DOI:
10.1039/C5GC01334H
(Paper)
Green Chem., 2015,
17, 4980-4990
The synthesis and analysis of advanced lignin model polymers†
Received
15th June 2015
, Accepted 31st July 2015
First published on 3rd August 2015
Abstract
If the lignin-first biorefinery concept becomes a reality, high quality lignins close in structure to native lignins will become available in large quantities. One potential way to utilise this renewable material is through depolymerisation to aromatic chemicals. This will require the development of new chemical methods. Here, we report the synthesis and characterisation of advanced lignin model polymers to be used as tools to develop these methods. The controlled incorporation of the major linkages in lignin is demonstrated to give complex hardwood and softwood lignin model polymers. These polymers have been characterised by 2D HSQC NMR and GPC analysis and have been compared to isolated lignins.
1. Introduction
Lignin is an aromatic rich bio-polymer which is second only to cellulose as the most abundant renewable carbon source on the planet.1 As such it holds great potential to supply a future chemical industry with renewable aromatic chemicals as the world economy transitions away from the use of fossil fuels. However, the challenge of selective lignin depolymerisation and valorisation has yet to be fully met and continues to be the focus of a great deal of scientific research.2–5
For over a century lignin has been a major by-product of the pulp and paper industry and it is estimated that currently around 63 million tonnes is extracted annually.6 A small proportion of this production consists of lignosulfonates from sulfite pulping for which there exists an established market in which Borregard are world leaders.7 However, the vast majority is produced through the kraft process.8 In both case the extracted lignins are typically severely chemically altered compared to native lignins, making the production of aromatic chemicals, particularly in good yields, much more challenging.9 This has led to the development of the “lignin-first” biorefinery concept where the production of high quality lignins, close in structure to native lignin, has been proposed to facilitate the production of aromatic chemicals in good yields.10
Whilst significant advances have been made in recent years,11–20 the selective depolymerisation of lignin to small molecules is still a challenge. In order to develop new methods, model compounds are often used as a starting point. This greatly simplifies the analysis of new products and the optimisation of reaction conditions. However, these models frequently fail to replicate the surrounding linkages (2D environment) let alone the complex 3-dimensional structure of lignin. These limitations can ultimately lead to apparently promising reactions on models failing on lignin. In order to overcome this, interest has started to grow in the synthesis of more complex oligomeric and polymeric models.21–23 Indeed, recently the synthesis of an advanced hexameric lignin model was reported which incorporates a number of different linkages into one molecule.21
Previous research on the chemical synthesis of model polymers has focussed only on the β-O-4 linkage, however these lack several of the major linkages present in lignin and therefore a great deal of the complexity. The synthesis of more complex polymers can be achieved through the dehydrogenative polymerisation (DHP) of the monolignols coniferyl, sinapyl and coumaryl alcohol. However this remains challenging and control over the relative distribution of linkages is lacking due to the reliance on a radical polymerisation process. These factors perhaps explain why the use of DHP polymers has largely been limited to a number of excellent investigations into the biosynthesis24–29 and biodegradation30–35 of lignin rather than chemical depolymerisation.
In order to widen the use of complex polymers for investigations into the chemical depolymerisation of lignin we were interested in combining the simplicity of previously described β-O-4 polymer syntheses11,22 with the structural complexity of DHP polymers. For example, whilst our previously reported model polymer11 contained exclusively β-O-4 linkages (with an S
:
G ratio of 1
:
1), here we prepare considerably more complex structures that include other common linkages in addition to the β-O-4 linkage. Such substrates should prove useful in developing and testing novel chemical methods for lignin valorisation, in particular as stepping stone models between the commonly used dimeric model compounds and more challenging biomass derived substrates. We have recently shown the utility of polymeric models in developing a novel method for the selective depolymerisation of birch lignin to aromatic chemicals11 and others have used simpler model polymers to study lignin depolymerisation.36,37 As an example Samec et al. reported the development of an efficient method for selective depolymerisation of dimeric lignin model compounds and simple model polymers using a heterogenous Pd/C catalyst. Unfortunately, this methodology failed to produce significant amounts of monomers from lignin37 highlighting the need for more advanced and structurally faithful polymeric models. Ultimately, such models could accelerate the introduction of lignin derived green alternatives to fossil fuel products.
2. Results and discussion
As the composition of natural lignins can vary significantly both in the relative abundances of inter-unit linkages and G
:
S ratios we wanted to develop a synthesis of model polymers that would allow control over both of these variables. Based on the work of Nakatsubo et al.22 we recently reported the facile synthesis of a S–G β-O-4 polymer as a model for a hardwood lignin.11 As this methodology makes use of monomers which can be easily accessed from vanillin and syringaldehyde in one step without chromatography and in excellent yield,11,22 it formed the basis of the work we report here.
Hardwood lignin models
The first extension we considered was the introduction of the β–β (resinol) unit into the polymer as a model for hardwood lignins. These lignins are typically rich in β-O-4 and β–β linkages, but have low abundances of β-5 (phenylcoumaran) units.38–40 We proposed this could be achievable using monomer 1, the synthesis of which was accomplished in five steps from syringaldehyde (2) (Scheme 1) following established literature procedures. Knoevenagel condensation of 2 with malonic acid gave sinapic acid (3), which was esterified to methyl sinapate (4) and then reduced to give sinapyl alcohol (5). A biomimetic oxidative dimerization gave syringaresinol (6) which was alkylated with ethyl bromoacetate to give the required monomer 1. This synthesis could be achieved on a multigram scale without any chromatographic purifications. As the majority of resinol units in hardwood lignins appear to be derived from syringaresinol38 the introduction of units arising from the homo- or hetero-dimerisation of the other monolignols (coniferyl or p-coumaryl alcohol) was not attempted.
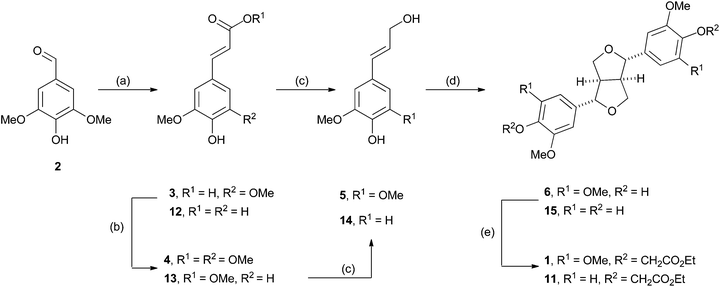 |
| Scheme 1 The synthesis of β–β monomers 1 and 11. Reagents and conditions: (a) malonic acid, cat. aniline, pyridine, 60 °C, 16 h, 86%.41 (b) AcCl, MeOH, reflux, 1 h. 95% for 4, 100% for 13 (c) LiAlH4, n-BuBr, THF, −78 °C to r.t.425 used as crude; 61% for 14. (d) CuSO4·5H2O, H2O, light, air, r.t., 38% over 2 steps for 6.43 FeCl3, H2O/Acetone, 1 h, r.t. 20% for 15. (e) Ethyl bromoacetate, K2CO3, acetone, reflux, 24 h. 86% for 1; 95% for 11. | |
With monomer 1 in hand, its incorporation into an S–G polymer was attempted. This proceeded smoothly using a 0.2
:
1
:
1 mixture of 1
:
7
:
8 (Scheme 2) with LDA in THF to give a polymeric material, the ester groups in which were reduced using NaBH4/MeOH in EtOH at 50 °C without purification after the first step. Precipitation in acidified water and purification of the crude polymer by re-precipitation in Et2O gave polymer 9 containing both β-O-4 and β–β units in 48% yield over 2 steps on a 2 g scale (Scheme 2).
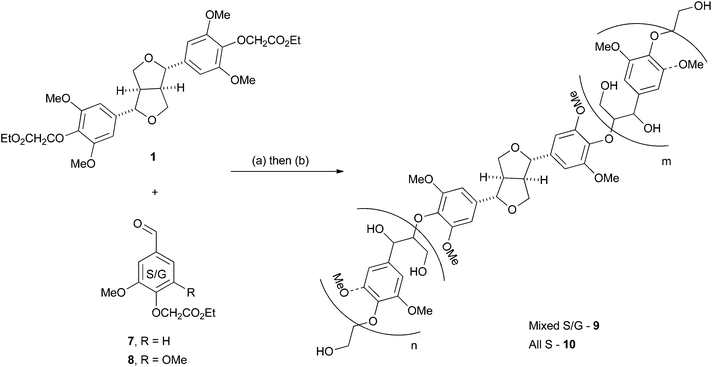 |
| Scheme 2 The synthesis of β-O-4 and β–β containing polymers as models for hardwood lignins. Reagents and conditions: (a) LDA, THF, 0 °C, 30 min, 0.17 mmol mL−1. (b) NaBH4/MeOH, EtOH, 50 °C, 1 h. 9 – 48%; 10 – 28% over 2 steps. n and m can be but are not necessarily equal. | |
The synthesis of all S polymer 10 was also undertaken (0.1
:
0.9 ratio of 1
:
8) using the same experimental procedure as for 9 in 28% yield. This is an interesting model as the production of extremely S rich lignins has been reported in transgenic hybrid poplar trees44 which show significantly improved pulping characteristics over the wild type trees. These trees are therefore potentially economically interesting for future pulping and biorefinery industries45 which could potentially produce extremely S rich lignins as co-products. Interestingly, the synthesis of syringyl rich polymers from sinapyl alcohol using DHP methods gives low molecular weight products in poor yields highlighting one advantage of the synthesis reported here.46
Softwood lignin models
With hardwood lignin model polymers in hand, our attention turned to the synthesis of more complex softwood lignin models. Although, softwood lignins are composed almost exclusively of G units, the inter-unit connectivity is much more complex than in hardwood lignins (see Fig. 1). In particular, such lignins contain significant proportions of β-5 units as well as β-O-4 and minor amounts of β–β units.47,48 As a result the polymer synthesis required the preparation of novel β-5 and β–β G unit monomers. Following a similar route to that used previously, the required β–β monomer 11 was prepared in 4 steps from ferulic acid 12 (see Scheme 1). Esterification of 12 to methyl ferulate (13) followed by reduction gave coniferyl alcohol (14), which underwent dimerization in the presence of FeCl3 to give pinoresinol (15) from which monomer 11 was prepared.
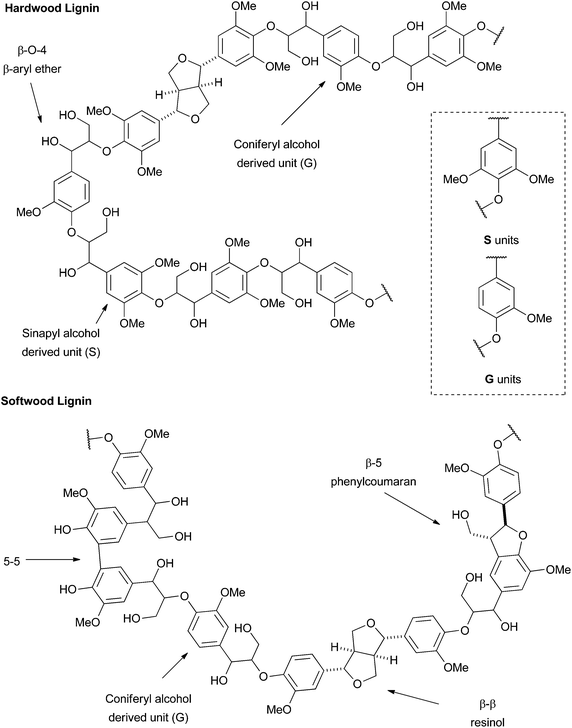 |
| Fig. 1 Structural representations of sections of hardwood and softwood lignins showing the most abundant units (S/G) and linkages found in each. The known relative stereochemistry of the β–β and β-5 linkages is shown. The β-O-4 are present as both erythro and threo isomers in lignin. | |
For the β-5 monomer, the synthesis of a bi-functional monomer 16 which would support polymerisation was developed from β-5 coupled diferulate 17 (Scheme 3). Diferulate 17 was readily prepared by the horseradish peroxidase mediated oxidative dimerization of 13 as reported by Brunow et al. and Ralph et al. (Scheme 3).49,50 We found that this underutilised and green preparation was preferable to the more commonly reported silver(I) mediated dimerisations.21,51,52 Crude 17 could be separated from the reaction by simple filtration and was purified directly by crystallisation from methanol in a 43% yield. Alkylation of the phenolic group in 17 with ethyl iodoacetate in the presence of K2CO3 gave 18. Oxidative cleavage of the olefinic bond in 18 with catalytic amounts of RuCl3 (ca. 0.2 mol%) in the presence of NaIO4 gave the required bifunctional monomer 16 in good yield (Scheme 3). Both 16 and 18 could be crystallised directly from the crude reaction mixtures in 70% and 72% yields respectively.
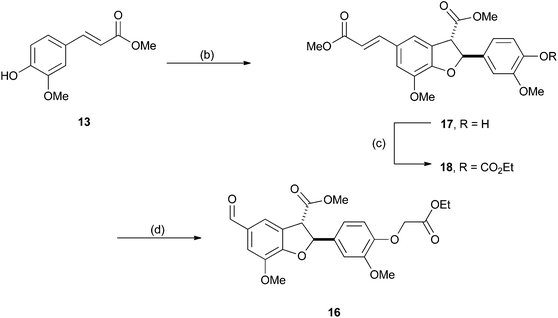 |
| Scheme 3 The synthesis of the β-5 monomer 16. Reagents and conditions: (b) HRP, H2O2, H2O/MeOH (87 : 13), pH 3, 37 °C, 10 min, 43%. (c) Ethyl iodoacetate, K2CO3, acetone, reflux, 16 h, 72%. (d) RuCl3·xH2O (∼0.2 mol%), NaIO4, EtOAc/MeCN/H2O, 0 °C to r.t, 3 h, 70%. | |
The subsequent polymerisation of a mixture of 7, 11 and 16 (1
:
0.3
:
0.1) by LDA in THF followed by reduction of the ester groups with NaBH4/MeOH yielded the synthetic lignin polymer 19 in a 40% yield containing β-O-4, β–β and β-5 units (Scheme 4).
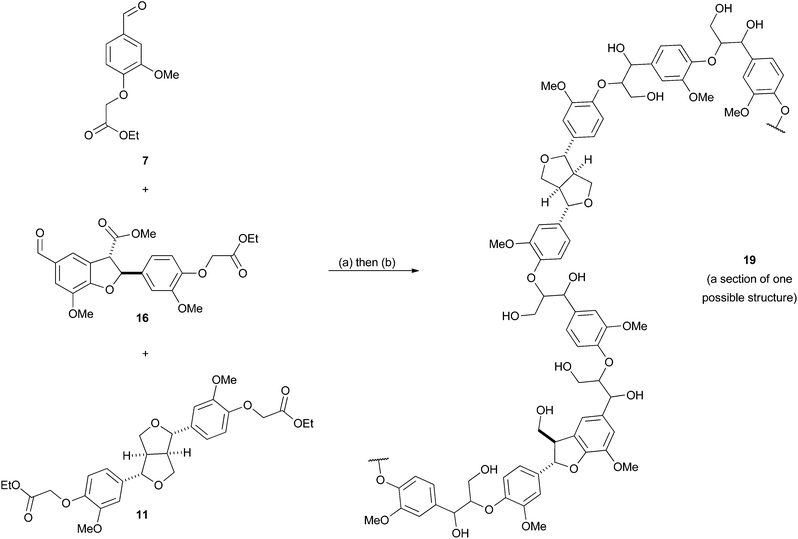 |
| Scheme 4 The synthesis of a softwood lignin model polymer 19. Reagents and conditions: (a) LDA, THF, −78 °C to 0 °C, 1 h. (b) NaBH4/MeOH, EtOH, 50 °C, 1 h, 40% over 2 steps. | |
Phenolic models
Whilst polymers 9, 10 and 19 should prove useful for most chemical investigations into lignin valorisation the lack of phenolic groups sets them apart from natural lignins. Whilst we feel in many cases that this would not have a negative impact in the application of these models, we were still interested in introducing such groups for instances where they may be important. In order to do this a protected 5–5 coupled divanillin monomer 20 was synthesised which would serve to introduce phenolic groups into the final polymer, as well as introducing 5–5 linkages. Such linkages are present in softwood lignins53,54 and are reported to be mainly found as the free phenols in isolated lignins.55 The required monomer was prepared by the dimerisation of vanillin (21) to give divanillin (22) followed by alkylation with in situ generated MOMCl (Scheme 5). We chose a MOM protecting group as we believed it could be deprotected during the acidic work-up of the NaBH4/MeOH reduction of the ester groups and therefore no additional deprotection step would be required. Incorporation of this monomer into a model polymer was then attempted (Scheme 6). Analysis of the resulting polymer 23 by 31P NMR confirmed the presence of diagnostic peaks for the phenolic 5–5 groups (Fig. 2) which was supported by 13C NMR analysis which showed the appearance of resonances consistent with the C4 and C5 carbons in this structural unit (Fig. S1†).
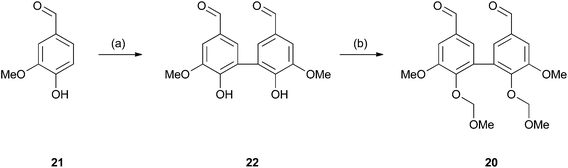 |
| Scheme 5 The synthesis monomer 20. Reagents and conditions: (a) K2S2O8, (NH4)2·Fe(SO4)2·H2O, H2O, 90 °C, 15 min, 82%. (b) Dimethoxymethane, AcCl, ZnBr2 (cat.), toluene, r.t. 3 hours then 22, Hunig's base, DMF, 24 hours, r.t., 64%. | |
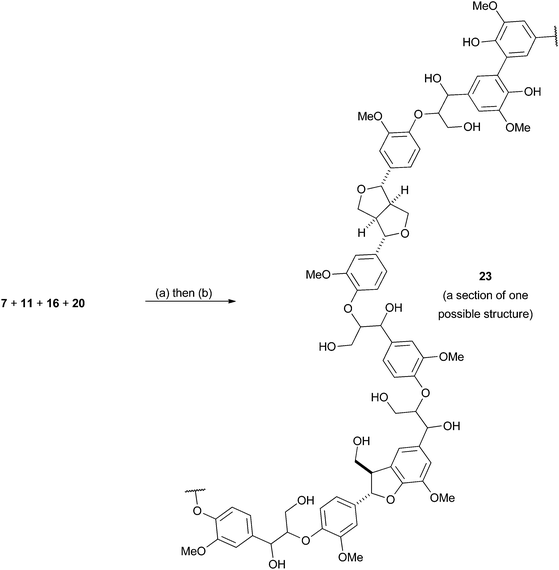 |
| Scheme 6 The synthesis of a phenolic softwood lignin model polymer 23. Reagents and conditions: (a) LDA, THF, −78 °C to 0 °C, 1 h. (b) NaBH4/MeOH, EtOH, 50 °C, 1 h, 32% over 2 steps. | |
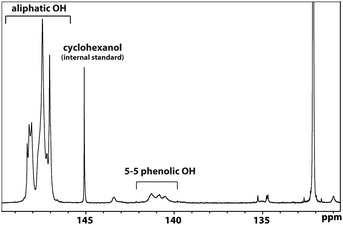 |
| Fig. 2
31P NMR analysis of polymer 23 indicating the presence of 5–5 phenolic groups. Derivatisation of 23 using 2-chloro-4,4,5,5-tetramethyl-1,3,2-dioxaphospholane was followed by 31P NMR analysis. The observation of the signals in the 140–142 ppm region was consistent with polymer 23 containing a 5–5 phenolic unit (with the phenols having reacted with the phosporylating reagent in order to be visible by this method). This assignments was based on extensive literature precedent (for example Argyropoulos et al.56 and references therein). | |
2D HSQC NMR analysis
Due to the high molecular weight and heterogenous nature of these polymers overlapping and broad signals were observed in the 1D 1H NMR spectra (see ESI†). To overcome this, 2D HSQC NMR, a method now well established in lignin analysis,57,58 was used to characterise them. For the polymers synthesised in this study excellent quality 2D HSQC spectra can be obtained in 20 minutes using approximately 10–20 mg of polymer in 0.6 mL of solvent on a 500 MHz spectrometer, whilst good quality spectra can be obtained in 10 minutes or on a 400 MHz spectrometer. Similar experiments for lignin typically require 80–100 mg of material and a 2 hour experiment time, although this can be shorten to as little as 30 minutes using modified NMR protocols.59
Detailed analysis of 9 indicated that the initial monomer composition was well conserved in the final polymer and, based on end group analysis the degree of polymerisation (DPn) was approximately 10.4 (Table 1, entry 1). It is interesting to note that benzyl alcohol (BA) end groups are almost completely absent in this polymer, consistent with the incorporation of monomer 1 into the polymer chain. A similar analysis of 10 revealed that the initial monomer composition was again well conserved and that the DPn was estimated to be 10.6 (Table 1, entry 2).
Table 1 Results of 2D HSQC NMR analysis of model polymers
Entry |
Polymer |
β-O-4 : β–β : β-5 |
DPn b,c |
Expected |
Founda |
We have previously determined the standard deviation for polymer analysis by 2D HSQC NMR to be less than 0.05.11.
Calculated based on end-group analysis and given as a function of the number of C9 units. See ESI Fig. S2 for more details.
Values are calculated based on volume integrals and no response factors were used. As end-groups are likely to be more mobile and therefore slower relaxing than the polymer backbone, they may be over represented in these experiments.
|
1 |
9 (S–G) |
90 : 10 : 0 |
87 : 13 : 0 |
10.4 |
2 |
10 (S) |
90 : 10 : 0 |
88 : 12 : 0 |
10.6 |
3 |
19 (G) |
76 : 6 : 18 |
75 : 9 : 16 |
9.0 |
4 |
23 (G phenolic) |
79 : 4 : 17 |
79 : 7 : 14 |
6.7 |
2D HSQC NMR analysis of the more complex polymer 19 revealed the successful incorporation of the β-5 units into the polymer, together with the β–β and β-O-4 units. Pleasingly, the ratio of the units was again found to reflect approximately that used in the initial polymerisation, demonstrating excellent control over these ratios in both S–G and all G polymers. In this case end group analysis indicated a DPn of approximately 9.0 (Table 1, entry 3). The phenolic polymer 23 also closely matched the expected composition but displayed the lowest apparent DPn of the prepared polymers (Table 1, entry 4).
The 2D HSQC NMR spectra of these models were compared to those of birch (hardwood) and douglas fir (softwood) lignins isolated via a mild acid dioxasolv extraction process (Fig. 3).60 In general the spectra are remarkably similar, and the chemical shifts of the linkages and aromatic resonances correspond well between model polymers and lignins (Fig. 3). In addition to the expected cross peaks for the linkages, a number of additional peaks are present in the natural lignins, particularly the douglas fir lignin, which are not present in the polymers. These are believed to correspond to other minor linkages present in the native lignin formed during the oxidative polymerisation process and to minor acidolysis products formed during the extraction process. Similarly there are a number of peaks in the spectra of the model polymers not present in the natural lignins which can be assigned to end groups resulting from the synthetic route used to prepared these polymers (Fig. 3 and Schemes 2 and 4).
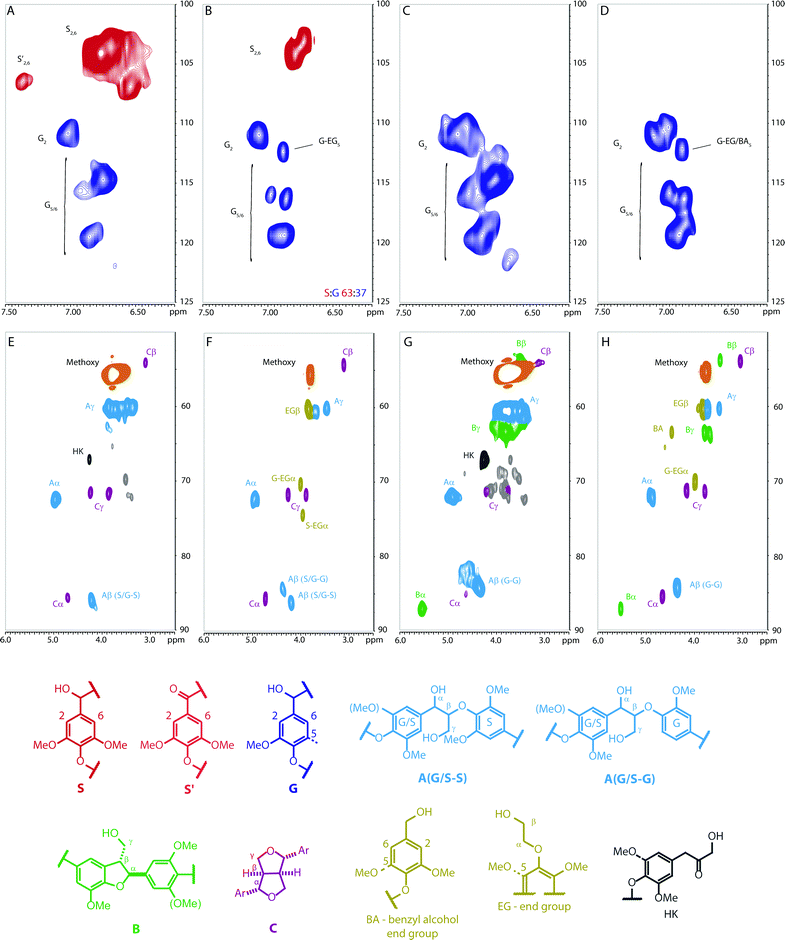 |
| Fig. 3 2D HSQC NMR spectra of birch lignin (A and E), polymer 9 (B and F), doulgas fir lignin (C and G) and polymer 19 (D and H). Cross peaks are coloured according to the structures to which they are assigned. NMR spectra were recorded on a 500 MHz spectrometer in d6-acetone/D2O (9 : 1, 0.65 mL) using 80 mg for lignin and 15–20 mg for polymer models. Further experimental details and HSQC spectra for 10 and 23 can be found in the ESI.† | |
Gel permeation chromatography analysis
GPC analysis was carried out to assess polydisperity and to allow comparison of our synthetic polymers with isolated hard and softwood lignins (Fig. 4). This analysis indicated that the hardwood model polymer 9 was slightly higher in molecular weight than the isolated birch lignin whilst the polydispersity of the polymer was almost the same (Fig. 4 and Table 2, entries 1 and 5). The softwood model polymer 19 had the highest molecular weight of the polymers synthesised here and was higher than the douglas fir lignin (Fig. 4 and Table 2, entries 3 and 6). Analysis of phenolic polymer 23 indicated it had the lowest molecular weight of all the samples which is consistent with the results of the 2D HSQC NMR analysis (Table 1, entry 4 and Table 2, entry 4). Whilst the mild dioxasolv lignins used in this study maintain many of the characteristics of the native lignin, the lignin is chemically changed during the extraction process. In particular partial cleavage of β-O-4 linkages likely leads to the isolation of lignins which are lower in molecular weight than the protolignin originally present in the biomass.‡
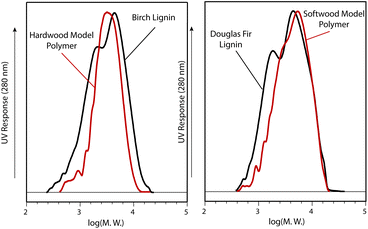 |
| Fig. 4 GPC analysis of isolated birch and douglas fir lignins (black lines) and polymers 9 and 19 (red lines). (Acetylated samples in THF at 1 mL min−1, 30 °C, 280 nm). | |
Table 2 The results of GPC analysis of lignins and polymeric models
Entry |
Polymer |
M
n a |
M
w a |
PDI (Mw/Mn) |
Values are given relative to polystyrene standards.
|
1 |
9 (S–G) |
2670 |
3692 |
1.38 |
2 |
10 (S) |
3110 |
3978 |
1.28 |
3 |
19 (G) |
3264 |
5196 |
1.59 |
4 |
23
|
1891 |
2712 |
1.43 |
5 |
Birch |
2118 |
3890 |
1.36 |
6 |
Doulgas fir |
2551 |
4681 |
1.83 |
Polymer stereochemistry
Establishing the erythro to threo ratio of the β-O-4 units in these complex polymers is important as this ratio can change significantly between lignins from different plants and can affect the chemical reactivity of the linkage.61,62 In particular softwood lignins have been shown to have a lower erythro to threo ratio than hardwoods.63 Determination of the erythro/threo ratio in lignins, and by extension polymeric models, by NMR methods remains challenging. For units that have the G/S–S structure (see Fig. 3) the ratio could be assessed from analysis of the β-protons in the HSQC NMR spectra as the erythro and threo forms can be distinguished. This analysis indicated that such units display a clear preference for the erythro form (Fig. 5), consistent with natural lignins.63 For the G/S–G structures this ratio could not be assessed from the HSQC spectra due to signal overlap and therefore the 13C NMR was used as an indicator. This showed that the erythro form appears to be favoured for these units, although to a lesser extent than for the G/S–S units.
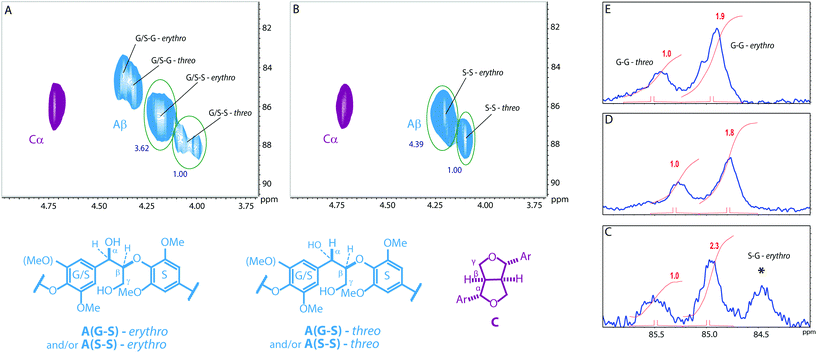 |
| Fig. 5 Determination of approximate ratios of erythro to threo isomers by HSQC and 13C NMR analysis. Expansions of the 2D HSQC NMR spectra of A – 9 and B – 10 and 13C NMR spectra of C – 9, D – 19 and E – 23 show the key β-proton-carbon resonances of the β-O-4 units. The 13C NMR used here is not quantitative but we have found that for dimeric models it reasonably reflects the e/t ratio and so has been used as an indicator for these polymers. As such the integrals are added only as a guide. *Tentative assignment. | |
In addition, whilst the relative stereochemistry of the β-5 and β–β units in lignin is frequently overlooked or taken for granted, it this is in fact well defined.59,64 Comparison of the similarity of the 2D HSQC NMR for the polymers and lignins (Fig. 3) spectra clearly shows the relative stereochemistry of these linkages in our polymers closely matches those in lignin based on 1H and 13C chemical shift analysis.59
Chemical reactivity
In order to assess how the reactivity or our model polymers compared to natural lignins we decided to use the well-established DFRC method of lignin analysis developed by Ralph et al.65 This method has been extensively employed to analyse lignin in situ and following isolation. The results of this analysis are represented in Fig. 6. For polymer 19 (Fig. 6A) and doulgas fir lignin (Fig. 6B) only coniferyl alcohol diacetate is detected, consistent with NMR analysis indicating that only G units are present in both. An additional peak is present for 19 assigned to an end group unit whilst the douglas fir lignin gives remarkably clean products. As expected, for polymer 9 (Fig. 6C) and birch lignin (Fig. 6D) peaks are present for both coniferyl and sinapyl alcohol diacetate. In this case additional minor peaks are detected from birch lignin whilst 9 shows two additional peaks assigned to S and G end groups. The G
:
S ratio calculated for 9 using this method was 51
:
49 which is in excellent agreement with the expected 50
:
50 ratio based on the mixture of monomers used to prepared this polymer. This differs from the ratio determined by 2D HSQC NMR (Fig. 3) because the coniferyl and sinapyl alcohol diacetate monomers detected during this analysis arise from the cleavage of the β-O-4 linkages and not the resinol units.65
 |
| Fig. 6 FID GCs of monomeric DFRC products from isolated lignins and polymeric models. A – 19, B – douglas fir lignin, C – 9, D – birch lignin. Gc/t – coniferyl alcohol diacetate (G unit), Sc/t – sinapyl alcohol diacetate (S unit), t = trans, c = cis. The G : S ratio for polymer 9 was calculated using previously reported response factors for Gc/t and Sc/t.65 | |
Scalability
For these models to be useful substrates for the development of depolymerisation strategies they need to be accessible on gram to multigram scales. With this in mind the number of steps requiring purification by column chromatography has been minimised facilitating scale up. This has allowed the synthesis of polymer 9 on a 2 g scale, with no need for column chromatography from start to finish. Similar or larger scale synthesis of any of the polymers reported should be achievable if required as all the monomers have been prepared on gram to multi-gram scales. Additionally, given the relatively low abundance of resinol units in softwood lignins it could arguably be reasonable in some cases to omit this from the softwood lignin polymers, removing the need for any chromatography during the synthesis of non-phenolic β-O-4 and β-5 polymers, further improving scalability. What is, however, still unknown is how minor linkages such as the β–β unit affect the 3D structure of lignin in solution and hence their potential impact on the chemical reactivity of the lignin polymer.
3. Conclusions
A new method for the synthesis of complex lignin polymers as an alternative to DHP polymers has been developed for the investigation of lignin depolymerisation and valorisation. The method presented here provides fine control over the G
:
S ratio and the linkage composition of the polymer. The synthesis of polymer 9 containing both S and G units was demonstrated which was composed of both β-O-4 and β–β units representing a hardwood lignin model. As an extension to this softwood model polymer 19 was synthesised containing β-O-4, β–β and β-5 units, as was polymer 23 which also contained 5–5 units and phenolic groups. This is the first time, to the best of our knowledge, that polymers containing all three or four units have been synthesis by non-radical processes and therefore with excellent compositional control. In addition the scalability of such a synthesis has been demonstrated to give model polymers on multigram scales. It is hoped that complex model polymers such as those synthesised here will aid in the development of novel methods for lignin depolymerisation and valorisation ultimately allowing the full potential of this renewable resource to be unlocked.
Acknowledgements
This work was funded by the EP/J018139/1, EP/K00445X/1 grants and an EPSRC Doctoral Prize Fellowship. We acknowledge the EPSRC UK National Mass Spectrometry Facility at Swansea University for mass spectrometry analysis. We would like to thank Professor Kamer (St Andrews) for use of a GC-FID and Dr Tomas Lebl for NMR support.
Notes and references
- W. Boerjan, J. Ralph and M. Baucher, Annu. Rev. Plant Biol., 2003, 54, 519 CrossRef CAS PubMed
.
- J. Zakzeski, P. C. A. Bruijnincx, A. L. Jongerius and B. M. Weckhuysen, Chem. Rev., 2010, 110, 3552 CrossRef CAS PubMed
.
- H. Lange, S. Decina and C. Crestini, Eur. Polym. J., 2013, 49, 1151 CrossRef CAS PubMed
.
- C. Xu, R. A. D. Arancon, J. Labidi and R. Luque, Chem. Soc. Rev., 2014, 43, 7485 RSC
.
- P. J. Deuss and K. Barta, Coord. Chem. Rev Search PubMed
, in press.
- This figure is an estimate based on data available from the Food and Agriculture Organization of the United Nations Statistic Division (FAOSTAT) available at http://faostat3.fao.org/download/F/FO/E. In 2013 chemical wood pulp production was reported as 131 million tonnes. Assuming average pulp yields of 50% this means a total of 262 million tonnes of lignocellulosic biomass was used for pulp production. Taking an average of 30% lignin content with an 80% degree of delignification gives a total extracted lignin of 63 million tonnes.
- “The World's Leading Biorefinery.” Borregaard, http://www.borregaard.com/content/view/full/10231, (accessed June 2015).
- The FAOSTAT estimate that in 2013 global kraft pulp production was 127 million tonnes (33 million tonnes unbleached and 94 million tonnes bleached) which was 97% of world pulp production. 4.1 million tonnes of sulfite pulp was produced (1.3 million tonnes unbleached and 2.8 million tonnes bleached).
- F. P. Bouxin, A. McVeigh, F. Tran, N. J. Westwood, M. C. Jarvis and S. D. Jackson, Green Chem., 2015, 17, 1235 RSC
.
- S. Van den Bosch, W. Schutyser, R. Vanholme, T. Driessen, S. F. Koelewijn, T. Renders, B. De Meester, W. J. J. Huijgen, W. Dehaen, C. M. Courtin, B. Lagrain, W. Boerjan and B. F. Sels, Energy Environ. Sci., 2015, 8, 1748 CAS
.
- C. S. Lancefield, O. S. Ojo, F. Tran and N. J. Westwood, Angew. Chem., Int. Ed., 2015, 54, 258 CrossRef CAS PubMed
.
- A. Rahimi, A. Ulbrich, J. J. Coon and S. S. Stahl, Nature, 2014, 515, 249 CrossRef CAS PubMed
.
- Q. Song, F. Wang, J. Cai, Y. Wang, J. Zhang, W. Yu and J. Xu, Energy Environ. Sci., 2013, 6, 994 CAS
.
- M. V. Galkin and J. S. M. Samec, ChemSusChem, 2014, 7, 2154 CrossRef CAS PubMed
.
- P. J. Deuss, M. Scott, F. Tran, N. J. Westwood, J. G. de Vries and K. Barta, J. Am. Chem. Soc., 2015, 137, 7456 CrossRef CAS PubMed
.
- K. Barta, G. R. Warner, E. S. Beach and P. T. Anastas, Green Chem., 2014, 16, 191 RSC
.
- K. Barta, T. D. Matson, M. L. Fettig, S. L. Scott, A. V. Iretskii and P. C. Ford, Green Chem., 2010, 12, 1640 RSC
.
- P. D. Sainsbury, E. M. Hardiman, M. Ahmad, H. Otani, N. Seghezzi, L. D. Eltis and T. D. H. Bugg, ACS Chem. Biol., 2013, 8, 2151 CrossRef CAS PubMed
.
- J. Zakzeski and B. M. Weckhuysen, ChemSusChem, 2011, 4, 369 CrossRef CAS PubMed
.
- S. Dabral, J. Mottweiler, T. Rinesch and C. Bolm, Green Chem., 2015 Search PubMed
, in press.
- W. G. Forsythe, M. D. Garrett, C. Hardacre, M. Nieuwenhuyzen and G. N. Sheldrake, Green Chem., 2013, 15, 3031 RSC
.
- R. Katahira, H. Kamitakahara, T. Takano and F. Nakatsubo, J. Wood Sci., 2006, 52, 255 CrossRef CAS
.
- T. Kishimoto, Y. Uraki and M. Ubukata, Org. Biomol. Chem., 2006, 4, 1343 CAS
.
- Y. Tobimatsu, F. Chen, J. Nakashima, L. L. Escamilla-Treviño, L. Jackson, R. A. Dixon and J. Ralph, Plant Cell, 2013, 25, 2587 CrossRef CAS PubMed
.
- J. Ralph, R. F. Helm, S. Quideau and R. D. Hatfield, J. Chem. Soc., Perkin Trans. 1, 1992, 2961 RSC
.
- N. D. Bonawitz, J. I. Kim, Y. Tobimatsu, P. N. Ciesielski, N. A. Anderson, E. Ximenes, J. Maeda, J. Ralph, B. S. Donohoe, M. Ladisch and C. Chapple, Nature, 2014, 509, 376 CrossRef CAS PubMed
.
- Q. Zhao, Y. Tobimatsu, R. Zhou, S. Pattathil, L. Gallego-Giraldo, C. Fu, L. A. Jackson, M. G. Hahn, H. Kim, F. Chen, J. Ralph and R. A. Dixon, Proc. Natl. Acad. Sci. U. S. A., 2013, 110, 13660 CrossRef CAS PubMed
.
- J. H. Grabber, J. Ralph, R. D. Hatfield, S. Quideau, T. Kuster and A. N. Pell, J. Agric. Food Chem., 1996, 44, 1453 CrossRef CAS
.
- Y. Tobimatsu, C. L. Davidson, J. H. Grabber and J. Ralph, Biomacromolecules, 2011, 12, 1752 CrossRef CAS PubMed
.
- T. Sonoki, Y. Iimura, E. Masai, S. Kajita and Y. Katayama, J. Wood Sci., 2002, 48, 429 CrossRef CAS
.
- R. Kondo, T. Iimori, H. Imamura and T. Nishida, J. Biotechnol., 1990, 13, 181 CrossRef CAS
.
- J. Perez and T. W. Jeffries, Appl. Environ. Microbiol., 1992, 58, 2402 CAS
.
- S. Yoshida, A. Chatani, Y. Honda, T. Watanabe and M. Kuwahara, J. Wood Sci., 1998, 44, 486 CrossRef CAS
.
- S. Shary, S. A. Ralph and K. E. Hammel, Appl. Environ. Microbiol., 2007, 73, 6691 CrossRef CAS PubMed
.
- N. G. Lewis, R. A. Razal and E. Yamamoto, Proc. Natl. Acad. Sci. U. S. A., 1987, 84, 7925 CrossRef CAS
.
- S. Chu, A. V. Subrahmanyam and G. W. Huber, Green Chem., 2013, 15, 125 RSC
.
- M. V. Galkin, S. Sawadjoon, V. Rohde, M. Dawange and J. S. M. Samec, ChemCatChem, 2014, 6, 179 CrossRef CAS PubMed
.
- J. Rencoret, A. Gutiérrez, L. Nieto, J. Jiménez-Barbero, C. B. Faulds, H. Kim, J. Ralph, Á. T. Martínez and J. C. del Río, Plant Physiol., 2011, 155, 667 CrossRef CAS PubMed
.
- J. C. del Río, J. Rencoret, P. Prinsen, Á. T. Martínez, J. Ralph and A. Gutiérrez, J. Agric. Food Chem., 2012, 60, 5922 CrossRef PubMed
.
- A. Rahimi, A. Azarpira, H. Kim, J. Ralph and S. S. Stahl, J. Am. Chem. Soc., 2013, 135, 6415 CrossRef CAS PubMed
.
- K. Freudenberg and R. Dillenburg, Chem. Ber., 1951, 84, 67 CrossRef CAS PubMed
.
- Z. Liu, Y. Gong, H.-S. Byun and R. Bittman, New J. Chem., 2010, 34, 470 RSC
.
- K. Freudenberg, J. M. Harkin, M. Reichert and T. Fukuzumi, Chem. Ber., 1958, 91, 581 CrossRef CAS PubMed
.
- J. J. Stewart, T. Akiyama, C. Chapple, J. Ralph and S. D. Mansfield, Plant Physiol., 2009, 150, 621 CrossRef CAS PubMed
.
- S. K. Huntley, D. Ellis, M. Gilbert, C. Chapple and S. D. Mansfield, J. Agric. Food Chem., 2003, 51, 6178 CrossRef CAS PubMed
.
-
Y. Tobimatsu, T. Takano, H. Kamitakahara and F. Nakatsubo, in Holzforschung, 2008, vol. 62, p. 495 Search PubMed
.
- A. Wagner, Y. Tobimatsu, L. Phillips, H. Flint, K. Torr, L. Donaldson, L. Pears and J. Ralph, Plant J., 2011, 67, 119 CrossRef CAS PubMed
.
- M. Sette, R. Wechselberger and C. Crestini, Chem. – Eur. J., 2011, 17, 9529 CrossRef CAS PubMed
.
- J. Ralph, M. T. Garcia Conesa and G. Williamson, J. Agric. Food Chem., 1998, 46, 2531 CrossRef CAS
.
- F. Chioccara, S. Poli, B. Rindone, T. Pilati, G. Brunow, P. Pietikainen and H. Setala, Acta Chem. Scand., 1993, 47, 610 CrossRef CAS
.
- S. Apers, D. Paper, J. Bürgermeister, S. Baronikova, S. Van Dyck, G. Lemière, A. Vlietinck and L. Pieters, J. Nat. Prod., 2002, 65, 718 CrossRef CAS PubMed
.
- D. L. A. Rakotondramanana, M. Delomenède, M. Baltas, H. Duran, F. Bedos-Belval, P. Rasoanaivo, A. Negre-Salvayre and H. Gornitzka, Bioorg. Med. Chem., 2007, 15, 6018 CrossRef CAS PubMed
.
- P. Karhunen, P. Rummakko, J. Sipilä, G. Brunow and I. Kilpeläinen, Tetrahedron Lett., 1995, 36, 169 CrossRef CAS
.
- D. S. Argyropoulos, L. Jurasek, L. Krištofová, Z. Xia, Y. Sun and E. Paluš, J. Agric. Food Chem., 2002, 50, 658 CrossRef CAS PubMed
.
- C. Crestini, F. Melone, M. Sette and R. Saladino, Biomacromolecules, 2011, 12, 3928 CrossRef CAS PubMed
.
- A. Granata and D. S. Argyropoulos, J. Agric. Food Chem., 1995, 43, 1538 CrossRef CAS
.
- J.-L. Wen, S.-L. Sun, B.-L. Xue and R.-C. Sun, Materials, 2013, 6, 359 CrossRef CAS PubMed
.
-
C. Heitner, D. Dimmel and J. Schmidt, Lignin and Lignans: Advances in Chemistry, Taylor & Francis, 2010 Search PubMed
.
- F. Tran, C. S. Lancefield, P. C. J. Kamer, T. Lebl and N. J. Westwood, Green Chem., 2015, 17, 244 RSC
.
- D. V. Evtuguin, C. P. Neto, A. M. S. Silva, P. M. Domingues, F. M. L. Amado, D. Robert and O. Faix, J. Agric. Food Chem., 2001, 49, 4252 CrossRef CAS PubMed
.
- S. Shimizu, T. Yokoyama, T. Akiyama and Y. Matsumoto, J. Agric. Food Chem., 2012, 60, 6471 CrossRef CAS PubMed
.
- D. J. Yelle, A. N. Kapich, C. J. Houtman, F. Lu, V. I. Timokhin, R. C. Fort, J. Ralph and K. E. Hammel, Appl. Environ. Microbiol., 2014, 80, 7536 CrossRef PubMed
.
-
T. Akiyama, H. Goto, S. Nawawi Deded, W. Syafii, Y. Matsumoto and G. Meshitsuka, in Holzforschung, 2005, vol. 59, p. 276 Search PubMed
.
- J. Ralph, K. Lundquist, G. Brunow, F. Lu, H. Kim, P. Schatz, J. Marita, R. Hatfield, S. Ralph, J. Christensen and W. Boerjan, Phytochem. Rev., 2004, 3, 29 CrossRef CAS
.
- F. Lu and J. Ralph, J. Agric. Food Chem., 1997, 45, 2590 CrossRef CAS
.
Footnotes |
† Electronic supplementary information (ESI) available: Detailed synthetic procedures for the synthesis of monomers and polymers, characterization of novel compounds and NMR spectra. See DOI: 10.1039/c5gc01334h |
‡ Whilst we report molecular weights for these polymers and lignins it should be noted that these are based on polystyrene standards and as such are unlikely to reflect accurately the actual molecular weight of these polymers. As such these values should only be used for comparative purposes. |
|
This journal is © The Royal Society of Chemistry 2015 |
Click here to see how this site uses Cookies. View our privacy policy here.