DOI:
10.1039/C4RA01124D
(Paper)
RSC Adv., 2014,
4, 15797-15806
Synthesis of phosphoric acid supported on magnetic core–shell nanoparticles: a novel recyclable heterogeneous catalyst for Kabachnik–Fields reaction in water
Received
8th February 2014
, Accepted 12th March 2014
First published on 13th March 2014
Abstract
In this paper, supported phosphoric acid on silica coated magnetic nanoparticles (γ-Fe2O3@SiO2-PA) was synthesized as a new solid acid via the reaction of chloro-functionalized γ-Fe2O3@SiO2 with triethyl phosphite followed by hydrolysis. The synthesized γ-Fe2O3@SiO2-PA was characterized by SEM, HRTEM, BET, FT-IR, TGA, ICP and VSM. It was used as a magnetically recyclable heterogeneous catalyst for the efficient one-pot synthesis of α-aminophosphonates through Kabachnik–Fields reaction in water. Good to high yields of α-aminophosphonates showed that γ-Fe2O3@SiO2-PA had strong and sufficient acidic sites, which were responsible for its catalytic performance. More importantly, the catalyst was easily isolated from the reaction mixture by a magnetic bar and reused at least five times without significant degradation in the activity.
Introduction
In the last decades there has been increased interest in the study of α-aminophosphonates, structural analogues of α-amino acids, due to their wide agricultural and biological applications as fungicides, herbicides, plant growth regulators, enzyme inhibitors, antibiotics, peptide mimics, antitumor, antiviral and pharmacological agents.1 These vast applications have motivated the development of a number of methods for the synthesis of α-aminophosphonates. One of the most significant existing routes for the synthesis of α-aminophosphonates involves one-pot three-component reaction of aldehydes, amines and phosphites (Kabachnik–Fields reaction). Different catalysts were reported for this condensation reaction.2 Although, the reported methods are valuable, most of them suffer from one or more of the following drawbacks: high temperature, low yields of the products, long reaction times, tedious work-up procedures, requiring stoichiometric amounts of toxic and non-recyclable catalysts, using hazardous solvents, generating large amounts of waste and needing strictly anhydrous conditions. Therefore, it is preferable to introduce a green and efficient procedure that applies a reusable catalyst for the one-pot three-component synthesis of α-aminophosphonates.
Phosphoric acid is a well-known mineral acid which is used in fertilizers, pharmaceuticals and detergents. It is also applied as an active homogeneous catalyst in organic synthesis. Despite the desirable catalytic activity of phosphoric acid, its separation from homogeneous reaction mixtures requires neutralization or column chromatography. To facilitate catalyst removal and minimize the amount of waste formed, phosphoric acid was immobilized onto solid supports such as SiO2,3 Nb2O5,4 Al2O3,5 nano silica,6 MCM-41,7 SBA-15,8 zeolite9 and polysilsesquioxane.10 However, although the supported phosphoric acid was recycled by filtration or centrifugation techniques, these methods were time and energy consuming and caused loss of the supported catalyst during the separation process.
Magnetic nanoparticles (MNPs) are one of the most fascinating supports for the immobilization of homogenous catalysts.11 MNPs can be separated from the reaction mixture by an external magnet. Magnetic separation of MNPs is easy, economical, and saves time and energy. Moreover, MNPs such as iron oxide have a high surface area, excellent thermal and chemical stability, surface modification ability, ease of synthesis, and low toxicity and cost.12 Owing to these attractive features, catalysts supported on iron oxide have been designed and applied as magnetically recyclable heterogeneous catalysts.
On the line of our recent research on the development of new heterogeneous catalysts based on MNPs,13 in this work, we report the synthesis of phosphoric acid supported on magnetic core–shell nanoparticles (γ-Fe2O3@SiO2-PA) (Scheme 1).
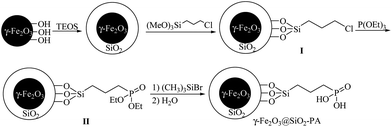 |
| Scheme 1 Synthesis of phosphoric acid immobilized on silica-coated γ-Fe2O3 MNPs (γ-Fe2O3@SiO2-PA). | |
It is worth to note that a recyclable catalyst requires a suitable reaction media for application in large scale in chemical industries. In recent years, organic reactions in water as a reaction media have attracted a great deal of interest in both academic and industrial research, because water is safe, nontoxic, environmentally friendly, readily available and cheap. In addition, reactions in aqueous media demonstrate unique selectivities and reactivities compared with those observed in organic media.14
To investigate the catalytic activity of γ-Fe2O3@SiO2-PA in organic reactions, we have studied one-pot three-component reactions of amines, trialkyl phosphites and aldehydes or ketones in water as an environmentally friendly reaction media in the presence of γ-Fe2O3@SiO2-PA (Scheme 2).
 |
| Scheme 2 Synthesis of α-aminophosphonates catalyzed by γ-Fe2O3@SiO2-PA in water. | |
Results and discussion
Synthesis and characterization of γ-Fe2O3@SiO2-PA
At first, a reported chemical co-precipitation technique was used for the synthesis of γ-Fe2O3 nanoparticles.15 Fig. 1 shows the XRD pattern of γ-Fe2O3 MNPs. The observed diffraction patterns have a good agreement with the cubic structure of maghemite (JCPDS file no. 04-0755), a unit cell dimension of 8.35 Å and the space group of P4132 (213). The average crystallite size was calculated to be 13.1 nm using Scherrer equation in which K = 0.9 and λ = 0.154 nm.
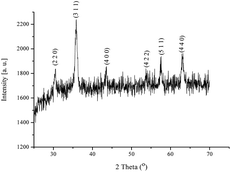 |
| Fig. 1 XRD pattern of γ-Fe2O3 MNPs. | |
Subsequently, γ-Fe2O3 MNPs suspension was sonicated in an alkaline solution of tetraethyl orthosilicate (TEOS) to obtain MNPs coated by silica. The shell of silica not only improves the dispersibility but also provides suitable sites (Si–OH groups) for further surface functionalization of MNPs. The resulting silica-coated γ-Fe2O3 MNPs (γ-Fe2O3@SiO2) was allowed to react with (3-chloropropyl)trimethoxysilane in toluene under reflux conditions to give chloro-functionalized γ-Fe2O3@SiO2 (I). Triethyl amine and triethyl phosphite were then added to I in toluene under reflux conditions to afford γ-Fe2O3@SiO2 functionalized with diethyl phosphonate (II). Finally, γ-Fe2O3@SiO2-PA was obtained by drop wise addition of bromotrimethyl silane to II in chloroform, followed by the reaction with water. The synthesized γ-Fe2O3@SiO2-PA was characterized by SEM, HRTEM, BET, FT-IR, TGA, ICP and VSM.
SEM image of γ-Fe2O3@SiO2-PA showed uniformity and spherical morphology of MNPs (Fig. 2).
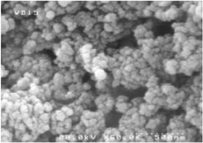 |
| Fig. 2 SEM image of γ-Fe2O3@SiO2-PA. | |
HRTEM images of γ-Fe2O3@SiO2-PA displayed a dark γ-Fe2O3 core surrounded by a grey silica shell with thickness of about 3–4 nm. The average size of the particles was 15 nm using HRTEM images (Fig. 3). This observation is in agreement with reducing surface area calculated by BET method for γ-Fe2O3@SiO2-PA (78 m2 g−1) compared with γ-Fe2O3 (91 m2 g−1). It is worth to note that reducing surface area is also a consequence of incorporation of organic spacer containing phosphoric acid groups onto the surface of nanoparticles.
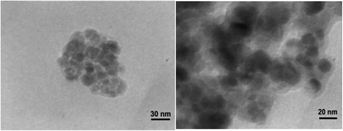 |
| Fig. 3 HRTEM images of γ-Fe2O3@SiO2-PA. | |
FT-IR spectra of γ-Fe2O3, γ-Fe2O3@SiO2 and γ-Fe2O3@SiO2-PA (Fig. 4) depicted broad bands at around 550–650 cm−1, which were attributed to Fe–O vibrations.16 In the spectra of γ-Fe2O3@SiO2 and γ-Fe2O3@SiO2-PA, a strong peak at around 1082 cm−1 were related to Si–O–Si antisymmetric stretching vibration. A band at 810 cm−1 was also evidence of the symmetric stretching vibration of Si–O–Si bond. In the spectrum of γ-Fe2O3@SiO2-PA, bands at 1160 and 810 cm−1 were ascribed to P–O stretching vibrations of phosphoric acid. Another band at 1220 cm−1 was related to stretching vibration of P
O bond. Meanwhile, the P–O–H stretching modes observed as broad peaks at about 2510 and 2660 cm−1.17 Moreover, the typical band at around 2910 cm−1 was belonged to C–H stretching vibrations of alkyl chains. These results indicate that phosphoric acid was successfully grafted onto γ-Fe2O3@SiO2 MNPs.
 |
| Fig. 4 FT-IR spectra of (a) γ-Fe2O3, (b) γ-Fe2O3@SiO2 and (c) γ-Fe2O3@SiO2-PA. | |
The thermal stability of γ-Fe2O3@SiO2-PA was investigated by thermogravimetric analysis (TGA) (Fig. 5). The TG curve of γ-Fe2O3@SiO2-PA showed the weight loss within 190 °C, which was related to the adsorbed water molecules on the support. The organic parts were decomposed completely in the temperature range of 193–490 °C. According to the TGA, the amount of phosphoric acid supported on γ-Fe2O3@SiO2 was evaluated to be 0.51 mmol g−1. These results were in agreement with those obtained by ICP. The ICP analysis showed that 0.49 mmol of phosphoric acid was anchored on 1.0 g of MNPs.
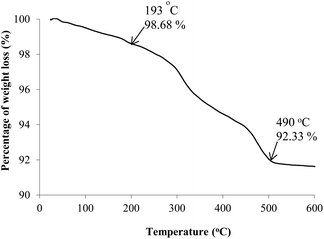 |
| Fig. 5 TGA of γ-Fe2O3@SiO2-PA. | |
Magnetic properties of γ-Fe2O3 and γ-Fe2O3@SiO2-PA were characterized by vibrating sample magnetometer (VSM) at room temperature (Fig. 6). γ-Fe2O3 and γ-Fe2O3@SiO2-PA displayed a superparamagnetic behaviour, as evidenced by a zero coercivity on the magnetization loop. The saturation magnetizations of γ-Fe2O3 and γ-Fe2O3@SiO2-PA were 68.9 and 62.9 emu g−1, respectively. A slight decrease of the saturation magnetization of γ-Fe2O3@SiO2-PA was due to the immobilization of phosphoric acid on the surface of γ-Fe2O3 MNPs.
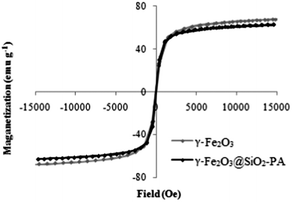 |
| Fig. 6 Magnetization curves of γ-Fe2O3 and γ-Fe2O3@SiO2-PA. | |
Synthesis of α-aminophosphonates catalyzed by γ-Fe2O3@SiO2-PA
In continuation of our ongoing research on the development of new methods for the synthesis of phosphonate derivatives,18 we have recently focused our attention towards the one-pot three-component synthesis of α-aminophosphonates.19 Along this line, we have investigated one-pot three-component synthesis of α-aminophosphonates in the presence of γ-Fe2O3@SiO2-PA as a magnetically recyclable heterogeneous catalyst.
At first, a model reaction of benzaldehyde, aniline and triethyl phosphite in aqueous media was chosen to optimize the reaction conditions such as temperature and molar ratio of the catalyst (Table 1, entries 1–5). It was found that the best yield of the product was obtained at 80 °C in the presence of 1 mol% of γ-Fe2O3@SiO2-PA (Table 1, entry 3). Virtually moderate catalytic activity was observed under solvent-free conditions or in commonly used organic solvents (Table 1, entries 6–10).
Table 1 One-pot reaction of benzaldehyde, aniline and triethyl phosphite under different conditionsa
Entry |
Catalyst (mol%) |
Solvent |
Tem. (°C) |
Time (h) |
Yieldb (%) |
Reaction conditions: benzaldehyde (1 mmol), aniline (1 mmol), triethyl phosphite (1 mmol). Isolated yield. Under reflux conditions. |
1 |
γ-Fe2O3@SiO2-PA (1) |
Water |
rt |
24 |
65 |
2 |
γ-Fe2O3@SiO2-PA (1) |
Water |
50 |
8 |
80 |
3 |
γ-Fe2O3@SiO2-PA (1) |
Water |
80 |
1 |
95 |
4 |
γ-Fe2O3@SiO2-PA (2) |
Water |
80 |
1 |
95 |
5 |
γ-Fe2O3@SiO2-PA (0.5) |
Water |
80 |
3 |
74 |
6 |
γ-Fe2O3@SiO2-PA (1) |
— |
80 |
3 |
86 |
7 |
γ-Fe2O3@SiO2-PA (1) |
EtOH |
80 |
1 |
91 |
8 |
γ-Fe2O3@SiO2-PA (1) |
CH3CN |
80 |
1 |
79 |
9 |
γ-Fe2O3@SiO2-PA (1) |
n-Hexanec |
80 |
3 |
55 |
10 |
γ-Fe2O3@SiO2-PA (1) |
Toluene |
80 |
3 |
54 |
11 |
— |
Water |
80 |
8 |
71 |
12 |
γ-Fe2O3 (0.02 g) |
Water |
80 |
8 |
70 |
13 |
γ-Fe2O3@SiO2 (0.02 g) |
Water |
80 |
4 |
68 |
14 |
H3PO4 (1) |
Water |
80 |
2.5 |
88 |
The examination of five solvents, such as ethanol, acetonitrile, n-hexane, toluene and water showed that protic solvent, in particularly, water promoted the yield of the product. The possibility of using water as a standard green reaction media is a remarkable advantage, especially due to the very low solubility of the organic compounds in water, providing easy separation of the products.
In order to show the role of the catalyst, reaction of benzaldehyde, aniline and triethyl phosphite in the absence of the catalyst and in the presence of γ-Fe2O3 and γ-Fe2O3@SiO2 were also examined in aqueous media at 80 °C. Under these conditions, the reactions led to the formation of the desired product in low yields after a long reaction time (Table 1, entries 11–13).
A similar reaction in the presence of phosphoric acid (H3PO4) gave the desired product in 88% yield after 2.5 h. Comparison of the results obtained in the presence of H3PO4 and γ-Fe2O3@SiO2-PA (entries 3 and 14), indicates that the catalytic activity of H3PO4 was increased by immobilization onto γ-Fe2O3. Unlike H3PO4, γ-Fe2O3@SiO2-PA and reactants were insoluble in water. This was presumed that the adsorption of reactants on the surface of the catalyst increased the local concentration of reactants around the active sites of the γ-Fe2O3@SiO2-PA and promoted the reaction effectively.
The generality and versatility of this method for the synthesis of different α-aminophosphonates were investigated by one-pot three-component reaction of various aniline, trialkylphosphites and aldehydes or ketones under optimized reaction conditions (1 mol% of γ-Fe2O3@SiO2-PA at 80 °C in water). The results of these studies are summarized in Table 2.
Table 2 Synthesis of α-aminophosphonates in the presence of γ-Fe2O3@SiO2-PAa
Entry |
Aldehyde/ketone |
Amines |
Phosphite |
Product |
Time (h) |
Yieldb (%) |
Reaction conditions: aldehyde or ketone (1 mmol), aniline (1 mmol), trialkyl phosphite (1 mmol), γ-Fe2O3@SiO2-PA (1 mol%), water (1 mL), 80 °C. Isolated yields. |
1 |
 |
 |
P(OEt)3 |
 |
1 |
95 |
2 |
 |
 |
HPO(OEt)2 |
 |
2.5 |
84 |
3 |
 |
 |
P(OMe)3 |
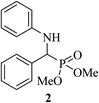 |
1 |
92 |
4 |
 |
 |
P(O–i-Pr)3 |
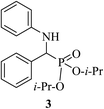 |
3 |
85 |
5 |
 |
 |
P(OEt)3 |
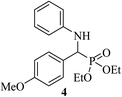 |
1 |
94 |
6 |
 |
 |
P(OEt)3 |
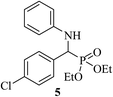 |
2 |
86 |
7 |
 |
 |
P(OEt)3 |
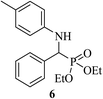 |
1 |
96 |
8 |
 |
 |
P(OEt)3 |
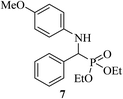 |
1 |
82 |
9 |
 |
 |
P(OEt)3 |
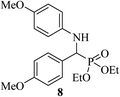 |
4 |
85 |
10 |
 |
 |
P(OEt)3 |
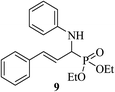 |
2 |
83 |
11 |
 |
 |
P(OEt)3 |
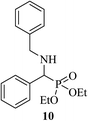 |
3.5 |
87 |
12 |
 |
 |
P(OEt)3 |
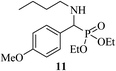 |
2 |
88 |
13 |
 |
 |
P(OEt)3 |
 |
3 |
91 |
14 |
 |
 |
P(OEt)3 |
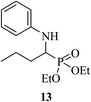 |
2 |
93 |
15 |
 |
 |
P(OEt)3 |
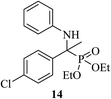 |
6 |
88 |
16 |
 |
 |
P(OEt)3 |
 |
2 |
85 |
As the results of Table 2 indicate, one-pot reaction of benzaldehyde and aniline with different phosphite esters such as triethyl/diethyl/trimethyl/tri-iso-propyl phosphites proceeded well and the desired products were produced in 84–95% yields (Table 2, entries 1–4). These results demonstrate that both the yields and the reaction time are relatively independent of the phosphorus compounds. Differently substituted benzaldehydes and anilines underwent successful reaction with triethyl phosphite and generated α-aminophosphonates 4–8 in good to high yields (Table 2, entries 5–9). This method was also applicable for the synthesis of α-aminophosphonate (9) from the reaction of cinnamaldehyde as an α,β-unsaturated aldehyde with aniline and triethyl phosphite (Table 2, entry 10). Interestingly, γ-Fe2O3@SiO2-PA promoted the efficient synthesis of α-aminophosphonates using aliphatic amines and aldehydes (Table 2, entries 11–14). γ-Fe2O3@SiO2-PA was also applied successfully for the synthesis of α-aminophosphonates from the reaction of aniline and triethyl phosphite with various ketones (Table 2, entries 15 and 16).
This protocol was also easily amenable to scale-up. For example, the reaction of benzaldehyde, aniline and triethyl phosphite in a semi scale-up procedure (10 times) in the presence of γ-Fe2O3@SiO2-PA was carried out successfully and the desired product was isolated in 94% yield.
In order to show the special catalytic behavior of γ-Fe2O3@SiO2-PA in the synthesis of α-aminophosphonates, the reaction of benzaldehyde, aniline and triethyl phosphite was performed in the presence of a catalytic amount of metal oxides (e.g. ZnO, SnO2, CdO, HgO, Sb2O3 and Al2O3) and BrØnsted acids (e.g. HClO4–SiO2, n-PS-γ-Fe2O3 and H3PW12O40) (Table 3). As is evident from Table 3, γ-Fe2O3@SiO2-PA was the most effective catalyst for this purpose leading to the formation of α-aminophosphonate 1 in high yield in a short reaction time.
Table 3 Comparison of the catalytic activity of γ-Fe2O3@SiO2-PA with various catalysts for the synthesis of α-aminophosphonate 1a
Entry |
Catalyst |
Time (h) |
Yieldb (%) |
Reaction conditions: benzaldehyde (1 mmol), aniline (1 mmol), triethyl phosphite (1 mmol), catalyst (1 mol%), water, 80 °C. Isolated yield. n-Propylsulfonated γ-Fe2O3.13a–c |
1 |
γ-Fe2O3@SiO2-PA |
1 |
95 |
2 |
ZnO |
4 |
41 |
3 |
SnO2 |
3 |
49 |
4 |
CdO |
4 |
44 |
5 |
HgO |
2 |
65 |
6 |
Sb2O3 |
5 |
69 |
7 |
Al2O3 |
4 |
64 |
9 |
HClO4–SiO2 |
3 |
94 |
10 |
n-PS-γ-Fe2O3c |
6 |
81 |
11 |
H3PMo12O40 |
3.5 |
69 |
Catalyst recyclability is highly preferable for a catalytic process. In this regard the recyclability of γ-Fe2O3@SiO2-PA was investigated in a model reaction of benzaldehyde, aniline and triethyl phosphite under optimized reaction conditions. After the reaction was completed, the whole amount of the catalyst simply separated by a magnetic bar (Fig. 7). The recovered catalyst was washed with EtOH, dried at room temperature and reused for a similar reaction. It is worth to note that the magnetic property of γ-Fe2O3@SiO2-PA facilitates its efficient recovery from the reaction mixture during work-up procedure. Comparison of HRTEM image (Fig. 8) and FT-IR spectrum (Fig. 9) of used catalyst with those of the fresh catalyst (Fig. 3 and 4) showed that the morphology and structure of γ-Fe2O3@SiO2-PA remained intact after five recoveries. Furthermore, the loading amount of the catalyst after five times reuse was determined by TGA, and found that 0.49 mmol of phosphoric acid was grafted onto 1 g of MNPs (based on ICP analysis 0.48 mmol of phosphoric acid was grafted onto 1 g of MNPs). In each run, the desired pure product (1) was obtained after centrifugation (Fig. 7) and decantation of the remaining solution following by flash chromatography. The average isolated yield of the product for five consecutive runs was 89.2%, which clearly demonstrates the practical recyclability of the catalyst (Fig. 10).
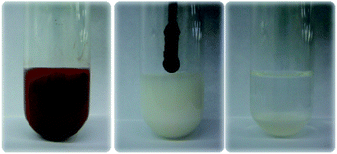 |
| Fig. 7 Catalyst separation from the reaction mixture using a magnetic bar. | |
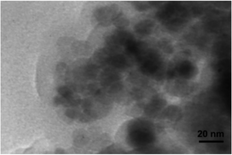 |
| Fig. 8 HRTEM image of γ-Fe2O3@SiO2-PA after five reuses. | |
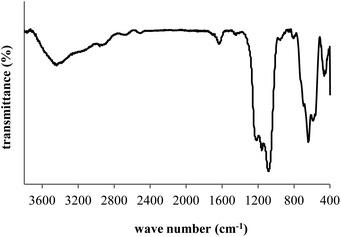 |
| Fig. 9 FT-IR spectrum of γ-Fe2O3@SiO2-PA after five reuses. | |
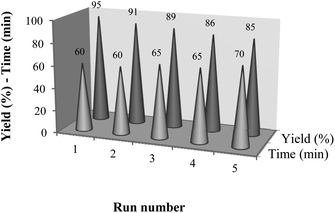 |
| Fig. 10 Reusability of γ-Fe2O3@SiO2-PA for the synthesis of α-aminophosphonate 1. | |
In order to know whether the reaction takes place at the surface of γ-Fe2O3@SiO2-PA as a truly heterogeneous catalyst or any phosphoric acid-leached species as a homogeneous catalyst, ICP analysis of the remaining mixture after catalyst and product separation was investigated upon reaction completion. ICP results proved that any amount of leached phosphoric acid was not detected. These observations indicated that the catalyst was stable and could tolerate the present reaction conditions.
Conclusions
In conclusion, a novel supported phosphoric acid on silica coated magnetic nanoparticles (γ-Fe2O3@SiO2-PA) was synthesized and characterized by different techniques. This solid acid was applied as a magnetically recyclable heterogeneous catalyst for the efficient synthesis of α-aminophosphonates in water. By this method, various α-aminophosphonates were obtained in good to high yields via one-pot three-component reaction of amines (aromatic and aliphatic), aldehydes or ketones (aromatic and aliphatic) and phosphites. The present protocol offers several advantages such as generality and simplicity, using a reusable and stable catalyst, an environmentally benign reaction media avoiding hazardous organic solvents and toxic catalysts, and being amenable to scale-up. Importantly, the catalyst was easily separated by a magnetic bar and reused five times without significant loss of its catalytic activity.
Experimental section
General
Chemicals were purchased from Merck Chemical Company. NMR spectra were recorded on a Bruker Avance DPX-250 using deutrated CDCl3 as solvent and TMS as internal standard. The purity of the products and the progress of the reactions were accomplished by TLC on silica-gel polygram SILG/UV254 plates. High-resolution transmission electron microscopy analyses were performed using HRTEM microscope (Philips CM30). FT-IR spectra were recorded on a Shimadzu Fourier Transform Infrared Spectrophotometer (FT-IR-8300). The morphology of the products was determined by using Hitachi Japan, model s4160 Scanning Electron Microscopy (SEM) at accelerating voltage of 15 kV. Power X-ray diffraction (XRD) was performed on a Bruker D8-advance X-ray diffractometer with Cu Kα (λ = 0.154 nm) radiation. Thermogravimetric analysis (TGA) was performed using a Shimadzu thermogravimetric analyzer (TG-50). Elemental analysis was carried out on a Costech 4010 CHN elemental analyzer. The content of phosphorous in the catalyst was determined by OPTIMA 7300DV inductively coupled plasma (ICP) analyzer. Room temperature magnetization isotherms were obtained using a vibrating sample magnetometer (VSM, LakeShore 7400). The BET surface area measurements were performed on a BEL-MAX (Japan) instrument at liquid nitrogen temperature.
Synthesis of γ-Fe2O3@SiO2
γ-Fe2O3 MNPs were synthesized by a reported chemical co-precipitation technique of ferric and ferrous ions in alkali solution with minor modifications.15 FeCl2·4H2O (3.98 g) and FeCl3·6H2O (6.50 g) were dissolved in deionized water (60 mL) under Ar atmosphere at room temperature. A NH4OH solution (0.6 M, 400 mL) was then added drop wise (drop rate = 1 mL min−1) to the stirring mixture at room temperature to reach the reaction pH to 11. The resulting black dispersion was continuously stirred for 1 h at room temperature and then heated to reflux for 1 h to yield a brown dispersion. The magnetic nanoparticles were then purified by a repeated centrifugation (1730–3461 × g, 20 min), decantation and redispersion (3 times). The as-synthesized sample was heated in air at 2 °C min−1 up to 200 °C and then kept in the furnace for 3 h to give a reddish-brown powder. Concentrated solution of ammonia (3.5 mL) was then added to the dispersed γ-Fe2O3 nanoparticles (3.5 g) in deionized water (40 mL)–ethanol (160 mL) and the resulting mixture was stirred at 40 °C for 30 min. Subsequently, tetraethyl orthosilicate (TEOS, 2.0 mL) was charged to the reaction vessel and the mixture was continuously stirred at 40 °C for 24 h. The silica-coated nanoparticles (γ-Fe2O3@SiO2) were collected by a permanent magnet followed by washing three times with EtOH and diethyl ether and dried at 100 °C in vacuum for 24 h.
Synthesis of chloro-functionalized γ-Fe2O3@SiO2 (I)
A mixture of γ-Fe2O3@SiO2 (2 g) in dry toluene (40 mL) was sonicated for 30 min. 3-Chloropropyl trimethoxysilane (1 mL) was added to the dispersed γ-Fe2O3@SiO2 in toluene and slowly heated to 105 °C. The reaction mixture was stirred at this temperature for 24 h. Compound I was separated by an external magnet and washed three times with diethyl ether and CH2Cl2, and dried under vacuum.
Synthesis of γ-Fe2O3@SiO2 functionalized with diethylphosphonate (II)
A mixture of I (ref. 20) (1.7 g) in dry toluene (15 mL) was sonicated for 30 min. Then triethyl amine (0.1 mL) and triethyl phosphite (0.2 mL) were added to the dispersed I in toluene and heated to 105 °C. The reaction mixture was stirred at this temperature for 24 h. Compound II was separated by an external magnet and washed three times with EtOH, CH2Cl2 and diethyl ether, and dried under vacuum.
Synthesis of γ-Fe2O3@SiO2-PA
Bromotrimethyl silane (0.5 mL) was added drop wise to II (1.7 g) in chloroform under a nitrogen atmosphere at room temperature. After the addition was completed (30 min), the mixture was stirred for 30 h. The resulting solid material was separated by an external magnet, washed with chloroform, and dried at room temperature in vacuum to afford γ-Fe2O3@SiO2 functionalized with bis(trimethylsilyl)phosphonate. Water (50 mL) was added to the resulting solid (1.7 g) and the mixture was stirred at room temperature for 24 h. The obtained particles was separated by an external magnet and washed three times with water and dried under vacuum to afford γ-Fe2O3@SiO2-PA (1.7 g).
Synthesis of α-aminophosphonates in the presence of γ-Fe2O3@SiO2-PA
γ-Fe2O3@SiO2-PA (1 mol%, 0.02 g) was added to a stirred mixture of aldehyde (1 mmol), amine (1 mmol) and trialkyl phosphite (1 mmol) in water (1 mL). The reaction mixture was stirred at 80 °C for the appropriate time (Table 2). The catalyst was separated by a magnetic bar from cooled mixture, washed with EtOH, dried at room temperature and re-used for a consecutive run under the same reaction conditions. The solid was isolated after centrifugation and decantation of the remaining solution and purified by flash chromatography on silica gel eluted with n-hexane–EtOAc (1
:
1) to obtain the pure products (except for α-aminophosphonates 10 and 11).21
Diethyl phenyl(phenylamino)methylphosphonate (1). 1H NMR (CDCl3, TMS): 1.11 (t, 3H, 2JH,H = 7.1 Hz, OCH2CH3), 1.28 (t, 3H, 2JH,H = 7.1 Hz, OCH2CH3), 3.59–3.69 (m, 1H, OCH2CH3), 3.88–3.95 (m, 1H, OCH2CH3), 4.07–4.16 (m, 2H, OCH2CH3), 4.75 (d, 1H, 2JP,H = 26.4 Hz, CH), 4.79 (bs, 1H, NH), 6.59 (d, 2H, 2JH,H = 7.9 Hz, Ar), 6.68 (t, 1H, 2JH,H = 7.3 Hz, Ar), 7.10 (t, 2H, 2JH,H = 8.0 Hz, Ar), 7.25–7.35 (m, 3H, Ar), 7.47 (d, 2H, 2JH,H = 7.4 Hz, Ar) ppm; 13C NMR (CDCl3, TMS): 16.6 (d, 3JC,P = 5.8 Hz, OCH2CH3), 16.8 (d, 3JC,P = 5.8 Hz, OCH2CH3), 56.4 (d, 1JC,P = 150.4 Hz, CH), 63.7 (d, 2JC,P = 7.0 Hz, OCH2CH3), 114.2, 118.8, 128.2, 129.6, 136.3, 146.6, 146.8 (C6H5) ppm; IR: 3305 (NH) cm−1; MS (70 eV), m/z: 319 (M+), 182 [M-P(O)(OEt)2].
Dimethyl phenyl(phenylamino)methylphosphonate (2). 1H NMR (CDCl3, TMS): 3.40 (d, 3H, 2JP,H = 10.0 Hz, OCH3), 3.69 (d, 3H, 2JP,H = 10.0 Hz, OCH3), 4.66–4.79 (m, 2H, CH, NH), 6.51–6.63 (m, 3H, Ar), 7.00–7.07 (m, 2H, Ar), 7.19–7.31 (m, 3H, Ar), 7.39–7.42 (m, 2H, Ar) ppm; 13C NMR (CDCl3, TMS): 52.7 (d, 2JC,P = 7.1 Hz, OCH3), 54.6 (d, 1JC,P = 151.5 Hz, CH), 112.8, 117.5, 126.7, 126.8, 127.0, 127.7, 128.1, 134.5 (Ar) ppm; IR: 3296 (NH) cm−1; MS (70 eV), m/z: 291 (M+), 182 [M-P(O)(OMe)2].
Di-iso-propyl phenyl(phenylamino)methylphosphonate (3). 1H NMR (CDCl3, TMS): d 0.83–1.09 [m, 3H, OCH(CH3)2], 1.16–1.26 [m, 9H, OCH(CH3)2], 4.36–4.40 [m, 2H, OCH(CH3)2], 4.55–4.67 (m, 2H, CH, NH), 6.50–6.63 (m, 5H, Ar), 7.02 (t, 2H, 2JH,H = 7.5 Hz, Ar), 7.19–7.27 (m, 1H, Ar), 7.39 (d, 2H, 2JH,H = 7.4 Hz, Ar) ppm; 13C NMR (CDCl3, TMS): 23.2 [d, 2JC,P = 5.8 Hz, OCH(CH3)2], 23.7 [d, 2JC,P = 5.8 Hz, OCH(CH3)2], 56.4 (d, 1JC,P = 151.8 Hz, CH), 71.8 [d, 2JC,P = 7.6 Hz, OCH(CH3)2], 72.4 [d, 2JC,P = 7.6 Hz, OCH(CH3)2], 113.7, 118.2, 127.7, 127.9, 128.0, 128.4, 129.1, 136.2, 146.4, 146.6 (Ar) ppm; IR: 3308 (NH) cm−1; MS (70 eV), m/z: 347 (M+), 182 [M-P(O)(O-i-pr)2].
Diethyl (4-methoxyphenyl)(phenylamino)methylphosphonate (4). 1H NMR (CDCl3, TMS): 1.02–1.08 (m, 3H, OCH2CH3), 1.18–1.22 (m, 3H, OCH2CH3), 3.70 (s, 3H, OCH3), 3.63–4.06 (m, 4H, OCH2CH3), 4.58–4.67 (m, 2H, CH, NH), 6.50–6.63 (m, 3H, C6H4, C6H5), 6.77–6.81 (m, 2H, C6H4, C6H5), 7.00–7.03 (m, 2H, C6H4, C6H5), 7.29–7.31 (m, 2H, C6H4, C6H5) ppm; 13C NMR (CDCl3, TMS): 16.7 (d, 3JC,P = 5.8 Hz, OCH2CH3), 16.8 (d, 3JC,P = 5.8 Hz, OCH2CH3), 55.7 (d, 1JC,P = 152.1 Hz, CH), 55.6 (OCH3), 63.5 (OCH2CH3), 114.3, 114.4, 116.2, 118.7, 129.3, 129.5, 146.4, 146.6 (Ar) ppm; IR: 3303 (NH) cm−1; MS (70 eV), m/z: 349 (M+), 212 [M-P(O)(OEt)2]. Anal. calc. for C18H24NO4P: C, 61.88; H, 6.92. Found: C, 61.85; H, 6.90%.
Diethyl (4-chlorophenyl)(phenylamino)methylphosphonate (5). 1H NMR (CDCl3, TMS): 1.09 (t, 3H, 2JH,H = 7.1 Hz, OCH2CH3), 1.21 (t, 3H, 2JH,H = 7.1 Hz, OCH2CH3), 3.69–4.09 (m, 4H, OCH2CH3), 4.60–4.70 (m, 2H, CH, NH), 6.48 (d, 2H, 2JH,H = 7.8 Hz, Ar), 6.63 (t, 1H, 2JH,H = 7.3 Hz, Ar), 7.03 (t, 2H, 2JH,H = 7.8 Hz, Ar), 7.23 (d, 2H, 2JH,H = 8.4 Hz, Ar), 7.32–7.36 (m, 2H, Ar) ppm; 13C NMR (CDCl3, TMS): 16.6 (d, 3JC,P = 5.8 Hz, OCH2CH3), 16.8 (d, 3JC,P = 5.8 Hz, OCH2CH3), 55.9 (d, 1JC,P = 150.5 Hz, CH), 63.7, 63.9 (OCH2CH3), 114.2, 119.1, 129.2, 129.6, 134.1, 135.0, 146.3, 146.5 (Ar) ppm; IR: 3299 (NH) cm−1; MS (70 eV), m/z: 353 (M+), 355 (M2+), 216 [M-P(O)(OEt)2]. Anal. calc for C17H21ClNO3P: C, 57.71; H, 5.98. Found: C, 57.69; H, 5.95%.
Diethyl 3-phenyl-1-(phenylamino)allylphosphonate (9). 1H NMR (CDCl3, TMS): 1.26–1.33 (m, 6H, OCH2CH3), 4.10–4.23 (m, 5H, OCH2CH3, NH), 4.47 (dd, 1H, 2JH,H = 6.0 Hz, 2JP,H = 27.5 Hz, CH), 6.24–6.30 (m, 1H, CH
CH), 6.68–6.77 (m, 4H, Ar, CH
CH), 7.14–7.37 (m, 7H, Ar) ppm; 13C NMR (CDCl3, TMS): 22.9, 23.1 (OCH2CH3), 60.5 (d, 1JC,P = 153.3 Hz, CH), 69.5 (d, 2JC,P = 7.0 Hz, OCH2CH3), 70.0 (d, 2JC,P = 7.0 Hz, OCH2CH3), 120.3, 124.9, 125.6, 125.8, 128.1, 128.7, 134.0, 139.6 (Ar) ppm; IR: 3297 (NH) cm−1; MS (70 eV), m/z: 345 (M+), 208 [M-P(O)(OEt)2]. Anal. calc for C19H24NO3 P: C, 66.07; H, 7.00. Found: C, 66.00; H, 6.68%.
Diethyl (benzylamino)(phenyl)methylphosphonate (10). 1H NMR (CDCl3, TMS): 1.05 (t, 2JH,H = 7.0 Hz, 3H, OCH2CH3), 1.17–1.32 (m, 3H, OCH2CH3), 2.95 (brs, 1H, NH), 3.44–4.07 (m, 7H, OCH2CH3, CH2C6H5, CH), 7.19–7.34 (m, 10H, Ar) ppm; 13C NMR (CDCl3, TMS): 16.6 (d, 3JC,P = 5.8 Hz, OCH2CH3), 16.8 (d, 3JC,P = 6.1 Hz, OCH2CH3), 51.6 (d, 3JC,P = 17.5 Hz, CH2), 59.9 (d, 1JC,P = 153.4 Hz, CH), 63.1 (d, 2JC,P = 6.8 Hz, OCH2CH3), 63.3 (d, 2JC,P = 7.2 Hz, OCH2CH3), 127.5, 127.6, 128.1, 128.4, 129.0, 129.1, 136.0, 139.7 (Ar). IR: 3309 (NH) cm−1. MS (70 eV), m/z: 333 (M+), 196 [M-P(O)(OEt)2].
Diethyl 1-(phenylamino)butylphosphonate (13). 1H NMR (CDCl3, TMS): 0.84 (t, 3H, 2JH,H = 7.2 Hz, CH3), 1.09–1.24 [m, 6H, OCH2CH3], 1.50–1.82 [m, 4H, (CH2)2CH3], 3.60–3.65 (m, 2H, NH, CH), 3.94–4.09 (m, 4H, OCH2CH3), 6.58 (d, 2H, 2JH,H = 8.2 Hz, Ar), 6.65 (d, 1H, 2JH,H = 7.4 Hz, Ar), 7.09 (t, 2H, 2JH,H = 7.6 Hz, Ar) ppm; MS (70 eV), m/z: 285 (M+), 148 [M-P(O)(OEt)2].
Acknowledgements
We are thankful to University of Birjand Research Council for their support on this work.
Notes and references
- M. C. Allen, W. Fuhrer, B. Tuck, R. Wade and J. M. Wood, J. Med. Chem., 1989, 32, 1652–1661 CrossRef CAS PubMed
; P. P. Giannousis and P. A. Bartlett, J. Med. Chem., 1987, 30, 1603–1609 CrossRef PubMed
; X. Rao, Z. Song and L. He, Heteroat. Chem., 2008, 19, 512–516 CrossRef
; I. Kraicheva, A. Bogomilova, I. Tsacheva, G. Momekov and K. Troev, Eur. J. Med. Chem., 2009, 44, 3363–3367 CrossRef PubMed
; R. Hirschmann, A. B. Smith, C. M. Taylor, P. A. Benkovic, S. D. Taylor, K. M. Yager, P. A. Sprengeler and S. J. Benkovic, Science, 1994, 265, 234–237 Search PubMed
. - E. K. Fields, J. Am. Chem. Soc., 1952, 74, 1528–1531 CrossRef CAS
; W. Jie, S. Wei, W. W. Zi and X. H. Guang, Chin. J. Chem., 2006, 24, 1054–1057 CrossRef
; A. S. Paraskar and A. Sudalai, ARKIVOC, 2006, x, 183–189 Search PubMed
; M. T. Maghsoodlou, S. M. Habibi-Khorassani, R. Heydari, N. Hazeri, S. S. Sajadikhah and M. Rostamizadeh, Chin. J. Chem., 2010, 28, 285–288 CrossRef
; K. Ando and T. Egami, Heteroat. Chem., 2011, 22, 358–362 CrossRef
; J. T. Hou, J. W. Gao and Z. H. Zhang, Appl. Organomet. Chem., 2011, 25, 47–53 CrossRef
; Z. Karimi-Jaberi and M. Amiri, Heteroat. Chem., 2010, 21, 96–98 CrossRef
; Z. Karimi-Jaberi, M. Amiri and N. Sadeghi, Synth. Commun., 2010, 40, 2948–2953 CrossRef
; A. A. Jafari, S. Amini and F. Tamaddon, J. Iran. Chem. Soc., 2013, 10, 677–684 CrossRef
; S. D. Mitragotri, D. M. Pore, U. V. Desai and P. P. Wadgaonkar, Catal. Commun., 2008, 9, 1822–1826 CrossRef
; B. Kaboudin and M. Sorbiun, Tetrahedron Lett., 2008, 48, 9015–9017 CrossRef
; B. C. Ranu, A. Hajra and U. Jana, Org. Lett., 1999, 1, 1141–1143 CrossRef
; A. K. Bhattacharya and T. Kaur, Synlett, 2007, 5, 745–748 CrossRef
; S. Chandrasekhar, S. Jaya Prakash, V. Jagadeshwar and C. Narsihmulu, Tetrahedron Lett., 2001, 42, 5561–5563 CrossRef
; A. Vino, P. Kalita, V. V. Balasubramanian, H. Oveisi, T. Selvan, A. Mano, M. A. Chari and B. V. Subbareddy, Tetrahedron Lett., 2009, 50, 7132–7136 CrossRef
; Z. Rezaei, H. Firouzabadi, N. Iranpoor, A. Ghaderi, M. R. Jafari, A. A. Jafari and H. R. Zare, Eur. J. Med. Chem., 2009, 44, 4266–4277 CrossRef PubMed
; K. S. Ambica, S. C. Taneja, M. S. Hundal and K. K. Kapoor, Tetrahedron Lett., 2008, 49, 2208–2212 CrossRef
; S. D. Dindulkar, M. V. Reddy and Y. T. Jeong, Catal. Commun., 2012, 17, 114–117 CrossRef
; S. Bhagat and A. K. Chakraborti, J. Org. Chem., 2007, 72, 1263–1270 CrossRef PubMed
; S. M. Vahdat, R. Baharfar, M. Tajbakhsh, A. Heydari, S. M. Baghbanian and S. Khaksar, Tetrahedron Lett., 2008, 49, 6501–6504 CrossRef
; H. Sharghi, S. Ebrahimpour Moghaddam and M. M. Doroodmand, Tetrahedron, 2013, 69, 4708–4724 CrossRef
. - M. A. Zolfigol, F. Shirini, K. Zamani, E. Ghofrani and S. Ebrahimi, Phosphorus, Sulfur Silicon Relat. Elem., 2004, 179, 2177–2182 CrossRef CAS
. - Z. C. Tang, D. H. Yu, P. Sun, H. Li and H. Huang, Bull. Korean Chem. Soc., 2010, 31, 3679–3683 CrossRef CAS
. - L. R. R. Araujo, C. F. Scofield, N. M. R. Pastura and W. A. Gonzalez, Mater. Res., 2006, 9, 181–184 CrossRef
; H. R. Shaterian, N. Fahimi and K. Azizi, Res. Chem. Intermed. DOI:10.1007/s11164-013-1047-x
. - A. Bamoniri, B. F. Mirjalili and S. Nazemian, Journal of Nanostructures, 2012, 2, 101–105 Search PubMed
. - R. Wang and Y. Li, Catal. Commun., 2010, 11, 705–709 CrossRef CAS
. - B. Wu, Z. Tong and X. Yuan, J. Porous Mater., 2012, 19, 641–647 CrossRef CAS
; R. J. P. Corriu, L. Datas, Y. Guari, A. Mehdi, C. Reyé and C. Thieuleux, Chem. Commun., 2001, 763–764 RSC
. - K. V. Thiruvengadaravi, J. Nandagopal, P. Baskaralingam, V. S. S. Bala, P. Vijayalakshmi, S. D. Kirupha and S. Sivanesan, Energy Sources, 2012, 34, 2234–2241 CrossRef CAS
. - M. Sebah, S. P. Maddala, P. Haycock, A. Sullivan, H. Toms and J. Wilson, J. Mol. Catal. A: Chem., 2013, 374–375, 59–65 CrossRef CAS
. - N. T. S. Phan and C. W. Jones, J. Mol. Catal. A: Chem., 2006, 253, 123–131 CrossRef CAS
; E. Karaoglu, A. Baykal, M. Senel, H. Sozeri and M. S. Toprak, Mater. Res. Bull., 2012, 47, 2480–2486 CrossRef
; P. Rattanaburi, B. Khumraksa and M. Pattarawarapan, Tetrahedron Lett., 2012, 53, 2689–2693 CrossRef
. - N. Koukabi, E. Kolvari, M. A. Zolfigol, A. Khazaei, B. Shirmardi Shaghasemi and B. Fasahati, Adv. Synth. Catal., 2012, 354, 2001–2008 CrossRef CAS
; E. Rafiee and S. Eavani, Green Chem., 2011, 13, 2116–2122 RSC
; A. Dyal, K. Loos, M. Noto, S. W. Chang, C. Spagnoli, K. V. P. M. Shafi, A. Ulman, M. Cowman and R. A. Gross, J. Am. Chem. Soc., 2003, 125, 1684–1685 CrossRef PubMed
; Y. H. Liu, J. Deng, J. W. Gao and Z. H. Zhang, Adv. Synth. Catal., 2012, 354, 441–447 CrossRef
. -
(a) S. Sobhani, Z. Pakdin Parizi and N. Razavi, Appl. Catal., A, 2011, 409–410, 162–166 CrossRef CAS
;
(b) S. Sobhani, Z. Pakdin Parizi and R. Nasseri, J. Chem. Sci., 2013, 125, 975–979 CrossRef CAS
;
(c) S. Sobhani and R. Jahanshahi, New J. Chem., 2013, 37, 1009–1015 RSC
;
(d) S. Sobhani, M. Bazrafshan, A. Arabshahi Delluei and Z. Pakdin Parizi, Appl. Catal., A, 2013, 454, 145–151 CrossRef CAS
;
(e) S. Sobhani and M. Honarmand, Appl. Catal., A, 2013, 467, 456–462 CrossRef CAS
;
(f) S. Sobhani and Z. Pakdin Parizi, RSC Adv., 2014, 4, 13071–13077 RSC
. - S. Kobayashi, Y. Mori, S. Nogayama and K. Manabe, Green Chem., 1999, 1, 175–177 RSC
. - R. Massart, E. Dubois, V. Cabuil and E. Hasmonay, J. Magn. Magn. Mater., 1995, 149, 1–5 CrossRef CAS
; B. Z. Tang, Y. Geng, J. W. Y. Lam, B. Li, X. Jing, X. Wang, F. Wang, A. B. Pakhomov and X. X. Zhang, Chem. Mater., 1999, 11, 1581–1589 CrossRef
; K. M. Ho and P. Li, Langmuir, 2008, 24, 1801–1807 CrossRef PubMed
. - Z. Zhang, F. Zhang, Q. Zhou, W. Zhao, B. Ma and Y. Ding, J. Colloid Interface Sci., 2011, 360, 189–194 CrossRef CAS PubMed
. - M. Masteri Farahani and N. Tayyebi, J. Mol. Catal. A: Chem., 2011, 348, 83–87 CrossRef CAS
; R. M. Silverstein, G. C. Bassler and T. C. Morrill, Spectrometric Identification of Organic Compounds, Wiley, New York, 5th edn, 1963, p. 162 Search PubMed
. - S. Sobhani and Z. Pakdin Parizi, Tetrahedron, 2011, 67, 3540–3545 CrossRef CAS
; S. Sobhani and M. Faal Maleki, Synlett, 2010, 383–386 CrossRef
; S. Sobhani and M. Honarmand, Synlett, 2013, 383–386 Search PubMed
; S. Sobhani and Z. Tashrifi, Tetrahedron, 2010, 66, 1429–1439 CrossRef
. - S. Sobhani, E. Safaei, M. Asadi, F. Jalili and Z. Tashrifi, J. Porphyrins Phthalocyanines, 2008, 12, 849–856 CrossRef CAS
; S. Sobhani, E. Safaei, M. Asadi and F. Jalili, J. Organomet. Chem., 2008, 693, 3313–3317 CrossRef
; S. Sobhani and Z. Tashrifi, Synth. Commun., 2009, 39, 120–131 CrossRef
; S. Sobhani and Z. Tashrifi, Heteroat. Chem., 2009, 20, 109–115 CrossRef
; S. Sobhani and A. Vafaee, J. Iran. Chem. Soc., 2010, 7, 227–236 CrossRef
. - The loading amount of Cl atom was 0.6 mmol per gram I based on elemental analysis and TGA.
- After catalyst separation, the crude products were isolated from aqueous phase by extraction with EtOAc (3 × 10 mL). The separated organic layer was dried over Na2SO4 and filtered. Evaporation of the filtrate produced almost pure product which was purified by flash chromatography on silica gel eluted with n-hexane–EtOAc (1
:
1).
|
This journal is © The Royal Society of Chemistry 2014 |
Click here to see how this site uses Cookies. View our privacy policy here.