DOI:
10.1039/C2RA20884A
(Review Article)
RSC Adv., 2012,
2, 8867-8882
Recent advances of sodium borohydride reduction in coal water slurry desulfurization: integration of chemical and electrochemical reduction
Received
9th May 2012
, Accepted 21st June 2012
First published on 21st June 2012
Abstract
Clean fuel technologies have been widely developed in current society because fuel combustion can directly bring about the emission of hazardous gasses, i.e. SO2, sulfate particulate matter (SPM), resulting in environmental pollution and other related problems that endanger public heath and community property; as well as reducing the life of the engine due to corrosion. The research efforts for developing conventional hydrodesulfurization (HDS) and alternative desulfurization methods such as selective adsorption, biodesulfurization, oxidation/extraction (oxidative desulfurization), etc. for removing these refractory sulfur compounds from liquid fuel products are on the rise. The reductive desulfurization method under ambient conditions has rarely been researched. This paper reviews the current status of various desulphurization techniques being studied worldwide. It presents an overview of novel emerging technologies of chemical and electrochemical reduction (CECR) for deep desulfurization of coal water slurry (CWS) so as to provide a new way of thinking about ultra-clean fuel technology.
 Yafei Shen | Yafei Shen (Josh) got his M.S. (2005) degree in applied chemistry from Nanjing University of Information Science & Technology. Then, he worked as a M.S. (2009–2012) student in Shanghai Jiaotong University (SJTU) on the major of environmental engineering. At present, he undertakes research work on environmental chemistry, energy & chemical engineering, especially in clean coal technology, flue gas desulfurization. |
 Xunyue Liu | Xunyue Liu was born in 1987, Shandong, China. She got her B.S. (2009) degree in Biotechnology from Weifang University. Currently, she is diligently studying Ph.D. degree on the major of environmental toxicology at Institution of Nuclear Agricultural Science in Zhejiang University. She is interested in environmental biochemistry & agricultural biotechnology. |
 Tonghua Sun | Tonghua Sun received his Ph.D. (2004) degree in environmental engineering from SJTU, China. Currently, he is a research professor at the School of Environmental Science & Engineering in SJTU. His research interests include industrial pollutants treatment, energy & chemical engineering and flue gas desulfurization. In the past, he directed the National “863” Project, the Baosteel COREX gas desulfurization project, etc. |
 Jinping Jia | Jinping Jia earned his B.S. (1983) & M.S. (1986) degrees in applied chemistry from University of Science & Technology of China (USTC). Then, he received Ph.D. (1999) degree in material science from SJTU. He is currently a professor at the School of Environmental Science & Engineering in SJTU. He is interested in the related works on the study of environmental electrochemical method, the study of new technology in monitoring and toxicity of the environmental pollutants, new technology of clean production and crafts, TiO2 photocatalytic technology. |
1. Introduction
Sulfur dioxide (SO2) emission from coal-fired power plants, refinery operations and vehicles has been implicated as a cause of acid rain and other air pollution related problems.1Fig. 1 presents the formation of acid precipitation (rain, snow, etc.) from SO2 and NOx. It can cause significant damage to landmarks (e.g. historical relics), modern constructions, plants (e.g. forests), animals (e.g. fish), and so on. Meanwhile, acid rain always falls in the economically developed and densely populated region at the southeast of China.
 |
| Fig. 1 The formation of acid rain from SO2 and NOx. | |
According to the report on the state of the environment in China by the Ministry of Environmental Protection (MEP), national SO2 emissions decreased continuously from a maximum of 2.59 billion tons in 2006 to 2.17 billion tons in 2010, that is, a 14% reduction had been achieved in relation to the 2.55 billion tons in 2005, mainly through flue gas desulfurization (FGD) in more than 70% of coal-fired power plants.2 In the recent years, coal is still the predominant fossil fuel. Clean coal technology is being applied and popularized at an unprecedented rate in China.3 Coal water slurry (CWS) is a coal-based clean liquid fuel, which is currently prepared with refined coal. In the course of coal washing, most of the ash and inorganic sulfur can be removed, so the concentration of ash and SO2 will be lower than that of the original coal by combustion and gasification. But with the more restricted environment legislation and more complex coals being used to make the slurry, the release of sulfur is greater, sometimes beyond the requirements of environment protection. As a clean liquid coal, desulfurization of CWS prior to combustion can save significant costs in follow-up FGD.4
A number of physical, microbial, chemical, pyrolytic, and radiation assisted oxidative desulfurization methods have been reported. Physical processes such as froth flotation and magnetic force separation can only remove a portion of pyritic sulfur but cannot reduce organic sulfur.5–8 Besides, some physical processes are not cost effective methods.9 Microbial desulfurization of coal is usually carried out with chemolithoautotrophic bacteria such as T. thiooxidans and T. ferrooxidans.10 However, both of the microorganisms for leaching organic sulfur from coal are not effective.11 Coal pyrolysis can remove most sulfurs, including inorganic and organic forms, but requires rigorous operating conditions, e.g., the treatment temperature is generally higher than 600 °C.12,13 Ultrasonic, microwave, and γ-ray radiolysis assisted oxidative desulfurization of coal, operated at low temperature conditions (<100 °C), have been reported by many workers with organic sulfur reduction in the 30–60% range.4,14–16 However, these processes involve some drawbacks that are hard to overcome, such as large energy consumption and the obvious loss of caloric value. Thus, chemical oxidative methods at low temperature conditions have been extensively studied (Table 1). Exciting as these researches are, they also have their problems. Firstly, all these chemical desulfurization approaches mentioned above have involved oxidation reactions. As shown in Table 1, little literature has been published on the reductive desulfurization of coal, especially at mild conditions. Secondly, these treatments are tedious and costly because of their long duration, high reaction temperature, large reagent consumption and miscellaneous approach. Thirdly, some chemical reagents, such as hydrogen peroxide and nitric acid are poisonous and highly corrosive. Finding a simple, effective, technologically feasible, economically viable and commercially exploitable method of coal desulfurization, capable of simultaneously removing inorganic and organic sulfur from coal without any loss of calorific value is of immediate industrial and environmental significance.16
Table 1 Various chemical desulfurization methods of coal 41
Author |
Reagent |
Time |
Sulfur removal |
Ref. |
Mukherjee |
H2O2 + H2SO4 |
4 h |
Using 15% (vol.) H2O2 and 0.1N H2SO4: 45% of total sulfur removed (complete removal of inorganic sulfur and 31% removal of organic sulfur) |
20
|
Ozdemmir |
Chlorine in CCl4 + H2O |
6 h |
Using 0.033 L min−1 chlorine flow rate at ambient temperature and pressure: All pyritic and sulphate sulfur removed and 30% organic sulfur removed |
21
|
Ahnonkitpanit and Prasassarakich |
Aqueous H2O2 + H2SO4 |
2 h |
Using 15% H2O2 and 0.1N H2SO4 at 40 °C: 48.7% total sulfur removed (97% pyritic, 89% sulphate and 7.1% organic sulfur removed) |
22
|
Krzymien |
Aqueous CuCl2 |
48 h |
Using 10 mL of 10% (vol.) CuCl2 at 200 °C, 100% sulfur removed |
23
|
Sonmez and Giray |
Peroxy acetic acid |
72 h |
45% sulfur removed from Gediz lignite; 85% sulfur removed from Cayirhan lignite |
24
|
Chandra |
Atmospheric oxidation |
106 days |
44% sulfur removed (36% organic sulfur removal) |
25
|
Steinberg |
O3 + O2 |
1 h |
Using a flow rate of 200 mL min−1, 1% O3 at 25 °C, 20% sulfur removed. |
26
|
Chaung |
Dissolved oxygen and alkalis:NaHCO3, Na2CO3 and Li2CO3 |
1 h |
0.2M alkali solution with 3.4 atm O2 partial pressure at 150 °C. Na2CO3:72% of sulfur removed; Li2CO3: 73.1% of sulfur removed; At 0.4 M NaHCO3: 77% of sulfur removed. |
27
|
Liu |
Aeration + NaOH, HCl |
5 h |
Using 0.25 M NaOH at 90 °C with aeration rate of 0.136 m3/h and 0.1 N HCl solution: 73% organic sulfur removed; 83% sulfide sulfur removed; 84% pyritic sulfur removed. |
28
|
Zaidi |
NaOH |
3 h |
Using 0.2 N NaOH at 70 °C, 36.2% sulfur removed |
29
|
Aarya |
NaOH |
8 h |
Using 100 g dm−3 NaOH at 80 °C, 30% sulfur removed |
30
|
Rodriguez |
HNO3 |
2 h |
Using 20% HNO3 at 90 °C, 90% inorganic and 15% organic sulfur removed |
31
|
Prasassarakich and Thaweesri |
Sodium benzoxide |
90 min |
Using 600 mL sodium benzoxide at 205 °C, 45.9% sulfur removed (83.7% sulphate, 68.6% pyritic, 33.3% organic sulfur removed) |
32
|
Yang |
NaOH |
60 min |
Using 10 wt% NaOH at 250 °C: 55% sulfur removed (95% pyritic and 33% organic sulfur removed) |
33
|
Kara and Ceylan |
Molten NaOH at different temperatures |
30 min |
Using 20 wt% NaOH at 450 °C: 83.5% sulfur removed |
34
|
Ratanakandilok |
Methanol/water and methanol/KOH |
90 min |
Using 2% methanol and 0.025 g KOH/g coal at 150 °C: 58% total sulfur removed (77% sulphate, 47% pyritic and 42% organic sulfur removed) |
35
|
Aacharya |
Thio-bacillas, ferro-oxidants |
30 days |
91.81% sulfur removed from lignite, 63.17% sulfur removed from polish bituminous coal, 9.41% sulfur removed from Assam coal |
36
|
Ali |
H2O2, NH4OH, K2Cr2O7 and CH3COOH |
30 min |
50–90% of sulfur removed, depending on concentration and solvent. |
37
|
Baruah |
Water |
120 h |
77.59% pyritic sulfur removed with aqueous leaching at 45 °C. |
38
|
Hamamci |
Fe(NO3)3·9H2O |
12 h |
Using 50 mL of 1 M solvent at 70 °C, 72.2% total sulfur (96.6% pyritic sulfur) removal |
39
|
Li and Cho |
NaClO |
2 h |
Pittsburgh No.8 coal: More than 70% of pyritic sulfur removal was achieved at the optimum conditions of 0.4 M hypochlorite, 0.4 M NaOH, and 90 °C. |
40
|
Li |
NaBH4 |
1 min |
Using 1.6 mM of NaBH4 concentration, −109 μm of particle size, neutral pH of initial media, 1 min of treated time, 100 rpm of shaking rate, 30 °C of temperature: 23.8% and 59.0% reduction in the pyritic sulfur, 70.4% and 100% reduction in the sulfate sulfur, 11.0% and 15.0% reduction in the organic sulfur, and 31.3% and 40.8% reduction in the total sulfur for the YZ coal and the YS coal, respectively. |
19
|
However, a method for removing sulfur compounds from gasoline was reported involving the conversion of sodium metaborate (NaBO2) to sodium borohydride (NaBH4) by electrochemical reduction and the incorporation of a type of metal compound. The desulfurization efficiency was 48.1%.17 Guo18 had performed research on borohydride potassium (KBH4) as a reducing agent in order to remove benzothiophene sulfur in gasoline. Li19 conducted a new desulfurization process of NaBH4 reduction for high-sulfur coals of Yanzhou and Yanshan in China. The combustion characteristics were slightly improved after treatment. This research revealed the potential of metal borohydride (KBH4, NaBH4, etc.) for reductive desulfurization. This review will present chemical and electrochemical works for CWS desulfurization via sodium borohydride reduction.
2. Chemical reduction
2.1. Hydrogenation reduction
The current widely utilized method of industrial reductive desulfurization of fuels is hydrodesulfurization (HDS), which is a catalytic process under high temperature and pressure conditions.42 The HDS reaction in refineries is carried out in trickle-bed reactors. These reactors are commonly operated at temperatures in the range 300–450 °C, and at H2 pressures of 3.0–5.0 MPa, usually with CoMo/Al2O3 or NiMo/A12O3 catalysts.43,48 This makes HDS a very costly option for deep desulfurization. Scheme 1 shows the HDS mechanism of dibenzothiophene (DBT) at 300 °C and 102 atm in the presence of CoMo/Al2O3. Moreover, HDS is not effective for removing heterocyclic sulfur compounds such as DBT and its derivatives, especially 4, 6-dimethyldibenzothiophene (4, 6-DMDBT).49 Interest in HDS was initially stimulated by the availability of hydrogen from catalytic reformers.44 Typically, the HDS process involves catalytic treatment with hydrogen to convert the various sulfur compounds to H2S and sulfur-free organic compounds at high temperature and partial pressure of hydrogen.45,46 Conventional catalytic HDS method for reducing sulfur content requires severe conditions of operation. In refineries, the H2S resulting from the HDS reaction is eventually converted to elemental sulfur (S) by a modified version of the Claus process.47Fig. 2 presents the Claus process for elemental S production from waste H2S gasses.
 |
| Fig. 2 The modified version Claus process for elemental S production from H2S gasses. | |
 |
| Scheme 1 HDS of DBT at 300 °C and 102 atm in the presence of CoMo/Al2O3.49 | |
Under these harsh conditions, olefins get hydrogenated, leading to a loss of octane rating and excess hydrogen consumption. Under mild HDS conditions, H2S can react with olefins in the reactor to create recombinant mercaptans which are linear or branched thiols of typically 5–12 carbons. The formation of recombinant mercaptans causes sulfur to be retained in the product, limiting the effectiveness of the HDS process. Further research in HDS catalysis and process designs are being carried out so as to increase the sulfur removal and still maintain the fuel quality at some minimum specification.44 In general, when the unpaired electrons of the sulfur can resonate with the pi electrons of the organic structure, the energy of the carbon-sulfur bond (C–S) becomes practically identical with that of the carbon-carbon (C–C) bond.50 It leads to a reduction in the selectivity of the HDS process, and hydrogenation of carbon-carbon bonds happens. Saturated hydrocarbons lead to a lower-grade fuel, and require additional processing steps.
There are several constraints in the HDS process. Meeting the sulfur requirement for gasoline is believed to be the greatest challenge for the refining business requiring substantial revamps to equipment or even construction of new units. This is due to the fact that most of the gasoline production in the market today comes from cracked stocks that contain a larger concentration of compounds with aromatic rings and high olefin content, thus making sulfur removal more difficult. The need to desulfurize the cracked stocks in addition to the straight-run streams is forcing the refiners to choose the most cost-effective technology.51–56 Although HDS processes have dominated desulfurization of FCC gasoline/diesel in the past their cost and the requirements of the upcoming strict fuel specifications combine to motivate the development of innovative process technologies.
2.2. NaBH4 reduction
Reductant costs, strict equipment and operation conditions have seriously restricted the development and utilization of chemical reduction methods by HDS. Sodium borohydride (NaBH4) is a versatile reducing agent used in many industrial processes. It releases hydrogen as a consequence of hydrolysis. This is a quick reaction at normal pressure and temperature (NPT). Four moles of protonic hydrogen come from borohydride, and four moles of protons come from water.57 Also, it is the cheapest metal hydride and easy to store and dispose of.58
As mentioned above, Li proposed a new desulfurization process with sodium borohydride reduction for high-sulfur coals.19 After that, we researched the use of NaBH4 for deep desulfurization of CWS and gasoline in depth and the common influencing factors such as reductant (NaBH4) concentration, treatment time, coal particle size, reaction temperature, shaking rate, and initial pH value have been taken into account. Ultimately, optimized reaction conditions were obtained. Fig. 3 shows the general desulfurization procedure of coal slurry via NaBH4 reduction by Ni catalysis under ambient conditions. At first, NaBH4 can react with NiCl2 to generate the Ni2B catalyst. Secondly, NaBH4 can rapidly hydrolyse with the Ni2B catalyst under ambient conditions. Finally, the produced H2 or active hydrogen atom can translate sulfur compounds into H2S by catalytic reduction, releasing from coal particles. Fig. 4 presents our research work on CWS desulfurization by NaBH4 reduction. It could be found that the chemical reaction easily occurred in the aqueous phase and the electrolysis of NaBH4 was a key step to the desulfurization of CWS (Fig. 4A). Significantly, compared with catalysis, there was no evident improvement when using ultrasonics to enhance the desulfurization efficiency. Meanwhile, the desulfurization efficiency of CWS depended on the hydrogen ratio and hydrolysis rate of borohydrides. In Fig. 4B, the hydrolysis rate of KBH4 under Ni catalysis was slower and more stable than NaBH4, resulting in a lower desulfurization efficiency. After treatment, the removed sulfur compounds were converted into H2S (Fig. 4C). The hydrogenation and deashing exceeded to the decarbonization, which contributed to the slightly improvement of combustion characteristics (i.e. ignition temperature, calorific value).
 |
| Fig. 3 General procedure of liquid coal desulfurization via NaBH4 catalytic reduction. | |
 |
| Fig. 4 Mechanism (A), results (B), and GC analysis (C) of NaBH4 reduction for CWS desulfurization.4,41 | |
Moreover, the reaction details of NaBH4 hydrolysis by Ni catalysis41,59 are shown as the following eqn. (1)–(3):
| 4NaBH4 + 9H2O + 2NiCl2 → Ni2B↓ (black precipitates) + 3H3BO3 + 4NaCl + 12.5H2↑ | (1) |
| NaBH4 + 2H2O → NaBO2 + 8H* (4H2, catalytic hydrolysis) | (2) |
| 4NaBO2 + 11H2O → Na2B4O5 (OH)4·8H2O (sodium borate) + 2NaOH | (3) |
In the process of desulfurization, pyritic sulfur (FeS2) widely existing in the coals is removed according to below eqn. (4)–(6).19
| FeS2 + 2H* → Fe + H2S↑ + S | (4) |
| H2S + 2NaOH → Na2S + 2 H2O | (5) |
|  | (6) |
Since NaBH4 had high reducing property, the oxygen functional groups of OS (S
O, –SO2−, etc.) were reduced into the non-oxygen functional groups (C–S, etc.) by catalytic hydrogenation and hydrolysis. After that, the activated hydrogen (H*) produced by NaBH4 hydrolysis attacked the C–S bond, accordingly organic sulfur compounds were converted into H2S and released from the coal (Fig. 5).
 |
| Fig. 5 FT-IR analysis of the solid CWS samples before and after NaBH4 reduction.41 | |
As mentioned above, NaBH4 reduction can be better utilized for oil fuel desulfurization due to the good water solubility of NaBH4. The reducing reaction occurred in the aqueous phase, so the catalysts and by-products can be easily separated and recycled from the fuels after treatment. As Fig. 6A shows, catalytic hydrolysis of the reductants occurs in the aqueous phase, while catalytic reduction takes place in the oil phase. The desulfurization procedure very conveniently includes the two steps of reduction and separation (Fig. 6C). In addition, the desulfurization efficiency of gasoline is proportional to the hydrolysis ratio of NaBH4 and hydrogenation ratio (Fig. 6B).
 |
| Fig. 6 Mechanism (A), results (B), and procedure (C) of NaBH4 reduction for gasoline desulfurization.59 | |
3. Electrochemical reduction
Electrochemical desulfurization (ECDS) technology has been explored to remove sulfur by electrochemical oxidation or the reduction of sulfur compounds in fossil fuels.60–65 This technology is able to remove sulfur at relatively low temperatures and pressures, which potentially makes the process much less energy intensive and more economical than conventional technologies. In ECDS, there is also a degree of freedom to control products by adjusting the applied potential.
Promising results have been reported using this technique. However, the ECDS technology is still in its early development stage, and further research is needed to push this technology toward commercialization. With the intension to facilitate the research and development, we reviewed the progress of this technology, and discussed the principles and technology development for the electrochemical desulfurization of fossil fuels. As the organic compositions of coal, petroleum products, and bitumen are similar, a method for one can provide insight into methods for the others.
Several methods have been employed for electrochemical desulfurization, which can be generally grouped into two categories. The methods that facilitate electrochemical desulfurization by applying a fixed potential or drawing a fixed current can be categorized as static methods. Other methods where the applied potential changes over time, such as linear or square wave voltammetry can be categorized as dynamic methods. Bio-electrochemical desulfurization (BECDS) , which uses microorganisms such as bacteria to mitigate the sulfur removal in fossil fuels, is classified as an independent method.66
3.1 Common electroreduction
As early as 1960s, Sterber proposed electrochemical reduction (ECR) for coal desulfurization. However, ECR methods were inefficient and rigid without reasonable reductants. Later on, Lalvani62,67 studied the electrochemical oxidation (ECO) for coal desulfurization. It can be easy to find excellent oxidizers and get a high desulfurization efficiency. After that, ECO has become the prevailing ECDS method in the world, while ECR is rarely researched. Oxidation in the anode is the key step for ECDS. During the oxidation process, the coal structure is usually destroyed to an appreciable, or significant, extent.68–70 While ECR methods can utilize cathodic reduction to change some chemical compounds into strong reducing agents which convert S into H2S and S2−, thus releasing S from coals. Meanwhile, ECR can proceed under mild conditions, as well as producing high-purity hydrogen.60,61,71 Thus, this method has a prospective future for coal desulfurization and hydrogen production, if outstanding reductants are found.
ECDS is based on the reduction and/or oxidation of sulfur-containing compounds in fossil fuels.72–77 The electrochemical cathodic reduction of organic sulfur compounds (expressed as R–SH) leads to the formation of H2S, as shown in eqn. (7):
| R–SH + 2H+ +2e− = R–H + H2S | (7) |
The resulting H2S can be removed by a gas/liquid separation process or the aformentioned Claus process. The electrochemical anodic oxidation of organic sulfur compounds is expressed in eqn. (8):
| R–SH + 4OH− − 4e− = R–H + SO2 + 2H2O | (8) |
In eqn. (8), SO2 represents RSH oxidation products, which might be O-containing RSH molecules (e.g. RSOxH). The addition of oxygen to sulfur-containing compounds increases the polarity of the sulfur compounds so that they can be removed by extraction with polar solvents or by adsorption with polar adsorbents.
Electrooxidation of CWS occurred on the interface between coal particles and electrode, thus sulfur macromolecules inside the coal were not removed by electrochemical desulfurization. Decreasing the size of the coal particles can improve electrolysis desulfurization effects,78 however, there are still some organic sulfur (OS) structures inside coal particles, e.g. thioether, thiophenol, thiophene, and so on, leading to the low removal ratio of OS in coal.79 Some researchers found that CWS electrolysis in water-organic solvents such as methanol, ethanol and acetone increased the desulfurization effect.80 The desulfurization efficiency of CWS was improved with the addition of organic solvents as the organic solvent used would extract some of the OS, and lower the energy of some chemical bonds.79 The conductivity of these organic solvents was less than that of water with electrolyte, so that the electrolysis process was also influenced by them. On the other hand, CWS electrolysis generates pure hydrogen at the cathode. If this hydrogen reacted with the OS, electrolysis HDS was achieved on the cathode. But there is no appropriate hydrogen donating solvent at the cathode, and the hydrogen donating effects of water is not obvious. Thus, it is necessary to seek the appropriate hydrogen donating solvents or electrodes for hydrogen evolution at the cathode to achieve the HDS reaction. At present, we investigated the ECDS of CWS in the mixed solvent water–alcohol (H2O–C2H5OH). Compared with alcohol, water is the prime substance providing the protons. A mass of protons in the electrolyte is beneficial for coal hydrogenation in the cathode, while NaBH4 reacts more easily with water than with sulfides in coal. Therefore, the water content in the electrolyte has a significant effect on desulfurization efficiency (Fig. 7a). Oxygen in water molecules and sulfur in sulfides have one electron pair, but the polarity of a water molecule is stronger than that of a sulfide, so NaBH4 is prone to react with water. It can be concluded that a low water content of the electrolyte is beneficial for the ERD process. On the contrary, the hydrogen yield shows a positive correlation with water content (Fig. 7b).81
 |
| Fig. 7 Desulfurization of CWS under atmospheric conditions via sodium metaborate (NaBO2) electroreduction in the isolated system. (a. Effect of water content on desulfurization efficiency; b. Effect of water content on hydrogen yield). Process conditions: 12 g L−1 of NaBO2, 3.0 V of electrolytic voltage, 5 h of electrolytic time, 50 g L−1 of CWS, 140 mesh of coal particle size, and 1.0 g L−1 of NaOH.81 | |
3.2. NaBO2 electroreduction
On the whole, NaBH4 reduction shows incomparable advantages: mild conditions, short reaction time, high hydrogen donating effect and high efficiency for reductive desulfurization,4,19 but it is also an expensive, incomplete reaction with excessive waste. NaBO2,82 the end product of both the hydrolysis and electrooxidation of NaBH4,17 is much cheaper and more stable. It is of great importance to convert NaBO2 into NaBH4. Electrochemical methods can realize boron recycling only by the process of discharge and recharge,81 that is to say, it is a good idea to combine chemical and electrochemical methods of realizing boron (B) recycling for coal desulfurization by NaBH4 reduction. It can resolve the problem of deoxidizer costs and realize the recycling of the filtrate. Besides, this kind of clean reduction method only uses electricity and green solutions (H2O), so it reduces additional pollution, realizing reasonable application and sustainable development of resources (Scheme 2). NaBO2 electroreduction for fuels desulfurization is based on converting NaBO2 into NaBH4 by electrolysis in the cathode. Then, sulfur (S) can be reduced into H2S or S2−, separated from fuels.
 |
| Scheme 2 Green chemical pathway of converting NaBO2 into NaBH4 to realize B recycling | |
3.2.1 Non-isolated system.
A non-isolated system can be widely used in the electrochemical reaction, which is simply operated. The cathode and anode can simultaneously present reductive and oxidative performance. In addition, parts of the sulfur compounds in fuels can be oxidated into SO42− and removed easily by washing and filtering. As Scheme 3 and Fig. 7 show, the reductive electrode basically removes OS from the mercaptan (R–SH) and the thioether (R–S–R¢) (eqn. 9–14). Electrolysis in alkaline systems allows OH− lose charges on the anode surface and create active oxygen free radicals (H2O˙, O˙, H2O2˙, O2˙, etc.). These active free radicals attack organic sulfur (OS) in coals, which is oxidated into polysulfide. Furthermore, the polysulfide is oxidated into sulfoxide (R–S
O–R¢) and sulphone (R–O
S
O–R¢). Then sulphone is converted into sulfonic compounds or SO42− by hydrolysis (eqn. 15–19).83,84 The oxidizing electrode removes fat sulfur and thiophenic sulfur. The participation of anodic oxidation is beneficial for OS reduction. The desulfurization efficiency of CWS increased with the increase of electrolytic time (Fig. 8) | Cathode: BO2− + 6H2O + 8e− → BH4− + 8OH− | (9) |
| BH4− + 2H2O → BO2−+ 8H* (active hydrogen atom) | (10) |
| (1) Pyrite sulfur (PS) removal: FeS2 + 2H* → Fe + S + H2S↑ 4,19 | (11) |
| (2) Fat-sulfur removal: 2H* + R–SH → R–H + H2S↑ | (12) |
| 4H* + R–S–R¢ → R–H* + R¢–H* + H2S↑ | (13) |
| H2S + H2O2 → S↓ + 2H2O | (14) |
| Anode: 4OH− − 4e− → O2[O] (active oxygen free radicals) + 2H2O | (15) |
| (3) Fat-sulfur removal: 2R–SH + [O] → R–S–S–R + H2O | (16) |
| [O] + R–S–S–R → R–S–S(O)R¢ | (17) |
| 4[O] + R–S–S–R → R–S(O2)–S(O2)R¢ | (18) |
| R–S(O2)–S(O2)R¢ + 6H2O → R–OH + R¢–OH +10H+ + 2SO42− | (19) |
 |
| Fig. 8 Schematic diagram of ECD process for CWS in the non-isolated alkaline NaBO2 system.84 | |
 |
| Scheme 3 Electrolysis desulfurization of CWS without membrane83 | |
(4) Dibenzothiophene (DBT) sulfur removal (special example inScheme 4)
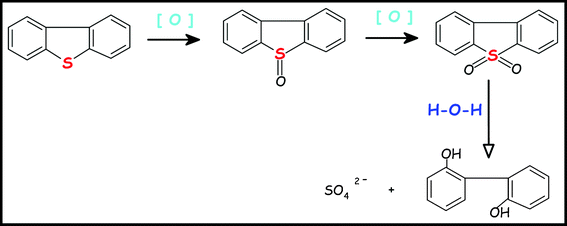 |
| Scheme 4 Sulfur removal pathway of DBT by electrooxidation in the alkaline NaBO2 electrolyte | |
3.2.2 Isolated system.
According to the principle of different electric charges attracting each other, the negative charge of BO2− will move to the anode, resulting in a decrease of BO2− concentration near the cathode, which needs to be adjusted for. Meanwhile, a produced negative charge (BH4−) may be attracted to the anode, resulting in BH4− being consumed because of anodic oxidation.82 Before Fairbridge et al.85 described a desulfurization process using a polymer electrolyte membrane system. The process involved electrocatalytic hydrogenation of the organic compound through electroreduction in the cathode compartment, proton production through water electrolysis in the anode compartment, and proton transfer from anode to cathode through the membrane, as shown in Fig. 9. In the process, sulfur is freed from the organic compound through electroreduction and then combines with hydrogen to form hydrogen sulfide that can be easily removed. An advantage of this system is that it can operate at low temperatures and pressures relative to conventional HDS conditions. Consequently, the isolated apparatus 1 or 2 in Fig. 9 & 10 is designed for the ERD. It can avoid anions (BH4−, BO2−, etc.) moving to the anode and can also decrease the coal calorific value loss caused by anodic oxidation.82 The innovative isolated apparatus can surmount the above disadvantages and completely utilize the oxidation. The disadvantage of isolated apparatus 1 is that it can not be utilized for high concentrations of CWS due to blockage of the ion exchange membrane, although it is used for gasoline desulfurization.59 However, the isolated apparatus 2, without an ion exchange membrane, designed by us is an alternative for any liquid fuel desulfurization. We found that the NaBH4 concentration and desulfurization efficiency of CWS increased with the electrolytic time, while the relationship of NaBH4 yield and electrolytic time accorded with a first order kinetic reaction (Fig. 10).82
 |
| Fig. 9 ECDS in the alkaline NaBO2 electrolyte with an ion exchange membrane. | |
 |
| Fig. 10 ECDS in the alkaline NaBO2 electrolyte without an ion exchange membrane. | |
In the cathode, NaBO2 was transformed into NaBH4 by electrochemical reduction, and the sulfur compounds in CWS were converted into H2S and released from the coal particles. In the anode, the removed sulfur or H2S was partially converted into S or SO42−, leaching and filtering away from the electrolytic cell (Fig. 11).
 |
| Fig. 11 Schematic of ECDS in the alkaline NaBO2 system without a cation-exchange membrane.82 | |
4. Integrative process of CECR
As described above, no matter whether chemically reductive desulfurization by sodium borohydride (NaBH4) reduction or electrochemical reductive desulfurization by sodium metaborate (NaBO2) electroreduction was performed, the desired desulfurization efficiency for CWS was obtained. Obviously, it is necessary to combine the NaBH4 reduction with the NaBO2 electroreduction for CWS desulfurization to realize boron (B) recycling and the integrative process of chemical and electrochemical reduction (CECR), described as follows. At first, NaBH4 reduction can be used for fuel desulfurization. Then, the by-product of NaBO2 can be reduced into NaBH4 once again by electroreduction. This desulfurization system can be easily realized, while some problems, such as operation expenses, electrochemical efficiency, which should be resolved in further works. According to our research, the integrative process of CECR for coal or CWS can be carried out as in the following industrial schematic. Firstly, raw coal can be crushed to a certain particle size. Then, pulverized coal is made into raw CWS by adding water. After that, ECDS of the prepared CWS is carried out by the CECR apparatus. Significantly, the filtrate can be reused for coal washing at the first step of the industrial process (Fig. 12).
 |
| Fig. 12 Schematic diagram of integrative chemical and electrochemical desulfurization process of CWS via NaBH4 reduction (ECDS mechanism, ECDS experimental apparatus, electrode preparation and industrial procedure). | |
5. Future outlook
(1) Ionic liquids (utilization and recycle)
Ionic liquids (ILs) are organic salts which are typically a liquid at ambient temperature resulting from the combination of organic cations and various anions, and have aroused increasing interest owing to their unique properties such as negligible vapor pressure, good dissolving ability, a wide electrochemical work window and high ionic conductivity, thus they have been utilized as a green solvent in many fields.86–88 In the patent and academic literature, the term “ionic liquids” now refers to liquids composed entirely of ions that are fluid around or below 100 °C.89 Recent literature describes their potential applications for embalming fluids,90 in ion drives for space travel,91 for desulfurization of fuels.92
Gong93 has investigated three kinds of ILs including 1-butyl-3-methylimidazolium chloride (C8H15N2Cl), 1-butyl-3-methylimidazolium bromide (C8H15N2Br) and N-butylpyridinium bromide (C9H14NBr) for ECDS of CWS in the HCl electrolyte. The desulfurization reaction occurred in the electrolysis apparatus with or without a membrane, as shown in Fig. 13A. With the addition of three ILs, electrolysis desulfurization efficiency increased, improving organic sulfur removal. CWS electrolysis on the cathode achieved hydrogenation of coal under mild conditions, and electrolysis desulfurization of ILs with a hexatomic ring as an additive was higher than that of the five-membered ring (Fig. 13B, 13C). Firstly, ILs used as solvent extracted parts of the sulfur structure from solid to liquid phase, thus the desulfurization reaction occurred easily on the electrode surface. Secondly, during electrolysis desulfurization on the cathode, the ILs acted as a kind of hydrogen donating solvent and accelerated hydrogenation of the organic sulfurs’ structure.
 |
| Fig. 13 Desulfurization of electrolyzed coal water slurry in HCl system with ionic liquid addition 94 | |
Meanwhile, ILs have been examined for possible applications related to green chemical processes, such as liquid/liquid extraction, gas separations, electrochemistry and catalysis.94–102 These liquids are easy to handle because of their non-volatility, non-flammability, and high thermal stability. The ILs have been applied for the selective removal of sulfur from fuels in recent years because ILs are easily regenerated from adsorbed S-containing compounds by distillation or by dissolution in water, where ILs are air- and moisture-stable at low temperature and non-corrosive. Hence, ILs can be used appropriately under the conditions of ECDS for liquid fuels.
(2) Electrodes (alloy or BDD, etc.)
The electrode is a significant sub-unit of electrolysis apparatus. Commonly, the oxidation and reduction reactions occur near the electrodes by electrical transfer. It is attractive for researchers to seek a high-performance electrode material (environmental friendly, low energy consumption, negative potential, etc.), in the electrochemistry field. Furthermore, alloy electrodes can be developed for ECDS because of their hardness, low expense, corrosion resistance, and so on.
Boron-doped Diamond (BDD) is another well-characterised electrode material with well known attributes, such as hardness, chemical inertness, optical transparency, high thermal conductivity and electrical conductivity (depending on the doping level).103–109 The electrochemistry on BDD is not complicated by extraneous change-transfer reactions and is stable over a wide electrochemical window,110 thereby making it an ideal substrate for electrolysis at a very negative potential in ILs.111 In the future, it is a priority to try BDD as a basal electrode material for ECDS in the alkaline NaBO2 system, reducing the electrode potential and formation of hydrogen.
Once the basal electrode is chosen, some single or composite catalysts (Ni, Co, Mo, NiMo, CoMo, etc.) can be mingled in the surface of the alloy or BDD electrode. On one hand, the development of the catalyst doped electrode will realize the catalyst recycling, reducing the process expense and secondary pollution due to the wastage of catalysts. On the other hand, it can improve the activity of catalyst and conversion efficiency.
(3) Hydrogen production
As an important energy in the current or prospective world, hydrogen is mainly a by-product of ECDS, derived from electroreduction at the cathode and hydrolysis of NaBH4, which can be easily separated and collected. The hydrogen storage properties could be enhanced by promoting the NaBH4 yield.
Acknowledgements
This work is financially supported by the National High Technology Research & Development Program of China (“863” program, Grant No. 2009AA062603). The thoughtful comments provided by anonymous editor and reviewers are greatly appreciated.
References
- C. Huang, C. A. Linkous, O. Adebiyi and A. T. Raissi, Hydrogen production via photolytic oxidation of aqueous sodium sulfite, Environ. Sci. Technol., 2010, 44, 5283–5288 CrossRef CAS.
- L. Duan, X. Ma, T. Larssen, J. Mulder and J. Hao, Response of surface water acidification in upper Yangtze River to SO2 emissions abatement in China, Environ. Sci. Technol., 2011, 45, 3275–3281 CrossRef CAS.
- W. Chen and R. Xu, Clean coal technology development in China, Energy Policy, 2010, 38(5), 2123–2130 CrossRef.
- Y. Shen, T. Sun and J. Jia, Novel desulfurization method of sodium borohydride reduction for coal water slurry, Energy Fuels, 2011, 25, 2963–2967 CrossRef CAS.
- A. Demirbas, Demineralization and desulfurization of coals via column froth flotation and different methods, Energy Convers. Manage., 2002, 43, 885–895 CrossRef CAS.
- M. S. Celik and I. Yildirim, A new physical process for desulfurization of low-rank coals, Fuel, 2000, 79, 1665–1669 CrossRef CAS.
- W. Zhao, W. J. Xu, S. T. Zhong and Z. M. Zong, Desulfurization of coal by an electrochemical-reduction flotation technique, Journal of China University of Mining and Technology, 2008, 18, 571–574 CrossRef CAS.
- M. Abdollahy, A. Z. Moghaddam and K. Rami, Desulfurization of mezino coal using combination of ‘flotation’ and ‘leaching with potassium hydroxide/methanol', Fuel, 2006, 85, 1117–1124 CrossRef CAS.
- H. G. Alam, A. Z. Mohaddam and M. R. Omidkhah, The influence of process parameters on desulfurization of Mezino coal by HNO3/HCl leaching, Fuel Process. Technol., 2009, 90, 1–7 CrossRef CAS.
- S. S. Tripathy, R. N. Kar, S. K. Mishra, I. Twardowska and L. B. Sukla, Effect of chemical pretreatment on bacterial desulphurisation of Assam coal, Fuel, 1998, 77, 859–864 CrossRef CAS.
- C. Acharya, L. B. Sukla and V. N. Misra, Biological elimination of sulphur from high sulphur coal by Aspergillus-like fungi, Fuel, 2005, 84, 1597–1600 CAS.
- Q. Liu, H. Hu, S. Zhu, Q. Zhou, W. Li, X. Wei and K. Xie, Desulfurization of coal by pyrolysis and hydropyrolysis with addition of KOH/NaOH, Energy Fuels, 2005, 19, 1673–1678 CrossRef CAS.
- Y. Qi, W. Li, H. Chen and B. Li, Desulfurization of coal through pyrolysis in a fluidized-bed reactor under nitrogen and 0.6% O2–N2 atmosphere, Fuel, 2004, 83, 705–712 CrossRef CAS.
- E. Jorjani, B. Rezai, M. Vossoughi and M. Osanloo, Desulfurization of Tabas coal with microwave irradiation/peroxyacetic acid washing at 25, 55 and 85 °C, Fuel, 2004, 83, 943–949 CrossRef CAS.
- P. S. Tripathi, K. K. Mishra, R. R. Roy and D. N. Tewary, Investigations on desulphurization of some high-sulphur Indian coals by γ-ray-induced chlorinolysis, Appl. Radiat. Isot., 2002, 56, 975–984 CrossRef CAS.
- P. S. M. Tripathi, K. K. Mishra, R. R. P. Roy and D. N. Tewari, γ-Radiolytic desulphurization of some high-sulphur Indian coals catalytically accelerated by MnO2, Fuel Process. Technol., 2001, 70, 77–96 CrossRef CAS.
- Z. Wang, S. Wang, G. Liu and W. Wang, Electrochemical method preparing sodium borohydride for gasoline desulfurization, Journal of Oil Refining and Chemical Engineering, 2007, 38((11)), 6-9 Search PubMed.
- X. Guo, S. Li, C. Yue and X. Ni, New reduction methods for removing benzothiophene organic sulfur, Journal of Applied Chemistry, 2006, 23(9), 852-987 Search PubMed (In Chinese).
- Z. Li, T. Sun and J. Jia, An extremely rapid, convenient and mild coal desulfurization new process: sodium borohydride reduction, Fuel Process. Technol., 2010, 91, 1162–1167 CrossRef CAS.
- S. Mukherjee, S. Mahiuddin and P. C. Borthakur, Demineralization and desulfurization of sub bituminous coal using hydrogen peroxide, Energy Fuels, 2001, 15, 1418–1424 CrossRef CAS.
- M. Ozdemmir, S. Bayrakceken, A. Gurses and S. Gulaboglu, Desulfurization of two Turkish lignites by chlorinolysis, Fuel Process. Technol., 1990, 26, 15–23 CrossRef.
- E. Ahnonkitpanit and P. Prasassarakich, Coal desulfurization in aqueous hydrogen peroxide, Fuel, 1989, 68, 819–824 CrossRef CAS.
- L. L. Krzymien, Complete removal of sulfur from coal using solutions containing cupric ions, Fuel, 1982, 61, 871–873 CrossRef.
- O. Sonmez and E. S. Giray, The influence of process parameters on desulfurization of two Turkish lignites by selective oxidation, Fuel Process. Technol., 2001, 70, 159–169 CrossRef CAS.
- D. Chandra, J. N. Chakrabarti and Y. V. Swamy, Auto-desulfurization of coal, Fuel, 1982, 61, 204–205 CrossRef CAS.
- M. Steinberg, R. T. Yang, T. K. Horn and A. L. Berlad, Desulfurization of coal with ozone: an attempt, Fuel, 1977, 56, 227–228 CrossRef CAS.
- K. C. Chaung, R. Markuszewesky and T. D. Wheelock, Desulfurization of coal by oxidation in alkaline solutions, Fuel Process. Technol., 1983, 7, 43–57 CrossRef.
- K. Liu, J. Yang, J. Jia and Y. Wang, Desulfurization of coal via low temperature atmospheric alkaline oxidation., Chemosphere, 2008, 71, 183–188 CrossRef CAS.
- S. A. H. Zaidi, Ultrasonically enhanced coal desulfurization, Fuel Process. Technol., 1993, 33, 95–100 CrossRef CAS.
- P. E. Araya, R. B. Ohlbaum and S. E. Droguett, Study of the treatment of sub bituminous coals by NaOH solutions, Fuel, 1981, 60, 1127–1130 CrossRef CAS.
- R. A. Rodriguez, C. C. Jul and D. D. Limon, The influence of process parameters on coal desulfurization by nitric leaching, Fuel, 1996, 75, 606–612 CrossRef CAS.
- P. Prasassarakich and T. Thaweesri, Kinetics of coal desulfurization with sodium benzoxide, Fuel, 1996, 75, 816–820 CrossRef.
- R. T. Yang, S. K. Das and B. M. C. Tsai, Coal demineralization using sodium hydroxide and acid solutions, Fuel, 1985, 65, 735–742 CrossRef.
- H. Kara and R. Ceylan, Removal of sulfur from four central Anatolian lignites by NaOH, Fuel, 1988, 67, 170–172 CrossRef CAS.
- S. Ratanakandilok, S. Ngamprasertsith and P. Prasassarakich, Coal desulfurization with methanol/water and methanol/KOH, Fuel, 2001, 80, 1937–1942 CrossRef CAS.
- C. Aacharya, R. N. Kar and L. B. Sukla, Bacterial removal of sulfur from three different coals, Fuel, 2001, 80, 2207–2216 CrossRef.
- A. Ali, S. K. Srivatsava and R. Haque, Chemical desulfurization of high sulfur coals, Fuel, 1992, 71, 835–839 CrossRef CAS.
-
B. P. Baruah, B. K. Saikia, P. Kotoky, P. G. Rao, Aqueous leaching on high sulfur sub-bituminous coals, in Assam, India, Energy Fuels, 2006, 20, 1550-1555 Search PubMed.
- C. Hamamci, F. Kahraman and M. Z. Diiz, Desulfurization of southeastern Anatolian asphaltites by the Meyers method, Fuel Process. Technol., 1997, 50, 171–177 CrossRef CAS.
- W. Li and E. H. Cho, Coal desulfurization with sodium hypochlorite, Energy Fuels, 2005, 19, 499–507 CrossRef CAS.
- Y. Shen, T. Sun, X. Liu and J. Jia, Rapid desulfurization of CWS via ultrasonic enhanced metal boron hydrides reduction under ambient conditions, RSC Adv., 2012, 2, 4189–4197 RSC.
- V. C. Srivastava, An evaluation of desulfurization technologies for sulfur removal from liquid fuels, RSC Adv., 2012, 2, 759–783 RSC.
- D. D. Whitehurst, I. Isoda and I. Mochida, Present state of the art and future challenges in the hydrodesulfurization of polyaromatic sulfur compounds, Adv. Catal., 1998, 42, 345–357 CrossRef CAS.
-
C. N. Saterfield, Heterogenous catalysis in industrial practice 2nd Ed, McGraw-Hill, New York, 1993, Search PubMedAuto Fuel Policy, Ministry of petroleum and Natural gas, Government of India 2003, http://petroleum.nic.in/autoeng.pdf.
- K. Chan, J. Jung, J. Lee, B. Sang, C. Kyungil and H. M. Sang, Hydrodesulfurization of DBT, 4-MDBT, and 4,6-DMDBT on fluorinated CoMoS/Al2O3 catalysts, Appl. Catal., A, 2000, 200, 233–242 CrossRef.
- H. Nikkolaj, M. Brosrson and T. Henrik, Activities of unsupported second transition series metal sulfides for hydrodesulfurization of sterically hindered 4,6 DMDBT and of unsubstituted DBT, Catal. Lett., 2000, 65, 196–174 Search PubMed.
-
G. T. Austin, Shreve's Chemical Process Industries, McGraw-Hill, New York 1984 Search PubMed.
- R. Shafi and G. J. Hutchings, Hydrodesulfurization of hindered dibenzothiophenes: an overview, Catal. Today, 2000, 59, 423–442 CrossRef CAS.
- M. Houalla, N. K. Nag, A. V. Sapre, D. H. Broderick and B. C. Gates, Hydrodesulfurization of dibenzothiophene catalyzed by sulfided CoO-MoO3-Al2O3: The reaction network, AIChE J., 1978, 24, 1015–1021 CrossRef CAS.
-
I. March, Advanced Organic Chemistry, John Wiley and Sons, New York, 1985 Search PubMed.
- K. Chan, J. Jung, J. Lee, B. Sang, C. Kyungil and H. M. Sang, Hydrodesulfurization of DBT on fluorinated CoMoS/Al2O3 catalysts, Appl. Catal., A, 2000, 200, 233–242 CrossRef.
- H. Nikkolaj, M. Brosrson and T. Henrik, Catal. Lett., 2000, 65, 196–174 Search PubMed.
- J. G. Michael and C. C Bruce, Ind. Eng. Chem. Res., 1991, 30, 2021–2058 CrossRef.
- K. Heeyeon, J. Jung, S. Lee and M. Heup, Hydrodesulfurization of dibenzothiophene compounds using fluorinated NiMo/Al2O3 catalysts, Appl. Catal., B, 2003, 44, 287–299 CrossRef.
-
A. S. Rappas, V. P. Nero, S. J. Decanio, US Patent 6402940, B1, 2002.
- I. V. Babich and J. A. Moulijn, Fuel, 2003, 82, 607–631 CrossRef CAS.
- P. Krishnan, T. Yang, W. Lee and C. Kim, PtRu-LiCoO2-an efficient catalyst for hydrogen generation from sodium borohydride solutions, J. Power Sources, 2005, 143, 17–23 CrossRef CAS.
- R. M. Tinnacher and B. D. Honeyman, Modeling the chemical conversion of organic compounds in sodium borohydride reduction reactions, Organic Process Research & Development, 2008(12), 456–463 Search PubMed.
- Y. Shen, T. Sun and J. Jia, Indirect hydrodesulfurization of gasoline via sodium borohydride reduction with nickel catalysis under ambient conditions, RSC Adv., 2012, 2, 3123–3132 RSC.
- M. Farooque and R. W. Coughlin, Anodic coal reaction lowers energy consumption of metal electrowinning, Nature, 1979, 280, 666–668 CrossRef CAS.
- R. W. Coughlin and M. Farooque, Hydrogen production from coal, water, electrons, Nature, 1979, 279, 301–303 CrossRef CAS.
- S. Lalvani, M. Pata and R. W. Coughlin, Sulphur removal from coal by electrolysis, Fuel, 1983, 62, 427–437 CrossRef CAS.
- W. Zhao, W. Xu, S. Zhong and Z. Zong, Desulfurization of coal by an electrochemicalreduction flotation technique, Journal of China University of Mining and Technology, 2008, 18, 571–574 CrossRef CAS.
- W. Wang, S. Wang, H. Liu and Z. Wang, Desulfurization of gasoline by a new method of electrochemical catalytic oxidation, Fuel, 2007, 86, 2747 CrossRef CAS.
- D. Li, J. Gao and G. Yue, Catalytic oxidation and kinetics of oxidation of coal-derived pyrite by electrolysis, Fuel Process. Technol., 2003, 82(1), 75–85 CrossRef CAS.
- V. Lam, G. Li, C. Song, J. Chen, C. Fairbridge, R. Hui and J. Zhang, A review of electrochemical desulfurization technologies for fossil fuels, Fuel Process. Technol., 2012, 98, 30–38 CrossRef CAS.
- P. G. Wapner and S. B. Lalvani, Organic sulfur removal from coal by electrolysis in alkaline media, Fuel Process. Technol., 1988, 18(2), 25–34 CrossRef CAS.
- A. M. Aitani, M. F. Ali and H. H. Al-Ali, Review of non-conventional methods for the desulfurization of residual fuel oil, Pet. Sci. Technol., 2000, 18(5), 537–553 CrossRef CAS.
- Y. Grigory, D. Keith and T. Norman, New technique for the electrochemical analysis of coal-derived materials, Fuel, 1997, 76(10), 965–974 CrossRef.
- D. Li, J. Gao and G. Yue, Catalytic oxidation and kinetics of oxidation of coal-derived pyrite by electrolysis, Fuel Process. Technol., 2003, 82(1), 75–85 CrossRef CAS.
- M. Farooque and R. W. Coughlin, Electrochemical gasification of coal (investigation of operating conditions and variables), Fuel, 1979, 58, 705–712 CrossRef CAS.
-
H. Ahonen, Method for Desulphurisation of liquid fuels and petrochemical feedstocks, WO Patent, 1993, 025636 Search PubMed.
-
R. C. Schucker, Electrochemical oxidation of sulfur compounds in Naphtha, U.S. Patent, 2001, 6274026 B1 Search PubMed.
-
R. C. Schucker, W. C. Baird Jr, Electrochemical oxidation of sulfur compounds in Naphtha using ionic liquids, U.S. Patent, 2002, 6338788 B1 Search PubMed.
-
M. A. Greaney, K. Wang, F. C. Wang, Electrochemical treatment of heavy oil feedstocks followed by caustic extraction or thermal treatment, U.S. Patent, 2009, 0159503 A1 Search PubMed.
-
M. A. Greaney, C. A. Wright, J. M. McConnachie, H. Freund, K. Wang, Electrodesulfurization of heavy oils, U.S. Patent, 2009, 0159500 A1 Search PubMed.
-
M. A. Greaney, K. Wang, F. C. Wang, Partial electrochemical hydrogenation of sulfurcontaining feedstreams followed by sulfur removal, WO Patent, 2009, 082467 Search PubMed.
- Y. Zhang and G. Zhang, Electrolysis desulfuration of GANLIN coal in Alkaline Media, Journal of Magang Staff and Workers' University, 2001, 11(4), 17–22 CAS (In Chinese).
- D. Li, J. Gao and G. Yue, Catalytic oxidation and kinetics of oxidation of coal-derived pyrite by electrolysis, Fuel Process. Technol., 2003, 82, 75–85 CrossRef CAS.
- P. Yi, J. Liu and N. Huang, Electrolysis desulfuration of high sulfur coal in water- organic solvent mixtures, Clean Coal Technology, 1998, 4(4), 48–51 Search PubMed (In Chinese).
- Y. Shen, X. Yang, T. Sun and J. Jia, Innovative desulfurization process of coal water slurry under atmospheric condition via sodium metaborate electroreduction in the isolated slot, Energy Fuels, 2011, 25, 5007–5014 CrossRef CAS.
- Z. Yusuf and J. Cameron, Decarbonization reactions between sodium metaborate and sodium carbonate, Ind. Eng. Chem. Res., 2004, 43(26), 8148–8154 CrossRef CAS.
- X. Gong, M. Yang, Z. Wang and Z. Guo, Desulfuration of electrolyzed coal water slurry in HCl system with ionic liquid addition, Fuel Process. Technol., 2012, 99, 6–12 CrossRef CAS.
- Y. Shen, T. Sun and J. Jia, A novel desulphurization process of coal water slurry via sodium metaborate electroreduction in the alkaline system, Fuel, 2012, 96, 250–256 CrossRef CAS.
-
C. Fairbridge, E. Taylor, S. Petrovic, J. Lessard and J. Chapuzet, Electrocatalytic hydrogenation of organic sulphur compounds, NCUT Report 96-17 (CF), 1996 Search PubMed.
- W. Zhu, G. Zhu, H. Li, Y. Chao, Y. Chang, G. Chen and C. Han, Oxidative desulfurization of fuel catalyzed by metal-based surfactant-type ionic liquids, J. Mol. Catal. A: Chem., 2011, 347, 8–14 CrossRef CAS.
-
C. S. Robert and C. B. William, Electrochemical oxidation of sulfur compounds in naphtha using ionic liquids, USP6274026B1, 2001 Search PubMed.
- W. Zhu, W. Huang, H. Li, M. Zhang, W. Jiang, G. Chen and C. Han, Polyoxometalate-based ionic liquids as catalysts for deep desulfurization of fuels, Fuel Process. Technol., 2011, 92, 1842–1848 CrossRef CAS.
- R. D. Rogers and K. R. Seddon, Ionic Liquids-Solvents of the Future?, Science, 2003, 5646(302), 792–793 CrossRef.
- P. Majewski, A. Pernak, M. Grzymislawski, K. Iwanik and J. Pernak, Ionic liquids in embalming, tissue preservation, Can traditional formalin-fixation be replaced safely?, Acta Histochem., 2003, 105(2), 135–142 CrossRef CAS.
- M. Gamero-Castano and V. Hruby, Electrospray as a source of nanoparticles for efficient colloid thrusters, J. Propul. Power, 2001, 17(5), 977–987 CrossRef CAS.
- A. Bosmann, L. Datsevich, A. Jess, A. Lauter, C. Schmitz and P. Wasserscheid, Deep desulfurization of diesel fuel by extraction with ionic liquids, Chem. Commun., 2001, 2494–2495 RSC.
- X. Gong, M. Wang, Z. Wang and Z. Guo, Desulfuration of electrolyzed coal water slurry in HCl system with ionic liquid addition, Fuel Process. Technol., 2012, 99, 6–12 CrossRef CAS.
-
K. A. Howard, H. L. Mitchell, R. H. Waghore, US Pat., 1982, 4,359, 596.
-
D. R. Boate, M. J. Zaworoktko, US Pat., 1993, 5,220,106.
-
F. G. Sherif, L. Shyyu, C. C. Greco, US Pat., 1998, 5,824, 832.
-
V. R. Koch , C. Nanjundian,.R. T. Carlin, US Pat., 1998, 5,827, 602.
- S. M. Silvu, P. A. Z. Suarcz and R. F. de Souza, Polym. Bull., 1998, 40, 401–405 CrossRef.
- A. J. Carmichael, D. M. Haddleton, S. A. F. Bon and K. R. Seddon, Copper (I) mediated living radical polymerization in an ionic liquid, Chem. Commun., 2000, 14, 1237–1238 RSC.
- R. T. Carlin and J. S. Wilkes, J. Mol. Catal., 1990, 63, 125–129 CrossRef CAS.
- M. Goledzinowski and V. I. Birss, Oligomerization of low-molecular-weight olefins in ambient temperature molten salts, Ind. Eng. Chem. Res., 1993, 32, 1795–1797 CrossRef CAS.
- J. A. Boon, J. A. Levisky, J. L. Pflug and J. S. Wilkes, Friedel–Crafts reactions in ambient-temperature molten salts, J. Org. Chem., 1986, 51, 480–483 CrossRef CAS.
- J. H. T. Luong, K. B. Male and J. D. Glennon, Boron-doped diamond electrode: synthesis, characterization, functionalization and analytical application, Analyst, 2009, 134, 1965–1979 RSC.
- J. Xu and G. M. Swain, Voltammetric and amperometric investigations of azide oxidation at the basal plane of high oriented pyrolytic graphite, Anal. Chem., 1999, 71, 4603 CrossRef CAS.
- J. Xu, Q. Chen and G. M. Swain, Anthraquinonedissulfonate electrochemistry, a comparison of glassy carbon, hydrogenated glassy carbon, highly oriented pyrolytic graphite, and diamond electrodes, Anal. Chem., 1998, 70, 3146 CrossRef CAS.
- J. Xu and G. M. Swain, Oxidation of azide anion at boron-doped diamond thin-film electrodes, Anal. Chem., 1998, 70, 1502 CrossRef CAS.
- J. Xu, M. C. Granger, Q. Chen, J. W. Strojek, T. E. Lister and G. M. Swain, Boron-doped diamond thin-film electrodes, Anal. Chem., 1997, 69, 591A CrossRef CAS.
- O. Chailapakul, E. Popa, H. Tai, D. A. Sarada, D. A. Tryk and A. Fujishima, The electrooxidation of organic acids at boron-doped diamond electrodes for aluminium electrodeposition, Electrochem. Commun., 2000, 2, 422 CrossRef CAS.
- M. D. Koppang, M. Witek, J. Blau and G. M. Swain, Electrochemical oxidation of polyamines at diamond thin-film electrodes, Anal. Chem., 1999, 71, 1188 CrossRef CAS.
- J. Wang, K. Li, C. Yang, Y. Wang and J. Jia, Ulrasound electrochemical determination of chemical oxygen demand using boron-doped diamond electrode, Electrochem. Commun., 2012, 18, 51–54 CrossRef CAS.
- M. V. Jean-Pierre, D. H. Michael, T. Ruther, M. B. Alan and T. Rodopoulos, Favorable surface properties of boron-doped diamond electrodes for aluminium electrodeposition from ionic liquids, Electrochem. Commun., 2012, 18, 85–87 CrossRef.
|
This journal is © The Royal Society of Chemistry 2012 |
Click here to see how this site uses Cookies. View our privacy policy here.