DOI:
10.1039/C4RA09595B
(Paper)
RSC Adv., 2014,
4, 57996-58004
Characterization and phenolation of biorefinery technical lignins for lignin–phenol–formaldehyde resin adhesive synthesis
Received
1st September 2014
, Accepted 23rd October 2014
First published on 23rd October 2014
Abstract
Technical lignins are cheap, abundant and renewable phenolic substances that have been attracting increasing attention. In this study, the structural features and active sites of four technical lignins obtained from different biorefinery processes were thoroughly characterized. Their suitability for partial incorporation into a phenol–formaldehyde (PF) resin adhesive was also evaluated. Phenolation treatment under alkaline conditions was conducted to enhance the reactivity of the technical lignins. Composition analysis indicated that all four technical lignins had a high purity (>88%). 13C nuclear magnetic resonance (NMR) and gel permeation chromatography (GPC) analyses revealed that the technical lignins from different original feedstocks and biorefinery processes had different structural features, but all of these technical lignins could be used in the synthesis of a lignin–phenol–formaldehyde (LPF) resin adhesive. The structural features and active sites of the different technical lignins before and after phenolation treatment were determined using quantitative two-dimensional heteronuclear single-quantum correlation (2D HSQC) and 31P NMR spectroscopies. The results confirmed that the phenolation treatment under alkaline conditions could effectively increase the number of active sites on the technical lignins and could be easily included in the synthesis process of LPF resin adhesives.
1. Introduction
Advances in genetics, biotechnology, process chemistry and engineering are leading to new manufacturing concepts for converting renewable biomass to valuable fuels and products, which is generally referred to as biorefining.1 With the development of the modern biorefinery industry (bio-ethanol, oligosaccharide, bio-diesel etc.) and the application of this concept in conventional biomass utilization, large amounts of biorefinery technical lignins have been generated. These globally abundant technical lignins have the potential to replace a significant portion of petrochemical feedstocks in the future, if combined with residual lignins produced at emerging advanced lignocellulose biorefineries.2 As phenolic polymers, technical lignins are considered to be potential renewable sources for industrial applications.3 However, being similar to technical lignins from the conventional pulp and paper industry, the complicated structures and compositions of the technical lignins obtained from the modern biorefinery industry restrict their application.4 Currently, a vast quantity of technical lignins are incinerated to produce process steam and energy and only a very small portion are used for the production of value-added products. The current utilization of these technical lignins is a great waste of a valuable renewable resource and the biorefinery enterprises are beset with this problem. It was widely accepted that maximizing the use of all feedstock components, byproducts and waste streams will significantly improve the economic benefit of the biorefinery process.5
The rising cost and foreseeable scarcity of petrochemicals has led many researchers to investigate the use of natural products for preparation of adhesives.6 Because of the structural similarity between lignin and phenol–formaldehyde (PF) resin, phenolic resin is an attractive area for the application of technical lignin.7–9 As a cheap and abundant renewable material, technical lignin can drive down the production costs of phenolic resin adhesives when it is used as a substitution for phenol. The lignin present in plant tissues is referred to as native or natural lignin. In our previous studies, the structural and chemical features of native lignin from various plants have been investigated in detail.10–13 However, the technical lignins obtained from industrial processes are not identical to the native ones in terms of their structural and chemical features. During the industrial delignification process, lignin undergoes significant structural changes. The resulting technical lignins have modified structures and contain impurities that result from the respective processing methods. The final properties of the LPF resin adhesive are significantly dependent on the structural and chemical (active sites) features of the lignin, including the molecular weight, phenolic and aliphatic hydroxyl groups, unsubstituted 3- or 5-positions in phenolic C9 units.14 Thus, a complete characterization of the technical lignin is extremely necessary prior to the synthesis of LPF resin adhesive. Thanks to advances in nuclear magnetic resonance (NMR) technology, it has become the most widely used technique for lignin characterization. NMR provides unambiguous evidence for the specific structure as well as quantitative structural information.23 For example, the type and number of the phenolic and aliphatic hydroxyl groups in lignin can be quantified by 31P-NMR. The number of unsubstituted ortho-position of the phenolic hydroxyl groups in lignin (i.e. active sites during the synthesis of LPF resin adhesive) can be obtained from this result. The active site number can act as a reference for design of a reasonable LPF resin adhesive formulation. Furthermore, the structural features can be obtained using 13C-NMR and two-dimensional heteronuclear single-quantum correlation (2D-HSQC) spectroscopies.
Various technical lignins obtained from the conventional pulp and paper industry have been investigated for preparing lignin–phenol–formaldehyde (LPF) resin adhesive.15–17 Nowadays, more and more studies on technical lignin obtained from modern biorefinery processes for this application are being carried out.18 Unfortunately, a really stable application of LPF resin adhesive in an industrial scale is difficult to be achieved up to now.18 This should be attributed to the low activity of work on technical lignin caused by industry complicacy and inhomogeneity of the lignin structure to some extent. To increase the reactivity of technical lignin and enhance the degree of poly-condensation during LPF resin adhesive synthesis, various modification methods have been applied. The most common reactivity-enhancing processes are phenolation, methylolation and demethylation.19–22 Due to the basic catalyst conditions applied in LPF resin adhesive synthesis, the alkaline phenolation treatment is easily combined into the LPF resin adhesive synthesis process. The liquid mixture obtained after phenolation could be used directly as a starting material for the synthesis of LPF resin adhesive without any further treatment. Therefore, comprehensive consideration of the economy and operability of the formulation, the phenolation treatment of technical lignin under alkaline condition should be a very promising modification method for the preparing of LPF resin adhesive.
In this study, four technical lignins obtained from three different biorefinery processes were characterized using various qualitative and quantitative NMR methods to evaluate their suitability for the production of LPF resin adhesive as a partial substitution for phenol. 13C NMR and 2D HSQC NMR were used to obtain important structural information about the technical lignins, which will facilitate the understanding of the fundamental chemistry of the lignin for further use in the production of LPF resin adhesive. Accurate number of active sites (mmol g−1) of the technical lignins was tested using 31P NMR. The modification mechanism of the technical lignins during the phenolation treatment under an alkaline condition was also investigated.
2. Experimental
2.1. Materials
All of the four biorefinery technical lignins were kindly supplied by three enterprises. Corn cob lignin (L1) was obtained from Shandong Longlive Bio-technology Co., Ltd, China. The general production process for this material was as follows: first, the corn cob was treated hydrothermally to degrade the hemicelluloses and obtain xylo-oligosaccharides. Following this, the residue was treated with an alkaline solution to release lignin and obtained a cellulose-rich residue. The solid residue from this step was used as a feedstock for bio-ethanol production, while the effluent, following alkaline treatment, was adjusted to acidic condition to precipitate the lignin. Poplar wood lignins (L2 and L3) were supplied by Shandong Sun Paper Industry Joint Stock Co., Ltd, China. The general isolation process was as follows: first, the material was treated hydrothermally to eliminate the hemicelluloses and the low molecular weight lignin fraction (L2). Next, the treated solid substance was cooked according to the traditional kraft pulping process. The L3 product was isolated from the black liquor following the kraft pulping process. Wheat straw lignin (L4) was kindly supplied by Geyi Energy Company in Anhui province of China. The general separation process for this material consisted of two steps: first, the wheat straw was treated with a steam explosion technique and then washed with water to recover the degraded hemicelluloses. Next, the treated material was extracted with aqueous alkali under mild condition. The filtrate was passed through a membrane to separate the lignin solution which was spray dried. To eliminate the ash in the lignin, it was further purified to yield product L4. The spray dried lignin was mixed with deionized water and acidified to pH 2 with 20% (w/w) sulfuric acid to precipitate the lignin, which was then recovered by filtration and washed with acidic water to solubilize the residual sugars. All of these four technical lignins were oven dried to a constant weight and stored in dry ambient condition for further use. Sodium hydroxide (NaOH) and phenol were of analytical grade and used as obtained without further purification.
2.2. Phenolation of the technical lignins
To investigate the changes of structure and active sites after phenolation treatment, the dried technical lignins were phenolated under the following alkaline condition. For each experiment, 4.7 g of technical lignin and 4.7 g of phenol were added to a three neck flask. Then, the pH value of the mixture was adjusted to 9–10 using 30 wt% NaOH solution. The temperature of the mixture was raised to 95 °C and held constant for 1 h with constant agitation. The resulting product was poured in a diethyl ether/water solution (1
:
1 v/v) and the pH value of this mixture was adjusted to 2. The precipitated phenolated lignin was isolated by centrifuging and then thoroughly washed with diethyl ether and oven dried in a vacuum dryer at 40 °C to a constant weight.
2.3. Characterization of the technical lignins
The chemical compositions of the four technical lignins were determined according to the standard laboratory analytical procedures developed by the National Renewable Energy Laboratory (NREL/TP-510-42618).24 The analysis of the carbohydrate moieties associated with the four technical lignins was conducted according to a previous study.19 The weight-average (Mw) and number-average (Mn) molecular weights of the four acetylated technical lignins were determined using gel permeation chromatography (GPC) on a PL-gel 10 mm Mixed-B 7.5 mm ID column according to a procedure described by Wen et al.13 NMR spectra were recorded on a Bruker AVIII 400 MHz spectrometer (Germany) at 25 °C according to a previous paper.23 For the 13C NMR and 2D-HSQC analyses, 100 and 80 mg of lignin samples were dissolved in 0.5 mL DMSO-d6, respectively. A quantitative analysis of the intensities of the HSQC cross-signal was performed according to the method given in a previous article.23 31P NMR spectra were acquired after the reaction of lignin with 2-chloro-4,4,5,5-tetramethyl-1,3,2-dioxaphospholane (TMDP) according to a previous literature.25 The parameters used in quantitative 31P NMR experimental were listed as follows: the 30° pulse angle; 2 s relaxation delay (d1); 64 K data points, and 1024 scans.
3. Results and discussion
3.1. Composition and GPC analyses of the technical lignins
Table 1 shows the results of composition and GPC analyses of the four technical lignins. Product L1 obtained from the corn cob residue after hydrolysis of the hemicelluloses had the highest purity (94.42%) among the four technical lignins. The content of associated carbohydrates in L2 was higher than that in the other technical lignins, because most of hemicelluloses in poplar wood were hydrolyzed during the hydrothermal treatment process and dissolved in hydrolysate together with the dissolved lignin. Consequently, the content of associated carbohydrates in the subsequent product L3 was very low (0.61%), which was due to the pre-hydrolysis of hemicelluloses. However, the kraft pulping process led to a high content of ash in L3 as compared with L2. These results indicated that the composition and purity of the technical lignin was dependent to some extent on the delignification method and isolation process. However, the lignin content of these four technical lignins was more than 88%. The acid-soluble and acid-insoluble lignins both reacted with formaldehyde when lignin was incorporated with phenol and formaldehyde during the synthesis process of LPF resin adhesive.22 Thus, the technical lignin with a high purity is more suitable for the production of LPF resin adhesive. The remained carbohydrates in technical lignin also affect the feasibility of the lignin used in LPF resin adhesive. Generally, the carbohydrates would reduce the water resistance of the cured LPF resin adhesive and produced more formaldehyde during the hot-pressing process.26
Table 1 The chemical composition and molecular weight of the biorefinery technical lignins
Composition (%) |
L1 |
L2 |
L3 |
L4 |
ND: not detected. |
Total lignin |
94.42 |
88.56 |
88.95 |
88.85 |
Klason lignin |
90.81 |
82.38 |
81.92 |
85.03 |
Acid-soluble lignin |
3.61 |
6.18 |
7.03 |
3.82 |
Carbohydrate content |
0.63 |
5.01 |
0.61 |
2.67 |
Arabinose |
0.13 |
0.13 |
0.04 |
0.24 |
Galactose |
0.02 |
0.40 |
0.02 |
0.16 |
Glucose |
0.32 |
0.91 |
0.12 |
0.48 |
Xylose |
0.13 |
3.19 |
0.43 |
1.75 |
Mannose |
0.03 |
0.25 |
NDa |
0.04 |
Glucuronic acid |
ND |
0.10 |
ND |
ND |
Galacturonic acid |
ND |
0.03 |
ND |
ND |
Ash |
2.16 |
2.49 |
5.39 |
3.00 |
Others |
2.79 |
3.94 |
5.05 |
5.44 |
Mw (g mol−1) |
3258 |
1830 |
1840 |
4330 |
Mn (g mol−1) |
2260 |
900 |
910 |
2700 |
Mw/Mn |
1.44 |
2.03 |
2.02 |
1.60 |
The weight-average (Mw) and number-average (Mn) molecular weights, and polydispersity (Mw/Mn) of the four technical lignins are listed in Table 1. L2 and L3 obtained from poplar wood both had relatively low molecular weights. L2 was obtained from the effluent liquor of the poplar wood following hydrothermal treatment. This treatment mainly eliminated the hemicelluloses and low molecular weight lignin fraction of the starting feedstock. L3 was mainly comprised of S-type units, as revealed by the 2D HSQC spectrum in the following section. Since the ortho-positions of S-type phenolic –OH in lignin units were blocked by methoxy groups, S units were mainly linked with other phenylpropane units through the ether bond (mainly β-O-4 linkage). Generally, the ether bond is broken during the kraft pulping.27 Thus, the molecular weight of L3 was relatively low. However, the relatively low molecular weight of L3 was not only related to the kraft pulping, but also affected by the hydrothermal treatment. It has been reported that fragmented lignin fractions were more suitable for reacting with formaldehyde, due to its abundant active sites.26 Therefore, L2 and L3 would be ideal feedstocks for the synthesis of the LPF resin adhesive. By contrast, the molecular weights of L1 and L4 were higher than those of L2 and L3. In most case, due to the inherent drawback of lignin macromolecular structure, technical lignin with a high molecular weight used in LPF resin adhesive resulted in a more heterogeneous structure in the cured LPF resin adhesive, especially at a high lignin substitution rate for phenol. This would be harmful to the performance of the prepared LPF resin adhesive. However, some previous studies have also reported that lignin with a high molecular weight could be used in phenolic resin.17,28 Thus, the high molecular weight lignins L1 and L4 could also be potential materials for the synthesis of LPF resin adhesive. Besides molecular weight, the polydispersity value is also an important index for evaluating the structural features of lignin. The data reveal that the polydispersity value of L1 and L4 were lower than those of L2 and L3. Basically, lignin with a low polydispersity value is more suitable for the synthesis of LPF than that with a high polydispersity value.
3.2. 13C NMR analysis of the technical lignins
13C NMR spectroscopy is a reliable method for investigating the structural features of lignin and it also provides a more comprehensive view of the entire lignin macromolecule. The 13C NMR spectra of the four technical lignins are shown in Fig. 1. The detail assignments of these lignins were achieved by a recent publication about NMR characterization of lignin.23 The signals of typical herbaceous lignin, i.e. ferulic acid (FA) (C2 at 110.7 ppm, C6 at 123.1 ppm and C8 at 115.2 ppm) and p-coumaric acid (PCA) (C2,6 at 130.2 ppm, C7 at 144.8 ppm and C8 at 113.7 ppm) were found in the spectra of L1 and L4. The signals of the β-O-4 linkages (Cα at 71.5 ppm and Cβ at 83.9 ppm) in the side chain of the lignin units were very weak in all the spectra of the four technical lignins, especially in the spectrum of L3. However, the signals of β-O-4 alkyl–aryl ethers of the original lignin were obviously stronger than those of the corresponding technical lignins.10–13 This indicated that the β-O-4 linkages of the original lignin in the raw materials have been cleaved significantly during the biorefinery processes.
 |
| Fig. 1 13C NMR spectra of the four biorefinery technical lignins. | |
It was clear that the signals of aromatic condensed C–C structure at 124–140 ppm could be observed in the spectra of the four technical lignins. The intensities of the signals were relatively stronger in the spectra of L1 and L4 than those of L2 and L3. It was not surprising to note the low content of carbon–carbon condensed structures in L2 and L3, since a high proportion of S-type units in L2 and L3 was revealed by the 2D HSQC spectra. Higher proportions of G-type units in L1 and L4 would lead to the formation of more aromatic carbon–carbon linkages8 and these stable linkages were not broken during the biorefinery processes. Furthermore, the strong condensed C–C linkage signals in the spectra of L1 and L4 indicated that a possible condensation reaction between the low molecular weight intermediates may have occurred during the corresponding biorefinery processes. Therefore, although the signals of β-O-4 linkages in the spectra of L1 and L4 were relatively weak, their molecular weights were higher than those of L2 and L3. The mechanical performance of the cured LPF resin was significantly dependent on the structural features of its composition. The condensed C–C linkages had relatively high bond energy. Therefore, a high proportion of the condensed C–C linkages between lignin units would favor the mechanical stability of the cured bond line of the LPF resin adhesive.
3.3. 2D HSQC NMR analyses of the unphenolated and phenolated technical lignins
A typical, 2D HSQC NMR spectrum of the lignin shows three regions corresponding to aliphatic, side chain and aromatic 13C–1H correlations. In this study, lignin contours in the HSQC spectra were assigned based on the previous literature reports.29–32 The aliphatic (nonoxygenated) region shows signals with no structural information and; therefore, is not discussed herein. The side-chain (δC/δH 50–90/2.5–6.0) and the aromatic (δC/δH 100–135/5.5–8.5) regions of the HSQC spectra of these four technical lignins are shown in Fig. 2 and the main substructures are depicted in Fig. 4. The main cross-signals in the aromatic regions of the HSQC spectra corresponded to the different aromatic lignin units. Because of the existence of FA and PCA in the cell walls of herbaceous plants, the spectra of L1 and L4 had corresponding correlations in the aromatic region. Similarity, these correlated signals were also observed in aforementioned 13C NMR spectra. H, G and S type units which were easily identified by their corresponding correlations. Signals of oxidized S2,6 could also be found in the spectra of these four technical lignins. When compared with the milled wood lignins (MWLs) obtained from the respective starting materials of the four technical lignins as reported in the previous literature,18–21 the intensity of the main signals corresponding to typical β-O-4 substructures (Cα–Hα at δC/δH 71.5/4.83, Cβ–Hβ at δC/δH 84.0/4.35 and 85.6/4.08) were significantly decreased, especially in the spectra of L1 and L3. The cleavage of the ether bonds in the original lignin led to the depolymerization of lignin during the biorefinery process and new free phenolic hydroxyl groups in lignin were produced. Thus, more active sites, which could participate in the synthesis of LPF resin adhesive, could be discovered and defined in the technical lignin. The intensity of the signals corresponding to the Cβ–Hβ of β–β linkages located at δC/δH 71.3/3.8 and 4.16 were also lower than those of the MWLs obtained from the starting materials.18–21 The spectra of the phenolated technical lignins are plotted in Fig. 3.
 |
| Fig. 2 2D HSQC NMR spectra of the four biorefinery technical lignins. | |
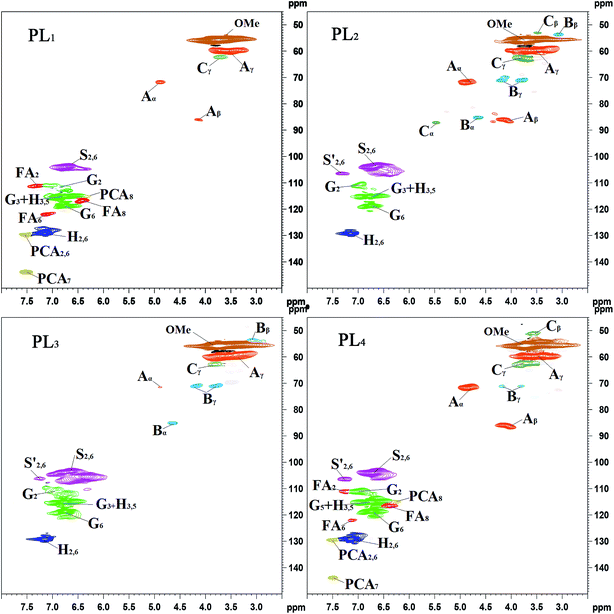 |
| Fig. 3 2D HSQC NMR spectra of the phenolated biorefinery technical lignins. | |
 |
| Fig. 4 (A) β-O-4 alkyl–aryl ethers; (B) resinols; (C) phenylcoumarans; (PCA) p-coumaric acid; (FA) ferulic acid; (H) p-hydroxyphenyl units; (G) guaiacyl units; (S) syringyl units; (S′) oxidized syringyl units bearing a carbonyl at Cα. | |
To obtain explicit structural information of the technical lignins, a quantification of lignin based on 2D-HSQC NMR spectroscopy was conducted.23 Both the unphenolated and phenolated technical lignins were analyzed and the results are given in Table 2. Clearly, L3 contained trace amount of β-O-4 and β-5 substructures, which would be due to the severe kraft pulping conditions. However, L2 had a relatively high content of β-O-4, β–β and β-5 linkages. This was probably due to the moderate conditions applied in the hydrothermal treatment process. Both L2 and L3 had higher contents of S-type units than L1 and L4 as shown by the S/G/H ratio in Table 2. Due to the blocked ortho- and para-positions of the phenolic –OH in S-type units, the high S-type proportion was disadvantageous for its further utilization in the LPF resin adhesive. The proportions of G-type units in L1 and L4 were higher than those of L2 and L3. Generally, lignin with more G- and H-type units suggested that it had more active sites. The proportions of H-type units in L2, L3, and L4 were all extremely low as compared to L1. This implied that L1 may be an ideal material for the synthesis of LPF resin adhesive among the four technical lignins.
Table 2 The content of the main interunit linkages (expressed per 100Ar) and S/G/H ratio of the unphenolated and the phenolated biorefinery technical lignins
Sample |
β-O-4 |
β–β |
β-5 |
S/G/H |
T means trace. PL means the phenolated lignin. |
L1 |
10.17 |
Ta |
T |
40 : 29 : 31 |
L2 |
25.34 |
8.82 |
2.92 |
85 : 12 : 3 |
L3 |
T |
2.42 |
T |
82 : 13 : 5 |
L4 |
26.13 |
T |
T |
59 : 32 : 9 |
PL1b |
10.01 |
T |
T |
20 : 16 : 64 |
PL2 |
28.07 |
8.78 |
3.35 |
36 : 13 : 51 |
PL3 |
T |
2.83 |
T |
42 : 14 : 44 |
PL4 |
28.54 |
T |
T |
51 : 13 : 36 |
The quantification results revealed that no obvious changes of β-O-4, β–β, and β-5 linkages of the phenolated technical lignins could be found as compared to those of the unphenolated technical lignins (Table 2). The S/G/H ratios obtained based on the volume integral quantity of the G2, S2,6 and H2,6 of all the lignin samples are also listed in Table 2. The results illustrated that the proportion of H units in the phenolated technical lignins increased significantly as compared to those of the unphenolated technical lignins. The increase of H units could be caused by the introduction of phenol. It is widely accepted that the increase of H units in lignin can improve its reactivity in the synthesis process of LPF resin adhesive, and; therefore, make the lignin embedded in PF resin system more easily.
3.4. 31P NMR analysis of the unphenolated and phenolated technical lignins
31P NMR analysis involving phosphorylation of hydroxyl groups followed by quantitative analysis in the presence of an internal standard allows quantification of all –OH groups present in lignin. Therefore, the total content of potential active sites for application in LPF adhesive synthesis can be obtained using 31P NMR analysis.33 The 31P NMR spectra of the technical lignins and their phenolated products are shown in Fig. 5 and the quantitative data on the distribution of the various –OH groups are listed in Table 3. The assignments and calculation methods were accomplished according to a previous literature report.25 Generally, the unsubstituted ortho position of G- and H-type phenolic –OH in lignin are considered to be the active sites in the synthesis of LPF resin adhesive. The content of H-type phenolic-OH in L1 was the highest (0.65 mmol g−1) of these four technical lignins, which was due to the highest proportion of H units (S/G/H = 40
:
29
:
31). The other reason for this could be that corn cob is a gramineous biomass and a large amount of PCE were associated with its lignin, which were identified by the aforementioned 2D HSQC analysis. L4 was also obtained from a gramineous biomass (wheat straw), but the content of H-type phenolic –OH in this lignin was relatively low (0.25 mmol g−1). This difference may be due to the two different delignification and isolation methods. Although the noncondensed G-type phenolic –OH in L4 was more than that in L1, the total number of active sites in L1 was more than that in L4. High contents of S-type –OH were found in L2 and L3, and their H-type phenolic-OH contents were also very low. However, the contents of G-type –OH in the two hardwood technical lignins were higher than those in L1 and L4. In short, more active sites in technical lignin would make it more suitable for the synthesis of LPF resin adhesive. With this point of view, L1 should be the best choices for this purpose. Furthermore, considering the chemical reaction, the LPF resin adhesive formulation designed based on active sites number should be more advantageous for obtaining a high performance and low formaldehyde emission LPF resin adhesive.
 |
| Fig. 5 31P NMR spectra of the four biorefinery technical lignins before and after pehnolation treatment under the alkaline condition. | |
Table 3 The content of the different hydroxyl groups and active sites (mmol g−1) quantified by 31P NMR of the unphenolated and the phenolated biorefinery technical lignins
Sample |
–OH (mmol g−1) |
Active sites (mmol g−1) |
Total S |
Total G |
Noncondensed phenolic |
Total –COOH |
Total aliphatic |
S |
G |
H |
PL means the phenolated lignin. |
L1 |
0.65 |
0.64 |
0.55 |
0.42 |
0.65 |
1.09 |
1.77 |
1.72 |
L2 |
1.59 |
0.88 |
1.32 |
0.59 |
0.11 |
0.20 |
1.83 |
0.81 |
L3 |
2.20 |
1.27 |
1.72 |
0.95 |
0.22 |
0.51 |
1.09 |
1.39 |
L4 |
0.53 |
0.70 |
0.45 |
0.49 |
0.25 |
0.88 |
2.65 |
0.99 |
PL1a |
0.61 |
0.77 |
0.51 |
0.62 |
1.26 |
0.28 |
1.96 |
3.14 |
PL2 |
1.60 |
0.92 |
1.30 |
0.59 |
0.82 |
0.30 |
2.02 |
2.23 |
PL3 |
1.85 |
1.22 |
1.41 |
0.80 |
0.70 |
0.44 |
0.89 |
2.20 |
PL4 |
0.53 |
0.71 |
0.42 |
0.49 |
1.34 |
0.86 |
1.84 |
3.17 |
The data in Table 3 show that the contents of total S-type phenolic –OH of all these technical lignins were almost no changes during the phenolation treatment. Only slight changes of G-type phenolic –OH were found in the phenolated technical lignins as compared to the unphenolated technical lignins. These results indicated that no obvious cleavage of β-O-4 linkages occurred during the phenolation process in the present study. These results are also in agreement with those obtained from the 2D HSQC NMR spectra. However, a notable increase of H-type phenolic –OH in all the phenolated technical lignins was evident. The increase of H-type phenolic –OH was mainly ascribed to the effective crosslinking of phenol on the lignin molecules under alkaline condition. It has been reported that the phenol would be introduced to α position of side chain in lignin units during the phenolation process.34,35 The increase of the H-type phenolic –OH indeed increased the active sites of the phenolated technical lignins. The synthesis and application of LPF resin adhesives prepared with these four biorefinery technical lignins is reported in the following report of this research series.
4. Conclusions
The composition, structural features and reactivity of the four biorefinery technical lignins were investigated in the present study. Considering the reactivity of the lignin, the corn cob lignin (L1) should be the best feedstock for the synthesis of LPF resin adhesive among the four technical lignins tested. Phenolation treatment under the alkaline condition can effectively increase the active sites of the technical lignins and can be easily combined with the synthesis process of LPF resin adhesive. The comprehensive investigation of the technical lignins and their phenolation process provides reasonable guidance for their further utilization in LPF resin adhesive.
Acknowledgements
We are grateful for financial support of this research from State Forestry Administration (201404617), National Science Foundation of China (31110103902) and the open fund project of State Key Laboratory of Pulp and Paper Engineering, South China University of Technology, China (201364).
References
- A. J. Ragauskas, C. K. Williams, B. H. Davison, G. Britovsek, J. Cairney, C. A. Eckert, W. J. Frederick Jr, J. P. Hallett, D. J. Leak, C. L. Liotta, J. R. Mielenz, R. Murphy, R. Templer and T. Tschaplinski, Science, 2006, 311, 484–489 CrossRef CAS PubMed.
- V. K. Gupta, M. Tuohy, C. P. Kubicek, J. Saddler and F. Xu, Bioenergy Research: Advances and Applications, Elsevier, Waltham, 2013 Search PubMed.
- F. G. Calvo-Flores and J. A. Dobado, ChemSusChem, 2010, 3, 1227–1235 CrossRef CAS PubMed.
- A. G. Vishtal and A. Kraslawski, BioResources, 2011, 6, 3547–3568 Search PubMed.
- S. Fernando, S. Adhikari, C. Chandrapal and N. Murali, Energy Fuels, 2006, 20, 1727–1737 CrossRef CAS.
- G. Váquez, G. Antorrena, J. Gonzáilez and J. Mayor, Bioresour. Technol., 1995, 51, 187–192 CrossRef.
- M. H. Hussin, A. A. Rahim, M. N. Mohamad Ibrahim and N. Brosse, Ind. Crops Prod., 2013, 49, 23–32 CrossRef CAS PubMed.
- A. Tejado, C. Pena, J. Labidi, J. M. Echeverria and I. Mondragon, Bioresour. Technol., 2007, 98, 1655–1663 CrossRef CAS PubMed.
- M. Turunen, L. Alvila, T. T. Pakkanen and J. Rainio, J. Appl. Polym. Sci., 2003, 88, 582–588 CrossRef CAS.
- R. C. Sun, B. Xiao and J. M. Lawther, J. Appl. Polym. Sci., 1998, 68, 1633–1641 CrossRef CAS.
- T. Q. Yuan, S. N. Sun, F. Xu and R. C. Sun, J. Agric. Food Chem., 2011, 59, 10604–10614 CrossRef CAS PubMed.
- S. N. Sun, M. F. Li, T. Q. Yuan, F. Xu and R. C. Sun, Ind. Crops Prod., 2013, 43, 570–577 CrossRef CAS PubMed.
- J. L. Wen, S. L. Sun, B. L. Xue and R. C. Sun, Holzforschung, 2013, 67, 613–627 CrossRef CAS.
- N. E. El Mansouri and J. Salvadó, Ind. Crops Prod., 2006, 24, 8–16 CrossRef CAS PubMed.
- B. Danielsona and R. Simonsonb, J. Adhes. Sci. Technol., 1998, 12, 923–939 CrossRef PubMed.
- M. V. Alonso, M. Oliet, F. Rodríguez, G. Astarloa and J. M. Echeverría, J. Appl. Polym. Sci., 2004, 94, 643–650 CrossRef CAS.
- A. Pizzi, J. Adhes. Sci. Technol., 2006, 20, 829–846 CrossRef CAS PubMed.
- W. Zhang, Y. F. Ma, C. P. Wang, S. H. Li, M. M. Zhang and F. X. Chu, Ind. Crops Prod., 2013, 43, 326–333 CrossRef CAS PubMed.
- G. Vazquez, J. Gonzalez, S. Freire and G. Antorrena, Bioresour. Technol., 1997, 60, 191–198 CrossRef CAS.
- A. R. Goncalve and P. Benar, Bioresour. Technol., 2001, 79, 103–111 CrossRef.
- Y. J. Ma, X. Zhao, X. Chen and Z. C. Wang, Colloids Surf., 2011, 377, 284–289 CrossRef CAS PubMed.
- M. Oilvares, J. A. Guzman, A. Natho and A. Saavedra, Wood Sci. Technol., 1988, 22, 157–165 CrossRef.
- J. L. Wen, S. L. Sun, B. L. Xue and R. C. Sun, Materials, 2013, 6, 359–391 CrossRef CAS PubMed.
- A. Sluiter, B. Hames, R. Ruiz, C. Scarlata, J. Sluiter, D. Templeton and D. Crocker, Determination of structural carbohydrates and lignin in biomass, Laboratory Analytical Procedure, NREL Research Group Report NREL/TP-510–42618, Colorado, 2008 Search PubMed.
- C. Crestini and D. S. Argyropoulos, J. Agric. Food Chem., 1997, 45, 1212–1219 CrossRef CAS.
- A. Pizzi and K. L. Mittal, Handbook of adhesive technology, revised and expanded, Marcel Dekker, New York, 2003 Search PubMed.
- N. E. El Mansouri, Q. L. Yuan and F. R. Huang, BioResources, 2011, 6, 2647–2662 CAS.
- A. Pizzi, Wood adhesives chemistry and technology, Dekker, New York, 1989 Search PubMed.
- J. C. del Rio, J. Rencoret, P. Prinsen, A. T. Martinez, J. Ralph and A. Gutierrez, J. Agric. Food Chem., 2012, 60, 5922–5935 CrossRef CAS PubMed.
- A. T. Martinez, J. Rencoret, G. Marques, A. Gutierrez, D. Ibarra, J. Jimenez-Barbero and J. C. del Rio, Phytochemistry, 2008, 69, 2831–2843 CrossRef CAS PubMed.
- E. A. Capanema, M. Y. Balakshin and J. F. Kadla, J. Agric. Food Chem., 2004, 52, 1850–1860 CrossRef CAS PubMed.
- E. A. Capanema, M. Y. Balakshin and J. F. Kadla, J. Agric. Food Chem., 2005, 53, 9639–9649 CrossRef CAS PubMed.
- F. Monteil-Rivera, M. Phuong, M. Ye, A. Halasz and J. Hawari, Ind. Crops Prod., 2013, 41, 356–364 CrossRef CAS PubMed.
- M. V. Alonso, M. Oliet, F. Rodríguez, J. García, M. A. Gilarranz and J. J. Rodríguez, Bioresour. Technol., 2005, 96, 1013–1018 CrossRef CAS PubMed.
- Y. Matsushita, H. Sano, M. Imai, T. Imai and K. Fukushima, J. Wood Sci., 2007, 53, 67–70 CrossRef CAS PubMed.
|
This journal is © The Royal Society of Chemistry 2014 |
Click here to see how this site uses Cookies. View our privacy policy here.