DOI:
10.1039/C4RA13582B
(Paper)
RSC Adv., 2015,
5, 5343-5356
Enhanced water retention and proton conductivity of proton exchange membranes by incorporating hollow polymer microspheres grafted with sulfonated polystyrene brushes†
Received
1st November 2014
, Accepted 4th December 2014
First published on 4th December 2014
Abstract
Hollow polymer microspheres grafted with sulfonated polystyrene brushes (HPSS) were synthesized via a combination of surface-initiated atom transfer radical polymerization (SI-ATRP) of styrene from SiO2@P(MAA-co-DVB-co-CMSt) core–shell microspheres, sulfonation of the polystyrene brushes, and final removal of the silica core. These HPSSs were then incorporated into a sulfonated poly(ether ether ketone) (SPEEK) matrix to fabricate hybrid membranes. As a comparison, SPEEK/HPS hybrid membranes were prepared by incorporation of sulfonated hollow polymer microspheres (HPS) into a SPEEK matrix. Water retention, methanol resistance and proton conductivity were increased by doping with both kinds of hollow polymer microspheres. The SPEEK/HPSS hybrid membranes exhibited much higher proton conductivity than did the SPEEK/HPS hybrid membranes with the same filler contents ranging from 2.5 to 15 wt%. The highest conductivity was obtained at 0.33 S cm−1 for SPEEK/HPSS under 75 °C and 100% relative humidity (RH), which was 83.3% higher than that (0.18 S cm−1) for a SPEEK control membrane under the same conditions. The increment in proton conductivity was mainly attributed to the large cavities of HPSS acting as water reservoirs, and the excellent flexibility and high accessibility of the sulfate groups (–SO3H) on the surface grafted polymer brushes, which provide proton hopping sites for proton-conducting pathways. Moreover, the hybrid membranes exhibited good thermal and mechanical stability.
1 Introduction
Direct methanol fuel cells (DMFC) have received great attention because of their high energy-conversion efficiency, high power density and environmentally friendly features.1–3 One of the most important components of DMFC, the proton exchange membrane (PEM) transfers protons and separates the fuel and the oxidant on the anode and cathode sides.4–6 The PEM should be a methanol-barrier and have excellent proton conductivity, along with long-term stability for its application in DMFC.7,8 Among others, sulfonated poly(ether ether ketone) (SPEEK) has recently attracted considerable attention as a PEM because of its low cost, good thermal stability and mechanical strength.9,10 SPEEK membranes have increasing proton conductivity and water uptake with enhancing degree of sulfonation (DS).11 However, high DS can lead to high water uptake by SPEEK, resulting in deterioration of mechanical strength and relatively high methanol permeability.12,13
Different methods have been investigated to improve the stability of SPEEK with high proton conductivity and water uptake at relatively low DS and low humidity conditions, including covalent crosslinking14 and blending with inorganic or organic fillers.15,16 Incorporation of fillers bearing functional groups (mainly sulfonic acid group (–SO3H), phosphoric acid group (–PO3H2) and carboxylic acid group (–COOH)) can enhance the proton conductivity and water retention of the hybrid membranes, and block fuel permeation.17,18 To date, the –SO3H group has been the most widely used as proton conductivity site for its superior proton conductive capacity compared with the –COOH and –PO3H2 groups.19–21 Gosalawit et al.22 reported a 4-fold increase of proton conductivity and about 30% decrease in methanol permeability of SPEEK membranes after embedding sulfonated montmorillonite. However, the number of functional sulfonic groups was very low because of the low reactivity of the inorganic fillers for surface modification, which limited the further improvement of proton conductivity of PEM composites.23,24
More recently, hollow polymer microspheres have shown potential as drug carriers, absorbent materials and microreactors.25,26 Template-directed synthesis, especially using the hard template method, is widely used to prepare hollow polymer microspheres, which are usually fabricated by coating the template with a polymer shell of the desired materials and subsequent removal of the template.27–29 Inspired by the water storage mechanisms in plant cells and the proton transfer mechanism, hydrophilic hollow polymer microspheres bearing different functional groups, such as –SO3H and –CO2H groups, may be promising candidate materials for preparation of hybrid membranes.30–32 The large cavity of the hollow sphere can serve as a water reservoir to allow high water uptake, which can facilitate proton transfer by the vehicle mechanism, especially under low humidity.33 Meanwhile, the functional groups of the polymer shell can immobilize water molecules and provide proton conductive sites as hopping protons according to the Grotthuss mechanism.34 In addition, the flexibility of the polymer shell improves interfacial compatibility with the polymer membrane matrix. Wang et al. reported that incorporation of carboxylic acid microcapsules into a chitosan matrix dramatically enhanced water retention properties to result in a proton conductivity for the composite membrane 14-fold that of a chitosan control membrane under 20% RH.30 Pu et al. prepared Nafion-based hybrid membranes by incorporating sulfonated hollow polystyrene nanospheres into Nafion, which enhanced the water retention and proton conductive capacity of the hybrid membranes even when the temperature increased to 110–120 °C.35 All these results imply potential applications for hollow polymer microspheres as a component of PEM.
In our previous works, a series of polymer microcapsules bearing different functional groups were embedded into matrix membranes to enhance their water retention and proton conductivity.36–38 However, because of the high degree of crosslinking of the polymer shell, the mobility of the macromolecular chains was significantly restrained, which might block proton transfer and lower water diffusion through PEM. Herein, a novel hollow poly(methacrylic acid-co-divinylbenzene-co-chloromethyl styrene) microsphere grafted with sulfonated polystyrene brushes (P(MAA-co-DVB-co-CMSt)-g-PSt-SO3H, HPSS) was prepared by a combination of precipitation polymerization and surface initiated atom transferring radical polymerization of styrene (SI-ATRP), together with sulfonation of PSt brush and final removal of the silica core by HF. The HPSSs were then incorporated into a SPEEK matrix to fabricate SPEEK/HPSS hybrid membranes. To investigate the role of the sulfonated polystyrene brush, the SPEEK/HPS hybrid membranes were prepared by incorporation of hollow sulfonated polymer microspheres with SPEEK matrix. Successful synthesis of HPSS microspheres was confirmed by TEM, FT-IR and TGA. The performance of the hybrid membranes was investigated at high temperature and low humidity, including water retention, swelling behavior, methanol permeability and proton conductivity.
2 Experimental
2.1 Materials
Tetraethyl orthosilicate (TEOS, 98%), 3-(methacryloxy) propyl trimethoxysilane (MPS) and 2,2-bipyridine (bpy) were purchased from Alfa Aesar and used without further purification. Methacrylic acid (MAA, analytical grade) was purchased from Tianjin Chemical Reagent II Co. and purified by vacuum distillation before use. Divinylbenzene (DVB, 80% divinylbenzene isomers, Alfa Aesar) was purified by washing with 5% aqueous sodium hydroxide and water three times to remove the inhibitor, then dried over anhydrous magnesium sulfate prior to utilization. 4-Chloromethylstyrene (CMSt) was purchased from Acros. 2,2′-Azobisisobutyronitrile (AIBN) was provided by Chemical Factory of Nankai University and recrystallized from methanol. Styrene (St, analytical grade) was purchased from Tianjin Chemical Reagent II Co. and purified by washing with 5% aqueous sodium hydroxide and water three times, drying over anhydrous magnesium sulfate and distilling under reduced pressure. CuCl (Tianjin Chemical Reagent II Co.) was purified by stirring in glacial acetic acid, washed with methanol, and then dried in a vacuum oven. Toluene was purchased from Tianjin Chemical Reagent II and purified by distillation in presence of sodium. Ammonium hydroxide (25 wt%), hydrofluoric acid (HF, 40 wt%), N,N-dimethylformamide (DMF) and sulfuric acid (94%) were obtained from Tianjin Chemical Reagent III Co. Poly(ether ether ketone) (PEEK) Virtrex 381 G was supplied by Nanjing Yuanbang Engineering Plastics Co., Ltd. Deionized water was used throughout all the experiments. All other reagents were used without further purification.
2.2 Preparation of monodisperse SiO2@P(MAA-co-DVB-co-CMSt) core–shell microspheres
Monodisperse MPS-modified silica (SiO2-MPS) microspheres were prepared through a modified Stöber method via a sol–gel process according to the literature.39 240 mL of ethanol, 30 mL of deionized water and 6 mL of ammonium hydroxide were added to a 500 mL of round flask and stirred at room temperature for 30 min. Then, a mixture of 18 mL of TEOS and 60 mL of ethanol were added to the above mixture solution. After 24 h, 2.0 mL of MPS was dropped into the mixture solution and stirred for another 24 h. The resultant MPS-SiO2 microspheres were collected by centrifugation and washed with ethanol three times, and finally dried in a vacuum oven till constant weight.
The silica@poly(methacrylic acid-co-divinylbenzene-co-4-chloromethylstyrene) (SiO2@P(MAA-co-DVB-co-CMSt)) core–shell microspheres were synthesized by two-stage precipitation copolymerization of MAA, DVB and CMSt monomers with the MPS-SiO2 microspheres as seeds. The details were as follows: 0.40 g of MPS-SiO2 seeds, 0.80 mL of MAA, 0.32 mL of DVB, 0.48 mL of CMSt and 0.032 g of AIBN (2 wt% relative to co-monomers) were dissolved in 160 mL of acetonitrile in a 250 mL flask. The flask attached to a Liebig condenser was submerged in a heating mantle. The reaction mixture was heated from ambient room temperature to boiling within 15 min and then kept refluxing for 2 h. After the first-stage polymerization, the resultant SiO2@P(MAA-co-DVB-co-CMSt) core–shell microspheres were utilized as seeds for the second-stage polymerization. The second-stage polymerization procedure was the same as for the first. After the polymerization, the SiO2@P(MAA-co-DVB-co-CMSt) core–shell microspheres were purified by repeating centrifugation, decantation and resuspension in ethanol three times, and dried in a vacuum oven till constant weight.
2.3 Preparation of SiO2@P(MAA-co-DVB-co-CMSt)-g-PSt microspheres
Surface-initiated atom transfer radical polymerization (SI-ATRP) was carried out to prepare the SiO2@P(MAA-co-DVB-co-CMSt)-g-PSt microspheres. The details were as follows: 0.60 g of SiO2@P(MAA-co-DVB-co-CMSt) microspheres, 0.064 g of bpy (0.41 mmol), 3.60 mL of styrene (31.3 mmol) were dispersed in 2.80 mL of toluene in a 25 mL Schlenk flask. The flask was immersed once in liquid nitrogen for degassing. Then, 0.02 g of CuCl (0.2 mmol) was added to the dispersion under an argon atmosphere. Then, the solution was degassed by three freezing–pumping–thawing cycles. SI-ATRP of styrene was conducted at 110 °C for 6 h with vigorous stirring. The polymerization was stopped by exposure of the solution to air. The resultant SiO2@P(MAA-co-DVB-co-CMSt)-g-PSt microspheres were purified by repeating centrifugation, decantation and resuspension in ethanol and deionized water three times and finally dried in a vacuum oven till constant weight.
2.4 Preparation of hollow P(MAA-co-DVB-co-CMSt)-g-PSt-SO3H (HPSS) microspheres
The resultant SiO2@P(MAA-co-DVB-co-CMSt)-g-PSt microspheres were sulfonated by concentrated sulfuric acid (94%). A typical procedure was as follows: 0.60 g of the SiO2@P(MAA-co-DVB-co-CMSt)-g-PSt microspheres were dispersed in 21.0 mL of H2SO4 (94%) at 50 °C for 6 h under vigorous stirring, and purified by centrifugation and washed with ethanol and deionized water three times and finally dried in a vacuum oven till constant weight.
Subsequently, the as-prepared microspheres were etched by excessive hydrofluoric acid aqueous solution (HF, 40 wt%) to completely remove the silica core. The details were as follows: 0.60 g of SiO2@P(MAA-co-DVB-co-CMSt)-g-PSt-SO3H microspheres were dissolved in 15 mL of ethanol, then 12 mL of HF solution was added to the mixture. After being stirred for 4 h, the resultant hollow P(MAA-co-DVB-co-CMSt)-g-PSt-SO3H (HPSS) microspheres were purified by several cycles of centrifugation and washed with ethanol and finally dried in a vacuum oven till constant weight.
2.5 Preparation of hollow P(MAA-co-DVB-co-CMSt)-SO3H (HPS) microspheres
The process for preparation of the hollow P(MAA-co-DVB-co-CMSt)-SO3H (HPS) microspheres was as follows. The SiO2@P(MAA-co-DVB-co-CMSt) core–shell microspheres were sulfonated by sulfuric acid (94%). The silica core of the resultant microspheres was similarly etched by HF aqueous solution to form a hollow structure.
2.6 Preparation of SPEEK
Prior to sulfonation, poly(ether ether ketone) (PEEK) was dried at 80 °C for 24 h followed by dissolving in concentrated sulfuric acid (95–98 wt%) with vigorous stirring at 25 °C for 4 h and at 45 °C for another 8 h. Then the dark red solution was decanted into an ice-water bath to stop the sulfonation. The SPEEK was washed with de-ionized water until it reached pH 7, and then dried at room temperature for 24 h and then at 60 °C for another 24 h in a vacuum oven. The degree of sulfonation (DS) of SPEEK was determined by acid–base titration to be 64%.
2.7 Preparation of the membranes
The hybrid membrane was fabricated by the solution-casting method.40 0.35 g of SPEEK was dispersed in 3.5 mL of DMF and stirred vigorously for 12 h at room temperature. Then, a certain amount of HPS microspheres or HPSS microspheres were suspended in the above mixture solution and stirred vigorously for another 12 h to form a homogenous solution. After degassification, the resultant solution was cast onto a glass plate and dried at 60 °C in a vacuum oven for 12 h, and then at 80 °C for another 12 h. After cooling down to room temperature, the membrane was peeled from the glass plate. Then, the hybrid membrane was immersed in 2.0 M H2SO4 solution for 48 h and rinsed with deionized water until it reached pH 7, and dried in a vacuum oven for 24 h. The as-prepared membranes were designed as SPEEK/HPS-X or SPEEK/HPSS-X, where X (X = 2.5, 5, 10 or 15) was the weight percentage of the HPS microspheres or HPSS microspheres to SPEEK. The pristine SPEEK membrane was fabricated using a similar method.
2.8 Characterization
The morphology of the resultant nanoparticles was determined by transmission electron microscopy (TEM) using a JEM 100 CII microscope. The size and size distribution reflect averages of about 100 particles each, calculated according to the following formulae: |
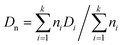 | (2) |
|
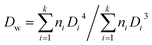 | (3) |
where U is the polydispersity index, Dn is the number average diameter, Dw is the weight-average diameter, and Di is the diameter of the determined microspheres. The thickness of the shell layer is calculated as half of the difference between the average diameter of the core–shell particles and that of the cores.
The microstructure of the membrane cross-section was observed by field emission scanning electron microscopy (FESEM, JSM7500F) after being freeze-fractured in liquid nitrogen and then sputtered with gold.
Fourier transform infrared spectra (FT-IR) were determined on a Bio-Rad FTS 135 FT-IR spectrometer over potassium bromide pellet, and the diffusion reflectance spectra were scanned over the range 4000–400 cm−1.
The thermal stability of the microspheres and hybrid membranes was conducted by thermogravimetric analysis (TGA) from 30 to 800 °C with a heating rate of 10 °C min−1 using a TA TGA-2950 apparatus. Differential scanning calorimetry (DSC) was carried out on a DSC, Netzsch 204 F1 instrument with a heating or cooling rate of 10 K min−1 in N2 flow to determine the glass transition temperature (Tg) of the membranes.
The sulfur content in the microspheres was measured using an Inductively Coupled Plasma Optical Emission Spectrophotometer (ICP-9000 (N + M), USA Thermo Jarrell-Ash Corp.).
2.9 Water uptake, swelling, water release and water retention
Prior to measurement, the microspheres and the membranes were dried in an oven at 60 °C for 24 h and the weight (Wdry) and area (Adry) were measured. Then, the samples were immersed in deionized water for 24 h at room temperature. After being completely hydrated, the weight (Wwet) and area (Aarea) of the membranes were measured. The final value of the water uptake and area swelling were taken as an average of three measurements and calculated using the following equations: |
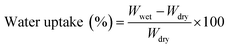 | (4) |
|
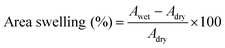 | (5) |
Immediately after the water uptake measurement, the wet hybrid membranes were placed in a climate box, which was maintained at 40 °C and 20% room humidity (RH). The sample weights (Wwet) were measured at 3 min intervals in a climate box. The water release and water retention were calculated using the following equations:
|
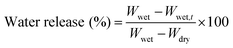 | (6) |
|
 | (7) |
2.10 Proton conductivity
The proton conductivity of all the membranes was measured in a two-point-probe conductivity cell using the AC impedance spectroscopy method. The membrane resistance was measured using a frequency response analyzer (FRA, Compactstat, IVIUM Tech.) with an oscillating voltage of 20 mV in a frequency range of 1 to 106 Hz. The relative humidity was kept at 100% and the testing temperature was controlled by the water vapor from 25 °C to 80 °C. The membrane resistance was measured at 5 °C intervals. Proton conductivity of the membranes was also tested under low humidity at high temperature (65 °C), for which the various degrees of low humidity were maintained via holding a saturated salt (K2CO3, 41%, NaNO2 (57%) and KBr (78%)) container in the chamber. The proton conductivity (σ, S cm−1) of the membrane was calculated as follows: |
 | (8) |
in which l is the distance between the two electrodes (cm), A is the cross-section area of the testing membrane (cm2), and R is the membrane resistance from FRA (Ω).
2.11 Methanol permeability
Methanol permeability of the membranes was investigated using a glass diffusion cell consisting of two compartments of identical volume separated by a membrane sheet. The membrane was fully hydrated in deionized water for 24 h and then clamped tightly between two compartments. The two compartments were then filled with deionized water and 2.0 M of a methanol solution, respectively. The concentration of methanol that permeated into the water compartment was detected using a gas chromatograph (Agilent 6820) equipped with a Thermal Conductivity Detector (TCD) and a DB624 column. The methanol permeability (P, cm2 s−1) was calculated as follows: |
 | (9) |
where S is the slope of the straight line of methanol concentration in compartment B versus time (mol L−1 s−1), VB is the solution volume of compartment B (L), and l, A and CA0 are the membrane thickness (cm), effective membrane areas (cm2), and the initial methanol concentration in compartment A (mol L−1), respectively.
3 Results and discussion
3.1 Synthesis of hollow polymer microspheres
The preparation process of the hollow P(MAA-co-DVB-co-CMSt)-g-PSt-SO3H (HPSS) and hollow P(MAA-co-DVB-co-CMSt)-SO3H (HPS) microspheres is shown in detail in Scheme 1. First, functional SiO2@P(MAA-co-DVB-co-CMSt) core–shell microspheres with active groups (phenyl and benzyl chloride group) were synthesized by two-stage precipitation copolymerization of 4-chloromethylstyrene (CMSt) as the functional monomer, methacrylic acid (MAA) as the comonomer, divinylbenzene (DVB) as cross linker and 2,2′-azobisisobutyronitrile (AIBN) as initiator in the presence of MPS-modified SiO2 microspheres as the seeds. Precipitation polymerization, with the outstanding advantage of the absence of any stabilizer in the polymerization process, provides a simple and highly efficient protocol for preparation of various uniform and clean polymer particles, such as microspheres, core–shell particles, rattle-type particle, and double-shell hollow particles.41,42 In this work, the vinyl groups on the silica particle surface helped to form a polymer shell by radical capture of monomers and oligomers during precipitation polymerization to obtain silica/polymer core–shell microspheres.43 Then, the polystyrene brush on the surface of the core–shell microspheres was synthesized via surface-initiated atom transfer radical polymerization (SI-ATRP), in which the residual surface benzyl chloride group (–C6H4–CH2Cl) was used as the ATRP initiator, and then sulfonated by concentrated sulfuric acid. In the last two decades, SI-ATRP has been proven to be a versatile technique for synthesis of uniform polymer brushes.44,45 However, these SI-ATRP systems still require several time-consuming steps under specific conditions, in which surface modification is necessary to incorporate initiator sites for ATRP. Herein, the SI-ATRP initiator groups (–C6H4–CH2Cl) were facilely anchored on the surface during synthesis of P(MAA-co-DVB-co-CMSt) via precipitation polymerization. Finally, the silica core was selectively removed by HF aqueous solution to obtain HPSS microspheres. Meanwhile, the phenyl group on the surface and gel layer of the core–shell microsphere was sulfonated directly by concentrated sulfuric acid, and then the SiO2 core was etched by HF solution to form HPS microspheres.
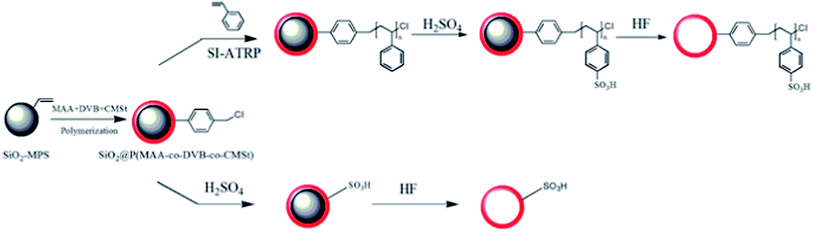 |
| Scheme 1 The process of synthesis of HPSS and HPS microspheres. | |
A TEM image of the MPS-modified SiO2 microspheres is shown in Fig. 1a, exhibiting a spherical shape and smooth surface with average diameter of about 260 nm. The corresponding FT-IR spectrum is shown in Fig. 2a. The strong absorption peak at 1100 cm−1 was attributed to asymmetrical vibration of the Si–O–Si group. The absorption peak at 1642 cm−1 was attributed to vibration of vinyl and carbonyl groups of the MPS component, respectively. After a two-stage precipitation polymerization of comonomers in the presence of MPS-SiO2 as seeds, polymer shells with a thickness of about 22 nm were coated uniformly without any aggregation, as shown in Fig. 1b. A typical core–shell structure can be observed clearly, with a deep contrast silica core and a light contrast polymer shell. Encapsulation of polymer shell on the silica core was further investigated in a FT-IR spectrum, shown in Fig. 2b. The strong adsorption peak at 1730 cm−1 was attributed to stretching vibration of the carboxylic acid group of the PMAA component. The new absorption peaks at 1458, 1510, 1615 and 700 cm−1 were typical of absorption of the phenyl group in the shell layer. A TEM image of SiO2@P(MAA-co-DVB-co-CMSt)-g-PSt microspheres is shown in Fig. 1c. Because the polystyrene brush layer had a similar mass contrast to the P(MAA-co-DVB-co-CMSt) shell because of their similar composition, it was difficult to distinguish the grafted polystyrene brushes from the shell layer via the simple observation of contrast from TEM. However, the total thickness of polymer shell was increased from 22 nm to 38 nm, which meant that the polystyrene brush was successfully grafted from the surface of the core–shell microspheres and the polystyrene shell thickness was about 16 nm. The corresponding FT-IR spectrum is shown in Fig. 2c. The absorption peaks at 1458, 1510, 1615 and 700 cm−1 attributed to the phenyl group, were stronger than that of the core–shell microspheres, indicating successful SI-ATRP. After sulfonation by H2SO4, the FT-IR spectrum of SiO2@P(MAA-co-DVB-co-CMSt)-g-PSt-SO3H (Fig. 2d) exhibited new peaks at 1180 and 1010 cm−1, corresponding to stretching vibration of O
S
O in the –SO3H group. The TEM image and FT-IR spectrum of the HPSS microspheres are illustrated in Fig. 1d and 2e, respectively. As shown in Fig. 2e, the disappearance of the strong wide peak at 1100 cm−1 assigned to the silica core implied that the silica was successively removed via the etching process. As directly observed in Fig. 1d, the HPSS microspheres maintained a uniform integrated hollow spherical shape with a slight collapse. The HPS microspheres (Fig. 1e) exhibited a clear hollow spherical structure with few cracks. The HP microspheres were fabricated by directly removing the silica core of the core–shell microspheres with obviously deformed structure as shown in Fig. 1f, which may have occurred because of the thin polymer shell and the slightly swollen P(MAA-co-DVB-co-CMSt) shell with hydrophilicity.
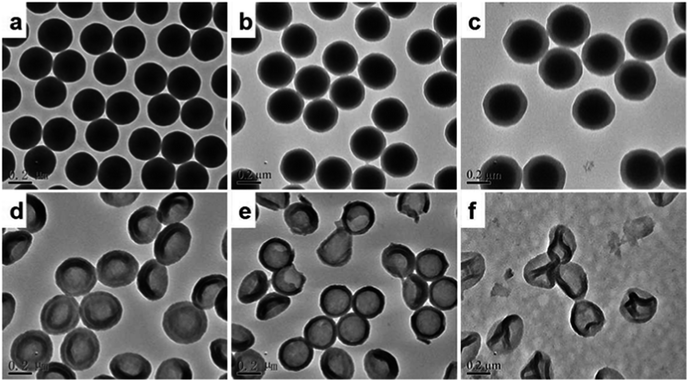 |
| Fig. 1 TEM images: (a) MPS-SiO2 microspheres; (b) SiO2@P(MAA-co-DVB-co-CMSt) core–shell microspheres; (c) SiO2@P(MAA-co-DVB-co-CMSt)-g-PSt microspheres; (d) hollow P(MAA-co-DVB-co-CMSt)-g-PSt-SO3H (HPSS) microspheres; (e) hollow P(MAA-co-DVB-co-CMSt)-SO3H (HPS) microspheres; and (f) hollow P(MAA-co-DVB-co-CMSt) (HP) microspheres (scale bars = 200 nm). | |
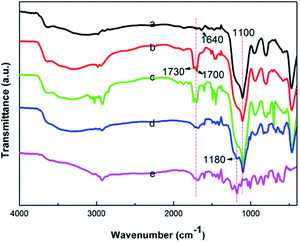 |
| Fig. 2 FT-IR spectra: (a) SiO2-MPS microspheres; (b) SiO2@P(MAA-co-DVB-co-CMSt) core–shell microspheres; (c) SiO2@P(MAA-co-DVB-co-CMSt)-g-PSt microspheres; (d) SiO2@P(MAA-co-DVB-co-CMSt)-g-PSt-SO3H microspheres; and (e) HPSS microspheres. | |
Thermogravimetric analysis (TGA) measurements were determined for further demonstration of the successful synthesis of these microspheres, as shown in Fig. S1.† Generally, all three samples exhibited a two-stage weight loss process when the samples were heated from 25 °C to 800 °C. The first weight loss stage to 200 °C was attributed to desorption of the physically adsorbed water and solvent. The second major weight loss stage from 250 °C to 500 °C was attributed to decomposition of the polymer component of SiO2@P(MAA-co-DVB-co-CMSt) or SiO2@P(MAA-co-DVB-co-CMSt)-g-PSt microspheres. The weight loss of core–shell microspheres was about 35.4%. After SI-ATRP of styrene on the core–shell microspheres, weight loss was increased to about 49.6%, which meant the mass percentage of polystyrene (PSt) brush was about 14.2%. This was consistent with results from the corresponding TEM images. Inductive coupled plasma (ICP) was carried out to determine the content of sulfur (S) as 10.5% and 3.6% for HPSS and HPS microspheres, respectively, which meant that the loading capacities of the sulfonic acid group were 3.3 and 1.1 mmol g−1, respectively. The content of –SO3H group of HPSS microspheres was almost twice that of the HPS microspheres. The increment of S content was attributed to the large amount of phenyl groups resulting from grafting of polystyrene brushes on the core–shell microspheres. To some extent, it is unavoidable that the P(MAA-co-DVB-co-CMSt) shells were partially sulfonated by concentrated H2SO4. From the above characterizations, schematic depictions of the possible chemical structure of the HPS and HPSS microspheres are illustrated in Fig. 3.
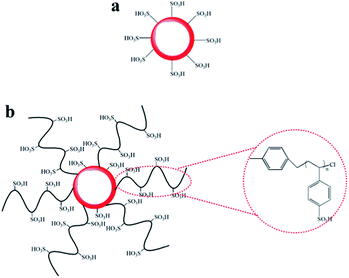 |
| Fig. 3 Schematic depiction of chemical structures: (a) HPS; and (b) HPSS. | |
3.2 Water release and water retention of HPSS and HPS microspheres
In our previous works,30,31,38 a series of polymer microcapsules and double-shell hollow spheres were designed as water reservoirs within membranes to enhance the water retention properties of those membranes. The large lumen and elastic hydrophilic polymer shell with numerous micro-channels and many different functional groups, such as carboxylic acid, sulfonic acid and pyridyl groups, provides high water uptake and low water release under low relative humidity. In this work, a hollow polymer microsphere grafted with sulfonated polystyrene brushes (HPSS) was prepared. HPSS exhibited the highest water uptake and the lowest water release rate compared with HP and HPS microspheres.
The initial water uptakes of HPSS, HPS and HP microspheres were 161%, 139% and 127%, respectively. The superior water uptake can be attributed to the large lumens and the incorporation of –SO3H groups on the surface of the polymer shells and at the side chains of polystyrene brushes. The high water binding energy (44.4 kJ mol−1) and low average zero point energy (69.9 kJ mol−1) for the –SO3H group implies high water retention and low proton conduction barrier.46 Furthermore, about four water molecules were bound tightly with one sulfonic acid group.47 Therefore, the HPSS microspheres, bearing more –SO3H groups, displayed the highest water uptake in these three samples with similar structure and composition, as depicted in Fig. S2a,† which was consistent with the content of sulfur element (S, 3.3 mmol g−1). Besides water uptake, the release rate of absorbed water was another significant parameter for investigation of water retention properties. As shown in Fig. S2b,† linear dynamic water release from HPSS, HPS and HP microspheres was observed at 40 °C and 20% RH. The slope (S) indicates the water release rate. Compared with the HP microspheres (S = 0.081) and HPS microspheres (S = 0.063), the water release rate of HPSS microspheres (S = 0.037) was the lowest. There are two main reasons for this. The first is that the polymer shell prevented the absorbed water within the confined lumen from being released. The second is that the hydrogen bond interaction between water molecules and the sulfonic acid groups in the polymer shell inhibited the water release. Moreover, these three kinds of microspheres lost only 58.5%, 44.2% and 38.6% of the initially absorbed water, even after testing in the determination condition for 700 min. Water retention is evaluated by both water uptake and water release behavior. In Fig. S2a,† the slope (S) indicates the water retention capability. The water retention decrease rate of the HPSS microspheres (S = 0.0870) was slightly lower than that of the HPS microspheres (S = 0.0877). Such a result indicates that the large lumen has a key role in the water retention behaviors of these three samples. The HPSS microspheres exhibited the best water retention because of the highest water uptake and the slowest water release.
3.3 Characterization of the hybrid membranes
All three types of hollow polymer microspheres (HPSS, HPS and HP) were embedded into SPEEK matrix to prepare hybrid membranes via a solution coating method. The internal microstructure and distribution of the hollow polymer microspheres containing various contents within the SPEEK matrix were investigated by FESEM micrographs, shown in Fig. 4. All the hybrid membranes were relatively dense with uniform shape. The hollow microspheres maintained the pristine structure and dispersed homogeneously without any agglomeration with the SPEEK matrix, which was mainly attributed to the excellent compatibility between the sulfonic acid groups of the HPSS (or HPS) microspheres and those of the SPEEK matrix.
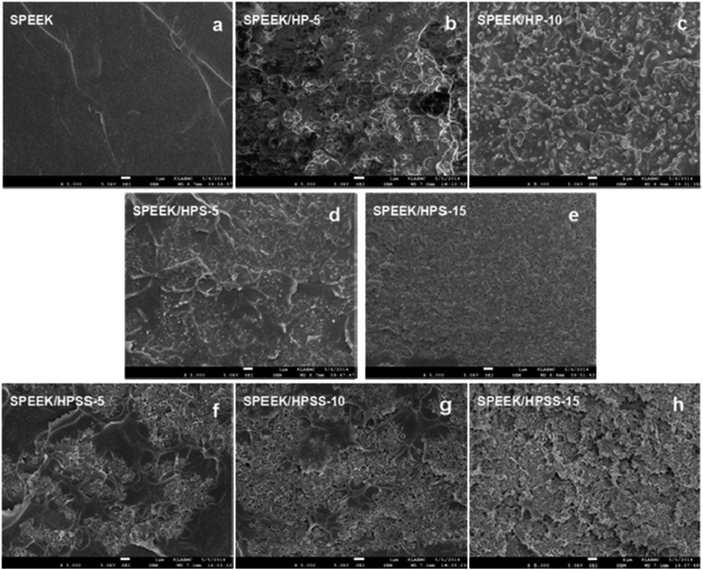 |
| Fig. 4 FESEM images of the cross-section of the pristine SPEEK membrane and the SPEEK hybrid membranes: (a) SPEEK; (b) SPEEK/HP-5; (c) SPEEK/HP-15; (d) SPEEK/HPS-5; (e) SPEEK/HPS-15; (f) SPEEK/HPSS-5; (g) SPEEK/HPSS-10; and (h) SPEEK/HPSS-15. (Scale bars = 1 mm). | |
The chemical composition of the hybrid membranes was determined by FT-IR spectra, as shown in Fig. 5. The characteristic absorption peaks at 1215, 1070 and 1024 cm−1 attributed to the symmetric and asymmetric stretching vibration of O
S
O in the sulfonic acid group were found in SPEEK membranes, thus demonstrating the successful sulfonation of the SPEEK. Compared with SPEEK membrane, all three hybrid membranes had a new absorption peak around 1710 cm−1 corresponding to the stretching vibration of the carbonyl group of the three hollow microspheres.
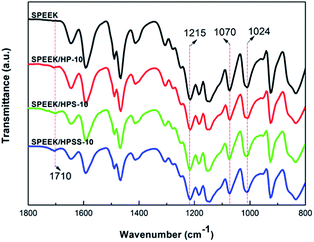 |
| Fig. 5 FT-IR curves of the pristine SPEEK, SPEEK/HP-10, SPEEK/HPS-10 and SPEEK/HPSS-10 hybrid membranes. | |
The thermal stability of the pristine SPEEK control membrane and the hybrid membranes was investigated by TGA measurement, as shown in Fig. S3.† All membranes had a similar decomposition profile with a three-stage weight loss process when the membranes were heated from room temperature to 750 °C. The first weight loss until 200 °C was attributed to evaporation of the physically absorbed water. The second weight loss stage ranging from 240 to 370 °C was assigned to the decomposition of the sulfonic acid group. The final weight loss ranging from 400 to 750 °C was related to decomposition of the polymer backbone of the SPEEK matrix and the hollow microspheres. It could be observed from TGA results that the residual mass of the hybrid membranes (e.g. 48.3–46.2% for the SPEEK/HPSS-X membranes) was lower than that of the pristine SPEEK membrane (48.9%) because of incorporation of the HPSS microspheres. Notably, all as-prepared membranes were thermally stable up to 260 °C, which is adequate for practical applications of fuel cells.
The glass transition temperature (Tg) of the pristine and hybrid membranes was characterized by DSC, as summarized in Table S1.† The Tg of the pristine SPEEK membrane was 216 °C, consistent with that reported in literature.48 After incorporation of HPS into HPSS microspheres, the glass transition temperatures of the corresponding hybrid membranes were decreased obviously to 178–184 and 182–190 °C, dependent on the incorporated hollow spheres. These mainly originated from the enhanced flexibility and mobility of the pristine SPEEK polymer chain after introduction of hollow microspheres into hybrid membranes. The Tg of SPEEK/HPSS-X membranes increased from 182 to 190 °C, with the filler content (X) increasing from 2.5 to 15%, which was attributed to good compatibility between the pendant –SO3H groups on the surface of HPSS microspheres and the same groups in the SPEEK matrix. The same tendency (178–184 °C) was also observed for SPEEK/HPS membranes (5–15% filler). However, a new Tg appeared at temperatures ranging from 134 to 145 °C, which were highly dependent on the loading amount and types of hollow polymer microspheres in these hybrid membranes. These results implied that a new phase was formed after incorporation of HPSS or HPS into the SPEEK matrix. This phase may be formed by the more flexible SPEEK domains far away from hollow sphere with more space for chain movement and weaker inter-chain interaction in SPEEK/HPSS and SPEEK/HPS hybrid membranes.
The stress–strain curves are shown in Fig. S4† and mechanical properties of the membranes are listed in Table 1. The pristine SPEEK membrane displayed a typical good mechanical stability with a tensile strength of 50.1 MPa and elastic modulus of 1.6 GPa at an elongation of 17.1%.49 Incorporation of HPSS microspheres into SPEEK matrix enhanced the tensile strength and Young's modulus of the hybrid membranes with filler content of 2.5 and 5 wt%. Further increasing the filler content to 10 and 15 wt%, the tensile strength and Young's modulus decreased slightly. This was probably a result of the promoted chain mobility of SPEEK and the minor aggregation of the filler. However, the elongation of the SPEEK/HPSS hybrid membranes was lower than that of the SPEEK membranes. The elongation was considerably reduced from 8.7% to 3.2%, with the filler content enhancing from 2.5 to 15 wt%, which may be attributed to strong interaction between the HPSS microspheres and the SPEEK matrix. Among these hybrid membranes, the SPEEK/HPSS-5 membrane exhibited superior mechanical stability with a tensile strength of 53.2 MPa (6.2% increase) and Young's modulus of 1.9 GPa (18.8% increase) at an elongation of 5.2% (69.6% decrease). Based on the above results, the SPEEK/HPSS hybrid membranes with filler contents ranging from 2.5 to 15 wt% possessed good mechanical stability close to the SPEEK membrane and would be adequate for fuel cell application.
Table 1 Mechanical properties of the membranes at room temperature
Membrane |
Tensile strength (MPa) |
Young's modulus (GPa) |
Elongation at break (%) |
SPEEK |
50.1 |
1.6 |
17.1 |
SPEEK/HP-5 |
37.7 |
1.3 |
4.3 |
SPEEK/HPS-5 |
51.5 |
1.8 |
7.3 |
SPEEK/HPSS-2.5 |
52.8 |
1.8 |
8.7 |
SPEEK/HPSS-5 |
53.2 |
2.0 |
5.2 |
SPEEK/HPSS-10 |
47.1 |
1.5 |
4.5 |
SPEEK/HPSS-15 |
42.2 |
1.5 |
3.2 |
3.4 Water uptake, water release, water retention and swelling property of the hybrid membranes
3.4.1 Water uptake. In PEMs, adequate water is essential to ensure efficient proton conduction, in order to serve as proton carriers for vehicle-type proton transfer and form hydrogen-bond network for Grotthuss-type proton transfer.33,34 The water uptake of the membranes under study is shown in Fig. 6. For all hybrid membranes, the water uptake was higher than that of the pristine SPEEK membrane (27.9 wt%) and increased with a similar trend with increased filler content. The SPEEK/HPSS hybrid membrane displayed the best water uptake among the three hybrid membranes at the same filler content. As the filler content was increased from 2.5 to 15 wt%, the water uptake of the SPEEK/HPSS hybrid membranes was enhanced from 34.9 to 44.9 wt% (relative to the weight of the corresponding dry hybrid membrane). These results revealed that the big inner lumens of the filling hollow microspheres can act as water reservoirs, hence increasing water uptake for the hybrid membranes.30 Meanwhile, the pendant sulfonic acid groups on the surface of the polymer shell and grafted on the polystyrene brushes can bind water molecules tightly via hydrogen bond interaction.36 Area swelling of all hybrid membranes is shown in Fig. 6. For the SPEEK/HP and SPEEK/HPS hybrid membranes, the swelling of the membranes was lower than that of the pristine SPEEK membrane (30.1%), and decreased further with increasing filler content. This was probably a result of the strong interaction between the HP or HPS microspheres and the SPEEK matrix, which inhibited the free mobility of the SPEEK chain. However, after introduction of HPSS microspheres, the swelling of the hybrid membranes increased slightly from 32.8% to 34.3%, with the filling content increasing from 2.5 to 10 wt%, which could be attributed to good mobility of the sulfonated polystyrene brushes of the HPSS microspheres in a high stretching state under wet state. It was notable that further increasing the filler content to 15 wt%, the swelling of the SPEEK/HPSS hybrid was considerably decreased to 31.0%, which may be ascribed to minor aggregation of the HPSS microspheres in the hybrid membranes restraining the mobility of the SPEEK matrix.
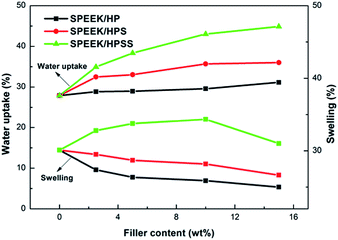 |
| Fig. 6 The water uptake and swelling properties of the pristine SPEEK, SPEEK/HP, SPEEK/HPS and SPEEK/HPSS hybrid membranes. | |
3.4.2 Water release. To evaluate the dynamic water retention behavior of the hybrid membranes, the water release of all membranes was tested at 40 °C and 20% RH as a function of time. As shown in Fig. 7, the water release from all membranes displayed a similar two-stage process: rapid water evaporation as the first stage during the first 20 min; slow water loss as the second stage from 20 to 180 min. The SPEEK membrane suffered from serious water loss, especially in the first stage. As a result, 86% of the absorbed water was released after 180 min testing. Encouragingly, the incorporation of these three kinds of hollow polymer microspheres obviously reduced the water release rate of the corresponding hybrid membranes. In particular, the water release in the SPEEK/HPSS hybrid membranes was decreased from 83% to 69% with increasing filler content from 2.5 to 15 wt% after 180 min testing. For the hybrid membranes, the water release rate decreased in the order of SPEEK/HP > SPEEK/HPS > SPEEK/HPSS, in agreement with that of the corresponding hollow microspheres.
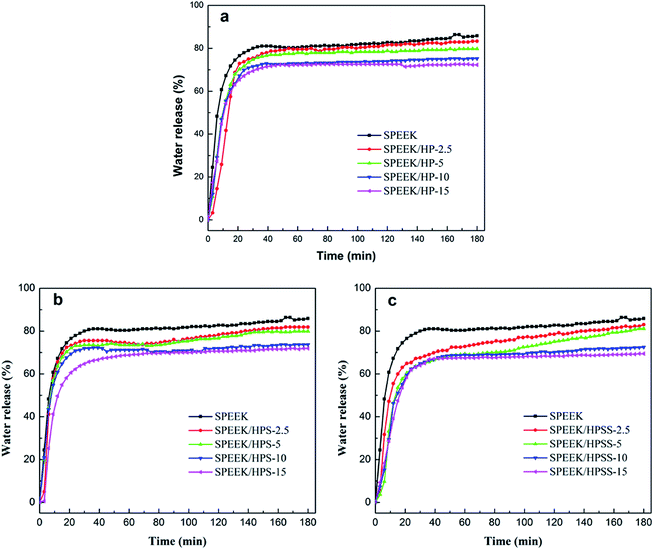 |
| Fig. 7 Water release: (a) SPEEK/HP; (b) SPEEK/HPS; and (c) SPEEK/HPSS hybrid membranes as a function of time at 40 °C and 20% RH. | |
3.4.3 Water retention. Water retentions of SPEEK/HP, SPEEK/HPS, and SPEEK/HPSS membranes at 40 °C and 20% RH are presented in Fig. 8. From the above results, the HPSS microspheres exhibited the best water retention property among these three hollow microspheres. Water retention increased from 4.2% for the SPEEK matrix membrane up to 13.8% for SPEEK/HPSS-15 hybrid membrane after 180 min testing. The result indicated that incorporation of HPSS microspheres significantly improved the water retention property of the hybrid membranes. The water retention decreased in the order of SPEEK/HPSS > SPEEK/HPS > SPEEK/HP. All these results indicated that the compact polymer shell and the large amounts of pendant sulfonic acid groups on the polymer shell and polystyrene brushes had a key role in the water retention behavior of the hollow microspheres and the corresponding hybrid membranes.
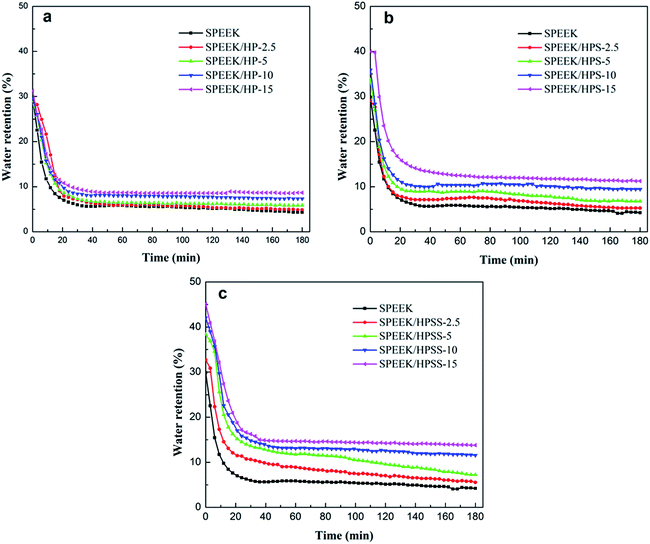 |
| Fig. 8 Water retention: (a) SPEEK/HP; (b) SPEEK/HPS; and (c) SPEEK/HPSS hybrid membranes as a function of time at 40 °C and 20% RH. | |
3.5 Proton conductivity of the membranes
Proton conductivity is an essential and performance-limiting parameter for PEMs, which affects the operational voltage and current output of a fuel cell.50 Fig. 9a–d shows the proton conductivity of the membranes as a function of temperature at 100% RH. All the proton conductivities of the hybrid membranes increased obviously with increasing testing temperature. The proton conductivity of the pristine SPEEK membranes was 0.04 S cm−1 at 25 °C, which increased to 0.18 S cm−1 at 75.3 °C. After introduction of the HP or HPS microspheres, the proton conductivity of the hybrid membranes changed slightly, especially at low temperature. On the contrary, the proton conductivities of the SPEEK/HPSS hybrid membranes were significantly enhanced in the cases of filler content ranging from 2.5 to 15 wt% at each testing temperature range from 25 to 75 °C. For example, when the HPSS microspheres content was elevated from 2.5 to 15 wt%, the proton conductivity of the SPEEK/HPSS hybrid membrane was enhanced from 0.08 to 0.33 S cm−1 at 75 °C with an increment of 312.5%. Furthermore, Fig. 9d shows the proton conductivity of all the membranes with 10 wt% filler content as a function of temperature at 100% RH. For all the hybrid membranes, the proton conductivity displayed a positive temperature–conductivity correlation and increased in the order of SPEEK/HPSS-10 > SPEEK/HPS-10 > SPEEK/HP-10 > SPEEK at each testing temperature range from 25 to 75 °C. All these results demonstrated that the incorporation of the HPSS microspheres significantly enhanced its proton conductivity compared with those for the other corresponding membranes.
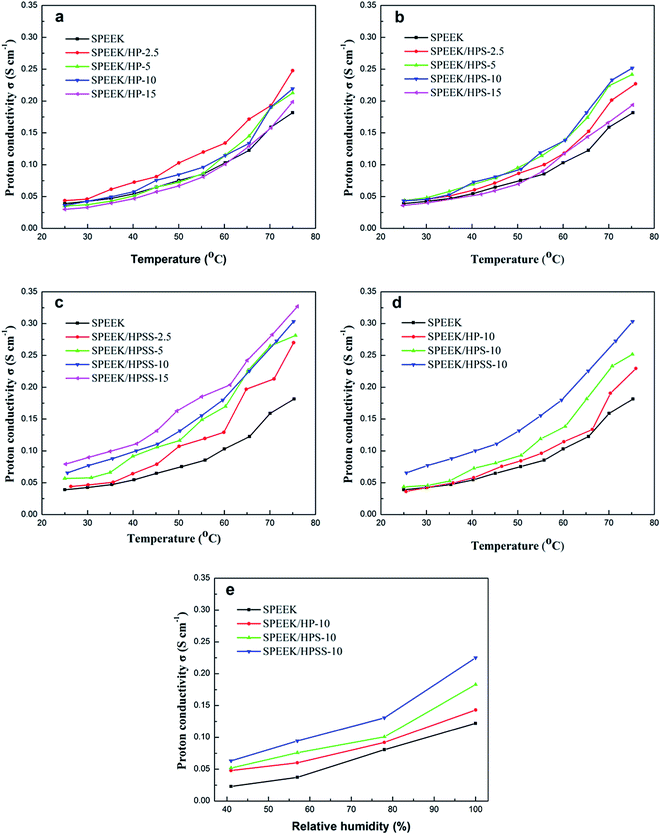 |
| Fig. 9 Proton conductivities of the pristine SPEEK membrane and the hybrid membranes as a function of temperature at 100% RH: (a) SPEEK/HP; (b) SPEEK/HPS; (c) SPEEK/HPSS; and (d) SPEEK/hollow polymer microspheres with 10 wt% filler content. (e) Proton conductivity of the pristine SPEEK membrane and the hybrid membranes with 10 wt% filler content at 65 °C and various relative humidities. | |
The change of proton conductivity of the hybrid membranes may originate from many factors. Theoretically, proton transfer through a PEM is classified into two mechanisms: the vehicle mechanism (protons diffusing together with water molecules by forming hydronium ions, such as H5O2+, H7O3+ and H9O4+), and the Grotthuss mechanism (protons hopping from one proton carrier site to a neighboring one through hydrogen bonding).33,34 In most cases, these two mechanisms jointly govern the proton transfer.50 The proton conductivity of a PEM is dominated by its water content and the number of proton carriers. Increased water uptake not only increases the amount of proton vehicles and facilitates protonation of water to form hydronium ions, but also provides sufficient hydrogen-bond networks to facilitate proton transport and generates more solvated species to dissociate sulfonic acid groups for proton hopping.18
For the SPEEK/HP hybrid membranes, the proton conductivity elevated slightly compared with that for the SPEEK matrix, probably because of the small amount of carboxylic acid groups (–COOH) in the polymer shell and the superior water retention property of the hybrid membranes. After incorporation of the HPS microspheres, the proton conductivity of the hybrid membranes increased gradually at each testing temperature with the filler content below 15 wt% owing to the introduction of the strong proton transfer group (–SO3H). However, when the filler content increased to 15 wt%, the proton conductivity decreased obviously. It was even lower than that of SPEEK/HPS-2.5 hybrid membranes, which could be explained by serious aggregation of the HPS microspheres in the hybrid membranes blocking construction of the proton-conduction pathway and hindering proton transfer, as illustrated in Fig. 4e. Compared with the above hybrid membranes, the proton conductivity of the SPEEK/HPSS hybrid membranes was enhanced significantly by incorporating HPSS microspheres under identical conditions, as shown in Fig. 9. The superior proton conductivity could be attributed to the following factors: (I) the superior water retention of the hybrid membranes facilitated the proton transfer through the membranes via the vehicle and Grotthuss mechanisms.18,51 (II) The high concentration of highly conductive –SO3H groups on the grafted polystyrene brushes rendered more facile hopping sites, and coupled with water molecules at the SPEEK/HPSS interfaces to form an additional pathway for rapid proton transport.35 (III) The HPSS microspheres with linear sulfonated polystyrene polymer brushes dispersed homogeneously in the SPEEK matrix in the absence of any aggregation in all hybrid membranes, which may have generated a continuous channel for proton transfer.
Low humidity proton conductivities of both the pristine SPEEK and the hybrid membranes with 10 wt% filler content at 65 °C are shown in Fig. 9e. For the SPEEK membrane, the proton conductivities were 0.023, 0.037, 0.081 and 0.122 S cm−1, respectively, at relative humidities of 41%, 57%, 78% and 100%. The proton conductivities of all hybrid membranes were higher than that of the SPEEK membrane, which was mainly attributed to the increasing water content. Because of the better water retention property by incorporation of HPSS microspheres in the hybrid membranes and the large number of –SO3H groups, the SPEEK/HPSS-10 hybrid membrane possessed the least reliance of proton conductivity on humidity. Compared with the SPEEK membranes, the SPEEK/HPSS-10 hybrid membranes exhibited a higher proton conductivity of 173.9% at 41% RH, 154.1% at 57% RH, 61.7% at 87% RH, and 84.4% at 100% RH. The above results demonstrate that the SPEEK/HPSS-X hybrid membranes could be competitive candidates for direct methanol fuel cell membranes even in a temperature as high as 75 °C or relative humidity reduced as low as 41%.
3.6 Methanol crossover of the membranes
Methanol permeability of membranes is another important factor that greatly affects the performance of direct methanol fuel cells (DMFC).7,8 As shown in Fig. 10, the methanol permeability of the SPEEK control membrane was 2.33 × 10−7 cm2 s−1 at room temperature, which satisfies the requirement (methanol permeability <10−6 cm2 s−1) for PEM used in DMFC. After incorporation of the three kinds of hollow polymer microspheres, the methanol crossover of the SPEEK membrane decreased notably with a similar trend. Furthermore, increasing the filler content significantly intensified methanol barrier properties of the hybrid membranes. Because of a few cracks in the HPS microspheres as illustrated in Fig. 1e, the SPEEK/HPS-X exhibited the worst methanol barrier property in the whole filler content. With filler contents of 2.5 and 5 wt%, the SPEEK/HPSS-X displayed the best methanol barrier property among these hybrid membranes. However, increasing the filler content to 10 and 15 wt%, the methanol crossover of SPEEK/HP-X was lower than that of the SPEEK/HPSS-X, which may be ascribed to minor aggregation of the HPSS microspheres in the hybrid membranes, as shown in Fig. 4h. The methanol permeability reduced from 2.33 × 10−7 cm2 s−1 for the SPEEK membrane to 1.34 × 10−7 cm2 s−1 for SPEEK/HPSS-15 (42.5% reduction), which was still much lower than 10−6 cm2 S−1. The improved methanol barrier properties were ascribed to strong interaction between the hollow microspheres and the SPEEK matrix hindering the permeation of methanol molecules. Meanwhile, the methanol diffusion pathway was prolonged and became tortuous after incorporation of the hollow polymer microspheres in the hybrid membranes.
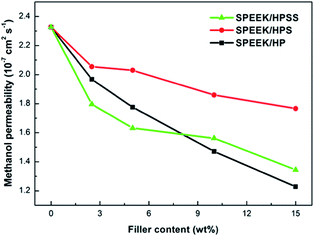 |
| Fig. 10 Methanol permeability of the pristine SPEEK, SPEEK/HP, SPEEK/HPS and SPEEK/HPSS hybrid membranes. | |
4 Conclusion
In summary, two kinds of sulfonated hollow polymer microspheres were synthesized by a combination of sulfonation of polystyrene brushes grafted on SiO2/P(MAA-co-DVB-co-CMSt)-g-PSt core–shell microspheres or phenyl groups of the SiO2/P(MAA-co-DVB-co-CMSt) shell layer, and the subsequent removal of the silica core by HF solution. These two kinds of sulfonated hollow polymer microspheres were homogeneously incorporated into the pristine SPEEK matrix to fabricate the SPEEK/HPS and SPEEK/HPSS hybrid membranes. The SPEEK/HPSS hybrid membranes bearing more sulfonic acid groups were endowed with the best water retention properties and the highest proton conductivity compared with the other two hybrid membranes (SPEEK/HPS and SPEEK/HP). The superior water retention of the hybrid membranes doped with HPSS microspheres (in the loading range from 2.5 to 15 wt%) could be attributed to the large lumen and large amount of –SO3H groups. Meanwhile, the superior proton conductivity could be tentatively attributed to the excellent water retention property of the hybrid membranes, the good mobility of the polystyrene brushes and the high concentration of effective proton-conducting groups (–SO3H). The highest proton conductivity obtained was 0.33 S cm−1 at 75 °C (100 RH) for the hybrid membranes with 15 wt% of HPSS microspheres, 83.3% higher than that of the SPEEK control membranes (0.18 S cm−1). Moreover, the hybrid membranes exhibited obviously enhanced proton conductivity under reduced RH in comparison with the SPEEK membrane. Furthermore, the SPEEK/HPSS-15% hybrid membranes exhibited a 42.5% decrease in methanol permeability and possessed good mechanical performance. Thus, the as-prepared SPEEK/HPSS hybrid membranes are attractive candidates for fabrication of high-performance hybrid proton exchange membranes.
Acknowledgements
This work was supported by the Natural Science Foundation of China (Grant no. 21174065, and 21374049), PCSIRT (IRT1257).
Notes and references
- C. Laberty-Robert, K. Vallé, F. Pereira and C. Sanchez, Chem. Soc. Rev., 2011, 40, 961 RSC.
- H. W. Zhang and P. K. Shen, Chem. Rev., 2012, 112, 2780 CrossRef CAS PubMed.
- X. Zhao, M. Yin, L. Ma, L. Liang, C. P. Liu, J. H. Liao, T. H. Lu and W. Xing, Energy Environ. Sci., 2011, 4, 2736 CAS.
- B. P. Tripathi and V. K. Shahi, Prog. Polym. Sci., 2011, 36, 945 CrossRef CAS PubMed.
- A. Chandan, M. Hattenberger, A. El-kharouf, S. F. Du, A. Dhir, V. Self, B. G. Pollet, A. Ingram and W. Bujalski, J. Power Sources, 2013, 231, 264 CrossRef CAS PubMed.
- A. C. Dupuis, Prog. Mater. Sci., 2011, 56, 289 CrossRef CAS PubMed.
- S. Bose, T. Kuila, T. X. H. Nguyen, N. H. Kim, K. Lau and J. H. Lee, Prog. Polym. Sci., 2011, 36, 813 CrossRef CAS PubMed.
- C. Y. Tseng, Y. S. Ye, M. Y. Cheng, K. Y. Kao, W. C. Shen, J. Rick, J. C. Chen and B. J. Hwang, Adv. Energy Mater., 2011, 1, 1220 CrossRef CAS.
- G. Gebel, Macromolecules, 2013, 46, 6057 CrossRef CAS.
- B. Campagne, G. David, B. Améduri, D. J. Jones, J. Rozière and I. Roche, Macromolecules, 2013, 46, 3046 CrossRef CAS.
- W. J. Lau and A. F. Ismail, J. Membr. Sci., 2009, 334, 30 CrossRef CAS PubMed.
- S. N. Feng, K. Z. Shen, Y. Wang, J. H. Pang and Z. H. Jiang, J. Power Sources, 2013, 224, 42 CrossRef CAS PubMed.
- N. W. Li, D. W. Shin, D. S. Hwang, Y. M. Lee and M. D. Guiver, Macromolecules, 2010, 43, 9810 CrossRef CAS.
- H. T. Li, G. Zhang, J. Wu, C. J. Zhao, Y. Zhang, K. Shao, M. M. Han, H. D. Lin, J. Zhu and H. Na, J. Power Sources, 2010, 195, 6443 CrossRef CAS PubMed.
- A. K. Sahu, S. D. Bhat, S. Pitchumani, P. Sridhar, V. Vimalan, C. George, N. Chandrakumar and A. K. Shukla, J. Membr. Sci., 2009, 345, 305 CrossRef CAS PubMed.
- A. K. Mishra, S. Bose, T. Kuila, N. H. Kim and J. H. Lee, Prog. Polym. Sci., 2012, 37, 842 CrossRef CAS PubMed.
- Z. Q. Jiang, X. S. Zhao, Y. Z. Fu and A. Manthiram, J. Mater. Chem., 2012, 22, 24862 RSC.
- J. T. Wang, S. Jiang, H. Zhang, W. J. Lv, X. L. Yang and Z. Y. Jiang, J. Membr. Sci., 2010, 364, 253 CrossRef CAS PubMed.
- H. Zarrin, D. Higgins, Y. Jun, Z. W. Chen and M. Fowler, J. Phys. Chem. C, 2011, 115, 20774 CAS.
- J. C. Mckeen, Y. S. Yan and M. E. Davis, Chem. Mater., 2008, 20, 5122 CrossRef CAS.
- Y. H. Su, Y. L. Liu, Y. M. Sun, J. Y. Lai, D. M. Wang, Y. Gao, B. J. Liu and M. D. Guiver, J. Membr. Sci., 2007, 296, 21 CrossRef CAS PubMed.
- R. Gosalawit, S. Chirachanchai, S. Shishatskiy and S. P. Nues, J. Membr. Sci., 2008, 323, 337 CrossRef CAS PubMed.
- R. Marschall, J. Rathousky and W. Michael, Chem. Mater., 2007, 19, 6401 CrossRef CAS.
- T. Chakrabarty, A. K. Singh and V. K. Shahi, RSC Adv., 2012, 2, 1949 RSC.
- P. Tanner, P. Baumann, R. Enea, O. Onaca, C. Palivan and W. Meier, Acc. Chem. Res., 2011, 44, 1039 CrossRef CAS PubMed.
- C. J. Ke, Y. J. Lin, Y. C. Hu, W. L. Chiang, K. J. Chen, W. C. Yang, H. L. Liu, C. C. Fu and H. W. Sung, Biomaterials, 2012, 33, 5156 CrossRef CAS PubMed.
- G. D. Fu, G. L. Li, K. G. Neoh and E. T. Kang, Prog. Polym. Sci., 2011, 36, 127 CrossRef CAS PubMed.
- J. W. Cui, M. P. V. Koeverden, M. Müllner, K. Kempe and F. Caruso, Adv. Colloid Interface Sci., 2014, 207, 14 CrossRef CAS PubMed.
- D. S. Feng, J. Shi, X. J. Wang, L. Zhang and S. K. Cao, RSC Adv., 2013, 3, 24975 RSC.
- J. T. Wang, H. Zhang, X. L. Yang, S. Jiang, W. J. Lv, Z. Y. Jiang and S. Z. Qiao, Adv. Funct. Mater., 2011, 21, 971 CrossRef CAS.
- E. W. Yan, J. T. Wang, Z. Y. Jiang, H. L. Feng, L. L. Nie, T. Xu, X. L. Yang and X. Zhang, J. Mater. Chem. A, 2013, 1, 11762 CAS.
- B. Guo, S. W. Tay, Z. L. Liu and L. Hong, Polymers, 2012, 4, 1499 CrossRef PubMed.
- K. D. Kreuer, Chem. Mater., 1996, 8, 610 CrossRef CAS.
- D. Riccardi, P. König, X. Prat-Resina, H. B. Yu, M. Elstner, T. Frauenheim and Q. Cui, J. Am. Chem. Soc., 2006, 128, 16302 CrossRef CAS PubMed.
- H. T. Pu, D. Wang and Z. L. Yang, J. Membr. Sci., 2010, 360, 123 CrossRef CAS PubMed.
- L. L. Nie, H. Dong, X. Han, G. W. He, H. Wu and Z. Y. Jiang, J. Power Sources, 2013, 240, 258 CrossRef CAS PubMed.
- G. W. He, Y. F. Li, Z. Y. Li, L. L. Nie, H. Wu, X. L. Yang, Y. N. Zhao and Z. Y. Jiang, J. Power Sources, 2014, 248, 951 CrossRef CAS PubMed.
- G. W. He, Z. Y. Li, Y. F. Li, Z. Li, H. Wu, X. L. Yang and Z. Y. Jiang, ACS Appl. Mater. Interfaces, 2014, 6, 5362 CAS.
- W. Stöber and A. Fink, J. Colloid Interface Sci., 1968, 26, 62 CrossRef.
- F. Q. Liu, B. L. Yi, D. M. Xing, J. R. Yu, Z. J. Hou and Y. Z. Fu, J. Power Sources, 2003, 124, 81 CrossRef CAS.
- K. Li and H. D. H. Stöver, J. Polym. Sci., Polym. Chem. Ed., 1993, 31, 3257 CrossRef CAS.
- G. L. Li, H. Möhwald and D. G. Shchukin, Chem. Soc. Rev., 2013, 42, 3628–3646 RSC.
- J. S. Downey, R. S. Frank, W. H. Li and H. D. H. Stöver, Macromolecules, 1999, 32, 2838 CrossRef CAS.
- J. Pyun, T. Kowalewski and K. Matyjaszewski, Macromol. Rapid Commun., 2003, 24, 1043 CrossRef CAS.
- S. Edmondson, V. L. Osborne and W. T. S. Huck, Chem. Soc. Rev., 2004, 33, 14 RSC.
- S. J. Paddison, K. D. Kreuer and J. Maier, Phys. Chem. Chem. Phys., 2006, 8, 4530 RSC.
- J. Wu, W. F. Lin, Z. Wang and S. F. Chen, Langmuir, 2012, 28, 7436 CrossRef CAS PubMed.
- B. J. Liu, G. P. Robertson, D. S. Kim, M. D. Guiver, W. Hu and Z. H. Jiang, Macromolecules, 2007, 40, 1934 CrossRef CAS.
- E. Sgreccia, J. F. Chailan, M. Khadhraoui, M. L. D. Vona and P. Knauth, J. Power Sources, 2010, 195, 7770 CrossRef CAS PubMed.
- A. C. Dupuis, Prog. Mater. Sci., 2011, 56, 289 CrossRef CAS PubMed.
- G. A. Ludueña, T. D. Kühne and D. Sebastiani, Chem. Mater., 2011, 23, 1424 CrossRef.
Footnote |
† Electronic supplementary information (ESI) available: Fig. S1: TGA curves: (a) SiO2–MPS microspheres; (b) SiO2@P(MAA-co-DVB-co-CMSt) core–shell microspheres; and (c) SiO2@P(MAA-co-DVB-co-CMSt)-g-PSt microspheres, Fig. S2: water preservation of the hollow microspheres: (a) water retention; and (b) water release, all these data were determined at 40 °C and 20% RH. Fig. S3: TGA curves of the pristine SPEEK, SPEEK/HPS: (a) and SPEEK/HPSS; (b) hybrid membranes. Fig. S4: stress–strain curves of the pristine SPEEK and SPEEK/HPSS hybrid membranes, Table S1: glass transition temperature (Tg) of the pristine SPEEK and hybrid membranes. See DOI: 10.1039/c4ra13582b |
|
This journal is © The Royal Society of Chemistry 2015 |
Click here to see how this site uses Cookies. View our privacy policy here.