DOI:
10.1039/C2RA00829G
(Paper)
RSC Adv., 2012,
2, 2768-2772
Synthesis and properties of thermosetting resin based on urushiol
Received
4th October 2011
, Accepted 20th December 2011
First published on 8th February 2012
Abstract
We have synthesized a novel benzoxazine monomer and polybenzoxazine thermosetting resin based on urushiol, a natural product. Fourier transform infrared (FTIR) spectroscopy and differential scanning calorimetry (DSC) studies demonstrate that the thermally activated ring opening polymerization of the benzoxazine occurs at around 210 °C without addition of catalyst. Thermal gravimetric analysis (TGA) measurements show the temperatures corresponding to 5% and 10% weight loss are 325 °C and 357 °C, respectively, with a char yield of 22% at 600 °C. Dynamic mechanical analysis (DMA) studies indicate the urushiol-based polybenzoxazine exhibits excellent toughness with a storage modulus (G′) of 606 MPa at room temperature and an elongation at break of 17.4%.
Introduction
There are around 600 species of oriental lacquer tree in Southeast Asia, and lacquer sap or raw lacquer is collected from the trees.1,2 It is reported that lacquer was used as a durable coating material in China thousands of years ago.3 Such a renewable coating exhibits beauty, extraordinary durability and high gloss with an environmentally friendly enzyme-catalyzed curing process at room temperature. Urushiol is the main component of Chinese and Japanese lacquer. It forms the lacquer sap together with glycoproteins, laccase enzymes, polysaccharides and water.4–6 Urushiol in Chinese lacquer is a mixture of 3-substituted catechol derivatives with 0–3 olefins in the side chains (Scheme 1).7–10
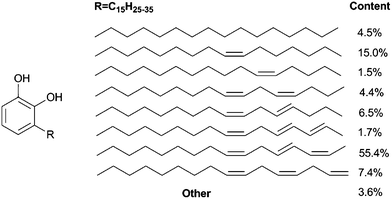 |
| Scheme 1 Structure of urushiol. | |
Polybenzoxazines are a kind of phenol–formaldehyde resin, which have received increasing interest because they possess excellent and unique properties such as high strength, high decomposition temperature, near-zero shrinkage upon polymerization, low moisture absorption, good flame retardancy, and remarkable toughness.11–16 However, the polymers still have some disadvantages which restrict their applications. For instance, the resins require a high curing temperature and often show poor ductility. Attempts have been made to improve the properties. One approach is to blend polybenzoxazine with other polymeric or inorganic materials to form polymer hybrids or composites.17–29 Another one is to introduce reactive functional groups to polybenzoxazine or the monomer.30–38 Besides, polybenzoxazine resins based on cardanol was also developed.39 In the present work, we report the synthesis and properties of a novel urushiol-based benzoxazine monomer (UBz) and polybenzoxazine (PUBz). Our aim is to develop a high performance thermosetting resin from a natural product.
Experimental
Materials
Chinese lacquer was purchased from Xi'an Institute of Lacquer, China. Urushiol was extracted from orient lacquer using ethanol following a procedure reported elsewhere.37 Absolute ethanol, n-butyl alcohol, dichloromethane, chloroform, and sodium hydroxide from Sinopharm were used as received. Aniline and pyridine from Sinopharm was distilled prior to use. Paraformaldehyde (96%) from Aladdin was used as received.
Determination of reactive hydroxyl groups in urushiol
Since urushiol is a mixture of 3-substituted catechol derivatives, and only half of the hydroxyl groups in urushiol can react with aniline and formaldehyde to form benzoxazine in principle, the hydroxyl content must be determined. The determination followed AOAC Official Method 965.32 through the Acetylation Method.40 Typically, 0.5 g of urushiol together with 10 mL of acetone was added into a 250 mL Erlenmeyer flask equipped with a reflux condenser, and then 1.0 mL of acetic anhydride and 3.0 mL of pyridine were introduced. The solution was gradually heated to 90 °C and refluxed for one hour. After adding 20 mL of water and 25 mL n-butyl alcohol through the reflux condenser, the mixture was cooled down to room temperature. The mixture was then titrated by NaOH aqueous solution (0.4 mol L−1) with phenolphthalein as the indicator. The reagent blank contained all corresponding reagents but urushiol. The value of the reactive hydroxyl group was estimated to be 2.80 × 10−3 mol g−1.
Synthesis of urushiol-based benzoxazine and polybenzoxazine
To a 100 mL three-necked round bottom flask equipped with a thermometer, a reflux condenser and a dropping funnel, paraformaldehyde (0.05 mol, 1.50 g), aniline (0.025 mol, 2.33 g), and 20 mL of dioxane were added and stirred at room temperature for 40 min. After adding a solution of urushiol (0.025 mol, 8.97 g) in 10 mL dioxane dropwise within 20 min, the solution was gradually heated to 90 °C, and the brown mixture was refluxed for 5 h. The solvent was removed by distillation under reduced pressure, and the residual was dissolved in 100 mL of dichloromethane. The solution was washed three times with distilled water, and dried with anhydrous magnesium sulfate for 6 h. The solvent was removed by rotary evaporation, and the brown product was dried under vacuum at room temperature. Further purification was conducted by column chromatography and a light red liquid was obtained.
The monomer was deposited into a rectangular aluminum mold and heated stepwise at 100, 140, 180, and 200 °C each for one hour, yielding a dark brown urushiol-based polybenzoxazine film with high gloss.
Characterization
Proton nuclear magnetic resonance (1H NMR) and 13C nuclear magnetic resonance (13C NMR) spectra were recorded on a Bruker AV400 NMR spectrometer using CDCl3 as the solvent and tetramethylsilane (TMS) as the internal standard at a proton frequency of 400 MHz and the corresponding carbon frequency.
Fourier transform infrared (FTIR) spectra were recorded on a Bruker VECTOR-22 IR spectrometer at room temperature (20 °C). The spectra were collected at 16 scans with a spectral resolution of 4 cm−1. Transmission spectra were obtained from a thin film cast on a KBr plate after heating.
Thermogravimetric analysis (TGA) was performed on a TA SDT-Q600 instrument under nitrogen atmosphere at a heating rate of 10 °C min−1 in the range 25 to 600 °C. Differential scanning calorimetry (DSC) was conducted on a Mettler Toledo DSC822e instrument under a nitrogen flow of 50 mL min−1.
The viscoelastic properties of the urushiol-based polybenzoxazine were characterized on a TA Q800 instrument where tensile mode with a ramp rate of 3 °C min−1 and a frequency of 10 Hz in air (20% oxygen) were used. The test of the film was performed in a temperature range of 25 °C to 300 °C. The sample for the DMA experiment was prepared in a rectangular shaped aluminum mold and the sample dimension was 15 × 4 × 0.5 mm3. Tensile measurement was also performed on a TA Q800 instrument at room temperature. The sample with a dimension of 14 × 2 × 0.5 mm3 was stretched at a ramp rate of 0.5 N min−1 until breakage.
Results and discussion
Synthesis of the urushiol-based benzoxazine
The synthesis of urushiol-based benzoxazine precursor is shown in Scheme 2. The novel monomer was prepared via the condensation reaction of urushiol, aniline and paraformaldehyde. The reaction time was determined by the disappearance of starting materials using thin layer chromatography (TLC).
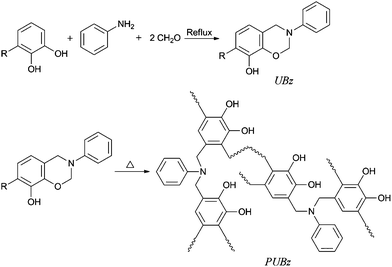 |
| Scheme 2 Synthesis of urushiol-based benzoxazine and the polybenzoxazine. | |
The structure of the monomer was confirmed by 1H NMR, 13C NMR and FTIR. Fig. 1 shows the 1H NMR spectrum of urushiol. Urushiol is composed of different 3-substituted catechol derivatives with 0–3 olefins in the side chains and their polarities are similar. Thus, the integral ratio can not give exactly the amount of hydrogen atoms in the alkyl side chain.41 The three peaks in the range 5.60 to 6.40 ppm are assigned to the protons in –CH
CH–CH
CH–. The peaks from 0.75 to 3.00 ppm are assigned to protons of the saturated bond in the alkyl side group. In comparison with the spectrum of urushiol, we can observe two new resonances centered at 4.59 and 5.40 ppm in the spectrum of UBz (Fig. 2), which are attributed to the protons in Ar–CH2–N and O–CH2–N, respectively. The proton resonance peak of the oxazine ring (O–CH2–N) overlaps that of the hydroxyl. The integral ratio of the aromatic hydrogen atoms to the hydrogen atoms in the oxazine ring agrees well with the theoretical value. Specifically, the relative integration ratios for the resonance signals at δ 7.24, 7.09, 6.92, 6.64, 6.49 and 4.58 ppm are 1.1, 1, 0.5, 0.5, 0.5 and 1, respectively. The 13C NMR spectrum of UBz in Fig. 3 shows the resonances at 49.91 and 80.28 ppm, which are characteristic for a benzoxazine. The facts further indicate the UBz structure.
Fig. 4 shows the FTIR spectra of urushiol and UBz at room temperature. The bands at 948 and 985 cm−1 in the spectra of UBz and urushiol are assigned to the bending vibration of the conjugated double bond, and that at 3009 cm−1 is assigned to the stretching vibration of the isolated double bond. The broad band at 3200 to 3600 cm−1 is due to the –OH vibration. In comparison with urushiol, UBz exhibits a band at 959 cm−1 corresponding to the out-of-plane C–H vibration of the benzene ring to which the oxazine ring is attached and a band at 1255 cm−1 due to the asymmetric stretching of C–O–C of benzoxazine. Clearly, FTIR also confirms the structure of UBz.
Thermally activated polymerization
Thermally activated polymerization of UBz was examined by FTIR and DSC. Fig. 4 shows a sharp band at 3548 cm−1 due to free –OH in the monomer. After polymerization, the shoulder at 3410 cm−1 appears due to the formation of hydrogen bonds.42,43 In the fingerprint area of the spectra, the intensity of the band 959 cm−1, the characteristic benzene ring mode of benzoxazine, dramatically decreases at 140 °C indicating that the oxazine ring opens at that temperature. The change that occurs at a relatively low temperature is attributed to the catalysis of the hydroxyl groups in UBz.43–45 It is reported that aminoalkylation occurs at both the ortho and para positions to the 1-hydroxyl on the aromatic ring to form a Mannich base bridge structure in the ring-opening reaction of benzoxazine.46 Here, since the ortho position is already substituted, the attachment of oxazine can only occur at the para position. This is confirmed by the new band at 1715 cm−1 for the overtone of penta-substituted benzene ring. The fact also indicates the PUBz structure. The intensity of the band at 1635 cm−1 greatly increases after polymerization because the original hydroxyl group turns into a quinone. The bands at 3009, 985 and 948 cm−1 disappear after the reaction, suggesting that all the olefins react with each other yielding a cross-linked polymer.39
Fig. 5 shows the DSC thermogram. The onset of the exotherm for the ring opening polymerization is at 181 °C. The maximum exotherm located at 211 °C is 141 J g−1. Such a small exotherm allows a small shrinkage during the curing. Moreover, since only one exotherm is observed in the DSC thermogram, the ring opening polymerization of the urushiol-based benzoxazine and the reaction between double bonds should happen at around 211 °C.47 The amount of exotherm decreases to 102 J g−1 after heating at 100 °C for one hour, indicating the ring-opening of oxazine occurs. The exotherm disappears after heating at 140 °C for one hour, indicating the completion of the reaction. This is further confirmed by the dramatic decrease of the intensity of the band at 959 cm−1 in FTIR. On the other hand, PUBz cured at 200 °C does not show an exotherm in the DSC thermogram (Fig. 5), and the bands for double bonds in the FTIR spectrum vanish (Fig. 4), clearly indicating the completion of the ring-opening reaction and cross-linking of olefins. Note that the urushiol does not show an exotherm in the range of 50 to 300 °C (Fig. 5). This is because the large amount of aromatic hydroxyl groups in urushiol act as an inhibitor for the reaction between olefins. In the case of UBz, some hydroxyls are involved in the ring-opening reaction, which greatly decreases the inhibition. Thus, the olefins can slowly react, reflecting in the slow decrease and finally the disappearance of bands of olefins in the FTIR.
Thermogravimetric analysis
The TGA profile of cured UBz is shown in Fig. 6. The temperatures corresponding to 5% and 10% weight loss (T5 and T10) are 325 and 357 °C, respectively. They are close to those of the typical polybenzoxazine, i.e., poly(3-phenyl-3,4-dihydro-2H-1,3-benzoxazine (PP-a). The char yield at 600 °C for the urushiol-based benzoxazine is 22%, less than that of PP-a (46%).19
Dynamic mechanical analysis (DMA)
Fig. 7 displays DMA curves of the urushiol-based polybenzoxazine. At 30 and 100 °C, the storage modulus (G′) values are 607 and 213 MPa, respectively, whereas the loss modulus (G′′) values are 51 and 45 MPa. For PP-a, the corresponding G′ and G′′ are 1.9 × 103 and 10 MPa.19 Since the storage modulus reflects the stiffness, PUBz exhibits better flexibility than PP-a. Fig. 7 also shows that G′ sharply decreases at ca. 100 °C. We can observe two peaks at 104 and 49 °C in the loss modulus. The former is attributed to α transition or glass transition, whereas the latter is attributed to β transition associated with the formation of intermediate structures that are not completely incorporated into the network.48,49 Glass transition temperature (Tg) values of the urushiol-based polybenzoxazine are 104 and 140 °C from G′′ and tan δ, respectively, which are somewhat lower than those of PP-a. The decrease of Tg can be attributed to the flexible alkyl chains in PUBz, which has a lower energy barrier for motion.
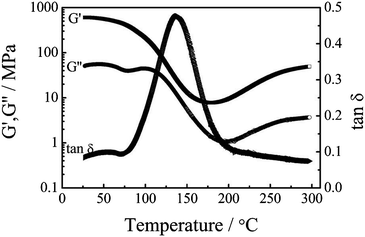 |
| Fig. 7 DMA curves of PUBz. | |
Mechanical properties
The tensile stress–strain curve for the urushiol-based polybenzoxazine film is shown in Fig. 8. The urushiol-based polybenzoxazine film fails at 17.4% of elongation and the strain at the break point is 15.3 MPa. It is reported that the difunctional polybenzoxazine or poly[6,6'-(1-methylethylidene) bis(3,4-dihydro-3-phenyl-2H-1,3-benzoxazine] (PB-m) and the polysiloxane modified difunctional polybenzoxazine have elongation at break of 1.3% and 5.7%, respectively.15,50 Clearly, the elongation of PUBz is larger than those of the above polybenzoxazines. Namely, PUBz has a high toughness. The tensile strength and elongation at break are affected by intermolecular packing, free volume, molecular architecture, and molecular weight between cross-links.15 The high toughness of PUBz is attributed to the long hydrocarbon chains in urushiol, which enhances the mobility of segments under load and thereby increases the ultimate elongation. The tensile modulus of PUBz is 87.9 MPa, lower than that of PB-m (4.3 GPa).15 This is because of the presence of the flexible alkyl chains.
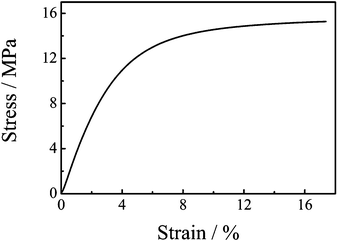 |
| Fig. 8 Stress–strain curve of PUBz. | |
Conclusions
By utilizing a renewable natural product, we have prepared a urushiol-based benzoxazine monomer and polybenzoxazine. The thermally activated polymerization of the benzoxazine happens in solvent-free conditions. The studies on the properties of the polybenzoxazine demonstrate that such a urushiol-based thermosetting polymer exhibits excellent toughness. It is expected to find applications in the future.
Acknowledgements
The financial support of the National Distinguished Young Investigator Fund (20725414), the National Natural Science Foundation of China (21074067) and the Ministry of Science and Technology of China (2007CB936401) is acknowledged.
References
- R. Lu, S. Harigaya, T. Ishimura, K. Nagase and T. Miyakoshi, Prog. Org. Coat., 2004, 51, 238–243 CrossRef CAS.
- J. Kumanotani, Prog. Org. Coat., 1995, 26, 163–195 CrossRef CAS.
- H. Langhals and D. Bathelt, Angew. Chem., Int. Ed., 2003, 42, 5676–5681 CrossRef CAS.
- J. Peisach, W. G. Levine and W. E. Blumberg, J. Biol. Chem., 1967, 242, 2847–2858 CAS.
- R. Oshima and J. Kumanotani, Carbohydr. Res., 1984, 127, 43–57 CrossRef CAS.
- J. Kumanotani, Prog. Org. Coat., 1998, 34, 135–146 CrossRef CAS.
- R. Majima, Ber. Dtsch. Chem. Ges., 1922, 55, 172–191 CrossRef.
- W. F. Symes and C. R. Dawsons, Nature, 1953, 171, 2 CrossRef.
- W. F. Symes and C. R. Dawson, J. Am. Chem. Soc., 1954, 76, 2959–2963 CrossRef CAS.
- S. V. Sunthankar and C. R. Dawson, J. Am. Chem. Soc., 1954, 76, 5070–5074 CrossRef CAS.
- T. Takeichi and T. Agag, High Perform. Polym., 2006, 18, 777–797 CrossRef CAS.
- H. D. Kim and H. Ishida, J. Appl. Polym. Sci., 2001, 79, 1207–1219 CrossRef CAS.
- S. B. Shen and H. Ishida, J. Polym. Sci., Part B: Polym. Phys., 1999, 37, 3257–3268 CrossRef CAS.
- N. N. Ghosh, B. Kiskan and Y. Yagci, Prog. Polym. Sci., 2007, 32, 1344–1391 CrossRef CAS.
- H. Ishida and D. J. Allen, J. Polym. Sci., Part B: Polym. Phys., 1996, 34, 1019–1030 CrossRef CAS.
- X. Ning and H. Ishida, J. Polym. Sci., Part A: Polym. Chem., 1994, 32, 1121–1129 CrossRef CAS.
- B. Kiskan and Y. Yagci, Polymer, 2008, 49, 2455–2460 CrossRef CAS.
- H. Ishida and H. Y. Low, J. Appl. Polym. Sci., 1998, 69, 2559–2567 CrossRef CAS.
- T. Agag and T. Takeichi, Macromolecules, 2003, 36, 6010–6017 CrossRef CAS.
- H. J. Kim, Z. Brunovska and H. Ishida, Polymer, 1999, 40, 6565–6573 CrossRef CAS.
- T. Agag and T. Takeichi, Macromolecules, 2001, 34, 7257–7263 CrossRef CAS.
- Z. Brunovska and H. Ishida, J. Appl. Polym. Sci., 1999, 73, 2937–2949 CrossRef CAS.
- T. Chaisuwan and H. Ishida, J. Appl. Polym. Sci., 2010, 117, 2559–2565 CAS.
- Y. L. Liu, J. M. Yu and C. I. Chou, J. Polym. Sci., Part A: Polym. Chem., 2004, 42, 5954–5963 CrossRef CAS.
- J. Meng and X. Hu, Polymer, 2004, 45, 9011–9018 CrossRef CAS.
- B. Gacal, L. Cianga, T. Agag, T. Takeichi and Y. Yagci, J. Polym. Sci., Part A: Polym. Chem., 2007, 45, 2774–2786 CrossRef CAS.
- T. Takeichi, Y. Saito, T. Agag, H. Muto and T. Kawauchi, Polymer, 2008, 49, 1173–1179 CrossRef CAS.
- H. Ishida and S. Ohba, Polymer, 2005, 46, 5588–5595 CrossRef CAS.
- M. A. Espinosa, M. Galià and V. Cádiz, Polymer, 2004, 45, 6103–6109 CrossRef CAS.
- S. Tragoonwichian, N. Yanumet and H. Ishida, J. Appl. Polym. Sci., 2007, 106, 2925–2935 CrossRef CAS.
- T. Chaisuwan and H. Ishida, J. Appl. Polym. Sci., 2006, 101, 548–558 CrossRef CAS.
- J. Jang and D. Seo, J. Appl. Polym. Sci., 1998, 67, 1–10 CrossRef CAS.
- H. Ishida and Y. H. Lee, J. Appl. Polym. Sci., 2001, 81, 1021–1034 CrossRef CAS.
- H. Ishida and Y. H. Lee, Polymer, 2001, 42, 6971–6979 CrossRef CAS.
- H. M. Huang and S. J. Yang, Polymer, 2005, 46, 8068–8078 CrossRef.
- B. Kiskan and Y. Yagci, Polymer, 2005, 46, 11690–11697 CrossRef CAS.
- T. Takeichi, Y. Guo and T. Agag, J. Polym. Sci., Part A: Polym. Chem., 2000, 38, 4165–4176 CrossRef CAS.
- M. Baqar, T. Agag, H. Ishida and S. Qutubuddin, Polymer, 2011, 52, 307–317 CrossRef CAS.
- E. Cal, A. Maffezzoli, G. Mele, F. Martina, S. E. Mazzetto, A. Tarzia and C. Stifani, Green Chem., 2007, 9, 754 RSC.
- Association of Official Analytical Chemists, AOAC Official Methods of Analysis, Method, 965(32), 1990 Search PubMed.
- J. Xia, J. Lin, Y. Xu and Q. Chen, ACS Appl. Mater. Interfaces, 2011, 3, 482–489 CAS.
- H.-D. Kim and H. Ishida, Macromol. Symp., 2003, 195, 123–140 CrossRef CAS.
- J. Dunkers, E. A. Zarate and H. Ishida, J. Phys. Chem., 1996, 100, 13514–13520 CrossRef CAS.
- B. Kiskan, B. Koz and Y. Yagci, J. Polym. Sci., Part A: Polym. Chem., 2009, 47, 6955–6961 CrossRef CAS.
- R. Kudoh, A. Sudo and T. Endo, Macromolecules, 2010, 43, 1185–1187 CrossRef CAS.
- W. J. Burke, J. L. Bishop, E. L. M. Glennie and W. N. Bauer, J. Org. Chem., 1965, 30, 3423–3427 CrossRef CAS.
- L. Jin, T. Agag, Y. Yagci and H. Ishida, Macromolecules, 2011, 44, 767–772 CrossRef CAS.
- X. Ning and H. Ishida, J. Polym. Sci., Part B: Polym. Phys., 1994, 32, 921–927 CrossRef CAS.
-
G. Strobl, in The Physics of Polymers, Springer, Berlin, 3rd edn, 2007, ch. 6, 245–277, p. 518 Search PubMed.
- H. Ardhyananta, T. Kawauchi, H. Ismail and T. Takeichi, Polymer, 2009, 50, 5959–5969 CrossRef CAS.
|
This journal is © The Royal Society of Chemistry 2012 |
Click here to see how this site uses Cookies. View our privacy policy here.