What is necessary to fill the technological gap to design sustainable dye-sensitized solar cells?
Received
17th October 2022
, Accepted 13th January 2023
First published on 16th January 2023
Abstract
The deployment of photovoltaic technologies is forecast to increase substantially in the near to mid future to meet society's energy demand in a sustainable way. Dye-sensitized solar cells (DSSCs) in particular are a prime candidate to be integrated into buildings and to power a myriad of small electronic devices in outdoor and especially indoor environments. As the number of fabricated devices increases, serious consideration should be given to their end-of-life. In this perspective we evaluate various alternatives for each DSSC component from an environmental impact point of view, both during their fabrication and at their end-of-life. We analyze degradation factors occurring during a device's lifetime and discuss the few existing life cycle assessments for this technology, to determine which components can be reused or recycled, and which should be instead disposed of. Our findings show that DSSCs are a particularly sustainable technology; however further studies are needed to fully understand its environmental impact, especially for the scale up of the production process.
1 Introduction
Global energy consumption is forecast to increase by 50% by 2050;1 at the same time emissions of greenhouse gases should be gradually reduced, due to the effect that they have on climate change.2 In order to meet both requirements, humankind must quickly transition to clean and renewable energy production. In 2021, 28.7% of the global electricity was produced using renewable sources,3 a figure that is projected to reach 85% by 2050.4 The installed global capacity of photovoltaics (PV) has increased from 40 GW in 2010 to 709 GW in 2020, and is forecast to reach 8500 GW in 2050.4 The increasing number of solar panels will pose an issue from an environmental perspective, with 78 million tons of waste material expected by 2050.5 Thus, it becomes necessary to devise a recycling and disposal plan for the panels’ end-of-life, for these to fit inside a circular economy framework. On this regard, in 2012 the European Union included solar panels in the waste electrical and electronic equipment (WEEE) regulation.6 According to this policy, from 2018 85% of the panels must be collected back and 80% of that must be recycled or prepared to be re-used. Currently, silicon-based solar panels account for 95% of the total PV production,7 and have well established recycling procedures.8 In recent years new PV technologies have entered or are entering the market and it is important to start evaluating their end-of-life recycling process. Among these, dye-sensitized solar cells (DSSCs) are considered a particularly green technology, due to their environmentally friendly components and low cumulative energy demand (CED)9 values for their fabrication.10 Their introduction on the market has so far been precluded by their low efficiency, however more recently they have been identified as good candidates to be used as ambient light harvesters to power internet of things devices11–13 or for building-integrated photovoltaic applications (BIPV).14–16 The aim of this perspective is to discuss about sustainable design of devices with low environmental impact based on the type of embedded materials, life cycle assessment (LCA) analysis, and degradation factors, building upon the existing literature on the subject.
Sustainability is described as “the focus on meeting the needs of the present without compromising the ability of future generations to meet their needs”.17 The design of sustainable devices begins with the choice of materials and compounds used for their fabrication (Fig. 1). For example some compounds use rare metals, which makes them a non-sustainable choice due to scarce material availability. The choice of materials also plays a big role in determining the efficiency and lifetime of a device, and influences the techniques that can be employed to reuse or recycle device components at their end-of-life. LCA analysis is crucial to understand a device's environmental impact and which of its components have a larger footprint. Among other information that it provides, LCA can help to determine which device components must have a low environmental impact and which ones instead can trade a higher individual sustainability to offer higher efficiency and longer lifetime of a device, which improves the overall device sustainability. Finally, understanding the degradation factors of device components is important to determine which of them can be reused or recycled and which should be designed for safe disposal. To date there is some information available to determine the sustainability of DSSCs and their components, however further studies are required to be able to fully address this subject, especially for what concerns materials of more recent discovery. In this perspective we highlight which research data is still missing to make fully informed decisions, while providing some speculative opinions about where future DSSC research should stir toward based on the authors’ experience.
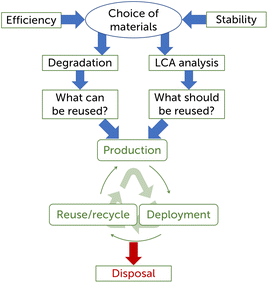 |
| Fig. 1 Scheme of the key parameters and of the key end-of-life analyses for the sustainable design of DSSCs. | |
2 Working principles and applications of dye-sensitized solar cells
The working mechanism of DSSCs mimics that of photosynthesis18 and devices for this technology are classified either as n- or p-type, depending on the direction of the electron flow, or as a combination of the two (tandem).19 In DSSCs photons are absorbed by a dye molecule, which is chemisorbed on a mesoporous layer of a semiconductor material; a redox couple closes the circuit by transporting charges to the counter-electrode (Fig. 2). In an n-type device, when a photon is absorbed by the dye an electron is excited from its highest occupied molecular orbital to its lowest unoccupied molecular orbital. The electron is then injected into the conduction band of the semiconductor layer and transported to the electrode.20 The regeneration of the dye is provided by either a liquid redox mediator or a solid-state hole transporting material (HTM).21
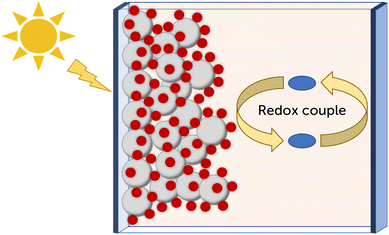 |
| Fig. 2 Schematics of a liquid DSSC. The mesoporous semiconductor (grey discs) is sintered on a conductive substrate and the dye (red discs) is adsorbed on its surface. A solution of the redox couple fills the space between the electrodes. | |
Two of the peculiarities of DSSCs compared to other technologies are their tunable color, given by the use of different dyes, and their transparency, which gives them unique fields of application. For example, in 2020 Dessì et al. developed a series of dyes that absorb in the green region of the light spectrum, with device efficiencies between 5.6 and 6.1%.22 Such devices could be used as part of a greenhouse roof, being able to generate energy without interfering with the plants’ photosynthesis process (Fig. 3b). Other than in greenhouses, these devices can be used in different BIPV projects for the implementation of colorful15 or (almost) colorless windows (Fig. 3a and d).23 Finally, DSSC modules can be an excellent energy source to power small electronic devices in ambient light conditions (Fig. 3c). In this environment DSSCs show their highest potential with efficiencies currently up to 34.5%,24 generating enough energy to power internet of things (IoT) devices and their machine learning algorithms.14
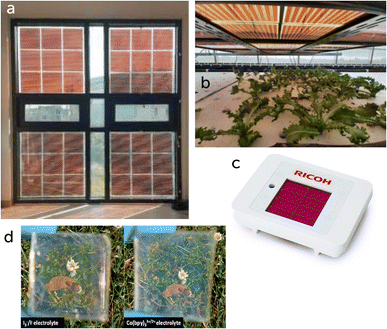 |
| Fig. 3 Examples of DSSC applications: (a) window-integrated PV. Adapted from ref. 15 with permission from Elsevier, copyright 2018. (b) Greenhouse roof. Adapted from ref. 25 under Creative Commons CC-BY license. (c) DSSC-powered IoT sensor. Reproduced with permission from Ricoh Company Ltd., copyright 2022. (d) Colorless DSSC for BIPV applications. Reproduced from ref. 26 under Creative Commons CC-BY-NC-ND license. | |
2.1 Module fabrication
Before focusing on materials and how they can be reused/recycled, it is useful to outline how DSSC modules are fabricated, while a more thorough description is provided by Fakharuddin et al.27 All modules investigated in the literature are based on liquid electrolytes and their fabrication follows this route: fabrication of the photoanode, fabrication of the counter-electrode, substrates match and sealing, and electrolyte injection. Substrates are first patterned, commonly with the laser scribing technique, by selectively removing the conductive thin layer on their surface to allow for the deposition of multiple cells on a single substrate. After that, silver contacts are deposited with different patterns depending on the module design. The mesoporous layer is then deposited by screen printing and subsequently sintered at 450–500 °C. The completed photoelectrode is immersed in a solution containing the dye to sensitize the mesoporous semiconductor. The counter-electrode is also first patterned and decorated with silver contacts, followed by the deposition of the catalyst material. The two substrates are finally sealed together with materials such as thermoplastic, resin or glass frit, and filled with electrolyte solution.
3 Materials and degradation factors
3.1 Device components
One of the claims often made about DSSCs is that they are comprised of non-toxic and abundant materials, two properties that are important in terms of sustainability. While it is true that they can be fabricated using such materials, it is also true that the DSSC literature is full of examples of devices that use toxic metals or critical raw materials (CRMs28,29), which undermine the sustainability claim. Therefore, the choice of materials for device fabrication is the first concern to address to achieve the goal of making DSSCs truly sustainable. Mariotti et al. have compiled an extensive review of materials for DSSCs with a particular focus on sustainability.30 Here, a summary of the choice of materials will be given, together with an indication of where future research should stir toward.
3.1.1 Conductive substrate.
The conductive substrate is the foundation on which all other cell components are deposited. It is comprised of a transparent material (most commonly glass but plastic in the case of flexible substrates) coated with a conductive thin film (conductive metal oxides are the current commercial solution but graphene layers31 or thin metal grids32,33 are also being researched). In DSSCs fluorine-doped tin oxide-coated glass (FTO glass) is the most widely employed substrate and it accounts for over 90% of the mass of the final module, contributing significantly to the environmental impact of the device. There are currently no real alternatives to the FTO layer; however it should be noted that tin is listed as a CRM by the US government and it is close to the threshold in the EU classification as well.28,29 Despite this, the FTO layer in conductive glass substrates is only a few hundreds of nanometers thick, so the amount of material required is very little and it should not pose an issue even in the case of large scale production. Unless there are special engineering needs for a certain application, in which case ultra-thin glass or polymeric substrates could be investigated as an alternative, FTO glass should remain the preferential choice for DSSC fabrication.
3.1.2 Electrical contacts.
Silver is the most commonly used material for electrical contacts in the photovoltaics field, thanks to its high conductivity and high resistance to corrosion. It is usually deposited via screen printing or doctor blading of a precursor paste.34,35 Although it is not included in the list of CRMs, silver's contribution to the device environmental impact is substantial, so it is important to reuse or at least recycle this material (see Section 4). When it comes to device stability, silver is corroded over time by the iodide/triiodide redox couple, a commonly used electrolyte material.36 To overcome this issue, graphene has been proposed as an alternative material for electrical contacts in DSSC modules.37,38 Although there is not a compelling necessity to replace silver in electrical contacts, given its important role in the environmental impact of a DSSC module, research on the feasibility and stability of alternative materials such as graphene is encouraged.
3.1.3 Semiconductor.
Metal oxides are the most commonly used class of materials for the fabrication of the mesoporous semiconducting layer in DSSCs. In n-type devices the material of choice is titanium dioxide (TiO2), a non-toxic and abundant compound that is also used in many other industrial applications such as pigments, food, sunscreen and more.39,40 In p-type devices a good material for this layer has not been identified yet.19 The most commonly used compound is NiO, which is toxic and not well performing. Other metal oxides are being researched, of which CuO is the most promising.20,41,42 Titanium metal is considered a CRM by both the US and the EU,28,29 however as an element it is very abundant on Earth, present mostly as titanium dioxide. Given its good electrical and sustainability characteristics, TiO2 should remain the material of choice for the mesoporous semiconducting layer.
3.1.4 Dye.
Dyes in DSSCs are numerous and varied in light absorbing and electrochemical properties.20 They can be categorised in two main families: organometallic and organic. Efficient organometallic dyes, such as N719 (Fig. 4), are commonly based on ruthenium, which is a very rare and toxic metal.43 Solar cells based on these dyes have a maximum efficiency of 11.9%.44 These compounds have a relatively short synthetic procedure, which reduces chemical waste during their manufacture. However, the scarcity and toxicity of ruthenium, which is considered a CRM, limit their use on a large scale. Viable, more sustainable alternatives are being pursued with copper- or iron-based complexes, but their efficiency remains low.45,46 Organic dyes have a broader color palette, are more efficient, and are not based on CRMs. Devices with this category of dyes reach efficiencies up to 15.2%.47 Although organic dyes vary greatly in molecular structure, all high efficiency compounds are characterized by a lengthy synthetic process,48–51 which wastes a higher amount of solvents and chemicals, and which results in a higher price compared to organometallic dyes. A notable exception is constituted by natural organic dyes extracted from plants, which however do not perform efficiently.52 The commercial future of DSSCs lies in the use of organic dyes, as ruthenium-based metal complexes are not viable on a large scale due to the scarcity of this element, which is also required by other technological industries. However, the extensive synthesis of organic dyes is of concern, as upscaling from milligrams to grams quantities is not always straightforward. The synthesis of compounds at an industrial level often involves different reaction pathways compared to the laboratory, as the price of certain reagents, the use of toxic solvents and the need for greener processes have to be taken into account.53 The synthesis of organic dyes can be compared to that of complex pharmaceutical compounds. As several complex drugs are synthesized every day in a large scale in the pharmaceutical industry, so the synthesis of complex organic dyes should be equally feasible; especially as some of the most used reactions such as Pd-catalyzed cross-coupling and the use of organolithium reagents are already used at industrial level.54 Nevertheless, efficient dyes with a simpler synthetic procedure should be sought, together with the investigation of more natural dyes.
 |
| Fig. 4 Examples of molecular structures of dyes (top) and redox couples (bottom). | |
3.1.5 Redox couple.
The nature of the redox couple determines the type of the final device: liquid, quasi-solid or solid. Liquid redox mediators are the most studied solution and with one exception the only one available commercially. The most commonly employed redox couple is iodide/triiodide, which is good from an abundance point of view, but which presents several drawbacks in terms of device operation, such as high potential losses and corrosivity toward other cell components.55,56 In terms of environmental friendliness worth notice is the use of water-57 and deep eutectic solvent-based electrolytes,58 which remove the use of harmful and volatile organic solvents. However, their efficiency remains low and for the most part iodide/triiodide is still the redox couple employed. In order to find materials with better redox properties organic redox couples have been investigated, which are also very sustainable, with average performance up to 8.6% for the 2-azaadamantan-N-oxyl compound.59 However, it is with cobalt and copper complexes that the best efficiencies are obtained. Cobalt complexes were the first organometallic compounds used as redox couple in DSSCs and they yield high efficiency up to 14.3%.60 However, cobalt is toxic and a CRM, which hinders its widespread commercial adoption. Copper complexes are much more viable from an environmental perspective and they also provide high efficiencies up to 15.2%.47 Regardless of the chemical properties of the redox mediator, all liquid-based devices present long-term stability issues derived from solvent evaporation and leakage through a non perfectly tight sealing.61 For this reason, solid-state HTMs are likely going to become the redox couple of choice for future DSSC commercialization. Many organic compounds have been tested as hole conductors for DSSCs, however they never reached high performance, with the record held by X60 at 7.3%.62 The iodide/triiodide redox couple can also be used in solid-state devices.63 However, it is with copper complexes that solid-state devices are starting to rival with their liquid counterparts, as they now reach a record efficiency of 11.7% with Cu(tmby)2.51 Future research should focus on the fabrication of efficient solid-state devices, which remove some commercialization issues compared to their liquid counterparts. The search for efficient organic hole conductors should continue, together with an improvement of metal complexes based on non-toxic and abundant metal cations such as copper and iron, which to date show the most promise.
3.1.6 Counter-electrode.
The purpose of the counter-electrode is to close the electrical circuit by regenerating the oxidized form of the redox couple. In liquid and in sandwich solid-state devices it is comprised of a catalyst deposited on a conductive substrate, while in monolithic solid-state cells the supporting substrate is removed. Platinum is the most common catalyst for liquid devices, used in conjunction with the iodide/triiodide redox couple. Although it has extraordinary catalytic activity,64 it is also very expensive and a CRM,28,29 which calls for more sustainable alternatives. Carbon, with its many allotropes, is a good replacement. Carbon black, graphene, graphite and carbon nanotubes have all been used as counter-electrode materials, and while they have good catalytic properties, they detach from the conductive substrate over time, thus hindering the long-term stability of devices.65–69 Conductive polymers such as PEDOT (poly(3,4-ethylenedioxythiophene)) are the catalysts of choice for metal complex redox couples. The synthesis of their precursors is often simple, does not require rare metal catalysts, and they can be electrodeposited directly on the substrate via water-based solutions for green processing.70 In monolithic architectures thermally evaporated precious metals (gold, silver) are most often used as counter-electrode.71,72 Since most of these metals are CRMs, carbon-based alternatives have also been investigated but with poor results.73 For what concerns liquid and sandwich solid-state devices, conductive polymers such as PEDOT should become the material of choice: they can be deposited on the underlying substrate in a stable manner, they have an efficiency comparable to that of platinum with the iodide/triiodide electrolyte74,75 and they outperform the latter with metal complex and organic redox couples,70,76 and they are hole selective so that they can be put in direct contact with the photoanode to minimize cell thickness.77 However, the ideal solution is to develop efficient monolithic solid-state devices based on a carbon counter-electrode: carbon is the most sustainable among the aforementioned materials, the removal of one glass substrate reduces the weight and the environmental impact of the final device, and it allows the use of easier forms of device encapsulation, potentially using the same well-established procedure employed for commercial silicon panels.
3.1.7 Encapsulant and sealant.
The encapsulant and sealant play the key role of protecting all internal device components from the outer environment. In liquid devices they also act as a containment wall for the electrolyte and sometimes as spacer between the two substrates. From a sustainability point of view their properties are particularly crucial, as they need to account for two competing interests: on one hand, they need to provide a sealing as tight as possible, to improve device lifetime; on the other hand they need to be (relatively) easy to remove without damaging the other device components, to allow for their potential reuse. Aitola et al. provide a good summary of materials used for the encapsulation and sealing of DSSCs and other photovoltaic technologies.78 Historically thermoplastic polymers such as Surlyn and Bynel have been the edge sealant of choice in DSSC research, as they are easy to apply and require low processing temperatures; however they suffer from relatively high water vapor permeability and instability at temperatures close to their melting point.79 Resins – and especially UV-curable resins – overcome the temperature stability issues of thermoplastics and can be processed at room temperature, resulting in a lower stress for other device components. However, they are degraded by UV light over time,80,81 and they do not provide a perfect seal to avoid solvent evaporation. Glass frits are by far the best encapsulant for DSSCs in terms of protection from the outer environment,82 however they require high temperatures for their deposition, which can degrade other cell components. To overcome this issue, Mendes research group has developed a low temperature laser-based technique for the annealing of this material.83 UV light is harmful to the stability of DSSCs, as it promotes the formation of highly reactive holes in the TiO2 which lead to dye degradation and can directly degrade other cell components.84–86 For this reason, in addition to edge sealants, DSSCs should also be fully enveloped by a UV-protective encapsulant. For this role, materials already used in commercial photovoltaic technologies or in the glass coating industry can be used. As stated above, sustainable encapsulants must walk a narrow path between good operational properties and ease of removal at the end-of-life. If practical disassembling techniques can be developed, the glass frit technology coupled with low temperature deposition will be by far the most suitable one in production lines that do not require continuous operation (such as batch-to-batch processing). Alternatively, UV-curable resins with excellent properties in terms of water and organic solvent vapours permeability should be developed and employed.
3.2 Degradation factors
Understanding the degradation factors of DSSCs is crucial to maximize the device lifetime and to assess the possibility of components reuse. Some components, in fact, can be refreshed and reused at the end of a device life cycle, while others will be too degraded and will have to be made new. Several environmental factors are responsible for device degradation such as UV light, humidity, oxygen, and temperature, which affect each component in different ways (Fig. 5).87 UV light, with its high energy photons, can degrade the dye and the redox couple at a molecular level, especially by activating the catalytic effect of TiO2 for the degradation of organic compounds. Ingress of moisture and oxygen leads to a reduction of the dye regeneration capabilities of the redox couple, unwanted oxidation of molecular components and poisoning of the counter-electrode catalyst.61 High temperatures can facilitate solvent evaporation and HTM morphological rearrangements, while low temperatures can degrade the sealant and reduce kinetic rates for all redox processes. Over time other degradation factors consist in dye desorption from the mesoporous semiconductor, two and in the detachment of the semiconductor and of the catalyst from their respective electrodes.88–90
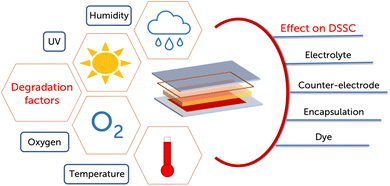 |
| Fig. 5 Degradation factors in DSSCs and their affected components. | |
4 Life cycle assessment of dye-sensitized solar cells
The life cycle assessment (LCA) is a useful tool to quantify and evaluate the environmental impact of a product or a service. It takes into account the constituting raw materials, transportation, manufacturing process, maintenance, and end-of-life of a product. These analyses are based on ISO international standards 14040:2006 (ref. 91) and 14044:2006 (ref. 92) and they can focus on different parts of a product's life. It is also possible to compare the environmental impact of single components or (sub)processes of a product/service to identify those that carry the major impact.
4.1 Life cycle assessment parameters
There are several environmental and energy-related parameters that comprise a LCA, which are dependent not only on the production processes inherent to the analyzed product but also on external factors such as the energy mix of the area in which each component is processed. The cumulative energy demand (CED) quantifies the direct and indirect amount of energy spent for the processing of the product in its entire life cycle from raw materials to transport, fabrication and end-of-life.9 The energy payback time (EPBT)93 is the time required by the solar cell to produce the same amount of energy that was required for its fabrication and is calculated with eqn (1): |  | (1) |
where YAO is the yearly energy output of the DSSC and C is the electricity conversion factor. The carbon dioxide payback time (CO2PBT) indicator describes the time required by the solar cell to produce enough clean electricity to offset the amount of CO2 released during its fabrication. This parameter is affected by the energy mix of both production and deployment areas. It is defined by eqn (2): | 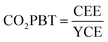 | (2) |
where CEE is the total amount of CO2 emitted during DSSC fabrication and YCE represents the yearly CO2eq emissions of the energy mix in the deployment area.
The life cycle inventory (LCI) is a type of analysis that aims to create a database of every single component and fabrication process of a product containing all the needed materials and energy requirements, and all the waste and emissions generated for each entry. This database is crucial for the completion of a LCA analysis and for the evaluation of alternative materials and processes. The life cycle impact assessment (LCIA) analyses all the components and processes identified in the LCI from the perspective of their impact on the environment and human health, divided in several categories such as climate change, human toxicity, freshwater toxicity, depletion of fossil and mineral sources, and more.
4.2 Current life cycle assessment studies
Life cycle assessment investigations for DSSC module fabrication are scarce and incomplete.94–99 All studies suffer from the absence of a rigorous LCI database for the panel components, especially for what concerns some processing steps. Without this database, and its related LCIA, it is impossible to provide comprehensive life cycle assessments for the DSSC technology. The most complete works are compiled by Parisi et al.100,101 and they are summarized here as an overview of the current state of the art.
In 2014 Parisi et al. performed a LCA study based on data for quantities needed for lab-scale devices that were mathematically up-scaled for the production of a 1 m2 module.100 The work analyzed the environmental impact differences of modules made with three different dyes: N719 (ruthenium-based), D5 (organic) and YD2-o-C8 (zinc porphyrin). The ruthenium precursor was the major source of impact for N719, while for both D5 and YD2-o-C8 the largest impact came from the solvents and chemicals used for their synthesis. In all cases, however, the CED related to the dye was a minimal part of the CED of the whole device, as the amount of dye used for each module is very small (a few hundred milligrams). The environmental impact of the module was evaluated as well using the ReCiPe 2008 methodology.102 The analysis highlighted that FTO glass is the most impactful component in almost all categories. It is interesting to notice that the iodide/triiodide redox mediator has a higher impact compared to cobalt complexes, especially in the ozone depletion category, due to the use of harmful solvents for its production. The silver paste also contributes significantly to all toxicity-related categories.
In 2020 Parisi et al. performed a second, more realistic LCA study based on DSSC modules fabricated at the semi-automated pilot line located in Rome, which can produce A4-size modules for BIPV applications.101 The devices use a ruthenium-based dye with iodide/triiodide as redox mediator. The CED calculation revealed that 35% of the energy used derived from the modules’ production, 30% was due to the sourcing of raw materials, 12% from the FTO glass and a non-negligible contribution came from ruthenium and silver (5% and 3%). Furthermore, the LCIA analysis revealed that silver and ruthenium have the major impact in the four most significant categories, followed by platinum. Electricity also provides a significant contribution in three of these categories. The CED was calculated using the Italian energy mix scenario with a value of 6.7 MJ kW−1 h−1. The energy payback time was estimated ranging between 3.63 and 1.78 years, which is comparable with values obtained for other technologies. They concluded by pointing out that the environmental profile can be improved by reducing the energy involved in the fabrication process and by reducing the use of silver, ruthenium and FTO glass, which contribute for 90% of the total impact according to the ILCD 2011 methodology, a life cycle impact assessment method.103
4.3 Future directions for life cycle assessment studies
As mentioned above, none of the DSSC-related LCA studies existing to date are complete. Most of them do not take into account the whole lifetime of the product (the so-called cradle-to-grave or cradle-to-cradle approaches) and even those that do (e.g. Parisi's 2020 work101) have to make assumptions due to lack of empiric data. Sometimes these assumptions are plausible, sometimes they oversimplify reality. An example of this is present in Parisi's 2014 work:100 in that analysis the authors assume the same efficiency for the panels with the three different dyes, which is unlikely. They also assume that the photoanode is the same for all three dyes, without taking into account that the higher extinction coefficient of e.g. YD2-o-C8 over N719 allows for thinner titania layers, thus reducing the amount of material used per unit area. This is not meant to be a criticism to Parisi's work (as the simplifications they make are reasonable in order to avoid having too complex assumptions), but rather a request for more data. To avoid the use of these assumptions, in fact, there is a pressing need for experimental data on modules/panels that reflect all the advances in the DSSC field of the past 10 years. Most (if not all) module manufacturers, in fact, are still “stuck” with old technologies (Ru dye, iodide electrolyte, platinum counter-electrode), while the time is mature to start experimenting with high-efficiency organic dyes, organic and metal complex-based electrolytes and organic counter-electrodes such as PEDOT or carbon. Experimental data in this regard would greatly help the compilation of future LCA studies for DSSCs. In the meantime, a “theoretical” LCA study that makes a number of reasonable assumptions and analyzes the use of these novel materials compared to the current more established ones could push the experimental work on these new materials forward, if results were in favor of them.
An interesting parameter present in Parisi's later work, especially for what concerns contrast to climate change, is the CO2 payback time. The global warming potential value is present in several of the LCA studies, but the CO2PBT is hardly ever found. It would be interesting to see this parameter analyzed further in future studies, although it is going to be the result of guesswork for many years to come, as this parameter is dependent on the energy mix of the investigated area and all energy mixes worldwide are undergoing important changes yearly as humankind transitions more and more to renewable energy generation. Worth notice is Parisi's conclusion that while this energy transition is ongoing worldwide, the faster this transition is carried out, the higher the CO2PBT will be, as a device has fewer chances of displacing CO2 emissions (the YCE denominator in eqn (2) is decreased). This leads to the counter-intuitive situation that, while a device fabrication process should always strive to minimize this parameter, once the process is in place the hope is to see the CO2PBT value raise as much as possible, as this would correlate to a faster adoption of renewable energies, adoption which is only possible if said device is actually fabricated.
All current LCA studies for the DSSC technology are focused on its application in the BIPV sector. However, in the last five years the use of this technology for indoor, ambient lighting applications has gathered a lot of momentum. LCA studies for this particular niche field are required, as they will differ greatly from those related to BIPV. While the energy and material requirements for device fabrication are the same, in fact, the energy output of the device is very different and about three orders of magnitude lower, given the low energy of the light source. Thus, the values of the EPBT and of the CO2PBT will be much higher compared to full sun applications. Although device degradation will be slower given the lower amount of energy involved, it is highly probable that both parameter values will be higher than the device lifetime. The aim of the deployment of DSSCs in ambient setups is to displace batteries that are currently used to power IoT sensors and other small electronic equipment. Therefore, any LCA of DSSCs for ambient applications should compare the values obtained for the photovoltaic devices to the values obtained for the batteries they are replacing, multiplied by the number of batteries each photovoltaic device is displacing (e.g. assuming that a device can last the lifetime of the electronic equipment it is attached to, the number of batteries that said equipment would need in its lifetime) to decide if DSSCs in ambient environments are a technology worth pursuing. LCAs for batteries are established and comprehensive,104–108 making this comparison easy to be carried out.
5 Reuse, recycling and disposal
At the end of a solar panel lifetime a decision has to be made on how to handle the exhausted device. For commercial photovoltaic technologies there are now procedures in place for the reuse or recycling of a panel's components.8 The constituents of a DSSC module are however very different and a separated analysis has to be made while keeping in mind the LCA analysis and the degradation of each material. To date, there is no large-scale data available on the reuse, recycling or disposal of DSSC panels. Thus, only a qualitative and speculative analysis can be made about how to treat device components at their end-of-life; although intrinsic sustainability figures for each material, coupled with the results of current LCA analyses, can point us in the right direction about the treatment of each component. In this section existing data about the status of DSSC components at their end-of-life will be shown, either inferred directly from the DSSC technology or based on similar conditions in different technologies. Emphasis will be given to data that is still missing, to highlight research that still needs to be conducted to fully understand the DSSC sustainability issue.
Miettunen and Santasalo-Aarnio provide an interesting overview of how DSSC devices can be recycled using common techniques employed for other technologies.109 However, they do not provide any indication of reuse of device components or of methods that are tailored to DSSCs, e.g. washing of electrolyte or desorption of dye from the semiconductor. Here, DSSC-tailored recycling processes will be proposed, however their economical viability compared to simple disposal is unknown. When it comes to device end-of-life, the waste hierarchy (Fig. 6) shows the different levels for waste prevention, from the least (at the top of the pyramid) to the most impactful. For DSSCs, reducing implies the fabrication of more efficient and longer-lived panels, so that fewer materials are needed per unit of generated energy and so that panel replacement needs to happen less often. All the other waste hierarchy steps have to be considered for each module component, once this is disassembled; for this reason the encapsulating material should be designed for easy removal, to avoid breakages during disassembling. Reusing involves the recovery of a component as is (or with a little refreshment) to be used again for the same purpose. Recycling implies a more extensive work-up of a material to be used either for the same or for different applications. The recovery step tries to recuperate the energy embedded in a material when recycling is not possible (e.g. by incineration). Disposal is the least wanted step and consists in bringing the material to a landfill. In the following sections each device component will be assessed to find its place on the waste hierarchy pyramid.
 |
| Fig. 6 The waste hierarchy inverted pyramid, describing the possible end-of-life procedures from the most (at the top) to the least wanted for sustainability. | |
5.1 Photoanode stack
As discussed in Section 4.2 the conductive substrate (in particular FTO glass) is the DSSC component with the highest environmental impact; fortunately, it is also a component that is possible to reuse. In 2014 Binek et al. reported the recovery of FTO glass from perovskite solar cells, showing that devices made with the reused substrate had similar efficiencies compared to the fresh ones.110 In 2021 Chowdhury et al. confirmed Binek's results, claiming that the electrical, morphological and physical properties of the recovered substrate were comparable to the pristine one.111 Despite the differences in design between perovskite and dye-sensitized solar cells, the same conclusions can be applied to the latter as well. In the case of DSSC it is possible to reuse not only the conductive substrate, but also the substrate-semiconductor assembly. Dr Renaud Demadrille, in fact, mentioned during his talk at HOPV21 that according to experimental work in his research group, after desorbing the dye in end-of-life photoanodes derived from commercial panels, a simple TiCl4 treatment (often used for the fabrication of efficient devices) is enough to restore TiO2's complete functionality.112 A similar conclusion was also made by Chen et al.113 although for non-aged devices. Extra considerations should be made in case of flexible plastic substrates, as the UV component of sunlight may degrade the polymeric chains over time, precluding their reuse. In cases in which reuse of the FTO glass substrate is not possible, this component can be recycled to produce non-conductive glass for different purposes, in some cases even without prior removal of other device components.114 As they are a simple metallic strip deposited on top of the FTO, it should be possible to reuse the silver contacts (which, after the FTO glass, are the second most impactful component in a module) together with the substrate-semiconductor assembly after dye removal and after visual inspection for degraded contact paths, which should be restored. However, no experimental data exist to prove this possibility: investigation of silver contacts ageing is required. If the silver contact is too degraded to be reused, its removal and recycling is possible using techniques developed for silicon panels, which allow simple recovery of a high percentage of the initial silver content with high purity.115 The preliminary results that indicate that the whole glass/FTO/TiO2 stack can be efficiently reused even from panels that are decades old are very encouraging for the sustainability of DSSCs; not only because the FTO glass is the biggest contributor to the module's environmental impact, but also because TiO2 sintering is the step that requires the highest energy usage during panel fabrication. Further research on the reuse of the photoanode stack from end-of-life, old commercial panels is needed to confirm its feasibility. From conversations with panel manufacturers such as Solaronix we know that research in this direction is being carried out at these companies, but no public results are available yet.
5.2 Dye
Dye molecules, being responsible for light absorption, are the DSSC component most subject to degradation over time.116,117 There are no studies that analyze dye reuse at the end of a panel's life cycle or its degradation. In principle, dyes can be easily desorbed from the semiconductor by immersing the photoanode in an organic solvent-based alkaline solution.118 After desorption dyes can be reused by separating the degraded fraction from the pristine one using purification techniques such as column chromatography. However, it is unknown if the recoverable molecules can be easily separated from other impurities, if this process is more energy- and environmental impact-intensive compared to disposal of the old dye and application of a fresh one, or if the lifetime of reused dye molecules is comparable to that of freshly synthesized ones. Experimental work focused on dye ageing and its recovery is necessary to come to a conclusion about dye reuse. When looking at LCA studies, the key finding to keep in mind is that the amount of dye employed for module fabrication is so little that its impact on the global LCA is often negligible. This, coupled with the fact that dye reuse is an unknown quantity, leads to the conclusion that the most efficient action for dyes is their disposal. On this regard, dyes should be divided in two categories: organic and metal-containing. In the former case two disposal pathways are available: incineration at high temperature while attached to the semiconductor, or desorption. In the latter case incineration is not possible, as the dye's metal center would not evaporate, but it would instead poison the semiconductor. As discussed in the materials section, organic dyes – despite their higher energy demand due to their synthesis – are the more sustainable option, as they do not rely on scarcely available materials. Even if DSSCs were to become widely adopted, in the grand scheme of industrial production of organic compounds the synthesis of dyes would still represent only a tiny fraction of the yearly general production. Thus, it can be assumed that the precursor materials needed for their synthesis will always be available. Therefore, if future studies will show that dye reuse is not feasible, their disposal should not become a concern. In the case of metal-containing dyes, however, a distinction should be made. If the metal used for dye fabrication is not precious (e.g. Zn porphyrins) then dye disposal is also not a concern. However, if precious or rare metals are used, as is the case of Ru dyes, then metal recovery through recycling steps is paramount, to avoid depletion of a CRM. Once the dye is separated from the photoanode, Ru can be recovered with existing techniques.109 To date, ruthenium is a scarcely recycled material119 and even if recycling is technically feasible in this context, it is still best to avoid its use.
5.3 Redox couple
Together with the dye, the redox couple (either liquid or solid) is probably the DSSC component most subject to degradation. Furthermore, unlike the dye, the liquid electrolyte/HTM is comprised of several different chemicals, which makes separation and reuse harder to achieve. For all these reasons, coupled with the fact that the LCA analysis shows that redox couples do not have a big impact with respect to the overall device environmental footprint, disposal is probably the preferred pathway for this component. Both liquid and solid-state redox couples can be easily washed away from the photoanode using a suitable solvent, and such step should especially be carried out if the iodide/triiodide redox couple is present and the aim is to recycle the FTO glass with a high temperature process, as this material will release toxic gases at high temperatures.109 In the case of cobalt- and copper-based redox mediators the metal can be recovered via existing techniques as in the case of ruthenium, if necessary.
5.4 Counter-electrode
The counter-electrode is usually comprised of a conductive substrate with a catalyst deposited on its surface in the case of sandwich devices, or of an evaporated precious metal or of carbon-based materials in the case of monolithic solid-state devices. In the latter case the precious metal can be easily recovered as a foil after washing away the HTM layer. For sandwich devices, if the conductive substrate is FTO glass, this should be recovered and reused; while flexible, plastic-based substrates – which are less impactful and harder to regenerate – should be disposed of. When it comes to the catalyst deposited on the conductive substrate, preferred sustainable alternatives such as carbon-based materials and PEDOT can be removed from the substrate by incineration, so that a fresh catalyst can be applied. Recovery for these materials is not advised as it is troublesome to remove them from the substrate, as they probably got partially degraded during device lifetime, and as they are based on abundant sources and their production's environmental impact is relative small. In the case of the less sustainable platinum catalyst, this should be chemically removed and recycled. However, dissolution of platinum is only possible with aqua regia, which requires careful handling. Pt can also be recovered with other conventional techniques, if reuse of the FTO substrate is not necessary.109
5.5 Encapsulant and sealant
As stated before, the key end-of-life property of the encapsulant and sealant is that they should be easily removed without causing damage to other device components. Glass frits and resins can only be disposed of, and even thermoplastic materials will likely be too degraded after being exposed to UV light for a long time to be reused or recycled. Only if the device was employed in indoor environments, where UV light is hardly present, thermoplastic polymers may be in good enough conditions for recycling, when mechanical removal from the device is possible.
6 Conclusions and future outlook
Compared to conventional photovoltaic technologies, dye-sensitized solar cells can be fabricated from completely non-toxic materials and with little energy requirements. In fact, although they are not as efficient as silicon panels, their energy payback time is very short and comparable with competing technologies. The most environmental impactful module components according to LCA analyses, and those that represent the vast majority of the module's mass should this be disposed of – conductive substrate, silver contacts and semiconductor – are also those that can be more easily reused or at least recycled at the end-of-life of a device, thus greatly reducing the overall environmental footprint of this technology once an established commercial collection and reuse chain will be in place. For what concerns the other device components, the current state-of-the-art material combination for module fabrication – namely ruthenium dye, iodide/triiodide electrolyte and Pt counter-electrode – is what lowers the sustainability of the DSSC technology the most. Fortunately, all new materials that have been developed in the past decade for each component – and which provide better efficiencies in small-scale devices compared to the aforementioned trio – are more sustainable, have a lower environmental impact and work best in combination with each other; an example of this is the combination of organic dye, cobalt/copper complex electrolyte and PEDOT counter-electrode. Although existing studies already prove that DSSCs have the potential of being a very sustainable technology with low environmental impact, very little is known about the possibility to reuse and recycle their components at their end-of-life, and only educated guesses can currently be made. Therefore, it is important to begin the fabrication of DSSC modules with more modern materials, in order to have empiric evidence on which to base future LCA studies, to help with the choice of materials at the time of DSSC commercialization. Moreover, although large scale fabrication of DSSC devices is likely to begin only in a few years at the earliest, comprehensive studies about the reuse and recycling of DSSC components should begin soon; both to prove the sustainability of this technology to make it more appealing to the market, and to acquire a good foundation of knowledge for when DSSC panels will begin to reach end-of-life on a large scale in the future.
The highest efficiency for DSSCs is obtained in low light environments and although in this scenario a device may never reach its energy payback time, it is important here to consider the difference in environmental impact between the fabrication of a DSSC device compared to that of the batteries that the DSSC is replacing.120 Batteries, in fact, make use of several CRMs,104–108 and although there are established recycling procedures for them, both fabrication and recycling processes are quite energy intensive. Even in this scenario, then, DSSCs are much more promising than existing energy source technologies.
In conclusion, DSSCs have unique features such as the possibility to be fabricated in different colors, potentially high transparency, and high efficiency especially in ambient light conditions, coupled with low-energy fabrication and use of non-toxic and sustainable materials. This combination of properties make them a very promising technology for applications in areas where conventional silicon photovoltaic is not viable, such as low light environments, greenhouse roofs, and other BIPV applications, where light harvesting and energy generation can meet design and aesthetic needs.
Conflicts of interest
Authors declare no competing interests.
Acknowledgements
M. F. acknowledges the support by the Royal Society through the University Research Fellowship (URF\R1\191286), Research Grant 2021 (RGS\R1\211321), and EPSRC New Investigator Award (EP/V035819/1).
Notes and references
-
EIA, International Energy Outlook 2021, U.S. Energy Information Administration technical report, 2021 Search PubMed.
-
IPCC, Climate Change 2021: The Physical Science Basis, Intergovernmental Panel on Climate Change technical report, 2021 Search PubMed.
-
IEA, Renewable Electricity, International Energy Agency technical report, 2022 Search PubMed.
-
IRENA, Global Energy Transformation: A Roadmap to 2050, International Renewable Energy Agency technical report, 2019 Search PubMed.
-
IRENA, End-of-Life Management: Solar Photovoltaic Panels, International Renewable Energy Agency technical report, 2016 Search PubMed.
-
European Union, Directive 2012/19/EU of the European Parliament and of the Council of 4 July 2012 on Waste Electrical and Electronic Equipment (WEEE), 2012 Search PubMed.
-
S. Philipps and W. Warmuth, Photovoltaics Report, Fraunhofer ISE technical report, 2021 Search PubMed.
- M. S. Chowdhury, K. S. Rahman, T. Chowdhury, N. Nuthammachot, K. Techato, M. Akhtaruzzaman, S. K. Tiong, K. Sopian and N. Amin, Energy Strategy Rev., 2020, 27, 100431 CrossRef.
-
R. Frischknecht, N. Jungbluth, H.-J. Althaus, C. Bauer, G. Doka, R. Dones, R. Hischier, S. Hellweg, S. Humbert, T. Köllner, Y. Loerincik, M. Margni and T. Nemecek, Implementation of Life Cycle Impact Assessment Methods, Swiss Centre for Life Cycle Inventories Technical Report 3, v2.0, 2007 Search PubMed.
- N. A. Ludin, N. I. Mustafa, M. M. Hanafiah, M. A. Ibrahim, M. Asri Mat Teridi, S. Sepeai, A. Zaharim and K. Sopian, Renewable Sustainable Energy Rev., 2018, 96, 11–28 CrossRef.
- J. Muangprathub, N. Boonnam, S. Kajornkasirat, N. Lekbangpong, A. Wanichsombat and P. Nillaor, Comput. Electron. Agric., 2019, 156, 467–474 CrossRef.
- Y. Lin, J. Chen, M. M. Tavakoli, Y. Gao, Y. Zhu, D. Zhang, M. Kam, Z. He and Z. Fan, Adv. Mater., 2019, 31, 1804285 CrossRef PubMed.
- M. Haghi Kashani, M. Madanipour, M. Nikravan, P. Asghari and E. Mahdipour, J. Netw. Comput. Appl., 2021, 192, 103164 CrossRef.
- H. Michaels, M. Rinderle, R. Freitag, I. Benesperi, T. Edvinsson, R. Socher, A. Gagliardi and M. Freitag, Chem. Sci., 2020, 11, 2895–2906 RSC.
- H. M. Lee and J. H. Yoon, Appl. Energy, 2018, 225, 1013–1021 CrossRef.
- M. A. Zainol Abidin, M. N. Mahyuddin and M. A. A. Mohd Zainuri, Sustainability, 2021, 13, 7846 CrossRef.
-
WCED, Report of the World Commission on Environment and Development – Our Common Future, World Commission on Environment and Development Technical Report, 1987 Search PubMed.
- Y. Koyama, T. Miki, X.-F. Wang and H. Nagae, Int. J. Mol. Sci., 2009, 10, 4575–4622 CrossRef CAS PubMed.
- E. Benazzi, J. Mallows, G. H. Summers, F. A. Black and E. A. Gibson, J. Mater. Chem. C, 2019, 7, 10409–10445 RSC.
- A. B. Muñoz-García, I. Benesperi, G. Boschloo, J. J. Concepcion, J. H. Delcamp, E. A. Gibson, G. J. Meyer, M. Pavone, H. Pettersson, A. Hagfeldt and M. Freitag, Chem. Soc. Rev., 2021, 50, 12450–12550 RSC.
- I. Benesperi, H. Michaels and M. Freitag, J. Mater. Chem. C, 2018, 6, 11903–11942 RSC.
- A. Dessì, M. Calamante, A. Sinicropi, M. L. Parisi, L. Vesce, P. Mariani, B. Taheri, M. Ciocca, A. D. Carlo, L. Zani, A. Mordini and G. Reginato, Sustainable Energy Fuels, 2020, 4, 2309–2321 RSC.
- F. Grifoni, M. Bonomo, W. Naim, N. Barbero, T. Alnasser, I. Dzeba, M. Giordano, A. Tsaturyan, M. Urbani, T. Torres, C. Barolo and F. Sauvage, Adv. Energy Mater., 2021, 11, 2101598 CrossRef CAS.
- D. Zhang, M. Stojanovic, Y. Ren, Y. Cao, F. T. Eickemeyer, E. Socie, N. Vlachopoulos, J.-E. Moser, S. M. Zakeeruddin, A. Hagfeldt and M. Grätzel, Nat. Commun., 2021, 12, 1777 CrossRef CAS PubMed.
- J. Barichello, L. Vesce, P. Mariani, E. Leonardi, R. Braglia, A. Di Carlo, A. Canini and A. Reale, Energies, 2021, 14, 6393 CrossRef CAS.
- W. Naim, V. Novelli, I. Nikolinakos, N. Barbero, I. Dzeba, F. Grifoni, Y. Ren, T. Alnasser, A. Velardo, R. Borrelli, S. Haacke, S. M. Zakeeruddin, M. Graetzel, C. Barolo and F. Sauvage, JACS Au, 2021, 1, 409–426 CrossRef CAS PubMed.
- A. Fakharuddin, R. Jose, T. M. Brown, F. Fabregat-Santiago and J. Bisquert, Energy Environ. Sci., 2014, 7, 3952–3981 RSC.
-
U. G. Survey, 2022 Final List of Critical Minerals, U.S. Geological Survey, Technical Report 2022-04027, 2022 Search PubMed.
-
G. A. Blengini, C. E. Latunussa, U. Eynard, C. Torres De Matos, D. Wittmer, K. Georgitzikis, C. Pavel, S. Carrara, L. Mancini, M. Unguru, D. Blagoeva, F. Mathieux and D. Pennington, Study on the EU's List of Critical Raw Materials (2020): Final Report, Publications Office of the European Union Technical Report, 2020 Search PubMed.
- N. Mariotti, M. Bonomo, L. Fagiolari, N. Barbero, C. Gerbaldi, F. Bella and C. Barolo, Green Chem., 2020, 22, 7168–7218 RSC.
- G. S. Selopal, R. Milan, L. Ortolani, V. Morandi, R. Rizzoli, G. Sberveglieri, G. P. Veronese, A. Vomiero and I. Concina, Sol. Energy Mater. Sol. Cells, 2015, 135, 99–105 CrossRef CAS.
- Y. Jang, J. Kim and D. Byun, J. Phys. D: Appl. Phys., 2013, 46, 155103 CrossRef.
- P. Bellchambers, S. Varagnolo, C. Maltby and R. A. Hatton, ACS Appl. Energy Mater., 2021, 4, 4150–4155 CrossRef CAS.
- J. D. Fields, M. I. Ahmad, V. L. Pool, J. Yu, D. G. Van Campen, P. A. Parilla, M. F. Toney and M. F. A. M. van Hest, Nat. Commun., 2016, 7, 11143 CrossRef CAS PubMed.
- Y. Yang, S. Seyedmohammadi, U. Kumar, D. Gnizak, E. d. Graddy and A. Shaikh, Energy Procedia, 2011, 8, 607–613 CrossRef CAS.
- M. Wang, N. Chamberland, L. Breau, J.-E. Moser, R. Humphry-Baker, B. Marsan, S. M. Zakeeruddin and M. Grätzel, Nat. Chem., 2010, 2, 385–389 CrossRef CAS PubMed.
- S. Casaluci, M. Gemmi, V. Pellegrini, A. D. Carlo and F. Bonaccorso, Nanoscale, 2016, 8, 5368–5378 RSC.
- P. Mariani, A. Agresti, L. Vesce, S. Pescetelli, A. L. Palma, F. Tomarchio, P. Karagiannidis, A. C. Ferrari and A. Di Carlo, ACS Appl. Energy Mater., 2021, 4, 98–110 CrossRef CAS.
- B. O'Regan and M. Grätzel, Nature, 1991, 353, 737–740 CrossRef.
- A. J. Haider, Z. N. Jameel and I. H. M. Al-Hussaini, Energy Procedia, 2019, 157, 17–29 CrossRef CAS.
- I. R. Perera, T. Daeneke, S. Makuta, Z. Yu, Y. Tachibana, A. Mishra, P. Bäuerle, C. A. Ohlin, U. Bach and L. Spiccia, Angew. Chem., Int. Ed., 2015, 54, 3758–3762 CrossRef CAS PubMed.
- T. Jiang, M. Bujoli-Doeuff, Y. Farré, Y. Pellegrin, E. Gautron, M. Boujtita, L. Cario, S. Jobic and F. Odobel, RSC Adv., 2016, 6, 112765–112770 RSC.
- A. Carella, F. Borbone and R. Centore, Front. Chem., 2018, 6, 481 CrossRef CAS PubMed.
- H. Ozawa, T. Sugiura, T. Kuroda, K. Nozawa and H. Arakawa, J. Mater. Chem. A, 2016, 4, 1762–1770 RSC.
- C. E. Housecroft and E. C. Constable, Chem. Soc. Rev., 2015, 44, 8386–8398 RSC.
- A. R. Marri, E. Marchini, V. D. Cabanes, R. Argazzi, M. Pastore, S. Caramori and P. C. Gros, J. Mater. Chem. A, 2021, 9, 3540–3554 RSC.
- Y. Ren, D. Zhang, J. Suo, Y. Cao, F. T. Eickemeyer, N. Vlachopoulos, S. M. Zakeeruddin, A. Hagfeldt and M. Grätzel, Nature, 2023, 613, 60–65 CrossRef CAS PubMed.
- Y. Hao, Y. Saygili, J. Cong, A. Eriksson, W. Yang, J. Zhang, E. Polanski, K. Nonomura, S. M. Zakeeruddin, M. Grätzel, A. Hagfeldt and G. Boschloo, ACS Appl. Mater. Interfaces, 2016, 8, 32797–32804 CrossRef CAS PubMed.
- H. N. Tsao, C. Yi, T. Moehl, J.-H. Yum, S. M. Zakeeruddin, M. K. Nazeeruddin and M. Grätzel, ChemSusChem, 2011, 4, 591–594 CrossRef CAS PubMed.
- X. Zhang, Y. Xu, F. Giordano, M. Schreier, N. Pellet, Y. Hu, C. Yi, N. Robertson, J. Hua, S. M. Zakeeruddin, H. Tian and M. Grätzel, J. Am. Chem. Soc., 2016, 138, 10742–10745 CrossRef CAS PubMed.
- W. Zhang, Y. Wu, H. W. Bahng, Y. Cao, C. Yi, Y. Saygili, J. Luo, Y. Liu, L. Kavan, J.-E. Moser, A. Hagfeldt, H. Tian, S. M. Zakeeruddin, W.-H. Zhu and M. Grätzel, Energy Environ. Sci., 2018, 11, 1779–1787 RSC.
- R. Baby, P. D. Nixon, N. M. Kumar, M. S. P. Subathra and N. Ananthi, Environ. Sci. Pollut. Res., 2022, 29, 371–404 CrossRef CAS PubMed.
- T. Schaub, Chem.–Eur. J., 2021, 27, 1865–1869 CrossRef CAS PubMed.
- R. W. Dugger, J. A. Ragan and D. H. B. Ripin, Org. Process Res. Dev., 2005, 9, 253–258 CrossRef CAS.
- M. K. Nazeeruddin, F. De Angelis, S. Fantacci, A. Selloni, G. Viscardi, P. Liska, S. Ito, B. Takeru and M. Grätzel, J. Am. Chem. Soc., 2005, 127, 16835–16847 CrossRef CAS PubMed.
- G. Boschloo and A. Hagfeldt, Acc. Chem. Res., 2009, 42, 1819–1826 CrossRef CAS PubMed.
- F. Bella, C. Gerbaldi, C. Barolo and M. Grätzel, Chem. Soc. Rev., 2015, 44, 3431–3473 RSC.
- C. L. Boldrini, A. F. Quivelli, N. Manfredi, V. Capriati and A. Abbotto, Molecules, 2022, 27, 709 CrossRef CAS PubMed.
- F. Kato, A. Kikuchi, T. Okuyama, K. Oyaizu and H. Nishide, Angew. Chem., Int. Ed., 2012, 51, 10177–10180 CrossRef CAS PubMed.
- K. Kakiage, Y. Aoyama, T. Yano, K. Oya, J.-i. Fujisawa and M. Hanaya, Chem. Commun., 2015, 51, 15894–15897 RSC.
- M. I. Asghar, K. Miettunen, J. Halme, P. Vahermaa, M. Toivola, K. Aitola and P. Lund, Energy Environ. Sci., 2010, 3, 418–426 RSC.
- B. Xu, D. Bi, Y. Hua, P. Liu, M. Cheng, M. Grätzel, L. Kloo, A. Hagfeldt and L. Sun, Energy Environ. Sci., 2016, 9, 873–877 RSC.
- M. Sutton, B. Lei, H. Michaels, M. Freitag and N. Robertson, ACS Appl. Mater. Interfaces, 2022, 14, 43456–43462 CrossRef CAS PubMed.
- A. Hauch and A. Georg, Electrochim. Acta, 2001, 46, 3457–3466 CrossRef CAS.
- T. N. Murakami, S. Ito, Q. Wang, M. K. Nazeeruddin, T. Bessho, I. Cesar, P. Liska, R. Humphry-Baker, P. Comte, P. Péchy and M. Grätzel, J. Electrochem. Soc., 2006, 153, A2255 CrossRef CAS.
- G. Veerappan, W. Kwon and S.-W. Rhee, J. Power Sources, 2011, 196, 10798–10805 CrossRef CAS.
- K. Suzuki, M. Yamaguchi, M. Kumagai and S. Yanagida, Chem. Lett., 2003, 32, 28–29 CrossRef CAS.
- J. D. Roy-Mayhew, D. J. Bozym, C. Punckt and I. A. Aksay, ACS Nano, 2010, 4, 6203–6211 CrossRef CAS PubMed.
- H. Hu, B.-L. Chen, C.-H. Bu, Q.-D. Tai, F. Guo, S. Xu, J.-H. Xu and X.-Z. Zhao, Electrochim. Acta, 2011, 56, 8463–8466 CrossRef CAS.
- H. Ellis, N. Vlachopoulos, L. Häggman, C. Perruchot, M. Jouini, G. Boschloo and A. Hagfeldt, Electrochim. Acta, 2013, 107, 45–51 CrossRef CAS.
- P. Liu, B. Xu, K. M. Karlsson, J. Zhang, N. Vlachopoulos, G. Boschloo, L. Sun and L. Kloo, J. Mater. Chem. A, 2015, 3, 4420–4427 RSC.
- M. Chevrier, H. Hawashin, S. Richeter, A. Mehdi, M. Surin, R. Lazzaroni, P. Dubois, B. Ratier, J. Bouclé and S. Clément, Synth. Met., 2017, 226, 157–163 CrossRef CAS.
- M. Xu, G. Liu, X. Li, H. Wang, Y. Rong, Z. Ku, M. Hu, Y. Yang, L. Liu, T. Liu, J. Chen and H. Han, Org. Electron., 2013, 14, 628–634 CrossRef CAS.
- M. Kouhnavard, D. Yifan, J. M. D’Arcy, R. Mishra and P. Biswas, Solar Energy, 2020, 211, 258–264 CrossRef CAS.
- E. Marchini, S. Caramori, C. A. Bignozzi and S. Carli, Appl. Sci., 2021, 11, 3795 CrossRef CAS.
- J. Burschka, V. Brault, S. Ahmad, L. Breau, M. K. Nazeeruddin, B. Marsan, S. M. Zakeeruddin and M. Grätzel, Energy Environ. Sci., 2012, 5, 6089–6097 RSC.
- Y. Cao, Y. Liu, S. M. Zakeeruddin, A. Hagfeldt and M. Grätzel, Joule, 2018, 2, 1108–1117 CrossRef CAS.
- K. Aitola, G. Gava Sonai, M. Markkanen, J. Jaqueline Kaschuk, X. Hou, K. Miettunen and P. D. Lund, Solar Energy, 2022, 237, 264–283 CrossRef CAS.
- A. Visco, C. Scolaro, D. Iannazzo and G. Di Marco, Int. J. Polym. Anal. Charact., 2019, 24, 97–104 CrossRef CAS.
- S. Nikafshar, O. Zabihi, M. Ahmadi, A. Mirmohseni, M. Taseidifar and M. Naebe, Materials, 2017, 10, 180 CrossRef PubMed.
- A. Sharma, D. Agarwal and J. Singh, J. Chem., 2008, 5, 904–913 CAS.
- J. Maçaira, L. Andrade and A. Mendes, Sol. Energy Mater. Sol. Cells, 2016, 157, 134–138 CrossRef.
- S. Emami, J. Martins, L. Andrade, J. Mendes and A. Mendes, Opt. Lasers Eng., 2017, 96, 107–116 CrossRef.
- O. Carp, C. L. Huisman and A. Reller, Prog. Solid State Chem., 2004, 32, 33–177 CrossRef CAS.
- K. F. Jensen, W. Veurman, H. Brandt, C. Im, J. Wilde and A. Hinsch, MRS Online Proc. Libr., 2013, 1537, 1114 Search PubMed.
-
D. Bari, N. Wrachien, G. Meneghesso, C. Andrea, R. Tagliaferro, T. M. Brown, A. Reale and A. Di Carlo, 2013 IEEE International Reliability Physics Symposium (IRPS), 2013, pp. 4B.3.1–4B.3.7 Search PubMed.
- M. Kokkonen, P. Talebi, J. Zhou, S. Asgari, S. A. Soomro, F. Elsehrawy, J. Halme, S. Ahmad, A. Hagfeldt and S. G. Hashmi, J. Mater. Chem. A, 2021, 9, 10527–10545 RSC.
- M. Toivola, J. Halme, L. Peltokorpi and P. Lund, Int. J. Photoenergy, 2009, 2009, e786429 CrossRef.
- E. Figgemeier and A. Hagfeldt, Int. J. Photoenergy, 2004, 6, 127–140 CrossRef CAS.
- G. Syrrokostas, A. Siokou, G. Leftheriotis and P. Yianoulis, Sol. Energy Mater. Sol. Cells, 2012, 103, 119–127 CrossRef CAS.
-
International Organization for Standardization, Environmental Management — Life Cycle Assessment — Requirements and Guidelines (ISO Standard No. 14044:2006), 2006 Search PubMed.
-
International Organization for Standardization, Environmental Management — Life Cycle Assessment — Principles and Framework (ISO Standard No. 14040:2006), 2006 Search PubMed.
-
R. Frischknecht, R. Itten, P. Sinha, M. de Wild-Scholten, J. Zhang, G. A. Heath and C. Olson, Life Cycle Inventories and Life Cycle Assessments of Photovoltaic Systems, International Energy Agency, Technical Report NREL/TP-6A20-73853, 2015 Search PubMed.
- M. L. Parisi, A. Sinicropi and R. Basosi, Int. J. Heat Technol., 2011, 29, 161–169 Search PubMed.
-
M. J. de Wild-Scholten and A. C. Veltkamp, 22nd European Photovoltaic Solar Energy Conference and Exhibition, 2007 Search PubMed.
-
M. L. Parisi, A. Sinicropi and R. Basosi, ECOS 2012, 2012, pp. 119–132 Search PubMed.
- H. Greijer, L. Karlson, S.-E. Lindquist and H. Anders, Renewable Energy, 2001, 23, 27–39 CrossRef CAS.
- N. I. Mustafa, N. A. Ludin, N. M. Mohamed, M. A. Ibrahim, M. A. M. Teridi, S. Sepeai, A. Zaharim and K. Sopian, Solar Energy, 2019, 187, 379–392 CrossRef.
- P. K. Ng and N. Mithraratne, Renewable Sustainable Energy Rev., 2014, 31, 736–745 CrossRef.
- M. L. Parisi, S. Maranghi and R. Basosi, Renewable Sustainable Energy Rev., 2014, 39, 124–138 CrossRef CAS.
- M. L. Parisi, S. Maranghi, L. Vesce, A. Sinicropi, A. Di Carlo and R. Basosi, Renewable Sustainable Energy Rev., 2020, 121, 109703 CrossRef.
-
M. Goedkoop, R. Heijungs, M. Huijbregts, A. De Schryver, J. Struijs and R. van Zelm, ReCiPe 2008: A Life Cycle Impact Assessment Method Which Comprises Harmonised Category Indicators at the Midpoint and the Endpoint Level, Ministry of VROM technical report, Netherlands, 2009 Search PubMed.
-
Institute for Environment and Sustainability (Joint Research Centre), International Reference Life Cycle Data System (ILCD) Handbook: General Guide for Life Cycle Assessment: Provisions and Action Steps, Publications Office of the European Union, LU, 2013 Search PubMed.
- A. Boyden, V. K. Soo and M. Doolan, Procedia CIRP, 2016, 48, 188–193 CrossRef.
- C. M. Costa, J. C. Barbosa, R. Gonçalves, H. Castro, F. J. D. Campo and S. Lanceros-Méndez, Energy Storage Mater., 2021, 37, 433–465 CrossRef.
- S. R. Golroudbary, D. Calisaya-Azpilcueta and A. Kraslawski, Procedia CIRP, 2019, 80, 316–321 CrossRef.
- W. Mrozik, M. A. Rajaeifar, O. Heidrich and P. Christensen, Energy Environ. Sci., 2021, 14, 6099–6121 RSC.
- J. F. Peters, M. Baumann, B. Zimmermann, J. Braun and M. Weil, Renewable Sustainable Energy Rev., 2017, 67, 491–506 CrossRef CAS.
- K. Miettunen and A. Santasalo-Aarnio, J. Cleaner Prod., 2021, 320, 128743 CrossRef CAS.
- A. Binek, M. L. Petrus, N. Huber, H. Bristow, Y. Hu, T. Bein and P. Docampo, ACS Appl. Mater. Interfaces, 2016, 8, 12881–12886 CrossRef CAS PubMed.
- M. S. Chowdhury, K. S. Rahman, V. Selvanathan, A. K. M. Hasan, M. S. Jamal, N. A. Samsudin, M. Akhtaruzzaman, N. Amin and K. Techato, RSC Adv., 2021, 11, 14534–14541 RSC.
-
R. Demadrille, HOPV21, 2021 Search PubMed.
- R.-T. Chen and C.-F. Liao, Int. J. Photoenergy, 2014, 2014, e650945 Search PubMed.
- F. Schoden, A. K. Schnatmann, E. Davies, D. Diederich, J. L. Storck, D. Knefelkamp, T. Blachowicz and E. Schwenzfeier-Hellkamp, Materials, 2021, 14, 6622 CrossRef CAS.
- A. Kuczyńska-Łażewska, E. Klugmann-Radziemska, Z. Sobczak and T. Klimczuk, Sol. Energy Mater. Sol. Cells, 2018, 176, 190–195 CrossRef.
- P. T. Nguyen, P. E. Hansen and T. Lund, Solar Energy, 2013, 88, 23–30 CrossRef CAS.
- T. Lund, P. T. Nguyen, H. M. Tran, P. Pechy, S. M. Zakeeruddin and M. Grätzel, Solar Energy, 2014, 110, 96–104 CrossRef CAS.
- P. J. Holliman, K. J. Al-Salihi, A. Connell, M. L. Davies, E. W. Jones and D. A. Worsley, RSC Adv., 2013, 4, 2515–2522 RSC.
-
L. Sundqvist Ökvist, X. Hu, J. Eriksson, J. Kotnis, Y. Yang, E. Yli-Rantala, J. Bacher, H. Punkkinen, T. Retegan, M. González Moya and M. Drzazga, Production Technologies of CRM from Secondary Resources: SCRREEN Deliverable D4.2, 2018 Search PubMed.
- Editorial, Nature, 2021, 595, 7, https://www.nature.com/articles/d41586-021-01735-z Search PubMed.
|
This journal is © The Royal Society of Chemistry 2023 |
Click here to see how this site uses Cookies. View our privacy policy here.