DOI:
10.1039/C2RA20617J
(Paper)
RSC Adv., 2012,
2, 6504-6508
A new type of unsaturated polyester resin with low dielectric constant and high thermostability: preparation and properties
Received
3rd April 2012
, Accepted 13th May 2012
First published on 15th May 2012
Abstract
A new type of unsaturated polyester resins (UP) with low dielectric constant (κ) and high thermostability was prepared by doping N-phenylmaleimides containing perfluoroalkyl substituents (–CF3 and –C6F13) into a commercial unsaturated polyester resin. In comparison with neat UP resin, the doped UP resins showed decreased dielectric constant and increased char yields. The best result was obtained when the substituent was –CF3, which gave a dielectric constant of 3.63 and 5 wt%, loss temperature of 336 °C with a char yield of 5.57% under N2. Such data are superior to those of neat UP resin, which showed dielectric constants of 4.38 and 5 wt%, a loss temperature of 327 °C with a char yield of 2.25% . In this contribution, a new environmentally-friendly procedure for the synthesis of the fluoro-containing maleimides was also provided, in which a Brønsted acidic room temperature ionic liquid was employed as a catalyst and the products were obtained through merely decanting and removal of the solvent.
1. Introduction
As one of the most important thermosetting resins, unsaturated polyester (UP) resins have been thoroughly investigated and widely used as coatings1,2 and structural adhesives for glass (or carbon)-fiber composites3,4 in the construction industry, boat-building industry and automotive industry,5–9 because of their low cost, ease of processing and good balance of mechanical and chemical properties.10,11 In recent years, many efforts have been paid to improving the toughness and thermostability of the resins,12–16 and a lot of modified UP resins have been prepared, which showed excellent mechanical and heat-resistance properties. However, there have been few reports regarding the enhancement of electrical properties of the resins. With the development of electronic information technology, low dielectric materials are required. Although there have been many polymeric materials with low dielectric constants, including polyimides,17,18 poly(aryletherketone),19 benzocyclobutene resins,20,21 SiLK resins22,23 and fluorinated polymers,24–26 they are usually expensive and sometimes are not readily available. Accordingly, developing materials which show both good electrical properties and low cost are desirable.
It is noted that the introduction of fluoro-containing moieties to the backbones of the polymers can efficiently improve the electrical and thermostable properties of the polymers. 24–26 On the basis of the situation of the abovementioned UP resins, we designed and synthesized two N-phenylmaleimides containing perfluoroalkyl substituents (–CF3 and –C6F13). By adding the fluoro-containing maleimides to a commercial unsaturated polyester resin UP resin, new types of UP resins were obtained, which were cured in the presence of a radical initiator to give resins with low dielectric constant and good thermostability. For comparison, we also added a fluoro-free maleimide (e.g., N-phenylmaleimide) to the UP resin, wherein the properties of the resin showed no great improvement, suggesting that the fluoro-containing maleimides were superior to N-phenylmaleimide. Considering that most of the procedures for the synthesis of the maleimides were not convenient, we also developed a new route for the synthesis of maleimide derivatives, in which a Brønsted acidic room temperature ionic liquid (RTIL) was used as a catalyst and the products were obtained through merely decanting and removal of the solvent. In this contribution, we report the details.
2. Experimental
2.1 Materials
The starting chemicals were purchased from Aladdin Chemical Co. and used as received unless otherwise stated. A commercial unsaturated polyester resin containing 24 wt% of styrene with a brand of P17-902 was purchased from Jinling DSM Resin Co., Ltd. in China. A Brønsted acidic room temperature ionic liquid used in this work (RTIL, Scheme 1) was prepared according to a reported route.271H NMR (300 MHz, CDCl3) δ 8.52 (s, 1H), 7.25 (d, 2H), 4.03 (t, 2H), 3.67 (s, 3H), 2.81–2.64 (m, 2H), 1.79 (dd, 2H), 1.53 (dd, 2H)
2.2 Measurement
1H NMR and 19F NMR spectra were carried out on a Mercury 300 spectrometer. Differential scanning calorimetry (DSC) was determined with TA Instrument DSC Q200 at a heating rate of 10 °C min−1 under nitrogen flow. Thermogravimetric analysis (TGA) was performed on a TA Instruments Q500 with a heating rate of 20 °C min−1 in a nitrogen atmosphere. The dielectric constant (κ) and dissipation factor (tan δ) of the cured samples were measured in a frequency of 1 MHz on cured cylindric samples (average diameters were 2.5 cm and thicknesses were 2–3 mm, respectively) at room temperature using a high resolution dielectric analyzer BDS40 (Novocontrol GmbH). Before each measurement, the samples were thoroughly dried under vacuum. The morphology of modified UP resins was observed by a scanning electron microscope (SEM) on a JSM 6390LV (JEOL co., Japan). The transmittance of the cured resins was taken with a Cary 5000 UV-Vis-NIR spectrometer using the cured resin films on the quartz sheets. A Waters Breeze GPC system was employed to deduce number-average molecular weight (Mn) based on polystyrene standards with THF as an eluent.
2.3 Synthesis
Synthesis of 4-(perfluorohexyl) aniline (13F-NH2).
To a stirring solution containing 4-iodoaniline (4.38 g, 0.02 mol), perfluorohexyl iodide (13.38 g, 0.03 mol) and dimethyl sulfoxide (DMSO, 50 mL) was added copper powder (3.84 g, 0.06 mol). The mixture was heated to 110 °C and maintained at this temperature for 24 h. The solid was filtered, and the cake was washed with CHCl3. The organic layer was combined and washed with water and dried over anhydrous Na2SO4. After removal of the solvents, the residue was purified by column chromatography on silica gel using a mixture solvent of petroleum ether and CHCl3 as the eluent (3
:
1, v/v) to give 13F-NH2 as a brown liquid. 11.1 g, yield of 63%. 1H NMR (300 MHz, CDCl3) δ 7.34–7.37 (d, 2H), 6.69–6.72 (d, 2H), 3.97 (s, 2H). 19F NMR (282 MHz, CDCl3): δ −81.48 (t, 3F), −110.04 (t, 2F), −122.08 (s, 2F), −122.59 (s, 2F), −123.43 (s, 2F), −126.78 (s, 2F).
Synthesis of N-aryl maleimides.
Aniline (27.9 g, 0.3 mol) was added dropwise to a solution of maleic anhydride (29.4 g, 0.3 mol) in toluene (100 mL) at room temperature, and the mixture was stirred for 6 h at this temperature. The precipitate was filtered, washed with toluene and dried to give N-phenylmaleamic acid (0F-AA) as pale yellow powders. 49 g, yield of 86%. Analogously, 3F-AA and 13F-AA were prepared in yields of 85% and 87%, respectively.
To a three-necked flask with a Dean–Stark trap was added 0F-AA (49 g, 0.3 mol), RTIL (31.62 g, 0.1 mol) and toluene (200 mL). The mixture was heated to reflux and kept at the reflux temperature for 6 h. After being cooled to room temperature, the upper layer containing toluene and product was separated by decanting, and the lower layer was extracted by toluene (50 mL × 3). The organic layers were combined, followed by evaporation under vacuum to give N-phenylmaleimide (0F-MI) as a pale-yellow crystal solid in a yield of 80%. Analogously, 3F-MI and 13F-MI were prepared with yields of 77% and 67%, respectively.
Characterization: 0F-MI: 1H NMR (300 MHz, CDCl3) δ 7.50–7.35 (m, 5H), 6.86 (s, 2H). 3F-MI: 1H NMR (300 MHz, CDCl3) δ 7.74 (d, 2H), 7.55 (d, 2H), 6.90 (s, 2H); 19F NMR (282 MHz, CDCl3) δ −63 (s, 3F). 13F-MI: 1H NMR (300 MHz, CDCl3) δ 7.74 (d, 2H), 7.55 (d, 2H), 6.90 (s, 2H); 19F NMR (282 MHz, CDCl3) δ −81.48 (t, 3F), −110.04 (t, 2F), −122.08 (s, 2F), −122.59 (s, 2F), −123.43 (s, 2F), −126.78 (s, 2F).
2.4 Sample preparation
The unsaturated polyester resin and a modifier (0F-MI, 3F-MI or 13F-MI) (0–10 wt% of the total weight of the modifier and the unsaturated polyester resin) were mixed and kept at a certain temperature (at 60 °C for 0F-MI; at 70 °C for 3F-MI; at 80 °C for 13F-MI) for 15 min. The obtained transparent liquid was cooled to 60 °C, and methyl ethyl ketone peroxide (1 wt% of the total weight) was added carefully. The mixture was divided into two portions: one was cooled to room temperature and used for the measurement of DSC, and the other was poured to a flat-bottomed tube (with a diameter of 2.5 cm and a highness of 8.5 cm) filled with argon. The tube was maintained at 80 °C for 12 h and then at 120 °C for 12 h, respectively. A completely cured sample was thus obtained.
3. Results and discussion
3.1 Synthesis and characterization
The maleimides with perfluoroalkyl substituents (–C6F13 and –CF3) were synthesized according to the route illustrated in Scheme 1. For comparison, N-phenylmaleimide without fluoro groups was also prepared (Scheme 1). Usually, the synthesis of N-arylmaleimides was carried out via a ring-closing of the corresponding maleamic acids, and acetic anhydride was often used as a dehydrating agent. However, such a procedure was not environmentally-friendly because large amounts of water were required in order to decompose the excess acetic anhydride and remove acetic acid formed during the dehydration and post-processing. In our cases, a Brønsted acidic room temperature ionic liquid (RTIL, Scheme 1) and toluene were employed as a catalyst and an azeotropic dehydrating agent, respectively, and the maleamic acids (0F-AA, 3F-AA and 13F-AA, Scheme 1) were converted to the corresponding maleimides (0F-MI, 3F-MI and 13F-MI, Scheme 1) in yields of more than 70%. Moreover, the products were obtained through merely a decanting and removal of the solvent (toluene), suggesting that the ionic liquid route for the synthesis of maleimides is economical and environmentally-friendly
The obtained maleimides were characterized by 1H NMR and 19F NMR spectra. All of the detected peaks were consistent with the proposed structure, implying the chemical structure of 3F-MI and 13F-MI were confirmed.
3.2 Curing behavior
The curing behaviors of neat UP resin and the modified resins were characterized by DSC, and the results are shown in Fig. 1. As can be seen from Fig. 2, two exothermic peaks were observed at about 100 °C and 150 °C, respectively. The first peak is generated from the copolymerization between styrene and the active double bonds of the unsaturated polyester and/or the modifiers; the second peak is attributed to the homopolymerization of the active double bonds of the unsaturated polyester and/or the modifiers.28 For details, the data obtained from DSC curves are summarized in Table 1. Compared to neat UP resin, the modified UP resins exhibit a wide processing window with both low onset temperature and exothermic peak, suggesting that the processing properties of UP resin can be efficiently improved by adding the modifiers.
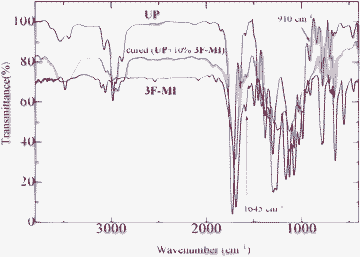 |
| Fig. 1 FTIR spectra of the modifier, uncured neat UP resin and a cured modified UP resin. | |
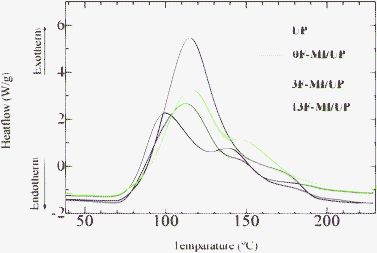 |
| Fig. 2 DSC curves of neat UP resin and the modified resins. The weight ratio between neat UP resin and the modifier was 10%. | |
Table 1 DSC data of neat UP resin and the modified UP resinsa
Resin |
T
onset (°C) |
T
max (°C) |
T
end (°C) |
ΔH (J g−1) |
The weight ratio between UP resin and the modifier was 10%.
|
UP
|
70 |
115 |
219 |
349.5 |
0F-MI/UP
|
62 |
94 |
222 |
221.3 |
3F-MI/UP
|
70 |
112 |
229 |
242.5 |
13F-MI/UP
|
63 |
116 |
221 |
275.3 |
The copolymerization reaction between neat UP resin and the modifiers were also elucidated by FTIR spectroscopy. Taking 3F-MI as an example, the FTIR spectra of uncured neat UP resin, modifier 3F-MI and the cured UP resin modified by 3F-MI are carried out, and the results are shown in Fig. 3. The absorptions at 910 and 1645 cm−1, assigned to the double bonds in neat UP resin and 3F-MI, have disappeared in the cured modified UP resin, indicating that the copolymerization has been completely carried out.
Considering that the modifiers may react with styrene in UP resin during the curing period of the resin, to investigate the reactive ability of the three maleimides with styrene, we carried out the reactions, and the results showed that the copolymerization between the maleimides and styrene can be easily realized and gave the copolymers with average number molecular weights of more than 50
000 (measured by GPC based on polystyrene standards with THF as an eluent), suggesting the high reactive ability of the modifiers with styrene.
We also investigated the curing level of the modified UP resins. Three modified UP resins were heated at 150 °C for 2 h. Their DSC curves showed no exothermic peaks, implying that the modified UP resins had been completely cured.
3.3 Optical properties
It was noted that UP resins usually showed good optical properties. To investigate the effect of the maleimides on the optical properties of the UP resins, the transmittance of cured neat UP resin and cured 3F-MI modified UP resin was measured, and the results are shown in Fig. 3.
As can be seen from Fig. 3, both the cured neat UP and 3F-MI modified UP resin showed high transmittance in a range from 400–800 nm, showing that modifiers did not influence the optical properties of UP resins. However, the resins indicated very low transmittance in the UV region (below 400 nm). The reason was that there was a lot of aryl units on the backbones of the resins, which often showed absorption at 250–400 nm.
3.4 Thermostability
The thermostability of cured neat and the modified UP resins was evaluated by thermogravimetry (TGA). The results are listed in Table 2. In comparison with cured neat UP resin, the cured modified UP resins show an increasing thermostability with the increase of the amount of modifiers. Such improvement of the thermostability may be attributed to the introduction of the modifiers with heteroaromatic rings. In addition, the modified UP resin containing –C6F13 substituents showed much higher char yield than either neat UP resin or the UP resin modified by adding N-phenyl maleimide. Such behavior is desirable for the high performance polymers.
Table 2 TGA data of cured UP resin and the modified UP resinsa
Weight loss (%) |
Weight loss T/°C |
Neat UP resin |
Modified UP resins |
0F-MI/UP
a
|
3F-MI/UP
a
|
13F-MI/UP
a
|
5% |
10% |
5% |
10% |
5% |
10% |
Weight ratio between UP resin and a modifier.
Measured at 500 °C.
|
5% |
327 |
327 |
331 |
332 |
336 |
318 |
329 |
10% |
354 |
356 |
359 |
357 |
361 |
356 |
355 |
Char yieldb |
2.25% |
— |
5.46% |
— |
5.57% |
— |
6.34% |
3.5 Electrical properties
The electrical properties of cured neat UP resin and the modified UP resins were characterized by their dielectric constant (κ) and dissipation factor (tan δ), and the results are depicted in Table 3 and Fig. 4. Obviously, the UP resins modified by adding fluorine-containing maleimides (3F-MI and 13F-MI) showed lower κ and tan δ than both neat UP resin and 0F-MI modified UP resin. The reason is probably attributed to the unique properties of fluorine-containing molecules. It is known that the κ is directly related to the polarizability of a polymer, which is strongly dependent on its chemical structure.29 Consequently, introducing fluorine-containing units or moieties to the backbone or side chains of a polymer can decrease the polarizability and the moisture absorption of the polymer,29 resulting in the decrease of dielectric constant (κ) of the polymer.
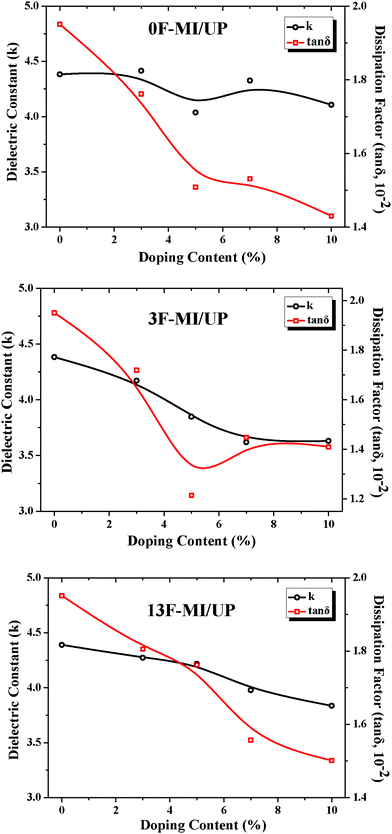 |
| Fig. 4 The relationship between the electrical properties of the modified UP resins and the concentration of the modifiers. | |
Table 3 Dielectric constant and dissipation factor (tan δ) of UP resin containing 10% modifiersa
Resin |
Dielectric constant |
Dissipation factor (tan δ) |
Measured under 1M Hz at 298 K.
|
UP
|
4.38 |
0.019 |
0F-MI/UP
|
4.10 |
0.014 |
3F-MI/UP
|
3.63 |
0.014 |
13F-MI/UP
|
3.83 |
0.015 |
3.6 Morphology
As mentioned above, 3F-MI-modifed UP resins showed good thermostability and electrical properties. To investigate their morphology, SEM analysis of four samples based on various concentrations of 3F-MI was carried out. As shown in Fig. 5, homogenous phase behavior could be observed in the four samples, exhibiting good compatibility between UP resin and 3F-MI.
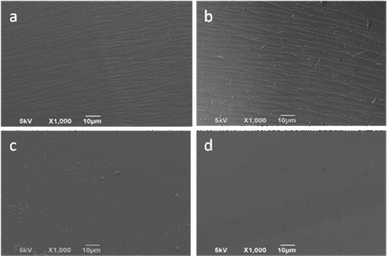 |
| Fig. 5 SEM images of 3F-MI-modified UP resins. The concentration of 3F-MI: (a) 3 wt%, (b) 5 wt%, (c) 7 wt% and (d) 10 wt%. | |
4. Conclusions
Two N-phenyl maleimides with perfluoroalkyl substituents, 3F-MI and 13F-MI, were synthesized and used as modifiers for a commercial unsaturated polyester (UP) resin. The results showed that the modified resins had lower dielectric constant than neat UP resin. Moreover, the modified resins also possessed higher thermostability than neat UP resin. On the basis of the wide applications and low cost of UP resin, this contribution would provide a new way for obtaining the polymers with both thermostability and good electrical properties. In addition, we also investigated the synthesis of the maleimides and provided a new environmentally-friendly procedure, in which a Brønsted acidic room temperature ionic liquid was employed as a catalyst. By using such a route, the products were obtained through merely decanting and removal of the solvent.
Acknowledgements
Financial supports from Ministry of Science and Technology of China (2010BAK67B12 and 2011ZX02703) are gratefully acknowledged.
References
- A. M. Atta, A. M. Elsaeed, R. K. Farag and S. M. El-Saeed, React. Funct. Polym., 2007, 67, 549–563 CrossRef CAS.
- A. A. Prabu and M. Alagar, Prog. Org. Coat., 2004, 49, 236–243 CrossRef.
- P. Wambua, J. Ivens and I. Verpoest, Compos. Sci. Technol., 2003, 63, 1259–1264 CrossRef CAS.
- S. Mishra, A. K. Mohanty, L. T. Drzal, M. Misra, S. Parija, S. K. Nayak and S. S. Tripathy, Compos. Sci. Technol., 2003, 63, 1377–1385 CrossRef CAS.
- H. Yang and L. J. Lee, J. Appl. Polym. Sci., 2001, 79, 1230–1242 CrossRef CAS.
-
L. R. Comstock, S. Charleston, P. L. Smith, US Patent 3718714 Search PubMed.
- Y. Li, Y. W. Mai and L. Ye, Compos. Sci. Technol., 2000, 60, 2037–2055 CrossRef CAS.
- B. N. Dash, A. K. Rana, H. K. Mishra, S. K. Nayak and S. S. Tripathy, J. Appl. Polym. Sci., 2000, 78, 1671–1679 CrossRef CAS.
- A. O′Donnell, M. A. Dweib and R. P Wool, Compos. Sci. Technol., 2004, 64, 1135–1145 CrossRef.
- L. B. Manfredi, E. S. Rodríguez, M. Wladyka-Przybylak and A. Vázquez, Polym. Degrad. Stab., 2006, 91, 255–261 CrossRef CAS.
-
W. G. Hager, T. W. Ramey, R. Krumlauf, J. J. Beckman, US Patent 5373058, 1994 Search PubMed.
- M. Abbate, E. Martuscelli, P. Musto, G. Ragosta and M. Leonardi, J. Appl. Polym. Sci., 1996, 62, 2107–2119 CrossRef CAS.
- M. S. Lin, C. C. Liu and C. T. Lee, J. Appl. Polym. Sci., 1996, 72, 585–592 CrossRef.
- M. Abbate, E. Martuscelli, P. Musto, G. Ragosta and G. Scarinzi, J. Appl. Polym. Sci., 1995, 58, 1825–1837 CrossRef CAS.
- M. Worzakowska, J. Appl. Polym. Sci., 2009, 114, 720–731 CrossRef CAS.
- B. Gawdzik, T. Matynia and E. Chmielewska, J. Appl. Polym. Sci., 2001, 82, 2003–2007 CrossRef CAS.
- H. Behniafar and S. Habibian, Polym. Int., 2005, 54, 1134–1140 CrossRef CAS.
- C. S. Wang and T. S. Leu, Polymer, 2000, 41, 3581–3591 CrossRef CAS.
- Y. M. Niu, X. L. Zhu, L. Z. Liu, Y. Zhang, G. B. Wang and Z. H. Jiang, React. Funct. Polym., 2006, 66, 559–566 CrossRef CAS.
- M. E. Mills, P. Townsend, D. Castillo, S. Martin and A. Achen, Microelectron. Eng., 1997, 33, 327–334 CrossRef CAS.
- A. Modafe, N. Ghalichechian, M. Powers, M. Khbeis and R. Ghodssi, Microelectron. Eng., 2005, 82, 154–167 CrossRef CAS.
- M. Fayolle, G. Passemard, M. Assous, D. Louis, A. Beverina, Y. Gobil, J. Cluzel and L. Arnaud, Microelectron. Eng., 2002, 60, 119–124 CrossRef CAS.
- H. S. Tseng, B. S. Chiou, W. F. Wu and C. C. Ho, Microelectron. Eng., 2008, 85, 104–109 CrossRef CAS.
- Y. Watanabe, Y. Shibasaki, S. Ando and M. Ueda, Polym. J., 2006, 38, 79–84 CrossRef CAS.
- K. I. Fukukawa, Y. J. Shibasaki and M. Ueda, Macromolecules, 2004, 37, 8256–8261 CrossRef CAS.
- Z. Q. Tao, S. Y. Yang, Z. Y. Ge, J. S. Chen and L. Fan, Eur. Polym. J., 2007, 43, 550–560 CrossRef CAS.
- J. Z. Gui, X. H. Cong, D. Liu, X. T. Zhang, Z. D. Hu and Z. L. Sun, Catal. Commun., 2004, 5, 473–477 CrossRef CAS.
- M. Avella, E. Martuscelli and M. Mazzola, J. Therm. Anal., 1985, 30, 1359–1366 CrossRef CAS.
- G. Hougham, G. Tesoro, A. Viehbeck and J. D. Chapple-Sokol, Macromolecules, 1994, 27, 5964–5971 CrossRef CAS.
|
This journal is © The Royal Society of Chemistry 2012 |
Click here to see how this site uses Cookies. View our privacy policy here.