DOI:
10.1039/C4NJ01332H
(Paper)
New J. Chem., 2015,
39, 172-178
Synthesis of high surface area mixed metal oxide from the NiMgAl LDH precursor for nitro-aldol condensation reaction†
Received
(in Montpellier, France)
7th August 2014
, Accepted 8th October 2014
First published on 8th October 2014
Abstract
We have investigated the effect of divalent metal cations on the structural and catalytic activity of MgAl-layered double hydroxide (LDH), by partially substituting Mg2+ with M2+ (M2+ = Ni2+ or Co2+) keeping the metal to aluminium ratio (M2+Mg/Al3+) = 3 and Mg2+/M2+ = 1. The LDH precursors were prepared by a coprecipitation method. The products were finally calcined at 450 °C for 4 h to obtain mixed metal oxides. The catalysts were characterized by powder X-ray diffraction (PXRD), Fourier transform infra-red spectroscopy (FTIR), thermogravimetric analysis (TGA), scanning electron microscopy (SEM), and Brunauer–Emmett–Teller (BET) surface area techniques. The catalysts were then tested for nitro-aldol condensation reaction under different reaction conditions. The mixed metal oxide obtained by the calcination of the NiMgAl LDH precursor was found to be a more efficient catalyst for nitro-aldol condensation under solvent free conditions at room temperature due to its high BET-surface area and pore volume.
Introduction
Nitro-aldol condensation, commonly known as Henry reaction, is one of the most important C−C bond formation reactions and mostly used in bulk and fine chemical industries.1 The product of the Henry reaction is also extensively used in many important syntheses including the synthesis of various biological compounds.2,3 Usually, the product 2-nitroalkanol is produced by the aldol condensation of carbonyl compounds with nitroalkanes. The classical methods for the synthesis of this product use different bases including carbonates and bicarbonates. Formation of nitro-alkene by the elimination of water molecules from 2-nitroalkanol is one of the disadvantages of Henry reaction. Therefore, it is very much challenging to develop a green and economically cheaper solid base catalyst for selective synthesis of 2-nitroalkanol.
Layered double hydroxides (LDHs) are layered compounds with structural similarities to hydrotalcite clays.4–9 These compounds are also known as anionic clay10–13 with the property of anion exchange due to which these compounds can be widely used in various fields as catalysts,14–17 catalyst supports,18–20 and adsorbents.21–24 They can be represented by the general formula [M2+1−xM3+x(OH)2]x+ (An−x/n)·mH2O, where M2+ and M3+ are divalent and trivalent metal ions, x is the ratio of M3+/(M2+ + M3+), An− is the anion that can be organic or inorganic by which excess positive charge in the layer can be compensated and m is the amount of water present in the interlayer.25,26 Ternary LDHs exhibit better catalytic activity over precursor LDHs and greatly extend their application to various fields such as organic transformations,27–29 photocatalysis etc.30–32 These ternary compounds can be prepared by changing divalent or trivalent cations in the precursor LDHs. Calcination of LDHs gives mixed metal oxides which can be used as basic catalysts in various organic transformations along with the advantages of high surface area and thermal stability.33–37 Due to their simplicity, cost effectiveness and reusability, application of mixed metal oxides has great importance in organic transformations.38,39 The selective synthesis of 2-nitroalkanol by modified LDH has been investigated. However, catalytic performance of the mixed metal oxides from the LDH precursor has not been well examined.
The aim of the present work is to prepare a green and environmentally benign solid base catalyst by partial substitution of Mg2+ with M2+ (M2+ = Ni2+ or Co2+) ion in MgAl LDH. The synthetic method used to prepare LDHs is the co-precipitation method.40 The synthesized and calcined catalysts were employed to test the catalytic activity for the nitro-aldol condensation reaction under solvent free condition at room temperature changing various reaction conditions.
Experimental section
Materials
Mg(NO3)2·6H2O, Ni(NO3)2·6H2O, Co(NO3)2·6H2O, Al(NO3)3·9H2O, NaOH, and Na2CO3 were purchased from Merck, Mumbai; nitromethane was purchased from G.S. Chemicals Testing Lab & Allied Industries, New Delhi; silica gel, iodine and solvents were purchased from RANKEM, New Delhi.
Synthesis of LDHs
LDHs were prepared by co-precipitation of an aqueous solution of metal nitrates – Ni(NO3)2·6H2O, Co(NO3)2·6H2O, Mg(NO3)2·6H2O and Al(NO3)3·9H2O with an aqueous solution of NaOH and Na2CO3 at a constant pH of (10 ± 0.2) with a M2+/M3+ ratio of 3
:
1. After the formation of the precipitate, the gels were aged at 80 °C for 24 h. The solid product was then centrifuged, washed several times with distilled water until pH of the filtrate was 7 and then dried in the oven at 80 °C for 12 h. In MgAl LDH, Mg2+ was partially substituted with M2+ (M2+ = Ni2+ or Co2+) keeping the metal ratio (M2+Mg/Al3+) = 3 and Mg2+/M2+ = 1. The samples were calcined at 450 °C for 6 h in flowing air and at the heating rate of 2 °C min−1.
Characterization
The powder X-ray diffraction (XRD) patterns were recorded on a Rigaku Multiflex instrument using a nickel-filtered CuKα (0.15418 nm) radiation source and a scintillation counter detector. The intensity data were collected over a 2θ range of 5°–70°. The crystallite size was calculated using the Scherrer equation:
D = Bλ/β1/2 cos θ |
where D is the average crystallite size, B is the Scherrer constant (0.89), λ is the wavelength of the X-ray beam, β1/2 is the full-width at half-maximum (FWHM) of the diffraction peak and θ is the diffraction angle. Elemental analyses for metal ions were performed using inductively coupled plasma optical emission spectroscopy (ICP-OES, PerkinElmer, Optima 2100 DV). The solutions of the samples were prepared by keeping the samples to dry at 80 °C for 24 h and then dissolving the samples in (1
:
1) dil. HCl.41 Infra-red spectra were measured in a FTIR spectrophotometer, Model Nicolet Impact I-410. Measurements are performed by pelletizing the samples with KBr in the mid-infrared region. The TGA curves were obtained on a Thermal Analyzer (Model TGA-50, Shimadzu) instrument. The samples were heated from ambient temperature to 700 °C under N2 flow. The heating rate in each case was kept at 10 °C min−1. To study the surface topography, SEM analyses were carried out with “JEOL, JSM Model 6390 LV” Scanning Electron Microscopes, operating at an accelerating voltage of 15 kV. The Brunauer–Emmett–Teller (BET) surface areas were determined by N2 adsorption using Quantachrome Instruments (Model: NOVA 1000e). All the BET values in this study were measured within a precision of ±5%. The pore size and pore volume are determined following the Barrett–Joyner–Halenda (BJH) method in the same instrument. The 1H and 13C NMR spectra were recorded on a JEOL JNM-ECS 400 spectrometer taking Me4Si as the internal standard in CDCl3 and CD3OD solvents. Preparative column chromatography was carried out with silica gel with a mesh size of 60–120 and thin-layer chromatography (TLC) was carried out on glass plates with silica gel.
Catalytic activity
The nitro-aldol condensation reactions were performed under the solvent free conditions by taking 1 mmol of the aldehyde, 10 mmol of the nitromethane and 10 mg of the catalysts. For a comparative study all reactions were carried out for 36 h and the reaction conditions were optimized by varying the substituent, temperature and the amount of catalysts. The reactions were monitored via thin layer chromatography and % conversions were obtained from 1H and 13C NMR analyses of the crude reaction mixture. To evaluate the catalytic activity more clearly, the turnover frequency (TOF) of the catalysts was calculated using the general equation,
where, TON refers to the turnover number. For the turn over number calculations, the number of active or basic sites was calculated by basicity measurements. In this method, a suspension of the 15 mg catalyst in a 2 mL toluene solution of phenolphthalein (0.1 mg mL−1) was stirred for 30 minutes and titrated with a toluene solution of benzoic acid (0.01 M). The aqueous soluble amount of basic sites was determined by the acid–base titration method reported previously.42
Results and discussion
Characterization
Powder XRD patterns of LDHs are shown in Fig. 1(i). The formation of hydrotalcite (HT) type layered structure has been confirmed from the presence of sharp intense peaks at low 2θ angles and comparatively broad, less intense peaks at higher 2θ angles which match well with previous reports.12,27 In the case of all the synthesized LDHs, the diffraction peaks were observed approximately at 2θ values 11.6°, 23.4°, 34.8°, 38.8°, 46.3°, 60.85° and 62.1° that could be assigned to (003), (006), (012), (015), (018), (110) and (113) reflections, respectively (JCPDS card no. 38-0478).33 It has been observed that partial substitution of Mg2+ ions with Ni2+ and Co2+ affects the crystallization procedure which is well reflected from the broad and less intense peaks of both CoMgAl and NiMgAl samples in comparison to the MgAl sample. The peaks for (015) and (018) reflections were not distinct in the case of NiMgAl while the reflections at (015), (018), (110) and (013) completely disappeared in CoMgAl. This can be attributed to the larger size of Co2+ (0.88 Å) and Ni2+ (0.83 Å) which could not accommodate well in the brucite layers. The effect can be understood from the calculation of lattice parameters and crystallite sizes. The value of the lattice parameter ‘a’, which is a function of the average distance of metal ions within the layers can be obtained from the (110) reflection peak while the ‘c’ parameter which is related to the thickness of the brucite-like layer and the interlayer distance can be obtained from the (003) reflection peak.30 The lattice parameters ‘a’ (a = 2d110) and ‘c’ (c = 3d003) are calculated and summarized in Table 1. It is observed from the table that the ‘a’ parameter gradually increases in the case of substituted LDH which can be due to the increased metal–metal distance on partial substitution of metal cations on MgAl LDH. However, the ‘c’ parameter increases in NiMgAl LDH while it decreases in the case of CoMgAl LDH. This difference in lattice parameter ‘c’ can be attributed to the larger ionic radius of Co2+ (0.88 Å) than Ni2+ (0.83 Å).12,27 Again the crystallite sizes of NiMgAl and CoMgAl are found to be less comparable to that of MgAl LDH indicating the inclusion of larger cations in LDH layers resulting in the distortion of layered structure.43
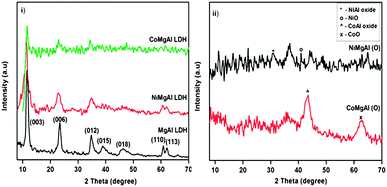 |
| Fig. 1 X-ray powder diffraction patterns of (i) LDHs and (ii) mixed oxides. | |
Table 1 Chemical analysis, crystallographic data and crystallite size of LDHs
Catalysts |
Atomic ratio |
d
003 (Å) |
d
110 (Å) |
Cell parameters (Å) |
Crystallite size (Å) |
Starting |
Analyzeda |
c
|
a
|
003 |
110 |
Determined by ICP.
|
MgAl |
3 : 1 |
3 : 0.9 |
7.69 |
1.52 |
23.07 |
3.04 |
90 |
134 |
Ni2+MgAl |
1.5 : 1.5 : 1 |
1.5 : 1.47 : 0.9 |
7.87 |
1.53 |
23.61 |
3.05 |
63.5 |
113 |
Co2+MgAl |
1.5 : 1.5 : 1 |
1.5 : 1.48 : 1 |
7.68 |
1.55 |
23.04 |
3.09 |
54 |
70 |
As shown in Fig. 1(ii), the powder XRD patterns of the mixed oxides do not possess characteristic peaks corresponding to LDH, because on calcination, the layered structure gets collapsed and were converted to corresponding mixed oxides (ESI†).
The chemical compositions of LDHs were determined from the elemental analyses and presented in Table 1. The Table showed that the molar ratio of M2+Mg/Al is close to 3 and that of M2+/Mg (M2+ = Ni2+ or Co2+) is 1
:
1 which is nearly the same as that of the starting solution.
The FTIR spectra of LDHs are shown in Fig. 2(i). The bands at 3478.2 cm−1 and 1662.9 cm−1 can be assigned to the stretching and bending vibrations of the –OH group of LDH layers and the interlayer water molecule.27,30 The sharp band observed at 1388.5 cm−1 is due to asymmetric stretching of the CO32− ion and broad peaks observed below 1000 cm−1 (500–800 cm−1) correspond to M–O vibrations.30
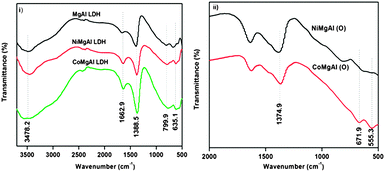 |
| Fig. 2 FT-infrared spectra of (i) LDHs and (ii) mixed oxides. | |
In the case of mixed oxides as shown in Fig. 2(ii), the bands observed near 555.3 and 671.9 cm−1 could be attributed to the vibration of the metal–oxygen (M–O) bond. Moreover, the band observed near 1374.9 cm−1 is due to the carbonate which may arise from the adsorption of carbon dioxide from air on the surface of the metal oxides.27
The thermogravimetric analysis of the precursor LDHs was carried out before calcination. From the TGA curve, shown in Fig. 3, two weight loss steps are observed. The first weight-loss can be observed in the temperature range of 50–200 °C, which corresponds to the removal of water molecules absorbed on the surface and in the interlayer region of LDHs with a weight loss of ∼17.8%. The second weight-loss step observed between 250–400 °C with a weight-loss of ∼19.5% is due to the dehydroxylation of the brucite layer as well as the decomposition of the carbonate anions.44
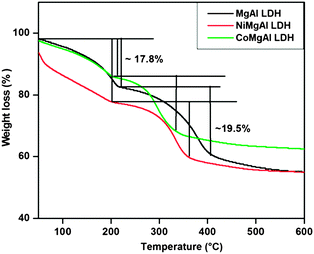 |
| Fig. 3 Thermogravimetric curves of LDHs. | |
The SEM images of LDHs are presented in Fig. 4. Flat plate-like shapes are observed in the case of MgAl LDH. Whereas, in the case of NiMgAl and CoMgAl LDH, crystallites with a large irregular particle size are observed which are due to agglomeration taking place on partial substitution of Mg2+ with M2+ (M2+ = Ni2+ or Co2+) in MgAl LDH.
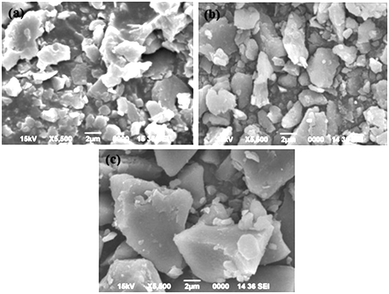 |
| Fig. 4 Scanning electron micrographs of (a) MgAl, (b) CoMgAl and (c) NiMgAl LDHs. | |
The porosity of the mixed oxides obtained by calcination of LDH precursors was investigated by nitrogen adsorption–desorption measurements. The nitrogen adsorption–desorption curve showed that NiMgAl mixed oxides exhibit a type IV isotherm with hysteresis loop H1 (Fig. 5), which is the characteristic of mesoporous material with regular pore structure45 and along with an average pore size of around 49.6 Å (inset of Fig. 5). However, in the case of MgAl and CoMgAl mixed oxides, an isotherm of type IV with combination of hysteresis loops H1 and H341,46 (ESI,† Fig. S1) and an average pore size of around 88 and 107 Å (ESI,† Fig. S2) were observed. The BET surface areas and pore volumes of all the three mixed oxides were calculated and summarized in Table S1 (ESI†). From the table it can be observed that NiMgAl mixed oxide possessed a high BET surface area and a pore volume of 753 m2 g−1 and 1.279 cm3 g−1, respectively. While in the case of MgAl and CoMgAl mixed oxides; the observed surface area and pore volume were 561 m2 g−1, 401 m2 g−1, 0.974 cm3 g−1 and 0.937 cm3 g−1, respectively. The high BET surface area and the pore volume of the mixed oxides are due to the removal of adsorbed and interlayer water molecules and carbonate ions from the LDH layers at high temperature.
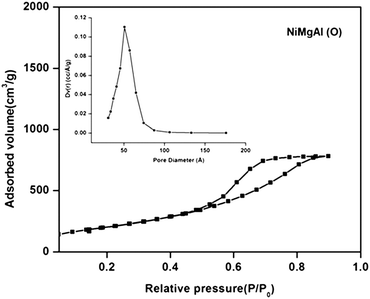 |
| Fig. 5 Nitrogen sorption isotherms of NiMgAl mixed oxide; the inset shows pore size distribution. | |
Catalytic performance
To test the catalytic activity of the synthesized LDHs and mixed oxides, we first performed the reaction under solvent free conditions by taking a 1
:
10 molar ratio of 4-nitrobenzaldehyde and nitromethane in a mmol scale and 10 mg of the catalyst at room temperature. From thin layer chromatography observation it was seen that good to excellent conversion to the product was obtained (84–91%) for all the uncalcined catalysts but the time taken to complete the reaction was more (8–10 h) [Table 2]. Besides, we observed that partial substitution of metal ions on MgAl LDH further improved the catalytic activity. This increase in catalytic activity on partial substitution of metal ions can be explained on the basis of increased cell parameters ‘a’ and ‘c’ in the case of NiMgAl and CoMgAl LDH (Table 1). The increased d value in the case of NiMgAl LDH (d003 = 7.87 Å) can be attributed to the superior catalytic activity providing increased basal spacing for the reaction to take place between the two layers. However, performing the reaction under the same reaction conditions, it was observed that the reaction with calcined LDHs was much faster than the uncalcined LDHs and showed improvement of time giving 95–99% conversion of the product within 2–6 hours with 100% selectivity. Therefore, calcined catalysts were preferred over the uncalcined ones and all reactions were carried out further by mixed oxides. We have also observed from the table that in both the cases (uncalcined and calcined), NiMgAl LDH was found to be a more efficient catalyst compared to that of MgAl and CoMgAl LDHs (entries 2 and 5, Table 2). The high surface area and the large pore volume of the NiMgAl mixed oxide (Fig. 5) results in the superiority of its catalytic activity over the other two mixed oxides for nitro-aldol condensation reaction. Therefore, NiMgAl mixed oxide was considered as the best catalyst in this study.
Table 2 Nitroalkylation of 4-nitrobenzaldehyde with nitromethane over various catalysts at room temperaturea
Entry |
Catalysts |
Time (h) |
Conversionb (%) |
Reactions were carried out with a 1 : 10 molar ratio in a 1 mmol scale of 4-nitrobenzaldehyde and nitromethane using 10 mg catalyst.
Determined from 1H NMR data of the crude mixture.
|
1 |
MgAl LDH |
12 |
86 |
2 |
NiMgAl LDH |
8 |
91 |
3 |
CoMgAl LDH |
10 |
84 |
4 |
MgAl (O) |
6 |
95 |
5 |
NiMgAl (O) |
2 |
99 |
6 |
CoMgAl (O) |
4 |
97 |
After finding the best catalyst from our observation, we then studied the effect of various reaction parameters to optimize the reaction conditions for nitro-aldol condensation reaction. At first we studied the temperature effect on the reaction by varying temperature from 25 °C (RT) to 60 °C (Table 3). It can be observed that on increasing the temperature upto 60 °C, the reaction time decreases from 2 h to 30 minutes. However, temperature does not have great effect over the conversion and we observed almost a similar type of conversion in all cases. Therefore, it is convenient to use the greener path. So, further studies were performed at room temperature under solvent free conditions.
Table 3 Effect of temperature on nitro-aldol condensation reaction of 4-nitrobenzaldehyde and nitromethane catalyzed by NiMgAl mixed oxidea
Entry |
Temperature (°C) |
Time (h) |
Conversionb (%) |
Reactions were carried out with a 1 : 10 molar ratio in a 1 mmol scale of 4-nitrobenzaldehyde and nitromethane using 10 mg catalyst.
Determined from 1H NMR data of the crude mixture.
|
1 |
RT |
2 |
99 |
2 |
40 |
1 |
98 |
3 |
60 |
30 min |
99 |
We next investigated the effect of the amount of catalyst on reaction time and percentage conversion (Table 4). Upon increasing the catalyst amount from 5 to 15 mg, the % conversion increases along with decrease in reaction time. Further, upon increasing the catalyst amount to 20 mg, it was observed that the reaction completed within 1 h while conversion (%) was almost similar. So, we have selected 10 mg catalyst as our optimum amount for further studies at room temperature under solvent free conditions.
Table 4 Effect of the amount of catalyst (NiMgAl mixed oxide) used in the conversion (%) of nitro-aldol condensation reactiona
Entry |
Catalyst (mg) |
Time (h) |
Conversionb (%) |
Reactions were carried out with a 1 : 10 molar ratio in a 1 mmol scale of 4-nitrobenzaldehyde and nitromethane using 10 mg catalyst.
Determined from 1H NMR data of the crude mixture.
|
1 |
5 |
4 |
95 |
2 |
10 |
2 |
99 |
3 |
15 |
2 |
98 |
4 |
20 |
1 |
99 |
After getting optimizing conditions for nitro-aldol condensation reaction, the reaction was then performed with a variety of aldehydes, e.g. simple aromatic aldehydes, heterocyclic aldehydes and polycyclic aromatic aldehydes (Table 5). It is observed from the table that by changing the substituents, the amount of the % conversions is also getting changed. As expected, substrates with electron withdrawing groups give higher % conversion (97–99%, entries 1–3, Table 5) while the % conversion decreases (80–91%) in the case of the substrate with electron donating groups (entries 6–8). However it can be observed from the table that the reaction with polycyclic aldehydes gives better % conversion of 70–80 (entries 4 and 5).
Table 5 Nitro-aldol condensation reaction of nitromethane with different aldehydes
Entry |
Substrate |
Time (h) |
Conversiona (%) |
Determined by 1H NMR data of the crude mixture.
Isolated pure product.
|
1 |
4-Nitrobenzaldehyde |
2 |
99b |
2 |
2-Nitrobenzaldehyde |
4 |
98 |
3 |
3-Nitrobenzaldehyde |
4 |
97 |
4 |
1-Naphthaldehyde |
20 |
76 |
5 |
Furfuraldehyde |
20 |
70 |
6 |
4-Hydroxybenzaldehyde |
36 |
80 |
7 |
4-Methylbenzaldehyde |
36 |
78 |
8 |
Chloroaldehyde |
36 |
91 |
Comparing our results with the reported one, we have observed that A. Cwik et al.47 carried out nitroaldol-reaction of aldehydes in the presence of non-activated Mg
:
Al 2
:
1 hydrotalcite. The reaction was performed at room temperature in methanol, tetrahydrofuran and nitromethane and best results were observed using nitromethane as solvent (20 mol equivalent). However, conversion was 95% in 5 h. R. Manikandan et al.48 reported the synthesis and spectral characterization of three new nickel(II) complexes containing pyridoxal N(4)-substituted thiosemicarbazone ligands with triphenylphosphine. The new nickel(II) complexes were used as catalysts in the nitroaldol (Henry) reaction by employing various aldehydes with nitromethane in an ionic liquid medium. The reaction was carried out at room temperature for 5 h and the yield was observed to be about 52%. However, upon using ionic liquid as solvent medium, a slight improvement in the yield was observed from 52 to 64%. The maximum yield of 92% was observed in 12 h at a 3.0 μmol concentration of the catalyst in 2 mL of methanol. M. Sutradhar et al.49 reported the synthesis of a new cyclic binuclear Ni(II) complex, [Ni2(H2L)2]·4MeOH using the Schiff base N′1,N′3-bis(2-hydroxybenzylidene) malonohydrazide (H4L). A maximum conversion of ca. 93% was obtained at 60 °C, for a 24 h reaction time, with 1 mol% loading of the catalyst with the good syn
:
anti molar ratio of 72
:
28.
We have also studied the effect of calcination temperature on catalytic activity under optimum reaction conditions. We have calcined the catalyst at a lower (350 °C) and at a higher (550 °C) calcination temperature to the reported one (450 °C). The sample calcined at 350 °C, showed low catalytic activity with 84% conversion in 6 h (Table S2, ESI†). This lower calcination temperature leads to no any characteristic change in the layered structure. It can be considered as a dehydrated one with its basic sites occupied by CO32− ions. Consequently, the BET surface area of the catalyst was relatively lower (584 m2 g−1) that leads to the lower catalytic activity. On the other hand, the sample calcined at 550 °C, also exhibited lower activity with the 86% conversion in 8 h (Table S2, ESI†). The high calcination temperature results in the phase transformation of mixed oxides into crystalline spinel phases which results in the lower BET surface area (566 m2 g−1) and hence lower catalytic activity.7,50–54 The N2 adsorption desorption graphs of NiMgAl (O) at 350 and 550 °C calcination temperatures also followed a type IV isotherm (Fig. S3, ESI†). The basic sites formed after calcination of LDHs at 450 °C were considered as the active sites in mixed metal oxides. The presence of different types of basic sites is related to –OH groups, O2−–Mn+ pairs and O2− anions.55–60
The turnover frequency (TOF) of the mixed metal oxides is shown in Fig. S4 (ESI†). It can be seen from the figure that the TOF increases on partial substitution of metal cations with Mg2+ in MgAl mixed oxides and has been found to be maximum in the case of NiMgAl (O) mixed oxide (149 h−1). While in the case of MgAl (O) and CoMgAl (O), the TOF is 12.5 and 36 h−1, respectively, which is almost 11 and 4 times less than NiMgAl (O). This increase in TOF reflects the better catalytic performance of NiMgAl (O) mixed oxides for nitro-aldol condensation reaction.
After testing the catalytic activity it is important to check the recyclability of the catalyst for their practical application. To test the recyclability we carried out the condensation reaction upto four cycles employing 10 mg of the catalyst and it was found that the catalyst becomes active up to 4 cycles as shown in Table S3 (ESI†). In the first 3 cycles, it took 2–3 h to complete the reaction with decrease in % conversion from 96 to 92%. However, after the 3rd cycle, the time to complete the reaction increased up to more than 4 h. Thus we observed that with increasing the number of cycles, the time taken to complete the reaction gradually increases along with the decrease in catalytic activity. The reason for this decrease in the catalytic activity of the catalyst may be due to the loss of catalyst during separation or deactivation of the active sites in the catalyst. The leaching of metals during recyclability of catalysts was observed. For this test, 1 mmol 4-nitrobenzaldehyde, 10 mmol nitromethane and 10 mg of the catalyst were taken in a round bottomed flask and stirred for 1 h at room temperature without any solvent. The catalyst was then filtered off and the experiment was continued with the filtrate for upto 24 h. It was observed that the conversion remained unchanged indicating the absence of any metal in the filtrate.
Conclusions
In summary, we have synthesized high surface area mixed metal oxides from their precursor LDHs and also observed the influence of divalent metal cations on the structural properties and catalytic activity of MgAl LDH. The PXRD of all the as prepared LDHs revealed the formation of a hydrotalcite (HT) type layered structure. The partial substitution of Mg2+ ions with Ni2+ and Co2+ affects the crystallization procedure which is well reflected from the broad and less intense peaks of both CoMgAl and NiMgAl samples in comparison to the MgAl sample. The formation of mixed oxides can be revealed from the powder XRD patterns which possess no any characteristic peaks corresponding to LDH. The mixed metal oxides were found to be catalytically more active towards nitro-aldol condensation reaction under solvent free conditions at room temperature with NiMgAl mixed oxide being more active. The high catalytic activity of NiMgAl mixed oxide can be attributed to the high BET surface area (753 m2 g−1). The catalysts can be reused up to the 4th cycle without any characteristic loss in their activity.
Spectral data
2-Nitro-1-(4-nitrophenyl) ethan-1-ol (ESI,†1H and 13C spectra).
1H NMR (400 MHz, CDCl3): δ 3.75 (s, 1 H), δ 4.58–4.61 (m, 2H), δ 5.60–5.62 (m, 1H), δ 7.64(d, JHH = 8.7 Hz, 2H), 8.27 (d, JHH = 9.2 Hz, 2H); 13C NMR (400 MHz CDCl3): 70.0, 80.8, 124.2, 127.0, 145.4, 148.2 ppm.
Acknowledgements
DB acknowledges the financial support from UGC, New Delhi for providing Rajiv Gandhi National Fellowship. The authors also thank DST, New Delhi, for financial support.
Notes and references
- B. M. Choudary, B. Kavita, N. S. Chowdari, B. Sreedhar and M. L. Kantam, Catal. Lett., 2002, 78, 373–377 CrossRef CAS.
- B. M. Choudary, M. L. Kantam, C. V. Reddy, K. K. Rao and F. Figueras, Green Chem., 1999, 1, 187–189 RSC.
- R. Devi, R. Borah and R. C. Deka, Appl. Catal., A, 2012, 433–434, 122–127 CrossRef CAS.
- S. Miyata, Clays Clay Miner., 1983, 31, 305–311 CAS.
- I. Y. Park, K. Kuroda and C. Kato, J. Chem. Soc., Dalton Trans., 1990, 3071–3074 RSC.
- I. C. Chisem and W. Jones, J. Mater. Chem., 1994, 4, 1737–1744 RSC.
- V. R. L. Constantino and T. J. Pinnavaia, Inorg. Chem., 1995, 34, 883–892 CrossRef CAS.
- S. Zhu, S. Jiao, Z. Liu, G. Pang and S. Feng, Environ. Sci. Nano, 2014, 1, 172–180 RSC.
- K. Klemkaite, I. Prosycevas, R. Taraskevicius, A. Khinsky and A. Kareiva, Cent. Eur. J. Chem., 2011, 9, 275–282 CrossRef CAS.
- Y. Zhao, F. Xiao and Q. Jiao, J. Nanotechnol., 2011, 1–6 CrossRef.
- M. del Arco, S. Gutierrez, C. Martin and V. Rives, Inorg. Chem., 2003, 42, 4232–4240 CrossRef CAS PubMed.
- S. Velu, K. Suzuki, S. Hashimoto, N. Satoh, F. Ohashi and S. Tomura, J. Mater. Chem., 2001, 11, 2049–2060 RSC.
- S. Mandal, D. Tichit, D. A. Lerner and N. Marcotte, Langmuir, 2009, 25, 10980–10986 CrossRef CAS PubMed.
- R. Sen, S. Bhunia, D. Mal, S. Koner, Y. Miyashita and K. I. Okamoto, Langmuir, 2009, 25, 13667–13672 CrossRef CAS PubMed.
- M. L. Kantam, B. M. Choudary, C. V. Reddy, K. K. Rao and F. Figueras, Chem. Commun., 1998, 1033–1034 RSC.
- L. Mohapatra, K. M. Parida and M. Satpathy, J. Phys. Chem. C, 2012, 116, 13063–13070 CAS.
- N. Baliarsingh, K. M. Parida and G. C. Pradhan, Ind. Eng. Chem. Res., 2014, 53, 3834–3841 CrossRef CAS.
- J. R. Ruiz, C. Jiménez-Sanchidrián and M. Mora, Tetrahedron, 2006, 62, 2922–2926 CrossRef CAS.
- J. W. Boclair, P. S. Braterman, B. D. Brister and F. Yarberry, Chem. Mater., 1999, 11, 2199–2204 CrossRef CAS.
- J. C. Villegas, O. H. Giraldo, K. Laubernds and S. L. Suib, Inorg. Chem., 2003, 42, 5621–5631 CrossRef CAS PubMed.
- S. Mandal, D. Tichit, D. A. Lerner and N. Marcotte, Langmuir, 2009, 25, 10980–10986 CrossRef CAS PubMed.
- L. Ai, C. Zhang and L. Meng, J. Chem. Eng. Data, 2011, 56, 4217–4225 CrossRef CAS.
- N. Kannan and M. M. Sundaram, Dyes Pigm., 2001, 51, 25–40 CrossRef CAS.
- K. Morimoto, K. Tamura, N. Iyi, J. Ye and H. Yamada, J. Phys. Chem. Solids, 2011, 72, 1037–1045 CrossRef CAS.
- R. P. Bontchev, S. Liu, J. L. Krumhansl, J. Voigt and T. M. Nenoff, Chem. Mater., 2003, 15, 3669–3675 CrossRef CAS.
- K. M. Parida, M. Sahoo and S. Singha, J. Mol. Catal. A: Chem., 2010, 329, 7–12 CrossRef CAS.
- N. N. Das and S. C. Srivastava, Bull. Mater. Sci., 2002, 25, 283–289 CrossRef CAS.
- N. N. Labidi, A. Ghorbel, D. Tichit and G. Delahay, React. Kinet. Catal. Lett., 2006, 88, 261–268 CrossRef CAS.
- Z. Houa and T. Yashima, Appl. Catal., A, 2004, 261, 205–209 CrossRef.
- K. Parida, L. Mohapatra and N. Baliaarsingh, J. Phys. Chem. C, 2012, 116, 22417–22424 CAS.
- K. Parida, M. Satpathy and L. Mohapatra, J. Mater. Chem., 2012, 22, 7350–7357 RSC.
- R. K. Sahu, B. S. Mohanta and N. N. Das, J. Phys. Chem. Solids, 2013, 74, 1263–1270 CrossRef CAS.
- F. Cavani, F. Trifiro and A. Vaccari, Catal. Today, 1991, 11, 173–301 CrossRef CAS.
- F. Kovanda, T. Grygar, V. Dorničák, T. Rojka, P. Bezdička and K. Jirátová, Appl. Clay Sci., 2005, 28, 121–136 CrossRef CAS.
- T. Shishido, M. Sukenobu, H. Morioka, M. Kond, Y. Wanga, K. Takaki and K. Takehira, Appl. Catal., A, 2002, 223, 35–42 CrossRef CAS.
- L. Chmielarz, P. Kustrowski, A. Rafalska-Łasocha and R. Dziembaj, Thermochim. Acta, 2003, 395, 225–236 CrossRef CAS.
- W. Xie, H. Peng and L. Chen, J. Mol. Catal. A: Chem., 2006, 246, 24–32 CrossRef CAS.
- M. B. Gawande, R. K. Pandey and R. V. Jayaram, Catal. Sci. Technol., 2012, 2, 1113–1125 Search PubMed.
- C. Yuan, H. B. Wu, Y. Xie and X. W. Lou, Angew. Chem., Int. Ed., 2014, 53, 1488–1504 CrossRef CAS PubMed.
- W. T. Reichle, Solid State Ionics, 1986, 22, 135–141 CrossRef CAS.
- F. Li, X. Jiang, D. G. Evans and X. Duan, J. Porous Mater., 2005, 12, 55–63 CrossRef CAS.
- J. M. Fraile, N. Garcia, J. A. Mayoral, E. Pires and L. Roldan, Appl. Catal., A, 2009, 364, 87–94 CrossRef CAS.
- W. Trakarnpruk, J. Met., Mater. Miner., 2012, 22, 131–136 CAS.
- P. Deka, R. C. Deka and P. Bharali, New J. Chem., 2014, 38, 1789–1793 RSC.
- B. Naik, S. Hazra, V. S. Prasad and N. N. Ghosh, Catal. Commun., 2011, 12, 1104–1108 CrossRef CAS.
- M. An, J. Cui and L. Wang, J. Phys. Chem. C, 2014, 118, 3062–3068 CAS.
- A. Cwik, A. Fuchs, Z. Hell and J.-M. Clacens, Tetrahedron, 2005, 61, 4015–4018 CrossRef CAS.
- R. Manikandan, P. Anitha, G. Prakash, P. Vijayan and P. Viswanathamurthi, Polyhedron, 2014, 81, 619–627 CrossRef CAS.
- M. Sutradhar, M. F. C. Guedes da Silva and A. J. L. Pombeiro, Catal. Commun., 2014, 57, 103–106 CrossRef CAS.
- M. K. Ram Reddy, Z. P. Xu, G. Q. (Max) Lu and J. C. Diniz da Costa, Ind. Eng. Chem. Res., 2006, 45, 7504–7509 CrossRef CAS.
- N. D. Hutson, S. A. Speakman and E. A. Payzant, Chem. Mater., 2004, 16, 4135–4143 CrossRef CAS.
- W. Yang, Y. Kim, K. T. Liu, M. Shahimi and T. T. Tsotsis, Chem. Eng. Sci., 2002, 57, 2945–2953 CrossRef CAS.
- D. Tichit, M. N. Bennani, F. Figueras and J. R. Ruiz, Langmuir, 1998, 14, 2086–2091 CrossRef CAS.
- M. Bellotto, B. Rebours, O. Clause, J. Lynch, D. Bazin and E. Elkaïm, J. Phys. Chem., 1996, 100, 8535–8542 CrossRef CAS.
- C. Noda Pérez, J. L. F. Monteiro, J. M. L. Nieto and C. A. Henriques, Quim. Nova, 2009, 32, 2341–2346 Search PubMed.
- A. Corma, S. Iborra, J. Primo and F. Rey, Appl. Catal., A, 1994, 114, 215–225 CrossRef CAS.
- M. J. Climent, A. Corma, S. Iborra and J. Primo, J. Catal., 1995, 151, 60–66 CrossRef CAS.
- M. J. Climent, A. Corma, S. Iborra, K. Epping and A. Velty, J. Catal., 2004, 225, 316–326 CrossRef CAS.
- C. Noda Pérez, C. A. Pérez, C. A. Henriques and J. L. F. Monteiro, Appl. Catal., A, 2004, 272, 229–240 CrossRef.
- J. I. Di Cosimo, V. K. Díez, M. Xu, E. Iglesias and C. R. Apestegía, J. Catal., 1998, 178, 499–510 CrossRef CAS.
Footnote |
† Electronic supplementary information (ESI) available: XRD analysis and the textural properties of mixed oxides, the effect of calcination temperature on nitro-aldol reaction, the recyclability test, N2 adsorption–desorption isotherms and pore size distribution of MgAl and CoMgAl mixed oxides, N2 adsorption–desorption isotherms of NiMgAl mixed oxide at different calcination temperatures, the turnover frequency (TOF) plot of mixed metal oxides, and 1H and 13C NMR spectra of the pure product. See DOI: 10.1039/c4nj01332h |
|
This journal is © The Royal Society of Chemistry and the Centre National de la Recherche Scientifique 2015 |
Click here to see how this site uses Cookies. View our privacy policy here.