DOI:
10.1039/D3MA00948C
(Paper)
Mater. Adv., 2024,
5, 4345-4353
In situ growth of NiSe2 nanoparticles on g-C3N4 nanosheets for an efficient hydrogen evolution reaction†
Received
1st November 2023
, Accepted 25th March 2024
First published on 28th March 2024
Abstract
A safe, non-precious, and low-cost catalyst, having a high hydrogen evolution rate, is one of the key demands for a sustainable hydrogen economy. In this study, we used a low-cost hydrothermal technique to prepare a NiSe2 nanoparticle-based catalyst. These particles were grown on 2D g-C3N4 nanosheets to improve their physical and chemical properties. The synthesized NiSe2/g-C3N4 nanocomposite catalyst demonstrated a high HER performance when compared to bare NiSe2 and g-C3N4. Specifically, the NiSe2/g-C3N4 composite demonstrated a lower Tafel slope of 64 mV dec−1, a stable HER up to 1000 min, and a low overpotential of 87 mV at a current density of 10 mA cm−2. The superior HER performance of the composite on 2D g-C3N4 corresponds to high active sites, and the synergistic interfacial contact leads to enhanced conductivity for rapid charge transport and long chemical stability. Thus, our study offers a pathway for the synthesis and development of non-precious, non-toxic, and highly stable electrocatalysts to replace noble metal-based catalysts and reduce the production costs of H2 gas.
1. Introduction
The depletion of fossil fuels and accompanying environmental damage, requires a search for a new and unconventional energy source.1 Hydrogen has emerged as an optimal solution for tackling the escalating energy and environmental challenges faced globally. The energy density of hydrogen is about 140 MJ kg−1, which is nearly three times that of gasoline (46.5 MJ kg−1).2 Hydrogen is produced using different technologies such as photolysis, electrolysis, or thermolysis. Electrocatalytic water splitting, one of the major energy study fields, has been under intense development by researchers to produce a high yield of H2 gas with an acceptable energy and cost consumption. Using suitable electrocatalysts, the water splitting leads to the hydrogen evolution reaction (HER). An ideal electrocatalyst should increase the faradaic efficiency, speed up the reaction kinetics, reduce ohmic losses, and work in different pH conditions. Extensive research has revealed a wide range of electrocatalysts that catalyze these critical reactions. Currently, platinum (Pt) and Pt-based electrodes show a very high catalytic performance and stability for HER. However, their commercial application is constrained by their high price and limited availability. Overall, there is an urgent requirement to develop state-of-the-art, high-performance, nonprecious metal-based electrocatalysts for electrocatalytic H2 generation.3–7
Recently, earth-abundant8 transition metal-based chalcogenides,9 hydroxides, phosphides,10 carbides, nitrides, metal–organic-frameworks (MOF),11 are being investigated for their HER activities. The chalcogenides are anticipated to be more covalent, have smaller band gaps, and offer better band alignment with water redox levels than their counterparts, allowing for more effective charge transfer and improved catalytic efficiency. Among chalcogenides, nickel selenide (NiSe2) exhibits a relatively superior electrochemical catalytic activity, chemical stability, low toxicity, and bio-compatibility. However, particle agglomeration and low electrical conductivity lead to a low HER performance because of the sluggish charge kinetics, which need to be resolved.12,13
Several strategies have been utilized to improvise the electrochemical activity of NiSe2. Some examples include nano-structurization,14 dual-anion doping,15 doping,16 interfacial engineering.16,17 In particular, 2D-based layered materials offer greater potential for different electrochemical applications.18 Graphitic carbon nitride (g-C3N4) offers simple synthesis, excellent stability, a 2D layered structure, and a tunable molecular structure for heterogeneous electrocatalysts.19,20 The g-C3N4 enhances the interaction with materials by providing N sites, resulting in abundant active sites, optimized electronic states, and rapid mass/charge transfer.21,22
Different research groups have utilized g-C3N4 to design heterostructures for enhancing the electrocatalytic HER activity. Guan et al. synthesized a MoS2/g-CN heterostructure that demonstrated an overpotential of 141 mV at 10 mA cm−2 and a Tafel slope of 57 mV dec−1.23 In another report, Zulqarnain et al. FeCoSe2/g-C3N4 was found to show an HER at an overpotential of 83 mV at 20 mA cm−2 and a current density of 14.80 mA cm−2 at 0 V (vs. RHE),24 which was considerably greater when compared to bare FeCoSe2. Other researchers studied g-C3N4/MoS2,25 holey g-C3N4 supported single-atom catalysts (SACs),26 FeSe2/g-C3N4,27 MoB/g-C3N4,28 C3N4@MoN,29 g-C3N4/C,30 FeSe2/g-C3N431 and demonstrated the role of g-C3N4 in improving the HER properties of compounds. Thus, it is expected that hetero-structuring of g-C3N4 with NiSe2 can effectively improve the electrochemical properties of NiSe2 to give a high-performance HER.
Herein, we have grown NiSe2 on g-C3N4 nanosheets to form a NiSe2/g-C3N4 nanocomposite using a hydrothermal method. The N-sites of g-C3N4 during the hydrothermal process interacted synergistically with NiSe2 to improve the electrical conductivity, active surface area, and charge kinetics. The prepared electrocatalyst exhibited excellent HER activity with a smaller overpotential of 87 mV to give a current density of 10 mA cm−2, a reduced Tafel slope of 64 mV dec−1, and a long-time stable HER activity up to 1000 min.
2. Experimental details
2.1. Materials
The high purity chemicals were utilized without further purification. Melamine, hydrazine hydrate, nickel(II) acetate tetrahydrate, and N-methyl-2-pyrrolidinone (NMP), selenium powder (Se), acetylene black and polyvinylidene fluoride (PVDF) were purchased from Sigma-Aldrich Chemical Reagent Co. Ltd.
2.2. Preparation of g-C3N4
Using a previously reported method,32 bulk g-C3N4 was synthesized using the thermal polycondensation of melamine.33,34 To achieve this, 5 g of melamine was heated in an alumina crucible under an air environment, until it gradually reached 550 °C (5 °C min−1). After a 4 h heating period, the mixture was cooled naturally to room temperature and ground in a mortar, to form a yellow bulk g-C3N4 powder. It was then transferred to an alumina crucible and subjected to a heating process in a nitrogen environment. The temperature was raised to 500 °C (5 °C min−1)/2 h. Finally, the obtained mixture was cooled naturally to ambient temperature, resulting in the formation of light yellow layered g-C3N4 nanosheet powder.
2.3. Preparation of NiSe2/g-C3N4
In a typical synthesis, an equal volume ratio of g-C3N4 nanosheets and deionized (DI) water was subjected to ultrasonication at room temperature for 1 h. The resulting solution was centrifuged at 2500 rpm/5 min, and the supernatant collected was a g-C3N4 nanosheet suspension. Next, a mixture was prepared by combining 2 mmol of nickel acetate, 2 mmol of selenium powder, and 20 mL of g-C3N4 nanosheet suspension (1 mg mL−1) in 50 mL of DI water. The mixture was stirred (800 rpm) for 20 min followed by dropwise addition of 20 mL of hydrazine. The solution was introduced into a hydrothermal reactor with a volume of 100 mL and held at a temperature of 180 °C for 12 h. To eliminate containments, the resulting precipitate underwent multiple washings using DI water and ethanol. The deep-gray precipitate was collected and dried overnight in vacuum oven at 80 °C to produce the NiSe2/g-C3N4 nanocomposite.5
2.4. Measurement of the catalytic activity towards the HER
The electrocatalytic properties of prepared materials were measured using a PGSTAT302N electrochemical workstation (Metrohm Autolab), in a three-electrode configuration at room temperature. The setup consists of Hg/HgO (reference), graphite rod (counter) and synthesized material (working) electrodes in an aqueous 1 M KOH electrolyte. The active electrode was prepared by drop-casting the active catalyst (2 mg) in 5 wt% Nafion (15 μL) and isopropanol (2 mL) onto the 1 × 1 cm2 nickel foam (NF). Prior to the electrochemical analysis, cyclic voltammetry (CV) was carried out for 50 cycles in the potential window of 1 V to 1.6 V vs. RHE. The linear sweep voltammetry (LSV) curves acquired were adjusted using the iR compensation at a scan rate of 10 mV s−1. Electrical impedance spectroscopy (EIS) was carried out in the frequency range of 1 MHz to 100 mHz, and chronoamperometry was carried out to measure the stability. The reversible hydrogen electrode (RHE) scale was utilized for standardizing LSV potential values using, E vs. RHE = E vs. Hg/HgO + 0.950 V. To compute the electrical double layer capacitance (Cdl), in the potential range of 0 to 0.2 V vs. RHE, the scan speeds in CV curves were varied from 5 to 50 mV s−1.
2.5. Material characterization
The physicochemical characteristics of the synthesized materials were investigated using different characterization techniques. X-ray diffraction (XRD, Rigaku Ultima IV) using CuKα radiation (λ = 0.15406 nm) was used for the phase configuration and structural details. The field emission scanning electron microscopy (FE-SEM, Jeol JSM-7900F, Japan), was utilized for understanding surface morphological characteristics. A spectrophotometer (Bruker, USA) was used to perform Fourier transform infrared (FTIR) spectroscopy. Selected area electron diffraction (SAED) and high-resolution transmission electron microscopy (HR-TEM) were performed using a Jeol JEM-2200FS. A K-alpha+ X-ray spectrometer was used for the X-ray photoelectron spectroscopy (XPS) investigation. The contact angles were measured with respect to standard liquids with a Rame-Hart goniometer.
3. Results and discussion
3.1. Reaction and growth mechanism
The possible reaction mechanism for the formation of NiSe2 and NiSe2/g-C3N4 was explained by chemical reactions. First, the ionic dissociation of nickel acetate in the reactant solution takes place (see eqn (1)). In the presence of the strong reducing agent, hydrazine hydrate, Ni2+ is reduced forming an intermediate complex (see eqn (2)). Moreover, the highly basic hydrazine hydrate and the temperature inside hydrothermal treatment promote the dissolution of the Se powder in DI water to form Se2− and SeO32− ions (eqn (3)). The used hydrazine hydrate controls the pH and release of the Se2− ions. The used Ni
:
Se precursor ratio was 1
:
2, so the final product should be a diselenide. These Se2− ions will react with the Ni complex to form NiSe2 (the desired product, see eqn (4)). | Ni(CH3CO2)2·4HO → Ni2+ + 2(CH3CO2)− + 4H2O | (1) |
| 2Ni2+ + 6N2H4 + 4OH− → 2[Ni(N2H4)3]2+ + 4OH− | (2) |
| 3Se + 6OH− → 2Se2− + SeO32− + 3H2O | (3) |
| [Ni(N2H4)3]2+ + 2Se2− → NiSe2 + 6N2H4 | (4) |
To form the composite, a similar procedure was used with addition of g-C3N4 during the hydrothermal treatment. The g-C3N4 nanosheets provide enormous active sites for NiSe2 nanoparticles to grow. To reduce the reaction energy, these particles tend to aggregate which leads to self-assembly and anisotropic growth. The favorable surface and electronic charge distribution of g-C3N4 encourages the attachment of the NiSe2 nanoparticles on its surface. The directed attachment process, the Gibbs–Thompson law, and the Ostwald ripening stabilize the chemical system, forming the NiSe2/g-C3N4 composite.35–38
3.2. Material characterization
The crystal phase and structure of NiSe2, g-C3N4, and NiSe2/g-C3N4 were analyzed by X-ray diffraction (XRD). In the XRD pattern of g-C3N4 (Fig. 1(a)), a peak at 13.2° is related to the (100) plane that arose due to in-planar tri-s-triazine units, whereas another peak at 27.5° belonged to the (002) plane originating from the layer stacking arrangement of conjugated aromatic systems.39 The XRD pattern of NiSe2 reveals stronger intensity peaks at 2θ = 29.93°, 33.55°, 36.91°, 50.71°, and 57.79° corresponding to the crystal planes of (020), (021), (121), (131), and (132), respectively, which was confirmed from the standard card (JCPDS no. 96-901-2538).40 The stronger peaks in the composite sample proved that the NiSe2/g-C3N4 composite was successfully synthesized, and that there were no extra peaks. The peak positions of NiSe2/g-C3N4 are consistent with NiSe2, and a smaller peak of g-C3N4 at 27.5° was observed suggesting that the crystal structure remains unaffected in presence of g-C3N4. Using the Debye Scherrer equation, the calculated crystallite sizes for NiSe2 and NiSe2/g-C3N4 samples were 26.16 and 24.89 nm, respectively. Surface functionalities were studied using FTIR spectroscopy. The FTIR spectra of NiSe2, g-C3N4, and NiSe2/g-C3N4, are shown in Fig. 1(b). A peak at 801 cm−1 arose due to the characteristic absorption of the condensed heptazine heterocyclic (C6N7) ring in g-C3N4. The bending and stretching modes of N-containing heterocycles in g-C3N4 were characterized by the peak at 890 cm−1 and the absorption band in the range of 1000–1750 cm−1, respectively. The broader peaks in 3000–3500 cm−1 range were related to –NH or –NH2 groups in g-C3N4.41 For NiSe2, a broad band in the region of 500 to 900 cm−1 is attributed to the stretching vibrations of nickel–selenium bonds. The bending and stretching vibrations of adsorbed water on Ni(OH)2 are responsible for bands observed at around 1600 cm−1 and 3600 cm−1, respectively. Moreover, the adsorption peaks of NiSe2/g-C3N4 are comprised of the respective peaks of NiSe2 and g-C3N4, indicating the successful integration of the NiSe2 nanoparticles on the g-C3N4 nanosheet.42–48
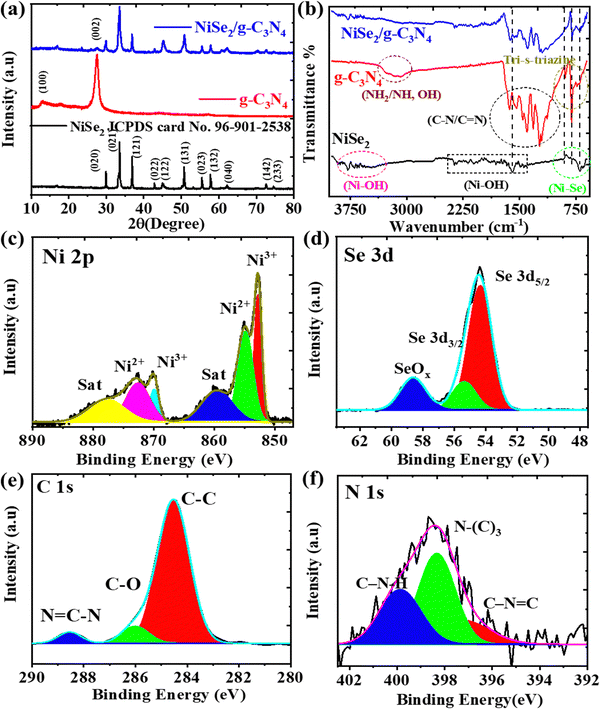 |
| Fig. 1 (a) XRD and (b) FTIR patterns for the NiSe2, g-C3N4, and NiSe2/g-C3N4 nanocomposite. (c)–(f) XPS patterns of Ni 2p, Se 3d, C 1s, and N 1s in NiSe2/g-C3N4 nanocomposite. | |
To investigate surface chemical states, XPS measurements were performed. Fig. S1a–c (ESI†) shows the XPS spectra of Ni 2p and Se 3d of NiSe2. The Ni 2p spectrum contains Ni 2p1/2, Ni 2p3/2, and corresponding satellite peaks. The deconvoluted peaks of Ni2+ 2p1/2 of NiSe2 and Ni2+ 2p1/2 of Ni(OH)2 are located at 870 and 872.77 eV, respectively.49 The other two deconvoluted peaks at 852.82 and 855.17 eV are related to the Ni2+ 2p3/2 of NiSe2 and Ni2+ 2p3/2 of Ni(OH)2. The surface absorption of water may be responsible for the occurrence of the deconvoluted peaks of Ni2+ 2p of Ni(OH)2.50 The peaks at 860 and 880.15 eV correspond to standard Ni 2p satellite peaks.
Fig. S1d–f (ESI†) shows XPS survey spectra and the deconvolution curves for the g-C3N4 sample. The C 1s XPS spectra consist of three peaks at 287.33 eV (N–C
N), 285.51 eV (C–O) and 284.09 eV (C–C). For N 1s spectra, peaks are observed at 400.2 eV (–C–N–H), 399.07 eV (N–C3), and 397.8 eV (C–N
C). The presence of different functional groups consisting of C and N elements on the surface of the g-C3N4 nanosheets could facilitate the ion adsorption and electron transfer required for the HER.21 The XPS survey spectrum of NiSe2/g-C3N4 (Fig. 1(c), (f) and Fig. S1g, ESI†), indicate the existence of Ni, Se, C, and N elements. In the case of NiSe2/g-C3N4, Ni 2p peaks are found to be red-shifted when compared to NiSe2 implying that there was electron migration from g-C3N4 to NiSe2 and a subsequent charge redistribution around Ni atoms in the composite. This shows the greater synergy between NiSe2 and g-C3N4 required for improved HER activity.
The growth and morphology of NiSe2 on the g-C3N4 sheets were analyzed by FE-SEM. Fig. 2(a)–(d) show the FE-SEM images of NiSe2 and NiSe2/g-C3N4, respectively. The uniformly grown NiSe2 nanoparticles on the g-C3N4 nanosheets are seen. These particles are less agglomerated in NiSe2/g-C3N4 when compared to NiSe2. This leads to a greater availability of exposed active sites required for electrochemical reactions and ion adsorption during the HER. The structural analysis of the NiSe2/g-C3N4 nanocomposite was examined using HR-TEM, and it was clear from this that NiSe2 grains were successfully grown on the g-C3N4 nanosheets (Fig. 2(e) and (f)). This direct growth improves the mechanical and chemical stability needed for the increased electrocatalytic activity and stability, which in turn accelerates the ionic/electron transfer. The EDS spectrum of the NiSe2/g-C3N4 composite (Fig. 2(g)–(l)) indicates the presence of Ni, Se, C, and N elements in the NiSe2/g-C3N4 composite sample. All the elements show peaks at their known energies. The intensity count ratio for Ni and Se was approximately 1
:
2, which implied the presence of NiSe2 in the composite. Fig. S1h (ESI†) displays the EDS elemental mapping for Ni, Se, C, and N in NiSe2/g-C3N4 samples. These images reveal the presence of all the elements in the composite, and a homogeneous distribution of NiSe2 on the g-C3N4 sheets could be inferred, confirming the successful fabrication of the nanocomposite.
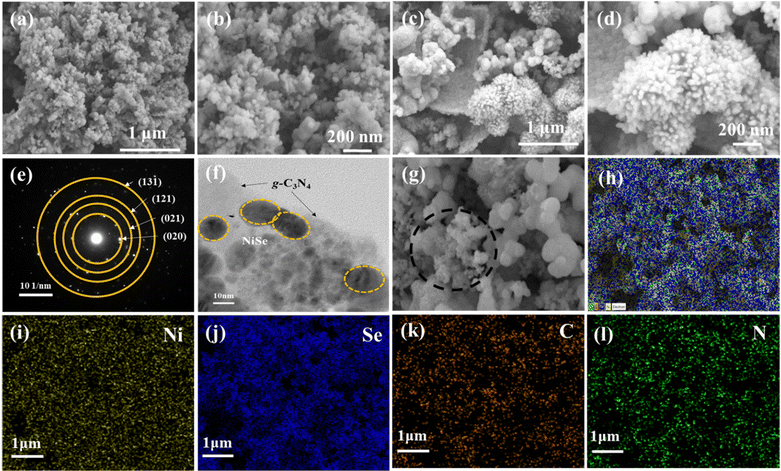 |
| Fig. 2 FE-SEM images of (a), (b) NiSe2, (c), (d) NiSe2/g-C3N4, and (e), (f) HR-TEM of NiSe2/g-C3N4. (g)–(l) Energy dispersive spectroscopy (EDS) mapping of elements Ni, Se, C, and O in NiSe2/g-C3N4. | |
The electrode/electrolyte compatibility is the most crucial for numerous issues that aid the HER performance. Thus, surface wettability becomes significant for the analysis of electrode surface energy and transportation of charges/ions at the interface.51 To do so, the contact angle, which determines the effective surface energy and hydrophilicity, is used to measure the interaction between electrode surfaces in contact with the electrolyte. The contact angle has an inverse relationship with the surface free energy. From Fig. 3(a), the contact angles of NF, g-C3N4/NF, NiSe2/NF, and NiSe2/g-C3N4/NF for a 1 M KOH electrolyte are 0°, 113°, 64° and 36° respectively. Thus, the low contact angle of the NiSe/g-C3N4 composite implies enhanced wettability.52,53 The Fowkes’ approximation was used to compute the surface free energy.54,55 A set of four distinct standard liquids (distilled water, ethylene glycol, formamide, and glycerol) with known values of surface tension parameters (polar and dispersion components) were employed for this (see Fig. 3(b)).56 The calculated surface free energies for g-C3N4/NF, NiSe2/NF, and NiSe2/g-C3N4/NF were found to be 25.12, 38.49, and 49.2 mJ m−2, respectively (see Fig. 3(c)). The presence of lone pair electrons in g-C3N4 enhanced the charge carrier mobility and wettability of the composite. As a result, the reduced contact angle and larger surface energy of the composite electrode aid in the enhancement of the interfacial charge transfer and ion diffusion accessibility.
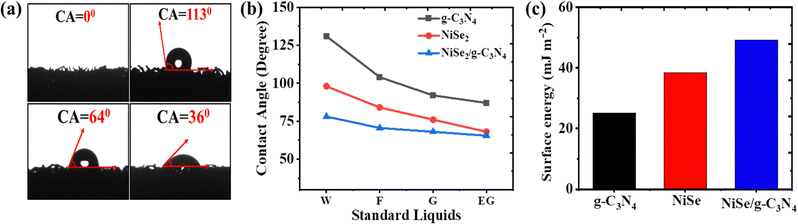 |
| Fig. 3 (a) Contact angle of NF, g-C3N4, NiSe2, and NiSe2/g-C3N4 electrodes with 6 M KOH solution. (b) The contact angle of g-C3N4, NiSe2, and NiSe2/g-C3N4 electrodes with distilled water (W), ethylene glycol (EG), glycerol (G), formamide (F) as standard liquids. (c) Surface energy of g-C3N4, NiSe2, and NiSe2/g-C3N4 electrodes. | |
3.3. Electrochemical studies
A three-electrode configuration was used to measure the HER electrochemical behavior of the synthesized samples. In a typical setup, NiSe2/g-C3N4/NF (working), Hg/HgO (reference), and graphite rod (counter) electrodes were used in 1.0 M KOH electrolyte. Further, a comparison was carried out with 20%Pt/C@NF and bare NF to study their HER activity. Fig. 4(a) displays iR-corrected LSV polarization curves measured in the potential range of −0.6 V to 0 vs. RHE. The overpotential values were found to be 228, 189, 153, 87, 116, and 64 mV for g-C3N4, NiSe2, NiSe2/10g-C3N4, NiSe2/20g-C3N4, NiSe2/30g-C3N4 and 20%Pt/C electrodes, respectively, at a current density of 10 mA cm−2. The NiSe2-based samples demonstrated higher cathodic currents and more positive onset potentials compared to the bare NF indicating the greater HER activities of nickel selenides compared to that of Ni metal. Thus, the HER overpotential for NiSe2/20g-C3N4 was just 23 mV more than Pt/C@NF and is the lowest among the prepared samples. Additionally, the overpotentials for all the samples were also measured and compared at a current density of 50 mA cm−2 (see Fig. 4(b)). The increase in the current density, increases the overpotential value considerably. The sequence in the decreasing order for the overpotential is g-C3N4 > NiSe2 > NiSe2/10g-C3N4 > NiSe2/30g-C3N4 > NiSe2/20g-C3N4, and 20%Pt/C. Thus, compared to the other samples, NiSe2/20g-C3N4 exhibits the lowest overpotential and is closer to that of the 20%Pt/C electrode even at a high current density of 50 mA cm−2.
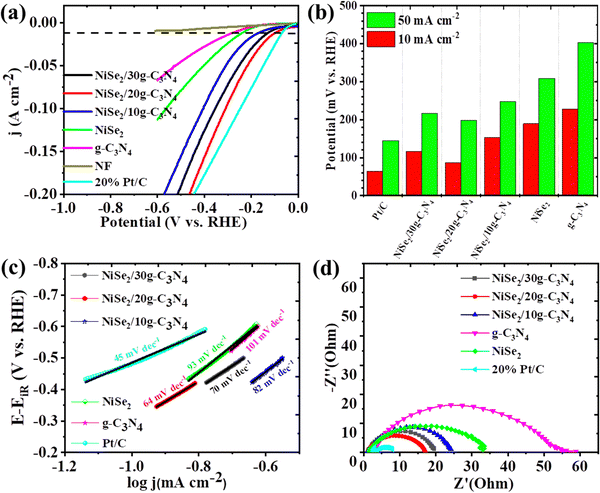 |
| Fig. 4 HER performances (a) LSV, (b) overpotentials, (c) Tafel plots, and (d) Nyquist plot of NiSe2, g-C3N4, NiSe2/10g-C3N4 NiSe2/20g-C3N4, NiSe2/30g-C3N4, and 20%Pt/C. | |
The Tafel slopes derived from related LSV sweeps aid in a better understanding of the HER reaction kinetics (Fig. 4(c)). The Tafel slopes for g-C3N4, NiSe2, NiSe2/10g-C3N4, NiSe2/20g-C3N4, NiSe2/30g-C3N4 and 20% Pt/C were calculated to be 103, 93, 82, 64, 70, and 45 mV dec−1, respectively. Pt/C shows the lowest Tafel slope and best HER activity. However, NiSe2/20 g-C3N4 shows a lower Tafel slope and an accelerated HER when compared to those of the other samples. The Volmer step serves as a bottleneck for the Volmer–Heyrovsky process in alkaline HER. Thus, heterostructured electrocatalysts with their electronic structure modulation and multiple active sites can promote the adsorption of Had/OHad for faster water dissociation in the Volmer step-determined alkaline HER phenomenon.57 Moreover, the Tafel value is considerably lower than the theoretical Tafel slope of 120 mV dec−1 for the Volmer step in alkaline HER, indicating an accelerated water dissociation for NiSe2/20 g-C3N4.49 According to Tafel slope calculations, the synthesized electrocatalyst NiSe2/20g-C3N4 follows the Volmer–Heyrovsky mechanism.
Taking into consideration the HER properties, i.e. overpotential and Tafel slope, a comparison of our work with that of different research groups, is shown in Table S1 (ESI†). The NiSe@g-C3N4 electrode shows the lowest Tafel slope and overpotential amongst all the reported electrocatalysts, suggesting that there is superior HER electrocatalytic activity in an alkaline medium. This high HER catalytic activity of NiSe2/g-C3N4 may correspond to the optimum charge transfer kinetics, intrinsic electrode activity, and the presence of several active sites.
EIS measurements help in examining the electrode kinetics. The Nyquist plot helps in the evaluation of Rs (solution resistance) and Rct (charge transfer resistance). The magnitude of Rs is obtained from the X-intercept of the Nyquist curve, while Rct is dependent on the diameter of the semi-circle.58 The low value of Rs implies that there is better electrical integration of the electrode/electrolyte. From Fig. 4(d), it is seen that the diameter of the semi-circle for NiSe2/20g-C3N4 is smaller than that of the other samples, which implies there is a lower Rct at the electrode/electrolyte interface during the HER. The Rct values of g-C3N4, NiSe2, NiSe2/10g-C3N4, NiSe2/20g-C3N4, NiSe2/30g-C3N4 and 20%Pt/C were calculated to be 55.34, 33.04, 24.17, 17.04, 19.59, and 7.93 Ω, respectively. Thus, NiSe@20g-C3N4 shows higher charge transfer kinetics and HER activity compared to the other samples during alkaline water oxidation.
The electrochemical active surface area (ECSA) was determined using scan rate-dependent normalized CV-derived Cdl measurements in the non-faradaic region. The Cdl values for g-C3N4, NiSe2, and NiSe2/20g-C3N4, were computed to be 6.45, 10.9 and 22.7 mF cm−2, respectively, (Fig. 5(a), (b), and Fig. S2b–d, ESI†). Thus, NiSe2/20g-C3N4 displayed a Cdl which is greater than that of bare NiSe2 and g-C3N4. Accordingly, the ECSA of g-C3N4, NiSe2, and NiSe2/20g-C3N4 electrodes were calculated to be 161.25, 275.5, and 567.5 cm−2, respectively. It is also seen that the Cdl and ECSA values of NiSe@20g-C3N4 are higher than those of other samples. This implies that NiSe@g-C3N4 has the highest density of HER active sites. The turnover frequency (TOF) was calculated to study the intrinsic activity. The TOF values for NiSe2, and NiSe2/20g-C3N4 were found to be 0.054 and 0.085 s−1, respectively. A TOF value of 0.085 s−1 means that 85 hydrogen molecules are produced per second per active site.59 Thus, the intrinsic activity for NiSe2/20g-C3N4 was the highest among all the prepared samples.
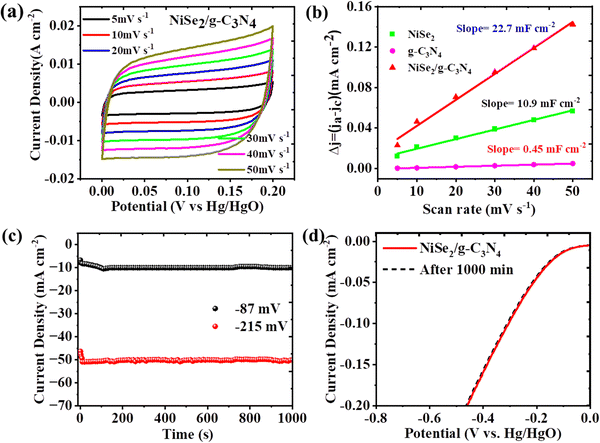 |
| Fig. 5 (a) CV of NiSe2/g-C3N4 at 5–50 mV s−1 scan rates, (b) estimated values of Cdl for g-C3N4, NiSe2, and NiSe2/g-C3N4. (c) Chronoamperometric measurement at constant potentials −0.087 and 0.215 V vs. RHE for NiSe2/g-C3N4. (d) LSV curves of NiSe2/g-C3N4 before and after 1000 min. | |
For commercial scale-up of hydrogen production using water decomposition, in addition to high performance, the long-term stability also becomes significant. The chronoamperometry measurements were carried out for NiSe2/g-C3N4 electrode at two different potentials i.e. 87 and 215 mV vs. RHE for a time interval of 1000 min. Fig. 5(c) demonstrates that the current density fairly remains constant even after 1000 min of HER, which explains the long-term durability of the electrode. This stability is higher when compared to that of the bare NiSe2 and g-C3N4 electrodes (see Fig. S2a, ESI†). Moreover, LSV curves did not change significantly even after 1000 min of the experiment (Fig. 5(d)), suggesting the potential of NiSe2/g-C3N4 for long-run applications. As a consequence, the enhanced electrocatalytic performance of NiSe2/g-C3N4 over bare NiSe2 and g-C3N4 is the result of the modified surface chemistry generated by g-C3N4 and tailored electronic characteristics of the composite. Thus, the optimal loading of 20g-C3N4 in the NiSe2 composite showed an enhanced synergistic interaction and provided a balance between active sites and electron transfer pathways, thus enhancing the charge transfer kinetics and HER activity. This loading also provided an optimal surface area, facilitating efficient mass/charge transport, while promoting a favorable electronic structure that optimized the adsorption and activation of hydrogen intermediates during the HER process.
4. Conclusion
In summary, the synthesis of a NiSe2/g-C3N4 nanocomposite using a simple hydrothermal technique was carried out. The composite electrode demonstrated high HER catalytic activity in 1 M KOH aqueous solution. The Tafel slope and overpotential values for NiSe2/g-C3N4 were less than those for the NiSe2 and g-C3N4 electrodes. The nanocomposite shows excellent performance which is close to that of the Pt/C catalyst. Moreover, long term stability for 1000 min without performance decline was achieved. A stronger NiSe2 catalyst supported by the g-C3N4 interface arises primarily due to in situ growth and higher chemical stability. The electrochemical tests and analysis reveal that improved intrinsic catalytic activity, larger ECSA, lowered contact angle, and faster charge kinetics contribute to the excellent catalytic performance. This study sheds light on the development of a high-performance, long-term stable, noble-metal-free electrocatalyst for use in the HER.
Data availability
Data will be made available on request.
Author contributions
Somnath R. Khaladkar: conceptualization, data curation, formal analysis, investigation, validation, visualization, writing – original draft. Oshnik Maurya: data curation, formal analysis, writing – original draft. Girish Gund: validation, visualization, writing – review and editing. Bhavesh Sinha: writing – review and editing. Girish Kamble: data curation. Jin Hyeok Kim: resources, project administration, supervision, funding acquisition. R. R. Deshmukh: project administration, resources, writing – review and editing. Archana Kalekar: conceptualization, funding acquisition, investigation, project administration, resources, supervision, writing – review and editing.
Conflicts of interest
There are no conflicts to declare.
Acknowledgements
The funding for Dr Archana Kalekar research is provided by SERB [EEQ/2022/001076]. Dr Girish Gund acknowledges the DST-SERB [SRG/2021/001791] for their funding. Somnath R. Khaladkar and Oshnik Maurya acknowledge their financial support from the UGC NET-JRF (517906) and UGC NFOBC (202021-201610071195), respectively. This work was also supported by a National Research Foundation of Korea (NRF) grant funded by the government of the Republic of Korea (MSIT) (no. 2022R1A2C2007219). Moreover, this work was supported by the Priority Research Centers Program of the National Research Foundation of Korea (NRF) funded by the Ministry of Education, Science, and Technology (2018R1A6A1A03024334).
References
- O. Maurya, S. R. Khaladkar, B. Sinha, B. M. Bhanage, R. R. Deshmukh, J. H. Kim and A. Kalekar, Electrochim. Acta, 2023, 471, 143391 CrossRef CAS.
-
S. Lavate, H. P. S. Yalamati and R. Srivastava, in Solar-Driven Green Hydrogen Generation and Storage, ed. R. Srivastava, J. Chattopadhyay and D. M. F. Santos, Elsevier, 2023, pp.507–524 Search PubMed.
- N. Kumar, M. Rehan, S. Khaladkar, O. Maurya, K. Rao, A. Kalekar, M. Kumar and J. Kumar, Mater. Chem. Phys., 2024, 316, 129072 CrossRef CAS.
- O. Maurya, S. Khaladkar, M. R. Horn, B. Sinha, R. Deshmukh, H. Wang, T. Y. Kim, D. P. Dubal and A. Kalekar, Small, 2021, 17, 1–29 CrossRef PubMed.
- S. Khaladkar, G. Gund, O. Maurya, B. Sinha, P. Salame, D. Dubal, R. Deshmukh and A. Kalekar, Adv. Energy Sustainability Res., 2023, 2300013 CrossRef CAS.
- J. B. M. Parambath, N. Hussain, H. Alawadhi, Y. Park, D. D. Dionysiou, C. Han and A. A. Mohamed, Comments Inorg. Chem., 2022, 42, 249–270 CrossRef CAS.
-
R. R. Deshmukh, A. S. Kalekar, S. R. Khaladkar and O. C. Maurya, in Nanotechnology for Energy and Environmental Engineering, ed. L. Ledwani and J. S. Sangwai, Springer International Publishing, Cham, 2020, pp.329–354 Search PubMed.
- M. R. Ansari, S. Khaladkar, A. Kalekar, M.-D. Kim and K. R. Peta, J. Energy Storage, 2023, 74, 109494 CrossRef.
- S. Shen, H. Zhang, K. Song, Z. Wang, T. Shang, A. Gao, Q. Zhang, L. Gu and W. Zhong, Angew. Chem., Int. Ed., 2024, 63, e202315340 CrossRef CAS PubMed.
- X. Wang, Y. Fei, J. Chen, Y. Pan, W. Yuan, L. Y. Zhang, C. X. Guo and C. M. Li, Small, 2022, 18, 2103866 CrossRef CAS PubMed.
- X. Wang, Y. Fei, W. Wang, W. Yuan and C. M. Li, ACS Appl. Energy Mater., 2019, 2, 8851–8861 CrossRef CAS.
- S. Bama Sundararaj, S. Tamilarasan, K. Kadirvelu and S. Thangavelu, Appl. Surf. Sci., 2023, 612, 155785 CrossRef CAS.
- Z. Wang, Z. Lin, Y. Wang, S. Shen, Q. Zhang, J. Wang and W. Zhong, Adv. Mater., 2023, 35, 1–8 Search PubMed.
- N. Sahu, J. K. Das and J. N. Behera, Inorg. Chem., 2022, 61, 2835–2845 CrossRef CAS PubMed.
- W. Yuan, Y. Li, L. Liang, F. Wang and H. Liu, ACS Appl. Energy Mater., 2022, 5, 5036–5043 CrossRef CAS.
- Z. Tian, Y. Liu, Q. Xu, Y. Shi, C. Ma, B. Peng, G. Liu, J. Yang and W. Zheng, Electrochim. Acta, 2022, 425, 140711 CrossRef CAS.
- K. Song, H. Zhang, Z. Lin, Z. Wang, L. Zhang, X. Shi, S. Shen, S. Chen and W. Zhong, Adv. Funct. Mater., 2023, 2312672, 1–9 Search PubMed.
- X. Fan, X. Wang, W. Yuan and C. M. Li, Sustainable Energy Fuels, 2017, 1, 2172–2180 RSC.
- Y. Chen, B. Zhang, Y. Liu, J. Chen, H. Pan and W. Sun, Mater. Today Catal., 2023, 1, 100003 CrossRef.
- S. R. Khaladkar, O. Maurya, G. Gund, B. Sinha, D. Dubal, R. R. Deshmukh and A. Kalekar, J. Energy Chem., 2023, 87, 304–313 CrossRef CAS.
- K. Li, Z. Shi, L. Wang, W. Wang, Y. Y. Liu, H. Cheng, Y. Yang and L. Zhang, J. Hazard. Mater., 2023, 448, 130890 CrossRef CAS PubMed.
- S. R. Khaladkar, O. Maurya, G. Gund, B. Sinha, D. Dubal, R. Deshmukh and A. Kalekar, ACS Appl. Mater. Interfaces, 2024, 16(9), 11408–11420 CrossRef CAS PubMed.
- M. Guan, C. Wang, S. Li, H. Du and Y. Yuan, ACS Sustainable Chem. Eng., 2020, 8, 10313–10320 CrossRef CAS.
- M. Zulqarnain, A. Shah, M. A. Khan, F. Jan Iftikhar and J. Nisar, Sci. Rep., 2020, 10, 1–8 CrossRef PubMed.
- S. Yousefzadeh and N. Morovati, Int. J. Hydrogen Energy, 2020, 45, 33512–33520 CrossRef CAS.
- X. Lv, W. Wei, H. Wang, B. Huang and Y. Dai, Appl. Catal., B, 2020, 264, 118521 CrossRef CAS.
- J. Jia, W. Sun, Q. Zhang, X. Zhang, X. Hu, E. Liu and J. Fan, Appl. Catal., B, 2020, 261, 118249 CrossRef CAS.
- Z. Zhuang, Y. Li, Z. Li, F. Lv, Z. Lang, K. Zhao, L. Zhou, L. Moskaleva, S. Guo and L. Mai, Angew. Chem., Int. Ed., 2018, 57, 496–500 CrossRef CAS PubMed.
- H. Jin, X. Liu, Y. Jiao, A. Vasileff, Y. Zheng and S. Z. Qiao, Nano Energy, 2018, 53, 690–697 CrossRef CAS.
- J. Liang, Y. Zheng, J. Chen, J. Liu, D. Hulicova-Jurcakova, M. Jaroniec and S. Z. Qiao, Angew. Chem., Int. Ed., 2012, 51, 3892–3896 CrossRef CAS PubMed.
- R. Shwetharani, S. Kapse, R. Thapa, D. H. Nagaraju and R. G. Balakrishna, ACS Appl. Energy Mater., 2020, 3, 12682–12691 CrossRef CAS.
- G. Dong, H. Fan, K. Fu, L. Ma, S. Zhang, M. Zhang, J. Ma and W. Wang, Composites, Part B, 2019, 162, 369–377 CrossRef CAS.
- Y. Liu, Y. Zheng, Q. Xu, Y. Shi, Z. Tian, R. wang, G. Zhang, J. Chen, Z. Wang and W. Zheng, Chem. Eng. J., 2020, 387, 124121 CrossRef CAS.
- Z. Chen, Y. Gao, F. Chen and H. Shi, Chem. Eng. J., 2021, 413, 127474 CrossRef CAS.
- H. Cölfen and S. Mann, Angew. Chem., Int. Ed., 2003, 42, 2350–2365 CrossRef PubMed.
- B. Z. Zhang, H. Sun, X. Shao, D. Li, H. Yu and M. Han, Adv. Mater., 2005, 17, 42–47 CrossRef.
- X. Wang, W. Mao, J. Zhang, Y. Han, C. Quan, Q. Zhang, T. Yang, J. Yang, X. Li and W. Huang, J. Colloid Interface Sci., 2015, 448, 17–23 CrossRef CAS PubMed.
- J. Safaei, N. A. Mohamed, M. F. Mohamad Noh, M. F. Soh, N. A. Ludin, M. A. Ibrahim, W. N. Roslam Wan Isahak and M. A. Mat Teridi, J. Mater. Chem. A, 2018, 6, 22346–22380 RSC.
- J. Kavil, P. M. Anjana, P. Periyat and R. B. Rakhi, Sustainable Energy Fuels, 2018, 2, 2244–2251 RSC.
- G. K. Subhash, M. D. Benoy, J. Duraimurugan, S. Prabhu, R. Siranjeevi, R. Ramesh, G. Suresh kumar and M. Shkir, Inorg. Chem. Commun., 2022, 142, 109719 CrossRef.
- F. Shiravani, J. Tashkhourian and B. Haghighi, Sustainable Energy Fuels, 2021, 5, 3229–3239 RSC.
- T. Ivanova, A. Harizanova, M. Shipochka and P. Vitanov, Materials, 2022, 15, 1742 CrossRef CAS PubMed.
- S. Wang, P. He, L. Jia, M. He, T. Zhang, F. Dong, M. Liu, H. Liu, Y. Zhang, C. Li, J. Gao and L. Bian, Appl. Catal., B, 2019, 243, 463–469 CrossRef CAS.
- D. Sun, J. Zhang, H. Ren, Z. Cui and D. Sun, J. Phys. Chem. C, 2010, 114, 12110–12116 CrossRef CAS.
- J. Nai, X. Xu, Q. Xie, G. Lu, Y. Wang, D. Luan, X. Tao and X. W. Lou, Adv. Mater., 2022, 34, 1–7 CrossRef PubMed.
- B. Jansi Rani, G. Ravi, R. Yuvakkumar, B. Saravanakumar, M. Thambidurai, C. Dang and D. Velauthapillai, ACS Omega, 2020, 5, 14702–14710 CrossRef CAS PubMed.
- S. Manickam, H. Kuzhandaivel, Y. Selvaraj, M. C. Franklin and K. Sivalingam Nallathambi, Dalton Trans., 2022, 51, 1542–1552 RSC.
- I. Ahmad, S. B. Khan, T. Kamal and A. M. Asiri, J. Mol. Liq., 2017, 229, 429–435 CrossRef CAS.
- Y. Bai, H. Zhang, X. Lu, L. Wang, Y. Zou, J. Miao, M. Qiao, Y. Tang and D. Zhu, Chem. – Eur. J., 2023, 29(28), 0947–6539, DOI:10.1002/chem.202300205.
- L. Zhao, Y. Zhang, Z. Zhao, Q. H. Zhang, L. B. Huang, L. Gu, G. Lu, J. S. Hu and L. J. Wan, Natl. Sci. Rev., 2020, 7, 27–36 CrossRef CAS PubMed.
- M. M. Vadiyar, S. C. Bhise, S. K. Patil, S. S. Kolekar, A. R. Shelke, N. G. Deshpande, J. Y. Chang, K. S. Ghule and A. V. Ghule, Chem. Commun., 2016, 52, 2557–2560 RSC.
- H. S. Lee, G. S. Gund and H. S. Park, J. Power Sources, 2020, 451, 227763 CrossRef CAS.
- T. Liu, K. Wang, Y. Chen, S. Zhao and Y. Han, Green Energy Environ., 2019, 4, 171–179 CrossRef.
- F. M. Fowkes, J. Phys. Chem., 1963, 67, 2538–2541 CrossRef CAS.
- F. M. Fowkes, J. Adhes. Sci. Technol., 1987, 1, 7–27 CrossRef CAS.
- R. R. Deshmukh and A. R. Shetty, J. Appl. Polym. Sci., 2008, 107, 3707–3717 CrossRef CAS.
- X. Ma, J. Yang, X. Xu, H. Yang and C. Peng, RSC Adv., 2021, 11, 34432–34439 RSC.
- N. O. Laschuk, E. B. Easton and O. V. Zenkina, RSC Adv., 2021, 11, 27925–27936 RSC.
- K. S. Ranjith, S. Y. Lee, S. M. Ghoreishian, N. R. Chodankar, G. S. Rama Raju, S. J. Patil, Y. S. Huh, S. J. Park and Y. K. Han, Carbon N. Y., 2023, 206, 246–259 CrossRef CAS.
|
This journal is © The Royal Society of Chemistry 2024 |
Click here to see how this site uses Cookies. View our privacy policy here.