DOI:
10.1039/C4RA04185B
(Paper)
RSC Adv., 2014,
4, 35750-35756
Facile hydrothermal synthesis and luminescent properties of Eu-doped CaF2–YF3 alkaline-earth ternary fluoride microspheres†
Received
6th May 2014
, Accepted 7th August 2014
First published on 7th August 2014
Abstract
Large-scale CaF2–YF3 alkaline-earth ternary fluoride microspheres with diameters of about 2.5 μm were prepared by a facile hydrothermal method in the presence of disodium ethylenediamine tetraacetate (Na2H2L). The influences of several experimental parameters, such as reaction time, amount of Na2H2L, pH values, and fluoride source on the final products were investigated. The formation mechanism of the as-obtained microspheres was proposed on the basis of all these studies. It is also found that the addition amount of the Y3+ ions had an effect on the morphology of CaF2–YF3. The luminescence spectrum of Eu3+-doped CaF2–YF3 microspheres showed the strong characteristic dominant emission of the Eu3+ ions at 590 nm, indicating that the Eu3+ ions occupy a site of inversion symmetry in the CaF2–YF3 matrix.
1. Introduction
It is well known that micro/nanomaterials syntheses have attracted considerable interest during the past few years. Great effort has been devoted to the investigation of morphology, size and dimensions of the micro/nanomaterials.1–6 Among them, fluoride materials have drawn much attention due to their unique optical and electronic properties, such as low-energy phonons, high ionicity, electron-acceptor behavior, high resistivity and anionic conductivity. For example, the fabrication of metal fluoride nanomaterials, such as CaF2 nanocubes,7 SrF2 nanospheres,8 BaF2 nanocubes9 or nanorods,10 and hexagonal GdF3 plates with holes in the center,11 has been reported for their application in UV lithography, UV-transparent optical lenses, surface conditioning of glass, and upconversion luminescence. However, compared with above mentioned binary lanthanide fluorides (LnF3, Ln = lanthanide elements), ternary ALnF4 or Ln1−yMyF3−y (A = alkali metals, Ln = lanthanide elements, M = Ca, Sr, Ba, Cd) fluorides are rarely studied. It is reported that barium yttrium fluoride crystals such as BaY2F8 and BaYF5 are excellent host matrixes which can be doped with various lanthanide ions, exhibiting strong up/down-conversion luminescence.12
Up to now, the fabrication of these ternary fluorides mainly involved solid state reactions,13–16 which has disadvantages of uncompleted production, irregular morphology, and larger particle size distribution. In comparison, solution-based syntheses possess some advantages in economical energy and facilities and controllable reaction conditions which result in refined morphology and size as well. Nevertheless, there are only a few documented literatures on the syntheses of alkaline-earth ternary fluorides via solution-based methods until now. Wang's group modified the uneven size and shape of alkaline-earth fluoride to monodisperse ultra small nanospheres through lanthanide doping in solution.17,18 Huang in our group reported the hydrothermal synthesis and luminescence of Eu-doped Ba0.92Y2.15F8.29 submicrospheres.19 To our knowledge, there has been no literature available on the hydrothermal synthesis of cubic-phase CaF2–YF3.
Herein, we report the preparation of CaF2–YF3 alkaline-earth ternary fluoride microspheres by the hydrothermal method with the disodium ethylenediamine tetraacetate (EDTA-2Na or Na2H2L) as chelator and NaBF4 as fluoride source, respectively. The influence of reaction time, the amount of Na2H2L, pH values and fluoride source were also systemically investigated. Besides, the effects of initial amount of Y3+ on the Y3+/Ca2+cation ratio in the final product were also studied. In order to explore the luminescent property and the environment of Y3+ ions in CaF2–YF3 host lattice, the luminescence of Eu3+ doped CaF2–YF3 were researched as well.
2. Experiment section
Reagents
The rare-earth oxides RE2O3 (RE = Y, Eu) (99.99%) were purchased from Shanghai Yuelong Non-Ferrous Metals Limited. Rare-earth nitrates stock solutions were obtained by dissolving the corresponding metal oxide in HNO3 solution under heating with agitation. The excess HNO3 was evaporated until the pH value was 4. The other chemicals (ethylenediamine tetraacetic acid, calcium chloride, and sodium fluoborate, AR) were purchased from Beijing Chemical Co. and used as received without further purification.
Preparation
In a typical procedure of preparing CaF2–YF3 microspheres, 1 mmol Na2H2L was first added into deionized water (20 mL). Sodium hydroxide aqueous solution (2 mol L−1) was then added dropwise with vigorous stirring until EDTA was dissolved absolutely to form a transparent solution with a pH value of 4. Subsequently, 1 mmol CaCl2 and 0.5 mmol Y(NO3)3 were introduced into the above solution. After the solution was stirred for 30 min, 20 mL of aqueous solution containing 1 mmol NaBF4 was added into it under thorough stirring. After additional agitation for 15 min, The resultant solution was transferred into a 50 mL Teflon autoclave, which was then tightly sealed and heated at 180 °C for 24 h followed by cooling down to room temperature naturally. The resulting precipitates were washed with deionized water and ethanol each three times. The final product was dried at 60 °C in air.
A similar process was employed for preparing Eu-doped CaF2–YF3. A stoichiometric amount of Eu(NO3)3 was added at an initial stage with Y(NO3)3 and other processes the same afterwards.
Characterization
Powder X-ray diffraction measurements were performed on a Bruker D8 focus X-ray powder diffractometer with Cu Kα radiation (λ = 0.15405 nm). The size and morphology of the products were characterized using an Hitachi S-4800 field emission scanning electron microscope equipped with an energy dispersive X-ray (EDX) spectrometer, operated at an acceleration voltage of 10 kV. The size and morphology of the samples were inspected using a field emission scanning electron microscope equipped with an energy-dispersive spectrometer (EDS) (FE-SEM, S-4800, Hitachi, Japan). The transmission electron microscope (TEM) images and selected area electron diffraction (SAED) patterns were obtained by a JEOL H-8100 transmission electron microscope at the accelerating voltage of 200 kV. The photoluminescence excitation and emission spectra were recorded with an Hitachi F-4500 fluorescence spectrophotometer equipped with a 150W xenon lamp as the excitation source. All the measurements were performed at room temperature.
3. Results and discussion
Phase identification and morphology of as-synthesized CaF2–YF3 microspheres
The crystal structure and phase purity of the product were examined by X-ray powder diffraction. Fig. 1a shows the XRD pattern of the as-synthesized product. All the diffraction peaks are coincident with the cubic-phase Ca0.9Y0.1F2.1 (JCPDS 79-0094, space group Fm3m, z = 8, and cell parameter α = 5.489 Å) well, except for a small shift toward the lower 2θ side, indicating a slight expansion of the crystal lattice (the calculated cell parameter α = 5.5194 Å) compared with the standard pattern. In the lattice of CaF2, when replacing Ca2+ by Y3+, more F− came into the lattice to balance the electric charge. In this case, the lattice expansion caused by the repulsion of the interstitial F− is dominated, while the lattice contraction ascribed to the replacement of smaller ionic radius is inconspicuous.17 This explained the small shift toward lower 2θ side in the XRD pattern. Furthermore, the EDX spectrum analysis (Fig. 1b) confirms the presence of elements Ca, Y, and F in the product, which can effectively support the XRD result. It is speculated that the emergence of the slight amount of Na showed that Na+ ions entered the lattice in the hydrothermal synthesis process. The average crystallite size of the product can be estimated from the Scherrer formula D111 = Kλ/(β
cos
θ), where λ is the X-ray wavelength (0.15405 nm), β is the full-width at half-maximum, θ is the diffraction angle, K is a constant (0.89), and D111 means the size along the (111) direction. The estimated average crystallite size is 21.5 nm.
 |
| Fig. 1 (a) XRD pattern of the product obtained in the typical procedure and the standard data of cubic-phase Ca0.9Y0.1F2.1 (JCPDS 79-0094) as a reference and (b) the corresponding EDX spectrum. | |
The morphology and size of the as-prepared product were further examined by SEM and TEM. As shown in the overall view SEM image in Fig. 2a, the product displayed as uniform microspheres with an average size of approximately 2.5 μm. The magnified SEM image (Fig. 2b) indicates that the microspheres with rough surfaces are stacked up by small nanoparticles. The TEM image further demonstrates that the sample is composed of monodisperse microspheres with a uniform spherical morphology (Fig. 2c). A careful observation of a single microsphere can also find the rough contour of the microsphere (Fig. 2d), which further imply that the microspheres are assembled by small nanoparticles. The observation is in consistent with crystal size obtained by the Scherrer formula on the basis of the XRD pattern. The corresponding SAED pattern shows dot rings, revealing the polycrystalline nature (Fig. 2e).
 |
| Fig. 2 (a and b) SEM images, (c and d) TEM images and (e) SAED pattern corresponding to (d) of the product obtained in the typical procedure. | |
Effect of the reaction time
In order to investigate the formation mechanisms of the CaF2–YF3 microspheres, time-dependent experiments were systemically carried out. Fig. 4 shows SEM images of the products obtained at 0.5 h, 1 h, 3 h and 12 h, respectively. The spherical morphology of the product began to form after 0.5 h with the mean diameter of 500 nm. However, the spheres showed polydispersity in dimensions after reacting for 0.5 and 1 h (Fig. 3a and b). As the reaction time was increased to 3 h, the size distribution because narrow and the sphere diameters increased to 2.5 μm (Fig. 3c). Further prolonged the reaction time to 12 h, the microspheres became tighter in structure and their diameters grew to 2.5 μm. The XRD patterns of the products corresponding to Fig. 3a–d are shown in Fig. 3e. All the products can be readily indexed into the cubic-phase CaF2–YF3, and the crystallinity increased as time went by.
 |
| Fig. 3 SEM images of the products with different reaction time: (a) 0.5 h; (b) 1 h; (c) 3 h; (d) 12 h and (e) XRD patterns corresponding to (a–d), respectively. | |
 |
| Fig. 4 SEM images of product produced with different amount of Na2H2L: (a) 0 mmol; (b) 0.2 mmol; (c) 0.4 mmol and (d) corresponding XRD patterns. | |
Effect of the addition amount of Na2H2L chelator
Many microspheres or submicrospheres were prepared with the assistance of additives, such as CTAB and EDTA. During the hydrothermal process, organic surfactants or inorganic ions have often been employed as morphology controlling agents to manipulate the growth behavior by selective absorption on high-energy facets, eventually favoring the formation of different morphologies. The influence of the chelator Na2H2L on the product was also observed by SEM images and XRD patterns. Contrast experiments were carried out by varying the amount of Na2H2L chelator. As shown in Fig. 4a, when no Na2H2L was added in the reaction, the product showed up as irregular plates and loose rod structures. Combining with their corresponding XRD patterns shown in Fig. 4d, we conclude the coexistence of cubic CaF2 and minor YF3. When the amount was less than 0.5 mmol, such as 0.2 mmol and 0.4 mmol, the morphology of the product was irregular spherical aggregates (<0.5 μm) even after 24 h incubation as shown in Fig. 4b and c. It is thus suggested that the chelator Na2H2L played an important role in the synthesis of pure phase CaF2–YF3. The Na2H2L can chelate with Ca2+ and Y3+ to form stable complex CaL2− and YL− which can release Ca2+ and Y3+ gradually to react with F−.20,21 Because of Na2H2L absorbing on the surface of the product, the sample exhibits good monodispersity.22,23
Effect of pH value
The pH value of the solution has great effect on the size and the final morphology of the hydrothermal product. The pH-dependent morphological evolution of the CaF2–YF3 microspheres was observed by SEM. When the reaction was carried out at pH = 2, some loose and irregular aggregates formed as well as microspheres (Fig. 5a), which show great similarity as the product obtained when Na2H2L is not enough. At pH = 3, together with microspheres were some polyhedron bulks (Fig. 5b). As is known, there is ionization equilibrium in the solution:
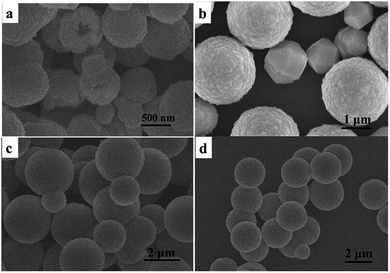 |
| Fig. 5 SEM images of product produced with different pH values: (a) pH = 2, (b) pH = 3, (c) pH = 5 and (d) pH = 6. | |
When the pH value is low, the equilibrium shifts to the left and Na2H2L turns into ethylenediaminetetraacetic acid (EDTA), which is only slightly soluble in water and thus plays weaker chelating ability. In fact, we failed to prepare CaF2–YF3 microspheres when EDTA was used instead of Na2H2L while the other conditions were unchanged. At pH = 4, large scale of uniform microspheres were obtained (Fig. 2). When the pH value was further increased to 5 or 6, the spherical morphology was maintained but the size distribution became relatively wider (Fig. 5c and d). The reason is that activity of Na2H2L chelator increased with the pH value increasing, making Ca2+ and Y3+ be released more slowly. So, the nucleation rate was decreased. In a word, the successful fabrication of CaF2–YF3 microspheres has been realized in a pH range above 4, and the low pH value affects the morphology by means of reducing the activity of Na2H2L chelator.
Effect of alkaline source
When ammonia is chosen as the alkaline source instead of NaOH to adjust the pH values, two kinds of spheres in different size scales were formed, namely microspheres and nanospheres (Fig. 6a and b). Refer to the corresponding XRD patterns, an unexpected obvious diffraction peak at low 2θ could be found, comparing with the Ca0.9Y0.1F2.1 cubic phase standard pattern. It is suggested that NH4+ itself might participate in the reaction to course the unwanted XRD peak. This result indicates that the alkali source also plays an important role.
 |
| Fig. 6 (a and b) SEM images of product produced when ammonia is chosen as the alkaline source. (c) corresponding XRD patterns and the standard data of cubic-phase Ca0.9Y0.1F2.1 (JCPDS 79-0094) as a reference. | |
Effect of fluoride source
The influence of fluoride source was also investigated by replacing NaBF4 with NaF and NH4F. Smaller nanoparticles form as illustrated in Fig. 7. The XRD patterns show that the products were both indexed as CaF2–YF3 ternary fluoride (Fig. 7c). However, irregular nanoparticles in diameter of 10–20 nm were yielded instead of uniform microspheres (Fig. 7a and b). The difference was attributed to the weak electrolytic ability of NaBF4 in comparison with the strong electrolyte NaF and NH4F. In NaBF4 solution, the following ionic reaction happens:
BF4− + 3H2O → H3BO3 + 3HF + F− |
 |
| Fig. 7 SEM images of product by using different fluoride source: (a) NaF, (b) NH4F, and (c) corresponding XRD patterns. | |
That is to say, F− ions provided by NaBF4 were in a lower concentration than the ones provided by NaF and NH4F. The smaller size was ascribed to the fast nucleation rate when F− ions were in a high concentration. Thus, the NaBF4 in our case was supposed to decrease the nucleation rate and result in a larger size by releasing F− ions slowly.
Mechanism of the microsphere growth
On the basis of the experimental conditions discussed above, the growth mechanism of CaF2–YF3 could be concluded into three steps as follows: (1) at room temperature, HxL(4−x)− combined with Ca2+ and Y3+ to form stable complex CaL2− and YL−, respectively; (2) in high temperature and pressure atmosphere, F− ions hydrolyzed from NaBF4 reacted with cations dissociated from CaL2− and YL− to form numerous CaF2–YF3 nuclei; (3) the nuclei grew into nanoparticles and tended to aggregate into microspheres to minimize their surface energy. The small submicrospheres possessing higher surface energy had a faster growth rate than the large ones, which make the size uniformity possible after a long ripening process.24,25 During the process, HxL(4−x)− absorbed on the surface of the product to keep the microspheres from aggregation. That is to say, Na2H2L in this reaction play the role of both chelator and stabilizer.
Effect of the amount of Y3+ ions
As shown in Fig. 8, the product didn't show any obvious difference in the microsphere morphology and size when the addition of Y3+ ions is in the range of 0.2–0.5 mmol. Meanwhile, the product lost its spherical shape and became loose and irregular when the value increased to 0.6 mmol, which might be due to the relative insufficiency of Na2H2L caused by excess of Y3+ ions.
 |
| Fig. 8 SEM images of the product prepared with different Y3+ ions (a): 0.2 mmol; (b): 0.3 mmol; (c): 0.4 mmol and (d): 0.6 mmol. | |
Luminescence of CaF2–YF3:Eu
It is well known that Eu3+ ions are widely used as a structure probes to detect the chemical environments in a matrix. The obtained microspheres in our system are proved to be suitable matrix of Eu3+ ions and didn't show any change in morphology after Eu3+ ions are introduced. The XRD patterns show a slight shift to lower angle for the Eu-doped CaF2–YF3 because of the larger ionic radius of Eu3+ (Fig. S1†). The EDS further confirmed the presence of element Eu in the doped samples (Fig. S1†). Fig. 9 shows the excitation and emission spectra of 5% Eu3+ doped CaF2–YF3. The excitation peak at 397 nm is assigned to the 7F0 → 5L6 transitions within the Eu3+ (4f6) configuration. Upon excitation at this wavelength, series of emission bands appear in the range of 500–700 nm, which is ascribed to the 5D1 and 5D0 to 7FJ (J = 1, 2, 3 and 4) transitions of the Eu3+ ions, respectively. In the CaF2–YF3:Eu crystal structure, the Y3+ and Eu3+ ions occupy the sites of the Ca2+ ions, where the Ca2+ ion bonds to eight F− ions, forming a CaF8 cubic polyhedron, as illustrated in the left-up inset panel in Fig. 9. The cubic polyhedron can be visualized to give Ca2+ high inversion centrosymmetry. In general, if the Eu3+ ions locate at a site of inversion symmetry, then the 5D0 → 7F1 is the main transition, contrariwise, the 5D0 → 7F2 is the dominated transition.26,27 As seen in Fig. 9, the high intensity ratio between 590 nm (5D0 → 7F1) and 615 nm(5D0 → 7F2) indicates that the Eu3+ ions occupy a site of inversion symmetry in the CaF2–YF3 matrix, which is consistent with the above analysis.
 |
| Fig. 9 Excitation (left) and emission (right) emission spectra of Eu3+ doped CaF2–YF3. | |
4. Conclusion
In summary, our work provided a facile method to synthesize cubic CaF2–YF3 ternary fluoride microspheres through introducing alkaline-earth ions as dopants in a hydrothermal system. The synthetic method was based on the chelating and capping ability of Na2H2L. Our investigation reveals that the reaction conditions play important role in determining the final morphology and size of the products. Furthermore, the possible formation mechanism for the microspheres was termed into three steps as a nanoparticle aggregation process. Finally, the luminescent investigation indicates that the earth ions occupy a site of inversion symmetry in the cubic-phase CaF2–YF3 matrix.
Acknowledgements
This work is financially supported by the National Natural Foundation of China (Grant no. 21271167) and the Fund for Creative Research Groups (Grant no. 21221061), and the National Basic Research Program of China (973 Program, Grant no. 2014CB643803).
References
- B. L. Cushing, V. L. Kolesnichenko and C. J. O'Connor, Chem. Rev., 2004, 104, 3893–3946 CrossRef CAS PubMed.
- A. R. Tao, S. Habas and P. Yang, Small, 2008, 4, 310–325 CrossRef CAS PubMed.
- F. Esteban-Betegon, C. Zaldo and C. Cascales, Chem. Mater., 2010, 22, 2315–2324 CrossRef CAS.
- S. Kundu, A. Kar and A. Patra, J. Lumin., 2012, 132, 1400–1406 CrossRef CAS PubMed.
- Y. Zheng, Y. Huang, M. Yang, N. Guo, H. Qiao, Y. Jia and H. You, J. Lumin., 2012, 132, 362–367 CrossRef CAS PubMed.
- B. Shao, Q. Zhao, N. Guo, Y. Jia, W. Lv, M. Jiao, W. Lu and H. You, CrystEngComm, 2013, 15, 5776–5783 RSC.
- X. Sun and Y. Li, Chem. Commun., 2003, 1768–1769 RSC.
- Y. Jin, W. Qin and J. Zhang, J. Fluorine Chem., 2008, 129, 515–518 CAS.
- P. Gao, Y. Xie and Z. Li, Eur. J. Inorg. Chem., 2006, 3261–3265 CrossRef CAS PubMed.
- G. H. De, W. P. Qin, J. Zhanga, J. H. Zhang, Y. Wang, C. Y. Cao and Y. Cui, J. Solid State Chem., 2006, 179, 955–958 CrossRef CAS PubMed.
- Q. Zhao, B. Shao, W. Lu, Y. Jia, W. Lv, M. Jiao and H. You, Dalton Trans., 2013, 15482–15488 RSC.
- L. F. Johnson, H. j. Guggenhe, F. w. Ostermay and T. C. Rich, J. Appl. Phys., 1972, 43, 1125 CrossRef CAS PubMed.
- S. Bigotta, D. Parisi, L. Bonelli, A. Toncelli, M. Tonelli and A. Di Lieto, J. Appl. Phys., 2006, 100, 013109 CrossRef PubMed.
- V. Toccafondo, S. A. Cerqueira Jr, S. Faralli, E. Sani, A. Toncelli, M. Tonelli and F. Di Pasquale, J. Appl. Phys., 2007, 101, 023104 CrossRef PubMed.
- N. I. Sorokin and B. P. Sobolev, Phys. Solid State, 2008, 50, 416–421 CrossRef CAS.
- B. Moine and L. Beauzamy, J. Lumin., 2013, 142, 135–138 CrossRef CAS PubMed.
- D. Chen, Y. Yu, F. Huang, P. Huang, A. Yang and Y. Wang, JACS, 2010, 132, 9976–9978 CrossRef CAS PubMed.
- D. Chen, Y. Yu, F. Huanga and Y. Wang, Chem. Commun., 2011, 47, 2601–2603 RSC.
- Y. Huang, H. You, G. Jia, Y. Zheng, Y. Song, M. Yang, K. Liu and L. Zhang, J. Phys. Chem. C, 2009, 113, 16962–16968 CAS.
- Y. Zheng, H. You, G. Jia, K. Liu, Y. Song, M. Yang and H. Zhang, Cryst. Growth Des., 2009, 9, 5101–5107 CAS.
- G. B. Deacon and R. J. Phillips, Coord. Chem. Rev., 1980, 33, 227–250 CrossRef CAS.
- J. Wang, Y. Xu, M. Hojamberdiev and G. Zhu, J. Alloys Compd., 2009, 487, 358–362 CrossRef CAS PubMed.
- Z. J. Wang, F. Tao, L. Z. Yao, W. L. Cai and X. G. Li, J. Cryst. Growth, 2006, 290, 296–300 CrossRef CAS PubMed.
- F. Maxim, P. Ferreira, P. M. Vilarinho, A. Aimable and P. Bowen, Cryst. Growth Des., 2010, 10, 3996–4004 CAS.
- H. Zhan, X. Yang, C. Wang, C. Liang and M. Wu, J. Phys. Chem. C, 2010, 114, 14461–14466 CAS.
- X. Y. Chen and G. K. Liu, J. Solid State Chem., 2005, 178, 419–428 CrossRef CAS PubMed.
- F. Tao, Z. Wang, L. Yao, W. Cai and X. Li, J. Phys. Chem. C, 2007, 111, 3241–3245 CAS.
Footnote |
† Electronic supplementary information (ESI) available. See DOI: 10.1039/c4ra04185b |
|
This journal is © The Royal Society of Chemistry 2014 |
Click here to see how this site uses Cookies. View our privacy policy here.