DOI:
10.1039/C1RA00163A
(Paper)
RSC Adv., 2012,
2, 658-664
Fenton-like ionic liquids/H2O2 system: one-pot extraction combined with oxidation desulfurization of fuel†
Received
10th May 2011
, Accepted 23rd September 2011
First published on 16th November 2011
Abstract
The extraction desulfurization (EDS) and extraction combined with oxidation desulfurization (EODS) for the removal of dibenzothiophene (DBT), benzothiophene (BT), and 4,6-dimethyldibenzothiphene (4,6-DMDBT) in a model oil were carried out in Fenton-like ionic liquids, such as [Et3NHCl]FeCl3, [Et3NHCl]CuCl2, [Et3NHCl]ZnCl2, [Et3NHCl]CoCl2, [Et3NHCl]SnCl2 and [Et3NHCl]CrCl3. The deep desulfurization could be achieved in [Et3NHCl]FeCl3 for only 5 min at room temperature. The reaction conditions such as temperature, the molar ratio of H2O2 and DBT and the amount of ionic liquid (IL) were investigated in the EODS system. By controlling the way of adding H2O2 into the desulfurization system, the sulfur content in the model oil could decrease from 500 mg L−1 to less than 10 mg L−1 at the IL/oil volume of 1
:
5. The oxidation reactivity of the different sulfur-containing compounds was found to be in the order of DBT > BT > 4,6-DMDBT. Moreover, the EODS system could be recycled ten times with a slight decrease in activity to model oil. EODS process was applied to prehydrotreated gasoline and the sulfur content could decrease from 150 to 15 mg L−1 after two rounds of reaction.
Introduction
Currently, the deep desulfurization of fuel oil has attracted wide interest.1 Many countries have made stringent environmental regulations to limit the sulfur level in gasoline and diesel oil.2 Some refractory sulfur compounds, such as dibenzothiophene (DBT) and its derivatives are difficult to remove via conventional hydrodesulfurization, due to their aromaticity and steric hindrance.2–4 Therefore, much attention has been focused on the alternative desulfurization technologies.5–7
In the past several years, nonhydrogenation desulfurization methods, such as the processes of oxidation7–15 and extraction16–21 have been explored. Among these processes, oxidative desulfurization (ODS) has attracted wide interest owing to its advantages like mild conditions, high efficiency and selectivity.3 The ODS process was usually achieved through two steps. Firstly, organic sulfides were selectively oxidized to sulfoxides and sulfones, which further needed to be removed by appropriate extractants or adsorbents.22–24 Recently, oxidative desulfurization with hydrogen peroxide combined with extraction has been considered as one of the most promising processes. DBT and its derivatives can be oxidized to their corresponding sulfoxides and sulfones easily in the ODS process, and can be removed by extraction with organic solvents.3,22 However, the volatile organic compounds employed as extractants result in further environmental concerns.
Ionic liquids (ILs) have received great attention as a new kind of “green solvent”.25–27 The new process for sulfur removal through extraction desulfurization with ILs has been reported in the literature. Many types of ILs have been employed in extraction desulfurization. However, the desulfurization efficiency is relatively low caused by the similar polarity between the sulfur-containing molecules and remaining diesel fuels. As a result, the method of the one-pot chemical oxidation combined with ionic liquids extraction has been developed,28–33 which could improve the desulfurization efficiency effectively. Recently, a liquid–liquid extraction and catalytic oxidative desulfurization (ECODS) system composed of a catalyst, H2O2 and ionic liquid ([bmim]BF4) has been found to be suitable for the deep removal of refractory sulfur compound DBT in a model oil by our group.34–39 The S-removal could achieve deep desulfurization, which was the remarkable advantage of this process over the desulfurization by sole solvent extraction with IL. However, in this ECODS system a higher temperature was required while the reaction time was longer. Besides that, ionic liquids are rather expensive and only act as extractants in the ECODS system.
The iron-based ionic liquids have been employed in many organic reactions, however most attention was paid to the character of the Lewis acid.40–41 Up to now, few studies on its oxidation–reduction character were reported, especially using a Fenton-like agent with H2O2 in oxidative desulfurization. Our group found that a Fenton-like ionic liquid [(n-C8H17)3NCH3]FeCl4 could act as a phase-transfer catalyst in oxidative desulfurization and exhibited high catalytic activity.42 However, this ionic liquid is expensive and the solubility in model oil is relatively big. In this work, inexpensive [Et3NHCl]FeCl3 was synthesized from low cost raw materials and showed good desulfurization efficiency using H2O2 in a one-pot extraction combined with oxidation desulfurization (EODS) system. The solubility of [Et3NHCl]FeCl3 in a model oil was improved greatly. Deep desulfurization could be achieved in [Et3NHCl]FeCl3/H2O2 at room temperature in a very short time (5 min). The ionic liquid acted not only as the catalyst but also as an extractant in the process of desulfurization.
Experimental
Preparation of model oil and ionic liquids
2.932 g DBT was dissolved in 1000 mL n-octane to form the model oil, the sulfur content of which was 500 mg L−1. Other kinds of model oil were prepared with the same method-by dissolving BT and 4,6-DMDBT in n-octane with sulfur contents of 250 mg L−1 and 250 mg L−1, respectively.
[Et3NHCl]FeCl3, [Et3NHCl]CuCl2, [Et3NHCl]ZnCl2, [Et3NHCl]CoCl2, [Et3NHCl]SnCl2 and [Et3NHCl]CrCl3 were synthesized as mentioned in the literature procedure.41,43 The structure has been identified by IR and Raman and the results were listed in the ESI,† Fig. S2.
EDS and EODS of the model oil
Both the EDS and EODS were carried out in a 40 mL two-necked double-deck flask. The mixture in the EDS system, containing 5 mL of model oil and the required amount of IL was stirred with magnetic agitation at 30 °C in the water circulating thermostatic bath. The mixture in the EODS system, containing 5 mL of model oil, 30 wt.% H2O2 aqueous solution [n(H2O2)/n(DBT) = 6] and 2 mL of IL, was stirred with magnetic agitation at 30 °C in the water circulating thermostatic bath.
Analysis of sulfur content in the model oil and prehydrotreated gasoline
The sulfur content in the model oil was tested by gas chromatography (GC) (Agilent 7890A). After the reaction, the upper phase (model oil) was withdrawn at room temperature and analyzed by GC with tetradecane as the internal standard, coupled with a flame ionization detector (FID). A 30 m × 0.32 mm inner diameter × 0.25 μm film thickness HP-5 capillary column was used for the separation. The carrier gas was high purity nitrogen and the flow rate was 25 mL min−1. Hydrogen and air flow rates were 30 mL min−1 and 400 mL min−1, respectively. The GC process for DBT and BT started at 100 °C and the temperature was raised to 200 °C at 15 °C min−1. The GC process for 4,6-DMDBT started at 100 °C and the temperature was raised to 160 °C at 20 °C min−1 and then raised to 230 °C at 25 °C min−1. The injector temperature was 300 °C and detector temperature was 250 °C. The conversion of DBT, BT and 4,6-DMDBT in the model oil was used to calculate the removal of sulfur compounds. For example, sulfur removal of DBT is calculated by the equations below: |  |
(2)
|
The system was applied to the oxidation of prehydrotreated gasoline (150 mg L−1 S, Jiangsu Jia Yu Xin Industrial Co., Ltd.) under optimal conditions. The total sulfur content in prehydrotreated gasoline was analyzed by microcoulometric analyzer (WK-2D, Jiangsu Jiangfen Electroanalytical Instrument Co., Ltd. China, detection limit: 0.5 ppm).
[Et3NHCl]FeCl3 and n-octane were mixed at 30 °C for 10 min in order to prepare the sample of IL-saturated n-octane. The sample of IL-saturated n-octane, [Et3NHCl]FeCl3 and n-octane were analyzed with HPLC (Agilent Technologies 1200 series equipped with a UV-Vis detector under 248 nm wavelength; column, Eclipse XDB-C18 (5 μm, 4.6 × 150 mm); temperature, 25 °C; mobile phase, V(methanol): V(water) = 80
:
10; flowrate, 1.0 mL min−1).
Results and discussion
Influence of the anion of ionic liquid on the removal of DBT
The influence of various types of anion in ILs on the oxidation of DBT was investigated at 30 °C and the volume ratio of IL to model oil was 2
:
5. The results in two different desulfurization systems, including EDS and EODS systems are shown in Fig. 1. As can be seen, compared with [Et3NHCl]FeCl3, [Et3NHCl]CuCl2, [Et3NHCl]ZnCl2, [Et3NHCl]CoCl2, [Et3NHCl]SnCl2 and [Et3NHCl]CrCl3 ionic liquids, the ability for both EDS and EODS of [Et3NHCl]FeCl3 was better. The sulfur removal of DBT in the model oil could only get to 56.8% in the extraction desulfurization system with [Et3NHCl]FeCl3. With the addition of H2O2, the desulfurization efficiency increased greatly, reaching 97.1%. However, the sulfur removal in the desulfurization systems containing other ILs with the same cation was all below 45%. The experimental results indicate that the type of anion in ILs is critical for the removal of DBT in the model oil. As a result, iron-based IL show the highest desulfurization activity among all of the listed ILs.
![Comparison of different ionic liquids in EDS and EODS systems. Experimental conditions: EDS: T = 30 °C, t = 10 min, model oil = 5 mL, IL = 2 mL; EODS: T = 30 °C, t = 5 min, model oil = 5 mL, IL = 2 mL, [n(H2O2)/n(DBT) = 6].](/image/article/2012/RA/c1ra00163a/c1ra00163a-f1.gif) |
| Fig. 1 Comparison of different ionic liquids in EDS and EODS systems. Experimental conditions: EDS: T = 30 °C, t = 10 min, model oil = 5 mL, IL = 2 mL; EODS: T = 30 °C, t = 5 min, model oil = 5 mL, IL = 2 mL, [n(H2O2)/n(DBT) = 6]. | |
The oxidative desulfurization agreed with the mechanism of extraction combined with oxidation desulfurization.35Sulfur compounds were extracted into IL firstly, and then were oxidized by a oxidizing agent. DBT was firstly oxidized to sulfoxide, and then to sulfone. The remanent sulfur in the model oil was non-oxidated sulfur compounds, which could be testified by gas chromatography-flame ionization detector (GC-FID). Oxidated S-compounds could not be detected by GC-FID in oil phase. To the S-compounds in the IL phase, tetrachloromethane (CCl4) was used to re-extract S-compounds from the IL phase, and then the resulting CCl4 solution was analyzed by GC-FID. The results indicated that DBT, DBTO and DBTO2 co-existed in the IL phase. This phenomena lay in the very short reaction time (only 5 min). During such a short time, DBT was extracted into the IL, but the oxidation was not finished completely. So DBT, DBTO and DBTO2 co-existed in the IL. These results could further validate the mechanism of EODS.
Influence of Et3NHCl to FeCl3 molar ratio on the removal of DBT
Table 1 shows the results of EDS and EODS with ionic liquids obtained with different molar ratios of FeCl3 to Et3NHCl (Table 1). It can be found that the molar ratio of FeCl3 to Et3NHCl was an important factor influencing the desulfurization efficiency. In the EODS system, the sulfur removal with sole Et3NHCl (2.8%) or anhydrous FeCl3 (57.4%) was lower than that with Fenton-like ILs. Also, the ILs showed good ability for sulfur removal. From the results listed in the Table 1, all of these ILs were also good extractants, and the sulfur removal was above 50%. The difference in the desulfurization efficiency might be caused by the Lewis acidity and viscosities of ILs and so on. With the addition of H2O2, the desulfurization activity increased sharply, especially for the molar ratio of Et3NHCl to FeCl3 equal to 1
:
1, reaching 97.1% sulfur removal (Table 1, entry 3). When the molar ratio of Et3NHCl to FeCl3 was 1
:
0.5 and 1
:
1.5, sulfur removal was 71.6% and 64.6%, respectively. As described previously, the performance of [Et3NHCl]FeCl3 in the EDS and EDOS systems was excellent, so [Et3NHCl]FeCl3 was the ideal ionic liquid among the studied in this work.
Table 1 Comparison of different desulfurization systems of the model oila
Entry |
IL |
Sulfur removal (%) |
EDS
b |
EODSc |
Experimental conditions: T = 30 °C, model oil = 5 mL, IL = 2 mL.
t = 10 min.
t = 5 min, [n(H2O2)/n(DBT) = 6].
m(Et3NHCl) = 1.2451 g.
Results from Li and coworkers.44
|
1 |
Et3NHCl
|
— |
2.8d |
2 |
Et3NHCl/0.5FeCl3 |
50.2 |
71.6 |
3 |
Et3NHCl/FeCl3 |
56.8 |
97.1 |
4 |
Et3NHCl/1.5FeCl3 |
54.6 |
64.6 |
5 |
Anhydrous FeCl3 |
— |
57.4e |
Influence of different temperatures on the removal of DBT
The content of DBT was tested at different temperatures (30 °C, 40 °C, 50 °C and 60 °C) in order to investigate the performance of [Et3NHCl]FeCl3 in the EODS system. The results indicated that an increase in the temperature led to a remarkable decrease in the removal of DBT in the model oil. When the reaction temperature was changed from 30 °C to 60 °C, the final sulfur content increased from 14 mg L−1 to 157 mg L−1. The reason might be the severe decomposition of H2O2 with the increasing temperature, which results in the worse utilization of H2O2 in the oxidative desulfurization. These experimental results indicated that room temperature (30 °C) was the most appropriate.
Influence of H2O2/DBT molar ratio on the removal of DBT
To study the influence of the amount of oxidizing agent on the sulfur removal properties, the oxidation of DBT in the model oil under various H2O2/DBT (O/S) molar ratios was carried out at 30 °C, 40 °C and 50 °C, respectively. The results were shown in Fig. 2, where O/S molar ratios of 2
:
1, 3
:
1, 4
:
1, 5
:
1, 6
:
1, 7
:
1 and 8
:
1 were plotted. The hydrogen peroxide had more opportunity to oxidize DBT and the desulfurization increased as the amount of oxidizing agent increased. The sulfur removal increased from 77.1% (O/S = 2
:
1) to 97.1% (O/S = 6
:
1) at 30 °C for 5 min. When the O/S molar ratio reached 7
:
1 and 8
:
1, the sulfur removal of DBT increased slowly to 97.7% and 98.3%, respectively. It can be also found that the trend of sulfur removal was similar at 40 °C and 50 °C. Therefore, the optimal O/S molar ratio was 6
:
1, owing to the waste of using an excess amount of oxidant.
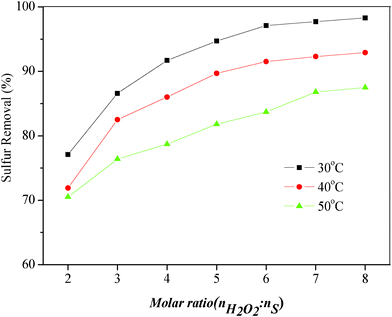 |
| Fig. 2 Influence of H2O2/DBT molar ratio and temperature on sulfur removal of DBT. Experimental conditions: t = 5 min, model oil = 5 mL, IL = 2 mL. | |
Influence of [Et3NHCl]FeCl3 amount on removal of DBT
The independent experiments of extractive desulfurization and extraction combined with oxidative desulfurization of DBT were carried out under the same conditions as the molar ratio of IL and model oil varied from 1
:
10 to 1
:
1 in Fig. 3. The results show that the amount of [Et3NHCl]FeCl3 was a significant parameter influencing the desulfurization efficiency. The sulfur removal of DBT increased with the increase volume ratio of IL and model oil, no matter what desulfurization systems were, such as EDS or EODS. When the volume ratio of IL and model oil was 1
:
10 and 1
:
5, the sulfur removal was bad in both of the two desulfurization systems. As the volume ratio of IL and model oil increased from 2
:
5 to 1
:
1, the sulfur removal of DBT increased slightly from 97.1% to 99.5%. However, the utilization of IL at the IL/oil volume ratio of 1
:
1 would result in wasting resources. Therefore, the most appropriate IL/oil volume ratio was 2
:
5.
![Influence of the different contents of IL on sulfur removal of DBT. Experimental conditions: EDS: T = 30 °C, t = 10 min, model oil = 5 mL; EODS: T = 30 °C, t = 5 min, model oil = 5 mL, [n(H2O2)/n(DBT) = 6].](/image/article/2012/RA/c1ra00163a/c1ra00163a-f3.gif) |
| Fig. 3 Influence of the different contents of IL on sulfur removal of DBT. Experimental conditions: EDS: T = 30 °C, t = 10 min, model oil = 5 mL; EODS: T = 30 °C, t = 5 min, model oil = 5 mL, [n(H2O2)/n(DBT) = 6]. | |
To achieve the aim of reducing the dosage of [Et3NHCl]FeCl3, a series of experiments through adding H2O2 in batches were designed and the results are shown in Table 2. The gross amounts of H2O2 was the same with the above experiments, and the O/S molar ratio was 6
:
1. Under the reaction conditions of 30 °C for 10 min, 3.0 equivalent H2O2 with DBT was added into the desulfurization system at the time of 0 min and 5 min in turn, respectively. From the data in Table 2, the sulfur removal could reach 98.3% in the given experiment, when the IL/oil volume ratio decreased to 1
:
5 (Table 2, entry 2). As a result, the cheap and low dosage of IL was better for deep desulfurization.
Table 2 Results of adding H2O2 in batches on removal of DBT under different volume ratio of IL and model oila
Entry |
V(IL)/V(oil) |
Sulfur removal (%) |
Experimental conditions: T = 30 °C, t = 10 min, model oil = 5 mL, n(H2O2)/n(DBT) = 6, 3.0 equivalent H2O2 with DBT was added into the desulfurization system at the time of 0 min and 5 min in turn, respectively.
|
1 |
2 : 5 |
99.7 |
2 |
1 : 5 |
98.3 |
3 |
1 : 10 |
78.2 |
Influence of the substrate nature
In the experiments described above, it can be verified that DBT in the model oil could be removed effectively in the EODS system. To research the performance of the [Et3NHCl]FeCl3 on the different sulfur-containing compounds, DBT, BT and 4,6-DMDBT were chosen as substrates in the present study (Scheme 1). The results shown in Table 3 show that the S-removal through EODS decreased in the order DBT > BT > 4,6-DMDBT.
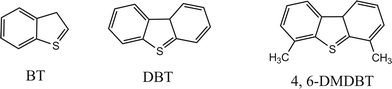 |
| Scheme 1 Molecular structure of sulfur-contaning compounds. | |
Table 3 Results of different substrates in the desulfurization system
Entry |
Substrates |
S-removal (%) |
K
N in mg (S) L (IL)−1/mg (S) L (oil)−1b |
Electron densityc |
EODSa |
EDS
b |
Experimental conditions: T = 30 °C, t = 5 min, model oil = 5 mL, V([Et3NHCl]FeCl3) = 2 mL , [n(H2O2)/n(DBT) = 6].
Experimental conditions: T = 30 °C, t = 10 min, model oil = 5 mL, V([Et3NHCl]FeCl3) = 2 mL.
Results from Otsuki and coworkers.45
|
1 |
DBT
|
97.1 |
56.8 |
3.29 |
5.758 |
2 |
BT |
86.9 |
56.9 |
3.30 |
5.739 |
3 |
4,6-DMDBT
|
82.5 |
37.5 |
1.50 |
5.760 |
The process of the EODS system involved extraction and oxidation in two steps, and substrates were extracted from n-octane before they were oxidized in the IL phase. Therefore, the ability of IL to extract sulfur-containing compounds is an important factor influencing desulfurization efficiency. According to EDS data in Table 3, the Nernst partition coefficients (KN) of DBT, BT and 4,6-DMDBT could be calculated by eqn (1).
| KN = mg (Sulfur) L−1 (IL)/mg (Sulfur) L−1 (oil) | (1) |
For example, removal of DBT, BT and 4,6-DMDBT was 56.8%, 56.9% and 37.5%, respectively, and calculated KN was 3.29, 3.30 and 1.50, respectively. As can be seen by KN, [Et3NHCl]FeCl3 ionic liquid showed a better ability than imidazolium-based IL to extract different sulfur compounds.44 Therefore, the larger KN was, the higher the concentration of sulfur compounds in the IL. A high concentration of substrates led to a high reaction rate. Owing to this reason, DBT, BT and 4,6-DMDBT could be removed effectively in the desulfurization containing [Et3NHCl]FeCl3.
From the data in Table 3, the desulfurization efficiency of 4,6-DMDBT was the lowest. This phenomenon can be explained in the following two aspects. On one hand, 4,6-DMDBT shows much lower KN in comparison with DBT and BT. On the other hand, there are two methyl groups in phenyl, causing the higher steric hindrance to S-atom, forming obstacle in the catalytic oxidation. As for DBT and BT, although the KN of DBT was close to that of BT, the electron density on the sulfur atom of DBT is higher than that of BT45 which led to the highest oxidative reactivity. Therefore, the oxidation reactivity of the different substrates was in the following order of sulfur removal: DBT > BT > 4,6-DMDBT, which is affected by electron density, steric hindrance and KN synergistically.
Regeneration and recycling of ionic liquids
The regeneration and subsequent recycling of ILs are of great importance, so the possibility of recycling the [Et3NHCl]FeCl3 is investigated in the EODS of a DBT-containing model oil. After the reaction, the IL phase (underlayer) was recycled and heated to evaporate the residual oxidizing agents and model oil from the IL at 70 °C. Afterwards, the fresh H2O2 and model oil were added for the next run. The results indicated that the [Et3NHCl]FeCl3 ionic liquid could be recycled four times at 30 °C without a substantial decrease in its activity (Fig. 4). When the IL was recycled for the fifth times and sixth times, the sulfur removal dropped slightly to 95.0% and 93.2%, respectively. According to our observation, as the recycle times increased, more and more DBT sulfone was produced in the IL, which led to the decrease in the extraction performance of IL and the desulfurization activity. In order to testify the above presumption, the regeneration of IL experiments was performed. At the end of each cycle, the IL phase was re-extracted with tetrachloromethane twice at 30 °C in order to remove DBT sulfone from the IL. The regenerated IL was then recycled into the desulfurization. The results indicated that [Et3NHCl]FeCl3 could be recycled ten times with little decrease in desulfurization activity, and sulfur removal only dropped from 97.1% to 96.6%.
![Recycle of [Et3NHCl]FeCl3 ionic liquid in desulfurization system. Experimental conditions: T = 30 °C, t = 5 min, model oil = 5 mL, IL = 2 mL, [n(H2O2)/n(DBT) = 6].](/image/article/2012/RA/c1ra00163a/c1ra00163a-f4.gif) |
| Fig. 4 Recycle of [Et3NHCl]FeCl3 ionic liquid in desulfurization system. Experimental conditions: T = 30 °C, t = 5 min, model oil = 5 mL, IL = 2 mL, [n(H2O2)/n(DBT) = 6]. | |
The solubility of ionic liquids in n-octane is considered as an important factor in choosing an extractant, because the noticeable solubility of IL in the model oil may not only contaminate the fuel but also lead to possible NOx pollution during the process of removing the SOx pollution. According to the method in our previous work,44 samples of IL-saturated n-octane, [Et3NHCl]FeCl3 and n-octane were analyzed with HPLC. As can be seen in Fig. 5, the retention time (tR) of [Et3NHCl]FeCl3 and n-octane was 1.517 min and 3.841 min, respectively. However, there was no peak of from the IL in the chromatogram of the sample of IL-saturated n-octane, which was proof that [Et3NHCl]FeCl3 has negligible solubility in the model oil. Therefore, the problem that has attracted much attention could be solved. The peaks (tR, about 4.7 min) were due to the impurities in n-octane.
![HPLC
chromatograms of [Et3NHCl]FeCl3, n-octane and IL-saturated n-octane. aExperimental conditions: T = 30 °C, t = 10 min, n-octane = 5 mL, IL = 2 mL.](/image/article/2012/RA/c1ra00163a/c1ra00163a-f5.gif) |
| Fig. 5
HPLC
chromatograms of [Et3NHCl]FeCl3, n-octane and IL-saturated n-octane. aExperimental conditions: T = 30 °C, t = 10 min, n-octane = 5 mL, IL = 2 mL. | |
Oxidative desulfurization of prehydrotreated gasoline
EODS process was applied to prehydrotreated gasoline. To prehydrotreated gasoline, the hydrotreatment greatly improved the quality of the fuels and thiols and thiophene which were refractory in the ODS process could be easily removed in the HDS process. The sulfur species mainly remained as DBT and alky-substituted DBTs in prehydrotreated gasoline, which were easily oxidized in the ODS process. The sulfur-containing compounds in the gasoline were oxidized with the [Et3NHCl]FeCl3/H2O2 system under optimal experimental conditions: 5 mL gasoline, T = 30 °C, t = 30 min, V(H2O2) = 0.2 mL, m([Et3NHCl]FeCl3) = 3 mL. The sulfur content decreased from 150 to 31 mg L−1 S after the first round of reactions. Then the oil was moved to another reaction flask and added to fresh H2O2 and IL for next round reaction. With the increase of reaction rounds, the dark yellow gasoline became clearer. The sulfur content could reach 15 mg L−1 after two rounds of reaction. So Fenton-like ionic liquid/H2O2 system is feasible and effective in deep desulfurization of prehydrotreated gasoline.
Reusability of [Et3NHCl]FeCl3 has been performed with prehydrotreated gasoline. After the first reaction, the reaction system was still a biphasic system, in which the IL phase was the under-layer and oil phase was the upper-layer. Therefore, the oil phase could be separated from the biphasic system easily. Afterwards, the fresh H2O2 and prehydrotreated gasoline were added in regenerated IL (the method refers to the model oil) for the next run. The results indicated that the [Et3NHCl]FeCl3 could be recycled four times at 30 °C and sulfur removal was 79.3%, 80.1%, 79.4% and 78.8%, respectively. We compared the Raman spectra of fresh [Et3NHCl]FeCl3 with regenerated [Et3NHCl]FeCl3(Fig. 6), which indicated no transformation of the anion [FeCl4]− (333 cm−1). These results also indicated nitrogen compounds (Lewis bases) in real fuels could not deactivate the catalyst and reduce its reusability, which may attribute to the ·OH mechanism in Fenton-like ionic liquids/H2O2 system.44
![Raman spectra of fresh [Et3NHCl]FeCl3 and recycled regenerated [Et3NHCl]FeCl3.](/image/article/2012/RA/c1ra00163a/c1ra00163a-f6.gif) |
| Fig. 6
Raman spectra of fresh [Et3NHCl]FeCl3 and recycled regenerated [Et3NHCl]FeCl3. | |
Conclusion
In summary, a cheap ionic liquid [Et3NHCl]FeCl3 showed the best desulfurzation efficiency among several kinds of ILs, such as [Et3NHCl]CuCl2, [Et3NHCl]ZnCl2, [Et3NHCl]CoCl2, [Et3NHCl]SnCl2 and [Et3NHCl]CrCl3. The optimal molar ratio of FeCl3 to Et3NHCl was 1
:
1. The reaction time of EODS system was very short, consuming only 5 min. The temperature, the H2O2 to DBT molar ratio, the amount of IL all played important roles in the desulfurization efficiency. The sulfur removal could reach 98.3% at room temperature, when the IL/oil volume ratio was 1
:
5 and the H2O2 was added into the desulfurization system at the time of 0 min and 5 min in turn for 10 min. The oxidation reactivity of the different substrates was in the following order: DBT > BT > 4,6-DMDBT. Moreover, [Et3NHCl]FeCl3 was hardly miscible with the model oil. The EODS system could be recycled ten times with a slight decrease in sulfur removal. The sulfur content in prehydrotreated gasoline could decrease from 150 to 15 mg L−1 S after two rounds of reaction. This research extended the function of Lewis acidic IL Et3NHCl/FeCl3 and developed a simple method for deep desulfurization of fuels.
Acknowledgements
This work was financially supported by the National Nature Science Foundation of China (No. 20876071, 21076099, No. 21106055), Specialized Research Fund for the Doctoral Program of Higher Education of China (No. 20103227110016), Postdoctoral Foundation of China (No.20090461067, No.201003556), The Natural Science Foundation of Jiangsu Province (No. BK2011506).
References
- P. S. Kulkarni and C. A. M. Afonso, Green Chem., 2010, 12, 1139 RSC.
- M. C. Capel-Sanchez, J. M. Campos-Martin and J. L. G. Fierro, Energy Environ. Sci., 2010, 3, 328 RSC.
- C. Li, Z. X. Jiang, J. B. Gao, Y. X. Yang, S. J. Wang, F. P. Tian, F. X. Sun, X. P. Sun, P. L. Ying and C. R. Han, Chem.–Eur. J., 2004, 10, 2277 CrossRef CAS.
- J. M. Campos-Martin, M. C. Capel-Sanchez, P. Perez-Presas and J. L. G. Fierro, J. Chem. Technol. Biotechnol., 2010, 85, 879 CrossRef CAS.
-
M. Feng, Recent Pat. Chem. Eng., 2010, 3, 30 Search PubMed.
- E. Ito and J. A. Rob van Veen, Catal. Today, 2006, 116, 446 CrossRef CAS.
- A. Anisimov and A. Tarakanova, Russ. J. Gen. Chem., 2009, 79, 1264 Search PubMed.
- A. Nisar, J. Zhuang and X. Wang, Adv. Mater., 2011, 23, 1130 CrossRef CAS.
- C. Komintarachat and W. Trakarnpruk, Ind. Eng. Chem. Res., 2006, 45, 1853 CrossRef CAS.
- J. M. Campos-Martin, M. C. Capel-Sanchez and J. L. G. Fierro, Green Chem., 2004, 6, 557 RSC.
- Y. Wang, G. Li, X. S. Wang and C. Z. Jin, Energy Fuels, 2007, 21, 1415 CrossRef CAS.
- D. Huang, Z. Zhai, Y. C. Lu, L. M. Yang and G. S. Luo, Ind. Eng. Chem. Res., 2007, 46, 1447 CrossRef CAS.
- X. Jiang, H. M. Li, W. S. Zhu, L. N. He, H. M. Shu and J. D. Lu, Fuel, 2009, 88, 431 CrossRef CAS.
- R. Sundararaman, X. L. Ma and C. S. Song, Ind. Eng. Chem. Res., 2010, 49, 5561 Search PubMed.
- H. Y. Lü, J. B. Gao, Z. X. Jiang, Y. X. Yang, B. Song and C. Li, Chem. Commun., 2007, 150 RSC.
- A. Bösmann, L. Datsevich, A. Jess, A. Lauter, C. Schmitz and P. Wasserscheid, Chem. Commun., 2001, 2494 RSC.
- F. T. Li, Y. Liu, Z. M. Sun, L. J. Chen, D. S. Zhao, R. H. Liu and C. G. Kou, Energy Fuels, 2010, 24, 4285 Search PubMed.
- E. Kuhlmann, M. Haumann, A. Jess, A. Seeberger and P. Wasserscheid, ChemSusChem, 2009, 2, 969 CrossRef CAS.
- Y. Nie, C. X. Li, A. J. Sun, H. Meng and Z. H. Wang, Energy Fuels, 2006, 20, 2083 CrossRef CAS.
- N. H. Ko, J. S. Lee, E. S. Huh, H. Lee, K. D. Jung, H. S. Kim and M. Cheong, Energy Fuels, 2008, 22, 1687 CrossRef CAS.
- H. S. Gao, M. F. Luo, J. M. Xing, Y. Wu, Y. G. Li, W. L. Li, Q. F. Liu and H. Z. Liu, Ind. Eng. Chem. Res., 2008, 47, 8384 CrossRef CAS.
- Y. Shiraishi, K. Tachibana, T. Hirai and I. Komasawa, Ind. Eng. Chem. Res., 2002, 41, 4362 CrossRef CAS.
- X. L. Ma, A. N. Zhou and C. S. Song, Catal. Today, 2007, 123, 276 CrossRef CAS.
- A. Ishihara, D. H. Wang, F. Dumeignil, H. Amano, E. W. Qian and T. Kabe, Appl. Catal., A, 2005, 279, 279 CrossRef CAS.
- H. Olivier-Bourbigou, L. Magna and D. Morvan, Appl. Catal., A, 2010, 373, 1 CrossRef CAS.
- H. Zhao, S. Q. Xia and P. S. Ma, J. Chem. Technol. Biotechnol., 2005, 80, 1089 CrossRef CAS.
-
P. Wasserscheid and T. Welton, Ionic Liquid in Synthesis, Wiley-VCH: Weinheim, 2003 Search PubMed.
- W. H. Lo, H. Y. Yang and G. T. Wei, Green Chem., 2003, 5, 639 RSC.
- E. Lissner, W. F. de Souza, B. Ferrera and J. Dupont, ChemSusChem, 2009, 2, 962 CrossRef.
- F. T. Li, R. H. Liu, J. H. Wen, D. S. Zhao, Z. M. Sun and Y. Liu, Green Chem., 2009, 11, 883 RSC.
- D. S. Zhao, J. L. Wang and E. P. Zhou, Green Chem., 2007, 9, 1219 RSC.
- H. S. Gao, C. Guo, J. M. Xing, J. M. Zhao and H. Z. Liu, Green Chem., 2010, 12, 1220 RSC.
- W. Zhang, K. Xu, Q. Zhang, D. L. Liu, S. Y. Wu, F. Verpoort and X. M. Song, Ind. Eng. Chem. Res., 2010, 49, 11760 Search PubMed.
- W. S. Zhu, H. M. Li, X. Jiang, Y. S. Yan, J. D. Lu and J. X. Xia, Energy Fuels, 2007, 21, 2514 CrossRef CAS.
- W. S. Zhu, H. M. Li, X. Jiang, Y. S. Yan, J. D. Lu, L. N. He and J. X. Xia, Green Chem., 2008, 10, 641 RSC.
- L. N. He, H. M. Li, W. S. Zhu, J. X. Guo, X. Jiang, J. D. Lu and Y. S. Yan, Ind. Eng. Chem. Res., 2008, 47, 6890 CrossRef CAS.
- H. M. Li, L. N. He, J. D. Lu, W. S. Zhu, X. Jiang, Y. Wang and Y. S. Yan, Energy Fuels, 2009, 23, 1354 CrossRef CAS.
- H. M. Li, W. S. Zhu, Y. Wang, J. T. Zhang, J. D. Lu and Y. S. Yan, Green Chem., 2009, 11, 810 RSC.
- Y. X. Ding, W. S. Zhu, H. M. Li, W. Jiang, M. Zhang, Y. Q. Duan and Y. H. Chang, Green Chem., 2011, 13, 1210 RSC.
- X. J. Cai, S. H. Cui, L. P. Qu, D. D. Yuan, B. Lu and Q. H. Cai, Catal. Commun., 2008, 9, 1173 CrossRef CAS.
- S. Q. Yang, Z. C. Liu, X. H. Meng and C. M. Xu, Energy Fuels, 2009, 23, 70 CrossRef CAS.
- Y. Q. Jiang, W. S. Zhu, H. M. Li, S. Yin, H. Liu and Q. J. Xie, ChemSusChem, 2011, 4, 399–403 Search PubMed.
-
F. G. Sherif, L. J. Shyu, C. C. Greco, US Patent., 5824832, October 20, 1998 Search PubMed.
- J. T. Zhang, W. S. Zhu, H. M. Li, W. Jiang, Y. Q. Jiang, W. L. Huang and Y. S. Yan, Green Chem., 2009, 11, 1801 RSC.
- S. Otsuki, T. Nonaka, N. Takashima, W. H. Qian, A. Ishihara, T. Imai and T. Kabe, Energy Fuels, 2000, 14, 1232 CrossRef CAS.
|
This journal is © The Royal Society of Chemistry 2012 |
Click here to see how this site uses Cookies. View our privacy policy here.