DOI:
10.1039/C1CE05830D
(Paper)
CrystEngComm, 2012,
14, 256-263
Apple pectin-mediated green synthesis of hollow double-caged peanut-like ZnO hierarchical superstructures and photocatalytic applications†
Received
2nd July 2011
, Accepted 12th September 2011
First published on 14th October 2011
Abstract
Hollow ZnO superstructures have potential technological applications. With this motivation, a simple approach is developed to prepare hollow double-caged peanut-like ZnO hierarchical superstructures with the assistance of apple pectin. The biotemplate-assisted approach concurs with “green” chemistry as it is simple and environmentally friendly. The products are characterized by scanning electron microscopy (SEM) and X-ray diffraction (XRD). The results reveal that the pectin-directed hydrothermal process is essential to obtain the final products. The morphologies and dimensions of the ZnO structures could be easily tuned by varying the molar ratios of the pectin to zinc ion, the amount of ammonia, the reaction time and the temperature. A possible formation mechanism for the hollow superstructures is described. In addition, the optical properties of the ZnO superstructures were investigated in some detail. The as-prepared samples showed high photocatalytic activity towards methyl orange (MO) under ultraviolet (UV) irradiation.
Introduction
Great interest has been attracted by self-assembly of micro- and nano-structured building blocks into hierarchical structures in recent decades. Particularly, nanocrystals with hollow structures have attracted considerable attention, owing to their unique structural, optical, and electrical properties.1–6 Therefore, they have wide applications including as electrodes for dye-sensitized solar cells, carriers for drug delivery systems, and other potential applications.7–11
Zinc oxide (ZnO) is one of the most suitable semiconducting materials with a wide bandgap (3.37 eV), because of its non-toxic nature and low-cost. Hence, ZnO is considered as a workhorse of technological development that exhibits excellent electrical, optical, and chemical properties. Thus, it is widely applied in optical devices, piezoelectric devices, sensors, solar cells, etc.12–18 In general, their physical and chemical properties are greatly dependent on the shape, crystalline structure, and size of the ZnO structures.19 As a result, a variety of ZnO structures with different morphologies and dimensions have been constructed, including prisms,20 ellipsoids,21 cages,22 spheres,23 tubes,24 hollow shells,25 wires,26 rods,27 flowers,28 and dumbbells.29 Accordingly, many methods have been developed, mainly involving hydrolysis in polyol media,30 chemical-precipitation,31 microwave heating,32thermal evaporation,22 templating,33 thermal oxidation processes34 and hydrothermal syntheses.28,35 Among them, the hydrothermal method is a facile, cost-effective, and scalable method. Its additional advantages are that the final product contains highly-crystalline powders with a narrow size distribution and high purity without heat treatment at high temperatures.36,37 Recently, solid dumbbell-like ZnO microcrystals were prepared by a hydrothermal process.35,38
Self-assembly of micro- or nano-structured hollow ZnO superstructures has wide practical/potential applications.29,39 The most prevalent strategy is using templates,4,23 hard or soft, to guide the formation of hollow structures. Alternatively, bio-inspired synthesis has been emerging as an important environmentally friendly route to prepare inorganic materials with controlled morphologies by self-assembly of organic superstructures, inorganic or organic additives, and templates with complex functionalization patterns.40,41 Consequently, the hydrocarbon chains tend to self-associate to minimize contact with the water molecules, resulting in the formation of various self-organized assemblies. The emerging surfactant-mediated templating and crystallization technique is widely used in shape and size control of the nanocrystals and superstructures.42 Its common feature is that ordered inorganic structures are a promising choice.43
Recently, supramolecular-directed self-assembly of inorganic nanostructures has become another active project. The supramolecular structures can serve as functional polymer templates for synthesis of novel inorganic nanoarchitectures, which has proved effective and versatile.44 For example, using sodium carboxymethyl cellulose as a crystal growth modifier, hierarchically complex hollow superstructures have been prepared by assembly of ZnO nanorods.39 In another example, dumbbell-like ZnO hollow architectures have been synthesized by the long-chain poly(sodium 4-styrenesulfonate)-assisted hydrothermal method.29 Recently, hollow flower-like ZnO superstructures have been obtained by a mannite-supported hydrothermal method in our lab.28
Pectin, a natural water soluble biopolymer extracted from plant cell walls, is one of the anionic polysaccharides. The typical chemical structure (Fig. 1) includes a backbone chain of 1,4-linked R-D-galacturonic acid units interrupted by 1,2-linked L-rhamnopyranosyl residues in adjacent or alternate positions. Here, we choose the pectin extracted from apples. Taking advantage of the assembling function of this molecule, hierarchically complex hollow superstructures have been constructed through the assembly of ZnO nanorods to form double-caged peanut-like hollow structures. The as-prepared products display strong photocatalytic efficiency in the photodegradation of methyl orange (MO). In addition, their possible growth mechanism is discussed in some detail.
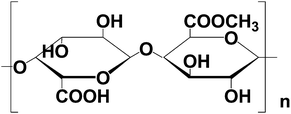 |
| Fig. 1 The typical chemical structure of pectin. | |
Experimental section
All the reagents were analytical grade and used without further purification. The typical experimental details are described as follows: 25 mL of an aqueous solution of zinc acetate dehydrate (0.220 g, 1 mmol) and 0.014 g of pectin were mixed together and maintained with mild magnetic stirring for 10 min. Then, 1.5 mL ammonia was slowly added into the above solution. After 15 min of stirring, the final aqueous solution was transferred into a 30 mL Teflon-lined stainless steel autoclave, sealed tightly, treated hydrothermally at 120 °C for 2 h and then cooled to room temperature naturally. The precipitates were collected, thoroughly washed with water and ethanol, and dried at 60 °C in vacuum. Control experiments with different amounts of pectin or ammonia, different alkaline substances and different temperatures were performed, respectively. Additionally, time-dependent experiments were conducted to study the growth mechanism of the ZnO structures.
Characterization
The crystal structure of the prepared ZnO products was analyzed by X-ray diffraction (XRD). The patterns were recorded using a Bruker-D8-AXS diffractometer system equipped with a Cu-Kα radiation (Bruker Co., Germany). The morphology and dimensions of the ZnO products were observed by scanning electron microscopy (SEM, JSM-6390LV, Japan). The UV-vis spectra of the ZnO samples were measured on a TU-1810 UV-vis spectrophotometer.
Measurement of photocatalytic activity
The photocatalytic ability of the prepared samples was evaluated through the photocatalytic decolorization of methyl orange (MO, Amresco Inc.) in aqueous solution at ambient temperature. Experiments were described as follows: 20 mg of the prepared ZnO powder was dispersed in a 60 mL MO (30 mg L−1) solution in a cylinder cell (bulk volume is 250 mL). The solution was allowed to reach an adsorption–desorption equilibrium among the ZnO and MO for 30 min before ultraviolet (UV) light irradiation. A 300 W high-pressure Hg lamp (Yaming Company, Shanghai, 8 cm away from the suspension) was used as a light source to trigger the photocatalytic reaction. After UV irradiation for some time, the reaction solution was filtered to measure the change of the MO concentration by UV-vis experiments.
Results and discussion
The shape and size of the typical product was investigated by SEM experiments (Fig. 2). The sample is mainly composed of peanut-like architectures with a length of about 6 μm (Fig. 2A). Interestingly, the ZnO samples are in fact built from very thin nanorods (ca. 100 nm in size), which spontaneously pile up together to form a peanut-like architecture (Fig. 2B–C). Moreover, there is a “wheel gear” structure in the middle of the peanut-like architecture. An obvious contrast is seen between the center portion and the edge of the peanut-like structures (Fig. 2B–C), which further confirms the hollow structures. These observations indicate that the hollow double-caged peanut-like ZnO superstructures are obtained. In addition, a typical XRD pattern of the as-prepared ZnO sample is presented (Fig. 2D). All the diffraction peaks can be perfectly indexed to wurtzite-type (space groupP63mc) ZnO. No peaks of impurities are detected in this case. The strong and sharp peaks indicate that the as-prepared product is highly crystalline.
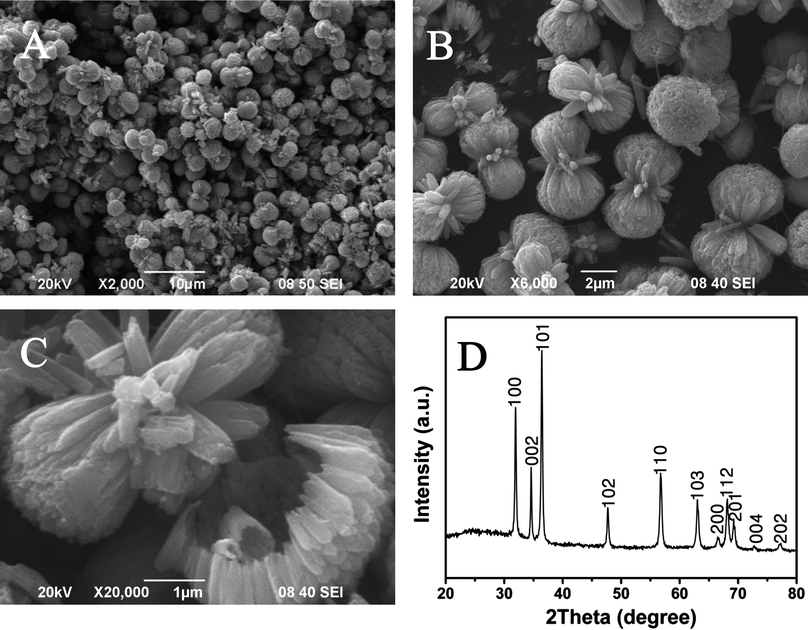 |
| Fig. 2 Morphological and structural characterizations of the as-prepared ZnO products: low (A) and high (B–C) magnification of the SEM images; and the powder XRD pattern of the hollow peanut-like ZnO product (D). | |
Influence of alkaline substances
The morphologies of the ZnO structures closely depend on different alkaline substances, while other conditions are unchanged (Fig. S1, ESI†). When using urea (A), NaOH (B), and HMTA (C) as alkaline substances, the products are microsheets, nanorods, and hexagonal prisms, respectively. In the presence of NaOH, Zn2+ ions preferentially exist as the complex ions of Zn(OH)42−.45 As a result, many tiny white particles formed, moved irregularly, and finally were suspended in solution. When the duration of hydrothermal treatment is prolonged, the precursor finally transformed to ZnO solid particles. However, the addition of urea46 or HMTA could release NH3 slowly and evenly at suitable temperatures. Moreover, the released NH3 could easily coordinate with Zn2+ ions to form Zn(NH3)42+. Nevertheless, ammonia, a good coordinating agent, could provide both NH3 and OH− ions which are beneficial to the formation of the Zn(NH3)42+ and Zn(OH)42− states, respectively.47 Therefore, the rates of nucleation and crystal grain growth of ZnO are related to different anions that could coordinate with Zn2+ ions, and consequently form different morphologies. Evidently, in the presence of ammonia, the final products contained uniform, well-defined double-caged peanut-like hollow structures.
Influence of the amount of ammonia
The presence of ammonia is crucial for the formation of unique double-caged peanut-like ZnO hollow architectures (Fig. 3). Control experiments show that without ammonia, only ZnO hexagonal prisms with rough surfaces are obtained (Fig. S2, ESI†). Using 0.5 mL ammonia, flower-like ZnO structures are obtained (Fig. 3A). The products mainly contain several crystal structures around a single center. The outer crystal structures are divided clearly by boundaries and have almost the same shape and size, consistent with the ZnO growth behavior in alkali solution.48 With 1.0 mL ammonia, ZnO nanorod bundles are observed (Fig. 3B). When the amount of ammonia is increased to 2.0 mL (Fig. 3C), the peanut-like ZnO structures are formed, where the cages of the ZnO structures are thinner, compared to those using 1.5 mL ammonia. When the ammonia content is 2.5 mL (Fig. 3D), only hollow microrods remain. The insets in Fig. 3C–D show that the interior of the superstructures is hollow. However, further increasing the ammonia content to 3.0 mL, almost no product is obtained. This is due to the amphoteric property of ZnO itself.49 To summarize, the amount of ammonia is a key factor for the formation of hollow peanut-like ZnO structures.
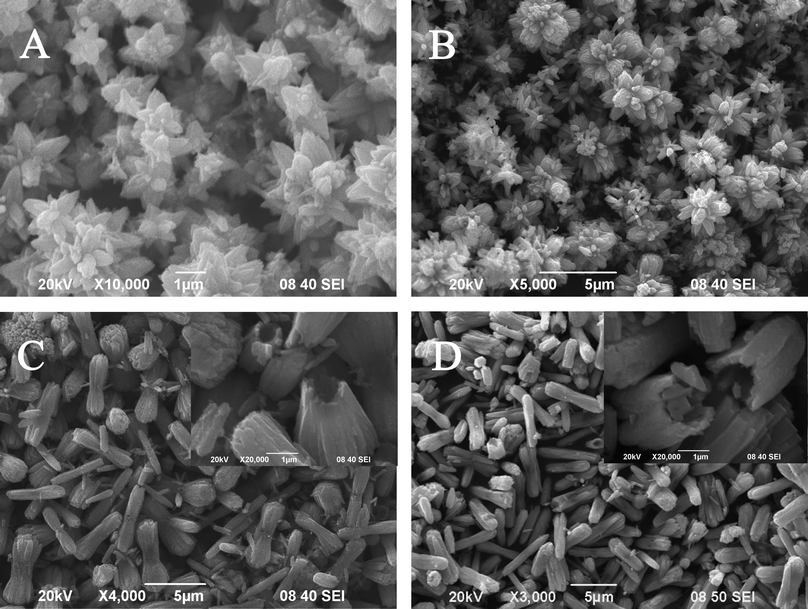 |
| Fig. 3
SEM images of the products prepared with different amounts of ammonia: 0.5 mL (A); 1.0 mL (B); 2.0 mL (C); 2.5 mL (D). Inset: high magnification of the images (C) and (D). | |
Influence of the amount of pectin
The pectin is important for the formation of unique peanut-like ZnO hollow architectures (Fig. S3, ESI†). Using 0.014 g pectin, representative hollow peanut-like ZnO structures are obtained (Fig. 2A–C). When the amount of pectin is reduced to 0.007 g, the products are uniform peanut-like structures (Fig. S3A, ESI†), which are assembled by the ZnO nanorods. In the middle of the structure, there is a “wheel gear”. However, the cages of the ZnO structures are smaller in size, compared to those with 0.014 g pectin. When the amount of pectin is increased to 0.028 g, the products contain uniform and smooth peanut-like structures (Fig. S3B, ESI†). The length of the peanut-like structures is ca. 5 μm, and the surface of the structure is clean. As the amount of pectin is increased to 0.056 g (Fig. S3C, ESI†), the structure is similar to that using 0.028 g pectin.
Pectin is a family of complex polysaccharides with 1,4-linked alpha-galacturonic acid residues on the backbone chain.50 In this sense, pectin may become a model of a biopolymer chain having a high anionic nature, although the carboxyl groups are partly methyl-esterified.51 In addition, pectin shows no coil–helix transition in aqueous solution. This simple behavior may enable an in depth investigation of the chain motion of anionic polyelectrolytes. During the process, pectin not only serves as a soft template to confine the growth of ZnO nanorods, but also serves as an assembling agent to construct the nanorods into the hollow superstructures.
Growth process and mechanism
Size and shape control over nanocrystals is generally achieved using a template during synthesis via solution processes such as hydrothermal reaction.52 The molecular structure, concentration, and molar ratios of the templates play an important role, as well as other reaction conditions including solvent, alkaline substances, reaction temperature and time, and heating rate.53 In fact, there are synergic effects between the amount of pectin and other reaction conditions, resulting in the evolution of dispersibility and shape transformation of the final products. Therefore, the specific growth mechanism should be further clarified. Accordingly, the reaction temperature and time could be precisely controlled and is discussed below.
Different morphologies are obtained with reaction temperatures between 80 °C and 160 °C (Fig. 4). At 80 °C, the products contain flower-like structures and nearly no branches appeared on the petals (Fig. 4A). At 100 °C, the products contain both flower-like and peanut-like structures (Fig. 4B). When the temperature is 120 °C, only peanut-like ZnO structures are observed (Fig. 2A–C). When the temperature is 160 °C, the structures are similar to those observed at 120 °C, while smaller sized peanut-like structures appeared with a length of ca. 4 μm (Fig. 4C). These results demonstrate that the rate of nucleation and crystal grain growth is sensitive to the temperature.
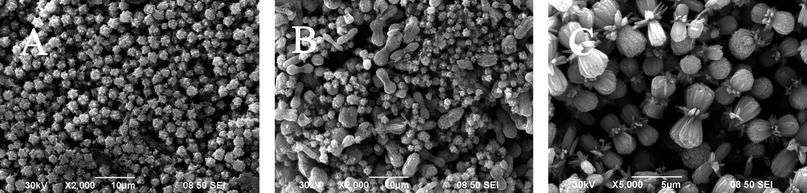 |
| Fig. 4
SEM images of the products obtained at different reaction temperatures: 80 °C (A); 100 °C (B); 160 °C (C). | |
At different temperatures, the precursor undergoes different processes in aqueous alkaline solution, via template-assistant or any other additives. Moreover, at low temperature, the rate of crystal grain growth is higher than that of nucleation. With increasing temperature, the nucleation rate is greatly facilitated, and the formed nuclei aggregate together more easily. This makes adequate space for the crystal growth, and consequently forms peanut-like ZnO structures. Further increasing the temperature, the nucleation rate is much higher than that of crystal grain growth, and hence many crystal nuclei are produced. As shown in Fig. 5B–C, the morphology is determined by the temperature. Obviously, smaller sized products would be generated at higher temperatures.
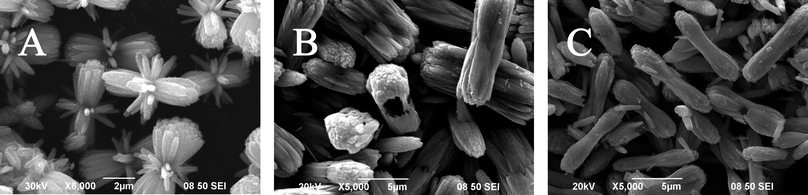 |
| Fig. 5
SEM images of the sample prepared with less ammonia (1.0 mL) at 160 °C for 2 h (A); with more ammonia (2.0 mL) at 120 °C for 24 h (B); and with more ammonia (2.0 mL) at 200 °C for 24 h (C). | |
To investigate the growth process of the peanut-like hollow superstructures obtained at 120 °C, time dependent experiments were carried out. From the SEM images (Fig. 6), the morphological transformations from ZnO nanoparticles to hollow peanut-like structures are clearly observed at different reaction times. When the reaction time is 0.5 h (Fig. 6A), the products contain flower-like structures, and almost no branches appeared on the petals.
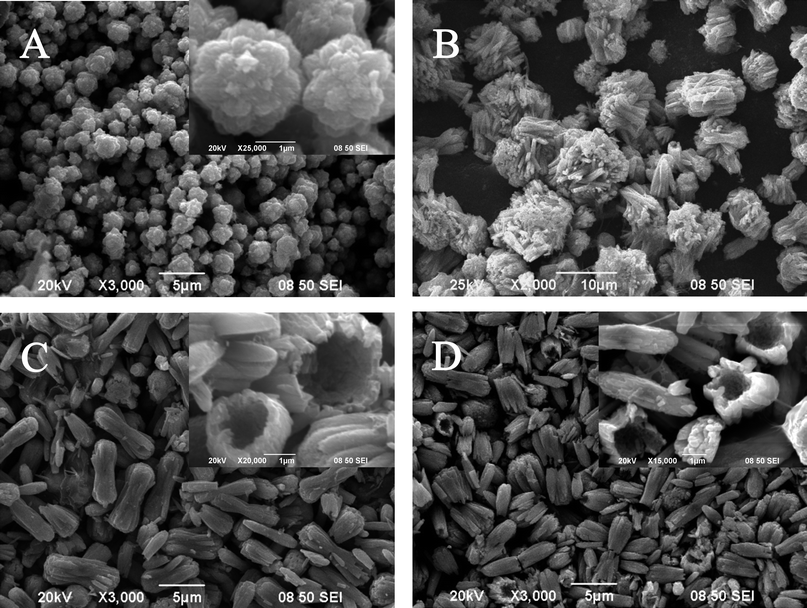 |
| Fig. 6
SEM images of the products obtained at different reaction times: 0.5 h (A); 1 h (B); 4 h (C); 24 h (D). Inset: high magnification of the images (A), (C) and (D). | |
Moreover, the products mainly contain several crystal structures (Inset in Fig. 6A), similar to that observed in our previous work with less ammonia.28 When the reaction time is prolonged to 1 h, the length of the aggregated nanorods is about 7 μm across the whole view (Fig. 6B). Evidently, the cluster structure is the intermediate product, which is formed when the reaction time is less than 2 h. When the hydrothermal time is 2 h, typical peanut-like hollow structures are obtained (Fig. 2A–C). Further increasing the reaction time to 4 h, well-defined peanut-like structures are also observed (Fig. 6C). However, there is no “wheel gear” structure in the middle of the peanut-like hollow structures any more (Inset in Fig. 6C); additionally a more smooth surface is observed in this case. When the reaction time is 24 h, the peanut-like structures are cracked from the connection points between the two hollow cages (Fig. 6D). Clearly, the hollow cages are still assembled with short nanorods. Until now, we can conclude that the hollow ZnO structures are obtained when the reaction time is longer than 2 h. Further increasing the reaction time would make the peanut-like hollow structures more defined with the assistance of the Ostwald ripening process. However, when the reaction time is too long, such as 24 h, the formed structures could be ruptured.
Based on all the results above, the growth mechanism of the peanut-like hollow ZnO structures is proposed and schematically shown in Scheme 1. First, Zn2+ ion reacts with NH3·H2O to produce Zn(NH3)42+ and Zn(OH)42− states. Then, very tiny ZnO particles are formed under the hydrothermal conditions. Two hydroxyl groups are linked in each monosaccharide unit of the pectin, which act as hydrophilic functional groups in this system. Upon dispersal of pectin in the mixed metal salt solution, its hydrophilic functional groups are able to bind metal cations by coordination or electrostatic interactions.54 Under the Coulomb force interactions between the Zn2+ ions and oxygen atoms on the backbone chain of pectin, the ZnO nuclei can be preferentially formed on the coalescent sites. Once the crystal has nucleated from the precursor, the negative pectin molecules have strong effects on the further growth of the ZnO superstructures. Next, different dimensions of ZnO nanorods are generated on the surface of the active sites through initial nucleation. The individual nanorods are aggregated to bundle ZnO nanorods arranged in a three-dimensional array. Furthermore, the size of the nanorods tends to be uniform upon the erosion effect of extra base as reported.24 Then, the nanorods grow into novel ZnO architectures. The special structure of the pectin serves as a molecular template that can induce the product to grow in the subsequent hydrothermal process, where the hydrogen and oxygen show different polarities. As a consequence, there will be polarization between different pectin molecules that is arrayed either horizontally or longitudinally. These pectin molecules may further interlace with each other. Obviously, this stage is the most important step for the formation of the hollow structures. The speculations are described as follows: on one hand, the existence of a large amount of NH3 and a gas–liquid equilibrium in the autoclave are the key factors, which make the bundled nanorods erode from the center to the outside in sequence. At the center point, the local zinc concentration is higher, which induces a faster erosion rate at the center.55 The competition between the NH3·H2O erosion and the ZnO growth is an important factor in the formation of the hollow structures. At low reaction temperatures, such as 120 °C, and moderate NH3·H2O concentration, the low growth rate of ZnO and high erosion speed would result in the formation of the hollow structures (Fig. 2A–C). But at high reaction temperature and low NH3·H2O concentration, the growth rate is very fast and the erosion function of NH3·H2O is relatively weak, leading to partial erosion and two smaller cages of the peanut-like structures (Fig. 5A). Moreover, at high NH3·H2O concentration, the interior of the structures are hollow (Fig. 5B). All of these results demonstrate that moderate NH3·H2O concentration is critical to form the special structures.
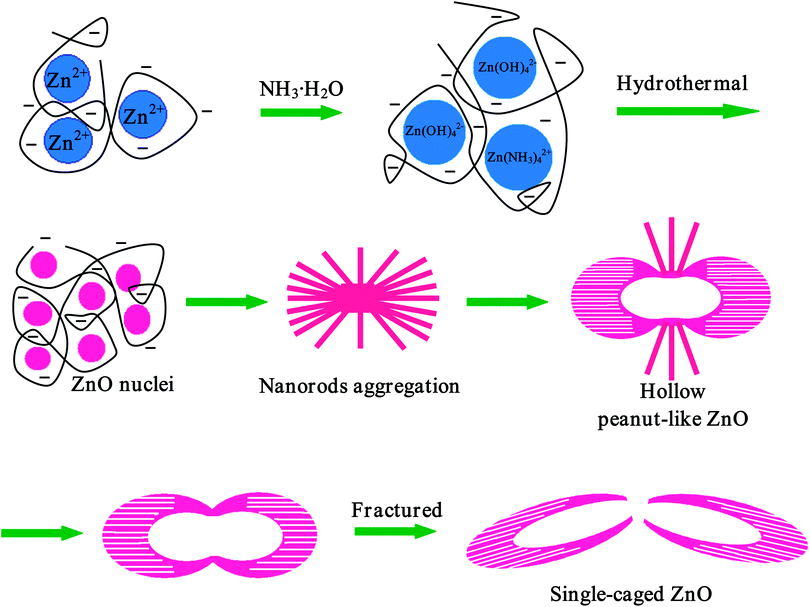 |
| Scheme 1 Schematic illustration of the growth mechanism of the hollow peanut-like ZnO structures based on time evolution of the aggregation process. | |
On the other hand, due to the intrinsic density variations inside the starting solid particles, the inner space can be formed when less stable parts are undergoing mass transport through dissolving and recrystallizing in the particles. As the reaction proceeds, some interior space would be generated within the solid aggregates through the Ostwald ripening process.56,57 Larger crystallites are essentially immobile, while smaller or loosely packed ones are undergoing mass transport through dissolving, diffusing outward, and recrystallizing.58 As a result, the void space would extend outside, and finally form the double-caged peanut-like hollow structures. As is known, ZnO has a basal positive polar plane (001) and a negative polar plane (001). These polar planes with surface dipoles are thermodynamically unstable and have a higher growth rate to reduce their surface energy.59 In the hydrothermal process, the growth along the (001) direction is faster, since the growth unit of the [Zn(OH)4]2− ion prefers to be adsorbed on the positive polar plane (001) by relatively strong electrostatic adsorption.60 When the heating time is prolonged, the “wheel gear” structure disappears, due to the confined growth on certain specific crystal planes of the ZnO and the strong binding selectively linked with pectin molecules. When the reaction time has elapsed, the shell of the hollow structure becomes thin, and the connection of the two cages fractures, leading to the formation of single-caged ZnO superstructures.
Photocatalytic activity
It is well-known that ZnO has been used as a semiconductor photocatalyst for the photocatalytic degradation of organic pollutants in aqueous solution. In our study, the photocatalytic performance of the typical hollow double-caged peanut-like ZnO microstructures was evaluated by photodegradation of the azo dye, MO, that is a typical pollutant in the textile industry under UV irradiation. Fig. 7 shows the UV-vis absorption spectra of the aqueous MO solution (initial concentration, 30 mg L−1; 60 mL) with 20 mg of the sample as a photocatalyst and exposure to ultraviolet light for various durations. From the results, the characteristic absorption of MO at 465 nm decreases rapidly when extending the exposure time. After 180 min of irradiation, the MO in aqueous solution could almost be eliminated by the ZnO sample. Its photocatalytic superiority can be attributed to the special structural features. The conduction-band electrons and valence-band holes are generated on the surfaces of the ZnO microstructures when they are illuminated by UV light. The vacancy can react with water adhering to the surface of the ZnO microstructures to form highly reactive hydroxyl radicals, which have a powerful oxidation ability to degrade organic dyes.61 The arrangement of nanorods in the peanut-like ZnO microstructures would effectively prevent aggregation and thus maintain a large active surface area. The specific surface area of the ZnO sample is about 25.5 m2 g−1, which is estimated from the plots of the N2 adsorption–desorption isotherms of the ZnO samples (Fig. S4, ESI†). The unique structures with large surface areas are beneficial to the photocatalytic performance.62,63 The surface photochemical reaction of MO degradation occurs in the sequence of dispersion, diffusion, adsorption, surface reaction, and finally desorption, and each of these elementary processes affects the surface reaction rate. The large surface area and capacious interspaces in the ZnO microstructures offer greater opportunity for the diffusion and mass transportation of MO molecules and hydroxyl radicals in the photochemical reaction of MO degradation.
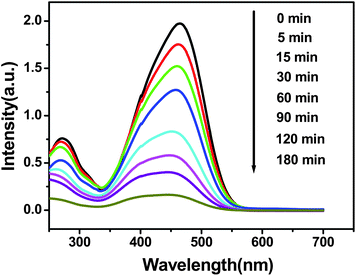 |
| Fig. 7
UV-vis absorption spectra from a 30 mg L−1 MO solution with hollow peanut-like ZnO powder at different time intervals. | |
Conclusions
In summary, hollow double-caged peanut-like ZnO microstructures have been synthesized via a simple hydrothermal route with the green biotemplate of pectin at low temperature. The shapes and sizes of the ZnO structures are determined by the molar ratios of the pectin to zinc ion, the amount of ammonia, the reaction time and the temperature. In particular the pectin, containing hydroxyl groups, plays an important role in this system. On the basis of these experiments, we propose a growth mechanism for the formation of the special ZnO structures. In addition, the as-prepared samples display high photocatalytic activity towards MO degradation under UV light irradiation. The present method can be extended to synthesize other metal oxides with hollow peanut-like structures, which have wide applications in the treatment of organic pollutants and other potential applications.
Acknowledgements
This work was financially supported by the Natural Science Foundation of China (Nos. 20805011, 20905021, 21175118).
References
- F. Caruso, R. A. Caruso and H. Mohwald, Science, 1998, 282, 1111 CrossRef CAS.
- F. Caruso, M. Spasova, A. Susha, M. Giersig and R. A. Caruso, Chem. Mater., 2001, 13, 109 CrossRef CAS.
- Q. Peng, Y. Dong and Y. Li, Angew. Chem., Int. Ed., 2003, 42, 3027 CrossRef CAS.
- M. Izaki, M. Watanabe, H. Aritomo, I. Yamaguchi, S. Asahina, T. Shinagawa, M. Chigane, M. Inaba and A. Tasaka, Cryst. Growth Des., 2008, 8, 1418 CAS.
- B. Liu and H. C. Zeng, J. Am. Chem. Soc., 2004, 126, 16744 CrossRef CAS.
- B. Liu and H. C. Zeng, Chem. Mater., 2007, 19, 5824 CrossRef CAS.
- Y. Sun and Y. Xia, Science, 2002, 298, 2176 CrossRef CAS.
- A. Imhof and D. J. Pine, Nature, 1997, 389, 948 CrossRef CAS.
- B. T. Holland, C. F. Blanford and A. Stein, Science, 1998, 281, 538 CrossRef CAS.
- Y. Wang, L. Cai and Y. Xia, Adv. Mater., 2005, 17, 473 CrossRef CAS.
- F. Caruso, Adv. Mater., 2001, 13, 11 CrossRef CAS.
- E. A. Meulenkamp, J. Phys. Chem. B, 1998, 102, 5566 CrossRef CAS.
- H. Zeng, W. Cai, Y. Li, J. Hu and P. Liu, J. Phys. Chem. B, 2005, 109, 18260 CrossRef CAS.
- M. H. Huang, S. Mao, H. Feick, H. Yan, Y. Wu, H. Kind, E. Weber, R. Russo and P. Yang, Science, 2001, 292, 1897 CrossRef CAS.
- H. Zeng, W. Cai, P. Liu, X. Xu, H. Zhou, C. Klingshirn and H. Kalt, ACS Nano, 2008, 2, 1661 CrossRef CAS.
- Z. W. Pan, Z. R. Dai and Z. L. Wang, Science, 2001, 291, 1947 CrossRef CAS.
- R. Brayner, R. Ferrari-Iliou, N. Brivois, S. Djediat, M. F. Benedetti and F. Fiévet, Nano Lett., 2006, 6, 866 CrossRef CAS.
- H. Zeng, P. Liu, W. Cai, S. Yang and X. Xu, J. Phys. Chem. C, 2008, 112, 19620 CAS.
- J. Liang, J. Liu, Q. Xie, S. Bai, W. Yu and Y. Qian, J. Phys. Chem. B, 2005, 109, 9463 CrossRef CAS.
- J. Q. Hu, Q. Li, N. B. Wong, C. S. Lee and S. T. Lee, Chem. Mater., 2002, 14, 1216 CrossRef CAS.
- R. Xie, D. Li, H. Zhang, D. Yang, M. Jiang, T. Sekiguchi, B. Liu and Y. Bando, J. Phys. Chem. B, 2006, 110, 19147 CrossRef CAS.
- H. J. Fan, R. Scholz, F. M. Kolb, M. Zacharias and U. Gosele, Solid State Commun., 2004, 130, 517 CrossRef CAS.
- Z. Deng, M. Chen, G. Gu and L. Wu, J. Phys. Chem. B, 2008, 112, 16 CrossRef CAS.
- Q. P. Ding, Q. Q. Cao, H. B. Huang, S. G. Yang, X. N. Zhao and Y. W. Du, J. Phys. D: Appl. Phys., 2006, 39, 46 CrossRef CAS.
- Y. Gao, A. D. Li, Z. B. Gu, Q. J. Wang, Y. Zhang, D. Wu, Y. F. Chen, N. B. Ming, S. X. Ouyang and T. Yu, Appl. Phys. Lett., 2007, 91, 031910 CrossRef.
- T. Ghoshal, S. Biswas, S. Kar, A. Dev, S. Chakrabarti and S. Chaudhuri, Nanotechnology, 2008, 19, 065606 CrossRef.
- X. Zhou, D. Zhang, Y. Zhu, Y. Shen, X. Guo, W. Ding and Y. Chen, J. Phys. Chem. B, 2006, 110, 25734 CrossRef CAS.
- J. J. Feng, Q. C. Liao, A. J. Wang and J. R. Chen, CrystEngComm, 2011, 13, 4202 RSC.
- S. Yue, L. Zhang, J. Lu and J. Zhang, Mater. Lett., 2009, 63, 1217 CrossRef CAS.
- L. Poul, S. Ammar, N. Jouini, F. Fiévet and F. Villain, Solid State Sci., 2001, 3, 31 CrossRef CAS.
- H. Zhou, T. Fan and D. Zhang, Microporous Mesoporous Mater., 2007, 100, 322 CrossRef CAS.
- I. A. Siddiquey, T. Furusawa, M. Sato and N. Suzuki, Mater. Res. Bull., 2008, 43, 3416 CrossRef CAS.
- X. Wang, P. Hu, Y. Fangli and L. Yu, J. Phys. Chem. C, 2007, 111, 6706 CAS.
- Y. Zhang, W. Zhang and H. Zheng, Scr. Mater., 2007, 57, 313 CrossRef CAS.
- J. H. Sun, S. Y. Dong, Y. K. Wang and S. P. Sun, J. Hazard. Mater., 2009, 172, 1520 CrossRef CAS.
- Y. Liu, Y. C. Zhang and X. F. Xu, J. Hazard. Mater., 2009, 163, 1310 CrossRef CAS.
- S. Xu, Z. H. Li, Q. Wang, L. J. Cao, T. M. He and G. T. Zou, J. Alloys Compd., 2008, 465, 56 CrossRef CAS.
- H. Zhang, D. Yang, D. Li, X. Ma, S. Li and D. Que, Cryst. Growth Des., 2005, 5, 547 CAS.
- J. Yin, Q. Lu, Z. Yu, J. Wang, H. Pang and F. Gao, Cryst. Growth Des., 2009, 10, 40 Search PubMed.
- L. A. Estroff and A. D. Hamilton, Chem. Mater., 2001, 13, 3227 CrossRef CAS.
- M. Li, H. Schnablegger and S. Mann, Nature, 1999, 402, 393 CrossRef CAS.
- D. M. Dabbs and I. A. Aksay, Annu. Rev. Phys. Chem., 2000, 51, 601 CrossRef CAS.
- M. P. Pileni, Nat. Mater., 2003, 2, 145 CrossRef CAS.
- J. D. Hartgerink, E. R. Zubarev and S. I. Stupp, Curr. Opin. Solid State Mater. Sci., 2001, 5, 355 CrossRef CAS.
- Y. Wang, X. Li, N. Wang, X. Quan and Y. Chen, Sep. Purif. Technol., 2008, 62, 727 CrossRef CAS.
- X. Zhou, Z. Hu, Y. Fan, S. Chen, W. Ding and N. Xu, J. Phys. Chem. C, 2008, 112, 11722 CAS.
- Z. Wang, X. F. Qian, J. Yin and Z. K. Zhu, J. Solid State Chem., 2004, 177, 2144 CrossRef CAS.
- R. A. McBride, J. M. Kelly and D. E. McCormack, J. Mater. Chem., 2003, 13, 1196 RSC.
- H. S. Qian, S. H. Yu, J. Y. Gong, L. B. Luo and L. L. Wen, Cryst. Growth Des., 2004, 5, 935 Search PubMed.
- J. I. Horinaka, H. Mori, K. Kani and S. Maeda, Macromolecules, 2004, 37, 10063 CrossRef CAS.
- F. Kar and N. Arslan, Carbohydr. Polym., 1999, 40, 285 CrossRef CAS.
- Y. W. Jun, J. S. Choi and J. Cheon, Angew. Chem., Int. Ed., 2006, 45, 3414 CrossRef CAS.
- M. Moriya, K. Yoshikawa, W. Sakamoto and T. Yogo, Inorg. Chem., 2009, 48, 8544 CrossRef CAS.
- X. Sun, J. Liu and Y. Li, Chem.–Eur. J., 2006, 12, 2039 CrossRef CAS.
- Z. Chen and L. Gao, Cryst. Growth Des., 2008, 8, 460 CAS.
- B. Liu and H. C. Zeng, Small, 2005, 1, 566 CrossRef CAS.
- X. W. Lou, Y. Wang, C. Yuan, J. Y. Lee and L. A. Archer, Adv. Mater., 2006, 18, 2325 CrossRef CAS.
- X. Tian, J. Li, K. Chen, J. Han and S. Pan, Cryst. Growth Des., 2009, 9, 4927 CAS.
- J. Zhang, L. D. Sun, J. L. Yin, H. L. Su, C. S. Liao and C. H. Yan, Chem. Mater., 2002, 14, 4172 CrossRef CAS.
- K. Govender, D. S. Boyle, P. B. Kenway and P. O'Brien, J. Mater. Chem., 2004, 14, 2575 RSC.
- B. Li and Y. Wang, J. Phys. Chem. C, 2009, 114, 890 Search PubMed.
- A. Bhattacharyya, S. Kawi and M. B. Ray, Catal. Today, 2004, 98, 431 CrossRef CAS.
- D. R. Chu, J. H. Mo, Q. Peng, Y. P. Zhang, Y. G. Wei, Z. B. Zhuang and Y. D. Li, ChemCatChem, 2011, 3, 371 CrossRef CAS.
Footnote |
† Electronic supplementary information (ESI) available. See DOI: 10.1039/c1ce05830d |
|
This journal is © The Royal Society of Chemistry 2012 |
Click here to see how this site uses Cookies. View our privacy policy here.