DOI:
10.1039/C4RA17065B
(Paper)
RSC Adv., 2015,
5, 19955-19960
Growth mechanism of curved Mg–Al–CO3 layered double hydroxide nanostructures in a one-pot assembly procedure under ambient pressure
Received
26th December 2014
, Accepted 3rd February 2015
First published on 3rd February 2015
Abstract
We show that the amount of peroxide added is a governing factor, leading to the curved or amorphous morphologies of Mg–Al-LDH products in a reflux system under ambient pressure. A concerted growth mechanism is proposed to elucidate the formation of the unconventional nano-features of the products.
Introduction
Layered double hydroxides (LDHs), with the general formula of [M1−x2+Mx3+(OH)2]Ax/nn−·mH2O, are composed of the layered planar sheets of M2+/M3+ hydroxides and the interlayer of An− anions.1–8 By assembling functional agents to the delaminated LDHs,9–12 a broad variety of applications may be developed, including polymer/LDH nanocomposites,13–21 functional thin films,22–25 catalysts,26,27 electrode materials,28–33 photo-functional materials34,35 and bioinorganic hybrid materials.36 Thus, an appropriate and simple delamination method is required before functionalization. In general, there are two strategies for delaminating LDH compounds, namely the “bottom-up” approach and the “top-down” approach.1 For the bottom-up synthesis, LDH products are typically prepared via a microemulsion-mediated hydrothermal synthesis. The size of the particles can be controlled both in diameter and thickness by tuning the water to surfactant ratio in different reverse microemulsion systems.37–44 In parallel, significant efforts have focused on the delamination of LDHs by the top-down synthesis in polarized solvents, such as butanol,45–47 acrylates,10 formamide48–52 and N,N-dimethylformamide–ethanol mixture,53–55 as well as in nonpolarized solvents such as CCl4,56–58 and other type of solvents.59,60 Adachi-Pagano et al.45 reported the complete delamination of the Zn–Al-LDH using sodium dodecyl sulfate (SDS) as an anionic surfactant and butanol as the dispersant. Ma et al.61 exfoliated Co–Fe-LDHs into nanosheets in formamide by an ultrasonic treatment through hexamethylenetetramine (HMT) hydrolysis. Wu et al.62 reported the direct delamination of Mg–Al–NO3 in formamide using an ultrasonic treatment at room temperature. The obtained delaminated LDH products in these reports are generally unilamellar sheets. However, for the use in applications, such as catalysis, sensing and electrochemical energy storage devices, designing appropriate client–substrate interactions for the functionalized LDH products is more important to obtain the desired physico-chemical properties.63–65 To this end, unconventional curved LDHs could provide a higher surface area, metal dispersion, suitable morphological structure, reduction properties, and porosity,66 which would of course increase the accessibility to both the internal galleries and the outer surface, compared with typical plane LDHs.67–72
Several reports have synthesized non-conventional LDH morphologies and found that they exhibit interesting sensing,73 catalytic,74 photocatalytic,75 and supercapacitive76–79 performances. Adachi-Pagano et al.80 reported a sand-rose morphology of Mg–Al-LDHs using a urea hydrolysis method in a mixture solvent of water and ethylene glycol (EG). The size distribution of the mono-dispersed particles was determined by the water/EG ratio, urea concentration and Mg/Al ratio. The preferential adsorption of EG on the (00l) planes of Mg–Al-LDH prevents growth in the direction perpendicular to the layers, leading to the inhibition of particle ripening and resulting in the as-obtained sand-rose morphologies. The same phenomenon was observed by Wei et al.81 when synthesizing Li–Al-LDHs using the urea method in a water–ethanol mixture solvent, where the Ostwald ripening mechanism was employed to elucidate the formation of the polymorphic morphologies. The petal-like Li/Al LDHs showed a much higher specific capacitance compared with the spiral structure and hexagonal nanosheets. Using chitosan as a template, Li and coworkers82 suggested that the Ni–Al-LDH particles co-precipitated through the urea method curves in the a direction, while the growth in both the a and c directions will be inhibited, resulting in a curved fibre-like shapes of the products. Liu et al.65 reported special nanocone structures of Co–M-LDHs (M = Ni, Cu, Zn) using the urea method and simultaneously intercalated dodecyl sulfate (DS) into the interlayer spaces. The LDH nanocones with controllable transition-metal compositions, peculiar hollow feature and large interlayer spacing, exhibited high specific capacitance and remarkable cycling stability when used as supercapacitor electrodes.
We have already mentioned that the polymorphic structural features of different LDH compounds generally occur with the urea method, and that third-party agents, either organic solvents or surfactants, play an important role in forming the special spatial configuration. In fact, these third-party agents should act as an inhibitor to slow down the growth at certain lattice directions or to prevent the particles from agglomerating. Recently, Yan et al.83 reported a one-pot approach to assemble Mg–Al-LDH nanosheets using the urea method, where peroxide was selected as the third-party agent. Within an autoclave environment, the prepared LDH appeared as unilamellar flat nanosheets, and delamination was concluded to be implemented by the oxygen gas from the peroxide decomposition. In the present study, we implemented this one-pot process under ambient pressure within a reflux system. Interestingly, unlike in the sealed system, our procedure offered the opportunity to tune the polymorphic features of Mg–Al-LDH products by changing the peroxide concentration. In particular, with a 20 wt% addition of H2O2, curved or even cross-linked delaminated sheets were observed. Based on the XRD, SEM, FT-IR and TGA characterizations, we proposed a different concerted growth mechanism to explain the as-obtained curved patterns, which might be useful for understanding the synthesis of different morphologies for similar hydroxide systems.
Experimental
Preparation of the materials
All analytical-grade chemicals utilized in our experiments were used as purchased. The Mg2+, Al3+ precursors (as Mg(NO3)2·6H2O, Al(NO3)3·9H2O, respectively) and urea were dissolved in deionized water or peroxide solution in a 500 mL round-bottom flask with a Mg2+
:
Al3+
:
urea molar ratio of 4
:
1
:
10 at room temperature, where the Mg2+ concentration was set to 0.004 mol L−1. The following co-precipitation process was carried out within the same flask under ambient pressure with reflux. For the water solvent, we considered four bath temperatures (100 °C, 120 °C, 150 °C and 180 °C) and three bath durations (3 h, 5 h and 8 h) to determine the optimal synthesis conditions. These parameters were successively employed for the peroxide solution solvent, where three different peroxide concentrations (10 wt%, 20 wt% and 30 wt%) were studied. The filtered solid products were washed with deionized water five times and then dried at 60 °C for 12 h before characterization.
Characterization techniques
The X-ray diffraction (XRD) data of all the samples were collected on a German Bruker D8-Focus powder X-ray diffractometer with Cu Kα radiation (λ = 1.540598 Å) at a scanning rate of 0.05 seconds per step. Thermogravimetric analysis was carried out on a TGA-DSC (STA449 F3, NETZSCH, German) instrument, where the temperature range was set to 30–1000 °C at a heating rate of 10 °C min−1 under N2 atmosphere. Fourier-transform infrared (FT-IR) spectra were recorded with a Fisher Nicolet 6700. Scanning electron microscopy (SEM) was performed on a Hitachi D8-Focus instrument at an acceleration voltage of 0.1–30 kV.
Results and discussion
We first characterized the LDH samples prepared in water solvent at different temperatures, where the synthesis duration was set to 8 h. The XRD patterns are shown in Fig. 1. At the temperature of 100 °C, no observable diffraction peak can be observed, indicating the products may appear as an amorphous state. As the bath temperature increases to 120 °C and 150 °C, typical diffraction peaks at low angles as indexed by (003), (006), (009) and at high angles for (110), (113) in the XRD patterns suggest the lamellate layers are well crystallized. However, if the bath temperature is set too high (180 °C in our experiments), the crystalline behaviour is considerably weakened. According to the chemical properties of the precursors we used, we can conclude that the major reason for the observed crystalline behaviour is due to the hydrolysis/decomposition of urea. Since the LDH nucleation process occurs in a water or water–peroxide environment, where the temperature variation is limited at different bath temperature, the detailed composition of the as-obtained LDH products should be approximated,84,85 leading to the typically observed XRD patterns of Mg–Al–CO3 LDHs as reported previously.35,86 On the other hand, at the liquid–gas interface, the boiled species may be over-heated by the bath and the reflux system will then recycle the agents. At relatively low temperatures, urea hydrolysis plays the dominant role and provides –OH species for the co-precipitation. The increased bath temperature accelerates the hydrolysis kinetics, leading to better crystalline features. Over-heating the liquid/gas phase results in the decomposition of both the peroxide and urea to generate O2 and –NCO species, as well as –OH production might be lowered. Therefore, a high bath temperature is not beneficial for the crystalline behaviour. In addition, the top two XRD patterns, which belong to the duration of 3 h and 5 h at 150 °C, indicate that the reaction duration is also essential to the LDH crystallization. Consequently, we assigned 150 °C and 8 h as the optimal conditions in our subsequent studies.
 |
| Fig. 1 XRD patterns of LDH samples prepared at different bath temperatures and durations: 100 °C 8 h, 120 °C 8 h, 150 °C 8 h, 180 °C 8 h, 150 °C 3 h and 150 °C 5 h. | |
Similar to the report by Yan et al.83 herein, we utilized different peroxide–water mixers as the solvent (with the peroxide ratios of 10 wt%, 20 wt% and 30 wt%, and denoted the products as LDH-P10, LDH-P20, LDH-P30, respectively) to carry out the one-pot co-precipitation of Mg–Al-LDH in the same ambient-pressure reflux system. Fig. 2 displays the XRD patterns of the three samples, as well as the optimal sample prepared at 150 °C for 8 h (denoted by LDH-W) for comparison purposes. Moreover, under the same conditions, the introduction of peroxide led to considerable structural changes of LDH. As the peroxide concentration increased, the LDH feature peaks gradually diminished and then vanished as the H2O2 concentration reached 30 wt%. In general, the weakening of the peaks (003) and (006) should be an unambiguous clue for the degree of LDH delamination.76 In accordance with the SEM characterizations shown in Fig. 3a, uniform and round-shaped LDH sheets can be obtained in water solvent in the ambient-pressure reflux system, with a mean sheet size of 2 μm and a thickness of about 30 nm. The addition of peroxide resulted in a general decrease in the LDH size. At 10 wt% (Fig. 3b), the lateral sizes of the LDH-P10 nanosheets were around 0.5 μm, while the thickness of the sheets decreased to about one-third of LDH-W, implying that the LDH was partially delaminated. Once the peroxide concentration was adjusted to 20 wt% (Fig. 3c1), both the particle size and thickness shrank slightly, with the XRD features suggesting that the delamination degree was improved. The major difference between these two peroxide concentrations is that a lower peroxide addition led to a slight edge bending of the sheets, while a higher peroxide addition resulted in a severe distortion of the planar sheets. Part of the heavily curved fragments even cross-linked, and thus formed a petal-like morphology, as shown in Fig. 3c2. As we increased the peroxide ratio to 30 wt% (Fig. 3d), both the vanished XRD peaks and the amorphous SEM morphologies of the sample suggest that the crystalline structure could not be assembled.
 |
| Fig. 2 The XRD patterns of four resultant materials: (a) LDH-W, (b) LDH-P10, (c) LDH-P20 and (d) LDH-P30. | |
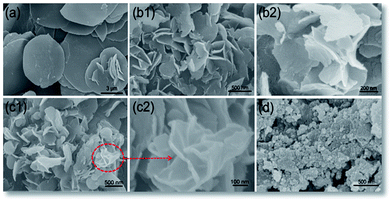 |
| Fig. 3 The SEM image of the samples: (a) LDH-W, (b) LDH-P10, (c) LDH-P20 and (d) LDH-P30. | |
As seen in Fig. 4 and Table 1, for the standard Mg–Al-LDH products, there are two distinct weight loss stages within the temperature ranges of 30–232.5 °C and 232.5–500 °C.87,88 The first stage (S1) corresponds to the evaporation of the physically adsorbed water molecules around the particle shell and the intercalated water molecules, while the second stage (S2) is ascribed to the thermal decomposition of carbonate groups and the conversion of hydroxide to oxide. As shown in Fig. 4, the weight loss behaviours of the four samples in both the two stages exhibit an apparent dependence with respect to the concentration of the peroxide. Compared with LDH-W, both the S1 and S2 weight losses decrease when the amount of H2O2 added is below 20 wt%, which leads to shrinking particle sizes and weakened LDH crystalline feature, as elucidated by the XRD and SEM results. Herein, we mentioned that for the 10 wt% and 20 wt% amounts of peroxide added, the TG curves vary only slightly. While for LDH-P30, the S1 weight loss is the highest due to the strong amorphous morphology and smallest particle sizes, which provide more sites for physisorbing water molecules. Such a non-crystalline feature implies that the abundance of intercalated carbonate groups is lower than in the other three cases, and the S2 weight loss should mainly be attributed to the hydroxide decomposition. Beyond 500 °C, the low weight loss of LDH-P30 is the highest due to its non-crystalline nature. For the other three samples, the weight loss of S3 belongs to the final conversion of hydroxides to oxides, along with the deconstruction of the sheet structures.
 |
| Fig. 4 TG curves of the Mg–Al–CO3 LDH samples: (a) LDH-W, (b) LDH-P10, (c) LDH-P20 and (d) LDH-P30. | |
Table 1 The weight loss of two stages for the four samples
Sample |
S1 (30–232.5 °C) |
S2 (232.5–500 °C) |
S3 (500–1000 °C) |
(a) LDH-W |
13.08% |
23.18% |
5.00% |
(b) LDH-P10 |
11.32% |
18.68% |
6.21% |
(c) LDH-P20 |
10.56% |
19.04% |
5.58% |
(d) LDH-P30 |
13.17% |
18.17% |
2.64% |
The FT-IR spectra shown in Fig. 5 suggest that the absorption at 3460 cm−1, which belongs to the –OH stretching of the intercalated and absorbed water molecules, was observed for all the four samples. Three peaks at 3080 cm−1, 1357 cm−1 and 691 cm−1, associated with the hydrogen bonding of the water–carbonate, symmetric stretching and translational mode of carbonate, respectively, are present except for LDH-P30, which is consistent with our analysis from the TG measurements. Due to the amorphous nature of LDH-P30, the translation modes of hydroxyl ions associated with trivalent aluminium peak at 774 cm−1 and 556 cm−1 also vanished. In addition, the absorption band at around 1389 cm−1 can be assigned to the characteristic diffraction peaks of the intercalated nitrate groups, which appear only in LDH-P30. Interestingly, a non-negligible peak at 984 cm−1, which can be assigned to the deformation modes of the –OH groups89 connected with Al3+, was observed for all the samples prepared with the addition of peroxide, but was invisible for the sample of LDH-W assembled in pure water solvent. This motivated us to speculate whether the curling or amorphous nature of the LDH-P series might be connected to this unexpected peak, and consequently led us to deduce the growing mechanism that governs the assembly of the LDH-P samples.
 |
| Fig. 5 FT-IR spectra of LDH samples: (a) LDH-W, (b) LDH-P10, (c) LDH-P20 and (d) LDH-P30. | |
From the periodic model of the Mg–Al-LDH in Fig. 6a, the –OH groups covering on the dual side of the plane all adopt an sp3 hybridization configuration. In a perfect LDH plane, each –OH connects three-foldedly with metal cations, and each cation attaches with three hydroxyl groups. At the Al3+ sites, extra carbonate groups should reside nearby to balance the charge. Such a configuration provides strong restriction to the –OH deformation and makes each single layer a flat plane. The appearance of the peak at 984 cm−1 suggests that the –OH deformation around Al3+ has been unlocked for LDH-P10, LDH-P20 and LDH-P30. In accordance with the curved or amorphous morphologies, this implies the existence of point defects in the LDH plane. Considering the fact that the hydrolysis of urea is the major source of the hydroxyl group, adding peroxide should lower –OH production, which would slow down the crystalline process to a certain degree. On the other hand, the decomposition of peroxide generates large amounts of oxygen gas, which should provide the driving force for the delamination.83 Herein, we mentioned that the peroxide decomposition and LDH co-precipitation in fact occur simultaneously, which implies that the delamination of large LDH particles might not be realistic.
 |
| Fig. 6 Schematic illustration of (a) perfect Mg–Al-LDH slab and (b) defective Mg–Al-LDH slab with the defect compensated by the carbonate group. The white, red, grey, green and pink atoms stand for the H, O, C, Mg and Al atoms, respectively. | |
Instead, we proposed that, when peroxide participates in the reaction, the growth of the LDH-P10, LDH-P20 and LDH-P30 samples should follow a concerted pathway, which combines peroxide decomposition and LDH co-precipitation. Under such a condition, the generated O2 would prevent the particles from being ripened. Once a certain amount of nuclei are formed, the growth then prefers to cumulate at the plane edge rather than aggregating with the adjacent particles. Within this locally gaseous environment, –OH defects have a certain probability to appear during co-precipitation, and the remaining charges are compensated by carbonate groups generated from the urea decomposition. Compared with a perfect Mg–Al-LDH slab (Fig. 6a), the chemically attached carbonate groups at the –OH defects are repulsive to the –OH groups nearby. Such repulsion forces the planar slab to curve in order to release the intrinsic stress, as illustrated by Fig. 6b. Due to their chemically bonded nature, the thermal stability of carbonate groups should be a little bit higher, as evidenced by the higher thermal decomposition temperatures of carbonate in the TG curves in Fig. 4. Simultaneously, the slight blue-shift of the carbonate feature peaks shown in Fig. 5 is also a clear clue for such a compensation form instead of the traditional intercalated carbonate form. Finally, if the peroxide is in excess, a high O2 production would heavily influence the co-precipitation and result in small cross-linked fragments or an amorphous state. In fact, these unusual morphologies of LDH products are mostly observed when using the urea method as the precipitator.65,80–82 We believe that the proposed concerted growth mechanism for explaining the curved morphology in our experiments can be also employed to elucidate those atypical growth phenomena.
Conclusions
We implemented a simple one-pot procedure for assembling Mg–Al–CO3 LDH through a co-precipitation method within a reflux system under atmospheric pressure. Using water as a dispersing medium, typical uniform LDH sheets can be obtained at the optimal bath temperature of 150 °C and at a duration of 8 h. Under such conditions, as peroxide participates in the process, the morphological features of the as-obtained LDH products are determined by the amount of peroxide added. Through XRD and SEM characterization, we noted that not only did the LDH particle size decreased with the increasing peroxide concentration, but the products display curved or even amorphous nature. The clues provided by TGA and FT-IR measurements imply that under the set condition, the assembling of Mg–Al–CO3 LDH may not adopt a typical crystallization–delamination process as reported previously. In fact, we deduced that a locally gaseous environment created by the O2 from the peroxide decomposition plays an essential role for generating the curved or amorphous morphologies. Besides the function that prevents the particles from being aggregated, –OH point defects also occur and the net charges are compensated by carbonate groups, leading to a defective configuration and presenting a curved sheet or amorphous state.
Acknowledgements
The study was supported by the Fundamental Research Founds for National University, China, the University of Geosciences (Wuhan) (“Tengfei” plan, Grant. CUG110501; Innovative Team, Grant CUG120115), and the Natural Science Foundation of Hubei (Grant 2013CFB413 and 2011CDA070).
References
- Q. Wang and D. O'Hare, Chem. Rev., 2012, 112, 4124 CrossRef CAS PubMed.
- D. G. Evans and R. C.T. Slade, Struct. Bonding, 2006, 119, 1 CAS.
- A. I. Khan, A. Ragavan, B. Fong, C. Markland, M. O'Brien, T. G. Dunbar, G. R. Williams and D. O'Hare, Chem. Rev., 2009, 48, 10196 CAS.
- A. I. Khan and D. O'Hare, J. Mater., 2002, 12, 3191 RSC.
- P. Benito, M. Herrero, F. M. Labajos and V. Rives, Appl. Clay Sci., 2010, 48, 218 CrossRef CAS.
- F. Cavani and F. Trifirò, Catal. Today, 1991, 11, 173 CrossRef CAS.
- J. He, M. Wei, B. Li, Y. Kang, D. G. Evans and X. Duan, Struct. Bonding, 2006, 119, 89 CrossRef CAS.
- G. R. Williams, A. I. Khan and D. O'Hare, Struct. Bonding, 2006, 119, 161 CrossRef CAS.
- R. Z. Ma and T. Sasaki, Adv. Mater., 2010, 22, 5082 CrossRef CAS PubMed.
- S. O'Leary, D. O'Hare and G. Seeley, Chem. Commun., 2002, 1506 RSC.
- L. Z. Qiu, W. Chen and B. J. Qu, Polym. Degrad. Stab., 2005, 87, 433 CrossRef CAS.
- L. Li, R. Z. Ma, Y. Ebina, N. Iyi and T. Sasaki, Chem. Mater., 2005, 17, 4386 CrossRef CAS.
- D. P. Yan, J. Lu, M. Wei, J. B. Han, J. Ma, F. Li, D. G. Evans and X. Duan, Angew. Chem., Int. Ed., 2009, 48, 3073 CrossRef CAS PubMed.
- E. P. Landman and W. W. Focke, S. Afr. J. Sci., 2006, 102, 581 CAS.
- Y. Z. Bao, L. F. Cong, Z. M. Huang and Z. X. Weng, J. Mater. Sci., 2008, 43, 390 CrossRef CAS.
- A. R. Wang, Y. Z. Bao, Z. X. Weng and Z. M. Huang, Chin. J. Chem. Eng., 2008, 16, 938 CrossRef CAS.
- D. Sudha and A. Ramasubbu, Asian J. Chem., 2013, 25, S120 CAS.
- F. Leroux and J. P. Besse, Chem. Mater., 2001, 13, 3507 CrossRef CAS.
- Q. Z. Yang, D. J. Sun, C. G. Zhang, X. J. Wang and W. A. Zhao, Langmuir, 2003, 19, 5570 CrossRef CAS.
- M. S. Cho, B. Shin, S. D. Choi, Y. Lee and K. G. Song, Electrochim. Acta., 2004, 50, 331 CrossRef CAS.
- J. Tronto, F. Leroux, M. Dubois, J. F. Borin, C. F. de Oliveira Graeff and J. B. Valim, J. Phys. Chem. Solids, 2008, 69, 1079 CrossRef CAS.
- R. Gao, M. J. Zhao, Y. Guan, X. Y. Fang, X. H. Lia and D. P Yan, J. Mater. Chem. C, 2014, 2, 9579 RSC.
- H. Y Ma, R. Gao, D. P. Yan, J. W. Zhao and M. Wei, J. Mater. Chem. C, 2013, 1, 4128 RSC.
- J. M. Oh, S. Y. Kwak and J. H. Choy, J. Phys. Chem. Solids, 2006, 67, 1028 CrossRef CAS.
- M. J. Masarudin, K. Yusoff, R. A. Rahim and M. Z. Hussein, Nanotechnology, 2009, 20, 045602 CrossRef PubMed.
- A. L. McKenzie, C. T. Fishel and R. J. Davis, J. Catal., 1992, 138, 547 CrossRef CAS.
- B. Sels, D. D. Vos, M. Buntinx, F. Pierard, A. K. de Mesmaeker and P. Jacobs, Nature, 1999, 400, 855 CrossRef CAS.
- B. Yang and Z. H. Yang, RSC Adv., 2013, 3, 12589 RSC.
- M. Sebastian, C. Nethravathi and M. Rajamathi, Mater. Res. Bull., 2013, 48, 2715 CrossRef CAS.
- J. Han, K. C. Roh, M. R. Jo and Y. M. Kang, Chem. Commun., 2013, 49, 7067 RSC.
- X. M. Fan, Z. H. Yang, R. J. Wen, B. Yang and W. Long, J. Power Sources, 2013, 224, 80 CrossRef CAS.
- A. B. Béléké, E. Higuchi, H. Inoue and M. Mizuhata, J. Power Sources, 2013, 225, 215 CrossRef.
- J. W. Zhao, J. Chen, S. Xu, M. F. Shao, D. P. Yan, M. Wei, D. G. Evans and X. Duan, J. Mater. Chem. A, 2013, 1, 8836 CAS.
- D. P. Yan, J. Lu, J. Ma, M. Wei, D. G. Evans and X. Duan, Angew. Chem., Int. Ed., 2011, 50, 720 CrossRef CAS PubMed.
- D. P. Yan, Y. B. Zhao, M. Wei, R. Z. Liang, J. Lu, D. G. Evans and X. Duan, RSC Adv., 2013, 3, 4303 RSC.
- A. M. Bashi, S. M. Haddawi and M. A. A. Mezaal, Arabian J. Sci. Eng., 2013, 38, 1663 CrossRef CAS.
- G. Hu, N. Wang, D. O'Hare and J. Davis, Chem. Commun., 2006, 287 RSC.
- G. Hu and D. O'Hare, J. Am. Chem. Soc., 2005, 127, 17808 CrossRef CAS PubMed.
- G. Hu, N. Wang, D. O'Hare and J. Davis, J. Mater. Chem., 2007, 17, 2257 RSC.
- C. J. Wang, Y. A. Wu, R. M. J. Jacobs, J. H. Warner, G. R. Williams and D. O'Hare, Chem. Mater., 2010, 23, 171 CrossRef.
- F. Bellezza, A. Cipiciani, U. Costantino, M. Nocchetti and T. Posati, Eur. J. Inorg. Chem., 2009, 18, 2603 CrossRef.
- S. N. Khadzhiev, K. M. Kadiev, G. P. Yampolskaya and M. K. Kadieva, Adv. Colloid Interface Sci., 2013, 197–198, 132 CrossRef CAS PubMed.
- J. Liang, Y. Y. Ma, H. Sun, W. Li and L. X. Wu, J. Colloid Interface Sci., 2013, 409, 80 CrossRef CAS PubMed.
- J. Stergar, G. Ferk, I. Ban, M. Drofenik, A. Hamler, M. Jagodič and D. Makovec, J. Alloys Compd., 2013, 576, 220 CrossRef CAS.
- M. Adachi-Pagano, C. Forano and J. P. Besse, Chem. Commun., 2000, 91 RSC.
- F. Leroux, M. Adachi-Pagano, M. Intissar, S. Chauviere, C. Forano and J. P. Besse, J. Mater. Chem., 2001, 11, 105 RSC.
- M. Singh, M. I. Ogden, G. M. Parkinson, C. E. Buckley and J. M. Connolly, J. Mater. Chem., 2004, 14, 871 RSC.
- F. Wypych, G. A. Bubniak, M. Halma and S. Nakagaki, J. Colloid Interface Sci., 2003, 264, 203 CrossRef CAS PubMed.
- T. Hibino, Chem. Mater., 2004, 16, 5482 CrossRef CAS.
- Z. P. Liu, R. Z. Ma, M. Osada, N. Iyi, Y. Ebina, K. Takada and T. Sasaki, J. Am. Chem. Soc., 2006, 128, 4872 CrossRef CAS PubMed.
- Z. P. Liu, R. Z. Ma, Y. Ebina, N. Iyi, K. Takada and T. Sasaki, Langmuir, 2006, 23, 861 CrossRef PubMed.
- J. B. Liang, R. Z. Ma, N. Iyi, Y. Ebina, K. Takada and T. Sasaki, Chem. Mater., 2009, 22, 371 CrossRef.
- Y. Zhao, W. D. Yang, Y. H. Xue, X. G. Wang and T. Lin, J. Mater. Chem., 2011, 21, 4869 RSC.
- R. L. Frost, J. Kristof, E. Horvath and J. Kloprogge, J. Phys. Chem. A, 1999, 103, 9654 CrossRef CAS.
- S. Letaief and C. Detellier, J. Mater. Chem., 2005, 15, 4734 RSC.
- M. Jobbágy and A. E. Regazzoni, J. Colloid Interface Sci., 2004, 275, 345 CrossRef PubMed.
- W. Y. Tseng, J. T. Lin, C. Y. Mou, S. Cheng, S. B. Liu, P. P. Chu and H. W. Liu, J. Am. Chem. Soc., 1996, 118, 4411 CrossRef CAS.
- V. V. Naik, T. N. Ramesh and S. Vasudevan, J. Phys. Chem. Lett., 2011, 2, 1193 CrossRef CAS PubMed.
- J. Gaume, S. Therias, F. Leroux, A. Rivaton and J. L. Gardette, J. Appl. Polym. Sci., 2013, 129, 1345 CrossRef CAS.
- X. H. Liu, R. Z. Ma, Y. Bando and T. Sasaki, Angew. Chem., Int. Ed., 2010, 49, 8253 CrossRef CAS PubMed.
- R. Z. Ma, Z. P. Liu, K. Takada, N. Iyi, Y. Bando and T. Sasaki, J. Am. Chem. Soc., 2007, 129, 5257 CrossRef CAS PubMed.
- Q. L. Wu, A. Olafsen, O. B. Vistad, J. Roots and P. Norby, J. Mater. Chem., 2005, 15, 4695 RSC.
- M. Q. Zhao, Q. Zhang, J. Q. Huang and F. Wei, Adv. Funct. Mater., 2012, 22, 675 CrossRef CAS.
- L. Wang, Z. H. Dong, Z. G. Wang, F. X. Zhang and J. Jin, Adv. Funct. Mater., 2013, 23, 2758 CrossRef CAS.
- X. H. Liu, R. Z. Ma, Y. Bando and T. Sasaki, Adv. Mater., 2012, 24, 2148 CrossRef CAS PubMed.
- A. Di Fronzo, C. Pirola, A. Comazzi, F. Galli, C. L. Bianchi, A. Di Michele, R. Vivani, M. Nocchetti, M. Bastianini and D. C. Boffito, Fuel, 2014, 119, 62 CrossRef CAS.
- J. B. Wei, J. Wang, Y. C. Song, Z. S. Li, Z. Gao, T. Mann and M. L. Zhang, J. Solid State Chem., 2012, 196, 175 CrossRef CAS.
- Z. P. Xu, L. Li, C. Y. Cheng, R. G. Ding and C. H. Zhou, Appl. Clay Sci., 2013, 74, 102 CrossRef CAS.
- Y. Zhou, Y. Kuang, W. Y. Li, Z. L. Chen, M. Megharaj and R. Naidu, Chem. Eng. J., 2013, 223, 68 CrossRef CAS.
- B. Li and J. He, J. Phys. Chem. C, 2008, 112, 10909 CAS.
- M. Jobbágy and N. Iyi, J. Phys. Chem. C, 2010, 114, 18153 Search PubMed.
- T. Gomez, E. Florez, J. A. Rodriguez and F. Illas, J. Phys. Chem. C, 2011, 115, 11666 CAS.
- F. T. Zhang, X. Long, D. W. Zhang, Y. L. Sun, Y. L. Zhou, Y. R. Ma, L. M. Qi and X. X. Zhang, Sens. Actuators, B, 2014, 192, 150 CrossRef CAS.
- R. K. Sahu, B. S. Mohanta and N. N. Das, J. Phys. Chem. Solids, 2013, 74, 1263 CrossRef CAS.
- S. J. Xia, F. X. Liu, Z. M. Ni, J. L. Xue and P. P. Qian, J. Colloid Interface Sci., 2013, 405, 195 CrossRef CAS PubMed.
- Q. F. Wang, X. F. Wang, B. Liu, G. Yu, X. J. Hou, D. Chen and G. Z. Shen, J. Mater. Chem. A, 2013, 1, 2468 CAS.
- X. Sun, G. K. Wang, H. T. Sun, F. Y. Lu, M. P. Yu and J. Lian, J. Power Sources, 2013, 238, 150 CrossRef CAS.
- L. H. Su, Z. W. Song, L. H. Lu and G. L. Pang, Mater. Res. Bull., 2013, 8, 3636 CrossRef.
- M. Hu, X. D. Ji, L. X. Lei and X. W. Lu, Electrochim. Acta, 2013, 105, 261 CrossRef CAS.
- M. Adachi-Pagano, C. Forano and J. P. Besse, J. Mater. Chem., 2003, 13, 1988 RSC.
- J. B. Wei, Z. Gao, Y. C. Song, W. L. Yang, J. Wang, Z. S. Li, T. Mann, M. L. Zhang and L. H. Liu, Mater. Chem. Phys., 2013, 139, 395 CrossRef CAS.
- B. Li, J. He, D. G. Evans and X. Duan, J. Phys. Chem. Solids, 2006, 67, 1067 CrossRef CAS.
- Y. X. Yan, Q. Liu, J. Wang, J. B. Wei, Z. Gao, T. Mann, Z. S. Li, Y. He, M. L. Zhang and L. H. Liu, J. Colloid Interface Sci., 2012, 371, 15 CrossRef CAS PubMed.
- D. P. Yan, J. Lu, M. Wei, J. Ma, D. G. Evans and X. Duan, Phys. Chem. Chem. Phys., 2009, 11, 9200 RSC.
- D. P. Yan, J. Lu, M. Wei, J. Ma, D. G. Evans and X. Duan, Phys. Chem. Chem. Phys., 2010, 12, 15085 RSC.
- X. B. Wang, Z. M. Bai, D. Zhao, Y. P. Chai, M. Guo and J. Y. Zhang, Mater. Res. Bull., 2013, 48, 1228 CrossRef CAS.
- M. Dixit, M. Mishra, P. A. Joshi and D. O. Shah, J. Ind. Eng. Chem., 2013, 19, 458 CrossRef CAS.
- X. Y. Xu, D. Q. Li, J. Q. Song, Y. J. Lin, Z. Lv, M. Wei and X. Duan, Particuology, 2010, 8, 198 CrossRef CAS.
- T. Zhang, Q. R. Li, H. Y. Xiao, H. X. Lu and Y. M. Zhou, Ind. Eng. Chem. Res., 2012, 51, 11490 CrossRef CAS.
|
This journal is © The Royal Society of Chemistry 2015 |
Click here to see how this site uses Cookies. View our privacy policy here.