DOI:
10.1039/D3MA00732D
(Paper)
Mater. Adv., 2024,
5, 632-641
Ginger-derived hierarchical porous carbon as an anode material for potassium-ion batteries and capacitors†
Received
19th September 2023
, Accepted 29th November 2023
First published on 12th December 2023
Abstract
Carbonaceous materials are ideal as an anode for potassium-ion batteries (KIBs) because of their low cost, tunable physiochemical properties, and excellent reversible intercalation of potassium-ions (K+). In this work, we propose for the first time an economically viable and environmentally friendly route for producing hierarchical nanoporous activated ginger-derived carbon (AGC). Large interlayer spacing with a disordered microstructure of AGC provides a reason to investigate it as a high-capacity anode for rechargeable KIBs. AGC exhibits excellent electrochemical characteristics under moderate (100 mA g−1) to high rate (1000 mA g−1) discharge conditions. Against a current density of 100 mA g−1, a steady-state reversible capacity of 220 mA h g−1 was delivered. Furthermore, a 175 mA h g−1 capacity has been demonstrated at a 1000 mA g−1 rate for an impressive 1000 cycles. Another striking feature of AGC is its high surface area of 2717 m2 g−1 which makes it a potential candidate as an electrode for constructing a potassium-ion capacitor (KIC). AGC was used as a negative electrode while activated candle soot (ACS) as the positive electrode to develop a dual carbon KIC with high-rate capability. The as developed dual carbon KIC delivered a reversible capacity of 120 mA h g−1 over 100 cycles at 50 mA g−1. In essence, due to the extraordinary physiochemical characteristics, AGC is therefore not only a superior electrode material to other biomass-derived carbons but also a viable contender for various other electroactive applications.
1. Introduction
The demand for new, advanced and sustainable batteries with high energy density is growing in response to developing electronic devices, electric cars, and smart grids.1–3 The current use of lithium-ion batteries in large-scale energy storage applications such as electric vehicles has led to a rapid depletion of available lithium supplies and an increase in costs.4–9 As a result, addressing the demand for stationary energy storage at a low cost and with the fewest rare components possible has become critical. The scientific community has been focusing on sodium-ion batteries for the past decade or so, due to the abundance of sodium and the “rocking chair” electrochemical behavior similar to LIBs.10 However, due to recent advancements in anode and cathode materials for potassium-ion batteries, as well as whole-cell prototypes, the state of this emerging field is rapidly evolving. Potassium-ion batteries may have many advantages compared to sodium-ion batteries. According to reports, the redox potential of potassium is lower than that of sodium (standard electrode potentials are −2.93, −2.71 vs. the standard hydrogen electrode, respectively), implying that high voltage and high energy density batteries are similar to lithium-ion batteries (lithium redox potential of −3.04 V vs. SHE).11 When compared to lithium, potassium is a more abundant element on the planet, accounting for 1.5% vs. 0.0017% for Li, and its cost is around one-tenth that of lithium.12 Although the higher radius of the K ion (0.138 nm vs. 0.102 nm (Na ion) and 0.076 nm (lithium-ion)) may obstruct the intercalation process, its compatibility with some electrolytes, such as 1,2-dimethoxyethane (DME) has been demonstrated to produce an even smaller K ion-solvent Stroke's radius, which may have kinetic benefits.13
According to previous studies, non-carbon anodes have several disadvantages that are difficult to overcome. Metal anodes, for example, have a mainly reversible alloying reaction with K, although the alloy produces a significant volume change.14–16 Carbon materials have emerged as the most viable solution for KIBs among all anode materials when considering economic efficiency, environmental friendliness, sustainability, outstanding electrolyte accessibility, and adjustable interlayer space.17–21 As a result, various carbon-based materials have been investigated for KIBs, such as carbon fiber, graphite, hard carbon, soft carbon, activated carbon, and composite materials to see if they may increase the K-ion storage capability of KIBs.11,17,22–29
Recently, the synthesis of porous and disordered carbon materials from bio-waste has gained significant importance based on the bio-waste-derived carbons that find various applications because of their abundant availability and low cost.7,30–40 The development of full KIBs from biowaste-derived materials will not only lower the cost of raw materials, resulting in lower production costs, but will also create a sustainable and clean environment.41 For example, Qing et al. successfully prepared a carbon material using corn husk and used it as an anode for KIBs.42 Lotfabad et al. generated hard carbon from biomass via pyrolysis of banana peels, and this hard carbon demonstrated good electrochemical performance.43 Zhenrui Wu and co-workers reported the carbon obtained from loofah as an anode material with the capacity of 150 mA h g−1 at 100 mA g−1 over 200 cycles.44
Inspired by the above developments, herein, we demonstrate ginger as a novel, low-cost, and easily available precursor for the synthesis of unique interconnected hierarchical porous carbon nanosheets. In addition to domestic garbage at home, we gather waste ginger from the locals in the southern region of India, particularly after making ginger tea, which discards significant amounts of ginger. This waste material, which was deemed unsuitable for any other use, was gathered and processed in an effort to convert it from filth to wealth. It was then used as an electromagnetic composite by biomass transmission and an electrode material for KIBs.45–49 The high surface area and interconnected porous character of carbon as derived from ginger have resulted from KOH activation during carbonization. The in-house produced interconnected porous carbon facilitates large accessible surface-active sites for electrolyte interaction and has been demonstrated as a potential anode for KIBs through this study for the first time. In other words, ginger-derived carbon material has an outstanding capacity of 380, 250, and 175 mA h g−1, corresponding to current densities of 100, 500, and 1000 mA g−1, respectively. Specifically, in-house synthesized carbon exhibits high reversible capacity and ultralong life. Furthermore, we successfully developed a low-cost asymmetric potassium dual carbon capacitor, which was constructed with activated ginger carbon (AGC) as an anode and activated candle soot carbon (ACS) as the cathode. This research aids in the development of a biomass derived carbon as a promising KIB anode material.
2. Experimental details
2.1. Material synthesis
Synthesis of AGC involves a simple approach as described below and shown in a schematic as Fig. 1. The ginger was collected from the local market, washed thoroughly with water, cut into small pieces, and dried subsequently at 80 °C for 24 h. Pre-carbonization was carried out at 400 °C under a nitrogen atmosphere for 3 h. Afterward, the pre-carbonized material was mixed with KOH in a 1
:
3 ratio, and the furnace heated at 800 °C for 2 h with a heating rate of 5 °C min−1 in a nitrogen atmosphere. The powder thus obtained was washed thoroughly with 1 M HCl to remove metal impurities and washed repeatedly with distilled water until it attains a neutral pH. The resulting carbon material was dried at 100 °C. The synthesized carbon material is denoted as AGC.
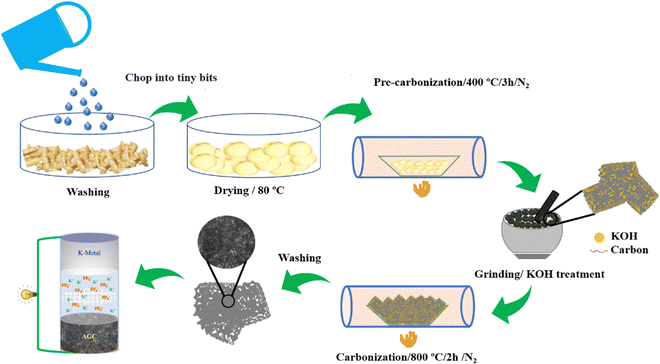 |
| Fig. 1 Schematic illustration of the preparation of activated ginger-derived carbon. | |
2.2. Activated candle soot carbon (ACS)
As per our previous report, candle soot carbon was prepared as below.50 On a steel plate, burning candle soot was gathered from the flames tip and cleansed using ultrasonic technology to get rid of the impurities. The accumulated soot was scraped off the surface and heated to 450 °C for two hours in an air environment. To activate the candle soot carbon, it was soaked in KOH solution in the mass ratio of 1
:
3 and then the furnace was heated at 700 °C for 2 h with a heating rate of 5 °C min−1 in a nitrogen atmosphere. The powder thus obtained was washed thoroughly with 1 M HCl to remove metal impurities and washed repeatedly with distilled water until it attains a neutral pH and dried at 100 °C.
2.3. Material characterization
X-ray diffraction (PANalytica X’pert pro-X-ray diffractometer) of the sample was recorded with a Cu-Kα radiation (λ = 1.5406 Å) source. Raman spectra (WITec Raman spectroscopy) were obtained by using green laser excitation (λ = 532 nm with excitation energy of 2.33 eV). Field emission scanning electron microscopy (FESEM) images of the samples were captured using a JEOL-JEM-2011(200KV) system, and transmission electron microscopy (TEM) images of the samples were obtained using a JEOL-JSM-700F. The specific surface area and pore size distribution of the product were determined by using N2 adsorption isotherms (Autosorb iQ, Quantachrome, USA).
2.4. Electrochemical measurements
Electrochemical measurements were carried out using CR2032 type coin cells, wherein copper foil has been used as the current collector, potassium metal as both the counter electrode and reference electrode, and glass microfiber as the separator. The electrolyte of 0.8 M of KPF6 in a 1
:
1 (v/v) mixture of ethylene carbonate (EC) and dimethyl carbonate (DMC) was prepared and stored in an Ar-filled glovebox. To make a working electrode, a slurry was prepared by mixing ginger carbon (activated and inactivated) (70 wt%) as the active material, Super-P as a conductive carbon (20 wt%), and polyvinylidene fluoride binder (10 wt%) in N-methyl-2-pyrrolidone as solvent. The slurry was coated on copper foil and dried in an oven at 80 °C to evaporate NMP. The hot roll is pressed to ensure better adherence and cut into circular discs of 1 mm diameter to act as an anode in the coin cell assembly. The coin cell (CR2032) was assembled in a high-purity Ar-filled glovebox with water and oxygen content lower than 1 ppm. Cyclic voltammetry (CV) was recorded on a VMP3 multichannel potentiostat–galvanostat system (Biologic Science Instrument) in the potential window of 0.01–3.0 V and at the scan rate of 0.05 mV s−1. Before the manufacturing of the full KIC cell, the AGC anode was prepotassiated utilizing the half-cell configuration at 50 mA g−1. The loading of the cathode material and anode material was about 1 mg and 0.3 mg, respectively, which was cycled within 0.01 to 3.5 V. The charge–discharge behaviour was investigated using a biological battery cycler. Electrochemical impedance spectroscopy (EIS) measurements were carried out using a biologic VSP electrochemical workstation in the frequency range from 10 KHz to 100 mHz with an amplitude voltage of 10 mV at room temperature.
The energy density (E) and power density (P) of the supercapacitor cell were estimated according to eqn (1) and (2), respectively, represented as:
| 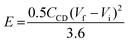 | (1) |
|  | (2) |
where
CCD (F g
−1) signifies the specific capacitance, (
Vf −
Vi) (V) represents the potential window, and Δ
t (
t) is the discharge time from the charge–discharge curve in the case of the device.
3. Results and discussion
3.1. Physiochemical characterization
The structural characterization of AGC has been carried out by powder X-ray diffraction study, as shown in Fig. 2a. We can observe two peaks at 2θ = 23.4° and 43.4°, which can be assigned to the (002) and (100) crystallographic planes of graphite, respectively, and the wide and broad peaks reflect the amorphous characteristic of the AGC material.51 The (002) plane computed d spacing value is 0.386 nm higher than the pure graphitic carbon structure (0.335 nm). The large interlayer spacing allows for the de/intercalation of potassium ions between the layers.52 The peak at 2θ = 43.4° with a lower intensity results from the (001) plane due to the low graphitic character of the as-prepared AGC sample. According to the XRD results, the carbon produced from ginger has a significant quantity of the amorphous phase combined with the low graphitic form.
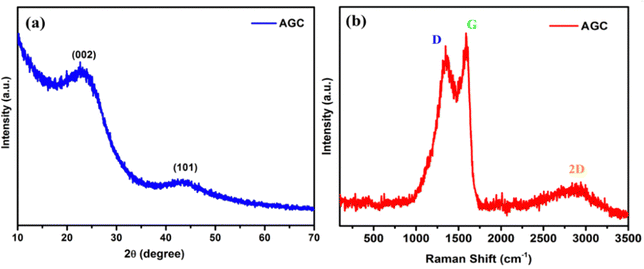 |
| Fig. 2 (a) XRD pattern and (b) Raman spectrum of AGC. | |
The papered carbon (AGC) sample was subjected to Raman spectroscopy analysis to establish its graphitic and amorphous structure, as shown in Fig. 2b. In the Raman spectra, two main peaks were exhibited at around 1350 cm−1 and 1587 cm−1 corresponding to the disordered D band (defect band, corresponding to the A1g vibration mode) and graphitic G band (graphite band, corresponding to the E2g hexagonal graphitic lattice), respectively.53 The D-band is related to the sp3-bond of defective carbon structures, and the G-band represents the conjugated structure of the sp2-bond of graphitic carbon domains. The number of structural flaws and the level of molecular order inside the carbon structure can be expressed by the intensity ratio of the D-band and G-band (ID/IG). The ID/IG ratio of AGC was 0.96, which confirms the highly disordered structure of the synthesized carbon.42 Furthermore, a minor hump with a maximum at 2876 cm−1 is a typical peak of two-dimensional (2D) materials, indicating the presence of additional stacked graphite-like layers in AGC and the high degree of order of the graphitic layers with pseudo-graphite units.44 As a result, AGC with a lot of interlayer space and a lot of disordering may be an ideal material for storing and releasing K ions.
Nitrogen adsorption–desorption measurements were used to evaluate the specific surface area and porosity of the carbon produced from ginger (Fig. 3a and b). The adsorption isotherm has Type II features, showing that the carbon is microporous with mesoporosity, implying a complex pore structure and network effect in the sample. The large presence of micropores in the carbons is revealed by the adsorbed nitrogen in the initial relative pressure range (less than 0.1). Furthermore, the presence of well-developed mesopores is suggested by the detected hysteresis loops in the relative pressure range of 0.4 to 0.9.54–56 As shown in Fig. 3b, the majority of the micropores in the sample are bigger than 1.7 nm. Therefore, the sample possesses both micro and mesopores. Furthermore, the Brunauer–Emmett–Teller (BET) specific surface area (SSA) of the AGC was measured to be 2717 m2 g−1, whereas the micropore surface area was 1621 m2 g−1. The interconnected micro and mesopores can efficiently shorten the ion diffusion distance, and the pore walls can act as highways for electron transport, boosting the rate performance and cycling stability. As a result, the large SSA and hierarchical interconnected porous structure can ensure adequate contact between the electrolyte and the active material surface, resulting in offering a well-organized path for ion transport.57,58 Therefore, AGC with micro and mesopores, high interlayer spacing, and disordered microstructure possesses all characteristics needed for storing and releasing K ions.
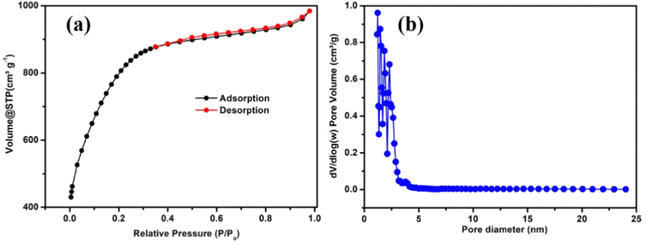 |
| Fig. 3 (a) Nitrogen adsorption–desorption isotherm, and (b) pore size distribution of AGC. | |
To further understand the surface features of the AGC material, X-ray photoelectron spectroscopy (XPS) was used to analyze the chemical composition, as shown in Fig. 4. The AGC is mostly constituted of C and O, as demonstrated in the XPS survey spectrum (Fig. 4a), with atomic concentrations of 90.4 and 9.6%, respectively. The high resolution deconvoluted C 1s spectrum (Fig. 4b) shows four peaks at about 282.1, 284.8, 286.6, and 288.5 eV, corresponding to the C–C/C
C, C–OH, C
O, and COOH bonds, respectively (Table 2). The high-resolution XPS spectrum of O 1s (Fig. 4c) can be deconvoluted into three peaks at binding energies of 530.6, 531.6, and 533.1 that are ascribed to O–I (C
O carbonyl groups), O–II (C–OH hydroxylic groups or C–O–C ether groups), and O-III (COOH carboxyl groups) (Table 1).51,59 The individual atomic percentages of C
O, C–OH or C–O–C, and COOH are 34.1%, 33.9%, and 32.0%, respectively. Although the presence of oxygen atoms in the carbon framework may diminish the materials' electroconductivity, on the other hand, it can improve the wettability by reducing the inert surface area and providing several active sites.59 To be more specific, the C–OH hydroxyl groups promote carbon material wetting, while the presence of C
O in carboxyl groups can boost surface acidity.
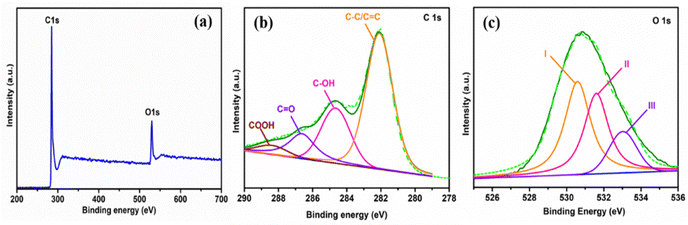 |
| Fig. 4 (a) XPS survey spectrum. High-resolution XPS spectra for (b) C 1s and (c) O 1s. | |
Table 1 Peak assignment of C 1s and O 1s of the synthesized AGC
Peak |
Binding energy (eV) |
Assignment |
Atom % |
C 1s |
282.1 |
C–C/C C |
91.0 |
284.8 |
C–OH |
286.6 |
C O |
288.5 |
COOH |
|
O 1s |
530.6 |
C O |
9.0 |
531.6 |
–C–OH/C–O–C |
533.1 |
COOH |
Fig. 5 shows the SEM and TEM images for the as-prepared activated ginger carbon materials. SEM images of AGC are shown in Fig. 5a and b, demonstrating the densely linked hierarchically porous structure. These uniformly distributed pores of AGC possibly arise when the pre-carbonized char of ginger was activated with KOH.60 The more detailed texture of the AGC material was examined with TEM images (Fig. 5c and d) and high-resolution TEM images (Fig. S1, ESI†). Fig. S1 (ESI†) shows graphitization interlayer spacing in the AGC. As seen in Fig. 5c, the carbon structure contains graphene-like wrinkled nanosheets that are intertangled and well-connected, resulting in a highly porous carbon network. The presence of a unique porous structure can improve the K-ion transport and reduce the internal resistance of the material as discussed in the next section.
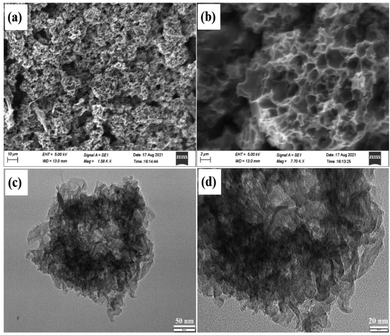 |
| Fig. 5 (a and b) SEM and (c and d) TEM images of the AGC. | |
3.2. Electrochemical characterization
We employed a 2032 button battery for half-cell configuration, and AGC was used as the anode material and the electrochemical performance was tested. The electrochemical K ion storage properties of AGC were investigated using CV and EIS. Fig. 6a exhibits the first five CV profiles of the AGC anode in the potential range of 0.01 to 3.00 V at a scan rate of 0.05 mV s−1. In the first cycle, the cathodic peak appears at 0.71 V, which demonstrates electrolyte decomposition and the formation of a solid electrolyte interphase (SEI) layer, which is primarily responsible for the irreversible capacity during the first discharging/charging cycle.61–63 The cathodic peak disappeared from the subsequent cycles, ensuring the stable SEI formation and the cycling stability of the electrode.64 Another strong peak around 0.5 V corresponds to the intercalation of K ions into the AGC layers and the KC8 formation.11,21,65 The deintercalation of K ions from AGC is represented by the wide anode peak from 0.2 to 0.5 V.66 Furthermore, most of the CV curves overlap after the second cycle, indicating strong reversibility of the potassium ion insertion/de-insertion processes in the AGC electrode.
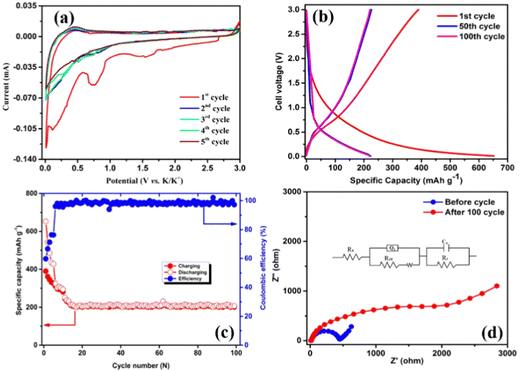 |
| Fig. 6 (a) Cyclic voltammogram of the synthesized AGC anode cycled between 0.1 and 3.0 V vs. K+/K with the scan rate of 0.05 mV s−1. (b) Discharge–charge profiles of the AGC anode at 100 mA g−1. (c) Cycling stability and coulombic efficiency of the AGC anode at the current density of 100 mA g−1. (d) EIS spectra of the as-fabricated AGC anode (blue color) and the cell under the influence of 100 mA g−1 after 100 cycles (red color) and the fitted equivalent circuit. | |
The selected charge–discharge curves of the AGC anode at a current density of 100 mA g−1 are shown in Fig. 6b. The AGC sample initial charge/discharge curves follow the same pattern as the CV curves, indicating highly reversible K-ion storage. The first cycle discharge/charge capacities of the AGC anode are 650 and 401 mA h g−1, respectively, greatly exceeding the theoretical capacity of graphite, which is 272 mA h g−1 and corresponding to an initial coulombic efficiency (ICE) of 61.7%. The SEI layer creation on the AGC surface can be linked to the low Coulombic efficiency, which can also be seen in the CV result.65 The coulombic efficiency of the AGC electrode increases slowly in the subsequent cycles and remains lower than 90% until the 10th cycle (Fig. 6c) due to the hierarchical porous structure and large specific surface area. The low initial efficiency and slow capacity stabilization requiring a longer time for the SEI layer to form fully is a frequent phenomenon in porous carbon materials. As a result, at 100 mA g−1, a steady-state reversible capacity of 220 mA h g−1 (100 cycles) and the coulombic efficiency of 99% was attained (Fig. 6c) after 20 cycles, which is higher than that of previous other biomass-derived carbons (Table 3).42,44,67–72 These phenomena prove that the existence of a large number of micro and mesopores in AGC is responsible for the high specific capacity reported, as they operate as a potassium reservoir, favoring the transit path and increasing K ion diffusion and electrolyte penetration.
To further demonstrate the storage mechanism of K ions in AGC, the CV curves were recorded at various scan rates ranging from 0.1 to 1 mV s−1 and the b value was calculated (Fig. S2, ESI†). The power-law formula I = aνb describes the peak current I and scan rates (v), where a and b are constants. Plotting the current and sweep rate in the logarithm log
i = b
log
ν + log
a yields the b-value. The current is contributed by capacitive behavior (surface-induced K storage) when the b-value is 1, and the current is dominated by the ion-diffusion regulated contribution when the b-value is 0.5 (intercalating K storage).73 The b-value might range from 0.5 to 1, indicating the presence of mixed processes in the charge storage process. The b-value calculated for AGC (0.73) from the CV curves (slope of log
i vs. log
v) and shown in Fig. S2b (ESI†) indicates that the capacitive process is dominated and the diffusion process also exists in the charge storage process. The cathodic peak suggests that AGC exhibits a diffusion-controlled charge storage mechanism. To understand quantitatively, the percentage contributions of the diffusion-controlled process and capacitive process of the AGC electrode were determined using Trasatti method analysis and the relevant graphs are shown in Fig. S3a–c (ESI†), where a full explanation of the Trasatti analysis method is also provided. Fig. S3c (ESI†) shows a bar plot of the AGC electrode material's specific capacity with diffusion-controlled and capacitance contributions. AGC has an 81% diffusion-controlled and 19% capacitance-controlled contribution due to the K ions stored in the carbon inter-layer spacing and the shortened ion diffusion path. To have a better understanding of the capacity decay and diffusion kinetics change of the AGC under the current density of 100 mA g−1, EIS is conducted with a frequency range from 10 kHz to 100 mHz. From the EIS (Fig. 6d), there is not much change of electrolyte resistance before and after discharge/charge. However, the decrease in the Warburg type impedance slope indicates that the electron transfer inside the battery becomes more difficult with the accumulation of the SEI layer on the surface during cycling. The fitted equivalent circuit was in Fig. 6d. From the circuit, the electron transfer resistance (Rct) change was very much in the high-frequency region, and before and after the 100 cycles, it was 440 to 2500 Ω (Table 2). Furthermore, such a large rise could be attributed to a rapid loss of electrochemical active sites, or it could be owing to a massive volume change expansion and irreversible potassium accumulation.74,75
Table 2 Variation of impedance of the AGC anode under the influence of 100 mA g−1 current density
S. no. |
Before cycling |
After 100 cycles |
R
s
|
16.9 |
10.4 |
R
ct
|
440.0 |
2500.0 |
Table 3 Performance of the biomass-derived carbon material as KIB anodes
Anode materials |
Electrolyte |
Current density |
Reversible capacity (mA h g−1) |
Ref. |
Potato |
KFSI in DME |
500 mA g−1 |
207 |
66
|
Corn husk |
0.8 M KPF6 in EC:DEC |
2 A g−1 |
167 |
42
|
Loofah-derive carbon |
1 M KPF6 in EC:DEC |
100 mA g−1 |
100 (400th cycle) |
44
|
Walnut septum |
0.8 M KPF6 in EC:DEC |
1 A g−1 |
120 (1000th cycle) |
67
|
Bamboo charcoal |
KPF6 in EC:DEC |
200 mA g−1 |
203 (300th cycle) |
68
|
Maple leaves |
1.0 M KClO4 in EC:DEC |
500 mA g−1 |
181 |
69
|
Sugar cane |
1 M KPF6 in EC:DEC |
2 A g−1 |
182 |
70
|
Cyanobacteria |
0.8 M KPF6 in EC:DEC |
500 mA g−1 |
180 |
71
|
Ginger derived carbon |
0.8 M KPF6 in EC:DEC |
500 mA g−1 |
286 |
This work |
1000 mA g−1 |
175 |
The rate performance of AGC is evaluated in Fig. 7a. It also exhibits the best rate performance, delivering reversible capacities of 576, 431, 365, 340, 286, 180, and 240 mA h g−1 at 20, 40, 80, 100, 500, 1000, and 100 mA g−1, respectively. When compared to alternative biomass-derived carbons, the AGC anode exhibits better reversible capacities at higher current densities (500 and 1000 mA g−1).67–72 More interestingly, after subjecting the cell to varied high current densities, a reversible capacity of 240 mA h g−1 was attained, especially when switched back to 100 mA g−1. Fig. 7b shows that AGC has outstanding long-term cycling stability, with a reversible specific capacity of 175 mA h g−1 after 1000 cycles at a current density of 1000 mA g−1. To the best of our knowledge, the AGC anode has a higher reversible capacity and rate performance than any other amorphous carbon generated from various biomass sources. As a result, AGC qualifies as a low-cost, high-capacity, high-rate anode material for KIBs, opening new avenues for developing economically feasible and environmentally friendly KIB electrode materials.
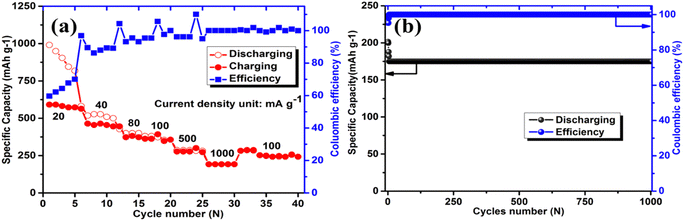 |
| Fig. 7 (a) Rate capability at current densities from 20 to 1000 mA g−1 and (b) long-term cycling performance at 1000 mA g−1 of AGC. | |
3.3. Dual carbon potassium-ion capacitor (KIC)
To investigate the electrochemical properties further, we constructed an asymmetric dual carbon potassium ion capacitor (KIC) using potassiation AGC as the anode, activated candle soot carbon (ACS) as the cathode, and KPF6 containing organic electrolyte (Fig. 8a). In the charging process, when PF6− ions are absorbed in the ACS and K+ are intercalated in AGC, the discharge process is completely reversible. The asymmetric KIC has two types of electrode material in the positive and negative electrodes, which work in various electrochemical potential windows and have different specific capacities. Before fabricating the full cell, the half-cell was fabricated with ACS and the CV, cycling study and charge discharge profiles were carried out, and presented in Fig. S4 (ESI†). At a current density of 100 mA g−1, the specific capacity of AGC and ACS in their designated working potential windows is around 300 mA h g−1 and 75 mA h g−1 (Fig. S4b, ESI†), respectively. As a result, the optimal mass ratio of the two electrodes should be 3.8 to 4 and the voltage window 0.01 to 3.5 V (Fig. S5, ESI†). The charge/discharge performance of the dual carbon KIC was investigated at various current densities (Fig. 8b), yielding the revisable capacities of 164, 136, 121, 94, 84, 78, 51 and 42 mA h g−1 at 50, 100, 200, 250, 300, 400 and 500 mA g−1 current densities, respectively. Moreover, the revisable capacity recovered to 147 mA h g−1 at 100 mA g−1 current density even after high current density was applied to the ACS//AGC. The decrease in the device capacity at high current densities due to the accessibility of the electrochemical active sites being lower. Fig. 8c displays the GCD curves of the ACS//AGC device in the shape of quasilinear, indicating that the carbon materials combined capacitor-type and battery-type charge storage behavior.76 Furthermore, as shown in Fig. S3 (ESI†), the KIC shows a reversible capacity of 120 mA h g−1 over 100 cycles at 50 mA g−1. Notably, a rise in the capacitance from the 20th cycle onwards is due to the oxygen functional groups and activation of the electrode material. The half-cell and full-cell show outstanding results due to the rapid ion transport, which is provided by a high specific surface area and rich porous architectures of nanocarbon derived from AGC through a potential channel pathway.
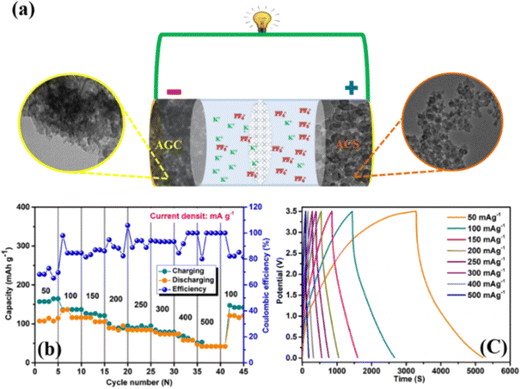 |
| Fig. 8 Electrochemical performance of the AGC//ACS K-ion capacitor: (a) schematic illustration of the fabrication of the KIC full cell, (b) rate capability at current densities from 50 to 500 mA g−1, and (c) GCD curves recorded at different current densities. | |
Fig. 9 Ragone plot contrasts our AGC//ACS KIC device with those of other hybrid capacitors. Our created device has a high energy density and power density since it uses carbons made from activated candle soot and activated ginger (calculated from eqn (1) and (2)). Comparing our designed KIC to other documented devices as AS-HC//AS-AC, N-CNTs//LCG, NGC//K2Ti6O13, K-V2C, and MHC//ACF, we find that they exhibit higher energy and power densities.76–80 These remarkable results are explained by the quick ion transport provided by the high specific surface area of carbons produced from activated ginger and activated candle soot via a possible channel mechanism.
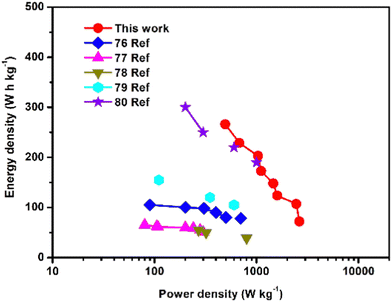 |
| Fig. 9 Ragone plot with specific energy and power density compared with previous KIC devices. | |
4. Conclusions
In conclusion, porous carbon material was successfully synthesized using a simple activation method, with low-cost ginger as the precursor and KOH as the activating agent. Activated carbon as derived from ginger (AGC) with an interlayer spacing of 0.38 nm and interconnecting micro and mesopores with a high BET surface area of 2717 m2 g−1 can alter the electrical structure, increase conductivity, and improve wettability, resulting in improved electrochemical performance. When the obtained AGC is applied as the anode in KIBs, it exhibits superior electrochemical performance under both conventional and high-rate. At 100 and 1000 mA g−1, it produces a steady-state reversible capacity of 220 and 175 mA h g−1. The combination of micro and mesoporous carbon having interconnected graphene sheets and a high surface area may explain the AGC anodes improved electrochemical performance over other biomass-derived carbons. To the best of our knowledge, this is the first report that shows the anode behavior of ginger-derived carbon material for use in potassium-ion batteries. We also demonstrated the use of AGC along with ACS for the dual carbon K-ion capacitor. The low-cost, simple, and controllable synthesis technique should result in large-scale industrial production of AGC to address the demand for long-term energy storage.
Conflicts of interest
There are no conflicts to declare.
References
- M. Armand and J.-M. Tarascon, Nature, 2008, 451, 652–657 CrossRef CAS PubMed.
- C. Wei, H. Fei, Y. An, Y. Zhang and J. Feng, Electrochim. Acta, 2019, 309, 362–370 CrossRef CAS.
- Y. Wei, Y. Yan, Y. Zou, M. Shi, Q. Deng, N. Zhao, J. Wang, C. You, R. Yang and Y. Xu, Electrochim. Acta, 2019, 310, 45–57 CrossRef CAS.
- H. Pan, Y.-S. Hu and L. Chen, Energy Environ. Sci., 2013, 6, 2338–2360 RSC.
- W. Luo, F. Shen, C. Bommier, H. Zhu, X. Ji and L. Hu, Acc. Chem. Res., 2016, 49, 231–240 CrossRef CAS PubMed.
- L. Meng, C. Hou, J. Hou, H. Xie, Z. Yue, H. Lu, S. Yang and B. Gong, Eng. Sci., 2022, 20, 134–143 CAS.
- M. Culebras, G. A. Collins, A. Beaucamp, H. Geaney and M. N. Collins, Eng. Sci., 2022, 17, 195–203 CAS.
- D. Wang, R. Wang, K. Huang, M. Lei and H. Tang, Adv. Compos. Hybrid Mater., 2022, 5, 1362–1375 CrossRef CAS.
- Y. Zhang, L. Liu, L. Zhao, C. Hou, M. Huang, H. Algadi, D. Li, Q. Xia, J. Wang and Z. Zhou, Adv. Compos. Hybrid Mater., 2022, 5, 2601–2610 CrossRef CAS.
- Q. Wang, B. Zhao, S. Zhang, X. Gao and C. Deng, J. Mater. Chem. A, 2015, 3, 7732–7740 RSC.
- W. Luo, J. Wan, B. Ozdemir, W. Bao, Y. Chen, J. Dai, H. Lin, Y. Xu, F. Gu and V. Barone, Nano Lett., 2015, 15, 7671–7677 CrossRef CAS PubMed.
- J. C. Pramudita, D. Sehrawat, D. Goonetilleke and N. Sharma, Adv. Energy Mater., 2017, 7, 1602911 CrossRef.
- Y.-H. Zhu, Q. Zhang, X. Yang, E.-Y. Zhao, T. Sun, X.-B. Zhang, S. Wang, X.-Q. Yu, J.-M. Yan and Q. Jiang, Chem, 2019, 5, 168–179 CAS.
- I. Sultana, T. Ramireddy, M. M. Rahman, Y. Chen and A. M. Glushenkov, Chem. Commun., 2016, 52, 9279–9282 RSC.
- Y. An, Y. Tian, L. Ci, S. Xiong, J. Feng and Y. Qian, ACS Nano, 2018, 12, 12932–12940 CrossRef CAS PubMed.
- I. Sultana, M. M. Rahman, Y. Chen and A. M. Glushenkov, Adv. Funct. Mater., 2018, 28, 1703857 CrossRef.
- Z. Jian, Z. Xing, C. Bommier, Z. Li and X. Ji, Adv. Energy Mater., 2016, 6, 1501874 CrossRef.
- K. Share, A. P. Cohn, R. Carter, B. Rogers and C. L. Pint, ACS Nano, 2016, 10, 9738–9744 CrossRef CAS PubMed.
- Z. Xing, Y. Qi, Z. Jian and X. Ji, ACS Appl. Mater. Interfaces, 2017, 9, 4343–4351 CrossRef CAS PubMed.
- S. Komaba, T. Hasegawa, M. Dahbi and K. Kubota, Electrochem. Commun., 2015, 60, 172–175 CrossRef CAS.
- Z. Jian, W. Luo and X. Ji, J. Am. Chem. Soc., 2015, 137, 11566–11569 CrossRef CAS PubMed.
- C. Chen, Z. Wang, B. Zhang, L. Miao, J. Cai, L. Peng, Y. Huang, J. Jiang, Y. Huang and L. Zhang, Energy Storage Mater., 2017, 8, 161–168 CrossRef.
- R. Hao, H. Lan, C. Kuang, H. Wang and L. Guo, Carbon, 2018, 128, 224–230 CrossRef CAS.
- D. Li, X. Ren, Q. Ai, Q. Sun, L. Zhu, Y. Liu, Z. Liang, R. Peng, P. Si and J. Lou, Adv. Energy Mater., 2018, 8, 1802386 CrossRef.
- X. Wang, K. Han, D. Qin, Q. Li, C. Wang, C. Niu and L. Mai, Nanoscale, 2017, 9, 18216–18222 RSC.
- Z. Jian, S. Hwang, Z. Li, A. S. Hernandez, X. Wang, Z. Xing, D. Su and X. Ji, Adv. Funct. Mater., 2017, 27, 1700324 CrossRef.
- G. Suo, J. Zhang, R. Li, Z. Ma, Y. Cheng and S. M. Ahmed, Mater. Today Chem., 2023, 27, 101300 CrossRef CAS.
- D. Li, J. Zhang, S. M. Ahmed, G. Suo, W. A. Wang, L. Feng, X. Hou, Y. Yang, X. Ye and L. Zhang, J. Colloid Interface Sci., 2020, 574, 174–181 CrossRef CAS PubMed.
- G. Suo, S. M. Ahmed, Y. Cheng, J. Zhang, Z. Li, X. Hou, Y. Yang, X. Ye, L. Feng and L. Zhang, J. Colloid Interface Sci., 2022, 608, 275–283 CrossRef CAS PubMed.
- R. Hao, Y. Yang, H. Wang, B. Jia, G. Ma, D. Yu, L. Guo and S. Yang, Nano Energy, 2018, 45, 220–228 CrossRef CAS.
- D. Li, Y. Sun, S. Chen, J. Yao, Y. Zhang, Y. Xia and D. Yang, ACS Appl. Mater. Interfaces, 2018, 10, 17175–17182 CrossRef CAS PubMed.
- Y. Li, R. A. Adams, A. Arora, V. G. Pol, A. M. Levine, R. J. Lee, K. Akato, A. K. Naskar and M. P. Paranthaman, J. Electrochem. Soc., 2017, 164, A1234 CrossRef CAS.
- X. Zhou, P. Wang, Y. Zhang, L. Wang, L. Zhang, L. Zhang, L. Xu and L. Liu, J. Mater. Chem. A, 2017, 5, 12958–12968 RSC.
- L. Jiang, L. Sheng and Z. Fan, Sci. China Mater., 2017, 61, 133–158 CrossRef.
- K. Chaitra, R. Vinny, P. Sivaraman, N. Reddy, C. Hu, K. Venkatesh, C. Vivek, N. Nagaraju and N. Kathyayini, J. Energy Chem., 2017, 26, 56–62 CrossRef.
- N. Sinan and E. Unur, J. Energy Chem., 2017, 26, 783–789 CrossRef.
- G. Yuan, T. Wan, A. BaQais, Y. Mu, D. Cui, M. A. Amin, X. Li, B. B. Xu, X. Zhu and H. Algadi, Carbon, 2023, 212, 118101 CrossRef CAS.
- J. Ruan, Z. Chang, H. Rong, T. S. Alomar, D. Zhu, N. AlMasoud, Y. Liao, R. Zhao, X. Zhao and Y. Li, Carbon, 2023, 118208 CrossRef CAS.
- A. Vijeata, G. R. Chaudhary, A. Umar and S. Chaudhary, Eng. Sci., 2021, 15, 197–209 Search PubMed.
- M. Kumari, G. R. Chaudhary, S. Chaudhary and A. Umar, Eng. Sci., 2021, 17, 101–112 Search PubMed.
- S. M. Ahmed, G. Suo, W. A. Wang, K. Xi and S. B. Iqbal, J. Energy Chem., 2021, 62, 307–337 CrossRef CAS.
- Q. Wang, C. Gao, W. Zhang, S. Luo, M. Zhou, Y. Liu, R. Liu, Y. Zhang, Z. Wang and A. Hao, Electrochim. Acta, 2019, 324, 134902 CrossRef CAS.
- E. M. Lotfabad, J. Ding, K. Cui, A. Kohandehghan, W. P. Kalisvaart, M. Hazelton and D. Mitlin, ACS Nano, 2014, 8, 7115–7129 CrossRef CAS PubMed.
- Z. Wu, L. Wang, J. Huang, J. Zou, S. Chen, H. Cheng, C. Jiang, P. Gao and X. Niu, Electrochim. Acta, 2019, 306, 446–453 CrossRef CAS.
- G. Qi, Y. Liu, L. Chen, P. Xie, D. Pan, Z. Shi, B. Quan, Y. Zhong, C. Liu and R. Fan, Adv. Compos. Hybrid Mater., 2021, 4, 1226–1238 CrossRef CAS.
- M. Liu, H. Wu, Y. Wu, P. Xie, R. A. Pashameah, H. M. Abo-Dief, S. M. El-Bahy, Y. Wei, G. Li and W. Li, Adv. Compos. Hybrid Mater., 2022, 5, 2021–2030 CrossRef CAS.
- G. Fan, Z. Wang, H. Ren, Y. Liu and R. Fan, Scr. Mater., 2021, 190, 1–6 CrossRef CAS.
- G. Fan, Z. Wang, K. Sun, Y. Liu and R. Fan, J. Mater. Sci. Technol., 2021, 61, 125–131 CrossRef CAS.
- P. Xie, Z. Zhang, K. Liu, L. Qian, F. Dang, Y. Liu, R. Fan, X. Wang and S. Dou, Carbon, 2017, 125, 1–8 CrossRef CAS.
- A. K. Chourasia, M. Shavez, K. M. Naik, C. Bongu and C. S. Sharma, ACS Appl. Energy Mater., 2023, 6, 378–386 CrossRef CAS.
- J. Yang, Z. Ju, Y. Jiang, Z. Xing, B. Xi, J. Feng and S. Xiong, Adv. Mater., 2018, 30, 1700104 CrossRef PubMed.
- H. Fei, Y. Liu, Y. An, X. Xu, J. Zhang, B. Xi, S. Xiong and J. Feng, J. Power Sources, 2019, 433, 226697 CrossRef CAS.
- D. Yoon, D. H. Kim, K. Y. Chung, W. Chang, S. M. Kim and J. Kim, Carbon, 2016, 98, 213–220 CrossRef CAS.
- G. Dong, H. Wang, W. Liu, J. Shi, S. Sun, D. Li, H. Zhang, Y. Yang and Y. Cui, ACS Appl. Energy Mater., 2018, 1, 5636–5645 CAS.
- N. Wang, Y. Wang, X. Xu, T. Liao, Y. Du, Z. Bai and S. Dou, ACS Appl. Mater. Interfaces, 2018, 10, 9353–9361 CrossRef CAS PubMed.
- M. Kruk and M. Jaroniec, Chem. Mater., 2001, 13, 3169–3183 CrossRef CAS.
- J. Zhang, Z. Lyu, F. Zhang, L. Wang, P. Xiao, K. Yuan, M. Lai and W. Chen, J. Mater. Chem. A, 2016, 4, 6350–6356 RSC.
- L. Qie, W. Chen, H. Xu, X. Xiong, Y. Jiang, F. Zou, X. Hu, Y. Xin, Z. Zhang and Y. Huang, Energy Environ. Sci., 2013, 6, 2497–2504 RSC.
- Q. Lu, B. Lu, M. Chen, X. Wang, T. Xing, M. Liu and X. Wang, J. Power Sources, 2018, 398, 128–136 CrossRef CAS.
- H. Li, Z. Sun, L. Zhang, Y. Tian, G. Cui and S. Yan, Colloids Surf., A, 2016, 489, 191–199 CrossRef CAS.
- Y. Xu, C. Zhang, M. Zhou, Q. Fu, C. Zhao, M. Wu and Y. Lei, Nat. Commun., 2018, 9, 1720 CrossRef PubMed.
- E. Zhang, X. Jia, B. Wang, J. Wang, X. Yu and B. Lu, Adv. Sci., 2020, 7, 2000470 CrossRef CAS PubMed.
- J. H. Choi, G. D. Park and Y. C. Kang, Chem. Eng. J., 2021, 408, 127278 CrossRef CAS.
- J. Ruan, X. Wu, Y. Wang, S. Zheng, D. Sun, Y. Song and M. Chen, J. Mater. Chem. A, 2019, 7, 19305–19315 RSC.
- Z. Ju, S. Zhang, Z. Xing, Q. Zhuang, Y. Qiang and Y. Qian, ACS Appl. Mater. Interfaces, 2016, 8, 20682–20690 CrossRef CAS PubMed.
- J. Ruan, F. Mo, Z. Chen, M. Liu, S. Zheng, R. Wu, F. Fang, Y. Song and D. Sun, Adv. Energy Mater., 2020, 10, 1904045 CrossRef CAS.
- W. Cao, E. Zhang, J. Wang, Z. Liu, J. Ge, X. Yu, H. Yang and B. Lu, Electrochim. Acta, 2019, 293, 364–370 CrossRef CAS.
- C. Gao, Q. Wang, S. Luo, Z. Wang, Y. Zhang, Y. Liu, A. Hao and R. Guo, J. Power Sources, 2019, 415, 165–171 CrossRef CAS.
- S. Tian, D. Guan, J. Lu, Y. Zhang, T. Liu, X. Zhao, C. Yang and J. Nan, J. Power Sources, 2020, 448, 227572 CrossRef CAS.
- M. Liu, D. Jing, Y. Shi and Q. Zhuang, J. Mater. Sci.: Mater. Electron., 2019, 30, 8911–8919 CrossRef CAS.
- Z. Zhang, B. Jia, L. Liu, Y. Zhao, H. Wu, M. Qin, K. Han, W. A. Wang, K. Xi and L. Zhang, ACS Nano, 2019, 13, 11363–11371 CrossRef CAS PubMed.
- Y. Sun, H. Xiao, H. Li, Y. He, Y. Zhang, Y. Hu, Z. Ju, Q. Zhuang and Y. Cui, Chem. – Eur. J., 2019, 25, 7359–7365 CrossRef CAS PubMed.
- H. Lindström, S. Södergren, A. Solbrand, H. Rensmo, J. Hjelm, A. Hagfeldt and S.-E. Lindquist, J. Phys. Chem. B, 1997, 101, 7717–7722 CrossRef.
- Y. Lei, L. Qin, R. Liu, K. C. Lau, Y. Wu, D. Zhai, B. Li and F. Kang, ACS Appl. Energy Mater., 2018, 1, 1828–1833 CrossRef CAS.
- Z. Wu, J. Zou, S. Shabanian, K. Golovin and J. Liu, Chem. Eng. J., 2022, 427, 130972 CrossRef CAS.
- H. D. Pham, K. Mahale, T. M. L. Hoang, S. G. Mundree, P. Gomez-Romero and D. P. Dubal, ACS Appl. Mater. Interfaces, 2020, 12, 48518–48525 CrossRef CAS PubMed.
- M. Moussa, S. A. Al-Bataineh, D. Losic and D. P. Dubal, Appl. Mater. Today, 2019, 16, 425 CrossRef.
- S. Dong, Z. Li, Z. Xing, X. Wu, X. Ji and X. Zhang, ACS Appl. Mater. Interfaces, 2018, 10, 15542 CrossRef CAS PubMed.
- F. Ming, H. Liang, W. Zhang, J. Ming, Y. Lei, A.-H. Emwas and H. N. Alshareef, Nano Energy, 2019, 62, 853 CrossRef CAS.
- H. D. Pham, J. F. Fernando, M. Horn, J. MacLeod, N. Motta, W. O. Doherty, A. Payne, A. K. Nanjundan, D. Golberg and D. Dubal, Electrochim. Acta, 2021, 389, 138717 CrossRef CAS.
|
This journal is © The Royal Society of Chemistry 2024 |
Click here to see how this site uses Cookies. View our privacy policy here.