DOI:
10.1039/C4RA10639C
(Paper)
RSC Adv., 2015,
5, 11371-11377
Effect of interactions of PVC and biomass components on the formation of polycyclic aromatic hydrocarbons (PAH) during fast co-pyrolysis†
Received
17th September 2014
, Accepted 12th January 2015
First published on 12th January 2015
Abstract
The interactions of polyvinyl chloride (PVC) and biomass components (hemi-cellulose, cellulose and lignin) during fast pyrolysis were investigated at 800 °C in a fixed bed reactor. The interactions of PVC and biomass components decreased the HCl yield and increased the tar yield significantly. During the co-pyrolysis of PVC with the biomass components, most polycyclic aromatic hydrocarbon (PAH) components were decreased compared with the calculated proportion results. The mechanism of the interactions may be that in the fast pyrolysis process, the processes of dehydrochlorination and chain scission occur in a very short time. Biomass materials and/or bio-char can act as catalysts which inhibit the dehydrochlorination process or promote the chain scission of PVC. Therefore, the dehydrochlorination process might not be completed, resulting in the production of chlorinated oil compounds. Thus, the HCl yield is reduced and PAH concentrations are decreased during the co-pyrolysis of PVC and biomass.
Introduction
With the shortage of fossil fuels and the crisis of global warming, biomass, as a renewable energy source is attracting growing interest. Pyrolysis is regarded as a promising technology for biomass utilization, due to the versatility of the end-uses of the char, oil and gas produced from biomass pyrolysis.1 Recent research has shown that co-feeding of plastics during biomass pyrolysis may provide a viable means to improve biomass conversion.2 However, there are several challenges for the co-pyrolysis of biomass and plastics towards large-scale development; for example, the formation of polycyclic aromatic hydrocarbons (PAH) in the product oil.3 PAH are a group of semi-volatile hydrocarbons, which may cause teratogenesis, cancer or mutations if absorbed by the human body.4 Due to the large number and complex nature of PAH compounds, 16 PAH (naphthalene, acenaphthylene, acenaphthene etc.) have been identified as priority pollutants by the US Environmental Protection Agency (US EPA).5
It has been reported that polyvinyl chloride (PVC) plays an important role in the formation of PAH during pyrolysis.6 PVC is the second most used plastic (after polyethylene) because of its low price and durability,7 and it is found in significant quantities in municipal solid waste (MSW). Research on PVC pyrolysis has shown that thermal degradation of PVC is a two stage process.8 The first stage consists of the progressive dehydrochlorination of the polymer resulting in a conjugated polyene structure as a residue, which can undergo further pyrolysis (second stage) to yield a series of hydrocarbon products.9
Studies of the interactions between PVC and biomass during co-pyrolysis will be important for fundamentally understanding PAH formation. Several preliminary studies have been undertaken to investigate the interaction between PVC and biomass during co-pyrolysis. Matsuzawa et al.10 studied the interaction of cellulose (a major component of biomass) with polyethylene (PE), polypropylene (PP), polystyrene (PS), and PVC by thermogravimetry-direct mass spectrometry (TG-MS). Interaction was reported only for co-pyrolysis of cellulose and PVC. Fourier Transform Infrared Spectroscopy (FTIR) analysis indicated that the char derived from pyrolysis of a mixture of cellulose and PVC had fewer hydroxyl groups and more C
O and C
C bonds compared with the char from pyrolysis of pure cellulose. It was suggested that HCl evolution from the chlorinated polymer promotes reactions of dehydration, scission in the intra-ring of the glucose unit, cross-linkage and charring rather than the depolymerisation of cellulose.10 McGhee et al. pyrolyzed mixtures of PVC and straw in a tube furnace at a heating rate of 10 K min−1, and showed that the yield of bio-char from straw was increased, and also the bio-char became less reactive, compared with the pyrolysis of straw alone.11
Currently, there is very limited literature investigating PAH formation during the co-pyrolysis of biomass and PVC. Several studies investigating the interactions of PVC and biomass have been carried out under slow pyrolysis conditions.10,11 However, there are few investigating fast pyrolysis where different heat transfer and mass transfer processes would be expected, resulting in different interactions between plastics and biomass. Also, fast pyrolysis technology is at present considered as an emerging energy technology for liquid-tar and solid-char production, and is preferred to slow pyrolysis technology.12
It has been reported that bio-char production from biomass pyrolysis in terms of yield and chemical properties has been significantly affected by the presence of PVC.11 Furthermore, it is not clear whether PAH formation during the co-pyrolysis of biomass and PVC is affected by bio-char generation from biomass pyrolysis.
In this paper, we investigated the interaction of PVC with three biomass components (hemi-cellulose, cellulose, and lignin) during fast pyrolysis using a fixed bed reactor coupled with a HCl absorption system. The formation of PAH and HCl are discussed, together with the production of other gas and solid residue products.
Materials and methods
Materials
The PVC and xylan (commonly representative of hemi-cellulose, from beech wood) were obtained from Sigma-Aldrich. Cellulose (microcrystalline) was provided from Research Chemicals Ltd. Lignin (dealkaline) was obtained from Tokyo Chemical Industry Co., Ltd. The sample sizes were less than 150 μm. Before the experiments, all the samples were dried at 105 °C. Results of the proximate analysis (thermogravimetric analyser) and ultimate analysis (CE Instruments CHNS-O analyser) of the samples are shown in Table 1.
Table 1 Proximate and ultimate analysis of different samples
Samples |
Proximate analysisa (wt%) |
Ultimate analysisb (wt%) |
Ash |
Volatile |
Fixed carbon |
C |
H |
O |
Cl |
N |
S |
Dry basis. Dry ash free basis. |
PVC |
0.00 |
94.93 |
5.07 |
38.34 |
4.47 |
— |
56.35 |
0.23 |
0.61 |
Xylan |
3.83 |
82.60 |
13.57 |
40.26 |
5.49 |
51.55 |
— |
2.70 |
0.00 |
Cellulose |
0.07 |
97.94 |
1.98 |
41.66 |
5.71 |
52.20 |
— |
0.41 |
0.02 |
Lignin |
16.15 |
54.61 |
29.25 |
63.86 |
4.45 |
25.83 |
— |
0.18 |
5.67 |
From Table 1 it can be noted that; PVC has a chlorine content of 56.35 wt%, which is consistent with its structure;13 xylan has a notable amount of nitrogen (2.70 wt%); cellulose shows the highest volatile content (97.94 wt%); lignin has considerable ash (16.15 wt%) and fixed carbon content (29.25 wt%); the sulphur content of lignin is also quite high (5.67 wt%). The high volatile content of cellulose and high sulphur content of lignin have been reported by other researchers.14
Pyrolysis–gasification process
Pyrolysis of the samples was carried out using a fixed bed reactor system (Fig. 1). The reaction system was composed of a pyrolysis reactor, tar collection system and gas collection stages. N2 (100 ml min−1) was used as carrier gas, and the residence time of volatiles was approximately 2.6 s. During the experiment, the reactor was initially heated to the set point (800 °C). Once the temperature had stabilized, the sample (1 g) was inserted into the hot zone of the reactor and rapidly pyrolyzed. The average heating rate was approximately 350 °C min−1, which was a rough evaluation of how fast the sample was heated. The reactor was kept at the reaction temperature for a further 30 min to ensure the pyrolysis–gasification process was completed. The products from the pyrolysis were cooled using air and dry ice cooled condensers, thereby collecting the condensed tar. The generated HCl was absorbed by a scrubber/condenser system (water bubbler for HCl absorption and another dry-ice condenser) placed between the existing condensers and the gas sample bag. The non-condensed gases were collected using a Tedlar™ gas sample bag, and further analysed off-line using packed column gas chromatography (GC). Gases were collected for an additional 20 minutes to ensure complete collection of the gas products. Some selected experiments were repeated three times. Out of these repeats, the maximum standard deviations were 3.3% for mass distribution and 3.2% for gas production, and the maximum relative standard deviation for PAH generation was 4.1%. Therefore, the standard deviations for other experiments can be estimated from this data. The mass balance of each experiment was also checked to ensure the reliability and consistency of the results.
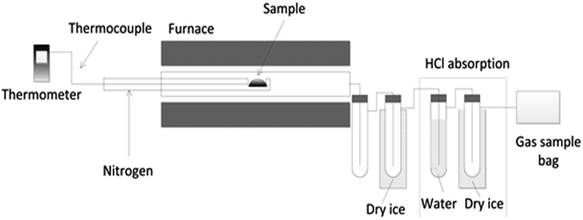 |
| Fig. 1 Schematic of the pyrolysis reaction system. | |
Products analysis and characterization
Gas chromatography. Non-condensed gases collected in the Tedlar™ gas sample bag were analysed off-line by packed column gas chromatography. H2, CO and N2 were analysed with a Varian 3380 GC on a 60–80 mesh molecular sieve column with argon carrier gas, whilst CO2 was analysed by another Varian 3380 GC on a Hysep 80–100 mesh column with argon as carrier gas. C1–C4 hydrocarbons were analysed using a third Varian 3380 gas chromatograph with a flame ionization detector, with an 80–100 mesh Hysep column and nitrogen as carrier gas. From the known N2 concentration measured, and calculated from the flow rate and collection time, the volume and mass of other gases can be calculated.
Characterization of PAH. After each experiment, the condenser and the tar connecting sections were weighed to obtain the mass of tar (weight difference of condensation system). The tar products from the condensers were washed by ethyl acetate to collect the tar adhered to the condenser wall. The water content in the liquid mixture was eliminated by filtering through a column of anhydrous sodium sulphate. The liquid, which contained PAH, was analysed using a Varian CP-3800 gas chromatograph coupled with a Varian Saturn 2200 mass spectrometer fitted with a 30 m × 0.25 μm DB-5 equivalent column. 2 μl of the extracted tar sample was injected into the GC injector port at a temperature of 290 °C; the oven programme temperature was at 50 °C for 6 min, then ramped to 210 °C at 5 °C min−1, held for 1 min and ramped at 8 °C min−1 to 300 °C (total analysis time of 61 min). The transfer line was at 280 °C, manifold at 120 °C and the ion trap temperature was held at 220 °C. The ion trap was initially switched off for 7 min to allow the elution of the solvent prior to data acquisition to safeguard the life of the trap. The PAH compounds present in the tars were quantified by internal standard method with 2-hydoxyacetophenone as internal standard (IS). The GC/MS was calibrated by standard PAH supplied by Sigma-Aldrich Ltd., thus PAH could be quantitatively determined. The analysis reported 10 of the 2-4-ring PAH from US EPA priority list and also 2 naphthalene derivatives (1-methylnaphthalene and 2-methylnaphthalene). The GC peaks of benzo[a]anthracene and chrysene could not be separated clearly by the GC system used; therefore the concentration of these two compounds was reported together.
Results and discussion
Pyrolysis of single components
Product mass distribution and gas production. The mass balance for the experiments is shown in Table 2. The mass balance was calculated as the mass of products and reactants after the experiment (tar (including water), gas and residue) divided by the mass of inputs (sample). The mass balance of all the experiments were between 95.7 and 102.5 wt%, which ensures the accuracy of the experiments. The product mass distribution for the pyrolysis of PVC, xylan, cellulose, and lignin is shown in Fig. 2. As shown in Fig. 2, the pyrolysis of PVC generated 46.0 wt% HCl, which was lower than the chlorine content of PVC in Table 1, indicating that chlorine participated in the formation of compounds of tar or solid. Similar results have been reported by Masuda et al. in a fixed bed reactor at 800 °C.15 The chlorine in tar in the form of various chlorobenzenes was detected by Iida et al. at 700 °C using a pyrolysis gas chromatograph.16 The pyrolysis of xylan produced the highest tar yield (43.2 wt%), and the pyrolysis of cellulose produced the highest gas yield (69.5 wt%) with a negligible amount of residue, which was consistent with the low fixed carbon and ash content (less than 2%) shown in Table 1 and other report.17,18 Also, Shen and Gu reported that the char yield from cellulose pyrolysis was 1.03% at 730 °C.19 The pyrolysis of lignin produced the highest residue yield, which was consistent with the contents of fixed carbon and ash in the lignin, as shown in Table 1. The highest content of volatiles from the decomposition of cellulose and the lowest volatiles content from the decomposition of lignin has also been reported using thermogravimetric analysis (TGA).20
Table 2 Mass balance of different experiments
Sample |
PVC |
Xylan |
Cellulose |
Lignin |
PVC + xylan |
PVC + cellulose |
PVC + lignin |
Mass balance was calculated as the mass of products and reactants after the experiment (tar (including water) + gas + residue) divided by the mass of sample. |
Mass balancea (wt%) |
102.5 |
96.9 |
95.7 |
99.5 |
99.8 |
100.5 |
98.4 |
 |
| Fig. 2 Mass distribution for the pyrolysis of samples. | |
The gas production from the pyrolysis of the four samples was analysed by GC (ESI Fig. S1†). At 800 °C, xylan, cellulose, and lignin produced similar H2 yields (∼100 ml g−1 sample). Cellulose produced the highest volume of CO (∼350 ml g−1 sample), the high CO generation from cellulose pyrolysis was also reported by Banyasz et al.21 CO was generated from C–O–C,22 which was abundant in the structure of cellulose. Xylan generated the most CO2 (∼150 ml g−1 sample), because of the –COO– unit in the monomer. Cellulose also generated the most CH4 and C2–C4 (ESI Fig. S1†). The pyrolysis of PVC produced only a small amount of gas apart from HCl, which was consistent with the low gas yield as shown in Fig. 2.
PAH production from pyrolysis of single components. PAH present in the tar derived from the pyrolysis process were analysed quantitatively by GC/MS. As shown in Table 3, PVC generated far more PAH (18
009 μg g−1 sample) than the biomass components. Compared to xylan and cellulose, lignin generated more PAH than the other two biomass components. Naphthalene was the most abundant PAH in the tar derived from lignin pyrolysis. The large amounts of PAH from lignin pyrolysis were consistent with our previous research in a two-stage reactor system.23 The high PAH yields might be due to the unique phenyl-propane units of the lignin structure.24 Cellulose produced only a small amount of naphthalene, acenaphthylene, fluorene, phenanthrene, and anthracene, which has also been reported by Stefanidis et al.25 Xylan produced a range of PAH except fluoranthene, chrysene, and benzo[a]anthracene.
Table 3 PAH from pyrolysis of PVC, xylan, cellulose, and lignin (μg g−1 sample)
PAH |
PVC |
Xylan |
Cellulose |
Lignin |
Naphthalene |
5419 |
16.1 |
7.7 |
143 |
1-Methylnaphthalene |
2111 |
32.8 |
0.0 |
79.0 |
2-Methylnaphthalene |
2074 |
33.6 |
0.0 |
103 |
Acenaphthylene |
654 |
19.9 |
6.4 |
102 |
Acenaphthene |
70.7 |
2.9 |
0.0 |
3.1 |
Fluorene |
1240 |
19.6 |
6.7 |
33.0 |
Phenanthrene |
2425 |
21.6 |
34.5 |
50.9 |
Anthracene |
367 |
4.1 |
3.7 |
7.9 |
Fluoranthene |
498 |
0.0 |
0.0 |
0.0 |
Pyrene |
336 |
5.5 |
0.0 |
6.7 |
Chrysene + benzo[a]anthracene |
2811 |
0.0 |
0.0 |
10.7 |
Total |
18 009 |
156.2 |
59.1 |
541 |
Co-pyrolysis of PVC and biomass components
In this section, possible interactions between PVC and biomass were investigated by carrying out experiments of the co-pyrolysis of PVC and the biomass components (cellulose, xylan and lignin). The weight ratio of PVC and biomass components was 1
:
1 (50%
:
50%). The expected proportionate results calculated from the pyrolysis of the single components (eqn (1)) were used to compare with experimental results of co-pyrolysis; this method is widely used for the studying of component interaction.26 |
X(cal) = 50% XPVC + 50% Xxylan/cellulose/lignin
| (1) |
where X(cal) is the calculated component proportion result; XPVC is the product yield of pyrolysis of PVC; Xxylan/cellulose/lignin represents the product yield of pyrolysis of single xylan, cellulose or lignin, respectively.
Mass distribution and gas analysis. The experimental results (exp) and calculated component proportion results (cal) of product mass distribution of co-pyrolysis of PVC with xylan, cellulose and lignin are shown in Fig. 3(a), (b) and (c), respectively. The interactions between PVC and biomass components are significant in terms of product mass distribution. For example, HCl yield was decreased largely when the biomass components and PVC were co-pyrolyzed compared to the calculated component proportion results; in particular, the HCl yield was decreased from 23.0 to 9.3 wt% when PVC was mixed with lignin. Accordingly, the tar yield from co-pyrolysis was increased compared to the calculated proportion result.
 |
| Fig. 3 Mass distribution of mixtures of PVC and biomass components. | |
As shown in Fig. 3, interaction in relation to char and gas yield is different when PVC is mixed with xylan, cellulose and lignin, respectively. For example, gas yield was increased for the mixture of PVC and xylan or lignin, while interaction of PVC and cellulose decreased the gas yield. The interaction of PVC and lignin decreased the residue yield compared with the calculated component proportion result. It has been reported that interaction of PVC and cellulose during slow pyrolysis resulted in an increase of char yield.27 As shown in Fig. 3(b), the residue yield from co-pyrolysis of PVC and cellulose was increased slightly compared to the slow pyrolysis as reported in the literature.27
Co-pyrolysis of PVC and each biomass component showed a clear influence on hydrogen production, and CO production, compared with the calculated component proportion results (ESI Fig. S2†). In addition, co-pyrolysis of PVC and lignin showed an increase of CO2 yield (from 39.9 to 62.0 ml g−1 sample) and CH4 yield (from 33.7 to 45.5 ml g−1 sample) (ESI Fig. S2†).
PAH analysis for co-pyrolysis of PVC and biomass components. Fig. 4(a) shows that during the co-pyrolysis of PVC and xylan, several PAH were decreased compared with pyrolysis of each single component (calculated component proportions). The formation of naphthalene and chrysene plus benzo[a]anthracene was inhibited significantly due to the interaction between PVC and biomass components. For example, the amount of naphthalene from experimental work of co-pyrolysis of PVC and xylan (1361 μg g−1 sample) decreased to half of the component proportion results (2717 μg g−1 sample), and the amount of chrysene plus benzo[a]anthracene decreased from 1405 μg g−1 sample to almost zero (Fig. 4(a)). Other PAH components decreased slightly through co-pyrolysis of PVC and xylan compared with the component proportion results.
 |
| Fig. 4 PAH formation of mixtures of PVC and biomass components. | |
The interaction of PVC and cellulose decreased most of the PAH, while the amounts of fluorene, phenanthrene, and anthracene did not change significantly (Fig. 4(b)). The interaction of PVC and lignin decreased several PAH except phenanthrene and anthracene (Fig. 4(c)).
Discussion of interaction of PVC and biomass components. Both volatiles and solid char residue were generated during biomass pyrolysis; therefore, interactions could occur between pyrolysis products from PVC and volatiles from biomass pyrolysis, and/or between products from PVC and solid char residue from biomass pyrolysis. In this work, to further investigate the mechanism of interactions of PVC and biomass components, lignin pyrolysis char/residue (LPR) and PVC was mixed and tested at the same experimental conditions as before. The char residue was prepared from the pyrolysis of lignin at 800 °C in N2 atmosphere. The comparison of mass distribution of the experimental results and calculated proportion results is shown in Fig. 5. Interaction of PVC and LPR decreased HCl and increased tar yield significantly. The results were consistent with the results for the decrease in HCl and increased tar for PVC mixed with lignin shown in Fig. 3. The similarity in char residue yield from experimental and calculated proportion results in Fig. 5 suggests that the lignin solid residue is a catalyst of PVC pyrolysis, which can reduce HCl formation.
 |
| Fig. 5 Mass distribution of mixtures of PVC and LPR. | |
The PAH formation of experimental and calculated component proportion results of PVC with LPR is shown in Fig. 6. Interaction of PVC and LPR decreased most PAH except fluorene and phenanthrene. The results were consistent with the results in Fig. 4. Naphthalene and chrysene plus benzo[a]anthracene from the experimental results were much lower than that of the component proportion results.
 |
| Fig. 6 PAH formation of mixtures of PVC and lignin pyrolysis char/residue. | |
It has been reported that two processes (dehydrochlorination and chain scission) occur during the decomposition of PVC, as shown in Fig. 7.28,29 The process of dehydrochlorination is believed to start at imperfections in the polymer chain.30 In the process of slow pyrolysis, the dehydrochlorination is a slow process, thus almost all chlorine in PVC will be captured in the form of HCl.29,30 However, in the fast pyrolysis process used in this research, with much higher heating rate, the processes of dehydrochlorination and chain scission occur in a very short time. Therefore, the dehydrochlorination process might be incomplete, which suggests that some chlorine in the PVC might be present in organic chlorinated compounds, such as chlorobenzene (CBz). Therefore, the detected HCl would be lower than the chlorine content in PVC, as shown in Fig. 2. Our previous research of fast pyrolysis of a plastic mixture in a fluidized bed reactor showed that a large amount of chlorine could not be detected as HCl.31
 |
| Fig. 7 Mechanisms of PVC degradation.26 | |
As reported by Matsuzawa et al.,10,27 acceleration of dehydration and production of aldehyde compounds was observed to occur temporarily with the dehydrochlorination of PVC. HCl evolution from the chlorinated polymer may act as a Lewis acid, thus possibly inducing reactions of dehydration, scission in the intra-ring of the glucose unit, cross-linkage and charring rather than the depolymerization of cellulose.10,27 Therefore, more residue was observed in the co-pyrolysis of PVC and cellulose, as shown in Fig. 3(b).
As shown in Fig. 3, HCl was decreased during the co-pyrolysis of PVC and biomass components. Similar results were obtained in the research of Kuramochi et al.,32 where HCl emission was reduced by the presence of wood during the pyrolysis of PVC. The reason suggested by the authors was that hemi-cellulose significantly reduced HCl emission by fixing most of the Cl molecules present in a sample into pyrolyzed residue.32
As shown in Fig. 3 and 5, biomass materials, whether xylan, cellulose, and lignin or lignin pyrolysis char/residue, may decrease the production of HCl. It is suggested that biomass materials can act as a catalyst which inhibits the dehydrochlorination process or promotes the chain scission of PVC. As a result, dehydrochlorination during PVC pyrolysis is only partly complete. As reported by Jakab et al.,33 charcoal had a marked impact on the thermal behavior of PP. The thermal decomposition of PP shifted to lower temperature in the presence of charcoal, which indicated the enhancement of the hemolytic scission of polymer.33 Furthermore, it has been reported that carbon black promotes chain scission and participates in the radical transfer reactions. In addition, the hydrogenation process was also promoted when carbon black was added,34 which might be responsible for the decrease of PAH during co-pyrolysis of PVC and biomass shown in Fig. 4 and 6.
The mechanisms of the synergetic effect during co-pyrolysis of PVC and biomass might be that biomass is thermally degraded at lower temperature than the polyolefins, and the solid residue produced from biomass plays the role of radicals donor in the initiation of the polymer chain scission.35
Conclusions
The interactions of PVC and biomass components (hemi-cellulose, cellulose and lignin) during fast pyrolysis were investigated at 800 °C in a fixed bed reactor. The interactions of PVC and biomass components decreased the HCl yield and increased the tar yield significantly. During the co-pyrolysis of PVC with the biomass components, most PAH components were decreased. Furthermore, interactions between PVC and lignin pyrolysis char/residue showed a similar pattern of PAH components. In fast pyrolysis, the processes of dehydrochlorination and chain scission occurs in a very short time, thus it is suggested that the dehydrochlorination process might be incomplete. It is suggested that biomass materials and/or bio-char can act as a catalyst which inhibits the dehydrochlorination process or promotes the chain scission of PVC. This study is a preliminary study about the co-pyrolysis of PVC and biomass. The fate of chlorine during the co-pyrolysis should be investigated in further work, since the chlorine may produce chlorinated compounds in the product oils such as chlorobenzenes or dioxins and furans. The consequence of producing pyrolysis oils which contain such toxic chlorinated compounds would have significant implications on the their safe handling and environmental impact on their subsequent use.
Acknowledgements
The financial support from National Basic Research Program of China (973 Program, no. 2011CB201502) is gratefully acknowledged.
Notes and references
- C. Couhert, J. M. Commandre and S. Salvador, Fuel, 2009, 88, 408–417 CrossRef CAS PubMed.
- X. Li, H. Zhang, J. Li, L. Su, J. Zuo, S. Komarneni and Y. Wang, Appl. Catal., A, 2013, 455, 114–121 CrossRef CAS PubMed.
- C. M. Rochman, C. Manzano, B. T. Hentschel, S. L. M. Simonich and E. Hoh, Environ. Sci. Technol., 2013, 47, 13976–13984 CrossRef CAS PubMed.
- C. Moeckel, D. T. Monteith, N. R. Llewellyn, P. A. Henrys and M. G. Pereira, Environ. Sci. Technol., 2014, 48, 130–138 CrossRef CAS PubMed.
- Office of the Federal Register, Code of Federal Regulations, U.S. Government Printing Office, Washington, 2000 Search PubMed.
- I. Aracil, R. Font and J. A. Conesa, J. Anal. Appl. Pyrolysis, 2005, 74, 465–478 CrossRef CAS PubMed.
- S. Kim, Waste Manag., 2001, 21, 609–616 CrossRef CAS.
- H. M. Zhu, X. G. Jiang, J. H. Yan, Y. Chi and K. F. Cen, J. Anal. Appl. Pyrolysis, 2008, 82, 1–9 CrossRef CAS PubMed.
- A. Marcilla and M. Beltran, Polym. Degrad. Stab., 1995, 48, 219–229 CrossRef CAS.
- Y. Matsuzawa, M. Ayabe and J. Nishino, Polym. Degrad. Stab., 2001, 71, 435–444 CrossRef.
- B. McGhee, F. Norton, C. E. Snape and P. J. Hall, Fuel, 1995, 74, 28–31 CrossRef CAS.
- W. T. Tsai, M. K. Lee and Y. M. Chang, J. Anal. Appl. Pyrolysis, 2006, 76, 230–237 CrossRef CAS PubMed.
- K. Endo, Prog. Polym. Sci., 2002, 27, 2021–2054 CrossRef CAS.
- H. Yu, Z. Zhang, Z. Li and D. Chen, Fuel, 2014, 118, 250–256 CrossRef CAS PubMed.
- Y. Masuda, T. Uda, O. Terakado and M. Hirasawa, J. Anal. Appl. Pyrolysis, 2006, 77, 159–168 CrossRef CAS PubMed.
- T. Iida, M. Nakanishi and K. Goto, J. Polym. Sci., Polym. Chem. Ed., 1974, 12, 737–749 CrossRef CAS.
- Q. A. Liu, Z. P. Zhong, S. R. Wang and Z. Y. Luo, J. Anal. Appl. Pyrolysis, 2011, 90, 213–218 CrossRef CAS PubMed.
- Z. Luo, S. Wang, Y. Liao and K. Cen, Ind. Eng. Chem. Res., 2004, 43, 5605–5610 CrossRef CAS.
- D. K. Shen and S. Gu, Bioresour. Technol., 2009, 100, 6496–6504 CrossRef CAS PubMed.
- H. Zhou, Y. Long, A. Meng, Q. Li and Y. Zhang, Thermochim. Acta, 2013, 566, 36–43 CrossRef CAS PubMed.
- J. L. Banyasz, S. Li, J. Lyons-Hart and K. H. Shafer, Fuel, 2001, 80, 1757–1763 CrossRef CAS.
- D. Ferdous, A. K. Dalai, S. K. Bej and R. W. Thring, Energy Fuels, 2002, 16, 1405–1412 CrossRef CAS.
- C. F. Wu, Z. C. Wang, J. Huang and P. T. Williams, Fuel, 2013, 106, 697–706 CrossRef CAS PubMed.
- S. R. Wang, X. J. Guo, K. G. Wang and Z. Y. Luo, J. Anal. Appl. Pyrolysis, 2011, 91, 183–189 CrossRef CAS PubMed.
- S. D. Stefanidis, K. G. Kalogiannis, E. F. Iliopoulou, C. M. Michailof, P. A. Pilavachi and A. A. Lappas, J. Anal. Appl. Pyrolysis, 2014, 105, 143–150 CrossRef CAS PubMed.
- P. Giudicianni, G. Cardone and R. Ragucci, J. Anal. Appl. Pyrolysis, 2013, 100, 213–222 CrossRef CAS PubMed.
- Y. Matsuzawa, M. Ayabe, J. Nishino, N. Kubota and M. Motegi, Fuel, 2004, 83, 1675–1687 CrossRef CAS PubMed.
- K. J. Jordan, S. L. Suib and J. T. Koberstein, J. Phys. Chem. B, 2001, 105, 3174–3181 CrossRef CAS.
- R. Miranda, J. Yang, C. Roy and C. Vasile, Polym. Degrad. Stab., 1999, 64, 127–144 CrossRef CAS.
- I. C. McNeill, L. Memetea and W. J. Cole, Polym. Degrad. Stab., 1995, 49, 181–191 CrossRef CAS.
- E. A. Williams and P. T. Williams, J. Anal. Appl. Pyrolysis, 1997, 40, 347–363 CrossRef.
- H. Kuramochi, D. Nakajima, S. Goto, K. Sugita, W. Wu and K. Kawamoto, Fuel, 2008, 87, 3155–3157 CrossRef CAS PubMed.
- E. Jakab, G. Várhegyi and O. Faix, J. Anal. Appl. Pyrolysis, 2000, 56, 273–285 CrossRef CAS.
- E. Jakab and M. Omastová, J. Anal. Appl. Pyrolysis, 2005, 74, 204–214 CrossRef CAS PubMed.
- N. Marin, S. Collura, V. I. Sharypov, N. G. Beregovtsova, S. V. Baryshnikov, B. N. Kutnetzov, V. Cebolla and J. V. Weber, J. Anal. Appl. Pyrolysis, 2002, 65, 41–55 CrossRef CAS.
Footnote |
† Electronic supplementary information (ESI) available: The details of gas products (H2, CO, CO2, CH4, C2–CH4) from pyrolysis of single components and mixture experiments. See DOI: 10.1039/c4ra10639C |
|
This journal is © The Royal Society of Chemistry 2015 |
Click here to see how this site uses Cookies. View our privacy policy here.