DOI:
10.1039/B9NR00400A
(Paper)
Nanoscale, 2010,
2, 1027-1032
Received
10th December 2009
, Accepted 8th March 2010
First published on
11th May 2010
Abstract
Monodisperse iron oxide nanocrystals were synthesized by a simplified method using iron chloride as precursor. In the presence of Cl ions, the as-produced iron oxide nanocrystals preferred a cubic shape with {100} facets exposed. The function of halogens including Cl and Br ions on stabilizing {100} facets of spinel structured iron oxides, rather than the regulation of thermolysis kinetics and surfactants, was found influential on the shape control of nanocubes in this organic phase approach. The synthesis can be also extended for cobalt ferrite nanocubes and cobalt oxide polyhedrons.
Introduction
Iron oxide nanocrystals (NCs) are a class of interesting magnetic materials due to their crystal structure and oxygen stoichiometry dependent and convertible magnetic properties.1 They offer chemical ways to control properties of materials, for instance, from ferromagnetic Fe3O4 to antiferromagnetic α-Fe2O3via the controlled oxidation,2 or from the ferromagnetic spinels to superparamagnetic ones via reducing crystal size down to nanoscale.3 The spinel-structured iron oxide NCs including Fe3O4 (inverse spinel) and γ-Fe2O3 have received tremendous attention in recent years since they are quite potential for information storage devices, rotary shaft sealing, position sensing,4 as well as the biology based applications such as medical diagnosis and drug delivery.5 The most popular synthetic methods for these spinel structured iron oxide NCs include the co-precipitation in aqueous solution by adding hydroxides into iron salt solutions,6 and the thermal decomposition of iron organometallic compounds in high boiling point organic solutions in the presence of stabilizers.3 In particular, the organic phase approach offers good controls on dispersity, crystallization, size, and shape. So-produced iron oxide NCs can be readily transferred into aqueous solution by surface modification.7 Therefore, the organic phase approach has been extensively utilized as a main laboratory technique for the production of magnetic iron oxide NCs.
In this article, we present a facile organic synthesis of monodisperse spinel iron oxide nanocrystals using iron chloride as precursor. It was found interestingly that Cl played an important role in the formation of cubic shaped iron oxide NCs. Without Cl ions, only spherical iron oxide NCs were produced. A similar function for the shape control of iron oxide NCs was also found on Br ions. The experiments provided a unique example that the shape control of transition metal oxide NCs was achieved by employing halogen ions as shape controller rather than the regulations of precursor thermolysis kinetics8 and surfactants. In addition, the method further simplified the current organic phase synthesis of iron oxide NCs toward laboratory environmental benign9 as well as recipe economy. Handling a heavy metal chloride salt instead of its organometallic powder is quite friendly for both environment and researchers.
Experimental
Materials
Iron chloride (>97%), 1-octadencene (>95%), oleic acid (>90%), and oleylamine (>70%) were purchased from Aldrich. Sodium oleate (>99%), sodium chloride (>99%), and sodium bromide (>99%) were purchased from National Chemicals Co (China). All the chemicals were used as received without further purification.
Synthesis of cubic iron oxide NCs using FeCl3
0.5 mmol FeCl3·6H2O, 3 mmol Na-oleate, and 10 mL 1-octadecene were mixed in a three necked flask and heated to 130 °C for 1 h under N2 flow protection. The solution was then heated up to 317 °C and kept at this temperature for 2 h. The reaction solution was solid-like as cooling down to room temperature. It was sonicator-washed by adding 20 mL hexane, 5 mL ethanol, and 20 mL deionized water for three times to remove NaCl and then NCs (dispersed in hexane phase) were collected upon adding 20 mL ethanol followed by centrifuging. The reaction was varied by changing refluxing time for 1, 2, 3, and 6 h, and heating rate for 1.5, 10, 20, and 30 K min−1, respectively.
Synthesis of spherical iron oxide NCs
0.5 mmol FeCl3·6H2O, 1.5 mmol Na-oleate, 1.5 mmol oleic acid and 10 mL 1-octadecene were mixed in a three necked flask and heated to 130 °C for 1 h under N2 flow protection. The solution was then heated up to 317 °C and kept at this temperature for 2 h. The reaction solution was washed by adding 20 mL hexane, 2 mL acetone, and 20 mL deionized water for two times to remove NaCl and then NCs (dispersed in hexane phase) were collected upon adding 20 mL ethanol followed by centrifuging.
Synthesis of Fe-oleate
According to the reported method,3b 5.4 g FeCl3·6H2O and 18.5 g Na-oleate were dissolved in a solution containing 40 mL ethanol, 30 mL deionized water, and 70 mL hexane and refluxed at 70 °C for 4 h. The hexane phase with Fe-oleate dissolved was washed with deionized water for three times and then dried under vacuum.
Synthesis of cubic iron oxide NCs using NaCl and NaBr as additives
0.5 mmol Fe-oleate, 1.5 mmol Na-oleate, NaCl (or NaBr) and 10 mL 1-octadecene were mixed in a three necked flask and heated to 130 °C for 1 h under N2 flow protection. The solution was then heated up to 317 °C and kept at this temperature for 2 h. The reaction solution was sonicator-washed by adding 20 mL hexane, 5 mL ethanol, and 20 mL deionized water for two times to remove NaCl and then NCs (dispersed in hexane phase) were collected upon adding 20 mL ethanol followed by centrifuging. The reaction was varied by varying the adding amount of NaCl and NaBr at 0.1, 0.5, 1, 1.5, 2, and 3 mmol, respectively.
Synthesis of cobalt ferrite nanocubes and cobalt oxide polyhedrons
(1) cobalt ferrite cubes: 0.2 mmol CoCl2·6H2O, 0.4 mmol FeCl3·6H2O, 3 mmol Na-oleate, and 10 mL 1-octadecene were mixed in a three necked flask and heated to 130 °C for 1 h under N2 flow protection. The solution was then heated up to 317 °C and kept at this temperature for 2 h; (2) triangular cobalt oxide NCs: 0.6 mmol CoCl2·6H2O, 3 mmol Na-oleate, and 10 mL 1-octadecene were mixed in a three necked flask and heated to 130 °C for 1 h under N2 flow protection. The solution was then heated up to 317 °C and kept at this temperature for 6 h; (3) polyhedral cobalt oxide NCs: 2 mmol CoCl2·6H2O, 4 mmol Na-oleate, 4 mmol oleylamine and 20 mL 1-octadecene were mixed in a three necked flask and heated to 130 °C for 1 h under N2 flow protection. The solution was then heated up to 317 °C and kept at this temperature for 2 h. The washing procedure was same as that described above.
Characterizations
Samples for TEM were prepared by drying the nanocrystal solutions on amorphous carbon coated copper grid and imaged by a JEOL 200CX transmission electron microscopy at 120 kV. High resolution TEM was performed on a Tecnai F20 (FEI Corp.) microscopy. SEM study was carried out in a XL30 S-FEG FEI field emission type scanning electron microscope at 10 kV. X-Ray powder diffraction patterns were recorded on a Rigaku D/MAX 2400 X-ray diffractometer with Cu-Kα radiation (λ = 1.5406 Å). FT-IR spectra were recorded by a Bruker Vector 22 Fourier transform infrared spectrometer. The hysteresis loop was recorded by a Quantum Design PPMS 6000 between −40 and 40 kOe at 10 and 300 K. The energy dispersive X-ray (EDX) spectrum was recorded on a XL30 S-FEG field emission type scanning electron microscope.
Results and discussion
A typical transmission electron microscopic (TEM) image of as-synthesized iron oxide nanocubes with the side length 11.5 ± 2.0 nm is shown in Fig. 1a. The yield of cubic shaped NCs is nearly 90%. The reaction also produced 60–100 nm particles in a small amount, which were readily removed by centrifuging a hexane solution of NCs at a low speed (Fig. S1 in the ESI†). The selected area electron diffraction (SAED) pattern of iron oxide cubes (Fig. 1b) clearly shows the typical cubic spinel structure diffraction rings. The enhanced reflection of {400} and the weakened reflection of (311) are ascribed to the cubic shape and the alignment of the <100> axis perpendicular to the substrate.8a The high resolution TEM image of a single iron oxide cube (Fig. 1c) shows lattice fringes with an interfringe distance of approximately 0.292 nm, which is close to the interplane distance of the {220} planes in the cubic spinel structured iron oxide. The X-ray diffraction pattern of these iron oxide nanocubes (Fig. 1d) shows the typical cubic spinel structure. The enhanced intensity of (400) diffraction peak is consisted with the SAED pattern and confirms that the cubic shaped NCs are abundant in {100} facets.10 Furthermore, the (400) peak is narrower than the other peaks, convincing that the side of cubic NCs are preferentially along the <100> direction.3b,10 The calculated lattice parameter from these diffraction peaks is 8.373 Å, which is between the standard lattice parameters of magnetite (Fe3O4, 8.396 Å) and maghemite (γ-Fe2O3, 8.346 Å).3d It implies that the as-synthesized iron oxide NCs are in the form of (Fe3O4)(γ-Fe2O3) and the ratio of these two components is nearly 1
:
1.3b,d Although the characteristic diffraction of Fe3O4 was found around 89°, it cannot exclude the existence of γ-Fe2O3.3d The XPS spectrum of Fe 2p shows a weak Fe2+ signal shoulder around 709.4 eV and multiplets of Fe3+ from both Fe3O4 and γ-Fe2O3 (Fig. S2 in the ESI†), further indicating the co-existence of Fe3O4 and γ-Fe2O3.11 The as-synthesized iron oxide nanocubes showed superparamagnetic properties at the room temperature (300 K) and ferromagnetic behaviors with a small coercivity (HC) of 500 Oe at low temperature (10 K, Fig. 2). The saturation magnetization (Ms) at 300 K of these iron oxide nanocubes was ∼42 emu g−1, which is lower than that of magnetite nanoparticles in similar size.3d It is probably because these iron oxide nanocubes are in the form of (Fe3O4)(γ-Fe2O3) and the component of γ-Fe2O3 weakened the overall magnetization of nanocrystals. At low temperature, the Ms increased slightly to ∼45 emu g−1 and the HC was also weakened by the presence of γ-Fe2O3 component compared with the pure magnetite nanoparticles.8b
 |
| Fig. 2 The hysteresis loops of as-synthesized cubic iron oxide NCs at 10 K (red) and 300 K (blue). The inset shows the enlarged partial hysteresis curves between ±4.0 Tesla. The NCs show superparamagnetic properties at 300 K and ferromagnetic behavior at 10 K. | |
Intermediate product and thermolysis kinetics
To understand the formation procedure of iron oxide nanocubes, the reaction was studied by varying reaction temperature, reaction time, and heating rate. It was found that below the refluxing point of the solution (∼317 °C, bp of 1-octadecene) there was no nanocrystal produced. The formation of iron oxide NCs only takes place above 310 °C. The Fourier transform infrared (FT-IR) spectra of the reaction solution as aged at 130, 200, and 300 °C was recorded (Fig. 3a, b, and c) and it revealed that the iron-oleate complex3b probably was formed firstly from the reaction between iron chloride and sodium oleate at the thermal condition. As the intermediate product, iron-oleate then thermal decomposed to iron oxide NCs by aging for a period at the refluxing point. The refluxing time was varied for 1, 2, 3, and 6 h. The TEM image of the product collected within 1 h shows small cubic shaped NCs with a side length 6.2 ± 1.9 nm (Fig. 4a). It indicates that the nucleation of small sized iron oxide NCs took place in 1 h, which is consisted with the experimental phenomena that the solution changed the color gradually from dark brown to dark within 1 h refluxing. Refluxing the solution for another 1 h lead to the further growth of cubic NCs. Fig. 4b shows that the growth of iron oxide nanocubes were nearly accomplished within a total refluxing time of 2 h and the side length of these cubic NCs increased to 11.5 ± 2.0 nm. Refluxing 3 h allowed the growth of NCs fully accomplished and the size of NCs increased slightly to 12.0 ± 1.4 nm (Fig. 4c). Fig. 4d shows a TEM image of the NCs obtained by refluxing for 6 h. The cubic shape of NCs did not maintain well after a long refluxing time. The experiments imply that the small cubic iron oxide NCs were firstly produced within 1 h and an optimal refluxing time for the fully growth of cubic NCs is 2 or 3 h. Refluxing for a long time did not lead to a further growth of NCs, but a shape damage. Since the nucleation and growth of NCs mainly processed around the refluxing point, an assumption may be made that the heating rate is not sensitive for the shape and size control of NCs. This is confirmed by the results of the experiments that varied heating rate for 1.5, 10, 20, 30 K min−1. Unlike the synthesis of CoO NCs by thermal decomposition of Co-oleate,12 it was found that the morphologies of these NCs were not heating rate dependant. The produced NCs at different heating rates were similar and no remarkable size or shape evolution was observed (Fig. S3 in the ESI†).
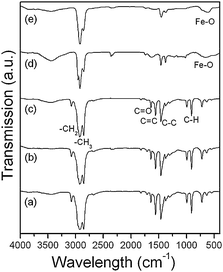 |
| Fig. 3 The FT-IR spectra of the dark brown solution aged at 130 (a), 200 (b), 300 °C (c), and refluxing for 1 (d) and 2 h (e). It revealed that the intermediate product iron-oleate only decomposed at refluxing point. With the increase of refluxing time, the characteristic band of Fe–O at low frequency became remarkable, indicating the formation of iron oxide crystals. | |
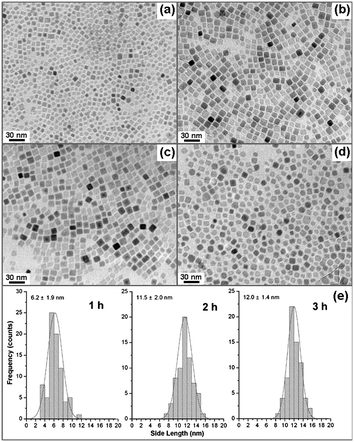 |
| Fig. 4 The refluxing time was varied for 1, 2, 3, and 6 h. It was found that the small cubic shaped iron oxide NCs were formed within 1 h (a). Refluxing for 2 and 3 h lead to a further growth of NCs and resulted in size-uniformed nanocubes (b and c). Over refluxing for 6 h did not show the size involution of NCs, but damages on the cubic shape (d). (e) The side length size distributions of iron oxide NCs obtained by refluxing 1, 2, and 3 h. | |
It should be noticed that with the formation of the intermediate iron-oleate NaCl was also produced in one flask. The produced cubic iron oxide NCs without water washing contained NaCl as detected by energy dispersive X-ray (EDX, Fig. S4 in the ESI†). In recent years, stabilizing {100} facets of fcc metals via coordination or chemical etching between metals and halogens in the presence of surfactants has been widely reported in the synthesis of cubic noble metal NCs. The examples include Ag, Pd, Pt and Rh nanocubes in polyol systems13 and Pt, Pd, PtPd and PtCu nanocubes in organic phases.14 It has been found that the metal–halogen coordination induced facets—preferential adsorption of halogens is quite influential in the regulation of growth rates of low-index facets.13a The differences in nature of these low-index facets in terms of atoms and configurations give each of them a different coordination environment and thus the regulation of growth rates of facets by selective adsorption of halogens can be achieved.13b Similarly, we believe that this NaCl is not only a by-product during the formation of the intermediate, but a key chemical for the shape control of iron oxide NCs. We propose that Cl− ions may effectively stabilize the {100} facets of cubic spinel structured iron oxide NCs and induce the formation of cubic shaped NCs. The function of Cl− ions is probably due to the fact that the packing density of atoms in {100} of the cubic spinel is lowest and only Fe atoms are packed,1 which allows the effective absorption of Cl− ions via co-ordinating with Fe atoms. In the absence of Cl−, using Fe(acac)3 as precursor, the reaction produced non-cubic shaped NCs with a wide size distribution (Fig. S5a in the ESI†). In the absence of Na-oleate, using oleic acid and oleylamine as stabilizer, the reaction produced some NCs in cubic shape (Fig. S5b in the ESI†), but the yield and quality of NCs were not as high as the one using Na-oleate. This is probably because Cl− ions combined with protons (dissociated from surfactants) and escaped in the form of HCl with N2 flow, which is convinced by the fact that the pH value of emission gas is below 7 (tested by a wetted pH paper, Fig. S6 in the ESI†). The two control experiments indicates that Cl− is indeed important for the shape control of NCs and combined with Na+ the yield and quality of cubes can be improved significantly. Therefore, all the reactants including their building atoms and groups are essential for producing cubic shaped iron oxide NCs.
To further ensure the function of halogens on stabilizing {100} facets of cubic iron oxide NCs, the thermolysis of Fe-oleate in the presence of NaCl and NaBr was conducted with different adding amounts. Fig. S7 and S8 in the ESI† show the typical TEM images of iron oxide NCs produced as NaCl and NaBr were used as additives, respectively. The adding amount for each salts were varied at 0.1, 0.5, 1, 1.5, 2, and 3 mmol. Interestingly, it was found that both Cl− and Br− worked on the production of cubic NCs and the yield of cubic NCs was dependent on the amount of halogens. With the increase of NaCl amount, the yield of cubic NCs was increased and then decreased (Fig. 5) and the amount of big-sized NCs was increased. A similar trend was also found in the case of NaBr as additive. It indicates that probably few halogens can be dissociated from haloids and work on stabilizing {100} facets. Increasing haloids resulted in an increase of dissociated halogens, but also lead to an increase of undissolved solid salts, which in organic system seriously interrupted the homogenous growth of NCs. As more haloids were presented in the system, the heterogeneous growth became more dominant and more large-sized crystals were produced. The yield of cubic NCs using FeCl3 as Cl− source was much higher than the one using NaCl directly, which is probably because most NaCl formed through the thermal reaction between FeCl3 and Na-oleate remained in a molecular level and thus the formation of solid salts was avoided efficiently.13b It implies that using FeCl3 as precursor instead of Fe-oleate in this synthesis can improve the yield of cubic NCs significantly. However, it must be noted that the reaction using FeBr3 instead of FeCl3 cannot give a similar result since FeBr3 is not stable as heated over 100 °C and it decomposed before the Fe-oleate and NaBr formed. The function of halogens on stabilizing {100} facets of spinel iron oxide is probably similar with the one of halogen adsorption observed in fcc metals13a,14 since the two crystal structures have common points such as both in cubic and similar configurations of {100} and {111} facets (Fig. S9 in the ESI†). The remarkable differences may be also noticed: (1) their {110} are in different configurations; (2) on {100} and {111}, iron is in Fe3+ (for both spinel and inverse spinel),1 but noble metal is in atom; and (3) iron is not close packing, but noble metal in fcc is. In fact, the first does not favor the adsorption of halogens onto the {110} of the spinel due to the presence of oxygen. However, the latter two characteristics should make the {100} and {111} of the spinel more favorable for coordinating with halogens because the coordination activity of Fe3+ is higher than that of noble metal atoms, while the lowered packing density enlarges the free surface space for halogen adsorption.15 Further notice that the {111} of spinel is about 4.5-fold higher than the {100} in packing density,1,16 which probably results in the preferential adsorption on the {100} and thus cubic shaped NCs formed by exposing well-stabilized {100} facets.
 |
| Fig. 5 The yield of cubic iron oxide NCs versus the amounts of NaCl and NaBr. | |
Synthesis of spherical NCs
As found in the control experiments, the function of Cl− ions can be eliminated by removing these ions as protons presented. The recipe was further modified by using a mixture of Na-oleate and oleic acid to produce spherical iron oxide NCs. Fig. 6a shows a typical TEM image of as-synthesized spherical iron oxide NCs. The NCs shows a high monodispersity and their size is 14.2 ± 0.9 nm (Fig. S10 in the ESI†). The yield of these NCs is as high as ∼99%. The SAED pattern in Fig. 6b shows the clear diffraction rings of the cubic spinel structure for (220), (311), (400), and (440). Fig. 6c is a high resolution TEM image of these NCs and it revealed that the NCs are indeed in spherical shape.
Synthesis of cobalt ferrite nanocubes and cobalt oxide polyhedrons using chlorides
The synthetic method can be also extended to the synthesis of cubic CoFe2O4 NCs,17 as cobalt chloride and iron chloride were used as precursors in a molar ratio of 1
:
2. Fig. 7a shows the TEM image of as-synthesized cubic cobalt ferrite NCs with an average side length of ∼14 nm. The XRD pattern of these cobalt ferrite NCs is shown in Fig. 7b and matched well with the standard one (PDF#22-1086). The energy dispersive X-ray analysis indicates that the ratio of Co/Fe persisted from the ratio of feeding metal ions (the top in Fig. 7b). Further increasing the feeding ratio of Co/Fe cannot result in the production of composition controlled cubic cobalt ferrite NCs. The shape of cobalt ferrite NCs was not cubic as the feeding ratio of Co/Fe increased to 1 (Fig. S11 in the ESI†). These NCs are in various shapes including rods, truncated polyhedrons, and spheres, and the sizes are located in the range of 30–40 nm. The disability of shape control and the size increase on these cobalt ferrite NCs are probably due to the increase of cobalt portion, which interrupted the anisotropic growth along <100> directions. As only cobalt chloride was used in this synthetic procedure, ∼60% triangular CoO NCs were produced and these triangular CoO NCs are ∼50 nm in the side length (Fig. 7c). If further modify the synthetic conditions by adding oleylamine in the equivalent of sodium oleate, polyhedral CoO NCs with the average size of ∼90 nm can be produced (as shown in Fig. 7d). These experiments preliminarily discovered the potentials of the presented method as a diverse synthetic approach for the shape controlled production of other transition metal oxide NCs using metal chlorides.
Conclusions
In summary, we have presented a halogen assisted synthesis of cubic iron oxide NCs. The study shows that both Cl− and Br− work on stabilizing {100} facets of spinel structured iron oxide NCs. The synthesis indicates that the shape control on transition metal NCs in the thermolysis method can be achieved not only via the regulations of precursor thermolysis kinetics and surfactants, but also via the facets—preferential coordination with halogens. By this experimental discovery, it is expected that an alternative general technical route can be developed for the shape-controlled synthesis of transition metal oxide NCs.
Acknowledgements
The work was supported by National Science Foundation of China and national “863” program.
Notes and references
-
R. M. Cornell, U. Schwertmann, The Iron Oxides: Structure, Properties, Reactions, Occurrence and Uses, VCH, New York, 1996 Search PubMed.
- Y. Hou, Z. Xu and S. Sun, Angew. Chem., Int. Ed., 2007, 46, 6329 CrossRef CAS.
-
(a) S. Sun and H. Zeng, J. Am. Chem. Soc., 2002, 124, 8204 CrossRef CAS;
(b) J. Park, K. An, Y. Hwang, J. G. Park, H. J. Noh, J. Y. Kim, J. H. Park, N. M. Hwang and T. Hyeon, Nat. Mater., 2004, 3, 891 CrossRef CAS;
(c) J. Park, E. Lee, N. Hwang, M. Kang, S. C. Kim, Y. Hwang, J. G. Park, H. J. Noh, J. Y. Kim, J. H. Park and T. Heyon, Angew. Chem., Int. Ed., 2005, 44, 2872 CrossRef CAS;
(d) Z. Xu, C. Shen, Y. Hou, H. Gao and S. Sun, Chem. Mater., 2009, 21, 1778 CrossRef CAS;
(e) T. Yang, C. Shen, Z. Li, H. Zhang, C. Xiao, S. Chen, Z. Xu, D. Shi, J. Li and H. Gao, J. Phys. Chem. B, 2005, 109, 23233 CrossRef CAS;
(f) T. Hyeon, S. S. Lee, J. Park, Y. Chung and H. B Na, J. Am. Chem. Soc., 2001, 123, 12798 CrossRef CAS;
(g) L. Zhang, J. Wu, H. Liao, Y. Hou and S. Gao, Chem. Commun., 2009, 4378 RSC;
(h) N. R. Jana, Y. Chen and X. Peng, Chem. Mater., 2004, 16, 3931 CrossRef CAS.
- K. Raj and R. Moskowitz, J. Magn. Magn. Mater., 1990, 85, 233 CrossRef CAS.
-
(a) J. Xie, K. Chen, H. Y. Lee, C. Xu, A. R. Hsu, S. Peng, X. Chen and S. Sun, J. Am. Chem. Soc., 2008, 130, 7542 CrossRef CAS;
(b) C. Xu, B. Wang and S. Sun, J. Am. Chem. Soc., 2009, 131, 4216 CrossRef CAS;
(c) Y. W. Jun, Y. M. Huh, J. S. Choi, J. H. Lee, H. T. Song, S. Kim, S. Yoon, K. S. Kim, J. S. Shin, J. S. Suh and J. Cheon, J. Am. Chem. Soc., 2005, 127, 5732 CrossRef CAS;
(d) W. S. Seo, J. H. Lee, X. Sun, Y. Suzuki, D. Mann, Z. Liu, M. Terashima, P. C. Yang, M. V. Mcconnell, D. G. Nishimura and H. Dai, Nat. Mater., 2006, 5, 971 CrossRef CAS.
-
(a) C. Hui, C. Shen, T. Yang, L. Bao, J. Tian, H. Ding, C. Li and H. Gao, J. Phys. Chem. B, 2008, 112, 11336 CAS;
(b) T. Fried, G. Shemer and G. Markovich, Adv. Mater., 2001, 13, 1158 CrossRef CAS.
-
(a) Z. Xu, Y. Hou and S. Sun, J. Am. Chem. Soc., 2007, 129, 8698 CrossRef CAS;
(b) S. Peng, C. Wang, J. Xie and S. Sun, J. Am. Chem. Soc., 2006, 128, 10676 CrossRef CAS;
(c) J. Xie, C. Xu, Z. Xu, Y. Hou, K. L. Young, S. X. Wang, N. Pourmond and S. Sun, Chem. Mater., 2006, 18, 5401 CrossRef CAS.
-
(a) M. V. Kovalenko, M. I. Bodnarchuk, R. T. Lechner, G. Hesser, F. Schäffler and W. Heiss, J. Am. Chem. Soc., 2007, 129, 6352 CrossRef CAS;
(b) H. Yang, T. Ogawa, D. Hasegawa and M. Takahashi, J. Appl. Phys., 2008, 103, 07D526 CrossRef;
(c) H. Zeng, P. M. Rice, S. X. Wang and S. Sun, J. Am. Chem. Soc., 2004, 126, 11458 CrossRef CAS;
(d) D. Kim, N. Lee, M. Park, B. H. Kim, K. An and T. Hyeon, J. Am. Chem. Soc., 2009, 131, 454 CrossRef CAS;
(e) A. Ahniyaz, Y. Sakamoto and L. Bergström, Proc. Natl. Acad. Sci. U. S. A., 2007, 104, 17570 CrossRef CAS.
- X. Peng, Chem.–Eur. J., 2002, 8, 335 CrossRef.
-
(a) Y. Sun and Y. Xia, Science, 2002, 298, 2176 CrossRef CAS;
(b) J. Zhang, A. Kumbhar, J. He, N. C. Das, K. Yang, J. Q. Wang, H. Wang, K. L. Stokes and J. Fang, J. Am. Chem. Soc., 2008, 130, 15203 CrossRef CAS.
- A. P. Grosvenor, B. A. Kobe, M. C. Biesinger and N. S. Mclntyre, Surf. Interface Anal., 2004, 36, 1564 CrossRef CAS.
- K. An, N. Lee, J. Park, S. C. Kim, Y. Hwang, J. G. Park, J. Y. Kim, J. H. Park, M. J. Han, J. Yu and T. Hyeon, J. Am. Chem. Soc., 2006, 128, 9753 CrossRef CAS.
-
(a) Y. Zhang, M. E. Grass, J. N. Kuhn, F. Tao, S. E. Habas, W. Huang, P. Yang and G. A. Somorjai, J. Am. Chem. Soc., 2008, 130, 5868 CrossRef CAS;
(b) Y. Xiong, H. Cai, B. J. Wiley, J. Wang, M. J. Kim and Y. Xia, J. Am. Chem. Soc., 2007, 129, 3665 CrossRef CAS;
(c) B. J. Wiley, T. Herricks, Y. Sun and Y. Xia, Nano Lett., 2004, 4, 1733 CrossRef CAS.
-
(a) D. Xu, Z. Liu, H. Yang, Q. Liu, J. Zhang, F. Fang, S. Zou and K. Sun, Angew. Chem., Int. Ed., 2009, 48, 4217 CrossRef CAS;
(b) X. Huang, H. Zhang, C. Guo, Z. Zhou and N. Zheng, Angew. Chem., Int. Ed., 2009, 48, 1 CrossRef.
-
R. H. Crabtree, The Organometallic Chemistry of the Transition Metals, Wiley, Canada, 5th edn, 2009 Search PubMed.
-
(a) Y. Le, G. G. Totir, G. W. Flynn and R. M. OsgoodJr, Surf. Sci., 2006, 600, 665 CrossRef CAS;
(b) A. Barbieri, W. Weiss, M. A. Van Hove and G. A. Somorjai, Surf. Sci., 1994, 302, 259 CrossRef CAS.
-
(a) S. Sun, H. Zeng, D. B. Robinson, S. Raoux, P. M. Rice, S. X. Wang and G. Li, J. Am. Chem. Soc., 2004, 126, 273 CrossRef CAS;
(b) N. Bao, L. Shen, W. An, P. Padhan, C. H. Turner and A. Gupta, Chem. Mater., 2009, 21, 3458 CrossRef CAS.
Footnotes |
† Electronic supplementary information (ESI) available: Fig. S1–S11 including TEM images, EDX spectrum, XPS spectrum, the configurations of low-index facets of spinel and fcc, and the size distribution histogram of spherical NCs. See DOI: 10.1039/b9nr00400a |
‡ Current address: Department of Mechanical Engineering, Massachusetts Institute of Technology, Cambridge, Massachusetts 02139 (USA) |
|
This journal is © The Royal Society of Chemistry 2010 |
Click here to see how this site uses Cookies. View our privacy policy here.