DOI:
10.1039/C4RA01423E
(Communication)
RSC Adv., 2014,
4, 15630-15634
Facile surface modification of high-voltage lithium-ion battery cathode materials with electroconductive zinc antimonate colloidal nanoparticles
Received
18th February 2014
, Accepted 17th March 2014
First published on 18th March 2014
Abstract
The high-voltage cell approach has garnered a great deal of attention as a simple and effective way to increase the energy density of lithium-ion batteries. Here, we demonstrate a new class of surface modification based on electroconducitve zinc antimonate (AZO, ZnSb2O6) colloidal nanoparticles as a facile and scalable interface engineering strategy for high-voltage cathode materials. The electroconductive AZO colloidal nanoparticles are directly introduced on the surface of cathode materials via simple one-pot solution coating followed by post heat-treatment, in contrast to traditional surface modification using metal oxide precursors that often requires complex sol–gel reaction and high-temperature calcination. LiCoO2 (LCO) powder is chosen as a model cathode material to explore the feasibility of AZO nanoparticle coatings. A salient feature of the AZO nanoparticle layers, as compared to conventional metal oxides-based coating layers that are electrically inert, is the provision of electronic conduction, which thus boosts the electronic conductivity of LCO powders. This beneficial effect of the AZO nanoparticle layers, in collaboration with their contribution to suppressing unwanted interfacial side reactions between delithiated LCO and liquid electrolytes, enables significant improvement in high-voltage (here, 4.4 V) cell performance (AZO nanoparticle-deposited LCO (AZO–LCO) vs. pristine LCO: capacity retention after 50th cycle = 84% vs. 28%, discharge rate capability (2.0 C/0.2 C) = 78% vs. 55%). The potential application of AZO–LCO in high-voltage cells is also discussed with an in-depth consideration of the variation in AC impedance and electrode polarization of cells during cycling.
Introduction
As a promising power source to accelerate the advent of rapidly growing industry fields such as smart portable electronics, (hybrid) electric vehicles, and grid-scale energy storage systems, high-energy density lithium-ion rechargeable batteries with reliable/sustainable electrochemical performances are highly required.1–3 Taking into account that energy density of cells is determined by two major factors (=coulomb capacity [C] and voltage [V]), one simple and effective way to achieve the aforementioned challenging goal is raising the charge cut-off voltage of cells.4–6
The high-voltage cell approach, however, has suffered from unwanted deterioration of cell performance (in particular, capacity loss during charge/discharge cycling). It is believed that these stringent concerns of high-voltage cells mainly arise from unwanted interfacial side reactions between delithiated cathode materials and liquid electrolytes, wherein liquid electrolytes are prone to electrochemical decomposition at high voltage conditions.7,8 Hence, to promote the progress of high-voltage cells, there is no doubt that understanding and control of interfacial phenomena between cathode material and liquid electrolyte, along with research efforts for developing advanced electrode and electrolyte materials, are highly needed as a prerequisite.
Among various approaches to control cathode materials–liquid electrolyte interface, surface modification of cathode materials with metal oxides such as Al2O3, ZrO2, AlPO4, and ZnO has been extensively investigated.9–12 Although these metal oxide-based materials turn out to be effective in suppressing the interfacial side reactions, however, they are electronically inert and thus act as a resistive layer impeding electronic conduction in cathodes. This limitation of the metal oxide coatings remains a big technical obstacle in bolstering cell performance (particularly at fast faradaic reactions).
Here, stimulated by the above-mentioned drawbacks of conventional metal oxide coatings, we present a new class of surface modification based on electroconducitve zinc antimonate (AZO, ZnSb2O6) colloidal nanoparticles as a facile and scalable interface engineering strategy for high-voltage cathode materials. AZO is known to be a kind of ternary antimonite, which is characterized with crystalline structure of two edge-sharing SbO6 octahedra. The SbO6 octahedra of AZO are distorted with three different Sb–O bonds, enabling AZO to be electrically active.13–15 Thus, it is envisaged that the electroconductive AZO nanoparticle coatings, as compared to electrically-inert metal oxide coatings, contribute to improving electronic conduction of cathode materials, in addition to acting as a protective layer that suppresses undesired interfacial side reactions between cathode materials and liquid electrolytes.
Another distinctive feature of the AZO nanoparticle-based surface modification is the easy processability. Instead of using AZO precursors that necessitate complex sol–gel reaction and high-temperature calcination, electroconductive AZO colloidal nanoparticles (dispersed in methanol solvent) are directly introduced on cathode materials (here, LiCoO2 (LCO) powders, one of the most widely used cathode materials in lithium-ion batteries, are chosen as a model system to explore the feasibility of AZO nanoparticle coatings) via simple one-pot solution coating followed by post heat-treatment, leading to the successful formation of AZO nanoparticles-deposited LCO (denoted as “AZO–LCO”).
Based on structural/physicochemical characterization of AZO–LCO powders, their potential application to high-voltage cells is investigated by analyzing electrochemical performance of the cells at various charge/discharge conditions, which is further discussed with an in-depth consideration of variation in AC impedance and electrode polarization of cells during cycling.
Experimental section
Bare LCO powders without any post treatment (average particle size (D50) ∼5 μm, Umicore, Korea) were poured into AZO coating solution (particle size = 10–20 nm, solid content = 1 wt%, solvent = methanol, FNC CHEM Co., Korea) and stirred for 1 h, followed by filtering and drying. The AZO nanoparticle-deposited LCO powders were then subjected to heat treatment at 400 °C for 5 h, in order to firmly fixate AZO nanoparticles on LCO surface. The chemical composition of AZO–LCO was measured by inductive coupled plasma-optical emission spectroscopy (ICP-OES, OPTIMA 7300 DV, PerkinElmer). The electronic conductivity of AZO–LCO (or pristine LCO) was characterized using linear four-point probe measurement system, where the average value was obtained by repeating measurement ten times at different position of a disc (diameter = 15 mm, thickness = 1 mm) fabricated with AZO–LCO (or pristine LCO) powders. The surface morphology of AZO–LCO was examined using a field emission scanning electron microscope (FE-SEM, Hitachi) equipped with an energy-dispersive spectrometer (EDS) and a transmission electron microscope (TEM, JEOL). The crystalline phase of AZO–LCO was analyzed with a powder X-ray diffractometer (XRD, MPD) using Cu Kα radiation. The cathodes incorporating AZO–LCO (or pristine LCO) powders were fabricated by coating NMP-based slurry with a mixture comprising 95 wt% of AZO–LCO (or pristine LCO) powders, 3 wt% of polyvinylidene fluoride (PVdF) binder, and 2 wt% of carbon black on an aluminum current collector. The areal mass loading of the cathodes was 14.5 mg cm−2. A unit cell (2032 coin) was assembled by sandwiching a PE separator (Tonen) between a natural graphite anode (graphite/PVdF/carbon black = 90/8/2 w/w/w) and the AZO–LCO cathode. The unit cell was then activated by being filled with a liquid electrolyte of 1 M LiPF6 in ethylene carbonate (EC)–dimethyl carbonate (DMC) = 1/1 v/v (Soulbrain). The discharge capacities and C-rate capability were evaluated by varying discharge current densities from 0.2 (=0.46 mA cm−2) to 2.0 C at a constant charge current density of 0.2 C under a voltage range of 3.0–4.4 V, wherein the charge/discharge capacities were determined based exclusively on the weight of AZO–LCO (or LCO) powders. The cycling performance of cells was evaluated at a charge/discharge current density of 1.0 C/1.0 C. The AC impedance (frequency range = 10−3 to 106 Hz at an amplitude of 10 mV) and cyclic voltammetry (scan rate = 0.1 mV s−1 under 2.5–4.4 V) of cells were obtained using a potentiostat/galvanostat with an impedance analyzer (VSP classic, Bio-Logic).
Results and discussion
Structural/physicochemical characterization of AZO–LCO
Structural uniqueness of AZO–LCO was elucidated, with a particular focus on the AZO nanoparticle layer. While the pristine LCO has smooth planes and no foreign materials (Fig. 1(a)), the AZO–LCO shows that a plethora of AZO nanoparticles are well strewed on the LCO surface (Fig. 1(b)). This unusual surface structure of AZO–LCO was also characterized by TEM measurement. Fig. 1(c) verifies that the AZO nanoparticles are successfully deposited on the LCO surface and their average thickness is approximately 20 nm, although perfectly-uniform morphology was not observed. Most AZO nanoparticles are observed to range in size from 10 to 20 nm (an inset of Fig. 1(c)), which is a good evidence to prove that mono- or bi-layers of AZO nanoparticles are established on the LCO surface. The presence of the AZO nanoparticle layer was further confirmed by analyzing an EDS image (Fig. 1(d)). The bright dots assigned to Sb elements of AZO nanoparticles are uniformly dispersed on the LCO surface. The loading amount of AZO nanoparticle layer was quantitatively estimated using ICP-OES analysis. The molar-based composition ratio of Co/Zn is observed to be 100/0.32, indicating that the amount of deposited AZO nanoparticles is very small compared to that of bulk LCO powders as speculated from the morphological analysis. The content of AZO coating layer is expected to crucially affect the suppression of side reactions at LCO–liquid electrolyte interface and also electrochemical performance of AZO–LCO. More detailed works on the optimization of AZO content and its influence on cell performance will be conducted in future studies.
 |
| Fig. 1 Structural characterization of AZO–LCO: (a) FE-SEM photograph of pristine LCO; (b) FE-SEM photograph of AZO–LCO. (c) TEM photograph of AZO–LCO (inset shows AZO colloidal nanoparticles dispersed in methanol). (d) EDS image (bright dots represent Sb elements of AZO nanoparticles) of AZO–LCO. (e) XRD patterns of pristine LCO and AZO–LCO. (f) A schematic representation illustrating morphology of AZO nanoparticle layers and their multifunctional effects in terms of electroconductive protection. | |
The XRD patterns of AZO–LCO were compared with those of pristine LCO. Both LCO samples show typical layered structure of hexagonal α-NaFeO2 type with R
m space group.16,17 Moreover, the lattice parameters of the pristine LCO and AZO–LCO were calculated by the Rietveld refinement of XRD patterns. The estimated lattice parameters of the AZO–LCO (a = 2.8145 Å and c = 14.04 Å) are similar to those of the pristine LCO (a = 2.8151 Å and c = 14.03 Å), revealing no significant crystallographic difference between the pristine LCO and AZO–LCO. This XRD result demonstrates that the layered crystalline structure of LCO is not impaired after the introduction of AZO nanoparticle layers. A schematic representation illustrating the structure of AZO nanoparticle layers and their multifunctional effects in terms of boosting electronic conductivity of LCO powders and also mitigating unwanted interfacial side reactions are displayed in Fig. 1(f).
Effect of AZO–LCO on high-voltage cell performance
Effect of AZO–LCO on high-voltage cell performance (here, 4.4 V is chosen as a representative high-voltage condition) was investigated. The discharge profiles (Fig. 2(a) and (b)) show that the cell polarization (particularly ohmic polarization18,19) is significantly alleviated at the AZO–LCO compared to the pristine LCO. Notably, this advantageous contribution to the cell polarization becomes more pronounced as discharge current densities are increased. The AZO–LCO presents the superior discharge C-rate capability (e.g., capacity at 2.0 C/capacity at 0.2 C = 78%), in comparison to the pristine LCO (=55%).
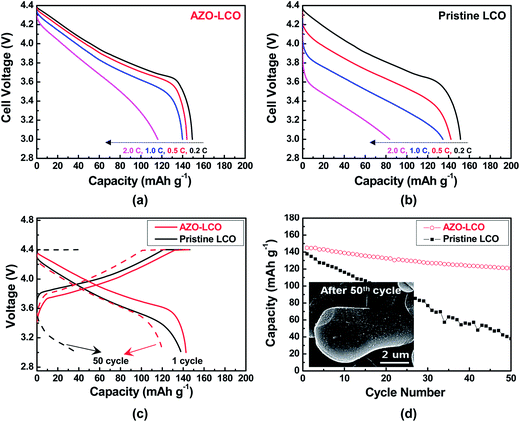 |
| Fig. 2 High-voltage (=4.4 V) cell performance, wherein charge/discharge capacities are determined based exclusively on the weight of AZO–LCO (or LCO) powders. Discharge profiles of cells as a function of discharge current density (i.e., discharge C-rate): (a) AZO–LCO/graphite; (b) pristine LCO/graphite. (c) Variation in charge/discharge profiles during cycling (charge/discharge current density = 1.0 C/1.0 C at voltage range of 3.0–4.4 V). (d) Comparison of cycling performance between pristine LCO and AZO–LCO (inset depicts surface morphology of AZO–LCO after 50th cycle). | |
This noticeable improvement in the cell polarization and discharge C-rate capability is explained by measuring electronic conductivity of AZO–LCO. The 4-point probe analysis shows that the AZO–LCO provides higher electronic conductivity (∼2.5 × 10−4 S cm−1) than the pristine LCO (∼9.8 × 10−5 S cm−1), where cathode discs comprising solely AZO–LCO (or pristine LCO) powders without the incorporation of PVdF binders and carbon black conductive additives were fabricated.20,21 This result demonstrates that the AZO nanoparticle layers effectively improve electronic conduction of LCO particles, thereby facilitating faradaic reaction of LCO over a wide range of discharge current density.
The high-voltage cycling performance (i.e., capacity retention as a function of cycle number) of AZO–LCO was investigated under relatively faster charge/discharge current density of 1.0 C/1.0 C. Fig. 2(c) shows that the AZO–LCO mitigates the cell polarization during cycling and also remarkably improves capacity retention, while capacity of the pristine LCO continues to sharply decline. Comparison of cycling performance between the pristine LCO and AZO–LCO was summarized in Fig. 2(d). The capacity retention after 50th cycle is found to be 84% for the AZO–LCO, in contrast to that (=28%) of the pristine LCO. Long-term structural durability of the AZO nanoparticle layers after being subjected to the high-voltage cycling was examined (an inset of Fig. 2(d)). The AZO nanoparticles are still well-adhered to the LCO surface and also no serious morphological disruption is observed in the AZO–LCO.
This advantageous effect of the AZO–LCO on the high-voltage cycling performance is further verified by analyzing the variation in the AC impedance spectra of fully charged cells during cycling. Previous studies22–24 on a possible equivalent circuit of cells reported that the semicircle of impedance spectra at high frequency ranges indicates resistance of surface film formed on electrode materials and the semicircle observed at medium-to-low frequency regions is ascribed to charge transfer resistance between electrode materials and liquid electrolytes. Fig. 3(a) depicts that, after 50th cycle, the cell impedance of pristine LCO significantly increases (ZRe (50th cycle) − ZRe (1st cycle) = ΔZRe > 2000 ohm). This result shows that the sharp capacity fading of pristine LCO during cycling is mainly attributed to formation of unwanted resistive layers,25–27 which may impede charge transfer toward LCO, giving rise to the continued increase of cell impedance. In comparison, for the AZO–LCO, the growth of cell impedance is considerably retarded (ΔZRe ≅ 100 ohm, Fig. 3(b)). This AC impedance analysis demonstrates the AZO nanoparticle layer prevents the direct exposure of delithiated LCO to liquid electrolyte, which in turn mitigates the decomposition of liquid electrolyte on LCO surface during the high-voltage cycling. In addition, the lower cell impedance of AZO–LCO at the 1st cycle (ZRe ≅ 27 ohm for pristine LCO vs. 18 ohm for AZO–LCO, insets of Fig. 3(a) and (b)) confirms the improvement in electronic conduction owing to the electroconductive AZO nanoparticle layers.
 |
| Fig. 3 Electrochemical analysis of high-voltage (=4.4 V) cells upon charge/discharge cycling. Variation in AC impedance spectra (1st → 50th cycle) of cells assembled with: (a) pristine LCO; (b) AZO–LCO. Variation in cyclic voltammograms (1st → 50th cycle) of cells assembled with: (c) pristine LCO; (d) AZO–LCO. | |
As another evidence to prove the superior cycling performance of AZO–LCO, the variation in electrode polarization during cycling was monitored using cyclic voltammetry. In cyclic voltammograms, potential difference between anodic and cathodic peak (=ΔV) is known to reflect the reversibility of Li+ intercalation/deintercalation processes, where larger potential difference represents stronger electrode polarization.28,29 In the pristine LCO (Fig. 3(c)), the ΔV increases from 0.33 V (after 1st cycle) to 1.12 V (after 50th cycle), revealing the serious deterioration in reversibility of Li+ (de)intercalation during cycling. On the other hand, at the AZO–LCO, the growth of ΔV with cycling is significantly retarded (Fig. 3(d), ΔV = 0.27 (after 1st cycle) → 0.35 (after 50th cycle)). This result exhibits that the (de)intercalation reaction of lithium ions is facilitated at the AZO–LCO, thus contributing to the retarded growth of ΔV during cycling.
The abovementioned electrochemical analysis results underline that the electroconductive AZO nanoparticle layers suppress the unwanted interfacial side reactions between LCO and liquid electrolyte. As a consequence, the formation of resistive layers that hamper charge transfer at LCO/liquid electrolyte interface is mitigated. Subsequent studies of AZO-based surface modification will be devoted to elucidating compositional variation of AZO nanoparticle layers and also investigating its effect on cell performance as a function of charge voltage, with an in-depth characterization of byproduct formation on electrode surface (specifically, transition metal dissolution from delithiated cathode materials and hydrofluoric acid-triggered decomposition of LiPF6 salts).
Conclusions
We have presented the electroconducitve AZO colloidal nanoparticles-mediated surface modification as a new interface control strategy to bolster high-voltage (4.4 V was chosen as a representative condition) cell performance of cathode materials (LCO powders were selected as a model system). In contrast to using AZO precursors, the AZO nanoparticles were directly introduced on LCO surface via simple one-pot solution coating followed by post heat-treatment. The AZO nanoparticle layers effectively improved electronic conduction of LCO powders, in addition to alleviating unwanted interfacial side reactions between LCO and liquid electrolytes. These multifunctional effects of AZO nanoparticle layers brought remarkable improvement in the high-voltage cell performance, which was verified by observing the retarded growth in the AC impedance and electrode polarization of cells. We believe that the AZO colloidal nanoparticles-based interface engineering opens a facile and scalable route for surface modification of cathode materials and is also suggested as a versatile platform technology that can be readily applicable to a variety of next-generation electrode materials (including high-voltage spinel/phosphate cathode materials and high-capacity metal/metal alloy anode materials).
Acknowledgements
This work was supported by Energy Efficiency and Resources R&D program (20112010100150) under the Ministry of Knowledge Economy, Republic of Korea. This research was also supported by the National Research Foundation of Korea Grant funded by the Korean Government (MEST) (NRF-2009-C1AAA001-2009-0093307). This research was also supported by the MSIP (Ministry of Science, ICT & Future Planning), Korea, under the C-ITRC (Convergence Information Technology Research Center) support program (NIPA-2013-H0301-13-1009) supervised by the NIPA (National IT Industry Promotion Agency). This study was also supported by the BK21 Plus funded by the Ministry of Education, Korea (10Z20130011057).
References
- P. G. Bruce, B. Scrosati and J. M. Tarascon, Angew. Chem., Int. Ed., 2008, 47, 2930–2946 CrossRef CAS PubMed.
- H. Li, Z. Wang, L. Chen and X. Huang, Adv. Mater., 2009, 21, 4593–4607 CrossRef CAS.
- C. Liu, F. Li, L. P. Ma and H. M. Cheng, Adv. Mater., 2010, 22, E28–E62 CrossRef CAS PubMed.
- A. Manthiram, J. Phys. Chem. Lett., 2011, 2, 176–184 CrossRef CAS.
- B. Scrosati, J. Hassoun and Y. K. Sun, Energy Environ. Sci., 2011, 4, 3287–3295 CAS.
- J. H. Park, J. H. Cho, S. B. Kim, W. S. Kim, S. Y. Lee and S. Y. Lee, J. Mater. Chem., 2012, 22, 12574–12581 RSC.
- M. S. Whittingham, Chem. Rev., 2004, 104, 4271–4301 CrossRef CAS PubMed.
- B. L. Ellis, K. T. Lee and L. F. Nazar, Chem. Mater., 2010, 22, 691–714 CrossRef CAS.
- S. T. Myung, K. Izumi, S. Komaba, T. K. Sun, H. Yashiro and N. Kumagai, Chem. Mater., 2005, 17, 3695–3704 CrossRef CAS.
- Z. Chen and J. R. Dahn, Electrochem. Solid-State Lett., 2002, 5, A213–A216 CrossRef CAS.
- J. Cho, Y. W. Kim, B. Kim, J. G. Lee and B. Park, Angew. Chem., Int. Ed., 2003, 42, 1618–1621 CrossRef CAS PubMed.
- W. Chang, J. W. Choi, J. C. Im and J. K. Lee, J. Power Sources, 2010, 195, 320–326 CrossRef CAS.
- S. B. M. Krishna, A. R. Babu, R. Sree and C. D. K. Rao, J. Non-Cryst. Solids, 2010, 356, 1754–1761 CrossRef CAS.
- W. Liu, P. Lin, H. Jin, H. Xue, Y. Zhang and Z. Li, J. Mol. Catal. A: Chem., 2011, 349, 80–85 CrossRef CAS.
- N. Chantarat, S. H. Hsu, C. C. Lin, M. C. Chiang and S. Y. Chen, J. Mater. Chem., 2012, 22, 8005–8012 RSC.
- K. Kushida and K. Kuriyama, J. Cryst. Growth, 2002, 237, 612–615 CrossRef.
- I. D. Scott, Y. S. Jeong, A. S. Cavanagh, Y. Yan, A. C. Dillon, S. M. George and S. H. Lee, Nano Lett., 2011, 11, 414–418 CrossRef CAS PubMed.
- J. H. Park, J. H. Cho, W. Park, D. Ryoo, S. J. Yoon, J. H. Kim, Y. U. Jeong and S. Y. Lee, J. Power Sources, 2010, 195, 8306–8310 CrossRef CAS.
- J. H. Cho, J. H. Park, M. H. Lee, H. K. Song and S. Y. Lee, Energy Environ. Sci., 2012, 5, 7124–7131 CAS.
- P. Ghosh, S. Mahanty and R. N. Basu, Electrochim. Acta, 2009, 54, 1654–1661 CrossRef CAS.
- M. Park, X. Zhang, M. Chung, G. B. Less and A. M. Sastry, J. Power Sources, 2010, 195, 7904–7929 CrossRef CAS.
- Y. K. Sun, S. W. Cho, S. T. Myung, K. Amine and J. Prakash, Electrochim. Acta, 2007, 53, 1013–1019 CrossRef CAS.
- J. Liu and A. Manthiram, J. Phys. Chem. C, 2009, 113, 15073–15079 CAS.
- L. A. Riley, S. V. Atta, A. S. Cavanagh, Y. Yan, S. M. George, P. Liu, A. C. Dillon and S. H. Lee, J. Power Sources, 2011, 196, 3317–3324 CrossRef CAS.
- K. Xu, Chem. Rev., 2004, 104, 4303–4417 CrossRef CAS PubMed.
- S. S. Zhang, J. Power Sources, 2006, 162, 1379–1394 CrossRef CAS.
- J. H. Park, J. S. Kim, E. G. Shim, K. W. Park, Y. T. Hong, Y. S. Lee and S. Y. Lee, Electrochem. Commun., 2010, 12, 1099–1102 CrossRef CAS.
- P. Zhang, L. Zhang, X. Ren, Q. Yuan, J. Liu and Q. Zhang, Synth. Met., 2011, 161, 1092–1097 CrossRef CAS.
- J. T. Son and E. J. Cairns, J. Power Sources, 2007, 166, 343–347 CrossRef CAS.
|
This journal is © The Royal Society of Chemistry 2014 |
Click here to see how this site uses Cookies. View our privacy policy here.