DOI:
10.1039/C3NR04871C
(Paper)
Nanoscale, 2014,
6, 477-482
Graphene–NiO nanohybrid prepared by dry plasma reduction as a low-cost counter electrode material for dye-sensitized solar cells†
Received
12th September 2013
, Accepted 15th October 2013
First published on 18th October 2013
Abstract
NiO nanoparticles (NPs) were hybridized on the surface of reduced graphene oxide (RGO) by dry plasma reduction (DPR) at atmospheric pressure without any toxic chemicals and at a low temperature. NiO-NPs of 0.5–3 nm size, with a typical size of 1.5 nm, were uniformly hybridized on the surface of RGO. An XPS analysis and the Raman spectra also revealed the repair of some structural damage on the basal plane of the graphene. The material when applied to the counter electrode (CE) of dye-sensitized solar cells (DSCs) exhibited a power conversion efficiency of 7.42% (±0.10%), which is comparable to a conventional Pt-sputtered CE (8.18% (±0.08%)). This material outperformed CEs produced using NiO-NPs (1.53% (±0.15%)), GO (4.48% (±0.12%)) and RGO (5.18% (±0.11)) due to its high electrochemical catalytic activity and high conductivity. The charge transfer resistance for NiO-NP–RGO was as low as 1.93 Ω cm2, while those of a NiO-NP-immobilized electrode and a GO-coated electrode were 44.39 Ω cm2 and 12.19 Ω cm2, respectively, due to a synergistic effect.
1. Introduction
Due to their low fabrication cost, environmentally benign process, glossy transparency, and relatively high energy conversion efficiency, dye-sensitized solar cells (DSCs) have attracted considerable attention as next-generation solar cells.1 One of the issues with DSCs is the need to improve the generation of iodide from the triiodide existing in the counter electrode (CE). Pt is considered to be one of the best materials as a CE for DSCs.1–5 However, the scarcity and high cost of Pt limits the mass production of these types of DSCs. Thus, numerous substitutes, such as carbon nanotubes (CNTs),6 CNT-TiN,6,7 CNT-Pt,6,8 chemical vapor deposition (CVD)-grown graphene,9 Pt NPs hybridized on CVD-grown graphene,9 graphene oxide (GO) and reduced graphene oxide (RGO)/Pt-NP materials10 have been developed to replace or reduce the amount of expensive Pt required. Nevertheless, carbon materials usually require a thick carbon film to achieve an acceptable level of catalytic activity.6 Pt-nanoparticles (NPs) supported on carbon materials can be a reasonable alternative, as they satisfy the inevitable requirements of a low cost compared to a Pt-sputtered layer, excellent catalytic functionality, and high electric conductivity. However, Pt metals are still required.
Recently, NiO-NPs supported on graphene were used as an electrocatalyst for the CE of a DSC.11 This material can be prepared by pulsed laser ablation,11 homogeneous precipitation and subsequent annealing at 400 °C for 3 h in a nitrogen atmosphere,12,13 a rapid microwave treatment and subsequent annealing at 400 °C for 3 h in a nitrogen atmosphere,14 or by thermal decomposition at 500 °C for 5 h in a vacuum (<10 Pa).15 However, it remains a great challenge to synthesize high-quality nanohybrids containing many uniform metal NPs that are well dispersed on a graphene surface due to the high chemical reduction rate,12 the long reduction time for the cooling process required after thermal decomposition or the agglomeration of NPs during high-temperature reduction,12–15 or the need for expensive equipment like a vacuum chamber.11,15 All of these factors render it difficult to develop an economic continuous process.11
A cold plasma treatment was applied to synthesize NiO-loaded semiconductors with sequential reduction at 773 K and oxidation at 473 K.16 However, the system also required a vacuum chamber. Recently, we developed a new process that efficiently synthesizes supported Pt-NPs using dry plasma reduction (DPR) at temperatures close to room temperature at atmospheric pressure.5,8–10 This technique is able to overcome the previously mentioned process restrictions, especially those related to a high temperature, low pressure, liquid environment, and to the chemical toxicity.10 Furthermore, it can reduce the number of oxygen-containing functional groups on the surface of the GO6 due to the formation of hydrogen radicals and electrons during the plasma reduction process.10,17
Herein, we present a strategy which easily, continuously, uniformly and stably hybridizes NiO-NPs on the surface of reduced graphene oxide (RGO) with the simultaneous co-reduction of Ni precursor ions and GO to Ni atoms and RGO, respectively, through DPR. Additionally, owing to formation of oxygen radicals during the plasma reduction process,6 NiO is generated on the surfaces of Ni-NPs.16 It is expected that the NiO-NP–RGO nanohybrids will show high catalytic activity and conductivity for regenerating iodide from triiodide at the CEs of DSCs.
2. Experimental section
2.1. Materials
GO was synthesized from graphite flakes using a method available in the literature.10 A precursor solution containing 10 mM nickel(II) chloride hexahydrate (Aldrich) in iso-propyl alcohol (IPA) (99.5%, Sigma-Aldrich) was initially prepared. FTO glass as a conductive transparency electrode was purchased from Pilkington in the USA (∼8 Ω □−1). These substrates were used after a sonic cleaning treatment in acetone (Fluka). Nonporous TiO2 paste and a ruthenium-based dye (N719) were purchased from Solaronix, Switzerland. The dye was adsorbed from a 0.3 mM solution in a mixed solvent of acetonitrile (Sigma-Aldrich) and tert-butyl alcohol (Aldrich) at a volume ratio of 1
:
1. The electrolyte was a solution of 0.60 M 1-methyl-3-butylimidazolium iodide (Sigma-Aldrich), 0.03 M I2 (Sigma-Aldrich), 0.10 M guanidinium thiocyanate (Sigma-Aldrich), and 0.50 M 4-tert-butylpyridine (Aldrich) in a mixed solvent of acetonitrile (Sigma-Aldrich) and valeronitrile, with a volume ratio of 85
:
15.
2.2. Synthesis and characterization of NiO-NPs hybridized on graphene oxide sheets
The GO paste and GO CEs were prepared using a method available in the literature.10 3 μl of a Ni precursor was dropped onto a GO CE and the solvent was allowed to evaporate at 70 °C for 10 min. The specimens were then reduced using Ar plasma at atmospheric pressure at a power of 150 W, a gas flow rate of 5 lpm, a reduction time of 15 min, and a substrate moving speed of 5 mm s−1.5,8–10
The morphology of the NiO-NP–RGO nanohybrid was characterized using field-emission scanning electron microscopy (FESEM) (Jeol JSM 7000F). The structure of the NiO-NP–RGO nanohybrid was analyzed by X-ray diffraction (XRD) spectroscopy (Rigaku D/MAX-RC) and transmission electron microscopy (TEM) (JEM-2100F, Joel, Japan). The chemical state of the nanohybrids was analyzed by X-ray photoelectron spectroscopy (XPS) using a spectrometer (Sigma Probe Thermo Fisher VG Scientific) equipped with a monochromatic Al Kα X-ray source, and by energy-dispersive X-ray spectroscopy (EDS) (JEM-2100F, Joel, Japan). For a TEM analysis of a highly magnified NiO-NP–RGO nanohybrid, we scratched part of the coated layer, dispersed it in an ethanol suspension, and transferred it to a holey carbon grid.5,10 The Raman spectra were measured using a 532 nm DPSS laser and with a UniRAM high-resolution dispersive Raman spectrograph.
2.3. Preparation and electrochemical characterization of counter electrodes
We prepared five different CEs for comparison. The first one was a GO-coated CE. The details of the electrode fabrication are described in an earlier study.6 The second sample was a Pt-sputtered CE. It was deposited by the DC-sputtering of Pt at 10 mA at a pressure of 2 × 10−3 torr for 5 min.3 The third one was a NiO-NP–RGO-coated CE. It was prepared as explained in the previous section. The fourth sample utilized NiO-NPs directly immobilized on FTO glass using dry plasma reduction (see the ESI, Fig. S1†). It was prepared as described in a previous study.5 Finally, the fifth one was a RGO-coated electrode prepared from a GO-coated electrode through DPR.5 The redox behaviors of these electrodes were evaluated through a comparative analysis of their CVs. Three electrode electrochemical cells were used. A Pt mesh and a Hg/Hg2+ electrode served as the CE and the reference electrode, respectively. The electrolyte consisted of 10 mmol L−1 LiI, 1 mmol L−1 I2 and 1 mmol L−1 LiClO4. The CVs were recorded in a range of 600 to −300 mV at a scan rate of 50 mV s−1.3
2.4. Assembly and measurement of DSCs
The assembly and measurement of the DSCs were carried out as described in our previous study.3 The photocurrent–voltage characteristics were assessed with an IviumStat device under illumination from a Sun 3000 solar simulator consisting of 1000 W mercury-based Xe arc lamps and AM 1.5-G filters. The impedance spectroscopy of the DSCs was measured under constant light illumination (100 mW cm−2) biased under an open-circuit condition with a frequency range of 100 kHz to 100 mHz and a perturbation amplitude of 10 mV.
3. Results and discussion
3.1. Synthesis and characterization of NiO-NP–RGO nanohybrid materials
SEM and TEM images of the NiO-NP–RGO nanohybrid structures are shown in Fig. 1(a) and (b). The SEM images show that the NiO-NPs are successfully immobilized on the RGO. The reduction of GO to RGO was confirmed by XPS data in a previous study.10 Additionally, the formation of NiO was proved by the EDS, XRD and XPS data in Fig. 1(c)–(e) and the Raman spectra in Fig. 2. As shown in Fig. 1(b), NiO-NPs are highly dispersed on the surface of RGO with a small agglomeration. The TEM image further confirms the results of the SEM analysis, showing that the NiO-NPs are 0.5–3 nm in size, typically 1.5 nm; they are quite small and highly mono-dispersed. The average sizes of NiO-NPs formed on the surface of graphene prepared by pulsed laser ablation11 and thermal decomposition15 were 14.2 and ∼25 nm, respectively. Our NiO-NPs are not only uniform but are also well distributed on the surface of the RGO without any aggregation, as distinctly shown in Fig. 1(b). The estimated lattice spacing of a NiO-NP is 2.10 Å, which coincides well with NiO {200}.12,13,15 EDS, measured during the TEM observation in Fig. 1(b), identified the NiO-NPs immobilized on the surface of the RGO. The peaks of Ni were observed as shown in Fig. 1(c). The peak of O originates from both NiO and the oxygen functional groups of the RGO. The other peaks for C and Cu likely originated from the RGO, and from the background grid and system, respectively. XRD of the NiO-NP–RGO nanohybrid samples on the Si wafer substrate is shown in Fig. 1(d). The single broad diffraction peak at around 2θ = 33° belongs to the Si wafer substrate. All of the XRD patterns of the NiO-NP–RGO nanohybrid sample exhibit the characteristic diffraction peaks of NiO (111) and NiO (200). In order to identify the formation of NiO on the surface of RGO during DPR, we recorded the XPS spectrum of Ni2p, as represented in Fig. 1(e). The fitting results of the Ni2p spectrum are listed in Table 1. The major peaks at 854.1, 855, 855.8 and 861.2 eV can be assigned to the state of NiO; the peaks at 856.1 eV and 858.5 eV can be attributed to NiCl2 and Ni metal, respectively. This result shows that the NiO was formed on the RGO given the percentage of the NiO state of Ni (79.64%).
 |
| Fig. 1 (a) SEM image of NiO-NP–RGO CE; (b) TEM image showing the NiO-NPs immobilized on RGO, and the inset image shows the lattice spacing and particle size distribution of NiO-NPs attached onto the RGO; (c) EDS spectra obtained from all areas of the TEM image in (b); (d) XRD pattern of a NiO-NP–RGO nanohybrid on a Si wafer substrate; and (e) XPS Ni2p core-level spectrum of NiO-NP–RGO. | |
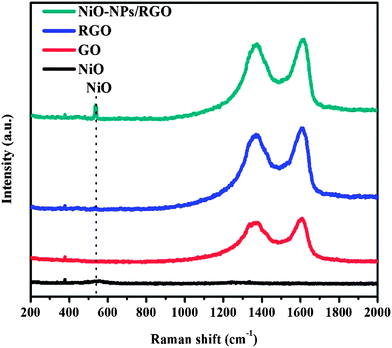 |
| Fig. 2 Raman spectra of the NiO (black line), GO (red line), RGO (blue line) and NiO-NP–RGO nanohybrid (dark cyan). | |
Table 1 Results of the fitting of the Ni2p spectrum of NiO-NP–RGO
Binding energy (eV) |
NiO |
NiO |
NiO |
NiCl2 |
Ni |
NiO |
854.1 |
855.0 |
855.8 |
856.1 |
858.5 |
861.2 |
Sample |
Atomic percentage (%) |
NiO-NP–RGO |
2.36 |
12.36 |
7.78 |
7.86 |
12.51 |
57.13 |
The Raman spectroscopy results for NiO, GO, RGO and NiO-NP–RGO are presented in Fig. 2. The discernible peaks can be indexed as a D band at 1340 cm−1, a G band at 1595 cm−1, and a D′ band at 1620 cm−1 (ESI, Fig. S2†). Furthermore, the intensity of the D band is higher than that of the G band. These phenomena can be attributed to the significant decrease in the size of the in-plane sp2 domains due to oxidation and ultrasonic exfoliation, and to the partially ordered graphite crystal structure of the graphene nanosheets.18,19 At the same time, a strong D′ peak occurred, which can be assigned to the nonzero phonon density of the states above the G band. These phonons, which are usually Raman-inactive, can become active due to phonon confinement caused by the defects.20 We noted that the ID/IG intensity ratio of GO (2.36) is in good agreement with the value found in earlier work,10 and it is higher than that for the RGO (2.05) and NiO-NP–RGO nanohybrid (2.11). The lowering of the D to G peak ratio indicates an increase in the average size of the sp2 domains upon reduction of the GO due to the loss of oxygen.10,21 Furthermore, the Raman spectrum in Fig. 2 shows the characteristic peak of NiO.12–14 This is evidence of the immobilized NiO-NPs on the surface of the RGO and FTO glass.
3.2. Photocurrent–voltage characteristics of NiO-NP–RGO nanohybrid materials as the CE of a DSC
Fig. 3 shows the photocurrent–voltage (I–V) characteristics of DSCs fabricated with Pt-sputtered, NiO-NP–RGO nanohybrid-coated, GO-coated, RGO-coated, and NiO-NP-immobilized CEs. The device photovoltaic parameters are summarized in Table 2. The DSC with the NiO-NP–RGO nanohybrid-coated CE shows an energy conversion efficiency of 7.42% (±0.10%), which is better than those of the DSCs with the GO-coated and RGO-coated CEs and NiO-NP-immobilized CEs, viz. 4.48% (±0.12%), 5.18% (±0.11%) and 1.53% (±0.15%) due to the predominant synergic effect of graphene and NiO-NPs and owing to the greater number of interfacial active sites.6–10 The performance of the NiO-NP–RGO CE is generally comparable with that of the typical Pt-sputtered CE. It shows a slight disadvantage in the short-circuit current density (Jsc) and conversion efficiency (η) owing to a low electrical conductivity3–6 in the NiO-NP–RGO-coated CE as well as the lack of a reflection effect of the Pt mirror.6,9,10
 |
| Fig. 3 Photocurrent–voltage characteristics of DSCs fabricated with Pt-sputtered, NiO-NP–RGO nanohybrid-coated, GO-coated, RGO-coated, and NiO-NP-immobilized CEs. | |
Table 2 Photoelectric performance of the five cells shown in Fig. 3
Counter electrode |
J
sc (mA cm−2) |
V
oc (mV) |
FF (%) |
η (%) |
Pt-sputtered |
16.80 ± 0.05 |
763.33 ± 2.36 |
63.84 ± 0.09 |
8.18 ± 0.08 |
NiO-NP–RGO |
15.57 ± 0.12 |
763.33 ± 4.71 |
62.40 ± 0.32 |
7.42 ± 0.10 |
RGO |
15.26 ± 0.26 |
767.50 ± 2.50 |
44.27 ± 0.68 |
5.18 ± 0.11 |
GO |
14.37 ± 0.27 |
775.00 ± 3.07 |
40.18 ± 0.36 |
4.48 ± 0.12 |
NiO |
6.48 ± 0.51 |
755.00 ± 7.07 |
31.31 ± 0.29 |
1.53 ± 0.15 |
The effect of the CE type on the DSC performance was mainly derived from its different electrical conductivity and electrocatalytic activity during the reduction of triiodide to iodide.22–24 In the cyclic voltammograms (ESI, Fig. S3†), the peak positions of the I3−/I− redox energy level provide evidence of the different open circuit voltages (Voc) of the DSCs.3 However, the NiO-NP–RGO nanohybrid-coated electrode has a higher current density, suggesting a larger active surface,25 while the reduction reactions of triiodide ions on the GO-coated electrode and the NiO-NP-immobilized electrode are clearly lower. Therefore, the introduction of NiO-NPs on the surface of the GO-coated electrode, which was transferred to RGO under DPR, leads to an obvious improvement in the electrocatalytic activity.
3.3. Electrochemical impedance spectroscopy of the DSC with the NiO-NP–RGO nanohybrid-coated CE
Fig. 4 shows Nyquist plots of DSCs with the NiO-NP–RGO nanohybrid-coated, GO-coated, RGO-coated, NiO-NP-immobilized and Pt-sputtered CEs. As mentioned earlier, the introduction of the NiO-NPs on the GO-coated electrode leads to an obvious improvement in the electrocatalytic activity because it provides a larger active surface area.6,7 We found that the Rct1 of the NiO-NP–RGO nanohybrid-coated electrode was as small as 1.93 Ω cm2, whereas the Rct1 values of the NiO-NP-immobilized electrode, GO-coated electrode and RGO-coated electrode were 44.39 Ω cm2, 12.19 Ω cm2, and 3.06 Ω cm2, respectively. The Rct1 of the NiO-NP–RGO CE is close to that of the Pt-sputtered electrode (1.22 Ω cm2). The value of the constant-phase element (CPE1 = (CPE1-T)−1(jw)−(CPE1-P), in which j2 = −1, w = frequency, CPE1-T and CPE1-P are the frequency-independent parameters of the CPE) of the CE also confirms that the active surface area of the NiO-NP–RGO nanohybrid-coated electrode is larger than those of the Pt-sputtered electrode, NiO-NP-immobilized electrode, GO-coated electrode, and RGO-coated electrode. Indeed, the value of CPE1-T of 2.91 × 10−3 F cm−2 for the NiO-NP–RGO nanohybrid-coated electrode is much greater than the value of 9.59 × 10−5 F cm−2 of the Pt-sputtered electrode. It is also greater than 1.04 × 10−4 F cm−2 for the NiO-NP-immobilized electrode, and even greater than 2.16 × 10−3 F cm−2 and 2.66 × 10−3 F cm−2 for GO-coated and RGO-coated electrodes (Table 3). A larger CPE1-T means an increase in the active surface area. The porosity value (CPE1-P) for the five types of CEs are listed in Table 3. A decrease of the CPE1-P value means an increase in the porosity.26 We found that the CPE1-P values are 0.75 for the NiO-NP–RGO nanohybrid-coated electrode, 0.52 for the GO-coated electrode10 and 0.66 for the RGO-coated electrode, which are much smaller than those of Pt-sputtered electrode and NiO-NP-immobilized electrode, viz. 0.85 and 0.90, respectively. A larger porosity value means an increase in the capacitance.26 The Rh value of the NiO-NP–RGO nanohybrid-coated electrode measured at a high frequency range was found to be 2.44 Ω cm2, which is slightly lower than the value of 2.45 Ω cm2 found for both GO-coated and RGO-coated electrodes and 2.53 Ω cm2 for the NiO-NP-immobilized electrode. This effect is related to the existence of NiO-NPs on the RGO surface, which results in bridges that facilitate electron conductivity between RGOs (see the ESI†).2 However, the Rh value of the NiO-NP–RGO nanohybrid-coated electrode is higher than the value of 2.27 Ω cm2 for the Pt-sputtered electrode. A smaller Rh means an increase in the conductivity, which results in an increase in the Jsc value.3,4
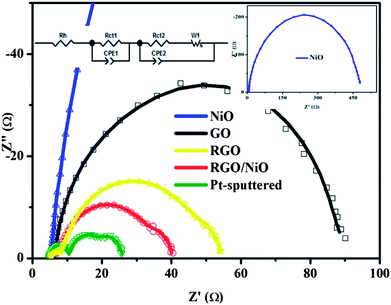 |
| Fig. 4 Nyquist plots of five DSCs equipped with Pt-sputtered, NiO-NP–RGO nanohybrid-coated, NiO-NP-immobilized, GO-coated, and RGO-coated CEs. The inset image shows the equivalent circuit diagram used to fit the observed impedance spectra in this figure and a Nyquist plot of a DSC equipped with a NiO-NP-immobilized CE. | |
Table 3 Impedance parameters of five DSCs with GO-coated, RGO-coated, NiO-NP–RGO nanohybrid-coated, NiO-NP-immobilized and Pt-sputtered CEs, as estimated from the impedance spectra and equivalent circuit shown in Fig. 4
Counter electrode |
R
h (Ω cm2) |
R
ct1 (Ω cm2) |
CPE1-T (F cm−2) |
CEP1-P |
R
ct2 (Ω cm2) |
W
s
|
CPE2-T (mF cm−2) |
CPE2-P |
R
|
T
|
P
|
NiO |
2.53 |
44.39 |
1.04 × 10−4 |
0.9 |
186.15 |
3.84 |
1.81 |
0.5 |
8.49 |
0.93 |
GO |
2.45 |
12.19 |
2.16 × 10−3 |
0.52 |
17.76 |
13.09 |
0.07 |
0.5 |
5.10 |
0.92 |
RGO |
2.45 |
3.06 |
2.66 × 10−3 |
0.66 |
14.70 |
2.95 |
0.48 |
0.5 |
4.23 |
0.90 |
NiO-NP–RGO |
2.44 |
1.93 |
2.91 × 10−3 |
0.75 |
13.27 |
2.92 |
0.37 |
0.5 |
1.61 |
0.90 |
Pt-sputtered |
2.27 |
1.22 |
9.59 × 10−5 |
0.85 |
3.39 |
2.54 |
0.45 |
0.5 |
6.53 |
0.92 |
According to Koide et al., the fill factor depends on the internal series resistance, which is composed of the following three elements: the redox reaction resistance at the counter electrode, the resistance of carrier transport by ions in the electrolyte, and resistance due to the sheet resistance of the transparent conducting oxide.27 Thus, fill factor was improved by reduction of the internal series resistance. The reduction of the total internal resistance due to the decrease in charge-transfer resistance is the cause of the increase in the fill factor of the DSCs,27 which confirms the increase in the conversion efficiency, as previously shown.
Conclusions
In summary, a high performing NiO-NP–RGO nanohybrid was successfully synthesized by dry plasma reduction at a low temperature. TEM results showed NiO-NPs ranging in size from 0.5 nm to 3 nm (typically 1.5 nm) dispersed on the surface of RGO. The electrochemical impedance measurement of the DSCs revealed that the charge-transfer resistance of the NiO-NP–RGO nanohybrid-coated electrode was close to that of a Pt-sputtered electrode. Thus, we expect that the NiO-NP–RGO nanohybrid-coated electrode can also be a low-cost electrode for energy conversion devices such as fuel cells or for energy storage devices such as lithium ion batteries or supercapacitors.
Acknowledgements
This research was supported by the Basic Science Research Program through the National Research Foundation of Korea (NRF) funded by the MEST (Ministry of Education, Science and Technology (2010-0006120)). This work was also supported by the Korean Brain Pool Program 2013 (131S-6-3-0538) and by the Future Core Technology Project (2E23964-13-045) of the Korea Institute of Science and Technology (KIST).
Notes and references
- B. O'Regan and M. Gratzel, Nature, 1991, 353, 737–739 CrossRef CAS.
- V. D. Dao and H. S. Choi, Electrochim. Acta, 2013, 93, 287–292 CrossRef CAS PubMed.
- V. D. Dao, S. H. Kim, H. S. Choi, J. H. Kim, H. O. Park and J. K. Lee, J. Phys. Chem. C, 2011, 115, 25529 CAS.
- V. D. Dao, H. S. Choi and K. D. Jung, Mater. Lett., 2013, 92, 11–13 CrossRef CAS PubMed.
- V. D. Dao, C. Q. Tran, S. H. Ko and H. S. Choi, J. Mater. Chem. A, 2013, 1, 4436 CAS.
- V. D. Dao, S. H. Ko, H. S. Choi and J. K. Lee, J. Mater. Chem., 2012, 22, 14023 RSC.
- G.-R. Li, F. Wang, Q.-W. Jiang, X. P. Gao and P. W. Shen, Angew. Chem., 2010, 122, 3735–3738 CrossRef.
- V. D. Dao and H. S. Choi, Chem. Commun., 2013, 49, 8910–8912 RSC.
- V. D. Dao, L. V. Nang, E. T. Kim, J. K. Lee and H. S. Choi, ChemSusChem, 2013, 6, 1316 CrossRef CAS PubMed.
- V. D. Dao, N. T. Quynh Hoa, L. L. Larina, J. K. Lee and H. S. Choi, Nanoscale, 2013 10.1039/c3nr03219a.
- R. Bajpai, S. Roy, N. Koratkar and D. S. Misra, Carbon, 2013, 56, 56–63 CrossRef CAS PubMed.
- X. J. Zhu, H. L. Dai, J. Hu, L. Ding and L. Jiang, J. Mater. Chem., 2012, 203, 243–249 CAS.
- X. J. Zhu, J. Hu, H. L. Dai, L. Ding and L. Jiang, Electrochim. Acta, 2012, 64, 23–28 CrossRef CAS PubMed.
- X. Su, H. Chai, D. Jia, S. Bao, W. Zhou and M. Zhou, New J. Chem., 2013, 37, 439–443 RSC.
- W. Lv, F. Sun, D. M. Tang, H. T. Fang, C. Liu, Q. H. Yang and H. M. Cheng, J. Mater. Chem., 2011, 21, 9014–9019 RSC.
- J. J. Zou, C. J. Liu and Y. P. Zhang, Langmuir, 2006, 22, 2334 CrossRef CAS PubMed.
- W. Xu, X. Wang, Q. Zhou, B. Meng, J. Zhao, J. Qiu and Y. Gogotsi, J. Mater. Chem., 2012, 22, 14363 RSC.
- H. M. Villullas, F. I. Mattos-Costa and L. O. S. Bulhoes, J. Phys. Chem. B, 2004, 108, 12898–12903 CrossRef CAS.
- K. N. Kudin, B. Ozbas, H. C. Schniepp, R. K. Prud'homme, I. A. Aksay and R. Car, Nano Lett., 2008, 8, 36–41 CrossRef CAS PubMed.
- G. Wang, J. Yang, J. Park, X. Gou, B. Wang, H. Liu and J. Yao, J. Phys. Chem. C, 2008, 112, 8192 CAS.
- Z. Luo, L. A. Somers, Y. Dan, T. Ly, N. J. Kybert, E. J. Mele and A. T. C. Johnson, Nano Lett., 2010, 10, 777–781 CrossRef CAS PubMed.
- B. A. Gregg, Coord. Chem. Rev., 2004, 248, 1215 CrossRef CAS PubMed.
- N. Papageorgiou, Coord. Chem. Rev., 2004, 248, 1421 CrossRef CAS PubMed.
- J. Halme, M. Toivola, A. Tolvanen and P. Lund, Sol. Energy Mater. Sol. Cells, 2006, 90, 872 CrossRef CAS PubMed.
- M. K. Wang, A. M. Anghel, B. Marsan, N. C. Ha, N. Pootrakul-chote, S. M. Zakeeruddin and M. Gratzel, J. Am. Chem. Soc., 2009, 131, 15976 CrossRef CAS PubMed.
- T. N. Murakami, S. Ito, Q. Wang, M. K. Nazeeruddin, T. Bessho, I. Cesar, P. Liska, R. Humphry-Baker, P. Comte, P. Péchy and M. Gratzel, J. Electrochem. Soc., 2006, 153, A2255 CrossRef CAS PubMed.
- N. Koide, A. Islam, Y. Chiba and L. Han, J. Photochem. Photobiol., A, 2006, 182, 296 CrossRef CAS PubMed.
Footnote |
† Electronic supplementary information (ESI) available. See DOI: 10.1039/c3nr04871c |
|
This journal is © The Royal Society of Chemistry 2014 |
Click here to see how this site uses Cookies. View our privacy policy here.