DOI:
10.1039/C4RA03171G
(Paper)
RSC Adv., 2014,
4, 25683-25691
An advanced preparation and characterization of the PET/MgAl-LDH nanocomposites
Received
8th April 2014
, Accepted 15th May 2014
First published on 15th May 2014
Abstract
A new nanocomposite poly(ethylene terephthalate)/sulfanilic acid salt-modified layered double hydroxide (PET/MgAl LDH-SAS) was synthesized by an in situ polymerization method using MgAl LDH-SAS as a catalyst. This study employed a magnesium–aluminum layered double hydroxide (MgAl LDHs) with various particle sizes, which was modified by sulfanilic acid salt (SAS) through the hydrothermal process to form the MgAl LDH-SAS, and then intercalated by bis-hydroxy ethylene terephthalate (BHET) to form PET/MgAl LDH-SAS. Because of MgAl LDH-SAS, catalytic activity increased the polymerization rate, and nanocomposites also exhibited good thermal stability without the decomposition during the PET polymerization. The results indicated that the modified MgAl LDH-SAS improves the interlayer compatibility between the PET and MgAl LDH-SAS layers, thus making it easier for the oligomer to enter the gallery of MgAl LDH-SAS layers. Thus, the polymer chains can be included between the LDHs layers during the polymerization of the polymer matrix. The gas barrier, thermomechanical properties, and crystallization behavior of these new types of PET nanocomposites are investigated.
1. Introduction
Polyethylene terephthalate (PET) is a hydrophobic and semi-crystalline polymer containing numerous excellent properties such as mechanical strength, thermal stability, fatigue resistance, high crystal-melting temperature, good flexibility, and low cost, etc. It finds applications in electronic-packing materials, molding compounds, passive components, information-storage materials, and food and beverage packaging.1 A large-scale industrial PET production is normally carried out in two stages: one is the oligomerization of bis(2-hydroxyethyl) terephthalate (BHET), and another associated with prepolymer is synthesized either through esterification or transesterification of terephthalic acid (TPA) or dimethyl terephthalate (DMT) with ethylene glycol (EG). However, manganese or zinc acetate catalysts used for transesterification can catalyze the polycondensation reaction but they do not provide satisfactory products because they are also active in ester decomposition.2 Moreover, commonly, PET is manufactured by a different catalyst, mostly an antimony compound for a continuous polycondensation step in most commercial plants, which exploits the economy of scale. However, residual heavy-metal catalysts in PET products are harmful to the health of mammals, particularly when used in food or beverage packaging. Thus, the development of a method for the rapid polymerization of PET without the addition of heavy-metal catalysts is desirable.3
Fortunately, organically modified layered double hydroxides (LDHs) provide an opportunity to solve the above mentioned problems. LDHs are a family of compounds such as Zn/Al, Mn/Al, Fe/Al, Li/Al, and Mg/Al types of hydrophilic and hydrophobic LDHs, which are synthesized and modified by different organo-modifiers.4 In general, LDHs can be applied as catalysts, photocatalysts, ion exchangers, separation science, and adsorbents, etc.5 Here, we developed a modified LDH as a new catalyst without heavy metals. The major advantage of LDHs is that their particle size and aspect ratio can be controlled by changing the reaction conditions. The study on the LDH nanocomposites with various polymers, concerning physical properties and dispersion, has been widely reported.6 In this paper, our focus is on PET/MgAl LDH-SAS nanocomposites, which were synthesized via an in situ polymerization route by using MgAl LDH-SAS. LDH has catalytic properties and has been used for the synthesis of nanocomposites, following a novel polymerization process to proportionally disperse the stratiform inorganic materials in PET and form nanocomposites. It was proposed that the LDH-SAS nucleophilic attack on bis(2-hydroxyethyl) terephthalate (BHET) proceeded via the activation of the hydroxyl end group of BHET to form an ester carbonyl bond, which is followed by the subsequent intermolecular rearrangement to generate a new ester bond. The thermal and mechanical properties and the morphologies of the obtained PET/LDH-SAS nanocomposites were then investigated, and the results were discussed briefly.
2. Experimental
2.1 Materials
All the chemicals used were of analytical grade or of the highest purity commercially available. Aluminum nitrate nonahydrate (Al(NO3)3·9H2O), sodium hydroxide (NaOH) were purchased from SHOWA. Magnesium nitrate hexahydrate (Mg(NO3)2·6H2O) and bis(2-hydroxyethyl) terephthalate (BHET) were purchased from Sigma Aldrich, and sulfanilic acid salt (SAS) was purchased from J. T. Baker. Commercial MgAl LDH was purchased from Desunnano Co. Ltd, Taiwan, and double-distilled, high-purity water was obtained from the Milli-Q water (Millipore) system.
2.2 Preparation of organomodified LDHs
Experimentally, 34.65 g of 0.135 mol Mg(NO3)2·6H2O and 25.38 g of 0.067 mol Al(NO3)3·9H2O were dissolved in 240 ml of deionized water to form a clear solution; the pH of the resulting solution was then maintained at 10 ± 0.1 by adding 21.6 g of 0.54 mol 30 ml NaOH solution. This solution was rapidly agitated at room temperature for 2 min and then placed in a high-pressure autoclave to react at 100 °C and 150 °C for 24 h to form LDH precipitation. The obtained precipitation were collected by centrifugation and washing with deionized water, followed by freeze-drying. The synthesized samples are designated as MgAl LDH-100 °C and MgAl LDH-150 °C. Synthesized LDHs and commercial MgAl LDH (CL94) were calcined at 600 °C for 24 h to produce magnesium–aluminum layered double oxide (LDO). After LDO is reconstructed and modified with SAS both synthesized and commercial LDHs, sulfanilic acid salt (SAS) (at 1.5 times the AEC of the magnesium–aluminum layered double hydroxide) was used as a modifier and dissolved in 50 ml of water to form a modifier aqueous solution. 10 g of magnesium–aluminum layered double oxide was then slowly added to the modifier aqueous solution, which was then placed in a high-pressure autoclave to react at 100 °C overnight with agitation to form MgAl LDH-SAS precipitation. The precipitation was collected by centrifugation and then washed with deionized water, followed by freeze-drying. Modified samples are designated as MgAl100 °C LDH-SAS, MgAl150 °C LDH, and CL94 LDH-SAS.
2.3
In situ polymerization of PET/LDH-SAS nanocomposites
Organo-modified LDHs were then blended with the bis(2-hydroxyethyl) terephthalate (BHET), and LDH-SAS contents of the nanofillers were 0.1, 0.5, and 1.0 wt% with respect to BHET. BHET was melted at 100 °C with uniform agitation to form a mixture and after cooling to room temperature, the mixture was milled to form a powder. This powder was then uniformly blended with another BHET and reacted at 270 °C to form a composite material of the magnesium–aluminum layered double hydroxide and PET. Finally, synthesized materials are represented as PET/MgAl100 °C LDH SAS-0.1 wt%, PET/MgAl100 °C LDH SAS-0.5 wt%, PET/MgAl100 °C LDH SAS-1.0 wt%, PET/MgAl150 °C LDH SAS-0.1 wt%, PET/MgAl150 °C LDH SAS-0.5 wt%, and PET/MgAl150 °C LDH SAS-1.0 wt%, and PET/CL94 LDH SAS-0.1 wt%, PET/CL94 LDH SAS-0.5 wt%, PET/CL94 LDH SAS-1.0 wt%, respectively.
3. Characterization
X-ray diffraction was carried out on a PANalytical PW3040/60 X'Pert Pro, with Cu Kα radiation (45 kV, 40 mA) and wavelength λ = 1.54 Å. The scan angle covered 2° < 2θ < 80° for LDHs and nanocomposites at a scan speed of 3° min−1. IR spectra were recorded with a JASCO, FTIR-4200 Type A spectrometer using KBr pellets. The morphology of PET/MgAl LDH nanocomposites was measured by scanning electron micrographs (SEM), and was obtained on a JEOL JSM 6500F. Transmission electron microscopy (TEM) images were obtained on a Model JEOL JEM2010, 200 kV. A sample with a thickness of 80 nm was prepared using a Leica Ultracut-UCT to verify the physicochemical properties of LDHs. The chemical structure and the inhibitive effect the side products of the synthesized nanocomposites was confirmed by NMR spectra (Bruker, Avance 400 MHz). The preparation of the PET nanocomposites was dissolved in deuterated trifluoro acetic acid and a small amount of CDCl3. Thermogravimetric analysis (TGA) was carried out using SII TG/DTA6200, and the experiment was performed by a 10 mg sample of PET nanocomposites under air gas flow from 40 °C to 900 °C at a scanning rate of 10 °C min−1. Gas permeability analysis (GPA) was performed with a Yanco (GTR-31). UV-visible transmission and absorption spectra were obtained with a Cary-100 UV-vis spectrophotometer. The dynamic mechanical analysis (DMA) measurements were performed with a TA-Q800 instrument in the air at a scanning range of 40–100 °C with a heating rate of 3 °C min−1 with a film size of 1 cm × 4 cm (width and length) and a thickness of 80–100 μm. The molecular weight of the PET was measured by gel permeation chromatography (GPC) using an ALLIANCE-GPCV 2000 at 40 °C. The PET was first dissolved in 1,1,1,3,3,3-hexafluoro-2-propanol with a concentration of 0.5 mg ml−1 for the GPC analysis.
3.1 Results and discussion
3.1.1 Characterization of LDH and organo-modified LDH.
Diffraction patterns of the MgAl LDHs and SAS-modified MgAl LDH are shown in Fig. 1 and 2. Both samples show the diffraction maxima characteristic of hydrotalcite, the main examples, labeled in the figure with their Miller indices and corresponding to the reflections, are recorded at 2θ = 11.7° (d003), 23.4° (d006), and 34.5° (d009). The diffraction near 60.2° corresponds to the (d110), and 61.4° corresponds to the (d113) crystal planes. The basal spacing (d003) of MgAl LDH and MgAl LDH-SAS are 7.8 Å and 17.3 Å, respectively. The basal spacing (d003) of MgAl LDH-SAS increased, providing an evidence that modifier SAS is intercalated into the galleries of LDHs, as shown in Fig. 2. The most drastic changes in the MgAl LDH structure are due to SAS chemically bonding with the interlayer of LDH. The changes affecting the interlayer distances and the basal spacing increase up to 9.5 Å, providing the evidence for SAS intercalation. However, the shape and real intensity peaks of different modified MgAl LDH-SAS samples have the same basal spacing (d003), 17.3 Å, and different crystallinity. The stronger intensity of the peaks indicate a greater crystallinity of the sample.
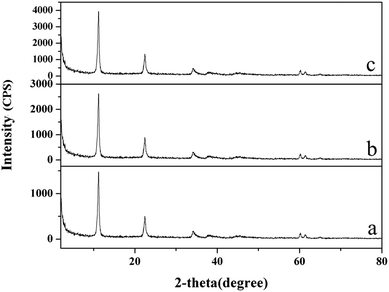 |
| Fig. 1 XRD profiles of pristine MgAl LDH from the different powders: (a) CL94 LDH, (b) MgAl LDH-100 °C, and (c) MgAl LDH-150 °C. | |
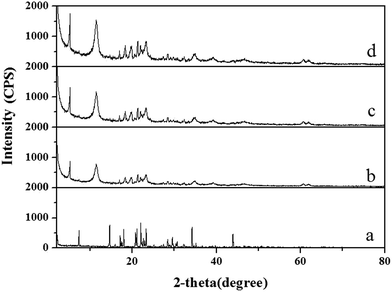 |
| Fig. 2 XRD profiles of modified-MgAl LDH-SAS from the different powders: (a) SAS, (b) CL94 LDH-SAS, (c) MgAl LDH-SAS-100 °C, and (d) MgAl LDH-SAS-150 °C. | |
SEM images of LDHs and modified LDHs are shown in Fig. 3(a)–(f), the order of the particle size is CL94 LDH-SAS < MgAl100 °C LDH-SAS < MgAl150 °C LDH-SAS, which is the respective particle size and size distributions of CL94 LDH-SAS, MgAl100 °C LDH-SAS and MgAl150 °C LDH-SAS from 50 to 120 nm, 50 to 150, 50 to 150 nm, and 100 to 350 nm. The average particle size is increased by increasing the reaction temperature. Before the modification, the particle size of CL94 LDH-SAS, MgAl100 LDH-SAS, and MgAl150 LDH-SAS is the same as after the modification. Thus, it can be anticipated that the increased space between the MgAl LDH nanolayers is due to the intercalation of SAS. This intercalation promotes the oligomer and increases the compatibility between the modified MgAl LDHs and PET molecules, leading to an easy exfoliation of the nanolayers in the polymer matrix to form well-dispersed PET/MgAl LDH nanocomposites.
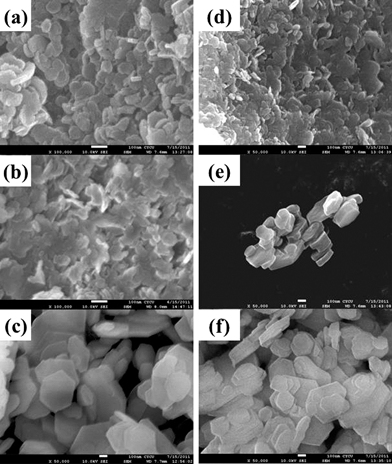 |
| Fig. 3 SEM images of modified MgAl LDH from the different powders: (a) CL94 LDH, (b) MgAl100 °C LDH, (c) MgAl150 °C LDH. (d) CL94 LDH-SAS, (e) MgAl100 °C LDH-SAS, and (f) MgAl150 °C LDH-SAS. | |
In addition to PXRD patterns, FTIR also confirms the formation of the LDH and modified LDH. Fig. 4(a)–(c) shows the FTIR spectra of CL94 LDH and synthesized MgAl LDHs at different temperatures. SAS-modified LDHs exhibit an important number of bands, among which the most characteristic can be assigned in the following manner. The broad peak around 3565 cm−1 can be ascribed to the stretching of OH groups attached to Al and Mg in the layers. The antisymmetric vibration of NO3−2 appears at 1384 cm−1.7 The band at 644 cm−1 represents Mg–O stretching vibrations, and the bands at 947, 790, and 554 cm−1 can be assigned to the Al–O stretching modes.8 From Fig. 4(d)–(f) spectra, because SAS incorporated into the MgAl LDH interlayer, stronger absorption peaks due to aromatic compound bands appeared at 1633 cm−1 to 1462 cm−1 and the bands at 1032, 1132 and 1160 cm−1 were the vibrations of the sulfanilic anion function group.
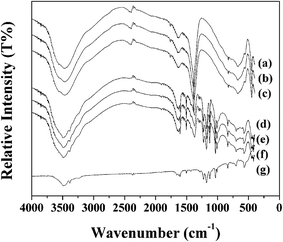 |
| Fig. 4 FT-IR spectrum of the different powders: (a) CL94 LDH, (b) MgAl100 °C LDH, (c) MgAl150 °C LDH, (d) CL94 LDH-SAS, (e) MgAl100 °C LDH-SAS, (f) MgAl150 °C LDH-SAS, and (g) SAS. | |
3.1.2 Morphology of the PET/LDH nanocomposites.
The PET/LDH nanocomposite morphology was confirmed by XRD and TEM for this analysis, and among all the samples, we chose 1.0 wt% modified LDH nanocomposites. XRD patterns of the PET nanocomposites containing 1.0 wt% SAS-modified LDHs are shown Fig. 5. The characteristic peak of MgAl LDH-SAS completely disappeared, indicating the exfoliation of nanolayers in the polymer matrix to form well-dispersed PET/LDH nanocomposites. The modified agent SAS anticipated that the increased basal spacing and hydrophobicity of the MgAl nanolayer because of the intercalation of SAS, supported an easy exfoliation of the stacking LDH layers during in situ polymerization, resulting in well-dispersed PET/MgAl LDH-SAS nanocomposites. The morphology measurements also show that the PET nanocomposites with different LDH are very similar to pure PET, indicating that these nanocomposites may form either intercalated or exfoliated dispersions. However, XRD patterns cannot be considered as conclusive evidence of monolayer exfoliation because they detect average diffractions from the overall X-ray irradiated sample area (scan range <1.5°). Because of the increased gallery spacing resulting from the partial intercalation of the PET molecules from XRD, it cannot be detected for LDH.
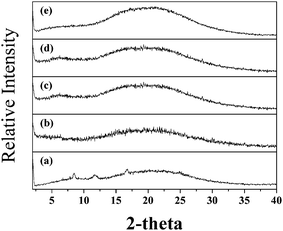 |
| Fig. 5 XRD patterns of PET/LDH nanocomposites with different particle sizes with 1.0 wt% modified LDHs: (a) PET/MgAl100 °C LDH (b) pristine PET, (c) PET/CL94 LDH-SAS-1.0 wt%, (d) PET/MgAl100 °C LDH-SAS-1.0 wt%, and (e) PET/MgAl150 °C LDH-SAS-1.0 wt%. | |
Therefore, TEM is the best way to describe the morphologies of nanocomposites. Fig. 6 shows the TEM images of PET nanocomposites containing 1.0 wt% CL94 LDH-SAS, 1.0 wt% MgAl100 °C LDH-SAS, and 1.0 wt% MgAl150 °C LDH-SAS. In Fig. 6(a)–(c), the dark areas representing the LDH layer stacks lose their ordered layer structures and are exfoliated with the layer by the PET molecules during in situ polymerization, and the gray/white areas representing exfoliated nanolayers are finely dispersed within the polymer matrix, indicating intercalated morphologies.9 From this result, it can be concluded that a critical distance exists between the LDH layers, and the favorable interaction between the LDH layers and polymer chains overwhelms the attractive interaction between the LDH plates. It can also be predicted that in the exfoliated PET matrix-modified LDHs, this could affect PET bulk properties such as thermal stability and mechanical properties.
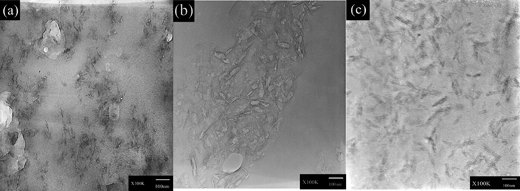 |
| Fig. 6 TEM morphologies of PET/MgAl LDH-SAS nanocomposites for a sample of 1.0 wt% modified LDHs: (a) PET/CL94 LDH-SAS-1.0 wt%, (b) PET/MgAl100 °C LDH-SAS-1.0 wt%, and (c) PET/MgAl150 °C LDH-SAS-1.0 wt%. | |
3.1.3 Thermomechanical properties of nanocomposites.
In the TGA curves of nanocomposites are shown in Fig. 7, indicating PET nanocomposites containing 0.1 wt% modified MgAl LDHs. Table 1 summarized the weight-reduction temperature (T5d) of 5% weight loss data for pristine PET and PET/LDH nanocomposites with different MgAl LDH-SAS. The thermal stability of the nanocomposite is 15 °C higher than that of pristine PET. It is believed that the introduction of LDH-SAS into the PET matrix can improve thermal stability. The 5% weight-reduction temperature of PET/MgAl150 °C LDH-SAS 0.1% is 400 °C and that of the pristine PET is 385 °C. The exfoliated LDHs exhibit an efficient barrier action to reduce the permeability of the thermal current.10
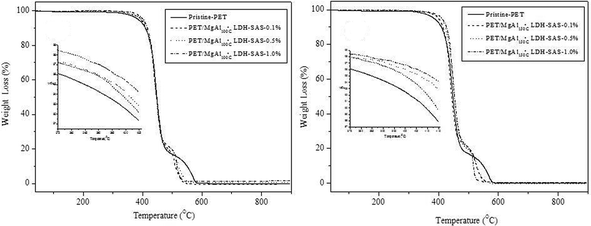 |
| Fig. 7 TGA of curves of pristine PET and PET/modified LDH nanocomposites. | |
Table 1 PET/LDH nanocomposites' thermal, crystallization and mechanical properties
Sample |
T
5d (°C) |
T
ch (°C) |
T
cc (°C) |
T
on (°C) |
T
1/2 (min) |
Storage modulus (Mpa) |
Pristine PET |
385 |
121.0 |
217.1 |
227.7 |
1.06 |
1854 |
PET/CL94 LDH-SAS-0.1 wt% |
394 |
130.6 |
199.6 |
221.4 |
2.18 |
2706 |
PET/MgAl100 °C LDH-SAS-0.1 wt% |
396 |
135.3 |
197.0 |
220.7 |
2.37 |
2780 |
PET/MgAl150 °C LDH-SAS-0.1 wt% |
400 |
138.6 |
196.9 |
220.8 |
2.39 |
2912 |
The DSCs of the pristine PET and PET/modified-LDHs nanocomposites are shown in Fig. 8 and Fig. 9. All the samples were heated well beyond their melting temperature and cooled −0 °C before the second test run, and the results are summarized in Table 2. The heating crystal temperatures (Tch) of the exothermic crystallization peaks are proportional to the particle sizes and aspect ratio during the heating process. However, the cooling crystal temperatures (Tcc) of the exothermic crystallization peaks are inversely proportional to the particle sizes and aspect ratio during the cooling process. It indicates that the modified LDH nanofillers acted as a nucleating agent for crystallization and accelerated the crystallization rate of the PET matrix. In Fig. 8, a prominent crystallization exothermic peak in the DSC thermograms recorded during the cooling period shows that the sample melts with a constant cooling rate. The catalysis properties can be obtained from the half-crystallization time (t1/2):
| 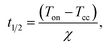 | (1) |
where
Ton is the crystallization onset temperature in which the thermograph initially departs from the baseline,
Tcc is the temperature where the exothermal shows a peak, and
χ is the cooling rate (°C min
−1).
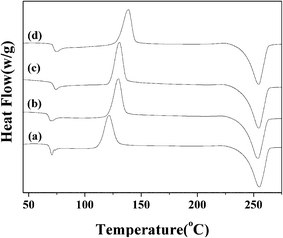 |
| Fig. 8 DSC thermograms of pristine PET and PET/modified LDH nanocomposites of heating scans: (a) pristine PET, (b) PET/CL94 LDH-SAS-0.1 wt%, (c) PET/MgAl100 °C LDH-SAS-0.1 wt%, and (d) PET/MgAl150 °C LDH-SAS-0.1 wt%. | |
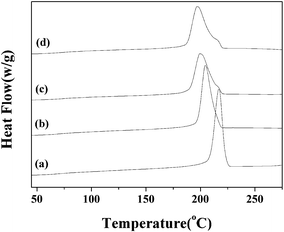 |
| Fig. 9 DSC thermograms of pristine PET and PET/modified LDH nanocomposites of cooling scans: (a) pristine PET, (b) PET/CL94 LDH-SAS-0.1 wt%, (c) PET/MgAl100 °C LDH-SAS-0.1 wt%, and (d) PET/MgAl150 °C LDH-SAS-0.1 wt%. | |
Table 2 PET/LDH nanocomposites' gas-barrier and optical properties
Sample |
Gas barrier |
UV |
O2 |
N2 |
375 nm |
550 nm |
800 nm |
Pristine PET |
0.238 |
0.068 |
79 |
84.6 |
86.5 |
PET/CL94 LDH-SAS-0.1 wt% |
0.114 |
0.024 |
78.5 |
85.0 |
86.4 |
PET/MgAl100 °C LDH-SAS-0.1 wt% |
0.107 |
0.023 |
79.9 |
84.3 |
86.8 |
PET/MgAl150 °C LDH-SAS-0.1 wt% |
0.099 |
0.019 |
70.6 |
81.9 |
84.7 |
The crystallization properties of the PET/LDH nanocomposites are described in Table 2. In all nanocomposites, the crystallization onset temperature and the cooling crystal temperature values for pristine PET are higher than those of the PET/modified LDH nanocomposites. The PET/MgAl150 °C LDH-SAS-0.1% exhibits the highest half-crystallization time (2.39 min) and the lowest cooling crystal temperature (196.9 °C). This indicates that the polymer matrix particle size increases, and the polymer chain growth decreases, thus slowing crystallization time. This is because when crystallization came under the influence of the inorganic layered material to limit the crystallization velocity, the resulting increase in the crystallization period causes an obvious delay in the crystal effect. However, in the heating scans, the melting peak (Tm) and the glass-transition temperature (Tg) of all the nanocomposites were nearly identical regardless of the modified LDH particle size. It can be assumed that because of different particle sizes, the modified LDH nanofillers cannot affect the perfection and/or lamellar thickness of the PET crystals but they can decrease the crystallization rate and increase the half-crystallization time. However, the melting temperature of all nanocomposites remains unchanged.
Particles in a polymer matrix can act to reinforce the polymer's mechanical properties. When the polymer cannot be inserted between the lamellate, an ordinary composite is obtained in the layered particles. Table 1 presents the mechanical properties of PET and PET/MgAl LDH-SAS with different particle sizes. The storage modulus of the nanocomposites is increased 1058 Mpa more than that of pristine PET. The storage modulus of PET/MgAl150 °C LDH-SAS 0.1% at 40 °C is 2912 Mpa and that of pristine PET is 1854 Mpa. The tensile tests show that the storage modulus increases when an MgAl LDH-SAS filler is added to the PET because intercalated SAS could increase the compatibility between the LDH layers and the PET matrix; thus adhesion between LDH and PET molecules could be increased. Another possible reason is that during the in situ polymerization. SAS can covalently bond with PET to provide good adhesion between these two phases. This may be ascribed to the presence of the inorganic phase and the enhancement of the degree of crystallinity induced by the filler nucleation.
3.1.4 Optical and gas-barrier properties of nanocomposites.
The optical clarity, anti-ultraviolet and gas-barrier properties of the PET/LDH nanocomposites results are summarized in Table 2. The large particle size of MgAl150 °C LDH-SAS in the PET results in the largest improvement of these material properties. The optical clarity at 550 nm and the anti-ultraviolet property at UVA 375 nm of the PET/MgAl LDH-SAS nanocomposites were measured by a UV-visible spectrophotometer. There are UV-visible transmission data of the membranes (100 ± 20 μm) for pure PET and PET/MgAl LDH-SAS nanocomposites, with different particle sizes of MgAl LDH-SAS. When observing the entire visible-light wavelength range (400–800 nm), the optical transmission of pristine PET with a wavelength of 550 nm was 84.6%, and the increasing LDH particle sizes of the PET/MgAl LDH-SAS nanocomposites show identical transmission ability in the visible-light region. In addition, the anti-UV properties improved from a UVA transmission of 79% of pristine PET down to a UVA transmission of 70.6% for the PET/MgAl150 °C LDH-SAS nanocomposites. The anti-ultraviolet property of the PET/MgAl150 °C LDH-SAS nanocomposites results from large aspect ratio and particle sizes of the LDHs, which provide the reflection of the UV light, and a good dispersion of the LDH platelets, which increase the UV-light pathway in the PET matrix.
Impermeable PET/LDH nanocomposites block gases transported through a polymer matrix and travel longer diffusive paths by creating a tortuous pathway force for permeation. Hence, a higher level of exfoliation is favorable for the enhancement of barrier properties.11 As previously mentioned, the presence of modified LDH increases the crystal content of the nanocomposites. The gas permeability of the pristine PET and the PET/MgAl LDH-SAS nanocomposite results are summarized in Table 3. Moreover, the O2 and N2 permeability of PET/MgAl150 °C LDH-SAS are 0.099 and 0.019 barriers, respectively. They are significantly improved barrier properties than that of pristine PET (0.238 barrier for O2 and 0.068 barrier for N2) because the nanoscale dispersion of modified LDH platelets in the PET matrix increases the pathway of gas diffusion with different particle sizes. All nanocomposites exhibit higher barrier properties than the pristine PET due to the presence of LDHs and larger crystal content. The gas permeability is calculated as
| 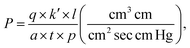 | (2) |
where
q is the permeation amount,
k′ is the coefficient,
l is the thickness,
p is the pressure,
a is the permeation area and
t is the measurement time.
Table 3 PET/LDH nanocomposite properties of the polymerization period, molecular weight and coefficient of polymerization rate
Sample |
Polymerization period (min) |
M
w
|
k/[g(mol min)−1] |
Pristine PET |
490 |
36 000 |
72.53 |
PET/CL94 LDH-SAS-0.1 wt% |
100 |
44 241 |
439.87 |
PET/MgAl100 °C LDH-SAS-0.1 wt% |
120 |
35 012 |
347.58 |
PET/MgAl150 °C LDH-SAS-0.1 wt% |
100 |
31 548 |
313.30 |
3.1.5 Catalyst and the catalyst mechanism of nanocomposites.
The various molecular weight populations of the PET/MgAl LDH-SAS nanocomposites would be affected by the different particle sizes of the modified LDHs (Table 3). PET/MgAl LDH-SAS nanocomposites present a slight reduction of molecular weight, which indicates the addition of LDH further influenced the polymer chain growth. However, the larger particle sizes of MgAl150 °C LDH-SAS had a higher anion exchange capacity for SAS than CL94 LDH-SAS and MgAl100 °C LDH-SAS, decreasing the polymer chain growth and slightly decreasing the molecular weight of the nanocomposites.
The 1H-NMR and 13C-NMR results shown in Fig. 10 the PET composite sample, which was adopted approach in current polymer science research.12 Chemical bonds can be influenced by the interaction between LDH nanofiller and PET molecules, and cannot discredit the PET structures.13 The structure of PET could be confirmed by observing the NMR chemical shift: 1H NMR (400 MHz, chloroform-D/CF3COOD, δ): 4.82 (s, CH2CH2), and 8.16 (s, C6H4); 13C NMR (400 MHz, chloroform-D/CF3COOD, δ): 167.94 (C
O), 63.86 (CH2CH2), 129.97 (ArC), and 133.28 (ArCH). From the structure of the PET nanocomposites, the 1H-NMR spectrum shows the polymeric CH2CH2 and C6H4 groups. The integration ratio of the CH2CH2 and C6H4 chemical shift at 1H-NMR was exactly 1
:
1. However, pristine PET and PET nanocomposites show the same peaks without any unusual signals such as chemical shifts or the appearance of new peaks in the spectra. The 13C NMR (400 MHz, chloroform-D/CF3COOD, δ): 167.94 (C
O), 63.86 (CH2CH2), 129.97 (ArC), and 133.28 (ArCH). Therefore, we expected that SAS in LDH layers could react with BHET during the ester interchange reaction, although additional peaks in corresponding bonds between SAS and PET were unfortunately not identified. It was observed that 1.0% of LDH-SAS content in the nanocomposites is too small to verify the existence of the additional bonds between SAS and PET. Finally, from the resulting 1H-NMR, we could extrapolate that adding LDH to the polymerization would not result in the formation of other chemical bonds.
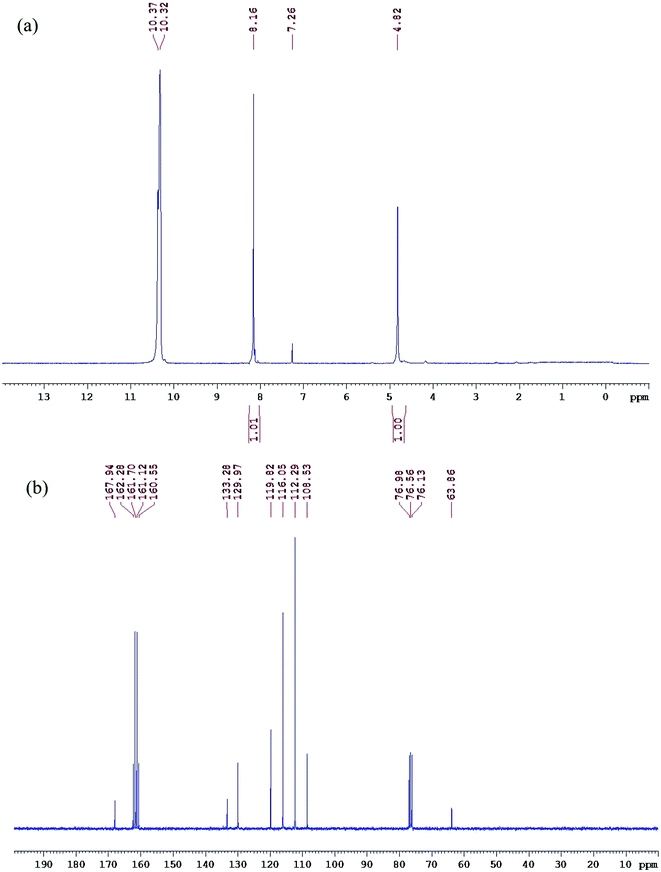 |
| Fig. 10 NMR spectra of PET nanocomposites: (a) 1H-NMR (b) 13C-NMR. | |
The modified-MgAl LDH catalysts were added in a molar ratio of 1/1000 relative to BHET. The modified-MgAl LDH catalytic activity is similar to LDH for the preparation of PET. Previously El-Toufaili et al. reported that LDH activity depends on the presence of hydroxides or interlayer anions and all of these active sites are easily accessible.14 For the BHET polycondensation-modified MgAl LDH as a catalyst, in this paper, we proposed the following routes for BHET polycondensation shown in Fig. 11. This result indicated that the monomer intercalates between the layers of LDH at the beginning of the reaction, enabling the complexation of oxygen-containing functional groups with the amine and hydroxide groups of the catalyst. Based on these findings, a polycondensation mechanism is proposed. One end group of the monomer is activated in the form of an alkoxide, which counterbalances the positive charge of the hydrotalcite layer. This alkoxide group attacks an ester carbonyl group fixed close to it, generating a new ester bond and a glycoxide species. The role of the hydrotalcite is to activate the reactants, rendering the attacking hydroxyl group more nucleophilic and the ester carbonyl group more electrophilic, and simultaneously fixing the reactant together in a favorable geometry. Therefore, we apply this mechanism for the inorganic layered material in the preparation of polyester.
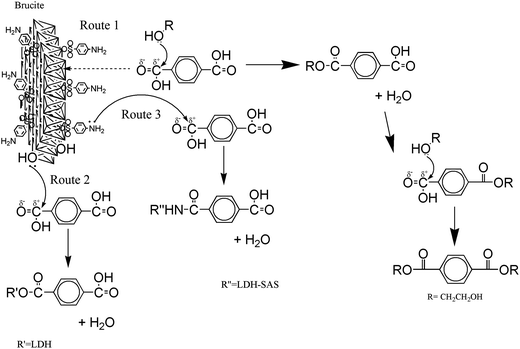 |
| Fig. 11 The catalytic mechanism of MgAl LDH is similar to the catalysts of the antimony triacetate. | |
The reaction's kinetic equation, derived from G. Rafter's equation, provides the method for determining the rate of polymerization as
where
t is the reaction time of polymerization,
k is the coefficient of the polymerization rate,
M0 is the average molecule weight of BHET, and
Mw is the molecular weight of the PET/MgAl LDH-SAS nanocomposites as determined by the GPC. According to G. Rafter's equation, the coefficient of the polymerization rate is determined as shown in
Table 3, providing the reactivity of the polymerization. Arrhenius' equations
15 are expressed as
|  | (4) |
and
| ln k ∝ −Ea. | (5) |
It is easy to see that a larger coefficient of the polymerization rate corresponds with a lower activation energy, which implies the improved reactivity of polymerization.
The coefficients of the polymerization rate of PET/CL94 LDH-SAS 0.1%, PET/MgAl100 °C LDH-SAS 0.1%, PET/MgAl150 °C LDH-SAS 0.1%, and pristine PET are 439.87, 347.58, 313.30, and 72.53 (k/[g(mol min)−1]). This indicates that an increase in the particle sizes of the MgAl LDH derivatives corresponds with a decrease in the coefficient of the polymerization rate of the PET nanocomposites, which implies reduced polymerization reactivity.
4. Conclusions
Here, we successfully report the in situ polymerization of PET/MgAl LDH-SAS nanocomposites using modified MgAl-LDH as a catalyst. The mechanism for the formation of PET/MgAl LDH-SAS nanocomposites by the driving force concept is proposed. In addition, modified MgAl-LDH catalytic activity depends on the basicity of its interlayer anions. The rate of proton removal from the hydroxyl end groups depends on the basicity of the interlayer anions. Therefore, the polycondensation of the BHET with MgAl-LDH as a catalyst most likely occurs by the reaction of an alkoxide end group with an ester end group fixed close to it. Increasing the basal spacing and hydrophobicity of the Mg/Al nanolayer because of the intercalation of SAS promoted easy exfoliation of the stacking LDH layers, resulting in well-dispersed PET/MgAl LDH-SAS nanocomposites. The modified-LDH not only exhibits catalyst properties but also participates in increasing the thermomechanical properties, crystallization behavior, and gas barrier properties of nanocomposites. The effect of exfoliated nanolayers, in which the raised crystal temperature (Tch) indicated the PET/modified LDH nanocomposites were better than that of the pristine PET. Segmentum posterius processing may slow crystallization to facilitate process completion when crystallization inconveniently shifts to an earlier time. The results indicate that increased particle sizes in the polymer matrix reduce polymer chain growth, thus slowing crystallization time. We expected that SAS in LDH layers could react with BHET during the ester interchange reaction. In addition, it is easy to understand that the larger the coefficient of polymerization rate, the lower the activation energy, which implies a better reactivity of polymerization. From the resulting 1H-NMR, we could extrapolate that loading LDH to the polymerization would not form other chemical bonds.
Acknowledgements
The authors are grateful to the Ministry of Economy Affairs of Taiwan and the National Science Council of Taiwan under Grant no. 99-EC-17-A-08-S1-143 and NSC-95-2113-M-033-008- MY3. Dr J. M. Yeh is gratefully acknowledged for assistance with the CO2 gas barrier measurements.
References
-
J. Scheirs and T. E. Long, Modern Polyesters: Chemistry and Technology of Polyesters and Copolyesters, Wiley, 2003 Search PubMed.
- W. A. MacDonald, Polym. Int., 2002, 51, 923 CrossRef CAS.
- L. Guihe, F. Zhifeng and C. Ding, China Pet. Process. Petrochem. Technol., 2013, 15, 65 Search PubMed.
- A. M. Youssef, T. Bujdosó, V. Hornok, S. Papp, A. F. A. Hakim and I. Dékán, Appl. Clay Sci., 2013, 77–78, 46–51 CrossRef CAS.
- A. Patzkó, R. Kun, V. Hornok, I. Dékány, T. Engelhardt and N. Schall, Colloids Surf., A, 2005, 265, 64–72 CrossRef.
- W. D. Lee and S. S. Im, J. Polym. Sci., Part B: Polym. Phys., 2007, 45, 28 CrossRef CAS.
- T. Cao, K. Xu, G. Chen and C.-y. Guo, RSC Adv., 2013, 3, 6282 RSC.
- T. Y. Tsai, S. W. Lu, Y. P. Huang and F. S. Li, J. Phys. Chem. Solids, 2006, 67, 938 CrossRef CAS.
- W. Cui, Q. Jiao, Y. Zhao, H. Li, H. Liu and M. Zhou, eXPRESS Polym. Lett., 2012, 6, 485 CrossRef CAS.
- S. S. Ray and M. Okamoto, Prog. Polym. Sci., 2003, 28, 1539 CrossRef CAS.
- E. L. Cussler, S. E. Hughes, W. J. Ward and R. J. Aris, J. Membr. Sci., 1988, 38, 161 CrossRef CAS.
- R. Saint-Loup, T. Jeanmaire and J. Robin, Polymer, 2003, 44, 3437 CrossRef CAS.
- R. Hariharan and A. G. Pinkus, Polym. Bull., 1993, 30, 91–95 CrossRef CAS.
- F. A. El-Toufaili, F. Ahmadniana, A. Dinse, G. Feix and K. H. Reichert, Mater. Eng., 2006, 291, 1136 CAS.
-
J. W. Moore and R. G. Pearson, Kinetics and Mechanism, John Wiley & Sons, New York, 3rd edn, 1981 Search PubMed.
|
This journal is © The Royal Society of Chemistry 2014 |
Click here to see how this site uses Cookies. View our privacy policy here.