DOI:
10.1039/C3RA46441E
(Paper)
RSC Adv., 2014,
4, 8966-8972
Polyaniline-decorated cellulose aerogel nanocomposite with strong interfacial adhesion and enhanced photocatalytic activity†
Received
6th November 2013
, Accepted 20th January 2014
First published on 21st January 2014
Abstract
Cellulose aerogel has attracted considerable attention due to its high surface area and the added advantages of being cost-effective and environmentally benign. It has been applied as supporting material for noble metal nanoparticle catalysts to prevent their agglomeration. In this paper, we have demonstrated a facile method to prepare polyaniline (PANI)-decorated cellulose aerogel via a dissolve/regeneration route using ionic liquid as solvent. Cellulose aerogel acted as a supporting material for PANI nanoparticles to prevent their agglomeration as confirmed by scanning electron microscopy. The strong interfacial interaction between PANI and cellulose aerogel was verified by Fourier transform infrared spectroscopy, differential scanning calorimetry, thermal gravimetric analysis and X-ray diffraction. PANI-cellulose aerogel exhibited excellent photocatalytic activity towards the degradation of methylene blue. The degradation efficiency reached 95% after 2 h. The approach promotes the use of renewable natural resources to prepare a variety of nanofibrillated cellulose-supported nanocomposites for catalysis, sensors, and other potential applications.
1. Introduction
Waste synthetic organic dyes produced from textile, food, pharmaceutical and photographic industries greatly harm the environment and ecosystem due to their high toxicity to aquatic creatures.1 Furthermore, most dyes contain aromatic rings, which make them easy to transport to the environment and may cause serious problems to our health.2 The efficient and cost-effective removal method for organic dyes has attracted the interest of extensive researchers. Methylene blue (MB), which is a heterocyclic aromatic chemical compound having IUPAC name 3,7-bis(dimethylamino)-phenothiazin-5-ium chloride with the molecular formula C16H18N3SCl, has been extensively used in various fields such as biology and chemistry. It has caused severe harm to the aesthetic nature of the environment and the health of aquatic life.
Typically, adsorption is the most widely used method in removing waste organic dyes.3,4 However, the long desorption period limited its application in large scale. Furthermore, it is difficult to dispose the adsorbed organic dyes without leading to secondary pollution. Heterogeneous photocatalysis which accelerates the photoreaction in the presence of photocatalyst is a feasible technology for the removal of organic dyes from water.5 It uses light irradiation as activation energy to in situ generate reactive radicals6 which allow the destruction of organic dyes.7 To date, various nanocomposites have been prepared as valid photocatalysts for the degradation of organic dyes.8,9 Among them, most studies focused on using metal oxide nanoparticles such as ZnO10 and TiO211 as catalysts. However, the application of metal oxide nanoparticles requires loading them on supporting materials, which is difficult due to the low surface activity of inorganic nanoparticles. The resulted complicated surface polymerization and modification limited its application in large scale.
Polyaniline (PANI) has been extensively studied as a conducting polymer due to its promising electronic and photoelectronic properties, high environmental stability and relatively simple preparation procedure.12–14 It has found wide applications in electro-chromic devices, sensor, light-emitting diodes, capacitors and electrostatic discharge protection.15,16 Furthermore, PANI has appeared as a novel photocatalytic material to dispose waste organic dyes during recent years.17,18 Due to the emphasis of sustainable materials, natural polymer has been widely applied in the preparation of composites.19,20 As the most abundant natural polymer in the world, cellulose, which originates from various natural sources such as high plants, cotton, algae and bacteria,21 has appeared as a sustainable and renewable natural polymer with promising properties. Our previous studies have demonstrated that nanofibrillated cellulose is a suitable supporting material for nanosized catalysts.22–24 As a new derivative of cellulose, cellulose aerogel has various advantages such as ultra-light, high surface area and bio-degradability,25,26 which makes it a new promising supporting material for catalysts.27 In this work, we present the study of the preparation and photocatalytic properties of PANI-decorated cellulose aerogel. A “green” ionic liquid, 1-butyl-3-methylimidazolium chloride ([Bmim]Cl), was used to dissolve cellulose. PANI-decorated cellulose aerogel was prepared through dissolve/regeneration route. Noncovalent interactions were built between cellulose and added PANI in the ionic liquid solution which helped to construct composite.28 The prepared PANI-cellulose aerogel was characterized and the effect of this interaction was studied. The photocatalytic properties of PANI-decorated cellulose aerogel were estimated by the degradation of MB under the irradiation of natural sunlight. The catalytic property was studied and compared with that of neat PANI, cellulose aerogel and microcrystalline cellulose (MCC)-stabilized PANI nanoparticles.
2. Experimental
2.1. Materials
Microcrystalline cellulose (MCC) of chemical pure grade was purchased from Kelong Chemical Regent Co., Ltd. (Chengdu, China). All other chemical reagents and solutions used in the experiment were of analytical grade and used without further purification. Ionic liquid (1-butyl-3-methylimidazolium chloride, [Bmim]Cl) was purchased from Chengjie Chemical Reagent Co., Ltd. (Shanghai, China). Methylene blue (MB), ammonium peroxydisulphate (APS) and diethylene glycol were all purchased from Kelong Chemical Regent Co., Ltd. (Chengdu, China). Solutions used in the study were prepared with deionized water.
2.2. Preparation of cellulose aerogel
Typically, approximately 10 g of [Bmim]Cl was placed in a glass flask and melted in an oil bath at 90 °C. Then 0.2 g of MCC was dissolved in the ionic liquid solution with stirring. The prepared cellulose suspension was immersed into deionized water coagulation bath to coagulate and regenerated. Then the obtained hydrogel was washed with deionized water until there was no Cl− in the washed water. Cellulose aerogel was obtained by freeze-drying the resulted hydrogel.
2.3. Synthesis of PANI homopolymer
PANI homopolymer was used as photocatalyst in this study. It was synthesized by oxidative polymerization of aniline monomer in the aqueous diethylene glycol medium. Typically, 0.4 M aniline monomer and 0.4 M APS were dissolved in 1 M aqueous diethylene glycol solution, respectively. Then 50 mL of these two solutions were mixed together and homogenized with stirring for 1 min. The resulted solution was kept in dark under ambient temperature for 2 h for polymerization. Then the obtained PANI was washed with deionized water and filtered. It was freeze-dried for 12 h to reach constant weight.
2.4. Preparation of PANI-decorated cellulose aerogel and MCC-stabilized PANI
Approximately 10 g of [Bmim]Cl was placed in a glass flask and melted in an oil bath at 90 °C, followed by dissolving 0.2 g of MCC in the ionic liquid solution to prepare 2 wt% cellulose solution. Then 0.04 g of the obtained PANI homopolymer was added to the cellulose solution and homogenized for 2 h by continuous stirring and ultrasonic treatment. The obtained suspension was immersed into deionized water coagulation bath to coagulate and regenerated. Then the obtained hydrogel was washed with deionized water until there was no Cl− in the washed water. PANI-decorated cellulose aerogel was obtained by freeze-drying the resulted hydrogel.
About 0.2 g of MCC was dispersed with stirring in 10 g deionized water to prepared MCC-stabilized PANI. 0.04 g of the obtained PANI homopolymer was slowly added to the suspension and homogenized by continuous stirring and ultrasonic treatment for 2 h. The resulted suspension was filtered and washed with deionized water. The obtained composite was dried in an oven under 40 °C to reach constant weight.
2.5. Characterization
The morphology of neat PANI and PANI-decorated cellulose aerogel was studied by scanning electron microscopy (SEM) on a scanning electron microscope (Jed JSM-590LV, JEOL Inc., Japan). Fourier transform infrared (FTIR) spectroscopy was used to investigate the structure of neat PANI, cellulose aerogel and PANI-decorated cellulose aerogel. FTIR spectra were recorded on a Nicolet 560 spectrophotometer. Thermogravimetric analysis (TGA) and derivative thermogravimetric analysis (DTG) were performed using Q20 Thermal Analyzer (TA Instruments Inc., America). The samples were dried in oven at 80 °C for more than 6 h before test. The measurements were conducted under a nitrogen purge with the temperature for scanning ranged from 30 to 700 °C at a heating rate of 10 °C min−1. Differential scanning calorimetry (DSC) was conducted on a Q50 differential scanning calorimetry (TA Instruments Inc., America) to study the thermal behavior of neat PANI, cellulose aerogel and PANI-decorated cellulose aerogel. About 5 mg of samples were placed into the apparatus and nitrogen was used as protection. The samples were heated from 60 to 300 °C at a heating rate of 10 °C min−1. The temperature was kept for 5 min and cooled the samples from 300 to 60 °C at a cooling rate of 10 °C min−1. X-ray diffraction (XRD) patterns were collected on a Philips Analytical X'Pert X-diffractometer (Philips Co., Netherlands), using Cu-Kα radiation (k = 0.1540 nm) at an accelerating voltage of 40 kV and the current of 40 mA. The data were collected from 2θ = 10–60° with a step interval of 0.03°.
2.6. Measurement of photocatalytic activity
The photocatalytic properties of neat PANI, PANI-cellulose aerogel and MCC-stabilized PANI nanoparticles were measured by the degradation of MB in beakers under the irradiation of visible light and natural sunlight. In each reaction, 100 mL dye solution (20 mg L−1) was mixed with a same amount (0.15 g) of catalysts. Before irradiation, the suspensions were homogenized with stirring under dark condition and stayed to still. Then the suspensions were irradiated under light source. A self-made halogen tungsten lamp (500 W) located in a light-tight chamber was used as the irradiation source (λ = 420 nm). The luminous intensity was 23
500 μW cm−2. In the investigation of the photocatalytic properties under natural sunlight, all experiments were conducted in an open atmosphere between 12.00 am and 3.00 pm in July as applied before by previous study.29 The experiments were conducted at a settled place in sunny days. The luminous intensities were measured in a range of 22
000–25
000 μW cm−2. The catalytic degradation of MB was investigated at ambient temperature in the presence/absence of different catalysts under irradiation.
The degradation efficiency of MB over the surface of catalysts was measured using UV-vis spectroscopy (Shimadzu UVmini-1240 spectrophotometer, Shimadzu Co., Japan). The absorbance of the characteristic wavelength of MB was recorded. The degradation rate of MB was estimated according to following equation:
Degradation rate = C0 − C/C0 = A0 − A/A0 |
where
C0 represents the initial concentration,
C represents variable concentration,
A0 and
A corresponds to the initial absorbance and variable absorbance, respectively.
3. Results and discussion
3.1. Morphological studies
The morphology of PANI homopolymer and PANI-decorated cellulose aerogel was investigated by SEM as shown in Fig. 1. Fig. 1a presents the microphotograph of PANI homopolymer. It is clear that the PANI homopolymer are presented as nanoparticles with a diameter of about 150 nm. The prepared PANI nanoparticles are severely agglomerated into huge bulk as observed in the SEM image. Fig. 1b illustrates the SEM photograph of PANI-decorated cellulose aerogel regenerated from cellulose-ionic liquid solution. Nanofibrillated cellulose and PANI nanoparticles are indicated in the SEM image by red arrows. Nanofibrillated cellulose with widths ranging from 30 nm to 100 nm is randomly packed as a 3D networked structure and PANI nanoparticles are closely deposited on the surface of cellulose aerogel. Although the PANI deposited cellulose is densely packed, the PANI nanoparticles are only slightly agglomerated in this system. It is noticeable that the size of PANI nanoparticles in PANI-decorated cellulose aerogel is slightly smaller than that of the original PANI homopolymer. This result is possibly attributed to the agitation and ultrasonic treatment during the preparation process. The use of cellulose aerogel as template for PANI nanoparticles increased the accessibility of photocatalysts to dye molecules in aqueous phase.
 |
| Fig. 1 The SEM photographs of PANI homopolymer (a) and PANI-decorated cellulose aerogel (b). | |
3.2. FTIR studies
FTIR analysis was carried out to investigate the structure of neat PANI, cellulose aerogel and PANI-decorated cellulose aerogel. As shown in Fig. 2, neat PANI presents characteristic bands around 3262 cm−1 which could be attributed to N–H stretching mode30 The C
N and C
C stretching of quinoid and benzenoid are found at 1586 cm−1 and 1505 cm−1, respectively. Besides, the bands at 1302 cm−1 and 1147 cm−1 are ascribed to the C–N stretching of benzenoid and quinoid unit of PANI, respectively. The presence of benzenoid and quinoid units demonstrates that the prepared PANI is in its emeraldine form. In the FTIR spectrum of cellulose aerogel, the characteristic broad band at 3433 cm−1 is attributed to the O–H group of cellulose and the band around 2911 cm−1 is ascribed to the asymmetrically stretching vibration of C–H in pyranoid ring. Other broad bands are resulted from various functional groups, e.g. C–O and C–O–C.12,31 The characteristic bands of PANI (1570 cm−1 and 1464 cm−1) and cellulose aerogel (3427 cm−1) are presented in the spectrum of the composite, illustrating the successful preparation of PANI-decorated cellulose aerogel. Comparing to the characteristic bands of the neat PANI (1586 cm−1 and 1505 cm−1), the characteristic bands of the obtained composite are shifted to lower wavenumbers, suggesting the existence of interaction between PANI and the –OH groups in the cellulose.32
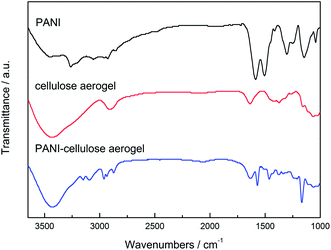 |
| Fig. 2 FTIR spectra of neat PANI, regenerated cellulose aerogel and PANI-decorated cellulose aerogel. | |
3.3. DSC analysis
The DSC thermograms of neat PANI, cellulose aerogel and PANI-decorated cellulose aerogel are presented in Fig. 3. The heating spectrograms of neat PANI and cellulose aerogel do not exhibit the glass transition temperature and melting point as shown in Fig. 3a. This may be attributed to their rigid molecular chain and close packing through hydrogen bonds. They were degraded before reaching melting point. For comparison, PANI-decorated cellulose aerogel exhibits a new endothermal peak. However, this peak does not appear in the cooling spectrogram as shown in Fig. 3b. This result could be ascribed to the breakage of hydrogen bond between PANI and cellulose, which is irreversible. Similar result was reported by Shi et al.28
 |
| Fig. 3 DSC endothermal (a) and exothermal (b) curves for neat PANI, cellulose aerogel and PANI-decorated cellulose aerogel. | |
3.4. TGA analysis
TGA analysis was carried out to investigate the thermal degradation behavior of PANI-decorated cellulose aerogel together with neat PANI and cellulose aerogel. Thermal gravimetric analysis and derivative thermogravimetric analysis plots of each sample are presented in Fig. 4a and b, respectively. A slight weight loss under 100 °C is observed in each sample due to the removal of moisture. For neat PANI, the weight loss process could be divided into three steps. The weight loss ranges from 150 °C to 450 °C is attributed to the degradation of the molecule of PANI homopolymer. The weight loss starting from around 450 °C corresponds to the thermal decomposition of PANI backbone chains.33 The degradation rate of PANI homopolymer is relatively slow. Large amount of residue was left (50.1 wt% in this case). The weight loss curve of cellulose aerogel shows a sharp decrease in the range of 240–350 °C which corresponds to the degradation of cellulose. From 350 °C to 600 °C, the residue of degraded cellulose was converted into gaseous components. Almost no solid residue (less than 0.1 wt%) was left at 700 °C. For comparison, the weight loss curve of PANI-decorated cellulose aerogel presents multiple steps of degradation. Although the second degradation step of neat PANI begins at 150 °C, the weight of PANI-decorated cellulose aerogel remains constant until 230 °C, which is slightly lower than that of cellulose aerogel. With the combination of PANI which is relatively more thermal stable, the degradation rate of PANI-decorated cellulose aerogel is slower than that of cellulose aerogel. The final weight loss step begins from 360 °C to 700 °C, which is mainly attributed to the thermal degradation of PANI. About 10 wt% of the composite was left at 700 °C. Considering the residual rate of PANI and cellulose aerogel, the initial mass fraction of PANI was calculated to be 20 wt%. However, the mass fraction of the added PANI was 16.7 wt%. This result may be attributed to the fact that cellulose was partially converted into carbon instead of forming gaseous components due to the strong interfacial interactions between PANI and cellulose.34 PANI deposited on the surface of cellulose aerogel acted as protective barrier which reduced the thermal decomposition rate. The much slower degradation rate and relatively larger residual rate indicate the protective effect of PANI to cellulose aerogel. This effect was also reported by Auad et al.35
 |
| Fig. 4 TG (a) and DTG (b) curves of neat PANI, cellulose aerogel and PANI-decorated cellulose aerogel. | |
3.5. XRD studies
The XRD patterns of neat PANI, cellulose aerogel and PANI-decorated cellulose aerogel are presented in Fig. 5. Three characteristic peaks are observed from the pattern of neat PANI. The most intense peak centered at 2θ = 18.3° ascribing to the (100) reflection of PANI36 is attributed to the periodicity parallel and perpendicular polymer chain of PANI. Another Bragg diffraction peak centered at 2θ = 25.7°, which is ascribed to the (200) plane of the orthorhombic unit cell of PANI, is assigned to the scattering from PANI chains at interplanar spacing.37 It can be observed from the graph that neat PANI has relatively high crystallinity. In the XRD pattern of cellulose aerogel, only one board peak is found centered at 2θ = 21.5°, which is assigned to the (200) planes of crystalline cellulose I. The board and faint peak indicate that cellulose aerogel has a low degree of crystallinity which might be resulted from its regeneration from ionic liquid. It is noticeable that the XRD pattern of the PANI-decorated cellulose aerogel shows only one peak near 21.8°. In this case, no characteristic peak of PANI can be observed, indicating that the crystalline phase of PANI had been destroyed and the incorporation with PANI did not influence the crystalline form of cellulose aerogel. The crystallization index (CrI) was calculated by following equation:
CrI = (I(200) − Iam)/I(200) |
where I(200) is the maximum intensity of the (200) lattice diffraction and Iam is the intensity of 18° of 2θ degrees. The CrI of cellulose aerogel and PANI-decorated cellulose aerogel was calculated to be 0.478 and 0.411, respectively. This result indicates the decrease of crystalline degree of cellulose with the incorporation with PANI. This result might be attributed to the strong interfacial interaction between PANI and cellulose which confined their crystallization.
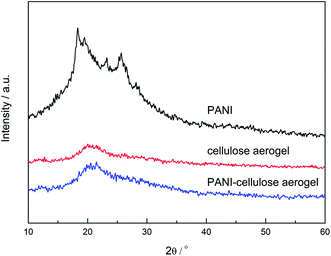 |
| Fig. 5 The XRD patterns of neat PANI, cellulose aerogel and PANI-decorated cellulose aerogel. | |
3.6. Catalytic properties
The photocatalytic degradation of MB dye in the presence/absence of different catalysts under different irradiation sources was studied. The UV-vis absorption spectra of MB catalyzed by PANI-decorated cellulose aerogel under natural sunlight and visible light irradiation are shown in Fig. 6. For original MB solution, a remarkable characteristic band can be found in 664 nm. The dramatic decrease of the absorption band intensity indicates the degradation of MB. This result demonstrates that PANI-decorated cellulose aerogel is an efficient catalyst for the photocatalytic degradation of MB dye. As can be seen in Fig. 6a, after exposing to natural sunlight in the presence of PANI-decorated cellulose aerogel for only 10 min, the characteristic absorption band intensity of MB dye decreased significantly. The degradation efficiency reaches 95% after reaction for 2 h. For comparison, the degradation rate for MB solution exposed to visible light is around 60% after 2 h as shown in Fig. 6b. This result may be attributed to the fact that the controlled visible light possesses only a single wavelength (λ = 420 nm) while natural sunlight has broad wavelengths ranging from the ultraviolet to the infrared. Irradiation of lights with various wavelengths contributed to the activation of the degradation of MB dye. Furthermore, comparing to artificial visible light or UV irradiation which requires substantial electrical power input, natural sunlight irradiation is a more efficient and economic irradiation source for the photocatalytic degradation of organic dyes. The better photocatalytic performance of catalysts under natural sunlight corresponds well with the result of ref. 18.
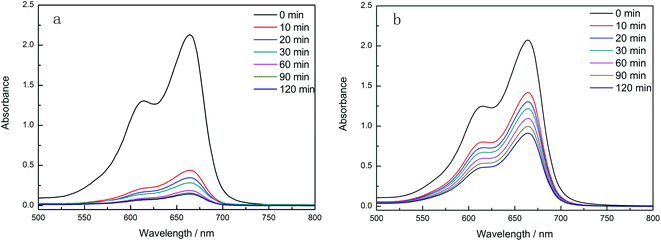 |
| Fig. 6 UV-vis absorption spectra of MB catalyzed by PANI-decorated cellulose aerogel under natural sunlight (a) and visible light irradiation (b). | |
Fig. 7 presents the UV-vis absorption spectra of MB solution in the absence/presence of different catalysts. In order to investigate the photocatalytic activity of PANI and the effect of cellulose aerogel as supporting material for catalyst, four sets of parallel experiments were conducted. The concentration of MB decreased in the absence of catalyst as a result of self-degradation under light irradiation. During this process, electron was generated which reacted with dissolved oxygen to form hydroxyl radicals.38 However, the degradation rate of MB solution is rather slow as shown in Fig. 7a. Only a slight change can be observed, the degradation grade is less than 20% after irradiation for 2 h. Fig. 7b shows the UV-vis absorption spectrum of MB solution catalyzed by neat PANI. The catalytic reaction rate is relatively fast for the first 10 min, which demonstrates that PANI is a valid catalyst for the photocatalytic degradation of MB. However, the poor dispersion of PANI powder led to much slower gradation rate afterwards, which is resulted from the poor accessibility of dye molecules to catalyst. In order to eliminate the absorption effect of cellulose aerogel, cellulose aerogel was added to MB solution under the irradiation of natural sunlight as shown in Fig. 7c. The degradation efficiency versus time is almost identical to that of MB solution without catalyst, which indicates that absorption effect of cellulose aerogel is negligible. The photocatalytic activity of PANI nanoparticles supported on another cellulose derivative, microcrystalline cellulose (MCC), was examined as shown in Fig. 7d. MCC increased the dispersibility of PANI nanoparticles in water phase to an extent, which resulted in better catalytic activity comparing to neat PANI.
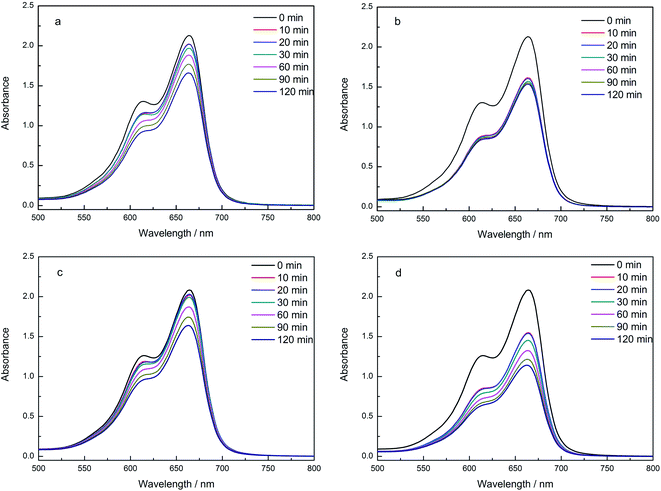 |
| Fig. 7 UV-vis absorption spectra of MB without catalyst (a) and catalyzed by different catalysts: neat PANI (b), cellulose aerogel (c) and MCC-stabilized PANI nanoparticles (d) (catalyst concentration = 1.5 mg mL−1, initial concentration of dyes = 20 mg mL−1). | |
The degradation rate of MB solution in the absence/presence of catalysts under the irradiation of natural sunlight is summarized in Fig. 8. It is clear that the degradation rate of PANI-decorated cellulose aerogel catalyzed reaction is significantly higher than other reactions. PANI is a valid photocatalyst whose catalytic activity is limited by its accessibility to reactants. As a supporting material, pristine cellulose aerogel has very limited effect on the degradation of MB, while it played a critical role to increase the catalytic activity of PANI. Wang and Shi39 used TiO2/PANI composite as a photocatalyst for the degradation of MB under irradiation of natural sunlight, in which PANI was used as a sensitizer for TiO2. The degradation rate of MB in their study was 80% after reaction for 1.5 h while the degradation rate exceeded 90% after 1.5 h for PANI-decorated cellulose aerogel catalyzed reaction. The degradation rate study illustrates that the photocatalytic activity of PANI-decorated cellulose aerogel is more effective than that of TiO2/PANI composite with even smaller catalyst/dye ratio (1.5 mg mL−1
:
20 mg L−1 to 2 mg mL−1
:
10 mg L−1). The results indicate that PANI-decorated cellulose aerogel is an efficient catalyst for the photocatalytic degradation of MB dye under the irradiation of natural sunlight.
 |
| Fig. 8 The degradation rate of MB solution in the absence/presence of catalysts under the irradiation of natural sunlight. | |
4. Conclusions
In this study, we have explored a facile and environmentally friendly method to prepare PANI-decorated cellulose aerogel for the photocatalytic degradation of MB. A green ionic liquid, [Bmim]Cl, was used to prepare cellulose solution. The morphology of PANI-decorated cellulose aerogel showed that cellulose aerogel served as the supporting material for PANI nanoparticles. The interfacial interaction between PANI and cellulose was characterized by FTIR, DSC, TGA and XRD studies. PANI-decorated cellulose aerogel showed superior photocatalytic activity towards the degradation of MB under the irradiation of natural sunlight. The easy access to PANI-decorated cellulose aerogel, sustainability of cellulose and the enhanced photocatalytic activity make this approach attractive for large-scale application.
Acknowledgements
The authors would like to thank the National Science Foundation of China (51203105) and National High Technology Research and Development Program (863 Program, SS2012AA062613) for financial support.
References
- H. L. Parker, A. J. Hunt, V. L. Budarin, P. S. Shuttleworth, K. L. Miller and J. H. Clark, RSC Adv., 2012, 2, 8992–8997 RSC.
- J. F. Wang, T. Tsuzuki, B. Tang, X. Hou, L. Sun and X. Wang, ACS Appl. Mater. Interfaces, 2012, 4, 3084–3090 CAS.
- B. Adhikari, G. Palui and A. Banerjee, Soft Matter, 2009, 5, 3452–3460 RSC.
- W. Ngah, L. Teong and M. Hanafiah, Carbohydr. Polym., 2011, 83, 1446–1456 CrossRef PubMed.
- S. K. Apte, S. N. Garaje, M. Valant and B. B. Kale, Green Chem., 2012, 14, 1455–1462 RSC.
- D. Bahnemann, Sol. Energy, 2004, 77, 445–459 CrossRef CAS PubMed.
- U. Gaya and A. Abdullah, J. Photochem. Photobiol., C, 2008, 9, 1–12 CrossRef CAS PubMed.
- H. Katsumata, Y. Oda, S. Kaneco and T. Suzuki, RSC Adv., 2013, 5, 6815–6819 Search PubMed.
- S. Chen, B. Zhou, W. Hu, W. Zhang, N. Yin and H. Wang, Carbohydr. Polym., 2013, 92, 1953–1959 CrossRef CAS PubMed.
- N. Kislove, J. Lahiri, H. Verma, D. Goswami, E. Stefanakos and M. Batzill, Langmuir, 2009, 25, 3310–3315 CrossRef.
- A. Panniello, M. Curri, D. Diso, A. Licciulli, V. Locaputo, A. Agostiano, R. Comparelli and G. Mascolo, Appl. Catal., B, 2012, 121–122, 190–197 CrossRef CAS PubMed.
- C. M. Correa, R. Faez, M. A. Bizeto and F. F. Camilo, RSC Adv., 2012, 2, 3088–3093 RSC.
- A. Katoch, M. Burkhart, T. Hwang and S. Kim, Chem. Eng. J., 2012, 192, 262–268 CrossRef CAS PubMed.
- Z. Zhou, Z. Zhang, D. Tian, R. Xiong and C. Lu, Mater. Res. Innovations, 2013, 17, 84–91 CrossRef CAS PubMed.
- L. Li, A. O. Raji, H. L. Fei, Y. Yang, E. L. G. Samuel and J. M. Tour, ACS Appl. Mater. Interfaces, 2013, 5, 6622–6627 CAS.
- D. Ghosh, S. Giri, A. Mandal and C. K. Das, RSC Adv., 2010, 81, 712–719 Search PubMed.
- S. Ameen, H. Seo, M. Akhtar and H. Shin, Chem. Eng. J., 2012, 210, 220–228 CrossRef CAS PubMed.
- V. Eskizeybek, F. Sari, H. Gülce, A. Gülce and A. Avci, Appl. Catal., B, 2012, 119–120, 197–206 CrossRef CAS PubMed.
- M. Liu, Y. Zhang, J. J. Li and C. R. Zhou, Int. J. Biol. Macromol., 2013, 5, 23–30 CrossRef PubMed.
- M. Liu, C. Wu, Y. Jiao, S. Xiong and C. R. Zhou, J. Mater. Chem. B, 2013, 1, 2078 RSC.
- D. Klemm, B. Heublein, H. Fink and A. Bohn, Angew. Chem., 2005, 44, 3358–3393 CrossRef CAS PubMed.
- R. Xiong, C. Lu, Y. Wang, Z. Zhou and X. Zhang, J. Mater. Chem. A, 2013, 1, 14910–14918 CAS.
- X. Wu, C. Lu, W. Zhang, G. Yuan, R. Xiong and X. Zhang, J. Mater. Chem. A, 2013, 1, 8645–8652 CAS.
- Z. Zhou, C. Lu, X. Wu and X. Zhang, RSC Adv., 2013, 3, 26066–26073 RSC.
- A. Javadi, Q. F. Zheng, F. Payen, A. Javadi, Y. Altin, Z. Y. Cai, R. Sabo and S. Q. Gong, ACS Appl. Mater. Interfaces, 2013, 5, 5969–5975 CAS.
- Q. F. Zheng, A. Javadi, R. Sabo, Z. Y. Cai and S. Q. Gong, RSC Adv., 2013, 3, 20816 RSC.
- C. Garcia-Gonzalez, M. Alnaief and I. Smirnova, Carbohydr. Polym., 2011, 86, 1425–1438 CrossRef CAS PubMed.
- X. Shi, L. Zhang, J. Cai, G. Cheng, H. Zhang, J. Li and X. Wang, Macromolecules, 2011, 44, 4565–4568 CrossRef CAS.
- W. Zhao, Z. Bai, A. Ren, B. Guo and C. Wu, Appl. Surf. Sci., 2010, 256, 3493–3498 CrossRef CAS PubMed.
- W. Zheng, M. Angelopoulos, A. Epstein and A. McDiarmid, Macromolecules, 1997, 30, 2953–2955 CrossRef CAS.
- Z. Mo, Z. Zhao, H. Chen, G. Niu and H. Shi, Carbohydr. Polym., 2009, 75, 660–664 CrossRef CAS PubMed.
- A. Youssef, M. El-Samahy and R. M. Abdel, Carbohydr. Polym., 2012, 89, 1027–1032 CrossRef CAS PubMed.
- S. Bhadra, N. Singha and D. Khastgir, J. Appl. Polym. Sci., 2007, 104, 1900–1904 CrossRef CAS.
- A. Stejskal, M. Trchova and I. Sapurina, J. Appl. Polym. Sci., 2005, 98, 2347–2354 CrossRef.
- M. Auad, T. Richardson, W. Orts, E. Medeiros, L. Mattoso, M. Mosiewicki, N. Marcovich and M. Aranguren, Polym. Int., 2011, 60, 743–750 CrossRef CAS.
- A. Hopkins, R. Lipeles and S. Hwang, Synth. Met., 2008, 158, 594–601 CrossRef CAS PubMed.
- S. Min, F. Wang and Y. Han, J. Mater. Sci., 2007, 42, 9966–9972 CrossRef CAS.
- S. Tawkaew and S. Supothina, Mater. Chem. Phys., 2008, 108, 147–153 CrossRef CAS PubMed.
- F. Wang and X. Shi, Chin. Chem. Lett., 2007, 18, 1273–1277 CrossRef CAS PubMed.
Footnote |
† Electronic supplementary information (ESI) available. See DOI: 10.1039/c3ra46441e |
|
This journal is © The Royal Society of Chemistry 2014 |
Click here to see how this site uses Cookies. View our privacy policy here.