DOI:
10.1039/C4RA05550K
(Paper)
RSC Adv., 2014,
4, 41469-41475
Sulfuric acid functionalized MCM-41 coated on magnetite nanoparticles as a recyclable core–shell solid acid catalyst for three-component condensation of indoles, aldehydes and thiols
Received
10th June 2014
, Accepted 21st August 2014
First published on 28th August 2014
Abstract
Magnetite nanoparticles were used as a core for –OSO3H functionalized mesoporous MCM-41 shell to provide a core–shell solid acid catalyst (Fe3O4@MCM-41-OSO3H). The catalyst was characterized by transmission electron microscopy (TEM), infrared spectroscopy (FT-IR), X-ray diffraction (XRD) and a vibrating sample magnetometer (VSM). The obtained nano-magnetic catalyst was used in the three-component reaction of indoles, aldehydes and thiols to furnish the desired 3-[(aryl)(arylthio)methyl]-1H-indoles in good yields under very mild reaction conditions. The unique feature of the reaction was the ease of work-up and catalyst recovery. The recovered catalyst maintained catalytic activity for five successive runs.
1. Introduction
Indoles have been a focus of interest for many years.1,2 Various indole derivatives occur in many pharmacologically and biologically active compounds.3 In particular, 3-substituted indoles have significant medical importance4,5 and can be prepared by a variety of strategies such as nucleophilic ring-opening of epoxides by indoles,6 condensation reaction of indoles and aldehydes or ketones in the presence of either protic or Lewis acids,7 Michael addition to conjugated carbonyl compounds8 and many others. Little attention however, has been paid to the 3-substituted indoles containing sulfur atoms,9,10 and to a lesser extent, multi-component reactions that incorporate sulfur in 3-substituted indoles have been investigated. Our involvement in the study of indoles and solid acid catalysts,11–13 along with a recent report on three-component reaction of indoles, aldehydes and thiols by Dar et al.14 prompted us to investigate application of functionalized magnetic nanoparticles to improve such a reaction with respect to the reaction time, catalyst loading, and above all, recovery and reuse of the catalyst which promises minimization of the waste and paves the way for scale-up usage. Acid functionalized magnetic nanoparticles were selected because they could be easily separated from the reaction mixture by an external magnet. An in-depth investigation on the sulfonic-acid functionalized amorphous silica-coated cobalt spinel ferrite nanoparticles and their application in deprotection of benzaldehyde dimethylacetals has been reported by Jones et al.15 Hereby, we introduce sulfuric acid functionalized MCM-41 coated magnetite nanoparticles with core–shell structure (Fe3O4@MCM-41-OSO3H, where Fe3O4 nanoparticles served as a core for mesoporous MCM-41 sulfuric acid shell) as a new and efficient solid acid catalyst for three component reaction of indoles, aldehydes and thiols under mild reaction conditions (Scheme 1).
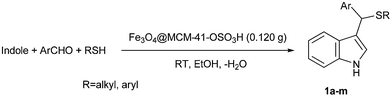 |
| Scheme 1 Fe3O4@MCM-41-OSO3H catalyzed condensation reaction of indoles, aldehydes and thiols. | |
2. Experimental
2.1. Materials
Fe3O4 magnetite nanoparticles were synthesized according to our previous report.16 For the synthesis of Fe3O4@MCM-41, 1.5 g of the synthesized Fe3O4 nanoparticles were dispersed in a mixture of ammonia solution (5 mL, 25%) and distilled water (50 mL) in a glass reactor by using ultrasound irradiation for 2 min at 40 °C. Then, tetraethylorthosilicate (TEOS, 10.0 mL), NaOH (0.9 g) and NaF (0.19 g) were added to the mixture and stirred for 2 h prior to addition of Cetyltrimethylammonium bromide (CTAB, 7.0 g). The mixture was then stirred at 40 °C for 2 h. At the end of this process, the magnetic composite was hydrothermally treated at 120 °C for 48 h in an autoclave. After two days, the resultant solid was filtered, washed with distilled water and dried at 60 °C. Finally, the template was removed by calcination of the synthesized particles for 3 h at 300 °C. SO3H functionalization on Fe3O4@MCM-41 was carried out according to Kiasat et al.17 In brief, Fe3O4@MCM-41 (2.0 g) was charged into a suction flask equipped with a constant pressure dropping funnel, and dispersed by ultrasound for 10 min in dichloromethane (0.075 L). Chlorosulfonic acid (2.92 g, 25 mmol) in CH2Cl2 (0.02 L) was added dropwise over a period of 30 min at room temperature. The mixture was then stirred for 90 min, while evolving HCl was eliminated by suction. Then the Fe3O4@MCM-41-OSO3H was separated from the reaction mixture by an external magnet and washed several times with CH2Cl2, then dried under vacuum at 60 °C. The amount of sulfonic acid loading was determined as 2.3 mmol SO3H g−1 of the catalyst according to the literature.17
2.2. Typical procedure for the preparation of 3-[(aryl)(arylthio)methyl]-1H-indoles
Indole (1.00 mmol), aldehyde (1.00 mmol), thiol (1.00 mmol) and ethanol (5 mL) were added to a flask and then Fe3O4@MCM-41-OSO3H (0.120 g) was added and the resulting mixture was mechanically stirred at room temperature until the disappearance of the starting indole was complete (monitored by TLC). After completion of the reaction, the catalyst was removed by an external magnet. The obtained solution was concentrated in vacuum, and the crude product was purified by short column chromatography (n-hexane/EtOAC, 10
:
3). The recovered catalyst was washed three times with ethanol and then dried under vacuum at 60 °C overnight.
2.3. Characterization data for 3-(benzylthio(phenyl)methyl)-1-methylindole (1m)
Beige solid, yield: 80%; m.p. 123–125 °C; IR (KBr): νmax 1464, 1389, 1218, 1180, 1080, 1008, 746, 609 cm−1. 1H NMR (400 MHz, CDCl3, 25 °C): δ 3.57 (d, 1H, J = 13.2 Hz, –CH2), 3.64 (d, 1H, J = 13.2 Hz, –CH2), 3.69 (s, 3H, CH3), 5.14 (s, 1H, CH), 6.85 (d, 1H, J = 1.6 Hz, ArH), 7.01 (t, 2H, J = 7.6 Hz, ArH), 7.10 (t, 2H, J = 8.0 Hz, ArH), 7.22–7.34 (m, 7H, ArH), 7.48 (d, 2H, J = 8.8 Hz, ArH), 7.55 (d, 1H, J = 8.0 Hz, ArH) ppm; 13C NMR (100 MHz, CDCl3): δ 33.63, 36.76, 45.51, 111.42, 116.54, 119.71, 119.83, 122.41, 123.62, 126.46, 127.11, 127.25, 128.53 (2C), 128.64 (2C), 128.71 (2C), 129.24 (2C), 136.61, 138.52, 141.72 ppm; Anal. Calc for C23H21NS: C, 80.42; H, 6.16; N, 4.08. Found: C, 80.48; H, 6.20; N, 4.15.
All of the other products are known compounds, and their spectroscopic and physical data were found to be identical to those described in the literature.14
2.4. Instrumentation
X-ray powder diffraction (XRD) measurements were performed using a Philips diffractometer with mono chromatized Cu kα radiation. IR spectra were recorded on a Shimadzu FTIR-8400S spectrometer. 1H NMR spectra were obtained on a Bruker DRX-400 Avance spectrometer and 13C NMR spectra were obtained on a Bruker DRX-100 Avance spectrometer. Chemical shifts of 1H and 13C NMR spectra were expressed in ppm downfield from tetramethylsilane. Melting points were measured on a Büchi Melting Point B-540 instrument and are uncorrected. Elemental analyses were made by a Carlo-Erba EA1110 CNNO–S analyzer and agreed with the calculated values. TEM images were obtained on a transmission electron microscope (TEM-PHILIPS MC 10) with an acceleration voltage of 80 kV. VSM curves were obtained on a vibrating sample magnetometer (VSM JDM-13) at room temperature.
3. Results and discussion
Mesoporous MCM-41 was selected as the shell for Fe3O4 magnetic nanoparticles because of its well defined channel system and higher external hydroxyl groups. Deposition of the shell onto Fe3O4 nanoparticles surface was performed by a simple, low cost and convenient method. Then, simple mixing of the core–shell nanocomposite and chlorosulfonic acid in dichloromethane provided the solid acid catalyst (Fe3O4@MCM-41-OSO3H) which was characterized by FT-IR, TEM, XRD and VSM techniques. FT-IR spectrum of Fe3O4@MCM-41 (Fig. 1a) showed characteristic bands of both magnetite and mesoporous MCM-41. In the FT-IR spectra of Fe3O4@MCM-41-OSO3H (Fig. 1b), basic characteristic vibrations of Fe–O at 588 cm−1 and Si–O–Si asymmetric stretching, symmetric stretching and bending vibrations at 1072, 795 and 453 cm−1 were observed. Characteristic bands of the sulfonyl groups were observed at 1229 cm−1 and 1120 cm−1, with simultaneous disappearance of Si–OH group peak at 900 cm−1.17 Broad absorption around 2800–3700 cm−1 is also, attributable to the OH stretching of the acid functionality.
 |
| Fig. 1 FT-IR spectra of (a) Fe3O4@MCM-41 and (b) Fe3O4@MCM-41-OSO3H. | |
X-ray diffraction (XRD) pattern of Fe3O4@MCM-41-OSO3H (Fig. 2b) showed peaks that could be indexed to both mesoporous structure and Fe3O4 nanoparticles. The Fe3O4 nanoparticles indicated peaks with 2θ at 29.72, 35.57, 43.17, 57.15 and 62.77 which is quite identical to pure magnetite (Fig. 2a, right) and matched well with the XRD pattern of the standard Fe3O4 (JCPDS no. 19-692).18 The smoothly varying peak intensity with 2θ at 10–30 range (Fig. 2b, right) results from the simultaneous formation of some amorphous silica. The siliceous mesoporous structure, however, indicated peaks with 2θ at 1.5–10 (Fig. 2b, left) or reflection from the 100, 110 and 200 planes, which are characteristic peaks of MCM-41.19
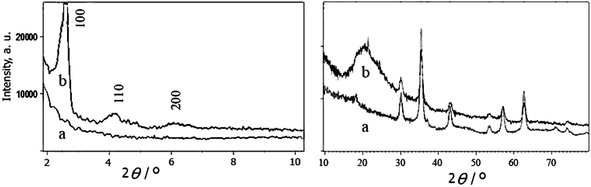 |
| Fig. 2 Left: low angle (2θ = 1.5–10) and right: high angle (2θ = 10–80) XRD patterns of (a) Fe3O4 nanoparticles, (b) Fe3O4@MCM-41-OSO3H nanoparticles. | |
Nanoscale size of the composite, however, was demonstrated by transmission electron microscopy (TEM, Fig. 3). Based on the TEM images, analysis of Fe3O4@MCM-41 surface morphology demonstrated the agglomeration of many ultrafine spherical-like particles which display dark magnetite cores surrounded by a shell. Particle size distribution analysis showed a narrow distribution of particle size about 15 nm.
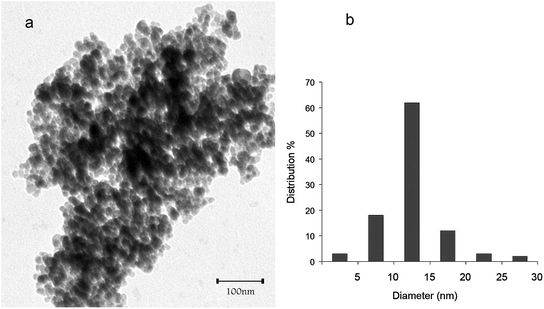 |
| Fig. 3 (a) TEM image of Fe3O4@MCM-41-OSO3H nanoparticles and (b) particle size distribution. | |
The magnetic hysteresis curves of magnetic nanoparticles were also, obtained. As can be seen in Fig. 4, typical magnetization curves as a function of applied magnetic field at 300 K are shown. Bare Fe3O4 and Fe3O4@MCM-41-OSO3H nanoparticles exhibited typical super paramagnetic behavior. The large saturation magnetization of bare Fe3O4 decreased from 82 emu g−1 to 50 emu g−1, due to coating with non-magnetic mesoporous hybrid.
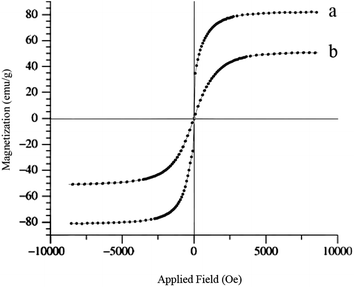 |
| Fig. 4 Hysteresis curves of (a) Fe3O4 and (b) Fe3O4@MCM-41-OSO3H nanoparticles measured at 300 K. | |
Acid content of the catalyst was determined by measuring the pH of proton-exchanged brine solutions. To an aqueous solution of NaCl (25.0 mL, 1.0 M), 100 mg of the catalyst was added and the suspension was stirred overnight. Decrease in the pH of the solution from 6.0 to 1.59 is equal to a loading of 2.3 mmol –OSO3H g−1 of the solid acid catalyst. Potentiometric back-titration of the solid acid catalyst, further confirmed this result.
The characterized catalyst, then, was used in one-pot three component condensation reaction of indoles, aldehydes and thiols. In order to optimize the reaction conditions with respect to catalyst type, catalyst loading, and to examine the effect of solvent and temperature on the reaction yield, indole, benzaldehyde and benzothiol were used as model substrates and their reaction was tested under different conditions. The results are summarized in Table 1.
Table 1 The effect of various parameters on the three component reaction of indole, benzaldehyde and benzothiol
Entrya |
Catalyst |
Solvent |
Catalyst loading (g per mmol of aldehyde) |
Temperature (°C) |
Yield, % |
The reaction was carried out according to general experimental procedure. |
1 |
No catalyst |
EtOH |
0 |
25 |
0 |
2 |
Fe3O4 |
′′ |
0.120 |
′′ |
<2 |
3 |
MCM-41 |
′′ |
0.120 |
′′ |
5 |
4 |
MCM-41-OSO3H |
′′ |
0.120 |
′′ |
67 |
5 |
Fe3O4@MCM-41-OSO3H |
′′ |
0.060 |
′′ |
52 |
6 |
Fe3O4@MCM-41-OSO3H |
′′ |
0.120 |
′′ |
63 |
7 |
′′ |
′′ |
0.250 |
′′ |
64 |
8 |
′′ |
′′ |
0.120 |
50 |
51 |
9 |
′′ |
CH3OH |
0.120 |
25 |
65 |
10 |
′′ |
Dioxane |
0.120 |
′′ |
34 |
11 |
′′ |
1,2-DCE |
0.120 |
′′ |
21 |
As it is shown, in the absence of catalyst, no formation of the desired product was observed (entry 1), and the best catalyst was found to be Fe3O4@MCM-41-OSO3H, in an optimum loading of 0.120 g per mmol of aldehyde (entry 6). MCM-41 sulfuric acid (entry 4) was also tested and the yield was comparable. Fe3O4@MCM-41-OSO3H, however, had the advantage of easy recycling. It seemed that the reaction yield does not change linearly with respect to the catalyst loading. For example, while increasing the catalyst amount from 0.060 g per mmol of aldehyde (entry 5) to 0.120 g mmol−1 improved the yield (entry 6), higher loads of the catalyst, did not improve the yield (entry 7). It is noteworthy that the yield of the product was solvent dependent and the best solvents were found to be ethanol and methanol. Considering toxicity however, ethanol was selected as the solvent of choice. Although the –OH functionality of alcohols could not compete in this reaction, it may be involved in the reaction mechanism in some way, and this is an issue that needs to be addressed in future studies. The order of addition of substrates on the other hand, had an impact on the yield of the desired product. When the catalyst was added to a mixture of indole and aldehyde, prior to addition of thiol, formation of bis(indolyl)methane was predominant. Finally, it was found that employing elevated temperature had an inverse effect on the yield of the target product (entry 8).
After obtaining the optimum reaction condition (Scheme 1), a series of thiols and aldehydes were used to investigate the generality and scope of the reaction (Table 2) and the results were satisfying.
Table 2 Fe3O4@MCM-41-OSO3H catalyzed three component reaction of indole, aldehydes and ketones
Entrya |
Indole |
Aldehyde |
Thiol |
Product |
τ/h, Yieldb, % |
All products were characterized by 1H NMR, 13C NMR and IR data. Isolated yields. |
1 |
Indole |
C6H5CHO |
C6H5CH2SH |
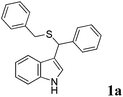 |
3, 63 |
2 |
′′ |
′′ |
p-MeC6H5CH2SH |
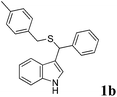 |
3, 68 |
3 |
′′ |
′′ |
p-MeOC6H5CH2SH |
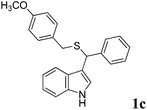 |
3, 70 |
4 |
′′ |
′′ |
p-NO2C6H5CH2SH |
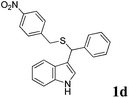 |
4, 28 |
5 |
′′ |
C6H5CHO |
C2H5SH |
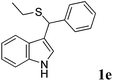 |
3, 72 |
6 |
′′ |
p-ClC6H4CHO |
′′ |
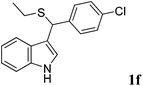 |
3, 70 |
7 |
′′ |
p-NO2C6H4CHO |
′′ |
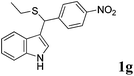 |
3, 68 |
8 |
′′ |
o-NO2C6H4CHO |
′′ |
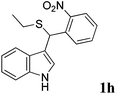 |
3, 36 |
9 |
′′ |
C6H5CHO |
C6H5SH |
 |
5, 30 |
10 |
′′ |
′′ |
p-MeC6H4SH |
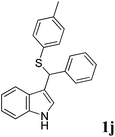 |
4, 67 |
11 |
′′ |
′′ |
p-NO2C6H4SH |
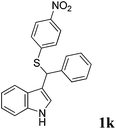 |
6, 25 |
12 |
′′ |
′′ |
p-MeOC6H4SH |
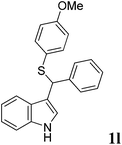 |
3, 65 |
13 |
1-methylindole |
′′ |
C6H5CH2SH |
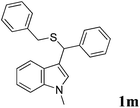 |
3, 80 |
As shown in Table 2, various aldehydes and thiols participated in the reaction and this catalytic system tolerated different functional groups. With regard to substituents, aliphatic character of thiols, electron-withdrawing character of aldehyde substituents and electron-releasing nature of the indole substituents favors the formation of products. To the best of our knowledge, this is the first report on the application of Fe3O4@MCM-41-OSO3H in one-pot three component condensation reaction of indoles, aldehydes and thiols.
Although the formulation of a mechanism for the reaction discussed in this study requires further data and analyses, we proposed following reaction pathway that rationalizes the formation of the products (Scheme 2). In general, after activation of the carbonyl group of the aldehyde, nucleophilic attack from C-3 carbon atom of indole gives intermediate I, which in turn loses one molecule of water. Thia-Michael addition to the iminium intermediate II, then provides the desired condensation product. Presence of excess indole, or addition of thiol after other substrates, however, disfavors this step and would result in bis(indolyl)methanes.
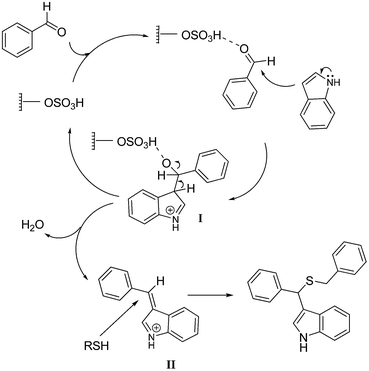 |
| Scheme 2 A proposed mechanistic pathway for the formation of 2a. | |
In order to evaluate reusability of the catalyst, the reaction of indole, benzaldehyde and benzothiol was carried out in the presence of the recycled catalyst in successive runs. From reaction run 1 to 5, the yields were 63%, 60%, 60%, 57% and 52%, respectively. Therefore after five runs, 11% decrease in the efficiency of the catalyst system was observed. This result shows that Fe3O4@MCM-41-OSO3H can be utilized as a moderate and recyclable catalyst for the formation of 3-[(aryl)(arylthio)methyl]-1H-indoles. In order to confirm heterogeneity of the catalyst, the amount of sulfonic acid loading was determined for the recycled catalyst of the 5th run and a similar result (2.2 mmol SO3H g−1) was obtained, which confirmed that no considerable leaching was occurred during the course of reaction.
4. Conclusion
In conclusion, we have developed a new synthetic protocol for the efficient synthesis of 3-[(aryl)(arylthio)methyl]-1H-indoles which might exhibit interesting pharmacological activities.20 To the best of our knowledge, this is the first report on the application of sulfuric acid functionalized MCM-41 coated magnetite nanoparticles in the less studied one-pot three component condensation reaction of indoles, aldehydes and thiols under very mild conditions. Highlights of the present work include higher yields, reasonably lower reaction times, ease of work-up, and above all, catalyst recovery and reuse. Further manipulation on this reaction is currently under way in our laboratory.
Acknowledgements
The authors are grateful to the Research Council of Guilan University for partial support of this study.
References
- M. Bandini and A. Eichholzer, Angew. Chem., Int. Ed., 2009, 48, 9608 CrossRef CAS PubMed.
- G. R. Humphrey and J. T. Kuethe, Chem. Rev., 2006, 106, 2875 CrossRef CAS PubMed.
- H.-C. Zhang, H. Ye, A. F. Moretto, K. K. Brumfield and B. E. Maryanoff, Org. Lett., 2000, 2, 89 CrossRef CAS PubMed.
- T. R. Garbe, M. Kobayashi, N. Shimizu, N. Takesue, M. Ozawa and H. Yukawa, J. Nat. Prod., 2000, 63, 596 CrossRef CAS PubMed.
- J. K. Porter, C. W. Bacon, J. D. Robins, D. S. Himmelsblach and H. C. Higman, J. Agric. Food Chem., 1977, 25, 88 CrossRef CAS.
- A. Khorshidi, Ultrason. Sonochem., 2012, 19, 570 CrossRef CAS PubMed.
- K. Tabatabaeian, M. Mamaghani, N. O. Mahmoodi and A. Khorshidi, Can. J. Chem., 2006, 84, 1541 CrossRef CAS.
- K. Tabatabaeian, M. Mamaghani, N. O. Mahmoodi and A. Khorshidi, J. Mol. Catal. A: Chem., 2007, 270, 112 CrossRef CAS PubMed.
- J. A. Campbell, C. A. Broka, L. Gong, K. A. M. Walker and J.-H. Wang, Tetrahedron Lett., 2004, 45, 4073 CrossRef CAS PubMed.
- J. S. Yadav, B. V. Subba Reddy and Y. Jayasudhan Reddy, Tetrahedron Lett., 2007, 48, 7034 CrossRef CAS PubMed.
- A. Khorshidi and K. Tabatabaeian, J. Serb. Chem. Soc., 2011, 76, 1347 CrossRef CAS.
- A. Khorshidi and K. Tabatabaeian, J. Mol. Catal. A: Chem., 2011, 344, 128 CrossRef CAS PubMed.
- A. Khorshidi, Chin. Chem. Lett., 2012, 23, 903 CrossRef CAS PubMed.
- A. A. Dar, S. Ali and A. T. Khan, Tetrahedron Lett., 2014, 55, 486 CrossRef CAS PubMed.
- C. S. Gill, B. A. Price and C. W. Jones, J. Catal., 2007, 251, 145 CrossRef CAS PubMed.
- F. Keyhanian, S. Shariati, M. Faraji and M. Hesabi, Arabian J. Chem., 2011 DOI:10.1016/j.arabjc.2011.04.012.
- A. R. Kiasat and J. Davarpanah, J. Mol. Catal. A: Chem., 2013, 373, 46 CrossRef CAS PubMed.
- J. H. Jang and H. B. Lim, Microchem. J., 2010, 94, 148 CrossRef CAS PubMed.
- A. A. Romero, M. D. Alba and J. Klinowski, J. Phys. Chem. B, 1998, 102, 123 CrossRef CAS.
- R. S. Vardanyan and V. J. Hruby, Synthesis Of Essential Drugs, Elsevier, Amsterdam, 2006 Search PubMed.
|
This journal is © The Royal Society of Chemistry 2014 |