DOI:
10.1039/C2RA21418K
(Paper)
RSC Adv., 2012,
2, 11432-11437
Polyphosphazene membranes with phenoxyls for enhanced desulfurization†
Received
11th July 2012
, Accepted 29th August 2012
First published on 31st August 2012
Abstract
By changing pendant groups of polyphosphazene, poly[bis(phenoxy)phosphazene] (PBPP) were synthesized, characterized and investigated in model gasoline desulfurization experiments via pervaporation. Compared with poly[bis(trifluoroethoxy)phosphazene] (PTFEP), PBPP was substantially improved in pervaporation performance, thermal stability and swelling stability. The possibility of PBPP composite membrane for industrial experiments was also investigated. PBPP showed high toughness, long time durability and effective desulfurization property in laboratory scale experiments and based on the obtained results, PBPP was firmly believed to be a promising pervaporative membrane material for pervaporation desulfurization of gasoline in industrial experiments.
Introduction
Pervaporation is a membrane based process that is of great potential for its high efficiency, easy manipulation, low capital, operational cost etc.,1 aiming the separation of liquid mixtures. It is highly valued in the following aspects: the dehydration of organic solvents; the removal of trace volatile organic compounds in aqueous streams; organic–organic separation. As the most important aspect, the separation of organic–organic mixtures arouses great research interest for its difficulty in establishing structure–property relationship, for its complexity in separation mechanism and mass transfer behavior, and most importantly for its wide industrial application. One typical illustration for pervaporation organic–organic mixture separation is the desulfurization of gasoline.2,3 Recently, stringent regulations were made worldwide to limit the upper limit of sulfur content in gasoline.4 Thus the desulfurization of gasoline is both scientifically and industrially important. Technically, the pervaporation membrane plays a vital role in pervaporation desulfurization of gasoline. Three types of membranes are commonly used, i.e., inorganic membranes,5,6 polymeric membranes7–10 and mixed matrix (organic–inorganic) membranes (MMMs).11–14 Generally, inorganic membranes are heavy and suffer from high cost and complex fabrication process, while the lack of adhesion between the solid and the polymer phase prevents the implementation of MMMs.15 Thus, the polymeric membranes would dominate this field. Seeking new polymeric membranes and enhancing its performance are of extreme importance in gasoline desulfurization to reduce plant scale and capital cost. In most cases, crosslinking either by its intrinsic crosslinking sites or via external crosslinking agents was applied.9,16,17 Other methods, such as chemical modification on polymer backbone, are rarely reported.
In our previous report,18 polyphosphazene19–22 (POP), specifically poly[bis(trifluoroethoxy)phosphazene] (PTFEP), was selected for pervaporation desulfurization of gasoline and great results were obtained. Based on the previous research, we positively believe that a membrane with even better performance can be obtained by introducing aryls into the backbone. Thus, we hereby wish to investigate the possibility of pervaporation performance enhancements of POP by pendant group alteration. By this means, we want to expand the impact of material chemistry (chemical modification of polymer in particular) on membrane performance enhancements in pervaporation gasoline desulfurization. By altering trifluoroethoxy groups into phenoxy groups, poly[bis(phenoxy)phosphazene] (PBPP) was synthesized and characterized by NMR, FTIR and DSC. Finally, PBPP membrane was fabricated, tested for model gasoline desulfurization and investigated for its swelling stability and its thermal stability. The mechanical strength, durability and desulfurization efficiency of PBPP membrane were also investigated. These obtained results suggested that the PBPP membrane was of promising industrial value.
Experimental
Materials
Hexachlorocyclotriphosphazene (HCCP) was purchased from XinYi Chemical. Co., Ltd (Jiangsu, China). It was recrystallized twice in heptane and sublimed at 50 °C before use. Phenol was purchased from Alfa Aesar (Johnson Matthey, UK) and stored at 5 °C. Tetrahydrofuran and heptane were purchased from FuChen Chemicals (Tianjin, China) and were freshly distilled from sodium benzophenone ketyl. Benzophenone ketyl and anhydrous 1,4-dioxane were purchased from Alfa Aesar (Johnson Matthey, UK). Other chemicals were purchased from FuChen Chemicals (Tianjin, China) and used as received. PVDF (PVDF-1015, Mw ∼ 2.38 × 105 g mol−1) porous support was previously prepared in our laboratory using non-solvent induced phase separation (NIPS) method.23
PBPP synthesis
The synthesis of PBPP was similar to that in literature20,21 and is summarized in Fig. 1. Poly(dichlorophosphazene) (PDCP) was obtained by thermal ring opening polymerization at 260 °C for 25 h of HCCP, which was sealed in a glass tube under vacuum. The obtained PDCP (20 g, 0.17 mol) was then dissolved in dry tetrahydrofuran (THF, 300 ml) and reacted with excess sodium phenoxide prepared by reacting phenol (36.06 g, 0.38 mol) with sodium (8 g, 0.35 mol) in dry THF (200 ml). After being refluxed for 36 h under vigorous stirring, part of the solvent THF was removed and anhydrous 1,4-dioxane (400 ml) was added. The obtained mixture was then refluxed at 90 °C with vigorous stirring for another 48 h. Finally, by concentrating the obtained reaction mixture under reduced pressure, precipitation into methanol and washing with large amount of deionized water, PBPP was obtained. The polymer was further purified by repeated precipitation from THF into hexane. Finally, it was thoroughly dried under vacuum at 60 °C.
 |
| Fig. 1 Schematic of PBPP synthesis. | |
PBPP characterization
The as prepared PBPP was characterized and confirmed by 31P-NMR (Fig. S1†), DSC (Fig. S2†) and Fourier transformed infrared spectra in combination with attenuated total reflectance technique (FTIR-ATR) (Fig. S3†). Thermal stability tests of PBPP were conducted on a thermal gravimetric analyser (TGA) under nitrogen at a heating rate of 10 °C min−1 from 20 °C to 950 °C.
PBPP membrane preparation and characterization
PBPP pervaporation membrane was fabricated by solution casting method as we previously reported.24 A homogeneous solution of PBPP in THF was cast onto porous PVDF support. After evaporating THF thoroughly at 25 °C overnight, the prepared membrane was finally heated at 80 °C for 4 h to further remove the solvent. The PBPP membrane was stored in dry and clean conditions for further characterization and application.
A self-designed apparatus18 was used to characterize the desulfurization performances of PBPP membrane. Two important factors, the sulfur enrichment factor (β) and pervaporation flux (F) were calculated as follows by the method shared in the literature.11,25
|
| (1) |
|
| (2) |
where
cp and
cf are the sulfur contents of the permeate samples and the feed mixture, respectively, Δ
m is the total amount of the permeated mixture during the experimental time interval Δ
t and
S is the effective membrane area in contact with the feed solution.
Swelling tests were conducted by calculating the total liquid uptake of a homogeneous membrane in heptane over a period of time by the following equation, where ms and md stands for the mass of the swelled membrane and the dry membrane, respectively. Mechanical strength was tested on a universal testing machine using standard specimens.
| 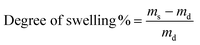 | (3) |
Results and discussion
Fig. 2 shows the desulfurization performance of PBPP composite membrane over the temperature range of 55 °C to 85 °C. The pervaporation flux increases when the temperature increases while the sulfur enrichment factor decreases with an increase in temperature. The obtained results suggested that the PBPP composite membrane shares a trade-off effect with other pervaporation membranes.25,26 Specifically, PBPP composite membrane exhibits the highest separation factor of 11.92 at 55 °C. Compared with PDMS,24 PEG27 and other membranes,17 the obtained enrichment factor is far beyond the average level. In our previous work,18 pervaporation desulfurization performance of PTFEP composite membrane was investigated. A critical issue in enhancing pervaporation performance was raised concerning the low pervaporation flux. Thus, the initial objective of this work was to increase the pervaporation flux of polyphosphazene membrane and to maintain its high enrichment factor by incorporating bulkier groups, i.e. phenoxyl. By introducing bulkier groups, the polymer would possess larger free volume which is believed to be favoured by mass transfer in a pervaporation process. Furthermore, by conducting this method we want to extend the means for membrane performance enhancements. Compared with PTFEP, PBPP is average 8 times increased in pervaporation flux. The obtained results offer a superior alternation for real application. Generally, the enrichment factor would decrease even if a slight increase occurs in the pervaporation flux.8,12 Surprisingly, the enrichment factor of PBPP is slightly decreased from an average of 10.6 to an average of 9.5 compared with PTFEP.
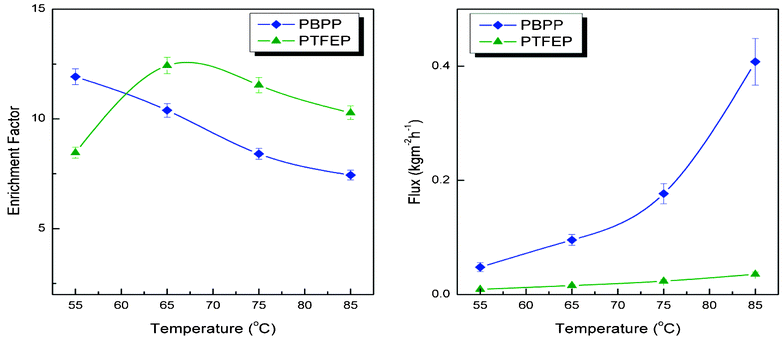 |
| Fig. 2 Comparison of pervaporation flux and sulfur enrichment factor of PTFEP (ref. 18, ▲) and PBPP (◆) at varying temperatures. The feed is composed of thiophene and heptane with a sulfur content of 400 ppm. | |
To fully investigate the membrane performance in pervaporation, the pervaporation separation index (PSI) was suggested.28 PSI was the product of separation flux and enrichment factor by the following equation.
When
β = 1, no separation occurs; a PSI of zero means either zero flux or no separation. PSI of both PBPP and PTFEP is presented in
Fig. 3. An average increase of around 6.5 times in PSI is observed. To our best knowledge, the enhancement is tremendous. It is commonly believed that membranes yield the same energy efficiency as distillation
29 for the pervaporation recovery of
ethanol when the separation factor is greater than twenty, which can also be viewed as an important initial target in pervaporation desulfurization. These results imply a huge potential for industrial application of gasoline desulfurization
via pervaporation.
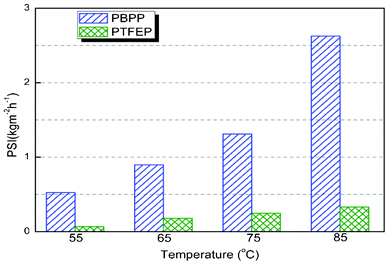 |
| Fig. 3 Pervaporation separation index of PBPP and PTFEP at varying temperatures. | |
Compared with the application in aqueous solutions, PV membranes are strictly required in stability for organic mixture separations, specifically gasoline desulfurization as presented in this work. The membrane swelling stability and thermal stability are substantially increased (see Fig. 4 and 5) in polyphosphazene membranes by alternating the pendant groups from trifluoroethoxy (PTFEP) to phenoxy (PBPP). The swelling tests reached equilibrium after 48 h of immersion in pure heptane. The degree of swelling for PTFEP and PBPP are 8% and 2%, respectively. The results show that by changing the pendant group, PBPP is 3 times decreased in liquid uptake compared with PTFEP. It implies higher stability for PBPP which is believed to be very important for organic mixture separation, especially model gasoline desulfurization. The difference in patterns between the degree of swelling and the pervaporation performance can be explained by a solution–diffusion model. The swelling is based solely on feed sorption and pervaporation is determined by both solution and diffusion. According to our previous research,18 PTFEP would be preferably absorbed resulting in higher degree of swelling. However, as for PBPP the larger free volume facilitated the mass transfer during pervaporation investigations and caused the difference in the pattern of swelling degree with that of pervaporation performance. Both PTFEP and PBPP were heated under nitrogen in a thermogravimetric analyzer (TGA) to characterize their thermal stability. A sharp decrease in weight occurred due to the breakage of covalent bonds at 370 °C and 420 °C for PTFEP and PBPP, respectively. Moreover, the final weight losses for PBPP and PTFEP are 78% and 96%, respectively. The results imply great thermal stability for both polyphosphazene polymers and PBPP is more stable than PTFEP.
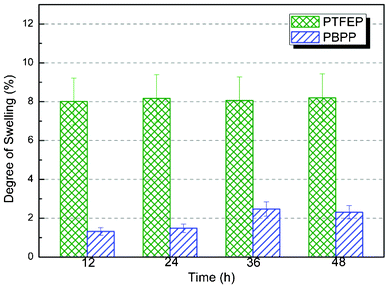 |
| Fig. 4 Comparison of swelling stability of PBPP with PTFEP at room temperature. Liquid uptake reaches equilibrium after 48 h of immersion in feed. | |
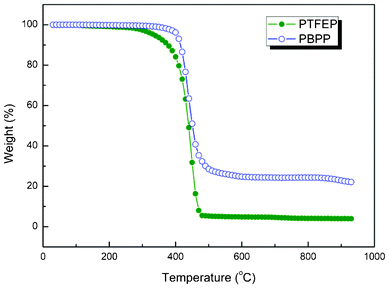 |
| Fig. 5 Thermal stability analysis on PTFEP and PBPP. The samples are heated under nitrogen at 10 °C min−1 from 20 °C to 950 °C. | |
By comprehensively comparing the above mentioned results and discussion, we can conclude that polyphosphazene membranes are substantially improved (as in pervaporation performance, thermal stability and swelling stability) in model gasoline desulfurization via pendant group altering, i.e. from PTFEP to PBPP.
Other parameters also have great impact on the desulfurization performance of PBPP composite membrane, such as feed composition and the sulfur content of feed mixtures. These factors were investigated and results are presented in Fig. 6 and 7. The sulfur enrichment factor substantially varies when the feed composition changes. PBPP composite membrane shows the highest enrichment factor for thiophene, followed by butylmercaptan and ethyl thioether. It can be explained according to the solubility parameter theory.30,31 The solubility parameter theory suggests that the component with the most similar solubility parameter (δ) would preferably be absorbed into the membrane and consequently enriched the downstream. The solubility parameters of PBPP, thiophene, ethyl thioether and butylmercaptan are presented in Table 1. The differences in solubility parameters with PBPP increase in the following order: thiophene < butylmercaptan < ethyl thioether. According to the prediction of solubility parameter theory, the enrichment factor of PBPP membrane for their separation from model gasoline decreased in the order thiophene > butylmercaptan > ethyl thioether. The obtained results exhibit unexceptionable accordance with theoretical predictions. As for separation fluxes, the predominant mass transfer component is heptane. Consequently, tiny differences are observed due to the relative small amount of sulfur compounds in the feeds (around 400 ppm). The same trend is observed for different thiophenes (in the order of: thiophene, 2-methylthiophene, 2,5-dimethylthiophene) at 80 °C despite the changes in feed sulfur content. All these experimental results are consistent with theoretical predictions. Moreover, sulfur enrichment factor and pervaporation flux changes slightly when feed sulfur content varies. The relative low concentration of sulfur compounds is responsible over the range.
Table 1 Solubility parameters of PBPP and sulfur compounds of this work
Species |
Solubility parameters (δ, MPa0.5) |
|Δδ| (MPa0.5) |
PBPP |
20.74 |
— |
Thiophene |
20.10 |
0.64 |
Ethyl thioether |
17.34 |
3.40 |
Butylmercaptan |
23.06 |
2.68 |
2-Methylthiophene |
19.60 |
1.14 |
2,5-Dimethylthiophene |
19.40 |
1.34 |
To apply PBPP membrane in pilot scale, mechanical strength, durability and desulfurization efficiency should be taken into consideration. Tests on these aspects were conducted and are presented in Fig. 8, 9 and 10, respectively. Although TGA is considered to be the most important factor in published reports,12,32,33 we firmly believe that the mechanical strength of a pervaporation membrane plays a much more important role. For example, the membrane modules have to be compacted in assembling, thus the membranes would be strictly required in toughness; otherwise defects would appear. The tensile strength and elongation at break for PBPP homogeneous membrane are average 13.24 MPa and 729.5%, respectively. The results imply high toughness for PBPP pervaporation membrane, which is very important for pilot scale application. Moreover, the PBPP composite membrane shows great durability in laboratory experiments over 200 h of continuous operation (see Fig. 9). By applying mass conservation equation on thiophene, the desulfurization efficiency of PBPP composite membrane was investigated. The mass conservation of thiophene is depicted by the following differential equation,
| 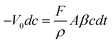 | (5) |
where,
V0 stands for the original volume of the feed;
c stands for feed sulfur content;
F is flux;
A is the effective membrane area;
β is enrichment factor;
ρ is the density of the permeate and
t is time. By integration over time, the relationship between feed sulfur content can be described as follows:
|  | (6) |
where
K is a constant based on the
F,
A,
V0,
β and
ρ, as shown in
eqn (7).
|  | (7) |
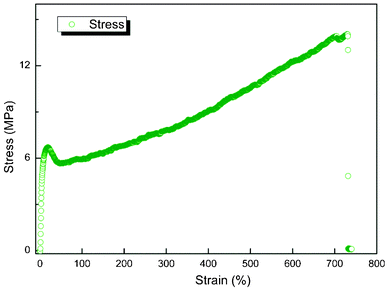 |
| Fig. 8 Stress–strain curve of homogeneous PBPP membrane (standard specimens used). Four repeated experiments were carried out and an average was made. | |
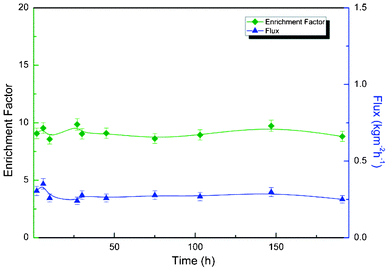 |
| Fig. 9 Durability experiments for PBPP composite membrane in model gasoline (heptane–thiophene) desulfurization at 80 °C. | |
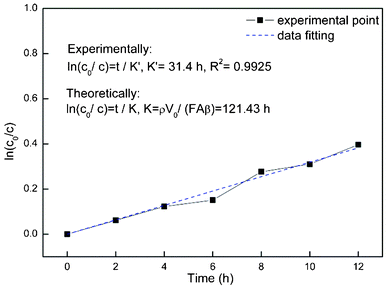 |
| Fig. 10 Modeling and desulfurization efficiency of PBPP composite membrane via pervaporation for model gasoline (heptane–thiophene) of 2 L at 80 °C; the initial sulfur content was around 1000 ppm. | |
Fig. 10 shows the experimental results and a data fitting process was applied to check the consistency and to validate the model. Good accordance was obtained (R2 = 0.9925). However, deviation does exist due to the assumption that F, V0 and β are constant over time and ρ can be replaced by the density of heptane.
Conclusions
Pervaporation desulfurization performance, swelling stability and thermal stability of polyphosphazene membrane were tremendously improved by altering the pendant groups from trifluoroethoxy to phenoxy. PBPP membrane was approximately 8-fold higher in pervaporation flux with little sacrifice in enrichment factor. Total pervaporation separation index (PSI) was 6.5 times increased. The reported results prove that methods for performance enhancement in a pervaporative membrane can be further explored. For a specific membrane, i.e. PBPP, the pervaporation performance can also be influenced by operating conditions, such as temperature and feed composition while feed sulfur content shows little impact. Taking into account the mechanical strength, durability and desulfurization efficiency, the obtained results suggests that PBPP is a promising pervaporation desulfurization membrane material for pilot scale experiments.
Acknowledgements
The authors greatly appreciate the financial supports of the Major State Basic Research Program of China (2009CB623404), National High Technology Research and Development Program of China (No. 2012AA03A607), National Natural Science Foundation of China (21176135). The authors greatly appreciate the suggestions of Prof. H. R. Allcock (Penn State University, USA) during the synthesis of PDCP. His kind help makes this manuscript available for publishing.
References
- P. Shao and R. Y. M. Huang, J. Membr. Sci., 2007, 287, 162–179 CrossRef CAS.
- L. Lin, Y. Zhang and Y. Kong, Fuel, 2009, 88, 1799–1809 CrossRef CAS.
- H. R. Mortaheb, F. Ghaemmaghami and B. Mokhtarani, Chem. Eng. Res. Des., 2012, 90, 409–432 CrossRef CAS.
- T. G. Kaufmann, A. Kaldor, G. F. Stuntz, M. C. Kerby and L. L. Ansell, Catal. Today, 2000, 62, 77–90 CrossRef CAS.
- T. C. Bowen, R. D. Noble and J. L. Falconer, J. Membr. Sci., 2004, 245, 1–33 CrossRef CAS.
- K. Sato, K. Sugimoto, N. Shimotsuma, T. Kikuchi, T. Kyotani and T. Kurata, J. Membr. Sci., 2012, 409–410, 82–95 CrossRef CAS.
- J. Chen, J. D. Li, J. X. Chen, Y. Z. Lin and X. G. Wang, Sep. Purif. Technol., 2009, 66, 606–612 CrossRef CAS.
- Y. Kong, L. Lin, Y. Zhang, F. Lu, K. Xie, R. Liu, L. Guo, S. Shao, J. Yang and D. Shi, Eur. Polym. J., 2008, 44, 3335–3343 CrossRef CAS.
- L. G. Lin, Y. Kong, G. Wang, H. M. Qu, J. R. Yang and D. Q. Shi, J. Membr. Sci., 2006, 285, 144–151 CrossRef CAS.
- L. G. Lin, Y. Kong, K. K. Xie, F. W. Lu, R. K. Liu, L. Guo, S. Shao, J. R. Yang, D. Q. Shi and Y. Z. Zhang, Sep. Purif. Technol., 2008, 61, 293–300 CrossRef CAS.
- R. Cao, X. Zhang, H. Wu, J. Wang, X. Liu and Z. Jiang, J. Hazard. Mater., 2011, 187, 324–332 CrossRef CAS.
- B. Li, D. Xu, Z. Y. Jiang, X. F. Zhang, W. P. Liu and X. Dong, J. Membr. Sci., 2008, 322, 293–301 CrossRef CAS.
- R. Qi, Y. Wang, J. Chen, J. Li and S. Zhu, Sep. Purif. Technol., 2007, 57, 170–175 CrossRef CAS.
- R. B. Qi, Y. J. Wang, J. Chen, J. D. Li and S. L. Zhu, J. Membr. Sci., 2007, 295, 114–120 CrossRef CAS.
- R. D. Noble, J. Membr. Sci., 2011, 378, 393–397 CrossRef CAS.
- J. Chen, J. D. Li, R. B. Qi, H. Ye and C. X. Chen, J. Membr. Sci., 2008, 322, 113–121 CrossRef CAS.
- H. M. Qu, Y. Kong, H. L. Lv, Y. Z. Zhang, J. R. Yang and D. Q. Shi, Chem. Eng. J., 2010, 157, 60–66 CrossRef CAS.
- Z. Yang, W. Zhang, J. Li and J. Chen, Sep. Purif. Technol., 2012, 93, 15–24 CrossRef CAS.
- H. R. Allcock, Science, 1976, 193, 1214–1219 CAS.
- H. R. Allcock and R. L. Kugel, J. Am. Chem. Soc., 1965, 87, 4216–4217 CrossRef CAS.
- H. R. Allcock, R. L. Kugel and K. J. Valan, Inorg. Chem., 1966, 5, 1709–1715 CrossRef CAS.
- H. R. Allcock, D. B. Patterson and T. L. Evans, J. Am. Chem. Soc., 1977, 99, 6095–6096 CrossRef CAS.
- W. Sun, T. Chen, C. Chen and J. Li, J. Membr. Sci., 2007, 305, 93–102 CrossRef CAS.
- R. B. Qi, Y. J. Wang, J. D. Li, C. W. Zhao and S. L. Zhu, J. Membr. Sci., 2006, 280, 545–552 CrossRef CAS.
- B. Li, W. Liu, Z. Jiang, X. Dong, B. Wang and Y. Zhong, Langmuir, 2009, 25, 7368–7374 CrossRef CAS.
- B. Li, S. Yu, Z. Jiang, W. Liu, R. Cao and H. Wu, J. Hazard. Mater., 2012, 211–212, 296–303 CrossRef CAS.
- L. G. Lin, Y. Z. Zhang and Y. Kong, J. Colloid Interface Sci., 2009, 339, 152–159 CrossRef CAS.
- D. Mitra, Sep. Purif. Rev., 2011, 41, 97–125 CrossRef.
- L. M. Vane, V. V. Namboodiri and T. C. Bowen, J. Membr. Sci., 2008, 308, 230–241 CrossRef CAS.
- C. M. Hansen, Ind. Eng. Chem. Prod. Res. Dev., 1969, 8, 2–11 CAS.
- R. P. Kambour, C. L. Gruner and E. E. Romagosa, J. Polym. Sci., Polym. Phys. Ed., 1973, 11, 1879–1890 CrossRef CAS.
- W. P. Liu, B. Li, R. J. Cao, Z. Y. Jiang, S. N. Yu, G. H. Liu and H. Wu, J. Membr. Sci., 2011, 378, 382–392 CrossRef CAS.
- Q. G. Zhang, B. C. Fan, Q. L. Liu and A. M. Zhu, J. Membr. Sci., 2011, 366, 335–341 CrossRef CAS.
|
This journal is © The Royal Society of Chemistry 2012 |
Click here to see how this site uses Cookies. View our privacy policy here.