DOI:
10.1039/D4TB01164C
(Paper)
J. Mater. Chem. B, 2025,
13, 3437-3447
Polyurethane packed graphene-coated spider silk by dip-casting for a highly stretchable strain sensor
Received
29th May 2024
, Accepted 8th December 2024
First published on 17th December 2024
Abstract
In recent years, naturally occurring materials have gained tremendous attention for their potential in the fabrication of advanced wearable electronic devices. Among these materials, spider silk is well-known for its outstanding mechanical strength and physical properties. Leveraging these attributes, a highly stretchable strain sensor was developed in this work utilizing polyurethane packed graphene-coated spider silk fabricated through a simple dip-casting method. The proposed sensor demonstrated remarkable mechanical strength, excellent sensitivity to strain and impressive recovery properties, attributed to the self-healing abilities of the polyurethane packaging. Additionally, polyurethane served as a protective layer, safeguarding the sensor from external environmental parameters and improving the lifetime of the device. The fabricated devices retained their performance parameters and other properties at up to 40% stretchability. FE-SEM and EDS elemental mapping were used to confirm the morphological properties and the homogenous coating of graphene on the spider silk fibers. The sensors were then attached to different parts of the human body to monitor pulse-rate, joint angles and posture, demonstrating outstanding results. This work paves the way for the design and fabrication of future wearable sensors using naturally occurring materials for advanced electronic applications.
1. Introduction
In recent years, flexible strain sensors have garnered tremendous attention for various applications, such as human motion detection,1–3 healthcare,4,5 structural damage detection,6–8 structural characterization,9,10 and exhaustion studies of materials.11,12 For these applications, strain sensors with excellent sensitivity, stability, and repeatability are required. However, the widespread applications of such devices is limited by several challenges,13 such as low stability, sensitivity, and size constraints. In human health monitoring, signals generated by pulse, body temperature fluctuations, breathing, and minor muscle movements are typically very weak, requiring highly sensitive and stable sensors14,15 for reliable detection of these signals. To address the mentioned challenges and satisfy the output requirements, different research groups are working on selection and synthesis of various types of active materials and substrates. One widely used category of materials being explored is nanomaterials, which include nanotubes,5,16–18 nanowires,19–21 nano flakes22,23 and nano particles (NPs)24–26 of various elements and compounds. Furthermore, among nanomaterials, nanoparticles (NPs) have received tremendous attention due to their high sensitivity and minimal deformation of the substrate. The working mechanism of NP-based strain sensors involves a change in the spacing between the NPs when an external strain is applied to the substrate, resulting in a corresponding change in electrical resistance.25 However, after the substrate reaches its maximum stretch, irreversible deformation and breakage of the NPs often occur, which can negatively impact the sensor's stability, repeatability, and sensitivity.27 Graphene flakes have emerged as a promising alternative to NPs in flexible and wearable devices, owing to their excellent electrical and mechanical properties.23,28 Additionally, the flake morphology of graphene provides a larger overlapping area between adjacent flakes, which increases the stretching capability while maintaining a high sensitivity comparable to that of NPs. The concentration of graphene plays a crucial role in determining the properties of the sensors.29,30 Higher graphene concentrations generally enhance the sensor's sensitivity due to the increased surface area and more active sites available for interaction with target analytes, resulting in better signal transmission and enhanced detection accuracy. Optimal graphene concentrations can reduce response times, as more conductive pathways facilitate quicker charge transfer and signal processing. On the other hand, the progressively increasing demand for flexible and printed electronics increases the chance for electronic waste and environmental pollution. This is a huge problem, requiring attention and best innovative solutions. Several toxic materials and non-biodegradable plastic substrates are commonly being used in conventional electronics, which can be replaced by some natural and eco-friendly biodegradable materials to reduce the quantity of toxic components produced by the electronic devices and sensors.31 Among such natural and biodegradable materials, spider silk is one of the most promising candidates to be used as a substrate, owing to its flexible nature,32,33 outstanding mechanical properties,34,35 and bio-compatibility.36 These properties make the spider silk a strategically promising candidate to be used as a substrate in flexible and printed electronic devices and sensors. Previous sensors were prepared with hard materials and flexible materials. There were breaks during bending and stretching, and also limiting issues. Polyurethane packed graphene-coated spider silk sensors do not break due to the self-healing property of polyurethane and spider elasticity.37
Herein, this paper proposes the fabrication of a highly stretchable strain sensor based on polyurethane packed graphene-coated spider silk using a simple dip-casting method. The mechanical property of the polyurethane-packed graphene-coated spider silk typically includes enhanced tensile strength and flexibility. The spider used for this sensor is 100 times stronger than steel and environmentally friendly. Graphene flakes are used for their conductivity, and polyurethane packing is used for its self-healing, environmental protection and elastic properties. The device offers advantages like high stretchability, self-healing properties, and the use of natural spider silk, which is biocompatible and environmentally friendly. Compared to other strain sensors,38–40 the key strengths are its environmental sustainability and self-healing capabilities. The materials and methods part is explained in Section 2; the results are covered in Section 3, while discussion on results has been presented in Section 4.
2. Methods
2.1 Materials preparations and spider silk collection
The spider silk was collected from the natural habitat of the spider species named Humped Golden Orb-weaver (Nephila plumipes), as presented in Fig. 1a. (All experiments were performed in compliance with the relevant guidelines and approved by the Ethical Committee International Islamic University, Islamabad, Pakistan). Graphite powder was purchased from Sigma Aldrich, as shown in Fig. 1c, and 0.05 g of the powder was dispersed in 10 ml NMP solvent. The solution was sonicated in a bath for 30 min at room temperature to exfoliate the graphite chunks. The large un-exfoliated graphite flakes were removed by vacuum filtration after bath sonication. The resulting solution was further purified through centrifugation for 60 min at 3000 rpm, and the supernatant was separated from the sediment afterwards. The viscosity of the ink was measured to be 26.1 mPa using the Viscometer VM-10A system, and the surface tension of the ink was measured to be around 67–71 mN m−1 using surface-electro-optics (SEO)'s contact angle analyzer. The final graphene flakes ink is presented in Fig. 1d, and the polyurethane (PU) used was UV curable.
 |
| Fig. 1 Step-by-step process of the sensor fabrication, showing (a) the spider silk, (b) formation of threads from the spider silk, (c) graphene powder and NMP solvent, (d) graphene ink, (e) coating of the spider silk thread with graphene flakes, (f) graphene-coated spider silk, (g) SEM image of the graphene-coated spider silk, (h) PU-coated sensor, (i) final device mounted on the finger. | |
2.2 Device fabrication
The sensor was fabricated by first carefully weaving together the single fibers of spider silk by hand to form a strong thread, as presented in Fig. 1b. The threads were then dipped in graphene ink to form a coating, as presented in Fig. 1e. The threads were dipped in graphene ink for 2 minutes for proper and uniform distribution of graphene flakes throughout the thread and between the fibers, as shown in Fig. 1f. The graphene-coated thread was then encapsulated with UV curable and self-healing polyurethane resin, as shown in Fig. 1h, using dip coating to isolate it from the external environment, as well as to help in the recovery process after stretching, owing to its elastic and self-healing nature. Fig. 1i shows the sensor mounted with a tape and conforming to a human finger to measure its bending angle. Fig. 1g is the SEM image of the graphene-coated spider silk.
2.3 Device characterizations
The sensor surface and cross-sectional morphology were analyzed using FE-SEM Jeol JSM-7600F. Agilent B1500A Semiconductor Device Analyzer was used for the electrical characterizations of the fabricated sensor. I–V curves were plotted for the sensor by sweeping the applied voltage from 0 V to 5 V. Elemental and EDS mapping analysis was performed by using field emission scanning electron microscope (TESCAN). Resistance vs. bending angle and resistance vs. percentage stretching curves were obtained using an in-house developed setup that provides a fixed 5 V to the sensor connected in a voltage divider configuration, and calculates the resistance of the sensor at various bending angles and stretch percentages through the voltage drop across the sensor. The stability of the device was verified by stretching and relaxing the device for hundreds of cycles continuously for 10 minutes.
3. Results
A field emission scanning electron microscope (FE-SEM) with energy dispersive spectroscopy (EDS) was used to analyze the surface morphology and elemental mapping of the fabricated sensors. Fig. 2 shows the results of EDS with elemental mapping and the spectra of the sensor materials. The combined mapping presented in Fig. 2a shows the presence of different materials, including carbon, oxygen, chlorine, sodium, potassium, sulphur, magnesium, and calcium.
 |
| Fig. 2 EDS maps of the sensor, showing (a) the combined map of C, O, Cl, Na, K, S, Mg and Ca, (b) carbon, (c) oxygen, (d) chlorine, (e) sodium, (f) potassium, (g) sulphur, (h) magnesium, (i) calcium, (j) and the percentage spectrum of each element. | |
Fig. 2b shows the uniformly distributed graphene/carbon over the spider silk substrate, while Fig. 2c–i show the distribution of O, Cl, Na, K, S, Mg and Ca, respectively, in the sensor's active structure. The EDS spectrum plotted in Fig. 2j shows the percentage presence of each element in the sensor. Carbon and oxygen are most abundant due to the organic nature of the materials and the coating of PU and graphene, while there are traces of other elements that indicate the presence of various proteins in the spider silk. Fig. 3a shows the FE-SEM image of a single thread of spider silk without graphene coating, while Fig. 3b shows the FE-SEM image of a bundle of spider silk threads without the graphene coating. Fig. 3c presents the SEM image of a PU/graphene-coated bundle of threads showing a uniform coating without any cracks, pores, or missed portions. The graphene was coated first, while the PU was coated next as the encapsulation and binding agent.
 |
| Fig. 3 FE-SEM images of the sensors, showing (a) single spider silk thread, (b) a bundle of threads, (c) PU/graphene coated threads, (d) a layer of graphene flakes over the threads, (e) cross-sectional image of the sensor, and (f) inner part of the sensor showing the presence of graphene flakes. | |
Fig. 3d shows the SEM image of the graphene flakes and PU layers over the threads of spider silk, and the position of a self-induced defect to observe the graphene flakes present at the inner portion of the fibers, as presented in Fig. 3f. The cross-sectional SEM image of the sensor is presented in Fig. 3e. Overall, the FE-SEM analysis confirms that the sensing devices were fabricated successfully without any defects or physical abnormalities.
Electrical versus mechanical characteristics of the fabricated sensors were investigated to evaluate the performance of strain sensing, and the results are presented in Fig. 4. The I–V characteristics of the sensors presented in Fig. 4b show that the device has a linear output showing Ohmic behavior, making it ideal for resistive sensing. The resistance of the device changes with a change in the percentage stretching (applied strain) and the bending angle. The devices were stretched up to 40% of their initial length in steps of 5%, while the bending test was performed in steps of 15° angular steps, as shown in Fig. 4e. The repeatability of the devices was also tested by bending and stretching (20%) the devices (45°) for up to 100 cycles each, and the results of the bending and stretching cycles are presented in Fig. 4a and Fig. 4c, respectively. The recovery of devices after the maximum allowed stretching and bending was also tested to ensure that there is no permanent hysteresis in the output due to any physical damage to the device. The results of bending from 0° to 90° and back to 0° are presented in Fig. 4e, while the results of stretching from 5% to 30% and back to 5% are presented in Fig. 4f. The conductivity of the polyurethane-packed, graphene-coated spider silk can be tuned by adjusting the concentration of graphene during preparation. Increasing the graphene content enhances the conductivity and electrical performance. Careful control of the coating thickness and uniformity also ensures optimal conductive properties. To ensure the cycle stability, more than 100 cycles are performed as shown in Fig. 4g, which confirm the stability of the sensor. Fig. 4h shows the zoomed image of the cycle stability to show its more clear and stable cycles. The recovery and response times of any sensor is an important parameter. The sensor exhibits a great response time of 0.69 s and recovery time of 0.73 s, as shown in Fig. 4i.
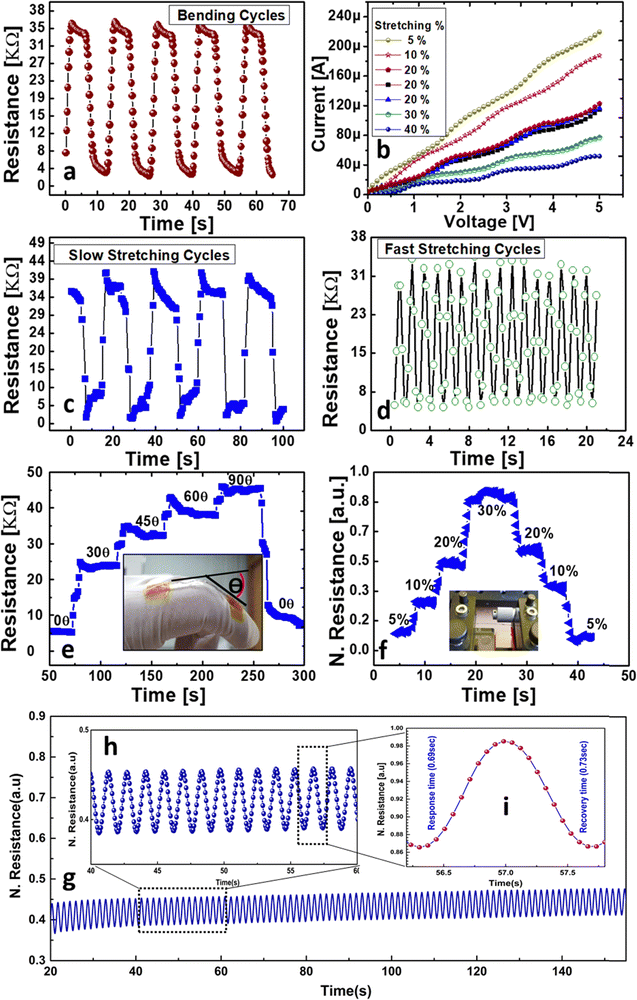 |
| Fig. 4 Electrical characteristics of the sensor, showing (a) the performance under bending cycles, (b) I–V curves at different stretching percentages, (c) slow stretching cycles, (d) fast stretching cycles, (e) bending at 90°, (f) stretching cycle, (g) cycle stability, (h) magnified image of the cycle stability, and (i) recovery and response times. | |
4. Discussion
4.1 Sensing mechanism
To understand the underlying working principle and sensing mechanism of the proposed devices for stretchability and electromechanical responses under a tensile load, structural and morphological changes in the active region of the device were observed under different levels of strain, as presented in Fig. 5.
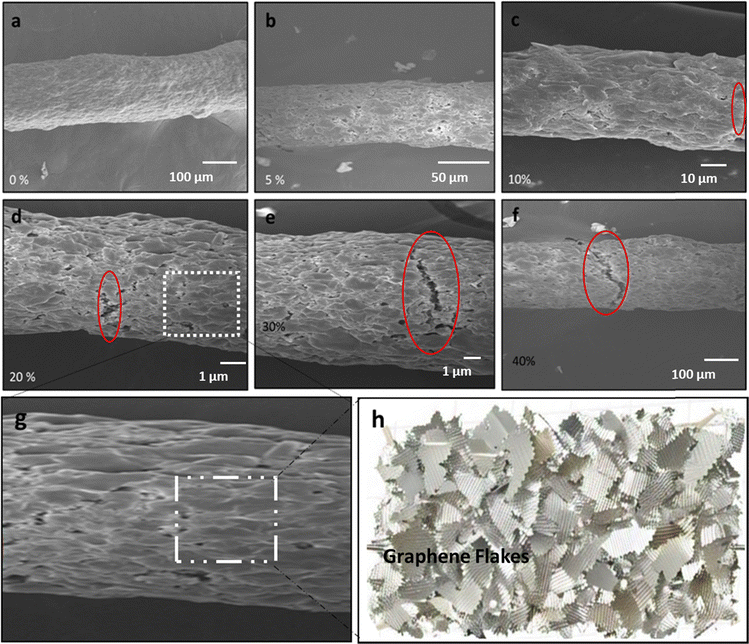 |
| Fig. 5 SEM images at different stretching percentages: (a) 0%, (b) 5%, (c) 10%, (d) 20%, (e) 30%, and (f) 40%. (g) and (h) Structural schematic diagrams. | |
As it can be observed from Fig. 5a, the graphene/PU coating is tightly packed in the case of 0% stretching. However, at 5% and 10% stretching, it can be observed from Fig. 5b and c that the graphene flakes embedded below the PU binder start to move apart. This results in a decrease in the overlapping area of the flakes, and in turn, an increase in the sensor resistance as observed in the electrical characteristics presented in Fig. 4. With the application of further strain, some micro-level cracks start appearing in the outer coating, as observed from Fig. 5d–f. The cracks result in a further increase of the device resistance. Thus, at a stretching of more than 10%, crack formation is the dominant reason for the change in resistance of the sensors. Meanwhile, below 10%, the reduction of the overlapping area is the reason for the resistance change. Fig. 5g and h exhibits a structural schematic diagrams to further clarify the mechanism. Once the applied strain is released, the device returns to its original morphological state, owing to the binding and self-healing properties of polyurethane (PU), thus resulting in no permanent damage or hysteresis. If the applied strain goes beyond 40% stretching, the cracks formed at the surface are too wide to completely heal by themselves and return to their original state, resulting in a permanent change in the sensor's resistance.
4.2 Practical applications
In order to demonstrate the possible applications of the fabricated spider silk-based strain sensor in human health monitoring, copper wires were attached to both ends of the sensor that was connected to the measuring system, as presented in Fig. 1h. The wearable sensors can be conformably attached to various parts of the human body using a simple tape, and the physical signals can be recorded (informed consent was duly obtained from all human participants involved in this study. All experimental procedures were conducted in accordance with applicable ethical guidelines and were approved by the Ethical Committee of the International Islamic University, Islamabad, Pakistan). The sensors were first attached to the wrist, as presented in Fig. 6a, and the human pulse pressure wave in the radial artery was monitored. The results of the senor's output for the detection of the pulse rate using arterial pressure are presented in Fig. 6b. The results clearly show a repeatable behavior of the sensor to detect the systolic and diastolic pressures, where the amplitude and frequency of the signal can be used to detect the blood pressure and pulse rate, respectively, in real time. The detection of systolic and diastolic arterial pressure ascertains that the fabricated sensors are extremely sensitive to even minor changes in the applied strain, and have excellent signal-to-noise ratio (SNR) at the output, showing very high reliability.
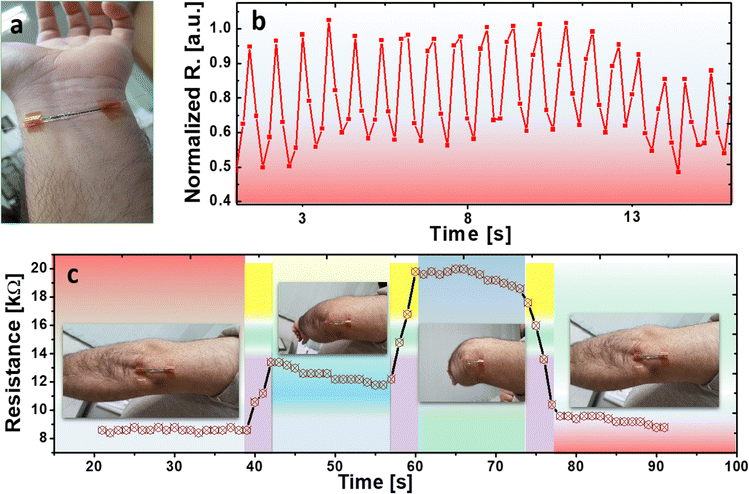 |
| Fig. 6 Applications of the fabricated sensors for the (a) pulse rate detection, (b) output of the pulse signals, and (c) detecting the arm position and elbow bending. | |
Next, the fabricated sensor was attached to the cubital (elbow) to detect its motion and bending angle, as presented in Fig. 6c. Initially, the arm (elbow) was in the straight position with zero bend and then the elbow was bent at half way, resulting in the change in the output of the sensor that remained stable at a certain value. Finally, the arms were completely bent while keeping in mind the maximum possible stretchability of the sensor, resulting in a further increase in the sensor resistance and maintaining a constant value. Finally, the sensor was straightened again to the mean position to 0° bend and the resistance of the sensor returned to its initial value, showing a repeatable behavior. As a final demonstration of the sensor in wearable device applications and to prove the conformability of the device when mounting onto various body surfaces, the sensor was attached onto the test subject's nape to monitor neck motion, as presented in Fig. 7a, and also on the wrist to detect hand movements, as presented in Fig. 7b. The results presented in Fig. 7a show that the sensor can effectively detect different postures and bending directions of the human head, and immediately returns to its intrinsic value when the posture returns to its mean position. Stretching of the sensor results in an increase of the sensor's resistance, while contraction of the device results in a drop in the resistance, as expected because of the increasing overlapping area of the graphene flakes and provision of movement paths for the current to flow through the device. Multiple devices can be mounted to different body parts to clearly distinguish between different motions and activities, such as whether the head is straight, turned right, turned left, bent down, or stretched up. Similarly, different positions of the wrist, including straight, bent up, and bent down, were also detected successfully using the same sensor, as presented in Fig. 7b, showing the same pattern of the output resistance of the sensor.
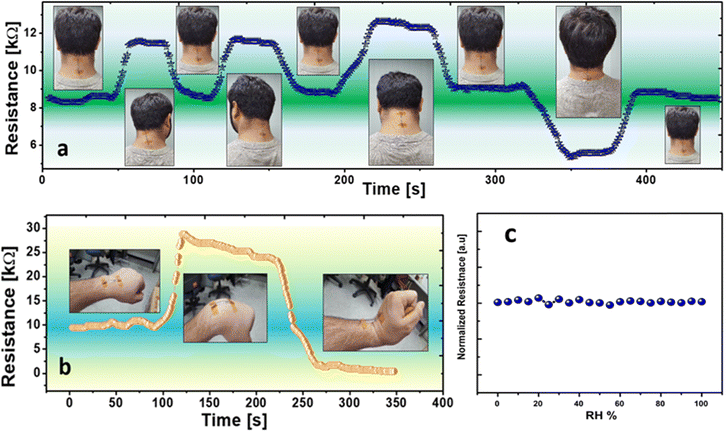 |
| Fig. 7 Detecting the posture of various body parts showing (a) the position of the head and (b) the motion of the wrist/hand. (c) Humidity test. | |
Employing the sensors to detect various human body postures demonstrates the robustness and versatility of the fabricated devices, indicating that they can be used in more than one wearable application to detect multiple parameters using the same kind of device. Since natural spider silk is sensitive to humidity, we performed experiments to check the humidity impact on the performance of the sensor. To prevent the sensor from environmental parameters, the sensor was encapsulated with polyurethane. Polyurethane protects the sensor from the environment, as evidenced from the experimental results. There is no notable change in the resistance of the sensor against increasing humidity level, as shown in Fig. 7c.
5. Conclusions
This paper highlights the significance of using the naturally occurring bio-degradable flexible materials in the applications of wearable devices and flexible electronics. A highly sensitive, stable, and reliable strain and bend sensor has been successfully fabricated using naturally occurring spider silk fibers as the substrate material that is coated with graphene flakes and encapsulated with a PU polymer binder. The fabrication method used was dip-casting, which is a simple and low-cost approach and is compatible with mass production. The sensors show excellent output characteristics, including the detection of very low strain, resulting in high SNR output. Various applications of the sensors have been investigated in the detection of the human pulse rate, arterial pressure, and elbow, neck, and wrist positions. The results demonstrate the great potential of the sensors to be employed in real-life wearable and flexible electronic applications with their seamless deployment, conformable nature, and excellent electromechanically characteristics.
Author contributions
G. H., J. B. and C. C. conceived the research. Z. A., G. H., M. U. K., H. A., B. H. and M. S. designed the experiment and fabricated the device. Z. A., G. H., M. U. K., H. A., B. H. and M. S. performed the experiment and took the measurements. Z. A., G. H., M. U. K., H. A., B. H. and M. S. analyzed the measured data. Z. A., G. H., M. U. K., H. A., B. H., M. S., J. B., C. C. and A. S. prepared the manuscript and discussed the results.
Data availability
Data will be made available upon reasonable request.
Conflicts of interest
All the authors contributing to this research work have no conflict of interest.
Acknowledgements
This work was supported by the research fund of Hanyang University (HY-2018-00000002370), National Research Foundation of Korea (NRF) grant funded by the Korea government (MSIP) (NRF-2016R1A2B4015627), and the National Research Program for Universities – NRPU (20-15054/NRPU/R&D/HEC/2021 2021) funded by the Higher Education Commission Pakistan.
References
- T. Yamada, Y. Hayamizu, Y. Yamamoto, Y. Yomogida, A. Izadi-Najafabadi, D. N. Futaba and K. Hata, A stretchable carbon nanotube strain sensor for human-motion detection, Nat. Nanotechnol., 2011, 296–301, DOI:10.1038/nnano.2011.36
.
- Y. Wang, L. Wang, T. Yang, X. Li, X. Zang, M. Zhu, K. Wang, D. Wu and H. Zhu, Wearable and highly sensitive graphene strain sensors for human motion monitoring, Adv. Funct. Mater., 2014, 24(29), 4666–4670, DOI:10.1002/adfm.201400379
.
- A. Atalay, V. Sanchez, O. Atalay, D. M. Vogt, F. Haufe, R. J. Wood and C. J. Walsh, Batch Fabrication of Customizable Silicone-Textile Composite Capacitive Strain Sensors for Human Motion Tracking, Adv. Mater. Technol., 2017, 2(9), 1700136, DOI:10.1002/admt.201700136
.
- B. U. Hwang, J. H. Lee, T. Q. Trung, E. Roh, D. Il Kim, S. W. Kim and N. E. Lee, Transparent Stretchable Self-Powered Patchable Sensor Platform with Ultrasensitive Recognition of Human Activities, ACS Nano, 2015, 9(9), 8801–8810, DOI:10.1021/acsnano.5b01835
.
- I. Kang, M. J. Schulz, J. H. Kim, V. Shanov and D. Shi, A carbon nanotube strain sensor for structural health monitoring, Smart Mater. Struct., 2006, 15(3), 737, DOI:10.1088/0964-1726/15/3/009
.
- N. Elvin, A. Elvin and D. H. Choi, A self-powered damage detection sensor, J. Strain Anal. Eng. Des., 2003, 38(2), 115–124, DOI:10.1243/030932403321163640
.
- G. Zhou and L. M. Sim, Damage detection and assessment in fibre-reinforced composite structures with embedded fibre optic sensors-review, Smart Mater. Struct., 2002, 11, 925, DOI:10.1088/0964-1726/11/6/314
.
- E. T. Thostenson and T. W. Chou, Carbon nanotube networks: Sensing of distributed strain and damage for life prediction and self healing, Adv. Mater., 2006, 18(21), 2837–2841, DOI:10.1002/adma.200600977
.
- C. Cochrane, V. Koncar, M. Lewandowski and C. Dufour, Design and development of a flexible strain sensor for textile structures based on a conductive polymer composite, Sensors, 2007, 7(4), 473–492, DOI:10.3390/s7040473
.
- J. Richeton, S. Ahzi, K. S. Vecchio, F. C. Jiang and R. R. Adharapurapu, Influence of temperature and strain rate on the mechanical behavior of three amorphous polymers: Characterization and modeling of the compressive yield stress, Int. J. Solids Struct., 2006, 43, 2318–2335, DOI:10.1016/j.ijsolstr.2005.06.040
.
- A. Alamusi, N. Hu, H. Fukunaga, S. Atobe, Y. Liu and J. Li, Piezoresistive strain sensors made from carbon nanotubes based polymer nanocomposites, Sensors, 2011, 11(11), 10691–10723, DOI:10.3390/s111110691
.
- K. Kesavan, K. Ravisankar, R. Senthil, B. Arun Sundaram and S. Parivallal, Studies on apparent strain using FBG strain sensors for different structural materials, Exp. Tech., 2014, 8(1), 25–32, DOI:10.1111/j.1747-1567.2012.00830.x
.
- M. Amjadi, K. U. Kyung, I. Park and M. Sitti, Stretchable, Skin-Mountable, and Wearable Strain Sensors and Their Potential Applications: A Review, Adv. Funct. Mater., 2016, 26(11), 1678–1698, DOI:10.1002/adfm.201504755
.
- M. Amjadi, A. Pichitpajongkit, S. Lee, S. Ryu and I. Park, Highly stretchable and sensitive strain sensor based on silver nanowire-elastomer nanocomposite, ACS Nano, 2014, 8(5), 5154–5163, DOI:10.1021/nn501204t
.
- S. Lee, M. Amjadi, N. Pugno, I. Park and S. Ryu, Computational analysis of metallic nanowire-elastomer nanocomposite based strain sensors, AIP Adv., 2015, 5, 117233, DOI:10.1063/1.4936635
.
- T. Yamada, Y. Hayamizu, Y. Yamamoto, Y. Yomogida, A. Izadi-Najafabadi, D. N. Futaba and K. Hata, A stretchable carbon nanotube strain sensor for human-motion detection, Nat. Nanotechnol., 2011, 6, 296–301, DOI:10.1038/nnano.2011.36
.
- W. Obitayo and T. Liu, A Review: Carbon Nanotube-Based Piezoresistive Strain Sensors, J. Sens., 2012, 652438, DOI:10.1155/2012/652438
.
- P. Dharap, Z. Li, S. Nagarajaiah and E. V. Barrera, Nanotube film based on single-wall carbon nanotubes for strain sensing, Nanotechnology, 2004, 15, 379, DOI:10.1088/0957-4484/15/3/026
.
- X. Xiao, L. Yuan, J. Zhong, T. Ding, Y. Liu, Z. Cai, Y. Rong, H. Han, J. Zhou and Z. L. Wang, High-strain sensors based on ZnO nanowire/polystyrene hybridized flexible films, Adv. Mater., 2011, 23(45), 5440–5444, DOI:10.1002/adma.201103406
.
- G. Zheng, F. Patolsky, Y. Cui, W. U. Wang and C. M. Lieber, Multiplexed electrical detection of cancer markers with nanowire sensor arrays, Nat. Biotechnol., 2005, 23, 1294–1301, DOI:10.1038/nbt1138
.
- J. M. Wu, C. Y. Chen, Y. Zhang, K. H. Chen, Y. Yang, Y. Hu, H. He and Z. L. Wang, Ultrahigh sensitive piezotronic strain sensors based on a ZnSnO3 nanowire/microwire, ACS Nano, 2012, 6(5), 4369–4374, DOI:10.1021/nn3010558
.
- S. Tadakaluru, W. Thongsuwan and P. Singjai, Stretchable and flexible high-strain sensors made using carbon nanotubes and graphite films on natural rubber, Sensors, 2014, 14(1), 868–876, DOI:10.3390/s140100868
.
- G. Hassan, J. Bae, A. Hassan, S. Ali, C. H. Lee and Y. Choi, Ink-jet printed stretchable strain sensor based on graphene/ZnO composite on micro-random ridged PDMS substrate, Composites, Part A, 2018, 107, 233–240, DOI:10.1016/j.compositesa.2018.01.031
.
- J. S. Kang, H. S. Kim, J. Ryu, H. Thomas Hahn, S. Jang and J. W. Joung, Inkjet printed electronics using copper nanoparticle ink, J. Mater. Sci.: Mater. Electron., 2010, 21, 1213–1220, DOI:10.1007/s10854-009-0049-3
.
- N. M. Sangeetha, N. Decorde, B. Viallet, G. Viau and L. Ressier, Nanoparticle-based strain gauges fabricated by convective self assembly: Strain sensitivity and hysteresis with respect to nanoparticle sizes, J. Phys. Chem. C, 2013, 117(4), 1935–1940, DOI:10.1021/jp310077r
.
- R. Ma, C. Levard, S. M. Marinakos, Y. Cheng, J. Liu, F. M. Michel, G. E. Brown and G. V. Lowry, Size-controlled dissolution of organic-coated silver nanoparticles, Environ. Sci. Technol., 2012, 46(2), 752–759, DOI:10.1021/es201686j
.
- J. Zhao, G. Y. Zhang and D. X. Shi, Review of graphene-based strain sensors, Chin. Phys. B, 2013, 22, 057701, DOI:10.1088/1674-1056/22/5/057701
.
- Y. Huang, E. Sutter, N. N. Shi, J. Zheng, T. Yang, D. Englund, H. J. Gao and P. Sutter, Reliable Exfoliation of Large-Area High-Quality Flakes of Graphene and Other Two-Dimensional Materials, ACS Nano, 2015, 9(11), 10612–10620, DOI:10.1021/acsnano.5b04258
.
- Elnaz Akbari, Vijay K. Arora, Aria Enzevaee, Mohammad Taghi Ahmadi, Mohsen Khaledian and Rubiyah Yusof, Gas concentration effects on the sensing properties of bilayer graphene, Plasmonics, 2014, 9, 987–992 CrossRef CAS
.
- M. Kong, M. Yang, R. Li, Y. Z. Long, J. Zhang, X. Huang and C. Li,
et al., Graphene-based flexible wearable sensors: mechanisms,
challenges, and future directions, Int. J. Adv. Des. Manuf. Technol., 2024, 131(5), 3205–3237 CrossRef
.
- P. Kiddee, R. Naidu and M. H. Wong, Electronic waste management approaches: An overview, Waste Manage., 2013, 33(5), 1237–1250, DOI:10.1016/j.wasman.2013.01.006
.
- J. A. Kluge, O. Rabotyagova, G. G. Leisk and D. L. Kaplan, Spider silks and their applications, Trends Biotechnol., 2008, 26(5), 244–251, DOI:10.1016/j.tibtech.2008.02.006
.
- Z. Shao and F. Vollrath, Surprising strength of silkworm silk, Nature, 2002, 418, 741, DOI:10.1038/418741a
.
- L. D. Koh, Y. Cheng, C. P. Teng, Y. W. Khin, X. J. Loh, S. Y. Tee, M. Low, E. Ye, H. D. Yu, Y. W. Zhang and M. Y. Han, Structures, mechanical properties and applications of silk fibroin materials, Prog. Polym. Sci., 2015, 46, 86–110, DOI:10.1016/j.progpolymsci.2015.02.001
.
- J. M. Gosline, M. E. DeMont and M. W. Denny, The structure and properties of spider silk, Endeavour, 1986, 10(1), 37–43, DOI:10.1016/0160-9327(86)90049-9
.
- O. Hakimi, D. P. Knight, F. Vollrath and P. Vadgama, Spider and mulberry silkworm silks as compatible biomaterials, Composites, Part B, 2007, 355, 123347, DOI:10.1016/j.compositesb.2006.06.012
.
- Su Yupei, Shuo Shi, Cong Wang, Zhuang Wang, Pengsong Li, Shuting Zhang, Bin Fei, Zhuohong Yang and Jinlian Hu, Spider silk-inspired tough materials: Multi-pathway synthesis advanced processing, and functional applications, Nano Today, 2024, 55, 102188 CrossRef
.
- Liao Xinqin, Song Weitao, Zhang Xiangyu, Huang Hua, Wang Yongtian and Zheng Yuanjin, Directly printed wearable electronic sensing textiles towards human–machine interfaces, J. Mater. Chem. C, 2018, 6(47), 12841–12848, 10.1039/C8TC02655F
.
- Z. Chen, W. Lin and C. Zhang,
et al., Multifunctional and Reconfigurable Electronic Fabrics Assisted by Artificial Intelligence for Human Augmentation, Adv. Fiber Mater., 2024, 6, 229–242, DOI:10.1007/s42765-023-00350-z
.
- X. Liao, W. Song, X. Zhang, H. Jin, S. Liu, Y. Wang, A. V.-Y. Thean and Y. Zheng, An Artificial Peripheral Neural System Based on Highly Stretchable and Integrated Multifunctional Sensors, Adv. Funct. Mater., 2021, 31, 2101107, DOI:10.1002/adfm.202101107
.
Footnote |
† Both Zaigham Abbas and Gul Hassan are considered as the first authors. |
|
This journal is © The Royal Society of Chemistry 2025 |
Click here to see how this site uses Cookies. View our privacy policy here.