DOI:
10.1039/C0NR00642D
(Review Article)
Nanoscale, 2011,
3, 825-838
Metallic surfaces with special wettability
Received
1st September 2010
, Accepted 9th October 2010
First published on 7th January 2011
Abstract
Metals are important and irreplaceable engineered materials in our society. Nature is a school for scientists and engineers, which has long served as a source of inspiration for humans. Inspired by nature, a variety of metallic surfaces with special wettability have been fabricated in recent years through the combination of surface micro- and nanostructures and chemical composition. These metallic surfaces with special wettability exhibit important applications in anti-corrosion, microfluidic systems, oil–water separation, liquid transportation, and other fields. Recent achievements in the fabrication and application of metallic surfaces with special wettability are presented in this review. The research prospects and directions of this field are also briefly addressed. We hope this review will be beneficial to expand the practical applications of metals and offer some inspirations to the researchers in the fields of engineering, biomedicine, and materials science.
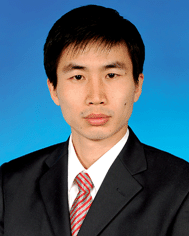 Kesong Liu | Kesong Liu is currently an associate professor at the School of Chemistry and Environment, Beijing University of Aeronautics and Astronautics. He obtained his PhD degree in materials science in 2006 from Harbin Engineering University of China under the supervision of Prof. Milin Zhang and Prof. Honggang Fu. He then worked as a postdoctoral fellow with Prof. Lei Jiang at the Institute of Chemistry, Chinese Academy of Sciences (ICCAS). His current scientific interests are focused on the design and fabrication of bio-inspired surfaces with special wettability and bio-inspired organic–inorganic composite functional materials with micro/nanoscale hierarchical structures. |
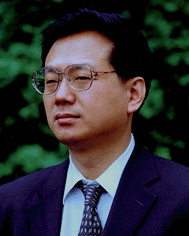 Lei Jiang | Lei Jiang is currently a professor at ICCAS, and Dean of School of Chemistry and Environment, Beijing University of Aeronautics and Astronautics. He received his B.S. degree (1987), M.S. degree (1990), and PhD degree (1994) from Jilin University (Tiejin Li's group). He then worked as a postdoctoral fellow in Prof. Akira Fujishima's group in Tokyo University. In 1996, he worked as a senior researcher in Kanagawa Academy of Sciences and Technology under Prof. Kazuhito Hashimoto. He joined ICCAS in 1999. In 2009, he was elected academician of CAS. His scientific interest is focused on bio-inspired surfaces and interfacial materials. |
1. Introduction
Wettability is a fundamental property of a solid surface, which has a variety of practical applications in the fields of daily life, industry, and agriculture. Usually, the wettability of solid surfaces is governed by their surface free energy and surface geometrical structures. Through long-term evolution, many biological materials, such as lotus leaves, rice leaves, butterfly wings, mosquito compound eyes, cicada wings, rose petals, gecko feet, desert beetles, spider silks, and fish scales, exhibit excellent surface wettability.1–11 The cooperation of micro- and nanoscale hierarchical structures and other specific components on these natural surfaces results in the special wettability. Inspired by nature, many different synthesis strategies have been developed to fabricate functional surfaces with special wettability, which have been reviewed in a number of publications.1,12–27
Metals are very important and irreplaceable engineered materials in many industrial fields, which are the major workhorse of our society and will remain so in the future.28 Apart from their unique properties, metals present some property limitations. For example, corrosion is headache for metals. In the past few decades, a great number of synthetic methods have been developed to fabricate non-metallic surfaces with special wettability. The construction of special wettability on metallic substrates is a scientifically and technologically challenging target. Recently, in order to extend the applications of metals, a variety of metallic surfaces with special wettability have been constructed by using different synthetic processes. These metallic surfaces with special wettability exhibit some important applications such as anti-corrosion, oil–water separation, friction reduction, liquid transportation, and microfluidic materials.
This review will focus on the recent progress in the fabrication and application of metallic surfaces with special wettability (such as superhydrophobicity, superamphiphobicity, superoleophilicity, switchable wettability, wettability gradients, etc.). This review is composed of eight sections. In section 2, we focus on superhydrophobic metallic surfaces, particularly on superhydrophobic copper, aluminium, alloy, and other metals. The recent progress in superamphiphobic (both superhydrophobic and superoleophobic) metallic surfaces, such as gold and engineering metals, is described in Section 3. Section 4 presents metallic surfaces possessing both superhydrophobicity and superoleophilicity, especially stainless steel mesh, copper mesh, nickel substrate, and other metals. Metallic surfaces with switchable wettability driven by pH, ion exchange, enthalpy, light, and other external stimuli are shown in Section 5. Section 6 briefly summarizes the recent developments of metallic surfaces with wettability gradients. In Section 7, practical applications of metallic surfaces with special wettability in corrosion resistance, microfluidic systems, oil–water separation, liquid transportation, and other fields are described. Finally, we provide our conclusions and outlook on the developments of metallic surfaces with special wettability.
2. Superhydrophobic metallic surfaces
In nature, many biological materials exhibit superhydrophobicity. Research indicated that micro- and nanoscale hierarchical structures on these biological surfaces play an important role in generating the desired wettability. Inspired by nature, using many different synthetics methods, a wide variety of superhydrophobic materials have been fabricated through the construction of appropriate surface hierarchical micro/nanostructures and chemical composition.1 These superhydrophobic materials have important applications in our daily life and in industrial fields.29 In this section, we will mainly discuss superhydrophobic metallic surfaces.
2.1
Copper
Copper is one of the most essential engineering materials, possessing important applications in industrial fields. Many different synthetic strategies have been developed to fabricate artificial superhydrophobic surfaces on copper substrates to date.
Stable bionic superhydrophobic surfaces were prepared by immersing a copper plate into a solution of fatty acids at ambient temperature.30 The one-step solution-immersion method was believed to extend to the construction of other superhydrophobic metallic surfaces. Using a similar method, superhydrophobic silver films on copper substrates were constructed by immersing the copper substrates in a silver nitrate solution containing benzoic acid.31 A one-step electrodeposition process was also developed to fabricate superhydrophobic surfaces on the copper substrate (Fig. 1).32 The micro- and nanoscale hierarchical structures endowed copper surfaces with excellent superhydrophobicity and the resultant surfaces showed superhydrophobicity even for some corrosive liquids including salt solutions and acidic and basic solutions at all pH values. Furthermore, this method can be expanded to construct superhydrophobic surfaces on other substrates such as titanium, iron, zinc, aluminium, and stannum. A lotus-leaf-like superhydrophobic copper surface with a high contact angle and a low sliding angle was prepared through both surface oxidation and chemical modification with low surface energy materials.33 Superhydrophobic three-dimensional porous copper films were prepared by using the hydrogen bubble dynamic template.34 Recently, mimicking the lotus leaf, three-dimensional honeycomb-like porous structures consisting of nanoslices of hydroxy cupric phosphate heptahydrate single crystals were fabricated by immersing copper foil in an aqueous solution of phosphoric acid and hydrogen peroxide. After surface oxidation and subsequent chemical modification, superhydrophobic surfaces were obtained on copper foils.35
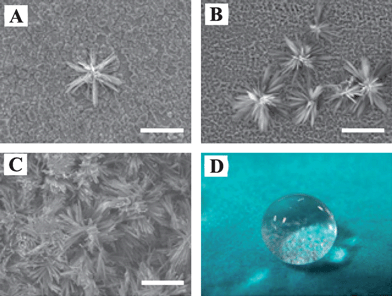 |
| Fig. 1
Scanning electron microscope (SEM) images of superhydrophobic surfaces constructed on copper wafer by the electrodeposition process. The reaction times are (A) 1, (B) 2.3, and (C) 3 h. (D) Digital photograph of 12 μL water droplet on superhydrophobic copper surface. The bars represent 50 μm.32 | |
Electroless galvanic deposition is an environmentally friendly method for the construction of double roughness on metal substrates. Superhydrophobic surfaces were prepared on a copper substrate by the electroless galvanic deposition method, followed by a self-assembled monolayer of polyfluoroalkyl thiol.36 Furthermore, the artificial “pond skater” constructed by this superhydrophobic copper can stand on a water surface. Inspired by the lotus leaf, superhydrophobic copper surfaces were fabricated through a process combining both electroless galvanic deposition and the self-assembly of n-octadecanethiol (Fig. 2).37 The resultant copper surface with a feather-like structure exhibited stable superhydrophobicity over a wide range of pH and temperature.
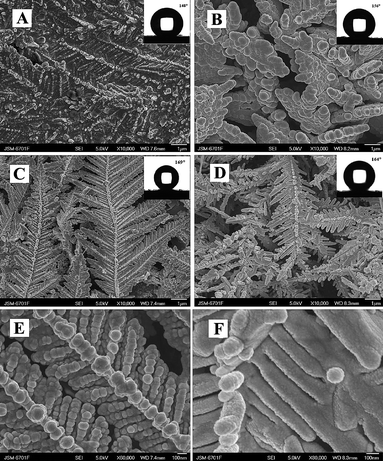 |
| Fig. 2 Effect of the deposition time on the morphology of the copper substrate after deposition of Ag for (A) 10 s, (B) 20 s, (C) 30 s, and (D) 60 s; (E, F) larger views of C and D; contact angles shown in inset pictures.37 | |
In nature, water striders can stand and walk freely on a water surface using their water-resistant legs. Superhydrophobic legs with a super-repellent force to water are attributed to the cooperative effect of hierarchical micro/nanostructures and a low-surface-energy wax coating.38 Recently, inspired by the hierarchical structures of water-strider legs, water-repellent materials with ribbed, conical nanoneedles were constructed on copper surfaces, consisting of copper hydroxide nanoneedle arrays sculptured with nanogrooves.39 The resultant superhydrophobic surface exhibited minimally water-adhesive and little contact-angle hysteresis even under certain hydrostatic pressure.
Besides the above mentioned superhydrophobic copper surfaces, other superhydrophobic surfaces on copper substrates also have been fabricated recently by using electrodeposition,40electroplating,41etching,42 sandblasting,43 solution-immersion,44–47 and other methods.
2.2 Aluminium
A phase separation technique was developed to prepare superhydrophobic coatings on aluminium substrates by using polycarbonate and its solvent and non-solvents.48 This method can be extended to fabricate white or colorful superhydrophobic coatings on other material substrates through a simple dipping and drying procedure. Superhydrophobic laurate-intercalated films with micro- and nanoscale hierarchical structures were fabricated on a porous aluminium/anodic alumina substrate by the anion exchange method, demonstrating long-term corrosion protection of the coated aluminium substrate.49Anodization combined with low-temperature plasma treatment was used to create micro/nanoscale hierarchical structures on aluminium substrates.50 After modifying with trichlorooctadecyl-silane, superhydrophobic aluminium was obtained. Recently, superhydrophobic aluminium surfaces were constructed by chemisorption of micelles of fluorinated block copolymers synthesized by reversible addition–fragmentation chain transfer in supercritical carbon dioxide.51 The surface modification and polymer deposition resulted in the enhancement of surface roughness in the microscale and nanoscale, respectively, resulting in the full superhydrophobicity over areas up to 4 cm2.
Biomimetic superhydrophobic surfaces were prepared on engineering materials of aluminium by immersing aluminium in NaOH solution and then decorating with perfluorononane (Fig. 3A–B).52 The obtained superhydrophobic surfaces presented long-term stability over a wide pH range, that is, not only for pure water but also for corrosive liquids including acidic and basic solutions. Furthermore, these superhydrophobic surfaces were used as substrates to investigate the suspension and movement of ferrofluid droplets in the presence of strong external magnetic fields.53 It was useful for the quantitative evaluation of friction forces between the droplets and superhydrophobic surfaces. Superhydrophobic surfaces on aluminium were fabricated by using a dislocation etchant and subsequent coating with a fluoroalkylsilane, which was also suitable for copper and zinc substrates.54 Recently, without a hydrophobic treatment, aluminium surfaces with superhydrophobicity were prepared by a chemical etching method in a mixed acid solution of hydrochloric and acetic acids, exhibiting self-cleaning properties with a low water sliding angle.55
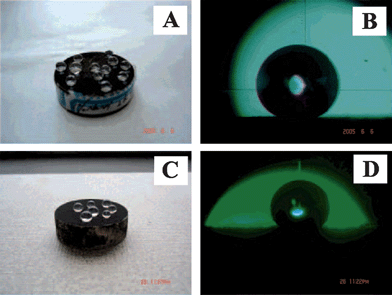 |
| Fig. 3 (A) Optical image of water droplets with different sizes on the surface of Al block treated with perfluorononane. (B) Profile of one water droplet on the surface having a contact angle of 168 ± 2°. (C) Optical image of water droplets with different sizes on the surface of super-hydrophobic aluminium alloy modified with PDMSVT. (D) Profile of the water droplet with a contact angle of 161 ± 2°.52 | |
2.3 Alloy
Stable biomimetic superhydrophobic surfaces were prepared on engineering materials of aluminium alloy by immersing aluminium in NaOH solution and then decorating with poly(dimethylsiloxane) vinyl terminated (PDMSVT), which exhibited long-term stability over a wide pH range (Fig. 3C–D).52 Controlled lateral movement of ferrofluidic droplets was achieved on these superhydrophobic aluminium alloy surfaces in a uniform magnetic field.53 Sticky superhydrophobic aluminium alloy surfaces were fabricated by using a selective etching method.56 The obtained surface showed a complementary structure to that of the lotus. The strong adhesion was attributed to the capillary force between the micro-orifices and water droplet and the van der Waal's force between the surface and water. Superhydrophobic aluminium alloy surfaces were prepared by the immersion method in HNO3/H2O2 mixed solutions and post-modification with stearic acid, which exhibited superhydrophobicity not only for pure water but also for corrosive liquids such as acidic, basic and salt solutions.57 Superhydrophobic aluminium alloy surfaces were fabricated by combining mechanical roughening and chemical etching, and subsequent decoration with alkylsiliane.58
Using a solution-immersion process, superhydrophobic surfaces were fabricated on common industrial Cu and Ti alloys, exhibiting stable superhydrophobicity even in many corrosive solutions, such as acidic or basic solutions over a wide pH range, and also in salt solutions (Fig. 4).59 Superhydrophobic nickel,60titanium,61copper,62 and Cu–Zn alloys63 were also constructed by using different synthesis methods.
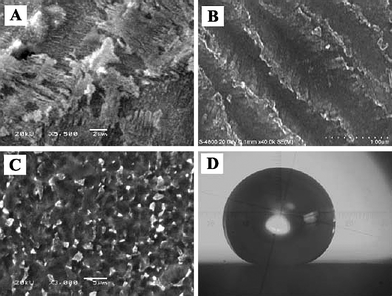 |
| Fig. 4
SEM images at (A) low and (B) high magnifications of the etched copper alloy treated with fluoroalkylsilane. (C) SEM image of the etched titanium alloy treated with fluoroalkylsilane. (D) Profile of a water droplet on the superhydrophobic titanium alloy surface with a contact angle of 151° ± 1°.59 | |
2.4 Others
Besides the above discussed superhydrophobic copper, aluminium, and alloy, other metallic surfaces with superhydrophobicity were also fabricated by using different synthesis processes.64–74 Mimicking the hierarchical structures of lotus leaves, superhydrophobic metal surfaces were prepared by using the simple electrochemical reaction of Cu or Cu–Sn alloy plated on steel sheets with sulfur gas, and subsequent perfluorosilane treatment.64 Hydrophobic to superhydrophobic surfaces were fabricated by depositing FePt alloy with varying degree of fluorinated ligands on their surface.65 Mimicking the legs of water striders, superhydrophobic coatings on gold threads were fabricated by combining a layer-by-layer assembly, electrochemical deposition, and surface modification.66 Utilizing a solution-immersion technique, superhydrophobic silver, zinc, and steel were also prepared.67–73
Although a great number of superhydrophobic metallic surfaces have been successfully fabricated, there remains a question we can not avoid. That is these artificial superhydrophobic metallic surfaces structures usually can be easily destroyed, resulting in the disappearance of the superhydrophobicity and exhibiting low mechanical properties. This is an important obstacle for the practical applications of superhydrophobic metallic surfaces.
3. Superamphiphobic metallic surfaces
In the previous section, metallic surfaces with superhydrophobicity were briefly discussed. Superhydrophobicity can be found in many natural materials surfaces, but on the other hand, superoleophobic properties are extremely rare. Materials surfaces possessing the superamphiphobic function, i.e., surfaces that exhibit both superhydrophobicity and superoleophobicity, have attracted much interest due to their important applications in daily life, industrial, and biological fields.1
Inspired by nature, a wide variety of superhydrophobic surfaces have been fabricated through the cooperation between the chemical composition and the surface micro- and nanostructures. However, oils and other organic liquids usually exhibit a higher solid surface attraction due to their lower surface tension compared to water. Therefore, it is much more difficult to construct superoleophobic surfaces than superhydrophobic surfaces.75 Inspired by the natural design principle of superhydrophobic surfaces, a number of artificial superamphiphobic materials have been fabricated through the combination of surface chemical composition, multiscale structures, and other factors.76–84 In this section, we will focus on the recent advances in superamphiphobic metallic surfaces.
3.1
Gold
Gold is a noble metal and has numerous applications in medicine, biology and materials science. In order to extend its practical application, it is essential to fabricate gold surfaces with superamphiphobicity.
Utilizing an electrochemical deposition method, nanopyramidal gold nanostructures were fabricated on sputtered gold substrates. After the modification of perfluorodecanthiol, the as-prepared nanostructured gold surfaces presented superamphiphobicity. The rough pyramidal nanostructures, the low surface energy perfluorodecanethiol coating, and very large fraction of air on the film resulted in the gold surfaces with both superhydrophobicity and superoleophobicity.85 Superamphiphobic surfaces with extremely low hysteresis and sliding angles were prepared by electrochemical polymerization of highly fluorinated 3,4-ethylenedioxypyrrole on gold (Fig. 5). It was found the antiwetting properties did not depend of the fluorocarbon chain length but were in fact governed by the nature of the electrochemically deposited core.86–88
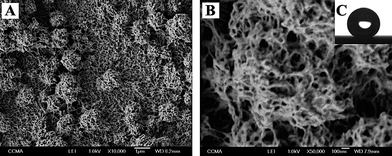 |
| Fig. 5 (A–B) SEM images of the polymeric surface on gold substrates at different magnifications and (C) picture of a hexadecane droplet on the surface.88 | |
3.2 Engineering metal
Using a one-step electrochemical reaction in perfluorocarboxylic acid solutions, superamphiphobic surfaces were constructed on zinc substrates (Fig. 6).89 The synergistic effect of special surface compositions and micro- and nanoscale hierarchical structures resulted in them being super-repellent to both water and oil. Furthermore, through controlling the chain length, concentration of perfluorocarboxylic acid, and the process time, this method can be expanded to fabricate superamphiphobic surfaces on other common engineering metals, such as aluminium, iron, nickel, and their alloys. Recently, superamphiphobic oxidized aluminium surfaces were fabricated by chemical vapor deposition of a branched-featured perfluoroalkyl hydridosilane, demonstrating no contact angle hysteresis for water and n-hexadecane.90 Due to the topological effect of the silanes monolayer, liquids hardly penetrated the monolayer to interact with residual aluminols on the surface.
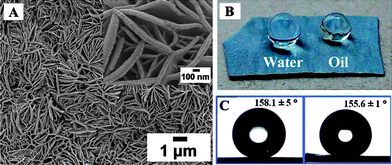 |
| Fig. 6 (A) Large-area SEM image of the prepared petal-like zinc surface; the inset is a high resolution SEM image. (B) The camera pictures of water and oil droplets setting on the as-prepared surface. (C) Contact angle profiles of water droplet (left) and oil droplet (right) on the surface.89 | |
The bulk metallic glasses (BMG) with excellent glass-forming ability possess many fascinating properties and features, which have received much attention not only for basic research but also for technological applications.91 A superamphiphobic CaLi-based BMG was prepared by the construction of micro- and nanoscale hierarchical structures first and then modification with fluoroalkylsilane.92 Owing to the combination of the surface roughness and the low surface free energy coating, the resultant BMG surface exhibited stable superhydrophobic and superoleophobic properties and improved corrosion resistance (Fig. 7). Recently, a design chart to assist in the a priori prediction of liquid wettability and the robustness factor against wetting by a specified liquid on cylindrically textured surfaces was proposed.93 This chart may be helpful for a rational design and the reproducible construction of superamphiphobic surfaces.
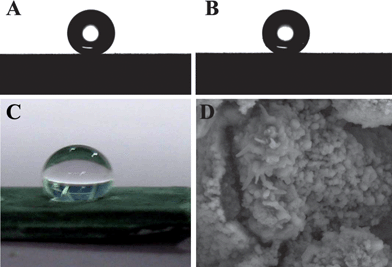 |
| Fig. 7 The water droplet (A) and oil droplet (B) shape on the CaLi-based BMG surface. (C) Photographic image of a water droplet on the BMG surface after exposure to air for three months. (D) SEM image of the CaLi-based BMG surface.92 | |
4. Superhydrophobic and superoleophilic metallic surfaces
In the preceding sections, we introduced metallic surfaces with superhydrophobicity and superamphiphobicity. A combination of superhydrophobicity and superoleophilicity can result in special functional surfaces with some important applications in industry and daily life.15,18,19 In the last decades, using metals or polymers as substrates, many different synthesis strategies have been developed to design functional interfacial materials with both superhydrophobic and superoleophilic properties. In this section, we will mainly discuss metallic surfaces with both superhydrophobicity and superoleophilicity.
4.1 Stainless steel mesh
The first example of a superhydrophobic and superoleophilic surface was prepared by a spray-and-dry method on stainless steel mesh substrates.94 A homogeneous emulsion containing low surface energy Teflon® (polytetrafluoroethylene) was used as the precursor. The combination of nanostructured crater-like morphology on the rough microscale surface and chemical composition confers superhydrophobicity and superoleophilicity simultaneously. The contact angle for water and diesel oil is about 156° and 0°, respectively. The hydrophobicity of the mesh coating films is affected by the pore size of meshes. Utilizing a sol–gel based perfluoroalkyltriethoxysilane dipping process, superhydrophobic and superoleophilic stainless steel meshes have been fabricated.95 The static contact angle on the mesh surface is greater than 150° for water, and close to 0° for kerosene, xylene, and toluene. The water contact angle depends on the pore size of meshes and decreases when the pore size is larger than 0.3 mm. Furthermore, the obtained mesh exhibited stable water-resisting, anti-chemical erosion, and anti-heat aging properties. Recently, in the absence of fluorinated chemicals, a superhydrophobic and superoleophilic stainless steel mesh was obtained by using tetraethoxysilane and methyltriethoxysilane as precursors and post-thermal treatment without further modification.96 The special wettability of mesh surfaces can be attributed to hierarchical structures of the silica film with methyl groups terminated domains constructed on the mesh. The fabrication of superhydrophobic surfaces using non-fluorinated polymers is an environmentally friendly route, which has received much attention and will be an important research branch of functional interface materials with special wettability.
4.2
Copper mesh
Inspired by the lotus effect, an electrochemical deposition method was applied to fabricate functional copper meshes with superhydrophobic and superoleophilic properties.97 The collaboration of micro- and nanoscale hierarchical structures on the copper mesh surfaces and the non-fluorine long-chain fatty acid resulted in this unique surface wettability. Superhydrophobic and superoleophilic copper meshes were also achieved by a immersion step in aqueous solution of NaOH and K2S2O8 and subsequent modification with n-dodecanethiol (Fig. 8), where the separation efficiency of the copper meshes was also quantitatively measured.98 Recently, using a similar method, copper meshes with superhydrophobicity and superoleophilicity were fabricated through solution-immersion in nitric acid solution and sequential modification with 1-hexadecanethiol.99
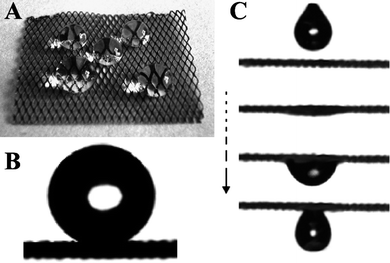 |
| Fig. 8 (A–B) Optical images of water droplets on the surface of a thiol-modified copper mesh. (C) Dynamic image of an oil droplet quickly spreads over and permeates through a thiol-modified copper mesh.98 | |
4.3
Nickel substrate and others
A wet-chemical process is an effective solution to control the size, shape, and dimensionality of micro and nanoscale materials. Superhydrophobic and superoleophilic nickel surfaces with flowery structures have been fabricated through a wet-chemical process by using monoalkyl phosphonic acid.100 Flowery microstructures gradually formed and constituted a continuous slipcover over the nickel surfaces. Furthermore, the surface roughness and wettability of nickel substrates can be tailored synchronously by controlling the steeping time and using phosphonic acids with different alkyl groups. This approach can be extended to construct stainless steel mesh and nickel alloy with superhydrophobic and superoleophilic properties. Electrodeposited films with micro- and nanoscale hierarchical structures were fabricated by electropolymerization of fluorinated ethylenedioxythiophene monomers on gold. The combination of low surface energy fluorinated chains with the dual-scaled hierarchical structures of the electrodeposited films enhanced the non-wetting of water while keeping the intrinsic wetting of oil, resulting in both superhydrophobicity and superoleophilicity.101,102
Superhydrophobic and superoleophilic metallic surfaces have some potential applications in industrial production and environmental protection. This will be presented in the section of application of metallic surfaces with special wettability.
5. Metallic surfaces with switchable wettability
Materials surfaces with single wettability cannot meet demand in the rapid development of smart systems. Smart surfaces with responsive switchable wettability have attracted even more attention owing to their wide applications in membranes, sensors, micro-fluidic devices, lab-on-a-chip systems, and so on.16 Recently, many different approaches have been developed to fabricate external stimuli smart surfaces with reversible, switchable wettability, especially switching between superhydrophobicity and superhydrophilicity. Usually, external stimuli, such as pH, light, temperature, enthalpy, the magnetic field, selected solvent, electrical potential, and others, can be used to drive the transition between hydrophilicity and hydrophobicity on different substrates by combining surface geometrical morphology with surface chemistry.103–105 This section will only focus on the recent advances in the switchable wettability on metallic surfaces.
5.1 pH stimulus
Owing to the easy construction of micro/nano hierarchical structures and facile introduction of stimuli-responsive materials through the self-assembly process, gold is usually used as substrate materials for fabricating special wettability surfaces.
A pH-responsive surface was fabricated on the fractal-like gold substrate decorated with a thiol self-assembled monolayer.106 The surface exhibited superhydrophobicity in an acidic and even neutral environment, but superhydrophilicity under basic conditions. Both the composition of the self-assembled monolayer and the rough gold structure are critical for the switchable wettability. Large-scale pH-responsive surfaces were fabricated after modification of the rough surface with the mercaptoalkyl derivative, which exhibited reversible wettability from nearly superhydrophobicity to superhydrophilicity.107 Compared to a flat gold surface, the roughness of the gold significantly enhanced the pH-responsive properties. Recently, responsive surfaces were prepared from self-assembled monolayers of a malachite green derivative on a rough gold surface.108 The surface wettability can be switched from superhydrophobicity to superhydrophilicity by pH as well as UV irradiation.
5.2 Ion exchange stimulus
Ion exchange is a reversible process where ions are exchanged between cationic or anionic electrolytes and their complexes. Therefore, the physicochemical properties and functions of smart surfaces can be modulated by carrying out the direct exchange of counterions.
Smart surfaces with switchable wettability were fabricated by constructing micro/nanotextured gold substrates through a galvanic cell displacement reaction and then grafting polyelectrolyte brushes with quaternary ammonium groups onto the rough gold surfaces through surface-initiated atom transfer radical polymerization.109 The reversible wettability switch between superhydrophobicity and superhydrophilicity was achieved by direct anion exchange. The counteranion played an important role in determining the hydrophobic/hydrophilic character of the switchable surfaces.
5.3 Enthalpy stimulus
Traditional responsive polymers usually involve an entropy-driven transformation from one disordered state to another disordered state by an external stimulus. However, some important life phenomena and molecular recognition most probably undergo an enthalpy-driven transformation from an ordered state into another ordered state to perform various intelligent behaviors.110 Recently, DNA molecules have been extensively investigated in the field of smart nucleic acid nanodevices, originating from their advantages of site-to-site molecular recognition.
A responsive surface was fabricated by decorating DNA with a fluoride-containing hydrophobic group, which was immobilized on a gold surface through a gold–thiol bond.111 The resultant switching surface can switch between stable superhydrophilic, metastable superhydrophobic, and stable superhydrophobic states by an enthalpy-driven process (Fig. 9). This macroscopic surface wetting phenomenon was attributed to the collaborative effects of surface microstructure and collective nanometre-scale motion of DNA nanodevices. Such enthalpy-driven switchable surfaces could provide a model to understand biological behavior, such as short- and long-term memory, as well as help in the design of intelligent surfaces.
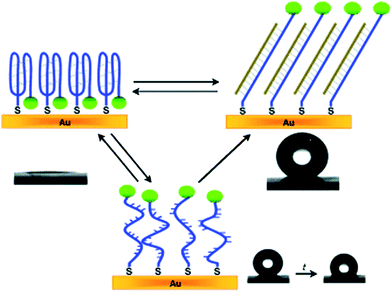 |
| Fig. 9 Enthalpy-driven three-state switching among stable superhydrophilic, metastable superhydrophobic, and stable superhydrophobic states.111 | |
5.4 Light stimulus
Light is one of the most important external stimuli. Self-assembled monolayers of a photocontrolled molecular shuttle on the basis of an α-cyclodextrin/azobenzene inclusion complex were constructed on gold surfaces (Fig. 10).112 By transferring external energy (UV/visible light) to molecular mechanical motion, the surface wettability was reversibly switched between hydrophobicity and hydrophilicity. Recently, lotus leaf-like copper hierarchical structures were constructed without chemical modification, where reversible transition from superhydrophobicity to superhydrophilicity was achieved by alternation of UV irradiation and dark storage.113
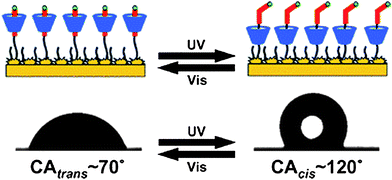 |
| Fig. 10 A photocontrolled molecular shuttle self-assembled monolayer based on an α-cyclodextrin/azobenzene inclusion complex on rough gold surfaces, exhibiting reversible wettability with UV/visible irradiation.112 | |
Current research of smart surfaces with switchable wettability was mainly focused on the wetting transition between superhydrophobicity and superhydrophilicity. Recently, surfaces with controllable oleophobicity and switchable oil adhesion were fabricated on engineering titanium surfaces.114 The synthetic approach involved the formation of rough microstructures on a titanium surface first and then the formation of hierarchical TiO2 nanotube arrays by further anodization, followed by post-modification with hydrophobic materials. Tunable oleophobicity was achieved by manipulating the UV irradiation (Fig. 11). Combining UV irradiation and heat treatment, the reversible adhesion of oil droplets between sliding superoleophobicity and sticky superoleophobicity were achieved on the titanium surfaces. Furthermore, the movement of a magnetic oil droplet was manipulated on the surface by applying an external magnetic field.
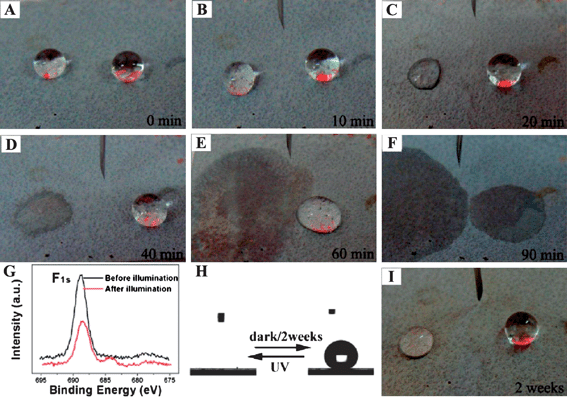 |
| Fig. 11 (A–G) Tunable contact angle of micro- and nanostructured TiO2/Ti under UV illumination with different times from 0 to 90 min and the XPS analysis. (H, I) The reversible performance after storing in the dark for two weeks. The left drop is hexadecane, and the right drop is glycerol.114 | |
5.5 Others
Besides above mentioned external stimuli, smart surfaces with reversibly switchable wettability can be prepared on metallic substrates driven by heat, the magnetic field, electrical potential, and others. A gold film with two-layer structure was fabricated on poly(dimethylsiloxane) by electroless plating.115 The wettability of the gold film could be rapidly switched between superhydrophilicity and superhydrophobicity by the alternation of heat and plasma treatment. Tunable adhesive superhydrophobic iron surfaces for superparamagnetic microdroplets were prepared as a function of the magnetic field.116 A reversibly switching surface possessing the dynamic change in wettability was constructed on gold surfaces.117 The wetting behavior change in response to an electrical potential originated from surface-confined, single-layered molecules undergoing conformational transitions between a hydrophilic and a moderately hydrophobic state.
6. Metallic surfaces with wettability gradient
Gradients play an important role in living organisms and can be observed in many biological key processes, which are ubiquitous in nature.118–120 A gradient surface possesses a gradual change in its chemical and physical properties along its length. Generally, gradients can be classified into two major categories: chemical gradients and physical gradients.121 In recent years, surface gradient materials have attracted much attention owing to their fundamental and practical applications in chemical, physical, and biological fields.122–124
Gradient wettability surfaces have a wide domain of applications ranging from fundamental studies to industrial fields, such as protein adsorption, cell adhesion, heat exchangers, and microfluidics.23,125,126 The wetting property gradient along a surface can allow water droplet movement along the gradient. The possibility of droplet movement originating from a surface gradient was first predicted by Greenspan in 1978.127 In 1992, Chaudhury and Whitesides experimentally demonstrated the movement of a water droplet along a 1 cm long wettability gradient, prepared by decyltrichlorosilane vapour diffusion on a silicon surface by evaporation.128 The chemical gradient surface can drive water droplets uphill with an average velocity of about 1 to 2 millimetres per second when the contact angle hysteresis on the surface is low (≤10°). Since then, many different synthesis strategies have been developed to synthesize gradient wettability surfaces to drive droplet movement on silicon, glass, metal, and other substrates by light,129 thermal,130 electrical,131 elastic,132 electrochemical,133 chemical,134 and physicochemical,135 methods. In this section, we will mainly discuss the wettability gradient on metallic surfaces.
Surface-chemical gradients of self-assembled monolayers can be prepared by a two-step immersion process on gold over a millimetre–centimetre scale (Fig. 12A).136 During the first immersion step, a surface concentration gradient was achieved upon gradually immersing a gold-coated substrate into a dilute thiol solution by means of a linear-motion drive. Subsequent immersion of the substrate into the complementary thiol solution resulted in a hydrophobicity gradient with a large range (50° of the water contact angle). The two-step immersion method mentioned above can also be used to fabricate submicrometer structure of surface-chemical gradients on gold. Lateral force microscopy and microdroplet density measurements revealed that the structure of chemical gradients is inhomogeneous on the <100 nm scale.137 Recently, this two-step immersion method was extended to prepare orthogonal, three-component, alkanethiol-based surface-chemical gradients on gold.138Water and hexadecane showed distinctly different wetting behaviors on the gradient surface owing to the differences in the hydrophobic and oleophobic natures of the three different constituents.
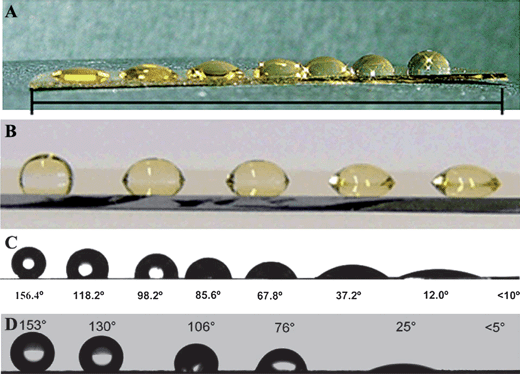 |
| Fig. 12 (A) Water droplets along a hydrophobic gradient using full-immersion method.136 (B) Photograph (side view) of water droplets along a hydrophilic gradient prepared by the combination of electron irradiation and exchange reaction.139 (C) Photograph of the water contact angles along the gradient surface.141 (D) Image of the gradient wettability along the surface via ion exchange.142 | |
Chemical gradients on gold substrates were fabricated by tuning the exchange reaction between a self-assembled monolayer covering the substrate and a potential molecular substituent. Fig. 12B presented the water drops on the hydrophilic gradient created using this method.139 Utilizing selective photo-oxidation of self-assembled monolayers of alkanethiols, molecular-scale composition gradients with different geometries were also prepared on gold surfaces.140 This method is applicable for the construction of gradient surfaces on different length scales.
Gradient surfaces with wetting property that can change from superhydrophobic to superhydrophilic have some potential applications, which would extend many new possibilities for industrial applications. Recently, by combining surface roughness and the chemical gradient, superhydrophobic-to-superhydrophilic gradients have been fabricated. Surface gradient materials from superhydrophobic to superhydrophilic were prepared by controlling the self-assembled monolayer of thiol molecules on a rough gold surface (Fig. 12C). The contact angles change continuously along the gradient surface from larger than 150° to smaller than 10° over a large scale.141 Tunable wettability and rewritable wettability gradients from superhydrophilic to superhydrophobic were also fabricated by the layer-by-layer technique.142 The water contact angle of the surface was switched between <5° and >150° (Fig. 12D). By controlling the ion-exchange kinetics along the surface, erasable and rewritable gradient wettability was achieved.
7. Application of metallic surfaces with special wettability
Metallic surfaces with special wettability have been fabricated through different synthesis strategies, exhibiting many important applications in a wide number of fields.18,19 In this section, the application of metallic surfaces with special wettability in the fields of corrosion resistance, microfluidic systems, oil–water separation, liquid transportation, and other fields was briefly discussed.
7.1 Corrosion resistance
Recently, superhydrophobic surfaces with anti-corrosion properties have received much attention owing to their important industrial applications. Stable hydrophobic 1-dodecanethiol films with high adhesive forces were fabricated with the help of preferential adhesion of polydopamine on the non-etching copper surfaces by a simple dip-coating method.143 The obtained hydrophobic functional films exhibited superior corrosion resistance properties and the long-term seawater stability, especially in limiting the infiltration of chlorine ions. Superhydrophobic surfaces with flower-like structures were constructed on copper substrates by immersing copper plates into an ethanol solution of n-tetradecanoic acid, showing improved corrosion resistance in seawater.144
Superhydrophobic surfaces on aluminium were prepared by the anodization process and then chemical modification with myristic acid.145 Electrochemical measurements showed, owing to the formation of a stable superhydrophobic film, the aluminium corrosion was effectively inhibited in seawater.146Neutron reflectivity showed the superhydrophobic nature of the aluminium surface prevented infiltration of water into the porous superhydrophobic film and thus limited the exposure of corrosive elements to the aluminium surface.147
Bioinspired superhydrophobic Mg–Li alloys surfaces were constructed by using solution immersion and post-modification with fluoroalkylsilane (Fig. 13).148 The obtained Mg–Li alloys surfaces with peony-like micro- and nanoscale hierarchical structures presented improved corrosion resistance and long-term stable superhydrophobicity with a small water sliding angle. Superhydrophobic coatings on zinc were fabricated by a solution immersion technique into a methanol solution of perfluorosilane followed by a short annealing. Superhydrophobic films acted as effective corrosion barriers for the zinc when they were immersed in an aqueous solution of sodium chloride for up to 29 days.149
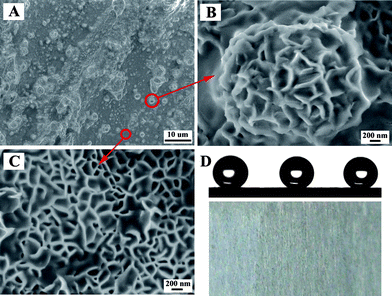 |
| Fig. 13 (A) Low-resolution SEM image of the superhydrophobic Mg–Li alloy surfaces. (B) High-resolution SEM image of a single microsized protrusion with the peony-like structure. (C) High-resolution SEM image of the non-protruding section on the alloy surface. (D) Digital photographs of superhydrophobic Mg–Li alloys after exposure to air for 180 days, the corresponding water droplet shapes on their surfaces were shown.148 | |
7.2 Microfluidic system
The superhydrophobic surface is a particularly interesting candidate for the realization of droplet-based microfluidic systems because the high mobility of water droplets on these surfaces offers the possibility of using more efficient approaches to droplet movement. Copper-based hierarchical surfaces were fabricated by etching polycrystalline plates, by electrodeposition of copper on copper foils, or by a combination of both (Fig. 14).150 After modification with thiol-modified fluorocarbons, superhydrophobic copper surfaces were achieved. These superhydrophobic surfaces were used to construct a droplet-based superhydrophobic chip using the developed structuring techniques from printed circuit board fabrication. Furthermore, after decorating with CuO nanowires by thermal oxidization, wire guidance with an optical fiber was obtained for droplet movement on the patterned superhydrophobic surfaces.
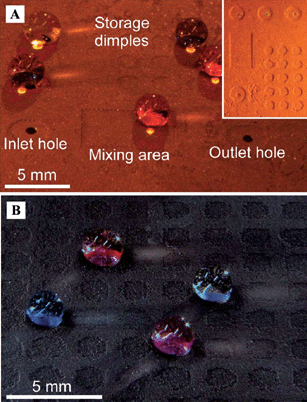 |
| Fig. 14 (A) Chip based on etched polycrystalline copper, inset showing chip layout. (B) Array of dimples on a surface made of nanowire decorated etched polycrystalline copper.150 | |
7.3 Oil–water separation
If the surface tension of a solid substrate is between that of water and oil, it might show both hydrophobicity and oleophilicity. A cooperation of appropriate surface roughness and chemical composition will result in superhydrophobicity and superoleophilicity simultaneously. Recently, it was found the combination of superhydrophobicity and superoleophilicity could produce novel functional surfaces possessing many potential industrial applications, such as oil–water separation.151–155 In section 4, we have discussed superhydrophobic and superoleophilic metallic surfaces. All the stainless steel and copper meshes mentioned in that section can possess the oil–water separation function.94–100
The first work of oil–water separation was achieved using a Teflon-coated stainless steel mesh film with both superhydrophobic and superoleophilic properties (Fig. 15).94 The water contact angle on the Teflon-coated mesh films is about 156°, indicating superhydrophobicity. However, when a diesel oil droplet comes into contact with the coating mesh film, the oil spreads quickly on the film and permeates thoroughly within just 240 ms, showing good superoleophilicity. If a mixture of oil and water is put on the mesh film, the water will remain on the upper part of the film, while the oil will gather together and penetrate through the film, which can be collected in the container below it.13 Up to now, different synthetic strategies have been developed to fabricated superhydrophobic and superoleophilic metallic materials for the separation of water and oil (such as diesel oil, toluene, xylene, diesel oil). However, the separation of water and oil mixtures by these metal meshes has only been investigated qualitatively. Recently, copper meshes possessing both superhydrophobic and superoleophilic properties were used for the separation of a small amount of water and hydrophobic solvents, such as hexane, petroleum oil, toluene, and diesel oil.98 The separation efficiency of copper meshes is quantitatively measured, which exhibited high separation efficiency. Mixtures of water and oily substances can be separated with up to and above 99% efficiency. This work may help stimulate the practical application of oil–water separation materials.
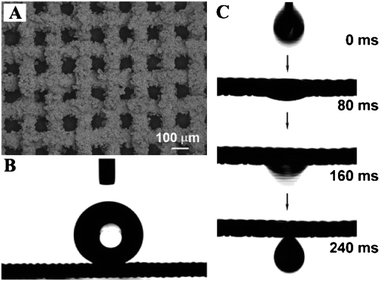 |
| Fig. 15 (A) SEM images of the coating mesh film prepared from a stainless steel mesh. (B) Shape of a water drop on the coating mesh film. (C) Quick penetrating process of diesel oil drop (within 240 ms).94 | |
7.4 Liquid transportation
Gradient surfaces can be used for the spontaneous motion of liquids, as discussed in Section 6. In recent years, many different methods have been developed to construct gradient surfaces for liquid self-transportation driven by chemical, thermal, mechanical, electrochemical, and photochemical strategies.121 Usually, the basic premise for moving a droplet is the creation of a gradient in the interfacial tension at the front and rear ends of the droplet.
A reversible and stepwise manipulation of droplets was reported by a dynamically controlled wetting gradient on gold substrates decorated with a ferrocenyl alkanethiol monolayer.156 The wetting gradient was generated by the application of an in-plane bias voltage to the gold substrate. Reversibility in the motion of nitrobenzene, dichloromethane, and hexadecane in aqueous solutions was realized by changing the bias direction. Furthermore, the motion of droplets in solutions was found to be used to manipulate microparticles on surfaces (Fig. 16). The liquid–liquid and/or solid-liquid–liquid interfaces acted as barriers for the hydrophilic glass beads in the microscale, resulting in the direct transport of them.
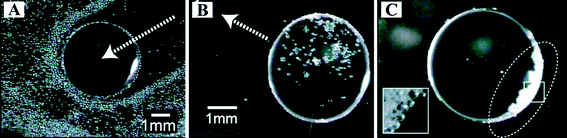 |
| Fig. 16 Transportation of glass beads by the droplet. (A) Hydrophilic glass beads were pushed by the oil droplet. The droplet moved from the upper right of the figure. A magnified image of the squared region is shown in the inset. Hydrophobic beads in the droplet (B) were carried with the motion of the oil droplet (C). The droplet shown in part C was moved for several millimetres in the direction shown by the arrow in part B.156 | |
7.5 Others
Recently, miniature boats with striking loading capacities were constructed using superhydrophobic copper meshes.157 The large loading capacity of the miniature boats was attributed to the air film surrounding the superhydrophobic meshes. Pore sizes of the copper meshes and the outer surface areas of the boats affected the loading capacity. Superhydrophobic surfaces combining surface chemistry with topological microfeatures exhibited drag reduction in laminar and turbulent flows, which was demonstrated by experimental and theoretical studies.158–161
8. Summary and outlook
In this review, we have summarized recent developments in metallic surfaces with special wettability, such as superhydrophobicity, superamphiphobicity, superoleophilicity, switchable wettability, wettability gradients, and others. Applications of metallic surfaces with special wettability in corrosion resistance, microfluidic systems, oil–water separation, liquid transportation, and other fields were also discussed in this review. Research on metallic surfaces with special wettability is of great importance for both fundamental research and practical applications. In order to fabricate metallic surfaces with desired wettability and functionalities and extend the practical applications of metallic materials in solid lubricating, self-cleaning, sensors, devices, and other fields, the following three basic points should be under consideration.
(i) Industry compatible approach to construct surface multiscale structures. Roughness plays a critical role in the achievement of multifunctional metallic surfaces. Although a wide variety of metallic surfaces with special wettability have been designed and fabricated, further fundamental investigations are still necessary to develop a facile method for the construction of functional metallic surfaces in industrial scale. Learning from nature should give us some inspiration to develop simple and low-cost methods to construct artificial functional structures.
(ii) Design of functional polymers. Surface chemical compositions also play an important role in achieving the desired wettability. In order to attain metallic surfaces with special wettability, various functional polymers have been used. However, the design of versatile non-fluorinated polymer materials is still a challenging task.
(iii) Construction of robust surfaces. Stability including mechanical and thermal stability is a crucial problem for the practical applications of metallic surfaces with special wettability. Therefore, the question of how to improve the stability of functional metallic surfaces will be an important issue in the future.
Nature is a school for scientists and engineers. Inspired by nature, a great number of non-metallic multifunctional surfaces have been constructed. Modern technologies not only strongly rely on these unique properties of metals, but urgently call for even better metals with multifunctions. Therefore, in order to extend the application fields of metals, biomimetic and bio-inspired approaches should provide an important avenue for the design and fabrication of bio-inspired advanced metallic materials with multiscale structures that are structurally and functionally optimized.
Acknowledgements
We appreciate the financial support of National Basic Research Program of China (2010CB934700, 2009CB930404, 2007CB936403), National High Technology Research and Development Program of China (2009AA03Z339), National Natural Science Foundation of China (20920102036, 20974113, 21001013), Specialized Research Fund for the Doctoral Program of Higher Education, and the Fundamental Research Funds for the Central Universities.
References
- K. Liu, X. Yao and L. Jiang, Chem. Soc. Rev., 2010, 39, 3240–3255 RSC.
- K. Koch, B. Bhushan and W. Barthlott, Prog. Mater. Sci., 2009, 54, 137–178 CrossRef CAS.
- L. Feng, S. H. Li, Y. S. Li, H. J. Li, L. J. Zhang, J. Zhai, Y. L. Song, B. Q. Liu, L. Jiang and D. B. Zhu, Adv. Mater., 2002, 14, 1857–1860 CrossRef CAS.
- Y. M. Zheng, X. F. Gao and L. Jiang, Soft Matter, 2007, 3, 178–182 RSC.
- X. F. Gao, X. Yan, X. Yao, L. Xu, K. Zhang, J. H. Zhang, B. Yang and L. Jiang, Adv. Mater., 2007, 19, 2213–2217 CrossRef CAS.
- C. W. Guo, L. Feng, J. Zhai, G. J. Wang, Y. L. Song, L. Jiang and D. B. Zhu, ChemPhysChem, 2004, 5, 750–753 CrossRef CAS.
- L. Feng, Y. A. Zhang, J. M. Xi, Y. Zhu, N. Wang, F. Xia and L. Jiang, Langmuir, 2008, 24, 4114–4119 CrossRef CAS.
- W. R. Hansen and K. Autumn, Proc. Natl. Acad. Sci. U. S. A., 2005, 102, 385–389 CrossRef CAS.
- A. R. Parker and C. R. Lawrence, Nature, 2001, 414, 33–34 CrossRef.
- Y. M. Zheng, H. Bai, Z. B. Huang, X. L. Tian, F. Q. Nie, Y. Zhao, J. Zhai and L. Jiang, Nature, 2010, 463, 640–643 CrossRef CAS.
- M. J. Liu, S. T. Wang, Z. X. Wei, Y. L. Song and L. Jiang, Adv. Mater., 2009, 21, 665–669 CrossRef CAS.
- X. M. Li, D. Reinhoudt and M. Crego-Calama, Chem. Soc. Rev., 2007, 36, 1350–1368 RSC.
- T. L. Sun, L. Feng, X. F. Gao and L. Jiang, Acc. Chem. Res., 2005, 38, 644–652 CrossRef CAS.
- M. J. Liu, Y. M. Zheng, J. Zhai and L. Jiang, Acc. Chem. Res., 2010, 43, 368–377 CrossRef CAS.
- X. J. Feng and L. Jiang, Adv. Mater., 2006, 18, 3063–3078 CrossRef CAS.
- F. Xia and L. Jiang, Adv. Mater., 2008, 20, 2842–2858 CrossRef CAS.
- D. Quéré, Annu. Rev. Mater. Res., 2008, 38, 71–99 CrossRef CAS.
- C. R. Crick and I. P. Parkin, Chem.–Eur. J., 2010, 16, 3568–3588 CrossRef CAS.
- X. Zhang, F. Shi, J. Niu, Y. G. Jiang and Z. Q. Wang, J. Mater. Chem., 2008, 18, 621–633 RSC.
- R. Blossey, Nat. Mater., 2003, 2, 301–306 CrossRef CAS.
- M. Callies and D. Quéré, Soft Matter, 2005, 1, 55–61 RSC.
- P. Roach, N. J. Shirtcliffe and M. I. Newton, Soft Matter, 2008, 4, 224–240 RSC.
- S. Morgenthaler, C. Zink and N. D. Spencer, Soft Matter, 2008, 4, 419–434 RSC.
- M. L. Ma and R. M. Hill, Curr. Opin. Colloid Interface Sci., 2006, 11, 193–202 CrossRef CAS.
- M. Nosonovsky and B. Bhushan, Curr. Opin. Colloid Interface Sci., 2009, 14, 270–280 CrossRef CAS.
- B. J. Berne, J. D. Weeks and R. H. Zhou, Annu. Rev. Phys. Chem., 2009, 60, 85–103 CrossRef CAS.
- M. Nosonovsky and B. Bhushan, Adv. Funct. Mater., 2008, 18, 843–855 CrossRef CAS.
- K. Lu, Science, 2010, 328, 319–320 CrossRef CAS.
- H. Bai, C. Li and G. Q. Shi, J. Adhes. Sci. Technol., 2008, 22, 1819–1839 CrossRef CAS.
- S. T. Wang, L. Feng and L. Jiang, Adv. Mater., 2006, 18, 767–770 CrossRef CAS.
- D. K. Sarkar and N. Saleema, Surf. Coat. Technol., 2010, 204, 2483–2486 CrossRef CAS.
- J. M. Xi, L. Feng and L. Jiang, Appl. Phys. Lett., 2008, 92, 053102 CrossRef.
- Z. G. Guo, W. M. Liu and B. L. Su, Appl. Phys. Lett., 2008, 92, 063104 CrossRef.
- Y. Li, W. Z. Jia, Y. Y. Song and X. H. Xia, Chem. Mater., 2007, 19, 5758–5764 CrossRef CAS.
- X. H. Chen, G. Bin Yang, L. H. Kong, D. Dong, L. G. Yu, J. M. Chen and P. Y. Zhang, Cryst. Growth Des., 2009, 9, 2656–2661 CrossRef CAS.
- I. A. Larmour, S. E. J. Bell and G. C. Saunders, Angew. Chem., Int. Ed., 2007, 46, 1710–1712 CrossRef CAS.
- X. H. Xu, Z. Z. Zhang and J. Yang, Langmuir, 2010, 26, 3654–3658 CrossRef CAS.
- X. F. Gao and L. Jiang, Nature, 2004, 432, 36–36 CrossRef CAS.
- X. Yao, Q. Chen, L. Xu, Q. Li, Y. Song, X. Gao, D. Quéré and L. Jiang, Adv. Funct. Mater., 2010, 20, 656–662 CrossRef CAS.
- N. J. Shirtcliffe, G. McHale, M. I. Newton, G. Chabrol and C. C. Perry, Adv. Mater., 2004, 16, 1929–1932 CrossRef CAS.
- W. J. Xi, Z. M. Qiao, C. L. Zhu, A. Jia and M. Li, Appl. Surf. Sci., 2009, 255, 4836–4839 CrossRef CAS.
- N. J. Shirtcliffe, G. McHale, M. I. Newton and C. C. Perry, Langmuir, 2005, 21, 937–943 CrossRef CAS.
- Y. F. Zhang, X. Q. Yu, Q. H. Zhou, F. Chen and K. N. Li, Appl. Surf. Sci., 2010, 256, 1883–1887 CrossRef CAS.
- Z. G. Guo, J. Fang, J. C. Hao, Y. M. Liang and W. M. Liu, ChemPhysChem, 2006, 7, 1674–1677 CrossRef CAS.
- Z. G. Guo, F. B. Han, L. B. Wang and W. M. Liu, Thin Solid Films, 2007, 515, 7190–7194 CrossRef CAS.
- X. H. Chen, L. H. Kong, D. Dong, G. B. Yang, L. G. Yu, J. M. Chen and P. Y. Zhang, J. Phys. Chem. C, 2009, 113, 5396–5401 CrossRef CAS.
- Y. C. Hong, S. C. Cho, D. H. Shin, S. H. Lee and H. S. Uhm, Scr. Mater., 2008, 59, 776–779 CrossRef CAS.
- Y. Zhang, H. Wang, B. Yan, Y. W. Zhang, P. Yin, G. L. Shen and R. Q. Yu, J. Mater. Chem., 2008, 18, 4442–4449 RSC.
- F. Z. Zhang, L. L. Zhao, H. Y. Chen, S. L. Xu, D. G. Evans and X. Duan, Angew. Chem., Int. Ed., 2008, 47, 2466–2469 CrossRef CAS.
- H. Wang, D. Dai and X. D. Wu, Appl. Surf. Sci., 2008, 254, 5599–5601 CrossRef CAS.
- S. Desbief, B. Grignard, C. Detrembleur, R. Rioboo, A. Vaillant, D. Seveno, M. Voue, J. De Coninck, A. M. Jonas, C. Jerome, P. Damman and R. Lazzaroni, Langmuir, 2010, 26, 2057–2067 CrossRef CAS.
- Z. G. Guo, F. Zhou, J. C. Hao and W. M. Liu, J. Am. Chem. Soc., 2005, 127, 15670–15671 CrossRef CAS.
- Z. G. Guo, F. Zhou, J. C. Hao, Y. M. Liang, W. M. Liu and W. T. S. Huck, Appl. Phys. Lett., 2006, 89, 081911 CrossRef.
- B. T. Qian and Z. Q. Shen, Langmuir, 2005, 21, 9007–9009 CrossRef CAS.
- Z. J. Chen, Y. B. Guo and S. M. Fang, Surf. Interface Anal., 2010, 42, 1–6 CAS.
- Z. G. Guo and W. M. Liu, Appl. Phys. Lett., 2007, 90, 223111 CrossRef.
- Q. Wang, B. W. Zhang, M. N. Qu, J. Y. Zhang and D. Y. He, Appl. Surf. Sci., 2008, 254, 2009–2012 CrossRef CAS.
- X. Y. Fu and X. H. He, Appl. Surf. Sci., 2008, 255, 1776–1781 CrossRef CAS.
- M. N. Qu, B. W. Zhang, S. Y. Song, L. Chen, J. Y. Zhang and X. P. Cao, Adv. Funct. Mater., 2007, 17, 593–596 CrossRef CAS.
- A. Raman, R. Quinones, L. Barriger, R. Eastman, A. Parsi and E. S. Gawalt, Langmuir, 2010, 26, 1747–1754 CrossRef CAS.
- Z. G. Guo, J. Liang, J. Fang, B. G. Guo and W. M. Liu, Adv. Eng. Mater., 2007, 9, 316–321 CrossRef CAS.
- C. D. Gu, H. Ren, J. P. Tu and T. Y. Zhang, Langmuir, 2009, 25, 12299–12307 CrossRef CAS.
- W. C. Wu, M. Chen, S. Liang, X. L. Wang, J. M. Chen and F. Zhou, J. Colloid Interface Sci., 2008, 326, 478–482 CrossRef CAS.
- J. T. Han, Y. Jang, D. Y. Lee, J. H. Park, S. H. Song, D. Y. Ban and K. Cho, J. Mater. Chem., 2005, 15, 3089–3092 RSC.
- Y. Ofir, B. Samanta, P. Arumugam and V. M. Rotello, Adv. Mater., 2007, 19, 4075–4079 CrossRef CAS.
- F. Shi, Z. Q. Wang and X. Zhang, Adv. Mater., 2005, 17, 1005–1009 CrossRef CAS.
- H. Q. Liu, S. Szunerits, M. Pisarek, W. G. Xu and R. Boukherroub, ACS Appl. Mater. Interfaces, 2009, 1, 2086–2091 CrossRef CAS.
- B. Wu, M. Zhou, J. Li, X. Ye, G. Li and L. Cai, Appl. Surf. Sci., 2009, 256, 61–66 CrossRef CAS.
- Z. W. Cao, D. B. Xiao, L. T. Kang, Z. L. Wang, S. X. Zhang, Y. Ma, H. B. Fu and J. N. Yao, Chem. Commun., 2008, 2692–2694 RSC.
- X. Zhang, F. Shi, X. Yu, H. Liu, Y. Fu, Z. Q. Wang, L. Jiang and X. Y. Li, J. Am. Chem. Soc., 2004, 126, 3064–3065 CrossRef CAS.
- S. Sethi and A. Dhinojwala, Langmuir, 2009, 25, 4311–4313 CrossRef CAS.
- A. M. Kietzig, S. G. Hatzikiriakos and P. Englezos, Langmuir, 2009, 25, 4821–4827 CrossRef CAS.
- H. Wang, M. Zou and R. Wei, Thin Solid Films, 2009, 518, 1571–1574 CrossRef CAS.
- Y. Li, C. C. Li, S. O. Cho, G. T. Duan and W. P. Cai, Langmuir, 2007, 23, 9802–9807 CrossRef CAS.
- A. Tuteja, W. J. Choi, G. H. McKinley, R. E. Cohen and M. F. Rubner, MRS Bulletin, 2008, 33, 752–758 CAS.
- H. J. Li, X. B. Wang, Y. L. Song, Y. Q. Liu, Q. S. Li, L. Jiang and D. B. Zhu, Angew. Chem., Int. Ed., 2001, 40, 1743–1746 CrossRef CAS.
- S. M. M. Ramos, A. Benyagoub, B. Canut and C. Jamois, Langmuir, 2010, 26, 5141–5146 CrossRef CAS.
- M. Nicolas, F. Guittard and S. Géribaldi, Angew. Chem., Int. Ed., 2006, 45, 2251–2254 CrossRef CAS.
- A. Tuteja, W. Choi, M. L. Ma, J. M. Mabry, S. A. Mazzella, G. C. Rutledge, G. H. McKinley and R. E. Cohen, Science, 2007, 318, 1618–1622 CrossRef CAS.
- X. J. Liu, W. C. Wu, X. L. Wang, Z. Z. Luo, Y. M. Liang and F. Zhou, Soft Matter, 2009, 5, 3097–3105 RSC.
- A. Steele, I. Bayer and E. Loth, Nano Lett., 2009, 9, 501–505 CrossRef CAS.
- R. T. R. Kumar, K. B. Mogensen and P. Boggild, J. Phys. Chem. C, 2010, 114, 2936–2940 CrossRef CAS.
- Q. D. Xie, J. Xu, L. Feng, L. Jiang, W. H. Tang, X. D. Luo and C. C. Han, Adv. Mater., 2004, 16, 302–305 CrossRef CAS.
- L. Joly and T. Biben, Soft Matter, 2009, 5, 2549–2557 RSC.
- Y. Tian, H. Q. Liu and Z. F. Deng, Chem. Mater., 2006, 18, 5820–5822 CrossRef CAS.
- T. Darmanin and F. Guittard, J. Am. Chem. Soc., 2009, 131, 7928–7933 CrossRef CAS.
- T. Darmanin and F. Guittard, Chem. Commun., 2009, 2210–2211 RSC.
- T. Darmanin and F. Guittard, J. Colloid Interface Sci., 2009, 335, 146–149 CrossRef CAS.
- H. F. Meng, S. T. Wang, J. M. Xi, Z. Y. Tang and L. Jiang, J. Phys. Chem. C, 2008, 112, 11454–11458 CrossRef CAS.
- A. Hozumi and T. J. McCarthy, Langmuir, 2010, 26, 2567–2573 CrossRef CAS.
- W. H. Wang, Adv. Mater., 2009, 21, 4524–4544 CrossRef CAS.
- K. Zhao, K. S. Liu, J. F. Li, W. H. Wang and L. Jiang, Scr. Mater., 2009, 60, 225–227 CrossRef CAS.
- S. S. Chhatre, W. Choi, A. Tuteja, K. C. Park, J. M. Mabry, G. H. McKinley and R. E. Cohen, Langmuir, 2010, 26, 4027–4035 CrossRef CAS.
- L. Feng, Z. Y. Zhang, Z. H. Mai, Y. M. Ma, B. Q. Liu, L. Jiang and D. B. Zhu, Angew. Chem., Int. Ed., 2004, 43, 2012–2014 CrossRef CAS.
- Q. J. Wang, Z. Cui, Y. Mao and Q. M. Chen, Appl. Surf. Sci., 2007, 253, 9054–9060 CrossRef CAS.
- H. Yang, P. H. Pi, Z. Q. Cai, X. F. Wen, X. B. Wang, J. Cheng and Z. R. Yang, Appl. Surf. Sci., 2010, 256, 4095–4102 CrossRef CAS.
- S. T. Wang, Y. L. Song and L. Jiang, Nanotechnology, 2007, 18, 015103 CrossRef.
- Q. M. Pan, M. Wang and H. B. Wang, Appl. Surf. Sci., 2008, 254, 6002–6006 CrossRef CAS.
- C. X. Wang, T. J. Yao, J. Wu, C. Ma, Z. X. Fan, Z. Y. Wang, Y. R. Cheng, Q. Lin and B. Yang, ACS Appl. Mater. Interfaces, 2009, 1, 2613–2617 CrossRef CAS.
- M. Li, J. H. Xu and Q. H. Lu, J. Mater. Chem., 2007, 17, 4772–4776 RSC.
- T. Darmanin, M. Nicolas and F. Guittard, Langmuir, 2008, 24, 9739–9746 CrossRef CAS.
- T. Darmanin, M. Nicolas and F. Guittard, Phys. Chem. Chem. Phys., 2008, 10, 4322–4326 RSC.
- B. W. Xin and J. C. Hao, Chem. Soc. Rev., 2010, 39, 769–782 RSC.
- F. Xia, Y. Zhu, L. Feng and L. Jiang, Soft Matter, 2009, 5, 275–281 RSC.
- S. T. Wang, Y. L. Song and L. Jiang, J. Photochem. Photobiol., C, 2007, 8, 18–29 CrossRef CAS.
- X. Yu, Z. Q. Wang, Y. G. Jiang, F. Shi and X. Zhang, Adv. Mater., 2005, 17, 1289–1293 CrossRef CAS.
- Y. G. Jiang, Z. Q. Wang, X. Yu, F. Shi, H. P. Xu and X. Zhang, Langmuir, 2005, 21, 1986–1990 CrossRef CAS.
- Y. G. Jiang, P. B. Wan, M. Smet, Z. Q. Wang and X. Zhang, Adv. Mater., 2008, 20, 1972–1977 CrossRef CAS.
- H. S. Lim, S. G. Lee, D. H. Lee, D. Y. Lee, S. Lee and K. Cho, Adv. Mater., 2008, 20, 4438–4441 CrossRef CAS.
- F. Avbelj and R. L. Baldwin, Proc. Natl. Acad. Sci. U. S. A., 2009, 106, 3137–3141 CrossRef CAS.
- S. T. Wang, H. J. Liu, D. S. Liu, X. Y. Ma, X. H. Fang and L. Jiang, Angew. Chem., Int. Ed., 2007, 46, 3915–3917 CrossRef CAS.
- P. B. Wan, Y. G. Jiang, Y. P. Wang, Z. Q. Wang and X. Zhang, Chem. Commun., 2008, 5710–5712 RSC.
- M. D. Pei, B. Wang, E. Li, X. H. Zhang, X. M. Song and H. Yan, Appl. Surf. Sci., 2010, 256, 5824–5827 CrossRef CAS.
- D. A. Wang, X. L. Wang, X. J. E. Liu and F. Zhou, J. Phys. Chem. C, 2010, 114, 9938–9944 CrossRef CAS.
- J. Wu, H. J. Bai, X. B. Zhang, J. J. Xu and H. Y. Chen, Langmuir, 2010, 26, 1191–1198 CrossRef CAS.
- Z. J. Cheng, L. Feng and L. Jiang, Adv. Funct. Mater., 2008, 18, 3219–3225 CrossRef CAS.
- J. Lahann, S. Mitragotri, T. N. Tran, H. Kaido, J. Sundaram, I. S. Choi, S. Hoffer, G. A. Somorjai and R. Langer, Science, 2003, 299, 371–374 CrossRef CAS.
- T. G. Ruardy, J. M. Schakenraad, H. C. van der Mei and H. J. Busscher, Surf. Sci. Rep., 1997, 29, 3–30 CrossRef.
- M. S. Kim, G. Khang and H. B. Lee, Prog. Polym. Sci., 2008, 33, 138–164 CrossRef CAS.
- M. H. Bolin, K. Svennersten, D. Nilsson, A. Sawatdee, E. W. H. Jager, A. Richter-Dahlfors and M. Berggren, Adv. Mater., 2009, 21, 4379 CrossRef CAS.
- J. Genzer and R. R. Bhat, Langmuir, 2008, 24, 2294–2317 CrossRef CAS.
- J. L. Zhang and Y. C. Han, Chem. Soc. Rev., 2010, 39, 676–693 RSC.
- M. J. Fasolka, C. M. Stafford and K. L. Beers, Adv. Polym. Sci., 2010, 225, 63–105 CAS.
- M. Reyssat, F. Pardo and D. Quere, Europhys. Lett., 2009, 87, 36003 CrossRef.
- R. R. Bhat, M. R. Tomlinson, T. Wu and J. Genzer, Adv. Polym. Sci., 2006, 198, 51–124 CAS.
- K. Ichimura, S. K. Oh and M. Nakagawa, Science, 2000, 288, 1624–1626 CrossRef CAS.
- H. P. Greenspan, J. Fluid Mech., 1978, 84, 125–143 CrossRef.
- M. K. Chaudhury and G. M. Whitesides, Science, 1992, 256, 1539–1541 CrossRef CAS.
- A. Diguet, R. M. Guillermic, N. Magome, A. Saint-Jalmes, Y. Chen, K. Yoshikawa and D. Baigl, Angew. Chem., Int. Ed., 2009, 48, 9281–9284 CrossRef CAS.
- A. M. Cazabat, F. Heslot, S. M. Troian and P. Carles, Nature, 1990, 346, 824–826 CrossRef CAS.
- O. D. Velev, B. G. Prevo and K. H. Bhatt, Nature, 2003, 426, 515–516 CrossRef CAS.
- X. P. Zheng, H. P. Zhao, L. T. Gao, J. L. Liu, S. W. Yu and X. Q. Feng, J. Colloid Interface Sci., 2008, 323, 133–140 CrossRef CAS.
- B. S. Gallardo, V. K. Gupta, F. D. Eagerton, L. I. Jong, V. S. Craig, R. R. Shah and N. L. Abbott, Science, 1999, 283, 57–60 CrossRef CAS.
- S. Daniel, M. K. Chaudhury and J. C. Chen, Science, 2001, 291, 633–636 CrossRef CAS.
- J. Tersoff, D. E. Jesson and W. X. Tang, Science, 2009, 324, 236–238 CrossRef CAS.
- S. Morgenthaler, S. W. Lee, S. Zurcher and N. D. Spencer, Langmuir, 2003, 19, 10459–10462 CrossRef CAS.
- S. M. Morgenthaler, S. Lee and N. D. Spencer, Langmuir, 2006, 22, 2706–2711 CrossRef CAS.
- E. Beurer, N. V. Venkataraman, A. Rossi, F. Bachmann, R. Engeli and N. D. Spencer, Langmuir, 2010, 26, 8392–8399 CrossRef CAS.
- N. Ballav, A. Shaporenko, A. Terfort and M. Zharnikov, Adv. Mater., 2007, 19, 998–1000 CrossRef CAS.
- P. Burgos, M. Geoghegan and G. J. Leggett, Nano Lett., 2007, 7, 3747–3752 CrossRef CAS.
- X. Yu, Z. Q. Wang, Y. G. Jiang and X. Zhang, Langmuir, 2006, 22, 4483–4486 CrossRef CAS.
- L. Wang, B. Peng and Z. Su, Langmuir, 2010, 26, 12203–12208 CrossRef CAS.
- S. G. Chen, Y. Chen, Y. H. Lei and Y. S. Yin, Electrochem. Commun., 2009, 11, 1675–1679 CrossRef CAS.
- T. Liu, Y. S. Yin, S. G. Chen, X. T. Chang and S. Cheng, Electrochim. Acta, 2007, 52, 3709–3713 CrossRef CAS.
- Y. S. Yin, T. Liu, S. G. Chen, T. Liu and S. Cheng, Appl. Surf. Sci., 2008, 255, 2978–2984 CrossRef CAS.
- T. He, Y. C. Wang, Y. J. Zhang, Q. Iv, T. G. Xu and T. Liu, Corros. Sci., 2009, 51, 1757–1761 CrossRef CAS.
- P. M. Barkhudarov, P. B. Shah, E. B. Watkins, D. A. Doshi, C. J. Brinker and J. Majewski, Corros. Sci., 2008, 50, 897–902 CrossRef CAS.
- K. S. Liu, M. L. Zhang, J. Zhai, J. Wang and L. Jiang, Appl. Phys. Lett., 2008, 92, 183103 CrossRef.
- H. Q. Liu, S. Szunerits, W. G. Xu and R. Boukherroub, ACS Appl. Mater. Interfaces, 2009, 1, 1150–1153 CrossRef CAS.
- F. Mumm, A. T. J. van Helvoort and P. Sikorski, ACS Nano, 2009, 3, 2647–2652 CrossRef CAS.
- J. K. Yuan, X. G. Liu, O. Akbulut, J. Q. Hu, S. L. Suib, J. Kong and F. Stellacci, Nat. Nanotechnol., 2008, 3, 332–336 CrossRef CAS.
- C. H. Su, Appl. Surf. Sci., 2009, 256, 1413–1418 CrossRef CAS.
- Y. L. Zhang, S. Wei, F. J. Liu, Y. C. Du, S. Liu, Y. Y. Ji, T. Yokoi, T. Tatsumi and F. S. Xiao, Nano Today, 2009, 4, 135–142 CrossRef.
- J. L. Zhang, W. H. Huang and Y. C. Han, Macromol. Rapid Commun., 2006, 27, 804–808 CrossRef CAS.
- C. W. Tu, C. H. Tsai, C. F. Wang, S. W. Kuo and F. C. Chang, Macromol. Rapid Commun., 2007, 28, 2262–2266 CrossRef CAS.
- R. Yamada and H. Tada, Langmuir, 2005, 21, 4254–4256 CrossRef CAS.
- Q. M. Pan and M. Wang, ACS Appl. Mater. Interfaces, 2009, 1, 420–423 CrossRef CAS.
- J. P. Rothstein, Annu. Rev. Fluid Mech., 2010, 42, 89–109 CrossRef.
- Y. L. Zhou, M. Li, B. Su and Q. H. Lu, J. Mater. Chem., 2009, 19, 3301–3306 RSC.
- G. McHale, M. I. Newton and N. J. Shirtcliffe, Soft Matter, 2010, 6, 714–719 RSC.
- M. B. Martell, J. P. Rothstein and J. B. Perot, Phys. Fluids, 2010, 22, 065102 Search PubMed.
|
This journal is © The Royal Society of Chemistry 2011 |
Click here to see how this site uses Cookies. View our privacy policy here.