Enhancing microplastic capture efficiencies with adhesive coatings on stainless-steel filters†
Received
15th December 2023
, Accepted 28th February 2024
First published on 7th March 2024
Abstract
Microplastics have been found in our food, water, and air, raising concerns about their potential health impacts. While environmental remediation may be intractable, we should prioritize minimizing our exposure. In this context, an adhesive-coated stainless-steel filter was developed herein to remove microplastics from water.
Introduction
Microplastics are typically formed via the erosion and abrasion of larger plastic materials. Examples include tire wear on roads1 and washing of synthetic textiles.2 As rain,3 wind,4 and rivers5 transport and disperse these microplastics throughout the environment, their remediation becomes challenging. Instead, efforts should focus on preventing more microplastics from entering the environment. At the same time, we should also focus on minimizing human exposure to what is already out there. It is within this latter context that microplastic contamination in drinking water (tap and bottled) has gained attention. In 2018, California became the first state to mandate testing of microplastic levels in drinking water and will ultimately set maximum allowable limits.6,7 As a result, technologies that can meet these standards are urgently needed.8–10
To date, researchers have evaluated the microplastic removal efficiencies of existing technologies within drinking water treatment plants.11–14 Most plants include purification via coagulation/sedimentation and filtration through sand or activated carbon followed by disinfection. Overall, these studies have shown that large microplastics are effectively removed, but small microplastics (10–45 μm (ref. 11) or 10–20 μm (ref. 12)) are more likely to pass through. In addition, Andrews and co-workers discovered that airborne microplastics (which are <10 μm) can be introduced during water treatment due to atmospheric deposition, negating the impacts of earlier removal steps.11 As such, additional technologies will likely be needed to effectively remove these smaller microplastics from drinking water.
Filtration is a common approach for water purification, and often employed in homes and businesses as an add-on water treatment step. Most filters rely on mechanical filtration, wherein particles become physically trapped on the filter (Scheme 1). The size of particle that is trapped depends on the mesh size, which corresponds to the size of the openings (in microns). Smaller mesh sizes trap more particles, but there is a trade-off between the size of the opening and the water flow rate. In an extreme example, ultrafiltration has small mesh sizes (0.01–0.1 μm), which can effectively capture the smaller microplastics,15 but the flow rate is too slow unless high pressures are used.
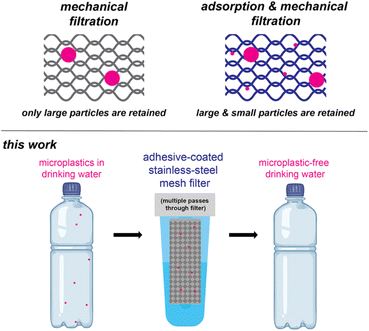 |
| Scheme 1 Filtering mechanisms (top) and an adhesive-coated stainless-steel filter for removing microplastics from drinking water (bottom). | |
Rather than decrease the mesh size, an alternative option is to coat mechanical filters with materials that can leverage adsorption processes.16–19 With adsorption, the particles are retained due to non-covalent interactions. For example, Guo and co-workers coated wood sawdust with ionically crosslinked polyphenol, which enhanced capture of both nano- and microplastics.20 Similarly, Quan and co-workers coated a porous loofah sponge with natural waxes to create a superhydrophobic coating that absorbed oil containing hydrophobic polystyrene (PS) microplastics from a water mixture.21 In another example, Qu and co-workers coated an aluminosilicate-based synthetic porous material with polydimethylsiloxane, creating a hydrophobic surface that captured polyethylene (PE), polypropylene (PP), and poly(vinyl chloride) (PVC) microplastics from water (99% removal at a concentration 1 g L−1).22 Similarly, we previously reported coating zirconium silicate beads with a pressure-sensitive adhesive (poly(2-ethylhexyl acrylate), PEH) to capture microplastics from water, including PS, poly(ethylene terephthalate), nylon-12, and rubber.23 Pressure sensitive adhesives24 are appealing materials for coatings because they can quickly conform to and wet materials such as microplastics. Although high removal efficiencies (>99%) of PS microplastics were observed within 5 min, the concentrations were high (1 g L−1; approx. 108 PS microplastics per L) relative to what is most often observed in drinking water (average <10 microplastics per L, range 0–1000 microplastics per L).25 To achieve high removal efficiencies at lower concentrations, we explore herein the role of filter material and architecture, adhesive chemical structure, as well as microplastic size and identity. This work culminates in quantitative removal of microplastics from water using an adhesive-coated stainless-steel mesh filter under realistic microplastic concentrations.
Results and discussion
Adhesives are advantageous as coating materials because they can be deposited with simple techniques (e.g., dip-coating, solvent-casting, or spray-coating), making this approach both versatile and low-cost. Additionally, some pressure-sensitive adhesives (i.e., poly(alkyl acrylate)s) can be synthesized from waste diapers as the feedstock, which we previously showed results in 22% fewer emissions than the analogous route from petroleum feedstocks.26 As such, using these diaper-based adhesives as filter coatings herein reduces both macro- and microplastic pollution.
One challenge with pressure-sensitive adhesive coatings is that they have low glass transition temperatures (<0 °C), meaning that the chains are mobile at room temperature. Consequently, the adhesives can, over time, move across and off the coated substrate, leading to uneven coatings and shedding. We observed this undesirable phenomenon in our previous system23 with PEH-coated zirconium silicate beads (Fig. 1A and Fig. S26 and S27†). Clumps of adhesive formed between the beads after stirring for 18 h in a microplastics/water/ethanol mixture. To overcome this challenge, we evaluated herein both alternative adhesives and substrates to identify an adhesive/substrate combination that exhibits a more stable coating and maintains fast removal efficiencies.
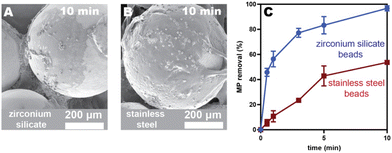 |
| Fig. 1 SEM images of PEH spray-coated zirconium silicate beads (A) and stainless-steel beads (B) after 10 min of a capture experiment. (C) Plot of microplastic removal efficiencies (percent removed relative to a control) versus time (min), as quantified by flow cytometry. All capture experiments were performed in 80/20 water/ethanol solutions containing 500 mg L−1 of PS microplastics (10 μm diameter). | |
Identifying the optimal substrate material
Spherical beads were chosen as the initial architecture because they can be packed into columns for large-scale, high-flow-rate filtration. To improve surface wetting and stability, stainless-steel (SS) beads were selected due to its high surface energy relative to the adhesive.27 Additional advantages include its low cost and high corrosion resistance. To compare the wetting and stability, the original adhesive (PEH, Mw = 735 kDa) was spray-coated onto both SS and zirconium silicate beads. Spray-coating enables the adhesive solution to be aerosolized and propelled forward as a fine mist. Once deposited, the solvent quickly evaporates, producing a more even coating than the original solvent-casting methods.23 The coated SS beads were stirred in an aqueous suspension of microplastics for 18 h to compare to the zirconium silicate beads. The SS coatings appeared more stable via scanning electron microscopy (SEM), though some evidence of adhesive migration was still visible (Fig. S26 and S27†). Nevertheless, stainless steel offered a significant improvement in adhesive retention over the zirconium silicate substrates.
To compare the relative capture efficiencies of SS and zirconium silicate beads, both adhesive-coated beads were agitated in vials with polystyrene microplastics (10 μm, 500 mg L−1) suspended in an 80/20 water/ethanol mixture to prevent microplastic clumping. Aliquots were taken at different time intervals for analysis using flow cytometry.23 Removal efficiencies were calculated by comparing the microplastic counts in the sample relative to the control (Table S3†). As evident in Fig. 1C, after 10 min the PEH-coated SS beads exhibited lower microplastic removal efficiencies (54 ± 2%) compared to the zirconium silicate beads (97 ± 2%). While disappointing, we realized that the large adhesive clumps that form between the zirconium silicate beads (due to adhesive migration) is likely responsible for this more efficient capture. Because adhesive shedding would be problematic in a drinking water application, we moved forward with stainless steel as the substrate for all future studies.
Identifying the optimal substrate architecture
We next evaluated stainless-steel mesh filters28 because the web-like architecture should facilitate more contact with microplastics, and the higher surface area might reduce adhesive migration. This architecture was inspired by similar filters marketed for microplastics capture in washing machine effluent. The average width of the openings in our mesh are approximately 3 and 1 mm, much larger than any microplastic examined herein (Table S1†). To efficiently coat the mesh filter with adhesive, we unrolled the material and spray-coated both sides with a 1 wt% solution of PEH in THF. We also dip-coated the mesh with the same solution for comparison. After coating, the mesh was packed into a small vial and a vertical shaker was used to pass the water through the mesh multiple times. Aliquots were removed via a syringe fitted with a wide-gauge needle and analyzed via flow cytometry. The PEH-coated SS mesh showed faster capture rates (97 ± 1% at 10 min; black data in Fig. 2C) than the SS beads (maroon data in Fig. 1C) at 500 mg L−1 concentrations. Interestingly, the uncoated mesh (as purchased) removed 50 ± 3% at 10 min (pink data in Fig. 2C), demonstrating that there is some nonspecific adsorption to the stainless steel and that the adhesive enhances microplastics capture. In both cases, the driving force for microplastics capture is likely to minimize unfavorable interactions with water (i.e., hydrophobic interactions).29 In the case of the adhesive-coated substrate, there is likely an additional benefit from favorable dispersive interactions between the microplastics and adhesive.23,30 Notably, the dip-coated substrates exhibited more even and higher coverage than spray-coating (by SEM), and as a result, gave faster removal efficiencies (Fig. S46†). Consequently, all further studies were done with dip-coated materials.
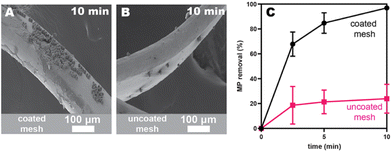 |
| Fig. 2 SEM images of PEH dip-coated stainless-steel mesh (A) and uncoated stainless-steel mesh (B) after 10 min of a capture experiment. (C) Plot of microplastic removal efficiencies (percent removed relative to a control) versus time (min), as quantified by flow cytometry. All capture experiments were performed in 80/20 water/ethanol solutions containing 500 mg L−1 of PS microplastics (10 μm diameter). | |
Identifying the optimal adhesive structure
We next explored whether alternative poly(alkyl acrylate)-based adhesives would exhibit stronger adhesion to SS than the original PEH, which could result in better and more stable coatings. Specifically, we measured the force of adhesion using a probe-tack protocol for a series of poly(alkyl acrylate)s from an “acrylate polymer kit” purchased from Scientific Polymer Products (Fig. 3, top). Of these nine adhesives, poly(isobutyl acrylate) (PiB) and our original adhesive (PEH) emerged as the leading materials based on their higher forces of adhesion to SS (Fig. 3A). Nevertheless, these commercial adhesives had a relatively low molar mass (Mw of 45–141 kDa), and we had previously shown that low molar mass adhesives perform better at short times but are more likely to shed adhesive (possibly via dissolution) over longer times.23,31 As a result, we synthesized higher molar mass derivatives of both PiB (Mw = 233 kDa) and PEH (Mw = 735 kDa) for further evaluation. Probe-tack testing of these higher molar mass polymers with stainless steel revealed similar forces of adhesion for both PiB and PEH (Fig. 3B). As such, we surmised that either adhesive would work for this application. We ultimately chose PEH over PiB for all further studies because it is accessible via the synthetic route from waste plastics.26
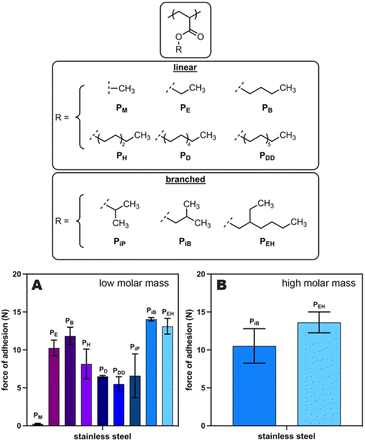 |
| Fig. 3 (Top) Adhesive structures evaluated in probe-tack measurements. Plots of force of adhesion versus probe type using a stainless-steel probe for (A) low molar mass adhesives and (B) high molar mass adhesives. | |
Impact of microplastic size and identity
To understand the impact of microplastic identity, the capture of PE and PS microplastics of the same size (10 μm) and concentration (500 mg L−1) were compared. The PS microplastics were captured more efficiently at short times (Fig. 4A, black versus pink), although both reach high removal efficiencies (>80%) at 60 min (Fig. S48†). This result is consistent with the probe-tack data, which showed that the PS exhibits a higher force of adhesion than PE to PEH (14.4 N ± 1 versus 8.46 ± 0.5 N, Table S6†). Previous studies have shown that PS has more favorable van der Waals interactions with itself, compared to PE with itself, which would lead to aggregation and more efficient capture in water.32
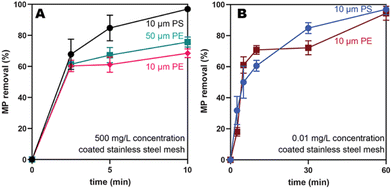 |
| Fig. 4 Plots of microplastic removal efficiencies (percent removed relative to a control) versus time (min) for (A) PE (10 μm, 50 μm) and PS (10 μm) at a concentration of 500 mg L−1 in an 80/20 water/ethanol solution, and (B) PE (10 μm) and PS (10 μm) at a concentration of 0.01 mg L−1 in neat water. All experiments were performed using the adhesive-coated stainless-steel mesh. | |
To examine the impact of size, PE microplastics of varying sizes (10 versus 50 μm) were compared. The larger microplastics were captured more efficiently (75 ± 3% versus 68 ± 3% at 10 min, Fig. 4A, teal versus pink) albeit by a narrow margin. One explanation may be that the larger particles have more area available to facilitate wetting and ultimately capture by the adhesive. Combined, these results suggest that microplastic size and polymer identity only modestly impacts capture efficiencies.
Application to drinking water
To target concentrations like what is currently found in drinking water, PS and PE microplastics (10 μm) were compared at a significantly lower concentration (0.01 mg L−1). Gratifyingly, both PS and PE exhibited high removal efficiencies at 60 min (97 ± 3% and 94 ± 5%, respectively; Fig. 4B) at these low concentrations. At shorter times (10 min), lower removal efficiencies (∼60%; Fig. S50 and S51†) were observed. The slower capture at these lower concentrations is expected because there will be fewer collisions of the microplastics with the mesh. Interestingly, both PS and PE behave similarly at these low concentrations, in contrast to the slight preference for PS at higher concentrations. As a control, the uncoated stainless-steel mesh removed only 50% of both microplastics at 60 min (Fig. S50 and S51†), likely via nonspecific adsorption.
We also evaluated the capture efficiency for the larger microplastics (PE, 50 μm) at these low concentrations (0.01 mg L−1). In this experiment, optical microscopy was utilized because there are so few particles (∼140 microplastics per L). With this method, the microplastics can be counted after filtering a large volume of water through an aluminum oxide filter (200 nm pore size). To facilitate counting, brightly colored fluorescent pink PE microplastics (50 μm) were used. As a control, 100 mL of a microplastics stock solution was filtered to yield approximately 18 PE microplastics on the filter, close to the expected microplastics count (Table S13, and Fig. S52†). When this same stock solution was shaken with the PEH-coated stainless-steel mesh, near quantitative (93%) removal of microplastics was observed (Table S13, and Fig. S53†). In contrast, the uncoated stainless-steel mesh removed only 50% of the PE microplastics, again via nonspecific adsorption (Table S13, and Fig. S54†). Combined, these results suggest that the adhesive-coated meshes are promising candidates for capturing microplastics at the small sizes and low concentrations observed in drinking water.
Conclusions and outlook
Herein, we demonstrated that adhesive-coated stainless-steel filters enhance the capture efficiency of pristine polystyrene and polyethylene microplastics at small (10 μm) and medium (50 μm) sizes, and under realistic contamination levels in drinking water (0.01 mg L−1). Specifically, under realistic contamination levels, we observed >90% capture within 60 min. Combined, these results highlight how adsorption can be leveraged to supplement mechanical filtration. One advantage of this approach is that, after use, the adhesive coatings could be removed via solvent- or thermal-based methods, enabling one to potentially reuse or repurpose the microplastics, adhesive, and SS mesh. A life cycle assessment is needed to provide more insight into the potential scenarios, especially for the captured microplastics (i.e., beyond landfilling or incineration). Future efforts should expand these studies to include other microplastic identities, sizes, and shapes, including environmental/weathered microplastics, as well as different water conditions.
Author contributions
The manuscript was written through contributions of all authors. MR, WJ, HET, and MEC were involved with conceptualization, data curation, formal analysis, investigation, methodology, validation, visualization, writing – reviewing and editing. SC was involved with investigation, methodology, and validation. AJM was involved with conceptualization, funding acquisition, project administration, resources, supervision, visualization, writing – original draft, review, and editing.
Conflicts of interest
There are no conflicts to declare.
Acknowledgements
The authors thank the National Science Foundation – Emerging Frontiers in Research and Innovation 2020 program for funding (#2029251).
References
- Z. Luo, X. Zhou, Y. Su, H. Wang, R. Yu, S. Zhou, E. G. Xu and B. Xing, Sci. Total Environ., 2021, 795, 148902 CrossRef CAS PubMed.
- S. Yadav, N. Kataria, P. Khyalia, P. K. Rose, S. Mukherjee, H. Sabherwal, W. S. Chai, S. Rajendran, J.-J. Jiang and K. S. Khoo, Chemosphere, 2023, 326, 138495 CrossRef CAS PubMed.
- J. Brahney, M. Hallerud, E. Heim, M. Hahnenberger and S. Sukumaran, Science, 2020, 368, 1257–1260 CrossRef CAS PubMed.
- J. E. Bullard, A. Ockelford, P. O'Brien and C. McKenna Neuman, Atmos. Environ., 2021, 245, 118038 CrossRef CAS.
- E. K. Owowenu, C. F. Nnadozie, F. Akamagwuna, X. S. Noundou, J. E. Uku and O. N. Odume, Aquat. Ecol., 2023, 57, 557–570 CrossRef CAS.
- A. Portantino, SB-1263: Ocean Protection Council, Statewide Microplastics Strategy, 2018 Search PubMed , https://leginfo.legislature.ca.gov/faces/billTextClient.xhtml?bill_id=201720180SB1263.
-
A. Portantino, SB-1422: California Safe Drinking Water Act: microplastics, 2018, https://leginfo.legislature.ca.gov/faces/billTextClient.xhtml?bill_id=201720180SB1422.
- Q. Liu, Y. Chen, Z. Chen, F. Yang, Y. Xie and W. Yao, Sci. Total Environ., 2022, 851, 157991 CrossRef CAS PubMed.
- R. Ahmed, A. K. Hamid, S. A. Krebsbach, J. He and D. Wang, Chemosphere, 2022, 293, 133557 CrossRef CAS PubMed.
- N. Badola, A. Bahuguna, Y. Sasson and J. S. Chauhan, Front. Environ. Sci. Eng., 2022, 16, 7 CrossRef.
- S. L. Cherniak, H. Almuhtaram, M. J. McKie, L. Hermabessiere, C. Yuan, C. M. Rochman and R. C. Andrews, Chemosphere, 2022, 288, 132587 CrossRef CAS PubMed.
- Y. Zhang, A. Diehl, A. Lewandowski, K. Gopalakrishnan and T. Baker, Sci. Total Environ., 2020, 720, 137383 CrossRef CAS PubMed.
- A. N. Velasco, S. R. Gentile, S. Zimmermann and S. Stoll, Front. Water, 2022, 4, 835451 CrossRef.
- A. S. Reddy and A. T. Nair, Environ. Technol. Innov., 2022, 28, 102815 CrossRef CAS.
- A. Sharma, S. Kumari, R. L. Chopade, P. P. Pandit, A. R. Rai, V. Nagar, G. Awasthi, A. Singh, K. K. Awasthi and M. S. Sankhla, Sci. Prog., 2023, 106, 00368504231176399 CrossRef CAS PubMed.
- L. Muthulakshmi, S. Mohan and T. Tatarchuk, Environ. Sci. Pollut. Res., 2023, 30, 84933–84948 CrossRef CAS PubMed.
- A. T. Adeleye, M. M. Bahar, M. Megharaj and M. M. Rahman, J. Water Process Eng., 2023, 53, 103777 CrossRef.
- I. Ali, X. Tan, J. Li, C. Peng, P. Wan, I. Naz, Z. Duan and Y. Ruan, Water Res., 2023, 230, 119526 CrossRef CAS PubMed.
- Z. Chen, J. Fang, W. Wei, H. H. Ngo, W. Guo and B.-J. Ni, J. Clean. Prod., 2022, 371, 133676 CrossRef CAS.
- Y. Wang, M. Wang, Q. Wang, T. Wang, Z. Zhou, M. Mehling, T. Guo, H. Zou, X. Xiao, Y. He, X. Wang, O. J. Rojas and J. Guo, Adv. Mater., 2023, 35, 2301531 CrossRef CAS PubMed.
- T. T. V. Ha, N. M. Viet, P. T. Thanh and V. T. Quan, Environ. Technol. Innov., 2023, 32, 103265 CrossRef CAS.
- X. Rong, X. Chen, P. Li, C. Zhao, S. Peng, H. Ma and H. Qu, Chemosphere, 2022, 299, 134493 CrossRef CAS PubMed.
- P. T. Chazovachii, J. M. Rieland, V. V. Sheffey, T. M. E. Jugovic, P. M. Zimmerman, O. Eniola-Adefeso, B. J. Love and A. J. McNeil, ACS EST Engg., 2021, 1, 1698–1704 CrossRef CAS.
- S. Mapari, S. Mestry and S. T. Mhaske, Polym. Bull., 2021, 78, 4075–4108 CrossRef CAS.
- D. Sol, C. Solís-Balbín, A. Laca, A. Laca and M. Díaz, Sci. Total Environ., 2023, 899, 165356 CrossRef CAS PubMed.
- P. T. Chazovachii, M. J. Somers, M. T. Robo, D. I. Collias, M. I. James, E. N. G. Marsh, P. M. Zimmerman, J. F. Alfaro and A. J. McNeil, Nat. Commun., 2021, 12, 4524 CrossRef CAS PubMed.
- Technibond Surface Energy Chart, https://www.technibond.co.uk/wp-content/uploads/2019/04/surface-energy-chart.pdf (accessed Oct 2023).
- SUNHE 40 Pieces Lint Traps, For Washing Machine, https://www.amazon.com/SUNHE-Pieces-Washing-Machine-Laundry/dp/B07594P4TV (accessed Oct 2023).
- A. Faghihnejad and H. Zeng, Soft Matter, 2012, 8, 2746–2759 RSC.
-
T. Jugovic, M. Robo, W. Ji, M. E. Clough, A. J. McNeil and P. Zimmerman, submitted.
- J. M. Rieland, Z. Hu, J. S. Deese and B. J. Love, Sep. Purif. Technol., 2023, 307, 122819 CrossRef CAS.
- C.-Q. Wang, H. Wang, G.-H. Gu, J.-G. Fu, Q.-Q. Lin and Y.-N. Liu, Waste Manage., 2015, 46, 56–61 CrossRef CAS PubMed.
|
This journal is © The Royal Society of Chemistry 2024 |
Click here to see how this site uses Cookies. View our privacy policy here.