DOI:
10.1039/C4RA11972J
(Paper)
RSC Adv., 2015,
5, 2405-2410
Ultrathin mesoporous NiCo2O4 nanosheets as an efficient and reusable catalyst for benzylic oxidation†
Received
8th October 2014
, Accepted 1st December 2014
First published on 1st December 2014
Abstract
Ultrathin mesoporous NiCo2O4 nanosheets as a high efficient and reusable catalyst for benzylic oxidation have been prepared. The nanosheets are less than 5 nm in thickness, the pore distribution is in the range of 2–5 nm and the specific surface area of the nanosheets is about 81.0 m2 g−1. The ultrathin and mesoporous features with high specific surface area not only provide large amount of binary active sites of Co and Ni, but also improve the contacting ability between the substrate and these active sites, therefore accelerating the rate of reaction and providing high catalytic efficiency for benzylic oxidation. The NiCo2O4 nanosheets are efficient heterogeneous catalyst in the oxidation of 4,4′-difluorodiphenylmethane into 4,4′-difluorobenzophenone with a yield of 99%. Furthermore, the NiCo2O4 nanosheets catalyst exhibits general applicability, convenient separability and good stability in the benzylic oxidation.
Introduction
Benzylic oxidation, as a representative of the oxidation of activated benzylic C–H groups, is one of the most helpful and significant transformations in organic chemistry, as generated ketones may act as valuable building blocks for the manufacture of pharmaceuticals and agrochemicals.1–3 The development of catalysts for benzylic oxidation has therefore attracted considerable interest. In the past decades, tremendous efforts had been devoted to transition-metal catalysts involving Cr,4,5 Mn,6,7 Bi,1 Cu,8 V,9,10 Rh,11 Au,12 and Fe13 for benzylic oxidation reactions. Bimetallic catalysts such as Au–Cu,14 Au–Pd,15,16 and Ag–Pd,17 particularly, may offer tunable catalytic properties with synergistic effect between the metallic moieties.18,19 However, such noble bimetallic catalysts are expensive with limited applications.
During the past few years, low-cost nickel-based and cobalt-based mono-metallic catalysts had also been explored for benzylic oxidation with considerable catalytic results.20,21 Herein, we reported the synthesis of mesoporous bimetallic oxide NiCo2O4 as an effective catalyst for benzylic oxidation. NiCo2O4 generally adapts a spinel structure in which nickel occupies the octahedral sites and cobalt is distributed over both octahedral and tetrahedral sites,22–24 affording multiple oxidation sites and excellent heat stability, which makes it as potentially excellent catalyst for benzylic oxidation. Although NiCo2O4 has been extensively studied for water splitting,25 batteries,26,27 and supercapacitors,28,29 its utilization as catalyst for benzylic oxidation was investigated scarcely. In this work, NiCo2O4 nanosheets with mesoporous structure and high specific surface area were synthesized using a facile low-temperature solution method, and their use as effective benzylic oxidation catalysts was demonstrated using various benzylic substrates such as benzylic methylenes, heteroaromatic benzylic compound and secondary benzylic alcohols. This work provided NiCo2O4 based materials as highly efficient, low-cost, reusable catalyst for benzylic oxidations.
Experimental
Materials
Ni(NO3)2·6H2O, Co(NO3)2·6H2O, hexamethylenetetramine, 70 wt% aqueous tert-butylhydroperoxide (THBP) and pyridine were purchased from Alfa Aesar. Ethyl alcohol and acetonitrile were provided from Beijing Chemical Reagents Company. NiO and Co3O4 power were also purchased from Alfa Aesar. All reagents were used as received without further purification.
Catalyst preparation
NiCo2O4 nanosheets were prepared according to previous research.29 In a typical procedure, Ni(NO3)2·6H2O (0.58 g, 2.0 mmol), Co(NO3)2·6H2O (1.16 g, 4.0 mmol) and hexamethylenetetramine (1.26 g, 9.0 mmol) were dissolved into a mixed solution of deionized water (80.0 mL) and ethyl alcohol (40.0 mL) to form a transparent pink solution. The solution was heated to 90 °C for 4 h, and then cooled down to room temperature. The product was washed with ethanol and deionized water several times, then dried under vacuum at 50 °C for 12 h. The powder annealed at 300 °C for 2 h under air with a heating rate of 1 °C min−1 to achieve mesoporous NiCo2O4 nanosheets.
Characterization and measurement
Field-emission scanning electron microscope (FESEM) images were observed by a ZEISS SUPRA55 operated at the accelerating voltages of 10 kV. High-resolution transmission electron microscope (HRTEM) images were obtained by a FEI Tecnai F20 operated at the accelerating voltages of 200 kV. Powder X-ray diffraction (XRD) patterns were recorded by a M21X diffractometer (MAC Science Co. Ltd., Japan) using a Cu Kα radiation (k = 1.541 Å) source at 40 kV and 200 mA. Fourier transform infrared (FTIR) spectra were acquired by a Nicolet 6700 using the potassium bromide (KBr) pellet technique. The thermal analysis (TG) was used to investigate the thermal decomposition behavior of the samples using Netzsch STA449F3 instrument at a heating rate of 5 °C min−1 under an air flow. Nitrogen adsorption–desorption isotherms were measured at 77 K with an AUTOSORB-1C analyzer (USA Quantachrome Instruments). The specific surface area was calculated with the Brunauer–Emmett–Teller (BET) method. The pore size distribution was derived from the adsorption branches of isotherms using the Barrett–Joyner–Halenda (BJH) model. The chemical compositions were analysed with an X-ray photoelectron spectrometer (XPS, ESCALAB 250Xi) and inductively coupled plasma-atomic emission spectrometry (ICP-AES, Vavian 715-ES).
Catalytic procedure
Oxidation of 4,4′-difluorodiphenylmethane (Scheme 1): a mixture of 4,4′-difluorodiphenylmethane (1 mmol), 70 wt% aqueous TBHP (3.0 mmol), additive and catalyst were added into acetonitrile (1.0 mL) in a 25 mL flask. The mixture was stirred at 90 °C for 24 h. After filtering the mixture, the filtrate was analyzed by Agilent 7890/5975C-GC/MS using nitrobenzene as internal standard.
 |
| Scheme 1 The conversion of 4,4′-difluorodiphenylmethane into 4,4′-difluorobenzophenone using the NiCo2O4 nanosheets as catalyst. | |
The leaching tests were performed by separating the catalyst at 8 h from the reaction mixture, the filtrate was stirred for a further 16 h. The reaction progress was monitored by GC as previously described.
The reusability of the catalyst was investigated. After completion of the reaction, the catalyst was filtered out and washed with acetonitrile for three times. Catalyst recovery was tested in the oxidation of 4,4′-difluorodiphenylmethane into 4,4′-difluorobenzophenone.
Results and discussion
Characterization
Typical morphology of NiCo2O4 nanosheets is shown in Fig. 1. It is obvious that the nanosheets are highly interconnected forming the three-dimensional nanosheets networks (Fig. 1a). TEM image clearly reveals that the ultrathin NiCo2O4 nanosheets are less than 5 nm in thickness and 500–1000 nm in length and width (Fig. 1b). Interestingly, HRTEM image (Fig. 1c) demonstrates that each ultrathin nanosheet consists of numerous interconnected nanoparticles and forms a mesoporous structure.28 The size of the mesopores is estimated to be in the range of 2–5 nm. The diffraction shown in the selected area electron diffraction (SAED) pattern (the inset of Fig. 1c) is indexed to (200), (311), (400), (420), (440) and (110) crystal planes of the spinel NiCo2O4, respectively. The HRTEM image in Fig. 1d clearly shows the polycrystalline nature of these nanosheets. The space between adjacent fringes of 0.28 nm and 0.24 nm (the inset of Fig. 1d) corresponds to the (220) and (311) lattice spaces of spinel NiCo2O4 respectively, which agrees well with previous reports.30–33
 |
| Fig. 1 Typical morphology of NiCo2O4 nanosheets: (a) SEM, (b) TEM, (c) and (d) HRTEM images. The inset in (c) is a SAED pattern. | |
X-ray diffraction (XRD) pattern of the NiCo2O4 nanosheets is shown in Fig. 2a. The well-defined diffraction peaks at 2θ values of 18.9°, 31.1°, 36.6°, 44.6°, 59.1° and 64.9° are indexed to (111), (220), (311), (400), (511) and (440) plane of the spinel NiCo2O4 (card no. 20-0781) with a space group of F*3 (202), respectively.34,35 No peaks from other crystallized phases are observed, indicating the formation of pure NiCo2O4 product. ICP-AES shows the molar ratio of Co to Ni is 2.06
:
1. XPS results indicate that both Co to Ni contain divalent and trivalent ions (ESI, Fig. S2†).
 |
| Fig. 2 (a) Typical XRD pattern of NiCo2O4 nanosheets, (b) nitrogen adsorption–desorption isotherms (inset: pore-size-distribution) of NiCo2O4 nanosheets, (c) TGA/DTA curves of the Ni–Co precursor and (d) FTIR spectrum of NiCo2O4 nanosheets. | |
N2 adsorption–desorption measurements are used to study the porosity and textural properties of the ultrathin NiCo2O4 nanosheets. As shown in Fig. 2b, a distinct hysteresis loop is observed in the large range of 0.1–0.9 P/P0, suggesting that typical mesoporous and macroporous structures for NiCo2O4 nanosheets.36 These pores come from the interstices of nanoparticles and also nanosheets. The pore distribution is relatively narrow, and mainly centered in the range of 2–5 nm (the inset of Fig. 2b). The specific surface area, average pore size and mesoporous volume of the ultrathin mesoporous NiCo2O4 nanosheets are 81.0 m2 g−1, 3.7 nm and 0.25 cm3 g−1, respectively. Such intriguing two-dimensional ultrathin mesoporous NiCo2O4 nanosheets feature could be critical to the catalytic performance, because large specific surface area provides more active sites and greatly increases the catalyst–substrate contact area in the catalytic reaction.
TG curve of the Ni–Co precursor shows that the total weight loss occurs at a typical stepwise decomposition process (Fig. 2c). The initial weight loss of 5.6% accompanied by an endothermic reaction below 150 °C is assigned to the loss of adsorbed water and the evaporation of intercalated water molecules. The subsequent weight loss of 21.6% at 150–300 °C and a broad exothermic peak at 280 °C is due to the loss of water produced by the decomposition and dehydroxylation of Co(OH)2 and Ni(OH)2.32,37
FTIR spectrum of the NiCo2O4 nanosheets is presented in Fig. 2d. Two sharp peaks at 642 cm−1 and 550 cm−1 are ascribed to the stretching vibration of low-spin Co ions at octahedral site and tetrahedrally coordinated Ni ions respectively, which corresponds to the formation of spinel NiCo2O4.35,38,39
Catalytic study
The catalytic potential of NiCo2O4 nanosheets was evaluated in benzylic oxidation reactions which included the oxidation of benzylic methylenes, heteroaromatic benzylic compound and secondary benzylic alcohols for the synthesis of keto compounds.
Optimization of reaction condition
Initially, the conversion of 4,4′-difluorodiphenylmethane into 4,4′-difluorobenzophenone was chosen as a model reaction in acetonitrile at 90 °C for 24 h. To identify the significance of the catalyst for the oxidation of 4,4′-difluorodiphenylmethane, a blank control experiment was performed (Table 1, entry 1), and no 4,4′-difluorobenzophenone was detected. An outstanding catalytic conversion (67%, entry 2) is observed when the NiCo2O4 nanosheets are used as the catalyst. This conversion is higher than that of NiO (16%, entry 3), Co3O4 (17%, entry 4) and their mixture (35%, entry 5). The NiCo2O4 nanosheets provide exposed binary active sites of Co and Ni species, which increase the contacted probability between active sites and substrates in liquid benzylic oxidation system and then improve the conversion of 4,4′-difluorodiphenylmethane. Furthermore, a low conversion (54%, entry 6) is observed when NiCo2O4 nanorods (synthesis and SEM image of NiCo2O4 nanorods were shown in ESI†) are used as the catalyst for the oxidation of 4,4′-difluorodiphenylmethane, indicating the NiCo2O4 nanosheets with ultrathin, mesoporous and high specific surface area feature can accelerate the reaction and improve the conversion of 4,4′-difluorodiphenylmethane. The selectivity of benzylic oxidation is all 99%, which can be due to that the intermediate could be immediately converted into 4,4′-difluorobenzophenone under enough TBHP oxidant and active sites.40
Table 1 Catalyst screening in the oxidation of 4,4′-difluorodiphenylmethanea
Entry |
Catalyst |
Conv.b (%) |
Sel.b (%) |
Reaction conditions: 4,4′-difluorodiphenylmethane (1.0 mmol), catalyst, aqueous TBHP (70 wt%) (3.0 mmol) and acetonitrile (1.0 mL) at 90 °C stirring for 24 h. Conversion and selectivity were determined by GC-MS using nitrobenzene as internal standard. NiCo2O4 nanosheets (5.0 × 10−2 mmol). NiO (5.0 × 10−2 mmol). Co3O4 (3.3 × 10−2 mmol). NiO (5.0 × 10−2 mmol) + Co3O4 (3.3 × 10−2 mmol). NiCo2O4 nanorods (5.0 × 10−2 mmol). |
1 |
No |
No |
— |
2c |
NiCo2O4 nanosheets |
67 |
>99 |
3d |
NiO |
16 |
>99 |
4e |
Co3O4 |
17 |
>99 |
5f |
NiO + Co3O4 |
35 |
>99 |
6g |
NiCo2O4 nanorods |
54 |
>99 |
Solvents play a crucial role in liquid phase catalytic reaction. The conversion of 4,4′-difluorobenzophenone is about 52% without solvent (Table 2, entry 1). The conversion of 4,4′-difluorobenzophenone is 0%, 26%, 51%, 58% and 67% when hexane, isopropylalcohol, acetone, toluene and acetonitrile are employed as the solvent, respectively (entry 2–6). This suggests that the aprotic solvents with larger dielectric constant are beneficial to the enhancing of the conversion of 4,4′-difluorobenzophenone. These solvents promote the dispersion and collisions of the oxygen source, the substrate and the catalyst. Besides, acetonitrile could form peroxyimidic acid, which further improve the conversion.41 However, no 4,4′-difluorobenzophenone is detected when H2O are employed as solvent (entry 7) owing to the limited dispersion of the oxygen source and the substrate.
Table 2 Oxidation of 4,4′-difluorodiphenylmethane in different solvents over NiCo2O4 nanosheets catalysta
Entry |
Solvent |
Dielectric constant |
Conv.b (%) |
Sel.b (%) |
Reaction conditions: 4,4′-difluorodiphenylmethane (1.0 mmol), 12.0 mg (5.0 × 10−2 mmol) NiCo2O4 nanosheets catalyst, aqueous TBHP (70 wt%) (3.0 mmol) and solvent (1.0 mL) at 90 °C stirring for 24 h. Conversion and selectivity were determined by GC-MS using nitrobenzene as internal standard. |
1 |
Neat |
— |
52 |
>99 |
2 |
n-Hexane |
1.89 |
No |
— |
3 |
Isopropanol |
15.7 |
26 |
>99 |
4 |
Acetone |
20.7 |
51 |
>99 |
5 |
Toluene |
2.4 |
58 |
>99 |
6 |
Acetonitrile |
37.5 |
67 |
>99 |
7 |
H2O |
80.4 |
No |
— |
Previous results confirmed that the role of base was pivotal in this reaction.11 The conversion of 4,4′-difluorodiphenylmethane is 8%, 43% and 88% when additive pyrrole, imidazole and pyridine is added, respectively (Table 3, entry 1–3). This is because that pyridine could behave as a hydrogen bond acceptor with TBHP to accelerate the formation of t-butoxyl radical.1 The radical abstract hydrogen atom at the benzylic carbon atom from the substrate.42,43 Moreover, the conversion shows a maximum when the content of pyridine is 10 mol% (Table 3, entry 4–7).
Table 3 Oxidation of 4,4′-difluorodiphenylmethane under a function of additivea
Entry |
Additive (mol%) |
Conv.b (%) |
Sel.b (%) |
Reaction conditions: 4,4′-difluorodiphenylmethane (1.0 mmol), 12.0 mg (5.0 × 10−2 mmol) NiCo2O4 nanosheets catalyst, aqueous TBHP (70 wt%) (3.0 mmol), additive and solvent (1.0 mL) at 90 °C stirring for 24 h. Conversion and selectivity were determined by GC-MS using nitrobenzene as internal standard. |
1 |
Pyrrole (100) |
8 |
>99 |
2 |
Imidazole (100) |
43 |
>99 |
3 |
Pyridine (100) |
88 |
>99 |
4 |
Pyridine (50) |
92 |
>99 |
5 |
Pyridine (10) |
>99 |
>99 |
6 |
Pyridine (5) |
73 |
>99 |
7 |
Pyridine (0) |
67 |
>99 |
The influence of reaction temperature on the conversion of 4,4′-difluorodiphenylmethane using NiCo2O4 nanosheets catalyst is also investigated. When the reaction temperature keeps at 70 °C, 80 °C and 90 °C, the conversion is 50%, 58% and 99%, respectively. This indicates that the increasing of the temperature can improve the conversion of 4,4′-difluorobenzophenone. Increased the temperature to 100 °C, the conversion maintains 99%, however the selectivity decreases slightly (95%), which is attributed to the formation of the byproduct (bis(4-fluorophenyl)methanol). Therefore, the optimized temperature for the conversion of 4,4′-difluorodiphenylmethane is 90 °C.
Fig. 3 shows the evolution of the conversion and selectivity as reaction time using the NiCo2O4 nanosheets catalyst. The conversion of 4,4′-difluorodiphenylmethane increases linearly as the reaction time and reach 88% at 12 h. Then, 4,4′-difluorodiphenylmethane completely converts to 4,4′-difluorobenzophenone at 24 h (curve (a) in Fig. 3). The selectivity maintains 99% during the whole reaction process. Therefore, the optimized catalytic procedure involves 1 mmol substrate, 5 mol% NiCo2O4 nanosheets catalyst and 10 mol% pyridine as an additive and 3.0 equivalents of aqueous TBHP as an oxidant in acetonitrile (1.0 mL) at 90 °C stirring for 24 hours. This procedure is more eco-friendly than previous researches. Bolm and his coworkers observed only 93% yield of 4,4′-difluorobenzophenone when used homogeneous FeCl3·6H2O as catalyst and pyridine (1.0 mL) as solvent.13 Barrett and his coworkers reported bismuth catalysed benzylic oxidation involving both pyridine and corrosive acid at 100 °C.1
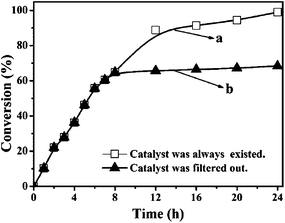 |
| Fig. 3 The leaching experiment, curve (a): change of conversion and selectivity over the reaction time for model reaction, curve (b): leaching test. | |
Heterogeneity and reusability tests
As we know, a crucial issue for solid catalyst is the migration of active site from the solid catalyst to the liquid phase.44 In order to verify the stability of Ni and Co active species of NiCo2O4 nanosheets, a leaching experiment was performed to estimate the contribution of leached active species to the catalytic activity. The solid catalyst was separated by centrifugation at 8 h. The residual liquid phase was transferred to a new reactor vessel for another 16 h reaction. GC determinations show that no more 4,4′-difluorobenzophenone is observed (curve (b) in Fig. 3), which indicates no active sites migrate from the solid catalyst to the liquid phase during the reaction.
In order to further evaluate the stability of NiCo2O4 nanosheets catalyst, the catalyst was used in the cycled reaction under the same reaction conditions. After each reaction, the catalyst was recovered and washed with acetonitrile to remove physical absorbed reagents. The NiCo2O4 nanosheets retain 85% of conversion, 93% of selectivity even after 5 recycles (Fig. 4). The XRD and FTIR results (ESI, Fig. S3†) show that the composition of the catalyst has no obvious change before and after reaction. While XPS results (ESI, Fig. S4†) show an increasing of the Ni3+ moiety in the recovered nanosheets, and SEM images (ESI, Fig. S3†) suggest the assembled structure of the nanosheets is slightly collapsed. These may lead to the slightly decreasing in the conversion and selectivity for the oxidation of 4,4′-difluorodiphenylmethane during the cycling experiment.
 |
| Fig. 4 The reusability of the NiCo2O4 nanosheets catalyst for the oxidation of 4,4′-difluorodiphenylmethane. | |
Oxidation of different benzylic substrates
To determine the general applicability of NiCo2O4 nanosheets catalyst, benzylic oxidation of benzylic methylenes, heteroaromatic benzylic compounds and secondary benzylic alcohols are also studied (Table 4). The conversion of ethyl benzene, 1-ethyl-4-fluorobenzene and 1-ethyl-4-methoxybenzene was 95%, 85% and 99%, respectively (Table 4, entry 1–3), indicating that the presence of electron-donating group favor the oxidation. Similar results are also observed for benzyl methyl ether and methyl 2-phenylacetate, whose conversion is 42% (entry 4) and 99% (entry 5), respectively. The relative conversion of the products suggests that the C–H bond energy of the benzyl positions is one main parameter to control the activity. To expand the scope of the catalytic system, heteroaromatic compounds, such as 2-ethylthiophene (entry 6) is chosen as the substrate. 2-Acetylthiophene is produced in good conversion (91%) due to the fact that the sulfur in a five membered aromatic ring may be regarded as an electron donating substituent.21 Interestingly, the reaction is also efficient for the ring 9H-fluorene (99%, entry 7) and various secondary benzylic alcohols (99%, entry 8–10). These exciting results confirm that NiCo2O4 nanosheets are efficient heterogeneous catalyst for the benzylic oxidation with high yield. It can be attributed to following critical merits. During the catalytic reaction, Co3+/Co2+ or Ni3+/Ni2+ redox couples would act as the active sites circularly and produce the carbon-centered radicals (ESI, Scheme S1†). The ultrathin NiCo2O4 nanosheets with high specific surface area have an increased portion of exposed surfaces and ensure high utilization of Co and Ni active sites. On the other hand, the mesoporous channels can ensure efficient contact between the active sites and the substrate.
Table 4 Oxidative activity of different benzylic substrates using NiCo2O4 nanosheets catalysta
Entry |
Substrate |
Product |
Conv.b (%) |
Sel.b (%) |
Reaction conditions for a 1.0 mmol scale. Reactions were conducted using substrates (1.0 mmol), pyridine (8.0 μL, 0.1 mmol), 12.0 mg (5.0 × 10−2 mmol) NiCo2O4 nanosheets catalyst, aqueous TBHP (70 wt%) (3.0 mmol) and acetonitrile (1.0 mL) at 90 °C stirring for 24 h. Conversion and selectivity were determined by GC-MS with internal standard method and 1HNMR analysis. NMR samples were prepared by careful removal of solvent and dissolving the residue in CDCl3. The reaction was performed 90 °C for 2 h. The reaction was performed at ambient temperature for 30 min. |
1 |
 |
 |
95 |
>99 |
2 |
 |
 |
85 |
>99 |
3 |
 |
 |
>99 |
>99 |
4 |
 |
 |
42 |
>99 |
5 |
 |
 |
>99 |
>99 |
6 |
 |
 |
91 |
>99 |
7 |
 |
 |
>99 |
>99 |
8c |
 |
 |
>99 |
>99 |
9 |
 |
 |
>99 |
>99 |
10d |
 |
 |
>99 |
>99 |
Conclusions
In summary, a novel, highly effective and recyclable NiCo2O4 nanosheet catalyst have been successfully synthesized and applied for benzylic oxidation. The ultrathin and high specific surface area feature of the catalyst increases the available Co and Ni binary active sites, and the mesopores ensure enough contact between these highly exposed active sites and the substrate, and then improve the conversion of the substrates. The NiCo2O4 nanosheets show excellent performance towards the oxidation of a wide range of benzylic substrates, such as benzylic methylenes, heteroaromatic benzylic compound and secondary benzylic alcohols. This provides a highly efficient, low-cost and reusable heterogeneous catalyst for benzylic oxidations and can be extended to the structure design for other nanohybrid catalysts with double- or multi-metal active sites.
Acknowledgements
This work was supported by the Co-building Special Project of Beijing Municipal Education and Natural Science Foundation of China (NSFC no. 51328202).
Notes and references
- Y. Bonvin, E. Callens, I. Larrosa, D. A. Henderson, J. Oldham, A. J. Burton and A. G. Barrett, Org. Lett., 2005, 7, 4549 CrossRef CAS PubMed.
- J. Zhang, Z. Wang, Y. Wang, C. Wan, X. Zheng and Z. Wang, Green Chem., 2009, 11, 1973 RSC.
- X. Han, Z. Zhou, C. Wan, Y. Xiao and Z. Qin, Synthesis, 2013, 45, 615 CrossRef CAS PubMed.
- J. Muzart, Chem. Rev., 1992, 92, 113 CrossRef CAS.
- T. Das, K. Chaudhari, E. Nandanan, A. Chandwadkar, A. Sudalai, T. Ravindranathan and S. Sivasanker, Tetrahedron Lett., 1997, 38, 3631 CrossRef CAS.
- G. Blay, I. Fernández, T. Giménez, J. R. Pedro, R. Ruiz, E. Pardo, F. Lloret and M. C. Muñoz, Chem. Commun., 2001, 2102 RSC.
- T. Bennur, S. Sabne, S. Deshpande, D. Srinivas and S. Sivasanker, J. Mol. Catal. A: Chem., 2002, 185, 71 CrossRef CAS.
- S. N. Azizi and S. Ehsani Tilami, Microporous Mesoporous Mater., 2013, 0167, 89 CrossRef CAS PubMed.
- S. K. Hanson, R. Wu and L. P. Silks, Org. Lett., 2011, 13, 1908 CrossRef CAS PubMed.
- J. B. Xia, K. W. Cormier and C. Chen, Chem. Sci., 2012, 3, 2240 RSC.
- A. J. Catino, J. M. Nichols, H. Choi, S. Gottipamula and M. P. Doyle, Org. Lett., 2005, 7, 5167 CrossRef CAS PubMed.
- H. Li, Z. Li and Z. Shi, Tetrahedron, 2009, 65, 1856 CrossRef CAS PubMed.
- M. Nakanishi and C. Bolm, Adv. Synth. Catal., 2007, 349, 861 CrossRef CAS.
- C. Della Pina, E. Falletta and M. Rossi, J. Catal., 2008, 260, 384 CrossRef CAS PubMed.
- S. Marx and A. Baiker, J. Phys. Chem. C, 2009, 113, 6191 CAS.
- Y. Chen, H. Wang, C. J. Liu, Z. Zeng, H. Zhang, C. Zhou, X. Jia and Y. Yang, J. Catal., 2012, 289, 105 CrossRef CAS PubMed.
- L. Liotta, A. Venezia, G. Deganello, A. Longo, A. Martorana, Z. Schay and L. Guczi, Catal. Today, 2001, 66, 271 CrossRef CAS.
- M. Y. Zheng, A. Q. Wang, N. Ji, J. F. Pang, X. D. Wang and T. Zhang, ChemSusChem, 2010, 3, 63 CrossRef CAS PubMed.
- D. M. Alonso, S. G. Wettstein and J. A. Dumesic, Chem. Soc. Rev., 2012, 41, 8075 RSC.
- J. M. Grill, J. W. Ogle and S. A. Miller, J. Org. Chem., 2006, 71, 9291 CrossRef CAS PubMed.
- B. B. Wentzel, M. P. Donners, P. L. Alsters, M. C. Feiters and R. J. Nolte, Tetrahedron, 2000, 56, 7797 CrossRef CAS.
- B. Cui, H. Lin, Y. Z. Liu, J. B. Li, P. Sun, X. C. Zhao and C. J. Liu, J. Phys. Chem. C, 2009, 113, 14083 CAS.
- P. Visuvamithiran, B. Sundaravel, M. Palanichamy and V. Murugesan, J. Nanosci. Nanotechnol., 2013, 13, 2528 CrossRef CAS PubMed.
- J. Jansson, A. E. Palmqvist, E. Fridell, M. Skoglundh, L. Österlund, P. Thormählen and V. Langer, J. Catal., 2002, 211, 387 CrossRef CAS.
- R. Singh, J. Pandey, N. Singh, B. Lal, P. Chartier and J. F. Koenig, Electrochim. Acta, 2000, 45, 1911 CrossRef CAS.
- J. Li, S. Xiong, Y. Liu, Z. Ju and Y. Qian, ACS Appl. Mater. Interfaces, 2013, 5, 981 CAS.
- J. Liu, C. Liu, Y. Wan, W. Liu, Z. Ma, S. Ji, J. Wang, Y. Zhou, P. Hodgson and Y. Li, CrystEngComm, 2013, 15, 1578 RSC.
- G. Q. Zhang and X. W. D. Lou, Adv. Mater., 2013, 25, 976 CrossRef CAS PubMed.
- G. Q. Zhang and X. W. D. Lou, Sci. Rep., 2013, 3, 1470 Search PubMed.
- M. Cabo, E. Pellicer, E. Rossinyol, O. Castell, S. Surinach and M. D. Baró, Cryst. Growth Des., 2009, 9, 4814 CAS.
- W. W. Liu, C. X. Lu, K. Liang and B. K. Tay, J. Mater. Chem. A., 2014, 2, 5100 CAS.
- L. Qian, L. Gu, L. Yang, H. Yuan and D. Xiao, Nanoscale, 2013, 5, 7388 RSC.
- Q. Wang, B. Liu, X. Wang, S. Ran, L. Wang, D. Chen and G. Shen, J. Mater. Chem., 2012, 22, 21647 RSC.
- H. W. Wang, Z. A. Hu, Y. Q. Chang, Y. L. Chen, H. Y. Wu, Z. Y. Zhang and Y. Y. Yang, J. Mater. Chem., 2011, 21, 10504 RSC.
- N. Padmanathan and S. Selladurai, Ionics, 2013, 19, 1535 CrossRef CAS.
- C. Z. Yuan, J. Y. Li, L. R. Hou, L. Yang, L. F. Shen and X. G. Zhang, J. Mater. Chem., 2012, 22, 16084 RSC.
- B. Cui, H. Lin, J. B. Li, X. Li, J. Yang and J. Tao, Adv. Funct. Mater., 2008, 18, 1440 CrossRef CAS.
- H. Guan, C. Shao, Y. Liu, N. Yu and X. Yang, Solid State Commun., 2004, 131, 107 CrossRef CAS PubMed.
- W. Luo, X. Hu, Y. Sun and Y. Huang, J. Mater. Chem., 2012, 22, 8916 RSC.
- J. B. Xia, K. W. Cormier and C. Chen, Chem. Sci., 2012, 3, 2240 RSC.
- L. H. Shu and Y. Shi, J. Org. Chem., 2000, 65, 8807 CrossRef CAS.
- G. Rothenberg, H. Wiener and Y. Sasson, J. Mol. Catal. A: Chem., 1998, 136, 253 CrossRef CAS.
- A. Dhakshinamoorthy, M. Alvaro and H. Garcia, J. Catal., 2009, 267, 1 CrossRef CAS PubMed.
- U. P. Tran, K. K. Le and N. T. Phan, ACS Catal., 2011, 1, 1207 Search PubMed.
Footnote |
† Electronic supplementary information (ESI) available: Synthesis and SEM image of NiCo2O4 nanorods. XRD, FTIR, SEM and XPS of the recovered catalyst. See DOI: 10.1039/c4ra11972j |
|
This journal is © The Royal Society of Chemistry 2015 |