Analysis and understanding of amido black 10B dye degradation in aqueous solution by electrocoagulation with the conventional oxidants peroxomonosulfate, peroxodisulfate and hydrogen peroxide†
Received
2nd August 2014
, Accepted 24th October 2014
First published on 11th November 2014
Abstract
We investigated the degradation of amido black 10B dye by electrocoagulation (EC) processes assisted by the conventional oxidants peroxomonosulfate (PMS), peroxodisulfate (PDS) and hydrogen peroxide (HP). These EC processes were based on the formation of hydroxyl (HO˙) and sulfate (SO4˙−) radicals through electrochemically generated Fe2+/Fe3+-mediated activation of PMS, HP and PDS. Special attention was given to understanding the influence of the applied current, the initial solution pH and the concentration of the different oxidants on the degradation of the amido black 10B dye. The optimum operating conditions for each of these parameters was verified experimentally using Fe electrodes. Our results suggested that a low applied current and an acidic environment (pH 5) were favorable and very effective conditions for oxidant-assisted EC processes. The experimental results also showed that the oxidant-assisted EC processes produced exceptional degradation (99%) of amido black 10B dye with low energy consumption under the optimum conditions of CAB = 0.16 mM, CNaCl = 17 mM, CPMS = CPDS = 0. 16 mM, CHP = 0.13 mM and pH 5. The efficiency of degradation of amido black 10B dye by oxidant-assisted EC was in the order PMS > PDS > HP. The UV–visible spectral changes clearly showed that the azo linkage (–N
N–) was degraded more easily by oxidant-assisted EC processes than the aromatic rings of the amido black 10B dye molecule. The maximum mineralization efficiencies attained for EC and EC assisted by PMS, PDS and HP were 34, 66, 57 and 46%, respectively.
Water impact
Electrocoagulation (EC) is a promising technology for water and wastewater treatment. In recent years, the EC process has been intensified with the addition of hydrogen peroxide (HP) for the degradation of organic pollutants. However, some drawbacks have been noted in HP-assisted EC. Therefore a new EC process is being developed that includes conventional oxidants such as peroxomonosulfate and peroxodisulfate. This process seems to be more effective for the degradation of organic pollutants present in wastewater. The aim of this study was to investigate the activation of conventional oxidants through EC for the degradation of dye molecules in aqueous media.
|
1. Introduction
Wastewaters from the textile dye industry contain a large number of persistent organic dye molecules that can adversely affect the environment, in addition to causing allergies, skin irritation and mutations in humans. Therefore the treatment of dye wastewaters is highly desirable for the well-being of both humans and aquatic ecosystems. There are a number of techniques available for treating dye wastewaters, such as adsorption, chemical coagulation, membrane processes, electrochemical oxidation, electrocoagulation (EC), biological methods and advanced oxidation techniques (AOTs).1–8 AOTs have been mainly used for the destruction of refractory organic compounds. The key function of AOTs is to generate highly oxidizing species such as hydroxyl radicals (HO˙). The electrophilic HO˙ generated efficiently degrade the organic compounds in the dye wastewaters through a series of complex reactions because they can react with almost all electron-rich organic compounds in a rapid and non-selective manner.1,2,8
Among the currently available AOTs, oxidation using Fenton's reagent (the Fenton and electro-Fenton processes) is an attractive and efficient technique for the demineralization of a large number of refractory organic pollutants. Fenton's reagent has a low toxicity and does not form any residual compounds.9–11 The electro-Fenton process is conducted in two different configurations. In the first configuration, Fenton's reagent is added to the electrochemical reactor externally and catalytically active inert electrodes are used as the anodes. In the second configuration, hydrogen peroxide (HP) is simply added to the reactor and ferrous (Fe2+) ions are generated from a sacrificial Fe anode. Chemically stable Pt anode materials have been explored for use in the first configuration, but are expensive. HP-assisted EC processes have also been demonstrated for the treatment of different types of industrial wastewaters using a sacrificial electrode (Fe or Al).12–23 Table S1† summarizes the different types of wastewater treatment reported using HP-assisted EC processes, together with the operating conditions and treatment efficiencies. However, the Fenton reaction and its modified processes have several shortcomings in practical applications, including the dependence of the reaction on the pH.
An alternative effective AOT is based on the sulfate radical (SO4˙−).24–30 SO4˙− is an exceptionally powerful oxidizing agent with oxidation/reduction potentials of E0 = +2.5 to +3.1 V vs. NHE (HO˙ E0 = +1.8 to +2.7 V vs. NHE). Conventional inorganic oxidants (peroxides) such as peroxomonosulfate (PMS, HSO5−) and peroxodisulfate (PDS, S2O82−) are generally used in the SO4˙−-based AOTs. These peroxides have standard redox potentials of E0 =1.82 V (PMS) and E0 = 2.1 V (PDS). The sulfate radicals are typically generated from PMS and PDS by UV photolysis, heat and bases or transition metals.24,26,27,29 PMS is more easily activated by transition metals than PDS as a result of its asymmetrical molecular structure.31 Homogeneous catalytic oxidation using PMS coupled with transition metals has been shown to efficiently degrade organic pollutants. However, the electrochemical activation of PMS and PDS has not been studied in detail. Our previous study successfully demonstrated the degradation of highly chlorinated phenol, pentachlorophenol (PCP) via the electrochemical activation of conventional oxidants such as PMS, PDS and HP.32 The reactivity of the free radicals (SO4˙− and HO˙) was assessed based on the first-order rate constant for the degradation of PCP. We evaluated the influence of the primary experimental parameters, such as the applied current, the initial solution pH and the oxidant concentration, on the degradation of PCP. In addition, the influence of factors involved in the degradation of PCP was optimized by Taguchi analysis based on an orthogonal array L9 (33) experimental design.32
In the present study, in addition to the influence of the applied current, the initial solution pH and the concentration of the oxidants, we also investigated the effect of the NaCl concentration on the electrode materials (Fe and Al) and energy consumption during the degradation of the azo dye amido black 10B (AB). The degradation and mineralization efficiency were also compared using the determined optimum experimental conditions.
2. Materials and methods
2.1 Materials
Hydrogen peroxide (H2O2, 30%) and sodium chloride (NaCl) were obtained from Merck Chemicals, India. Potassium peroxomonosulfate (a triple salt with the composition 2KHSO5·KHSO4·K2SO4) and potassium peroxodisulfate (K2S2O8) were purchased from Sigma-Aldrich Chemicals, India. Amido black 10B was used as received from LOBA Chemicals, India. All chemicals used in the study were of analytical-reagent grade. Double-distilled water was used to prepare the solutions.
2.2 EC cell configuration
All the EC experiments were conducted at ambient temperature (25 ± 2 °C) in an open and undivided batch electrochemical reactor (Fig. 1). Sacrificial Fe plates with a total effective surface area of 14.1 cm2 were used as the electrodes. The anode and cathode were connected in parallel at an inter-electrode distance of 2 cm and each had dimensions of 4.7 × 3 × 0.5 cm. In each run, 200 mL of electrolyte were taken into the 500 mL glass beaker and were agitated continuously. A DC current was applied via an A Lab L3202 DC power supply.
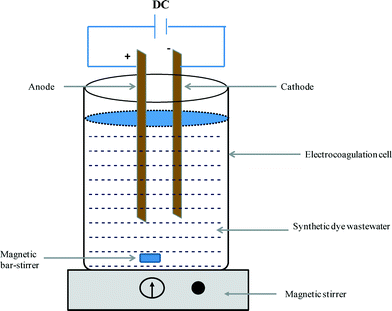 |
| Fig. 1 Schematic diagram of the configuration of the batch electrocoagulation cell. | |
2.3 Analytical methodology
Before the start of electrolysis, the electrolyte solution was stirred magnetically at a constant rate of 300 rev min−1. The concentration of AB in the bulk solution (determined from the absorbance of AB at λmax = 618 nm; εmax = 22
187 M−1 cm−1) was taken as the initial dye concentration (C0). Aliquots of 3 mL were withdrawn at regular time intervals during electrolysis and were filtered using a 0.22 μm pore size PVDF syringe filter (Pall Corporation, India). AB was determined in the filtered samples at λmax = 618 nm using a UV–visible spectrophotometer (JASCO-V670). The concentration obtained at a certain reaction time is represented as Ct. There was no change in the peak positions and no new peak was observed in the absorption spectrum of AB during the course of the reaction. The absorbance was proportional to the concentration of AB. The degradation efficiency can be calculated using the formula: |  | (1) |
The mineralization of AB was determined by measuring the total organic carbon (TOC) content of the electrocoagulated sample at regular time intervals. The TOC content was determined using a Shimadzu Model TOC-VLPH TOC analyzer. The TOC measured before the start of electrolysis was taken as the initial TOC concentration (TOC0) and the TOC concentration at various electrolysis times (t) was represented as TOCt. The mineralization efficiencies can be calculated using eqn (2):
|  | (2) |
The amount of electrical energy consumed (Econ) is calculated as follows:
where
Econ is the electrical energy consumption (kW h),
U is the voltage of the cell (V),
I is the applied current (A) and
tEC is the electrolysis time (h).
3. Results and discussion
3.1 Influence of applied current
The applied current is a key operating parameter and can strongly influence the efficiency of the whole process because it determines the rate of anodic dissolution. To determine the effect on the degradation of AB of the addition of an oxidant during EC, the degradation of AB was investigated using different applied currents (50–200 mA) under identical experimental conditions (CAB = 0.16 mM, CNaCl = 17 mM, Coxidant = 0.07 mM, initial solution pH 7 ± 0.2). Fig. 2 shows the degradation efficiency obtained during EC as a function of energy consumption (Econ) with and without added oxidant. In EC without oxidant, the degradation efficiency increased from 32 to 98% when the applied current increased from 50 to 200 mA (Fig. 2). This is because the rate of electrolytic dissolution at the Fe anode increases, forming increasing amounts of monomeric Fe(OH)3 and polymeric Fe(OH)n flocs. These insoluble metal hydroxides are capable of removing the dye molecules in a number of different ways: (i) the cationic species of the monomeric and polymeric metal hydroxides can bind with the anionic sites of the organic moiety, resulting in charge neutralization, which, in turn, reduces the concentration of the soluble organic compound (eqn (7) and (8)); (ii) the dye molecules may be enmeshed in particles of the metal hydroxide precipitates; and (iii) the dye molecules can be adsorbed on superficially charged metal hydroxide precipitates.33,34 The key reactions are:
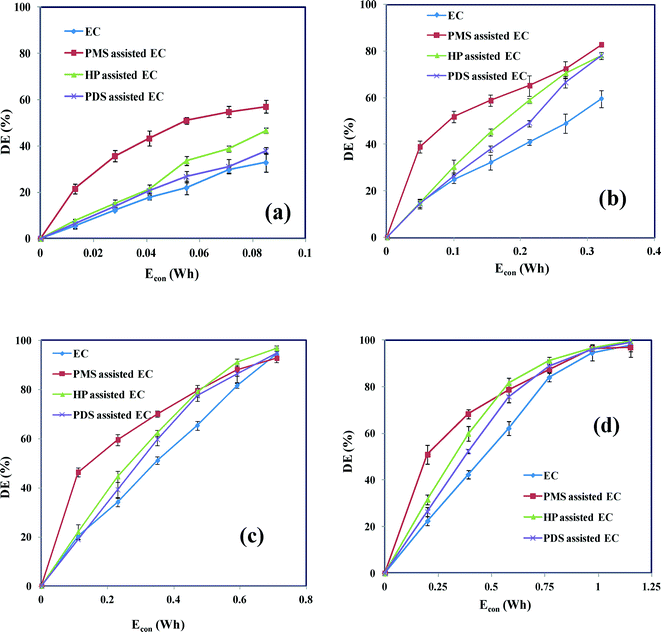 |
| Fig. 2 Degradation efficiency as a function of electrical energy consumption (Econ) in the presence and absence of oxidant-assisted EC at different applied currents: (a) 50 mA; (b) 100 mA; (c) 150 mA; and (d) 200 mA. CAB = 0.16 mM, CNaCl = 17 mM, Coxidant = 0.07 mM and pH 7 ± 0.2. | |
At the anode:
| 4Fe(s) → 4Fe2+(aq) + 8e− | (4) |
| 4Fe2+(aq) + 10H2O(l) + O2(aq) → 4Fe(OH)3(s) + 8H+(aq) | (5) |
At the cathode:
| 8H+(aq) + 8e− → 4H2(g) | (6) |
Precipitation:
| [monomeric iron hydroxide] + [dye] → [monomeric iron hydroxide–dye(s)] | (7) |
| [polymeric iron hydroxide] + [dye] → [polymeric iron hydroxide–dye(s)] | (8) |
Adsorption:
| Fe(OH)n(s) + dye → [sludge] | (9) |
| [polymeric iron hydroxide–dye](s) + Fe(HO)n(s) → [sludge] | (10) |
To examine the effects of the addition of oxidant on the degradation of AB in EC, further experiments were performed with the oxidants PMS, HP and PDS; the observed degradation efficiency profiles are given in Fig. 2. It is found that slight enhancement of degradation efficiency is due to the addition of oxidant in EC. The degradation efficiency is improved by increasing the applied current for all three oxidants. The maximum degradation efficiency in Fig. 2a–d, indicates that the oxidant assisted EC processes have great magnifying degradation efficiency than EC in low applied current such as 50 mA and 100 mA. In particular, the PMS-assisted EC process gives maximum degradation efficiencies of 59 and 72% when the applied current is 50 and 100 mA, respectively. These degradation efficiencies are relatively higher than those achieved with HP- and PDS-assisted EC at the same current. The increase in the degradation of AB in the oxidant-assisted EC processes is a result of the electrochemically generated ions (Fe2+/Fe3+), which catalyze the oxidants (PMS, HP and PDS) to produce potential oxidizing species such as sulfate (SO4˙−) and hydroxyl (HO˙) radicals. Fig. 3 shows the mechanism responsible for the degradation of AB by the oxidant-assisted EC process. The active radicals can degrade the dye molecule by chemical oxidation, which, in turn, decreases the concentration of the dye.28 The increase in degradation may also be attributed to the electrochemical reduction of the oxidant on the cathode surface to generate active radicals such as SO4˙− and HO˙ (eqn (11)–(14)). This may lead to an improvement in the degradation efficiency. PDS-assisted EC has a lower degradation efficiency than PMS- and HP-assisted EC. This can be attributed to the fact that the rate of dissociation of PDS is more stable than the rates of dissociation of PMS and HP.29 Possible cathodic reactions in the presence of the oxidants include:
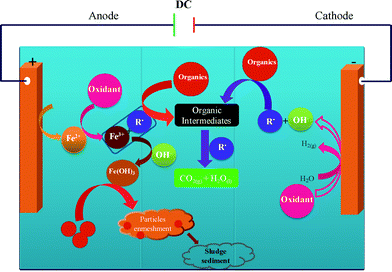 |
| Fig. 3 Mechanism responsible for the degradation the AB dye molecule by oxidant-assisted EC with Fe electrodes. | |
PMS addition:
| HSO5− + e− → HO˙ + SO42− | (11) |
| HSO5− + e− → HO− + SO4˙− | (12) |
PDS addition:
| S2O82− + e− → SO4˙− + SO42− | (13) |
HP addition:
| H2O2 + e− → HO˙ + OH− | (14) |
Increasing the applied current increases the formation of Fe2+ and also influences the generation and persistence of SO4˙− and HO˙. However, at currents greater than 100 mA, there is no appreciable change in the degradation of AB by oxidant-assisted EC. This is because the surplus amount of Fe2+ leads to an increase in the probability of collisions between the reactive radicals (SO4˙− and HO˙) and Fe2+.25,27–29 When this occurs, SO4˙− and HO˙ are quickly consumed by the excess Fe2+ ions, decreasing the availability of the reactive oxidizing species (eqn (15) and (16)).
| Fe2+ + SO4˙− → Fe3+ + SO42− | (15) |
Therefore an excessive amount of Fe2+ inhibits the degradation process. However, although SO4˙− interacts with Fe2+ at a diffusion-controlled rate when there is an excess amount of Fe2+ in solution, it further facilitates the reaction (eqn (15)). Based on the rate constant for the reaction between the sulfate radicals and Fe2+, SO4˙− is quenched by Fe2+ and this contributes to the major side reaction.25 These results are also supported based on concentration of Fe2+ (Fig. 4). A minimum concentration of Fe2+ is therefore essential to effectively activate these oxidants, although an excess of Fe2+ has detrimental effects on the degradation of the dye. These experimental results confirm that oxidant-assisted EC processes are more efficient at low Fe2+ concentrations. Therefore an applied current of 50 mA was chosen for the subsequent investigations.
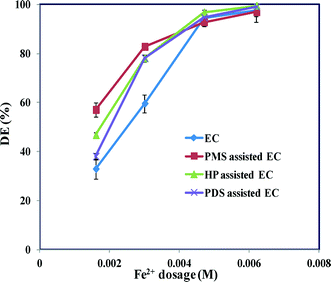 |
| Fig. 4 Effect of Fe2+ concentration on the maximum degradation of AB by EC and oxidant-assisted EC at different applied currents. CAB = 0.16 mM, CNaCl = 17 mM, Coxidant = 0.07 mM and pH 7 ± 0.2. | |
3.2 Influence of NaCl concentration
The effect of different concentrations of NaCl on the degradation of AB was studied by varying the concentration of NaCl from 8.5 to 25.5 mM. Fig. S3† shows the obtained degradation profiles versus Econ. The results indicated that the efficiency of dye degradation by HP- and PDS-assisted EC are not significantly affected by increasing the concentration of NaCl. However, PMS-assisted EC had a very limited ability to oxidize the dye molecules. This is because PMS interacts with chloride ions to produce the active chlorine species HOCl/Cl2 (eqn (17) and (18)), which degrade the dye molecule (eqn (19)). In addition, increasing the concentration of NaCl has an adverse effect on the degradation of the dye. This may be a result of the consumption of sulfate radicals by chloride ions and the formation of less reactive chlorine radicals (eqn (20)): | Cl− + HSO5− → SO42− + HOCl | (17) |
| 2Cl− + HSO5− + H+ → SO42− + Cl2 + H2O | (18) |
| HOCl/Cl2 + dye → oxidized products + CO2 + H2O + Cl− | (19) |
| SO4˙− + Cl− ↔ SO42− + Cl˙ | (20) |
3.3 Influence of initial solution pH in oxidant-assisted EC processes
We have previously shown that the initial solution pH can affect the oxidant-assisted EC processes. The pH of the solution was changed by the addition of dilute hydrochloric acid or sodium hydroxide. To study the influence of the initial pH on the degradation of AB, experiments were conducted under identical conditions of CAB = 0.16 mM, CNaCl = 17 mM, Coxidant = 0.07 mM and current = 50 mA at acidic (5), neutral (7) and basic (9) pH values. Fig. 5 shows the degradation efficiency versus Econ obtained by EC in the absence and presence of oxidant at different initial values of pH. The degradation efficiencies increased with increasing Econ for acidic, neutral and basic pH values, as expected. However, there is a notable enhancement in the degradation efficiency with increasing Econ for acidic pH values compared with neutral and basic pH values. Fig. 5d compares the maximum degradation efficiencies as a function of pH and shows that the degradation efficiency increased from 32 to 40% when the initial pH was increased from 5 to 9 without the addition of an oxidant in the EC process. This phenomenon can be explained by the observation that, at higher pH values, the Fe(OH)n(s) formed remains in solution as an insoluble precipitate that can remove the dye molecules either by electrostatic attraction or complexation followed by coagulation. Under acidic conditions Fe3+ can be hydrated and species such as Fe(OH)2+, Fe(OH)2+ and Fe2(OH)24+ may be present during the EC processes.35
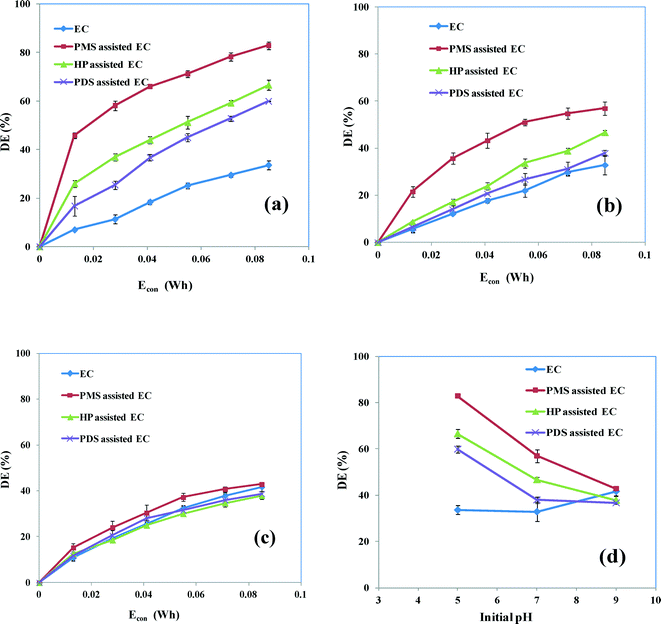 |
| Fig. 5 Degradation efficiency of EC and oxidant-assisted EC as a function of Econ with different initial values of solution pH: (a) pH 5; (b) pH 7; (c) pH 9; and (d) comparison of degradation efficiencies as a function of pH at 0.085 W h. CAB = 0.16 mM, CNaCl = 17 mM, Coxidant = 0.07 mM and current = 50 mA. | |
Fig. 5d shows that the degradation of the AB dye is considerably decreased as a result of the increase in the initial solution pH in oxidant-assisted EC. Oxidant-assisted EC also ensures that an acidic pH is more favorable for degradation than a neutral and alkaline pH. At the lower pH value (pH 5), maximum degradation efficiencies of 83, 65 and 59% were attained by EC in the presence of PMS, HP and PDS, respectively. This is because, under acidic conditions, the electrochemically generated Fe2+ efficiently activates the oxidants to create reactive free radicals33 that can significantly accelerate the degradation by oxidizing the dye molecule. It can be shown that the degradation obtained by oxidant-assisted EC is mainly a result of the action of radicals. The degradation of AB is lower in solutions with a higher pH, even with the addition of oxidants. This can be attributed to the formation of ferric hydroxo-complexes (eqn (21)–(24)),17i.e. the precipitation of Fe3+ as Fe(OH)3, which hinders the reaction between Fe3+ and the oxidant:
| Fe2+ + H2O → FeOH+ + H+ | (21) |
| Fe3+ + H2O → Fe(OH)2+ + H+ | (22) |
| Fe3+ + 2H2O → Fe(OH)2+ + 2H+ | (23) |
| 2Fe3+ + 2H2O → Fe2(OH)24+ + 2H+ | (24) |
At higher pH values in PMS-assisted EC, Fe3+ ions react with HSO5− to produce the less reactive peroxymonosulfate radical (SO5˙−) rather than SO4˙−,28 which may be why the degradation efficiency is reduced. Therefore an initial pH of 5 is more favorable for the oxidant-assisted EC processes and an initial solution pH of 5 was used in subsequent experimental work.
3.4 Influence of oxidant concentration on AB degradation
3.4.1 Influence of PMS concentration.
The influence of PMS on degradation was examined by varying the PMS concentration (CPMS) from 0.03 to 0.20 mM. Fig. 6a shows the observed degradation efficiency versus Econ. The maximum degradation of AB is rapidly increased from 62 to 99% with increasing concentrations of PMS from 0.03 to 0.17 mM. The increase in degradation is a result of the efficient activation of PMS by electrochemically produced Fe2+ ions. This leads to the formation of a large number of potentially oxidizing SO4˙− radicals (eqn (25)). These potentially oxidizing SO4˙− radicals have a tendency to attack organic compounds at various positions and cause fragmentation because SO4˙− is a strong one-electron oxidant (E0 = 2.6 V) compared with the parent oxidant (PMS).28 PMS also interacts with Fe3+ ions to produce SO5˙− radicals (eqn (26)), which are less reactive than SO4˙−. However, Fe2+ is regenerated in the same reaction and can react further with PMS to create highly energetic SO4˙− radicals.
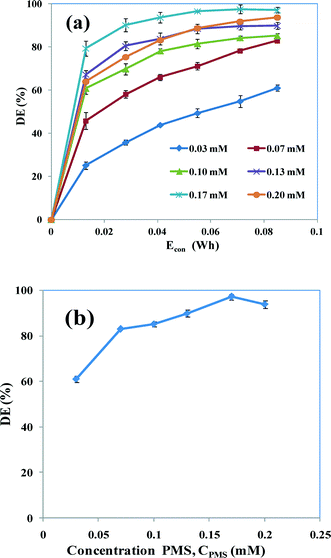 |
| Fig. 6 (a) Degradation efficiency of PMS-assisted EC as a function of Econ at various concentrations of PMS (0.03–0.2 mM). (b) Degradation efficiencies at 0.085 W h. CAB = 0.16 mM, CNaCl = 17 mM, current = 50 mA and pH 5. | |
PMS is also activated by chloride ions (Cl−) to form oxidizing agents such as hypochlorite (HOCl) and chlorine gas (Cl2) (eqn (17) and (18)), which may also oxidize the dye molecules. Hypochlorites in particular have a higher instability as a result of the ionic environment, leading to a higher reactivity towards the aromatic nucleus of the dye.26 A further increase in the concentration of PMS to 0.2 mM causes the degradation efficiency to decrease slightly. The maximum degradation efficiency was determined by varying the concentration of PMS (Fig. 6b). The efficiency of degradation increases up to 0.17 mM PMS, although the degradation efficiency at 0.2 mM is lower than at 0.17 mM PMS. This may be due to the reaction of the oxidant (PMS) itself with the SO4˙− formed, which, in turn, can reduce the oxidation ability towards the dye molecules and result in the formation of the less reactive SO5˙− radical (eqn (29)). Despite the rate of reaction with SO4˙−, the rate of the scavenging reaction by HSO5− is less than that of the typical rate of SO4˙− attack on organic compounds.28 This shows that the optimum dose of PMS is required for the effective degradation of the dye. The mechanisms of the reactions are:
| Fe2+ + HSO5− → Fe3+ + SO4˙− + OH− | (25) |
| Fe3+ + HSO5− → Fe2+ + SO5˙− + H+ | (26) |
| Dye + SO4˙− → dye intermediates | (27) |
| Dye intermediates + SO4˙− → mineralization products + CO2 + H2O | (28) |
| HSO5− + SO4˙− → SO5˙− + SO42− + H+ | (29) |
3.4.2 Influence of HP concentration.
To investigate the role of the concentration of HP on the degradation of AB, the concentration of HP (CHP) was varied from 0.03 to 0.20 mM at CAB = 0.16 mM, CNaCl = 17 mM and pH 5. Fig. 7a shows the degradation efficiency as a function of Econ. The results indicate that the maximum degradation of AB notably improves from 44 to 68% when the HP concentration is increased from 0.03 to 0.13 mM. This enhancement of the degradation is a result of the increasing concentration of hydroxyl radicals (HO˙) with increasing concentration of HP, which may enhance the oxidation of the dye molecule (eqn (30)). However, on increasing the HP concentration further (>0.13 mM), the degradation efficiency decreased dramatically. Fig. 7b shows the change in degradation efficiency with variations in the concentration of HP. This clearly shows that the degradation efficiency is increased up to 0.13 mM HP and then is significantly decreased at concentrations >0.13 mM. This is because at higher HP concentrations hydroxyl radical scavenging forms the hydroperoxyl radical (HO˙2) (eqn (31) and (32)), which has a comparatively lower oxidation potential than that of HO˙.36 The possible reactions are: | Fe2+ + H2O2 → Fe3+ + HO˙ + OH− | (30) |
| Fe3+ + H2O2 → Fe2+ + HO˙2 + H+ | (31) |
| H2O2 + HO˙ → HO˙2 + H2O | (32) |
| Dye + HO˙ → dye intermediates | (33) |
| Dye intermediates + HO˙ → mineralization products + CO2 + H2O | (34) |
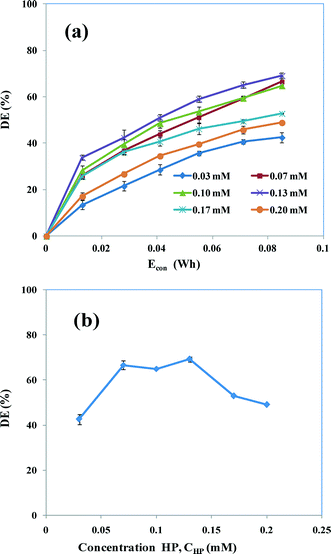 |
| Fig. 7 (a) Degradation efficiency of HP-assisted EC as a function of Econ in the presence of various concentrations of HP (0.03–0.2 mM). (b) Comparison of degradation efficiencies at 0.085 W h. CAB = 0.16 mM, CNaCl = 17 mM, current = 50 mA and pH 5. | |
3.4.3 Influence of PDS concentration.
To obtain a better understanding of the catalytic action of the electrochemically generated Fe2+ ion with PDS, the effect of the PDS concentration on the degradation of AB was evaluated by varying the concentration of PDS (CPDS) from 0.03 to 0.20 mM (Fig. 8a). The degradation efficiency increased with increasing PDS concentration up to 0.17 mM. On increasing the S2O82− concentration from 0.03 to 0.17 mM, a maximum AB degradation efficiency of 47–78% was achieved. This is because the Fe2+ species formed electrochemically catalyzes PDS to generate a reactive sulfate (SO4˙−) free radical (eqn (35)). The degree of formation of SO4˙− is increased with increasing concentrations of PDS.25,29 This high oxidation potential of SO4˙− efficiently decomposes the dye molecule and further develops the degradation. The possible reactions are: | S2O82− + 2Fe2+ → 2Fe3+ + 2SO4˙− | (35) |
| Fe2+ + SO4˙− → Fe3+ + SO42− | (36) |
| Dye + SO4˙− → dye intermediates | (37) |
| Dye intermediates + SO4˙− → mineralization products + CO2 + H2O | (38) |
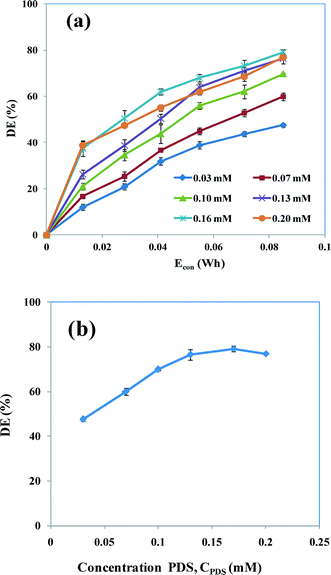 |
| Fig. 8 (a) Degradation efficiencies PDS-assisted EC as a function of Econ in the presence of various concentrations of PDS (0.03–0.2 mM). (b) Comparison of degradation efficiencies at 0.085 W h. CAB = 0.16 mM, CNaCl = 17 mM, current = 50 mA and pH 5. | |
Coincidently, the high oxidation potential of SO4˙− and the high reduction potential of Fe2+ may initiate an even stronger interaction between SO4˙− and electrochemically generated Fe2+ ions, which may decrease the rate of degradation (eqn (36)). In addition, the presence of a higher concentration of S2O82− increases the probability of collisions between S2O82− and Fe2+, which may increase the consumption of Fe2+ by S2O82−. Hence the lower number of SO4˙− radicals are quenched by Fe2+ ions, providing more opportunities to react with dye molecules, resulting in ameliorated degradation.25 The maximum degradation efficiency was studied by varying the PDS concentration (Fig. 8b). Fig. 8b clearly shows that the degradation efficiency was increased up to 0.17 mM PDS, but that the increase in degradation efficiency is insignificant at concentrations >0.17 mM. This is associated with the limited rate of radical formation as a result of the generation of a constant amount of Fe2+ (constant current), which tends to lower the oxidation activity of PDS. This result shows that the addition of excess oxidant has no positive effect on the degradation of the dye.
3.5 Influence of electrode materials
To examine the effect of the electrode materials on the degradation of the dye in oxidant-assisted EC, we carried out experiments with Fe and Al electrodes under the optimum conditions (CAB = 0.16 mM, CNaCl = 17 mM, CPMS = CPDS = 0. 17 mM, CHP = 0.13 mM, current = 50 mA and pH 5). Fig. 9a and b show the degradation efficiencies obtained for EC with Fe and Al electrodes, respectively. The maximum degradation efficiency of EC without oxidant is 51 and 35% for the Al and Fe electrodes, respectively. Hence the use of Al electrodes results in better removal of the dye than the use of Fe electrodes at pH 5. At pH 5–7, monomeric cationic species such as Al(OH)2+, Al(OH)2+ and Al(OH)3 may change to polymeric species such as Al2(OH)24+ and Al6(OH)153+. As a result of amorphism, the solubility of aluminum hydroxide is at a minimum at pH values between 5 and 8, although it dissolves at high pH values.37 Therefore most of the aluminum hydroxide precipitates, forming an aluminum coagulant that may accelerate coagulation; there are a number of reports claiming a higher rate of dye removal by EC with Al electrodes in acidic media.6 Although Al shows better dye removal, the electrode consumption is always higher for Al electrodes than for Fe electrodes because the anodic dissolution of Al3+ is favored in acidic media.38,39Fig. 9 shows that oxidant-assisted EC with an Al electrode gives a slight increase in dye degradation, but this effect is higher when an Fe electrode is used. This is because the electrochemically generated Fe2+/Fe3+ ions efficiently catalyze the oxidants with several different redox reactions, providing powerful oxidizing agents. This can speed up the destruction of the dye. However, a slight improvement in degradation efficiency has been observed for oxidant-assisted EC with Al electrodes as a result of the cathodic reduction of oxidant providing reactive radicals (eqn (11)–(14)).
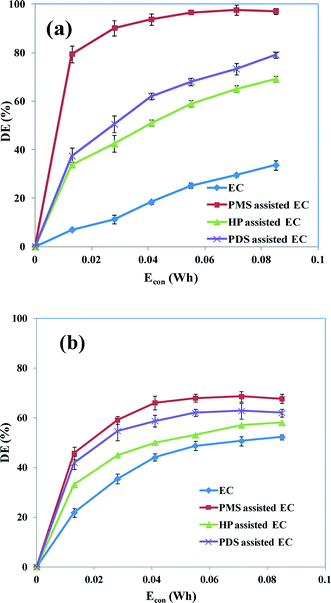 |
| Fig. 9 Degradation efficiencies as a function of Econ in EC and oxidant-assisted EC using (a) Fe and (b) Al electrodes. CAB = 0.16 mM, CNaCl = 17 mM, CPMS = CPDS = 0.17 mM, CHP = 0.13 mM, current = 50 mA and pH 5. | |
3.6 Comparison between degradation efficiency and mineralization efficiency
To determine the best oxidant addition to Fe for the degradation of AB, experiments were carried out under the optimum conditions (CAB = 0.16 mM, CNaCl = 17 mM, CPMS = CPDS = 0.17 mM, CHP = 0.13 mM and pH 5). Fig. 10a shows that the degradation efficiency is steadily increased during the initial stages of oxidant-assisted EC processes. By further increasing Econ by increasing the electrolysis time, the degradation efficiency is moderately increased. However, the degradation increases gradually (not rapidly) with increasing reaction time for EC without an oxidant. The reason for such dissimilarities in the efficiency of degradation is a result of the chemical oxidation of dye molecules by reactive species (SO4˙− and HO˙) in oxidant-assisted EC and the formation of Fe3+ hydroxo-complexes in EC in the absence of an oxidant. Specifically, PMS-assisted EC attained >99% degradation in a very short time. The PDS-assisted EC system showed a slightly better degradation efficiency than HP-assisted EC. This may be because HP allowed the increasing formation of HO˙, although the scavenging reaction of HO˙ is dominant, which may decrease the efficiency of dye degradation.
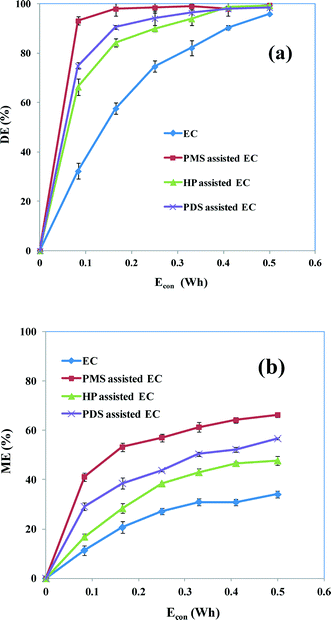 |
| Fig. 10 (a) Dye degradation efficiencies and (b) TOC reduction as a function of Econ by EC and oxidant-assisted EC. CAB = 0.16 mM, CNaCl = 17 mM, CPMS = CPDS = 0.17 mM, CHP = 0.13 mM, current = 50 mA and initial pH 5. | |
During the treatment process, the dye molecule was degraded and produced many intermediate products, some of which are more hazardous than the parent dye molecule. Hence the complete mineralization of the dye should mean that the process is more efficient. Even although there is rapid degradation (Fig. 10a), an increased Econ, obtained by increasing the electrolysis time, is required for the complete mineralization of the parent dye molecule. A TOC analysis was therefore carried out to determine the efficiency of the mineralization of AB by different EC processes. Fig. 10b shows the mineralization efficiency obtained as a function of Econ. PMS-assisted EC shows a maximum 66% reduction of TOC, which is appreciably higher than for the other EC processes. Apparent mineralization efficiencies of 34, 46 and 57% are obtained for EC, HP- and PDS-assisted EC, respectively. This result supports the view that PMS is the most efficient oxidant for the removal of AB dye by EC.
To confirm the mineralization process, the UV–visible spectral changes of the AB dye were measured at different electrolysis times in various EC processes. Fig. 11 and 12 show that, before EC, there is a broad peak at 618 nm in the visible region and two sharp peaks at 318 and 226 nm in the ultraviolet region. These correspond to the azo linkage (–N
N–), naphthalene group and aromatic ring, respectively (Table S2† gives the characteristics of the AB molecule), in which the chromophore peak at 618 nm is due to the absorption of the n → π* electronic transition associated with the –N
N– group. The UV peaks at 318 and 226 nm are attributed to the absorption of the π → π* transition related to the naphthalene and benzene rings.12 The peak at 618 nm decreases very rapidly and completely disappears in PMS-assisted EC. The intense peak also disappears gradually in other EC processes. These spectral changes suggest that rapid and complete degradation of AB has been achieved. The peaks at 318 and 226 nm also decrease slowly, but at a slower rate than the 618 nm peak, which ensures that the naphthalene and benzene moieties are also degraded. However, these two peaks are surprisingly retained after EC in both the absence and presence of an oxidant. This is because the removal of dye in this process is mainly due to an adsorption or charge neutralization mechanism and therefore the degradation of the dye molecule is unpredictable. Earlier reports found that azo dye degradation by EC with an Fe electrode takes place via minor pathways.40,41 It is evident that some organic intermediates are present in the residual solution for longer treatment times. This implies that a lower mineralization efficiency is attained as a result of the existence of byproducts similar to those at higher TOC concentrations, even for >99% degradation efficiency. For example, hydroxyl radicals and, perhaps, sulfate radicals interact with the nitrogen (azo group) via an electron transfer process. Consequently, decolorization occurs, but the aromatic rings are difficult to degrade with these radicals and are retained even for prolonged reaction times.
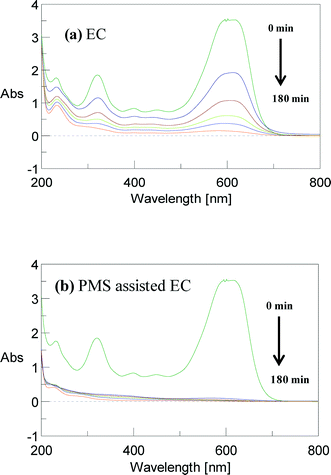 |
| Fig. 11 UV–visible spectra of AB dye observed at different electrolysis time with (a) EC and (b) PMS-assisted EC. CAB = 0.16 mM, CNaCl = 17 mM, CPMS = 0.17 mM, current = 50 mA and initial pH 5. | |
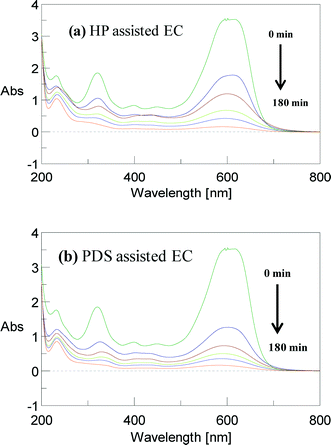 |
| Fig. 12 UV–visible spectra of AB dye observed at different electrolysis times for (a) HP-assisted EC and (b) PDS-assisted EC. CAB = 0.16 mM, CNaCl = 17 mM, CPDS = 0.17 mM, CHP = 0.13 mM, current = 50 mA and initial pH 5. | |
Conclusion
We investigated the effective degradation of AB dye by an EC process assisted by conventional oxidants (PMS, HP and PDS). The main operating parameters were optimized by EC using Fe electrodes; the degradation was strongly affected by process parameters such as the applied current, the initial solution pH and the oxidant concentration. The low applied current and acidic pH (pH 5) increased the efficiency of the oxidant-assisted EC process. In the absence of added oxidant, only 34% degradation was achieved by EC, although this degradation was significantly increased by oxidant-assisted EC processes. PMS-assisted EC gave a higher rate of degradation (99%) than PDS- and HP-assisted EC, which means that PMS is a more efficient oxidant addition for the removal of AB by EC. The degradation efficiency was compared with oxidant-assisted EC using Fe and Al electrodes. In the absence of added oxidant, higher degradation efficiencies were obtained by EC with Al electrodes than by EC with Fe electrodes. However, degradation of the dye with oxidant-assisted EC using Al electrodes was not significantly enhanced compared with Fe electrodes.
The TOC analysis implied that a lower mineralization efficiency was attained due to the existence of mineralized intermediate products at high TOC concentrations in the residual solution, even for greater than 99% degradation efficiency. The UV–visible spectral changes of AB in aqueous solution during the oxidant-assisted EC process were also studied. The azo linkage (–N
N–) was more easily degraded than the aromatic rings of the AB molecule by oxidant-assisted EC processes. Degradation efficiencies of 99% were achieved for EC assisted with PMS, HP and PDS at energy consumptions of 1.7, 4.1 and 3.3 W h (g dye)−1, respectively. Therefore oxidant-assisted EC is proposed as a suitable technique for the degradation of water contaminated with AB.
References
- T. Robinson, G. Mcmullan, R. Marchant and P. Nigam, Bioresour. Technol., 2001, 77, 247–255 CrossRef CAS.
- S. Ledakowicz, M. Solecka and R. Zylla, J. Biotechnol., 2001, 89, 175–184 CrossRef CAS.
- M. Zhou and J. He, Electrochim. Acta, 2007, 53, 1902–1910 CrossRef CAS PubMed.
- S. Raghu, C. Woo, S. Chellammal, S. Palanichamy and C. A. Basha, J. Hazard. Mater., 2009, 171, 748–754 CrossRef CAS PubMed.
- A. K. Verma, R. R. Dash and P. Bhunia, J. Environ. Manage., 2012, 93, 154–168 CrossRef CAS PubMed.
- V. Khandegar and A. K. Saroha, J. Environ. Manage., 2013, 128, 949–963 CrossRef CAS PubMed.
- M. M. Emamjomeh and M. Sivakumar, J. Environ. Manage., 2009, 90, 1663–1679 CrossRef CAS PubMed.
- J. R. Guimarães, M. G. Maniero and R. N. De Araújo, J. Environ. Manage., 2012, 110, 33–39 CrossRef PubMed.
- E. Brillas, I. Sire and M. A. Oturan, Chem. Rev., 2009, 109, 6570–6631 CrossRef CAS PubMed.
- P. V. Nidheesh and R. Gandhimathi, Desalination, 2012, 299, 1–15 CrossRef CAS PubMed.
- P. V. Nidheesh and R. Gandhimathi, Environ. Sci. Pollut. Res., 2013, 20, 2099–2132 CrossRef CAS PubMed.
- J. Sun, S. Sun, G. Wang and L. Qiao, Dyes Pigm., 2007, 74, 647–652 CrossRef CAS PubMed.
- K.-T. Kin, H.-S. Tang, S.-F. Chan, S. Raghavan and S. Martinez, IEEE Trans. Semicond. Manuf., 2006, 19, 208–215 CrossRef.
- A. Akyol, Sep. Purif. Technol., 2013, 112, 11–19 CrossRef CAS PubMed.
- S. Farhadi, B. Aminzadeh, A. Torabian, V. Khatibikamal and M. Alizadeh Fard, J. Hazard. Mater., 2012, 219–220, 35–42 CrossRef CAS PubMed.
- R. Daghrir and P. Drogui, Environ. Chem. Lett., 2013, 11, 151–156 CrossRef CAS.
- E. Yuksel, I. Sengil and M. Ozacar, J. Hazard. Mater., 2009, 152, 347–353 CAS.
- A. R. Khataee, V. Vatanpour, A. R. A. Ghadim and F. E. Only, J. Hazard. Mater., 2009, 161, 1225–1233 CrossRef CAS PubMed.
- O. Tu, I. Kabdas and T. Arslan, Water Sci. Technol., 2010, 61, 2005–2008 Search PubMed.
- G. Vasconcelos, D. M. Henriques, A. F. Martins and M. L. Wilde, Sep. Purif. Technol., 2006, 50, 249–255 CrossRef PubMed.
- G. Roa-morales, E. Campos-medina, J. Aguilera-cotero, B. Bilyeu and C. Barrera-d, Sep. Purif. Technol., 2007, 54, 124–129 CrossRef CAS PubMed.
- Ü. Tezcan Ün, S. Uğur, A. S. Koparal and Ü. Bakır Öğütveren, Sep. Purif. Technol., 2006, 52, 136–141 CrossRef PubMed.
- J. A. Davila, F. Machuca and N. Marrianga, Electrochim. Acta, 2011, 56, 7433–7436 CrossRef CAS PubMed.
- X. He, A. A. De and D. D. Dionysiou, J. Photochem. Photobiol., A, 2013, 251, 160–166 CrossRef CAS PubMed.
- X. Jiang, Y. Wu and P. Wang, Environ. Sci. Pollut. Res., 2013, 20, 4947–4953 CrossRef CAS PubMed.
- R. Yuan, S. N. Ramjaun, Z. Wang and J. Liu, J. Hazard. Mater., 2011, 196, 173–179 CrossRef CAS PubMed.
- S. Yang, P. Wang, X. Yang, L. Shan, W. Zhang, X. Shao and R. Niu, J. Hazard. Mater., 2010, 179, 552–558 CrossRef CAS PubMed.
- A. Rastogi, S. R. Al-abed and D. D. Dionysiou, Appl. Catal., B, 2009, 85, 171–179 CrossRef CAS PubMed.
- P. Nfodzo and H. Choi, Chem. Eng. J., 2011, 174, 629–634 CrossRef CAS PubMed.
- Y. Guan, J. Ma, Y. Ren, Y. Liu, J. Xiao, L. Lin and C. Zhang, Water Res., 2013, 3–10 Search PubMed.
- G. P. Anipsitakis and D. D. Dionysiou, Environ. Sci. Technol., 2004, 38, 3705–3712 CrossRef CAS.
- K. Govindan, M. Raja, M. Noel and E. J. James, J. Hazard. Mater., 2014, 272, 42–51 CrossRef CAS PubMed.
- K. Kin, H. Tang, S. Chan, S. Raghavan and S. Martinez, IEEE Trans. Semicond. Manuf., 2006, 19, 208–215 CrossRef.
- A. Akyol, O. Taner, E. Demirbas and M. Kobya, Sep. Purif. Technol., 2013, 112, 11–19 CrossRef CAS PubMed.
- S. Farhadi, B. Aminzadeh, A. Torabian, V. Khatibikamal and M. A. Fard, J. Hazard. Mater., 2012, 219–220, 35–42 CrossRef CAS PubMed.
- J. A. Davila, F. Machuca and N. Marrianga, Electrochim. Acta, 2011, 56, 7433–7436 CrossRef CAS PubMed.
- M. Ozacar, J. Hazard. Mater., 2009, 161, 1369–1376 CrossRef PubMed.
- C. Jime and M. A. Rodrigo, Environ. Sci. Technol., 2006, 40, 6418–6424 CrossRef.
- D. Lakshmanan and D. A. Clifford, Environ. Sci. Technol., 2009, 43, 3853–3859 CrossRef CAS.
- E. Pajootan, M. Arami and N. Mohammad, J. Taiwan Inst. Chem. Eng., 2012, 43, 282–290 CrossRef CAS PubMed.
- A. R. Amani-Ghadim, S. Aber, A. Olad and H. Ashassi-Sorkhabi, Chem. Eng. Process., 2013, 68–78 CrossRef CAS PubMed.
Footnote |
† Electronic supplementary information (ESI) available: A summary of a literature survey about HP-assisted EC process for wastewater treatment, the molecular properties of amido black 10B dye, and electrical energy consumption calculations are provided in the supporting information. See DOI: 10.1039/c4ew00030g |
|
This journal is © The Royal Society of Chemistry 2015 |
Click here to see how this site uses Cookies. View our privacy policy here.