DOI:
10.1039/C4RA08850F
(Paper)
RSC Adv., 2014,
4, 48676-48681
A triblock-copolymer-templating route to carbon spheres@SBA-15 large mesopore core–shell and hollow structures†
Received
18th August 2014
, Accepted 16th September 2014
First published on 16th September 2014
Abstract
The fabrication of mesoporous core–shell and hollow spheres with ordered mesostructures and tunable large pore sizes is highly desirable for fundamental research and practical applications. A direct triblock-copolymer-templating coating approach has been provided for the synthesis of carbon sphere@mesoporous silica core–shell (CS@SBA-15) and hollow structures in an acidic medium at room temperature. These CS@SBA-15 core–shell structures possess large mesopores (6.3–8.4 nm), high surface areas (318.1–438.4 m2 g−1) and large pore volumes (0.31–0.36 cm3 g−1). The corresponding hollow mesoporous silica spheres (HMSS) with controllable mesopores (6.0–8.2 nm), high surface areas (239.9–326.5 m2 g−1) and pore volumes (0.37–0.62 cm3 g−1) can be obtained after the removal of the carbon sphere cores through calcination at 700 °C in air. The current research results provide an effective methodology for the synthesis of other mesoporous silica core–shell structures with large pore sizes and multilayer core–shells, and even nanorattle structures.
1. Introduction
Recently, core–shell structures have attracted considerable interest owing especially to their nanoarchitectures, alterable compositions and sizes, which endow these materials with multifunctional properties, such as magnetic, electrical, optical, thermodynamics and catalytic properties, and thus have extensive applications in areas such as biology, physics, material science and catalysis.1–4 At present, core–shell materials with functional core and different shell compositions such as polymer, carbon, metal, silica and mesoporous silica have been successfully synthesized.5–9 Regarding the diverse kinds of core–shell structures, mesoporous silica coated inorganic nanomaterials have attracted considerable attention in recent years because the mesoporous silica shells can serve as an initial isolated interface and easily modifiable surface, and also provide a high surface area, large pore volume and readily accessible pore channels.10 Until now, mesoporous silica coated core–shell structures with diversified functional cores, such as Au@mSiO2,11 Pt@mSiO2,12 Fe3O4/SiO2/Au@mSiO2,13 γ-Fe2O3@nSiO2@mSiO2,14 β-NaYF4@SiO2@mSiO2,10 carbon nanotubes@mSiO2 and SiO2@mSiO2, have been reported.15,16 Moreover, these core–shell nanocomposites present excellent properties in catalysis,12,17 adsorption,18 drug delivery,19 biological imaging and photodynamic therapy.20–22 Although much effort has been focused on the synthesis approaches for mesoporous silica coated core–shell structures with n-octadecyltrimethoxysilane (C18TMS)23 and hexadecyltrimethylammonium bromide (CTAB) as surfactants,17,18,20 the general pore size of the mesoporous silica shell is around 2–3 nm. Consequently, one of the obstacles toward practical applications is the small pore size of mesoporous silica, due to the tedious synthesis methods. Therefore, the development of core–shell structures with large pore size mesoporous silica shells is necessary.24–26
In addition, hollow mesoporous silica spheres, possessing accessible chambers, large surface areas, uniform pore sizes, good biocompatibilities and surface functionalities, have revealed significant applications in many fields, e.g., adsorption, drug-delivery carriers, sensors, and catalysis.27–30 Traditionally, hollow mesoporous silica spheres are fabricated by an organic soft template and a sacrificial hard template. The soft template method usually requires strict control of the reaction conditions because the soft templates, such as micelles, emulsions, polymers and bubbles, are sensitive to the reaction environment.29–33 Particularly, polymer lattices, carbon spheres and metal oxides can serve as hard templates with various morphologies, controllable sizes and easily removable properties.34,35 Therefore, the hollow mesoporous silica spheres can be prepared with changeable particles sizes, tunable cavities and morphologies via the hard template methods.
Since Li and coworkers reported a simple hydrothermal method to synthesize carbon spheres with different sizes using glucose as the precursor,36 a variety of metal oxide hollow spheres have been prepared by utilizing carbonaceous microspheres as a removable template, attributing to the carbon spheres' hydrophilic surface and functional groups, i.e. OH and C
O.37,38 Although carbon spheres have been generally applied in the synthesis of all types of hollow structures,39 there are few studies on the synthesis of large mesopore silica encapsulating carbon spheres.40,41 Moreover, from the viewpoint of methodology, there are few reports on the controllable approach for the synthesis of mesoporous silica core–shell and hollow structures with large pore sizes and changeable cores by using triblock copolymers as the surfactant.24
Herein, we report a direct triblock-copolymer-templating coating strategy to synthesize the large mesoporous silica-coated carbon spheres core–shell structure (CS@SBA-15) and hollow mesoporous silica spheres (HMSS) by using Pluronic P123 (PEO20–PPO70–PEO20) as a surfactant template, tetraethyl orthosilicate (TEOS) as the silica source, and anhydrous magnesium sulfate as the inorganic salt in HCl solution at room temperature. These CS@SBA-15 and HMSS present ordered mesostructures, high surface areas and large pore size distributions. The pore size of the mesoporous silica shell can be adjusted in the range of 6.3–8.4 nm via changing the reaction conditions, including the hydrothermal temperature and the amount of anhydrous magnesium sulfate.
2. Experimental section
2.1. Chemicals
All chemicals were of analytical grade and used without further purification. Glucose, hydrochloric acid, anhydrous magnesium sulfate, tetraethyl orthosilicate (TEOS) and hexadecyltrimethylammonium bromide (CTAB) were purchased from Sinopharm Chemical Reagent Co. (China). Triblock poly(ethylene oxide)-b-poly(propylene oxide)-b-poly(ethylene oxide) copolymer Pluronic P123 (PEO20–PPO70–PEO20) was purchased from Acros Corp. Note that deionized water was used in all experiments.
2.2. Synthetic route
2.2.1 Preparation of carbon spheres. The carbon spheres (CS) were prepared by the hydrothermal polymerization of glucose according to a previously reported method.36 Briefly, 2.73 g of glucose was dissolved in 25 mL of deionized water and stirred for 20 minutes to form a clear solution. Subsequently, the solution was transferred into a 30 mL of Teflon-sealed autoclave for the hydrothermal treatment at 180 °C for 8 h. The black samples were obtained by continuous centrifugation at 5000 rpm for 5 min and washed with water and ethanol. The final products were obtained after vacuum-drying at 40 °C for 12 h.
2.2.2 Synthesis of CS@SBA-15 and hollow mesoporous silica spheres. CS@SBA-15 core–shell structures were synthesized using a nonionic copolymer as a surfactant and TEOS as the silica source in an acidic medium. In a typical procedure, 0.06 g of P123 and 0.18 g of anhydrous magnesium sulfate were dissolved in 30 mL of 2 M hydrochloric acid. Then, 0.15 g of carbon spheres was added into the above transparent solution with ultrasonication for 30 min. Finally, 0.15 g of TEOS was added dropwise to the mixture and stirred for 24 h before being transferred to an autoclave and heated at 100 °C for 24 h. The precipitate was obtained by centrifugation and washed with water and ethanol for three cycles. Then, the black powder was dried in a vacuum oven at 40 °C for more than 6 h. The large mesopore silica coated carbon sphere samples (CS@SBA-15) were obtained after calcination at 350 °C for 5 h under a nitrogen atmosphere with the heating rate of 1 °C min−1. The carbon sphere core was removed at 700 °C for 3 h in air, and then the hollow mesoporous silica spheres with a large pore size (HMSS) were formed. The CS@SBA-15 100H and HMSS 100H were prepared with the hydrothermal treatment at 100 °C for 24 h without the addition of anhydrous magnesium sulfate. The CS@SBA-15 130H-MgSO4 and HMSS 130H-MgSO4 were synthesized with anhydrous magnesium sulfate as the inorganic salt and hydrothermal treatment at 130 °C for 24 h. The traditional mesoporous silica hollow spheres were obtained by using carbon spheres as a core, CTAB as the surfactant, TEOS as the silica source in ammonia–ethanol–water solution and then calcined at 700 °C in air.
2.3. Characterization
Scanning electron microscopy (SEM) images were obtained on a Philip XL30 microscope. A thin film of gold was sprayed on the sample before characterization. Transmission electron microscopy (TEM) measurements were achieved on a JEOL 2011 microscope operating at 200 kV. The samples were suspended in ethanol and dried on a holey carbon film on a Cu grid for TEM measurements. Nitrogen sorption isotherms were measured at 77 K with a Micromeritics Tristar 3020 analyzer (USA). Before measurement, the samples were degassed in a vacuum at 180 °C for at least 6 h. The Brunauer–Emmett–Teller (BET) method was utilized to calculate the specific surface areas (SBET) by using the adsorption data in a relative pressure range from 0.04 to 0.2. The pore volume and pore size distributions were derived from the adsorption branches of the isotherms by using the Barrett–Joyner–Halenda (BJH) model. The total pore volume Vt was estimated from the amount adsorbed at a relative pressure P/P0 of 0.995. The small angle X-ray diffraction (XRD) patterns were recorded on a Bruker D4 X-ray diffractometer (Germany) with Ni-filtered Cu Kα radiation (40 kV, 40 mA).
3. Results and discussion
The large mesopore silica coated carbon spheres with a core–shell structure (CS@SBA-15) and the corresponding hollow mesoporous silica spheres (HMSS) are fabricated via three steps. As described in Scheme 1, first, carbon spheres are prepared as the core. Then, the large mesopore silica is coated on the surface of the carbon spheres by using Pluronic P123 as the surfactant template under an acidic system. Subsequently, the removal of surfactant P123 and the carbon sphere core yielded CS@SBA-15 and HMSS, respectively.
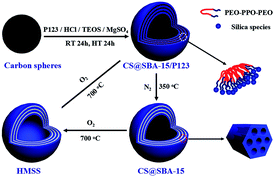 |
| Scheme 1 The preparation procedure for the large mesopore coated carbon sphere core–shell structure (CS@SBA-15) and the corresponding hollow mesoporous silica spheres (HMSS). | |
The carbon spheres are prepared with a hydrothermal method by using glucose as the carbon species. Fig. 1A shows a typical scanning electron microscopy (SEM) image of carbon spheres with an average diameter of about 550–650 nm. These uniform spheres with smooth surfaces possess hydrophilic properties and can resist the etching under a strong acid system; therefore, the carbon spheres can interact with the triblock copolymer P123 and silica source TEOS in the acidic medium. After sintering the as-made samples under a nitrogen atmosphere at 350 °C to remove the triblock copolymer surfactant, the CS@SBA-15 core–shell structure is obtained. As shown in Fig. 1B, the CS@SBA-15 products are all spherical on a large-scale, indicating the uniform coating process. Interestingly, the surface of these spherical samples become rough and tend to aggregate, as well as some strip-like structure can be observed, revealing the successful coating of the mesoporous silica. The morphology and microstructure of the obtained CS@SBA-15 are further characterized by transmission electron microscopy (TEM). The TEM image shows that the carbon spheres have been all coated by the homogeneous mesoporous silica with a thickness of 120–150 nm (Fig. 2A). The magnified TEM image further reveals the typical core–shell structure. Moreover, the shell is composed of many mesopore channels with a pore size of 6.5 nm and wall thickness of about 6 nm (Fig. 2B). It is noteworthy that the mesoporous silica shell shows a parallel mesoporous regional trend and some stripe-like mesochannels in the [110] direction, thus demonstrating a 2-D hexagonal ordered mesostructure (Fig. 2B). This result is in good agreement with the typical TEM images of SBA-15 mesoporous silica reported elsewhere.42
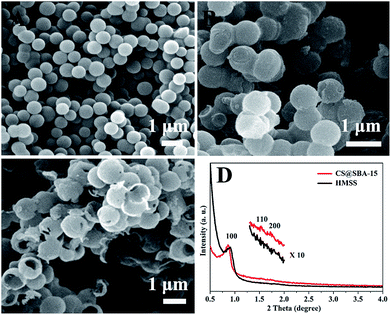 |
| Fig. 1 SEM images of (A) carbon spheres prepared through a hydrothermal method by using glucose as the carbon species, (B) large mesopore silica coated carbon spheres (CS@SBA-15) core–shell structures prepared by using carbon spheres as a core, Pluronic P123 as the surfactant template, TEOS as the silica source, anhydrous magnesium sulfate as the inorganic salt in HCl solution with hydrothermal treatment at 100 °C for 24 h and calcination at 350 °C for 5 h under a nitrogen atmosphere, (C) hollow mesoporous silica spheres (HMSS) after calcination at 700 °C for 3 h in air, (D) small-angle X-ray diffraction pattern of CS@SBA-15 and HMSS. | |
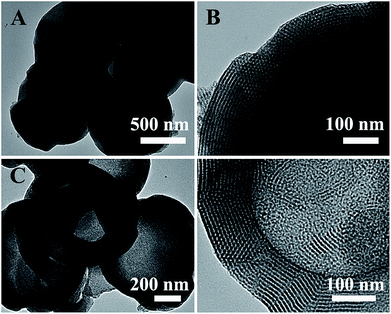 |
| Fig. 2 TEM images of (A) and (B) CS@SBA-15 core–shell structures after calcination at 350 °C for 5 h under a nitrogen atmosphere; (C) and (D) HMSS after calcination at 700 °C for 3 h in air. | |
The small-angle X-ray diffraction (XRD) pattern for CS@SBA-15 shows an obvious diffraction peak at 2θ = 0.86°, which is attributed to the (100) reflection associated with the p6mm hexagonal symmetry (Fig. 1D), indicating an ordered mesostructure. The N2 sorption isotherms of CS@SBA-15 (Fig. 3A) present typical type IV curves with a capillary condensation step at the broad relative pressure (P/P0) of 0.5–0.7, suggesting the uniform large pore size. The hysteresis loops are classified to be the H1-type, assigned to narrow pore size distributions and 1D cylindrical channels. The pore size calculated using the Barrett–Joyner–Halenda (BJH) analysis with the adsorption branch shows a narrow distribution at 6.7 nm (Fig. 3B). This result agrees very well with the TEM images (Fig. 2A and B); moreover, the CS@SBA-15 core–shell structure has a high BET surface area of 438.4 m2 g−1 and large pore volume of 0.36 cm3 g−1 (Table 1).
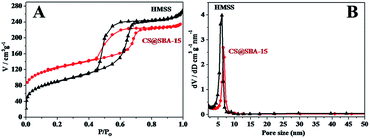 |
| Fig. 3 (A) N2 sorption isotherm curves and (B) pore size distribution plots of CS@SBA-15 and HMMS. | |
Table 1 Physicochemical properties of CS@SBA-15 and HMSS
Sample |
SBET (m2 g−1) |
Pore size (nm) |
Vt (cm3 g−1) |
CS@SBA-15 |
438.4 |
6.7 |
0.36 |
CS@SBA-15 100H |
376.1 |
6.3 |
0.31 |
CS@SBA-15 130H-MgSO4 |
318.1 |
8.4 |
0.33 |
HMSS |
326.5 |
6.0 |
0.42 |
HMSS 100H |
239.9 |
6.1 |
0.37 |
HMSS 130H-MgSO4 |
277.7 |
8.2 |
0.62 |
Since the triblock copolymer surfactant and carbon spheres can be easily removed with calcination treatment, which results in the formation of mesoporous silica shells with hollow interior structures. Significantly, the spherical shape is preserved for these hollow mesoporous silica spheres (HMMS) (Fig. 1C). As revealed by the SEM image, a number of spheres have a hole on the surface, indicating hollow structures (Fig. 1C). The TEM images further confirm that the hollow interiors of the HMMS are approximately 600 nm, originating from the carbon sphere core and mesoporous silica shell, which are about 120–150 nm (Fig. 2C and D); i.e. the regular stripe-like mesochannels encircle the cavity.
A wide weak peak still appears at 2θ = 0.90° for the small-angle XRD pattern, suggesting the retention of the mesoporous structure (Fig. 1D). It should be noted that the diffraction peak shifted to the higher angle region (from 2θ = 0.86° to 0.90°), indicating the shrinkage of the mesoporous silica shell to a certain extent. The N2 adsorption–desorption isotherms of the HMSS shows a representative typical type-IV curve, consisting of an H1-type hysteresis loop in the high relative pressure (P/P0) range of 0.5–0.7, indicating the existence of a large mesopore. The surface area and pore size distribution of the HMSS are 326.5 m2 g−1 and 6.0 nm, which is slightly lower than that of CS@SBA-15 (Table 1). The increased pore volume (0.42 cm3 g−1) is derived from the hollow interiors of the HMSS.
To explore the role of MgSO4 in the coating process, the CS@SBA-15 100H sample is synthesized without the addition of MgSO4. It is found that the CS@SBA-15 100H sample still possesses a spherical morphology with a diameter of about 900 nm, indicating that the mesoporous silica was coated on the surface of the carbon spheres (Fig. 4A). However, some sticky particles with irregularly rounded shapes are observed on the surface of the spheres, resulting in a rough surface and nonuniform coating. The obtained HMSS 100H after the removal of the carbon sphere core in air maintained the hollow structure (Fig. 4B). Furthermore, the CS@SBA-15 100H core–shell structure and HMSS 100H hollow sphere presents a type IV isotherm (Fig. S1†), and the BET surface area, pore size and pore volume are 376.1 m2 g−1, 6.3 nm, 0.31 cm3 g−1 and 239.9 m2 g−1, 6.1 nm, 0.37 cm3 g−1, respectively (Table 1), which are lower than those of samples with the addition of MgSO4. Furthermore, the XRD patterns of the core–shell structures and hollow spheres both display a distinct diffraction peak (Fig. S2†). These results reveal that the introduction of the inorganic salt MgSO4 can result in the uniform coating of mesoporous silica due to the enhanced electrostatic interactions between the triblock copolymer surfactant and silica precursor.24,26
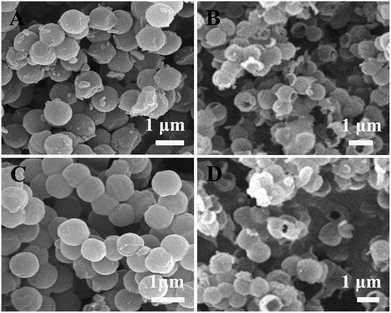 |
| Fig. 4 SEM images of (A) CS@SBA-15 100H, without the addition of anhydrous magnesium sulfate and hydrothermal treatment at 100 °C; (B) the corresponding hollow mesoporous silica spheres (HMSS 100H) after calcination at 700 °C for 3 h in air. (C) CS@SBA-15 130H-MgSO4, with the anhydrous magnesium sulfate as the inorganic salt and hydrothermal treatment at 130 °C; and (D) the hollow mesoporous silica spheres (HMSS 130H-MgSO4). | |
For the traditional synthesis approach of SBA-15, the pore size distribution is sensitive to the hydrothermal temperature. Generally, a higher hydrothermal temperature treatment favors a larger pore size distribution.42 Therefore, in order to obtain large pore size mesoporous silica shell during the coating process, an elevated hydrothermal temperature at 130 °C is chosen. It is noticeable that the carbon spheres are coated by the mesoporous silica shell (CS@SBA-15 130H-MgSO4) at such high hydrothermal temperature with an average size of 900 nm. From the broken spheres, the core–shell structure is apparently observed (Fig. 4C). The hollow spheres (HMSS 130H-MgSO4), which clearly appeared after the removal of the carbon core (Fig. 4D), further demonstrate the successful coating after the high hydrothermal treatment. Furthermore, the N2 adsorption–desorption isotherms of CS@SBA-15 130H-MgSO4 and HMSS 130H-MgSO4 exhibit typical IV curves with condensation steps at a high relative pressure (P/P0) of 0.7–0.8, indicating the larger pore size distribution (Fig. S1†). As shown in Table 1, the pore size distributions are centered at ∼8.4 and 8.2 nm, respectively.
Based on the aforementioned results, the mesoporous silica SBA-15 can be coated on the surface of carbon spheres under a low concentration of triblock copolymer and strong acidic system at room temperature. The hydrogen ion interacts with the oxygen derived from the hydrophilic chain of the block copolymer, and then reacts with the silica precursor through electrostatic interactions (Scheme 1).43 The micelles assemble to intermediate mesostructures, and thus are subsequently adsorbed on the surface of carbon spheres via polar interactions and hydrogen bonding. Because many OH and C
O groups exist on the surface of carbon spheres and present a hydrophilic property, which is confirmed by FTIR (Fig. S3†), the carbon spheres can also interact with the cationic surfactant hexadecyltrimethylammonium bromide (CTAB) and fabricate hollow mesoporous silica spheres with a small pore size (∼2.0 nm) distribution (Fig. S4†). This phenomena further verifies that the abundant OH and C
O groups around the surface of a carbon sphere facilitates the coating of mesoporous silica, even in an acidic system.
4. Conclusion
In summary, we have demonstrated a direct triblock-copolymer-templating strategy to prepare carbon sphere@mesoporous silica core–shell structures and mesoporous silica hollow spheres with controllable large mesopores using P123 as the surfactant template and TEOS as the silica source in an acidic medium. The large mesopore can be realized from 6.3 to 8.4 nm by changing the hydrothermal temperature and ionic strength. This elegant design with carbon spheres as the core and large pore mesoporous silica as the shell renders fascinating features and advantages. First, these large pore, i.e. CS@SBA-15 and HMSS, possess diversified applications in adsorption, drug-release and catalyst carriers. Second, carbon spheres as a benign and hydrophilic surface can offer a site for the adsorption of metal ions and organic molecules to construct other functionalized core–shells and hollow structures. Third, the carbon spheres are easily coated on the surface of other nanocrystals and protected cores, which is beneficial for the further formation of multilayer large pore mesoporous silica encapsulating core–shell and yolk–shell structures. At last, these large mesopore channels afford a location for loading and as a nanocasting template for other mesoporous shells. Therefore, for fundamental interest and methodology outlook, the current work is not limited to the synthesis of mesoporous silica hollow spheres with large pore sizes; however, it provides extensive directions for the synthesis of other large pore mesoporous core–shell, yolk–shell and hollow structures.
Acknowledgements
We gratefully acknowledge the financial support from the State Key Laboratory of Pollution Control and Resource Reuse Foundation (PCRRF12001) and the China Postdoctoral Science Foundation (2014M551455).
References
- L. Wang and Y. Yamauchi, J. Am. Chem. Soc., 2010, 132, 13636–13638 CrossRef CAS PubMed.
- Y. S. Li and J. L. Shi, Adv. Mater., 2014, 26, 3176–3205 CrossRef CAS PubMed.
- P. M. Arnal, M. Comotti and F. Schüth, Angew. Chem., Int. Ed., 2006, 45, 8224–8227 CrossRef CAS PubMed.
- M. M. Ye, Q. Zhang, Y. X. Hu, J. P. Ge, Z. D. Lu, L. He, Z. L. Chen and Y. D. Yin, Chem.–Eur. J., 2010, 16, 6243–6250 CrossRef CAS PubMed.
- L. Quaroni and G. Chumanov, J. Am. Chem. Soc., 1999, 121, 10642–10643 CrossRef CAS.
- J. X. Zhu, T. Sun, H. H. Hng, J. Ma, F. Y. C. Boey, X. W. Lou, H. Zhang, C. Xue, H. Y. Chen and Q. Y. Yan, Chem. Mater., 2009, 21, 3848–3852 CrossRef CAS.
- L. M. Liz-Marzn and P. Mulvaney, J. Phys. Chem. B, 2003, 107, 7312–7326 CrossRef.
- A. Schlossbauer, S. Warncke, P. M. E. Gramlich, J. Kecht, A. Manetto, T. Carell and T. Bein, Angew. Chem., Int. Ed., 2010, 49, 4734–4737 CrossRef CAS PubMed.
- J. Liu, S. Z. Qiao, S. B. Hartono and G. Q. Lu, Angew. Chem., Int. Ed., 2010, 49, 4981–4985 CrossRef CAS PubMed.
- J. P. Yang, Y. H. Deng, Q. L. Wu, J. Zhou, H. F. Bao, Q. Li, F. Zhang, F. Y. Li, B. Tu and D. Y. Zhao, Langmuir, 2010, 26, 8850–8856 CrossRef CAS PubMed.
- I. Gorelikov and N. Matsuura, Nano Lett., 2008, 8, 369–373 CrossRef CAS PubMed.
- S. H. Joo, J. Y. Park, C. K. Tsung, Y. Yamada, P. D. Yang and G. A. Somorjai, Nat. Mater., 2009, 8, 126–131 CrossRef CAS PubMed.
- J. P. Ge, Q. Zhang, T. R. Zhang and Y. D. Yin, Angew. Chem., Int. Ed., 2008, 47, 8924–8928 CrossRef CAS PubMed.
- X. H. Guo, Y. H. Deng, D. Gu, R. C. Che and D. Y. Zhao, J. Mater. Chem., 2009, 19, 6706–6712 RSC.
- K. L. Ding, B. J. Hu, Y. Xie, G. M. An, R. T. Tao, H. Y. Zhang and Z. M. Liu, J. Mater. Chem., 2009, 19, 3725–3731 RSC.
- S. Haffer, M. Tiemann and M. Fröba, Chem.–Eur. J., 2010, 16, 10447–10452 CrossRef CAS PubMed.
- Y. H. Deng, Y. Cai, Z. K. Sun, J. Liu, C. Liu, J. Wei, W. Li, C. Liu, Y. Wang and D. Y. Zhao, J. Am. Chem. Soc., 2010, 132, 8466–8473 CrossRef CAS PubMed.
- J. P. Yang, F. Zhang, Y. R. Chen, S. Qian, P. Hu, W. Li, Y. H. Deng, Y. Fang, L. Han, M. Luqman and D. Y. Zhao, Chem. Commun., 2011, 47, 11618–11620 RSC.
- Y. F. Zhu, Y. Fang and S. Kaskel, J. Phys. Chem. C, 2010, 114, 16382–16388 CAS.
- J. Kim, H. S. Kim, N. Lee, T. Kim, H. Kim, T. Yu, I. C. Song, W. K. Moon and T. Hyeon, Angew. Chem., Int. Ed., 2008, 47, 8438–8441 CrossRef CAS PubMed.
- H. S. Qian, H. C. Guo, P. C.-L. Ho, R. Mahendran and Y. Zhang, Small, 2009, 5, 2285–2290 CrossRef CAS PubMed.
- W. Li and D. Y. Zhao, Adv. Mater., 2013, 25, 142–149 CrossRef CAS.
- W. R. Zhao, J. L. Gu, L. X. Zhang, H. R. Chen and J. L. Shi, J. Am. Chem. Soc., 2005, 127, 8916–8917 CrossRef CAS PubMed.
- X. F. Qian, J. M. Du, B. Li, M. Si, Y. S. Yang, Y. Y. Hu, G. X. Niu, Y. H. Zhang, H. L. Xu, B. Tu, Y. Tang and D. Y. Zhao, Chem. Sci., 2011, 2, 2006–2016 RSC.
- W. Li, Q. Yue, Y. H. Deng and D. Y. Zhao, Adv. Mater., 2013, 25, 5129–5152 CrossRef CAS PubMed.
- J. P. Yang, F. Zhang, W. Li, D. Gu, D. K. Shen, J. W. Fan, W.-X. Zhang and D. Y. Zhao, Chem. Commun., 2014, 50, 713–715 RSC.
- J. P. Yang, D. K. Shen, L. Zhou, W. Li, X. M. Li, C. Yao, R. Wang, A. M. El-Toni, F. Zhang and D. Y. Zhao, Chem. Mater., 2013, 25, 3030–3037 CrossRef CAS.
- J. P. Yang, D. K. Shen, L. Zhou, W. Li, J. W. Fan, A. M. El-Toni, W. –X. Zhang, F. Zhang and D. Y. Zhao, Adv. Healthcare Mater., 2014 DOI:10.1002/adhm.201400053.
- I. I. Slowing, B. G. Trewyn, S. Giri and V. S.-Y. Lin, Adv. Funct. Mater., 2007, 17, 1225–1236 CrossRef CAS.
- X. W. Lou, L. A. Archer and Z. C. Yang, Adv. Mater., 2008, 20, 3987–4019 CrossRef CAS.
- G. G. Qi, Y. B. Wang, L. Estevez, A. K. Switzer, X. N. Duan, X. F. Yang and E. P. Giannelis, Chem. Mater., 2010, 22, 2693–2695 CrossRef CAS.
- Y. Q. Yeh, B. C. Chen, H. P. Lin and C. Y. Tang, Langmuir, 2006, 22, 6–9 CrossRef CAS PubMed.
- J. G. Wang, F. Li, H. J. Zhou, P. C. Sun, D. T. Ding and T. H. Chen, Chem. Mater., 2009, 21, 612–620 CrossRef CAS.
- J. Yang, J. U. Lind and W. C. Trogler, Chem. Mater., 2008, 20, 2875–2877 CrossRef CAS.
- Y. F. Zhu, E. Kockrick, T. Ikoma, N. Hanagata and S. Kaskel, Chem. Mater., 2009, 21, 2547–2553 CrossRef CAS.
- X. M. Sun and Y. D. Li, Angew. Chem., Int. Ed., 2004, 43, 597–601 CrossRef PubMed.
- X. M. Sun, J. F. Liu and Y. D. Li, Chem.–Eur. J., 2006, 12, 2039–2047 CrossRef CAS PubMed.
- M. M. Titirici, M. Antonietti and A. Thomas, Chem. Mater., 2006, 18, 3808–3812 CrossRef CAS.
- Y. Wan, Y. L. Min and S. H. Yu, Langmuir, 2008, 24, 5024–5028 CrossRef CAS PubMed.
- X. F. Qian, D. S. Xiong, A. M. Asiri, S. B. Khan, M. M. Rahman, H. L. Xu and D. Y. Zhao, J. Mater. Chem. A, 2013, 1, 7525–7532 CAS.
- L. Liang, Q. C. Zhu, T. B. Wang, F. X. Wang, J. Ma, L. Q. Jing and J. M. Sun, Microporous Mesoporous Mater., 2014, 197, 221–228 CrossRef CAS PubMed.
- D. Y. Zhao, J. L. Feng, Q. S. Huo, N. Melosh, G. H. Fredrickson, B. F. Chmelka and G. D. Stucky, Science, 1998, 279, 548–552 CrossRef CAS.
- J. P. Yang, W. Y. Chen, X. Q. Ran, W. Wang, J. W. Fan and W.-X. Zhang, RSC Adv., 2014, 4, 20069–20076 RSC.
Footnote |
† Electronic supplementary information (ESI) available. See DOI: 10.1039/c4ra08850f |
|
This journal is © The Royal Society of Chemistry 2014 |
Click here to see how this site uses Cookies. View our privacy policy here.