DOI:
10.1039/C5MH00136F
(Review Article)
Mater. Horiz., 2015,
2, 553-566
Structural design for anodes of lithium-ion batteries: emerging horizons from materials to electrodes
Received
13th July 2015
, Accepted 11th August 2015
First published on 11th August 2015
Abstract
High performance anodes are of great significance to high energy-power lithium ion batteries (LIBs); however, challenges are still pervasive in advancing new materials beyond commercial graphite. In this review, we outline the subsistent concerns on these adolescent anodes and systematically summarize the representative problem-solving designs, which are classified into two major categories totally including seven types, namely low-dimensional, inter-spatial, and composite design on materials; and ordered-array, cross-aligned, alternating-layer, and 3D porous design on electrodes. After generalizing advantageous features, we further highlight the burgeoning design horizon from materials to electrodes as well as their competences and perspectives to push the energy storage of LIBs to the next-generation level. These designing rationales represent general models of advanced LIB anodes and can illuminate the material and electrode innovations in other energy storage realms.
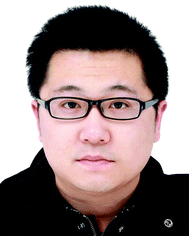
Yiren Zhong
| Yiren Zhong was born in Shandong, China in 1991. He received his BS degree in Chemistry in 2012 and ME degree in Materials Physics and Chemistry in 2015 (Advisor: Prof. Zhen Zhou) from Nankai University. Currently, he is working on his chemistry PhD program under the supervision of Prof. Hailiang Wang at Yale University. His research interest focuses on materials design for energy storage and conversion. |
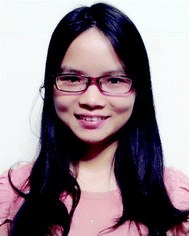
Mei Yang
| Mei Yang was born in Guizhou, China in 1988. She received her BS degree from Beijing Jiaotong University in 2010, and PhD degree from Nankai University in 2015 (Advisor: Prof. Zhen Zhou). She is currently an assistant professor at the School of Materials Science and Engineering of Nanjing University of Science and Technology. Her research interest focuses on energy storage systems with both high energy and power density. |
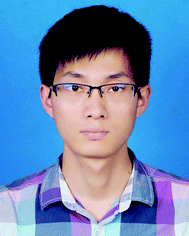
Xianlong Zhou
| Xianlong Zhou was born in Hubei, China in 1989. He received his BS degree from South-Center University for Nationalities in 2013. He is currently working on his ME degree at Nankai University (Advisor: Prof. Zhen Zhou). His research interest primarily focuses on electrochemical energy storage and conversion. |
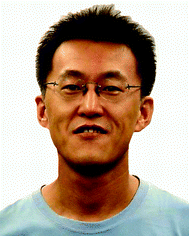
Zhen Zhou
| Zhen Zhou was born in Shandong, China in 1971. After he received his BSc in 1994 and PhD in 1999 at Nankai University, China, he joined the faculty in 1999. Two years later, he began to work at Nagoya University, Japan as a JSPS postdoctoral fellow. In 2005, he returned to Nankai University as an associate professor. In 2011, he was promoted as a full professor. He is now the Director of Institute of New Energy Material Chemistry, Nankai University. His main research interest is design, preparation and application of advanced materials for energy storage and conversion. |
1. Introduction
The fast economic development and huge energy consumption have triggered rapid depletion of fossil fuels along with large emission of CO2. To sustain non-renewable resources and solve this urgent global-warming concern, one way-out is to exploit various kinds of green energy sources, such as wind and solar energy. Yet discontinuous and intermittent nature of these renewable energies always leads to low efficiency of energy conversion and utilization, thus imperiously requiring powerful electrical energy storage (EES) to support the integration of new energies in smart grids.1,2 Amongst all the practical EES systems, lithium-ion batteries (LIBs) stand out from the conventional crowd owing to their higher gravimetric and volumetric capacity as well as better energy efficiency and power performance.3 Proposed in the early 1980's and commercialized from 1992, LIBs have become an underpinning star in the mobile energy market, with world-wide deployment ranging from personal electronics like mobile phones to large-scale applications such as electrical vehicles (EVs).4,5
A classical LIB prototype consists of layered LiCoO2 cathodes and lamellar graphite anodes, sandwiching electrolytes of the LiPF6 salt in mixed organic solvents and porous polymer membrane separators. Apparently, after nearly three decades of development, LIBs have entered a new era, with demanding criteria of higher energy-power integration to satisfy large-scale energy applications.6 For example, EVs, aiming at replacing conventional internal combustion vehicles and creating a zero-emission environment, require a long-range travelling distance of over 500 km per charge, yet presently LIBs could only afford a far shorter distance of 160 km.7 In terms of the energy and power density of mass applications, LIBs hold a bright future but still have a long way to go.
As the major constituent of LIBs, electrode materials (cathodes and anodes) are the key factors to upgraded performances towards high energy and power density. While improving the voltage and elevating ultimate Li storage of cathodes, researchers worldwide are casting about ways of substituting conventional graphite anodes.8,9 Owing to the limitation of lithium accommodation in the honeycomb lattice interlayer (LiC6) and low lithium diffusion coefficient (10−9 to 10−7 cm2 s−1), graphite exhibits undesirable Li-storage performances with restricted capacity (theoretically 372 mA h g−1) and also inferior rate capability, which cannot meet the ever-growing demand for high performances.10,11 Until now, many types of advanced anode materials have been innovatively explored, insightfully studied, and typically classified into three categories based on different storage mechanisms: insertion/extraction type (hard carbon, Li4Ti5O12, TiO2-B, etc.), alloying/dealloying type (Si, Sn, Ge, etc.), and conversion type (metal oxides, sulfides, oxysalts, etc.). Many previous reviews have already summarized or included LIB anodes following these three classes, mainly highlighting the pros and cons of particular materials as well as the nanosized effect on Li storage performances,10,12–14 which will not be specially mentioned in this review.
It has reached a consensus that structural design of morphologies and textures is essential for anode materials. With rational and favourable construction, a LIB anode could effectively solve common concerns induced by intrinsic drawbacks, such as structural expansion and agglomeration, poor conductivity, and Coulombic inefficiency.15,16 However, it is rarely noticed and summarized from a large scope of LIB anodes: the architectural buildings of electrodes. While coming to the electrode level, rational design is more difficult to control the whole structure to achieve high-level performance. In addition to the aforementioned concerns at the material deck, consideration is more complicated within overall electrodes, involving electron and ion transportation in a larger range, mechanical and electrical contact between active materials and current collectors, integrity and continuity of electrode entirety, etc. In this review, we focus on the structural design of advanced LIB anodes, wherein a neoteric horizon is introduced from materials design to electrode construction. To initialize the discussion, we first briefly present several common issues that jeopardize the Li storage performance of LIB anodes. Afterwards, materials design is elaborately summarized through three categories: low dimensional, inter-spatial and composite design, with further advancement towards electrode-level design (ordered-array, cross-aligned, alternating-layer, and 3D porous design, Fig. 1). In each section, we will discuss the metrics of structural characteristics, revisit state-of-the-art paradigms, conclude the general influence of structures on performances regarding the corresponding category. The selective horizon from materials to electrode design on LIB anodes will help understand the correlation between structural advantages and battery performances, build better electrode architectures to attain high energy-power storage, and could further be extended to broad realms in energy storage and conversion.
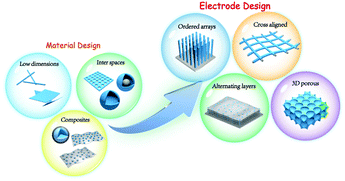 |
| Fig. 1 General illustration of emerging horizons from materials to electrode design. | |
2. Common issues of LIB anodes
2.1 Material issues
As mentioned, most technical issues of LIBs rely on the delicate and rational structural design. Typically, Li storage capacity, cyclic stability and rate capability constitute the evaluation of a laboratorial or half-cell battery, which needs careful engineering of material structures and further extends to electrode-level design, such as ion and electron kinetics, architectural integrity and interface stability. Furthermore for overall consideration of battery entirety regarding energy and power density (gravimetric or volumetric), it is of more importance to concentrate on electrode-level engineering, such as electrode geometry, continuity, mechanical attachment and bendability. In this section below, we are going to summarize the main issues that need to be taken into account when designing an advanced LIB anode.
Li ion and electron transport.
It is acknowledged that in LIBs' chemistry, an effective electrochemical reaction relies on the simultaneous intercalation of Li+ and e− into the Li storage host within electrodes (Fig. 2a).17 In this regard, concurrent control of ion and electron transport to achieve fast kinetics is essential for high performance anodes, including ion and electron diffusion within or between active materials as well as across electrolyte–electrode interfaces. For advanced anodes with diffusion-controlled kinetics, creating nanosized dimensions can effectively enhance the transport velocity over the bulk counterpart, which could benefit the complete utilization of active materials to gain high capacity even under high-rate circumstances. Moreover, as most neotype anodes are trapped into low electrical conductivity, accretion of heterogeneous conducive additives could further benefit Li storage performance by strengthening valid conductivity.
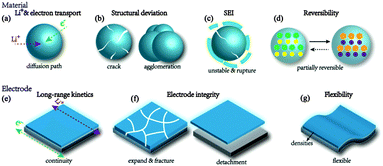 |
| Fig. 2 Illustration of common issues of LIB anodes: (a)–(d) the material level; (e) and (f) the electrode level. | |
Structural deviation.
Structural deviation arises from the phase changes during Li storage processes. Distinct from the insertion/extraction mechanism, phase-change reactions could facilitate high capacity owing to their breakthrough of host limitation and introduction of multi-electron reactions by taking advantages of the phase-change mechanism (bond breakage for alloys and phase transition for conversion, Fig. 2b). However, along with these phase evolutions, most anode materials cannot completely retrieve back to the original structures, thus demonstrating gradual deterioration on structural integrity, including volume expansion, particle pulverization and agglomeration.16,18 These fabric deformations will cause a series of lengthy and feeble electron and ion diffusion pathways, which result in the inactivity of host materials and finally lead to poor cyclic stability.
Solid electrolyte interphase.
When the electrochemical potential of anodes is lower than the lowest unoccupied molecular orbital (LUMO) of the electrolyte, a passivation layer will form on the surface through the reduction of electrolyte constituents, which is called solid electrolyte interphase (SEI) film.19 Based on the original models and further investigations, SEI film is regarded to be comprised of a series of lithium salts and some polymeric species, which allows Li+ penetration and offers protection to anode materials.20,21 However, these interphases have low electrical conductivity, wherein thick SEI film will not only insulate electron tunnelling but also affect lithium ion diffusion. In this scenario, structural deformation will impose negative effects on these important interphases, including instability, rupture, constant formation and incrassation of SEI film, which lead to severely low Coulombic efficiency and capacity fading (Fig. 2c). Except architectural detriment, decomposition of surface layers will also cause unstable SEI film, leading to large irreversible capacity commonly in conversion-type anodes.
Reversibility.
Coulombic efficiency and hysteresis are the key indices of reversibility. Except the mechanical failure of SEI film and structural integrity, low efficiency caused by thermodynamic irreversibility is also pervasive in many anode materials (Fig. 2d).22 Usually existing in many carbonaceous and conversion-type anode materials, this intrinsic irreversibility manifests divergence from the equilibrium reaction potential with additional consumption of Gibbs free energy, generating large voltage hysteresis in electrochemical behaviors.16 Consequently, the poor reversibility will arouse round-trip inefficiency and further huge energy loss, thus undermining the energy-power output of batteries in practical applications.
2.2 Electrode issues
Long-range kinetics.
Similar to materials, ion and electron diffusion relies on the geometry and structure of electrodes. Although good ion and electron transport is realized at the material level, the electrode may not show facile kinetics in a wide range (Fig. 2e).23 According to the thermal carrier trapping and release model, disordered structures form carrier trapping centres and produce a significant decrease of carrier mobility, which cannot develop an effective percolation path.24 Consequently, the uneven distribution of active materials and conductive carbon, or large cavities and void spaces within the electrode will result in feeble ion and especially electron diffusion and further inferior rate performances. In addition, the thickness and porosity also affect the overall transport, wherein thick and dense electrodes will elongate the ion and electron diffusion path.
Electrode integrity.
It is naturally adopted that material-level structural distortion will lead to the failure of electrode integrity. Typically, the material agglomeration or volume expansion will directly cause severe destruction at a larger scope, including bulge, concave and fracture within the overall electrode, which usually lead to poor cyclic stability (Fig. 2f).25,26 Except this electrode instability on the active material layers, there is another type of common issue regarding integrity, namely the mechanical and electrical contact between material layers and current collectors. Current collectors play significant roles in gathering electrons and facilitating electron transfer to active materials, which guarantees the basic electron supply for a valid electrochemical reaction. Once the materials are detached from current collectors (usually caused by volume variation), the electron pathways are blocked by the invalidation of electrochemical reactions, leading to “dead or inactive” Li-storage sites. The unsuccessful utilization of active materials will finally give rise to fast capacity fading and Coulombic inefficiency.
Flexibility.
With the development of personalization and diversification of electronics, the market puts forward the new demand for arbitrary shaped devices, which make flexibility or bendability a fresh requirement for the electrode used in flexional energy storage.27 Traditional LIB anode structures based on metal current collectors (i.e., Cu) are not applicable in this new-concept energy storage, as continuous folding strains will crack the electrode and impair the Li storage performance. Transforming from rigid basements to flexible architectures, ductile current collectors need to be utilized by further building a robust and interlinked matrix inside the structures (Fig. 2g). In particular, packing density should be carefully considered in these devices as many flexible electrodes are fabricated by low-density carbonaceous materials. To achieve compact energy storage, anode architectures should be carefully designed towards less void spaces and more active mass loading within the electrode (Fig. 2g).28
3. Materials design for LIB anodes
3.1 Low-dimensional design
Unlike bulk structures, materials with low dimensional structures (such as 0D nanodots, 1D nanowires, and 2D nanosheets) possess various unique advantages regarding transport kinetics and mechanical properties. Apparently, reducing dimensions endow materials with a shorter diffusion length and a large exposed surface for electrochemical procedures (Fig. 3a). Except for these kinetic virtues, such materials with specific morphology could facilely control the mechanical strain induced by volume variation, thus generating robust structural integrity.29
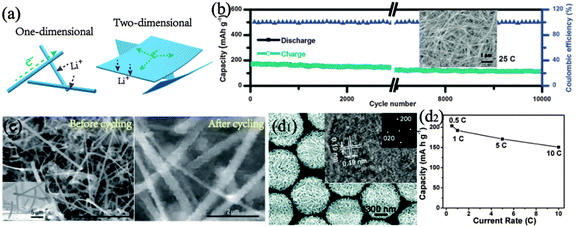 |
| Fig. 3 (a) Schematic illustration of 1D and 2D structures. (b) Long-term cyclic performance of elongated TiO2(B) nanotubes; the inset shows a typical scanning electron microscopy (SEM) image. Reproduced with permission from ref. 31. Copyright©2014, Wiley-VCH. (c) SEM image of Si nanowires before and after 5 charge–discharge cycles. Reproduced with permission from ref. 32. Copyright©2008, Nature Publishing Group. (d1) SEM, high-resolution transmission electron microscopy (HRTEM, inset) images and selected area electron diffraction (SAED, inset) with an indication of the exposed (001) facet; (d2) the rate performance of hierarchical TiO2 spheres. Reproduced with permission from ref. 41. Copyright©2010, American Chemical Society. | |
1D structures.
There is one significant parameter for 1D structures, namely the aspect ratio, which represents the length-to-diameter proportion in the 1D geometric configuration (nanowires, nanotubes, nanorods, nanobelts, etc.). While the long extension imparts good electrical contact between nanowires, the diameter is directly related to the ion diffusion path upon Li+ insertion and extraction.6 It is also elucidated that increasing the aspect ratio will optimize the electron/ion transport properties and enhance the Li storage performance at high rates.30 Recently, Tang et al. have rationally designed elongated TiO2(B) nanotubes via mechanical force-driven growth. Long nanotubular architectures with facile transport kinetics and high specific surface favour ultrafast lithium storage, which is highlighted by a large capacity of 114 mA h g−1 at 25 C rate for 10
000 cycle stability (Fig. 3b).31
Except for favourable ion diffusion, 1D materials with facile strain relaxation can also benefit effective control of structure deviation. As demonstrated by the Cui group, the structure of crystalline Si nanowires remains continuous and intact with only rough sidewalls on the edge and no fractured small parts, which still maintains good electrical conductive pathways. This restraint on the volume expansion ensures the decent cyclic stability even for a full deep discharge of ∼3500 mA h g−1 (Fig. 3c).32 Besides, as basic building blocks, these 1D structures could construct 3D structures with inter-wire spaces or ordered ensembles, which further benefit high-rate capability and cyclic stability.33–36
2D structures.
Similarly, the low index of thickness in 2D materials represents easier ion diffusion, which can be facilely narrowed down to lower than 10 nm through a simple synthetic protocol owing to the morphological advantage (Fig. 3a).37,38 The expansive characteristic can also facilitate a facile electron transport path across the 2D plane. Kim et al. prepared SnS2 nanosheets with variable thickness ranging from 2 to 26 nm. Through a systematic comparison amongst different nanosheets, it is disclosed that a 2 nm-thick SnS2 structure possesses the highest performance especially rate capability with 70% capacity retention of the initial value at 5 C, owing to the advantages on fast reaction kinetics.38 Liu et al. presented a nanosheet-assembly of ultrathin TiO2(B) with a high capacity of 202 mA h g−1 at 10 C and also good maintenance even at 30 C. In particular, compared with nanoparticles on the same scale and also nanowires or nanotubes, TiO2(B) nanosheets show obvious rate preponderance, highlighting the easy access of ultrathin nanoscale and rapid transport of the 2D structure.37 With regard to the stability, although 2D materials with an extensive scale own favourable relaxation of strains than particles, they are usually built on various flexible substrates forming a face-to-face fashion to further increase the structural robustness and ion/electron diffusion.39
In addition to common merits of other low-dimensional designs, 2D geometry brings opportunities to selectively expose the specific crystallographic facet. This unique characteristic is utilized to optimize the ion diffusion path in cathode materials,40 and can also boost the Li storage performances by creating abundant exposure of highly active surfaces. Chen et al. constructed hierarchical TiO2 structures assembled by ultrathin nanosheets with nearly 100% exposure of (001) facets (Fig. 3d1).41 The high facet activity accompanied by efficient ion diffusion along the [001] axis based on the dominating population of (001) planes renders TiO2 high reversible capacity even at fast insertion/extraction rates (Fig. 3d2).
3.2 Inter-spatial design
Generally, the aim of inter-spatial design (Fig. 4a) is to create pores or voids within the material structures, including various porous, hollow and yolk–shell structures. The interspace immensely promotes the infiltration of electrolytes than stuffed structures, and could delicately manufacture interconnected nanoscale sidewalls surrounding its hollow textures.42 Combining the continuous and fine-scale merits of wall frameworks, these advantageous features of interspatial structures facilitate huge improvement on rate capability of Li storage. Furthermore, the large internal space could perfectly accommodate a large volume change, thus protecting the original structure from damages during the whole cycling process.43
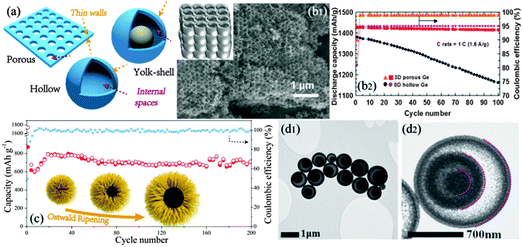 |
| Fig. 4 (a) Schematic illustration of porous, hollow and yolk–shell designs. (b1) SEM, illustration and (b2) electrochemical performance of 3D ordered porous Ge. Reproduced with permission from ref. 48. Copyright©2010, Wiley-VCH. (c) Synthetic mechanism and cyclic stability of rambutan-like hollow FeCO3 microspheres. Reproduced with permission from ref. 56. Copyright©2013, American Chemical Society. (d1 and d2) TEM images of yolk double-shelled SnO2. Reproduced with permission from ref. 59. Copyright©2013, Wiley-VCH. | |
Porous structures.
Porous structures are ubiquitous elements in many rational anode designs. It could be harmoniously integrated into many prototypes in various structural designs by the construction of pores at all dimensions. Ge et al. fabricated porous Si nanowires by one-step construction of massive pores on 1D architecture. Integrating the merits of both designing rationales, the as-prepared materials manifest outstanding Li storage performances.44 Accordingly, the porous Si nanowires stably achieve a high capacity over 2000 mA h g−1 at 2 A g−1, and maintain 1100 mA h g−1 even at ultrafast 18 A g−1 with long 250-cycle duration. In addition, they theoretically simulated the lithiation of Si and found the efficient management of volume expansion strain in the porous structure, which is also proved by the direct visualization of structural stability during cycling.45
Apart from randomly distributed pores, ordered porous structures were also investigated, highlighting the bicontinuous wall and pore with interconnected ion and electron diffusion pathways.46,47 For example, Cho and co-workers prepared 3D ordered porous Ge assembly regulated with uniform SiO2 templates, which shows a high capacity of over 1400 mA h g−1 at the fast rate of 1.6 A g−1 and also good reversibility with 99% Coulombic efficiency (Fig. 4b).48 It is generally known that pores are classified into three categories: micro- (<2 nm), meso- (2–50 nm) and macro- (>50 nm) pores. Other than controlling uniformity, hierarchical porous structures constituted by two or more kinds of pores show similar superior electrochemical performances in LIB anodes. Incorporating macro- and meso-(or micro-) pores can simultaneously improve the ionic diffusion kinetics and enhance the specific surface of active materials with interconnected features to further strengthen both the advantages. Shen et al. reported hierarchically porous Li4T5O12 (LTO) with artful meso- and macro-porosity built from an interconnected 3D network. Hierarchical channels create easy ion and electron diffusion pathways while the highly mesoporous fabrics introduce a large surface area, allowing 20 C rate high capacity and also the excellent Coulombic efficiency of 100% for a long cycle life.49 Such superior performances are also observed in other similar hierarchical constructions, such as amorphous GeOx and TiO2.50,51
Hollow structures.
Hollow structures with thin walls for Li diffusion and large volume-containable voids could benefit higher capacity and better stability than solid particles. For instance, iron oxide hollow nanoparticles attain 1228 mA h g−1 capacity with good stability, especially the significantly improved capacity with excellent rate capability;52 the interconnected Si hollow particles achieve high capacity of 2500 mA h g−1 at 0.5 C for 700 cycles.53 Actually, a single hollow structure cannot perfectly hold the structural integrity and sustain good cyclic stability, thus rational integration of other beneficial elements is always necessary. The plain outer-shells offer a devisable platform for building versatile hybridized structures and incorporating additional virtues, wherein many novel structures with 1D, 2D or porous subunits are involved.54,55 Based on the Ostwald ripening mechanism, Zhong et al. prepared rambutan-like hollow FeCO3 microspheres constituted by 1D nanofiber porous assembly.56 The unique porous architectures within 1D building blocks and large interior voids strengthened structural stabilization and contributed to efficient ionic transportation, leading to high Li-storage capability for a prolonged cyclic stability up to 200 cycles (Fig. 4c).
Except delicately producing various external shells, controlling the interior fabric has been intensively studied as an efficient strategy for improving volumetric performances. Since increasing occupation rate of active materials makes the hollow entirety approach the stuffed materials, it is of great significance to carefully engineer the internal hollow spaces, such as thickness, multi-shell and porosity.57,58 Recently, controllable syntheses of Fe2O3 hollow spheres were developed by Wang and co-workers, highlighting the tuneable multi-shell structure and wall thickness. It is demonstrated that the porous triple-shell structures generate maximum Li storage and thin exoteric wall fabrics provide superior cycling behavior.58 Although the enhancing effect of multi-shell assembly remains unclear (the same cases are also observed in Co3O4, possibly due to the improved surface area and further reversibly interfacial energy storage), such hollow design offers guidance towards desirable anode performances with enhanced energy density.
Yolk shell structures.
As mentioned above, the low tap density of hollow materials induces a barrier for their practical applications as LIB anodes. Other than inheriting the merits of hollow structures, yolk–shell materials with a core@void@shell configuration always demonstrate improvement of rate capability and especially energy density through implanting cores into hollow interior. Meanwhile, shell structures could also be manipulated to further increase the weight fraction of the electrochemically active materials. A yolk double-shelled SnO2 was prepared by the Kang group, which shows high and stable performances even at 5 C rate benefiting from the uniform void space and appropriate porosity (Fig. 4d).59 Similar routes are engaged in various ZnCo2O4 nanostructures to shed light on comparison between hollow and yolk shell structures. It turns out that the significant core component not only improves the rate capability, but also reinforces the cyclic stability, disclosing the advantages of intelligent void-space utilization within hollow structures.60
3.3 Composite design
Although improvements of electrochemical performances are achieved, the forenamed morphological designs on single-phase materials can only optimize the inherent properties of materials but cannot radically resolve the underlying drawbacks, such as poor conductivity and low Coulombic efficiency. In this section, we will review the extrinsic design of hybrid structures by integrating heterogeneous additives into active materials to enhance the overall mechanical and electrical properties. The discussion will focus on the composite design based on carbonaceous materials.
Carbon allotropes, such as graphene and carbon nanotubes, own flexible and robust mechanical properties as well as highly efficient electron conductivity due to their honeycomb sp2-C building blocks.61 Despite the fact that most of these plain carbonaceous materials demonstrate relatively inferior in-house Li storage, their addition in composites reveals a huge advancement of electrochemical performance when forming well-proportioned core–shell and hybrid structures.23,62–64 Generally, proper incorporation of carbon components can form a highly conductive matrix and favourable stress accommodation, setting a base for high performances with superior rate capability and cyclic stability, respectively. Furthermore, these extrinsic designs make it feasible for integrating multi-designing rationales into various novel single-phase structures, further strengthening the Li storage performance.
Core–shell structures.
Core–shell structures with versatile cores and highly conductive carbon shells provide much superiority when employed as LIB anodes. The flexible and protective carbonaceous outlayers offer strong confinement and a shield for inside vulnerable materials, hence reducing the particulate agglomeration and side reactions with high reversibility and also Coulombic efficiency (Fig. 5a).9 Yuan et al. proposed Fe3O4@C microcapsules consisting of mesoporous nanorods and uniformly coated carbon sheaths (Fig. 5b1).65 The supplementary 1D and mesoporous features offer further enhancement in Li permeation and structural integrity, thus imparting the core–shell structure excellent stability and rate performance. Note that the close-packed core–shell structure without inner space may not effectively accommodate the huge inward expansion, such as Si materials. Based on similar internal void concerns, Cui and co-workers presented a series of spatial design in core–shell structures.66,67 For instance, a yolk–shell structure resembling pomegranate was fabricated with rational engineering of the inner empty space. Such structures allow the free volume expansion without breaking the carbon shells in each secondary unit, even in the high particle-packing-density assembly (Fig. 5c).28 The Si@void@carbon pomegranate achieves excellent cyclic stability (97% capacity retention for 1000 cycles) and high mass loading with improved areal capacity (Fig. 5d), as well as particularly high volumetric capacity which is twice that of graphite anodes.
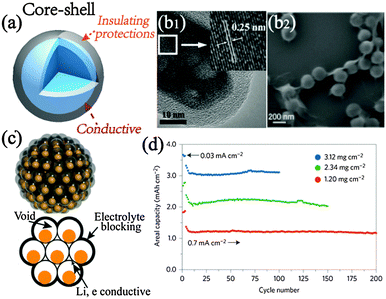 |
| Fig. 5 (a) Schematic illustration of core–shell structural design. (b1) SEM image of mesoporous Fe3O4 nanorod@C microcapsules; inset is the d-spacing of the [311] reflections. Reproduced with permission from ref. 65. Copyright©2011, American Chemical Society. (b2) Typical model of graphene encapsulated structures. Reproduced with permission from ref. 71. Copyright©2010, Wiley-VCH. (c) Illustration and (d) areal performance with different mass loadings of pomegranate-like microspheres. Reproduced with permission from ref. 28. Copyright©2014, Nature Publishing Group. | |
Carbonaceous engineering is also a key parameter for the core–shell composite,68 and a uniform and continuous layer with appropriate thickness is highly needed to achieve the optimal electrochemical performance. Reportedly, a conformally dopamine-derived carbon coating of 10 nm thickness on Fe3O4 possesses higher capacity and cyclic stability than the thicker 24 nm and thinner 2 nm coating. It is well acknowledged that N-doping greatly benefits carbon materials on electrical conductivity. Also, the N-induced defects facilitate fast Li percolation and additional Li storage compared with plain carbon materials.69 Hu et al. developed N-doped carbon coating on porous LTO through an ionic liquid based strategy. With more efficient ion filtration and charge transfer at the interface, LTO with 3D conductive networks shows better rate performance and lower hysteresis than non-doped carbon coating, let alone the pristine materials.70 Other than chemical doping to enhance the coating effect, an emerging model of graphene coating also exhibits superior performance with more robust mechanical structure and better electrical conductivity. Yang et al. assembled monodispersed metal oxide@graphene by electrostatic force (Fig. 5b2), wherein the thin graphene coating gives rise to high content of the active oxide.71 When evaluated as LIB anodes, the encapsulated structures show stably high Li storage performance owing to the aforementioned architectural merits.
Hybrid structures.
Graphene with ultrafast electron mobility and outstanding mechanical strength as well as high thermal stability endows the overall active material–graphene hybrids with unique electrochemical performance, obtaining fruitful improvement even under simple mechanical mixing (Fig. 6a).72 It is highlighted that graphene or reduced graphite oxide (RGO) shows attractive synergistic effects when forming hybrids.62 Briefly, the 2D graphene offers extensive support for uniform loading of nanostructures and the nanosized active materials act as nanospacers to refrain the restacking of graphene, thus forming the well-proportioned hybrid construction at all dimensions. For instance, uniformly distributed Mn3O4/RGO composites reported by Wang et al. show great enhancement in reversible capacity and stability than free Mn3O4 (Fig. 6b1);73 CoCO3 cube/graphene composites exhibit high reversible capacity of over 1000 mA h g−1 with improved retention.74 Besides, the expansive graphene domains afford various geometric particle loadings, such as 1D nanorods and 2D nanosheets with face-to-face stacking, which all reveal enhanced electrochemical performance.75–77 The flexible characteristics endow graphene-based materials with the ability of forming versatile intimate 3D structures without rigid connections between the 2D sheets. The 3D graphene (or RGO) matrices establish an interconnected conductive path and a porous internal framework, even forming a stable aerogel as a whole (Fig. 6b2).78,79 The Feng group presented a self-assembled Fe2O3/graphene aerogel (GA) with high reversible storage capacity and favourable rate performance. Taking advantage of the 3D graphene matrix with open porous Li+ infiltration and facilely continuous e− conductivity, Fe2O3–GA displays significant electrochemical improvement over the Fe2O3–graphene nanosheet counterpart.80
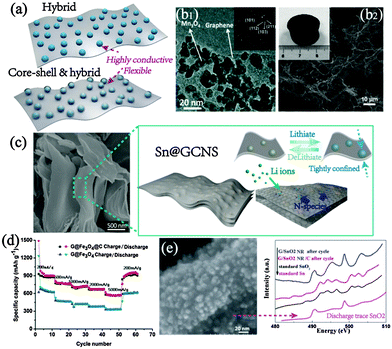 |
| Fig. 6 (a) Schematic illustration of typical hybrid and hybrid-coating designs. Representative examples of (b1) a graphene hybrid and (b2) a 3D graphene-based composite aerogels (inset shows the optical image of aerogels). Reproduced with permission from ref. 73 and 90. Copyright©2010 and 2014, American Chemical Society, respectively. (c) SEM and the designing strategy of Sn/graphene-based N-rich carbon. Reproduced with permission from ref. 89. Copyright©2015, Wiley-VCH. (d) Rate contrast between carbon-coated graphene hybrids and pristine graphene hybrids. Reproduced with permission from Ref. 91. Copyright©2012, American Chemical Society. (e) SEM image of sandwiched graphene/SnO2 nanorod/carbon with hybrid & core–shell design and Sn M edge X-ray absorption near edge structure (XANES) spectra of cycled products tracing the standard SnO2. Reproduced with permission from ref. 96. Copyright©2013, Royal Society of Chemistry. | |
However, note that the simple anchoring of active particles on graphene may not achieve the desirably stable performance, especially for anodes with high volume expansion upon cycling. Reportedly, the crumpled self-wrapped 3D Si/graphene derived from 2D Si/graphene composites reveals significantly enhanced stability and rate capability compared with the pristine anchored construction.81 Besides, a sandwich design with alternating layer-by-layer structure is also effective in the volume expansion suppression and capacity elevation. As shown by Prabakar et al., the strong-coupled composites comprised of alternating arrangement of SnO2 and graphene layers demonstrated excellent structural robustness, resulting in high and stable Li storage during cycling.82 The densely packed and ordered feature can admirably regulate the macroscopic volume change, with only half volume expansion than the merely anchored SnO2 hybrids. Similar results of improved cyclic stability were also reported for Si and other metal oxides.83–85
Similarly, N-doping also has positive effects on electrochemical performance, such as high conductivity, extra energy storage and facile ion penetration,86,87 which could solve the suggested negative effect on the Li+ mobility in the mixed graphene composites.23,88 Combining the intersectional design of graphene hybrids, the N-doped composites always obtain superior lithium storage properties. Zhong et al. in situ embedded ultrasmall Sn into graphene-based N-rich carbon sheets (GCNSs) and fabricated well-proportioned composites.89 The strong-coupled confinement of Sn largely improves the structural stability while the rich N-doping enriches the Li storage sites with 1000-cycle stability, high Coulombic efficiency and reversible capacity, which is observed by the negligible thickness change during cycling and proved by the optimally rich doping content of 13 wt% (Fig. 6c). In addition, analogous designs incorporating geometric control and chemical doping are realized in oxide hybrid structures, such as 3D SnO2, Fe3O4 and CoOx/N-doped graphene.90–92 For example, 3D macroscopic SnO2/nitrogen-doped graphene aerogels exploited by Wang et al. show an outstanding capacity of 1340 mA h g−1 and a high stability of 905 mA h g−1 at 2 A g−1 for 1000 cycles.90
Core–shell and hybrid structures.
As mentioned above, the graphene could offer a highly efficient conductive matrix and stress alleviation yet without complete coating on the exposed active materials, which may prone to disintegrate or aggregate during cycling. The core shell structure with intimate protection instead would isolate active materials from electrolytes. In this respect, the combinative design of versatile core–shell & hybrid architectures facilitates reciprocal merits either on structural stability or electrical conductivity. Su et al. reported a proof-of-concept fabrication of different prototype G@MO@C 2D hybrids. The further carbon coating on the metal oxide–graphene composite significantly improves the cyclic stability while still preserves original advantageous features of graphene, thus leading to high reversible capacity and superior fast storage capability than non-coating materials (Fig. 6d).93 Besides, various 3D core–shell hybrid architectures, such as cross-linked graphene–Fe3O4@graphene94 and graphene network anchored Sn@graphene,95 were fabricated and all succeed in achieving excellent Li storage performance. Other than improving the stability, the coated hybrid feature may render entire structures novel electrochemical performance beyond pristine constructions. Wang et al. reported layer-by-layer assembled sandwiched graphene/SnO2 nanorod/carbon structures, wherein the intact and robust protection reduces the irreversible reactions and improves the interlayered SnO2 stability with high cyclic stability and also Coulombic efficiency.96 Particularly, the strong confinement with little detachment of SnO2 even generates a new discovery of the storage mechanism that enables the conversion reaction (SnO2 + 4Li+ + 4e− → Sn + 2LiO2, commonly considered irreversible) to be reversible, proved by an exceptionally high capacity of 1419 mA h g−1 and a series of electrochemical and spectral measurements (Fig. 6e).
4. Electrode design for LIB anodes
Above we have presented three general categories of materials design for LIB anodes to improve and optimize the electrochemical performances. Although many outstanding structures show enhanced performance in Li storage, there are still challenges considering at the electrode scope to achieve efficient power delivery, superb cyclic stability and high-density energy storage. For example, active particles and graphene in a mixed manner resembling carbon black additives demonstrate a blocked Li diffusion pathway at some directions in the electrode.23 Also, long-range kinetics and electrode integrity of the mixture (active material–carbon additive–binder) should be taken into account, which are needed for the careful design of well-organized structures at the electrode level. Moreover, with a specific basement included, the overall electrodes are able to manifest the flexible feature. In this section, we will review the state-of-the-art designs of myriad desirable architectures from the emerging electrode's horizon.
4.1 Ordered-array design
Directly growing orderly active nano-arrays on versatile conductive substrates offer integrated merits as LIB anodes: (1) oriented and facile conductive pathways; (2) void spaces for restraining structural deviation of the single unit; (3) strong attachment to the electrode protecting from mechanical and electrical separation (Fig. 7a). The Wu group gave a prototype study of mesoporous Co3O4 arrays on the Ti foil, which display excellent performances (700 mA h g−1 at 1 C; up to 50% retention at 50 C with also good cycling stability) when evaluated as LIB anodes (Fig. 7b).97 The 1D array-on-substrate structure with mesoporosity, robust contact and integrity enlarges the conductive and diffusion kinetics, leading to the distinct improvement of rate performance over the peel-off nanowires or powders. It is particularly suggested that the propagation of discharged Co domains along the oriented path generates high electron conductivity to boost the electrochemical reactions, and hence imparts this no-carbon-added structure superior performance. Other than 1D nanowire or nanobelt arrays,98 2D nanosheet or nanoflake99 structures were also fabricated, highlighting the interconnected and porous matrix constructed by the subunits. The interspatial void enables an effective accommodation of volume changes and facilitates good cyclic stability. Song et al. directly captured the anisotropic expansion in the Si nanotube arrayed structures.100 The dominating expansion in the radial direction unmasks the importance of the inter-nanowire space, by reversibly stuffing and releasing upon cycling while maintaining the overall integrity (Fig. 7c).
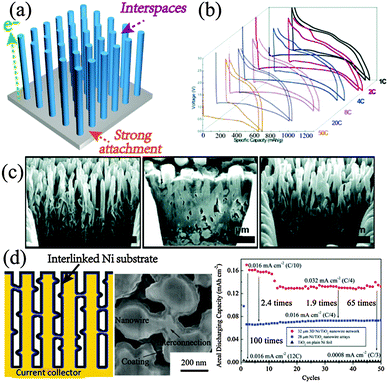 |
| Fig. 7 (a) Schematic illustration of the typical orderly arrayed electrode. (b) Outstanding rate performance of mesoporous Co3O4 arrays on the Ti foil. Reproduced with permission from ref. 97. Copyright©2008, American Chemical Society. (c) Cross-sectional observation of Si arrays during the pristine discharge–charge process. Reproduced with permission from ref. 100. Copyright©2010, American Chemical Society. (d) Scheme and SEM of the interlinked Ni substrate-loaded TiO2 electrode and its electrochemical performance in contrast to arrayed Ni–TiO2 and plain Ni–TiO2 electrodes. Reproduced with permission from ref. 104. Copyright© 2012, American Chemical Society. | |
The further coating by amorphous carbon or hybridization with graphene in the arrayed architectures renders higher conductivity or even a spatially interconnected conductive matrix, which effectively benefits better performance.101 Except building active arrays, depositing active materials on the arrayed substrates (such as Cu, Ni, and carbon nanotubes) also paves the way for high-performance anode construction.102–104 The highly ordered conductive bases with high surface area and facile particle–current collector contact give rise to large mass loading and high areal capacity as well as the superb ion and electron transport. For instance, the uniform Fe3O4-on-Cu arrayed structure fabricated by the Tarascon group demonstrates excellent rate capacity with 80% retention increasing from 0.03 C to 8 C and finally maintains fast and stable 7 min full charge.103 The comparison with the Fe3O4-on-Cu planar structure reveals a high mass loading on the arrayed current collector, with further significantly enhanced power density (5-fold improvement). Wang et al. prepared interconnected Ni arrays coated by TiO2.104 The 3D cross-linked and uniform features endow superior areal capacity with over 2 times straight arrayed Ni/TiO2 and 65 times plain Ni/TiO2, which could be further facilely improved by increasing the nanowire length (Fig. 7d). In term of areal mass loading and capacity, Zhang et al. provided a simple method to fabricate high-density SnO2 nanosheets with double-layer arrays grown on various substrates.105 The dense arrangement produces doubled areal capacity without sacrificing the gravimetric capacity, which offers a hint for the high energy density storage in the arrayed electrode.
4.2 Cross-aligned design
Cross-aligned electrodes based on the interlinked conductive matrix are favourable for electrolyte infiltration and volume change control, forming spatially penetrative and porous networks (Fig. 8a). One of the most classical models for this electrode architecture is carbon cloth based structures, a cross-aligned basis widely used in energy storage electrodes and devices. Till now, varieties of novel nanostructures, such as low-dimensional and hierarchical structures, are constructed on the carbon cloth, revealing comprehensive merits towards high-performance binder-free anodes.106,107 As an example, a hierarchical ZnCo2O4–urchin/carbon cloth electrode shows preeminently high capacity and rate performance (750 mA h g−1 even at 18 A g−1).108 It is claimed that the carbon cloth offers intimate adhesion for ZnCo2O4 and along with a high surface structure in urchin-like subunits (“V” type channel), and generates an expressway for electrons and ions (Fig. 8b). Besides, Ni meshes and carbon nanotubes are also utilized as the conductive bases.109–111 The cross-stacked carbon nanotube bundles developed by Zhang et al. produce a flexible and robust support for uniformly loaded SnO2 while still maintaining high porosity without agglomeration during cycling, which as a consequence, guarantees a stably high capacity with operation in various voltage ranges.110
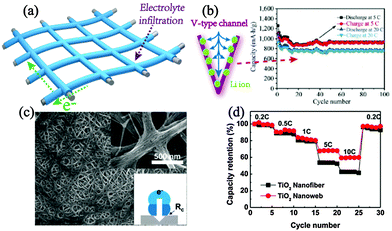 |
| Fig. 8 (a) Schematic illustration of cross-aligned electrodes. (b) Favourable Li ion diffusion of the V-type channel in hierarchical ZnCo2O4–urchin/carbon cloth electrodes and the related high rate performance. Reproduced with permission from ref. 108. Copyright©2013, Springer Group. (c) SEM of cross-aligned TiO2 nanowebs with an enlarged image and illustration of intimate inter-wire contact in the inset (d) rate contrast to TiO2 nanofibers of interlinked TiO2 nanoweb electrodes. Reproduced with permission from ref. 114. Copyright©2013, American Chemical Society. | |
Furthermore, the free-standing stagger nanowire electrode also describes the typical characteristics of the cross-aligned concept. Usually created by electrospinning, the intricate active nanowires can form a self-supported binder-free electrode, inheriting the merits of cross-aligned design.112,113 A nanoweb structure of TiO2, cross-linked between electrospun nanofibers, was fabricated by further uniaxially pressing on the pristine nanofiber electrode.114 The extremely tight wire–wire and electrode–current collector contact underlies the bases for high-power energy storage (Fig. 8c). The as-prepared nanoweb achieves superior performance to the nanofiber electrode, especially rate capability as well as Coulombic efficiency, showing an artful design on the cross-linked electrode (Fig. 8d).
4.3 Alternating-layer design
It is mentioned in the hybrid structure that layer-by-layer sandwiched structures are effective in volume deviation control and kinetics promotion. Despite these advantages at the material level, such structures may not form an extensive domain of alternating layered architectures at the whole electrode scope, and hence cannot fully develop the efficient conductance and ion transport in a wide range for ultrafast Li storage (Fig. 9a, merits of alternating layered electrodes). In studies of high-power capacitors, Li and co-workers have presented an excellent example of ordered layer assembly with outstanding performance. The densely packed graphene paper with continuous transport networks shows high capacitive performance, especially the compact energy storage.115 Based on similar vacuum filtration, a free-standing Si/graphene paper was fabricated with the in-plane vacancy incorporated (Fig. 9b).116 The interlinked graphene domains constitute compact and highly conductive networks with also favourable ion penetration ability, resulting in outstanding power performance as well as sustained cyclic stability. Chang et al. constructed multilayered Si–RGO alternating electrode architectures. Within this structure, the layer-by-layer assembled Si and RGO show uniform distribution and good contact, thus maintaining high conductivity, rate capability and active material utilization.117 Furthermore, the adjacent RGO layers give intact protection on the Si materials, achieving superb stability even at 3 C (7.2 A g−1, Fig. 9c).
 |
| Fig. 9 (a) Schematic illustration of the alternating layered electrode. (b) Typically alternating layers of the Si/graphene electrode (inset is the magnified cross section). Reproduced with permission from ref. 116. Copyright©2011, Wiley-VCH. (c) Long-term cyclic stability of the multilayered Si/RGO electrode; the inset shows the illustration of robust stability within the alternating layered electrode during cycling. Reproduced with permission from ref. 117. Copyright©2014, Wiley-VCH. (d) Ion and electron transport in large-area and small-area graphene composite electrodes and (e) their contrast in rate performance. Reproduced with permission from ref. 118. Copyright©2015, Wiley-VCH. | |
Besides the direct electrode construction, Zhong et al. innovatively proposed an orderly packed electrode based on the rational design of large-areal graphene (LG) materials, showing the horizons from materials engineering to electrode building.118 It is observed that LG could easily form an ordered alternating layered structure with MnCO3 owing to high contact area and oriented face-to-face arrangement. In contrast to the randomly arranged small-area graphene electrode, the MnCO3–LG orderly packed anode retains simultaneous high capacity, power delivery and stability (e.g., over 1000 mA h g−1 at 2 A g−1 for 1100 cycles), taking advantage of the continuous ion and electron transport without disorder-induced barriers (Fig. 9d and e). Above all, the alternating layered electrodes feature a highly efficient transfer network, robust structural stability as well as space-saving high packing density, which hold great promise for high energy-power LIB anodes.
4.4 3D porous design
Porous structures with thin walls possess shorter diffusion paths and sufficient space for volume changes (Fig. 10a). There are many electrode designs for the ordered porous films as anodes, with improved capacity and stability.119–121 Si honeycomb electrodes achieve a stable capacity of ∼1730 mA h g−1 for 200 cycles as well as 1480 mA h g−1 at a high rate of 8.4 A g−1, which is much better than that of planar Si structures.119 The ordered porous electrode could also be coated with carbon to further improve stability and conductivity. Observed by Esmanski et al., the coating on silicon inverse-opal-based macroporous electrodes show excellent structure stability at every stage of discharge and also after the 145th cycle, with remarkably enhanced rate capability and Coulombic efficiency.45
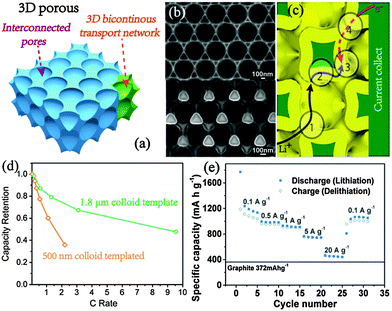 |
| Fig. 10 (a) Schematic illustration of 3D porous electrodes. (b) SEM images of the Ni fabric base and the derived 3D porous electrode after loading Si. Reproduced with permission from ref. 123. Copyright©2012, American Chemical Society. (c) Fast ion and electron transfer within 3D porous structures. Reproduced with permission from ref. 124. Copyright©2011, Nature Publishing Group. (d) Rate performance of the 3D porous Si electrode (ref. 123) with different pore sizes. (e) Rate performance of 3D porous Ni scaffolded Fe2O3. Reproduced with permission from ref. 125. Copyright©2015, American Chemical Society. | |
The Braun group presented a novel 3D porous metal scaffold, which sets a desirable support for versatile bicontinuous LIB anodes (Fig. 10b).122 The fabricated 3D Si anodes achieve a high capacity of 1450 mA h g−1 (based on the whole electrode) at 0.05 C while retaining a superb rate performance of 48% even at 9.5 C, which is far better than conventional anodes at both the energy and power index (Fig. 10b and d).123 Importantly, the bicontinuous feature simultaneously guarantees the high electrical conductivity and fast electrolyte-ion transport within the whole 3D scaffold (Fig. 10c).124 The 3D Ni scaffolded Fe2O3 achieves a reversible capacity of 450 mA h g−1 at ultrafast 20 A g−1 owing to the ensured highly efficient kinetics, which is also particularly highlighted by the reduced voltage hysteresis (Fig. 10e).125 The ultrafast storage concept is also applicable to other storage systems testified by the 3D porous electrodes of LIBs and aqueous battery cathodes. Besides, the bulky framework with high active loading obtains high volumetric density, much benefiting the practical assembly of miniature or typical battery devices.
5. Summary and outlook
With the pressing aim of the search for high-performance LIB anodes, an increasing number of new-type materials have been exploited beyond commercial graphite. However, owing to their intrinsic and mechanism handicaps, like low conductivity and volume deviation, rational and artful designs are highly required for these materials to simultaneously achieve high capacity, outstanding rate capability and long-term cyclic stability. In this review, we have summarized critical concerns on anode materials and presented a series of state-of-the-art structural designs to circumvent the corresponding issues, highlighting the emerging horizons from materials syntheses to electrode constructions. Single-phase material designs, such as low-dimensional and inter-spatial design, are effective in achieving favourable cyclic stability and high capacity, while the incorporation of composite design could further improve the rate capability by artfully engineering the carbon allotrope additives in hybrids. Fundamentally, these designs on materials benefit fast ion and electron transport as well as robust integrity within individual structures. Transferring these structural advantages from the material scope to the electrode perspective can further boost kinetics and stability throughout the whole electrodes, pushing the Li-storage performance, especially power delivery, to a higher level. Architectures with continuous transport paths and solid constructions built within overall electrodes, like ordered arrays, cross-aligned, alternating layered and 3D porous structures, manifest outstanding electrochemical performances, which are general and universal models to build all kinds of anode materials.
Although great achievement and remarkable progress have been made in advanced LIB anodes, there is still a long way to overcome the subsistent obstruction considering the practical realization, especially on the overall electrode scope. Firstly, to improve the areal capacity and maximize the energy density of full batteries, an electrode needs to be evaluated under high mass loading. Good electrochemical performances can be easily controlled at thin electrode layers, which yet may not be achieved within thick layered electrodes owing to intricate influences, such as electrolyte infiltration and continuity. Particularly, direct design on electrodes should be more carefully handled, as most current synthetic protocols only deposit restricted layers of materials on substrates. Secondly, owing to the limited space in cells, volumetric density is of vital importance to an anode structural design. In this regard, nanomaterials like hollow structures should be cautiously utilized to satisfy high-density energy storage. Secondary aggregation like pomegranate design assembled yolk–shell particles (twice volumetric energy density of graphite) and 3D bulk porous electrode designs (high performance microbatteries) have presented excellent cases on high-density energy storage. The alternating layered electrode with face-to-face stacking of 2D fabrics also reveals great potential for the compact Li storage performance. Yet, densely packed bulk electrodes with less inner void space and fully utilization of active materials are still challenges. Meanwhile, issues like ion and electron transport as well as structural stability should be simultaneously considered from the electrode viewpoint. Thirdly, although theories and observations are demonstrated in anode designs, more basic investigations are still needed within this side. Further well-designed measurements and advanced techniques should be utilized to monitor underlying issues and offer proof of concept, like ion and electron transport, especially for the global electrode. Particularly, modelling or high-throughput computation is beneficial to incorporate into these fundamental studies, which can lead to many interesting discoveries with more effective demonstration. Fourthly, alloys with large volume expansion and conversion-type anodes with large hysteresis are still hindered for practical application. Concerning these currently available anode materials, the search for new-type anode materials with less intrinsic handicaps is still in demand. Materials with suitably low voltage, small structural changes, stable SEI, high tap density and high reversibility hold great promise as anodes in future LIBs. Finally, anodes in high-performance full cells or microcells ought to be deeply studied to assess the potential in real applications. On this point, except problems at anodes, the match with cathodes should be concerned, which also need rational design to enhance the voltage and capacity. As a consequence, it is of great significance to incorporate electrode design into the integral LIB systems. So far, several artful electrode designs in LIBs or microbatteries with parallel cathode and anode construction are presented, manifesting high energy-power density and highlighting the merits of desirable electrode structures.
Above all, with deep exploration and investigation, we believe that the structural designs on advanced anodes are promising to promote the development of future LIBs, which can also be widely extended to illuminate the studies of other significant Li-based batteries, such as engineering on lithium electrodes in Li–S, Li–O2 and Li metal batteries.
Acknowledgements
This work was supported by NSFC (21421001) and MOE Innovation Team (IRT13022) in China.
References
- J. B. Goodenough and Y. Kim, Chem. Mater., 2010, 22, 587–603 CrossRef CAS.
- Z. Yang, J. Zhang, M. C. Kintner-Meyer, X. Lu, D. Choi, J. P. Lemmon and J. Liu, Chem. Rev., 2011, 111, 3577–3613 CrossRef CAS PubMed.
- J. M. Tarascon and M. Armand, Nature, 2001, 414, 359–367 CrossRef CAS PubMed.
- M. Armand and J. M. Tarascon, Nature, 2008, 451, 652–657 CrossRef CAS PubMed.
- B. Scrosati, J. Solid State Electrochem., 2011, 15, 1623–1630 CrossRef CAS.
- P. G. Bruce, B. Scrosati and J. M. Tarascon, Angew. Chem., Int. Ed., 2008, 47, 2930–2946 CrossRef CAS PubMed.
- P. G. Bruce, S. A. Freunberger, L. J. Hardwick and J. M. Tarascon, Nat. Mater., 2012, 11, 19–29 CrossRef CAS PubMed.
- M. Hu, X. Pang and Z. Zhou, J. Power Sources, 2013, 237, 229–242 CrossRef CAS PubMed.
- L. Su, Y. Jing and Z. Zhou, Nanoscale, 2011, 3, 3967–3983 RSC.
- S. Goriparti, E. Miele, F. De Angelis, E. Di Fabrizio, R. Proietti Zaccaria and C. Capiglia, J. Power Sources, 2014, 257, 421–443 CrossRef CAS PubMed.
- N. A. Kaskhedikar and J. Maier, Adv. Mater., 2009, 21, 2664–2680 CrossRef CAS PubMed.
- M. R. Palacin, Chem. Soc. Rev., 2009, 38, 2565–2575 RSC.
- P. Roy and S. K. Srivastava, J. Mater. Chem. A, 2015, 3, 2454–2484 CAS.
- H. Li, Z. Wang, L. Chen and X. Huang, Adv. Mater., 2009, 21, 4593–4607 CrossRef CAS PubMed.
- X. L. Wu, Y. G. Guo and L. J. Wan, Chem. – Asian J., 2013, 8, 1948–1958 CrossRef CAS PubMed.
- J. Cabana, L. Monconduit, D. Larcher and M. R. Palacin, Adv. Mater., 2010, 22, E170–E192 CrossRef CAS PubMed.
- Y. Ren, A. R. Armstrong, F. Jiao and P. G. Bruce, J. Am. Chem. Soc., 2010, 132, 996–1004 CrossRef CAS PubMed.
- M. N. Obrovac and V. L. Chevrier, Chem. Rev., 2014, 114, 11444–11502 CrossRef CAS PubMed.
- J. B. Goodenough, Energy Environ. Sci., 2014, 7, 14–18 CAS.
- D. Aurbach, J. Power Sources, 2000, 89, 206–218 CrossRef CAS.
- K. Xu, Chem. Rev., 2014, 114, 11503–11618 CrossRef CAS PubMed.
- L. Zhang, H. B. Wu and X. W. D. Lou, Adv. Energy Mater., 2014, 4, 1300958 Search PubMed.
- R. Raccichini, A. Varzi, S. Passerini and B. Scrosati, Nat. Mater., 2015, 14, 271–279 CrossRef CAS PubMed.
- Y. Kim, J.-H. Lee, S. Cho, Y. Kwon, I. In, J. Lee, N.-H. You, E. Reichmanis, H. Ko, K.-T. Lee, H.-K. Kwon, D.-H. Ko, H. Yang and B. Park, ACS Nano, 2014, 8, 6701–6712 CrossRef CAS PubMed.
- Y. He, X. Yu, G. Li, R. Wang, H. Li, Y. Wang, H. Gao and X. Huang, J. Power Sources, 2012, 216, 131–138 CrossRef CAS PubMed.
- Y. He, X. Yu, Y. Wang, H. Li and X. Huang, Adv. Mater., 2011, 23, 4938–4941 CrossRef CAS PubMed.
- K. Xie and B. Wei, Adv. Mater., 2014, 26, 3592–3617 CrossRef CAS PubMed.
- N. Liu, Z. Lu, J. Zhao, M. T. McDowell, H. W. Lee, W. Zhao and Y. Cui, Nat. Nanotechnol., 2014, 9, 187–192 CrossRef CAS PubMed.
- L. Mai, X. Tian, X. Xu, L. Chang and L. Xu, Chem. Rev., 2014, 114, 11828–11862 CrossRef CAS PubMed.
- Y. Tang, Y. Zhang, J. Deng, D. Qi, W. R. Leow, J. Wei, S. Yin, Z. Dong, R. Yazami, Z. Chen and X. Chen, Angew. Chem., Int. Ed., 2014, 53, 13488–13492 CrossRef CAS PubMed.
- Y. Tang, Y. Zhang, J. Deng, J. Wei, H. Le Tam, B. K. Chandran, Z. Dong, Z. Chen and X. Chen, Adv. Mater., 2014, 26, 6111–6118 CrossRef CAS PubMed.
- C. K. Chan, H. Peng, G. Liu, K. McIlwrath, X. F. Zhang, R. A. Huggins and Y. Cui, Nat. Nanotechnol., 2008, 3, 31–35 CrossRef CAS PubMed.
- S. W. Kim, T. H. Han, J. Kim, H. Gwon, H. S. Moon, S. W. Kang, S. O. Kim and K. Kang, ACS Nano, 2009, 3, 1085–1090 CrossRef CAS PubMed.
- S. Cavaliere, S. Subianto, I. Savych, D. J. Jones and J. Rozière, Energy Environ. Sci., 2011, 4, 4761–4785 CAS.
- J. Jiang, Y. Li, J. Liu and X. Huang, Nanoscale, 2011, 3, 45–58 RSC.
- W. Luo, X. Hu, Y. Sun and Y. Huang, J. Mater. Chem., 2012, 22, 8916–8921 RSC.
- S. Liu, H. Jia, L. Han, J. Wang, P. Gao, D. Xu, J. Yang and S. Che, Adv. Mater., 2012, 24, 3201–3204 CrossRef CAS PubMed.
- T.-J. Kim, C. Kim, D. Son, M. Choi and B. Park, J. Power Sources, 2007, 167, 529–535 CrossRef CAS PubMed.
- C. Yu, X. Li, T. Ma, J. Rong, R. Zhang, J. Shaffer, Y. An, Q. Liu, B. Wei and H. Jiang, Adv. Energy Mater., 2012, 2, 68–73 CrossRef CAS PubMed.
- Y. Zhao, L. Peng, B. Liu and G. Yu, Nano Lett., 2014, 14, 2849–2853 CrossRef CAS PubMed.
- J. S. Chen, Y. L. Tan, C. M. Li, Y. L. Cheah, D. Luan, S. Madhavi, F. Y. Boey, L. A. Archer and X. W. Lou, J. Am. Chem. Soc., 2010, 132, 6124–6130 CrossRef CAS PubMed.
- A. Vu, Y. Qian and A. Stein, Adv. Energy Mater., 2012, 2, 1056–1085 CrossRef CAS PubMed.
- Z. Wang, L. Zhou and X. W. David Lou, Adv. Mater., 2012, 24, 1903–1911 CrossRef CAS PubMed.
- M. Ge, J. Rong, X. Fang and C. Zhou, Nano Lett., 2012, 12, 2318–2323 CrossRef CAS PubMed.
- A. Esmanski and G. A. Ozin, Adv. Funct. Mater., 2009, 19, 1999–2010 CrossRef CAS PubMed.
- J. Haetge, P. Hartmann, K. Brezesinski, J. Janek and T. Brezesinski, Chem. Mater., 2011, 23, 4384–4393 CrossRef CAS.
- H. Liu, G. Wang, J. Liu, S. Qiao and H. Ahn, J. Mater. Chem., 2011, 21, 3046–3052 RSC.
- M. H. Park, K. Kim, J. Kim and J. Cho, Adv. Mater., 2010, 22, 415–418 CrossRef CAS PubMed.
- L. Shen, C. Yuan, H. Luo, X. Zhang, K. Xu and Y. Xia, J. Mater. Chem., 2010, 20, 6998–7004 RSC.
- X. L. Wang, W. Q. Han, H. Chen, J. Bai, T. A. Tyson, X. Q. Yu, X. J. Wang and X. Q. Yang, J. Am. Chem. Soc., 2011, 133, 20692–20695 CrossRef CAS PubMed.
- T. Lan, Y. Liu, J. Dou, Z. Hong and M. Wei, J. Mater. Chem. A, 2014, 2, 1102–1106 CAS.
- B. Koo, H. Xiong, M. D. Slater, V. B. Prakapenka, M. Balasubramanian, P. Podsiadlo, C. S. Johnson, T. Rajh and E. V. Shevchenko, Nano Lett., 2012, 12, 2429–2435 CrossRef CAS PubMed.
- Y. Yao, M. T. McDowell, I. Ryu, H. Wu, N. Liu, L. Hu, W. D. Nix and Y. Cui, Nano Lett., 2011, 11, 2949–2954 CrossRef CAS PubMed.
- Q. Q. Xiong, J. P. Tu, Y. Lu, J. Chen, Y. X. Yu, Y. Q. Qiao, X. L. Wang and C. D. Gu, J. Phys. Chem. C, 2012, 116, 6495–6502 CAS.
- L. Zhang, G. Zhang, H. B. Wu, L. Yu and X. W. Lou, Adv. Mater., 2013, 25, 2589–2593 CrossRef CAS PubMed.
- Y. Zhong, L. Su, M. Yang, J. Wei and Z. Zhou, ACS Appl. Mater. Interfaces, 2013, 5, 11212–11217 CAS.
- J. Wang, N. Yang, H. Tang, Z. Dong, Q. Jin, M. Yang, D. Kisailus, H. Zhao, Z. Tang and D. Wang, Angew. Chem., Int. Ed., 2013, 52, 6417–6420 CrossRef CAS PubMed.
- S. Xu, C. M. Hessel, H. Ren, R. Yu, Q. Jin, M. Yang, H. Zhao and D. Wang, Energy Environ. Sci., 2014, 7, 632–637 CAS.
- Y. J. Hong, M. Y. Son and Y. C. Kang, Adv. Mater., 2013, 25, 2279–2283 CrossRef CAS PubMed.
- S. H. Choi and Y. C. Kang, ChemSusChem, 2013, 6, 2111–2116 CrossRef CAS PubMed.
- A. K. Geim and K. S. Novoselov, Nat. Mater., 2007, 6, 183–191 CrossRef CAS PubMed.
- Z.-S. Wu, G. Zhou, L.-C. Yin, W. Ren, F. Li and H.-M. Cheng, Nano Energy, 2012, 1, 107–131 CrossRef CAS PubMed.
- H. Wang and H. Dai, Chem. Soc. Rev., 2013, 42, 3088–3113 RSC.
- X. Zhou, J. Bao, Z. Dai and Y.-G. Guo, J. Phys. Chem. C, 2013, 117, 25367–25373 CAS.
- S. M. Yuan, J. X. Li, L. T. Yang, L. W. Su, L. Liu and Z. Zhou, ACS Appl. Mater. Interfaces, 2011, 3, 705–709 CAS.
- N. Liu, H. Wu, M. T. McDowell, Y. Yao, C. Wang and Y. Cui, Nano Lett., 2012, 12, 3315–3321 CrossRef CAS PubMed.
- H. Wu, G. Zheng, N. Liu, T. J. Carney, Y. Yang and Y. Cui, Nano Lett., 2012, 12, 904–909 CrossRef CAS PubMed.
- X. Zhou, L. J. Wan and Y. G. Guo, Small, 2013, 9, 2684–2688 CrossRef CAS PubMed.
- C. Lei, F. Han, D. Li, W. C. Li, Q. Sun, X. Q. Zhang and A. H. Lu, Nanoscale, 2013, 5, 1168–1175 RSC.
- L. Zhao, Y. S. Hu, H. Li, Z. Wang and L. Chen, Adv. Mater., 2011, 23, 1385–1388 CrossRef CAS PubMed.
- S. Yang, X. Feng, S. Ivanovici and K. Mullen, Angew. Chem., Int. Ed., 2010, 49, 8408–8411 CrossRef CAS PubMed.
- S. M. Paek, E. Yoo and I. Honma, Nano Lett., 2009, 9, 72–75 CrossRef CAS PubMed.
- H. Wang, L. F. Cui, Y. Yang, H. Sanchez Casalongue, J. T. Robinson, Y. Liang, Y. Cui and H. Dai, J. Am. Chem. Soc., 2010, 132, 13978–13980 CrossRef CAS PubMed.
- L. Su, Z. Zhou, X. Qin, Q. Tang, D. Wu and P. Shen, Nano Energy, 2013, 2, 276–282 CrossRef CAS PubMed.
- Y. Zou and Y. Wang, Nanoscale, 2011, 3, 2615–2620 RSC.
- S. Yang, X. Feng and K. Mullen, Adv. Mater., 2011, 23, 3575–3579 CrossRef CAS PubMed.
- D. Wang, D. Choi, J. Li, Z. Yang, Z. Nie, R. Kou, D. Hu, C. Wang, L. V. Saraf, J. Zhang, I. A. Aksay and J. Liu, ACS Nano, 2009, 3, 907–914 CrossRef CAS PubMed.
- X. Jiang, X. Yang, Y. Zhu, J. Shen, K. Fan and C. Li, J. Power Sources, 2013, 237, 178–186 CrossRef CAS PubMed.
- W. Chen, S. Li, C. Chen and L. Yan, Adv. Mater., 2011, 23, 5679–5683 CrossRef CAS PubMed.
- L. Xiao, D. Wu, S. Han, Y. Huang, S. Li, M. He, F. Zhang and X. Feng, ACS Appl. Mater. Interfaces, 2013, 5, 3764–3769 CAS.
- X. Xin, X. Zhou, F. Wang, X. Yao, X. Xu, Y. Zhu and Z. Liu, J. Mater. Chem., 2012, 22, 7724–7730 RSC.
- S. J. Prabakar, Y. H. Hwang, E. G. Bae, S. Shim, D. Kim, M. S. Lah, K. S. Sohn and M. Pyo, Adv. Mater., 2013, 25, 3307–3312 CrossRef CAS PubMed.
- G. Zhou, D.-W. Wang, F. Li, L. Zhang, N. Li, Z.-S. Wu, L. Wen, G. Q. Lu and H.-M. Cheng, Chem. Mater., 2010, 22, 5306–5313 CrossRef CAS.
- X. Zhou, L. J. Wan and Y. G. Guo, Adv. Mater., 2013, 25, 2152–2157 CrossRef CAS PubMed.
- X. Zhou, Y.-X. Yin, L.-J. Wan and Y.-G. Guo, Adv. Energy Mater., 2012, 2, 1086–1090 CrossRef CAS PubMed.
- Z. S. Wu, W. Ren, L. Xu, F. Li and H. M. Cheng, ACS Nano, 2011, 5, 5463–5471 CrossRef CAS PubMed.
- H. Wang, C. Zhang, Z. Liu, L. Wang, P. Han, H. Xu, K. Zhang, S. Dong, J. Yao and G. Cui, J. Mater. Chem., 2011, 21, 5430–5434 RSC.
- G. Kucinskis, G. Bajars and J. Kleperis, J. Power Sources, 2013, 240, 66–79 CrossRef CAS PubMed.
- Y. Zhong, M. Yang, X. Zhou, J. Wei and Z. Zhou, Part. Part. Syst. Charact., 2015, 32, 104–111 CrossRef CAS PubMed.
- R. Wang, C. Xu, J. Sun, L. Gao and H. Yao, ACS Appl. Mater. Interfaces, 2014, 6, 3427–3436 CAS.
- Y. Chang, J. Li, B. Wang, H. Luo, H. He, Q. Song and L. Zhi, J. Mater. Chem. A, 2013, 1, 14658–14665 CAS.
- M. A. Garakani, S. Abouali, B. Zhang, C. A. Takagi, Z. L. Xu, J. Q. Huang, J. Huang and J. K. Kim, ACS Appl. Mater. Interfaces, 2014, 6, 18971–18980 CAS.
- Y. Su, S. Li, D. Wu, F. Zhang, H. Liang, P. Gao, C. Cheng and X. Feng, ACS Nano, 2012, 6, 8349–8356 CrossRef CAS PubMed.
- W. Wei, S. Yang, H. Zhou, I. Lieberwirth, X. Feng and K. Mullen, Adv. Mater., 2013, 25, 2909–2914 CrossRef CAS PubMed.
- J. Qin, C. He, N. Zhao, Z. Wang, C. Shi, E. Z. Liu and J. Li, ACS Nano, 2014, 8, 1728–1738 CrossRef CAS PubMed.
- D. Wang, J. Yang, X. Li, D. Geng, R. Li, M. Cai, T.-K. Sham and X. Sun, Energy Environ. Sci., 2013, 6, 2900–2906 CAS.
- Y. Li, B. Tan and Y. Wu, Nano Lett., 2008, 8, 265–270 CrossRef CAS PubMed.
- Y. Wang, H. Xia, L. Lu and J. Lin, ACS Nano, 2010, 4, 1425–1432 CrossRef CAS PubMed.
- M. V. Reddy, T. Yu, C. H. Sow, Z. X. Shen, C. T. Lim, G. V. Subba Rao and B. V. R. Chowdari, Adv. Funct. Mater., 2007, 17, 2792–2799 CrossRef CAS PubMed.
- T. Song, J. Xia, J. H. Lee, D. H. Lee, M. S. Kwon, J. M. Choi, J. Wu, S. K. Doo, H. Chang, W. I. Park, D. S. Zang, H. Kim, Y. Huang, K. C. Hwang, J. A. Rogers and U. Paik, Nano Lett., 2010, 10, 1710–1716 CrossRef CAS PubMed.
- J. Liu, N. Li, M. D. Goodman, H. G. Zhang, E. S. Epstein, B. Huang, Z. Pan, J. Kim, J. H. Choi, X. Huang, J. Liu, K. J. Hsia, S. J. Dillon and P. V. Braun, ACS Nano, 2015, 9, 1985–1994 CrossRef CAS PubMed.
- A. L. Reddy, M. M. Shaijumon, S. R. Gowda and P. M. Ajayan, Nano Lett., 2009, 9, 1002–1006 CrossRef CAS PubMed.
- P. L. Taberna, S. Mitra, P. Poizot, P. Simon and J. M. Tarascon, Nat. Mater., 2006, 5, 567–573 CrossRef CAS PubMed.
- W. Wang, M. Tian, A. Abdulagatov, S. M. George, Y. C. Lee and R. Yang, Nano Lett., 2012, 12, 655–660 CrossRef CAS PubMed.
- L. Zhang, H. B. Wu and X. Wen Lou, Mater. Horiz., 2014, 1, 133–138 RSC.
- C. Wang, W. Wan, Y. Huang, J. Chen, H. H. Zhou and X. X. Zhang, Nanoscale, 2014, 6, 5351–5358 CAS.
- Q. Q. Xiong, J. P. Tu, X. H. Xia, X. Y. Zhao, C. D. Gu and X. L. Wang, Nanoscale, 2013, 5, 7906–7912 RSC.
- B. Liu, X. Wang, B. Liu, Q. Wang, D. Tan, W. Song, X. Hou, D. Chen and G. Shen, Nano Res., 2013, 6, 525–534 CrossRef CAS.
- E. Hosono, S. Fujihara, I. Honma and H. Zhou, Electrochem. Commun., 2006, 8, 284–288 CrossRef CAS PubMed.
- H.-X. Zhang, C. Feng, Y.-C. Zhai, K.-L. Jiang, Q.-Q. Li and S.-S. Fan, Adv. Mater., 2009, 21, 2299–2304 CrossRef CAS PubMed.
- K. Evanoff, J. Benson, M. Schauer, I. Kovalenko, D. Lashmore, W. J. Ready and G. Yushin, ACS Nano, 2012, 6, 9837–9845 CrossRef CAS PubMed.
- M. Zhang, E. Uchaker, S. Hu, Q. Zhang, T. Wang, G. Cao and J. Li, Nanoscale, 2013, 5, 12342–12349 RSC.
- Y. Li, Y. Hu, Y. Lu, S. Zhang, G. Xu, K. Fu, S. Li, C. Chen, L. Zhou, X. Xia and X. Zhang, J. Power Sources, 2014, 254, 33–38 CrossRef CAS PubMed.
- S. Lee, J. Ha, J. Choi, T. Song, J. W. Lee and U. Paik, ACS Appl. Mater. Interfaces, 2013, 5, 11525–11529 CAS.
- X. Yang, C. Cheng, Y. Wang, L. Qiu and D. Li, Science, 2013, 341, 534–537 CrossRef CAS PubMed.
- X. Zhao, C. M. Hayner, M. C. Kung and H. H. Kung, Adv. Energy Mater., 2011, 1, 1079–1084 CrossRef CAS PubMed.
- J. Chang, X. Huang, G. Zhou, S. Cui, P. B. Hallac, J. Jiang, P. T. Hurley and J. Chen, Adv. Mater., 2014, 26, 758–764 CrossRef CAS PubMed.
- Y. Zhong, M. Yang, X. Zhou, Y. Luo, J. Wei and Z. Zhou, Adv. Mater., 2015, 27, 806–812 CrossRef CAS PubMed.
- Y. Zhao, L. Peng, Y. Ding and G. Yu, Chem. Commun., 2014, 50, 12959–12962 RSC.
- X. H. Xia, J. P. Tu, J. Y. Xiang, X. H. Huang, X. L. Wang and X. B. Zhao, J. Power Sources, 2010, 195, 2014–2022 CrossRef CAS PubMed.
- J. C. Lytle, H. Yan, N. S. Ergang, W. H. Smyrl and A. Stein, J. Mater. Chem., 2004, 14, 1616–1622 RSC.
- J. H. Pikul, H. Gang Zhang, J. Cho, P. V. Braun and W. P. King, Nat. Commun., 2013, 4, 1732 CrossRef PubMed.
- H. Zhang and P. V. Braun, Nano Lett., 2012, 12, 2778–2783 CrossRef CAS PubMed.
- H. Zhang, X. Yu and P. V. Braun, Nat. Nanotechnol., 2011, 6, 277–281 CrossRef CAS PubMed.
- J. Wang, H. Zhou, J. Nanda and P. V. Braun, Chem. Mater., 2015, 27, 2803–2811 CrossRef.
|
This journal is © The Royal Society of Chemistry 2015 |
Click here to see how this site uses Cookies. View our privacy policy here.