DOI:
10.1039/C4RA10074C
(Paper)
RSC Adv., 2014,
4, 63006-63015
Semiaromatic polyamides containing ether and different numbers of methylene (2–10) units: synthesis and properties†
Received
9th September 2014
, Accepted 6th November 2014
First published on 7th November 2014
Abstract
A series of semiaromatic difluorobenzamide monomers was synthesized by the reaction of diamine and 4-fluorobenzoic chloride using a facile interfacial method. These syntheses were conducted to react the monomers with 1,1-bis(4-hydroxyphenyl)-1-phenylethane (BHPPE), so as to prepare semiaromatic polyamides containing ether units by the method of nucleophilic polycondensation. These had excellent thermal properties with glass transition temperatures (Tg) of 134.4–195.6 °C and initial degradation temperatures (Td) of 405–443 °C. The activation energies of degradation were in the range of 180.1–275.9 kJ mol−1. The resultant polymers can be dissolved in strong polar solvents and supply a tough film with a tensile strength of 89–105 MPa. Also, we found that the complex viscosities of these semiaromatic polyamides ranged from 77 to 688 Pa s at 290 °C. They had the appropriate complex viscosities for melt processing. Moreover, they had much wider processing windows than those of traditional semiaromatic polyamides such as poly(hexamethylene terephthalamide) (PA6T). Interestingly, some of the resultant polymers were found to be naturally self-retardant.
Introduction
Nylons (such as PA6 or PA66) are a type of engineering thermoplastic that have been widely applied in modern industrial and commercial applications in the last three decades. They can be easily processed by melt processing to form different kinds of structural parts, polymer films and polymer fibers.1–3 With increasingly stringent requirements, applications of aliphatic polyamides are limited in some fields because of their poor dimensional stability and thermal properties, especially in surface mount technology (SMT) and the shells of automobile engines. To improve the thermal properties of polyamides, the fabrication method for polyamide compounds,4 or the incorporation of aromatic rings, are efficient approaches.5–9 Aromatic polyamides such as poly(p-phenylene terephthalamide) (PPTA)10 and poly(m-phenyleneisophthalamide) (PMIA)11 have been commercially accepted in industry for their excellent balance of mechanical and thermal properties. Despite their outstanding properties, they also have limited applications because they can only be processed by special methods (they do not melt below their decomposition temperatures).12,13 The high melting temperatures of aromatic polyamides are attributed to the high density of aromatic rings and strong inter-chain forces, mainly hydrogen bonding, that enhance an effective molecular packing.14 Also, semiaromatic polyamides have been developed rapidly in the last 20 years. The semiaromatic polyamides have been noted for their high thermal stability and chemical resistance. However, only a few semiaromatic polyamides are commercially available. These include copolymers of PA6T,15 poly(nonamethylene terephthalamide) (PA9T)16–19 and the products of Dupont, Evonik, Mitsui, and Solvay and so on. Usually, if the melting point of a semiaromatic polyamide is higher than 340 °C, it is thought to be not suitable for thermal processing.20 Thus, melt processing is impractical for those semiaromatic polyamides with short aliphatic diamines (2–7 CH2's) because their melt temperatures surpass the thermal decomposition temperatures, such as PA4T (Tm = 430 °C, Td = 350 °C) and PA6T (Tm = 370 °C, Td = 350 °C). Therefore, several synthetic approaches have been developed, such as incorporating naphthalene rings (Tm = 320 °C, Td = 495 °C),21 benzylidene structure (Tm = 290 °C),22 bulky pendant groups (Tg ≈ 270 °C, Td ≈ 500 °C),14 noncoplanar biphenylene moieties (Tg ≈ 300 °C, Td-10% ≈ 510 °C),23 azo groups,24,25 sulfone units,26 triazole units,27 thioether units28 and long-chain diamines (Tm ≈ 290 °C, Td ≈ 490 °C)29 [such as PA9T (Tm = 305 °C, Td-5% = 464 °C), PA-10T (Tm = 315 °C, Td-5% = 472 °C),30 PA-12T (Tm = 295 °C, Td = 429 °C),31 PA-18T (Tm = 245 °C), and so on] into the polymer backbones. It is known that the ether linkage is a flexible bond. It can be incorporated into the polymer backbone to improve the resin's processability, as in the cases of poly(arylene ether amide)2 and poly(arylene ether sulfone).32 They all have excellent processability, mechanical, thermal and antioxidant properties. Therefore, in the work described here, we expected to incorporate the ether (–O–) and different numbers of methylene units into the main chain of semiaromatic polyamides to improve their properties. In this study, five kinds of semiaromatic difluorobenzamide monomers which contained 2–10 CH2 groups were prepared by the reaction of 4-FBC with different diamine (ethylenediamine, 1,6-hexanediamine, 1,4-butanediamine, 1,8-octanediamine, and 1,10-decanediamine). Then these were reacted with BHPPE by nucleophilic polycondensation to prepare semiaromatic polyamides (usually, the polyamides were prepared by the reaction of dicarboxylic acid (dicarboxylic chloride) and diamine with electrophilic substitution). The effects of chemical structure on the thermal performances, mechanical properties, processability, flame retardant properties and thermal degradation kinetics of the resultant semiaromatic polyamides were investigated in detail.
Experimental
Materials
BHPPE was prepared according to the method reported earlier by our group,33 and 4-fluorobenzoic chloride (4-FBC) (99.5%, Lanning Chemical Company Limited), sodium hydroxide (NaOH) (AR, SiChuan ChengDu ChangLian Chemical Reagent Company), N-methyl-2-pyrrolidone (NMP) (JiangSu NanJing JinLong Chemical Industry Company), ethylenediamine, 1,4-butanediamine, 1,6-hexanediamine, 1,8-octanediamine, 1,10-decanediamine and other reagents were obtained commercially.
1,2-N,N′-bis(4-fluorobenzamide) ethane (BFBE) (Scheme 1)
BFBE was prepared according to the following procedure: 4-FBC (320 g, 2.02 mol) and dichloromethane (2000 ml) were added into a 5000 ml three-necked flask equipped with mechanical stirrer and thermometer. Then the mixture of ethylenediamine (60 g, 1 mol) and NaOH (80 g, 2 mol) (dissolved in 1000 ml deionized water) and sodium dodecyl sulfate (3 g, 0.01 mol) was added into the flask dropwise within 2 h. The mixture was vigorously stirred at 5–10 °C for about 6 h. After that the reaction mixture was evaporated under 50 °C to recover the solvent dichloromethane. Then the crude product was washed with hot deionized water, the mixture was filtered, and the above steps were repeated three times. Next, the wet filter cake was recrystallized from ethanol to afford needle-like crystals. The purified product was then vacuum-dried at 80 °C for more than 12 h to yield colorless crystals of BFBE.
Yield: 263.6 g, 86.7%. Elemental analysis (%): found: C, 62.93 (63.15); H, 4.60 (4.64); N, 9.31 (9.21) (data in brackets are calculated). Melt point: 234–236.4 °C. FT-IR (KBr, cm−1): 3302 (N–H), 1633 (–CO–), 3053 (C–H aromatic ring), 2944, 2883 (–CH2–), 1604, 1559, 1506 (C
C aromatic ring), 854 (para substituent of the aromatic ring). NMR [400 MHz, deuterated dimethyl sulfoxide (DMSO-d6)/tetramethylsilane (TMS), ppm]: 3.422–3.473 (m, 4H, H1), 7.266–7.325 (m, 4H, H2), 7.888–7.931 (m, 4H, H3), 8.627 (s, 2H, H4); 39.67 (C1), 115.23 (C2), 129.83 (C3), 130.98 (C4), 162.54 (C5) and 165.41 (C6). The other monomers were prepared using a similar method to that used for BFBE.
1,4-N,N′-bis(4-fluorobenzamide) butane (BFBB)
Yield: 283.2 g, 85.3%. Elemental analysis (%): found: C, 65.33 (65.05); H, 5.41 (5.46); N, 8.48 (8.43) (data in brackets are calculated). Melt point: 228.4–231.8 °C. FT-IR (KBr, cm−1): 3314 (N–H), 1630 (–CO–), 3036 (C–H aromatic ring), 2948, 2876 (–CH2–), 1605, 1540, 1504 (C
C aromatic ring), 850 (para substituent of the aromatic ring). NMR [400 MHz, deuterated dimethyl sulfoxide (DMSO-d6)/tetramethylsilane (TMS), ppm]: 1.558 (s, 4H, H1), 3.272–3.330 (d, 4H, H2), 7.261–7.306 (m, 4H, H3), 7.886–7.922 (m, 4H, H4), 8.492 (s, 2H, H5); 26.65 (C1), 39.66 (C2), 115.17 (C3), 129.74 (C4), 131.07 (C5), 162.49 (C6) and 165.02 (C7).
1,6-N,N′-bis(4-fluorobenzamide) hexane (BFBH)
Yield: 320.0 g, 88.9%. Elemental analysis (%): found: C, 66.39 (66.65); H, 6.17 (6.15); N, 7.89 (7.77) (data in brackets are calculated). Melt point: 197.8–200 °C. FT-IR (KBr, cm−1): 3317 (N–H), 1630 (–CO–), 3033 (C–H aromatic ring), 2937, 2868 (–CH2–), 1606, 1541, 1504 (C
C aromatic ring), 850 (para substituent of the aromatic ring). 1H-NMR [400 MHz, deuterated dimethyl sulfoxide (DMSO-d6)/tetramethylsilane (TMS), ppm]: 1.333 (s, 4H, H1), 1.504–1.536 (t, 4H, H2), 3.217–3.266 (d, 4H, H3), 7.258–7.302 (m, 4H, H4), 7.880–7.915 (m, 4H, H5), 8.463 (s, 2H, H6); 26.20 (C1), 29.05 (C2), 39.67 (C3), 115.17 (C4), 129.73 (C5), 131.11 (C6), 162.47 (C7) and 164.97 (C8).
1,8-N,N′-bis(4-fluorobenzamide) octane (BFBO)
Yield: 327.1 g, 84.3%. Elemental analysis (%): found: C, 68.35 (68.02); H, 6.73 (6.75); N, 7.34 (7.21) (data in brackets are calculated). Melt point: 174–176.8 °C. FT-IR (KBr, cm−1): 3318 (N–H), 1631 (–CO–), 3064 (C–H aromatic ring), 2935, 2855 (–CH2–), 1606, 1541, 1505 (C
C aromatic ring), 849 (para substituent of the aromatic ring). 1H-NMR [400 MHz, deuterated dimethyl sulfoxide (DMSO-d6)/tetramethylsilane (TMS), ppm]: 1.97 (s, 8H, H1–H2), 1.510 (s, 4H, H3), 3.212–3.260 (m, 4H, H4), 7.259–7.303 (m, 4H, H5), 7.885–7.919 (m, 4H, H6), 8.457 (s, 2H, H7); 26.44 (C1), 28.72 (C2), 29.04 (C3), 39.68 (C4), 115.18 (C5), 129.72 (C6), 131.13 (C7), 162.46 (C8) and 164.93 (C9).
1,10-N,N′-bis(4-fluorobenzamide) decane (BFBD)
Yield: 338.2 g, 81.3%. Elemental analysis (%): found: C, 69.39 (69.21); H, 7.24 (7.26); N, 6.96 (6.73) (data in brackets are calculated). Melt point: 170–172.4 °C. FT-IR (KBr, cm−1): 3321 (N–H), 1631 (–CO–), 3068 (C–H aromatic ring), 2923, 2852 (–CH2–), 1606, 1538, 1504 (C
C aromatic ring), 849 (para substituent of the aromatic ring). 1H-NMR [400 MHz, deuterated dimethyl sulfoxide (DMSO-d6)/tetramethylsilane (TMS), ppm]: 1.269 (s, 12H, H1–H3), 1.483–1.516 (t, 4H, H4), 3.202–3.252 (m, 4H, H5), 7.257–7.301 (m, 4H, H6), 7.878–7.913 (m, 4H, H7), 8.448 (s, 2H, H8); 26.44 (C1), 28.73 (C2), 28.92 (C3), 29.92 (C4), 39.68 (C5), 115.20 (C6), 129.73 (C7), 130.87 (C8), 162.18 (C9) and 164.83 (C10).
Polymer synthesis (as shown in Scheme 1)
A typical polymerization was performed as shown in Scheme 1. NMP (150 ml), toluene (20 ml), BHPPE (29.0 g, 0.1 mol), potassium carbonate (27.6 g, 0.2 mol) and BFBE (30.4 g, 0.1 mol) were added into a 500 ml three-necked flask equipped with “Dean Stark” trap, mechanical stirrer and thermometer. The flask was heated to 160 °C and maintained for about 2 h; during this period, 26.7 ml of liquid was removed. Then the reaction flask was heated to 200 °C and maintained for another 8 h. After that, the reaction solution was poured into water, with stirring, to precipitate white fibrous polymers. The collected polymer was washed with water and ethanol, pulverized to a powder, washed with water and ethanol again, and dried in a vacuum oven at 100 °C for 12 h to give BHPPE-2. (Yield: 51.4 g, 92.8%).
 |
| Scheme 1 Synthesis routes of semiaromatic difluorobenzamide monomers and polymers. | |
BHPPE-4, BHPPE-6, BHPPE-8 and BHPPE-10 were prepared by a similar procedure to that used for BHPPE-2. The yields were as follows: BHPPE-4, 53.1 g (91.3%); BHPPE-6, 57.2 g (93.8%); BHPPE-8, 59.0 g (92.6%); BHPPE-10, 61.0 g (91.6%).
Characterization
The intrinsic viscosities of BHPPE-(2–10) were obtained at 30 ± 0.1 °C with 0.500 g of polymer dissolved in 100 ml of NMP, using a Cannon-Ubbelodhe viscometer. The values were obtained by the one-point method (or Solomon–Ciuta equation):
Where ηr = η/η0, ηsp = η/η0 − 1.
The number-average molecular weights (Mn) and weight-average molecular weight (Mw) were obtained via GPC performed with a Waters 1515 performance liquid chromatography pump, a Waters 2414 differential refractometer (Waters Co., Milford, MA) and a combination of Styragel HT-3 and HT-4 columns (Waters Co., Milford, MA), the effective molecular weight ranges of which were 500–30
000 and 5000–800
000, respectively. N,N-Dimethyl formamide (DMF) was used as an eluent at a flow rate of 1.0 ml min−1 at 35 °C. Polystyrene standards were used for calibration.
The samples of monomers were measured with an elemental analyzer (EURO EA-3000). The melting points of the monomers were measured with a micro melting point apparatus (XRC-1). FT-IR spectroscopic measurements were performed on a Nexus670 FT-IR instrument. H nuclear magnetic resonance (NMR) spectra were obtained on a Bruker-400 NMR spectrometer in deuterated dimethyl sulfoxide. Differential scanning calorimetry (DSC) was performed on a Netzsch DSC 200 PC thermal analysis instrument. The heating rate for DSC measurements was 10 °C min−1. Thermogravimetric analysis (TGA) was performed on a TGA Q500 V6.4 Build 193 thermal analysis instrument with a heating rate of 5–40 °C min under a nitrogen atmosphere. The polymer powder was processed into the sheet shape by a hydraulic press (YJAC, Chengdu Hangfa Group, China) at 290 °C with a pressure of 8 MPa for 10 min. Then the sheets were cut into specific shapes for the different tests. The water absorption of the samples was measured according to standard GB/T1034. An Instron Corporation 4302 instrument was used to study the stress–strain behavior of the samples. Dielectric constants were measured on a TH2819A in a frequency region of 0.1 KHz–100 KHz at 25 °C. Dynamic mechanical analysis (DMA) was performed on a TA-Q800 apparatus operating in tensile mode at a frequency of 1 Hz from 40 to 250 °C with a heating rate of 5 °C min. A parallel plates rheometer (Bohlin Gemini 200, Britain) was fitted with 2.5 cm diameter stainless steel parallel plates. Temperature, frequency and time sweep tests were performed under a nitrogen atmosphere. Quantitative information for the melt flow of the samples could be obtained by recording the complex viscosities versus temperature, time and shear frequency during processing. The UL-94 vertical test was performed according to the testing procedure of FMVSS 302/ZSO 3975 with a test specimen bar 127 mm in length, 12.7 mm in width and about 1.27 mm in thickness. In the test, the polymer specimen was subjected to two 10 s ignitions. After the first ignition, the flame was removed and the time for the polymer to self-extinguish (t1) was recorded. Cotton ignition was noted when polymer dripping occurred during the test. After cooling, the second ignition was performed on the same sample and the self-extinguishing time (t2) and dripping characteristics were recorded. The flame test was performed on five specimens. If the average t1 plus t2 is less than 10 s without any dripping, the polymer is considered to be a V-0 material. If t1 plus t2 is in the range of 10–30 s without any dripping, the polymer is considered to be a V-1 material.34 The LOI was determined with an Atlas Limiting Oxygen Index Chamber. The solubility of the polymers in various solvents was tested at room temperature (or at the boiling points of the solvents).
Results and discussion
Synthesis of semiaromatic difluorobenzamide monomers (BFBE, BFBB, BFBH, BFBO, BFBD)
The synthesis route of monomers is shown in Scheme 1. The monomers were prepared with a facile interfacial reaction through a one-step procedure. The reaction temperature in this procedure could not exceed 30 °C because the reaction was difficult to control and side-effects could occur, in which case the resultant product was difficult to purify and the yield was low.
Chemical structure of monomers
The FT-IR spectra of monomers (ESI Fig. 1†) showed the characteristic absorptions of –CONH– near 3300 and 1630 cm−1. The characteristic absorption of benzene rings (C–H) was observed near 3050 cm−1. The aliphatic chain (–CH2–) was observed near 2970 and 2850–2880 cm−1. The absorptions near 1340 cm−1 and 850 cm−1 were attributed to the vibrations of C–F and para-substituted benzene rings. The 1H-NMR and 13C-NMR spectra of monomers (BFBE) (ESI Fig. 2 and 3†) showed two groups of peaks ranging from 7.2 to 8.0 ppm that were attributed to the two proton signals of a benzene ring. The aliphatic chain proton signals ranged from 1.2 to 3.5 ppm. The signals near 8.5 ppm were assigned to amide units. Six groups of peaks, C1–C6, were 39.67, 115.23, 129.83, 130.98, 162.54 and 165.41. Combining the FT-IR and elemental analysis results suggests that the monomers were synthesized as depicted in Scheme 1.
Synthesis of BHPPE-(2–10)
The polycondensation reaction was carried out by nucleophilic substitution polymerization using potassium carbonate as the catalyst. The reaction temperature was in the range 160–200 °C. The purpose of the first step was mainly to form the bisphenol salt and dehydrate water (with the azeotropic role of toluene). This was beneficial for obtaining polymers with a large molecular weight. The molecular weights of the polymers were measured by intrinsic viscosity and GPC. As shown in Table 1, the ηint values of BHPPE-(2–10) ranged from 0.71 to 1.01 dL g−1, the Mn and Mw values were in the ranges 6.0 × 104 to 10.5 × 104 and 1.26 × 105 to 2.02 × 105, respectively. This suggests that the resultant polyamides had more than 100 repeated units. The polydispersity indices (PDIs) of polymers were in the range 1.8–2.3.
Table 1 Intrinsic viscosities (ηint) and molecular weights of polymers (BHPPE-(2–10))
Polymers |
ηint (dL g−1) |
Mn (g mol−1) |
Mw (g mol−1) |
PDI (Mw/Mn) |
BHPPE-2 |
0.71 |
6.0 × 104 |
1.26 × 105 |
2.10 |
BHPPE-4 |
0.84 |
7.9 × 104 |
1.56 × 105 |
1.97 |
BHPPE-6 |
0.95 |
9.4 × 104 |
1.72 × 105 |
1.83 |
BHPPE-8 |
1.01 |
1.05 × 105 |
2.02 × 105 |
1.92 |
BHPPE-10 |
0.89 |
8.6 × 104 |
1.99 × 105 |
2.31 |
Chemical chain structure of BHPPE-(2–10)
The chemical structure of the resultant polymers was characterized by FT-IR and 1H-NMR. The FT-IR spectra (Fig. 1) of polymers exhibited the characteristic ether stretching near 1100 cm−1. The absorptions near 3320 and 1640 cm−1 were attributed to the amide group. Comparing with the spectra of the monomers, the characteristic absorption around 1340 cm−1 (C–F) had disappeared. Fig. 2 shows the 1H-NMR spectra of BHPPE-(2–10). The signals of protons on a benzene ring ranged from 6.6 to 8.0 ppm. The chemical shifts were so close that the proton peaks could not be distinguished. The signals near 2.12 and 8.5 ppm were assigned to –CH3 and the amide unit. From Fig. 2 we found that the proton signals shifted to high field with an increase of carbon numbers of the diamine used in the reaction. This may be caused by the shielding effects of the methylene unit. Combined with the FT-IR results, this suggests that the polymerization proceeded as depicted in Scheme 1.
 |
| Fig. 1 The FT-IR spectra of BFBE and polymers (BHPPE-(2–10)). | |
 |
| Fig. 2 The 1H-NMR spectra of polymers (BHPPE-(2–10)). | |
Tensile properties
The average tensile strength values of BHPPE-(2–10) are summarized in Table 2. As shown in Table 2, the average tensile strengths of BHPPE-(2–10) were 89–105 MPa. The elongation at break was in the range 13.2–18.7%. This suggests that BHPPE-(2–10) have similar mechanical properties to those of the commercial product PA9T.
Table 2 Thermal and mechanical properties of BHPPE-(2–10) and PA9T
Polymers |
Tg (°C) |
T5% (°C) |
Char yield (%) |
Tensile strength (MPa) |
Young's modulus (GPa) |
Elongation at break (%) |
Storage modulus at 125 °C (GPa) |
Glass transition temperaturea (°C) |
Detected by dynamic mechanical analysis (DMA). |
BHPPE-2 |
195.6 |
405 |
28.3 |
97 |
2.1 |
14.4 |
1.9 |
210.8 |
BHPPE-4 |
170.4 |
417 |
7.5 |
103 |
1.9 |
16.7 |
1.6 |
186.1 |
BHPPE-6 |
156.5 |
441 |
4.1 |
105 |
1.8 |
19.8 |
1.6 |
171.3 |
BHPPE-8 |
145.6 |
442 |
2.3 |
94 |
1.5 |
18.7 |
1.7 |
159.5 |
BHPPE-10 |
134.4 |
443 |
0.9 |
89 |
1.1 |
23.2 |
1.4 |
150.6 |
PA9T |
115 |
464 |
— |
86 |
2.7 |
4.2 |
— |
— |
Dynamic mechanical analysis
DMA was carried out to characterize the resulting semiaromatic polyamides. As shown in Fig. 3, one obvious transition behavior was observed, defined as the α relaxation. It is well-known that the glass transition temperature (Tg) of a polymer can be determined by α relaxation, as it is usually related to the segment movements in the noncrystalline area.35 The α relaxation temperatures of these semiaromatic polyamides were found to be 150.6, 159.5, 171.3, 186.1 and 210.8 °C, respectively. They are nearly the same as those obtained by the DSC method. The slight differences are mainly attributed to the different responses of the polymers to these two measurements. The α-relaxation temperatures (glass transition temperature) decreased with the increase in carbon number of the aliphatic chain (methylene) in the polymeric backbone. Fig. 4 displays the storage modulus curves of BHPPE-(2–10). As listed in Table 2, the semiaromatic polyamides exhibited high storage moduli of 2.1, 1.7, 1.8, 1.9 and 1.5 GPa. We also found that the polymers maintained above the 70% storage modulus (1.5 GPa) at 125 °C compared with that of samples at 40 °C, which indicates that these semiaromatic polyamides have excellent mechanical properties.
 |
| Fig. 3 The DMA curves (Tan delta) of BHPPE-(2–10). | |
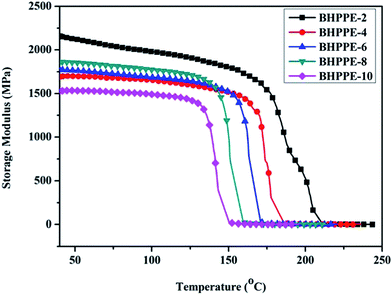 |
| Fig. 4 The DMA curves (storage modulus) of BHPPE-(2–10). | |
Water absorption
The water absorption of BHPPE-(2–10) was measured according to standard GB/T1034. The results are summarized in Table 3. As shown in Table 3, the water absorptions of BHPPE-(2–10) were found to be 0.31%, 0.30%, 0.27%, 0.24% and 0.24%, respectively, which were close to that of the commercial product PA9T (0.17%). The results indicate that these semiaromatic polyamides have low water absorption, which is good for their dimensional and mechanical stability. We also found that the water absorption decreased with lengthening of the aliphatic chain of the polyamides. The main reason was that the high content of methylene group can improve the hydrophobic property of the semiaromatic polyamides.
Table 3 The water absorption and dielectric properties of BHPPE-(2–10) compared to those of PA9T
Polymers |
Water absorption (%) |
Thickness (mm) |
Dielectric constant |
0.1 kHz |
1 kHz |
10 kHz |
100 kHz |
BHPPE-2 |
0.31 |
1.142 |
4.41 |
4.13 |
3.95 |
3.68 |
BHPPE-4 |
0.30 |
1.130 |
4.33 |
4.07 |
3.82 |
3.56 |
BHPPE-6 |
0.27 |
1.126 |
4.17 |
3.94 |
3.68 |
3.49 |
BHPPE-8 |
0.24 |
1.127 |
4.05 |
3.80 |
3.62 |
3.42 |
BHPPE-10 |
0.24 |
1.125 |
3.96 |
3.75 |
3.54 |
3.33 |
PA-9T |
0.17 |
1.137 |
4.06 |
3.78 |
3.92 |
3.64 |
Dielectric constant
Table 3 summarizes the dielectric constants of BPPPE-(2–10), which are in the range 3.33–3.68 at 100 kHz. These low dielectric constants may be attributed to the low polarizability of the C–H bonds of the alkyl groups and the low water absorption of the polymers.
Thermal properties of BHPPE-(2–10)
The thermal properties of BHPPE-(2–10) were examined by DSC and TGA. The results are displayed in Fig. 5 and 6, respectively. As shown in Fig. 5, the Tg values of BHPPE-(2–10) were in the range 134.4–195.6 °C (Table 2). They were higher than that of commercial products such as PA9T (Tg = 126 °C) and copolymers of PA6T (Tg is about 135 °C). Following the decreasing carbon number of the aliphatic chain, BHPPE-2 exhibited the highest Tg value (195.6 °C) in this series. We did not find the melting endothermic peaks from the DSC curves, which suggests the amorphous nature of the resultant semiaromatic polyamides. This was different to the other semiaromatic polyamides reported earlier.28 The main reason was that the introduction of a large pendent benzene group limited the locomotion of the molecular chain, so it could not be arranged in order. As shown in Fig. 6, the initial degradation temperatures (T5%) of BHPPE-(2–10) in nitrogen were 405, 417, 441, 442, and 443 °C, which are much higher than the glass transition temperature and close to those of PA9T (Td = 464 °C) and PA10T (Td = 472 °C). The char yield of BHPPE-(2–4) at 800 °C in nitrogen was about 28.3% and 7.5%, much higher than that of PA6T and PA9T. These results suggest that the thermal stability was almost maintained, with the incorporation of the ether linkage and different numbers of methylene units into the polymeric backbone.
 |
| Fig. 5 The DSC curves of BHPPE-(2–10) at a heating rate of 10 °C min−1 in N2. | |
 |
| Fig. 6 The TGA curves of BHPPE-(2–10) at a heating rate of 10 °C min−1 in N2. | |
Thermal degradation kinetics
The thermal decomposition behavior of these semiaromatic polyamides was studied with a differential method, the Kissinger method, which is the basis of the most powerful methods for the determination of kinetic parameters. The changes in thermogravimetric data, caused by variation of the heating rate, were analyzed. This method can be used to determine the activation energy of solid state reactions from plots of the logarithm of the heating rate versus the inverse of the temperature at the maximum reaction rate in constant heating rate experiments, and does not need a precise knowledge of the reaction mechanism, using the following eqn (1): |
 | (1) |
where β is the heating rate, Tmax is the temperature corresponding to the inflection point of the thermal degradation curves at the maximum reaction rate, A is the pre-exponential factor, αmax is the maximum conversion, and n is the reaction order. The activation energy E can be calculated from the slope of the plot of ln(β/T2max) versus 1000/Tmax and fitting to a straight line. The thermal degradation curves obtained at different heating rates, 5, 10, 20, 40 °C min−1, are shown in Fig. 7. The values of the maximum decomposition rate (Tmax) are shown in Table 4. Fig. 8 shows the curves of the Kissinger method applied to experimental data at different heating rates. The activation energy (as shown in Table 5) of the decomposition of BHPPE-(2–10) was calculated from a straight line fit of a plot of ln(β/T2max) versus 1000/Tmax. The value obtained from Fig. 8 for the activation energy (E) of BHPPE-(2–10) was in the range 180.1–275.9 kJ mol−1, respectively. The activation energy increased with lengthening of the aliphatic chain of the semiaromatic polyamides. This suggests that the long aliphatic chain is beneficial for the thermal stability of these semiaromatic polyamides. The reaction order (n) can be calculated by the peak value of the TGA secondary derivative curves. Then we can obtain the pre-exponential factor (ln
A) value from eqn (1).
 |
| Fig. 7 TGA curves of BHPPE-2 at heating rates of 5 °C min−1, 10 °C min−1, 20 °C min−1, 40 °C min−1 in N2. | |
Table 4 The maximum thermal degradation temperatures of BHPPE-(2–10)
Heating rates |
Tmax (°C) |
BHPPE-2 |
BHPPE-4 |
BHPPE-6 |
BHPPE-8 |
BHPPE-10 |
5 °C min |
421 |
465 |
468 |
471 |
471 |
10 °C min |
432 |
472 |
476 |
482 |
483 |
20 °C min |
452 |
485 |
494 |
501 |
500 |
40 °C min |
465 |
498 |
513 |
516 |
515 |
 |
| Fig. 8 Kissinger method applied to experimental data at heating rates of 5 °C min−1, 10 °C min−1, 20 °C min−1, 40 °C min−1 of BHPPE-(2–10). | |
Table 5 Results of BHPPE-(2–10) according to the Kissinger method
Polymers |
Activation energy E (kJ mol−1) |
Degradation order (n) |
Pre-exponential factor ln A (min−1) |
BHPPE-2 |
180.1 |
1.2 |
22.9 |
BHPPE-4 |
185.9 |
2.7 |
23.4 |
BHPPE-6 |
199.9 |
2.3 |
23.9 |
BHPPE-8 |
203.6 |
2.2 |
24.5 |
BHPPE-10 |
213.4 |
2.2 |
26.1 |
Rheological properties of polymers
A parallel plates rheometer was used to study the effects of the structure of the resulting polyamides on their rheological properties. As shown in Fig. 9, the complex viscosities of BHPPE-(2–10) were in the range 32–1890 Pa s at different temperatures (250–320 °C). We found that when a long aliphatic chain was introduced into the main chain of the polyamide, the complex viscosity of the polymer increased, and the longer the polyamide aliphatic chain, the higher the viscosity. This result mainly arises because the interactions between molecules become stronger as the polymer molecular chains become longer. Consequently, more entangled points should exist, and the complex viscosity of the polymer melts should get much higher. Also, we studied the effects of shear frequency (0.01–55 Hz, 290 °C) on the complex viscosities of the resultant polyamides (Fig. 10). The viscosities ranged from 94.4 to 1488 Pa s at different shear frequencies. The melts of these polyamides exhibited much more stability under high shear rates. In addition, we found that the complex viscosities of samples which contained a long aliphatic chain had a much larger change. This suggests that the sensitivity of the resins to the shear frequency increases with lengthening the aliphatic chain of the semiaromatic polyamides. The rheological study (both of temperature and frequency sweep) revealed that the resultant semiaromatic polyamides had good processability.
 |
| Fig. 9 Plot of complex viscosities versus temperature for BHPPE-(2–10). | |
 |
| Fig. 10 Plot of complex viscosities versus shear frequency for BHPPE-(2–10). | |
Flame retardancy
The LOI values of BPPPE-(2–4) are summarized in Table 6, and were 34 and 30, respectively. We found that BPPPE-2 had a larger LOI value than BPPPE-(4–10). Table 6 also lists the UL-94 data for BPPPE-(2–10). The flame retardancy of BPPPE-(2–4) could reach grades V-1 and V-2, respectively, while the commercial products such as PA6T and PA9T were combustible. Combing the results of LOI and UL-94 data, we find that the introduction of an aromatic ring and short aliphatic chain into the semiaromatic polyamides chain is beneficial for its flame retardancy. The main reason is that the high content of char yield formed during combustion of BPPPE-(2–4) segregated the samples from air, so that its flame retardancy was improved.
Table 6 LOIs and UL-94 data for BHPPE-(2–10)
Sample |
LOI |
1st burning time/s |
2nd burning time/s |
Dripping |
UL-94 grade |
BHPPE-2 |
34 |
7.8 |
5.6 |
No |
V-1 |
BHPPE-4 |
30 |
18.2 |
13.3 |
No |
V-2 |
BHPPE-6 |
Combustible |
BHPPE-8 |
Combustible |
BHPPE-10 |
Combustible |
Solubilities
Table 7 reports the solubilities of BPPPE-(2–10). These materials were found to be soluble in strong polar solvents such as NMP, DMF, and DMSO. They had better solubility than that of PA6T and PA9T. However, they were insoluble in formic acid, toluene, 1,4-dioxane, HCl, phosphoric acid and so on. Compared to alkyl polyamides (PA6), BPPPE-(2–10) showed better corrosion resistance.
Table 7 Solvent resistance of BPPPE-(2–10) and PA6a
Solvents |
Polymers |
PA6 |
BPPPE-2 |
BPPPE-4 |
BPPPE-6 |
BPPPE-8 |
BPPPE-10 |
+: soluble at room temperature; ±: swelling; −: insoluble with heating. |
Concentrated sulfuric acid |
+ |
+ |
+ |
+ |
+ |
+ |
Formic acid |
+ |
− |
− |
− |
− |
− |
NMP |
− |
+ |
+ |
+ |
+ |
+ |
CF3COOH |
+ |
+ |
+ |
+ |
+ |
+ |
HCl (6 mol L−1) |
− |
− |
− |
− |
− |
− |
Phosphoric acid |
+ |
− |
− |
− |
− |
− |
NaOH (1 mol L−1) |
− |
− |
− |
− |
− |
− |
Acetone |
− |
− |
− |
− |
± |
± |
Chloroform |
− |
− |
− |
− |
± |
± |
DMSO |
− |
+ |
+ |
+ |
+ |
+ |
1,4-dioxane |
− |
− |
− |
− |
− |
− |
Toluene |
− |
− |
− |
− |
− |
− |
Phenol + tetrachloroethane |
− |
− |
− |
− |
− |
− |
Conclusions
Semiaromatic difluorobenzamide monomers with different numbers of methylene units were synthesized to develop a series of semiaromatic polyamides [BHPPE-(2–10)]. The semiaromatic polyamides were prepared by nucleophilic polycondensation. The effects of the chemical structure of the semiaromatic polyamides on the physical performance of the polymers were investigated in detail. The properties of the semiaromatic polyamides could be improved by changing the structure of the aliphatic diamine. The glass transition temperature and water absorption were found to decrease with increasing aliphatic chain length in the polymers. In contrast, the thermal stability and complex viscosity of these polyamides continuously increased. These polyamides showed good thermal and mechanical properties and processability (including solution processing and melt processing). The resultant semiaromatic polyamides are suitable for melting processes even when the number of repeat units (methylene) in the aliphatic diamine that reacted with BHPPE is 2. With this method, a kind of semiaromatic polyamide which exhibits excellent performance can be obtained. Furthermore, it can be produced using much more affordable and cheap diamines (such as 1,2-ethanediamine and 1,6-hexanediamine) than can PA9T. Additionally, we found that a part of the resultant polymers [BHPPE-(2–4)] possess a natural flame retardancy that the traditional semiaromatic polyamides do not have. Thus, these semiaromatic polyamides can be good candidates as components for heat-resistant thermoplastic engineering materials, especially in some harsh environments which need resins to be thermo-stable and retardant.
Acknowledgements
This work was supported by research grants from the Youth Fund Natural Science Foundation of China (21304060) and Youth Fund of Sichuan University (2012SCU11009).
References
- A. Peacock and A. Calhoun, Polymer Chemistry: Properties and Applications, Carl Hanser Verlag, Munich, 2006 Search PubMed
. - M. G. José, C. Félix, F. S. García and L. de la P José, Prog. Polym. Sci., 2010, 35, 623–638 CrossRef PubMed
. - L. Crespo, G. Sanclimens, M. Pons, E. Giralt, M. Royo and F. Albericio, Chem. Rev., 2005, 105, 1663–1681 CrossRef CAS PubMed
. - C. L. Zhang, L. F. Feng, S. Hoppe and G. H. Hu, AIChE J., 2012, 58, 1921–1928 CrossRef CAS
. - G. Zhang, D. T. Bai, D. S. Li, S. R. Long, X. J. Wang and J. Yang, Polymer International, 2013, 62, 1358–1367 CrossRef CAS
. - G. Zhang, J. J. Hu, H. W. Yang, X. J. Wang, S. R. Long and J. Yang, Polymer International, 2012, 61, 800–809 CrossRef CAS
. - G. P. Yu, B. Li, J. L. Liu, S. F. Wu, H. J. Tan, C. Y. Pan and X. G. Jian, Polym. Degrad. Stab., 2012, 97, 1807–1814 CrossRef CAS PubMed
. - S. H. Hsiao, C. W. Chen and G. S. Liou, J. Polym. Sci., Part A: Polym. Chem., 2004, 42, 3302–3313 CrossRef CAS
. - G. S. Liou, H. Y. Lin and H. J. Yen, J. Mater. Chem., 2009, 19, 7666–7673 RSC
. - Y. Rao, A. J. Waddon and R. J. Farris, Polymer, 2001, 42, 5937–5946 CrossRef CAS
. - J. J. Ferreiro, C. J. G. dela, A. E. Lozano and A. J. de, J. Polym. Sci., Part A: Polym. Chem., 2005, 43, 5300–5311 CrossRef CAS
. - F. D. Wang, T. Peng, X. J. Cui, L. Y. Li and X. Q. Li, CN Patent, CN101724935A, 2010
. - C. Y. Song, X. Q. Song, Y. C. Wang, X. Wang and D. Gao, CN Patent, CN101736431A, 2010
. - D. J. Liaw, P. N. Hsu, W. H. Chen and S. L. Lin, Macromolecules, 2002, 35, 4669–4676 CrossRef CAS
. - A. Ballistreri, D. Garozzo, M. Giuffrida and P. Maravigna, Macromolecules, 1986, 19, 2693–2699 CrossRef CAS
. - A. J. Uddin, Y. Ohkoshi, Y. Gotoh, M. Nagura and T. Hara, J. Polym. Sci., Part B: Polym. Phys., 2003, 41, 2878–2891 CrossRef CAS
. - A. J. Uddin, Y. Ohkoshi, Y. Gotoh, M. Nagura and T. Hara, J. Polym. Sci., Part B: Polym. Phys., 2004, 42, 433–444 CrossRef CAS
. - A. J. Uddin, Y. Gotoh, Y. Ohkoshi, M. Nagura, R. Endo and T. Hara, J. Polym. Sci., Part B: Polym. Phys., 2005, 43, 1640–1648 CrossRef CAS
. - A. J. Uddin, Y. Ohkoshi, Y. Gotoh, M. Nagura, R. Endo and T. Hara, Int. Polym. Process., 2006, 21, 263–271 CrossRef CAS
. - H. H. Yang, Aromatic high-strength fibers, Wiley, New York, 1989 Search PubMed
. - S. H. Yang, P. Fu, M. Y. Liu, Y. D. Wang, Z. P. Li and Q. X. Zhao, eXPRESS Polym. Lett., 2010, 4, 346–354 CrossRef CAS
. - W. Z. Wang and Y. H. Zhang, eXPRESS Polym. Lett., 2009, 3, 470–476 CrossRef CAS
. - D. J. Liaw, F. C. Chang, M. K. Leung, M. Y. Chou and K. Muellen, Macromolecules, 2005, 38, 4024–4029 CrossRef CAS
. - H. Y. Huang, Y. T. Lee, L. C. Yeh, J. W. Jian, T. C. Huang, H. T. Liang, J. M. Yeh and Y. C. Chou, Polym. Chem., 2013, 4, 343–350 RSC
. - D. M. T. Tamaki and K. Ichimura, J. Mater. Chem., 2003, 13, 1558–1564 RSC
. - M. Shabanian, N. J. Kang, D. Y. Wang, U. Wagenknecht and G. Heinrich, RSC Adv., 2013, 3, 20738–20745 RSC
. - O. Ivanysenko, S. Strandman and X. X. Zhu, Polym. Chem., 2012, 3, 1962–1965 RSC
. - G. Zhang, H. W. Yang, S. X. Zhang, Y. Zhang, X. J. Wang and J. Yang, J. Macromol. Sci., Part A: Pure Appl.Chem., 2012, 49, 414–423 CrossRef CAS
. - S. H. Yang, P. Fu, M. Y. Liu, Y. D. Wang, Y. C. Zhang and Q. X. Zhao, eXPRESS Polym. Lett., 2010, 4, 442–449 CrossRef CAS
. - T. F. Novitsky, C. A. Lange, L. J. Mathias, S. Osborn, R. Ayotte and S. Manning, Polymer, 2010, 51, 2417–2425 CrossRef CAS PubMed
. - M. Y. Liu, K. F. Li, S. H. Yang, P. Fu, Y. D. Wang and Q. X. Zhao, J. Appl. Polym. Sci., 2011, 122, 3369–3376 CrossRef CAS
. - Y. Song, J. Y. Wang, G. H. Li, Q. M. Sun, X. G. Jian, J. Teng and H. B. Zhang, Polymer, 2008, 49, 724–731 CrossRef CAS PubMed
. - G. Zhang, X. J. Xing, D. S. Li, X. J. Wang and J. Yang, Ind. Eng. Chem. Res., 2013, 52, 16577–16584 CrossRef CAS
. - H. C. Chang, H. T. Lin and C. H. Lin, Polym. Chem., 2012, 3, 970–978 RSC
. - W. H. Li and D. Y. Yan, J. Appl. Polym. Sci., 2003, 88, 2462–2467 CrossRef CAS
.
Footnote |
† Electronic supplementary information (ESI) available. See DOI: 10.1039/c4ra10074c |
|
This journal is © The Royal Society of Chemistry 2014 |
Click here to see how this site uses Cookies. View our privacy policy here.