DOI:
10.1039/C0NR00015A
(Paper)
Nanoscale, 2010,
2, 1178-1184
Amino acid-assisted one-pot assembly of Au, Pt nanoparticles onto one-dimensional ZnO microrods
Received
7th January 2010
, Accepted 4th March 2010
First published on
17th May 2010
Abstract
In this contribution, a facile one-pot strategy is developed for the assembly of noble metal (Au and Pt) nanoparticles onto one-dimensional ZnO microrods using a green non-toxic reagent amino acid, lysine with two amino functional groups as the capping agent. Noble metal nanoparticles with a small size capped by lysine are formed and simultaneously anchored onto the surface of ZnO. No pre-functionalization of the ZnO support is needed, hence simplifying the synthesis and reducing the fabrication cost. Inspired by the catalytic properties of Au nanoparticles in both catalyst and sensor materials, we have examined the gas sensing performances towards ethanol detection. Obtained results demonstrate that after decoration by Au nanoparticles, the sensor shows significantly enhanced sensing performances in terms of high sensitivity, fast response and recovery, excellent reproducibility and good selectivity. The improved sensor properties are probably ascribed to the catalytic Au promoters and the Schottky barriers at the metal and semiconductor interface.
1. Introduction
Assembly of individual components in a synergic manner has been a hot topic of nanoscience and nanotechnology.1 From this viewpoint, assembly or organization of nanomaterials is a powerful technique for the construction of nanobuilding blocks and the bottom-up fabrication of nanodevices with advanced performances.2–4 Enormous efforts have been directed to the synthesis of multifunctional nanomaterials by assembling two or more components into well-organized and defined nanostructures. Using assembly, colloidal nanoparticles can be organized onto various supports to create a variety of functional nanomaterials for multiple applications. The assemblies of noble metal particles onto semiconductor oxides have attracted even more attention, because the complex composite can provide superior properties over their single counterpart for applications such as optics, electronics, catalysts and chemical sensors.5–8 Generally, the assembly of nanoparticles depends on the strong interparticle forces such as van der Waals and electrostatic interactions to form an integral system.1 For this purpose, surface functionalization of either host support or guest nanoparticles by organic linkers is usually a requisite for the successful construction of hybrid nanostructures.6
ZnO, as a n-type semiconductor, has been extensively studied for various device applications.9,10 Due to its unique crystal habit, ZnO can be easily synthesized into various morphologies including one-dimensional (nanorods and nanowires),11–13 two-dimensional (nanobelts and nanosheet)14–16 and three-dimensional (hierarchical architectures and porous hollow spheres)17–20 nanostructures using a very simple solution method. The diversity of ZnO nanostructures allows one to finely explore or tune their size and morphology-dependent properties. One-dimensional nanostructures are more advantageous for electronic and sensor applications, because its ordered nanostructure is highly beneficial to electron transportation.21,22 In addition, one-dimensional nanostructures also possess a large surface-to-volume ratio,23–28 which means that surface atoms have more opportunities to participate in the surface reactions, especially for ZnO-based sensor materials, which belongs to the surface-controlled type.26 In recent years, research attention in the area of chemical sensors has been focused on further increasing the sensor sensitivity. A very efficient strategy is to load noble metals such as Au, Pt and Pd onto an oxide matrix as sensitizer or promoter to improve the sensing reactions.29–31 Many approaches have been developed to assemble noble metals onto semiconductors. For instance, silicane coupling agents32 and polyelectrolytes33 have proven to be most effective in attaching diverse noble metals onto various support materials. Recently, Zhang et al.34 developed a PVP-assisted method for attaching Pd nanoparticles onto ZnO nanowires and the as-obtained hybrid material showed enhanced sensing performances towards detecting H2S gas. A more recent report from Joshi and co-workers26 demonstrated the synthesis of Au decorated ZnO nanowires for CO sensing. While these studies are unique and effective, the synthetic processes are not facile and convenient due to their multiple steps, where the noble metal nanoparticles are chemically pre-formed and subsequently attached onto support materials.
In this contribution, we have developed a facile one-pot strategy to immobilize noble metals (Au and Pt) onto one-dimensional ZnO microrods using amino acid, i.e., lysine as the capping agent for noble metals. The noble metal nanoparticles with a small size capped by lysine are formed and simultaneously anchored onto the surface of ZnO. This approach is convenient, time-saving and requires no need for pre-functionalization of ZnO support and pre-synthesis of noble metals. Furthermore, we have fabricated a chemical sensor based on the synthesized Au-decorated ZnO hybrid materials. A systematic sensing test is performed using mainly ethanol as the probe gas to evaluate the sensing properties of the sensor. Our results demonstrate that the Au-decorated sensor shows significantly enhanced response for ethanol in comparison to pristine ZnO materials. The Au-decorated ZnO sensor also possesses good selectivity and reproducibility towards ethanol detection. It is expected that this novel synthesis can be extended to fabricate other hybrid functional nanomaterials.
2. Experimental
2.1 Materials
Chemicals such as Zn(NO3)2·6H2O, hexamethylenetetramine (HMT), ethanol, lysine, and NaBH4 were of analytical grade and purchased from Guangfu Fine Chemical Research Institute (Tianjin, China). HAuCl4·4H2O and H2PtCl6·6H2O were obtained from Yingdaxigui Chemical Reagent Company (Tianjin, China). Distilled water was used throughout the experiments.
2.2 Preparation of ZnO microrods
ZnO microrods were synthesized using the well-established HMT-assisted hydrothermal method.11,12 80 ml of 0.01 M aqueous solution of Zn(NO3)2 and HMT was put into a Teflon autoclave with a volume of 100 ml and heated at 95 °C for 5 h. After cooling to room temperature, the white product was collected by centrifugation and washed with water and absolute ethanol several times, then dried at 80 °C.
This is a facile, fast one-pot synthesis, where noble metals were formed in the presence of lysine as the capping agent,35 and simultaneously anchored onto the surface of ZnO microrods. 0.3 g of ZnO was dispersed into 25 ml of H2O, followed by addition of 6 ml of 0.01 M HAuCl4 and 6 ml of 0.01 M lysine. The suspension was sonicated for 20 min, and then 5 ml of 0.1 M fresh NaBH4 solution was added to reduce HAuCl4 to metallic Au nanoparticles. After ca. 1 h, the precipitate with a purplish color was centrifuged and washed with water and absolute ethanol and dried at 80 °C. The change in color from white of pristine ZnO to purple also revealed the successful decoration of Au onto ZnO microrods. The assembly of Pt onto ZnO was similar to the process for Au with the only change being 9 ml of 0.0078 M H2PtCl6 solution instead of HAuCl4.
2.4 Sensor fabrication and test
Prior to the fabrication of the sensor, Au decorated ZnO microrods were thermally treated at 300 °C for 1 h to remove lysine. Detailed sensor fabrication is as follows. Au-decorated ZnO microrods were mixed with several drops of H2O to form a dilute slurry. The slurry was then coated onto the surface of an alumina tube (Fig. 1(a)) with a diameter of 1 mm and length of 4 mm, positioned with two Au electrodes and four Pt wires on each end. A Ni–Cr alloy filament was put through the alumina tube and used as a heater by tuning the heating voltage. The alumina tube was then welded onto a pedestal with six probes (Fig. 1(b)). Fig. 1(c) displays the photograph of the completed sensor. Gas sensing tests were performed on a static test system (HW-30A, HanWei Electronics Co., Ltd., Henan Province, China) using air as the reference and diluting gas at a relative humidity (RH) of 30–50%. The gas concentration was calculated according to the volumes of the gas chamber on a HW-30A system and test gas. Target gas such as ethanol with a known volume was injected into the gas chamber by a microsyringe. A heater in the gas chamber is used to gasify the liquid ethanol. The working principle is shown in Fig. 1(d). A load resistance (RL) is connected in series to the sensor. The sensor signal voltage (Vout) was collected by a computer at a test circuit voltage of 5 V (Vc). The sensor sensitivity is defined as the ratio of Rg/Ra, where Rg and Ra are the electrical resistance of the sensor in test gas and in air, respectively. The response time (τres) is defined as the time for the sensor to reach 90% of its maximum response.
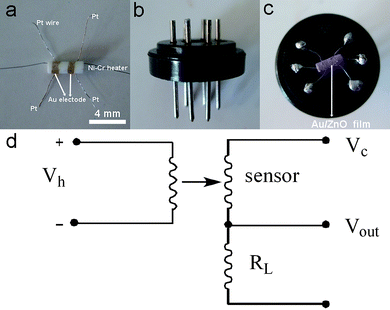 |
| Fig. 1 Fabrication and test of gas sensor (a) alumina tube; (b) pedestal; (c) completed sensor; and (d) working principle of sensing test. | |
3. Results and discussion
3.1 Synthesis and characterization
The synthetic process for the assembly of noble metals is illustrated in Fig. 2. This is a quasi one-pot approach, where Au nanoparticles are formed in the presence of lysine capping agents and simultaneously locked on the surface of ZnO microrods. Here it should be noted that the synthesis is quite facile, because no pre-functionalization of the ZnO support is needed, hence reducing the fabrication cost and simplifying the synthesis. Amino acid or peptides have many functional groups such as –NH2 and –COOH. Both amino and carboxylic groups are known to be capable of coordinating with transition metal ions,36–38 thus implying that amino acid may serve as a bridge or linker to connect noble metals with metal oxides. In addition, lysine is a green, non-toxic reagent and is a new kind of capping agent for producing monodispersed Au nanoparticles with a small size.35 The lysine-capped Au nanoparticles have been used to prepare CO oxidation catalysts,39,40 however the application for preparing sensor materials has not been reported.
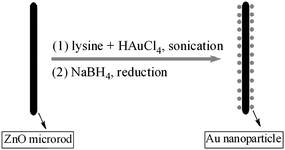 |
| Fig. 2 Schematic illustration of the one-pot procedure for assembling Au nanoparticles on ZnO microrods. | |
Fig. 3(a) displays the TEM image of the lysine-capped Au nanoparticles prepared according to the literature procedure,35 revealing a very small size of ca. 3–5 nm. The SEM image of the hydrothermally derived ZnO microrods is shown in Fig. 3(b). It can be seen that these microrods have a smooth surface and a diameter in the range of tens to hundreds of nanometres. XRD analysis (Fig. 4(a)) confirms the product is pure phase ZnO with all the diffraction peaks indexation to the wurtzite structure (JCPDS No. 36–1451). From Fig. 4(a), it is also observed that the product after assembly of Au nanoparticles shows significant diffraction peaks at ca. 38.2°, 44.4°, 64.6°, and 77.2°, which are ascribed to the (111), (200), (220), and (311) planes of face-centered cubic (fcc) Au (JCPDS No. 01-1172).
The assembly of Au nanoparticles on ZnO microrods has been observed by TEM techniques. Fig. 4(b–d) exhibits the TEM images of different magnification for the Au decorated ZnO. From these images, especially in Fig. 4(c and d) with a high magnification, Au nanoparticles can be clearly observed, together with a small size and a high dispersion on the surface of ZnO matrix. To further confirm the successful assembly of Au nanoparticles on ZnO, XPS analysis was conducted. The high resolution XPS spectra of Au 4f and Zn 2p are shown in Fig. 5. Fig. 5(a) displays significant binding energies at 83.5 and 87.3 eV, which are characteristic of Au. Note that an interference peak at 88.7 eV due to Zn 3p is also present. The binding energies at 1021.9 and 1044.7 eV in Fig. 5(b) are ascribed to Zn 2p.
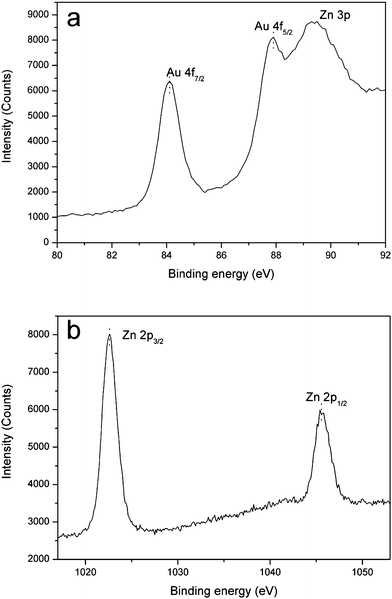 |
| Fig. 5 XPS spectra (a) Au 4f and (b) Zn 2p of Au nanoparticles decorated ZnO microrods (C 1s calibrated value: −0.768 eV). | |
Furthermore, to examine the universality of this facile method, we have extended this approach to assemble Pt nanoparticles onto ZnO microrods. The TEM images of the obtained Pt decorated ZnO are shown in Fig. 6(a–c). In Fig. 6(a), the ragged profile of the ZnO microrods clearly proves the assembly of Pt nanoparticles. On more careful observation in Fig. 6(b and c), it can be seen that a high density of Pt layer is coated on the surface of ZnO matrix. Fig. 6(d) compares the XRD patterns of ZnO microrods before and after loading of Pt nanoparticles, where only a weak diffraction peak at 39.3° for Pt (111) plane is observed. The phenomenon is probably caused by the line broadening of XRD peaks due to the small size of Pt, which is reflected in Fig. 6(c), as it can be seen that many ultrathin Pt nanoparticles aggregate into clusters. Thus we have used XPS to analyze the samples, and the Pt 4f spectrum is shown in Fig. 7(a), which clearly confirms the successful decoration of Pt on ZnO. Fig. 7(b) corresponds to the binding energies for Zn 2p, which are similar to Fig. 5(b).
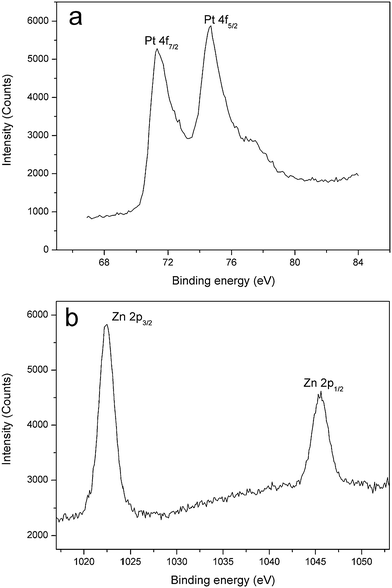 |
| Fig. 7 XPS spectra (a) Pt 4f and (b) Zn 2p of Au nanoparticles decorated ZnO microrods (C 1s calibrated value: −0.322 eV). | |
3.2 Sensor performance
One-dimensional ZnO nanostructures have been intensively studied as sensor materials, because of their high surface-to-volume ratio, high mobility of conduction electrons and good chemical and thermal stability under sensor operating conditions. Noble metals such as Au are known to exhibit unexpected electronic and catalytic properties when the particle sizes fall into the nanoscale range. To further increase the sensor sensitivity, catalytic noble metals have been widely used as dopants or promoters to fabricate sensor materials. Inspired by this idea, we have systematically investigated the sensing properties of our Au decorated ZnO microrods by using ethanol as the main probe analyte. As expected, significant improvement in sensor response towards ethanol detection has been observed.
First, the optimum operating temperature (OOT) for the sensors is determined by sensing 100 ppm ethanol in the temperature range of 240–350 °C. As shown in Fig. 8, the Au-decorated hybrid sensor shows much higher sensitivity than those of pristine ZnO sensors. The operating temperature is known to strongly affect the sensor response, because the dynamic of sensing reactions is influenced by temperature. From Fig. 8, one can see that the sensitivity of the hybrid sensor reaches a maximum of 52.5 at 310 °C, hence 310 °C is determined as the OOT in this work and all other control sensing tests are conducted at this temperature. Fig. 9 displays the dynamic response-recovery curves of the Au/ZnO sensor. By comparison, it can be clearly seen that the sensor response becomes faster with increasing operating temperature from 240 to 280 °C. As we know, the response speed directly reflects the kinetics of surface sensing reactions, which is dramatically influenced by temperature. It is now well understood that the sensing mechanism of n-type semiconductors such as ZnO and SnO2 is based on the change in conductance or resistance, which is changed by surface sensing reactions between analyte molecules and chemisorbed surface oxygen species (mainly O2−, O− and O2−).29,41,42 The surface oxygen species can trap electrons from the conduction band of metal oxides, resulting in the formation of the electron depletion layer on the surface of gas sensors. In addition, the category and concentration of surface oxygen species on the sensing layer have a direct relation to temperature.26,41 In other words, operating temperature significantly affects the sensor performances. As can be seen in Fig. 9, the dynamics of sensing reactions between ethanol and oxygen species on the sensor surface is gradually enhanced from 240 to 280 °C, and reaches a maximum at 310 °C, then slows down with further increase in temperature. The response speed is characterized by the response time (τres), which is defined as the time for the sensor to reach 90% of its whole response amplitude. As shown in Fig. 9, the response time is gradually decreased from 45 s at 240 °C to 7 s at 280 °C. When the operating temperature exceeds 290 °C, the sensor responds to its maximum response within 3 s. In addition, the Au-decorated sensor also shows a fast recovery within 2 min.
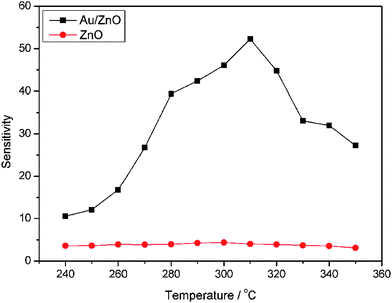 |
| Fig. 8 Sensor sensitivities to 100 ppm ethanol at different operating temperatures. | |
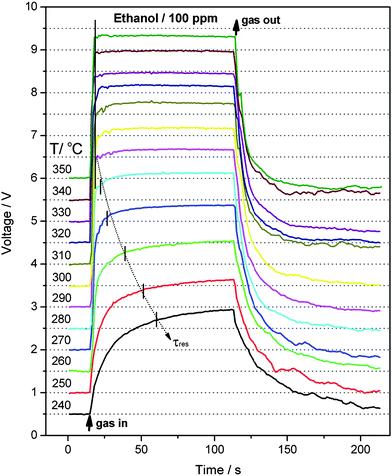 |
| Fig. 9 Dynamic response-recovery curves for 100 ppm ethanol of the sensor based on Au decorated ZnO microrods at different operating temperatures (for comparison, the curves are separated with a vertical offset of 0.5 V). | |
The sensor performances to different concentrations of ethanol are tested and the response-recovery curves are illustrated in Fig. 10. It can be seen that the hybrid Au/ZnO sensor exhibits significantly enhanced response towards each concentration in comparison to the pristine ZnO sensor. Their sensitivities are compared in Fig. 11, displaying that the sensitivities of both sensors increase with ethanol concentration. However, the hybrid sensor possesses much higher sensitivities due to the decoration of catalytic Au nanoparticles. Reproducibility is an important factor of chemical sensors. We have examined the sensor response for detecting 8 cycles of 100 ppm ethanol and the results are shown in Fig. 12. It demonstrates that the hybrid Au/ZnO sensor has good stability, as no obvious changes in the response amplitude and recovery process can be observed, even after 8 cycles of repeated test. Sensor sensitivities to six other gases with a concentration of 100 ppm are also tested to evaluate the selectivity of the sensor. As shown in Fig. 13, the sensor exhibits the highest sensitivity (52.5) to ethanol, almost two times higher than that for H2S (26.1), methanol (23.5) and acetone (22.1), while the sensitivities to formaldehyde, ether and chloroform are not higher than 5.
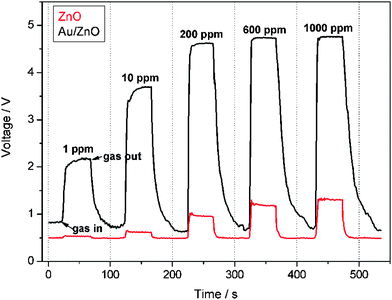 |
| Fig. 10 Dynamic response-recovery curves of the sensors to different ethanol concentrations at 310 °C. | |
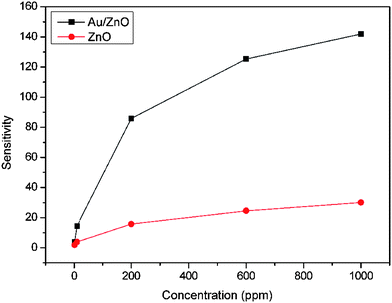 |
| Fig. 11 Sensor sensitivities to different ethanol concentrations at 310 °C. | |
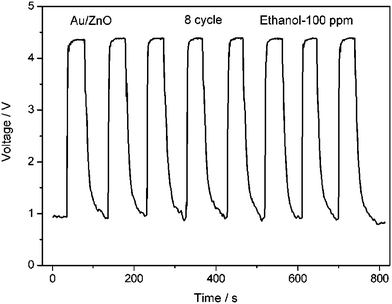 |
| Fig. 12 Reproducibility of the Au/ZnO sensor on successive exposure to 100 ppm ethanol at 310 °C. | |
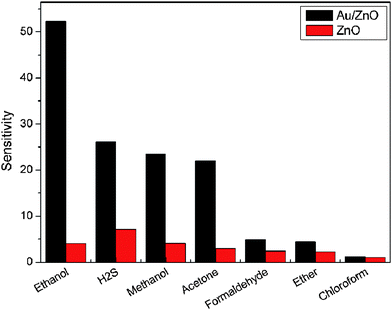 |
| Fig. 13 Comparison in sensor sensitivities to different analyte gases (100 ppm) at 310 °C. | |
Based on the above sensing results, it is obvious that the hybrid Au/ZnO sensor shows overwhelming advantages against pristine ZnO. Consequently, the much enhanced sensor performance should be directly attributed to the assembly of catalytic Au nanoparticles on the surface of ZnO microrods. First, the ionsorption of oxygen species onto the sensing layer is probably improved by Au nanoparticles due to its spillover effect.26,43,44 A second reason should be the increased Schottky barriers,26,31,43,45 which is caused by the electron depletion layer at the interface between Au nanoparticles and ZnO semiconductor. In this case, the Au nanoparticles may play a similar role as the surface oxygen species does in the formation of the electron depletion layer.
4. Conclusion
In summary, a facile one-pot approach is developed to assemble noble metals onto one-dimensional ZnO microrods using amino acid (lysine) as the capping agent. No pre-functionalization of the ZnO support is needed, hence simplifying the synthesis and reducing the fabrication cost. By using this method, both Au and Pt nanoparticles with a small size can be successfully decorated onto ZnO matrix. Inspired by the improving effect of noble metals, we have further systematically investigated the gas sensing properties of the as-prepared Au decorated ZnO microrods using ethanol as the main analyte gas. Results show that the hybrid sensor exhibited significantly enhanced response in comparison to pristine ZnO at 300 °C, as well as short response time within 3 s, fast recovery, excellent reproducibility and good selectivity to ethanol.
Acknowledgements
This work was supported by the National Natural Science Foundation of China (No. 20871071) and the Applied Basic Research Programs of Science and Technology Commission Foundation of Tianjin (No. 08JCYBJC00100 and 09JCYBJC03600).
References
- K. J. M. Bishop, C. E. Wilmer, S. Soh and B. A. Grzybowski, Small, 2009, 5, 1600–1630 CrossRef CAS.
- O. D. Velev and S. Gupta, Adv. Mater., 2009, 21, 1897–1905 CrossRef CAS.
- J. Li, S. B. Tang, L. Lu and H. C. Zeng, J. Am. Chem. Soc., 2007, 129, 9401–9409 CrossRef CAS.
- S. I. Lim and C. J. Zhong, Acc. Chem. Res., 2009, 42, 798–808 CrossRef CAS.
- L. M. Liz-Marzan and P. Mulvaney, J. Phys. Chem. B, 2003, 107, 7312–7326 CrossRef CAS.
- A. N. Shipway, E. Katz and I. Willner, ChemPhysChem, 2000, 1, 18–52 CrossRef CAS.
- M. C. Daniel and D. Astruc, Chem. Rev., 2004, 104, 293–346 CrossRef CAS.
- S. Q. Liu and Z. Y. Tang, J. Mater. Chem., 2010, 20, 24–35 RSC.
- U. Ozgur, Y. I. Alivov, C. Liu, A. Teke, M. A. Reshchikov, S. Dogan, V. Avrutin, S. J. Cho and H. Morkoc, J. Appl. Phys., 2005, 98, 041301 CrossRef.
- G. Shen, P. C. Chen, K. Ryu and C. Zhou, J. Mater. Chem., 2009, 19, 828–839 RSC.
- L. Vayssieres, Adv. Mater., 2003, 15, 464–466 CrossRef CAS.
- L. E. Greene, B. D. Yuhas, M. Law, D. Zitoun and P. D. Yang, Inorg. Chem., 2006, 45, 7535–7543 CrossRef.
- B. Liu and H. C. Zeng, J. Am. Chem. Soc., 2003, 125, 4430–4431 CrossRef CAS.
- Z. R. Dai, Z. W. Pan and Z. L. Wang, Adv. Funct. Mater., 2003, 13, 9–24 CrossRef CAS.
- E. Hosono, S. Fujihara, I. Honna and H. S. Zhou, Adv. Mater., 2005, 17, 2091–2094 CrossRef CAS.
- A. Umar and Y. B. Hahn, Nanotechnology, 2006, 17, 2174–2180 CrossRef CAS.
- F. Lu, W. P. Cai and Y. G. Zhang, Adv. Funct. Mater., 2008, 18, 1047–1056 CrossRef CAS.
- J. Zhang, S. R. Wang, M. J. Xu, Y. Wang, B. L. Zhu, S. M. Zhang, W. P. Huang and S. H. Wu, Cryst. Growth Des., 2009, 9, 3532–3537 CrossRef CAS.
- J. Zhang, S. R. Wang, Y. Wang, M. J. Xu, H. J. Xia, S. M. Zhang, W. P. Huang, X. Z. Guo and S. H. Wu, Sens. Actuators, B, 2009, 139, 411–417 CrossRef.
- B. Liu and H. C. Zeng, Chem. Mater., 2007, 19, 5824–5826 CrossRef CAS.
- M. Law, L. E. Greene, J. C. Johnson, R. Saykally and P. D. Yang, Nat. Mater., 2005, 4, 455–459 CrossRef CAS.
- J. B. Baxter and E. S. Aydil, Appl. Phys. Lett., 2005, 86, 053114 CrossRef.
- P. C. Chen, G. Z. Shen and C. W. Zhou, IEEE Trans. Nanotechnol., 2008, 7, 668–682 CrossRef.
- A. Kolmakov, Y. X. Zhang, G. S. Cheng and M. Moskovits, Adv. Mater., 2003, 15, 997–1000 CrossRef CAS.
- E. Comini, G. Faglia, M. Ferroni, A. Ponzoni, A. Vomiero and G. Sberveglieri, J. Mol. Catal. A: Chem., 2009, 305, 170–177 CrossRef CAS.
- R. K. Joshi, Q. Hu, F. Am, N. Joshi and A. Kumar, J. Phys. Chem. C, 2009, 113, 16199–16202 CrossRef CAS.
- J. X. Huang, S. Virji, B. H. Weiller and R. B. Kaner, J. Am. Chem. Soc., 2003, 125, 314–315 CrossRef CAS.
- J. X. Huang, S. Virji, B. H. Weiller and R. B. Kaner, Abstr. Pap. Am. Chem. Soc., 2004, 228, U445–U445.
- Y. Shimizu and M. Egashira, MRS Bull., 1999, 24, 18–24 CAS.
- M. Penza, C. Martucci and G. Cassano, Sens. Actuators, B, 1998, 50, 52–59 CrossRef.
- A. Kolmakov, D. O. Klenov, Y. Lilach, S. Stemmer and M. Moskovits, Nano Lett., 2005, 5, 667–673 CrossRef CAS.
- S. Guo, S. Dong and E. Wang, Chem.–Eur. J., 2009, 15, 2416–2424 CrossRef CAS.
- S. Wang, S. P. Jiang, T. J. White, J. Guo and X. Wang, Adv. Funct. Mater., 2009, 19, 1–8.
- Y. Zhang, Q. Xiang, J. Q. Xu, P. C. Xu, Q. Y. Pan and F. Li, J. Mater. Chem., 2009, 19, 4701–4706 RSC.
- P. Selvakannan, S. Mandal, S. Phadtare, R. Pasricha and M. Sastry, Langmuir, 2003, 19, 3545–3549 CrossRef CAS.
- J. Bandara, K. Tennakone and J. Kiwi, Langmuir, 2001, 17, 3964–3969 CrossRef CAS.
- J. Zhu, O. K. Tan, Y. C. Lee, T. S. Zhang, B. Y. Tay and J. Ma, Nanotechnology, 2006, 17, 5960–5969 CrossRef CAS.
- O. Durupthy, J. Bill and F. Aldinger, Cryst. Growth Des., 2007, 7, 2696–2704 CrossRef CAS.
- Z. Zhong, J. Ho, J. Teo, S. Shen and A. Gedanken, Chem. Mater., 2007, 19, 4776–4782 CrossRef CAS.
- Z. Zhong, J. Lin, S.-P. Teh, J. Teo and F. M. Dautzenberg, Adv. Funct. Mater., 2007, 17, 1402–1408 CrossRef CAS.
- B. Chwieroth, B. R. Patton and Y. Z. Wang, J. Electroceram., 2001, 6, 27–41 CrossRef CAS.
- N. Barsan and U. Weimar, J. Electroceram., 2001, 7, 143–167 CrossRef CAS.
- R. L. Vander Wal, G. W. Hunter, J. C. Xu, M. J. Kulis, G. M. Berger and T. M. Ticich, Sens. Actuators, B, 2009, 138, 113–119 CrossRef.
- S. C. Tsang, C. D. A. Bulpitt, P. C. H. Mitchell and A. J. Ramirez-Cuesta, J. Phys. Chem. B, 2001, 105, 5737–5742 CrossRef CAS.
- Q. Fu and T. Wagner, Surf. Sci. Rep., 2007, 62, 431–498 CrossRef CAS.
|
This journal is © The Royal Society of Chemistry 2010 |
Click here to see how this site uses Cookies. View our privacy policy here.