Modified guar gum/SiO2: development and application of a novel hybrid nanocomposite as a flocculant for the treatment of wastewater†
Received
25th July 2014
, Accepted 16th October 2014
First published on 5th November 2014
Abstract
Using the sol gel process, a novel hybrid nanocomposite (g-GG/SiO2) has been developed in the authors' laboratory by grafting synthetic polyacrylamide chains on a guar gum backbone (g-GG) in the presence of microwave irradiation followed by in situ nanosilica incorporation on the surface of g-GG. Various characterization methods propose that g-GG promotes silica polymerization and probably acts as a template for nanoscale silica formation. Rheological characteristics indicate the gelling properties of the hybrid material. The application of the composite material in flocculation has been investigated on the laboratory scale as well as on the pilot scale. The flocculation kinetics and mechanism have been explained on the basis of pH of the suspension and flocculant dosage. Because of strong matrix–nanofiller interactions as well as enhanced molecular weight and hydrodynamic radius, the modified biopolymer-based nanocomposite provides excellent potential as a flocculant for the treatment of various synthetic and industrial effluents through a green disposal technique.
Water impact
Wastewater generated from various industrial sources exhibits a wide range of toxic suspended particles, coloured wastes and chemical and microbiological contaminants. With the development of a modified biopolymer-based nanocomposite, it is possible to reduce the toxicity level of wastewater. Our work aims at the development and application of a novel modified biopolymer-based nanocomposite, which represents an outstanding contribution for sustainable development in the treatment and recovery of industrial chemical wastes. In comparison to existing systems, the guar gum–silica nanocomposite combines superior flocculation capacity, which improves the performance beyond the state of the art reported in the literature. Here, the synergistic properties between nanosilica filler and modified guar gum matrix contribute a significant technological development for water treatment and sustainability towards the environmental viewpoint.
|
Introduction
Recently, several efforts have been made to synthesize polymeric nanocomposites for their different applications.1,2 The sol–gel process is one of the most effective techniques to develop the nanoscale inorganic framework on the surface of natural/modified natural polymers.3 The strong synergistic effect between inorganic nanofiller and modified polysaccharide matrix generates hybrid composite materials with remarkable improvement of mechanical, thermal and surface properties compared to the individual components.4 Because of the interesting properties of hybrid nanocomposite materials, in recent years they have been extensively used for the treatment and remediation of industrial wastewater.5
The direct disposal of industrial wastewater without appropriate treatment contaminates the water bodies with toxic elements which are extremely harmful towards aquatic species and human health.6 Therefore, to reduce the toxicity level of wastewater as well as for the possible industrial reuse of treated wastewater, the separation of suspended solids along with other chemical and microbiological contaminants from the aqueous environment is extremely important in the field of wastewater management.7,8 There are various wastewater treatment methods such as flocculation, precipitation, evaporation, and adsorption. Among these, flocculation is an economical and efficient technique for purification and recycling of industrial effluents.9
Both inorganic and organic (synthetic and natural polymers) flocculants have been used for treatment of industrial effluents.7,10 However, these flocculants have some advantages as well as limitations.11 Of late, various synthetic/modified natural polymer-based flocculants have been developed and reported, in particular by grafting synthetic polymer chains onto a natural polymer backbone, which surpassed the flocculation efficacy of commercial flocculants.12–15 Out of various graft copolymerization techniques, the microwave irradiation-based grafting technique has reformed the field of sustainable green chemistry by reducing the consumption of non-renewable resources and organic solvents as well as condensing the formation of toxic by-products. This process improves the reaction rate and grafting yields.16,17 Thus this process is also cost-effective and energy efficient. The electromagnetic irradiation selectively excites the polar bonds compared to the non-polar bonds of polysaccharides, which results in the cleavage/breakage of the polar bonds. This would generate free radical sites for grafting on the polysaccharide backbone without rupture of the polysaccharide C–C backbone and therefore enhances the product selectivity in comparison to conventional chemical grafting methods.18,19
The use of graft copolymers as flocculants has certain limitations such as lower hydrodynamic volume, low radius of gyration, poor thermal stability and low surface area. However, there are strategies to overcome these limitations, in particular by incorporating nanoscale inorganic fillers on the surface of the polymer matrix, which enhance its radius of gyration, thermal stability as well as surface area, all of which are sought for in an efficient flocculant.20 Monodisperse silica nanoparticles have been used extensively as potential surface-modifiers owing to their uniform size, shape, composition and high specific surface area.21 Additionally, hydrogen bonding units of polysaccharides might operate as nucleating centres for silica generation and consequently act as an efficient template for the growth of nanoscale silica particles.22
In view of the selective excitation properties of the microwave irradiation technique as well as considering the synergistic effect of composite hybrid materials, herein, we report for the first time the development and application of a novel nanocomposite-based flocculant for the treatment of synthetic and industrial wastewater, which was derived from guar gum, polyacrylamide and silica nanoparticles (g-GG/SiO2). Guar gum (GG) is a galactomannan extracted from the seed of the leguminous shrub Cyamopsis tetragonoloba and consists of a (1, 4)-linked-β-D-mannopyranose main chain with a branched α-D-galactopyranose unit at the 6-position. GG was chosen as the base polysaccharide due to its easy availability, low cost and nontoxic nature.23
Our work aims at the efficient separation of toxic contaminants from synthetic and industrial wastewater using a novel natural polymer-based nanocomposite flocculant. In comparison to existing systems, the guar gum–silica nanocomposite combines superior flocculation capacity. In addition to providing insight into the mechanism and kinetic aspects of the flocculation phenomenon, our paper represents the first report on a nanocomposite derived from grafted guar gum (synthesised by microwave irradiation) and SiO2 nanoparticles, and the synthetic strategy can be generalized for the synthesis of other functional nanocomposite materials. Besides, the g-GG acts as an efficient template for the controlled and homogeneous growth and distribution of nanoscale silica particles, which is obvious from HRTEM analysis. Significantly higher grafting efficiency of the microwave synthesized product as well as the involvement of strong synergistic effect between silica particles and copolymer matrix, the hydrodynamic radius, hydrodynamic volume and molecular weight were enhanced drastically. Also it is likely that higher hydrodynamic radius and hydrodynamic volume of g-GG/SiO2 are extremely important for the separation of fine solid contaminants from wastewater. The nanocomposite obtained shows rapid and excellent flocculation efficiency for the treatment of various industrial wastewater. It is therefore expected to be a powerful alternative to the literature known flocculants for the separation of toxic contaminants from aqueous industrial wastes.
Experimental
Chemicals
Guar gum (a gift sample from Hindustan Gum & Chemicals Ltd., Bhiwani, Haryana, India), tetraethylorthosilicate (98% TEOS, Sigma-Aldrich, USA), acrylamide (Merck, India), ammonium hydroxide (30% NH3, Merck), ethanol (99.9% pure, Merck), acetone (SD Fine Chemicals, India), and potassium persulphate (Qualigens Fine Chemicals, India) were of analytical grade and used as received.
Fe ore and Mn ore were used as received from Tata Steel, Jamshedpur. For all of the experiments, double-distilled water was used.
Synthesis of g-GG
The microwave-assisted grafting technique was employed to synthesize g-GG. The grafting reaction proceeded using potassium persulphate (KPS) as the free radical initiator in the presence of microwave irradiation.
In a typical synthetic procedure, 1.0 g of GG was slowly dissolved in 85 mL of distilled water. Separately, 10 mL of acrylamide (0.175–0.245 moles) and 5 mL of KPS (1.85 × 10−5–3.70 × 10−5 moles) solutions were mixed with the GG solution. An electronic thermometer was inserted in the reaction vessel with an alarm set at 70 °C. The grafting reaction was continued in the presence of microwave irradiation (25 L LG microwave oven, model MH-6549QS) of 900 W at 70 °C for the desired time. Nitrogen gas was purged throughout the reaction time. After completion of the grafting reaction, saturated hydroquinone solution was used to terminate the radical polymerization. The reaction mixture was cooled with ice-cold water. The product was precipitated with 250 mL of acetone.
The homopolymer (polyacrylamide) was removed from the mixture of g-GG and PAM by washing with 1
:
1 formamide and acetic acid. Finally, the pure g-GG was dried in a hot air oven at 60 °C for 6 h. By varying the reaction parameters (such as irradiation time, initiator concentration and monomer concentration), various grades of g-GG were synthesized, details of which are reported in Table 1. The optimized grade (g-GG 7) was considered with respect to its higher percentage of grafting efficiency (% GE), intrinsic viscosity, and hydrodynamic radius as well as higher molecular weight.
Table 1 Synthesis details, intrinsic viscosity (IV), RH, molecular weight and PDI of GG, g-GGs and nanocomposites
Polymer |
MWI time (s) |
KPS conc. (mol × 10−5) |
AAm conc. (mol) |
% GE |
IV (dL g−1) |
R
H (nm) |
M
n (g mol−1 × 105) |
M
w (g mol−1 × 106) |
PDI |
GG |
— |
— |
— |
— |
5.8 |
5.7 |
19.5 |
0.19 |
1.01 |
g-GG 1 |
150 |
1.85 |
0.17 |
29.8 |
9.9 |
12.6 |
8.71 |
1.06 |
1.22 |
g-GG 2 |
180 |
1.85 |
0.17 |
54.8 |
13.4 |
16.2 |
17.7 |
2.18 |
1.24 |
g-GG 3 |
210 |
1.85 |
0.17 |
52.0 |
11.7 |
15.2 |
10.4 |
1.33 |
1.28 |
g-GG 4 |
240 |
1.85 |
0.17 |
38.3 |
10.1 |
13.7 |
8.77 |
1.12 |
1.27 |
g-GG 5 |
180 |
2.77 |
0.17 |
47.1 |
11.3 |
14.8 |
9.28 |
1.10 |
1.19 |
g-GG 6 |
180 |
3.70 |
0.17 |
42.2 |
11.1 |
14.1 |
9.13 |
1.09 |
1.19 |
g-GG 7 |
180 |
1.85 |
0.21 |
56.8 |
13.7 |
16.9 |
12.4 |
1.69 |
1.36 |
g-GG 8 |
180 |
1.85 |
0.25 |
44.2 |
13.2 |
15.8 |
11.0 |
1.41 |
1.28 |
Nanocomposite |
TEOS (mL) |
EtOH, 12 N NH4OH and time |
% Conv. |
IV (dL g−1) |
R
H (nm) |
M
n (× 106 g mol−1) |
M
w (× 106 g mol−1) |
PDI |
g-GG/SiO2-1 |
1.0 |
|
81.2 |
40.9 |
24.2 |
2.05 |
2.44 |
1.18 |
g-GG/SiO2-2 |
1.5 |
5 mL, |
86.4 |
43.3 |
25.2 |
2.26 |
3.32 |
1.47 |
g-GG/SiO2-3 |
2.0 |
3 mL, |
91.2 |
47.9 |
26.9 |
3.08 |
4.12 |
1.34 |
g-GG/SiO2-4 |
2.5 |
12 h |
88.6 |
45.7 |
25.8 |
2.79 |
3.97 |
1.42 |
Synthesis of the g-GG/SiO2 hybrid nanocomposite
The hybrid nanocomposite was synthesized by incorporating nanoscale silica particles in situ (using the Stöber method)24 on the surface of g-GG 7 through the sol–gel method, by alkaline hydrolysis followed by condensation of TEOS. The reaction procedure is given below.
1 g of g-GG 7 was dissolved in 100 mL of distilled water with constant stirring (500 rpm) at 70 °C. Separately in another beaker, a required amount of TEOS was dissolved in 5 mL of ethanol. 2 mL of 12 N NH4OH solution was prepared separately. Then at 70 °C temperature, these two solutions were added quickly into the g-GG solution with continuous stirring at 500 rpm. The reaction was continued up to 12 h. At the end of the reaction, the mixture was kept overnight and then precipitated using 250 mL of acetone solution. The hybrid material was dried to a constant weight at 60 °C in a hot air oven. The hydrolysis and condensation of the silica precursor in the presence of ammonia occurred in the following way:
Si(OEt)4 + 4H2O → Si(OH)4 + 4EtOH |
By changing the TEOS concentration, four grades of nanocomposites were synthesized and the best one was optimized with respect to its higher % conversion, intrinsic viscosity, and hydrodynamic radius as well as higher molecular weight (see Table 1).
Characterization
Intrinsic viscosities of GG, g-GG and g-GG/SiO2 were analysed using an Ubbelohde viscometer in 1 M sodium nitrate solution. The hydrodynamic radius was determined using a Zetasizer Nano ZS (Malvern, UK). C, H, N analyses were performed using an elemental analyzer (Perkin Elmer, Series-II, C H N S/O analyzer-2400). FTIR spectra were recorded using the KBr pellet method (Model IR-Perkin Elmer, Spectrum 2000). EDAX analysis and surface morphologies were carried out by field emission scanning electron microscopy (FESEM Supra 55, Zeiss, Germany) and high-resolution transmission electron microscopy (HRTEM, Model: JEM 2100, JEOL, Japan). The molecular weight and molecular weight distribution were determined using a GPC system (Model 2414; Waters (I) Pvt. Ltd., USA). For GPC analysis, the flow rate was fixed at 0.6 mL min−1 and at 30 °C column temperature.
Analysis of rheological properties
A pH 7.4 buffer solution was used to investigate the rheological behaviour of 1 wt% of GG, g-GG 7 and g-GG/SiO2 nanocomposites at 37 ± 1 °C using a Bohlin Gemini-2 rheometer (Malvern, UK). The storage modulus (G′) and loss modulus (G′′) were measured at a constant frequency of 0.5 Hz and different shear stresses ranging from 0 to 1000 Pa. Frequency sweep measurements were carried out in the frequency range of 0.1 to 10 Hz at a constant stress of 1 Pa. Besides, shear viscosity was evaluated at different shear rate regions.
Investigation of flocculation characteristics
Flocculation characteristics using synthetic wastewater.
The flocculation efficiency of GG, g-GG, g-GG/SiO2 nanocomposites and commercial flocculants was determined using settling and jar tests. To explain the flocculation mechanism and kinetics, two different synthetic effluents (Fe ore and Mn ore) were used. The flocculation characteristics were studied at different pH (acidic, neutral and basic) levels. Additionally, the zeta potential of the suspensions (before and after treatment) was measured using a Zetasizer Nano ZS. The floc size was determined by DLS analysis (Zeta Sizer Nano ZS). The details of the experimental procedure of jar and settling tests are explained in the ESI.†
Flocculation kinetic study.
1 wt% Fe ore/Mn ore suspensions (400 mL) of pH 9 were placed into a 1 L beaker. A required amount of the flocculant was added to the suspension and the flocculator was rotated at a constant speed of 100 rpm for 5 min. At predetermined time intervals, a constant volume of the supernatant was withdrawn, dried and weighed.
Flocculation characteristics using industrial wastewater.
Treatment of paper effluent.
The flocculation characteristics of GG, g-GG, g-GG/SiO2 and commercial flocculants were investigated for the treatment of paper industry effluent using 9 ppm flocculant dosage with 200 mL of the effluent. The treated effluent was analysed for the measurement of turbidity, total solids (TS), total dissolved solids (TDS), and total suspended solids (TSS) by standard chemical/environmental analysis. The concentration of various metal ions present (Zn2+, Pb2+, Fe3+) in the treated and untreated effluent was measured using an atomic absorption spectrophotometer (Thermo Scientific-ICE 3000 Series AA spectrometer).
Treatment of textile wastewater.
Various laboratory-developed flocculants as well as commercial flocculants were used to evaluate the % colour removal efficiency of textile effluent using 9 ppm flocculant dosage. After suitable treatment, the supernatant was collected and the colour of the treated and untreated textile effluent was determined using a UV-Visible spectrophotometer (Shimadzu, Model:UV 1800).
Treatment of mine process water on the pilot scale.
Pilot plant studies as well as laboratory-scale studies were performed for the treatment of mine process water using various flocculants developed under study in an iron ore beneficiation plant of Tata Steel, Jamshedpur, India. The pilot plant consists of a raw wastewater tank (height (H): 2.25 m, and diameter (D): 1.15 m), a flocculant preparation tank (H: 0.75 m, D: 0.35 m), a triple-coagulated sedimentation tank (H: 1.75 m, D: 1.5 m), a clear-water tank, a pump, a valve and a mechanical agitator (Fig. 1). The optimized quantity of the flocculant was added to the raw mine process water (1000 L) and stirred with an agitator for effective mixing of flocculant and wastewater. The details of experimental parameters are flocculant dosage: 9 ppm, agitation time: 15 min, and agitation speed: 75 rpm. At the end of the experiment, the flocculated particles settled down at the bottom of the thickener and the clear overflow water was collected in a separate water tank. Finally, the supernatant water was analysed for TS, TDS, TSS, turbidity measurements and metal ion concentrations. Each test was repeated and the average values are presented here.
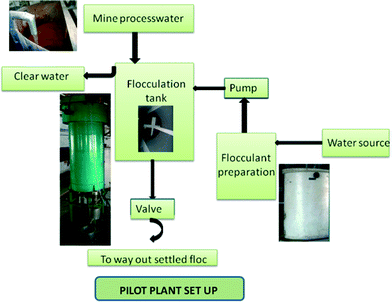 |
| Fig. 1 Flow chart of the pilot plant setup. | |
Results and discussion
Synthesis
Synthesis of g-GG.
g-GG was synthesized using an MWI-assisted technique where KPS was used as the initiator. It was presumed that initially the dielectric heating of the reaction medium at hot spot regions originates from rapid decomposition of peroxydisulphate into sulphate ion radicals (SO4−˙) as shown in Scheme 1. Subsequently, in the presence of electromagnetic irradiation, the radical extracts the H atom of the polar O–H bonds of GG (without rupture of the nonpolar C–C bond of the polysaccharide) to produce macroradicals, i.e. “selective excitation” of polar bonds took place. These macroradicals further react with the acrylamide monomer to initiate the grafting and propagate through the free radical polymerization technique. Finally, the graft copolymerization reaction was terminated using a saturated solution of hydroquinone as schematically represented in Scheme 1. Besides, the rate of the reaction as well as % GE of the graft copolymer synthesized using the microwave irradiation technique is higher due to the special effects of microwave irradiation of lowering Gibbs free energy of activation of the reaction,19 which originates from the differences in the dielectric constants of the reactants, radical intermediate and solvent water. By varying the reaction parameters, various grades of graft copolymers were synthesized. The optimized one was considered through its higher % GE, intrinsic viscosity, and higher hydrodynamic radius (Table 1) as well as higher molecular weight.
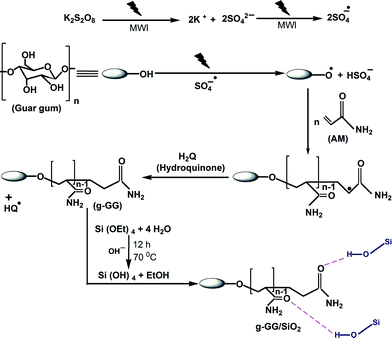 |
| Scheme 1 Schematic representation of the synthesis of g-GG/SiO2 nanocomposites. | |
Synthesis of the g-GG/SiO2 hybrid nanocomposite.
The preparation of the g-GG/SiO2 nanocomposite consists of the following steps: first, hydrolysis of the silica precursor (TEOS) followed by condensation of the formed monomer (silanols) to fabricate oligomers assembled as sol particles and, finally, cross-linking of the sol particles, which lead to the sol–gel transition in the presence of homogeneous ethanolic medium and NH4OH catalyst. The precursor medium accelerated the sol–gel process in the presence of the graft copolymer. Here, it is probable that the g-GG matrix acts as a template for the nucleation and growth of the SiO2 shell due to the hydrogen bonding interactions between the –CONH2 groups of the copolymer surface and the hydroxyl groups of silanols as shown in Scheme 1. In the presence of g-GG, the silanol groups can be further hydrolyzed and may participate in the polycondensation reaction to generate a nanoscale inorganic framework on the surface of the polymer matrix. Thus, it is believed that g-GG promotes silica polymerization through acceleration and catalysis of the sol–gel process.
Characterization
Intrinsic viscosity.
It is apparent from Table 1 that intrinsic viscosities of g-GG are higher than that of the polysaccharide. This is mainly due to the grafted polyacrylamide chains present on the GG backbone. In the case of g-GG 7, because of its higher % GE, the intrinsic viscosity was found to be maximum when compared to other graft copolymers. Besides, after incorporation of silica nanoparticles on the g-GG surface, an increase in viscosity was obvious (Table 1) due to the H-bonding interactions between the active sites of modified GG and silanol groups as proposed in Scheme 1. Further, the better distribution of nanofillers in the polymer surface is the key factor for the maximum intrinsic viscosity of the g-GG/SiO2-3 nanocomposite (Table 1).
Hydrodynamic radius (RH).
It was found that by grafting of PAAm chains on the GG backbone, the RH value increased (Table 1). This is because of the presence of grafted PAAm chains on polysaccharide segments. Also, g-GG 7 exhibits the highest RH out of various graft copolymers (Table 1), mainly owing to its higher % GE, i.e. the presence of longer PAAm chains. However, with nanofiller incorporation, the further rise in RH indicates the matrix–filler interaction, which was found to be highest for g-GG/SiO2-3 (Table 1).
Molecular weight.
The molecular weight and polydispersity index (PDI) of GG, g-GGs and nanocomposites were determined using GPC analysis (Table 1 and Fig. S1–S2, ESI†). All graft copolymers showed a higher molecular weight than GG, which is due to the presence of grafted PAAm chains. All the nanocomposites have a relatively high molecular weight mainly because of the presence of silica particles on the surface of g-GG. The nanocomposite g-GG/SiO2-3 showed a maximum molecular weight owing to the better interactions between the filler and the matrix.
CHN analysis.
Elemental analysis results (Table S1, ESI†) demonstrate that there is a considerable amount of nitrogen content in g-GG 7 as well as in composite material. This indicates the presence of PAAm chains on the GG backbone. Further, by comparing % O, it is obvious that the g-GG/SiO2-3 nanocomposite has higher % O (Table S1†). This signifies the presence of silanol –OH groups on the nanocomposite material.
FTIR spectroscopy.
The FTIR spectrum of GG (Fig. 2a) showed a broad peak at 3442 cm−1, which corresponds to stretching vibrations of –OH groups, and a sharp peak at 2915 cm−1 is attributed to C–H stretching vibrations. The bands at 1012 cm−1 and 920 cm−1 are responsible for C–O–C stretching vibrations. The FTIR spectrum of g-GG 7 (Fig. 2b) indicates the presence of a few additional peaks in comparison with that of GG. The peaks at 1657 cm−1 and 1570 cm−1 are responsible for amide-I and amide-II, respectively. The peak at 1432 cm−1 is attributed to C–N stretching vibrations. The presence of these additional peaks suggests the grafting of PAAm chains on the GG backbone. In the case of the FTIR spectrum of the g-GG/SiO2-3 nanocomposite (Fig. 2c), the sharp peak at 3758 cm−1 is due to the silanol –OH groups. Additionally, the peaks at 1112 cm−1 and 1015 cm−1 are assigned to Si–O–Si and Si–OH linkages, respectively, which confirmed the presence of SiO2 particles on the nanocomposite material.
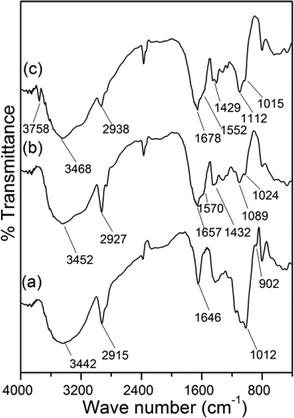 |
| Fig. 2 FTIR spectra of (a) GG, (b) g-GG 7, and (c) g-GG/SiO2-3 nanocomposites. | |
FE-SEM & EDAX analysis.
The FE-SEM image of GG (Fig. 3a) displayed an irregular particle/granular morphology. After grafting, the particle/granular appearance of GG was distorted and converted to interrelated three-dimensional networks of fibrillar morphology (Fig. 3b) owing to the random agglomeration of longer flexible PAAm chains present on the GG backbone. The FE-SEM image of the g-GG/SiO2-3 nanocomposite (Fig. 3c) shows that smaller, spherical white silica nanoparticles are well distributed throughout the surface of g-GG. This suggests that SiO2 nanoparticles are well embedded on the surface of the copolymer.
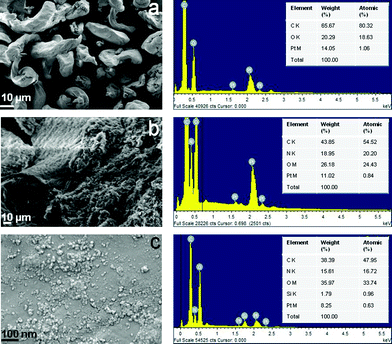 |
| Fig. 3 FESEM and EDAX analyses of (a) GG, (b) g-GG 7, and (c) g-GG/SiO2-3 nanocomposites. | |
Further, the presence of N in the graft copolymer and the presence of silica in the nanocomposite were confirmed by EDAX analysis (Fig. 3).
HRTEM and SAED analysis.
The HRTEM image (Fig. 4a) of the g-GG/SiO2-3 nanocomposite demonstrates the uniform distribution of very small (with diameters ranging from 6 to 18 nm) spherical silica nanoparticles throughout the surface of g-GG (also obvious from the histogram of particle size distribution, Fig. 4b). Besides, it is also observed that with an increase in concentration of the silica precursor, i.e. g-GG/SiO2-4, no aggregation of silica particles was observed (see Fig. S3, ESI†). This phenomenon signifies that during in situ synthesis of nanocomposites via the sol–gel method, polyfunctionality as well as structural organization of g-GG (H-bonding interaction sites of –CONH2 groups) serves as a template for synthesizing nanoscale silica components. G-GG also restricts the growth of silica particles by controlling the polycondensation of silanol monomers, which were formed during the hydrolysis of the TEOS precursor.
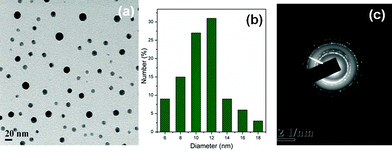 |
| Fig. 4 (a) HRTEM picture, (b) histogram and (c) SAED pattern of g-GG/SiO2-3. | |
The selected area electron diffraction pattern (SAED) of the g-GG/SiO2-3 nanocomposite (Fig. 4c) reveals a well-resolved set of concentric rings with bright spots, which indicates that the silica particles are nanocrystalline in nature.
Rheological characteristics
The rheological characteristics suggest that GG, g-GG 7 and the nanocomposites showed shear thinning behaviour (Fig. S4, ESI†). It is also apparent that all of the nanocomposites have higher shear viscosity than GG and g-GG 7 at both high and low shear rate regions (Fig. S4, ESI†). Since the nanocomposite materials are heterophase, the rise in solution viscosity obviously implies polymer matrix–nanofiller interaction, creating more restrained graft copolymer segments. However, maximum shear viscosity was demonstrated by g-GG/SiO2-3, confirming the maximum interactions at this composition compared to other hybrid composites. Further, the gel strength of all nanocomposites was investigated via frequency sweep and amplitude sweep oscillatory measurement within the linear visco-elastic regime through their respective storage (G′) and loss (G′′) moduli. Fig. S5 in the ESI† demonstrates the variation of storage and loss moduli with frequency (f). It was found that both G′ and G′′ are independent of frequency, which is a typical feature of gel structure.25Fig. 5 demonstrates the plot of G′ and G′′ vs. applied shear stress at a constant frequency of 0.5 Hz. At all shear stress values, G′ was found to be higher than G′′, suggesting the elastic nature of the nanocomposite. For all nanocomposites, it was observed that beyond the critical stress value (i.e. yield stress σy) both G′ and G′′ decline to a lower value, which signifies the flow behaviour of composite materials.25 Besides, it was found that g-GG/SiO2-3 has the maximum σy value (Table 2), which corroborates its highest mechanical strength than that of other composites. The better mechanical stability of g-GG/SiO2-3 is mainly because of the excellent matrix–filler interaction through H-bonding as proposed in Scheme 1.
 |
| Fig. 5
G′, G′′ vs. shear stress of (a) g-GG/SiO2-1, (b) g-GG/SiO2-2, (c) g-GG/SiO2-3, and (d) g-GG/SiO2-4 nanocomposites. | |
Table 2 Rheological properties of nanocomposites
Polymers |
Amplitude sweep |
Frequency sweep |
Yield stress (σy) (Pa) |
G′/G′′ |
G′/G′′ |
g-GG/SiO2-1 |
667 |
2.41 |
3.27 |
g-GG/SiO2-2 |
698 |
2.72 |
3.36 |
g-GG/SiO2-3 |
801 |
2.96 |
3.59 |
g-GG/SiO2-4 |
764 |
2.79 |
3.41 |
Flocculation characteristics
Flocculation behaviour in synthetic wastewater.
The flocculation characteristics of various flocculants (developed in the authors' laboratory as well as a couple of commercial flocculants, namely, FL920, non-ionic in nature, Mw 3.73 × 105 daltons; FL419, cationic in nature, Mw 2.39 × 105 daltons) were investigated in Fe ore/Mn ore suspensions under different pH conditions by carrying out settling tests (Fig. 6). Fig. 6 and Table S2 in the ESI† show that the flocculation efficacy at various pH is linearly related to the settling rate. It was observed that the decrease in the interface height was linear up to a certain height (i.e. until 20 cm), after which it was hindered. The initial settling rate was determined from the slope of the linear portion of settling curves. The settling rate of both suspensions with addition of different flocculants at acidic, neutral and alkaline environments is reported in Table S2 in the ESI.† The results (Fig. 6 and Table S2†) suggest that in both suspensions, g-GG 7 exhibited better flocculation characteristics than GG. This is because of the presence of dangling flexible synthetic polyacrylamide chains on the rigid polysaccharide backbone of the graft copolymer, which are able to come closer to the colloidal particles.26 Besides, the higher hydrodynamic volume, hydrodynamic radius and high molecular weight of g-GG 7 ensure its better flocculation ability in contrast to GG. However, the g-GG/SiO2-3 nanocomposite showed best flocculation characteristics than others including commercial flocculants. This is mainly because of the “synergistic effect” of modified GG matrix–silica nanofiller interactions through H-bonding in the case of the g-GG/SiO2-3 nanocomposite, which results in higher hydrodynamic volume, higher hydrodynamic radius (Table 1) and improved molecular weight (Table 1). Consequently, flocculation performance increased significantly. It is well known that most of the commercial flocculants are primarily linear in nature. In the case of linear polymers, the polymer fragments attach to the surface in trains, project into the solution as tails, or form a part of loops, which connect the trail together and can form bridges between the colloidal particles to form flocs.27,28 However, in the case of the nanocomposite, because of the branching nature as well as the presence of grafted polyacrylamide chains and the existence of the matrix–nanofiller interaction, the composite material would be able to form stronger bridging with colloidal particles to form larger flocs (floc size is reported in Table S2 in the ESI†). This type of bridging is not feasible in the case of linear commercial flocculants, and therefore the nanocomposite showed better flocculation efficacy compared to commercial flocculants. In addition, the higher hydrodynamic volume, RH and higher molecular weight are also responsible for better flocculation characteristics of g-GG/SiO2-3.
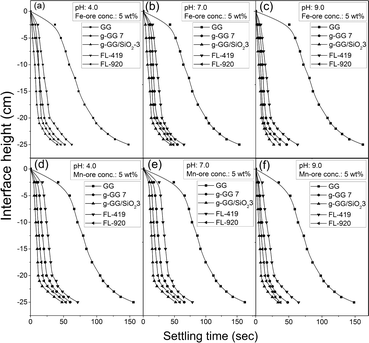 |
| Fig. 6 Settling characteristics of various flocculants in the Fe-ore suspension at (a) pH 4, (b) pH 7, (c) pH 9 and in the Mn-ore suspension at (d) pH 4, (e) pH 7, and (f) pH 9. | |
The flocculation characteristics were also studied in both Fe ore/Mn ore suspensions using jar test experiments (Fig. S6, ESI†). In a conventional jar test procedure (Fig. S6†), the correlation between flocculant doses and residual turbidity of the supernatant liquid was plotted. Obviously, it was found that g-GG/SiO2-3 showed the best flocculation characteristics. The correlation between flocculant dosage, residual turbidity and zeta potential of the treated suspensions using g-GG/SiO2-3 was plotted (Fig. 7). For both the suspensions under various pH conditions, the turbidity of the supernatant liquid is significantly high at low flocculant concentration. This is mainly because of the availability of insufficient flocculant molecules for bridging or charge neutralization. With an increase in flocculant concentration, more particles bridge together to form larger flocs, and hence the turbidity of the supernatant liquid decreased.29 On the contrary, above the optimum flocculant dosage, the residual turbidity of the supernatant liquid further increased due to the steric stabilization and electrostatic repulsion.30
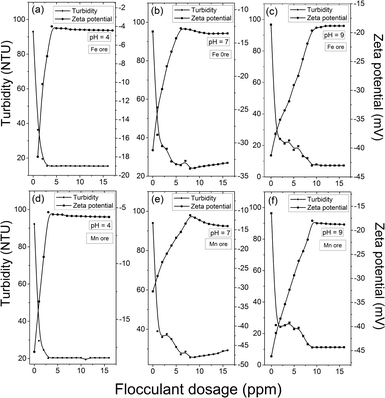 |
| Fig. 7 Variation of turbidity and ZP vs. flocculant dosage in the Fe ore suspension at (a) pH 4, (b) pH 7, (c) pH 9 and in the Mn-ore suspension at (d) pH 4, (e) pH 7, and (f) pH 9. | |
Fig. 6–7, S6 and Table S2† reveal that the efficiency of the g-GG/SiO2-3 nanocomposite as a flocculant (in terms of residual turbidity removal, higher settling rate and larger floc size) was superior in alkaline pH for both suspensions. This is because of the larger floc size as well as higher RH of the nanocomposite in alkaline pH compared to acidic or neutral pH (Table S2†). This indicates that polymer bridging plays an important role in effective flocculation.
Flocculation mechanism.
Flocculant concentrations and pH of the suspensions are two important parameters used to investigate the mechanism of a flocculation process. Therefore, the flocculation efficiency of g-GG/SiO2-3 has been investigated thoroughly by varying the polymer concentration as well as the pH of the synthetic effluents.
Fig. 7a and d demonstrate that at pH 4, the turbidity was reduced to 15.4 and 20.2 NTU with an optimum flocculant dosage of 3 ppm for Fe ore and Mn ore, respectively, beyond which the turbidity increased steadily. It has also been found that the zeta potential (ZP) of both suspensions is negative at the entire pH region (Fig. 7). In addition, point of zero charge (pzc) of g-GG/SiO2-3 was observed to be 4.48 (Fig. S7, ESI†). Hence, in an acidic environment, after addition of the flocculant, the magnitude of ZP of the suspensions decreased. This can be explained by the reverse charge effect between the flocculant and the synthetic suspensions.30 Moreover, in an acidic environment, due to the cationic surface charge of nanocomposites and the anionic nature of the suspensions, the charge neutralization mechanism is predominant. However, it is well known that flocs formed by the charge neutralization mechanism are relatively smaller in size.31 Here, the floc size has been found to be larger, suggesting that charge neutralization is not the only mechanism in the flocculation process.32 Besides, at pH <4.48 (pzc), the surface of the polymeric nanocomposite is positively charged, which would enhance the intra-chain electrostatic repulsion of the composite material.33 This would result in higher hydrodynamic radius (RH) (Table S2, ESI†) and better flocculation efficacy. At an acidic environment, the positive charges on the nanocomposite surface first create ‘island’ patches of charges enclosed with areas of opposite charges. Then the primary flocs, which are produced initially by the charge neutralization mechanism, are adsorbed on this in a “patchwise” manner so that oppositely charged particles of different regions may come into contact. This gives rise to strong electrostatic attraction and forms bigger flocs. Also, the better approachability of the nanocomposite towards the suspended particles makes the floc size bigger, indicating that the electrostatic patching mechanism plays a crucial role along with the charge neutralization mechanism.
At pH 7, the residual turbidity decreased sharply up to 25.7 NTU at 8 ppm flocculant dosage for Fe ore and 27.2 NTU with an optimum 8 ppm flocculant concentration for Mn ore, after which the turbidity was enhanced (Fig. 7b and e). At a neutral environment, due to the loss of surface charges, the grafted polyacrylamide chains present in the nanocomposite structure became close to each other, resulting in lower RH and less floc size compared to acidic conditions (Table S2, ESI†). Thus, the approachability of the nanocomposite material is reduced towards the contaminants, resulting in lower flocculation efficacy. Also, the magnitude of ZP decreased with increasing g-GG/SiO2-3 concentration (Fig. 7b and e). This phenomenon may be elucidated by the fact that the position of the shear plane shifts from the particle surface due to the adsorption of layers, since the surface charge of the nanocomposite is relatively lower.34
Under alkaline conditions (pH 9), the surface charge of the g-GG/SiO2-3 nanocomposite became highly negative (Fig. S7, ESI†). Therefore, the repulsive interactions between the grafted chains cause the copolymer structure to be more stretched and expanded, ensuring higher RH (Table S2, ESI†) and higher flocculation efficiency. This will enhance the flocculation efficiency (Fig. 7c, f). Consequently, the morphology of the polymeric chains becomes extensive, and more polymer loops and tails can be enlarged beyond the influence of the electric double layer repulsions.35 This results in the formation of stronger and larger flocs (Table S2, ESI†), which confirms that the bridging mechanism predominates. One of the crucial conditions for bridging flocculation is that there should be an adequate vacant space on the particle surface for adsorption of polymer chains. This experimental observation is also confirmed by the measurement of ZP values with flocculant doses (Fig. 7c, f). Here, the magnitude of ZP declined up to the optimum flocculant concentration, beyond which it was increased. The number of active binding sites present for effective bridging on the particle surface is higher at moderate flocculant concentrations than at lower concentrations. In contrast, in the over dosage region, steric stabilization occurs because of the higher surface coverage and strong electrostatic repulsions between the negatively charged surface of the nanocomposite and the colloidal particles. This will reduce the number of tails and loops available for bridging, and consequently, the magnitude of ZP was enhanced and the flocculation efficiency gradually declined.34
Flocculation kinetics.
Flocculation kinetics has been investigated to facilitate the relationship between the flocculation efficacy of a flocculant with dosage and time. Several factors such as mixing conditions, adsorption on the particles, re-conformation of the adsorbed polymers, collision efficiency and breakage of flocs are involved in the flocculation phenomenon.36 Since the lower residual turbidity as well as the better settling rate was found at pH 9, thus flocculation kinetics was performed under alkaline conditions.
Kinetics of aggregation of particles.
In the present study, Smoluchowski's classical model37 was used to determine the kinetics of flocculation, deflocculation and reflocculation processes. Here, two processes are simultaneously involved: the aggregation of particles with second-order kinetics and the aggregate breakage with first-order kinetics.36,37 The mathematical expression of the model is represented as: | 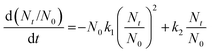 | (1) |
where N0 = number concentration of iron/manganese ore particles at t = 0, Nt = number concentration at time t, k1 = kinetic constant for aggregation of particles and k2 = kinetic constant for the aggregate breakage. This model is used to compare the kinetic constant of aggregation of particles and aggregate breakage at different initial concentrations. The correlation between both types of kinetic constants describes the equilibrium state of the flocculation process.
Fig. 8a–b show that maximum flocculation took place within the first 120 seconds after the addition of g-GG/SiO2-3. The rapid flocculation of the nanocomposite may be due to the fast aggregation of small particles initially, followed by aggregation of these particles through bridging to form larger flocs, resulting in faster settling. The values of the rate constants k1 and k2 were evaluated and are reported in Table S3 of the ESI.† It has been observed that with an increase in flocculant dosage from 3 to 9 ppm, the aggregation rate constant k1 increased and the aggregate breakage constant k2 decreased (Table S3, ESI†). This suggests that flocs formed at low flocculant concentration are soft in nature compared to those at high flocculant dosage.38 Beyond the optimum flocculant concentration (9 ppm), the aggregation rate constant k1 decreased while the aggregate k2 was enhanced. The phenomenon of lowering the flocculation efficacy beyond the optimum flocculant concentration may be explained by the coverage of maximum available active sites of g-GG/SiO2-3. However, in the over dosage region, the bridging mechanism is negligible because of the steric and electrostatic repulsions, which would result in the flocs to be destabilized in the suspension.34
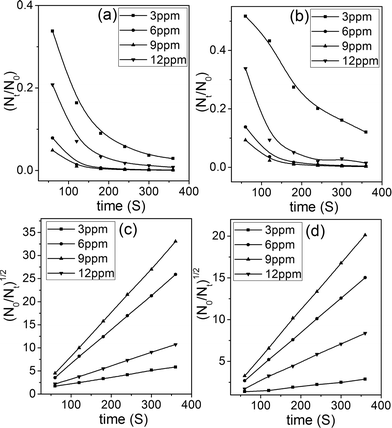 |
| Fig. 8 Kinetic curves of flocculation of (a) Fe ore and (b) Mn ore particles using g-GG/SiO2-3 as a flocculant at various initial concentrations and (N0/Nt)1/2 as a function of settling time at different initial concentrations of g-GG/SiO2-3 using (c) Fe ore and (d) Mn ore suspensions. | |
Frequency of collisions of particles.
Additionally, the particle collision model was investigated to assess the effect of dosage on the flocculation process. It was reported before that the order of flocculation is mainly bimolecular.36 The mathematical expression of the model is given as: | 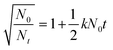 | (2) |
where N0 denotes the initial number concentration of Fe ore/Mn ore particles, Nt stands for the number concentration of the particles at time t, and k is the rate constant for collisions between the singlets. N0 values for a known weight (1 g) of Fe ore/Mn ore were calculated by considering the particle diameter (342 nm for Fe ore and 274 nm for Mn ore) and the density of ores (3.8 g cc−1 for iron and 7.2 g cc−1 for manganese). In contrast, the value of Nt was determined by knowing the weight of flocculated particles at specific time intervals. Here the hypothesis is based on the fact that the portion of the particles which did not flocculate is believed to be a singlet. Fig. 8c, d represent the plots of (N0/Nt)1/2vs. t having an intercept of 1 for the bimolecular process and from the slope data, the rate constant (k) was determined and is reported in Table S3 in the ESI.†
Experimental results demonstrate that with an increase in flocculant concentration, k increased. However, after the optimal dosage, it declined. It was further observed that under the optimum flocculant concentration, the linear correlation coefficient was significantly high (R2 > 0.99) (Table S3, ESI†) in comparison to other flocculant dosages, which suggests that the flocculation kinetics follows satisfactorily the flocculation model of the frequency of collisions of particles. Moreover, Table S3† illustrates that at low flocculant concentration, the rate constant was relatively low, but at the optimized flocculant dosage the rate constant sharply increased for both suspensions. This suggests that mainly molecular collision between polymeric nanocomposite and suspended particles took place at the optimum flocculant concentration.
Flocculation characteristics in industrial wastewater
Treatment of paper industry wastewater.
Wastewater from pulp and paper mills is a major cause of aquatic pollution as it contains a large amount of organic substances which generate high chemical oxygen demand (COD), chlorinated organic, toxic metal ions, suspended solids, and so on.39 Considering the adverse effects on aquatic biota and human health, primary treatment of paper industry effluent was performed using various flocculants. The results are reported in Table 3. It is obvious that g-GG/SiO2-3 showed tremendous potential for the reduction of turbidity, TS, TDS, TSS, and COD from paper effluent in comparison to GG, g-GG 7 and commercial flocculants. In addition, removal of various toxic metal ions such as Zn2+, Pb2+, and Fe3+ from paper effluent gives an overriding interest about the nanocomposite-based flocculant.
Table 3 Analysis results for treatment of paper industry effluent
Flocculant |
Turbidity (NTU) |
TS (ppm) |
TDS (ppm) |
TSS (ppm) |
COD (ppm) |
Fe3+ (ppb) |
Pb2+ (ppb) |
Zn2+ (ppb) |
Blank |
96 |
608 |
298 |
310 |
195 |
125 |
38 |
65 |
GG |
78 |
583 |
233 |
350 |
186 |
112 |
33 |
57 |
g-GG 7 |
24 |
312 |
217 |
95 |
136 |
45 |
17 |
16 |
g-GG/SiO2-3 |
15 |
246 |
177 |
69 |
99 |
17 |
12 |
10 |
FL-419 |
19 |
294 |
212 |
82 |
124 |
35 |
19 |
20 |
FL-920 |
17 |
281 |
205 |
76 |
118 |
26 |
23 |
19 |
Treatment of textile industry wastewater.
Effluent from textile industries consists of various kinds of dyes, which show very low biodegradability and high colour intensity due to their high molecular weight and complex chemical structures.40 Hence, before discharging this industrial effluent into water bodies or for possible industrial reuse, it is extremely crucial to remove its colour by using an eco-friendly technique. Since flocculation is an important method for removal of colour from industrial wastewater, we have tried to find out the suitability of the g-GG/SiO2-3 nanocomposite towards its efficacy to remove colour from real textile industry wastewater in our present study. Experimental studies (Fig. 9) reveal that the nanocomposite can be considered as a potential candidate for the removal of colour from textile effluent.
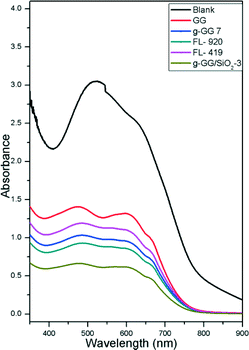 |
| Fig. 9 Comparative evaluation of colour removal capacity of various flocculants in textile wastewater. | |
Treatment of mine process water on the pilot scale.
In addition to the laboratory-scale study, the flocculation performance of mine process water was performed on the pilot scale using various flocculants to find out the effectiveness of different materials synthesised under study for real industrial applications.
The flow chart for the pilot plant is presented in Fig. 1. Table 4 shows that the g-GG/SiO2-3 nanocomposite significantly reduced the various pollutant contents (TS, TDS, TSS, and turbidity) and removed different metal ions (Mn2+, Fe3+, Ca2+ and Mg2+) from process water on the pilot scale. The experimental results of the pilot scale study were also verified with the investigation carried out on the laboratory scale. The results confirm that because of its higher hydrodynamic radius, molecular weight and superior polyfunctional characteristics, g-GG/SiO2-3 exhibits remarkable potential as a flocculant for real industrial applications.
Table 4 Analysis results for treatment of mine process water
Laboratory-scale treatment |
Flocculant |
Turbidity (NTU) |
TS (ppm) |
TDS (ppm) |
TSS (ppm) |
Mn2+ (ppm) |
Fe3+ (ppm) |
Ca2+ (ppm) |
Mg2+ (ppm) |
Blank |
92 |
208 |
98 |
110 |
0.84 |
2.4 |
29.9 |
16.7 |
GG |
68 |
182 |
81 |
99 |
0.74 |
1.8 |
26.3 |
14.8 |
g-GG 7 |
11.5 |
118 |
62 |
56 |
0.16 |
0.78 |
13.2 |
9.2 |
g-GG/SiO2-3 |
8.2 |
98 |
48 |
40 |
0.001 |
0.001 |
8.7 |
6.8 |
FL-920 |
12.5 |
126 |
69 |
57 |
0.27 |
0.92 |
15.6 |
11.3 |
FL-419 |
14.6 |
136 |
72 |
64 |
0.33 |
1.1 |
16.9 |
12.5 |
Pilot-scale treatment |
Blank |
98 |
274 |
112 |
162 |
1.1 |
2.4 |
33.4 |
20.1 |
GG |
76 |
252 |
102 |
150 |
0.92 |
1.6 |
29.5 |
18.3 |
g-GG 7 |
14.2 |
188 |
92 |
96 |
0.12 |
0.62 |
14.5 |
9.2 |
g-GG/SiO2-3 |
10.6 |
132 |
80 |
52 |
0.008 |
0.12 |
11.2 |
6.8 |
FL-920 |
15.2 |
194 |
94 |
100 |
0.14 |
0.76 |
15.2 |
11.6 |
FL-419 |
17.4 |
212 |
96 |
116 |
0.18 |
0.86 |
17.3 |
14.4 |
Conclusions
From the above experimental observations and discussion, it is apparent that grafting of synthetic polyacrylamide chains on the guar gum backbone through the eco-friendly microwave-assisted grafting method followed by the in situ insertion of silica nanoparticles via the sol–gel technique opens a new pathway in the field of hybrid composite materials. The “synergistic effect” between modified natural polymer and nanoscale filler, which originates from the uniform distribution of nanofillers on the copolymer surface, remarkably enhances the hydrodynamic radius, hydrodynamic volume and molecular weight of the nanocomposite, which shows excellent potential as a flocculant. The flocculation mechanism demonstrates that bridging is predominant under alkaline conditions, while the electrostatic and patching mechanism is dominant in an acidic environment. The flocculation capacity of g-GG/SiO2-3 is much higher in comparison to those of the other polymers/nanocomposites synthesised in this study and commercial flocculants for treatment of industrial effluents on the laboratory scale as well as on the pilot scale. Thus, the g-GG/SiO2 nanocomposite might be considered as a promising flocculant for the treatment of industrial wastewater.
Acknowledgements
Authors earnestly acknowledge financial support from the Department of Science & Technology, New Delhi, India, in the form of a research grant (No. DST/TM/WTI/2K12/67) to carry out the reported investigation.
References
- Z. H. Huang, X. Zheng, W. Lv, M. Wang, Q. H. Yang and F. Kang, Langmuir, 2011, 27, 7558 CrossRef CAS PubMed.
- S. Yang, J. Hu, C. Chen, D. Shao and X. Wang, Environ. Sci. Technol., 2011, 45, 362 CrossRef PubMed.
- S. Ghorai, A. Sarkar, M. Raoufi, A. B. Panda, H. Schönherr and S. Pal, ACS Appl. Mater. Interfaces, 2014, 6, 4766 CAS.
- V. Singh, A. Tiwari, S. Pandey, S. K. Singh and R. Sanghi, J. Appl. Polym. Sci., 2007, 104, 536 CrossRef CAS.
- V. Janaki, K. Vijayaraghavan, B. T. Oh and K. J. Lee, Carbohydr. Polym., 2012, 90, 1437 CrossRef CAS PubMed.
- T. Deblonde, C. Cossu-Leguille and P. Hartemann, Int. J. Hyg. Environ. Health, 2011, 214, 442 CrossRef CAS PubMed.
- A. K. Sarkar, N. R. Mandre, A. B. Panda and S. Pal, Carbohydr. Polym., 2013, 95, 753 CrossRef CAS PubMed.
- M. A. Montgomery and M. Elimelech, Environ. Sci. Technol., 2007, 41, 7 Search PubMed.
- T. M. König, S. Shulami and G. Rytwo, Appl. Clay Sci., 2012, 67, 119 CrossRef PubMed.
- K. E. Lee, N. Morad, T. T. Teng and B. T. Poh, Chem. Eng. J., 2012, 203, 370 CrossRef CAS PubMed.
- D. J. Joo, W. S. Shin, J. K. Choi, S. J. Choi, M. C. Kim, M. H. Han, T. W. Ha and Y. H. Kim, Dyes Pigm., 2007, 73, 59 CrossRef CAS PubMed.
- R. P. Singh, T. Tripathy, G. P. Karmakar, S. K. Rath, N. C. Karmakar, S. R. Pandey, K. Kannan, S. K. Jain and N. T. Lan, Curr. Sci., 2000, 78, 798 CAS.
- P. Adhikary, K. N. Tiwari and R. P. Singh, J. Appl. Polym. Sci., 2007, 103, 773 CrossRef CAS.
- R. Das, S. Ghorai and S. Pal, Chem. Eng. J., 2013, 229, 144 CrossRef CAS PubMed.
- R. P. Singh, B. R. Nayak, D. R. Biswal, T. Tripathy and K. Banik, Mater. Res. Innovations, 2003, 7, 331 CrossRef CAS.
- J. L. Tucker, Org. Process Res. Dev., 2010, 14, 328 CrossRef CAS.
- T. Erdmenger, C. Guerrero-Sanchez, J. Vitz, R. Hoogenboom and U. S. Schubert, Chem. Soc. Rev., 2010, 39, 3317–3333 RSC.
- F. Wiesbrock, R. Hoogenboom and U. S. Schubert, Macromol. Rapid Commun., 2004, 25, 1739 CrossRef CAS.
- S. A. Galema, Chem. Soc. Rev., 1997, 26, 233 RSC.
- S. Ghorai, A. Sinhamahpatra, A. Sarkar, A. B. Panda and S. Pal, Bioresour. Technol., 2012, 119, 181 CrossRef CAS PubMed.
- S. Pandey and S. B. Mishra, J. Sol-Gel Sci. Technol., 2011, 59, 73–94 CrossRef CAS PubMed.
- Y. A. Shchipunov and T. Y. Karpenko, Langmuir, 2004, 20, 3882–3887 CrossRef CAS.
- S. Pal, J. Appl. Polym. Sci., 2009, 111, 2630 CrossRef CAS.
- W. Stöber, A. Fink and E. Bohn, J. Colloid Interface Sci., 1968, 26, 62 CrossRef.
- A. Pal and J. Dey, Langmuir, 2011, 27, 3401 CrossRef CAS PubMed.
-
R. P. Singh, Advanced turbulent drag reducing and flocculating materials based on polysaccharides, in Polymers and Other Advanced Materials, ed. P. N. Prasad, J. E. Mark and T. J. Fai, Plenum Press, New York, 1995, pp. 227–249 Search PubMed.
- B. R. Nayak and R. P. Singh, J. Appl. Polym. Sci., 2001, 81, 1776 CrossRef CAS.
-
P. A. Rey and R. G. Varsanik, Application and Function of Synthetic Polymeric Flocculants in Wastewater Treatment, in Water Soluble Polymers: Beauty with Performances, ed. J. E. Glass, American Chemical Society, Washington, DC, 1986, p. 113 Search PubMed.
- M. Dash, R. K. Dwari, S. K. Biswal, P. S. R. Reddy, P. Chattopadhyay and B. K. Mishra, Chem. Eng. J., 2011, 173, 318 CrossRef CAS PubMed.
- Z. Yang, B. Yuan, X. Huang, J. Zhou, J. Cai, H. Yang, A. Li and R. Cheng, Water Res., 2012, 46, 107 CrossRef CAS PubMed.
-
T. Radeva, Physical Chemistry of Polyelectrolytes, Marcel Dekker Inc, New York, 2001 Search PubMed.
- Y. Zhou and G. V. Franks, Langmuir, 2006, 22, 6775 CrossRef CAS PubMed.
- P. Mpofu, J. A. Mensah and J. Ralston, J. Colloid Interface Sci., 2004, 271, 145 CrossRef CAS PubMed.
- V. Runkana, P. Somasundaran and P. C. Kapur, Chem. Eng. Sci., 2006, 61, 82 CrossRef PubMed.
- K. K. Das and P. Somasundaran, Colloids Surf., A, 2001, 182, 25 CrossRef CAS.
- Y. X. Chen, S. Y. Liu and G. Y. Wang, Chem. Eng. J., 2007, 133, 325 CrossRef CAS PubMed.
- M. Smoluchowski, Phys. Z., 1916, 17, 557 Search PubMed.
- S. Ghorai, A. Sarkar, A. B. Panda and S. Pal, Ind. Eng. Chem. Res., 2013, 52, 9731 CrossRef CAS.
- S. S. Wong, T. T. Teng, A. L. Ahmad, A. Zuhairi and G. Najafpour, J. Hazard. Mater., 2006, 135, 378 CrossRef CAS PubMed.
- A. K. Verma, R. R. Dash and P. Bhunia, J. Environ. Manage., 2012, 93, 154–168 CrossRef CAS PubMed.
Footnote |
† Electronic supplementary information (ESI) available: Details of settling test/jar test methods, GPC analysis results (Fig. S1 & S2), table of elemental analysis results (Table S1), HRTEM image of the g-GG/SiO2-4 nanocomposite (Fig. S3), rheological characteristics (Fig. S4 & S5), table of settling rate, floc size (Table S2), jar test results (Fig. S6), point of zero charge of the g-GG/SiO2-3 nanocomposite (Fig. S7), and parameters of flocculation kinetics (Table S3). See DOI: 10.1039/c4ew00023d |
|
This journal is © The Royal Society of Chemistry 2015 |
Click here to see how this site uses Cookies. View our privacy policy here.