DOI:
10.1039/C4RA15873C
(Paper)
RSC Adv., 2015,
5, 20674-20683
Facile synthesis of Fe3O4/hierarchical-Mn3O4/graphene oxide as a synergistic catalyst for activation of peroxymonosulfate for degradation of organic pollutants†
Received
5th December 2014
, Accepted 5th February 2015
First published on 5th February 2015
Abstract
Highly effective Fe3O4/Mn3O4/reduced graphene oxide (rGO) hybrids were synthesized as a heterogeneous catalyst for the degradation of organic dyes in aqueous solution using sulfate radical-based advanced oxidation processes. The physicochemical properties of the composite were characterized by several techniques, such as X-ray diffraction (XRD), Raman spectroscopy, Fourier transform infrared spectra (FTIR), transmission electron microscopy (TEM), X-ray photoelectron spectroscopy (XPS), and Brunauer–Emmett–Teller (BET) theory. The effects of different parameters on the catalytic activity of Fe3O4/Mn3O4/rGO, including initial Methylene Blue (MB) concentration, peroxymonosulfate (PMS) concentration, catalyst dosage, pH value, and temperature were assessed. Typically, 98.8% removal of 50 mg L−1 of MB and 68.3% reduction of TOC could be achieved in 30 min under the following conditions: temperature 25 °C, 100 mg L−1 of catalyst, and PMS dosage of 0.3 g L−1, showing a significant enhancement of the catalytic activity of the catalyst in the degradation of organic pollutants in aqueous solution compared with Fe3O4/rGO and Mn3O4/rGO. The catalyst exhibited high stability and good reusability according to three successive repeated reactions. Based on the radical experiments, the catalytic activity of Fe3O4/Mn3O4/rGO hybrids for degradation of MB is closely related with the amount of the sulfate and hydroxyl radicals generated from PMS. The excellent catalytic performance of the Fe3O4/Mn3O4/rGO is mainly attributed to the synergistic effects of Fe3O4, Mn3O4, rGO, and Oxone.
1. Introduction
Large amounts of water are polluted by colored dyes and other organic substances due to the need to color industrial products and produce other pesticides and medicines.1 These toxic substances can poison living things in the water and soil and threaten the safety of human drinking water. In addition, wastewater containing dyes is very difficult to treat, since the dyes are recalcitrant organic molecules, resistant to aerobic digestion, and are stable to light, heat and common oxidizing agents.2 A variety of physical, chemical, and biological methods are presently available for the treatment of wastewater discharged from various industrial processes. Biological treatment methods are cost-effective, but less effective towards organic pollutants. Physical methods such as adsorption and ion-exchange are also ineffective in wastewater treatment; furthermore, these methods can only transfer the pollutants to another phase rather than destroy them.3 Recently, advanced oxidation processes (AOPs) have become powerful and attractive techniques in the treatment of highly organic loaded and non-biodegradable wastewater.4 AOPs are based on the generation of reactive species, such as sulfate and hydroxyl radicals, that have a strong oxidizing potential for mineralizing organic pollutants into simple compounds, such as CO2 and H2O. Compared with hydroxyl radicals, sulfate radicals have also been recently suggested as an alternative due to their higher oxidation potential.5,6
Heterogeneous catalysts, compared with homogeneous catalysts, having the advantages of being easily recoverable and reusable and less harmful to the environmental, are widely used for the activation of peroxymonosulfate. Typical catalysts such as iron oxide and manganese oxide are active in generating SO4˙− via a Fenton-like reaction for advanced oxidation processes.7,8 It has been proven that the activity of catalysts follows the order of Mn3O4 > Co3O4 > Fe3O4.6 However, when combining the two different oxides into one hybrid, the situation is different. The newly formed hybrid not only shows easy separation properties by employment of a magnetic process, but also exhibits the enhanced ability to induce the reaction.9
In order to get the two different metal oxides together, we need a supporter, graphene oxide (GO) sheet. GO, one of the most important derivates of graphene, consists of a hexagonal ring-based carbon network with both sp2 and sp3 hybridized carbon atoms. Graphene has attracted tremendous attention for supporting metal and metal oxide applications due to its high electrical conductivity, unique mechanical strength, and large specific surface area.10,11 It has been found that graphene can significantly improve catalyst performance because it can effectively inhibit the aggregation of NPs and further can enhance the catalytic activity due to the synergistic effects.12–15
In this study, Fe3O4/rGO was prepared through an easy one step co-precipitation method. Mn3O4/Fe3O4/rGO was synthesized by a facile approach under basic conditions. The physical and chemical characterizations of Fe3O4/Mn3O4/rGO hybrids were evaluated in view of the effects of the main variables, such as PMS concentration, Methylene Blue concentration, catalyst dosage, pH value, and temperature. The reaction kinetics, material stability, and degradation mechanism were also discussed.
2 Experimental section
2.1 Materials
Manganese acetate tetrahydrate (Mn(C2H3O2)2·4H2O), ferric chloride hexahydrate (FeCl3·6H2O), and ferrous sulfate heptahydrate (FeSO4·7H2O) were purchased from Sinopharm Group Chemical Reagent Co., Ltd. Oxone (2KHSO5·KHSO4·K2SO4, PMS) was obtained from Aldrich. Methylene Blue was purchased from Northwest Geological Institute of Nonferrous Metals (Xi'an, China). Ethanol, tert-butyl alcohol and other chemicals were acquired from GuangFu Fine Chemical Company (Tianjin, China). All chemicals were used as received without further purification.
2.2 Synthesis of catalysts
Graphene oxide was prepared by a modified Hummer's method as described elsewhere.16 The Fe3O4/GO nanocomposite was prepared by a co-precipitation method in the presence of graphene oxide.17 For the preparation of Mn3O4/rGO hybrids, the prepared (1 mg mL−1) graphene oxide was exfoliated in 60 mL distilled water using ultrasonic treatment for more than 2 h. Mn(C2H3O2)2·4H2O 0.5023 g (0.0020 mol) dissolved in 10 mL distilled water was added to the above graphene oxide solution under magnetic stirring for 2 h. Then, 8.0 mL N2H4·H2O was added drop-wise to the above mixture, followed by stirring overnight at room temperature. The resultant product was washed several times with distilled water and ethanol and vacuum dried. The synthesis of Fe3O4/Mn3O4/rGO nanocomposites was as following: graphite oxide (68.5 mg) was dispersed in 250 mL deionized water and ultrasonicated for more than 2 h to get a transparent and homogeneous graphene oxide solution. FeCl3·6H2O 0.3468 g (0.0012 mol) and FeSO4·7H2O 0.1876 g (0.0006 mol) were dispersed separately in 25 mL deionized water and were added to the GO suspension. The aqueous suspension was vigorously stirred for 30 min at 80 °C under the protection of N2. Then, 5 mL ammonia solution (NH3·H2O) was quickly added into the reaction mixture, and the mixture was stirred vigorously for 2 h. The resultant product was washed several times with deionized water and then redispersed in 60 mL deionized water. Then 0.5023 g Mn(C2H3O2)2·4H2O (0.0020 mol) was added to the suspension of Fe3O4/GO under stirring. Subsequently, 8.0 mL N2H4·H2O was quickly added to the solution, and the mixture was stirred again for 18 h at room temperature. The final product was washed with deionized water and ethanol and vacuum dried at 60 °C before use. By changing the feed weight ratio of initial iron salts and manganese salts, three kinds of Fe3O4/Mn3O4/rGO hybrids were prepared (mFe/mMn = 0.2, 0.5, 5).
2.3 Characterization of catalyst
The crystalline structures of the as-synthesized hybrids were characterized by X-ray powder diffraction (X'pert Pro Philips X-ray diffractometer) over a 2θ range of 5–80°. The nanostructures of the samples were characterized by a transmission electron microscopy (TEM) system (Tecnai G2F30) equipped with an energy dispersive X-ray spectrometer (EDX). Morphology and size were investigated by scanning electron microscopy (SEM). Fourier transform infrared (FTIR) spectra were recorded on a Nicolet Nexus 670 Perkin-Elmer spectrometer. The XPS analysis was performed by using a PHI-5702 multifunctional spectrometer using an aluminum anode (monochromatic Al K radiation). C1s peaks were used as an inner reference calibration peak at 284.6 eV. Raman spectra were obtained using a confocal microprobe Raman system (Renishaw, RW2000). A nitrogen adsorption and desorption apparatus (Micromeritics ASAP 2020, USA) was employed to investigate the surface areas and the pore size distributions of the synthesized materials at 77 K. Prior to measurements, the samples were degassed at 80 °C overnight.
2.4 Experimental operations
Catalytic degradation experiments were carried out in a 250 mL conical flask with 100 mL of MB solution. The conical flasks containing aqueous solution were agitated at 150 rpm. The pH of the solution was initially adjusted to a desired value using NaOH or H2SO4 in all experiments. In the beginning, the nanocomposites were added into the MB solutions and ultrasonicated for 10 min to achieve the adsorption–desorption equilibrium between the catalyst and contaminants before the Oxone addition. Then, 1.0 mL sample solution was withdrawn at predetermined time intervals and filtered through a 0.22 μm filter. Next, 10 μL 1 M n-butanol was added to the sample to quench the reaction, and the sample was immediately diluted and measured by a UV-Vis spectrophotometer at 665 nm. The total organic carbon (TOC) of MB was measured for the mineralization experiment. For the successive recycle experiment, the used catalyst was separated by an external magnetic field and washed with water and ethanol to wipe off the adsorbed MB. Then, the catalyst was dispersed in 100 mL solution containing the same concentration of MB and PMS. After five repeated experiments, the catalyst was analyzed with XPS.
3 Results and discussion
3.1 Characterization of nanocomposites
TEM and HRTEM images were collected for bare GO, Mn3O4/rGO, and Fe3O4/Mn3O4/rGO hybrids, as shown in Fig. 1. It can be seen from Fig. 1(A) that GO had a sheet-like structure with some wrinkles on the planar surface. We observed that the GO microparticles had several layers of GO sheets from the HRTEM image of GO (Fig. 1(A1)). After the deposition of Mn3O4, the graphene surface was fully wrapped by Mn3O4, demonstrating the intimate bond between them. It can be evidently observed that the Mn3O4 nanoflakes wrap on graphene sheet and exhibit a folded silk-like morphology with some dark strips generated by the fold edges and wrinkles of nanoflakes (Fig. 1(B)).18 The SEM image of Mn3O4/rGO also confirmed the formation of hierarchical Mn3O4 on the rGO sheets (Fig. S1†). It can be observed that Mn3O4 had high crystallinity, revealing its single-crystal nature, and the lattice spacing agreed well with d[101] (Fig. 1(B1)).19 A TEM image Fig. 1(C) reveals that Fe3O4 with a small particle size was embedded into the gap of Mn3O4 flakes. A SEM image of Fe3O4/Mn3O4/rGO is shown in Fig. S2.† No Fe3O4 particles were observed for which Fe3O4 was smaller than Mn3O4. Under the magnification of 2000×, it was hard to observe Fe3O4 nanoparticles, and it can be observed from the SEM image that the morphology of Fe3O4/Mn3O4/rGO was similar to that of Mn3O4/rGO.20 On the basis of the TEM images, the presence of an intimate interaction between the Mn3O4 and Fe3O4 NPs and the graphene sheets could be confirmed, and such a combination enables fast electron transport through the graphene matrix to the Mn3O4 and Fe3O4 NPs, guaranteeing efficient chemical performance.21 The interface could form manganese iron binary oxides, which could be seen from the HRTEM image of Fe3O4/Mn3O4/rGO (Fig. 1(C1)). These sites were the most active sites in the catalytic process. DEX confirms the formation of a Fe3O4/Mn3O4/rGO hybrid, where Mn, Fe, C, and O elements on the rGO sheets can be detected with Cu peaks emanating from the TEM grids (Fig. 1(D)). The results of EDX spectra are consistent with the results of the elemental distribution maps of Fe3O4/Mn3O4/rGO (Fig. S3†), giving a ratio of Fe/Mn = 0.54, which was nearly equal to the initial feeding ratio of Fe/Mn (Table S1†).
 |
| Fig. 1 TEM and HRTEM images of graphene oxide (A), (A1), Mn3O4/rGO (B), (B1), and Fe3O4/Mn3O4/rGO (C), (C1); EDX spectrum of Fe3O4/Mn3O4/rGO (D). | |
The XRD pattern was analyzed for the as-synthesized GO, Fe3O4/rGO, Mn3O4/rGO, and Fe3O4/Mn3O4/rGO, as shown in Fig. 2. A broad diffraction peak emerged at 2θ = 10.9°, corresponding to the typical diffraction peak of GO nanosheets (Fig. 2(a)). The main peaks at 30.3°, 35.7°, 43.1°, 57.2°, and 62.7° of Fe3O4/rGO hybrids correspond to the (220), (311), (400), (511), and (440) planes, respectively, which is in good agreement with cubic spinel crystal structure of Fe3O4 (JCPDS no. 19-0629) (Fig. 2(b)).22 The peaks at 17.9°, 28.8°, 32.3°, 36.1°, 38.0°, 44.3°, 50.8°, 53.9°, 58.5°, 59.9°, and 64.7° of Mn3O4/rGO correspond to the (101), (112), (103), (211), (004), (220), (105), (312), (321), (224), and (314) planes, respectively, which is in good agreement with hausmannite Mn3O4 (JCPDS no. 89-4837) as reported previously (Fig. 2(c)).21,23 Fig. 2(d) shows the XRD peak of Fe3O4/Mn3O4/rGO. It can be observed that the peak at 17.9° corresponds to the (101) plane of Mn3O4 and 35.7° corresponds to the (311) plane of Fe3O4, indicating the coexistence of Fe3O4 and Mn3O4 in the hybrids.
 |
| Fig. 2 X-ray diffraction spectra of GO (a), Fe3O4/rGO (b), Mn3O4/rGO (c), and Fe3O4/Mn3O4/rGO (d). | |
The FT-IR spectra of GO, Fe3O4/rGO, Mn3O4/rGO, and Fe3O4/Mn3O4/rGO are shown in Fig. 3. In the FT-IR spectrum of GO, stretches of O–H, C
O, aromatic C
C, carboxyl C–O, epoxy C–O and alkoxy can be found at 3419 cm−1, 1737 cm−1, 1620 cm−1, 1384 cm−1, 1222 cm−1, and 1056 cm−1, respectively (Fig. 3(a)), which is in good agreement with the results of a previous report.24 For Fe3O4/rGO, Mn3O4/rGO, and Fe3O4/Mn3O4/rGO, the peaks at 3420 cm−1, 1719 cm−1, 1619 cm−1, 1222 cm−1, and 1042 cm−1 were diminished or decreased, which clearly implies the removal of oxy-functional groups after the reduction treatment. The peaks at around 482 cm−1 and 595 cm−1 are assigned to tetrahedral and octahedral Mn–O bands (Fig. 3(c)), suggesting that Mn3O4 was bound to the surface of graphene sheets.25 The peak at 583 cm−1 corresponds to the stretching vibration modes of Fe–O in Fe3O4 (Fig. 3(b)). The peaks at 528 cm−1 and 583 cm−1 in Fig. 3(d) are attributed to Mn–O and Fe–O vibrations, respectively, indicating that both iron oxide and manganese oxide exist in the hybrid Fe3O4/Mn3O4/rGO.26
 |
| Fig. 3 FT-IR spectra of GO (a), Fe3O4/rGO (b), Mn3O4/rGO (c), and Fe3O4/Mn3O4/rGO (d). | |
Raman spectroscopy is used for distinguishing ordered and disordered crystal structures of carbon. The G band around 1596 cm−1 and D band around 1350 cm−1 were observed in the Raman spectrum of graphene. The G-band at 1596 cm−1 corresponds to a well defined sp2 carbon type structure, while the D band at around 1350 cm−1 can be attributed to defects within the hexagonal graphitic structure. These results confirm the successful oxidation of graphite to graphene oxide sheets (Fig. 4(a)).27 The intensity ratio of the D to the G band (ID/IG) provides a sensitive measure of the disorder and crystallite size of the graphitic layers. The intensity ratio of ID/IG is 0.96 for GO, while the intensity ratio of ID/IG is 1.01 for Fe3O4/Mn3O4/rGO. The increase in ID/IG for GO and Fe3O4/Mn3O4/rGO indicates that higher defects and disorders of the graphitized structures in the composites, which is in agreement with the results of XRD analysis.28 A prominent peak at 644 cm−1 is characteristic of Mn–O lattice vibrations in the Fe3O4/Mn3O4/rGO hybrids (Fig. 4(b)).29,30
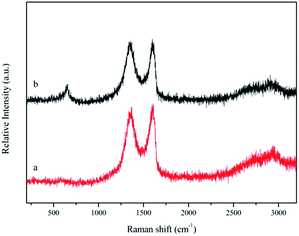 |
| Fig. 4 Raman spectra of GO (a) and Fe3O4/Mn3O4/rGO (b) composites. | |
N2 adsorption–desorption isotherms were collected to investigate the porous structure and surface area of the nanocomposites. Fig. S4(a–d)† shows the nitrogen-adsorption–desorption isotherms and the associated pore size distributions for GO, Fe3O4/rGO, Mn3O4/rGO, and Fe3O4/Mn3O4/rGO. It can be seen that all samples possess the type IV isotherm with a type H3 hysteresis loop indicating a mesoporous structure. The BET surface area of Mn3O4/rGO is 65.94 m2 g−1, which is larger than that of GO (49.98 m2 g−1). The results suggest that, on the one hand, Mn3O4 flakes dispersed on the graphene surface among the layers help to prevent the aggregation of graphene sheets, leading to the increase of surface area. On the other hand, Mn3O4 flakes mostly covering the surface of graphene (as shown in TEM results) makes the surface area increase limited.31 The surface area and pore volume of Fe3O4/Mn3O4/rGO (180.78 m2 g−1, 0.363 cm3 g−1) is higher than that of Mn3O4/rGO and is close to that of Fe3O4/rGO,32 indicating that flakes of Mn3O4 covering the graphene sheets contribute little to the surface area enlargement compared with Fe3O4 embedded into the gap between Mn3O4 flakes and the graphene sheet (Table 1). The high surface area of Fe3O4/Mn3O4/rGO is beneficial for the improvement of catalytic activity.
Table 1 Textural properties of GO, Fe3O4/rGO, Mn3O4/rGO, and Fe3O4/Mn3O4/rGO
Catalyst |
Surface area (SBET m2 g−1) |
Pore volume (cm3 g−1) |
Average pore diameter (nm) |
GO |
49.98 |
0.0332 |
3.60 |
Fe3O4/rGO |
185.83 |
0.394 |
8.54 |
Mn3O4/rGO |
65.95 |
0.259 |
17.33 |
Fe3O4/Mn3O4/rGO |
180.78 |
0.363 |
8.08 |
The chemical bonding states in the Fe3O4/Mn3O4/rGO composite was analyzed by XPS measurements, and the fitted data are shown in Fig. S5 and S6.† The survey scan of the hybrids showed photoelectron lines at binding energies of 284 eV, 528 eV, 640 eV, and 711 eV, corresponding to the C1s, O1s, Mn 2p, and Fe 2p, respectively, which are in good agreement with the result of EDX spectrum of the composite. The deconvolutions of the C1s peak, which consists of three peaks at 284.6 eV, 286.0 eV, and 288.7 eV, are ascribed to the C–C, C–O, and C(O)O in the hybrid (Fig. S6(a)†).33 The O1s spectrum of the nanocomposites could be deconvoluted into three peaks corresponding to Mn–O (529.6 eV), Fe–O (530.7 eV), and C–O (532.8 eV) (Fig. S6(b)†).15 The Fe 2p spectrum had simulation peaks at 709.7 eV, 712.3 eV, and 722.3 eV, which is in good agreement with the values of Fe3O4 reported in the literature (Fig. S6(c)†).22 The XPS spectra for the Mn 2p of the composite exhibits two peaks at 640.1 eV, and 651.6 eV, corresponding to the Mn 2p3/2 and Mn 2p1/2 states of Mn3O4, respectively.15,23 It is observed that there is an energy separation of 11.5 eV between the Mn 2p1/2 and Mn 2p3/2 peaks in the Mn 2p region (Fig. S6(d)†), which is in accordance with the spectrum of Mn3O4.14,34 The results of XPS analyses are in good agreement with the EDS and elemental distribution mapping results.
3.2 Catalytic oxidation of MB over different catalysts
Fig. 5 shows preliminary tests of adsorption and catalytic degradation of MB by Mn3O4/rGO, Fe3O4/rGO, and Fe3O4/Mn3O4/rGO hybrids in aqueous solution. The results show that the hybrids are able to absorb MB at low efficiency, which was negligible as compared to the fast removal of MB by the heterogeneous catalytic reaction. It is found that MB could hardly be degraded with only PMS due to the weak oxidation ability of PMS. The degradation efficiency of Fe3O4/Mn3O4/rGO–PMS (Fe/Mn = 0.2) is slightly higher than that of Mn3O4/rGO–PMS. When the ratio of Fe/Mn increased from 0.2 to 0.5, the degradation efficiency increased sharply from 86.7% to 93.5%, and also the time needed to degrade pollutants shortened from 120 min to 30 min. However, when the ratio of Fe/Mn further increased to 5, the degradation efficiency decreased from 93.5% to 92.5%. In addition, the rate of degradation decreased compared to that of Fe/Mn = 0.5. For the Fe3O4/rGO–PMS system, 78.5% degradation of MB was achieved within 120 min, which is lower compared to that achieved with the Fe3O4/Mn3O4/rGO–PMS system. These results can be explained as follows. When the ratio of Fe/Mn is low (<0.5), the increase in Fe content will increase the surface area and the activity of the catalyst. As can be seen from the SEM and TEM results, the existence of Fe3O4 nanoparticles embedded in the gaps between Mn3O4 flakes will provide more active sites to induce PMS to produce more sulfate radicals. However, when the ratio of Fe/Mn is further increased, the efficiency did not increase. It could be because the Mn3O4 component is more active than Fe3O4. When the dominant species immobilized on the rGO sheet was Fe3O4, it is not favourable for the degradation of MB.
 |
| Fig. 5 MB degradation in different systems. Fe3O4/Mn3O4/rGO–PMS (Fe/Mn = 0.5) (a), Fe3O4/Mn3O4/rGO–PMS (Fe/Mn = 0.2) (b), Mn3O4/rGO–PMS (c), Fe3O4/Mn3O4/rGO–PMS (Fe/Mn = 5) (d), Fe3O4/rGO–PMS (e), Fe3O4/Mn3O4/rGO (f), and PMS (g). (Reaction conditions: catalyst = 100 mg L−1, PMS dose = 0.3 g L−1, initial MB concentration = 50 mg L−1, pH = 7.0, T = 25 °C). | |
3.3 Effect of different operating parameters on the catalytic activity of Fe3O4/Mn3O4/rGO nanocomposites
The influence of the initial MB concentration on the heterogeneous degradation of MB by Fe3O4/Mn3O4/rGO was investigated with different initial concentrations (60 mg L−1, 80 mg L−1, and 100 mg L−1). As shown in Fig. 6(a), the degradation efficiencies for MB were 93.0%, 88.1%, and 77.0%, respectively, when the initial MB concentration was increased from 60 mg L−1 to 100 mg L−1.6,35,36 The MB/oxidant ratio was higher for the higher concentration of MB, because the addition of Oxone was the same for different initial concentrations of MB. The higher MB/Oxone ratio was disadvantageous for the degradation of MB. In addition, the excessive amounts of MB restrained the diffusion process and suppressed contact with the surface of the catalyst.
 |
| Fig. 6 MB degradation in the Fe3O4/Mn3O4/rGO–PMS system: the effect of initial MB concentration (a), the effect of catalyst dosage (b), the effect of PMS dosage (c), and the effect of initial pH value (d). (Except for the investigated parameter, other parameters were fixed at: catalyst = 100 mg L−1, Oxone dose = 0.3 g L−1, initial MB concentration = 50 mg L−1, pH = 7.0, and T = 25 °C). | |
The influence of catalyst dosage on the degradation of MB by Fe3O4/Mn3O4/rGO is illustrated in Fig. 6(b). The results indicate that the discoloration of MB was significantly influenced by the dosage of catalyst. The discoloration efficiency was enhanced from 65.4% to 90.4% when the catalyst dosage was increased from 5 mg L−1 to 10 mg L−1, mainly because the increase in the amount of Fe3O4/Mn3O4/rGO catalyst increased the presence of active sites on the catalyst surface as well as the sulfate radical generation. Moreover, more Fe3O4/Mn3O4/rGO catalyst could increase the adsorption of MB due to the large surface area and more functional groups on the surface of catalyst.13 Nevertheless, the degradation efficiency increased little when the catalyst concentration increased from 10 mg L−1 to 15 mg L−1, which was mainly attributed to possible scavenging of radicals by the reaction between excess active sites and the sulfate and hydroxyl radicals.37,38
The degradation of MB over Fe3O4/Mn3O4/rGO was further studied at varying amounts of PMS (Fig. 6(c)). Obviously, with an increase in Oxone dose (10 mg L−1, 20 mg L−1, and 30 mg L−1), the efficiency of MB decomposition increased. The increase in PMS concentration in the solution leads to an increase in the formation of sulfate radicals. Oxone reacts with M2+, generating sulfate radicals, and it can also react with M3+ to regenerate M2+ in the Fenton-like reaction. The increase in Oxone dose would provide more chances for reaction with Fe3O4/Mn3O4/rGO, which enhances the rate of activation of PMS to generate SO4˙−, resulting in an increase in MB removal.21
The effect of solution pH can remarkably influence the degradation of MB in aqueous solution as shown in Fig. 6(d). From the results, we can see that the degradation efficiency increased with the increase of solution pH from 3.00 to 11.00. The formation of M–OH is favoured at the elevated pH value. The M–OH complexes at the catalyst surface can enhance the activation of PMS to increase the degradation rates.14 The identification of radicals suggests that when the pH was from 2.00 to 7.00, the predominant species was SO4˙−. However, the sulfate radicals can convert to hydroxyl radicals under alkaline conditions. In the alkaline environment, both HO˙ and SO4˙− exist in the reaction system and can interconvert to attack the organic pollutants to create small molecules.39,40
The effect of reaction temperature on MB degradation was also investigated, and the results are shown in Fig. 7. A general trend can be observed that higher temperature will result in an increase in reaction rate. As seen, the MB degradation efficiency increased from 90.1% to 96.1% within 30 min when the temperature increased from 30 °C to 60 °C. The kinetics of MB degradation were investigated at different temperatures (30 °C, 45 °C, and 60 °C), as shown in Fig. 8. It was found that MB degradation in the Fe3O4/Mn3O4/rGO–PMS system is well fitted by pseudo-second-order kinetics (eqn (1)). The results are shown in Table 2.41,42
 |
| Fig. 7 Effect of temperature on the degradation of MB in the Fe3O4/Mn3O4/rGO–PMS system (reaction conditions: catalyst = 100 mg L−1, Oxone dose = 0.3 g L−1, initial MB concentration = 50 mg L−1, pH = 7.0). | |
 |
| Fig. 8 1/C − 1/C0 versus reaction time based on the effect of reaction temperature. Inset shows the Arrhenius curve (reaction conditions: catalyst = 100 mg L−1, Oxone dose = 0.3 g L−1, initial MB concentration = 50 mg L−1, pH = 7.0). | |
Table 2 Kinetic rate constants and activation energies of Fe3O4/Mn3O4/rGO–PMS for oxidation of MB
T (°C) |
kobs (L mg−1 min−1) |
R2 kobs |
ΔE (kJ mol−1) |
R2 ΔE |
30 |
0.0061 |
0.990 |
25.49 |
0.990 |
45 |
0.0096 |
0.991 |
60 |
0.0149 |
0.999 |
The relationship between reaction rate and temperature reveals that the PMS activation process is an endothermic reaction: higher temperature would drive the reaction to produce more active sulfate and hydroxyl radicals and thus enhance the MB degradation efficiency. To evaluate the activation energy, the correlation between the rate constants and reaction temperature was fitted by the Arrhenius equation (eqn (2)). The relationship is shown in the inset of Fig. 8. The activation energy of the Fe3O4/Mn3O4/rGO catalytic reaction was calculated to be 25.49 kJ mol−1 by plotting −ln(kobs) against 1/T. For comparison, Table 3 summarizes the activation energies obtained from previous studies of PMS activation. The results show that Fe3O4/Mn3O4/rGO presented a lower activation energy than most catalysts, suggesting that Fe3O4/Mn3O4/rGO catalyst is a promising catalytic material for oxidation processes.
|
ln k = ln A − Ea/R
| (2) |
Table 3 Comparison of activation energies in Fe/Mn-based catalysis
Catalyst |
Organics |
Activation energy (kJ mol−1) |
Reference |
Fe3O4/rGO |
Acid orange 7 |
24.3 |
43 |
Mn3O4/rGO |
Methylene Blue |
49.5 |
21 |
Mn3O4 |
Phenol |
38.5 |
6 |
MnFe2O4/rGO |
Orange II |
25.7 |
11 |
Fe3O4/Mn3O4/rGO |
Methylene Blue |
25.4 |
This work |
3.4 TOC removal during MB degradation
The efficiencies of MB discoloration and TOC removal at different reaction times are shown in Fig. S7.† It can be seen from Fig. S7† that the reduction of TOC reached 68.3%, while the discoloration of MB solution reached 98.8% in the Fenton degradation. The experimental results might be interpreted as follows: most MB molecules were destroyed by the strong oxidant species sulfate radicals and hydroxyl radicals. However, small organic intermediates produced in the catalytic process cannot be removed completely. The residual TOC may associate with some small molecules generated from the catalytic process.
3.5 Reactive species
It has been proven that several types of reactive radicals could be generated by PMS activated by transition metal ions, such as sulfate, peroxy-sulfate and hydroxyl radicals.44 SO4˙− and ˙OH could attack the organic molecules. But SO5˙− cannot due to its low redox potential (1.1 V).45,46 According to previous studies, the reaction rate of t-BuOH (TBA) (without α-hydrogen) with ˙OH is much higher than that with SO4˙− while the reaction rate of ethanol (with α-hydrogen) with ˙OH is comparable to that of SO4˙−. The reaction rate constants are listed in Table 4. On the basis of the different reaction rate constants, TBA was used as the scavenger for ˙OH and EtOH was used as the scavenger for ˙OH and SO4˙−.47 It can been seen from the results (Fig. 9) that the addition of 0.1 M ethanol inhibited MB degradation, leading to a decrease in the MB degradation to 38% compared to the 96% MB degradation that occurred without addition of ethanol. When 0.1 M TBA was added to the solution, the degradation of MB declined to 52% in 30 min. Thus, the inhibition of MB degradation caused by EtOH is much stronger than that caused by TBA, indicating that sulfate radicals were the dominant species in the degradation of MB.48
Table 4 Reaction rate constants of different alcohols with SO4˙− and ˙OH
Alcohol |
Rate constants (M s−1) |
˙OH |
SO4˙− |
TBA |
(3.8–7.6) × 108 |
(4–9.1) × 105 |
ETOH |
(1.2–2.8) × 109 |
(1.6–7.7) × 107 |
 |
| Fig. 9 Degradation of MB with different quenching agents (reaction conditions: catalyst = 100 mg L−1, Oxone dose = 0.3 g L−1, initial MB concentration = 50 mg L−1, pH = 7.0, T = 25 °C). | |
3.6 Stability and reusability of the Fe3O4/Mn3O4/rGO nanocomposite
The stability and recyclability of the Fe3O4/Mn3O4/rGO catalyst were evaluated by successive tests of MB degradation, as shown in Fig. 10. It was found that more than 90% of MB degradation could still be retained at the third run under similar reaction conditions with an initial MB concentration of 50 mg L−1 and PMS dosage of 0.3 g L−1. Therefore, the Fe3O4/Mn3O4/rGO hybrid has excellent long-term stability and can be reused with relative weak loss of catalytic activity for the degradation of organic pollutants in water. The decrease of the activity of the catalyst may be attributed to two reasons: first, there will be MB and other byproducts adhered on the catalyst surface even it was washed several times with deionzed water and ethanol after each cycle. Second, leaching of iron and manganese on the catalyst may also occur in the each reaction process.
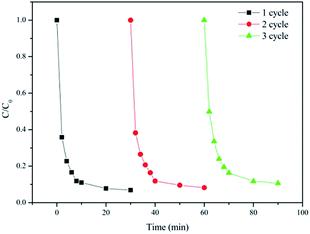 |
| Fig. 10 Degradation of MB with the recycled Fe3O4/Mn3O4/rGO hybrids (reaction conditions: catalyst = 100 mg L−1, Oxone dose = 0.3 g L−1, initial MB concentration = 50 mg L−1, pH = 7.0, T = 25 °C). | |
3.7 Mechanism of MB degradation
For the purpose of understanding the activation mechanism of PMS by Fe3O4/Mn3O4/rGO, we used XPS analysis to characterize Mn and Fe before and after the degradation of MB. The slight shift of Mn 2p3/2 from 640.1 eV to 641.5 eV and of Mn 2p1/2 from 651.6 eV to 652.0 eV and the formation of a new peak at 648.0 eV suggest that the Mn species on the catalyst surface and the ratio of Mn(III)/Mn(II) changed in the catalytic process.11 The loss of the satellite peak at 716.0 eV and the deconvolution of Fe 2p3/2 consisting of both Fe(III) and Fe(II) indicate that both
Fe and
Fe participate in the reaction cooperatively (Fig. 11).12,49 |
MnII + HSO5− → MnIII + SO4˙− + OH−
| (3) |
|
MnIII + HSO5− → MnII + SO5˙− + H+
| (4) |
|
FeII + HSO5− → FeIII + SO4˙− + OH−
| (5) |
|
FeIII + HSO5− → FeII + SO5˙− + H+
| (6) |
|
MnIII + FeII → MnII + FeIII
| (7) |
|
SO4˙− + H2O → H+ + SO42− + ˙OH
| (8) |
|
SO4˙−/˙OH + MB → intermediate → CO2 + H2O
| (9) |
 |
| Fig. 11 XPS spectra of Fe 2p (a) and Mn 2p (b) before and after the reaction. | |
Mn3O4 is believed to be composed of MnO·Mn2O3. The
MnII species can react with PMS to generate surface-bound SO4˙− and to produce a
MnIII site (eqn (3)). The formed
MnIII site can then react with HSO5− to regenerate a
MnII site, thus forming a small Mn circulation (eqn (4)).50 The iron oxide behaves similarly to the manganese oxide in the activation of PMS to produce SO4˙− to form a second circulation between
FeII and
FeIII (eqn (5) and (6)). The two circulations are combined together by the reaction between
MnIII and
FeII. The
FeII species may give an electron to the
MnIII and transfer it to
FeIII, because the standard redox potential of Mn3+/Mn2+ (1.51 V) is higher than that of Fe3+/Fe2+ (0.77 V) (eqn (7)).9 Regeneration of the active sites of the catalyst makes the reaction proceed cyclically until PMS is completely consumed after enough reaction time. The produced sulfate radicals can react with H2O to produce hydroxyl radicals. Both the radicals can attack the organic compounds to generate the mineralization products (eqn (8) and (9)) as illustrated in Scheme 1.
 |
| Scheme 1 Illustration of MB decomposition in the Fe3O4/Mn3O4/rGO composite–PMS system. | |
The excellent catalytic activity of Fe3O4/Mn3O4/rGO hybrids is probably due to positive synergistic effects between Fe3O4, Mn3O4, and graphene, which are mainly attributed to the following features.23 (i) BET measurements show that the surface area of the Fe3O4/Mn3O4/rGO is higher than that of Mn3O4/rGO. A higher surface area will provide more active sites for the adsorption of MB molecules. Such adsorption increases the effective concentration of MB molecules significantly near the surfaces of the Fe3O4/Mn3O4/rGO composite, resulting in the higher catalytic efficiency. Pore size analysis indicates that the Fe3O4/Mn3O4/rGO catalyst has a high pore volume and narrow size distribution, which shortens the diffusion path of PMS molecules toward the catalyst surface. (ii) Graphene sheets not only can prevent the aggregation of Fe3O4 and Mn3O4, but also can act as electron transfer channels to make the degradation process occur efficiently on these graphene-based nanomaterials.51 (iii) The hydrophilic nature of GO leads to the good dispersion of the Fe3O4/Mn3O4/rGO composite in water, thus improving the wettability of the catalyst in aqueous solution. The strong interaction Mn–O–C and Fe–O–C sites will favor the formation of OH on the Mn3O4 and Fe3O4 and promote activation of PMS.52 (iv) The redox reaction between
MnIII with
FeII accelerates the transfer of electrons, which will enhance the activation of PMS to produce sulfate radicals to degrade organic pollutants. (v) Good adhesion of hierarchical Mn3O4 prevents aggregation during the reaction course and provides reusability.53
Conclusions
A novel magnetic catalyst, a Fe3O4/Mn3O4/rGO nanocomposite, has been successfully synthesized through a facile two-step method and then used as a PMS activator for the degradation of MB. TEM observations indicate that graphene sheets were decorated with both Fe3O4 and Mn3O4: Mn3O4 nanoflakes enwrapped the graphene sheet, and Fe3O4, with its small particle size, was embedded in the gaps between Mn3O4. The catalytic performance showed that coupling the Fe3O4 and Mn3O4 with graphene sheets leads to a higher catalytic activity than Fe3O4/rGO and Mn3O4/rGO due to the synergistic effects of GO, Fe3O4, Mn3O4, and Oxone molecules. MB degradation in the Fe3O4/Mn3O4/rGO–PMS system follows pseudo-second-order kinetics, and the activation energy is 25.4 kJ mol−1. Both SO4˙− and ˙OH were generated as the radical species in the Fe3O4/Mn3O4/rGO–PMS system, and the dominant species was sulfate radicals. After recycling three times, the catalyst still keeps a high degradation efficiency, and the catalytic mechanism was proposed according to the XPS spectra analysis results. The present research synthesized a novel Fe3O4/Mn3O4/rGO nanocomposite, which is a promising candidate as the catalyst for the decomposition of organic pollutants in water.
Notes and references
- G. Crini, Bioresour. Technol., 2006, 97, 1061–1085 CrossRef CAS PubMed.
- Q. Sun and L. Yang, Water Res., 2003, 37, 1535–1544 CrossRef CAS.
- K. Dutta, S. Mukhopadhyay, S. Bhattacharjee and B. Chaudhuri, J. Hazard. Mater., 2001, 84, 57–71 CrossRef CAS.
- N. N. Tušar, D. Maučec, M. Rangus, I. Arčon, M. Mazaj, M. Cotman, A. Pintar and V. Kaučič, Adv. Funct. Mater., 2012, 22, 820–826 CrossRef.
- T. Olmez-Hanci and I. Arslan-Alaton, Chem. Eng. J., 2013, 224, 10–16 CrossRef CAS PubMed.
- E. Saputra, S. Muhammad, H. Sun, H.-M. Ang, M. O. Tadé and S. Wang, J. Colloid Interface Sci., 2013, 407, 467–473 CrossRef CAS PubMed.
- Y. Wang, H. Sun, H. M. Ang, M. O. Tadé and S. Wang, Appl. Catal., B, 2015, 164, 159–167 CrossRef CAS PubMed.
- P. Si, X. C. Dong, P. Chen and D. H. Kim, J. Mater. Chem. B, 2013, 1, 110–115 RSC.
- J. Liu, Z. Zhao, P. Shao and F. Cui, Chem. Eng. J., 2015, 262, 854–861 CrossRef CAS PubMed.
- Y. Yao, S. Miao, S. Liu, L. P. Ma, H. Sun and S. Wang, Chem. Eng. J., 2012, 184, 326–332 CrossRef CAS PubMed.
- Y. Yao, Y. Cai, F. Lu, F. Wei, X. Wang and S. Wang, J. Hazard. Mater., 2014, 270, 61–70 CrossRef CAS PubMed.
- S.-Q. Liu, B. Xiao, L.-R. Feng, S.-S. Zhou, Z.-G. Chen, C.-B. Liu, F. Chen, Z.-Y. Wu, N. Xu, W.-C. Oh and Z.-D. Meng, Carbon, 2013, 64, 197–206 CrossRef CAS PubMed.
- S. Guo, G. Zhang, Y. Guo and J. C. Yu, Carbon, 2013, 60, 437–444 CrossRef CAS PubMed.
- Y. J. Yao, C. Xu, S. M. Yu, D. W. Zhang and S. B. Wang, Ind. Eng. Chem. Res., 2013, 52, 3637–3645 CAS.
- Y. Li, J. Qu, F. Gao, S. Lv, L. Shi, C. He and J. Sun, Appl. Catal., B, 2015, 162, 268–274 CrossRef CAS PubMed.
- D. C. Marcano, D. V. Kosynkin, J. M. Berlin, A. Sinitskii, Z. Z. Sun, A. Slesarev, L. B. Alemany, W. Lu and J. M. Tour, ACS Nano, 2010, 4, 4806–4814 CrossRef CAS PubMed.
- A. Prakash, S. Chandra and D. Bahadur, Carbon, 2012, 50, 4209–4219 CrossRef CAS PubMed.
- C. Guo, H. Li, X. Zhang, H. Huo and C. Xu, Sens. Actuators, B, 2015, 206, 407–414 CrossRef CAS PubMed.
- R. Song, S. Feng, H. Wang and C. Hou, J. Solid State Chem., 2013, 202, 57–60 CrossRef CAS PubMed.
- M. Jing, H. Hou, Y. Yang, Y. Zhang, X. Yang, Q. Chen and X. Ji, Electrochim. Acta, 2015, 155, 157–163 CrossRef CAS PubMed.
- Y. Yao, C. Xu, S. Yu, D. Zhang and S. Wang, Ind. Eng. Chem. Res., 2013, 52, 3637–3645 CAS.
- M. Liu, T. Wen, X. Wu, C. Chen, J. Hu, J. Li and X. Wang, Dalton Trans., 2013, 42, 14710–14717 RSC.
- D. Wang, Y. Li, Q. Wang and T. Wang, Eur. J. Inorg. Chem., 2012, 2012, 628–635 CrossRef CAS.
- S. Park, K.-S. Lee, G. Bozoklu, W. Cai, S. T. Nguyen and R. S. Ruoff, ACS Nano, 2008, 2, 572–578 CrossRef CAS PubMed.
- Y. Wu, S. Liu, H. Wang, X. Wang, X. Zhang and G. Jin, Electrochim. Acta, 2013, 90, 210–218 CrossRef CAS PubMed.
- X. Luo, C. Wang, S. Luo, R. Dong, X. Tu and G. Zeng, Chem. Eng. J., 2012, 187, 45–52 CrossRef CAS PubMed.
- J. Sun, H. Zhang, L.-H. Guo and L. Zhao, ACS Appl. Mater. Interfaces, 2013, 5, 13035–13041 CAS.
- S. Zhu, J. Guo, J. Dong, Z. Cui, T. Lu, C. Zhu, D. Zhang and J. Ma, Ultrason. Sonochem., 2013, 20, 872–880 CrossRef CAS PubMed.
- H. Kim, D.-H. Seo, S.-W. Kim, J. Kim and K. Kang, Carbon, 2011, 49, 326–332 CrossRef CAS PubMed.
- N. Li, Z. Geng, M. Cao, L. Ren, X. Zhao, B. Liu, Y. Tian and C. Hu, Carbon, 2013, 54, 124–132 CrossRef CAS PubMed.
- M. Hu, K. S. Hui and K. N. Hui, Chem. Eng. J., 2014, 254, 237–244 CrossRef CAS PubMed.
- J. Huang, Q. Chang, Y. Ding, X. Han and H. Tang, Chem. Eng. J., 2014, 254, 434–442 CrossRef CAS PubMed.
- M. Seredych and T. J. Bandosz, J. Mater. Chem., 2012, 22, 23525–23533 RSC.
- D. W. Wang, Y. Q. Li, Q. H. Wang and T. M. Wang, Eur. J. Inorg. Chem., 2012, 628–635 CrossRef CAS.
- H. Liang, H. Sun, A. Patel, P. Shukla, Z. H. Zhu and S. Wang, Appl. Catal., B, 2012, 127, 330–335 CrossRef CAS PubMed.
- E. Saputra, S. Muhammad, H. Sun, A. Patel, P. Shukla, Z. H. Zhu and S. Wang, Catal. Commun., 2012, 26, 144–148 CrossRef CAS PubMed.
- T. D. Nguyen, N. H. Phan, M. H. Do and K. T. Ngo, J. Hazard. Mater., 2011, 185, 653–661 CrossRef CAS PubMed.
- J. H. Ramirez, F. J. Maldonado-Hódar, A. F. Pérez-Cadenas, C. Moreno-Castilla, C. A. Costa and L. M. Madeira, Appl. Catal., B, 2007, 75, 312–323 CrossRef CAS PubMed.
- Y.-H. Guan, J. Ma, X.-C. Li, J.-Y. Fang and L.-W. Chen, Environ. Sci. Technol., 2011, 45, 9308–9314 CrossRef CAS PubMed.
- C. J. Liang and H. W. Su, Ind. Eng. Chem. Res., 2009, 48, 5558–5562 CrossRef CAS.
- J. De Laat and H. Gallard, Environ. Sci. Technol., 1999, 33, 2726–2732 CrossRef CAS.
- N. D. Meeks, V. Smuleac, C. Stevens and D. Bhattacharyya, Ind. Eng. Chem. Res., 2012, 51, 9581–9590 CrossRef CAS PubMed.
- N. A. Zubir, C. Yacou, X. Zhang and J. C. Diniz da Costa, J. Environ. Chem. Eng., 2014, 2, 1881–1888 CrossRef CAS PubMed.
- M. Pagano, A. Volpe, G. Mascolo, A. Lopez, V. Locaputo and R. Ciannarella, Chemosphere, 2012, 86, 329–334 CrossRef CAS PubMed.
- G. P. Anipsitakis and D. D. Dionysiou, Environ. Sci. Technol., 2003, 37, 4790–4797 CrossRef CAS.
- Y.-H. Guan, J. Ma, Y.-M. Ren, Y.-L. Liu, J.-Y. Xiao, L.-q. Lin and C. Zhang, Water Res., 2013, 47, 5431–5438 CrossRef CAS PubMed.
- D. Chen, X. L. Ma, J. H. Zhou, X. Chen and G. R. Qian, J. Hazard. Mater., 2014, 279, 476–484 CrossRef CAS PubMed.
- J. Liu, Z. Zhao, P. Shao and F. Cui, Chem. Eng. J., 2015, 262, 854–861 CrossRef CAS PubMed.
- Y. Ding, L. Zhu, N. Wang and H. Tang, Appl. Catal., B, 2013, 129, 153–162 CrossRef CAS PubMed.
- L. Zhang, Y. Nie, C. Hu and X. Hu, J. Hazard. Mater., 2011, 190, 780–785 CrossRef CAS PubMed.
- Z. Y. Ji, X. P. Shen, G. X. Zhu, H. Zhou and A. H. Yuan, J. Mater. Chem., 2012, 22, 3471–3477 RSC.
- M. Seredych, O. Mabayoje and T. J. Bandosz, Langmuir, 2011, 28, 1337–1346 CrossRef PubMed.
- R. Edla, N. Patel, M. Orlandi, N. Bazzanella, V. Bello, C. Maurizio, G. Mattei, P. Mazzoldi and A. Miotello, Appl. Catal., B, 2015, 166–167, 475–484 CrossRef CAS PubMed.
Footnote |
† Electronic supplementary information (ESI) available. See DOI: 10.1039/c4ra15873c |
|
This journal is © The Royal Society of Chemistry 2015 |
Click here to see how this site uses Cookies. View our privacy policy here.