DOI:
10.1039/C4RA17025C
(Paper)
RSC Adv., 2015,
5, 23094-23100
Pickering emulsion polymerized smart magnetic poly(methyl methacrylate)/Fe2O3 composite particles and their stimulus-response†
Received
25th December 2014
, Accepted 24th February 2015
First published on 24th February 2015
Abstract
Smart polymer/inorganic composite magnetic particles were synthesized by Pickering emulsion polymerization using magnetic iron oxide (Fe2O3) particles as a solid stabilizer. The products were characterized by scanning electron microscopy and transmission electron microscopy, which revealed submicron-sized spherical PMMA covered with Fe2O3 nanoparticles. The thermal properties of the pristine Fe2O3 and PMMA/Fe2O3 composite particles were examined by thermogravimetric analysis. Fourier transform infrared spectroscopy was used to characterize the chemical structure of the samples. The magnetic properties of the products were observed by vibrating sample magnetometry. The rheology of the magnetorheological (MR) fluid of the PMMA/Fe2O3 particles dispersed in a non-magnetic medium fluid was examined using a rotational parallel disk rheometer under an applied magnetic field. Despite the lower magnetic properties compared to those of pristine Fe2O3, the PMMA/Fe2O3 composite particle based MR fluid showed typical MR characteristics with potential dispersion stability regarding the particle density.
1. Introduction
Magnetorheological (MR) fluids are dispersions of magnetic particles in non-magnetic medium liquids, exhibiting a remarkable change in their flow and rheological properties, transforming from a liquid-like to solid-like phase under an external magnetic field.1–6 This performance enables a range of applications of MR fluids in engineering fields, such as engine mounts, clutches, brakes, and ultrafine polishing,7,8 along with MR elastomers.9 On the other hand, conventional MR fluids with soft-magnetic carbonyl iron (CI) particles often have limited engineering applications because of the serious sedimentation problem.10 Several attempts have been made to improve this density mismatch between the CI particle and non-magnetic medium fluids, including coating the magnetic particles with polymer or adding sub-micron additives.11–14 Compared to modifying CI particles, other magnetic species, magnetite particles,15,16 and cobalt and nickel compounds17–20 have attracted interest because of the much lower density and good magnetic behavior. In particular, magnetic nanoparticles of different types of iron oxide either magnetite (Fe3O4) or maghemite (Fe2O3) have been used as MR materials.21
In this study, magnetic composite particles consisting of PMMA spheres coated with Fe2O3 magnetic nanoparticles with a much lower density than CI particles were prepared. The Fe2O3 particles had an extremely small size (≤50 nm) and high surface area to volume ratio.22 Fe2O3 has attracted considerable attention because of its wide abundance, low cost and non-toxicity.23–25 In addition, its superparamagnetic properties can be adopted to many industrial applications, such as magnetic resonance imaging, hyperthermia and MR fluids.26
On the other hand, polymer/inorganic magnetic hybrid particles have been recently synthesized by a Pickering emulsion polymerization method using inorganic particles as a solid stabilizer. This method does not require conventional organic surfactants because solid particles are being used as a stabilizer instead.21,27–29 Note that ordinary emulsion polymerization uses large amounts of organic surfactants as an emulsifier, which is difficult to eliminate or recycle after polymerization.30 Inorganic solid particles are adsorbed stably at the liquid–liquid interface of aqueous and organic liquids, forming oil/water or water/oil emulsions.31–33 The wettability of particulate stabilizers to the oil/water interface determines the stability and type of emulsions.34,35 Because this technique does not require extra organic surfactants, it has many advantages, such as lower toxicity, reduced foaming problem and simple process using environmentally benign green methods.36,37 Therefore, considerable effort has been made to fabricate core–shell structured polymer particles with solid particles not only as a solid surfactant but also as a functionality-induced material. Hasell et al.38 and Xu et al.39 synthesized Fe3O4 nanoparticle-armored PMMA spheres and Fe3O4/PS particles, respectively, using the Pickering emulsion method. Furthermore, Wei et al.31 reported the preparation of CH2Cl2 emulsion droplets with maghemite (Fe2O3) nanoparticles by dissolving poly(lactic-co-glycolic acid) in CH2Cl2, and obtained Fe2O3 coated PLGA by evaporating the oil from the CH2Cl2 solution of PLGA-in-water emulsions. Note that in addition to magnetic particles, a wide range of solid particles, such as silica, clay, TiO2, and graphene oxide, have been used to stabilize emulsion droplets and fabricate composite particles with Pickering emulsion polymerization. Yin et al.40 fabricated polystyrene (PS)/SiO2 particles by Pickering emulsion polymerization using modified SiO2 as a solid stabilizer.
Core–shell particles were obtained using oil-soluble initiator, azobisisobutyronitrile (AIBN), because polymerization in monomer droplets was dominant. Recently, Yin et al.41 fabricated PS/GO nanocomposite particles using hydrophilic GO nanosheets as a stabilizer.
PMMA/Fe2O3 magnetic composite particles were synthesized by Pickering emulsion polymerization by applying Fe2O3 nanoparticles (<50 nm) as a solid stabilizer, in which the Fe2O3 particles stabilize the MMA monomer droplets in the aqueous phase of an oil in water emulsion. The MR properties of the synthesized PMMA/Fe2O3 particles were measured over a range of magnetic fields. Compared to the conventional complicated processes of obtaining magnetic composite particles, this novel method can be conducted easily. Scheme 1 presents the mechanism of preparing PMMA/Fe2O3 nanoparticles by Pickering emulsion polymerization.
 |
| Scheme 1 Schematic diagram of an experimental route to synthesize PMMA/Fe2O3 particles. | |
2. Experimental
2.1 Materials
Methyl methacrylate (MMA) (99.8% purity, Duksan Pure Chem., Korea) was used as a monomer without further purification. AIBN (98% purity, Junsei Chemical Co., Japan) was used after recrystallization as an oil-soluble initiator, whereas 2,2′-azobis(2-methylpropionamidine) dihydrochloride (AIBA) (97% purity, Sigma-Aldrich, USA) was used as a water-soluble initiator. Iron oxide nanoparticles (Fe2O3) (≤50 nm) were purchased from Sigma-Aldrich. Methanol and distilled water were used as a solvent throughout the experiments.
2.2 Fabrication of PMMA/iron oxide composite particle
5 g of Fe2O3 nanoparticles were dispersed in 200 mL of distilled water, and then sonicated for 30 min. 0.1 g of AIBN (or AIBA) was mixed with 9 g of the MMA monomer to form an oil phase. Subsequently, the oil phase portion was poured into the aqueous Fe2O3 dispersion, and the mixture was then treated with a homogenizer until the oil phase was well dispersed in the water phase, forming emulsified droplets. The mixture was poured into a 500 mL three-neck flask and deoxygenated by bubbling with nitrogen gas for 30 min. The emulsion droplets of MMA coated with Fe2O3 nanoparticles were polymerized at 70 °C for 15 h. After the reaction, the final dispersion was washed with methanol and water sequentially by a centrifugation process to remove the residual monomer, initiator and Fe2O3 nanoparticles. The obtained final product was dried in a freeze-dryer for 3 days.
2.3 Preparation of MR fluid
The synthesized magnetic PMMA/Fe2O3 composite particles were dispersed in silicone oil (100 cSt, KF-96, Shin-Etsu, Japan) with a 10% volume fraction. The MR fluid was sonicated for 30 min to disperse the particles.
2.4 Characterization
The morphology and size of the synthesized particles were examined by scanning electron microscopy (SEM, Hitachi S-4300) and transmission electron microscopy (TEM, Philips CM200). Fourier transform infrared (FT-IR, Bruker VERTEX 80V) spectroscopy was determined in transmission mode using a potassium bromide pellet as a reference to check the chemical structure of the samples. Thermogravimetric analysis (TGA, STA 409 PC) was performed under a nitrogen gas atmosphere at a heating rate of 10 °C min−1, and the samples were heated from room temperature to 1000 °C. Vibrating sample magnetometry (VSM, DMS 1660) was used to observe the magnetic properties of the samples at 300 K. The rheological properties of the MR fluids were measured using a rotational rheometer (Physica MCR 300, Stuttgart, Germany) equipped with a magnetic field supply device and a 20 mm parallel plate measuring system.
3. Results and discussion
Fig. 1 presents TEM images of the synthesized PMMA/Fe2O3 composite particles, showing the products synthesized with both water-soluble initiator (AIBA) and oil-soluble initiator (AIBN). In Fig. 1, the smaller and black Fe2O3 nanoparticles were observed to be located around the PMMA particles. When AIBN was used as an initiator, the PMMA spheres were surrounded by Fe2O3 nanoparticles (Fig. 1(b)). In contrast, in the case of the AIBA, the Fe2O3 particles were just mixed with polymer and the shape of PMMA was not uniform (Fig. 1(a)). These results suggest that the type of initiator affects the final products. According to Ma and Li,42 although the initiator is hydrophobic, it can diffuse into the aqueous phase slightly and react with the monomer dissolved in the aqueous phase. After growth, the polymer reaches a critical length, and is then insoluble in water. The polymer then precipitates to form secondary nuclei, which capture radicals and absorb monomers from the aqueous phase to polymerize. Therefore, polymerization occurs inside both the monomer droplets and secondary nuclei. In the present study, however, the MMA monomer and AIBN initiator could be dissolved in the water phase because the Fe2O3 particles surround the monomer droplets densely. Accordingly, it is difficult to reach a critical length and form secondary nuclei for the growing polymer in the aqueous phase.37 As a result, when an oil-soluble initiator, AIBN, was used (Fig. 1(b)), polymerization in the monomer droplets was dominant and the products were spherical. In case of the water-soluble initiator of AIBA, however, the concentration of monomer that diffused into the water was quite low because of the high concentration of Fe2O3 particles, which prevent their diffusion. Therefore, it is difficult to encounter the initiator in the water phase, which means that the reaction would occur at the interface between the Fe2O3 particle-stabilized monomer droplets and the aqueous phase.43 Therefore, the PMMA with low conversion was obtained and its shape was not regular, as demonstrated in Fig. 1(a). On the other hand, TEM image of pure Fe2O3 nanoparticles used can be found from Fig. S1.†
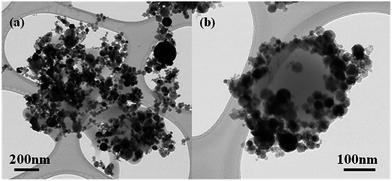 |
| Fig. 1 TEM images of PMMA/Fe2O3 composites using AIBA (a) and AIBN (b) respectively. | |
Fig. 2 shows the surface morphology of the PMMA/Fe2O3 composite particles synthesized using the AIBN initiator, in which the PMMA particles with about 250 nm in size were surrounded by the small Fe2O3 nanoparticles with a size of about 20 nm. The spherical composite particles have a bumpy surface and their mean size was 250–300 nm. Once the initiator was added, polymerization started and the Fe2O3 nanoparticles stabilizing the MMA droplets were adsorbed at the surface of the PMMA particles. More detailed information on particle size distribution of both pristine Fe2O3 nanoparticles and modified PMMA/Fe2O3 composite particles measured from a dynamic light scattering apparatus can be found from Fig. S2.†
 |
| Fig. 2 SEM image of PMMA/Fe2O3 composite particles. | |
The chemical compositions of the pristine Fe2O3 and modified PMMA/Fe2O3 were characterized by FT-IR spectroscopy, as shown in Fig. 3. The characteristic peak at 3400 cm−1 indicated the presence of hydroxyl groups on the surface of the Fe2O3 nanoparticles, whereas a new characteristic peak at 1450 cm−1 can be assigned to the C–H bending peak. The C–O asymmetric stretching of the ester group was detected at 1148 cm−1 and 1265 cm−1. In addition, a strong peak at 1730 cm−1, which was assigned to the stretching vibration of the C
O group, indicated the existence of PMMA. Consequently, these peaks suggest that the magnetic PMMA/Fe2O3 hybrid composites were fabricated successfully.
 |
| Fig. 3 FT-IR spectra of pristine Fe2O3 nanoparticles and PMMA/Fe2O3 composite particles. | |
Fig. 4 presents the TGA curves of both Fe2O3 and PMMA/Fe2O3 composites that exhibit the residual weight percentage versus temperature. The Fe2O3 magnetic particles are barely decomposed over a wide temperature range, whereas the PMMA/Fe2O3 hybrid composites begin to decompose sharply at ∼250 °C. Approximately 40% weight loss of the composite particles observed between 250–400 °C was attributed mainly to the decomposition of PMMA. From the result, the mass fraction of PMMA core was confirmed to be approximately 40 wt% which is quite low compared to conventional Pickering system.44
 |
| Fig. 4 TGA curves of the Fe2O3 and PMMA/Fe2O3 composite particles. | |
Fig. 5 shows the magnetic hysteresis loops of both Fe2O3 and PMMA/Fe2O3 composite particles with almost no hysteresis, indicating that both particles are superparamagnetic materials for various potential applications. The saturation magnetization values of Fe2O3 and PMMA/Fe2O3 were 40 and 19 emu g−1, respectively, indicating that the introduction of organic PMMA reduces the maximum saturation magnetization, being attributed to diluting contribution of non-magnetic PMMA in sampling volume.45 More specifically, the Ms of the composite particles was obtained by simply devising M for the mass of both the magnetic part (Fe2O3) and non-magnetic part (PMMA) while the Ms of the Fe2O3 nanoparticles took into account only the magnetic mass (Fe2O3). However, this value could be explained with the mass fraction of the Fe2O3 nanoparticles in the composites based on the TGA data. The mass fraction of Fe2O3 nanoparticles from the TGA was about 60%, suggesting that the Ms of PMMA/Fe2O3 composite particles could be about 24 emu g−1 while we observed 19 emu g−1 from the VSM. The difference might come from not only potential experimental measurement error but also extra Fe2O3 nanoparticles not-involved for the Pickering emulsion polymerization so that the actual Fe2O3 nanoparticle content on the sampling process for both TGA and VSM measurements could be slightly different. On the other hand, it can be also noted that while Fe2O3 nanoparticles themselves could not provide sufficient MR characteristics due to their too small size mainly being applied only for ferrofluid application,46 the PMMA/Fe2O3 composite particles despite their reduced Ms demonstrated sufficient MR behavior due to their enlarged particle size.
 |
| Fig. 5 VSM data of pristine Fe2O3 and PMMA/Fe2O3 composites. | |
Furthermore, the Ms of magnetic particles is a significant factor for their MR application because it is related to the yield stress as follows;47
where
μ0 is the permeability of free space,
ϕ is the volume fraction,
Ms is the magnetic saturation of the material, and
H is the strength of the applied magnetic field.
The MR fluid with a 10% volume fraction of the synthesized composite particles was prepared by dispersing the particles in silicone oil. The MR characteristics of the MR fluids were observed using a rotational rheometer in a parallel plate geometry equipped with a magnetic field supplier. Fig. 6 and 7 present the shear stress (Fig. 6) and shear viscosity (Fig. 7) as a function of the shear rate of the MR fluids with and without a magnetic field. The MR fluids showed an increase in shear stress and shear viscosity with increasing magnetic field strength. In the absence of magnetic fields, the MR fluid based on PMMA/Fe2O3 particles exhibited typical Newtonian behavior in that the shear stress increases linearly with increasing shear rate (Fig. 6). Under an applied external magnetic field, the MR fluids exhibited plateau behavior showing stable shear stress with the change in shear rate. This might be caused by magnetic field-induced chain structures of dispersed particulates. This suggests that the rigid chain-like structures of particles in an applied magnetic field are broken and reconstructed repeatedly.48 At a high shear rate, however, the shear stress increased gradually because the rate of breaks of the chain structures became faster than that of the rearrangement.
 |
| Fig. 6 Shear stress versus shear rate curves of PMMA/Fe2O3 particle-based MR fluid with various magnetic field strengths. The dotted lines are generated from the CCJ models with an optimal parameter. | |
 |
| Fig. 7 Shear viscosity versus shear rate of PMMA/Fe2O3 particle-based MR fluid with various magnetic field strengths. | |
The Bingham fluid model, shown in eqn (2), is the simplest model to fit the shear rate versus shear stress curve with two parameters derived from the yield stress, τ0, and the Newtonian viscosity, η0. This model has been widely adopted for rheological suspensions, but it is impossible to indicate an unusual decrease in shear stress in the low shear rate region (Fig. 6).
|
τ = τ0 + η
| (2) |
Therefore, another model called the Cho–Choi–Jhon (CCJ) model was adopted to describe the unconventional shear stress behavior.49 The CCJ model (eqn (3)) provides a better fit of the PMMA/Fe2O3-based MR fluids with six parameters.
|
 | (3) |
where
τ0 is the yield stress defined as the extrapolated stress from the low shear rate region, and the exponent
α is related to the decrease in stress.
η0 is the viscosity at a high shear rate and is interpreted as the viscosity in the absence of a magnetic field.
t2 and
t3 are both time constants, and
β has the range, 0 <
β ≤ 1.
Table 1 lists the yield stress and the optimal parameters for this model.
Table 1 Optimal parameters in CCJ model equation obtained from the flow curves of PMMA/Fe2O3 particle based MR fluid
|
Magnetic field strength (kA m−1) |
86 |
171 |
257 |
343 |
τ0 |
45 |
102 |
121 |
139 |
t2 |
4 |
3 |
1 |
4.5 |
α |
0.05 |
0.15 |
0.25 |
0.55 |
η∞ |
0.66 |
1.18 |
1.38 |
1.49 |
t3 |
0.006 |
0.015 |
0.015 |
0.011 |
β |
0.8 |
0.9 |
0.88 |
0.9 |
In addition to the flow curves, the dynamic yield stress was re-plotted as a function of the magnetic field strength (H) on a log–log scale, as shown in Fig. 8. According to previous reports, the dependency of the dynamic yield stress on the magnetic field strength can be represented using the following power law:
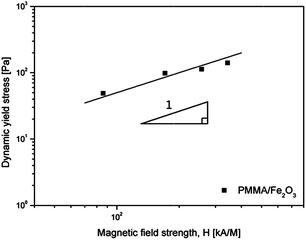 |
| Fig. 8 Dynamic yield stress as a function of the magnetic field strength for the PMMA/Fe2O3-based MR fluid. | |
The value of m is varies empirically from 1.0 to 2.0 depending on the different MR materials.50,51 On a logarithmic graph, the experimental points of τy could be placed on a straight line with a slope of 1.0.
An oscillatory test was also accomplished under different magnetic field strengths to examine the viscoelastic behavior of the MR fluids. Fig. 9 presents the amplitude sweep tested at a constant frequency of 1.0 Hz at various strains ranging from 0.001% to 10%. Based on the amplitude sweep, storage modulus (G′) and loss modulus (G′′) increase under an applied magnetic field because of the formation of a chain structure. Furthermore, G′ is much higher than G′′, which suggests that the MR fluids exhibit more solid-like under an applied magnetic field. The starting G′′ value is larger than G′, which means that liquid-like behavior will be observed over a high range of strain.7,52 Therefore, a strain amplitude of 0.005% was selected to ensure that there was no significant change in structure and the frequency sweep was carried out.
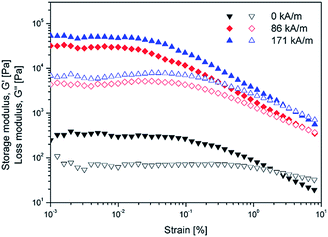 |
| Fig. 9 Amplitude sweep of PMMA/Fe2O3 particle based MR fluids under different magnetic field strength. Storage modulus: G′ (closed), loss modulus: G′′ (open). | |
Based on the selected strain of 0.005%, the frequency sweep was investigated at different magnetic field strengths. Fig. 10 presents the behavior of G′ and G′′ measured over the frequency range 0.1 to 100 Hz. G′ and G′′ increase slightly with increasing frequency meaning that the interaction between the particles is not strong enough to be retained under a high frequency. On the other hand, both G′ and G′′ show a constant value over a wide frequency range under an applied magnetic field. This suggests that the sample has a very strong solid-like structure when they are under a strong magnetic field.
 |
| Fig. 10 Frequency sweep of PMMA/Fe2O3 particle-based MR fluids. Storage modulus: G′ (closed), loss modulus: G′′ (open). | |
4. Conclusions
The PMMA/Fe2O3 magnetic particles were fabricated successfully by Pickering emulsion polymerization. This method enabled easier synthesis without organic surfactants. After polymerization, the PMMA spheres covered with Fe2O3 nanoparticles were obtained. This study was conducted with different types of initiator, and the results showed that the type initiator would affect the shape of the final products. When the oil-soluble initiator, AIBN, was used, polymerization in the oil phase was dominant, which allowed the polymer spheres to be covered with magnetic particles. SEM and TEM revealed the shape and size of the PMMA/Fe2O3 composite particles, and confirmed that the PMMA core was covered with Fe2O3 nanoparticles. The existence of PMMA was analyzed by FT-IR and TGA. VSM suggested that the maximum saturation magnetization decreased from 40 emu g−1 to 19 emu g−1 due to PMMA. The rheological properties of the PMMA/Fe2O3 particle-based MR fluid were examined by static and dynamic tests under a range of magnetic field strengths. Although the magnetic properties of the PMMA/Fe2O3 particles were lower than that of pristine Fe2O3, their MR fluid showed typical MR fluid characteristics with a yield stress under applied magnetic field strengths. The density of the PMMA/Fe2O3 particles was lower than that of the pristine Fe2O3 particles, suggesting better dispersion stability of MR fluids.
Acknowledgements
This study was supported by Ministry of Trade, Industry & Energy, Korea through Daeheung RNT (# 10047791).
Notes and references
-
(a) L. J. Felicia and J. Philip, Langmuir, 2013, 29, 110 CrossRef CAS PubMed;
(b) M. Machovsky, M. Mrlik, T. Plachy, I. Kuritka, V. Pavlinek, Z. Kozakova and T. Kitano, RSC Adv., 2015, 5, 19213 RSC.
-
(a) B. J. Park, F. F. Fang and H. J. Choi, Soft Matter, 2010, 6, 5246 RSC;
(b) I. Bica, E. M. Anitas, M. Bunoiu, B. Vatzulik and I. Juganaru, J. Ind. Eng. Chem., 2014, 20, 3994 CrossRef CAS PubMed.
-
(a) M. T. Lopez-Lopez, P. Kuzhir, G. Bossis and P. Mingalyov, Rheol. Acta, 2008, 47, 787 CrossRef CAS;
(b) A. J. F. Bombard, M. Knobel and M. R. Alcantara, Int. J. Mod. Phys. B, 2007, 21, 4858 CrossRef CAS.
- R. E. Moctezuma, F. Donado and J. L. Arauz-Lara, Phys. Rev. E: Stat., Nonlinear, Soft Matter Phys., 2013, 88, 032305 CrossRef CAS.
-
(a) H. An, S. J. Picken and E. Mendes, Polymer, 2012, 53, 4164 CrossRef CAS PubMed;
(b) J. L. Goncalves, A. J. F. Bombard, D. A. W. Soares and G. B. Alcantara, Energy Fuels, 2010, 24, 3144 CrossRef CAS.
- I. Bica, Y. D. Liu and H. J. Choi, J. Ind. Eng. Chem., 2013, 19, 394 CrossRef CAS PubMed.
- R. Shen, S. N. Shafrir, C. Miao, M. Wang, J. C. Lambropoulos, S. D. Jacobs and H. Yang, J. Colloid Interface Sci., 2010, 342, 49 CrossRef CAS PubMed.
- T. F. Tian, W. H. Li and Y. M. Deng, Smart Mater. Struct., 2011, 20, 025022 CrossRef.
- I. Bica, E. M. Anitas, L. M. E. Averis and M. Bunoiu, J. Ind. Eng. Chem., 2015, 21, 1323 CrossRef CAS PubMed.
- W. Q. Jiang, H. Zhu, C. Y. Guo, J. F. Li, Q. Xue, J. H. Feng and X. L. Gong, Polym. Int., 2010, 59, 879 CrossRef CAS.
- X. M. Quan, Y. D. Liu, W. S. Ahn and H. J. Choi, IEEE Trans. Magn., 2013, 49, 3410 CrossRef CAS.
- M. Mrlik, M. Ilcikova, V. Pavlinek, J. Mosnacek, P. Peer and P. Filip, J. Colloid Interface Sci., 2013, 396, 146 CrossRef CAS PubMed.
- F. F. Fang, Y. D. Liu, H. J. Choi and Y. Seo, ACS Appl. Mater. Interfaces, 2011, 3, 3487 CAS.
- N. M. Wereley, A. Chaudhuri, J. H. Yoo, S. John, S. Kotha, A. Suggs, R. Radhakrishnan, B. J. Love and T. S. Sudarshan, J. Intell. Mater. Syst. Struct., 2006, 17, 393 CrossRef CAS PubMed.
- L. J. Felicia and J. Philip, Phys. Rev. E: Stat., Nonlinear, Soft Matter Phys., 2014, 89, 022310 CrossRef.
- H. T. Pu, F. J. Jiang and Z. L. Yang, Mater. Chem. Phys., 2006, 100, 10 CrossRef CAS PubMed.
- F. Vereda, J. de Vicente and R. Hidalgo-Alvarez, J. Mater. Res., 2008, 23, 1764 CrossRef CAS.
- M. Ashtiani, S. H. Hashemabadi and A. Ghaffari, J. Magn. Magn. Mater., 2015, 374, 716 CrossRef CAS PubMed.
- M. Molazemi, H. Shokrollahi and B. Hashemi, J. Magn. Magn. Mater., 2013, 346, 107 CrossRef CAS PubMed.
- P. P. Phule, M. P. Mihalcin and S. Genc, J. Mater. Res., 1999, 14, 3037 CrossRef CAS.
-
(a) S. Fujii, Y. Eguchi and Y. Nakamura, RSC Adv., 2014, 4, 32534 RSC;
(b) Y. J. Kim, Y. D. Liu, Y. Seo and H. J. Choi, Langmuir, 2013, 29, 4959 CrossRef CAS PubMed.
- G. Liu, J. H. Gao, H. Ai and X. Y. Chen, Small, 2013, 9, 1533 CrossRef CAS PubMed.
- E. Amstad, M. Textor and E. Reimhult, Nanoscale, 2011, 3, 2819 RSC.
- U. T. Lam, R. Mammucari, K. Suzuki and N. R. Foster, Ind. Eng. Chem. Res., 2008, 47, 599 CrossRef CAS.
- M. Cavas, R. K. Gupta, A. A. Al-Ghamdi, Z. H. Gafer, F. El-Tantawy and F. Yakuphanoglu, Mater. Lett., 2013, 105, 106 CrossRef CAS PubMed.
- A. Schrade, K. Landfester and U. Ziener, Chem. Soc. Rev., 2013, 42, 6823 RSC.
-
(a) Y. J. He, Mater. Lett., 2005, 59, 2133 CrossRef CAS PubMed;
(b) L. Tian, B. Zhang, W. Li, X. Li, X. Fan, X. Jia, H. Zhang and Q. Zhang, RSC Adv., 2014, 4, 27152 RSC.
-
(a) Y. Y. Liu, X. Q. Chen, R. H. Wang and J. H. Xin, Mater. Lett., 2006, 60, 3731 CrossRef CAS PubMed;
(b) S. H. Piao, S. H. Kwon, W. L. Zhang and H. J. Choi, Soft Matter, 2015, 11, 646 RSC.
-
(a) J. Frelichowska, M. A. Bolzinger, J. P. Valour, H. Mouaziz, J. Pelletier and Y. Chevalier, Int. J. Pharm., 2009, 368, 7 CrossRef CAS PubMed;
(b) H. X. Liu, C. Y. Wang, Q. X. Gao, X. X. Liu and Z. Tong, Acta Biomater., 2010, 6, 275 CrossRef CAS PubMed.
- D. Z. Yin, X. Du, H. Liu, Q. Y. Zhang and L. Ma, Colloids Surf., A, 2012, 414, 289 CrossRef CAS PubMed.
- Z. J. Wei, C. Y. Wang, S. W. Zou, H. Liu and Z. Tong, Colloids Surf., A, 2011, 392, 116 CrossRef CAS PubMed.
- R. F. A. Teixeira, H. S. McKenzie, A. A. Boyd and S. A. F. Bon, Macromolecules, 2011, 44, 7415 CrossRef CAS.
- C. Y. Wang, C. J. Zhang, Y. Li, Y. H. Chen and Z. Tong, React. Funct. Polym., 2009, 69, 750 CrossRef CAS PubMed.
- B. P. Binks and J. H. Clint, Langmuir, 2002, 18, 1270 CrossRef CAS.
- M. Andresen and P. Stenius, J. Dispersion Sci. Technol., 2007, 28, 837 CrossRef CAS.
- F. W. Wang, H. R. Liu, J. D. Zhang, X. T. Zhou and X. Y. Zhang, J. Polym. Sci., Part A: Polym. Chem., 2012, 50, 4599 CrossRef CAS.
- K. Zhang, W. Wu, H. Meng, K. Guo and J. F. Chen, Powder Technol., 2009, 190, 393 CrossRef CAS PubMed.
- T. Hasell, J. X. Yang, W. X. Wang, J. Li, P. D. Brown, M. Poliakoff, E. Lester and S. M. Howdle, J. Mater. Chem., 2007, 17, 4382 RSC.
- Z. Z. Xu, A. Xia, C. C. Wang, W. L. Yang and S. K. Fu, Mater. Chem. Phys., 2007, 103, 494 CrossRef CAS PubMed.
- D. Z. Yin, Q. Y. Zhang, C. J. Yin, Y. Jia and H. P. Zhang, Colloids Surf., A, 2010, 367, 70 CrossRef CAS PubMed.
- G. N. Yin, Z. Zheng, H. T. Wang, Q. G. Du and H. D. Zhang, J. Colloid Interface Sci., 2013, 394, 192 CrossRef CAS PubMed.
- G. H. Ma and J. H. Li, Chem. Eng. Sci., 2004, 59, 1711 CrossRef CAS PubMed.
-
(a) H. O. Zhou, T. J. Shi and X. Zhou, Appl. Surf. Sci., 2013, 266, 33 CrossRef CAS PubMed;
(b) M. S. Cho, S. T. Lim, I. B. Jang, H. J. Choi and M. S. Jhon, IEEE Trans. Magn., 2004, 40, 3036 CrossRef CAS.
- M. Niu, M. Du, Z. Gao, C. Yang, X. Lu, R. Qiao and M. Gao, Macromol. Rapid Commun., 2010, 31, 1805 CrossRef CAS PubMed.
- M. Mrlik, M. Sedlacik, V. Pavlinek, P. Bazant, P. Saha, P. Peer and P. Filip, J. Appl. Polym. Sci., 2013, 128, 2977 CrossRef CAS.
- N. A. Brusentsov, V. D. Kuznetsov, T. N. Brusentsova, T. S. Gendler, A. A. Novakova, E. R. Volter, E. A. Haliulina and M. I. Danilkin, J. Magn. Magn. Mater., 2004, 272, 2350 CrossRef PubMed.
- J. M. Ginder, L. C. Davis and L. D. Elie, Int. J. Mod. Phys. B, 1996, 10, 3293 CrossRef CAS.
- J. de Vicente, J. A. Ruiz-Lopez, E. Andablo-Reyes, J. P. Segovia-Gutierrez and R. Hidalgo-Alvarez, J. Rheol., 2011, 55, 753 CrossRef CAS.
- M. S. Cho, H. J. Choi and M. S. Jhon, Polymer, 2005, 46, 11484 CrossRef CAS PubMed.
-
(a) K. P. S. Parmar, Y. Meheust, B. Schjelderupsen and J. O. Fossum, Langmuir, 2008, 24, 1814 CrossRef CAS PubMed;
(b) F. F. Fang, H. J. Choi and M. S. Jhon, Colloids Surf., A, 2009, 351, 46 CrossRef CAS PubMed.
- H. J. Choi, I. S. Lee, J. H. Sung, B. J. Park and M. S. Jhon, J. Colloid Interface Sci., 2006, 295, 291 CrossRef CAS PubMed.
- F. F. Fang, M. S. Yang and H. J. Choi, IEEE Trans. Magn., 2008, 44, 4533 CrossRef CAS.
Footnote |
† Electronic supplementary information (ESI) available. See DOI: 10.1039/c4ra17025c |
|
This journal is © The Royal Society of Chemistry 2015 |
Click here to see how this site uses Cookies. View our privacy policy here.