DOI:
10.1039/C4RA14353A
(Paper)
RSC Adv., 2015,
5, 10944-10950
Carbon-supported hollow palladium nanoparticles with enhanced electrocatalytic performance†
Received
12th November 2014
, Accepted 7th January 2015
First published on 7th January 2015
Abstract
Carbon-supported palladium nanoparticles (NPs) with hollow interiors (hPdNPs/C) are fabricated via a facile approach. In this strategy, core–shell NPs with an Ag core and an Ag–Pd alloy shell (Ag@Ag–Pd) are first synthesized in oleylamine by a galvanic replacement reaction between Ag seed particles and Pd2+ ion precursors. Then the core–shell Ag@Ag–Pd NPs are loaded on the XC-72 carbon supports and refluxed in acetic acid to remove the original organic surfactant. The carbon-supported core–shell Ag@Ag–Pd NPs are subsequently agitated in saturated Na2S or NaCl solution for 24 h to eliminate the Ag component from the core and shell regions, leading to the formation of hPdNPs/C. Specifically, the hPdNPs/C generated by NaCl treatment exhibit superior catalytic activity and durability for formic acid oxidation reaction (FAOR) and oxygen reduction reaction (ORR), compared with the commercial Pd/C catalysts from Johnson Matthey, mainly due to the high electrochemically active surface areas (ECSAs) of the hollow structure, whereas the hPdNPs/C obtained by Na2S treatment display very poor catalytic performance due to the serious poisoning induced by S2− adsorption.
1. Introduction
Although the galvanic replacement reaction (GRR) has been proved to be an effective approach to produce noble metal nanomaterials with hollow interiors,1–10 it is generally thought that the GRR between silver (Ag) nanoparticles (NPs) and palladium (Pd) metal precursors would result in the formation of Ag–Pd alloy NPs instead of nanoshells. A number of reports including those from us are devoted to the synthesis and characterization of such alloy NPs.11–13 For example, the Lee group reported the synthesis of Ag–Pd alloy NPs by reacting the polyvinylpyrrolidone (PVP)-stabilized Ag NPs of ca. 8 nm with PdCl2 in aqueous phase, and they ascribed the alloying process to the rapid inter-diffusion of metal atoms as a result of the reduced dimension of the Ag seed particles, elevated temperature and the large number of interfacial vacancy defects generated by the replacement reaction.11 We also reported the formation of alloy Ag–Pd NPs in toluene or oleylamine by replacement reaction between dodecylamine (DDA)- or oleylamine-stabilized Ag NPs and PdCl2 precursors.12,13 The alloy structures of the above-mentioned Ag–Pd NPs were also sufficiently characterized by electron microscopic images and element profiles of an arbitrary single particle, which indeed show an excellent atomic ordering within each particle and uniform distributions of Ag and Pd signals across the entire Ag–Pd nanoparticle, respectively.
In our recent progress in hollow structured Pd NPs with highly catalytic activities, we found the so-called Ag–Pd alloy NPs derived from replacement reaction between Ag seeds and Pd2+ ion precursors could be further tuned into hollow structured Pd NPs after removing Ag component using a chemical agent, e.g. NaCl.14 This is a strong evidence to illustrate the formation of core–shell structure during the replacement reaction between Ag seeds and Pd2+ ion precursors, and the uniform distribution of Ag across the entire particle might be an indication to show that the Ag component not only resides in the core, but also presents in the shell region. In this work, we further attempt developing a more facile approach to the fabrication of carbon-supported Pd NPs with hollow interiors, labeled as hPdNPs/C, based on the core–shell particles derived from galvanic replacement reaction. In this strategy, core–shell NPs with an Ag core and an Ag–Pd alloy shell (Ag@Ag–Pd) are firstly synthesized in oleylamine by galvanic replacement reaction between Ag seed particles and organic Pd2+ ion precursors. Then the core–shell Ag@Ag–Pd NPs are loaded on the XC-72 carbon supports and refluxed in acetic acid to remove the original organic surfactant. The carbon-supported core–shell Ag@Ag–Pd NPs are subsequently agitated in saturated Na2S or NaCl solution for 24 h to eliminate the Ag component from the core and shell regions, leading to the formation of hPdNPs/C. The purpose of this study is to provide a strategy with remarkable simplicity for the fabrication of hollow structured Pd NPs with enhanced catalytic activity and durability for formic acid oxidation reaction (FAOR) and oxygen reduction reaction (ORR). However, this study also calls for the specific concerns with respect to the reliability of element profile and mapping analyses in determining the structure of nanoparticles, particularly for those having multi-components in the core and shell regions.
2. Experimental
2.1 General materials
Silver nitrate (AgNO3, ACS reagent, ≥99.0%), palladium(II) acetylacetonate (Pd(acac)2, 99%), oleylamine (70%, technical grade) and Nafion 117 solution (5% in a mixture of lower aliphatic alcohols and water) from Sigma-Aldrich, sodium sulfide nonahydrate (Na2S·9H2O, ≥98%), sodium chloride (NaCl, ≥99.5%), ethanol (>99.7%), methanol (>99%), toluene (>99.5%), formic acid (>88%) and perchloric acid solution (70%) from Beijing Chemical Works, Vulcan XC-72 carbon powders (XC-72C with BET surface area of 250 m2 g−1 and average particle size of 40–50 nm) from Cabot, commercial Pd/C catalyst from Johnson Matthey (JM), were used as received. Deionized water was distilled by a Milli-Q Ultrapure-water purification system. All glassware and Teflon-coated magnetic stirring bars were cleaned with aqua regia, followed by copious rinsing with deionized water before drying in an oven.
2.2 Synthesis of core–shell Ag@Ag–Pd NPs
GRR was used for the synthesis of core–shell Ag@Ag–Pd NPs with an Ag core and an alloy Ag–Pd shell. In brief, 17 mg of AgNO3 was added to 10 mL of oleylamine in a three-necked flask fitted with a condenser and a stir bar. The solution was heated to 150 °C and kept at this temperature for 1 h for the reduction of Ag+ ions by oleylamine. Then, 9 mg of Pd(acac)2 was swiftly added to the as-prepared Ag NPs under vigorous stirring at 150 °C, and the mixture was kept at this temperature for 2 h, resulting in the formation of core–shell Ag@Ag–Pd colloidal solution with a color of dark reddish-brown. After the reaction, the core–shell Ag@Ag–Pd NPs were recovered by precipitation with methanol, followed by centrifugation and washing with methanol, and then re-dispersed in 10 mL of toluene.
2.3 Synthesis of carbon-supported Pd NPs with hollow interiors (hPdNPs/C)
For the preparation of hPdNPs/C, the core–shell Ag@Ag–Pd NPs dispersed into toluene were firstly loaded on XC-72 carbon. In detail, a calculated amount of carbon powder was added to the toluene solution of core–shell Ag@Ag–Pd NPs. After stirring the mixture for 6 h, carbon-supported core–shell Ag@Ag–Pd NPs (labeled as Ag@Ag–Pd NPs/C, 20 wt% Pd on carbon support) were collected by centrifugation and washed thrice with ethanol. Then the Ag@Ag–Pd NPs/C were re-dispersed in 30 mL of acetic acid by ultra-sonication, and the resulting mixture was refluxed for 3 h at 120 °C to remove the organic surfactants from the particle surface. Subsequently, the Ag@Ag–Pd NPs/C were collected by centrifugation, washed thrice with water, and then dried at room temperature in vacuum. For the removal of Ag component from the core and shell regions, the Ag@Ag–Pd NPs/C gained above were mixed with 30 mL of saturated aqueous NaCl solution (or saturated aqueous Na2S solution), and the mixture was aged for 24 h under vigorous stirring at room temperature. Finally, the resulting hPdNPs/C were collected by centrifugation, washed with water, and dried at room temperature in vacuum (labeled as hPdNPs/C–Cl with NaCl treatment and hPdNPs/C–S with Na2S treatment).
2.4 Particle characterizations
Transmission electron microscopy (TEM), high-resolution TEM (HRTEM), and scanning TEM (STEM) were performed on a JEOL JEM-2100 and JEOL JEM-2010F electron microscope operated at 200 kV with the supplied software for automated electron tomography. For the TEM measurements, a drop of the nanoparticle solution was dispensed onto a 3 mm carbon-coated copper grid, and excessive solution was removed by an absorbent paper. Then the sample was dried under vacuum at room temperature. An energy dispersive X-ray spectroscopy (EDX) analyzer attached to the TEM operated in the STEM mode was used to analyze the chemical compositions of the synthesized NPs. Powder X-ray diffraction (XRD) patterns were recorded on a Bruker D8 diffractometer, using Cu Kα radiation (λ = 0.154056 nm). X-ray photoelectron spectra (XPS) were collected using a Thermo Scientific K-Alpha XPS spectrometer.
2.5 Electrochemical measurements
Electrochemical measurements were carried out in a standard three-electrode cell, which was connected to a Bio-logic VMP3 (with EC-lab software version 9.56) potentiostat. A leak-free Ag/AgCl (saturated with KCl) electrode was used as the reference. The counter electrode was a platinum mesh (1 × 1 cm2) attached to a platinum wire.
The working electrode was a thin layer of Nafion-impregnated catalyst cast on a vitreous carbon disk. This electrode was prepared by ultrasonically dispersing 5 mg of the NPs/C in 1 mL of ethanol containing 0.05 mL of Nafion solution. A calculated volume of the ink was dispensed onto the 5 mm glassy carbon disk electrode to produce a nominal catalyst loading of 25.5 μg cm−2 (Pd basis). The carbon electrode was then dried in a stream of warm air at 70 °C for 1 h.
Electrochemical CO stripping voltammograms used to determine the electrochemically active surface areas (ECSAs) of the catalysts were obtained by the oxidation of pre-adsorbed CO (COad) in 0.1 M HClO4 at a scan rate of 50 mV s−1. CO was introduced into 0.1 M HClO4 for 20 min to allow for complete adsorption of CO onto the catalysts. During this process, the working electrode was maintained at 0.15 V. Excess CO in the electrolyte was then purged with high purity N2 for 20 min. The amount of COad was measured by integration of the COad stripping peak, and corrected for electric double-layer capacitance. The specific ECSA was calculated based on the following:
where
Q is the charge of CO desorption–electrooxidation in microcoulomb (μC), which is calculated by dividing the scan rate with the integral area of CO desorption peak,
G represents the total amount of Pd (μg) on the electrode, and 420 is the charge (μC cm
−2) required to oxidize a monolayer of CO on the catalyst.
The catalyst performance for formic acid oxidation reaction (FAOR) was measured in room temperature by cyclic voltammetry and chronoamperometry. For these measurements the potential window between −0.2 V to 1 V was scanned at 50 mV s−1 until a stable response was obtained. The electrolyte was HCOOH (1 M) in HClO4 (0.1 M), and the current density was normalized by the mass of Pd in the catalysts to obtain the specific activities.
The performance of carbon-supported hollow Pd NPs in room temperature oxygen reduction reaction (ORR) was also evaluated in 0.1 M HClO4 electrolyte solution using a glass carbon rotating disk electrode (RDE) at a rotation rate of 1600 rpm. Negative-going linear sweep voltammograms were recorded from 0.6 to 0.3 V at 10 mV s−1 at room temperature in the presence of bubbling ultra-pure oxygen to maintain a saturated oxygen atmosphere near the working electrode. For each catalyst (hPdNPs/C–Cl and commercial Pd/C catalysts), the measured current density was normalized by the mass of Pd in the catalysts.
3. Results and discussion
Fig. 1 is the schematic illustration for the preparation of hPdNPs/C. At first, Ag NPs as sacrificial template are synthesized by oleylamine reduction of AgNO3. The oleylamine simultaneously serves as the stabilizer of Ag NPs. The XRD pattern of Ag NPs is shown in Fig. S1 of ESI,† which clearly shows that face-centered cubic (fcc) Ag NPs have been synthesized successfully (ESI Fig. S1a†).15 The TEM image in ESI Fig. S2a† exhibits these spherical Ag seed particles with an average size of 12.4 nm are nearly mono-dispersed. The HRTEM image (ESI Fig. S2b†) illustrates the lattice planes in these NPs, showing an interplanar spacing of ca. 0.24 nm, which corresponds to the (111) planes of the fcc Ag (JCPDS Card File 893722).
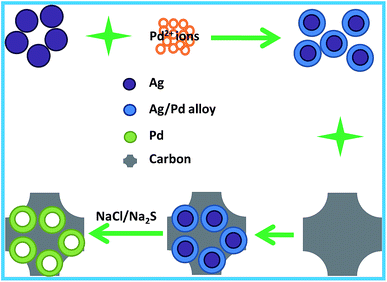 |
| Fig. 1 Schematic for the preparation of carbon-supported hollow Pd NPs using core–shell Ag@Ag–Pd NPs as starting templates, which are prepared by galvanic replacement reaction between Ag seeds and Pd2+ ion precursors. | |
3.1 Bimetallic Ag@Ag–Pd NPs with a core–shell structure
The synthesis of bimetallic Ag@Ag–Pd NPs with an Ag core and an Ag–Pd alloy shell is an important step preceding the preparation of hPdNPs/C. The core–shell Ag@Ag–Pd NPs were synthesized by the GRR between Ag seed particles and Pd2+ ion precursors, which can be described as 2Ag + Pd2+ → Pd + 2Ag+. During the galvanic replacement process, the Ag seed particles are transformed into a alloy shell made of Ag and Pd components through an alloying process,6,16 which inhibits the further oxidative dissolution of the Ag core by locking the unreacted Ag seeds away with the Pd2+ ions. As a result, the replacement reaction between Ag seed particles and Pd2+ ion precursors in oleylamine leads to the formation of core–shell Ag@Ag–Pd NPs instead of Ag–Pd alloy nanoshells. In comparison with the GRR in aqueous phase, a notable advantage in oleylamine was that the replacement reaction could be carried out at high concentrations of Ag seeds and Pd2+ ion precursors. This is because the GRR in an organic medium avoided the precipitates of low soluble salts such as AgCl.
The TEM, HRTEM and STEM images of the bimetallic NPs prepared via the GRR between Ag seeds and Pd2+ ion precursors are shown in Fig. 2a–c, respectively, which demonstrate the uniform bimetallic particles are spherical in shape and have an average diameter of ca. 9.3 nm. The STEM-EDX analysis (Fig. 2h) of arbitrary two particles framed in Fig. 2c illustrates that the particles derived from GRR between Ag seeds and Pd2+ ion precursors are indeed composed of Ag and Pd. However, although brightness contrast between the core and shell region could be discerned in the high resolution STEM image (Fig. 2d), which indicates the formation of core–shell structure, it is difficult to definitely make the same inference from the elemental mapping (Fig. 2e–g) of the two particles in Fig. 2d. In the elemental mapping patterns, both the Pd and Ag signals are observed to distribute throughout the entire particle. Indeed, as exhibited by Fig. 2e and f, the intensity of Ag signal at center is little stronger than that at peripheral region, while the intensity of Pd signal is uniform throughout the entire particle. This might be a weak evidence to support the formation of core–shell Ag@Ag–Pd NPs. A slight shift to lower angles is noted in the XRD pattern of the core–shell Ag@Ag–Pd NPs (ESI Fig. S1c†), compared with that of the Pd NPs prepared in oleylamine in the absence of Ag seeds (ESI Fig. S1b†). This is because Pd has smaller lattice parameter (0.390 nm) than that of Ag (0.409 nm), and the alloy with Ag results in an increase in the distance of lattice planes.17
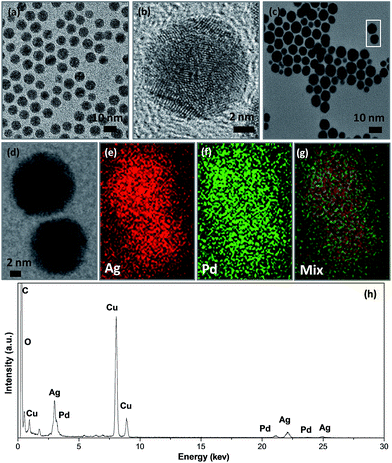 |
| Fig. 2 TEM image (a), HRTEM image (b), STEM image (c and d), elemental mapping (e–g), and STEM-EDX analysis (h) of core–shell Ag@Ag–Pd NPs as-prepared by GRR between Ag NPs and Pd2+ ion precursors in oleylamine. | |
3.2 Carbon-supported Pd NPs with hollow interiors
A more direct evidence to support the formation of core–shell Ag@Ag–Pd NPs is the product after eliminating Ag component from the bimetallic particles derived from GRR between Ag seeds and Pd2+ ion precursors. It has been well known that the Ag NPs could be etched by oxygen (O2) to produce Ag+ ions.13,18,19 In this case, sodium chloride (NaCl) and sodium sulfide (Na2S) could be the candidates to remove the Ag component from core–shell Ag@Ag–Pd NPs by reacting with the Ag+ ions. However, we experimentally found that the direct mixing of core–shell Ag@Ag–Pd organosol in toluene or oleylamine and aqueous solution of Na2S or NaCl usually results in particle aggregates instead of well dispersed metal nanoparticles with hollow interiors. As the reaction between Ag+ ions generated by O2 etching from Ag@Ag–Pd NPs and NaCl/Na2S could only occur at the interface between water and organic solvent, the failure to produce hollow structured Pd NPs is the result of poor contact between the two phases because of their lack of mutual solubility. Therefore, we designed an effective protocol to fabricate Pd NPs with hollow interiors. As illustrated by the scheme in Fig. 1, the core–shell Ag@Ag–Pd NPs synthesized in oleylamine via GRR and dispersed in toluene were firstly loaded on carbon supports to obtain Ag@Ag–Pd NPs/C, which were subsequently refluxed in acetic acid at 120 °C for 3 h to remove the oleylamine surfactant from the surface of core–shell NPs. The refluxing in acetic acid also renders the surface of core–shell NPs hydrophilic.20 Then, upon agitating the Ag@Ag–Pd NPs/C with saturated NaCl/Na2S solution, the Ag component in alloy Ag–Pd shell is firstly eliminated, and this leads to the establishment of the ionic channel for further removal of Ag from the core region of core–shell Ag@Ag–Pd NPs, finally resulting in the formation of hollow structured Pd NPs on carbon supports (hPdNPs/C).
The representative TEM image of the Ag@Ag–Pd NPs/C after refluxing in acetic acid was shown in ESI Fig. S3,† which clearly demonstrates that the size, morphology, and dispersion of core–shell Ag@Ag–Pd NPs are intact in comparison with those in Fig. 2. After agitating with saturated aqueous Na2S or NaCl solution for 24 h, the Ag component from the core and shell regions were removed from the core–shell Ag@Ag–Pd NPs, resulting in hPdNPs/C with an intact size, as displayed by the TEM (Fig. 3a and b) and HRTEM images (Fig. 3d and e). The void space in the core region upon the removal of Ag by NaCl/Na2S could be discerned clearly by the strong brightness contrast between central and surface regions in the TEM and HRTEM images of Fig. 3a, b, d, and e. The XRD pattern of hPdNPs/C obtained by NaCl treatment (hPdNPs/C–Cl) was shown in ESI Fig. S1d,† which is quite analogous to that of pure Pd NPs prepared by oleylamine reduction of Pd(acac)2 in oleylamine in the absence of Ag seeds. The direct evidence for the removal of Ag from core–shell Ag@Ag–Pd NPs was provided by the disappearance of Ag signal in the EDX analyses of Ag@Ag–Pd NPs/C after treatment with aqueous solution of NaCl (Fig. 3c) or Na2S (Fig. 3f). The trace of Ag and S detected in the EDX spectrum (Fig. 3f) of hPdNPs/C obtained by Na2S treatment (hPdNPs/C–S) might be attributed the adsorption of Ag2S on the hPdNPs and/or carbon supports. This is supported by the XRD pattern shown in ESI Fig. S1e,† in which besides those indexed to fcc Pd, the diffraction peaks from monoclinic Ag2S phase are also clearly observed.21
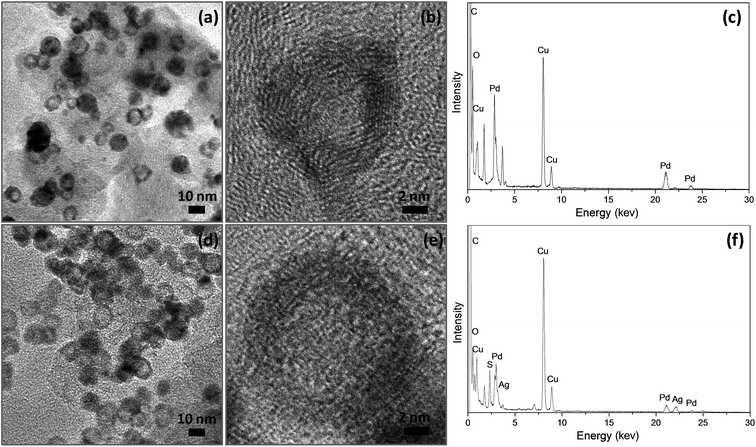 |
| Fig. 3 TEM images (a and d), HRTEM images (b and e), and EDX spectra (c and f) of hPdNPs/C obtained by NaCl (a–c) and Na2S treatment (d–f), respectively. | |
The maintaining of particle size and morphology after Na2S/NaCl treatment suggests that the removal of the Ag from the core and shell regions of core–shell Ag@Ag–Pd NPs would not cause the collapse of the particle geometry. In addition, the formation of Pd NPs with hollow interiors after Ag removal definitely illustrates that core–shell NPs with an Ag core are the dominant product instead Ag–Pd alloy NPs during the GRR between Ag seeds and Pd2+ ion precursors in oleylamine. The distribution of Ag throughout the entire particle (Fig. 2e) manifests that Ag is also present in shell region. The experimental observations here suggest that more careful characterizations are of necessity before determining the structure of nanoparticles using element profile and mapping analyses, particularly for those having complicated structure and multi-components simultaneously presented in different regions.
The chemical states of hPdNPs/C prepared by NaCl or Na2S treatment were determined using XPS. ESI Fig. S4a–d† are the 3d XPS spectra of Pd in Pd NPs by the reduction of oleylamine of Pd(acac)2 in the absence of Ag seeds, core–shell Ag@Ag–Pd NPs, hPdNPs/C–Cl, and hPdNPs/C–S, respectively. As shown, all Pd 3d XPS spectra can be deconvoluted into two pairs of doublets. The more intense doublet (at 335.9 and 341.1 eV for Pd 3d in Pd NPs, at 335.6 and 340.9 eV for Pd 3d in core–shell Ag@Ag–Pd NPs, at 335.9 and 341.1 eV for Pd 3d in hPdNPs/C–Cl, at 335.8 and 341.1 eV for Pd 3d in hPdNPs/C–S, respectively) is a signature of Pd in the zero-valent state, while the second and weaker doublet, with binding energies higher than those of zero-valent metal, could be assigned to the oxidation state of the Pd corresponding to PdO.22 It should be noted that the binding energies of the Pd 3d5/2 and 3d3/2 in core–shell Ag@Ag–Pd NPs (ESI Fig. S4b†) are shifted to lower values compared with those in Pd NPs, hPdNPs/C–Cl, and hPdNPs/C–S (ESI Fig. S4a, c, and d,† respectively), indicating the presence of electronic coupling effect between Ag and Pd in the core–shell Ag@Ag–Pd NPs. The difference in the electronegativity of Ag and Pd (1.93 and 2.20, respectively) may be favorable for the electron donation from Ag to Pd in core–shell Ag@Ag–Pd NPs, resulting in the increase of electron density around Pd atoms and hence the decrease of binding energies to electrons.23,24
3.3 Electrochemical properties of hPdNPs/C
To investigate the catalytic property of hPdNPs/C–Cl and hPdNPs/C–S, we use formic acid oxidation (FAOR) and oxygen reduction reaction (ORR) as models to examine the activity of hPdNPs/C and benchmark them with the commercial catalyst (Pd/C from JM, labeled as Pd/C-JM, 20 wt% Pd NPs with average size of 3.2 nm on Vulcan XC-72 carbon support, as shown by ESI Fig. S5† for the TEM image). The electrochemically active surface areas (ECSAs) of commercial Pd/C-JM catalysts, hPdNPs/C–Cl, and hPdNPs/C–S were determined using CO stripping voltammograms shown in Fig. 4.25 The ECSAs normalized by the mass of Pd are 71.3 m2 g−1, 82.8 m2 g−1, and 12.5 m2 g−1 for Pd/C-JM catalysts, hPdNPs/C–Cl and hPdNPs/C–S, respectively. The highest ECSAs of hPdNPs/C–Cl could easily be attributed to the access of inner surface due to the hollowing by NaCl. However, the ECSAs of hPdNPs/C–S are much lower than that of Pd/C-JM and hPdNPs/C–Cl, indicating that S2− ions have a strong poisonous effect on the surface of hPdNPs, which results in the deactivation of the Pd active sites.20
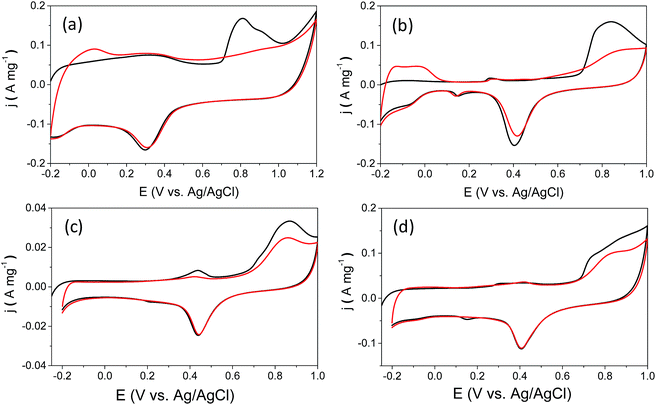 |
| Fig. 4 Cyclic voltammograms for CO stripping on commercial Pd/C catalyst (Pd/C-JM) (a), hPdNPs/C–Cl (b), hPdNPs/C–S (c), and hPdNPs/C–S after calcination at 300 °C for 1 h (d) in 0.1 M HClO4 at scan rate of 50 mV s−1. Black line: 1st scan; red line: 2nd scan. | |
The catalytic properties of hPdNPs–Cl was therefore examined for FAOR and benchmarked against commercial Pd/C-JM catalysts. Fig. 5a shows cyclic voltammograms of hPdNPs/C–Cl and Pd/C-JM for FAOR, which were obtained in the potential window of −0.2–1 V at a scan rate of 50 mV s−1. The current densities in the voltammograms were normalized with the mass of the Pd loaded on carbon support. As displayed, in the forward scan, the oxidation peaks for hPdNPs/C–Cl and Pd/C-JM are located at 0.57 and 0.84 V, respectively, which are assigned to the oxidation of formic acid. The hPdNPs/C–Cl show more negative peak potential and higher current density (1.28 A mg−1 for hPdNPs/C–Cl, and 1.16 A mg−1 for Pd/C-JM), implying the catalytic activity of hPdNPs/C–Cl for FAOR is higher than that of Pd/C-JM.26 The enhanced catalytic activity of the hPdNPs/C for FAOR could be definitely attributed to their larger ECSAs, analogous to the superior catalytic activity of hollow structured Pt NPs for methanol oxidation.3,20,27 However, if normalized by the ECSA of the catalysts, the current density of hPdNPs/C–Cl for FAOR (1.55 mA cm−2) is slightly lower than that of commercial Pd/C-JM catalyst (1.63 mA cm−2), probably due to the adsorption of Cl− and residual of AgCl on the surface of hollow structured Pd NPs, which may have negative influence on the intrinsic activity of Pd for FAOR. The enhancements in mass-based activity for FAOR can be understood as follows: since catalytic activities are measured by keeping the Pd mass constant, the lower mass densities of hollow Pd NPs means more NPs are loaded on the electrode. A higher particle loading increases the total surface area for the catalytic reactions and hence higher catalytic activities are obtained.
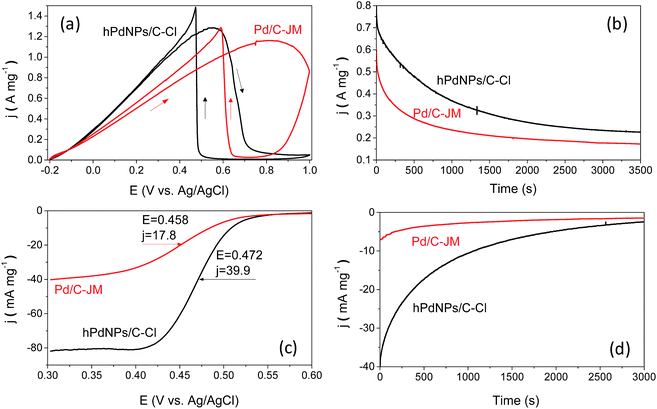 |
| Fig. 5 Cyclic voltammograms (a) and chronoamperograms at 0.2 V (b) of commercial Pd/C-JM catalyst and hPdNPs/C–Cl in 0.1 M HClO4 and 1 M formic acid at a scan rate of 50 mV s−1; negative-going linear sweep voltammograms (c) and chronoamperograms at 0.48 V (d) of commercial Pd/C-JM catalyst and hPdNPs/C–Cl in O2 saturated 0.1 M HClO4 at a scan rate of 10 mV s−1 and a rotating rate of 1600 rpm. | |
The long-term performance of hPdNPs/C–Cl and Pd/C-JM in FAOR is illustrated by the chronoamperograms in Fig. 5b. As exhibited, the current density for hPdNPs/C–Cl over the entire time is higher than that of Pd/C-JM (0.23 A mg−1 for hPdNPs/C–Cl and 0.17 A mg−1 for Pd/C-JM at the end), indicating the superior stability for hPdNPs/C–Cl as electrocatalysts for FAOR. In addition, as shown by ESI Fig. S6a,† the catalytic activity of hPdNPs/C–S for FAOR is much lower (0.06 A mg−1) than that of hPdNPs/C–Cl, which could be ascribed to the small ECSAs caused by the adsorption of poisoning S2− ions. However, after calcination at 300 °C for 1 h, the ECSAs of hPdNPs/C–S could reach 23.0 m2 g−1 (Fig. 4d), which leads to remarkable increase of the peak current density of hPdNPs/C–S for FAOR (0.2 A mg−1), as shown in ESI Fig. S6b.† This may be because thermal treatment activates the surfaces occupied by poisoning S2− ions, and renders them accessible to the catalytic reaction.
The catalytic activity of hPdNPs/C–Cl and Pd/C-JM for ORR were also examined and compared. Fig. 5c shows the negative-going linear sweep voltammograms (LSVs) in the potential range of 0.6 to 0.3 V for hPdNPs/C–Cl and Pd/C-JM catalysts in oxygen-saturated 0.1 M HClO4 at room temperature. For hPdNPs/C–Cl and Pd/C-JM, the half-wave potentials are 472 mV and 458 mV, respectively. The half-wave potential for hPdNPs/C–Cl is 14 mV more positive than that of commercial Pd/C-JM, indicating that the hPdNPs/C–Cl have higher catalytic activity in comparison with that of commercial Pd/C-JM, and the enhanced ORR activity of hPdNPs/C–Cl is again owing to the large ECSAs of the hollow structure.28 The inner surface of the hPdNPs/C–Cl is also accessible to the reactants due to the channels in the Pd shell established by the Ag removal. The chronoamperograms in Fig. 5d show that the hPdNPs/C–Cl also have better long-term performance for ORR than that of commercial Pd/C-JM catalysts.
4. Conclusions
In summary, we developed an efficient protocol for the preparation of carbon-supported Pd NPs with hollow interiors. In this strategy, bimetallic Ag@Ag–Pd NPs with an Ag core and an Ag–Pd alloy shell were synthesized in oleylamine as starting materials via GRR between Ag seed particles and Pd2+ ion precursors. The core–shell Ag@Ag–Pd NPs were then loaded in carbon supports and fluxed in acetic acid to remove the original organic surfactants for obtaining hydrophilic particle surface. The carbon-supported core–shell Ag@Ag–Pd NPs were subsequently agitated in saturated NaCl or Na2S solution to eliminate the Ag component from the core and shell regions, leading to the formation of carbon-supported Pd NPs with hollow interiors. In particular, the electrochemical measurements showed that the hollow structured Pd NPs generated by NaCl treatment exhibit superior catalytic activity and durability for formic acid oxidation reaction (FAOR) and oxygen reduction reaction (ORR), compared with the commercial Pd/C catalysts from Johnson Matthey, whereas the hollow Pd products obtained by Na2S treatment display very poor catalytic performance for same reactions.
Acknowledgements
Financial support from the 100 Talents Program of the Chinese Academy of Sciences, National Natural Science Foundation of China (Grant no.: 21173226, 21376247, 21476246), and State Key Laboratory of Multiphase Complex Systems, Institute of Process Engineering, Chinese Academy of Sciences (MPCS-2012-A-11) is gratefully acknowledged.
Notes and references
- Y. Sun, B. T. Mayers and Y. Xia, Nano Lett., 2002, 2, 481 CrossRef CAS.
- Y. Sun and Y. Xia, J. Am. Chem. Soc., 2004, 126, 3892 CrossRef CAS PubMed.
- H.-P. Liang, H.-M. Zhang, J.-S. Hu, Y.-G. Guo, L.-J. Wan and C.-L. Bai, Angew. Chem., Int. Ed., 2004, 43, 1540 CrossRef CAS PubMed.
- J. Chen, B. Wiley, J. McLellan, Y. Xiong, Z.-Y. Li and Y. Xia, Nano Lett., 2005, 5, 2058 CrossRef CAS PubMed.
- M. Chen and L. Gao, Inorg. Chem., 2006, 45, 5145 CrossRef CAS PubMed.
- H. M. Chen, R.-S. Liu, M.-Y. Lo, S.-C. Chang, L.-D. Tsai, Y. M. Peng and J.-F. Lee, J. Phys. Chem. C, 2008, 112, 7522 CAS.
- S. E. Skrabalak, J. Chen, Y. Sun, X. Lu, L. Au, C. M. Cobley and Y. Xia, Acc. Chem. Res., 2008, 41, 1587 CrossRef CAS PubMed.
- H. Zhang, M. Jin, J. Wang, W. Li, P. H. C. Camargo, M. J. Kim, D. Yang, Z. Xie and Y. Xia, J. Am. Chem. Soc., 2011, 133, 6078 CrossRef CAS PubMed.
- M. Mohl, D. Dobo, A. Kukovecz, Z. Konya, K. Kordas, J. Wei, R. Vajtai and P. M. Ajayan, J. Phys. Chem. C, 2011, 115, 9403 CAS.
- E. González, J. Arbiol and V. F. Puntes, Science, 2011, 334, 1377 CrossRef PubMed.
- Q. Zhang, J. Y. Lee, J. Yang, C. Boothroyd and J. Zhang, Nanotechnology, 2007, 18, 245605 CrossRef.
- J. Yang, E. H. Sargent, S. O. Kelley and J. Y. Ying, Nat. Mater., 2009, 8, 683 CrossRef CAS PubMed.
- H. Liu, J. Qu, Y. Chen, J. Li, F. Ye, J. Y. Lee and J. Yang, J. Am. Chem. Soc., 2012, 134, 11602 CrossRef CAS PubMed.
- D. Chen, P. Cui, H. He, H. Liu and J. Yang, J. Power Sources, 2014, 272, 152 CrossRef CAS PubMed.
- M. Łukaszewski, K. Klimek and A. Czerwiński, J. Electroanal. Chem., 2009, 637, 13 CrossRef PubMed.
- Y. Sun and Y. Xia, Nano Lett., 2003, 3, 1569 CrossRef CAS.
- S. Chen, B. D. Adams and A. Chen, Electrochim. Acta, 2010, 56, 61 CrossRef CAS PubMed.
- B. Wiley, T. Herricks, Y. Sun and Y. Xia, Nano Lett., 2004, 4, 1733 CrossRef CAS.
- R. D. Glover, J. M. Miller and J. E. Hutchison, ACS Nano, 2011, 5, 8950 CrossRef CAS PubMed.
- H. Liu, F. Ye and J. Yang, Ind. Eng. Chem. Res., 2014, 53, 5925 CrossRef CAS.
- W. F. McClune, Powder diffraction file alphabetical index inorganic phase. JCPDS, Swarthmore, PA, 1980 Search PubMed.
- Y. Tong, X. F. Lu, W. N. Sun, G. D. Nie, L. Yang and C. Wang, J. Power Sources, 2014, 261, 221 CrossRef CAS PubMed.
- M. J. Ren, J. Chen, Y. Li, H. F. Zhang, Z. Q. Zou, X. M. Li and H. Yang, J. Power Sources, 2014, 246, 32 CrossRef CAS PubMed.
- W. J. Wen, C. Y. Li, W. P. Li and Y. Tian, Electrochim. Acta, 2013, 109, 201 CrossRef CAS PubMed.
- T. J. Vidaković, M. H. Christov and K. Sundmacher, Electrochim. Acta, 2007, 52, 5606 CrossRef PubMed.
- D. S. Wu, Z. L. Zheng, S. Y. Gao, M. N. Cao and R. Cao, Phys. Chem. Chem. Phys., 2012, 14, 8051 RSC.
- J. Yang, J. Y. Lee, H.-P. Too and S. Valiyaveettil, J. Phys. Chem. B, 2006, 110, 125 CrossRef CAS PubMed.
- Y.-B. Cho, J. E. Kim, J. H. Shim, C. Lee and Y. Lee, Phys. Chem. Chem. Phys., 2013, 15, 11461 RSC.
Footnote |
† Electronic supplementary information (ESI) available: XRD patterns of Ag seeds, Pd NPs synthesized in oleylamine in the absence of Ag seeds, core–shell Ag@Ag–Pd NPs, hPdNPs/C–Cl, and hPdNPs/C–S, TEM image of Ag seeds, Ag@Ag–Pd NPs/C, and commercial Pd/C-JM catalysts, XPS spectra of Pd NPs synthesized in oleylamine in the absence of Ag seeds, core–shell Ag@Ag–Pd NPs, hPdNPs/Cl, and hPdNPs/C–S, Cyclic voltammograms of hPdNPs/C–S and hPdNPs/C–S after calcination. See DOI: 10.1039/c4ra14353a |
|
This journal is © The Royal Society of Chemistry 2015 |