DOI:
10.1039/D3QI00207A
(Research Article)
Inorg. Chem. Front., 2023,
10, 2276-2284
Cu–Ni alloy decorating N-doped carbon nanosheets toward high-performance electrocatalysis of mildly acidic CO2 reduction†
Received
1st February 2023
, Accepted 6th March 2023
First published on 7th March 2023
Abstract
Electrochemical CO2 reduction to value-added chemicals or fuels is a prospective strategy for facilitating the closing of the carbon loop. However, there still exist challenges in developing efficient catalysts and optimizing the electrolyzer components to meet industrial applications. Herein, nitrogen-doped “willow leaf” shaped carbon nanosheets modified with Cu–Ni alloy (CuNi-N-CNS) is designed for electrochemical CO2 reduction reaction (CO2RR), which shows high faradaic efficiency for CO of over 90% at a wide potential window ranging from −0.8 V to −1.0 V and robust durability with almost 100% of its initial selectivity after 36 h of electrolysis in H-type cell. Moreover, we evaluate its electrocatalytic activity in a self-assembly flow cell in a mildly acidic catholyte (CO2-saturated 3 M KCl solution, pH = 4.25), which can achieve a commercially viable current density of 420 mA cm−2 at −1.0 V versus reversible hydrogen electrode (vs. RHE) with CO selectivity above 95%. Experimental characterization and electrochemical analysis reveal that the synergistic effects of ultra-thin “willow leaf” structure and bimetallic alloy modification can not only increase electron transport efficiency but also decrease the reaction energy barrier of COOH* and promote the formation of CO.
Introduction
Massive carbon dioxide emissions from excessive utilization of fossil fuels have led to widespread environmental issues.1–3 To date, many approaches have been adequately investigated to reduce the concentration of carbon dioxide in the atmosphere, among which electrocatalytic CO2 reduction reaction (CO2RR) driven by renewable electrical energy represents a realizable and convenient carbon-neutral pathway for producing valuable carbon-based chemical feedstocks.4–6 However, the extremely stable C
O bond (806 kJ mol−1) in CO2 and the competing hydrogen evolution reaction in the aqueous phase hinder the activation of CO2.7,8 Besides, owing to the complex multiple proton and electron transfer processes during CO2 reduction, the variety of products from CO2 reduction adds extra difficulties in controlling its selectivity.9–11 Among these possible products, CO is a more accessible product (CO2 + 2H+ + 2e− → CO + H2O, −0.11 V vs. RHE) than other multi-carbon products in terms of reaction kinetics and is also an important raw material in industrial production.12–14 Thus, elevating the conversion efficiency of CO2 reduction into CO is crucial to promote the actual applications of CO2RR.15,16
On one hand, designing effective catalysts for CO2RR is still at the center of promoting the conversion efficiency of CO2RR.17,18 The electrocatalytic performance of catalysts is largely affected by their structure, crystal surface, and number of active sites.19–21 Earlier, a variety of nano-structured Ag, Au, and Pd-based electrocatalysts have been studied due to their high selectivity and relatively low overpotential for CO2 to CO in aqueous solutions.22–25 But the scarcity of noble metals always limits their practical use. In this regard, replacing noble metal catalysts with non-noble carbon-based metal materials is a promising way towards sustainable CO2RR.26 Metal–organic framework-derived carbon-based materials hold great promise for applications in CO2RR due to the exceptionally high surface areas, flexible electronic structure, multiple active sites, and designable morphology.27,28 The single metal atom sites anchored on carbon materials derived from MOF templates have been widely prepared for CO2RR and display excellent activity and selectivity for CO2 reduction.29 Compared with these carbon-based materials anchored with single sites, carbon-based materials modified with metal alloys have received less attention but are still worthy of being studied owing to their rich components with tunable electronic structure and multicomponent cooperative effect.30 For instance, Liu31 reported ultrathin porous g-C3N4 nanosheets modified with AuCu alloy NPs catalyst. The charge transfer from Au to Cu in the alloy enriches Cu with excessive negative charges, which promotes the formation of intermediate *CO on the surface, thus increasing the yield of C2 products. Roy's32 group found that the carbon-supported PtZn nano-alloy can efficiently convert CO2 to CH3OH, resulting from the intermetallic alloy's ability to fine-tune electron transport properties and structures. Though desirable performance has been achieved on these reported carbon-based alloy catalysts, there is still room for designing other novel carbon-based catalysts with excellent catalytic performance.
On the other hand, the CO2RR performance of catalysts is mainly investigated in H-cells or flow cells in neutral or alkaline electrolytes currently, where problems like CO2 mass transport limitation, carbonation, and poor stability exist.33 In these H-cells, the limited solubility and mass diffusion of CO2 seriously limit its conversion rate.15,34–36 In the widely reported gas diffusion electrode (GDE) based flow cells, the mass transport limitation problem can be avoided by constructing a gas–liquid–solid three-phase reaction interface, and the reaction rates are greatly improved.37 However, the commonly used alkaline electrolyte and the high local pH of the reaction interface at large current density accelerate the carbonation and flooding of the flow cell, leading to poor stability and rather low CO2 utilization.38,39 In comparison, the CO2RR performed in acidic media has emerged as a promising strategy to circumvent carbonation and its induced problems. Though hydrogen evolution reaction may be more favorable in acidic conditions, it can be suppressed by suitably adjusting the reaction interface of electrodes and the pH of the catholyte. For example, Sargent40 carried out CO2RR over copper in an electrolyte with pH < 1, which achieved a single-pass CO2 utilization of 77% and a conversion efficiency of 50% toward multi-carbon products at a current density of 1.2 A cm−2. Besides, Monteiro41 investigated the feasibility of CO2 electrolysis with 10 cm2 gold gas diffusion electrodes at pH of 2–4, obtaining CO faradaic efficiencies between 80–90%, with a 30% improvement of the overall process energy efficiency in comparison with neutral media. The research of CO2RR in acidic electrolytes opens up a unique routine for CO2RR, and studying the CO2RR performance of various catalysts in acidic electrolytes provides references for solving problems in practical applications of CO2RR.42–46
Herein, we strategically design a nitrogen-doped “willow leaf” shaped carbon nanosheets modified with Cu–Ni alloy (CuNi-N-CNS) through a facile solvothermal-evaporation-pyrolysis process. The Cu–Ni alloy nanoparticles encapsulated in the in situ formed carbon layers decorate on the ultra-thin lancet nanosheets. Such a unique composite structure can greatly improve the catalytic activity for CO2RR, which achieves a high CO faradaic efficiency of over 90% for CO2 electroreduction at a potential window of −0.8 V to −1.0 V vs. RHE in H-Cell. Besides, the CO2RR performance of the prepared catalyst was further investigated in a home-made flow cell with CO2-saturated 3 M KCl solution as catholyte (pH = 4.25), which can provide a mildly acidic environment to prevent carbonation and achieve high current density (420 mA cm−2) at −1.0 V with FECO above 95%. Consequently, our study affords an innovative idea of designing metal-based catalysts for CO2RR and provides the possibility for its industrialization.
Results and discussion
Catalyst preparation and characterization
As shown in Scheme 1, the catalyst was synthesized by a metal–organic framework (MOF) assisted method. The CuNi doped zeolitic imidazolate framework-8 (CuNi-ZIF-8) suspension was first fabricated by mixing zinc nitrate, copper nitrate, nickel nitrate, and 2-methylimidazole in DI water via vigorously stirring, and Resol-F127 solution was synthesized by heating phenolic resin and surfactant F127. Then, the nitrogen-doped ultra-thin carbon nanosheets modified with Cu–Ni alloy, named CuNi-N-CNS, were obtained via two steps of hydrothermal and pyrolysis reactions (for synthesis details, see ESI and Fig. S1, S2†). Remarkably, a gram-scale catalyst can be obtained via simply increasing feeding reagents (Fig. S3†) during synthetic processes, indicating the feasibility of scalable synthesis. For comparison, we probed the effect of raw material ratios on the structure of the CuNi-N-CNS catalyst to determine the optimal one. Ni-N-CNS, Cu-N-CNS, and N-CNS were also synthesized as controlled samples through a similar method (Fig. S2†).
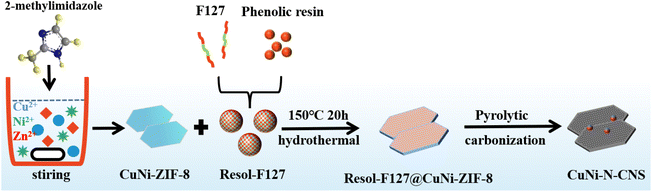 |
| Scheme 1 Schematic representation of the synthetic method of CuNi-N-CNS samples. | |
The morphology characterizations of CuNi-N-CNS were conducted by scanning electron microscopy (SEM) and transmission electron microscopy (TEM). As displayed in Fig. 1a–c, the as-prepared catalyst maintained the uniform structure of ultra-thin “willow leaf” shaped nanosheets. In contrast, samples without Resol-F127 composite would lose the “willow leaf” structure and agglomerate after pyrolysis (Fig. S4†). It could be inferred that Resol-F127 played a crucial role in the whole reaction process. Specifically, in the hydrothermal process, Resol-F127 would attach to CuNi-ZIF-8 nanosheets due to the surface induction effect and cure with increasing temperature. Then, it in situ formed a carbon layer after undergoing the pyrolysis at 900 °C, which encapsulated Cu–Ni alloy nanoparticles, as revealed by the TEM images (Fig. 1d). In the HRTEM images of the calcined sample (Fig. 1e and f), the well-defined lattice streaks with d-spacings of 2.24 and 1.96 Å could be safely indexed to the (111) and (200) planes of Cu–Ni alloy, respectively. From the element mapping images (Fig. 1g), it can be demonstrated that Cu, Ni, C, and N species are homogeneously distributed in the carbon substrate, and CuNi alloy is clearly distributed on the surface. Complementally, as revealed by the inductively coupled plasma optical emission spectrometry (ICP-OES), the Cu and Ni contents of CuNi-N-CNS are determined to be 2.60 and 2.39 wt%, respectively. (Table S1†). EDS and XPS data are further used to assist in the determination of Cu and Ni contents (Fig. S5–S12†). The N2 sorption isotherms (Fig. S13a†) further verify that the CuNi-N-CNS possesses a porous structure with a large specific surface area of 984.21 m2g−1. The pore size distribution (Fig. S13b†) peaks of the CuNi-N-CNS at ca. 0.68 nm (∼2.1 times the dynamic diameter of CO2 molecules) reveal its microporous structure, which could enhance the capture of CO2, resulting in CO2 enrichment around the active sites.
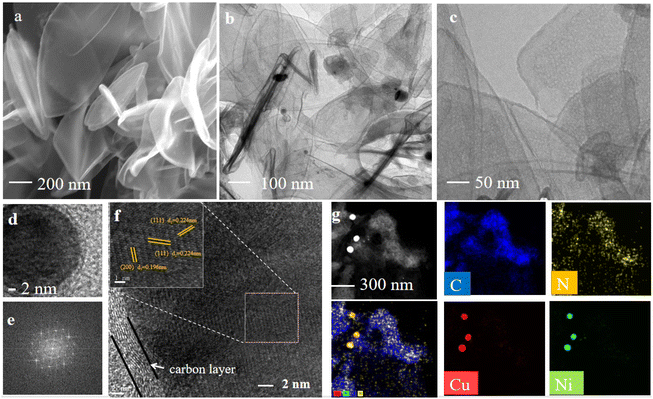 |
| Fig. 1 (a) High-resolution SEM patterns of CuNi-N-CNS. (b–c) TEM images of CuNi-N-CNS at different resolutions, and (d) CuNi@C in CuNi-N-CNS. (e) Corresponding FFT patterns. (f) HRTEM image and the enlarged image (g) EDS mapping of C, N, Cu, and Ni elements. | |
The X-ray diffraction (XRD) patterns exhibit that all as-prepared catalysts contain the characteristic peaks of carbon at 22° and 44° (Fig. S13d†). More concretely, CuNi-N-CNS display another three diffraction peaks at 43.6°, 50.8°, and 74.7°, which corresponded to the (111), (200), and (220) facets of Cu0.81Ni0.19 alloy (JCPSD no. 47-1406), respectively. For Ni-N-CNS and Cu-N-CNS, there are metallic Ni and Cu in the corresponding XRD patterns (Fig. S13d†). X-ray photoelectron spectroscopy (XPS) was then carried out to characterize the catalyst composition and elemental states on the surface (Fig. 2b). The high-resolution XPS N1s spectrum can be deconvoluted into pyridinic (∼398.43 eV), M-N (∼399.26 eV), pyrrolic (∼400.92 eV), graphitic (∼402.40 eV), and oxidized (∼404.62 eV) species (Fig. 2c). In the high-resolution Ni 2p spectrum (Fig. 2d), the Ni 2p3/2 peak of CuNi-N-CNS can be fitted into the Ni0 (855.03 eV) peak and Ni2+ (856.39 eV) peak.1,10–13 Moreover, the Cu 2p XPS spectrum in Fig. 2e reveals that the Cu 2p3/2 peak of CuNi-N-CNS can be fitted into Cu/Cu+ (932.26 eV) peak and Cu2+ (934.82 eV) peak.1,13,17 Besides, the energy shift in the spectrum of CuNi-N-CNS compared with the single-metal and non-metal counterparts suggest the strong electronic effect between Cu and Ni atoms (Fig. S14–S17†). In Fig. 2f, Raman spectroscopy confirms the ratio of the defects and graphitization (ID/IG) with a D peak at 1351 cm−1 and a G peak at 1580 cm−1, respectively. The intensity ratio ID/IG is widely used to indicate the activity and conductivity of the catalyst. Obviously, CuNi-C-CNS shows a relatively higher ID/IG ratio of 1.08 in comparison with those of other counterparts. The higher D peak in CuNi-N-CNS could be essentially ascribed to the plentiful O cavities and a high level of defects, which resulted in increased active sites for improving CO2RR performance.
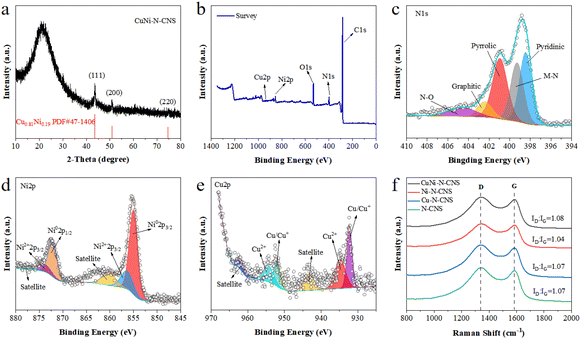 |
| Fig. 2 (a) X-ray diffraction patterns of CuNi-N-CNS. (b) The survey XPS spectrum of CuNi-N-CNS. (c–e) High-resolution spectra of N1s, Ni2p, and Cu2p of CuNi-N-CNS. (f) Raman spectra of CuNi-N-CNS, Ni-N-CNS, Cu-N-CNS, and N-CNS samples. | |
These above characterization results reveal that the composite structure corresponds to carbon nanosheets with abundant Cu–Ni alloys wrapped in Cu/Ni–Nx–carbon (N–C@CuNi alloy) structure at the surface. For these CuNi-N-CNS catalysts, the Cu–Ni alloys cannot be effectively removed by acid etching due to the covering of the carbon layer. Although these embedded Cu–Ni alloys cannot directly involve the CO2RR, the electronic interaction between Cu–Ni alloys and carbon nanosheets can enhance the activity of Cu/Ni–Nx–Cy coordination for CO2RR. Furthermore, recently reported works have suggested that the secondary metal Cu can not only positively shift the Ni 3d orbital energy to the Fermi level and thus accelerate the step of *COOH formation but also cause a considerable reaction barrier for water dissociation and thus decelerate the competing hydrogen evolution reaction.1,13
Electrochemical performance for CO2RR in H-cell
The electrocatalytic CO2RR activity of the developed CuNi-N-CNS catalyst was first investigated in a typical H-cell with CO2 saturated 0.5 M KHCO3 solution as the electrolyte. For comparison, the CO2RR activities of Ni-N-CNS, Cu-N-CNS, and N-CNS were also evaluated. As revealed by linear sweep voltammetry (LSV) curves in Fig. 3a, the CuNi-N-CNS exhibits a remarkably higher current density from −0.18 to −1.18 V vs. RHE compared with these controlled samples, giving current densities of 18 mA cm−2 at −0.78 V and 42 mA cm−2 at −1.18 V. Notably, the current density of CuNi-N-CNS increases faster than that of Ni-N-CNS at high potential, indicating the CuNi alloy may play a key role in elevating the conductivity of CuNi-N-CNS. Furthermore, the catalytic selectivity of these catalysts was also examined by the chronoamperometry technique. The gas and liquid products were monitored by gas chromatography (GC) and nuclear magnetic resonance (NMR), which indicated that CO and H2 were the only two gas products of the reduction, and there was almost no liquid product (Fig. S18†). Fig. 3b compares the faradaic efficiency of CO (FECO) for these prepared catalysts in the potential range from −0.6 V to −1.1 V. Among them, CuNi-N-CNS exhibits impressively high selectivity (>90%) for CO at a wide potential window (−0.8 V to −1.0 V). While the peak FECO of Cu-N-CNS and N-CNS are 58% and 10% at −0.7 V, far lower than that of CuNi-N-CNS. Fig. 3c shows the dependence of the CO partial current density (jCO) on the applied potential. CuNi-N-CNS delivers much higher jCO with respect to the other catalysts and achieves a current density of 11 mA cm−2 at −0.8 V, which is 1.2, 5, and 3 times higher than those of Ni-N-CNS, Cu-N-CNS, and N-CNS, respectively. The turnover frequency (TOF) of CO production for the developed CuNi-N-C catalyst was calculated based on the current density of CO2RR and FECO, which exhibits an exceptionally high TOF of 879 h−1 at −1.1 V, indicating the highly enhanced activity of bimetal-nitrogen sites. The Nyquist plot of CuNi-N-CNS exhibits the smallest semicircle among the prepared catalysts, which suggests its fast interfacial charge-transfer process during the CO2RR process (Fig. 3d). Besides, to further compare the intrinsic activity of these catalysts, cyclic voltammetry (CV) measurements were performed to determine their electrochemical active surface areas (ECSAs) via the evaluation of double-layer capacitance (Cdl). CuNi-N-CNS showed the highest Cdl of 244 mF cm−2, which was 1.3, 1.5, and 2.4-fold of Ni-N-CNS, Cu-N-CNS, and N-CNS, respectively (Fig. S19†), verifying more active catalytic sites in CuNi-N-CNS. To uncover the reaction kinetics on different catalysts, Tafel plots were further determined and analyzed. As shown in Fig. 3e, Tafel slopes of 73.9, 98.3, 84.2, and 113.1 mV decade−1 are found over CuNi-N-CNS, Ni-N-CNS, Cu-N-CNS, and N-CNS, respectively. The lowest Tafel slope of CuNi-N-CNS further confirms its accelerated CO2-to-CO conversion kinetics. Moreover, from the Tafel slope results, one can know that the first electron transfer (CO2 + H+ + e− → *COOH), which generates surface adsorbed *COOH intermediate, is the rate-determining step for CO2RR. The significantly lowered Tafel slope of CuNi-N-CNS indicates the kinetics of this step may be greatly enhanced. Beyond that, the CuNi-N-CNS also exhibits excellent durability for CO2RR, maintaining almost 100% of the initial FE for CO production at −0.8 V after 36 h of continuous electrolysis in an H-type cell (Fig. 3f). The stability of the prepared catalyst was further confirmed by checking the SEM and XRD of the catalyst after long-term electrolysis. The XRD patterns of catalysts of similar mass before and after the stability test showed no obvious changes (Fig. S20,† peaks of Cu0.81Ni0.19 are not so observable owing to the very small amounts of samples). The SEM images of the sample after electrolysis also display the morphology is well preserved, and the element mapping of the post-reaction sample shows the homogeneous distribution of elements and the preservation of CuNi alloy particles (Fig. S20 and S21†). The above results confirmed the excellent stability of the prepared catalyst. The fact that the CuNi-N-CNS catalyst outperformed the counterparts clearly points out the crucial role of the bimetallic alloy in the reaction.
 |
| Fig. 3 (a) LSV curves obtained in CO2-saturated 0.5 M KHCO3 solution (pH = 7.2) in the H-type cell. (b) faradaic efficiency for CO production at various applied potentials. (c) TOF of CuNi-N-CNS at various applied potentials. The blue curve is jCO. (d) Nyquist plots. (e) Tafel plots of the samples. (f) Current–time response of CuNi-N-CNS on carbon paper for CO2RR and the corresponding faradaic efficiency for CO/H2 production at a fixed potential of −0.80 V (versus RHE). | |
Electrochemical performance in the flow cell
Given the CO2 mass transfer limitation in H-type cells as well as the adverse impact of carbonation of CO2RR in neutral or alkaline electrolytes, the CO2RR performance of CuNi-N-CNS was further evaluated in a home-made flow cell with CO2-saturated KCl aqueous as the cathode electrolyte to verify its practical application potential (Fig. 4a and Fig. S22†). The assembled flow cell is set up with CuNi-N-CNS as the cathode in CO2-saturated 3 M KCl, a commercial RuIrTi mesh as the anode in 1 M KOH, an Ag/AgCl (saturated KCl aqueous solution) as the reference electrode in cathode chamber, and the Nafion 117 membrane as the separator. The use of a gas diffusion electrode can circumvent the transport limitation of CO2, leading to a much higher current density of CuNi-N-CNS in the flow cell. To shed light on how electrolytes influence CO2RR, the effects of different catholytes and concentrations on the flow cell performance were first explored.
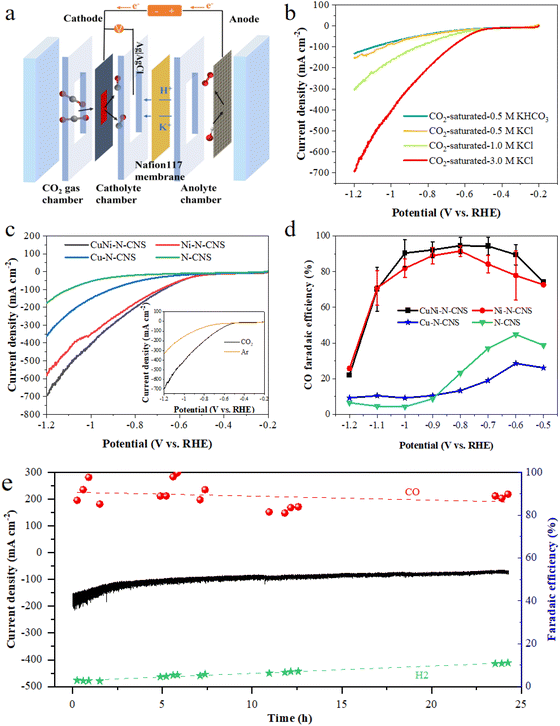 |
| Fig. 4 (a) Schematic diagram showing the basic structure of the flow cell that employs a gas diffusion electrode with the cathode electrolyte of 3 M KCl and the anode electrolyte of 1 M KOH. (b) LSV curves at a scan rate of 10 mV s−1 with different cathode electrolytes. (c) LSV comparison for CuNi-N-CNS, Ni-N-CNS, Cu-N-CNS, and N-CNS. Inset: the LSV comparison for CuNi-N-CNS in Ar- and CO2-saturated 3 M KCl solution. (d) FECO as a function of potentials for CuNi-N-CNS, Ni-N-CNS, Cu-N-CNS, and N-CNS in the flow cell. (e) Stability assessment for CuNi-N-CNS at −0.8 V in the flow cell. | |
As Fig. 4b displays, the CuNi-N-CNS in CO2-saturated 0.5 M KHCO3 aqueous solution presents a similar current density to that in 0.5 M KCl, and the current density significantly escalates from −152 mA cm−2 to −700 mA cm−2 with the KCl concentration increasing from 0.5 M to 3 M, which possibly results from that the high-concentration K+ cations can promote ion exchange. Besides, the selectivity of the reaction products is regulated by the electrolyte (Fig. S23†). It is found that Cl− is much better at converting CO2-to-CO than HCO3− at the same concentration of K+, and a highly concentrated solution of KCl can markedly improve the faradaic efficiency of CO while inhibiting hydrogen evolution.47 More importantly, a mildly acidic environment that can efficiently avoid carbonation is formed by saturating KCl aqueous with CO2. As shown in the inset of Fig. 4c, CuNi-N-CNS conveys a much smaller current density and higher onset potential in Ar-saturated KCl electrolyte compared with that in CO2-saturated KCl, indicating a promising CO2RR performance of CuNi-N-CNS in KCl electrolyte. The CO2RR performances of the controlled catalysts are also studied in the flow cell. The LSV curve trend of each sample in the flow cell is similar to those in H-cell. To be specific, the CuNi-N-CNS achieves a current density of 700 mA cm−2 at −1.2 V vs. RHE, which is 1.2-fold, 2.0-fold, and 3.7-fold of Ni-N-CNS (570 mA cm−2), Cu-N-CNS (355 mA cm−2), and N-CNS (190 mA cm−2), respectively (Fig. 4c). Besides, CuNi-N-CNS exhibits FECO value over 90% in a wide potential ranging from −0.6 to −1.0 V, obviously superior to other counterparts (Fig. 4d). Moreover, we tested the long-term operation stability at −0.80 V as shown in Fig. 4e. The current density can maintain at above 100 mA cm−2 during 24 h constant electrolysis with FECO over 90%, which proves the satisfying performance under industrial high current density. Besides, when tested at 250 mA cm−2, it can still maintain the perfect performance (Fig. S24†). It can be observed through the device diagram after a long-term test that the back of the carbon paper does not display serious flooding and salting out phenomenon, compared with that in the KHCO3 electrolyte (Fig. S25†). Moreover, the existence of carbonate in the electrolyte is confirmed by the phenomenon of precipitation experiment, which shows a very small amount of precipitation occurring in the electrolyte after long-term electrolysis when the BaCl2 solution was dropped into (Fig. S26†). We also tested the catalyst performance in the flow cell of a two-electrode system. The LSV curve showed that the current density could reach 1260 mA cm−2 at 3.8 V. Of course, under this condition, hydrogen production was preferred (Fig. S27 and S28†). While under a smaller cell voltage, CO2RR was dominant, which exhibited a maximum FECO of 94.14% at 2.2 V with a total current density of 180 mA cm−2 (Fig. S29†), thus enabling CO2 electrolysis at commercially relevant conditions (jCO > 100 mA cm−2 and ECell < 3 V).
Conclusion
In summary, we have successfully designed a Cu–Ni alloy-modified carbon nanosheet catalyst for CO2RR through a facile pyrolysis route, which owns a special “willow leaf” shaped structure. Multiple characterizations and experiments uncovered that the intermetallic CuNi alloy encapsulated with the N–C layer played an important role in regulating the electronic properties, thus accelerating *COOH adsorption and increasing the formation of CO. Benefiting from this, CuNi-N-CNS showed a high FE for CO of about 95% and a partial current density of about 400 mA cm−2 at −1.0 V vs. RHE in a self-assembly flow cell using CO2-saturated 3 M KCl solution as catholyte (pH = 4.25), which can also maintain good stability. This work not only affords new insights for the design of high-performance catalysts toward CO2RR but also provides a reference for industrial application through optimizing the electrolyzer component parameters, especially by changing the electrolyte.
Conflicts of interest
There are no conflicts to declare.
Acknowledgements
This work was financially supported by the National key Research & Development Program of China (2022YFE0115900 and 2021YFA1501500), the National Natural Science Foundation of China (No. 22225902, U22A20436 and 22209183), the CAS-Commonwealth Scientific and Industrial Research Organization (CSIRO) Joint Research Projects (121835KYSB20200039), and the Joint Fund of the Yulin University and the Dalian National Laboratory for Clean Energy (Grant YLU-DNL Fund 2021011), Fujian Province Central Government Guides to Science and Technology Development Special Project (No. 2022L3024), and Fujian Natural Science Foundation (2021J01210293).
References
- J. Zhu, M. Xiao, D. Ren, R. Gao, X. Liu, Z. Zhang, D. Luo, W. Xing, D. Su, A. Yu and Z. Chen, Quasi-Covalently Coupled Ni-Cu Atomic Pair for Synergistic Electroreduction of CO2, J. Am. Chem. Soc., 2022, 144, 9661–9671 CrossRef CAS PubMed.
- P. Ding, H. Zhao, T. Li, Y. Luo, G. Fan, G. Chen, S. Gao, X. Shi, S. Lu and X. Sun, Metal-based electrocatalytic conversion of CO2 to formic acid/formate, J. Mater. Chem. A, 2020, 8, 21947–21960 RSC.
- G. Wang, J. Chen, K. Li, J. Huang, Y. Huang, Y. Liu, X. Hu, B. Zhao, L. Yi, T. W. Jones and Z. Wen, Cost-effective and durable electrocatalysts for Co-electrolysis of CO2 conversion and glycerol upgrading, Nano Energy, 2022, 92, 106751 CrossRef CAS.
- M. Chen, S. Wan, L. Zhong, D. Liu, H. Yang, C. Li, Z. Huang, C. Liu, J. Chen, H. Pan, D. S. Li, S. Li, Q. Yan and B. Liu, Dynamic Restructuring of Cu-Doped SnS2 Nanoflowers for Highly Selective Electrochemical CO2 Reduction to Formate, Angew. Chem., Int. Ed., 2021, 60, 26233–26237 CrossRef CAS PubMed.
- J. Li, A. Ozden, M. Wan, Y. Hu, F. Li, Y. Wang, R. R. Zamani, D. Ren, Z. Wang, Y. Xu, D. H. Nam, J. Wicks, B. Chen, X. Wang, M. Luo, M. Graetzel, F. Che, E. H. Sargent and D. Sinton, Silica-copper catalyst interfaces enable carbon-carbon coupling towards ethylene electrosynthesis, Nat. Commun., 2021, 12, 2808 CrossRef CAS PubMed.
- K. Li, J. Xu, T. Zheng, Y. Yuan, S. Liu, C. Shen, T. Jiang, J. Sun, Z. Liu, Y. Xu, M. Chuai, C. Xia and W. Chen, In Situ Dynamic Construction of a Copper Tin Sulfide Catalyst for High-Performance Electrochemical CO2 Conversion to Formate, ACS Catal., 2022, 12, 9922–9932 CrossRef CAS.
- H. B. Yang, S.-F. Hung, S. Liu, K. Yuan, S. Miao, L. Zhang, X. Huang, H.-Y. Wang, W. Cai, R. Chen, J. Gao, X. Yang, W. Chen, Y. Huang, H. M. Chen, C. M. Li, T. Zhang and B. Liu, Atomically dispersed Ni(i) as the active site for electrochemical CO2 reduction, Nat. Energy, 2018, 3, 140–147 CrossRef CAS.
- T. Ahmad, S. Liu, M. Sajid, K. Li, M. Ali, L. Liu and W. Chen, Electrochemical CO2 reduction to C2+products using Cu-based electrocatalysts: A review, Nano Res. Energy, 2022, 1, e9120021 CrossRef.
- W. Liu, S. Wei, P. Bai, C. Yang and L. Xu, Robust coal matrix intensifies electron/substrate interaction of nickel-nitrogen (Ni-N) active sites for efficient CO2 electroreduction at industrial current density, Appl. Catal., B, 2021, 299, 120661 CrossRef CAS.
- Y. Niu, C. Zhang, Y. Wang, D. Fang, L. Zhang and C. Wang, Confining Chainmail-Bearing Ni Nanoparticles in N-doped Carbon Nanotubes for Robust and Efficient Electroreduction of CO2, ChemSusChem, 2021, 14, 1140–1154 CrossRef CAS PubMed.
- L. Ji, L. Li, X. Ji, Y. Zhang, S. Mou, T. Wu, Q. Liu, B. Li, X. Zhu, Y. Luo, X. Shi, A. M. Asiri and X. Sun, Highly Selective Electrochemical Reduction of CO(2) to Alcohols on an FeP Nanoarray, Angew. Chem., Int. Ed., 2020, 59, 758–762 CrossRef CAS PubMed.
- W. Zhu, J. Fu, J. Liu, Y. Chen, X. Li, K. Huang, Y. Cai, Y. He, Y. Zhou, D. Su, J.-J. Zhu and Y. Lin, Tuning single atom-nanoparticle ratios of Ni-based catalysts for synthesis gas production from CO2, Appl. Catal., B, 2020, 264, 118502 CrossRef CAS.
- H. Cheng, X. Wu, M. Feng, X. Li, G. Lei, Z. Fan, D. Pan, F. Cui and G. He, Atomically Dispersed Ni/Cu Dual Sites for Boosting the CO2 Reduction Reaction, ACS Catal., 2021, 11, 12673–12681 CrossRef CAS.
- H. Li, N. Zhang, S. Bai, L. Zhang, F. Lai, Y. Chen, X. Zhu and T. Liu, Strain-Regulated Pd/Cu Core/Shell Icosahedra for Tunable Syngas Electrosynthesis from CO2, Chem. Mater., 2022, 34, 7995–8003 CrossRef CAS.
- Z.-Z. Niu, L.-P. Chi, R. Liu, Z. Chen and M.-R. Gao, Rigorous assessment of CO2 electroreduction products in a flow cell, Energy Environ. Sci., 2021, 14, 4169–4176 RSC.
- H. Yang, Y. Wu, Q. Lin, L. Fan, X. Chai, Q. Zhang, J. Liu, C. He and Z. Lin, Composition Tailoring via N and S Co-doping and Structure Tuning by Constructing Hierarchical Pores: Metal-Free Catalysts for High-Performance Electrochemical Reduction of CO2, Angew. Chem., Int. Ed., 2018, 57, 15476–15480 CrossRef CAS PubMed.
- Z. Yin, H. Peng, X. Wei, H. Zhou, J. Gong, M. Huai, L. Xiao, G. Wang, J. Lu and L. Zhuang, An alkaline polymer electrolyte CO2 electrolyzer operated with pure water, Energy Environ. Sci., 2019, 12, 2455–2462 RSC.
- T. K. Todorova, M. W. Schreiber and M. Fontecave, Mechanistic Understanding of CO2 Reduction Reaction (CO2RR) Toward Multicarbon Products by Heterogeneous Copper-Based Catalysts, ACS Catal., 2019, 10, 1754–1768 CrossRef.
- Q. Chen, K. Liu, Y. Zhou, X. Wang, K. Wu, H. Li, E. Pensa, J. Fu, M. Miyauchi, E. Cortes and M. Liu, Ordered Ag Nanoneedle Arrays with Enhanced Electrocatalytic CO2 Reduction via Structure-Induced Inhibition of Hydrogen Evolution, Nano Lett., 2022, 22, 6276–6284 CrossRef CAS PubMed.
- H. Huo, J. Wang, Q. Fan, Y. Hu and J. Yang, Cu–MOFs Derived Porous Cu Nanoribbons with Strengthened Electric Field for Selective CO2 Electroreduction to C2+ Fuels, Adv. Energy Mater., 2021, 11, 2102447 CrossRef CAS.
- W. Wang, J. Han, Y. Sun, M. Zhang, S. Zhou, K. Zhao and J. Yuan, Metal-Free SeBN Ternary-Doped Porous Carbon as Efficient Electrocatalysts for CO2 Reduction Reaction, ACS Appl. Energy Mater., 2022, 5, 10518–10525 CrossRef CAS PubMed.
- R. Zhao, P. Ding, P. Wei, L. Zhang, Q. Liu, Y. Luo, T. Li, S. Lu, X. Shi, S. Gao, A. M. Asiri, Z. Wang and X. Sun, Recent Progress in Electrocatalytic Methanation of CO2 at Ambient Conditions, Adv. Funct. Mater., 2021, 31, 2009449 CrossRef CAS.
- Q. Chang, Y. Liu, J. H. Lee, D. Ologunagba, S. Hwang, Z. Xie, S. Kattel, J. H. Lee and J. G. Chen, Metal-Coordinated Phthalocyanines as Platform Molecules for Understanding Isolated Metal Sites in the Electrochemical Reduction of CO2, J. Am. Chem. Soc., 2022, 144, 16131–16138 CrossRef CAS PubMed.
- R. Sui, J. Pei, J. Fang, X. Zhang, Y. Zhang, F. Wei, W. Chen, Z. Hu, S. Hu, W. Zhu and Z. Zhuang, Engineering Ag-Nx Single-Atom Sites on Porous Concave N-Doped Carbon for Boosting CO2 Electroreduction, ACS Appl. Mater. Interfaces, 2021, 13, 17736–17744 CrossRef CAS PubMed.
- S. Mou, Y. Li, L. Yue, J. Liang, Y. Luo, Q. Liu, T. Li, S. Lu, A. M. Asiri, X. Xiong, D. Ma and X. Sun, Cu2Sb decorated Cu nanowire arrays for selective electrocatalytic CO2 to CO conversion, Nano Res., 2021, 14, 2831–2836 CrossRef CAS.
- Y. Cheng, S. Yang, S. P. Jiang and S. Wang, Supported Single Atoms as New Class of Catalysts for Electrochemical Reduction of Carbon Dioxide, Small Methods, 2019, 3, 1970026 CrossRef.
- Y. Zhao, L. Zheng, D. Jiang, W. Xia, X. Xu, Y. Yamauchi, J. Ge and J. Tang, Nanoengineering Metal-Organic Framework-Based Materials for Use in Electrochemical CO2 Reduction Reactions, Small, 2021, 17, e2006590 CrossRef PubMed.
- Y. Zhu, X. Yang, C. Peng, C. Priest, Y. Mei and G. Wu, Carbon-Supported Single Metal Site Catalysts for Electrochemical CO2 Reduction to CO and Beyond, Small, 2021, 17, e2005148 CrossRef PubMed.
- G. Wang, J. Chen, Y. Ding, P. Cai, L. Yi, Y. Li, C. Tu, Y. Hou, Z. Wen and L. Dai, Electrocatalysis for CO(2) conversion: from fundamentals to value-added products, Chem. Soc. Rev., 2021, 50, 4993–5061 RSC.
- A. Jedidi, S. Rasul, D. Masih, L. Cavallo and K. Takanabe, Generation of Cu–In alloy surfaces from CuInO2as selective catalytic sites for CO2 electroreduction, J. Mater. Chem. A, 2015, 3, 19085–19092 RSC.
- P. Li, L. Liu, W. An, H. Wang, H. Guo, Y. Liang and W. Cui, Ultrathin porous g-C3N4 nanosheets modified with AuCu alloy nanoparticles and C-C coupling photothermal catalytic reduction of CO to ethanol, Appl. Catal., B, 2020, 266, 118618 CrossRef CAS.
- S. Payra, S. Shenoy, C. Chakraborty, K. Tarafder and S. Roy, Structure-Sensitive Electrocatalytic Reduction of CO2 to Methanol over Carbon-Supported Intermetallic PtZn Nano-Alloys, ACS Appl. Mater. Interfaces, 2020, 12, 19402–19414 CrossRef CAS PubMed.
- T. N. Nguyen and C. T. Dinh, Gas diffusion electrode design for electrochemical carbon dioxide reduction, Chem. Soc. Rev., 2020, 49, 7488–7504 RSC.
- H. Yang, Q. Lin, C. Zhang, X. Yu, Z. Cheng, G. Li, Q. Hu, X. Ren, Q. Zhang, J. Liu and C. He, Carbon dioxide electroreduction on single-atom nickel decorated carbon membranes with industry compatible current densities, Nat. Commun., 2020, 11, 593 CrossRef CAS PubMed.
- Z. Xing, L. Hu, D. S. Ripatti, X. Hu and X. Feng, Enhancing carbon dioxide gas-diffusion electrolysis by creating a hydrophobic catalyst microenvironment, Nat. Commun., 2021, 12, 136 CrossRef CAS PubMed.
- K. Jiang, S. Siahrostami, T. Zheng, Y. Hu, S. Hwang, E. Stavitski, Y. Peng, J. Dynes, M. Gangisetty, D. Su, K. Attenkofer and H. Wang, Isolated Ni single atoms in graphene nanosheets for high-performance CO2 reduction, Energy Environ. Sci., 2018, 11, 893–903 RSC.
- C. Chen, X. Yan, Y. Wu, S. Liu, X. Zhang, X. Sun, Q. Zhu, H. Wu and B. Han, Boosting the Productivity of Electrochemical CO2 Reduction to Multi-Carbon Products by Enhancing CO2 Diffusion through Porous Organic Cage, Angew. Chem., Int. Ed., 2022, 61, e202202607 CAS.
- Z. Chen, G. Yu, B. Li, X. Zhang, M. Jiao, N. Wang, X. Zhang and L. Liu, In Situ Carbon Encapsulation Confined Nickel-Doped Indium Oxide Nanocrystals for Boosting CO2 Electroreduction to the Industrial Level, ACS Catal., 2021, 11, 14596–14604 CrossRef CAS.
- J. E. Huang, F. Li, A. Ozden, A. S. Rasouli, S. Zhang, M. Luo, X. Wang, D. Sinton and E. H. Sargent, CO2 electrolysis to multicarbon products in strong acid, Science, 2021, 372, 1074–1078 CrossRef CAS PubMed.
- M. C. O. Monteiro, M. F. Philips, K. J. P. Schouten and M. T. M. Koper, Efficiency and selectivity of CO2 reduction to CO on gold gas diffusion electrodes in acidic media, Nat. Commun., 2021, 12, 4943 CrossRef CAS PubMed.
- J. Gu, S. Liu, W. Ni, W. Ren, S. Haussener and X. Hu, Modulating electric field distribution by alkali cations for CO2 electroreduction in strongly acidic medium, Nat. Catal., 2022, 5, 268–276 CrossRef CAS.
- Y. Wu, K. Kamiya, T. Hashimoto, R. Sugimoto, T. Harada, K. Fujii and S. Nakanishi, Electrochemical CO2 Reduction Using Gas Diffusion Electrode Loading Ni-doped Covalent Triazine Frameworks in Acidic Electrolytes, Electrochemistry, 2020, 88, 359–364 CrossRef CAS.
- X. Zheng, P. De Luna, F. P. García de Arquer, B. Zhang, N. Becknell, M. B. Ross, Y. Li, M. N. Banis, Y. Li, M. Liu, O. Voznyy, C. T. Dinh, T. Zhuang, P. Stadler, Y. Cui, X. Du, P. Yang and E. H. Sargent, Sulfur-Modulated Tin Sites Enable Highly Selective Electrochemical Reduction of CO2 to Formate, Joule, 2017, 1, 794–805 CrossRef CAS.
- F. P. G. Arquer, C. T. Dinh, A. Ozden, J. Wicks, C. McCallum, D. Sinton and E. H. Sargent, CO2 electrolysis to multicarbon products at activities greater than 1 A cm−2, Science, 2020, 367, 661–666 CrossRef PubMed.
- H. Yano, T. Tanaka, M. Nakayama and K. Ogura, Selective electrochemical reduction of CO2 to ethylene at a three-phase interface on copper(I) halide-confined Cu-mesh electrodes in acidic solutions of potassium halides, J. Electroanal. Chem., 2004, 565, 287–293 CrossRef CAS.
- Z. Wang, P. Hou, Y. Wang, X. Xiang and P. Kang, Acidic Electrochemical Reduction of CO2 Using Nickel Nitride on Multiwalled Carbon Nanotube as Selective Catalyst, ACS Sustainable Chem. Eng., 2019, 7, 6106–6112 CrossRef CAS.
- Z. Zhao, J. Zhang, M. Lei and Y. Lum, Reviewing the impact of halides on electrochemical CO2 reduction, Nano Res. Energy, 2023, 2, e9120044 CrossRef.
|
This journal is © the Partner Organisations 2023 |
Click here to see how this site uses Cookies. View our privacy policy here.