DOI:
10.1039/C2RA20074K
(Paper)
RSC Adv., 2012,
2, 5323-5328
Synthesis of hierarchically porous zeolite A crystals with uniform particle size in a droplet microreactor†
Received
12th January 2012
, Accepted 30th March 2012
First published on 30th March 2012
Abstract
Simple and fast synthesis of zeolite A nanocrystals with uniform particle size and bimodal mesoporous-microporous distribution is presented. It takes only tens of minutes to synthesize rather than hours to days that are usually needed. A microfluidic system is devised and used for the hydrothermal synthesis, in which monodispersed nanolitre droplets containing a gel type precursor solution are generated in a lab-on-a-chip part of the system and then passed through a capillary tube part at 100 °C. A water-soluble alginate polymer was introduced into the gel to generate a hierarchically mesoporous-microporous zeolite A crystals with around 100 nm particle size and high crystallinity, which showed a superior catalytic performance in alkyl borate synthesis. The approach presented here could open a new avenue for producing high quality inorganic nanoparticles continuously with no clogging problem that is inherent in the synthesis of nanoparticles.
Introduction
The application of microfluidics in chemistry has gained significant importance in recent years. Miniaturized chemistry platforms provide controlled fluid transport, rapid chemical reactions, and cost saving advantages over conventional reactors.1 Microfluidic synthesis methods operate at steady state and offer superior control over reaction conditions, such as reagent addition, mixing, heat and mass transfer.2 These microreactors have emerged as a particular class of devices for chemical synthesis and have showed their wide applicability for the optimization of reactions and the production of chemicals.3 Microfluidics have been used in materials science mainly for the improvement of inorganic nanoparticle synthesis, namely metal, metal oxide, and semiconductor nanoparticles. However, the high surface-to-volume ratio often caused significant particle deposition and aggregation on microchannel walls, resulting in channel blockage in the continuous flow microfluidic system.2,4,5 Therefore, the isolation of growing particles from the microchannel walls to prevent channel clogging is a critical issue in the implementation of continuous flow microfluidic methods for the synthesis of uniform nanoparticles. Moreover, the inorganic particles synthesized in the microreactor with laminar flow also suffered from broad particle size distribution due to the non-uniform axial velocity profile, which gives rise to a broad residence-time distribution.2,5,6
An alternative approach involves the use of droplet-based microfluidics, which can address both of the above challenges.2,5b,7 Droplet methods offer the additional advantages of rapid mixing and reduced dispersion, and have been successfully implemented in the synthesis of monodisperse inorganic nanocrystals.1,2,5b,8
Zeolites are a class of aluminosilicate minerals having void spaces often called cages or channels. Their structure is based on a three-dimensional network of [AlO4]5− and [SiO4]4− tetrahedra which are linked to each other via doubly bridging oxygen atoms.9 Zeolite A crystals with LTA (Linde Type A) structure are used in many applications, such as solid acid catalysts, household products, agriculture and water treatment, owing to their adsorption, ion exchange and size selectivity properties.9b,c,10 Conventional zeolite crystals are normally the size of a few micrometers, consisting of thousands of pores along the crystal axis. The sole presence of micropores in zeolites often imposes diffusion limitations for catalytic applications involving large molecules. Therefore, zeolites containing open mesopores facilitate easy access and rapid transport to and from the active site to improve the catalytic performance. The significance of the mesopores in zeolites not only results in a highly efficient catalyst, but also much longer catalytic lifetime in several cases.9b,c The preparation of hierarchical zeolite materials have been attempted in various ways such as the polymerization-induced colloid aggregation method and silica self-assembly with various surfactants.9b,11 However, the zeolite products were mostly disadvantageous with aggregated particles of zeolite nanocrystals in either large diameter (>10 μm) or relatively small surface area with low mesoporous volume.11
In this paper, we report a novel hydrothermal synthesis of well-controlled nano zeolite A (also known as LTA zeolite) crystals. The crystals are uniform and the pores are hierarchically structured with meso- and micro-pores. We also present a droplet microreactor that is composed of a lab-on-a-chip part for droplet generation and a capillary tube part for extended reaction time at elevated temperature, which was used for the synthesis. The aqueous droplets surrounded in oil medium prevented contact between the growing nanocrystals and the microchannel walls, preventing channel clogging. In a droplet microreactor, rapid nucleation process of the initial crystals and a highly uniform growth process were well-controlled to obtain the nanoscale products with high uniformity by reducing the heating period and crystallization time. The hierarchically mesoporous-microporous zeolite A crystals were produced by addition of water-soluble alginate polymer as a pore-expanding agent into the gel precursor solution. Thus the LTA zeolite synthesized with uniform particle size and bimodal mesoporous-microporous distribution delivered excellent catalytic activity in the synthesis of alkylborate.
Experimental
Synthesis of nanozeolite A
Nano zeolite A particles were prepared by hydrothermal synthesis according to the procedure reported elsewhere.12 An alumina precursor solution was prepared by adding aluminum isopropoxide (Al(iprO)3, 99.99%, Sigma-Aldrich Co. Ltd.) to a solution of tetramethylammonium hydroxide (TMAOH, [(CH3)4N]OH, 25% (solution in water), and sodium hydroxide (NaOH, 98%, Sigma-Aldrich Co. Ltd.). This solution was stirred until completely dissolved (around 1 h). Then, tetraethyl orthosilicate (TEOS, 98%, Sigma-Aldrich Co. Ltd.) was added to the above alumina precursor solution to prepare a solution with a mole ratio of the composition Al(iPrO)3
:
TEOS
:
TMAOH
:
NaOH
:
H2O = 1.0
:
2.0
:
4.6
:
0.3
:
220.0. A transparent and homogeneous gel solution was obtained after aging for 10 h by stirring at room temperature. This gel solution was used as the precursor solution for the zeolite A synthesis. Zeolite A crystals were produced by a reaction in a droplet microreactor, as shown in Fig. 1. The zeolite precursor solution was forced into the continuous oil phase at the T-junction of the channel at flow rate of Qd μL min−1 (flow rate 2–5 μL min−1) to form a dispersed phase. The continuous phase, fluorocarbon oil (FC oil, 3 M, St. Paul, MN) was introduced from the horizontal inlet at a flow rate of Qc μL min−1 (flow rate 16–40 μL min−1). Both the dispersed and continuous phases were injected into the microfluidic device using a syringe pump (PHD 2000, Harvard Instruments, Holliston, MA). The generated droplets were then flowed into the PFA tube (i.d. 508 μm) with different delay loop lengths, which was immersed in a silicon oil bath at 100 °C. The experiments were carried out at various flow rates of the dispersed phase (Qd) and continuous phases (Qc) with a constant ratio Qd
:
Qc = 1
:
8, which allowed easy control of droplet generation. The synthesized products were collected at the outlet of the PFA tube and purified by centrifuging and washing three times with deionized water. Finally, the products were dried at 90 °C for 12 h, or subsequently calcined at 550 °C in air for 4 h if required.
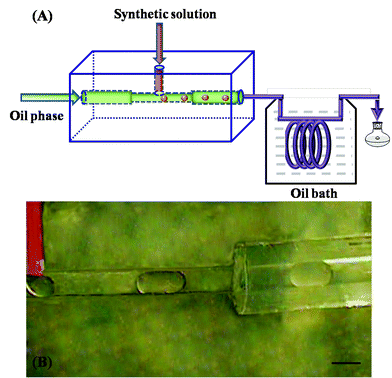 |
| Fig. 1 (A) Schematic diagram of the droplet microfluidic system composed of a lab-on-a-chip fluoropolymer part and capillary tube part, (B) optical image of the zeolite precursor solution droplets in the fluoropolymer device. The scale bar is 500 μm. | |
To prepare a hierarchically mesoporous-microporous zeolite, water-soluble alginate polymer (FMC Biopolymer, N-3002 Drammer, Norway) as a pore-expanding agent was added to the zeolite precursor solution at different mole ratios Al(iprO)3
:
TEOS
:
TMAOH
:
NaOH
:
H2O
:
alginate = 1.0
:
2.0
:
4.6
:
0.3
:
220.0 : m, 0.001 ≤ m ≤ 0.004, using the identical procedure. These transparent precursor solutions were also injected into the microfluidic channel to generate droplets under the identical conditions used for LTA nanozeolite synthesis. The synthesized products were collected at the outlet of the PFA tube and purified by centrifuging and washing three times with deionized water.
Finally, the products were dried at 90 °C for 12 h, or subsequently calcined at 550 °C in air for 4 h if required.
Catalytic test of zeolites
To examine the catalytic efficiency of the zeolite nanocrystals, the catalytic synthesis of alkylborate was performed by stirring 7 g boron oxide (Sigma-Aldrich)) and 36 g of an alcohol (2-propanol, n-butanol, Sigma-Aldrich) in a flask at 70 °C in the presence of 1 g of the zeolite sample. Prior to the reaction, the zeolite catalysts were activated at 550 °C for 4 h in flowing air. The catalytic reaction products were analyzed by 1H nuclear magnetic resonance (NMR) spectroscopy. The conversion (X) was calculated using the equation, X = A/(N + A) , where A is the peak intensity of a proton at the carbon atom bound to the ester group in ((CH3)2CHO)3B and N is the peak intensity of a proton at the carbon atom bound to the hydroxyl group in (CH3)2CHOH.13 In addition, the water uptake (WU) capability of the calcined zeolite nanoparticles at 550 °C for 4 h in air was measured by immersing them into deionized water for 1 h at 60 to 90 °C using the equation: WU (%) = ((W – W0)/W0) × 100%, where W0 and W are the weights of the dried and wet sample, respectively.
Characterization
High-resolution transmission electron microscopy (HRTEM) was performed using a JEM 2100F, JEOL, Japan, operating at 200 kV. Scanning electron microscopy (SEM) was performed using a JSM-7000F, JEOL, Japan. The particle size was measured by DLS (Dynamic Light Scattering) using a Part III laser particles analyzer (Photal Otsuka Electronic, Japan) at a concentration of 1 mg mL−1. X-ray diffraction (XRD) was performed on a Rigaku D/max lllC (3 kW) with a θ/θ goniometer equipped using a Cu KR radiation generator. The surface area and N2 adsorption–desorption isotherms were measured at 77 K on a Micromeritics (ASAP 2010, USA) using the Brunauer-Emmett-Teller (BET) method. The 1H NMR spectra were performed in CDCl3 on a Bruker DMX600 spectrometer with a 7788 Hz spectral width, a relaxation delay of 1.0 s, and a pulse width of 30°.
Results and discussion
Hydrothermal synthesis of well-controlled nano zeolite A in a droplet microreactor
The microfluidic system was designed using a combination of a lab-on-a-chip part (microfluidic device) to generate the droplet, and a capillary perfluoroalkoxyalkane (PFA) tube (100–150 cm, i.d 508 μm) part to control the reaction time at elevated temperature. The lab-on-a-chip microfluidic device for generating the droplets was fabricated using a low molecular weight perfluoropolyether (low MW PFPE).14a The fluoropolymer lab-on-a-chip with multi-sized channels was made in a simple, cost-effective single step using inexpensive assembled templates (Fig. S1, ESI†), which were developed by our group,14b,c and used to generate droplets at the T-junction. Moreover, the large outlet channel in the device is useful as an adaptor to connect with the extended PFA loop tube, which renders an assembly type of microfluidic system. This device could be used extensively for various chemical reactions by selecting suitable materials and required channel design.14c The fluoropolymer microchannel showed excellent resistance against strong swelling solvents, such as benzene, toluene, THF, hexane and chloroform, as well as acids and bases at room temperature.14c Fluorocarbon oil was used as the continuous phase because it wets the fluoropolymer channel walls preferentially, and is immiscible with the aqueous zeolite precursor solution as a dispersed phase. Therefore, the precursor solution retained the shape of the droplets in the lab-on-a-chip part of the microfluidic system and subsequently flowed into the PFA tube immersed in the 100 °C oil bath, where crystallization took place. The precursor solution in the droplet was confined in the nanoliter-scale droplet and kept moving along the channel and tube. In such a droplet, homogeneous temperature distribution is quickly reached due to efficient heat transfer, and good mixing is achieved by chaotic advection in the droplet.8b,c,d,14c Therefore, crystallization in droplets occurred quite rapidly within a short residence time of the order of minutes, which led to a narrow particle-size distribution with high crystallinity. Note that the mild conditions at 100 °C under ambient pressure are sufficient for synthesizing nano zeolite A crystals with controllable compositions. On the other hand, hydrothermal synthesis for alternative zeolite types is still challenging at the high temperatures and high pressures required with a sophisticated microfluidic system.
Fig. 2A and Fig. S4A† shows the XRD patterns of various zeolite A crystals with the Na/Si/Al ratio of 0.3
:
2
:
1 synthesized in droplet microreactor for different reaction times. It can be seen that the products synthesized in the droplet microreactor show the typical diffraction pattern of LTA zeolites with high crystallinity around ca. 96%, even within a short crystallization time of 25 min. This reaction time is similar to the crystallization time of a continuous flow capillary microreactor, but much shorter than the several hours of crystallization needed for the bulk reaction. The nanoscale crystallinity was also confirmed by TEM (Fig. S2, ESI†), which showed gradual increase in size with increasing residence time. From the SEM images in Fig. 2B and Fig. S4B†, the particle shape is seen to develop gradually from a nearly round-shape at 3 min retention time to a perfectly cubic shape at 25 min retention time. This behavior was clearly distinguished from the continuous flow capillary microreactor that rendered only round shape morphology of zeolite NaA as well as the less developed XRD patterns.6 In particular, the particle size distribution also changed with retention time (Fig. S3, ESI†). The LTA zeolite crystal showed a mean particle size of 90 nm with a wide range of 79–102 nm at a 3 min retention time. On the other hand, when the residence time was increased, the mean particle size was also increased with a narrower size distribution: 98 nm (92–111 nm), 117 nm (109–125 nm) and 130 nm (124–139 nm) at 6, 12 and 25 min retention, respectively, which was also observed by SEM (Fig. 2 and Fig. S4†). The continuous microreactor systems without droplet generators produced irregularly shaped LTA zeolite particles with wider size distribution (around 90–230 nm) and lower crystallinity.5b,8d In contrast, under the identical hydrothermal conditions the droplet microreactor yielded much higher uniformity with narrower particle size distribution and a cubic shape particle, and similar crystallinity as that prepared through bulk reaction for 15 h reaction time (Fig. 2). It indicates that the droplet-based microreactor is a reliable method for synthesizing a better-defined zeolite A. In the discrete droplets that become rapidly homogenized in chemical composition and temperature through efficient heat transfer and chaotic advection, better uniformity of the particle size can be expected. In addition, the crystallization in a nanoliter-scale droplet was also facilitated by enhanced mass transfer with a short diffusion distance. In other words, chaotic advection in the droplet increases the probability of a solute molecule coming into contact with an existing crystal. Moreover, rapid heat transfer in a droplet enables sufficient supply of thermal energy for bursting nucleation and subsequent crystal growth with fewer lattice defects. More recently, highly monodispersed inorganic and polymer nanoparticles, and better-defined block copolymers were also synthesized by the compartmentalized droplet microfluidic approach synthesis.4a,8b,c,d,14c
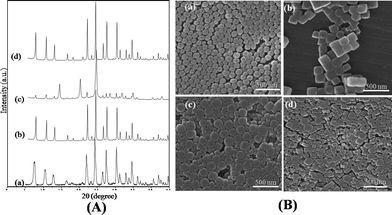 |
| Fig. 2 (A) XRD pattern of the zeolite synthesized in (a) a droplet microreactor for 3 min, (b) a droplet microreactor for 25 min, (c) continuous flow capillary microreactor for 25 min reaction and (d) bulk phase for 15 h reaction time; (B) SEM images of the zeolite A sample synthesized in (a) a droplet microreactor for 3 min, (b) a droplet microreactor for 25 min, (c) continuous flow capillary microreactor for 25 min reaction and (d) bulk phase for 15 h reaction time. | |
Generation of hierarchically porous zeolite A crystals in a droplet microreactor
In order to enhance the activity and catalytic lifetime of zeolite A catalyst, the high surface area mesoporous LTA zeolites were prepared by adding a water-soluble alginate polymer as a pore-expanding agent to the zeolite precursor solution at different mole ratios Al(iprO)3
:
TEOS
:
TMAOH
:
NaOH
:
H2O
:
alginate = 1.0
:
2.0
:
4.6
:
0.3
:
220.0
:
m, where m was 0.001, 0.002, and 0.004. The samples were labeled as LTA-01, LTA-02, and LTA-04, respectively, and synthesized using the identical procedure as that used for LTA zeolite (LTA-0) with no alginate. The crystallinity of the high surface area LTA-m samples obtained in 12 min of reaction time was examined by XRD (Fig. 3A). The increased amount of alginate additive induced gradual appearance of an amorphous background as well as peak broadening due to decreased crystalline domain size.15 The zeolite products obtained with more than 0.004 mole of alginate contained an amorphous phase (data not shown), whereas the XRD pattern of the LTA-01 sample was slightly different from that of the LTA-0 sample. In addition, as shown in the SEM images of Fig. 3B, the uniformity of particle size was seemingly kept although the size of the nanocrystal particle decreased with increasing amount of alginate. It was consistent with the results measured by DLS (Fig. S5, ESI†) that showed a reduced mean particle size and the comparable size distribution to LTA-0 sample (Table 1). Interestingly, alginate promoted early formation of the particle morphology to a cubic-shape even in 12 min of reaction time while LTA-0 sample formed the corresponding morphology in 25 min. Note that addition of a water soluble chitosan biopolymer in the zeolite gel could shorten the prenucleation and nucleation periods dramatically, and accelerate crystal growth.15,16
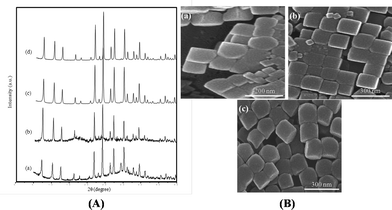 |
| Fig. 3 (A) XRD pattern of high surface area mesoporous LTA zeolites synthesized in a droplet microreactor for 12 min reaction with different mole ratios (m) of alginate as a pore-expanding agent, calcined at 550 °C in air. (a) LTA-04, m = 0.004, (b) LTA-02, m = 0.002, (c) LTA-01, m = 0.001 and (d) LTA-0, m = 0. (B) SEM images of the corresponded zeolite samples with various amounts of alginate (a) LTA-04, (b) LTA-02, (c) LTA-01. | |
Table 1 Pore characteristics and particle size of high surface area mesoporous LTA zeolites with various amounts of alginate addition synthesized in a droplet microreactor for 12 min reaction and calcined at 550 °C in air
Sample |
SBET, m2 g−1 |
SMICRO, m2 g−1 (VMICRO, cm3 g−1) |
SMESO, m2 g−1 (VMESO, cm3 g−1) |
Mean particle size, nm |
Particle size distribution, nm |
LTA-0 |
187 |
157 (0.10) |
30 (0.20) |
117 |
109–125 |
LTA-01 |
413 |
249 (0.11) |
165 (0.39) |
112 |
100–122 |
LTA-02 |
542 |
210 (0.13) |
333 (0.49) |
109 |
95–119 |
LTA-04 |
609 |
122 (0.17) |
487 (0.56) |
104 |
90–117 |
Table 1 summarizes the pore characteristics of the LTA-m samples. The samples showed a progressive increase in mesoporosity and BET surface area when the amount of alginate increased, which is consistent with the nitrogen adsorption-desorption isotherms (Fig. 4A). The BET surface area and mesopore volume for mesoporous LTA zeolite were increased significantly from 187 m2 g−1 and 0.20 cm3 g−1 for the LTA-0 sample to 609 m2 g−1 and 0.56 cm3 g−1 for LTA-04 sample, respectively.
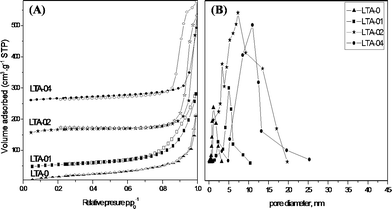 |
| Fig. 4 (A) N2 adsorption-desorption isotherm and (B) pore size distribution of mesoporous LTA-m zeolite samples synthesized in a droplet microreactor for 12 min with different mole ratios (m) of alginate as a pore-expanding agent after calcination at 550 °C in air. | |
The nitrogen adsorption-desorption isotherms of Fig. 4A also confirmed the highly developed hierarchical mesopore-micropore structures in the zeolite network. All LTA-m samples exhibited a type I isotherm at low p/p0 and the typical character of a micropore material, as well as a type IV isotherm with a large hysteresis loop in the high p/p0 range, as evidence of a hierarchical structure.11a Pore size analysis by BJH algorithm for the mesoporous LTA-m samples indicated sharp presence of mesoporosity, which is dependent on the amount of alginate additive. In particular, the major mesopore size was increased from 1.1 nm for LTA-0 to 5 nm for LTA-01, 7 nm for LTA-02 and 10 nm for LTA-04 (Fig. 4B). Furthermore, the TEM image in Fig. 5 of LTA-01 revealed the presence of both mesopores with 2 nm and 5 nm, and the micropores were also visible. The crystalline zeolitic phase (marked with rectangle in Fig. 5B) was alternated with the mesoporous phase of a worm-like mesostructure (Fig. 5A), which was consistent with the crystalline XRD pattern shown in Fig. 3.
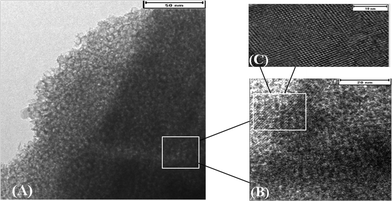 |
| Fig. 5 TEM images of mesoporous LTA-01 zeolite sample synthesized in a droplet microreactor for 12 min after calcination at 550 °C in air for 4 h. | |
The hydrophilic biopolymer alginate, (C6H8O6)n, containing abundant carboxyl and hydroxyl groups, bonds with the active aluminosilicate precursor species to form large aggregates.16 Moreover, the TMAOH molecule also behaves as a surfactant-like agent to stabilize the aggregates of alginate and aluminosilicate precursor. It can be emphasized that these reaction processes must have been facilitated by highly efficient mixing in the nanoliter-scale droplet. The well-established assembly conditions through an electrostatic interaction and/or hydrogen bonding may lead to crystallization of the zeolite precursor within the interstitial volumes of the aggregation under hydrothermal conditions.11b In particular, the fast mass transfer via chaotic advection as well as fast heat transfer in the droplet flow might enhance nucleation and crystal growth. The mesopores were formed by the sacrificial removal of alginate during calcination at 550 °C in air.
Catalytic efficiency of mesoporous LTA zeolite
The catalytic efficiency of the high surface area mesoporous LTA zeolite was examined using the reaction of 2-propanol or n-butanol with boron oxide to form isopropyl or butyl borate, which is the most popular model for preparing alkyl borates. In the reaction, LTA zeolite plays dual role as a catalyst to activate 2-propanol or n-butanol, and as water adsorbent to prevent further hydrolysis of the ester obtained. Therefore, it is expected that the high surface area mesoporous zeolite A as a catalyst and water absorbent would readily accelerate the mass-transfer process between the liquid and solid phase and efficiently remove the water formed.13 Firstly, the water uptake (WU) ability of the calcined LTA zeolite nanoparticles was measured by comparing the weights of the dried sample and wet sample after immersion in water at 60–90 °C for 1 h. As shown in Table S1†, the mesoporous LTA zeolite samples exhibited much better WU ability (36–45%) than that obtained for LTA-0 (28–30%) at the measured temperatures, which was attributed to the increased surface area and pore volume. This result is partly related to the facilitated diffusion behavior in the fully inter-connected porous zeolite network. As shown in Table 2, the high surface area mesoporous LTA zeolite exhibited superior catalytic efficiency and higher conversion than LTA-0 zeolite, that was better than bulk LTA zeolite.13 The conversion yields were generally proportional to the surface area and pore volume of the catalyst samples. For example, the 2-propanol conversion over LTA-01 was 40.5% when reaction was 10 min and 70.2% when it was 3 h. The LTA-04 sample showed the highest catalyst efficiency with 49.9 and 74.1% conversion for 10 min and 3 h reaction time, respectively. In addition, another alcohol, the n-butanol, was also chosen to react with boron oxide using LTA zeolite catalyst.
Table 2 Catalytic efficiency of mesoporous LTA zeolite samples, which were synthesized in a droplet microreactor for 12 min reaction and calcined at 550 °C in air, for alkyl borate synthesis
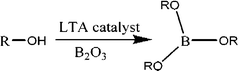
|
Reaction time |
Conversion of alcohola (%) |
LTA-01 |
LTA-02 |
LTA-04 |
LTA-0 |
Bulk LTA-0b |
No Catalyst |
Conversion of 2-propanol, measured by 1H NMR.
Results of zeolite LTA-0 synthesized in bulk phase, conversion of n-butanol in parentheses.
|
10 min |
40.5 (36.4) |
44.8 (40.1) |
49.9 (45.3) |
29.9 (24.2) |
- |
5 (4.1) |
20 min |
59.2 (52.7) |
61.6 (57.8) |
65.0 (61.6) |
38.8 (34.4) |
- |
8 (6) |
30 min |
67.3 (61.9) |
70.5 (64.0) |
71.7 (65.7) |
46.6 (31.6) |
40.1 (26.5) |
11 (9.5) |
3 h |
70.2 (63.6) |
73.4 (65.9) |
74.1 (67.4) |
51.2 (38.5) |
45.3 (31.8) |
16 (14.3) |
The conversion over LTA-01 was 36.4% for reaction time of 10 min and 63.6% for reaction time of 3 h. The LTA-04 sample also showed the highest catalytic efficiency with 45.3% and 67.4% conversion for 10 min and 3 h reaction time, respectively. The improved catalytic activities of the hierarchical mesoporous zeolite could be explained by the larger number of active sites on the increased surface area and the facile diffusion of reagents throughout the hierarchical micropore-mesopore structure. The stability of catalysis was also tested by using the same catalyst twice (Table S2†). The catalytic activity of LTA-04 decreased only to 47.3% conversion from 49.9% for 2-propanol and from 45.3% to 43.8% for n-butanol, whereas LTA-0 sample was decreased to 20.7% from 29.9% and from 24.2% to 15.2% for 2-propanol and n-butanol, respectively, when reacted for 10 min. It indicates that the hierarchical mesoporous zeolite is more resilient to catalytic deactivation. In the case of n-butanol, it is most likely that lower conversion is associated with its longer alkyl chain and higher viscosity.13 Nevertheless, the presence of mesoporosity is obviously advantageous for catalytic applications involving large molecules.
Conclusion
Hydrothermal synthesis of zeolite A was conducted in a droplet microreactor composed of a lab-on-a-chip part and capillary tube part, where the precursor solution was dispersed into monodisperse nanolitre droplets. Cubic shape of crystalline zeolite A nanoparticles with highly uniform and narrow particle size distribution were synthesized in a very short reaction time, approximately several minutes, when compared to the product synthesized using the continuous-flow microreactor and bulk reaction. Moreover, by adding bio-polymer alginate as a pore-expanding agent, mesoporous/microporous zeolite A with high surface areas was obtained with a slight change in particle size and its distribution. The hierarchical mesoporous zeolite A with higher water uptake ability showed a superior catalytic performance in the synthesis of isopropyl borate with higher conversion yields and improved stability. It is expected that the droplet-assisted microreactors can offer a new approach to the synthesis of high-quality inorganic nanoproducts via rapid mixing of reactants and easy handling of solid products with no clogging problems.
Acknowledgements
This work was supported by the National Research Foundation of Korean (NRF) grant funded by the Korea government (MEST) (No. 2008-0061983).
References
- A. Abou-Hassan, O. Sandre and V. Cabuil, Angew. Chem., Int. Ed., 2010, 49, 6268–6286 CrossRef CAS.
- S. Duraiswamy and S. A. Khan, Small, 2009, 5, 2828–2834 CrossRef CAS.
-
(a) G. M. Whitesides, Nature, 2006, 442, 368–373 CrossRef CAS;
(b) J. West, M. Becker, S. Tombrink and A. Manz, Anal. Chem., 2008, 80, 4403–4419 CrossRef CAS;
(c) D. Psaltis, S. R. Quake and C. Yang, Nature, 2006, 442, 368–373 CrossRef;
(d) A. J. deMello, Nature, 2006, 442, 394–402 CrossRef CAS.
-
(a) A. A. Hassan, O. Sandre, V. Cabuila and P. Tabeling, Chem. Commun., 2008, 1783 RSC;
(b) J. Boleininger, A. Kurz, V. Reuss and C. Sonnichsen, Phys. Chem. Chem. Phys., 2006, 8, 3824 RSC.
-
(a) S. A. Khan, A. Gunther, M. A. Schmidt and K. F. Jensen, Langmuir, 2004, 20, 8604 CrossRef CAS;
(b) B. K. H. Yen, A. Gunther, M. A. Schmidt, K. F. Jensen and M. G. Bawendi, Angew. Chem., Int. Ed., 2005, 44, 5447–5451 CrossRef CAS.
- J. X. Ju, C. F. Zeng, L. X. Zhang and N. P. Xu, Chem. Eng. J., 2006, 116, 115 CrossRef CAS.
- H. Song, J. D. Tice and R. F. Ismagilov, Angew. Chem., Int. Ed., 2003, 42, 768–772 CrossRef CAS.
-
(a) I. Shestopalov, J. D. Tice and R. F. Ismagilov, Lab Chip, 2004, 4, 316–321 RSC;
(b) H. Song, D. L. Chen and R. F. Ismagilov, Angew. Chem., Int. Ed., 2006, 45, 7336–7356 CrossRef CAS;
(c) J. D. Tice, H. Song, A. D. Lyon and R. F. Ismagilov, Langmuir, 2003, 19, 9127–9133 CrossRef CAS;
(d) P. H. Hoang, H. S. Park and D. P. Kim, J. Am. Chem. Soc., 2011, 133, 17654 Search PubMed.
-
(a) C. S. Cundy and P. A. Cox, Chem. Rev., 2003, 103, 663 CrossRef CAS;
(b) K. H. Cho, H. S. Cho, L.-C. d. Ménorva and R. Ryoo, Chem. Mater., 2009, 21, 5664 CrossRef CAS;
(c) L. Tosheva and V. P. Valtchev, Chem. Mater., 2005, 17, 2494 CrossRef CAS.
-
(a) J. Hedlund, B. Schoeman and J. Sterte, Chem. Commun., 1997, 1193 RSC;
(b) S. Y. Choi, Y. J. Lee, Y. S. Park, K. Ha and K. B. Yoon, J. Am. Chem. Soc., 2000, 122, 5201 CrossRef CAS;
(c) K. B. Yoon, Acc. Chem. Res., 2007, 40, 29 CrossRef CAS.
-
(a) F. N. Gu, F. Wei, J. Y. Yang, N. Lin, W. G. Lin, Y. Wang and J. H. Zhu, Chem. Mater., 2010, 22, 2442 CrossRef CAS;
(b) J. Zhao, J. Zhou, Y. Chen, Q. J. He, M. Ruan, L. Guo, J. L. Shi and H. Chen, J. Mater. Chem., 2009, 19, 7614 RSC.
- W. N. Lau, X. F. Zhang, K. L. Yeung and R. Martin-Aranda, Stud. Surf. Sci. Catal., 2005, 158, 1335 CrossRef.
- V. V. Molchanov, V. V. Goidin, A. V. Golovin, Y. B. Zolotovskaya, S. V. Bogdanov and A. M. Volodin, Kinet. Catal., 2002, 43, 580 CrossRef.
-
(a) J. Perumal, D. P. Kim and J. J. Lee, J. Nanosci. Nanotechnol., 2008, 8, 5341–5346 CrossRef CAS;
(b) A. Asthana, K. O. Kim, J. Perumal, D. M. Kim and D. P. Kim, Lab Chip, 2009, 9, 1138 RSC;
(c) P. H. Hoang, C. T. Nguyen, J. Perumal and D. P. Kim, Lab Chip, 2011, 11, 329 RSC.
- H. Greer, P. S. Wheatley, S. E. Ashbrook, R. E. Morris and W. Zhou, J. Am. Chem. Soc., 2009, 131, 17986 CrossRef CAS.
- J. F. Yao, D. Li, X. Zhang, C. -H. Kong, W. B. Yue, W. Zhou and H. T. Wang, Angew. Chem., Int. Ed., 2008, 47, 8397 CrossRef CAS.
Footnote |
† Electronic supplementary information (ESI) available: Fabrication of solvent-resistant microfluidic channel, Fig. S1–S5, Table S1, S2. See DOI: 10.1039/c2ra20074k |
|
This journal is © The Royal Society of Chemistry 2012 |
Click here to see how this site uses Cookies. View our privacy policy here.