been exploited for diverse applications like filtration, nano-sensors, tissue engineering, and so on.17 Many technologies such as so-gel,18 radio frequency sputtering,19 metal-organic chemical vapor deposition20 and atomic layer deposition21 have been reported for electrospinning inorganic nanofibers to obtain inorganic–inorganic core–shell or hierarchical nanostructure22–25 for its various functional properties. However, the fabrication of polymer-inorganic core–shell nanofibers is somewhat challenging because the deposition of inorganic shell layer requires a high temperature process that leads to the degradation of polymeric core structure easily. Very recently it emerged that the coaxial electrospinning technology provided an alternative route to design functional composite with core–shell or hollow structures.26–29 Therefore, the coaxial electrospinning become a kind of very promising technique for preparing functional composite material. Nevertheless, to the best of our knowledge, the focus on the fabrication of polymer-inorganic core–shell nanofibers directly by coaxial electrospinning has been very limited in the literature.16
Herein, we demonstrate a novel and simple approach to coat Al2O3 nanoparticles (NPs) onto PI fiber (denoted as Al2O3@PI) by coaxial electrospinning as shown in Fig. 1. Firstly, under proper voltage, polyvinylpyrrolidone (PVP) solution including Al2O3 NPs and poly(amic acid) (PAA) was sprayed through a coaxial spinneret simultaneously and the resultant composite fibers were collected by rotating collector with much higher speed for orientation. Secondly, the resultant film was cured to prepare Al2O3@PI composite fiber-based film. The fibers were oriented to maximize the conductivity, and the Al2O3 NPs coated on the fiber further provided much more thermal conductive paths in plane. Furthermore, the structure, morphology, thermal conductivity and mechanical properties of the as-prepared hybrid film were comprehensively investigated. At last, the practical thermal transfer performance was also investigated in the light emitting diode (LED) packaging.
 |
| Fig. 1 Schematic illustration for the fabrication of Al2O3@PI composite fiber-based film. | |
Experimental
Materials
Pyromellitic dianhydride (PMDA), 4,4′-oxidianiline (ODA) and N,N-dimethylacetamide (DMAc) were commercially obtained from China National Medicine Co. PVP was supplied by Aladdin. The Al2O3 NPs with an average diameter of 200 nm were supplied by Denki Kagaku Kogyo Kabushiki Kaisha, Japan. The commercial thermal conductive glue ST922 was commercially supplied by Balance Stars Co., LTD.
Preparation of precursor solutions
The precursor PAA was synthesized by the reaction between ODA and PMDA with an equivalent molar ratio. The polycondensation was performed in DMAc at about 0 °C for 4 hours. The solid content of the pristine PAA solution was 15 wt%. The as-prepared PAA solution was directly used as the core component in coaxial electrospinning. As the shell component, the typical procedure of preparing PVP solution including Al2O3 NPs was operated as follows. Firstly, the Al2O3 fine powder was fully dispersed in DMAc by ultrasonic for 4 hours. Then appropriate PVP was added into the solution under magnetic stirring until dissolved completely.
Coaxial electrospinning
Coaxial electrospinning equipment (SS3556H) was supplied by Beijing Ucalery Technology and Development Co., Ltd. The PVP solution and PAA solution were poured into 10 mL plastic syringes mounted on the pump with a multitrack grip, respectively. Hence, the flow rates of two kinds of solutions were identical during the process. The coaxial spinneret was comprised of an inner needle (inner diameter = 0.50 mm and outer diameter = 0.80 mm) concentrically mounted on an outer needle (i.d 1.26 mm, o.d. 1.66 mm) and was grounded by use of an alligator clip. Then electrospinning was carried out at an applied voltage of 15–20 kV. The feeding rate of each syringe was 0.60 mL h−1 and the spinneret-collector distance was 20 cm. Herein, by adjusting the concentrations of Al2O3 NPs in PVP, different contents Al2O3 NPs, including 0, 26.7, 42.2, 59.3, 74.5 wt%, of PAA composite fibers could be attained. Then all the electrospun fiber-based films were dried at 60 °C overnight to evaporate completely the residual solvent. And thermally imidization was completed by the following program: heated at 150 °C for 60 min, 270 °C for 60 min and 300 °C for 180 min with a heating rate of 5 °C min−1.
Characterization of composites
The morphology of as-prepared fibers was studied by scanning electron microscopy (SEM), which was recorded with a Nova NanoSEM 450. The weight losses of the composites were analyzed using thermal gravity analysis (TGA) which was made on a TA SDTQ600 thermo-gravimetric analyzer. The microbalance has a precision of ±0.1 μg. Samples of about 10 mg were placed into 70 μL alumina pans. The samples were heated from 30 to 800 °C under an air flow of 100 mL min−1. Fourier transform infrared (FTIR) spectra were recorded with Bruker Vertex 70 spectrometer (Bruker Optik GmbH, Ettlingen, Germany) in the range of 4000–400 cm−1. The thermal diffusivity of the composites was investigated at 25 °C through xenon flash equipment (LFA447, Germany) according to ASTM E1461. The diameter of sample used for laser flash method was 1 inch and a thickness of 50 ± 5 μm with the mirror-like polished surface. Differential scanning calorimetry (DSC) with sapphire reference was used to measure the specific heat capacity (Cp) with a heating rate of 5 °C min−1 under nitrogen. The density of composites was measured by the Archimedean buoyancy method using an electronic analytical balance (FA2104J, China).
Tensile test property of PI composites samples at room temperature was measured using dynamical mechanical analysis (DMA, Q800, TA instruments) with stress–strain model. The force was raised at the rate of 1 N min−1 to 18 N. The samples were cut in rectangle about 5 mm × 50 mm, with a thickness about 50 μm which measure by micrometer at five different points for each sample. And each point was measured for three times. FLIR-T355 infrared camera was used to take picture for the temperature field of LED at room temperature (24 °C) with relative humidity of 56%, and the measurement distance between the lens and the target was 0.2 m.
Results and discussion
Characterization of Al2O3@PI fiber-based film
Polyimide was used as the core layer of composite fiber due to its thermal stability and conventional use in microelectronic applications. Different contents of Al2O3 NPs were used as the thermal transfer medium in this design because of their excellent thermal conductivity and high filler contents. By controlling the electrospun polymer solution and the electrospinning conditions (e.g., voltage, speed), we can obtain highly aligned fibers with uniform diameter (about 1 μm) after imidization, as shown in Fig. 2. With increasing of Al2O3 contents from 26.7 wt% to 74.5 wt% in the composite fiber, the Al2O3 NPs located on the shell layer become denser and cover the whole surface of fiber.
 |
| Fig. 2 SEM images of PI fibers with Al2O3 NPs contents of (a) 26.7 wt%, (b) 42.2 wt%, (c) 53.9 wt% and (d) 74.5 wt%. | |
The uniform dispersion of the Al2O3 NPs in the composites is an important issue for the functional material. Thus, PVP was used to prepare stable solution including Al2O3 NPs not only it conducive to the dispersion of inorganic filler30,31 but also it is a template for preparing PAA fibers.32 However, to realize the thermal conductivity of composite fiber film, the PVP shell layer should be removed to expose the Al2O3 NPs. It can be seen that in the Al2O3@PAA composite fiber with a PVP coating layer, most of the Al2O3 NPs were covered by PVP and the fiber surface was very smooth (Fig. S1†). Then, during high-temperature imidization process, the PVP in the shell layer was removed and much more Al2O3 spherical NPs with content of 74.5 wt% could be exposed and evenly distributed over the surface of the fibers as shown in Fig. 2d. Therefore, the PVP can be facilely removed to decrease the interfacial thermal resistance of composite fiber-based film.
To characterize the structure variations during the process of imidization of composite, FT-IR spectra were recorded in Fig. 3 and S2.† It can be seen that the characteristic peaks at 1662, 1442 and 1296 cm−1 were attributed to the stretching vibration of carboxide (C
O), C–H bending vibration and stretching vibration of PVP, respectively, as shown in Fig. S2.† These characteristic peaks also presented in the samples before curing as shown in Fig. 3a–c which disappeared after imidization (Fig. 3d), indicating that PVP could be removed completely in the as-prepared composite fiber. Furthermore, in the curve of composite fiber, the characteristic peaks at 1780 cm−1, 1730 cm−1 and 723 cm−1, as shown in Fig. 3d, were attributed to asymmetric vibration, symmetric vibration and bending vibration of carboxide (C
O) of PI respectively,5,33 indicating that the PI fibers coated by Al2O3 NPs have been successfully prepared according to the proposed imidization procedure.
 |
| Fig. 3 FTIR spectra of composite fiber-based film at different stages during imidization: (a) room temperature, (b) after 150 °C for 1 hour, (c) after 270 °C for 1 hour and (d) after 300 °C for 3 hours. | |
Mechanical properties of Al2O3@PI fiber-based film
It was expected that the mechanical properties of the composite fiber would be enhanced due to the large aspect ratio of Al2O3 NPs, strong adhesion between Al2O3 NPs and PI fiber. The typical tensile stress–strain curves of Al2O3@PI fiber-based films are shown in Fig. 4 and summarized in Table 1. The oriented pure PI fiber-based film exhibits a remarkable tensile strength of 16.13 MPa and the elongation at the break is 2.67%. From the slope of the stress–strain curve, the elastic modulus was measured, which is 0.81 GPa for pure PI film, in the order of that of pure PI polymer as reported.34,35 As shown in Table 1, with the increase of Al2O3 contents, the elastic modulus of the composites was increased when the Al2O3 content was below than 59.3 wt%. However, the elastic modulus of Al2O3@PI fiber-based film with 74.5 wt% of Al2O3 was reduced which indicated that the inorganic particles with higher contents may deteriorate the mechanical performance of the composites, which was consistent with previous work.36,37 This might be related to poor dispersion of Al2O3 NPs in the PI matrix. The decrease of the tensile strength could be caused by the premature failure starting at the filler aggregates.38 In our work, the Al2O3@PI fiber-based film with high contents (59.3 wt%) of inorganic particles possessed higher elastic modulus (2.11 GPa) than those of pure PI film, which also has excellent flexibility as shown in Fig. 4b. After crimping and bending, there was no crack generated. Therefore, the composites with high inorganic filler contents were prepared by coaxial electrospinning. Such high loadings endow the fibers with high mechanical strength as well as excellent flexibility.
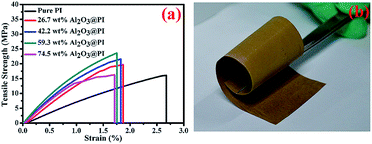 |
| Fig. 4 (a) Stress–strain curves of pure PI and Al2O3@PI fiber-based films and (b) the photograph of Al2O3@PI fiber-based film with 59.3 wt% of Al2O3 NPs under winding condition. | |
Table 1 Mechanical and thermal properties of the Al2O3@PI fiber-based films
Al2O3 (wt%) |
Tensile strength (MPa) |
Elongation (%) |
Elastic modulus (GPa) |
T5 (°C) |
0 |
16.13 |
2.67 |
0.81 |
420 |
26.7 |
19.71 |
1.87 |
1.53 |
430 |
42.2 |
21.58 |
1.83 |
1.85 |
437 |
59.3 |
23.62 |
1.75 |
2.11 |
474 |
74.5 |
16.28 |
1.71 |
1.74 |
517 |
Thermal properties of Al2O3@PI fiber-based films
The thermal stability of pure PI and Al2O3@PI fiber-based films were assessed as shown in Fig. 5. The temperature corresponding to 5% weight loss (T5) was taken as an index of thermal stability as shown in Table 1. It can be seen that the decomposition of pure PI and Al2O3@PI fiber-based films took place in a single step and it started at around 420 °C. From the inset we can see that the T5 of composites shifted to an obvious higher temperature with the increase of Al2O3 contents compared with that of pure PI. The T5 of 59.3 wt% Al2O3@PI film increased by 54 °C and up to 474 °C comparing to that of pure PI film. Therefore, these results suggested that the immobilization of Al2O3 NPs could enhance the thermal stability of composite films.
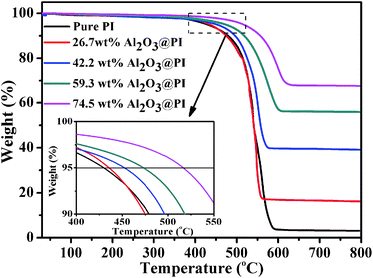 |
| Fig. 5 TGA curves of pure PI and Al2O3@PI fiber-based films. | |
It is recognized that the key to improve the thermal conductivity of a resin is the formation of effective thermal conductivity network in matrix. In present work, oriented fibers may improve the thermal conductivity of composites along the axial direction. Furthermore, the dense spherical Al2O3 NPs decorated on the whole surface of separate PI fiber would provide much more thermal conductivity channels in plane. Then, the thermal conductivity can be calculated using the definition of diffusivity
where
k is the thermal conductivity,
ρ is the density and
Cp is the specific heat at constant pressure as shown in Table S1.
† The thermal conductivities of composites with different contents of Al
2O
3 were determined using
eqn (1) and shown in
Fig. 6a. The pure PI film showed high thermal conductivity of 3.80 W m
−1 K
−1, which can be explained by the high orientation of the fiber as reported.
39,40 Furthermore, the thermal conductivity of composite films increased sharply with increasing Al
2O
3 contents from 0 to 59.3 wt%. With the densely decorating of the Al
2O
3 NPs in the alignment PI fiber which form effective conductive paths or network to improve the thermal diffusion ability in plane as shown in
Fig. 6b. When the content of Al
2O
3 was increased up to 59.3 wt%, the composite film showed excellent thermal conductivity of 9.66 W m
−1 K
−1, while the thermal conductivity of composite film with 74.5 wt% Al
2O
3 was 9.90 W m
−1 K
−1 by the increment of 2.5%. Therefore, the enhanced thermal conductive composite film with core–shell structure was developed by coaxial electrospinning technology facilely.
 |
| Fig. 6 (a) The thermal conductivity of Al2O3@PI fiber-based film with different contents of Al2O3 NPs and (b) one probable thermal transfer model in the Al2O3@PI fiber-based film. | |
To validate the practical application of the as-prepared Al2O3@PI fiber-based film in electronic device, LED was used as a typical heat source and placed at the center of the film sample with 59.3 wt% of Al2O3 NPs and bonded by commercial thermal conductive glue (ST922). By recording the changing of temperature of LED, the thermal diffusion ability of different films could be qualitatively compared. For reducing the error, the same amount of glue was used for packing the LED on the sample with Cu wire to connect the power supply. The size of film sample was 1 inch with 50 um of thickness as shown in Fig. 7. In order to imaging the temperature field of the thermal source during LED working, FLIR T335 infrared camera was used. With a thermal sensitivity of 0.05 °C and high speed data acquisition and evaluation of thermal images, it makes up an excellent investigative tool to analysis of the high-frequency temperature fields. Different voltages were used to investigate the thermal transfer property of pure PI and composite films as shown in Fig. 8. It depicts that temperature distribution of packaging just after the end of heating time th (th = 300 s, U = 3.2, 3.4 V). The stable temperature of composite and pure PI film under 3.2 V were in the order of 41.6, 45.7 °C, respectively, and under 3.4 V were about 85.4, 97.7 °C, respectively. It's worth noting that the thermal conductivity of the glue was 0.671 W m−1 K−1, and which could not diffuse the heat flow from LED to the film effectively. Therefore, there was not any significant improvement for PI composite film. However, it can be found that the composite film had comparative thermal transfer ability compared with that of pure PI film by infrared camera. Meanwhile, the LED packaging based on composite film possesses much broader thermal stream distribution than that of pure PI film. Furthermore, when the loaded voltage and heating time were the same, the temperature of LED packed on Al2O3@PI fiber-based film was always lower than that of LED packed on pure film as shown in Fig. 9, which suggested that the composite film possessed excellent thermal diffusion rate in plane.
 |
| Fig. 7 Schematic depicting the LED packed with Al2O3@PI fiber-based film. | |
 |
| Fig. 8 Local temperature of LED packaging under different voltages after 300 s: (a and b) 59.3 wt% Al2O3@PI fiber-based film and pure PI film under 3.2 V, (c and d) 59.3 wt% Al2O3@PI fiber-based film and pure PI film under 3.4 V. | |
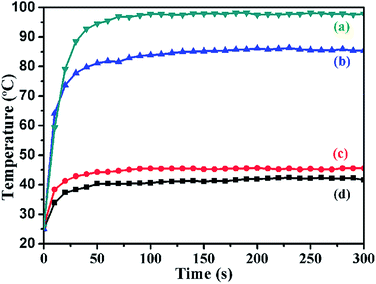 |
| Fig. 9 The temperature of LED packed by different films varying with times under different voltage: (a and b) pure PI film and 59.3 wt% Al2O3@PI film under voltage of 3.4 V, (c and d) pure PI film and 59.3 wt% Al2O3@PI film under voltage of 3.2 V. | |
Conclusions
In summary, a novel Al2O3@PI fiber-based film was successfully developed by a facile coaxial electrospinning technology for the first time. There into, the Al2O3 NPs can be coated on the separate PI fiber densely when the contents of Al2O3 rose up to 59.3 wt%, which still exhibited remarkably high elastic modulus (2.11 GPa), flexibility and enhanced thermal conductivity (9.66 W m−1 K−1). Furthermore, the specific composite film was used as a thermal dissipation material in the LED packaging. The results indicated that the as-prepared Al2O3@PI fiber-based film could disperse unwanted heat effectively and rapidly compared with pure PI film. Therefore, the present material and process design may provide a novel platform for the synthesis of other multifunctional composites for various special applications.
Acknowledgements
This work was financially supported by the National Natural Science Foundation of China (Grant no. 21201175), and Guangdong and Shenzhen Innovative Research Team Program (no. 2011D052, KYPT20121228160843692), and R&D Funds for basic Research Program of Shenzhen (Grant no. JCYJ20120615140007998).
Notes and references
- Y. Hwang, M. Kim and J. Kim, RSC Adv., 2014, 4, 17015 RSC.
- V. Singh, T. L. Bougher, A. Weathers, Y. Cai, K. Bi, M. T. Pettes, S. A. McMenamin, W. Lv, D. P. Resler, T. R. Gattuso, D. H. Altman, K. H. Sandhage, L. Shi, A. Henry and B. A. Cola, Nat. Nanotechnol., 2014, 9, 384–390 CrossRef CAS PubMed.
- Y. Zhou, Y. Yao, C. Y. Chen, K. Moon, H. Wang and C. P. Wong, Sci. Rep., 2014, 4, 4779 Search PubMed.
- C. Min, D. Yu, J. Cao, G. Wang and L. Feng, Carbon, 2013, 55, 116–125 CrossRef CAS PubMed.
- C. Zandén, X. Luo, L. Ye and J. Liu, Compos. Sci. Technol., 2014, 94, 54–61 CrossRef PubMed.
- R. Qian, J. Yu, C. Wu, X. Zhai and P. Jiang, RSC Adv., 2013, 3, 17373 RSC.
- Z. Han and A. Fina, Prog. Polym. Sci., 2011, 36, 914–944 CrossRef CAS PubMed.
- M. T. Pettes, H. Ji, R. S. Ruoff and L. Shi, Nano Lett., 2012, 12, 2959–2964 CrossRef CAS PubMed.
- R. Qian, J. Yu, C. Wu, X. Zhai and P. Jiang, RSC Adv., 2013, 3, 17373 RSC.
- T. L. Li and S. L. C. Hsu, J. Mater. Chem. B, 2010, 114, 6825 CAS.
- W. Yan, Y. Zhang, H. Sun, S. Liu, Z. Chi, X. Chen and J. Xu, J. Mater. Chem. A, 2014, 2, 20958–20965 CAS.
- A. Agrawal and A. Satapathy, Composites, Part A, 2014, 63, 51–58 CrossRef CAS PubMed.
- J. P. Cao, X. Zhao, J. Zhao, J. W. Zha, G. H. Hu and Z. M. Dang, ACS Appl. Mater. Interfaces, 2013, 5, 6915–6924 CAS.
- Z. Li, W. Wu, H. Chen, Z. Zhu, Y. Wang and Y. Zhang, RSC Adv., 2013, 3, 6417 RSC.
- Y. Shimazaki, F. Hojo and Y. Takezawa, Appl. Phys. Lett., 2008, 92, 133309 CrossRef PubMed.
- F. Kayaci, C. Ozgit-Akgun, I. Donmez, N. Biyikli and T. Uyar, ACS Appl. Mater. Interfaces, 2012, 4, 6185–6194 CAS.
- H. Yuan, S. Zhao, H. Tu, B. Li, Q. Li, B. Feng, H. Peng and Y. Zhang, J. Mater. Chem., 2012, 22, 19634 RSC.
- Y. Aykut, C. D. Saquing, B. Pourdeyhimi, G. N. Parsons and S. A. Khan, ACS Appl. Mater. Interfaces, 2012, 4, 3837–3845 CAS.
- L. Liu, H. Zhang, Y. Wang, Y. Su, Z. Ma, Y. Xie, H. Zhao, C. Chen, Y. Liu, X. Guo, Q. Su and E. Xie, Nanoscale Res. Lett., 2010, 5, 1418–1423 CrossRef CAS PubMed.
- M. E. Fragalà, I. Cacciotti, Y. Aleeva, R. Lo Nigro, A. Bianco, G. Malandrino, C. Spinella, G. Pezzotti and G. Gusmano, CrystEngComm, 2010, 12, 3858 RSC.
- S. W. Choi, J. Y. Park and S. S. Kim, Nanotechnology, 2009, 20, 465603 CrossRef PubMed.
- S. H. Ahn, D. J. Kim, W. S. Chi and J. H. Kim, Adv. Mater., 2013, 25, 4893–4897 CrossRef CAS PubMed.
- Y. Zhang, R. Li, X. Zhou, M. Cai and X. Sun, Cryst. Growth Des., 2009, 9, 4230–4234 CAS.
- N. Wang, C. Sun, Y. Zhao, S. Zhou, P. Chen and L. Jiang, J. Mater. Chem., 2008, 18, 3909 RSC.
- X. Wang, D. P. Yang, P. Huang, M. Li, C. Li, D. Chen and D. Cui, Nanoscale, 2012, 4, 7766–7772 RSC.
- T. Yuan, B. Zhao, R. Cai, Y. Zhou and Z. Shao, J. Mater. Chem., 2011, 21, 15041 RSC.
- Q. Ma, J. Wang, X. Dong, W. Yu, G. Liu and J. Xu, J. Mater. Chem., 2012, 22, 14438 RSC.
- H. Yang, C. R. Lightner and L. Dong, ACS Nano, 2012, 6, 622–628 CrossRef CAS PubMed.
- M. Pakravan, M. C. Heuzey and A. Ajji, Biomacromolecules, 2012, 13, 412–421 CrossRef CAS PubMed.
- G. Chang, L. He, W. Zheng, A. Pan, j. Liu, Y. Li and R. Cao, J. Colloid Interface Sci., 2013, 396, 129–137 CrossRef CAS PubMed.
- S. P. Bhardwaj, K. K. Arora, E. Kwong, A. Templeton, S. D. Clas and R. Suryanarayanan, Mol. Pharm., 2014, 11, 4228–4237 CrossRef CAS PubMed.
- C. Li, Z. H. Wang, D. G. Yu and G. R. Williams, Nanoscale Res. Lett., 2014, 9, 258 CrossRef PubMed.
- D. Chen, Y. E. Miao and T. Liu, ACS Appl. Mater. Interfaces, 2013, 5, 1206–1212 CAS.
- I. H. Tseng, J. C. Chang, S. L. Huang and M. H. Tsai, Polym. Int., 2013, 62, 827–835 CrossRef CAS.
- J. H. Seol, J. H. Won, M. S. Lee, K. S. Yoon, Y. T. Hong and S. Y. Lee, J. Mater. Chem., 2012, 22, 1634 RSC.
- S. Zhao, L. Schadler, H. Hillborg and T. Auletta, Compos. Sci. Technol., 2008, 68, 2976–2982 CrossRef CAS PubMed.
- L. Fang, C. Wu, R. Qian, L. Xie, K. Yang and P. Jiang, RSC Adv., 2014, 4, 21010 RSC.
- H. Liimatainen, N. Ezekiel, R. Sliz, K. Ohenoja, J. A. Sirvio, L. Berglund, O. Hormi and J. Niinimaki, ACS Appl. Mater. Interfaces, 2013, 5, 13412–13418 CAS.
- Y. Liu and S. Kumar, ACS Appl. Mater. Interfaces, 2014, 6, 6069–6087 CAS.
- G. Yuan, X. Li, Z. Dong, A. Westwood, B. Rand, Z. Cui, Y. Cong, J. Zhang, Y. Li, Z. Zhang and J. Wang, Carbon, 2014, 68, 426–439 CrossRef CAS PubMed.
Footnote |
† Electronic supplementary information (ESI) available. See DOI: 10.1039/c5ra00718f |
|
This journal is © The Royal Society of Chemistry 2015 |
Click here to see how this site uses Cookies. View our privacy policy here.